冷喷涂技术冷方法的产生和它的现状
冷喷涂技术冷方法的产生和它的现状
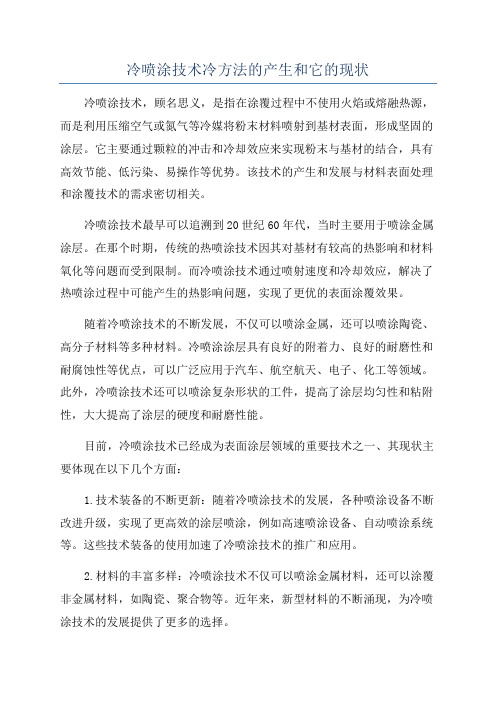
冷喷涂技术冷方法的产生和它的现状冷喷涂技术,顾名思义,是指在涂覆过程中不使用火焰或熔融热源,而是利用压缩空气或氮气等冷媒将粉末材料喷射到基材表面,形成坚固的涂层。
它主要通过颗粒的冲击和冷却效应来实现粉末与基材的结合,具有高效节能、低污染、易操作等优势。
该技术的产生和发展与材料表面处理和涂覆技术的需求密切相关。
冷喷涂技术最早可以追溯到20世纪60年代,当时主要用于喷涂金属涂层。
在那个时期,传统的热喷涂技术因其对基材有较高的热影响和材料氧化等问题而受到限制。
而冷喷涂技术通过喷射速度和冷却效应,解决了热喷涂过程中可能产生的热影响问题,实现了更优的表面涂覆效果。
随着冷喷涂技术的不断发展,不仅可以喷涂金属,还可以喷涂陶瓷、高分子材料等多种材料。
冷喷涂涂层具有良好的附着力、良好的耐磨性和耐腐蚀性等优点,可以广泛应用于汽车、航空航天、电子、化工等领域。
此外,冷喷涂技术还可以喷涂复杂形状的工件,提高了涂层均匀性和粘附性,大大提高了涂层的硬度和耐磨性能。
目前,冷喷涂技术已经成为表面涂层领域的重要技术之一、其现状主要体现在以下几个方面:1.技术装备的不断更新:随着冷喷涂技术的发展,各种喷涂设备不断改进升级,实现了更高效的涂层喷涂,例如高速喷涂设备、自动喷涂系统等。
这些技术装备的使用加速了冷喷涂技术的推广和应用。
2.材料的丰富多样:冷喷涂技术不仅可以喷涂金属材料,还可以涂覆非金属材料,如陶瓷、聚合物等。
近年来,新型材料的不断涌现,为冷喷涂技术的发展提供了更多的选择。
3.应用领域的扩大:冷喷涂技术的应用范围越来越广泛,不仅可以应用于传统的汽车、航空航天等行业,还可以应用于新兴的能源、生态环境等领域。
冷喷涂技术能够提供持久的耐磨性和优良的导热性,有望在新能源电池、太阳能电池等领域得到更广泛的应用。
然而,冷喷涂技术仍面临一些挑战。
首先,冷喷涂技术的喷涂效率和成本仍然需要进一步优化。
由于涂层与基材的结合不像热喷涂那样充分,喷涂速度相对较低,降低了涂层的生产效率。
2023年冷喷涂行业市场分析现状
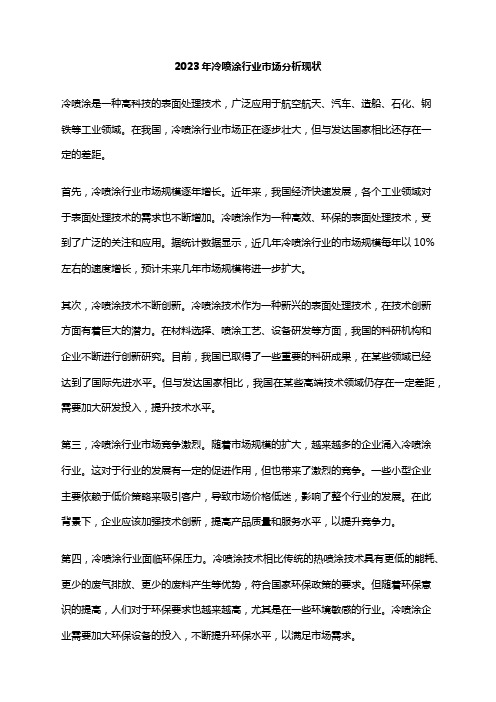
2023年冷喷涂行业市场分析现状冷喷涂是一种高科技的表面处理技术,广泛应用于航空航天、汽车、造船、石化、钢铁等工业领域。
在我国,冷喷涂行业市场正在逐步壮大,但与发达国家相比还存在一定的差距。
首先,冷喷涂行业市场规模逐年增长。
近年来,我国经济快速发展,各个工业领域对于表面处理技术的需求也不断增加。
冷喷涂作为一种高效、环保的表面处理技术,受到了广泛的关注和应用。
据统计数据显示,近几年冷喷涂行业的市场规模每年以10%左右的速度增长,预计未来几年市场规模将进一步扩大。
其次,冷喷涂技术不断创新。
冷喷涂技术作为一种新兴的表面处理技术,在技术创新方面有着巨大的潜力。
在材料选择、喷涂工艺、设备研发等方面,我国的科研机构和企业不断进行创新研究。
目前,我国已取得了一些重要的科研成果,在某些领域已经达到了国际先进水平。
但与发达国家相比,我国在某些高端技术领域仍存在一定差距,需要加大研发投入,提升技术水平。
第三,冷喷涂行业市场竞争激烈。
随着市场规模的扩大,越来越多的企业涌入冷喷涂行业。
这对于行业的发展有一定的促进作用,但也带来了激烈的竞争。
一些小型企业主要依赖于低价策略来吸引客户,导致市场价格低迷,影响了整个行业的发展。
在此背景下,企业应该加强技术创新,提高产品质量和服务水平,以提升竞争力。
第四,冷喷涂行业面临环保压力。
冷喷涂技术相比传统的热喷涂技术具有更低的能耗、更少的废气排放、更少的废料产生等优势,符合国家环保政策的要求。
但随着环保意识的提高,人们对于环保要求也越来越高,尤其是在一些环境敏感的行业。
冷喷涂企业需要加大环保设备的投入,不断提升环保水平,以满足市场需求。
综上所述,冷喷涂行业市场在我国正处于快速发展的阶段,市场规模逐年增长,技术不断创新。
但与发达国家相比还存在一定的差距,市场竞争激烈,面临环保压力。
冷喷涂企业应该加强技术创新,提高产品质量和服务水平,增强环保意识,以提升竞争力,推动行业的进一步发展。
冷喷涂工艺的进展及应用现状
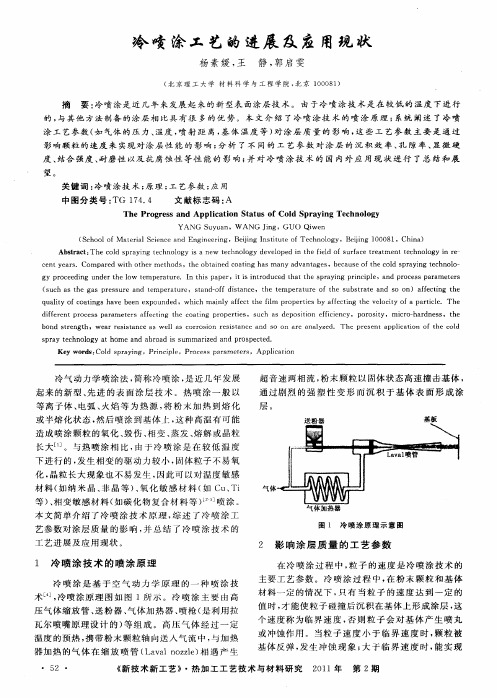
( c o l fM aeilS in ea dEn ie r g ej g I siueo c n lg S h o tr ce c n gn ei ,B in n t t f o a n i t Teh oo y,B in 0 0 1,C ia ej g1 0 8 i hn )
Ab tac : sr t Thec d s a i g t c o o s a n w e h l g e eope n t il u f c r a m e tt c no o y i e ol pr y n e hn l gy i e t c no o y d v l d i he fed ofs ra e te t n e h l g n r — c nty ar .Com p r d w ih ot rm e h ds,t eobt i d c a i g ha a y a a t ge e e s a e t he t o h ane o tn sm n dv n a s,b c u eoft ol pr yig t c o o e a s hec d s a n e hn l — g r e di de h ow e p r t r . I h spa e Y p oc e ng un rt e l t m e a u e n t i p r,i i n r du e h tt pr yig p i i l t si t o c d t a he s a n rncp e,a o e spa a e e s nd pr c s r m t r ( u h a he ga e s r n e pe a ur san — fdit n e, t e pe a u e oft ub tat nd O on) afe tng t s c st s pr s u e a d t m r t e, t d of s a c he t m r t r he s s r e a S f c i he q al y ofc tng a e n e o u i oa i s h ve b e xp und d,whih m anl fe tt i op ri sby a f c ig t e v l ct ril . The t e c i y a fc he fl pr e te fe tn h e o iy ofa pa tce m dfe e o e spa a e e s a f c ig h c tng r p r is, s h a p ii n e fce y, p ost m ir — a dne s, t if r ntpr c s r m t r fe tn t e oa i p o e te uc s de osto fiinc or iy, co h r s he
2024年冷喷涂市场需求分析

2024年冷喷涂市场需求分析引言随着工业发展的进一步推进,冷喷涂技术作为一种新兴的表面涂层处理方法,被广泛应用于各个行业。
本文将对冷喷涂市场需求进行分析,旨在了解目前市场对冷喷涂技术的需求状况以及未来的发展趋势。
市场背景冷喷涂技术是一种将涂料或者涂层材料喷射到工件表面形成保护层的方法。
相比传统的热喷涂技术,冷喷涂技术具有低温、低能耗、无污染等优势,越来越受到市场的关注和青睐。
市场需求分析1. 节能环保冷喷涂技术与传统的热喷涂技术相比,不需要加热处理,能有效降低能耗,减少环境污染。
随着全球对环境保护意识的提高,节能环保的需求也越来越迫切,因此对冷喷涂技术的需求也在不断增加。
2. 表面保护在工业生产中,很多工件需要在表面形成一层保护膜,以延长使用寿命、提高耐磨性等。
冷喷涂技术能够形成均匀的涂层,提供良好的表面保护效果,满足市场对于表面保护的需求。
3. 轻质材料应用冷喷涂技术适用于对轻质材料的涂层处理,如铝合金、镁合金等。
随着轻量化技术在汽车、航空航天、船舶等领域的应用,对轻质材料涂层的需求也在增加,冷喷涂技术在这些领域具有较大的市场潜力。
4. 高性能涂层需求冷喷涂技术能够制备出高性能的涂层,如高硬度、高耐磨、高耐腐蚀等。
在冶金、石油化工、航空航天等行业中,对于耐磨性、耐腐蚀性的需求非常迫切,冷喷涂技术能够满足这些高性能涂层的需求。
5. 维修和翻新市场冷喷涂技术在维修和翻新领域也有广泛的应用。
对于老化、损坏的工件,通过冷喷涂技术进行修复,能够延长使用寿命,减少更换成本,因此在维修和翻新市场中有较大的需求。
未来发展趋势随着冷喷涂技术的不断创新和推广应用,未来冷喷涂市场有望呈现以下趋势:1. 技术推陈出新随着科技的进步,冷喷涂技术将会不断推陈出新,不断提升涂层质量和性能。
新的冷喷涂材料和设备的研发,将为市场需求提供更好的解决方案。
2. 扩大应用领域随着对冷喷涂技术的认可度提高,其应用领域也将扩大。
除了传统的工业领域,冷喷涂技术有望应用于更多新兴领域,如新能源、电子等。
2023年冷喷涂行业市场规模分析

2023年冷喷涂行业市场规模分析冷喷涂(Cold spray)是一种新兴的喷涂工艺,采用压缩空气加速高速喷射金属粉末形成高速喷射流,在高速气流的冲击下,金属粉末颗粒受到严重变形,其表面原子产生高度活化,通过高速冲击和沉积,将喷材快速形成冷喷涂复合材料。
冷喷涂工艺具有高沉积效率、低能耗、无热应力等优势,在军工、航空航天、汽车制造等领域得到广泛应用,具有广阔的市场前景。
一、冷喷涂的市场需求分析1. 军工领域军工领域是冷喷涂技术的最早应用领域之一。
随着武器装备的高度复杂化和技术装备的高新化,军工装备对表面涂层材料的性能要求越来越高。
冷喷涂技术在生产模拟航空发动机部件、导弹外壳等方面已有广泛应用,其高效、高精度、低损伤的特点是军工行业的需求所在。
