生产过程检验流程
生产过程检验流程
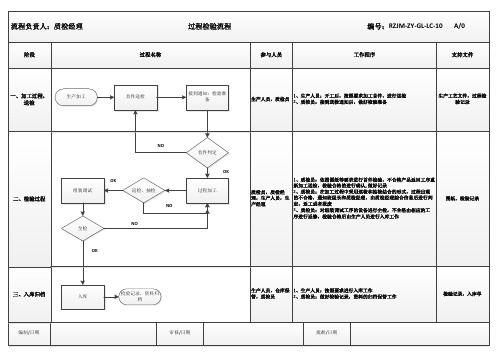
流程负责人:质检经理
阶段
一、加工过程, 送检
生产加工
过程名称
过程检验流程
参与人员
编号:RZJM-ZY-GL-LC-10 A/0
工作程序
支持文件
首件送检
接到通知:检验准 备
生产人员,质检员
1、生产人员:开工后,按照要求加工首件,进行送检 2、质检员:接到送检通知后,做好检验准备
生产工艺文件,过程检 验记录
3、质检员:对组装调试工序的设备进行全检,不合格由相应的工 序进行返修,检验合格后由生产人员进行入库工作
图纸,检验记录
三、入库归档
入库
检验记录,资料归 档
编制/日期
审核/日期
生产人员,仓库保 1、生产人员:按照要求进行入库工作
管,质检员
2、质检员:做好检验记录,资料的归档保管工作
批准/日期
检验记录பைடு நூலகம்入库单
二、检验过程
NO
组装调试 全检
OK 巡检,抽检 NO
NO
OK
首件判定 OK
过程加工
质检员,质检经 理,生产人员,生 产经理
1、质检员:依据图纸等要求进行首件检验,不合格产品返回工序重 新加工送检,检验合格的进行确认,做好记录 2、质检员:在加工过程中采用巡检和抽检结合的形式,过程出现 的不合格,通知班组长和质检经理,由质检经理综合信息后进行判 定,返工或者报废
过程检验流程
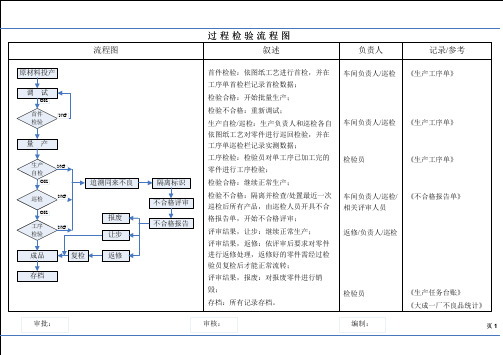
负责人
车间负责人/巡检
记录/参考
《生产工序单》
首件 检验
车间负责人/巡检
《生产工序单》
量
产
NG
生产 自检
OK
检验员
《生产工序单》
零件进行工序检验; 追溯同来不良 隔离标识 不合格评审 报废 不合格报告 检验合格:继续正常生产; 检验不合格:隔离并检查/处置最近一次 巡检后所有产品,由巡检人员开具不合 格报告单,开始不合格评审; 评审结果,让步:继续正常生产; 评审结果,返修:依评审后要求对零件 进行返修处理,返修好的零件需经过检 验员复检后才能正常流转; 评审结果,报废:对报废零件进行销 毁; 存档:所有记录存档。 检验员 《生产任务台账》 《大成一厂不良品统计》 编制:
页1
巡检
OK
NG
车间负责人/巡检/ 相关评审人员 返修/负责人/巡检
《不合格报告单》
工序 检验
NG
ห้องสมุดไป่ตู้
让步 复检 返修
成品 存档
审批:
审核:
1
过程检验流程图
流程图
原材料投产 调 试
OK NG
叙述
首件检验:依图纸工艺进行首检,并在 工序单首检栏记录首检数据; 检验合格:开始批量生产; 检验不合格:重新调试; 生产自检/巡检:生产负责人和巡检各自 依图纸工艺对零件进行巡回检验,并在 工序单巡检栏记录实测数据; 工序检验:检验员对单工序已加工完的
生产过程检验流程
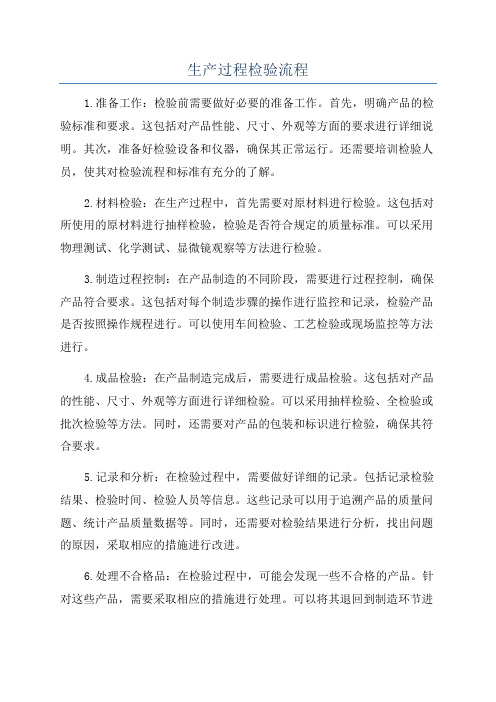
生产过程检验流程1.准备工作:检验前需要做好必要的准备工作。
首先,明确产品的检验标准和要求。
这包括对产品性能、尺寸、外观等方面的要求进行详细说明。
其次,准备好检验设备和仪器,确保其正常运行。
还需要培训检验人员,使其对检验流程和标准有充分的了解。
2.材料检验:在生产过程中,首先需要对原材料进行检验。
这包括对所使用的原材料进行抽样检验,检验是否符合规定的质量标准。
可以采用物理测试、化学测试、显微镜观察等方法进行检验。
3.制造过程控制:在产品制造的不同阶段,需要进行过程控制,确保产品符合要求。
