注塑模具设计时关于流道的着重点
1出8塑胶模具流道设计
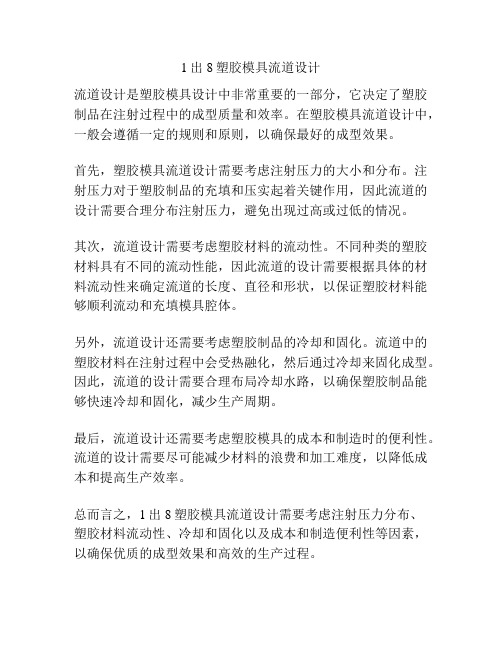
1出8塑胶模具流道设计
流道设计是塑胶模具设计中非常重要的一部分,它决定了塑胶制品在注射过程中的成型质量和效率。
在塑胶模具流道设计中,一般会遵循一定的规则和原则,以确保最好的成型效果。
首先,塑胶模具流道设计需要考虑注射压力的大小和分布。
注射压力对于塑胶制品的充填和压实起着关键作用,因此流道的设计需要合理分布注射压力,避免出现过高或过低的情况。
其次,流道设计需要考虑塑胶材料的流动性。
不同种类的塑胶材料具有不同的流动性能,因此流道的设计需要根据具体的材料流动性来确定流道的长度、直径和形状,以保证塑胶材料能够顺利流动和充填模具腔体。
另外,流道设计还需要考虑塑胶制品的冷却和固化。
流道中的塑胶材料在注射过程中会受热融化,然后通过冷却来固化成型。
因此,流道的设计需要合理布局冷却水路,以确保塑胶制品能够快速冷却和固化,减少生产周期。
最后,流道设计还需要考虑塑胶模具的成本和制造时的便利性。
流道的设计需要尽可能减少材料的浪费和加工难度,以降低成本和提高生产效率。
总而言之,1出8塑胶模具流道设计需要考虑注射压力分布、
塑胶材料流动性、冷却和固化以及成本和制造便利性等因素,以确保优质的成型效果和高效的生产过程。
注塑模具热流道
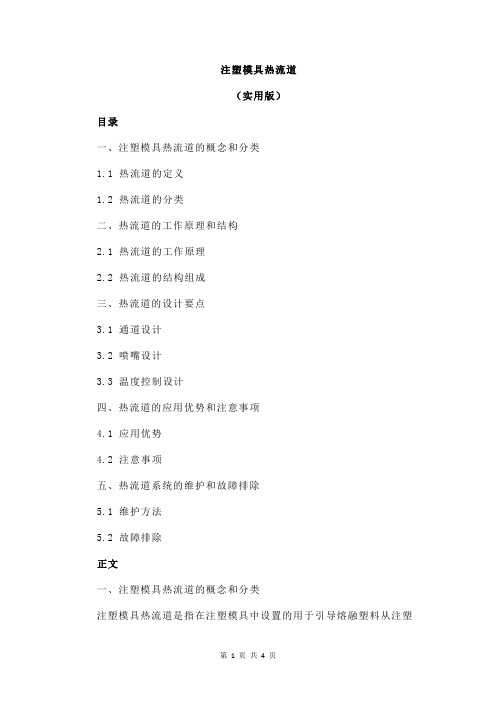
注塑模具热流道(实用版)目录一、注塑模具热流道的概念和分类1.1 热流道的定义1.2 热流道的分类二、热流道的工作原理和结构2.1 热流道的工作原理2.2 热流道的结构组成三、热流道的设计要点3.1 通道设计3.2 喷嘴设计3.3 温度控制设计四、热流道的应用优势和注意事项4.1 应用优势4.2 注意事项五、热流道系统的维护和故障排除5.1 维护方法5.2 故障排除正文一、注塑模具热流道的概念和分类注塑模具热流道是指在注塑模具中设置的用于引导熔融塑料从注塑机喷嘴到达模具腔体的通道。
热流道技术是注塑成型工艺的重要组成部分,能够提高生产效率、降低生产成本、提高产品质量。
根据热流道的结构和特点,热流道可以分为以下几类:1.1 热流道的定义热流道是一种特殊的注塑模具结构,它通过在模具中设置加热装置,使熔融塑料在进入模具腔体之前保持熔融状态,从而实现连续注塑,提高生产效率。
1.2 热流道的分类热流道可以根据不同的结构特点进行分类,常见的分类如下:(1)单点热流道:只有一个喷嘴的热流道系统,适用于单腔模具。
(2)多点热流道:多个喷嘴的热流道系统,适用于多腔模具。
(3)顺序热流道:按照一定顺序依次开启喷嘴的热流道系统,适用于有特定要求的注塑成型工艺。
二、热流道的工作原理和结构2.1 热流道的工作原理热流道的工作原理是通过在模具内设置加热装置,将熔融塑料从注塑机喷嘴引入模具腔体。
在热流道系统中,熔融塑料在通道内保持熔融状态,从而实现连续注塑。
热流道系统可以根据需要对各个喷嘴进行独立控制,以满足不同生产工艺的要求。
2.2 热流道的结构组成热流道系统主要由以下几部分组成:(1)通道:连接注塑机喷嘴和模具腔体的通道,用于引导熔融塑料流动。
(2)喷嘴:将熔融塑料引入通道的部件,可以根据需要设置多个喷嘴。
(3)加热装置:用于加热通道,保持熔融塑料的熔融状态。
(4)温度控制系统:用于控制加热装置的温度,保证熔融塑料在通道内保持一定的温度。
塑料注射成型中的流道设计优化
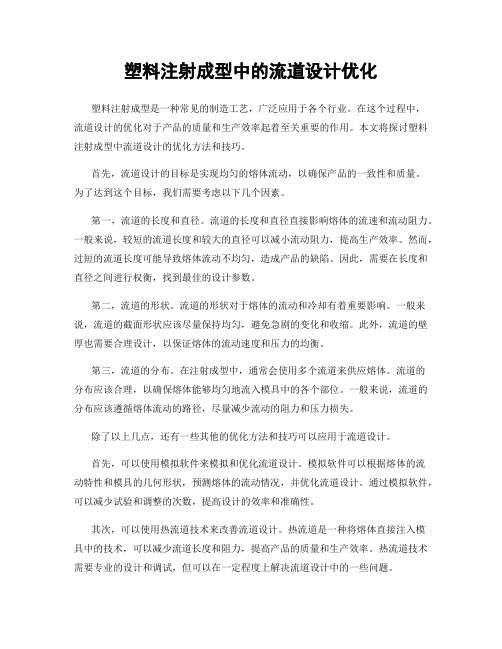
塑料注射成型中的流道设计优化塑料注射成型是一种常见的制造工艺,广泛应用于各个行业。
在这个过程中,流道设计的优化对于产品的质量和生产效率起着至关重要的作用。
本文将探讨塑料注射成型中流道设计的优化方法和技巧。
首先,流道设计的目标是实现均匀的熔体流动,以确保产品的一致性和质量。
为了达到这个目标,我们需要考虑以下几个因素。
第一,流道的长度和直径。
流道的长度和直径直接影响熔体的流速和流动阻力。
一般来说,较短的流道长度和较大的直径可以减小流动阻力,提高生产效率。
然而,过短的流道长度可能导致熔体流动不均匀,造成产品的缺陷。
因此,需要在长度和直径之间进行权衡,找到最佳的设计参数。
第二,流道的形状。
流道的形状对于熔体的流动和冷却有着重要影响。
