重介质
重介质文档

重介质概述在物理学中,介质是指一种能够传播或传递物理量的物质。
根据物理性质的不同,介质可以分为轻介质和重介质。
本文将重点介绍重介质。
重介质的定义重介质是指密度较大的介质,其密度大约为1 g/cm³以上。
重介质常见于液体和固体物质中,如水、铁、铅等。
与轻介质相比,重介质的密度较大,因此在物体受到重力的作用下会下沉。
重介质的性质1.密度大:重介质的密度一般较轻介质大,这是因为重介质的物质排列较紧密,分子之间的距离较小。
2.下沉:由于重介质的密度大,重介质在液体中会下沉。
当放置在液体中时,重介质会因为受到重力的作用而下沉到液体的底部。
3.压力传递:重介质能够有效地传递压力。
当一个重介质被施加力或受到压力时,这个压力会通过重介质传递到其他部分。
重介质在实际应用中的应用1.水库和水坝:水坝是由重介质构成的大型水体积蓄设施,通过拦截水流来积蓄水源供给人们的生活和发电等用途。
水坝的重介质特性使水能够被有效积蓄。
2.铅笔芯:铅笔芯是由石墨和粘合剂组成的材料,其中的石墨是一种具有较高密度的重介质。
重介质特性使得铅笔芯在书写时能够稳定下沉,并且便于控制压力以产生清晰的线条。
3.赛车轮胎:赛车轮胎常常会使用铅负荷来增加轮胎质量,提供更好的抓地力和稳定性。
铅是重介质,其在轮胎中的应用能够有效提高赛车的性能。
4.铁砧:铁砧作为金属加工中常用的工具,由于具有重介质的特性,能够稳定地接受冲压和打击,提供更好的工作效果。
重介质的实验室应用1.密度测量:由于重介质的密度较大,可以通过密度测量实验来测量物质的密度。
常见的测量方法包括浸水法、比重尺法等。
2.浮力实验:重介质可以用于浮力实验。
通过将一个重介质固定在弹簧上,可以观察到重力对物体产生的压力和弹力之间的平衡关系。
3.压力传递实验:重介质能够有效传递压力,因此可以通过搭建实验装置来观察重介质中压力的传递过程。
结论重介质是一种密度较大的介质,在物理学中具有重要的地位。
重介质选矿的操作方法
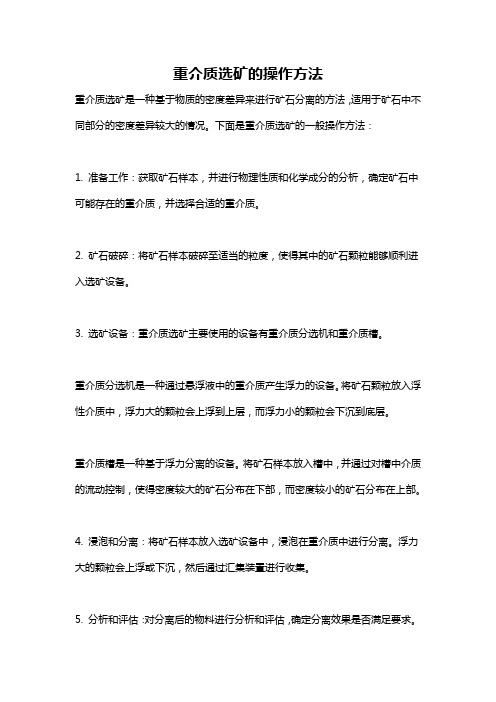
重介质选矿的操作方法
重介质选矿是一种基于物质的密度差异来进行矿石分离的方法,适用于矿石中不同部分的密度差异较大的情况。
下面是重介质选矿的一般操作方法:
1. 准备工作:获取矿石样本,并进行物理性质和化学成分的分析,确定矿石中可能存在的重介质,并选择合适的重介质。
2. 矿石破碎:将矿石样本破碎至适当的粒度,使得其中的矿石颗粒能够顺利进入选矿设备。
3. 选矿设备:重介质选矿主要使用的设备有重介质分选机和重介质槽。
重介质分选机是一种通过悬浮液中的重介质产生浮力的设备。
将矿石颗粒放入浮性介质中,浮力大的颗粒会上浮到上层,而浮力小的颗粒会下沉到底层。
重介质槽是一种基于浮力分离的设备。
将矿石样本放入槽中,并通过对槽中介质的流动控制,使得密度较大的矿石分布在下部,而密度较小的矿石分布在上部。