这包括对每个制造步骤的操作进行监控和记录,检验产品是否按照操作规程进行。
可以使用车间检验、工艺检验或现场监控等方法进行。
4.成品检验:在产品制造完成后,需要进行成品检验。
这包括对产品的性能、尺寸、外观等方面进行详细检验。
可以采用抽样检验、全检验或批次检验等方法。
同时,还需要对产品的包装和标识进行检验,确保其符合要求。
5.记录和分析:在检验过程中,需要做好详细的记录。
包括记录检验结果、检验时间、检验人员等信息。
这些记录可以用于追溯产品的质量问题、统计产品质量数据等。
同时,还需要对检验结果进行分析,找出问题的原因,采取相应的措施进行改进。
6.处理不合格品:在检验过程中,可能会发现一些不合格的产品。
针对这些产品,需要采取相应的措施进行处理。
可以将其退回到制造环节进行修复或调整,也可以将其报废或重新制造。
在处理过程中,需要确保对不合格品进行合理的标识和管理,以防止其误用或混淆。
7.客户反馈和改进:生产过程检验流程还包括对客户反馈的处理和产品质量的改进。
这包括对客户投诉进行分析和处理,及时采取措施进行纠正和改进。
同时,还需要对生产过程进行评估和改进,通过引入先进的工艺和技术,提高产品质量和生产效率。
总结起来,生产过程检验流程是确保产品质量的一系列流程和步骤。
通过对原材料、制造过程和成品的检验,记录和分析检验结果,并及时处理不合格品,可以确保产品质量符合要求,达到预定的标准和要求。
生产过程的质量检验

生产过程的质量检验:1、各生产环节的检验人员,应按产品图纸,技术标准和工艺规程的要求进行检验,合格产品,由检验人员签章后随《产品工序检验流程卡》流入下道工序,不合格产品开具《不合格品通知单》交品保部办手续处理。
检验前,检验员须先做到了解产品,了解工序,确定责任区内的检验量,灵活检验方式。
2、各生产环节的检验,均须强调“首检”,加强“巡检”,严格“完工检”,操作者“自检”。
(1)、首检:凡加工改变后的首件,均须进行检查,首件检查应由操作者自检合格后交首检,首检合格,检验员在《产品工序流程卡》及检验记录本上签字或盖首检章,方准成批加工生产,检验员应对首检后的零件负责。
(2)、巡检:在生产过程中反复进行、检验员每班至少巡检两次,做好巡检记录,并对巡检结果的零件负责。
巡检时必须同时检查作业员是否按工艺要求作业。
(3)、完工检:工序终结,零件去尽毛刺、铁屑、油污后进行。
检验时应作好检验记录,主要零件的关键尺寸按检测记录要求进行。
一般零件(或一般项目)抽检不少于10%,抽样检验时如发现不合格品,应加倍抽样复查,若仍不合格则退回生产车间自检处理,重新交验;否则,检验员可以拒检。
(4)、自检:操作者对自己加工的产品进行自我检验,起到自我监督的作用。
对不合格的产品要随即做好标识,分别隔离。
交检验员复验后处理。
3、凡跨部门加工的工序(零件)须凭加工部门检验人员在《产品工序流程卡》上签字,否则,下道工序可以拒检。
进货检验是工厂制止不合格物料进入生产环节的首要控制点。
(IncomingQualityCo ntrol)①进料检验项目及方法:a.外观:一般用目视、手感、对比样品进行验证;b.尺寸:一般用卡尺、千分尺等量具验证;c.特性:如物理的、化学的、机械的特性,一般用检测仪器和特定方法来验证。
②进料检验方法:一般是指对物料入仓后到成品入库前各阶段的生产活动的品质控制,即Inprocess QualityControl。
生产过程检验流程图

生产日报表/异 常联络单
OQC抽检
OK 入库 生产部/ 仓库
将已入箱的产品的工单 在ERP系统中办理入库 申请,仓管员核对无误 后封箱入库 ERP入库单