另外,冷喷涂技术可以在不影响基材表面质量和形状的情况下实现高精度复合材料的制备,可以降低基材的维修成本和维修时间,成为军工领域的一项重要技术。
2. 航空航天领域航空航天领域是冷喷涂技术应用的另一个重要领域。
冷喷涂技术可以用于制备航空、航天发动机叶片、涡轮、加速器等高温零件,具有与实际成型件性能相似的优点。
冷喷涂制备的复合材料可以显著提高航空器的性能和耐用性,提高飞行安全,同时也减少了对环境的影响,成为航空航天领域的热门技术。
3. 汽车制造领域随着汽车制造行业的不断发展,汽车制造所需材料种类、性能要求也在不断提高。
冷喷涂技术可以用于制备汽车零部件的表面涂层,例如制动系统、缸体、加速器、支架等,可增强汽车零部件的耐磨性、耐高温性、耐腐蚀性等性能。
冷喷涂技术还可以用于制备汽车的外壳、底盘和内饰,实现模块化设计,大大缩短了生产周期和成本。
二、冷喷涂市场现状分析1. 技术方面技术方面,国内在冷喷涂领域的技术研究和成熟应用相对较晚,与国际先进水平还有一定的差距。
目前,冷喷涂技术在国内主要是由一些国企、高校和科研单位开展研究,但企业对技术应用的投入和实践较少。
与国际先进水平相比,国内的冷喷涂技术尚处于初级阶段,需要加快研发投入和技术更新,推动冷喷涂技术的产业化进程。
喷射式制冷的发展研究现状

喷射式制冷的发展研究现状喷射式制冷是一种先进的制冷技术,具有高效、节能、环保等优点,被广泛应用于工业、商业和家庭领域。
在面临能源紧缺和环境问题日益严重的背景下,喷射式制冷的研究和发展具有重要意义。
本文将介绍喷射式制冷的概念、发展现状、研究方法、研究结果和结论与展望,以期为相关领域的研究和实践提供参考。
喷射式制冷是一种基于喷射原理的制冷技术,其主要组成部分包括喷嘴、吸入室、混合室和扩压器。
喷射式制冷器利用高压流体通过喷嘴喷出,在吸入室形成低压区,从而吸入室内的气体或液体混合物,然后在混合室进行混合和压缩,最后通过扩压器排出。
在这个过程中,蒸发器中的制冷剂吸收被冷却物体的热量,产生制冷效果。
随着技术的不断发展,喷射式制冷已经在国内外得到了广泛应用。
在市场前景方面,喷射式制冷市场呈现出稳步增长的趋势。
随着消费者对高效、节能、环保等要求的不断提高,喷射式制冷的市场份额也在逐步扩大。
同时,政府对环保和节能的支持也在推动喷射式制冷市场的发展。
在生产工艺和技术应用方面,喷射式制冷的生产工艺和技术已经相当成熟。
目前,国内外众多企业都在从事喷射式制冷设备的生产和销售,并且一些企业已经具备了较强的研发和创新能力。
喷射式制冷技术的应用领域也在不断拓展,除了传统的工业和商业领域,还涉及到新能源、生物医药、航空航天等领域。
本文主要采用文献调研、问卷调查和实地调研相结合的方法,对喷射式制冷的发展现状进行了深入研究。
通过文献调研了解喷射式制冷的基本原理和发展历程,并对现有的研究成果进行梳理和评价。
利用问卷调查收集从事喷射式制冷研发、生产和应用的企业和专家对喷射式制冷的看法和建议,了解该领域的最新动态和前沿技术。
结合实地调研,对喷射式制冷在各领域的应用情况进行深入了解,为研究结果的准确性提供保障。
通过对喷射式制冷的发展现状进行深入研究,本文得出以下市场规模方面:喷射式制冷市场呈现出稳步增长的趋势,市场规模不断扩大。
预计未来几年,随着消费者对高效、节能、环保等要求的不断提高,喷射式制冷的市场份额还将进一步扩大。
冷喷涂技术发展历史、趋势与挑战

㊀第43卷㊀第4期2024年4月中国材料进展MATERIALS CHINAVol.43㊀No.4Apr.2024收稿日期:2024-01-23㊀㊀修回日期:2024-03-30基金项目:国家自然科学基金资助项目(52171072)第一作者:王婉青,女,1999年生,硕士研究生通讯作者:所新坤,男,1982年生,教授,博士生导师,Email:suoxinkun@DOI :10.7502/j.issn.1674-3962.202401026冷喷涂技术发展历史㊁趋势与挑战王婉青1,熊成涛1,高建红2,任㊀潞1,徐小龙2,张勤号1,陈秀勇1,所新坤1(1.宁波大学机械工程与力学学院多维增材制造研究所,浙江宁波315000)(2.安徽马钢表面技术股份有限公司,安徽马鞍山243000)摘㊀要:冷喷涂作为一种新兴的涂层制备技术,具有沉积效率高㊁涂层孔隙率低㊁结合强度高等优点,引起了产业界的广泛关注,在航空航天㊁汽车㊁能源㊁海洋工程㊁石油和化工等领域有着广泛的应用前景㊂经过30多年的发展,冷喷涂技术的研究已从基础理论研究转变到产业化应用研究,在简述冷喷涂技术原理的基础上,综述了冷喷涂技术在成形机理㊁材料体系等方面的研究历程;其次,调研了冷喷涂近年来的发展现状,梳理并提出了未来冷喷涂技术向高性能㊁低成本㊁增材制造等方向发展的趋势,包括喷涂系统㊁粉末㊁工作气体以及离线编程路径设计等方面的改进提升;最后,提出了冷喷涂技术现存的问题与未来发展展望㊂关键词:冷喷涂;涂层;增材制造;发展趋势中图分类号:TG174.442㊀㊀文献标识码:A㊀㊀文章编号:1674-3962(2024)04-0273-08引用格式:王婉青,熊成涛,高建红,等.冷喷涂技术发展历史㊁趋势与挑战[J].中国材料进展,2024,43(4):273-280.WANG W Q,XIONG C T,GAO J H,et al .History,Trends and Challenges of Cold Spray[J].Materials China,2024,43(4):273-280.History ,Trends and Challenges of Cold SprayWANG Wanqing 1,XIONG Chengtao 1,GAO Jianhong 2,REN Lu 1,XU Xiaolong 2,ZHANG Qinhao 1,CHEN Xiuyong 1,SUO Xinkun 1(1.Institute of Multi-Dimensional Additive Manufacturing,Faculty of Mechanical Engineering and Mechanics,Ningbo University,Ningbo 315000,China)(2.Anhui Ma Steel Surface Technology Co.,Ltd.,Ma a nshan 243000,China)Abstract :Cold spray is an emerging coating preparation technology with advantages of high deposition efficiency,lowporosity and high bonding strength,which has broad application potential in aerospace,automobile,energy,ocean,petrole-um and chemical industries.The research focus of cold spray has transformed from theoretical research to industrial applica-tion over the past 30years.Therefore,development history of bonding mechanisms and material systems of cold spray was reviewed in this paper,followed a brief introduction on the principle of cold spray.Furthermore,development trends of cold spray in terms of high performance,low cost and additive manufacturing were summarized,involving improvements of spray systems,powders,working gases and off-line path optimization.Finally,challenges and prospects of cold spray were pro-posed.Key words :cold spray;coating;additive manufacturing;development trend1㊀前㊀言冷喷涂(cold spray,CS),又称为冷空气动力喷涂(cold gas dynamic spray,CGDS),是一种材料固态沉积技术,工作原理如图1所示,将一定温度和压力条件下的气体(氮气㊁氦气㊁压缩空气等)送入特定结构的喷嘴中产生高速气流,然后将具有一定粒径的粉末颗粒送入高中国材料进展第43卷速气流中,通过加速加热,固态粉末高速撞击基体,产生剧烈的塑性变形而沉积在基体表面形成涂层[1-4]㊂与传统的热喷涂技术[5,6]相比,冷喷涂最突出的特点是喷涂温度低和粉末颗粒速度高[7],因此冷喷涂技术更适合用于沉积熔点较低和易氧化金属材料的涂层,如镁㊁铝㊁铜㊁钛等材料,且冷喷涂过程存在 喷丸效应 [8],可使涂层之间产生残余压应力,改善涂层的结合情况㊂冷喷涂在上述材料零部件修复和再制造㊁增材制造及功能涂层等领域均有广阔的发展前景[9-11]㊂图1㊀冷喷涂工作原理示意图[4]Fig.1㊀Principle schematic diagram of cold spray [4]2㊀冷喷涂技术的发展历程冷喷涂技术发展经历了2个阶段㊂第1个阶段是原理探索阶段(1980年到2015年),主要集中于理论研究㊂1980年,前苏联科学院西伯利亚分院的理论与应用力学研究所的研究人员Papyrin 及其同事进行超声速风洞试验时发现,当固体颗粒在高速状态下,会逐层沉积在基材表面,最终形成具有一定厚度的涂层㊂因此,在1990年提出了冷喷涂的概念,发表了第一篇冷喷涂的论文[1],并且在1994年申请了第一个冷喷涂专利[2]㊂1995年,McCune 