4. 浸泡和分离:将矿石样本放入选矿设备中,浸泡在重介质中进行分离。
浮力大的颗粒会上浮或下沉,然后通过汇集装置进行收集。
5. 分析和评估:对分离后的物料进行分析和评估,确定分离效果是否满足要求。
6. 收尾工作:将分离后的物料进行清洗、干燥等后续处理,以便后续工艺的进行。
需要注意的是,重介质选矿的操作方法可能因具体矿石的性质和选矿设备的类型而有所不同,以上只是一种一般的操作方法。
实际操作时应根据具体情况进行调整和改进。
选煤用重介质生产工艺

01
重介质生产工艺优化与改 进建议
提高重介质生产效率的建议
增加自动化设备
使用自动化设备可以减少人工操作,提高生产效率。例如,使用智能化的泵站和控制系统,能够实现重介质的自 动化调配和运输。
优化生产流程
通过对重介质生产流程的优化,可以减少生产环节和运输距离,提高生产效率。例如,采用集中配料和混合的工 艺流程,能够减少重复运输和装卸的环节。
01
重介质生产工艺应用案例
案例一:某大型选煤厂的重介质生产工艺设计
背景介绍
某大型选煤厂为了提高选煤效率和精度,决定采用重介质 选煤技术。
工艺流程
该选煤厂的重介质生产工艺主要包括原煤准备、重介质制 备、重介质选煤、产品脱介、重介质回收和再利用等环节 。
技术特点
该工艺采用高效的重介质选煤技术,能够大幅度提高选煤 效率和精度,同时重介质回收和再利用技术也得到了很好 的应用。
排水
储存
将反冲洗水排出,收集残余的介质并处理 。
将反冲洗后的介质储存到指定的仓库或储 罐中备用。
介质回收流程
01
介质回收系统
使用介质回收系统将残余的介质 进行回收处理。
分离器
在介质回收系统中,使用分离器 将不同的介质进行分离和分类。收泵将残余的介质输送至 回收系统进行处理。
储存
将回收处理后的介质储存到指定 的仓库或储罐中备用。
04
01
重介质生产设备与材料
重介质生产设备
重介质生产设备种类繁多,根据工艺流程和规模可分为不同的类型。常见的设备包括混合桶、沉淀池 、磁选机、筛分机等。
混合桶用于将重介质粉和悬浮液混合均匀,沉淀池用于重介质悬浮液的固液分离,磁选机用于去除重 介质中的磁性杂质,筛分机用于将重介质按粒度分级。
重介选煤的基本原理

重介选煤的基本原理重介选煤是一种利用重介质进行分选的煤炭加工技术,其基本原理是根据不同物理性质的差异将混合物分离成不同密度的两部分。
本文将从以下几个方面详细介绍重介选煤的基本原理。
一、重介质重介质是指密度大于水的液体或固体,常用的有磁性流体、金刚石悬浮液、铁粉悬浮液等。
在重介选煤中,通常使用的是稀土永磁材料制成的永磁流体或铁粉悬浮液。
这些重介质具有密度大、稳定性好、可回收利用等优点,可以有效地实现对混合物中不同密度组分的分离。
二、原理1.浮力原理根据阿基米德原理,物体在液体中受到向上的浮力大小等于其排开液体的体积乘以液体密度。