按SIP,图纸对产品进行 检验,NG退给生产部并发 出《异常联络查记录表,首 检检验报告,异常联 络单
生产部
按SOP,工单,首检样板 进行生产
生产日报表
NG 巡检
品质部
依QC工程图,控制计划, SIP进行巡检,按控制计 划对特殊性进行监控,NG 联络生产部进行改善,OK 进行有效记录
生产过程检验流程图
流程 责任部门 流程说明
人员,设备,物料,作业 指导文件,环境的准备与 确认。
文件/记录
工单,BOM表,物料 领用清单,员工技能 矩阵图,设备点检表
生产前 准备
生产部
首件制作 NG 首检 OK 生产
生产部
按生产计划,SOP要求进行 调机,试装,做首件
试样检查记录表,生 产订单
品质部
巡检记录表,异常联 络单
OK NG LQC终检 OK NG 品质部
按工单及出货计划对待检 区域的产品进行抽样检验 确认,NG开出不合格检验 报告并开出《异常联络 单》通知生产部进行改善 检验记录表,异常联 络单
生产部
按工单,SOP,SIP检验包 装,标识,密封,入箱转 待检区,针对不合格开出 异常联络单
生产过程检验管理流程
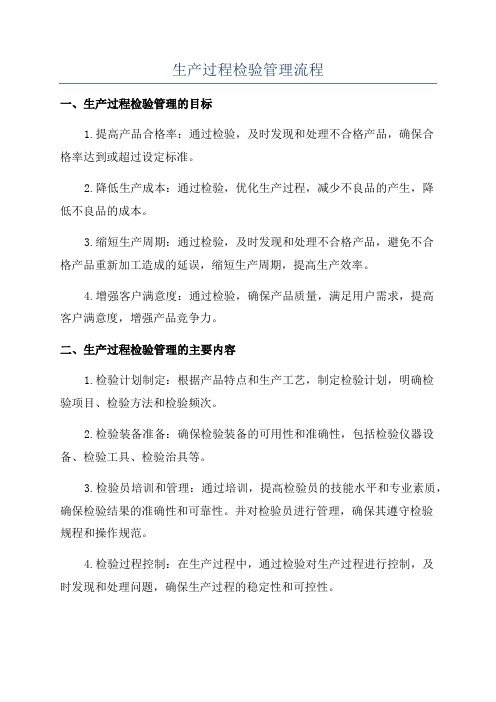
生产过程检验管理流程一、生产过程检验管理的目标1.提高产品合格率:通过检验,及时发现和处理不合格产品,确保合格率达到或超过设定标准。
2.降低生产成本:通过检验,优化生产过程,减少不良品的产生,降低不良品的成本。
3.缩短生产周期:通过检验,及时发现和处理不合格产品,避免不合格产品重新加工造成的延误,缩短生产周期,提高生产效率。
4.增强客户满意度:通过检验,确保产品质量,满足用户需求,提高客户满意度,增强产品竞争力。
二、生产过程检验管理的主要内容1.检验计划制定:根据产品特点和生产工艺,制定检验计划,明确检验项目、检验方法和检验频次。
2.检验装备准备:确保检验装备的可用性和准确性,包括检验仪器设备、检验工具、检验治具等。
3.检验员培训和管理:通过培训,提高检验员的技能水平和专业素质,确保检验结果的准确性和可靠性。
并对检验员进行管理,确保其遵守检验规程和操作规范。
4.检验过程控制:在生产过程中,通过检验对生产过程进行控制,及时发现和处理问题,确保生产过程的稳定性和可控性。
5.不合格品处理:对于不合格产品,及时做好处理,查找不合格的原因,采取纠正措施,防止不合格品流入下道工序或出厂。
6.反馈和改进:对于检验结果,及时进行反馈,并进行问题分析,提出改进措施,避免类似问题的再次发生。
三、生产过程检验管理的流程1.检验计划制定:根据产品特点和生产工艺,制定检验计划,确定检验项目、检验方法和检验频次。
2.检验装备准备:确保检验装备的可用性和准确性,校准检验仪器设备,配备检验工具和检验治具。
3.检验员培训和管理:对检验员进行培训,提高其技能水平和专业素质,建立检验员档案,并对其进行管理和考核。
4.检验过程控制:在生产过程中,及时采集产品样本,进行检验,对生产过程进行控制,避免不合格品流入下道工序。
5.不合格品处理:对不合格产品,及时进行处理,查找不合格的原因,采取纠正措施,避免不合格品流入下道工序或出厂。
6.检验结果的反馈和改进:对检验结果进行反馈,并进行问题分析,提出改进措施,避免类似问题的再次发生。
生产过程检测流程

生产过程检测流程
保证各工序的不合格半成品不得流入下道工序,防止对不合格半成品的继续加工和出现成批半成品不合格,确保正常的生产秩序。
