玻璃窑炉设计技术
玻璃马蹄焰窑炉结构设计

玻璃马蹄焰窑炉结构设计第⼆章结构设计2.1 熔化部设计2.1.1 熔化率K 值确定瓶罐玻璃池窑设计K 值在2.2 —2.6t/m 2.d 为宜。
熔化率取的过⼩,窑炉不节能,取得过⼤,熔化操作困难,或是达不到设计容量,本次取2.5t/ (m i ? d)。
理由如下:⽬前国外燃油瓶罐玻璃窑炉熔化率均在2.2 以上,⽽我国却在2.0 左右,偏低的原因: ( 1)整个池窑缺少有助于强化熔融的配套设计。
( 2)操作管理,设备,材料等使得窑后期⽣产条件恶化。
由于这些影响熔化能⼒的因素,现在瓶罐玻璃K 值偏⼩。
在全⾯改进窑炉结构和有关附属设备后,根据国内耐⽕材料配套情况和玻璃原料量与制备情况。
采取了K=2.5 t/ (nbd)。
2.1.2 熔化池设计(1)确定来了熔化率K值:熔化部⾯积100/2.5=40m2。
(2)熔化池的长、宽、深:L X B X H=8000m沐5000mr? 1200mm本设计取长宽⽐值为1.6 。
长宽⽐确定后,在具体确定窑池长度时,要保证玻璃液充分熔化和澄清,并考虑到砖窑材料的质量以及燃烧⽕焰的情况,⼀般要求⽕焰转向点在窑长的2/3处。
窑长应》4m。
在确定窑池宽度时,应考虑到⽕焰的扩展范围,此范围取决于⼩炉宽度、中墙宽度(两个⼩炉的间距,⼩炉的间距,既要便于热修,⼜不要降低⽕焰的覆盖⾯积,⼀般⼩炉之间的通道宽度取0.9~1.2 m )。
窑池宽度约为2~7m。
长宽选定后,当然具体尺⼨还要按照池底排砖情况(最好是直缝排砖)作出适量调整,池底⼀般厚为200~300m具体的池底排列会在后⾯设计的选材⽅⾯进⾏说明。
这⾥先不做细讲。
综上,本次选⽤L=8m ,B=5m。
窑池深度⼀般根据经验确定。
池深⼀般在900—1200m为宜。
池深不仅影响到玻璃液流和池底温度,⽽且影响玻璃液的物理化学均匀性以及窑炉的熔化率。
⼀般池底温度在1200 —1360 E之间较为合适。
池底温度的提⾼可使熔化率提⾼。
但池底温度⾼于1380C 时,需要提⾼池底耐⽕材料的质量及品种,否则则会加速池底的侵蚀并降低炉龄,且会增加玻璃球的结⽯含量,这对后道拉丝⽣产是不利的,影响池底温度的决定性因素是玻璃的铁含量和玻璃⽓氛。
玻璃窑炉设计技术之单元窑
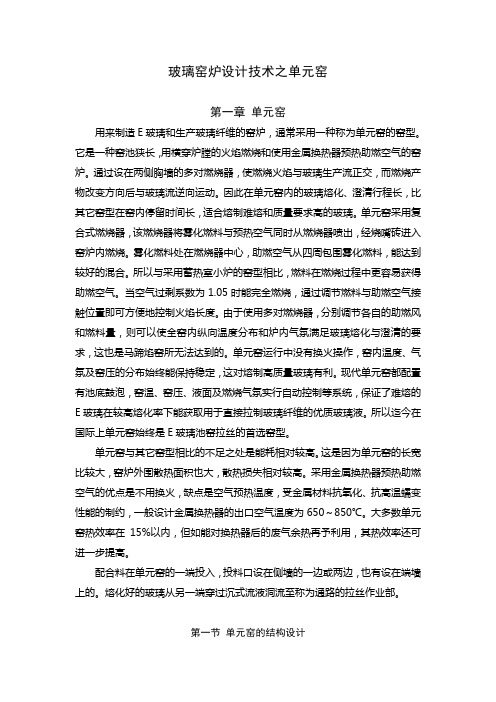
玻璃窑炉设计技术之单元窑第一章单元窑用来制造E玻璃和生产玻璃纤维的窑炉,通常采用一种称为单元窑的窑型。
它是一种窑池狭长,用横穿炉膛的火焰燃烧和使用金属换热器预热助燃空气的窑炉。
通过设在两侧胸墙的多对燃烧器,使燃烧火焰与玻璃生产流正交,而燃烧产物改变方向后与玻璃流逆向运动。
因此在单元窑内的玻璃熔化、澄清行程长,比其它窑型在窑内停留时间长,适合熔制难熔和质量要求高的玻璃。
单元窑采用复合式燃烧器,该燃烧器将雾化燃料与预热空气同时从燃烧器喷出,经烧嘴砖进入窑炉内燃烧。
雾化燃料处在燃烧器中心,助燃空气从四周包围雾化燃料,能达到较好的混合。
所以与采用蓄热室小炉的窑型相比,燃料在燃烧过程中更容易获得助燃空气。
当空气过剩系数为1.05时能完全燃烧,通过调节燃料与助燃空气接触位置即可方便地控制火焰长度。
由于使用多对燃烧器,分别调节各自的助燃风和燃料量,则可以使全窑内纵向温度分布和炉内气氛满足玻璃熔化与澄清的要求,这也是马蹄焰窑所无法达到的。
单元窑运行中没有换火操作,窑内温度、气氛及窑压的分布始终能保持稳定,这对熔制高质量玻璃有利。
现代单元窑都配置有池底鼓泡,窑温、窑压、液面及燃烧气氛实行自动控制等系统,保证了难熔的E玻璃在较高熔化率下能获取用于直接拉制玻璃纤维的优质玻璃液。
所以迄今在国际上单元窑始终是E玻璃池窑拉丝的首选窑型。
单元窑与其它窑型相比的不足之处是能耗相对较高。
这是因为单元窑的长宽比较大,窑炉外围散热面积也大,散热损失相对较高。
采用金属换热器预热助燃空气的优点是不用换火,缺点是空气预热温度,受金属材料抗氧化、抗高温蠕变性能的制约,一般设计金属换热器的出口空气温度为650~850℃。
大多数单元窑热效率在15%以内,但如能对换热器后的废气余热再予利用,其热效率还可进一步提高。
配合料在单元窑的一端投入,投料口设在侧墙的一边或两边,也有设在端墙上的。
熔化好的玻璃从另一端穿过沉式流液洞流至称为通路的拉丝作业部。
第一节单元窑的结构设计一、单元窑熔化面积的确定单元窑熔化面积可用公式F= G/g表示。
年产3000吨高硼硅玻璃窑炉的设计

年产3000吨高硼硅玻璃窑炉的设计2022年4月26日目录1.前言 (1)2.设计任务与原始资料 (2)3.窑型选择 (2)3.1全电熔窑的优点 (2)3.2全电熔窑的缺点 (4)4.窑体主要尺寸确定 (4)4.1 熔化池面积 (4)4.2熔化池的长度与宽度 (5)4.3熔化池的深度 (5)5.电极选择及插入方式 (6)5.1电极尺寸选择 (6)5.2钼电极的插入方法 (7)6.耐火材料选择及计算 (7)6.1可用耐火材料规格 (8)6.2耐火材料的使用 (8)7.窑炉电工和热工计算 (8)7.1玻璃熔化热计算 (8)7.2玻璃耗电量 (9)7.3玻璃热效率 (9)8.小结 (9)9.参考文献 (10)年产3000吨高硼硅玻璃窑炉的设计1.前言1902年,弗尔克(Voelker)获准了一个基本专利,其内容是利用电流通过玻璃配合料产生的热来熔化玻璃。
自那以后,玻璃电熔技术得到了广泛应用。
1979年,据Russel Burman 估计,世界上近半数的玻璃熔窑都将采用电熔技术。