在重介选煤中,混合物经过加入重介质后会形成两个相互分离的层,其中密度较大的组分会沉降到底部,而密度较小的组分则会浮到重介质表面。
这是由于密度较大的组分受到的浮力较小,无法与重介质竞争,因此会沉降到底部;而密度较小的组分受到的浮力较大,可以与重介质竞争,因此会浮到表面。
2.惯性原理在重介选煤中,混合物经过加入重介质后通过旋流器或离心机等设备进行分离。
当混合物进入旋流器时,由于离心力的作用,密度较大的组分会向外侧移动,而密度较小的组分则会向内侧移动。
这是由于惯性原理的作用,在旋流器中,由于速度快慢不同导致了不同密度组分向不同方向运动。
3.表面张力原理在重介选煤中,混合物经过加入重介质后通过气泡法进行分离。
气泡法是利用气泡与固体颗粒之间的表面张力差异使颗粒上浮或下沉实现分离。
当气泡被注入混合物中时,它们会吸附在颗粒表面并将其带到液体表面。
在液体表面,气泡的表面张力会将颗粒推向液体表面或底部,从而实现分离。
三、影响因素1.重介质密度重介质密度是影响重介选煤效果的关键因素。
一般来说,重介质密度越大,分离效果越好。
但是过高的密度会导致设备成本增加、能耗增加等问题,因此需要根据具体情况进行选择。
2.混合物性质混合物中不同组分的密度差异越大,分离效果越好。
此外,颗粒大小、形状、比表面积等也会影响分离效果。
《重介质选矿》课件
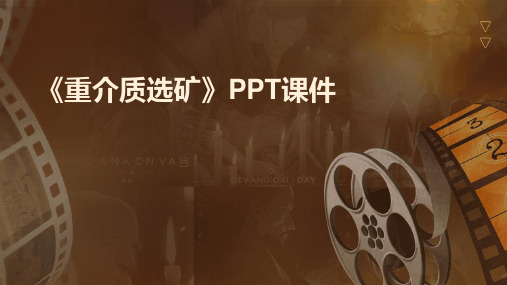
输标02入题
磁选机通常由磁系、给料装置、排料装置和传动装置 等部分组成。磁系是磁选机的核心部件,包括永久磁 铁、电磁铁等,负责产生磁场力。
01
03
磁选机广泛应用于黑色金属、有色金属、稀有金属、 非金属等矿物的选别,尤其在铁矿的选矿中占有重要
地位。
04
给料装置将物料均匀地加入磁系上方,排料装置则负 责将吸住的矿物排出。传动装置则负责驱动磁系旋转 ,使矿物在磁场中受到足够的磁力作用。
重介质选矿过程中,通常采用循环悬浮液作为重介质,通过调整悬浮液的密度和粘度等参数,实现对 不同密度矿物的有效分选。
重介质选矿的应用场景
重介质选矿广泛应用于铁矿石、煤炭、稀有金属等矿产资源的选矿。在 铁矿石选矿中,重介质选矿可以有效处理难选赤铁矿和磁铁矿,提高铁 精矿品位和回收率。
在煤炭领域,重介质选煤是高效清洁利用煤炭的重要手段之一,可以有 效脱硫降灰,提高煤质。
密度
重介质的密度是影响分选效果的关键因素,需要根据 待分选矿石的性质选择合适的重介质。
粘度
重介质的粘度对分选效果有一定影响,粘度过高或过 低都不利于分选。
稳定性
重介质的稳定性要好,以保持分选过程中的性能稳定 介质中的运动行为,进而影响 分选效果。
新型重介质开发
研究开发新型的重介质材料,提高分选效果和降低介质消耗。
环境保护与资源利用
绿色生产技术
01
推广环保型的重介质选矿技术,降低生产过程中的环境污染。