等[8]首次将气体动力学模型运用到冷喷涂中并预测了冷喷涂过程中粉末的速度㊂1999年,Gilmore 等[12]创新性地提出了冷喷涂过程中的临界速度的概念,即只有当颗粒速度加速达到一定值时才会在基体表面发生沉积㊂后续相关学者对不同种类的材料进行了冷喷涂实验以获得不同材料的临界速度㊂例如,2002年,Stoltenhoff 等[13]发现当含氧量较低的球形铜颗粒的速度超过临界速度(约为570m /s)时才会发生沉积㊂2003年,Assadi 等[14]利用数值模拟的方法模拟了颗粒的撞击过程,提出了一种冷喷涂过程中颗粒结合机制的假设,第一次指出颗粒之间所发生的粘结可归因于在颗粒表面发生的绝热剪切失稳现象㊂同时,根据经验归纳总结了冷喷涂形成涂层的临界速度公式,并通过公式计算指出颗粒温度每上升100ħ,粒子沉积的临界速度将减小40m /s,为后续颗粒预热的研究提供了理论支撑㊂随后,Schmidt 等[15]在Assadi 上述研究基础上考虑了颗粒尺寸的影响,进一步地推导出了冷喷涂临界速度公式㊂2006年,Richter 等[16]和Kreye 等[17]通过实验表明颗粒温度的升高会提高冷喷涂涂层质量㊂2007年,Li 等[18]在研究铝颗粒在铝基体上的变形行为时,首次观察到铝粉表面氧化膜对铝颗粒与基体间的结合情况的影响㊂2007年,Fukumoto 等[19]率先提出基体温度对冷喷涂过程中的颗粒沉积效率的影响,表明基体温度与颗粒的沉积效率呈正比,同时证明了基体预热对于提高冷喷涂涂层质量的重要性㊂2008年,Ogawa 等[20]首次研究了基体表面条件对颗粒沉积和冷喷涂涂层机械性能的影响㊂在第1阶段的原理探索过程中,冷喷涂材料体系得到了极大的发展㊂起初,学者们在应用较为广泛的金属基体上进行冷喷涂技术的相关研究㊂1996年,Tokarev [21]首次尝试并成功利用冷喷涂技术在钢材表面沉积铝涂层㊂同年,Mccune 等[22]成功制备了钢涂层和铜涂层,观察并对比了冷喷涂工艺与热喷涂工艺制备的同种材料涂层的机械性能和微观结构㊂随后,Dykhuizen 等[23]和Gilmore 等[12]又分别在不锈钢基体和铝基材上成功喷涂铜涂层㊂2000年,Karthikeyan 等[24]首次成功喷涂钛涂层并探讨了不同工艺参数对钛颗粒沉积效率和钛涂层性能的影响㊂同年,Mccune 等[25]成功通过冷喷涂技术制备了铁涂层和铜涂层,并观察到与热喷涂处理不同的是,通过冷喷涂技术制备的涂层,其颗粒结合界面并未出现熔化现象,其结合机制多为机械结合㊂2004年,Steenkiste 等[26]首次尝试利用大气冷喷涂制备钽涂层,并成功得到高硬度且低孔隙率的钽涂层㊂2005年,Li 等[27]采用氮气作为工作气体,通过冷喷涂成功制备了致密的锌涂层,并对涂层进行了表征,发现在其结合界面形成了纳米晶粒,而472㊀第4期王婉青等:冷喷涂技术发展历史㊁趋势与挑战颗粒内部的晶粒尺寸较原始粉末并没有发生太大变化㊂2012年,Suo等[28]首次成功制备镁涂层,通过数值模拟得出颗粒的临界沉积速度在653~677m/s之间,并讨论了沉积过程中镁颗粒的变形行为和结合机制㊂基体材料除了最常见的金属材料,研究人员将冷喷涂技术扩展延伸到了非金属材料领域㊂2006年,剑桥大学Sturgeon团队[29]首次成功在碳纤维增强聚合物上通过冷喷涂沉积铝涂层,开启了基于冷喷涂技术的高分子材料金属化的序幕㊂2009年,日本丰桥大学的Yamada团队[30]采用纯锐钛相TiO2纳米晶粒团聚粉末(粒径约20μm)为喷涂原料,沉积了厚度为350μm且均匀致密的涂层,实现了冷喷陶瓷涂层的突破性进展㊂2009年,Hussain等[31]成功将铜喷涂到了陶瓷基体上,形成均匀致密的涂层,并观察到陶瓷基板表面的高粗糙度能够促进涂层与基板之间的粘结,实现了陶瓷金属化㊂在设备研发方面,各个研发团队也开始尝试着手研发一系列冷喷涂设备,自2000年开始,德国冷气技术(Cold Gas Technology,CGT)公司㊁日本Plasma Giken公司以及美国VRC Metal Systems等纷纷投入到冷喷涂设备及系统的研发中,例如德国CGT于2001年在国际热喷涂大会上推出商用Kinetiks 3000型冷喷涂系统,其工作气体的温度和压力分别是550ħ和3MPa;2009年该公司开发了Kinetiks 8000系统,整体系统的加热功率可达到85kW,工作气体(如N2)的最高温度可达1000ħ㊂但是由于设备的工作温度与压力仍然无法满足特殊材料的喷涂需求,辅助冷喷涂技术应运而生,以提高喷涂质量㊂英国剑桥大学的Bray等[32]在2009年率先提出将冷喷涂与激光技术相结合的激光原位辅助冷喷涂复合技术㊂随后2015年,西安交通大学李长久和雒晓涛等[33]首先提出将原位喷丸技术应用到冷喷涂中以提高涂层质量,由此提出了微锻造辅助冷喷涂技术,大大降低了冷喷涂技术对设备的依赖程度㊂第2个阶段是冷喷涂技术工业化应用阶段(2015年至今),由于冷喷涂技术越来越完善,国内外市场对于冷喷涂设备的需求量增大,相关企业开始批量生产成熟的高性能冷喷涂设备并投入市场㊂德国Impact Innovations㊁日本Plasma Giken公司以及美国的VRC Metal Systems公司相继推出成熟的冷喷涂设备,工作性能不断得到提升㊂例如德国Impact Innovations公司在2021年5月推出了EvoCS II系列的冷喷涂设备,其设备性能得到了极大程度的提升,最高工作温度和工作压力分别达到了1200ħ和7.5MPa,接近高温合金的使用极限,可以满足大部分材料的工作要求㊂日本Plasma Giken公司研发的PCS-1000冷喷涂系统,其最高温度与压力分别可达到1100ħ和7.0MPa,送粉速度为300~500g/min[34]㊂随着设备的完善,冷喷涂技术在金属增材制造和航空航天等关键零部件的损伤修复中实现了具体的工业化应用,例如美国VRC Metal Systems公司将研发的冷喷涂设备用于美国军事领域相关设备的零件修复工作中[35],如图2a所示;湖北超卓航科公司利用冷喷涂技术成功对飞机结构件,例如飞机加油盖的裂纹部位进行了补强修复,将其剩余寿命提高至30倍以上,完成了国内该领域技术突破,如图2b所示[36];广州尤特新材料等公司通过冷喷涂技术制备旋转靶材,如图2c和2d所示[37,38]㊂图2㊀冷喷涂技术用于修复T7000前车架(a)[35]和飞机加油盖(b)[36];冷喷涂技术用于制备旋转银靶材(c)[37]和旋转硅铝靶材(d)[38]Fig.2㊀Repaired T7000front frame(a)[35]and aircraft refueling cap(b)[36]by cold spray technology;rotating silver target(c)[37]and rotating silicon aluminum target(d)[38]prepared by coldspray technology3㊀冷喷涂技术的发展趋势2000年至今,国内外多家企业专注于冷喷涂技术的发展,其工艺水平得到了很大程度的提升㊂据华经产业研究院整理预计[39],未来几年冷喷涂市场规模及增长速度会不断升高,预计2026年,全球冷喷涂行业市场规模将达到12.13亿美元,如图3所示㊂随着冷喷涂技术在工业领域的迅猛发展,该技术呈现高性能化㊁低成本化和增材制造等发展趋势㊂3.1㊀高性能化趋势随着冷喷涂技术在工业细分领域的应用,工业界对冷喷涂涂层性能和质量的要求越来越高,引领冷喷涂技术向高性能方向发展㊂涂层的高性能主要取决和依赖于设备高性能和粉末高性能㊂572中国材料进展第43卷图3㊀全球冷喷涂行业市场规模及增速曲线预测[39]Fig.3㊀Predicted market size and growth curve of global cold spray in-dustry [39]3.1.1㊀设备性能提高德国Impact Innovations 公司在2021年5月在市场上主推的新一代冷喷涂系统是EvoCS II 系列,如图4所示[40],该喷涂系统工作时的最高温度和压力可分别达到1200ħ和7.5MPa,送粉速率为1.5L /h㊂图4㊀Impact Innovations 公司2021年推出的EvoCS II 冷喷涂设备[40]Fig.4㊀EvoCS II cold spray equipment from Impact Innovations compa-ny at 2021[40]日本Plasma Giken 公司的PCS-1000V2冷喷涂系统(图5)最高工作温度和压力可以达到1200ħ和7.5MPa,送粉速率接近300~500g /min [41]㊂图5㊀Plasma Giken 公司的PCS-1000V2冷喷涂设备[41]Fig.5㊀Cold spray equipment PCS-1000V2of Plasma Giken company [41]与此同时,国内企业例如陕西德维科技股份有限公司㊁宁波普罗特新材料有限公司㊁厦门佰事兴新材料科技有限公司等也已经有了相对完善的高性能冷喷涂系统㊂3.1.2㊀粉末性能提高粉末作为冷喷涂的关键原材料之一,其纯度㊁粒度以及成分等都会对涂层的机械性能造成影响㊂Deforce 等[42]在AZ41A-T5合金基材上采用冷喷涂技术制备纯铝涂层,比较了商用铝粉末(99.5%)和高纯铝粉末(99.95%)对AZ41A-T5合金耐腐蚀性能的影响㊂结果发现商用纯铝涂层的腐蚀电流密度大约为2.35mA /cm 2,而高纯铝涂层的腐蚀电流密度仅为0.05mA /cm 2㊂同时,研究人员发现,利用混合粉末制备涂层同样可以获得极为优良的机械性能㊂Sova 等[43]发现在软金属(Al 和Cu)粉末中添加细硬质粉末可以显著降低喷涂 临界 温度,增大沉积效率㊂Liberati 等[44]将金属粉末(Al㊁Cu 和Zn)添加到锡粉末中混合后进行冷喷涂,结果表明,由于夯实机制,在锡粉末中添加任何的二次组分均可提高其沉积效率㊂除了粉末成分,粉末的粒径分布也会影响其涂层性能㊂2013年,Wong 