玻璃电熔窑原理:玻璃电熔是将电流通过电极引入玻璃液中,玻璃液直接通电加热,通电后两电极间的玻璃液在交流电的作用下产生电流焦耳热,从而达到熔化和调温的作用。
玻璃液之所以具有导电性,主要是因为电荷通过离子发生迁移。
硅酸盐玻璃具有一个稍无序的网络结构,包含硅、氧、玻璃改良剂离子,玻璃改良剂离子是相对自由的,特别是碱金属离子,它们结合能力最弱,是电流的载体,在硼硅酸盐玻璃中,碱金属离子较少,导电性较差。
玻璃电熔技术是目前国际上最先进的熔制工艺,是玻璃生产企业提高产品质量,降低能耗,从根本上消除环境污染的十分有效的途径。
对于15t/d以下的小型玻璃熔窑来说,在电力充足和电价适中的地区,用电熔工艺来生产各类玻璃制品的综合经济效益是很理想的;在电价较高的地区,对于彩色玻璃、乳浊玻璃、硼硅酸盐玻璃、铅玻璃、高挥发组分玻璃或特种玻璃生产也是合算的。
玻璃窑炉设计及先进经验技术引用

玻璃窑炉设计及先进经验技术引用第一章单元窑第一节单元窑的结构设计一、单元窑熔化面积的确定二、熔池长、宽、深的确定三、池底鼓泡位置的确定四、窑池结构设计五、火焰空间结构设计六、烟道七、通路结构设计第二节耐火材料的选用及砌筑一、单元窑选用的主要耐火材料二、窑炉的砌筑技术第三节单元窑的附属设备一、投料机二、鼓泡器三、燃烧系统四、金属换热器第四节助熔易燃技术的应用一、辅助电熔在单元窑上的应用二、纯氧助燃技术的应用第五节窑炉的启动和投产一、投产准备二、燃料准备三、熟料准备四、制定窑炉升温曲线五、采用热风烤窑技术六、点火烤窑注意事项七、投产第二章玻璃球窑第一节窑炉的结构一、球窑的种类二、马蹄焰球窑结构设计三、球窑砖结构和耐火材料第二节窑炉的熔制一、玻璃球的熔制二、玻璃球的成型三、玻璃球的退火四、玻璃球生产工艺规程第三章全电熔玻璃窑第一节全电熔玻璃窑概述一、全电熔窑的优缺点二、全电熔窑的分类三、全电熔窑一览四、熔制特性及对配合料要求五、电熔窑是防止环境污染有力措施六、玻璃全电熔窑的技术经济分析第二节全电熔窑的结构设计一、全电熔窑的形状二、全电熔玻璃窑炉的加料三、供电电源和电极连接第四章电助熔技术第一节火焰池窑电助熔的意义一、池窑电助熔的优缺点二、电助熔加热的技术分析第二节电助熔池窑设计和操作一、熔窑内电极布置和功率配置二、熔加热功率的计算第三节电助熔池窑的实例一、生产硼硅酸盐BL电助熔池窑二、生产有色BL的电助池窑三、生产平板BI的电助熔池窑第五章供料道的电加热第一节供料道电加热概述一、供料道工作原理及其加热现状二、供料道电加热的优越性三、供料道电加热分类第二节供料道电加热的设计一、料道加热方式的选择二、电加热能耗的计算三、变压器功率确定、电极配置第三节供料道电加热的使用第四节供料道电加热实例第六章先进经验、技术一、窑炉新技术二、窑炉富氧然绕技术三、窑炉图片玻璃窑炉设计及先进经验技术引用第一章单元窑用来制造E玻璃和生产玻璃纤维的窑炉,通常采用一种称为单元窑的窑型。
马蹄焰玻璃窑炉设计技术培训 ppt课件
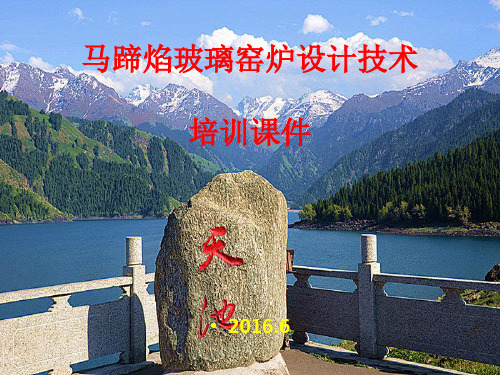
一、玻璃窑炉马蹄焰池窑简介
1.熔化池结构: 窑炉的熔化率主要取决于熔化温度,因为中碱和无碱玻璃球窑 的熔制温度比较高,如果进一步提高熔化温度来提高熔化率,会加 速对耐火材料的侵蚀,降低球质和影响炉龄。而采取鼓泡和电助熔 技术可以相应提高中下层玻璃温度,促进玻璃的均化,并且提高熔 化率。玻璃原料从熔化到澄清的行程也大,这有利于玻璃质量的控 制和提高,而长宽比又受到小炉结构设计、火焰长度及拐弯要求的 限制。池深不仅影响到玻璃液流和池底温度,而且影响玻璃液的物 理化学均匀性以及窑炉的熔化率。一般池底温度在1200—1360℃之 间较为合适。池底温度的提高可使熔化率提高。但池底温度高于 1380℃时,需要提高池底耐火材料的质量及品种,否则会加速池底 的侵蚀并降低炉龄,且会增加玻璃球的结石含量,这对后道拉丝生 产是不利的,影响池底温度的决定性因素是玻璃的铁含量和玻璃气 氛。当Fe2O3含量在0.25—0.3%范围内时,池深800—1200mm的玻 璃球窑,其垂直温降约为15—30℃/100mm。
一、玻璃窑炉马蹄焰池窑简介
6. 小炉: 目前小炉设计仍以实践经验为主,一个成功的设计者 应能用燃烧理论、火焰传热理论去分析、应用和总结实践经验。
(1) 小炉下倾角一般在18—35°范围内选用,燃油小炉一般 选用22—25°,燃烧天然气和干气的小炉下倾角可以大些。在实际 生产行中油枪有5°左右的上仰角,在采用天然气和干气时的仰角 还要更大些,其目的是让火焰与玻璃液面平行。
(2) 小炉喷出口速度(或小炉出口面积),由于燃油雾化后 喷入窑炉空间的燃烧过程中伴随着油雾的气化过程,因此燃料混合 物喷出的速度大,气化膨胀的阻力也大,油类燃料在窑内的停留时 间一般比天然气燃料的时间长,因此燃油小炉喷出的速度可以稍低。 当改用天然气时,如果喷出速度太低,会造成燃烧不完全。小炉喷 出口速度一般参照小炉喷出口处相应温度的空气速度来进行计算比 较合适。小炉喷出的助燃空气要有一定的容积厚度,取其宽高比为 2—3.5。 为了使火焰不直接冲刷胸墙,两座小炉内侧间距应不小于 0.6,小炉外侧与胸墙间距不小于0.3。
玻璃窑炉工艺(一)
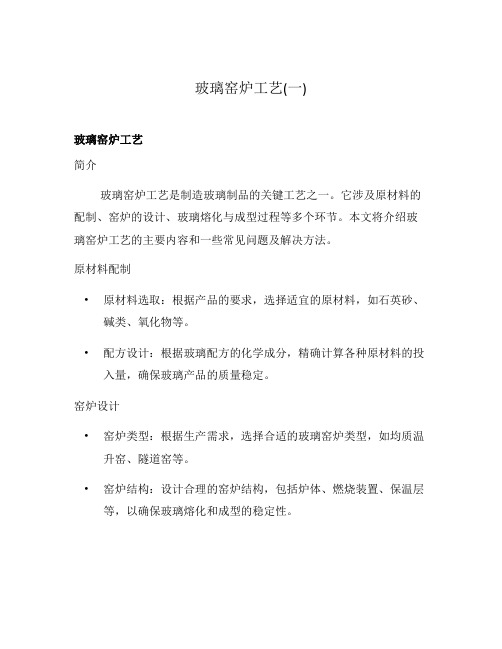
玻璃窑炉工艺(一)玻璃窑炉工艺简介玻璃窑炉工艺是制造玻璃制品的关键工艺之一。
它涉及原材料的配制、窑炉的设计、玻璃熔化与成型过程等多个环节。
本文将介绍玻璃窑炉工艺的主要内容和一些常见问题及解决方法。