资源循环利用
02
实现重介质选矿废料的资源化利用,降低对自然资源的依赖。
节能减排
03
优化重介质选矿工艺,降低能耗和减少温室气体排放。
市场需求与趋势
重介质选矿工艺参数要求严格 ,操作难度较大,需要专业技
重介质选煤的工艺流程

重介质选煤的工艺流程
重介质选煤(也称DMS选煤)是一种物理选矿方法,主要应用于选煤厂。
下面是重介质选煤的工艺流程:
1. 粗煤分级:将原始煤经过破碎、筛分等步骤,将煤块分成粗煤和细煤。
2. 破碎和洗选:将粗煤进行破碎,以便更好地与重介质混合。
然后,将粉碎后的煤与重介质混合,形成悬浮液。
3. 混合器:将悬浮液输送到混合器中,在混合器中根据煤的密度进行分层。
较重的煤会沉入悬浮液底部,较轻的煤会浮在悬浮液表面。
4. 密度分离:将混合器分离出的悬浮液通过旋流器等设备进行分离。
旋流器根据煤的密度将悬浮液分成重介质、重质产物和轻质产物。
5. 洗煤:重介质中的重质煤经过脱水、脱泥等步骤进行洗煤,提高品位。
6. 分选:将经过洗煤的重质煤进行再次分选,根据煤的尺寸和密度进行分级。
同时,轻质产物也可进行再次处理。
7. 末了处理:处理轻质产物和废水。
轻质产物经过脱水和干燥处理作为煤粉燃料或其他利用途径。
废水经过处理后可回用或排放。
以上就是重介质选煤的工艺流程,每个选煤厂的具体工艺细节可能会有所不同,但总的流程大致相似。
选煤工艺的目标是提高煤炭品位,减少有用矿物质的损失,并尽可能降低对环境的影响。
重介质选煤原理

重介质选煤原理宝子,今天咱来唠唠重介质选煤这个超有趣的事儿。
你看啊,煤这东西呢,从地底下挖出来的时候那可是乱七八糟的,啥样的都有。
重介质选煤就像是一场神奇的大筛选派对。
那啥是重介质呢?简单说,就是一种比较重的东西,像磁铁矿粉配成的悬浮液之类的。
这就好比是我们有一个特殊的魔法池塘,这个池塘里的水不是普通的水,而是这种重介质的悬浮液。
煤块们就像是一群小伙伴,有胖的有瘦的,有重的有轻的,它们都要跳进这个魔法池塘里。
那些比较重的煤块啊,就像是比较壮实的小胖子,一下子就会沉得比较深。
而那些比较轻的煤块呢,就像瘦弱的小瘦子,在池塘里就浮得比较高。
这就是根据煤块和杂质之间密度的不同来进行分选的啦。
你想啊,要是没有这个重介质选煤的办法,那煤里面的石头啊、杂质啊,就会跟着煤一起,这多不好呀。
就像我们做蛋糕,如果把鸡蛋壳也混在里面,那蛋糕还能吃吗?肯定不行啦。
在这个重介质选煤的过程里,那些重的杂质,像矸石之类的,就会很快地沉到池塘底部,而我们想要的优质煤呢,就会处在合适的位置。
这就好像是在一个大泳池里,会游泳的人在水面上扑腾,不会游泳的旱鸭子就沉下去了一样。
而且哦,这个重介质选煤的效率还挺高的呢。
它就像一个超级严格又超级高效的管理员,把煤和杂质分得清清楚楚。
它不会让那些杂质轻易地混在好煤里面。