等[45]研究了纯钛粉末形态和粒径分布对冷喷涂涂层性能的影响,发现平均粒径为29μm 的球形钛粉末制备的涂层具有最低的孔隙率和最佳的冷喷涂性㊂3.2㊀低成本化趋势低成本是企业在工业生产中获得市场竞争力的关键因素,随着近年来冷喷涂技术的不断成熟,冷喷涂技术的成本出现了大幅度的下降,冷喷涂铜涂层的价格从原来的100~200CNY /mm 2降到现在的10~20CNY /mm 2㊂冷喷涂技术实现低成本得益于以下几个方面㊂3.2.1㊀国产设备日益成熟冷喷涂是热喷涂领域的热门研究方向之一,在全球工业化的大背景下,关于冷喷涂的设备研发也越发地成熟㊂目前,已经广泛投入使用的冷喷涂设备来自德国Im-pact Innovations㊁日本Plasma Giken 以及美国VRC MetalSystems 等公司,但是由于运费及维修费等因素,进口设备往往价格昂贵,价格约为400万~500万人民币㊂因此国内市场涌现出了一批高质量的冷喷涂设备,2000年末,西安交通大学李长久教授课题组[34]最先自主研发了国内首套CS-2000型冷喷涂系统,带动了国内自主研发冷喷涂设备的风潮㊂2001年9月,中国科学院金属研究所[46]研发了一台冷气动力喷涂装置,其工作气体最高温度和压力可达到580ħ和3MPa㊂除了各高校团队以外,企业也开展了相应的研究设计㊂2005年6月,宝山钢铁股份有限公司[47]自主研发了冷气动力喷涂装置,很大程度上避免了喷涂粉末对喷嘴的堵塞情况,降低了零件修672㊀第4期王婉青等:冷喷涂技术发展历史㊁趋势与挑战复成本㊂目前,宁波普罗特㊁北京联合等公司均有相对完整的冷喷涂设备生产体系,设备和耗材成本较进口设备有较大幅度下降㊂3.2.2㊀定制化专用设备发展随着冷喷涂技术原理的不断完善和相关设备的研发,冷喷涂技术的应用场合得到了扩展,生产的产品逐渐多样化㊂在实际生产中,通常只需要对某一种特定材料进行批量化冷喷涂处理,因此,设备定制化成为了冷喷涂产业发展的趋势之一㊂多家国产冷喷涂装备公司已经推出了定制化专用设备,以满足特定材料的喷涂,同时进一步降低设备投入与运营成本㊂3.2.3㊀气体成本降低氮气㊁氦气是冷喷涂的主要工作气体,采用氦气作为喷涂气体可以显著提高沉积效率及沉积体性能㊂2015年,Yin等[48]分别用氦气㊁氩气及空气3种气体作为喷涂气体进行了铜颗粒的沉积,结果表明,氦气作为工作气体时颗粒速度最高,对颗粒表现出良好的加速性能㊂但由于我国氦气资源稀少,氦气供应主要依赖于国外进口,成本较高,约为50CNY/L㊂为保证涂层质量,冷喷涂过程中需要消耗大量的氦气,造成极大的成本消耗㊂为解决氦气费用昂贵的问题,法国ICB-PMDM-LERMPS实验室提出气体循环使用的方法,建立了氦气回收系统,用于氦气循环回收㊁净化和再利用[34],极大程度上降低了生产成本,国内科研单位如西安交通大学㊁宁波大学㊁中国兵器集团五二研究所等在这方面开展了相关的研究㊂3.2.4㊀多技术复合采用冷喷涂制备涂层时,为提高沉积效率,降低涂层内部缺陷,通常选择更高的喷涂气体温度㊁压力以及加速效果更好的氦气㊂然而,上述方法会极大提高设备和气体成本㊂为保证涂层质量同时降低制备成本,研究人员考虑通过将冷喷涂与其他技术结合起来共同制备涂层,通过技术的改进来降低冷喷涂工艺对设备的严格要求㊂2015年,雒晓涛等[33]首次将原位喷丸强化引入冷喷涂,以期降低涂层的孔隙率㊂2019年,雒晓涛和李长久等[49]首次提出基于原位微锻造冷喷涂制备高致密度金属沉积体的技术,其工作原理如图6所示㊂他们利用原位微锻造冷喷涂制备铝涂层时发现,当混合粉末中的喷丸颗粒的体积分数高于40%时,铝涂层的孔隙率低于0.35%,并且在AZ31B镁合金基材表面的铝涂层可使镁合金的腐蚀速率降低接近3个数量级,表现出良好的耐腐蚀性能㊂与传统的冷喷涂技术相比,通过该技术可以在较低的温度和压力条件下,在镁合金表面获得完全致密的铝腐蚀防护涂层,可以在很大程度上降低冷喷涂技术的成本㊂考虑到激光的加热软化处理能够提高基体和颗粒变形程度,英国剑桥大学的Bray等[32]首先提出将冷喷涂与激光相结合的激光原位辅助冷喷涂复合技术,随后国内浙江工业大学姚建华等[50]也开始了该项技术的研究工作,其原理如图7[32]所示,是将激光束同步引入冷喷涂加工过程,利用激光对喷涂颗粒㊁基材或两者同时加热并使之软化,在保持冷喷涂固态沉积特性的同时提高涂层性能㊂图6㊀原位微锻造辅助冷喷涂技术的原理示意图[49] Fig.6㊀Principle schematic diagram of in-situ micro-forging auxiliary cold spray technology[49]图7㊀激光原位辅助冷喷涂复合技术的原理示意图[32] Fig.7㊀Principle schematic diagram of laser in-situ assisted cold spray composite technology[32]3.3㊀增材制造应用趋势近年来,随着人工智能技术的发展,冷喷涂技术逐渐演变成为一种新的增材制造技术[51]㊂相较于传统的基于熔融过程的增材制造工艺,冷喷涂增材制造工艺具有热效应较低㊁制造效率高㊁产品尺寸限制小等优点,然而,冷喷涂增材制造技术制造精度较低,从而限制了冷772中国材料进展第43卷喷涂增材制造的广泛应用㊂迄今为止,一些公司和研究机构已在冷喷涂增材制造技术上进行了大量投资,并取得了各种突破性的成果㊂法国ICB-PMDM-LERMPS 实验室运用冷喷涂增材制造技术3D 打印了手掌模型,如图8所示[52]㊂近年来针对冷喷增材制造技术,主要围绕喷涂路径离线优化和喷嘴设计优化两方面进行了深入的探讨研究㊂图8㊀冷喷涂增材制造技术打印的手掌模型[52]Fig.8㊀Palm model printed by cold spray additive manufacturing[52]3.3.1㊀喷涂路径离线优化在冷喷涂过程中,为获得更精确的涂层厚度和涂层形状,需要精准控制喷枪路径,规划和创建合理的喷涂路径成为了保证涂层质量关键的一步㊂2012年,Deng 等[53]在机器人编程软件Robot Studio 上采用切片方式处理喷涂表面,并且开发了基于该软件的热喷涂专用程序包,为后续研究人员进行相关的研究提供了技术支持㊂采用RobotStudio 软件来创建针对制造对象的喷涂路径,可以真实反映实际喷涂过程,随时修改喷涂程序,还能观察各元素之间是否发生了干涉,进而有效防止实际喷涂中发生设备相互间的碰撞㊂进一步地,Deng 等[54]提出了一种基于冷喷涂增材制造中网格几何重构策略的通用MATLAB 数值沉积建模方法,以更准确地模拟沉积过程,通过仿真和实验验证了所提方法的有效性,实验结果表明,该方法能够准确模拟冷喷涂增材制造过程中的沉积物增长㊂3.3.2㊀喷嘴设计优化喷嘴是冷喷涂增材制造精度提高的关键之一,Sova 等[55-57]采用出口直径为1mm 的微型喷嘴来对铜㊁铝颗粒进行冷喷涂增材制造,以此来减少粉末的发散,得到了小于1mm 的喷涂斑点,提高了冷喷涂增材制造在小尺寸成形方面的能力㊂2012年,Suo 等[58]通过研究喷嘴尺寸对冷喷涂过程中颗粒分布情况的影响得出,颗粒分布随着喷嘴的出口直径的增加而变得更加扁平化㊁均匀化㊂2022年,Alonso 等[59]研究了不同尺寸参数的喷嘴对于不同种类的冷喷涂粉末颗粒速度以及沉积表面形貌的影响,并整理了不同粒径的铝和不锈钢粉末颗粒所对应的最佳喷嘴尺寸参数㊂通过对喷嘴设计的优化,能够一定程度上提高涂层表面质量㊂4㊀冷喷涂技术的挑战与机遇冷喷涂作为一种先进的表面处理与增材制造技术,经过30多年的研究,已经具备了产品化应用条件[60],但由于工业化要求的不断提高,该技术仍存在一些问题,主要表现在以下几个方面㊂4.1㊀装备性能接近极限随着冷喷涂技术工业应用的不断探索,对装备性能的要求也在不断提升㊂德国Impact Innovations 推出的EvoCS II 系列喷涂设备以及日本Plasma Giken 公司推出的PCS-1000V2冷喷涂系统最高工作温度和压力可达到1200ħ和7.5MPa,接近高温合金的使用极限㊂在现有基础上再要大幅度地提升气体的加热温度难度提高,需要在设计和材料等方面有所突破㊂4.2㊀打印精度有待提升由于工业生产中广泛应用的冷喷涂喷嘴出口直径范围为4~10mm,单道涂层宽度较大,因此一般的拉瓦尔喷嘴难以满足小尺寸工件的加工要求,受限于毫米级的分辨率㊂选区激光熔化(selective laser melting,SLM)技术以及超声波增材制造技术(ultrasonic additive manufactur-ing,UAM)可以达到微米级的分辨率[61]㊂同时在冷喷涂过程中,很难保证涂层形状精度,位于中心的颗粒速度高于外侧的颗粒速度,导致粉末颗粒数量沿喷嘴横截面呈类高斯分布,导致沉积在中心区域的颗粒数量大于边缘的[62,63]㊂Wu 等[64]指出,当喷枪移动速度较低或喷涂次数较多时,沉积体中心区域与边缘区域的厚度增长速度不一致,造成最终沉积体厚度不均匀,形成中间高两边低的 三角形 轮廓,如图9所示㊂4.3㊀专业人才缺口较大冷喷涂技术涵盖了多个学科的专业知识,若研究人员没有经过专业培养,对相关的知识与操作理解起来比较困难;其次,冷喷涂加工过程涉及的控制因素较多,比如喷涂距离㊁粉末粒度㊁喷嘴尺寸㊁气体参数等,它们对不同材料的涂层质量具有不同的影响,需要大量研究人员开展相关研究,以明确各种因素的影响及确定最佳喷涂参数,以此来指导解决工程实际问题㊂5㊀结㊀语自20世纪80年代中期冷喷涂技术被提出至今,对其工艺原理及结合机制等方面开展了大量的研究与讨论,为后续冷喷涂系统设备的开发研究提供了重要的理论依872㊀第4期王婉青等:冷喷涂技术发展历史㊁趋势与挑战图9㊀喷嘴处颗粒速度不同导致的沉积层厚度不一致[64]Fig.9㊀Inhomogeneous sprayed layer thickness caused by particle velocity difference of spray nozzle [64]据㊂目前冷喷涂技术已开始投入工业化生产,且其应用领域㊁设备生产规模逐渐扩大㊂但该技术面临着许多挑战,例如冷喷涂设备的工作性能提升面临极大的限制,最高工作温度及压力难以得到大幅提高㊂目前国内的冷喷涂设备在喷涂温度㊁喷涂压力和稳定性等方面,与国外相比存在一定的差距㊂为提高涂层质量,需要结合激光等其他辅助技术㊂与此同时,冷喷涂增材制造技术与其他的金属增材制造技术相比,尺寸精度较低,仍需大量研究提供理论支持㊂由于专业人才数量有限,冷喷涂技术发展受到了一定限制,亟需大量职业教育进行人才培养㊂参考文献㊀References[1]㊀ALKHIMOV A P,KOSAREV V F,PAPYRIN A N.Soviet PhysicsDoklady[J],1990,35:1047-1049.