一般来说,流道的截面形状应该尽量保持均匀,避免急剧的变化和收缩。
此外,流道的壁厚也需要合理设计,以保证熔体的流动速度和压力的均衡。
第三,流道的分布。
在注射成型中,通常会使用多个流道来供应熔体。
流道的分布应该合理,以确保熔体能够均匀地流入模具中的各个部位。
一般来说,流道的分布应该遵循熔体流动的路径,尽量减少流动的阻力和压力损失。
除了以上几点,还有一些其他的优化方法和技巧可以应用于流道设计。
首先,可以使用模拟软件来模拟和优化流道设计。
模拟软件可以根据熔体的流动特性和模具的几何形状,预测熔体的流动情况,并优化流道设计。
通过模拟软件,可以减少试验和调整的次数,提高设计的效率和准确性。
其次,可以使用热流道技术来改善流道设计。
热流道是一种将熔体直接注入模具中的技术,可以减少流道长度和阻力,提高产品的质量和生产效率。
热流道技术需要专业的设计和调试,但可以在一定程度上解决流道设计中的一些问题。
最后,流道设计的优化还需要考虑材料的选择和加工参数的调整。
不同的塑料材料具有不同的流动特性和熔体温度范围,需要根据具体情况来选择合适的材料。
此外,加工参数的调整也可以对流道设计产生影响,例如熔体温度、注射速度和压力等。
注塑模具分流道设计

注塑模具分流道设计
注塑模具分流道设计是指在注塑模具中设计一些分流道,用来分流或者汇流热介质,实现模具内的冷却或加热。
这样可以改善注塑过程中的温度控制,提高产品品质和稳定性,同时缩短生产周期,提高生产效率。
具体来说,注塑模具分流道设计需要考虑以下几个方面:
1. 分流道的数量和布局:需要根据产品尺寸、形状、材料等因素来确定分流道的数量和布局,保证模具内的热介质可以均匀流通,以达到更好的冷却或加热效果。
2. 分流道的尺寸:需要根据模具内部实际情况和冷却或加热要求来确定分流道的尺寸。
通常情况下,分流道的尺寸要比其他通道要大一些,以保证流量足够。
3. 分流道的材料选择:需要选择具有耐腐蚀、耐高温、导热性好等特点的材料,如不锈钢、铜等。
此外,还需要根据实际情况选择包括封口、连接部件等配套材料。
4. 分流道的维护和清洁:模具在生产结束后需要及时清洗,分流道中的堵塞物要及时清理。
同时,对于长期使用的模具,需要定期进行维护,及时更换不可用的部件。
总之,注塑模具分流道设计是一个比较复杂的工程,需要考虑多方面因素。
但如果设计得当,可以大大提高模具的使用寿命和生产效率,为企业创造更大的价值。
(整理)一般性注塑模具对于热流道的要求.
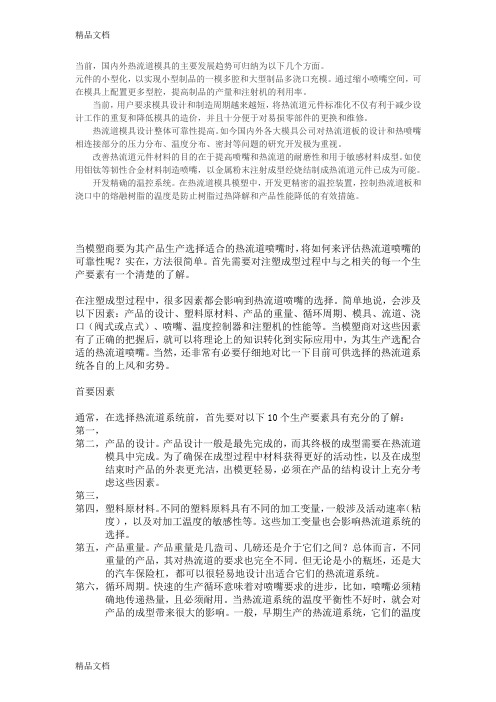
当前,国内外热流道模具的主要发展趋势可归纳为以下几个方面。
元件的小型化,以实现小型制品的一模多腔和大型制品多浇口充模。
通过缩小喷嘴空间,可在模具上配置更多型腔,提高制品的产量和注射机的利用率。
当前,用户要求模具设计和制造周期越来越短,将热流道元件标准化不仅有利于减少设计工作的重复和降低模具的造价,并且十分便于对易损零部件的更换和维修。
热流道模具设计整体可靠性提高。
如今国内外各大模具公司对热流道板的设计和热喷嘴相连接部分的压力分布、温度分布、密封等问题的研究开发极为重视。
改善热流道元件材料的目的在于提高喷嘴和热流道的耐磨性和用于敏感材料成型。
如使用钼钛等韧性合金材料制造喷嘴,以金属粉末注射成型经烧结制成热流道元件已成为可能。
开发精确的温控系统。
在热流道模具模塑中,开发更精密的温控装置,控制热流道板和浇口中的熔融树脂的温度是防止树脂过热降解和产品性能降低的有效措施。
当模塑商要为其产品生产选择适合的热流道喷嘴时,将如何来评估热流道喷嘴的可靠性呢?实在,方法很简单。
首先需要对注塑成型过程中与之相关的每一个生产要素有一个清楚的了解。
在注塑成型过程中,很多因素都会影响到热流道喷嘴的选择。
简单地说,会涉及以下因素:产品的设计、塑料原材料、产品的重量、循环周期、模具、流道、浇口(阀式或点式)、喷嘴、温度控制器和注塑机的性能等。
当模塑商对这些因素有了正确的把握后,就可以将理论上的知识转化到实际应用中,为其生产选配合适的热流道喷嘴。
当然,还非常有必要仔细地对比一下目前可供选择的热流道系统各自的上风和劣势。
首要因素通常,在选择热流道系统前,首先要对以下10个生产要素具有充分的了解:第一,第二,产品的设计。
产品设计一般是最先完成的,而其终极的成型需要在热流道模具中完成。