由于过程检验是按生产工艺流程和操作规程进行检验,因而能起到验证工艺和保证工艺规程贯彻执行的作用。
过程检验通常有首件检验、巡回检验(或流动检验)和完工检验三种形式。
1、首件检验。
首件检验是在生产开始时(上班或换班)或工序因素调整后(调整工艺、工装、设备等)对制造的第一件或前几件产品进行的检验。
目的是尽早发现过程中的系统因素,防止产品成批报废。
在首件检验中,可实施“首件三检制”,即操作人员自检、班组长检验和专职检验员检验。
首件不合格时,应进行质置分析,采取纠正措施,直到再次首件检验后才能成批生产。
检验员对检验合格的首件应按规定进行标识,并保留到该批产品完工。
2、巡回检验。
巡回检验是检验员在生产现场按一定的时间间隔对有关工序的产品质量和加工工艺进行的监督检验。
巡回检验员在过程检验中应进行的检验项目和职责是:
①巡回检验的重点是关键工序,检验员应熟悉所负责任检验范围内工序质量控制点的质量要求、检测方法和加工工艺,并对加工后产品是否符合质量要求检验指导书规定的要求及负有监督工艺执行情
况的责任。
②做好检验后的合格品、不合格品(返修品)、废品的专门存放处理工作。
3、完工检验。
完工检验是对一个工序一批完工的产品进行全面的检验。
完工检验的目的是挑出不合格品,使合格品继续流人下道工序。
注:生产过程检验不是单纯的质量把关,应与质量控制、质量分析、质量改进、工艺监督等相结合,重点做好主导质量要素的效果检查。
生产过程检验规程
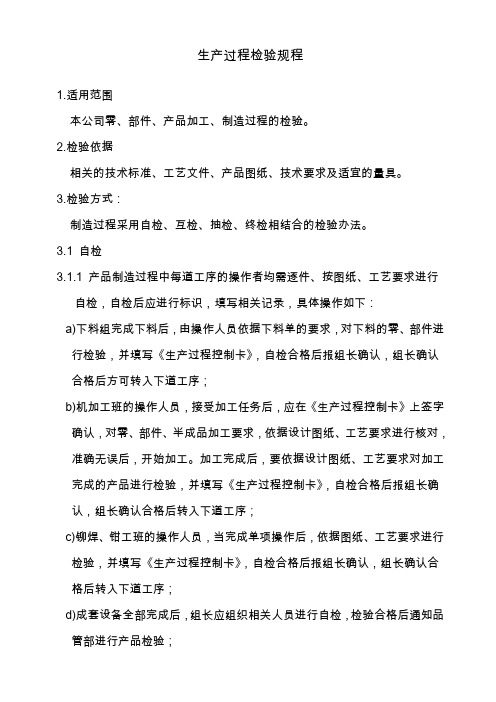
生产过程检验规程1.适用范围本公司零、部件、产品加工、制造过程的检验。
2.检验依据相关的技术标准、工艺文件、产品图纸、技术要求及适宜的量具。
3.检验方式:制造过程采用自检、互检、抽检、终检相结合的检验办法。
3.1 自检3.1.1 产品制造过程中每道工序的操作者均需逐件、按图纸、工艺要求进行自检,自检后应进行标识,填写相关记录,具体操作如下:a)下料组完成下料后,由操作人员依据下料单的要求,对下料的零、部件进行检验,并填写《生产过程控制卡》,自检合格后报组长确认,组长确认合格后方可转入下道工序;b)机加工班的操作人员,接受加工任务后,应在《生产过程控制卡》上签字确认,对零、部件、半成品加工要求,依据设计图纸、工艺要求进行核对,准确无误后,开始加工。
加工完成后,要依据设计图纸、工艺要求对加工完成的产品进行检验,并填写《生产过程控制卡》,自检合格后报组长确认,组长确认合格后转入下道工序;c)铆焊、钳工班的操作人员,当完成单项操作后,依据图纸、工艺要求进行检验,并填写《生产过程控制卡》,自检合格后报组长确认,组长确认合格后转入下道工序;d)成套设备全部完成后,组长应组织相关人员进行自检,检验合格后通知品管部进行产品检验;e)《生产过程控制卡》由各工序操作人员填写,组长确认,每日上报。
3.2 互检各生产班组之间或下道工序接收转序的产品时,由接收人员对转序产品进行互检,以验证自检结果的准确性,避免自检出现遗漏,并在《生产过程控制卡》互检拦内签字确认。
3.3 抽检各生产班组在制造生产过程中,由品管部安排检验员对各工序产品(零、部件)实行随机抽查,抽检后填写《过程产品检验记录》,发现问题及时反馈。
3.4 终检3.4.1 加工制造生产完成的产品(含组装完成的成套设备)在入库前,必须经检验员进行产品最终检验,并对产品进行标识(粘贴合格标签),填写《产品检验记录》。
检验合格后方可办理入库手续。
3.5 关键部件由工程技术部根据产品特性的需要进行界定,并在图纸上进行标识。
生产检验流程图