[2]㊀ALKHIMOV A P,PAPYRIN A N,KOSAREV V F,et al .Gas-Dynamic Spray Method for Applying A Coating:US5302414B1[P].1997-02-25.[3]㊀ASSADI H,KREYE H,GÄRTNER F,et al .Acta Materialia[J],2016,116:382-407.[4]㊀YIN S,CAVALIERE P,ALDWELL B,et al .Additive Manufacturing[J],2018,21:628-650.[5]㊀黄文,薛召露,刘侠,等.稀有金属[J],2021,45(7):836-847.HUANG W,XUE Z L,LIU X,et al .Chinese Journal of Rare Metals [J],2021,45(7):836-847.[6]㊀富伟,巫顺根,陈清宇,等.稀有金属[J],2021,45(6):673-679.FU W,WU S G,CHEN Q Y,et al .Chinese Journal of Rare Metals [J],2021,45(6):673-679.[7]㊀熊天英,王吉强.金属学报[J],2023,59(4):537-546.XIONG T Y,WANG J Q.Acta Metallurgica Sinica[J],2023,59(4):537-546.[8]㊀MCCUNE R C,PAPYRIN A N,HALL J N,et al .An Exploration ofthe Cold Gas-Dynamic Spray Method for Several Materials Systems [C]//Proceedings of 1995National Thermal Spray Conference.Hous-ton:ASM International,1995.[9]㊀宋凯强,丛大龙,何庆兵,等.装备环境工程[J],2019,16(8):65-69.SONG K Q,CONG D L,HE Q B,et al .Equipment EnvironmentalEngineering[J],2019,16(8):65-69.[10]李旭,王强,牛文娟,等.稀有金属[J],2020,44(11):1153-1162.LI X,WANG Q,NIU W J,et al .Chinese Journal of Rare Metals[J],2020,44(11):1153-1162.[11]陈枭,白小波,纪岗昌,等.稀有金属[J],2018,42(12):1332-1338.CHEN X,BAI X B,JI G C,et al .Chinese Journal of Rare Metals[J],2018,42(12):1332-1338.[12]GILMORE D L,DYKHUIZEN R C,NEISER R A,et al .Journal ofThermal Spray Technology[J],1999,8(4):576-582.[13]STOLTENHOFF T,KREYE H,RICHTER H J.Journal of ThermalSpray Technology[J],2002,11(4):542-550.[14]ASSADI H,GÄRTNER F,STOLTENHOFF T,et al .Acta Materialia[J],2003,51(15):4379-4394.[15]SCHMIDT T,GÄRTNER F,ASSADI H,et al .Acta Materialia[J],2006,54(3):729-742.[16]RICHTER P,HÖLL H.Proceedings of ITSC 2006[C].Seattle:ASMThermal Spray Society,2006:1447-1450.[17]KREYE H,SCHMIDT T,GÄRTNER F,et al .Proceedings of ITSC2006[C].Seattle:ASM Thermal Spray Society,2006:83-88.[18]LI W Y,LIAO H L,LI C J,et al .Applied Surface Science[J],2007,253(11):5084-5091.[19]FUKUMOTO M,WADA H,TANABE K,et al .Journal of ThermalSpray Technology[J],2007,16(5-6):643-650.[20]OGAWA K,ITO K,ICHIMURA K,et al .Journal of Thermal SprayTechnology[J],2008,17(5-6):728-735.[21]TOKAREV A O.Metal Science and Heat Treatment [J],1996,38(3):136-139.[22]MCCUNE R C,DONLON W T,CARTWRIGHT E L,et al .Proceed-ings of ITSC 1996[C].Ohio:ASM Thermal Spray Society,1996:397-403.[23]DYKHUIZEN R C,SMITH M F,GILMORE D L,et al .Journal ofThermal Spray Technology[J],1999,8(4):559-564.[24]KARTHIKEYAN J,KAY C M,LINDEMAN J,et al .Proceedings ofITSC 2000[C].Quebec,Canada:ASM Thermal Spray Society,2000:255-262.[25]MCCUNE R C,COOPER R P,POPOOLA O O.Proceedings of ITSC972。
冷喷涂技术的现状和未来应用

冷喷涂技术的现状和未来应用作者:加拿大CENTERLINE WINDSOR 有限公司JULIO VILLAFUERTE冷喷涂是使用高速气体喷嘴将粉末微粒加速喷向基板的一种固态喷涂工艺名称,在这种工艺中,金属微粒产生塑性变形并在冲击之下固化。
术语“冷喷涂”是指所需加工温度相对较低的工艺,一般比喷涂材料的熔点低很多。
尽管将金属材料冷喷涂到基板上的理念可以追溯到20世纪早期,但是,这种技术的适用性直到20世纪80年代才在位于Novosibirisk 的俄罗斯科学院理论与应用机械研究所展示出来。
由于到达基板及沉淀材料上的金属粉末粘接力使其形成固态,因此,冷喷涂沉淀的特征十分独特,所以它非常适合在多种类型的基板材料上沉淀广泛的传统和高级材料,特别是对于工艺温度敏感的非传统应用。
冷喷涂的一些特征包括其形成的密集沉淀物氧含量极低,没有残余拉伸应力,微粒增大,有再结晶区域以及相变化。
一些材料甚至会出现纳米级的晶粒细化。
由于具有这些属性,因此冷喷涂特别适合于沉淀各种高级和对温度敏感材料。
今天,冷喷涂越来越多地应用于各种工业领域,包括航天、能源和军事工业(图1和图2)。
冷喷涂如何工作?20世纪80年代,在冷喷涂技术的应用发展中,将喷涂材料喷射到喷嘴之内的两种图1:采用低压冷喷涂现场修理腐蚀后的表面。
方法获得了专利,今天我们称之为高压(利用高压供给气体将粉末喷射到喷嘴喉部之前)¹ 以及低压(利用低压供给气体将粉末喷入喷嘴分流区)。
²在高压冷喷涂中(图3),将高压氦或氮(高达1,000 psi )预热(高达1,000℃),然后强制通过DeLaval 缩扩喷嘴。
在喷嘴上面,气体膨胀将热焓转换为动能,将气流加速到超声波范围(1,000米/秒),同时降低其温度。
在喷嘴喉部之前,粉末给料被轴向导入气流。
加速后的固态微粒以足够的动能冲击基板,以产生机械或冶金粘接效果。
在低压冷喷涂中(图4),压力相对较低的空气或氮气 (80-140 psi) 也被预热(高达550℃),然后强制通过DeLaval 喷嘴。
冷喷涂技术调研
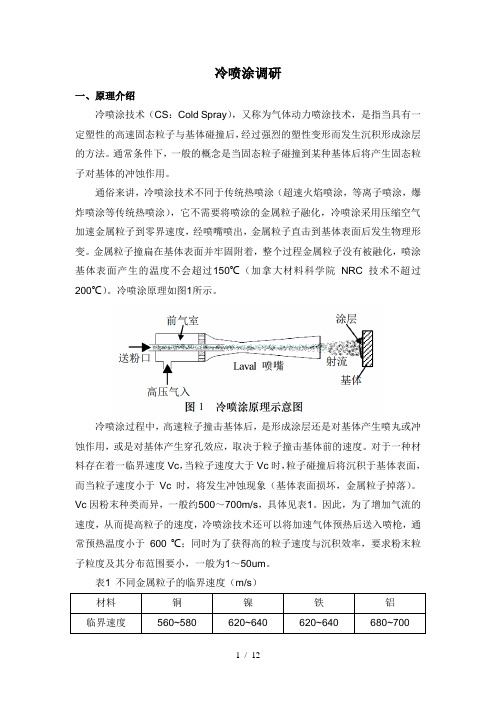
冷喷涂调研一、原理介绍冷喷涂技术(CS:Cold Spray),又称为气体动力喷涂技术,是指当具有一定塑性的高速固态粒子与基体碰撞后,经过强烈的塑性变形而发生沉积形成涂层的方法。
通常条件下,一般的概念是当固态粒子碰撞到某种基体后将产生固态粒子对基体的冲蚀作用。
通俗来讲,冷喷涂技术不同于传统热喷涂(超速火焰喷涂,等离子喷涂,爆炸喷涂等传统热喷涂),它不需要将喷涂的金属粒子融化,冷喷涂采用压缩空气加速金属粒子到零界速度,经喷嘴喷出,金属粒子直击到基体表面后发生物理形变。
金属粒子撞扁在基体表面并牢固附着,整个过程金属粒子没有被融化,喷涂基体表面产生的温度不会超过150℃(加拿大材料科学院NRC技术不超过200℃)。
冷喷涂原理如图1所示。
冷喷涂过程中,高速粒子撞击基体后,是形成涂层还是对基体产生喷丸或冲蚀作用,或是对基体产生穿孔效应,取决于粒子撞击基体前的速度。
对于一种材料存在着一临界速度Vc,当粒子速度大于Vc时,粒子碰撞后将沉积于基体表面,而当粒子速度小于Vc时,将发生冲蚀现象(基体表面损坏,金属粒子掉落)。
Vc因粉末种类而异,一般约500~700m/s,具体见表1。