宝子,你再想象一下,那些煤块在重介质悬浮液里的样子。
它们就像是在一个梦幻的世界里,按照自己的重量在不同的层次漂浮或者下沉。
这就像是一场大自然安排的特殊舞蹈,每个煤块都在找到自己合适的位置。
重介质选煤还有个好处呢,就是它能够处理各种不同粒度的煤。
不管是大煤块还是小煤粒,都能在这个重介质的魔法下被很好地分选。
这就像一个万能的筛子,大的小的都能搞定。
不过呢,这个重介质选煤也不是一点麻烦都没有。
比如说这个重介质的配置就很有讲究。
就像我们调一杯好喝的果汁,各种配料的比例得合适,这个重介质悬浮液里磁铁矿粉的浓度啊之类的都得刚刚好。
如果太浓了,可能那些本来可以浮起来的煤块也浮不起来了;如果太稀了呢,杂质又可能除不干净。
重介质选煤的工艺流程

重介质选煤的工艺流程重介质选煤是一种物理选煤的方法,主要通过不同比重的介质来进行煤炭的分选,是一种高效、节能、环保的选煤方式。
下面将介绍重介质选煤的工艺流程。
1. 煤炭的预处理首先将原始煤炭进行破碎、磨矿和筛分处理,将煤炭粉碎成合适的尺寸,去除其中的石灰岩、黄铁矿、硫铁矿等杂质,以及一些大块的煤炭。
2. 浮选机投料将预处理后的煤炭投入到浮选机中,在浮选机中加入相应比重的介质,通过搅拌设备混合均匀。
3. 浮选过程浮选机中的搅拌设备将浮选浆搅拌均匀后,打开给煤口,让煤炭和介质混合物通过高速流入浮选槽中。
在浮选槽中,煤炭和介质按照所含有的矿物组分的密度差异进行分选。
重矿物下沉到浮选槽底部,轻矿物则漂浮到浮选槽顶上。
4. 筛分过程浮选过程结束后,将浮选槽中的煤炭和介质混合物通过刮板输送到筛分设备中。
根据不同的煤炭需求,利用不同筛分设备对不同颗粒大小的煤炭进行筛分,将所需要的煤炭颗粒分离出来,同时将剩余的介质循环利用。
5. 介质循环利用介质中的重矿物在浮选过程中下沉到底部,一部分通过水泵抽出,经过过滤、除水等处理后再次投入到浮选槽中使用。
这种循环利用介质的方式不仅能节省资源,减少环境污染,还能降低生产成本。
6. 尾矿处理浮选过程中废弃的煤炭和介质混合物称为尾矿,在选煤过程中通过尾矿处理设备进行处理。
将尾矿进行干燥、脱水、后处理等工艺,将其中的水分和残留的介质进行分离,以便于后续的环境处理。
总结起来,重介质选煤的工艺流程主要包括煤炭的预处理、浮选过程、筛分过程、介质循环利用和尾矿处理等几个主要环节。
重介质选煤作为一种高效、节能、环保的选煤方式,可以在提高煤炭利用率的同时,减少煤炭的资源浪费,降低对环境的污染。
重介质分选

重介质分选重介质分选包括这样的选煤过程,将原煤浸没在液体中进行分选,液体的密度介于精煤和矸石之间。
由于灰份含量和密度之间有一定的相互关系,通过调节分选液体的密度,将原煤中的含灰杂质排除到要求的程度是可能的。
重介质分选方法具有下列由于其它选煤方法的特点:(1)在正常要求的密度范围内的任一分选密度点,即使入料中±0.1密度物含量很高,也能进行精确分选。