原材料配制•原材料选取:根据产品的要求,选择适宜的原材料,如石英砂、碱类、氧化物等。
•配方设计:根据玻璃配方的化学成分,精确计算各种原材料的投入量,确保玻璃产品的质量稳定。
窑炉设计•窑炉类型:根据生产需求,选择合适的玻璃窑炉类型,如均质温升窑、隧道窑等。
•窑炉结构:设计合理的窑炉结构,包括炉体、燃烧装置、保温层等,以确保玻璃熔化和成型的稳定性。
玻璃熔化过程•加料:按照配方要求,将各种原材料逐步加入窑炉中,保持适当的投料速度和顺序。
•燃烧控制:调节燃烧装置,控制燃烧温度和气氛,以实现玻璃原料的熔化。
•熔化调温:通过调节窑炉的温度分布和加热方式,实现熔化温度的控制和调节。
玻璃成型过程•出料:在玻璃熔化达到要求的情况下,逐步将熔融的玻璃从窑炉中取出,保持合适的速度和方法。
•成型方式:根据产品要求,选择合适的成型方式,如浇铸成型、挤压成型、玻璃纤维拉制等。
•冷却处理:经过成型后的玻璃制品需要进行冷却处理,以保证其性能稳定和形状完整。
常见问题及解决方法•玻璃熔化不充分:调整燃烧装置,增加燃料量或提高燃烧温度。
•玻璃成型不良:检查窑炉温度分布,调整加热方式或成型工艺参数。
•玻璃裂纹问题:优化原材料配方,改进冷却处理方式,避免温度快速变化。
以上就是玻璃窑炉工艺的基本内容和常见问题处理方法。
通过合理的配制和设计,以及严格的控制过程参数,可以提高玻璃制品的质量和生产效率。
玻璃炉窑的设计与运行

玻璃炉窑的设计与运行摘要:玻璃熔制是玻璃制造中的主要过程之一,是通过燃料的燃烧,将热量传递给配合料,从而达到熔化目的的过程。
玻璃的熔制过程是在玻璃窑炉内实现的。
着玻璃生产技术的不断发展进步,电子玻璃、浮法玻璃等生产行业在追求高质量和高效益的同时,对玻璃生产的环保也有了更高的要求.传统的玻璃熔制工艺已经很难满足更高的环保要求,此时采用全氧燃烧技术的玻璃窑炉的出现无疑成为解决行业生产“节能、环保”问题的一个有效途径。
关键词:玻璃炉窑节能环保设计与运行全氧燃烧玻璃炉1.窑炉的设计原则熔窑是浮法玻璃生产线三大热工设备之首,是实现全线产量、质量目标的关键设备之一,必须做到能耗低、产量高、熔化玻璃质量好、窑龄长等要求。
为了实现上述要求,具体提出了如下设计原则:(1)认真总结国外同级别浮法熔窑的经验和教训,结合国内生产线的实际情况、操作特点,围绕生产优质玻璃液这个重点来进行设计。
(2)着重节能降耗,采用国际先进的节能措施和节能产品,降低生产成本。
(3)全窑工艺尺寸确定既要注重以往的经验数据,同时要有理论创新,要在总结以往经验数据的基础上对新结构确立理论依据。
(4)本熔窑出现的超出国内设计手册的结构设计,必须确保结构安全,此类结构需建立相应的力学模型,并经过常温和热态理论论证通过后方可用于设计。
(5)设计中充分考虑延长窑龄的方法和措施,既要注重耐火材料装备水平,又要充分考虑生产后期保窑操作的可能性及方便性。
(6)节省投资,材料配置上注重实用性,不搞花架子。
主要材料立足于国内采购,尽量少引进硬件,以减少外汇开支。
2.全氧燃烧炉的设计我国已经有很多大学院校和设计单位对全氧燃烧窑炉进行过理论上的研究探讨,但是目前国内的全氧燃烧窑炉基本上是完全引进国外的设计、技术,甚至整条生产线,不仅投资很大,而且使我们自己的全氧燃烧技术发展缓慢。
近年来我院实际参与了国内几台全氧池炉的引进、,设计转化工作,对国外先进技术进行了一些研究,在全氧玻璃池炉的设计上积累了一些经验。
玻璃电熔窑炉技术

玻璃电熔窑炉技术玻璃电熔窑炉技术是一种重要的工业技术,是制造高质量玻璃制品的主要手段。
该技术的应用范围广泛,包括建筑、汽车、家居用品和光学玻璃等领域。
本文将从原理、特点、应用和未来发展等方面对玻璃电熔窑炉技术进行介绍。
原理:玻璃电熔窑炉技术是利用电能产生高温,使导电介质中的电能转化为热能,加热熔化玻璃原料。
它主要由熔融槽和加热系统两部分组成。
熔融槽是贮存玻璃原料的容器,加热系统则通过直接或间接方式加热熔融槽,使玻璃原料熔化后成型。
熔融槽可采用一次性熔融或多次循环熔融的方式,加热系统可采用电极、电阻、石英加热体等多种方式。
特点:1.高效节能。
相对于其他传统加热方式,玻璃电熔窑炉技术具有高效节能的特点,能够大幅降低生产成本。
2.可控性强。
玻璃电熔窑炉技术采用电能加热,具有加热温度和时间可控性强的优点,可根据生产需要随时调整加热参数。
3.生产效率高。
玻璃电熔窑炉技术具有高温、高速熔化的优点,生产效率可比其他传统方式高出数倍。
4.环保。
玻璃电熔窑炉技术不使用火炭、油、煤等传统燃料,可以大幅降低污染物排放。
应用:玻璃电熔窑炉技术已经广泛应用于各个领域。
例如,建筑领域中常常使用该技术制作各种平板玻璃、反光玻璃、屋面玻璃等产品。
在汽车领域中,玻璃电熔窑炉技术也是生产车窗、后视镜、挡风玻璃等产品的主要方法。
家居用品领域中,该技术可用于制造玻璃餐具、封口瓶等产品。
光学领域中,玻璃电熔窑炉技术则能够制造高精度的光学玻璃产品。
未来发展:在未来,玻璃电熔窑炉技术还将进一步发展。
目前,该技术在生产力和效率上已经达到了比较成熟的阶段,未来将主要集中在绿色制造和节能环保方向。
首先,可将电力来源改为清洁能源,如太阳能、水能等,以进一步降低对环境的影响。
其次,从技术方面来看,可以通过改进加热系统和生产过程,使玻璃电熔窑炉技术更加节能和环保。
结论:玻璃电熔窑炉技术是一种高效、环保、可控的玻璃制造技术,已经得到了广泛应用。
未来,它还将继续发展,并逐渐向更加绿色、节能、环保的方向发展。
日产300吨浮法玻璃窑炉课程设计
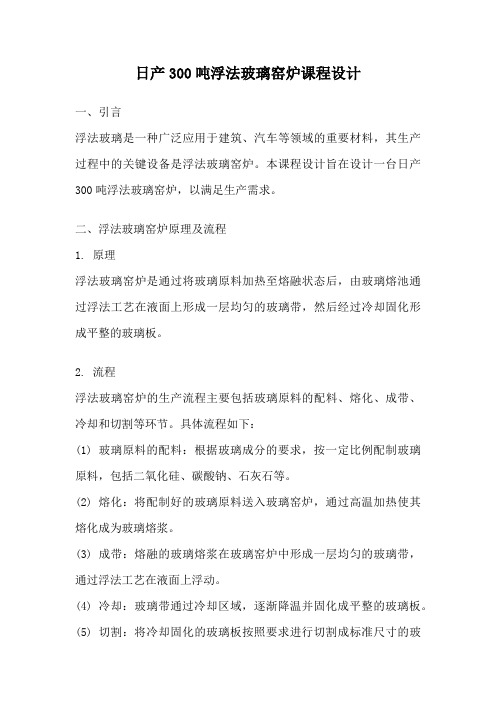