因此,为了增加气流的速度,从而提高粒子的速度,冷喷涂技术还可以将加速气体预热后送入喷枪,通常预热温度小于600 ℃;同时为了获得高的粒子速度与沉积效率,要求粉末粒子粒度及其分布范围要小,一般为1~50um。
表1 不同金属粒子的临界速度(m/s)材料铜镍铁铝临界速度560~580 620~640 620~640 680~700冷喷涂技术根据压缩空气的压力不同,分为高压冷喷涂和低压冷喷涂,其中高压冷喷涂使用的压缩空气为15个大气压(psi)以上,低压冷喷涂使用的压缩空气为10个大气压(psi)以下。
对比传统热喷涂技术,高压以及低压冷喷涂的技术有以下共同优势:①可以用于喷涂多类别的、具有一定塑性的材料,获得导电、导热、防腐、耐磨等涂层等,比如纯金属锌、铝、铜、铁、镍、钛等,不锈钢、青铜等合金,也可以制备NICR基高温合金等。
2014年1105冷喷涂技术调研

冷喷涂调研一、原理介绍冷喷涂技术(CS:Cold Spray),又称为气体动力喷涂技术,是指当具有一定塑性的高速固态粒子与基体碰撞后,经过强烈的塑性变形而发生沉积形成涂层的方法。
通常条件下,一般的概念是当固态粒子碰撞到某种基体后将产生固态粒子对基体的冲蚀作用。
通俗来讲,冷喷涂技术不同于传统热喷涂(超速火焰喷涂,等离子喷涂,爆炸喷涂等传统热喷涂),它不需要将喷涂的金属粒子融化,冷喷涂采用压缩空气加速金属粒子到零界速度,经喷嘴喷出,金属粒子直击到基体表面后发生物理形变。
金属粒子撞扁在基体表面并牢固附着,整个过程金属粒子没有被融化,喷涂基体表面产生的温度不会超过150℃(加拿大材料科学院NRC技术不超过200℃)。
冷喷涂原理如图1所示。
冷喷涂过程中,高速粒子撞击基体后,是形成涂层还是对基体产生喷丸或冲蚀作用,或是对基体产生穿孔效应,取决于粒子撞击基体前的速度。
对于一种材料存在着一临界速度Vc,当粒子速度大于Vc时,粒子碰撞后将沉积于基体表面,而当粒子速度小于Vc时,将发生冲蚀现象(基体表面损坏,金属粒子掉落)。
Vc因粉末种类而异,一般约500~700m/s,具体见表1。
因此,为了增加气流的速度,从而提高粒子的速度,冷喷涂技术还可以将加速气体预热后送入喷枪,通常预热温度小于600 ℃;同时为了获得高的粒子速度与沉积效率,要求粉末粒子粒度及其分布范围要小,一般为1~50um。
表1 不同金属粒子的临界速度(m/s)材料铜镍铁铝临界速度560~580 620~640 620~640 680~700 冷喷涂技术根据压缩空气的压力不同,分为高压冷喷涂和低压冷喷涂,其中高压冷喷涂使用的压缩空气为15个大气压(psi)以上,低压冷喷涂使用的压缩空气为10个大气压(psi)以下。
对比传统热喷涂技术,高压以及低压冷喷涂的技术有以下共同优势:①可以用于喷涂多类别的、具有一定塑性的材料,获得导电、导热、防腐、耐磨等涂层等,比如纯金属锌、铝、铜、铁、镍、钛等,不锈钢、青铜等合金,也可以制备NICR基高温合金等。
冷喷涂(金属气体动力喷涂GDS)技术冷方法的产生和它的现状

冷喷涂(金属涂层气体动力喷涂)技术方法的产生和它的现状卡史林阿·伊·.——奥柏尼斯克粉末喷涂中心执行经理史柯得金阿·弗·——奥柏尼斯克粉末喷涂中心总工艺师(本文写于2006年)金属涂层的气体动力喷涂方法是大约在二十年前,由俄罗斯学者第一次提出的,并得到研究人员和专家们的广泛关注。
在2004年以前,气体动力喷涂是一个够新的技术,并不被重视﹝1﹞。
近十几年以来,本方法在各领域发展得如此之快﹝2﹞﹝3﹞,是与它的基本特性有直接的关系。
这个特性就是能采用.未熔融金属颗粒,在被加工表面上制造金属涂层。
气体动力喷涂技术与众所周知的热气喷涂方法不同,涂层气孔率很低,基体材料和涂层的热负荷很小,材料氧化少,消除了涂层中结晶化不均匀的现象。
(一)气体动力喷涂方法的产生原苏联科学院西伯利亚分院理论和应用力学所﹝4﹞的学者阿·巴·阿尔赫莫夫、弗·费·柯沙列夫和阿·尼·马比林,将铝以超音速双相流绕过阻碍物时,发现它沉积在阻碍物的顶部。
这便是气体动力喷涂金属涂层方法的历史起源。
他们研究发现,当粒子流的速度超过一定值,即所谓的临界速度时,在阻碍物上沉积一层硬厚的金属粉末涂层。
作者们称它为“冷气动力喷涂”﹝5﹞﹝6﹞。
方法的实质,原则上是够简单的。
被驱动的未熔融金属颗粒的速度达到500-1000米/秒时,与阻碍物发生碰撞,会产生强烈的变形,并在表面固化形成厚涂层。
利用这种方法,作者们获得了许多金属(Al、Cu、Zn、Ni、Co、V、Fe、Ti等)、它们的合金和混合物的涂层。
最初的一些研究发现:随着粒子沉积效益的增加,当速度超过临界速度时,观察到颗粒的变形程度减弱,涂层的硬度降低和它的气孔率增加﹝5﹞。
此外,为了使粒子达到临界速度,大多数情况下,要求采用单一的原子气体,例如氦气。
这阻碍了该方法实际应用的扩展。
因此,必须扩大研究围,不仅要研究涂层的特性,而且还要研究其工作最佳方式和寻找实现本技术的具体办法。
海洋防腐冷喷涂技术的机理、特点及国内外发展现状综述

海洋防腐冷喷涂技术的机理、特点及国内外发展现状综述1 冷喷涂技术的起源通常情况下,一般的概念是当固态粒子碰撞到某种基体后将产生固态粒子对基体的冲蚀作用,然而,上世纪80年代中期前苏联科学院西伯利亚分部理论和应用机械研究所的科学家,在用示踪粒子进行超音速风洞试验时,发现当用作测速的示踪金属颗粒在其速度超过某一临界值时,粒子发生不断在基体靶材表面沉积的现象。
思路开阔的科学家萌发了由固态粒子沉积涂层的想法,由此在1990提出了冷喷涂的概念。
经过试验发现,要使高速固态粒子在基体表面沉积,粒子的速度需要超过某一临界值,该临界值与金属材料的种类有关,一般认为400m/s~500m/s。
与热喷涂技术相比,冷喷涂中的粒子属于低温而高速,低温指粒子的温度一般远低于材料的熔点,即以完全固态碰撞基体表面,而传统的热喷涂需要粒子完全熔化,或在半熔化的液固两相状态下沉积涂层;高速则指粒子速度一般达到500m/s~1000m/s的状态。
因此,冷喷涂实际上可以认为是粒子温度与速度向低温与高速进一步拓展而发展起来的新型热喷涂方法。
2 冷喷涂涂层的沉积机理冷喷涂技术的根本原理是:由一高速“冷”喷涂粒子流在一“冷”基体表面喷涂上涂层。
喷涂过程中撞击基体是形成涂层还是对基体喷丸或产生冲蚀作用,取决于粒子的速度。
对于一种材料,存在一定的临界速度,当大于该速度,形成涂层;而小于该速度,将发生冲蚀现象。
此外,这个关键速度的大小由冷喷涂粒子本身性质和基体共同决定。
冷喷涂过程一般会分为几个阶段,按照Van Steenkiste 等的研究发现,铝在金属表面的冷喷涂形成过程分为三个阶段,第一阶段是基体凹陷和第一层颗粒积聚;第二阶段是颗粒形变和重排;最后的第三阶段是冶金焊接形成和空隙的减少。
对于冷喷涂颗粒在基体表面的沉积机理目前为止还缺乏深入的了解。
一种普遍的冷喷涂沉积理论认为,在冲击过程中,固体颗粒发生弹性形变,破坏了目标靶体原来的表面,并在局部高压下与表面紧密接触,从而发生粘结。
冷喷涂技术的研究现状及在航空工业领域内的应用
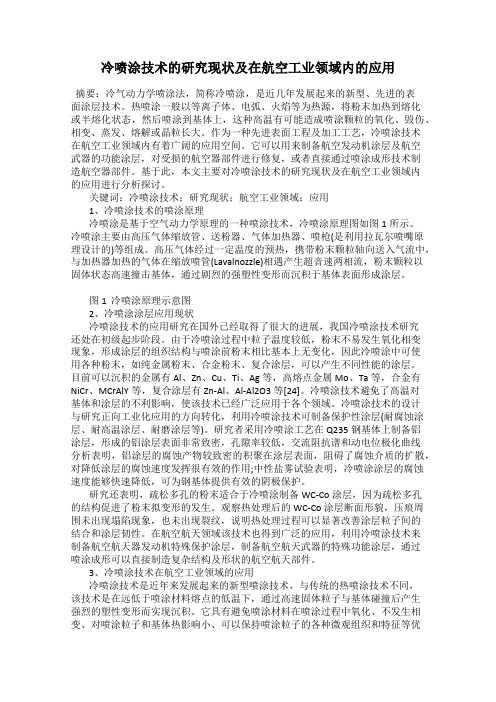
冷喷涂技术的研究现状及在航空工业领域内的应用摘要:冷气动力学喷涂法,简称冷喷涂,是近几年发展起来的新型、先进的表面涂层技术。
热喷涂一般以等离子体、电弧、火焰等为热源,将粉末加热到熔化或半熔化状态,然后喷涂到基体上,这种高温有可能造成喷涂颗粒的氧化、毁伤、相变、蒸发、熔解或晶粒长大。
作为一种先进表面工程及加工工艺,冷喷涂技术在航空工业领域内有着广阔的应用空间。
它可以用来制备航空发动机涂层及航空武器的功能涂层,对受损的航空器部件进行修复,或者直接通过喷涂成形技术制造航空器部件。
基于此,本文主要对冷喷涂技术的研究现状及在航空工业领域内的应用进行分析探讨。
关键词:冷喷涂技术;研究现状;航空工业领域;应用1、冷喷涂技术的喷涂原理冷喷涂是基于空气动力学原理的一种喷涂技术,冷喷涂原理图如图1所示。
冷喷涂主要由高压气体缩放管、送粉器、气体加热器、喷枪(是利用拉瓦尔喷嘴原理设计的)等组成。
高压气体经过一定温度的预热,携带粉末颗粒轴向送入气流中,与加热器加热的气体在缩放喷管(Lavalnozzle)相遇产生超音速两相流,粉末颗粒以固体状态高速撞击基体,通过剧烈的强塑性变形而沉积于基体表面形成涂层。
图1 冷喷涂原理示意图2、冷喷涂涂层应用现状冷喷涂技术的应用研究在国外已经取得了很大的进展,我国冷喷涂技术研究还处在初级起步阶段。
由于冷喷涂过程中粒子温度较低,粉末不易发生氧化相变现象,形成涂层的组织结构与喷涂前粉末相比基本上无变化,因此冷喷涂中可使用各种粉末,如纯金属粉末、合金粉末、复合涂层,可以产生不同性能的涂层。
目前可以沉积的金属有Al、Zn、Cu、Ti、Ag等,高熔点金属Mo、Ta等,合金有NiCr、MCrAlY等,复合涂层有Zn-Al、Al-Al2O3等[24]。
冷喷涂技术避免了高温对基体和涂层的不利影响,使该技术已经广泛应用于各个领域。
冷喷涂技术的设计与研究正向工业化应用的方向转化,利用冷喷涂技术可制备保护性涂层(耐腐蚀涂层、耐高温涂层、耐磨涂层等)。
全球及中国冷喷涂产业现状及前景分析

全球及中国冷喷涂产业现状及前景分析一、冷喷涂综述冷喷涂技术是一种以高压气流加速微小颗粒形成超音速气固双相流轰击金属或绝缘基体表面形成涂层的工艺。
冷喷涂在技术上是热喷涂的一个子集,但它的应用不需要像大多数热喷涂应用那样的燃烧过程。
冷喷涂原理是高压气体在进入控制柜后被分为两路气流,其中一路进入送粉器(powderhopper),作为送粉载气将粉末引入喷嘴;另一路通过加热器(gasheater)使气体膨胀,提高气流速度;两路气流进入喷枪后经过拉乌尔喷嘴的缩放加速后形成超音速气固双相流,固态粉末粒子与基体碰撞过程中发生塑性变形沉积于基体表面上形成涂层。
现代冷喷涂技术起源于前苏联,初步工业化于北美,技术完善于21世纪初,在降低工业生产制造成本和提高生产制造效率上发挥重要作用。
现代冷喷涂工艺发展历史现代冷喷涂工艺发展历史资料来源:公开资料,产业研究院整理相较其它增材技术,冷喷涂技术是各类增材修复技术中综合修复效果较好的技术,具备以下6大优势:1)涂层材料不会出现氧化和烧损,进而可以保持原始的材料特性。