(2)能够控制分选密度的波动范围在±0.005以内。
(3)能够处理粒度范围很广的物料,其最大粒度可达35.6cm。
(4)因其处理量高和占地空间小,投资和运输费用相对较低。
(5)能够改变分选密度以适应市场需求的变化。
(6)能够处理数质量发生波动的入料。
1.块煤重介质分选重介质分选是实验室浮沉试验在工业上的实际推广,浮沉试验可用作重力分选的标准(效率100%)。
工业生产与实验室的浮沉分离并不完全相同,其理由是:工业采用悬浮液而不是真溶液作为分选介质;入料的给入和浮物沉物的排放会赢棋分选介质的扰动;分选槽中需要搅拌或上升流以保证分选介质呈悬浮状态;由于实际要求处理量高,不允许有足够的停留时间使邻近密度物得到完善分选。
理论上,任意力度均可进行重介质分选;实际上,重介质分选的粒度范围大约为0.5~150mm,有时粒度达到35.6mm也可以进行分选。
粒度大约在6.3mm以上的物料通常在静态重介分选机中处理,而粒度在0.5mm~6.3mm的物料一般在离新分选机(如重介旋流器)中分选。
理想的分选介质应是真溶液,并具有下列性质:价格低廉、易于与水混合、能够在较宽的密度范围内调节、稳定、无毒、无腐蚀性和粘度低。
虽然理想的介质并不存在,但已经开发了许多种重介质,并正在应用于工业生产中,将原煤分选为矸石和商品精煤。
根据实际生产情况,任何介质应具有下列性质:从使用角度应价格便宜,物理性质稳定、在分选过程中不分解、化学性质不活泼且不与煤气反应、易从产品中脱除、易从矸石中回收、在要求的分选密度时粘度低、在要求的密度范围内白吃密度稳定。
重介质选矿的基本原理
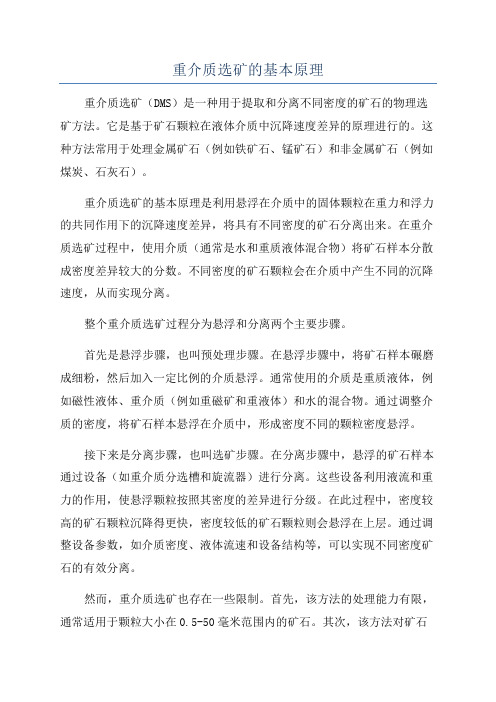
重介质选矿的基本原理重介质选矿(DMS)是一种用于提取和分离不同密度的矿石的物理选矿方法。
它是基于矿石颗粒在液体介质中沉降速度差异的原理进行的。
这种方法常用于处理金属矿石(例如铁矿石、锰矿石)和非金属矿石(例如煤炭、石灰石)。
重介质选矿的基本原理是利用悬浮在介质中的固体颗粒在重力和浮力的共同作用下的沉降速度差异,将具有不同密度的矿石分离出来。
在重介质选矿过程中,使用介质(通常是水和重质液体混合物)将矿石样本分散成密度差异较大的分数。
不同密度的矿石颗粒会在介质中产生不同的沉降速度,从而实现分离。
整个重介质选矿过程分为悬浮和分离两个主要步骤。
首先是悬浮步骤,也叫预处理步骤。
在悬浮步骤中,将矿石样本碾磨成细粉,然后加入一定比例的介质悬浮。
通常使用的介质是重质液体,例如磁性液体、重介质(例如重磁矿和重液体)和水的混合物。
通过调整介质的密度,将矿石样本悬浮在介质中,形成密度不同的颗粒密度悬浮。
接下来是分离步骤,也叫选矿步骤。
在分离步骤中,悬浮的矿石样本通过设备(如重介质分选槽和旋流器)进行分离。
这些设备利用液流和重力的作用,使悬浮颗粒按照其密度的差异进行分级。