日产300吨浮法玻璃窑炉课程设计一、引言浮法玻璃是一种广泛应用于建筑、汽车等领域的重要材料,其生产过程中的关键设备是浮法玻璃窑炉。
本课程设计旨在设计一台日产300吨浮法玻璃窑炉,以满足生产需求。
二、浮法玻璃窑炉原理及流程1. 原理浮法玻璃窑炉是通过将玻璃原料加热至熔融状态后,由玻璃熔池通过浮法工艺在液面上形成一层均匀的玻璃带,然后经过冷却固化形成平整的玻璃板。
2. 流程浮法玻璃窑炉的生产流程主要包括玻璃原料的配料、熔化、成带、冷却和切割等环节。
具体流程如下:(1) 玻璃原料的配料:根据玻璃成分的要求,按一定比例配制玻璃原料,包括二氧化硅、碳酸钠、石灰石等。
(2) 熔化:将配制好的玻璃原料送入玻璃窑炉,通过高温加热使其熔化成为玻璃熔浆。
(3) 成带:熔融的玻璃熔浆在玻璃窑炉中形成一层均匀的玻璃带,通过浮法工艺在液面上浮动。
(4) 冷却:玻璃带通过冷却区域,逐渐降温并固化成平整的玻璃板。
(5) 切割:将冷却固化的玻璃板按照要求进行切割成标准尺寸的玻璃产品。
三、日产300吨浮法玻璃窑炉设计要点1. 窑炉容量:根据日产量为300吨,需要设计具备足够容量的窑炉,以满足生产需求。
2. 燃料选择:选择适合的燃料,如天然气、重油等,保证窑炉的高效运行。
3. 温度控制:合理设计温度控制系统,确保玻璃熔浆在窑炉中达到适宜的熔化温度,并且在成带和冷却过程中保持稳定。
4. 玻璃带成型:通过合理的玻璃带成型机构,使得玻璃带在浮法工艺中形成均匀、平整的带状结构。
5. 冷却系统:设计合理的冷却系统,使得玻璃带能够逐渐降温并固化成平整的玻璃板。
6. 切割系统:设计高效的玻璃板切割系统,确保按照要求将玻璃板切割成标准尺寸的产品。
四、日产300吨浮法玻璃窑炉课程设计步骤1. 确定窑炉规格和参数,包括窑炉容量、燃料种类、温度控制范围等。
2. 设计窑炉结构,包括炉体、隔热层、加热系统、玻璃带成型机构、冷却系统和切割系统等。
3. 设计温度控制系统,包括温度传感器、温度控制器和加热控制装置等。
玻璃窑炉工艺技术

玻璃窑炉工艺技术
玻璃窑炉工艺技术是玻璃制造过程中非常重要的一环,它直接影响着玻璃制品的质量和成本。
下面我将介绍一下玻璃窑炉的工艺技术。
首先,玻璃窑炉的设计和结构非常重要。
一个好的窑炉应该具备良好的密封性能和热工性能,以确保窑内的温度和气氛稳定。
窑炉的直径和长度需要根据生产需求和玻璃的种类来确定,以确保玻璃能够充分地熔化和加工。
其次,玻璃窑炉的燃烧系统也是关键因素之一。
燃烧系统应该能够提供足够的热量,并且可以精确地控制窑内的温度分布。
常见的燃烧系统有煤气燃烧和油气燃烧两种,选择哪一种取决于当地的能源供应情况和环保要求。
另外,窑炉内的玻璃熔池的管理也是非常重要的。
玻璃熔池的温度和成分需要精确地控制,以确保玻璃的质量和成型的顺利进行。
在管理过程中,需要考虑到燃烧系统的输入、熔化过程中的加料和循环以及废料的处理等因素。
此外,玻璃窑炉的冷却系统也是不可忽视的一部分。
它可以通过调节冷却风的流速和温度分布来控制玻璃的冷却速率,以确保玻璃的成型和品质。
冷却系统的设计和使用需要根据具体的玻璃类型和加工要求来进行调整。
最后,玻璃窑炉的自动化控制系统可以提高生产效率和产品质量。
通过使用温度、压力和气氛等参数的实时监测和控制,可
以及时发现并修正窑内的异常情况,减少人为错误和产品缺陷的发生。
综上所述,玻璃窑炉工艺技术在玻璃制造过程中起着至关重要的作用。
通过合理设计和精确控制,可以提高生产效率、降低生产成本,并确保玻璃产品的质量。
随着科技进步的推动,玻璃窑炉工艺技术也在不断发展,带来更高效、环保的制造方式。
玻璃炉窑的设计与运行

玻璃炉窑的设计与运行摘要:玻璃熔制是玻璃制造中的主要过程之一,是通过燃料的燃烧,将热量传递给配合料,从而达到熔化目的的过程。
玻璃的熔制过程是在玻璃窑炉内实现的。
着玻璃生产技术的不断发展进步,电子玻璃、浮法玻璃等生产行业在追求高质量和高效益的同时,对玻璃生产的环保也有了更高的要求.传统的玻璃熔制工艺已经很难满足更高的环保要求,此时采用全氧燃烧技术的玻璃窑炉的出现无疑成为解决行业生产“节能、环保”问题的一个有效途径。
关键词:玻璃炉窑节能环保设计与运行全氧燃烧玻璃炉1.窑炉的设计原则熔窑是浮法玻璃生产线三大热工设备之首,是实现全线产量、质量目标的关键设备之一,必须做到能耗低、产量高、熔化玻璃质量好、窑龄长等要求。
为了实现上述要求,具体提出了如下设计原则:(1)认真总结国外同级别浮法熔窑的经验和教训,结合国内生产线的实际情况、操作特点,围绕生产优质玻璃液这个重点来进行设计。
(2)着重节能降耗,采用国际先进的节能措施和节能产品,降低生产成本。
(3)全窑工艺尺寸确定既要注重以往的经验数据,同时要有理论创新,要在总结以往经验数据的基础上对新结构确立理论依据。
(4)本熔窑出现的超出国内设计手册的结构设计,必须确保结构安全,此类结构需建立相应的力学模型,并经过常温和热态理论论证通过后方可用于设计。
(5)设计中充分考虑延长窑龄的方法和措施,既要注重耐火材料装备水平,又要充分考虑生产后期保窑操作的可能性及方便性。
(6)节省投资,材料配置上注重实用性,不搞花架子。
主要材料立足于国内采购,尽量少引进硬件,以减少外汇开支。
2.全氧燃烧炉的设计我国已经有很多大学院校和设计单位对全氧燃烧窑炉进行过理论上的研究探讨,但是目前国内的全氧燃烧窑炉基本上是完全引进国外的设计、技术,甚至整条生产线,不仅投资很大,而且使我们自己的全氧燃烧技术发展缓慢。