为了确保在成型过程中材料获得更好的活动性,以及在成型结束时产品的外表更光洁,出模更轻易,必须在产品的结构设计上充分考虑这些因素。
第三,第四,塑料原材料。
塑料模具设计 重点总结(高分子材料专业)2

塑料模具设计重点总结(高分子材料专业)2无流道浇注系统是指在注塑成形的过程中不产生流道凝料的浇注系统。
其原理是采用加热的办法或者绝热的办法,是整个生产周期中从主流道入口起到型腔浇口止的流道中的塑料一直保持熔融状态,因而在开模时,只需取出产品而不必取出浇注系统凝料。
采用绝热的办法的称为绝热流道模具,采用加热的办法的称为热流道模具,目前在应用上以后者为主。
绝热流道注塑模具绝热流道系统是将流道设计得相当粗大,以致流道中心部位的塑料在连续注塑时来不及凝固而始终保持熔融状态,从而让塑料熔体能通过它顺利地进入型腔。
分类:1.单型腔的井坑式喷嘴:又名井式喷嘴,绝热主流道,是最简单的绝热式流道,适用于单型腔。
2.多型腔的绝热流道模具:又称为绝热分流道模具,浇口常见有主流道型浇口,针点浇口等热流道注塑模具热流道模具的优点:1.节省了普通浇注系统流道凝料的回收加工的费用。
2.缩短成形周期,省去脱浇注系统的时间,和有时为了冷却粗大的浇注系统所多耗费的时间。
3.能更有效完成地利用注塑机的注塑能力生产出较大的产品,节省了每次注塑时耗于浇注系统的料。
与三板式模相比由于无需脱浇注系统,所需的开模行程大大减小能生产高度更大的制品。
4.浇注系统粗大且保持最佳的熔融状态,因此充模流动阻力减少,有效补料的时间延长,有利于提高制品质量。
同时由于不需在新料中大量掺入回收的浇口料,也有益于提高制品质量。
热流道模具的缺点:1.开机时要较长时间才能到达稳定操作,因此开机时废品较多。
2.需要操作技能较高的专业人员。
3.模具结构复杂,成本高,需要增添外接温控仪等辅助设备。
4.易出现熔体泄露、加热元件故障等较敏感问题,需精心维护,否则产生热降解等不良现象。
具有以下性质的塑料,适宜采用热流道模具:1.加工温度的范围宽,熔体粘度随温度变化小的塑料。
2.对压力敏感,不加压力时不流延,但施以很小压力即容易流动的塑料熔体。
3.热变形温度较高。
制品在高温下而能快速固化,并能快速脱出的塑件。
流道尺寸设计
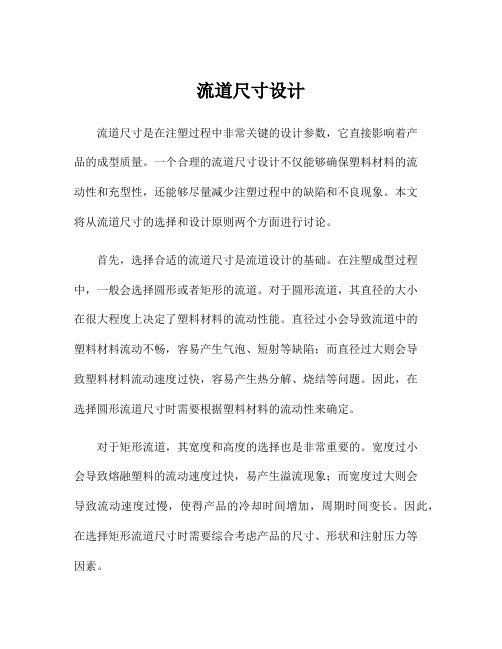
流道尺寸设计流道尺寸是在注塑过程中非常关键的设计参数,它直接影响着产品的成型质量。
一个合理的流道尺寸设计不仅能够确保塑料材料的流动性和充型性,还能够尽量减少注塑过程中的缺陷和不良现象。
本文将从流道尺寸的选择和设计原则两个方面进行讨论。
首先,选择合适的流道尺寸是流道设计的基础。
在注塑成型过程中,一般会选择圆形或者矩形的流道。
对于圆形流道,其直径的大小在很大程度上决定了塑料材料的流动性能。
直径过小会导致流道中的塑料材料流动不畅,容易产生气泡、短射等缺陷;而直径过大则会导致塑料材料流动速度过快,容易产生热分解、烧结等问题。
因此,在选择圆形流道尺寸时需要根据塑料材料的流动性来确定。
对于矩形流道,其宽度和高度的选择也是非常重要的。
宽度过小会导致熔融塑料的流动速度过快,易产生溢流现象;而宽度过大则会导致流动速度过慢,使得产品的冷却时间增加,周期时间变长。
因此,在选择矩形流道尺寸时需要综合考虑产品的尺寸、形状和注射压力等因素。
其次,流道尺寸的设计还要遵循一些原则。
首先,流道尺寸应该保持一致。
在同一产品的注塑过程中,流道尺寸应该保持一致,这样可以避免因流道尺寸不一致造成的塑料充填不均匀的问题。
其次,流道尺寸应该适当增大。
在设计流道尺寸时,应该适当增大其尺寸,以便增加塑料材料的流动路径,减少熔融塑料的流动速度,从而达到充填均匀、缩短冷却时间的效果。
最后,流道尺寸应该适当减小。
在一些特殊情况下,比如产品中有镶件、薄壁等要求时,需要适当减小流道尺寸,以便达到更好的充型效果。
除了上述原则外,还有一些其他因素也需要考虑。
比如,流道长度的选择。
流道长度过长会导致熔融塑料的流动速度减慢,对塑料材料的热损失增大,因此应尽量减小流道长度。
另外,流道与产品的连接方式也需要考虑。
一般流道与产品的连接处呈斜角或圆角状,这样可以使塑料材料充填更加均匀。
综上所述,流道尺寸设计是注塑过程中非常重要的一环。
合理选择和设计流道尺寸能够确保产品的成型质量,并最大限度地减少缺陷和不良现象的发生。