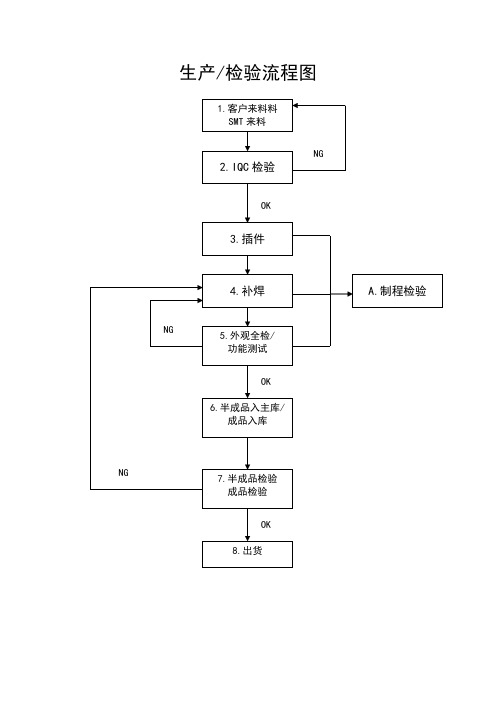
生产/检验流程图解释:1.客户来料/SMT来料客户来料:客人提供订单所需材料SMT来料:SMT车间所交PACB半成品(包括贴片 AI)2.IQC检验IQC对客户来料及SMT车间所交PCABA半成品进行检验。
检验OK则上线使用,检验NG时则开出IQC来料异常单,知会客户或者SMT车间处理。
3.插件制造部门(插件拉)根据客户样品/BOM清单/IPQC确认首件进行插件动作。
4.补焊制造部门(补焊拉)按相关客户要求,公司内部品质要求进行补焊动作。
5.外观总检/功能测试制造部门(补焊拉)按相关客户要求,公司内部品质要求进行外观总检/功能测试动作。
A.制程检验是指产品从物料投入生产到产品最终包装过程的品质控制。
在这生产过程中,产线拉长或者制程检验人员,当产品不良率超过3%时,需立即开出制程品质异常单,知会相关单位进行原因分析并提出可行性改善对策。
6.半成品入库/成品入库半成品/成品在经过以上生产流程及品质检验流程OK后。
可安排入库动作。
步骤:一、产线开出半成品/成品入库单,并在产品外箱上贴上标签(包括成品订单号/机种/批量/实际数量/日期等等相关讯息)。
二、将半成品/成品拖至品保指定待验区。
三、将半成品/成品入库单转交给品保相关检验人员(OQC检验员)。
7.半成品/成品检验品保OQC检验人员根据制造部门提供的半成品/成品入库单,AQL抽样水准/半成品/成品检验规范进行检验。
检验OK则在半成品/成品入库单上签字确认加盖品保检验PASS章,并在产品包装箱上贴附PASS标签。
检验NG时,则及时开出成品检验异常单。
知会制造部门确认动作,如是功能时,转工程分析具体不良原因。
制造部门确认相关不良品及不良现象后,需进行重工动作。
IPQC(制程检验人员)追综重工效果8.出货半成品/成品检验OK后,按客户需求日期出货。
核准:审核:制定:相关人员签字:。
过程检验规程

过程检验规程过程检验规程一、目的和范围过程检验是指对生产过程中各个环节进行检验和监控,确保产品质量符合要求的一种管理方法。
本规程的目的是明确过程检验的要求和流程,以提高产品质量,保证生产过程的稳定性。
本规程适用于所有需要进行过程检验的生产环节。
二、术语和定义1. 过程检验:指对生产过程中各个环节进行检验和监控。
2. 过程参数:指影响产品质量的各个环节中的关键参数。
3. 过程控制:指对生产过程中各个环节进行监控和调整,以确保产品质量达到要求。
三、工作责任1. 生产负责人:负责制定和实施过程检验规程,并对过程检验的准确性和及时性负责。
2. 检验人员:负责实施过程检验,并对检验结果的准确性和可靠性负责。
3. 设备维护人员:负责检验设备的维护和保养工作,确保设备的正常运转。
四、过程检验流程1. 制定检验计划:根据生产需要,确定需要进行过程检验的环节和参数,并制定相应的检验计划。
2. 检验设备准备:检验人员根据检验计划,准备好相应的检验设备,并确保设备的正常运作。
3. 进行检验:根据检验计划,检验人员对各个环节的过程参数进行检验,并记录检验结果。
所有检验工作要求严格按照相关操作规程进行,确保检验数据的准确性和可靠性。
4. 检验结果处理:根据检验结果,判断生产过程是否符合要求,如果发现异常,及时采取相应的措施进行调整。
5. 制定改进措施:根据检验结果和判断,制定相应的改进措施,以提高生产过程的稳定性和产品的质量。
五、过程控制1. 根据过程检验的结果,对生产过程进行控制,确保产品质量的稳定性。