近年来我院实际参与了国内几台全氧池炉的引进、,设计转化工作,对国外先进技术进行了一些研究,在全氧玻璃池炉的设计上积累了一些经验。
玻璃窑炉结构设计
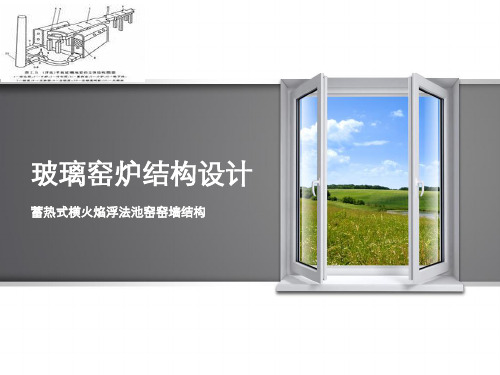
玻璃窑炉结构设计
蓄热式横火焰浮法池窑窑墙结构
一、玻璃窑炉种类
1、间歇式
多品种,小批量(几 百公斤~几吨) (1)坩埚窑
用于手工传统工艺品
(2)电炉
生产小型仿玉玻璃
LOGO
Page 2
2、连续式
一边加热,一边输热 (1)换热式
通过同形砖、金属换热器 温度稳定
(2)蓄热式:
限制交换时间, 效率高 火焰形成:马蹄焰 横火焰
LOGO
Page 12
二、蓄热式、横火焰、大型炉
窑炉结构
4、烟道及烟囱
(1)玻璃液面在10~12m时, 烟囱一般为55m以上
5、余热处理、净化系统
LOGO
Page 13
二、蓄热式、横火焰、大型炉
窑墙耐火材料
1、池壁砖 2.胸墙砖
砖电 熔 锆 刚 玉
粘 土 大 砖
保 温 层
砖电 熔 锆 刚 玉
硅 砖轻 质 质 硅 捣 打 料
轻 质 粘 土 砖
LOGO
Pa炉结构
2、卡脖
宽度:相当于融化部的1/3~1/4 深度:600~800mm,浅些好 材料、挡砖:不回流 长度:3m左右,根据产量 搅拌:水平较方便,垂直
LOGO
Page 11
二、蓄热式、横火焰、大型炉
窑炉结构
3、冷却部
小型化,占融化部面积的15%~20% 池深浅:400~600mm 冷却方式:强制冷却上部吹冷风,一般为自然冷却
LOGO
Page 3
蓄热体
在窑炉两侧建蓄热室:先通烟气,再通空气
1100~1300℃
1400℃左右
气空
蓄热室
气烟
镁砖,高铝砖 粘土砖
年产3000高硼硅玻璃窑炉的设计

百度文库年产3000吨高硼硅玻璃窑炉的设计2020年7月12日目录1.前言 (1)2.设计任务与原始资料 (2)3.窑型选择 (2)3.1全电熔窑的优点 (2)3.2全电熔窑的缺点 (4)4.窑体主要尺寸确定 (4)4.1 熔化池面积 (4)4.2熔化池的长度与宽度 (5)4.3熔化池的深度 (5)5.电极选择及插入方式 (6)5.1电极尺寸选择 (6)5.2钼电极的插入方法 (7)6.耐火材料选择及计算 (7)6.1可用耐火材料规格 (8)6.2耐火材料的使用 (8)7.窑炉电工和热工计算 (8)7.1玻璃熔化热计算 (8)7.2玻璃耗电量 (9)7.3玻璃热效率 (9)8.小结 (9)9.参考文献 (10)年产3000吨高硼硅玻璃窑炉的设计1.前言1902年,弗尔克(Voelker)获准了一个基本专利,其内容是利用电流通过玻璃配合料产生的热来熔化玻璃。
自那以后,玻璃电熔技术得到了广泛应用。
1979年,据Russel Burman 估计,世界上近半数的玻璃熔窑都将采用电熔技术。
玻璃电熔窑原理:玻璃电熔是将电流通过电极引入玻璃液中,玻璃液直接通电加热,通电后两电极间的玻璃液在交流电的作用下产生电流焦耳热,从而达到熔化和调温的作用。
玻璃液之所以具有导电性,主要是因为电荷通过离子发生迁移。
硅酸盐玻璃具有一个稍无序的网络结构,包含硅、氧、玻璃改良剂离子,玻璃改良剂离子是相对自由的,特别是碱金属离子,它们结合能力最弱,是电流的载体,在硼硅酸盐玻璃中,碱金属离子较少,导电性较差。
玻璃电熔技术是目前国际上最先进的熔制工艺,是玻璃生产企业提高产品质量,降低能耗,从根本上消除环境污染的十分有效的途径。
对于15t/d以下的小型玻璃熔窑来说,在电力充足和电价适中的地区,用电熔工艺来生产各类玻璃制品的综合经济效益是很理想的;在电价较高的地区,对于彩色玻璃、乳浊玻璃、硼硅酸盐玻璃、铅玻璃、高挥发组分玻璃或特种玻璃生产也是合算的。
玻璃窑炉技术改造工程方案

玻璃窑炉技术改造工程方案一、项目背景玻璃制造行业是国民经济中的重要组成部分,玻璃产品应用广泛,包括建筑玻璃、家用玻璃、汽车玻璃等。
而玻璃制造过程中所需的玻璃窑炉技术直接影响着生产效率和产品质量。
近年来,随着环保意识的提高和能源成本的上升,玻璃制造企业都面临着如何提高生产效率、降低能耗和排放的问题。
因此,进行玻璃窑炉技术改造成为许多玻璃制造企业的重要课题。
二、现状分析当前我国玻璃制造企业的玻璃窑炉技术主要存在以下问题:1. 能耗大,环境污染严重。
传统玻璃窑炉采用燃煤或者重油作为燃料,燃烧不充分导致排放大量废气和废渣,对环境造成严重污染。
同时,能源消耗大也直接影响了企业的生产成本。
2. 生产效率低。
传统玻璃窑炉采用手工操作或者简单的自动控制系统,无法实现智能化生产,生产效率低下。
3. 产品质量不稳定。
由于传统玻璃窑炉的控制能力有限,难以保证生产中产品的稳定质量。
综上所述,传统玻璃窑炉技术面临的问题亟待解决,需要进行技术改造来提高生产效率、降低能耗和排放、提升产品质量。
三、技术改造方案基于以上现状分析,针对玻璃窑炉技术的改造,提出如下技术方案:1. 优化燃烧系统。
采用高效、清洁的天然气燃料代替传统的煤炭或者重油,减少排放物的产生,提高能源利用率。
并且引入先进的燃烧控制技术,实现燃烧过程的精准控制,减少燃料的浪费,降低能耗。
2. 智能化控制系统。
引入先进的自动控制系统,实现对整个生产过程的智能化控制和监测,包括温度、压力、流量等参数的实时监控和调节。
通过数据采集和分析,实现生产过程的智能优化,提高生产效率。
3. 热回收技术。
利用余热回收技术,将窑炉烟气中的热能进行回收利用,用于加热水或者发电,提高能源利用效率。
4. 其他辅助设施改造。
对于玻璃窑炉周边的辅助设施,如气体净化系统、废气处理设备等也进行改造升级,保证整个生产过程的环保和安全。