2)较低的喷涂温度减少了涂层对基体的热影响,基体不会产生变形问题;3)容易形成结合力较高,厚度较大的涂层;4)送粉速度快,喷涂和沉积效率高;5)低温环境下,涂层粉末不会发生显著的物理化学反应,可回收利用,降低生产成本;6)涂层孔隙率低,致密度高。
常用增材修复技术特性常用增材修复技术特性资料来源:公开资料,产业研究院整理二、冷喷涂行业现状分析得益于冷喷涂技术的优势,以及其在航空与其他工业领域的应用潜力,未来冷喷涂技术市场有望持续成长。
据统计,2020年全球冷喷涂市场规模为9.87亿美元,预计到2026年全球冷喷涂市场空间将上涨至12.13亿美元,年均复合增长速度为3.5%。
2020-2026年全球冷喷涂行业市场规模及增速情况2020-2026年全球冷喷涂行业市场规模及增速情况资料来源:GrandViewMarket,GME,产业研究院整理从下游需求来看,冷喷市场空间交通占比最大。
论冷喷涂的现状和前景

论冷喷涂的现状和前景摘要:参考关于冷喷涂技术的论文,来总结冷喷涂技术现阶段国内外的发展和应用领域。
20 世纪80 年代中期前苏联科学院西伯利亚分院理论与应用力学研究所的科学家在进行风洞实验时发现,当示踪原子的速度超过某一临界速度时,示踪原子对靶材表面的作用由冲蚀变为沉积,在此基础上提出了冷喷涂的概念[ 1 ,2 ] 。
之后的数年里,美国、德国、日本等国家都成立了相关的科研团队,对冷喷涂的沉积机理和应用进行了深入的研究。
1 现阶段冷喷涂技术的研究现状:目前,关于冷喷涂沉积机制的研究很多,但尚无定论。
很多研究者根据实验结果提出了不同的机制来解释冷喷涂现象。
H. A ssadi等人[ 3 ]提出了“金属冶金结合机制”,认为冷喷涂沉积过程类似于冷/热压焊。
颗粒撞击基体时,颗粒和基体都产生很高的塑性变形,不仅使材料发生加工硬化,而且导致了在颗粒和基体界面处产生绝热升温,使得材料发生热软化。
当撞击速度超过一定值时,热软化超过加工硬化效果,导致了颗粒发生绝热剪切失稳(Adiabatic Shear Instability) ,塑性变形迅速增加, 从而使粒子与基体的接触面积迅速增大,促进了结合的形成。
另一方面,粒子速度的增加,不仅使接触面积增加,而且使局部温度增加。
当粒子速度超过一定速度后,温度的升高可能使粒子和基体部分熔化,形成局部冶金结合。
M. Grujicic等人[ 4 ]提出了“机械咬合机制”。
当粒子撞击基体时,由于粒子速度处于一定范围内,从而使基体表面发生Kel2 vin2Helmholtz失稳现象。
颗粒流在基体表面产生的塑性流变使得表面有着不同的表面速度。
不同的表面速度扰动了流体,而且产生了一个离心力,使得表面产生了一定的曲率,形成卷曲和漩涡。
这些卷曲和漩涡使颗粒与基体达到结合。
在表面失稳过程中,塑性流变惯性促进了表面失稳,但是材料黏性对塑性流变有着阻碍作用。
因此,只有颗粒速度超过临界值时,流变惯性超过黏性阻力,使表面发生失稳现象,这个临界值就是颗粒撞击的临界速度。
20131105冷喷涂技术调研

20131105冷喷涂技术调研冷喷涂调研一、原理介绍冷喷涂技术(CS:Cold Spray),又称为气体动力喷涂技术,是指当具有一定塑性的高速固态粒子与基体碰撞后,经过强烈的塑性变形而发生沉积形成涂层的方法。
通常条件下,一般的概念是当固态粒子碰撞到某种基体后将产生固态粒子对基体的冲蚀作用。
通俗来讲,冷喷涂技术不同于传统热喷涂(超速火焰喷涂,等离子喷涂,爆炸喷涂等传统热喷涂),它不需要将喷涂的金属粒子融化,冷喷涂采用压缩空气加速金属粒子到零界速度,经喷嘴喷出,金属粒子直击到基体表面后发生物理形变。
金属粒子撞扁在基体表面并牢固附着,整个过程金属粒子没有被融化,喷涂基体表面产生的温度不会超过150℃(加拿大材料科学院NRC技术不超过200℃)。
冷喷涂原理如图1所示。
冷喷涂过程中,高速粒子撞击基体后,是形成涂层还是对基体产生喷丸或冲蚀作用,或是对基体产生穿孔效应,取决于粒子撞击基体前的速度。
对于一种材料存在着一临界速度Vc,当粒子速度大于Vc时,粒子碰撞后将沉积于基体表面,而当粒子速度小于Vc时,将发生冲蚀现象(基体表面损坏,金属粒子掉落)。
Vc因粉末种类而异,一般约500~700m/s,具体见表1。
因此,为了增加气流的速度,从而提高粒子的速度,冷喷涂技术还可以将加速气体预热后送入喷枪,通常预热温度小于600 ℃;同时为了获得高的粒子速度与沉积效率,要求粉末粒子粒度及其分布范围要小,一般为1~50um。
表1 不同金属粒子的临界速度(m/s)材料铜镍铁铝临界速度560~580 620~640 620~640 680~700冷喷涂技术根据压缩空气的压力不同,分为高压冷喷涂和低压冷喷涂,其中高压冷喷涂使用的压缩空气为15个大气压(psi)以上,低压冷喷涂使用的压缩空气为10个大气压(psi)以下。
对比传统热喷涂技术,高压以及低压冷喷涂的技术有以下共同优势:①可以用于喷涂多类别的、具有一定塑性的材料,获得导电、导热、防腐、耐磨等涂层等,比如纯金属锌、铝、铜、铁、镍、钛等,不锈钢、青铜等合金,也可以制备NICR基高温合金等。
冷喷涂(金属气体动力喷涂GDS)技术冷方法的产生和它的现状
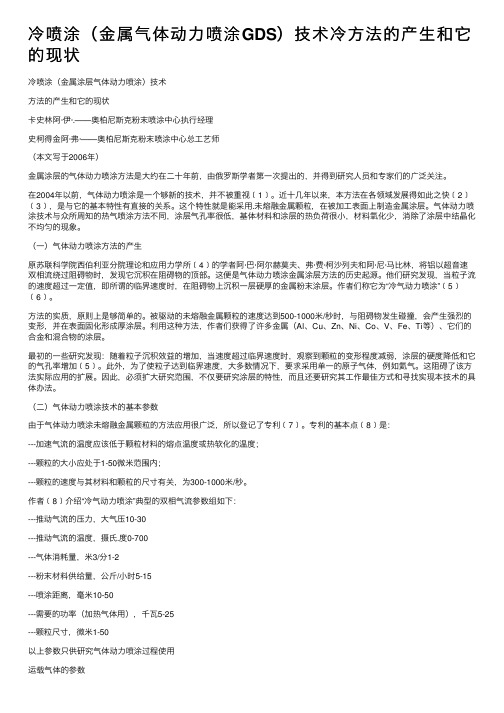
冷喷涂(⾦属⽓体动⼒喷涂GDS)技术冷⽅法的产⽣和它的现状冷喷涂(⾦属涂层⽓体动⼒喷涂)技术⽅法的产⽣和它的现状卡史林阿·伊·.——奥柏尼斯克粉末喷涂中⼼执⾏经理史柯得⾦阿·弗·——奥柏尼斯克粉末喷涂中⼼总⼯艺师(本⽂写于2006年)⾦属涂层的⽓体动⼒喷涂⽅法是⼤约在⼆⼗年前,由俄罗斯学者第⼀次提出的,并得到研究⼈员和专家们的⼴泛关注。
在2004年以前,⽓体动⼒喷涂是⼀个够新的技术,并不被重视﹝1﹞。
近⼗⼏年以来,本⽅法在各领域发展得如此之快﹝2﹞﹝3﹞,是与它的基本特性有直接的关系。
这个特性就是能采⽤.未熔融⾦属颗粒,在被加⼯表⾯上制造⾦属涂层。
⽓体动⼒喷涂技术与众所周知的热⽓喷涂⽅法不同,涂层⽓孔率很低,基体材料和涂层的热负荷很⼩,材料氧化少,消除了涂层中结晶化不均匀的现象。
(⼀)⽓体动⼒喷涂⽅法的产⽣原苏联科学院西伯利亚分院理论和应⽤⼒学所﹝4﹞的学者阿·巴·阿尔赫莫夫、弗·费·柯沙列夫和阿·尼·马⽐林,将铝以超⾳速双相流绕过阻碍物时,发现它沉积在阻碍物的顶部。
这便是⽓体动⼒喷涂⾦属涂层⽅法的历史起源。
他们研究发现,当粒⼦流的速度超过⼀定值,即所谓的临界速度时,在阻碍物上沉积⼀层硬厚的⾦属粉末涂层。
作者们称它为“冷⽓动⼒喷涂”﹝5﹞﹝6﹞。
⽅法的实质,原则上是够简单的。
被驱动的未熔融⾦属颗粒的速度达到500-1000⽶/秒时,与阻碍物发⽣碰撞,会产⽣强烈的变形,并在表⾯固化形成厚涂层。
利⽤这种⽅法,作者们获得了许多⾦属(Al、Cu、Zn、Ni、Co、V、Fe、Ti等)、它们的合⾦和混合物的涂层。
最初的⼀些研究发现:随着粒⼦沉积效益的增加,当速度超过临界速度时,观察到颗粒的变形程度减弱,涂层的硬度降低和它的⽓孔率增加﹝5﹞。
此外,为了使粒⼦达到临界速度,⼤多数情况下,要求采⽤单⼀的原⼦⽓体,例如氦⽓。
冷喷涂技术应用现状与展望

冷喷涂技术应用现状与展望张文毓【摘要】The cold spray coating is the new superficial coating technology which developed in the last few years, because the cold spray coating technology is carried on under the low temperature, compares with the alternative mean preparation coating has very many superiority.This article with forecast two aspects from the cold spray coating technology outline and the cold spray coating technology application present situation to carry on the elaboration to the cold spray coating technology, hope to have the understanding to the domestic and foreign cold spray coating technology application present situation.%冷喷涂是近几年来发展起来的新型表面涂层技术,由于冷喷涂技术是在较低的温度下进行的,与其他方法制备的涂层相比具有很多的优势。
本文从冷喷涂技术概述和冷喷涂技术应用现状与展望两方面对冷喷涂技术进行了论述,希望对国内外冷喷涂技术应用现状有所了解。
【期刊名称】《全面腐蚀控制》【年(卷),期】2015(000)002【总页数】5页(P17-21)【关键词】冷喷涂技术;应用现状;展望【作者】张文毓【作者单位】【正文语种】中文【中图分类】TG174.4冷喷涂于20世纪80年代中期,在俄罗斯科学院理论及应用力学研究所最早开发,近年来受到广泛关注,并在俄国、美国、德国等国家得到了快速发展。
- 1、下载文档前请自行甄别文档内容的完整性,平台不提供额外的编辑、内容补充、找答案等附加服务。
- 2、"仅部分预览"的文档,不可在线预览部分如存在完整性等问题,可反馈申请退款(可完整预览的文档不适用该条件!)。
- 3、如文档侵犯您的权益,请联系客服反馈,我们会尽快为您处理(人工客服工作时间:9:00-18:30)。
冷喷涂(金属涂层气体动力喷涂)技术方法的产生和它的现状卡史林阿·伊·.——奥柏尼斯克粉末喷涂中心执行经理史柯得金阿·弗·——奥柏尼斯克粉末喷涂中心总工艺师(本文写于2006年)金属涂层的气体动力喷涂方法是大约在二十年前,由俄罗斯学者第一次提出的,并得到研究人员和专家们的广泛关注。