2. 对于过程参数变化较大的环节,应及时采取调整措施,以保证产品质量在可控范围内。
六、记录和报告1. 检验人员要对每次检验的过程参数进行记录,并保留相应的数据和报告。
2. 检验计划和检验结果要及时向相关部门进行报告,以便制定相应的改进和调整措施。
七、设备维护1. 设备维护人员根据设备的使用情况,制定相应的维护计划,并及时进行设备的维护和保养工作。
过程检验控制流程

责任部门
工作流程
工作标准
考核细则
操作人员
操作人员
操作人员
班组长
分厂
操作人员
班组长
操作人员
班组长
分厂
1.生产人员依据产品图纸、“技术通知单”、封样件、检验标准、作业指导书等产品要求,调试机器,开始试生产。
2.操作人员按照产品检验指导书、图纸、“技术通知单”、封样件等,对生产出来的前三片产品进行检验,合格后填写首检记录,通知班长进行确认合格后方可量产,若不合格,需重新调试,直至符合要求后方可进行量产。
3.若出现更换产品型号、产品异常调整后、5M1E变更的情况时,重新进行首件检验。
4.生产过程中操作人员,按首检项目2小时/次进行过程检验,发现不良品执行《生产过程不合格品处理流程》,并保持相应的检验记录。
5.每道工序的班长须对本班生产出的半成品/成品按《成品抽样方案》进行抽检,抽检确认合格后才能转入下道工序或临时库。
6.最后一道工序班组长依据产品检验标准对成品进行抽检,合格入库;若不合格,责任班组执行《生产过程不合格品处理流程》,并填写“成品入库检验记录”。
7.在所有的规定程序或检验完成之前,不得将产品放行或投入使用,必要时需得到分管副总或顾客的批准和许可,执行《制程不合格品处理流程》的规定。
8.分厂负责人或质量负责人,每周组织相关人员≥1次,对产品的过程控制、成品质量进行监督抽查。
9.分厂质量负责人每周、月对品质进行数据统计、分析,提出改进,分厂负责人审核。
未完成项,根据实际情况,考核20-50元/次/项。
过程输出:作业指导书、产品检验指导书、通用外观标准、首件确认单、检验记录、成品入库检验记录。
生产过程控制和过程检验程序

生产过程控制和过程检验程序l 目的对生产过程中直接或间接影响产品质量的各种因素进行有效控制,以确保获证产品满足顾客的要求和期望及认证的要求。
2 范围适用于对产品的形成、过程的确认、产品的防护及放行、产品使用已交付后的活动、生产过程中对环境条件的要求、生产设备的维护保养等。
3 职责3.1 生产部负责指导车间进行生产和过程控制,负责生产设备的维护保养,对关键工序应编制作业指导书,负责产品标识的维护和产品的防护,对现场工作环境进行监督、检查;3.2 技质部负责编制相应的工艺规程;3.3 技质部负责过程检验的实施;3.4 综合部负责生产过程中各种物资的采购。
4 工作程序4.1 过程确认4.1.1 生产流程图(见附页)4.1.2 关键生产工序的识别在以下情况时,工厂应对其作为关键/特殊工序予以对待:A)工序的结果不能通过其后的检验和试验完全验证,或者加工后无法测量或需实施破坏性测量才能得出结果;B)工序对最终产品的安全质量、主要性能有重大影响。
4.1.3 本公司生产的关键过程是焊接、填充胶合与压制、阻燃处理、表面处理等工序。
对这些过程应进行确认,证实它们的过程能力。
适用时,这些确认的安排应包括:A)过程鉴定,证实所使用的过程方法是否符合要求并有效实施;B)对所使用的设备、设备能力(包括精确度、安全性、可用性等要求)及维护保养有严格要求(具体见设备操作规程),并保存维护保养记录,填写《特殊过程确认表》,同时相关生产人员要进行岗位培训、考核,持证上岗;C)编制与之相适宜的作业指导书。