四、项目实施方案1. 技术改造方案确定后,需要进行详细的项目实施方案制定。
45m2燃油高效节能玻璃窑炉的设计与施工

45m2燃油高效节能玻璃窑炉的设计简介山东省轻工业设计院王均光窑炉是玻璃厂的的心脏,其使用寿命的长短与熔化质量的高低将直接关系到工厂的经济效益(此不多述说)。
本文主要介绍了一座45m2燃油蓄热式马蹄燃玻璃窑炉,设计中所采用的主要节能技术与参数进行了简单的介绍,不妥之处恳请各位同仁指正。
一、设计的基础条件a、窑炉的熔化能力:要满足年产2万吨成品玻璃瓶。
b、产品方案:640ml啤酒瓶,标准:《GB4544-1996》。
c、料色:颜色料与无色料(主导产品为:640ml瓶)。
d、炉龄:5年以上。
e、能耗:要求≤140kg重油/t玻璃液。
二、熔化面积及窑型的确定综合以上条件,并考虑到熔化能力、能耗、炉龄、耐火材料的匹配、造价,并经过燃烧等方面的综合计算(此略),最终确定为:45m2蓄热式马蹄燃池窑。
三、设计中采用主要技术的内容,见下表四、设计中采用的主要技术参数五、关键部位的结构设计及材料的匹配耐火材料的选用与匹配是否合理将直接关系到窑炉的寿命。
窑炉的易损地方是与火焰与玻璃液接触部位,主要有:加料口拐角及上部连接碹、大碹、流液洞、窑坎、池底、加料口对墙、小炉及其喷火口、池壁、胸墙火焰拐弯的部位、前后墙等。
因此在设计与选材时要注意以上几个关键部位的材料选用与匹配,尤其是要注意酸、碱性材料不能直接接触使用。
5.1关键部位的耐火材料的匹配,见下表:注:“层序”是指所用材料在窑炉中自内到外:自上到下的排列次序。
5.2关键部位的几个有特点的结构设计窑炉的结构设计不仅要考虑各种砖材的搭配、砖缝的留设要合理,还要考虑砖与钢结构之间的结合的问题,否则可能要出现这样那样的事故也可能导致烤窑后整个窑炉的变形,影响窑炉的使用寿命。
a、加料口上部结构设计该加料口是专为裹入式加料机设计的,具有密闭与预熔的功能,主要有两部分组成:固定与移动部分,如下图:b、小炉结构设计示意该小炉采用了内倾与下倾且较扁的形式利于火焰拐弯与扩大覆盖面积,利于化料,形式如下:c、窑坎窑坎的结构形式是比较关键的,如果不合理可能导致池底的流料,本设计的窑坎在防止流料及使用寿命等方面都作了充分的考虑,其结构形式如下:d、蓄热室底部的设计该蓄热室底部采用风洞的结构形式,可有效的保护蓄热室基础,其结构形式如下:e、胸墙的结构设计该窑炉的胸墙的结构设计如下,形式比较新颖易于彻筑与维修,结构如下:总之,该窑炉无论在其结构上还是在其选材上都有许多独到之处,由于种种原因,在此仅讲到其中的部分内容,不当之处恳请同行指正。
玻璃窑炉设计

目录设计说明 ........................................................................................................................ ΙDesign Specification . (III)目录 (V)第一章浮法玻璃工业概述 (1)1.1玻璃 (1)1.2 玻璃工艺 (1)1.3 浮法玻璃 (2)1.4生产工艺 (3)1.4.1 原料生产工艺流程 (3)1.4.2 燃油系统工艺流程 (4)1.4.3 浮法联合车间玻璃生产工艺流程 (5)1.5 窑炉 (6)1.6 熔窑设计 (7)第二章玻璃原料 (9)2.1 主要原料 (9)2.1.1 引入二氧化硅的原料 (9)2.1.2 引入氧化铝的原料 (10)2.1.3 引入氧化硼的原料 (10)2.1.4 引入氧化钠的原料 (10)2.1.5 引入氧化钾的原料 (11)2.1.6 引入氧化钙的原料 (11)2.1.7 引入氧化镁的原料 (11)2.2 辅助原料 (11)2.2.1 澄清剂 (12)2.2.2 氧化剂 (12)2.2.3 还原剂 (12)2.2.4 脱色剂 (12)V2.2.5 着色剂 (12)2.3 配合料质量要求 (13)第三章熔制车间的物料平衡计算 (14)3.1 本设计工艺制度 (14)3.1.1料方及原料组成 (14)3.1.2碎玻璃用量 (14)3.1.3配合料(不包括碎玻璃) (14)3.2 玻璃成分确定 (14)3.3 配合料用量计算 (16)第四章热平衡计算 (17)4.1 玻璃形成过程的热量平衡 (17)4.1.1 支出热量 (17)4.1.2 收入热量 (18)4.2 熔化部热平衡 (18)4.2.1 熔化部的热平衡分析 (18)4.2.2 油燃烧计算 (19)4.2.3 各项热收入项的计算 (20)4.2.4 各项热支出项的计算 (21)4.2.5 热平衡计算 (23)第五章玻璃窑体主要尺寸确定 (24)5.1 玻璃熔制部分设计 (24)5.1.1 熔化部的设计 (24)5.1.2 分隔装置的设计 (27)5.1.3 投料部分设计 (27)5.1.4 冷却部的计算 (27)5.2 热源供给部分的设计 (28)5.3 余热回收设备—蓄热室的设计 (29)5.4 排烟供气系统的设计 (29)第六章窑炉耐火材料选用 (31)6.1 熔化部用耐火材料 (31)6.1.1 与玻璃液相接触的部分 (31)VI6.1.2 火焰空间 (32)6.2 冷却部用耐火材料 (32)6.3 锡槽用耐火材料 (33)6.4 蓄热室用耐火材料 (33)6.5 烟道和烟囱用耐火材料 (34)6.6 玻璃退火窑用的耐火材料 (34)参考文献 (35)致谢 (36)VII第一章浮法玻璃工业概述1.1玻璃玻璃:一种透明的固体物质,在熔融时形成连续网络结构,冷却过程中粘度逐渐增大并硬化而不结晶的硅酸盐类非金属材料。