注塑模具设计之浇口与流道设计

注塑模具设计之浇口与流道设计
1.浇口设计:
浇口是塑料进入模具腔体的通道,直接影响产品的质量和外观。
浇口设计应遵循以下原则:
1.1浇口的位置应尽量选择在产品的无重要表面或结构上,以减少产品上的痕迹和缺陷。
1.2浇口的形状应尽量简单,以便于注塑成型时的塑料流动,避免气泡和短流等缺陷。
1.3浇口的大小应根据产品的要求确定,过大会导致浇注时间过长,过小会导致注塑过程压力过高。
1.4浇口与产品的交界处应尽量平滑,以减少痕迹和切除时的损耗。
1.5浇口的数量应尽量减少,多个浇口可能导致注塑不平衡,造成产品尺寸不一致。
2.流道设计:
流道是浇口与模具腔体之间的连接通道,它将塑料从浇口引导到模具腔体中。
流道设计应遵循以下原则:
2.1流道的形状应尽量简单,避免过多的转弯或急角,以减少流动阻力和塑料流动不均匀导致的缺陷。
2.2流道的长度应尽量短,以减少注塑周期和塑料的凝结时间。
2.3流道的截面积应逐渐减小,以确保塑料在流道中均匀流动,避免气泡的产生。
2.4流道与模具腔体的接头处应尽量平滑,避免塑料流动时的冲击和挤压,以减少产品上的痕迹和缺陷。
总结起来,注塑模具设计中的浇口与流道设计需要考虑产品的要求、材料的特性和注塑工艺的要求等多个因素,以使得产品的质量达到最佳状态。
在实际设计中,需要结合实际情况进行调整和优化,不断改进和提高设计水平。
塑料模具流道设计标准

塑料模具流道设计标准塑料模具的流道设计十分重要,它直接影响到模具注塑过程中的温度控制、压力变化以及产品质量等方面。
以下是关于塑料模具流道设计的一些标准:一、流道宽度:在塑料模具的流道设计中,流道宽度一般应为2-4mm,以确保塑胶的流动性能良好。
如果流道宽度过大,将导致塑胶的流动速度过快,容易产生气泡和翘曲等缺陷;而如果流道宽度过小,会增加塑胶的流动阻力,导致注塑压力过高,还会产生热嵌痕等缺陷。
二、流道截面形状:流道的截面形状有圆形、矩形、梯形等多种选择,其中矩形和梯形常用于多孔板流道设计。
在流道截面形状设计中,需要考虑到塑胶流动的速度、流动的平稳性以及压力变化等因素。
一般来说,流道截面形状越宽越好,这样可以降低注塑时的压力损失,并减少塑胶的流动阻力,提高生产效率和产品质量。
三、流道长度:流道长度是指从注塑机喂料口到模具最远端的长度。
流道长度应根据具体的产品要求和注塑机的能力来决定。
一般来说,流道长度越短越好,可以减少塑胶的流动距离和时间,提高注塑效率和产品质量。
但是,流道长度过短也会导致注塑时的压力损失增加,可能会产生熔接痕等缺陷。
四、流道表面光洁度:流道的表面光洁度对于塑胶的流动性能和产品表面质量有着重要影响。
流道设计中,流道的表面应尽量保持光洁,并且不应有明显的凹凸或毛刺等缺陷。
这样可以减少塑胶在流动过程中的摩擦阻力,提高流动的平稳性,减少产品表面的瑕疵。
综上所述,塑料模具流道设计需要考虑流道宽度、流道截面形状、流道长度以及流道表面光洁度等因素。
通过合理的流道设计,可以提高塑料模具的注塑效率和产品质量,降低生产成本,符合相关的标准和要求。
注塑模具设计经常会用到热流道进胶,那么设计热流道要注意什么呢
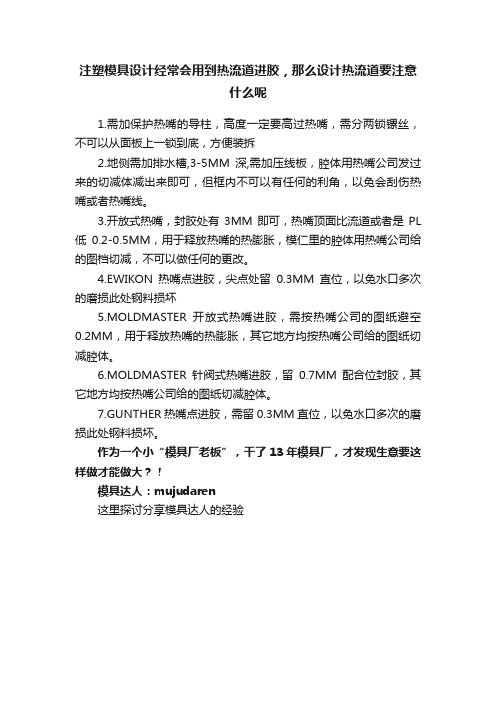
注塑模具设计经常会用到热流道进胶,那么设计热流道要注意
什么呢
1.需加保护热嘴的导柱,高度一定要高过热嘴,需分两锁镙丝,不可以从面板上一锁到底,方便装拆
2.地侧需加排水槽,3-5MM深,需加压线板,腔体用热嘴公司发过来的切减体减出来即可,但框内不可以有任何的利角,以免会刮伤热嘴或者热嘴线。
3.开放式热嘴,封胶处有3MM即可,热嘴顶面比流道或者是PL 低0.2-0.5MM,用于释放热嘴的热膨胀,模仁里的腔体用热嘴公司给的图档切减,不可以做任何的更改。
4.EWIKON热嘴点进胶,尖点处留0.3MM直位,以免水口多次的磨损此处钢料损坏
5.MOLDMASTER开放式热嘴进胶,需按热嘴公司的图纸避空0.2MM,用于释放热嘴的热膨胀,其它地方均按热嘴公司给的图纸切减腔体。
6.MOLDMASTER针阀式热嘴进胶,留0.7MM配合位封胶,其它地方均按热嘴公司给的图纸切减腔体。
7.GUNTHER热嘴点进胶,需留0.3MM直位,以免水口多次的磨损此处钢料损坏。
作为一个小“模具厂老板”,干了13年模具厂,才发现生意要这样做才能做大?!