4.2 产品生产过程中对工作环境的要求根据公司实际,工作环境主要包括配置适用的厂房、消防器材,保持适宜的温湿度和安全、噪声、振动、洁净度等。
生产部和各车间要识别并管理为实现产品符合性所需的工作环境中人和物的因素,根据生产作业需要,创造良好的工作环境,包括:A.配置适用的厂房并根据生产需要适当装修,防止暴晒,风雨侵入和潮湿;B.配置必要的通风、消防器材,保持适宜环境卫生、安全;C.生产部及仓库对各类设施和物资实行定置管理,提高工作效率;D.确保员工生产符合劳动法规的要求。
2、生产过程检验流程
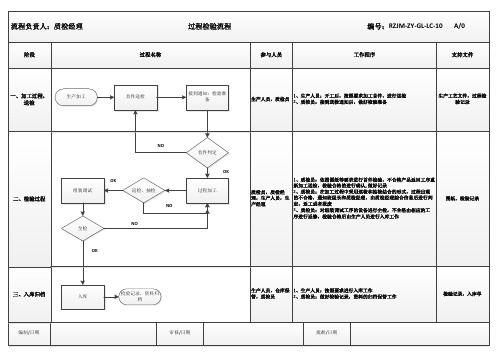
三、入库归档
入库
检验记录,资料归 档
编制/日期
审核/日期
生产人员,仓库保 1、生产人员:按照要求进行入库工作
管,质检员
2、质检员:做好检验记录,资料的归档保管工作
批准/日期
检验记录,入库单
流程负责人:质检经理
阶段
一、加工过程, 送检
生产加工
过程名称
过程检验流程
参与人员
编号:RZJM-ZY-GL-LC-10 A/0
工作程序
支持文件
首件送检
接到通知:检验准 备
生产人员,质检员
1、生产人员:开工后,按照要求加工首件,进行送检 2、质检员:接到送检通知后,做好检验准备
生产工艺文件,过程检 验记录
二、检验过程
NO
组装调试 全检
OK 巡检,抽检 NO
NO
OK
首件判定 OK
过程加工
质检员,质检经 理,生产人员,生 产经理
1、质检员:依据图纸等要求进行首件检验,不合格产品返回工序重 新加工送检,检验合格的进行确认,做好记录 2、质检员:在加工过程中采用巡检和抽检结合的形式,过程出现 的不合格,通知班组长和质检经理,由质检经理综合信息后进行判 定,返工或者报废
生产过程的质量检验

生产过程的质量检验:1、各生产环节的检验人员,应按产品图纸,技术标准和工艺规程的要求进行检验,合格产品,由检验人员签章后随《产品工序检验流程卡》流入下道工序,不合格产品开具《不合格品通知单》交品保部办手续处理。
检验前,检验员须先做到了解产品,了解工序,确定责任区内的检验量,灵活检验方式。
2、各生产环节的检验,均须强调“首检”,加强“巡检”,严格“完工检”,操作者“自检”。
(1)、首检:凡加工改变后的首件,均须进行检查,首件检查应由操作者自检合格后交首检,首检合格,检验员在《产品工序流程卡》及检验记录本上签字或盖首检章,方准成批加工生产,检验员应对首检后的零件负责。
(2)、巡检:在生产过程中反复进行、检验员每班至少巡检两次,做好巡检记录,并对巡检结果的零件负责。
巡检时必须同时检查作业员是否按工艺要求作业。
(3)、完工检:工序终结,零件去尽毛刺、铁屑、油污后进行。
检验时应作好检验记录,主要零件的关键尺寸按检测记录要求进行。
一般零件(或一般项目)抽检不少于10%,抽样检验时如发现不合格品,应加倍抽样复查,若仍不合格则退回生产车间自检处理,重新交验;否则,检验员可以拒检。
(4)、自检:操作者对自己加工的产品进行自我检验,起到自我监督的作用。
对不合格的产品要随即做好标识,分别隔离。
交检验员复验后处理。
3、凡跨部门加工的工序(零件)须凭加工部门检验人员在《产品工序流程卡》上签字,否则,下道工序可以拒检。
进货检验是工厂制止不合格物料进入生产环节的首要控制点。
(IncomingQualityCo ntrol)①进料检验项目及方法:a.外观:一般用目视、手感、对比样品进行验证;b.尺寸:一般用卡尺、千分尺等量具验证;c.特性:如物理的、化学的、机械的特性,一般用检测仪器和特定方法来验证。