在2004年以前,气体动力喷涂是一个够新的技术,并不被重视﹝1﹞。
近十几年以来,本方法在各领域发展得如此之快﹝2﹞﹝3﹞,是与它的基本特性有直接的关系。
这个特性就是能采用.未熔融金属颗粒,在被加工表面上制造金属涂层。
气体动力喷涂技术与众所周知的热气喷涂方法不同,涂层气孔率很低,基体材料和涂层的热负荷很小,材料氧化少,消除了涂层中结晶化不均匀的现象。
(一)气体动力喷涂方法的产生原苏联科学院西伯利亚分院理论和应用力学所﹝4﹞的学者阿·巴·阿尔赫莫夫、弗·费·柯沙列夫和阿·尼·马比林,将铝以超音速双相流绕过阻碍物时,发现它沉积在阻碍物的顶部。
这便是气体动力喷涂金属涂层方法的历史起源。
他们研究发现,当粒子流的速度超过一定值,即所谓的临界速度时,在阻碍物上沉积一层硬厚的金属粉末涂层。
作者们称它为“冷气动力喷涂”﹝5﹞﹝6﹞。
方法的实质,原则上是够简单的。
被驱动的未熔融金属颗粒的速度达到500-1000米/秒时,与阻碍物发生碰撞,会产生强烈的变形,并在表面固化形成厚涂层。
利用这种方法,作者们获得了许多金属(Al、Cu、Zn、Ni、Co、V、Fe、Ti等)、它们的合金和混合物的涂层。
最初的一些研究发现:随着粒子沉积效益的增加,当速度超过临界速度时,观察到颗粒的变形程度减弱,涂层的硬度降低和它的气孔率增加﹝5﹞。
此外,为了使粒子达到临界速度,大多数情况下,要求采用单一的原子气体,例如氦气。
这阻碍了该方法实际应用的扩展。
因此,必须扩大研究范围,不仅要研究涂层的特性,而且还要研究其工作最佳方式和寻找实现本技术的具体办法。
(二)气体动力喷涂技术的基本参数由于气体动力喷涂未熔融金属颗粒的方法应用很广泛,所以登记了专利﹝7﹞。
专利的基本点﹝8﹞是:---加速气流的温度应该低于颗粒材料的熔点温度或热软化的温度;---颗粒的大小应处于1-50微米范围内;---颗粒的速度与其材料和颗粒的尺寸有关,为300-1000米/秒。
作者﹝8﹞介绍“冷气动力喷涂”典型的双相气流参数组如下:---推动气流的压力,大气压 10-30---推动气流的温度,摄氏.度 0-700---气体消耗量,米3/分 1-2---粉末材料供给量,公斤/小时 5-15---喷涂距离,毫米 10-50---需要的功率(加热气体用),千瓦 5-25---颗粒尺寸,微米 1-50以上参数只供研究气体动力喷涂过程使用运载气体的参数为了进行气体动力喷涂,必须加速气体颗粒,形成颗粒流。
我们首先应该注意获得更高的气流速度,而它与音速a有直接的关系,为:其中,μ一气体分子量;γ—绝热常数;Cp/Cv 相对热容量;T—气体的绝对温度R—气体万能常数气体音速米/秒绝热系数克分子量克/摩尔密度公斤/米3空气 331 29氮气 334 28氖气 435 20氦气 965 4氢气 1284 2为了得到超音速气流,需用超音速喷嘴一拉瓦尔式喷嘴(包括收缩和扩展两部分)加速气体。
当气体通过临界喷嘴断面(最窄处)时,气体速度就是此部位的音速,而在喷嘴出口扩展部位,其速度可能超过音速若干倍。
从表1中可以看出,气流在氦气中比在空气中更容易达到高速。
因此,单从这点考虑,对于气体动力喷涂,最好是采用氦气或它与空气的混合物。
从公式(1)得出,加热气体能使其音速增大。
因此,喷嘴中的气流速度也增大。
这种特性常用于喷涂设备的设计工作中。
加热气体的功率可达到几十千瓦,而压缩气体的温度可达几百度。
在这种情况下,好像冷气动力喷涂是温热的,甚至好像是酷热的。
但是,沉积颗粒还是未熔融的固体状态。
质量为Mp的气体颗粒的加速度a为,其中Cd---颗粒的空气动力阻抗系数;Sp---颗粒的有效断面积;Pg---加速气体的密度;Vg---气流的速度;Vp---颗粒的速度。
必须指出:颗粒的加速度a ,除了与上述参数有明显的关系以外;而且其中Cd(气体动力阻抗系数)不仅与颗粒的形状和尺寸有关,而且与相互作用的气体参数(速度、密度、粘度和温度)也有关系。
因此,决定加速效率,不仅与气流速度有关,而且与它的其它参数,以及颗粒的特性都有关系。
图1上所载的是,运动在超音速喷嘴中的气流速度变化与温度的关系曲线。
虚线表示喷嘴临界断面和气体喷出断面的位置。
图1沿喷嘴中心轴气体速度Vg变化与温度Tg的特性曲线加速气体的制动压力是形成气流的决定因素,气体压力的增加会扩大喷嘴开口的程度,从而使气流速度增大;除了对气流产生严重影响以外,喷嘴壁上的加速气流也受阻。
这限制了喷嘴的长度,自然也就缩短了颗粒在喷嘴中加速的时间。
增大工作气体的压力和喷嘴开口的程度,可以降低这种影响。
在已研制的气体动力喷涂设备中,通常采用的气压为15-35大气压。
喷嘴超音速喷嘴出口处的断面积和长度,直接与加速气体的总消耗量和压力有关。
当气体动力喷涂的压力和消耗量为正常值时,其园断面喷嘴的出口直径,一般不会超过8-10毫米。
增大喷嘴出口直径一倍,会导致气体消耗量扩大4倍。
气体的实际消耗量大约限制在1-2米3/分。
因此,喷嘴出口断面的尺寸,不能增加太大。
要增加喷涂宽度,只能在保持喷嘴断面积不变的情况下,增加一个边的尺寸(断面为非园)。
为了减少颗粒在冲击层内的阻力,在气体动力喷涂技术研究的最初阶段,选择了长方形的断面。
这时,喷嘴出口断面一边尺寸愈小,则冲击波的输出愈小,颗粒在阻碍物前的阻力也愈小。
但是,过份地减小方形断面一边的尺寸,会减慢气体的速度,使输出喷嘴的颗粒速度也减少。
目前,大多数情况下都是采用园形断面的喷嘴。
为了获得高速的颗粒,必须增长它在加速气流中停留的时间。
这要求增长喷嘴的长度。
图2中所载的是,气体和尺寸为5微米和25微米的铜颗粒在喷嘴轴上运动时达到的(Vg、Vp5和Vp25)速度曲线。
虚线表示喷嘴的临界断面和出口处断面的位置。
显然可知,喷嘴长度的增大会使颗粒速度增高。
而喷嘴的总长度和断面积又与加速气体的参数有关。
所以,喷嘴长度的增加必定会增大气体的压力。
确定驱动喷嘴最佳的参数是气体动力喷涂技术的重要研究课题图2 气体和铜颗粒(速度为Vg、Vp5和Vp25)沿喷嘴轴线变化的曲线对沉积颗粒特性的要求从公式(2)中可知,颗粒的质量,尺寸和形状对气流的加速有很大的影响。
当然,颗粒愈轻,达到高速度就愈快。
但是,已加速的颗粒在输出喷嘴之后,受到阻碍物跟前气体层内的阻力。
因此,当轻颗粒与阻碍物相互作用时,其速度会大大地降低。
此时,愈重的颗粒,愈难用气流驱动;但当它接近阻碍物时,更容易保持自己的速度。
正因为这一点,颗粒材料的密度、尺寸和形状之间的关系是气体动力喷涂技术优化的重要参数。
气体动力喷涂技术最重要的参数之一是颗粒材料的硬度。
金属颗粒所以能在阻碍物上固定下来,是因为它在接触区内产生了塑性变形。
因此,为了固定较软颗粒所需要的速度较低;对于固定硬金属颗粒,要求大大增加它的速度。
采用预热的办法(利用硬度与温度的关系)可以降低颗粒材料的硬度。
这种预热运载气体的方法并不常用。
当在喷嘴中进行绝热扩展时,气体温度会下降很快。
所以通常预热只能补尝颗粒温度的降低。
在图3中,所载的是:当初始温度为673K(绝对温度)时,气体和直径为5 微米与25微米的铜颗粒,沿着喷嘴轴线运动的温度(Tg、Tp5和Tp25)特性曲线。
虚线表示临界断面和出口断面处的位置。
图3气体和铜颗粒沿喷嘴轴线变化的温度特性线(Tg、Tp5和Tp25)颗粒在气流中加热和冷却的速度,与颗粒材料的导热性和热容量以及它的尺寸有关系。
因此气体动力喷涂过程的优化,不仅与气流的选择有关,而且与选择适合的粉末材料也有关系。
涂层的性质气体动力喷涂方法所制备的涂层的突出特性,是保持原始粉末材料的化学成份不变。
因为喷涂过程是在比颗粒材料熔点温度低得多的温度下进行的,所以实际上不产生任何相位转变,任何化学变化和严重的材料氧化。
这种涂层特点是气孔率低。
因为在喷涂过程中,颗粒会产生强烈的变形。
当已加速的硬颗粒冲击阻碍物时,会产生严重的变形。
接触区内的局部强热会产生局部的升温,使接触表面附近硬度降低和变形加大。
此时,变形值可达到80%,涂层的粘合强度达30-80兆帕。
虽然涂层中存在内应力(因为涂层材料内有硬化),但它的热应力余留下来的很小。
这使涂层接合得很好,甚至厚度达到10mm和更厚的涂层也是如此。
由于颗粒产生强烈的冲击变形,其涂层材料晶格缺陷的密度也显着地增大。
晶格的缺陷率,涂层中颗粒强度的提高以及由于时间短和相互作用的温度所产生的颗粒之间的无渗入区的明显界线的存在,降低了涂层材料的相对伸长,其值小于1%。
实际上,用气体动力喷涂法所制的涂层,都是够脆的。
涂层材料在喷涂过程中的强烈硬化,大大地提高了它的硬度。
随后涂层的热处理,能保证涂层材料相对伸长值增加和它的硬度降低。
(三)气体动力喷涂技术的研究和发展作者(6)所称的“冷气动力喷涂技术“,是利用未熔融金属颗粒的高动能作用,进行金属颗粒喷涂的方法。
目前它称为冷喷(“Cold Spray”),在全世界得到了广泛的认知。
图4经典气体动力喷涂装置的示意图图中包括气体预热器、密封供粉筒、混合箱和拉瓦尔喷嘴过去和现在,本方法的发展道路都是多样化的。
但它的主要研制都是在经典法的框架内进行的,包括双相混合物的建立和它在超音速喷嘴中的加速(图4)。
在俄国科学院新西伯利亚分院的多相系统物理实验室中,阿·巴·阿尔赫莫夫、弗·费·柯沙列夫和谢·弗·克林柯夫继续并扩大了冷气动力喷涂技术的实验和理论研究。
他们大部分研究工作是优化驱动气体的喷嘴(9-13)。
对超音速双相气流的加速和阻尼的细致研究,促使建立了数学分析公式;利用这个公式,可以对在各种不同的压力、温度和驱动气体成份的情况下,同时还考虑颗粒的浓度,尺寸和密度的影响,评估颗粒由喷嘴输出的速度。
这就为我们设计出具有最好断面的喷嘴和选择最适合的从喷嘴断面到阻碍物的距离(14-17),提供了依据。
最近,,新西伯利亚的研究人员和阿·尼·巴比林(美国俄侨---译者)合作研制了冷喷过程的统计学模型。
这个模型是建立在“颗粒和阻碍物高速度相互作用使表面激活”的观点上(参阅А.П.Алхимов 等? ХОЛОДНОЕ ГАЗОДИНАМИЧЕСКОЕ НАПЫЛЕНИЕ?,(冷气动力喷涂,莫斯科,物理数学文献出版社,共535页。