模具达人:mujudaren
这里探讨分享模具达人的经验。
注塑模具热流道
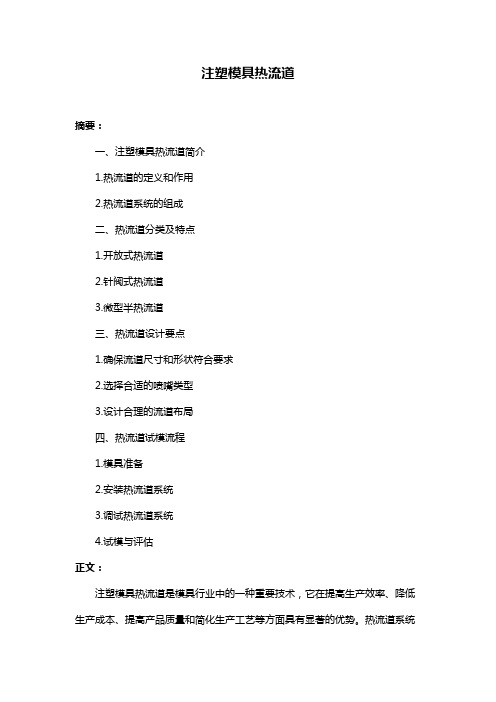
注塑模具热流道
摘要:
一、注塑模具热流道简介
1.热流道的定义和作用
2.热流道系统的组成
二、热流道分类及特点
1.开放式热流道
2.针阀式热流道
3.微型半热流道
三、热流道设计要点
1.确保流道尺寸和形状符合要求
2.选择合适的喷嘴类型
3.设计合理的流道布局
四、热流道试模流程
1.模具准备
2.安装热流道系统
3.调试热流道系统
4.试模与评估
正文:
注塑模具热流道是模具行业中的一种重要技术,它在提高生产效率、降低生产成本、提高产品质量和简化生产工艺等方面具有显著的优势。
热流道系统
由热喷嘴、分流板、温控箱和附件等组成,其核心部件是热喷嘴,其作用是将熔融塑料从注塑机喷嘴引导到模具中。
根据热喷嘴的结构形式,热流道主要分为开放式热流道、针阀式热流道和微型半热流道。
开放式热流道结构简单,适用于小型模具;针阀式热流道具有较好的封闭性能,适用于较大型模具;微型半热流道则结合了开放式和针阀式的优点,稳定好用,故障率低。
在设计热流道时,应确保流道尺寸和形状符合要求,选择合适的喷嘴类型,并设计合理的流道布局。
此外,还需考虑热流道的冷却系统、流道材料和加工工艺等因素。
热流道试模流程包括模具准备、安装热流道系统、调试热流道系统和试模与评估。
在试模过程中,需检查热流道系统的运行状况,如喷嘴是否堵塞、流道是否畅通、温度控制是否准确等,以保证生产过程中热流道系统的稳定运行。
三分钟弄懂注塑模具流道与浇口
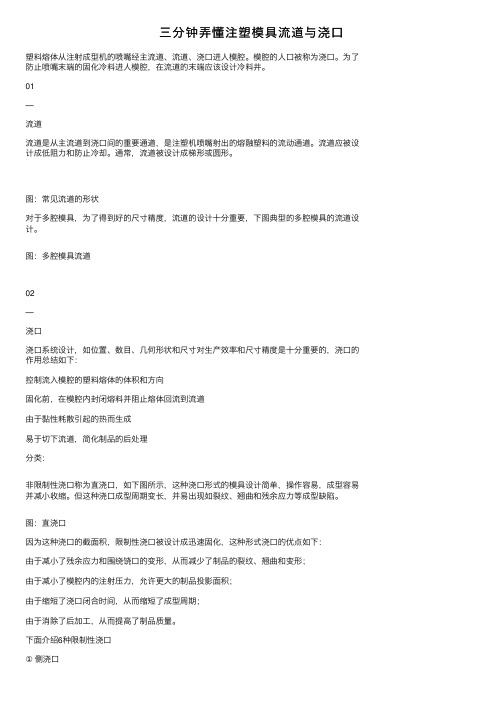
三分钟弄懂注塑模具流道与浇⼝塑料熔体从注射成型机的喷嘴经主流道、流道、浇⼝进⼈模腔。
模腔的⼈⼝被称为浇⼝。
为了防⽌喷嘴末端的固化冷料进⼈模腔,在流道的末端应该设计冷料井。
01—流道流道是从主流道到浇⼝间的重要通道,是注塑机喷嘴射出的熔融塑料的流动通道。
流道应被设计成低阻⼒和防⽌冷却。
通常,流道被设计成梯形或圆形。
图:常见流道的形状对于多腔模具,为了得到好的尺⼨精度,流道的设计⼗分重要,下图典型的多腔模具的流道设计。
图:多腔模具流道02—浇⼝浇⼝系统设计,如位置、数⽬、⼏何形状和尺⼨对⽣产效率和尺⼨精度是⼗分重要的,浇⼝的作⽤总结如下:控制流⼊模腔的塑料熔体的体积和⽅向固化前,在模腔内封闭熔料并阻⽌熔体回流到流道由于黏性耗散引起的热⽽⽣成易于切下流道,简化制品的后处理分类:⾮限制性浇⼝称为直浇⼝,如下图所⽰,这种浇⼝形式的模具设计简单,操作容易,成型容易并减⼩收缩。
但这种浇⼝成型周期变长,并易出现如裂纹、翘曲和残余应⼒等成型缺陷。
图:直浇⼝因为这种浇⼝的截⾯积,限制性浇⼝被设计成迅速固化,这种形式浇⼝的优点如下:由于减⼩了残余应⼒和围绕饶⼝的变形,从⽽减少了制品的裂纹、翘曲和变形;由于减⼩了模腔内的注射压⼒,允许更⼤的制品投影⾯积;由于缩短了浇⼝闭合时间,从⽽缩短了成型周期;由于消除了后加⼯,从⽽提⾼了制品质量。
下⾯介绍6种限制性浇⼝①侧浇⼝侧浇⼝厚度通常为制品壁厚的30%⼀-40%。
同时其宽度⼤约3倍于制品壁厚,侧浇⼝⼏乎可应⽤于所有的塑料,叠合式浇⼝和轮辐式浇⼝是侧浇⼝的变形设计。
②扇形浇⼝扇形浇⼝的截⾯宽⽽扁,有效地消除了浇⼝的缺陷,常被⽤于扁平的产品。
③膜式浇⼝上图是典型的膜式浇⼝设计,其浇⼝宽度与制品宽度⼀致,但厚度⼩很多,与扇形浇⼝⼀样能有效地消除制品的残余应⼒和变形。
④盘式浇⼝⼀个薄的盘式浇⼝围绕着盘形或环形制品以避免熔接痕的⽣成,环形浇⼝是盘式浇⼝的变形。
⑤针式浇⼝针式浇⼝通常位于制品的中间,⽽且常⽤于多点浇⼝,由于浇⼝的直径通常为0.8- -1.2mm,⼩的截⾯积引起⾼的流动阻⼒,建议使⽤低黏度塑料或⾼注射压⼒以避免⽋注。
模具流道设计标准要求是什么
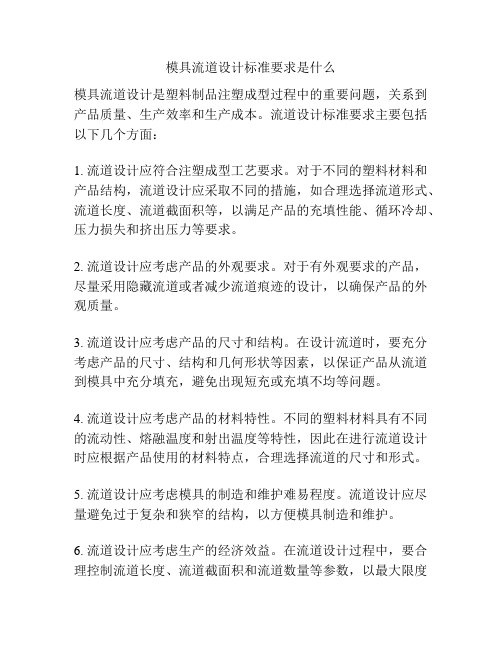
模具流道设计标准要求是什么
模具流道设计是塑料制品注塑成型过程中的重要问题,关系到产品质量、生产效率和生产成本。
流道设计标准要求主要包括以下几个方面:
1. 流道设计应符合注塑成型工艺要求。