- 1、下载文档前请自行甄别文档内容的完整性,平台不提供额外的编辑、内容补充、找答案等附加服务。
- 2、"仅部分预览"的文档,不可在线预览部分如存在完整性等问题,可反馈申请退款(可完整预览的文档不适用该条件!)。
- 3、如文档侵犯您的权益,请联系客服反馈,我们会尽快为您处理(人工客服工作时间:9:00-18:30)。
玻璃窑炉设计技术第一章单元窑用来制造E玻璃和生产玻璃纤维的窑炉,通常采用一种称为单元窑的窑型。
它是一种窑池狭长,用横穿炉膛的火焰燃烧和使用金属换热器预热助燃空气的窑炉。
通过设在两侧胸墙的多对燃烧器,使燃烧火焰与玻璃生产流正交,而燃烧产物改变方向后与玻璃流逆向运动。
因此在单元窑内的玻璃熔化、澄清行程长,比其它窑型在窑内停留时间长,适合熔制难熔和质量要求高的玻璃。
单元窑采用复合式燃烧器,该燃烧器将雾化燃料与预热空气同时从燃烧器喷出,经烧嘴砖进入窑炉内燃烧。
雾化燃料处在燃烧器中心,助燃空气从四周包围雾化燃料,能达到较好的混合。
所以与采用蓄热室小炉的窑型相比,燃料在燃烧过程中更容易获得助燃空气。
当空气过剩系数为1.05时能完全燃烧,通过调节燃料与助燃空气接触位置即可方便地控制火焰长度。
由于使用多对燃烧器,分别调节各自的助燃风和燃料量,则可以使全窑内纵向温度分布和炉内气氛满足玻璃熔化与澄清的要求,这也是马蹄焰窑所无法达到的。
单元窑运行中没有换火操作,窑内温度、气氛及窑压的分布始终能保持稳定,这对熔制高质量玻璃有利。
现代单元窑都配置有池底鼓泡,窑温、窑压、液面及燃烧气氛实行自动控制等系统,保证了难熔的E玻璃在较高熔化率下能获取用于直接拉制玻璃纤维的优质玻璃液。
所以迄今在国际上单元窑始终是E玻璃池窑拉丝的首选窑型。
单元窑与其它窑型相比的不足之处是能耗相对较高。
这是因为单元窑的长宽比较大,窑炉外围散热面积也大,散热损失相对较高。
采用金属换热器预热助燃空气的优点是不用换火,缺点是空气预热温度,受金属材料抗氧化、抗高温蠕变性能的制约,一般设计金属换热器的出口空气温度为650—850。
大多数单元窑热效率在15%以内,但如能对换热器后的废气余热再予利用,其热效率还可进一步提高。
配合料在单元窑的一端投入,投料口设在侧墙的一边或两边,也有设在端墙上的。
熔化好的玻璃从另一端穿过沉式流液洞流至称为通路的拉丝作业部。
第一节单元窑的结构设计一、单元窑熔化面积的确定单元窑熔化面积可用公式F= G/g表示。
式中F———熔化面积,M2;g———熔化率,(t/M2·d)。
熔化率反映单元窑的设计和生产管理水平,包括原料成分、水分、质量的控制和窑炉运行的控制水平等,同时还与纤维直径有关。
一般拉制纺织纱的单元窑,g取0.8—1.0 t/M2·d,拉制粗直径纱时可取略大一些1.5 t/M2·d。
早期的技术资料表明当年的单元窑平均日产玻璃的熔化面积,可见现在已有较大进步。
二、熔池长、宽、深的确定(1)池长L和池宽B是根据熔化面积和熔池长宽比(L/B)来决定的。
即:FB=————平方L/BL/B越大,投入窑炉的玻璃原料从熔化到完成澄清,其间的玻璃“行程”越长,也越有利于熔化和澄清。
早期设计的单元窑熔他是很长的,日产量在8—50t/d,(L/B)5—4。
随着单元窑配合料微粉化及熔制工艺和鼓泡技术的发展与成熟,以及窑体耐火材料的质量提高和采用保温技术等措施,使熔池长宽比在3左右,也同样可以获得满意的玻璃质量。
现在设计取(L/B)值时,只有在考虑为下届窑炉有较大扩产需要时才选取(L/B)大一些,一般情况下取(L/B)为3—4。
(2)他深h主要取决于玻璃的透热性及池底耐火材料能承受的温度。
早期池底铺面砖选用致密结砖时,池底温度一般控制在1350℃以内,而池底温度又直接影响玻璃熔化质量和窑炉熔化率。
现在的F 玻璃单元窑,由于池底部位采取保温和鼓泡技术措施,在提高熔化率的同时,使热点附近的池底玻璃温度也提高到1440—1470℃,因此池底2/3以上高温区域的铺面层砖改用耐温和耐侵蚀性能更好的致密铬砖。
有时也可通过适当加高池深来达到降低池底温度。
一般而言,E玻璃单元窑单产在以下30t/ d,池深选600—700mm,随着单产的增大,目前的最高池深可达900mm左右。
三、池底鼓泡位置的确定单元窑池底设置鼓泡装置,按其作用大致有以下几种方式。
(1)将鼓泡器布置在配合料生料堆聚集层最厚的部位有助于打散生料堆。
但由于投料口和投料机的改进,目前已没有必要使用这种方法了。
(2)将鼓泡器排布在生料堆消失的位置,该部位的玻璃液温度已经比较高了,因此通过鼓泡可强制较高温度的玻璃液向生料区推移,底部的玻璃液也可翻到面上吸收窑炉火焰空间更多热量,起到助熔作用,通过物理和数学模拟也都能证明这一点。
要注意的是不能让生料层覆盖在鼓泡区域的玻璃液面上,否则将无法起助熔作用。
(3)将鼓泡器布置在窑池玻璃液最高温度区,一般约为池长2/3 处,鼓泡作用可使更多的含气泡玻璃翻至玻璃液面排泡,起到促进澄清和均化的效果。
E玻璃单元窑的池底鼓泡位置通常按以下两种原则确定:一是在池长1/3处布置一排鼓泡器起助熔作用,在池长2/3—4/5处布置另一排鼓泡器,起促进澄清和均化作用。
这种布置也是轻工窑炉鼓泡常用的方式;二是第一排鼓泡布置在池长1m附近,第二排紧随其后,二排间相距约E或更近。
这种布置是近年来E玻璃单元窑常用的方式,理由是当采用细而干的微粉原料熔制* 玻璃时,熔化不再是难题,但由于玻璃液中存在大量的气泡,因此良好的澄清和均化是确保玻璃液质量和提高熔化率的主要因素,采用两排鼓泡集中布置可起到类似窑坎阻挡生料流的作用和加强玻璃液均化的作用。