②进料检验方法:一般是指对物料入仓后到成品入库前各阶段的生产活动的品质控制,即Inprocess QualityControl。
生产过程及过程检验程序
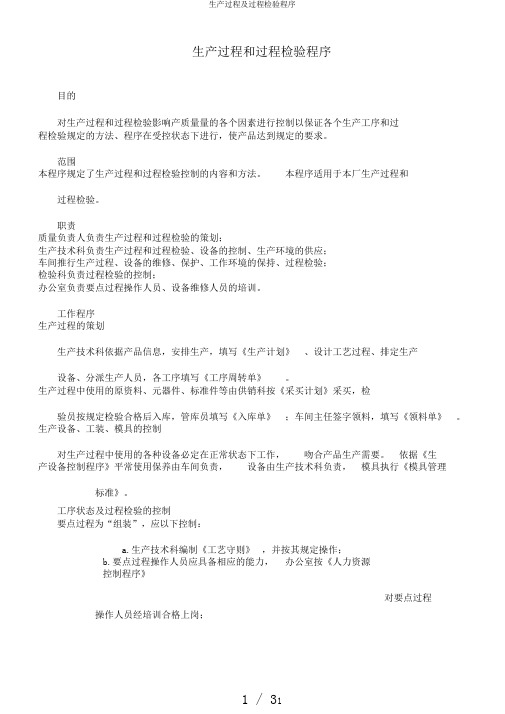
生产过程和过程检验程序目的对生产过程和过程检验影响产质量量的各个因素进行控制以保证各个生产工序和过程检验规定的方法、程序在受控状态下进行,使产品达到规定的要求。
范围本程序规定了生产过程和过程检验控制的内容和方法。
本程序适用于本厂生产过程和过程检验。
职责质量负责人负责生产过程和过程检验的策划;生产技术科负责生产过程和过程检验、设备的控制、生产环境的供应;车间推行生产过程、设备的维修、保护、工作环境的保持、过程检验;检验科负责过程检验的控制;办公室负责要点过程操作人员、设备维修人员的培训。
工作程序生产过程的策划生产技术科依据产品信息,安排生产,填写《生产计划》、设计工艺过程、排定生产设备、分派生产人员,各工序填写《工序周转单》。
生产过程中使用的原资料、元器件、标准件等由供销科按《采买计划》采买,检验员按规定检验合格后入库,管库员填写《入库单》;车间主任签字领料,填写《领料单》。
生产设备、工装、模具的控制对生产过程中使用的各种设备必定在正常状态下工作,吻合产品生产需要。
依据《生产设备控制程序》平常使用保养由车间负责,设备由生产技术科负责,模具执行《模具管理标准》。
工序状态及过程检验的控制要点过程为“组装”,应以下控制:a.生产技术科编制《工艺守则》,并按其规定操作;b.要点过程操作人员应具备相应的能力,办公室按《人力资源控制程序》对要点过程操作人员经培训合格上岗;c.对要点过程规定了控制参数,表现在《工艺守则》中,车间主任负责工序状态的控制,岗位操作人员负责产品自检和互检,质检员负责过程检验;d.设备、工装应吻合生产要求,保持圆满,本厂建立了《生产设备控制程序》;有吻合要求的检测设备并推行检验;为生产过程控制供应凭据的记录,包括:“生产计划”、“工序周转单”、各工序“自检记录”、“产品检验单”。
g.检验科负责产品工序过程检测和成品检测,负责填写《产品检验单》并保持,负责车间使用检测工具的检定、校准。
对一般过程也推行了过程监控,每个工序均进行自检、互检、专检填写《剪板工序自检记录》、《冲压工序自检记录》、《折弯工序自检记录》、《组焊工序自检记录》、《母线制作工序自检记录》。
生产过程检验流程图
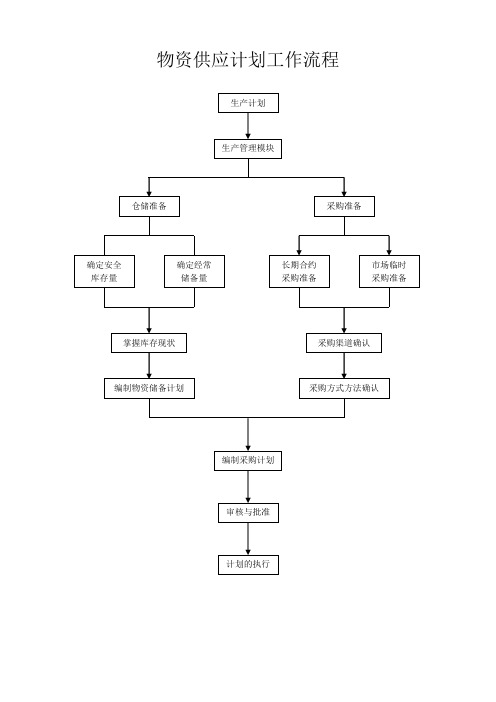
物资供应计划工作流程
生产过程组织设计流程
生产过程各职能模块配合流程
生产制程控制流程
退
货
返
工
返
工
返
工
劳动定额管理程序
说明:完善劳动生产定额管理,对于一车间这样的装备制造型车间尤为重要。
劳动工时消耗构成图
全部时间消耗
定额时间
非定额时间
作业时间
照管工作地时间
休息和生理需要时间
准备和结束时间
基本时间
辅助时间
机动时间
机手动时间
手动时间
非生产工作时间
非工人造成的损失时间
工人造成的损失时间
返工处理作业流程图
外协计划编制流程图
设备管理流程与责任图
)
设备使用的管理程序
原材料验收管理流程
成品出货质检流程图
产品生产质量控制流程
生产制程质量检验流程图
进料过程检验操作流程
进货检验不合格处理程序
仓储管理工作的基本流程
生产废料入库处理管理流程
包装物及其它废料处理工作流程图
企业物资消耗定额构成图
物资消耗定额制定流程
采购作业流程
物资请购作业流程。