对于不同的塑料材料和产品结构,流道设计应采取不同的措施,如合理选择流道形式、流道长度、流道截面积等,以满足产品的充填性能、循环冷却、压力损失和挤出压力等要求。
2. 流道设计应考虑产品的外观要求。
对于有外观要求的产品,尽量采用隐藏流道或者减少流道痕迹的设计,以确保产品的外观质量。
3. 流道设计应考虑产品的尺寸和结构。
在设计流道时,要充分考虑产品的尺寸、结构和几何形状等因素,以保证产品从流道到模具中充分填充,避免出现短充或充填不均等问题。
4. 流道设计应考虑产品的材料特性。
不同的塑料材料具有不同的流动性、熔融温度和射出温度等特性,因此在进行流道设计时应根据产品使用的材料特点,合理选择流道的尺寸和形式。
5. 流道设计应考虑模具的制造和维护难易程度。
流道设计应尽量避免过于复杂和狭窄的结构,以方便模具制造和维护。
6. 流道设计应考虑生产的经济效益。
在流道设计过程中,要合理控制流道长度、流道截面积和流道数量等参数,以最大限度
地提高生产效率和降低生产成本。
综上所述,模具流道设计的标准要求主要包括符合成型工艺要求、考虑产品外观要求、考虑产品尺寸和结构、考虑产品材料特性、考虑模具制造和维护难易程度,以及考虑生产的经济效益等方面。
只有满足这些标准要求,才能设计出高效、高质量的模具流道。
注塑模具设计知识点

注塑模具设计知识点注塑模具是在塑料制品生产中起关键作用的一种工具,它的设计质量直接影响着产品的质量和生产效率。
本文将介绍注塑模具设计的一些基本知识点,以及在设计中需要注意的事项。
一、模具结构注塑模具由模具板、芯轴、活塞、顶针等组成。
模具板承受注塑过程中的压力和冲击力,必须具备足够的强度和刚度。
芯轴用于形成注塑制品内部的空间形状,也要求具备较高的硬度和耐磨性。
活塞和顶针用于顶出注塑制品,其结构设计要考虑到顶出力的大小和顶出效果。
二、模具材料常用的模具材料有铝合金、钢材等。
铝合金模具具有质量轻、导热性好等优点,适用于小批量生产和快速开发新产品。
钢材模具则具有高强度、高硬度和耐磨性等特点,适用于大批量生产。
在选择模具材料时,需要根据生产要求、产品材料和使用寿命等方面综合考虑。
三、模具设计的重点1. 完整度:模具设计要保持产品的完整度,即保证产品的尺寸、形状和表面质量符合设计要求。
2. 排气性能:模具内部注塑过程会产生大量气体,需要保证模具具有良好的排气性能,以避免空气被封闭在注塑制品中形成气泡。
3. 冷却系统:注塑过程中,需要通过冷却系统将塑料制品迅速冷却固化,以确保产品的尺寸稳定性。
因此,在模具设计中要合理布置冷却水道,以提高冷却效果。
4. 塑料流道设计:塑料从注塑机进入模具的路径称为塑料流道,其设计要遵循塑料的流动特性和产品的要求。
塑料流道的布置和尺寸直接影响着产品的充填状况和成型效果。
5. 分型面设计:注塑制品在模具中成形后需要顶出,因此需要合理设置分型面,以方便产品的顶出和模具的拆卸。
四、模具制造工艺模具的制造工艺包括数控加工、装配和调试等环节。
数控加工技术能够快速高效地完成模具的加工工序,提高模具的精度和质量。
在模具装配过程中,需要确保模具的各部件相互协调和配合良好。
调试环节是验证模具性能和调整参数的过程,确保模具能够正常运行。
注塑模具设计是一个综合性较强的工程,需要根据具体的产品要求和生产条件来进行设计。
1出8塑胶模具流道设计
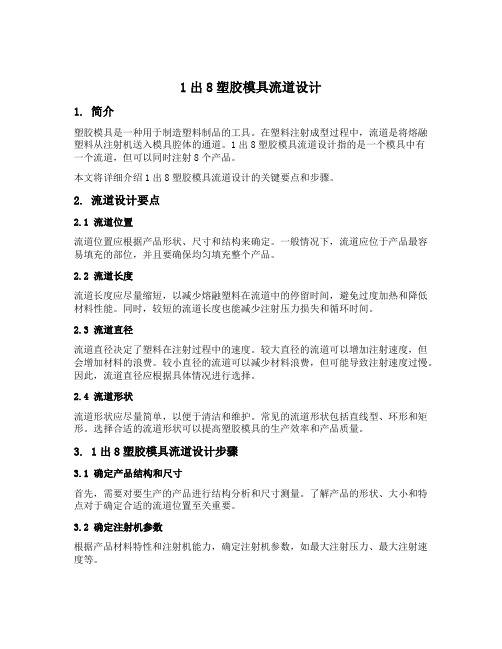
1出8塑胶模具流道设计1. 简介塑胶模具是一种用于制造塑料制品的工具。
在塑料注射成型过程中,流道是将熔融塑料从注射机送入模具腔体的通道。
1出8塑胶模具流道设计指的是一个模具中有一个流道,但可以同时注射8个产品。
本文将详细介绍1出8塑胶模具流道设计的关键要点和步骤。
2. 流道设计要点2.1 流道位置流道位置应根据产品形状、尺寸和结构来确定。
一般情况下,流道应位于产品最容易填充的部位,并且要确保均匀填充整个产品。
2.2 流道长度流道长度应尽量缩短,以减少熔融塑料在流道中的停留时间,避免过度加热和降低材料性能。
同时,较短的流道长度也能减少注射压力损失和循环时间。
2.3 流道直径流道直径决定了塑料在注射过程中的速度。
较大直径的流道可以增加注射速度,但会增加材料的浪费。
较小直径的流道可以减少材料浪费,但可能导致注射速度过慢。