四、窑池结构设计(1)E玻璃单元窑的池壁结构有多种排列方式,适合小型池窑,池壁内侧没有横缝,池壁使用期一般不超过5年,在窑炉运行后期部分池壁要进行喷水冷却保窑。
该结构对部分低温区可用致密锆砖替代昂贵的致密铬砖,节约部分投资。
适用于较低温的池壁,这种结构一般不用喷水冷却保窑,而用外层加贴新砖来延长窑炉运行期。
结构的池壁采用致密铬砖横向排列,因为致密铬砖不同于致密锆和AES, 砖,其横缝与竖缝的侵蚀速度差别不大。
(2)池底结构。
A.适合于池底温度长期不高于1350℃,短期不高于1370℃的窑池。
B.采取鼓泡孔二侧的致密铬砖高出池底面,而鼓泡头又高于两侧铬砖的方式,这样可在鼓泡头位置以下形成液滞流区,减少由于玻璃液冲刷对池底造成的侵蚀。
C.采取鼓泡砖高出池底面而鼓泡头又高出鼓泡砖50mm左右的方式,同样也可使池底耐火材料少受玻璃液的冲刷侵蚀。
(3)流液洞结构。
当熔化池中已熔化、澄清好的玻璃液流经流液洞时,被强制降温并流入作业部的主通路。
因此流液洞的作用既是熔池和通路间的连通道,也是熔化部和作业部的分隔区。
E玻璃单元窑除了采用通常结构流液洞外,也常采用一种带有挡砖的流液洞结构。
挡砖一般用优质错砖或铬砖做成,厚度为100—150mm,包覆合金皮,浸入玻璃液部分的铂合金皮厚1mm,露在玻璃液上面的铂合金皮厚0.5mm。
包铂合金皮的挡砖应伸进两边侧墙各150mm,以致当侧墙砖被侵蚀时,挡砖依然完整。
为安全起见,在制订窑炉砌筑计划时,要使得包铂挡砖能在砌窑收尾阶段插进去。
挡砖以下的流液洞尺寸一般是洞高为洞宽的1/2—4/5,这种洞口形式更有利于从熔化池获取熔制质量好的玻璃进入主通路。
此外玻璃液进入流液洞的流速不宜过快,以4_—12m/h范围为宜,同时流速比较高的玻璃对底砖的侵蚀也较大,因此在流液洞处底砖要用铬砖面衬。
铂铑合金包皮长期在高温玻璃液中浸泡,晶体会长大、变脆,在玻璃液的冲刷下便容易损坏。
为延长挡砖使用时间,可考虑在挡砖侧面开两个直径25mm的孔,通入水管冷却或吹风冷却,这适合于日产量比较大的单元窑和玻璃液在洞内流速较快的情况。
五、火焰空间结构设计火焰空间指大碹以下、玻璃液面以上的空间,它的周边包括胸墙、前墙和后墙。
窑池长、宽确定之后,影响火焰空间大小的就是胸墙高度。
对火焰空间容积的确定,主要考虑燃料的燃烧和发热状况。
玻璃窑炉内燃料的燃烧属于扩散式燃烧。
除了高温环境及充足的助燃空气条件外,燃烧速度还取决于氧气的扩散和不断与燃料混合! 燃烧的过程,氧气扩散速度将直接影响燃烧的速度,同时必须提供足够的扩散空间和时间,使燃料达到完全燃烧。
送入窑炉空间的燃料的化学能及燃料与空气的物理能之和与空间容积之比,称为容积发热强度。
根据窑炉运行经验及充分考虑到窑炉耐火材料所允许的承受强度,一般取容积发热强度为120—240KW/m3,通过该数值可以计算或核算胸墙高度。
一般轻工窑炉的胸墙较高,约为1—2m,而单元窑熔化率低,胸墙高度为0.8—1.0m。
一般胸墙重量都是独立支撑在立柱上,池壁与胸墙间用挂钩砖分隔,挂钩砖砌筑时应与池壁留有鼓胀间隙,烤窑结束后再用锆泥把余留的缝隙密封。
在胸墙部位沿窑长方向分设多对烧嘴。
支撑烧嘴的烧嘴砖,插入两侧胸墙,彼此相对放置。
烧嘴间距为600—1000mm,采用气体燃料或低粘度燃料油,烧嘴间距一般取600mm左右,采用高粘度重油时,烧嘴喷油孔过小容易堵塞,这时可适当放大油孔,烧嘴间距也相应放大。
在投料口区第一对烧嘴与后池墙之间的距离对生料熔化和排烟温度都有影响,距离越小该区温度高,化料快,但排烟温度高,会降低热效率,甚至使金属换热器过热。
距离太大不利化料,影响熔化率。
一般距离为1.2—1.6mm。
前池壁与最末一对烧嘴间距,一般为0.3—0.5mm。
为了监视窑内熔化状况和便于对燃烧嘴观察和调节,应在胸墙上设置一定数量可开闭的观察孔。
六、烟道从熔窑通到换热器的烟气,先经水平烟道,再过垂直烟道进入换热器。
水平烟道的截面尺寸,通常按1—2m/s的烟气流速来选取,高度宜大于宽度。
垂直烟道截面又略大于水平烟道截面。
烟道耐火材料的侵蚀通常是很严重的。
这不仅由于排出气体的速度快,而且还由于烟气中夹带有配合料粉尘。
所以在水平烟道入口处底面,使用质量好的致密铬砖,稍后部位才用致密锆砖,再往后的底面、侧墙、磁砖则使用标准铬砖或电熔AZS砖。
垂直烟道与换热器接口砖采用铬刚玉砖。
七、通路结构设计通路的作用是接受从熔窑流液洞或挡砖下通道流过来的玻璃,逐渐降温、恒温,并使之达到合适的成型温度。
尽管通路和熔窑两者实际是相连的,但通路的操作和控制完全与熔窑分开。
并在多段通路的情况下,每段也都要单独控制,以保证满足拉丝所必须的成型温度。
通常习惯称与熔窑相连接的通路部分为主通路;装有拉丝漏板的通路称为成型通路或作业通路,而从通路到各段作业通路间的连接通道称为过渡通路。
为了有助于玻璃液的均化和温度调制,不少专业人士认为主通路宜长,如5—8m,甚至更长些。
而过渡通路的长度以方便拉丝作业为原则,一般取4.5—5.5m。
通路深度:主通路液深自流液洞后分几个台阶逐渐减低,最后一个台阶的液深为100—160mm,常在该台阶前再设置一块铂铑合金包皮的挡砖,挡砖浸入玻璃50—80mm(也有在挡砖前设玻璃液溢流装置,可放掉上层B2O3挥发量较大的那层玻璃液)。
过渡通路液深在100—160mm间。
成型通路的液深与拉丝作业区玻璃的温度有关,目前常设计为100—110mm。