因此,流道直径应根据具体情况进行选择。
2.4 流道形状流道形状应尽量简单,以便于清洁和维护。
常见的流道形状包括直线型、环形和矩形。
选择合适的流道形状可以提高塑胶模具的生产效率和产品质量。
3. 1出8塑胶模具流道设计步骤3.1 确定产品结构和尺寸首先,需要对要生产的产品进行结构分析和尺寸测量。
了解产品的形状、大小和特点对于确定合适的流道位置至关重要。
3.2 确定注射机参数根据产品材料特性和注射机能力,确定注射机参数,如最大注射压力、最大注射速度等。
3.3 设计模具结构根据产品结构、尺寸和数量要求,设计模具结构,并确定最佳的模腔布局。
3.4 确定流道位置根据产品结构和填充分析结果,确定最佳的流道位置。
流道应位于产品的最容易填充的部位,并确保产品能够均匀填充。
3.5 设计流道形状和长度根据流道位置和注射机参数,设计合适的流道形状和长度。
流道直径应根据具体情况进行选择,以实现最佳的注射速度和材料利用率。
3.6 模拟分析和优化使用模拟软件对模具流道进行分析和优化。
通过模拟分析,可以评估流道设计的合理性,发现潜在问题并进行改进。
塑胶模具流道设计
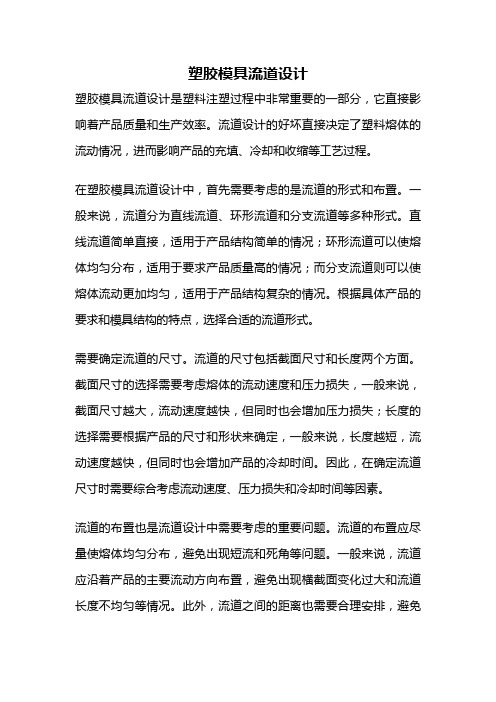
塑胶模具流道设计塑胶模具流道设计是塑料注塑过程中非常重要的一部分,它直接影响着产品质量和生产效率。
流道设计的好坏直接决定了塑料熔体的流动情况,进而影响产品的充填、冷却和收缩等工艺过程。
在塑胶模具流道设计中,首先需要考虑的是流道的形式和布置。
一般来说,流道分为直线流道、环形流道和分支流道等多种形式。
直线流道简单直接,适用于产品结构简单的情况;环形流道可以使熔体均匀分布,适用于要求产品质量高的情况;而分支流道则可以使熔体流动更加均匀,适用于产品结构复杂的情况。
根据具体产品的要求和模具结构的特点,选择合适的流道形式。
需要确定流道的尺寸。
流道的尺寸包括截面尺寸和长度两个方面。
截面尺寸的选择需要考虑熔体的流动速度和压力损失,一般来说,截面尺寸越大,流动速度越快,但同时也会增加压力损失;长度的选择需要根据产品的尺寸和形状来确定,一般来说,长度越短,流动速度越快,但同时也会增加产品的冷却时间。
因此,在确定流道尺寸时需要综合考虑流动速度、压力损失和冷却时间等因素。
流道的布置也是流道设计中需要考虑的重要问题。
流道的布置应尽量使熔体均匀分布,避免出现短流和死角等问题。
一般来说,流道应沿着产品的主要流动方向布置,避免出现横截面变化过大和流道长度不均匀等情况。
此外,流道之间的距离也需要合理安排,避免相互干扰和影响。
流道设计中还需要考虑一些特殊情况和特殊要求。
例如,在注塑过程中可能会出现熔体的温度过高或过低的情况,这就需要在流道设计中考虑冷却系统的设置;又如,在产品结构复杂或要求产品表面光滑的情况下,需要在流道设计中考虑使用流道加热或减压等特殊措施。
塑胶模具流道设计是塑料注塑过程中至关重要的一环。
通过合理的流道设计,可以使熔体均匀流动,保证产品的充填、冷却和收缩等工艺过程的顺利进行,从而提高产品的质量和生产效率。
因此,在进行塑胶模具流道设计时,需要综合考虑流道的形式和布置、尺寸和特殊要求等因素,以达到最佳的设计效果。
热流道结构知识点总结

热流道结构知识点总结热流道结构在塑料注射成型过程中扮演着重要的角色,它可以帮助提高注射成型的效率和质量。
本文将会总结热流道结构的相关知识点,包括热流道系统的基本原理、组成部分、优点和缺点、应用范围等内容。
一、热流道系统的基本原理热流道系统是一种在注射模具中用于传送加热的热载体,保持塑料材料在注射成型过程中的流动状态,以保证产品的成型质量和提高生产效率。
热流道系统的基本原理包括:1. 热载体传导热量:热流道系统中通常采用热载体(如热油、热水)传导热量,将热能传递到模具的热流道中,使塑料材料在注射成型过程中能够始终保持在合适的流动状态。
2. 控制模具温度:通过控制热载体的温度和流量,可以实现对注射模具中的温度进行精确的控制。
这样可以避免塑料材料在成型过程中受温度变化的影响,保证产品的尺寸稳定性和表面质量。
3. 优化成型条件:热流道系统可以根据不同的产品形状和材料特性,灵活调节模具中不同部位的温度,以实现最佳的注射成型效果。
二、热流道系统的组成部分热流道系统由多个组成部分组成,主要包括热流道控制器、加热装置、温度探测器、热流道喉口等。
1. 热流道控制器:负责对热流道系统的温度、压力等参数进行实时监控和调节,以确保注射成型过程中的稳定性和一致性。
2. 加热装置:通常采用电加热或加热用的热管,通过对热载体进行加热,传递热能到热流道系统中。
3. 温度探测器:用于监测热流道系统中的温度变化,反馈给热流道控制器,以实现自动调节和控制。
4. 热流道喉口:负责将加热好的热载体传递到模具的热流道中,为塑料材料提供适宜的加热条件。
三、热流道系统的优点和缺点热流道系统相比传统的冷流道系统具有许多优点,但也存在一些缺点。
1. 优点:(1)节能减耗:热流道系统采用热载体传导热量,可以有效减少注射成型过程中的能耗,提高生产效率。
(2)减少生产环境污染:热流道系统可以降低产品的废料率,提高成型质量,减少生产环境的污染。
(3)提高产品质量:热流道系统可以精确控制模具中不同部位的温度,保证产品的尺寸稳定性和表面质量。
最重要的最容易忽视的—模具主流道和分流道

最重要的最容易忽视的—模具主流道和分流道主流道、分流道和浇口的作用是将塑料熔体从注射成型机喷嘴中输送至各个型腔。
浇注系统凝料可以粉碎后再回用,这是确实的,但尽管如此,由于凝料的存在就意味着注射成型机生产力的降低,因为浇注系统部分的物料也必须在注射成型机的机筒里塑化。
就较小的塑件来说,浇注系统凝料可能占实际注射量的50或者更多一些。
主流道主流遭可看作是喷嘴的通道在模具中的延续。
在单型腔模具中,主浇道直接通向塑件的浇口称为直浇口。
单型腔注射模具的生产力通常是由主流道的冷却时间决定的。
除了对主流道衬套提供足够的冷却外,主流道衬套上进料口的最小直径应尽可能小,并且又能适时充满型腔。
但在此没有普遍适用的规律,因为型腔的充满是取决于诸多因素的.主流道应该有1.5·的脱模斜度。
脱模斜度较大,可使主流道从主流道衬套里容易脱出。
但是当主流道较长时会导致其直径较大,且因此需要比较长的冷却时间。
注射成型机喷嘴的出口直径应比主流道衬套最小孔径小o.5mm,这样在主流道的顶端不会形成凹槽妨碍主流道凝料的脱出。
分流道在多型腔模具中,塑料熔体必须通过设在模具分型面上的分流道注入各型腔。
适用于主流道的基本规律同样也适用于分流道的横断面。
还有一个附加的因素必须考虑,分流道横断面也是其长度的函数,因为可以假设分流道中压力损失的增大至少是与分流道长度成正比的。
而多半情况压力损失将更大,因为其横断面由于沿流道壁塑料熔体的固化而减小,而且离主流道距离越远,压力损失则更大。
另外主流道和分流道系统意味着损耗原料和白费了注射成型机的塑化量,所以分流道应尽可能设计得短,横断面应尽可能最小。
分流道的长度是由模具的型腔数和各型腔的几何排列决定的。
分流道横断面的形状因圆形断面分流道的表面积最小,相对于分流道断面积的热损失最少,故应尽可能采用圆形断面的分流道。
因在圆形断面分流道中心的熔料最后固化,故在保压压力的作用下,塑料熔体能沿着圆形断面分流道的中心流动最长的距离。
- 1、下载文档前请自行甄别文档内容的完整性,平台不提供额外的编辑、内容补充、找答案等附加服务。
- 2、"仅部分预览"的文档,不可在线预览部分如存在完整性等问题,可反馈申请退款(可完整预览的文档不适用该条件!)。
- 3、如文档侵犯您的权益,请联系客服反馈,我们会尽快为您处理(人工客服工作时间:9:00-18:30)。
注塑模具设计时关于流道的着重点
1、进胶口应开设在产品肉厚部分,保证充模顺利和完全;
2、尽量开设在不影响产品外观和功能处,可在边缘或底部处;
3、在浇口附近之冷料穴,尽端常设置拉料杆,以利于浇道脱模;
4、大型或扁平产品,建议采用多点进浇,可防止产品翘曲变形和缺料;
5、其位置应选在使塑料充模流程最短处,以减少压力损失,有利于模具排气;
6、在细长型芯附近避免开设浇口,以免料流直接冲击型芯,产生变形错位或弯曲;
7、浇口尺寸由产品大小,几何形状,结构和塑料种类决定,可先取小尺寸再根据试模状况进行修正;
8、可通过模流分析或经验,判断产品因浇口位置而产生之结合线处,是否影响产品外观和功能,可加设冷料穴加以解决;
9、一模多穴时,相同的产品采用对称进浇方式,对于不同产品在同一模具中成型时,优先将最大产品放在靠近主流道的位置。