在此过程中,密度较高的矿石颗粒沉降得更快,密度较低的矿石颗粒则会悬浮在上层。
通过调整设备参数,如介质密度、液体流速和设备结构等,可以实现不同密度矿石的有效分离。
然而,重介质选矿也存在一些限制。
首先,该方法的处理能力有限,通常适用于颗粒大小在0.5-50毫米范围内的矿石。
其次,该方法对矿石原料的物理性质要求较高,包括矿石颗粒大小、密度和形状等。
因此,在实际应用中,需要根据特定的矿石特点进行操作参数的优化和调整。
总之,重介质选矿是一种常用的物理选矿方法,适用于处理不同密度的金属和非金属矿石。
其基本原理是利用悬浮在介质中的固体颗粒在重力和浮力的共同作用下的沉降速度差异,实现矿石的有效分离。
重介质选矿具有高效性和精确度,但也有一些限制。
因此,在实际应用中,需要根据具体矿石的特点进行适当调整和改进。
重介质分选原理

重介质分选原理
嘿,咱今儿来聊聊重介质分选原理呀!你说这重介质分选,就好像是一场奇妙的“选拔大赛”。
想象一下,一堆物料就像是一群选手,站在起跑线上等着被挑选呢。
重介质呢,就是这场大赛的关键评判标准。
它就像是一把神奇的尺子,能把不同的物料区分开来。
那些符合要求的物料,就会被重介质这把尺子“量”出来,然后被选中啦。
比如说吧,有些物料比较重,就像那些实力超强的选手,一下子就能在重介质中“脱颖而出”,乖乖地沉到下面去;而有些物料比较轻呀,就像是实力稍逊一筹的选手,就会浮在上面啦。
这重介质分选可有意思了,它就像是一个超级聪明的裁判,能准确地把不同的物料分清楚。
而且它还特别稳定可靠呢,不会因为一点小干扰就出错。
你看啊,在实际应用中,重介质分选可帮了大忙了。
不管是选矿石啦,还是处理其他物料,它都能发挥巨大的作用。
这不就像是一个万能的工具,啥时候需要它,它都能顶上。
咱再想想,要是没有重介质分选,那得多麻烦呀!得用多少其他复杂的方法才能达到同样的效果呢。
所以说呀,重介质分选可真是个了不起的发明。
它就像是一个默默无闻的英雄,在背后默默地工作着,却能给我们带来巨大的好处。
它让我们的生产更高效,让我们能得到更纯净、更好的物料。
而且哦,重介质分选还在不断发展和进步呢。
科学家们一直在研究怎么让它变得更厉害,更精准。
说不定以后呀,它能分选的东西更多,效果更好呢!
总之呢,重介质分选原理真的很神奇,很重要!它就像是我们工业生产中的一把利剑,帮我们披荆斩棘,取得更好的成果。
咱可得好好感谢这个伟大的发明,让我们的生活变得更美好呀,你说是不是?。
重介质选煤
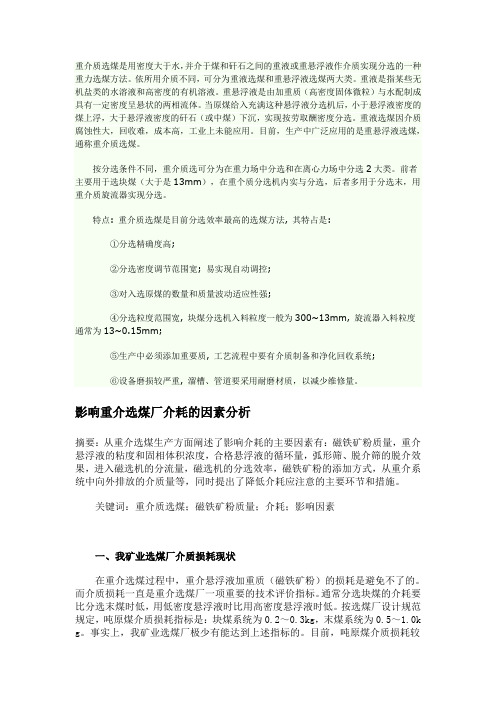
重介质选煤是用密度大于水,并介于煤和矸石之间的重液或重悬浮液作介质实现分选的一种重力选煤方法。
依所用介质不同,可分为重液选煤和重悬浮液选煤两大类。
重液是指某些无机盐类的水溶液和高密度的有机溶液。
重悬浮液是由加重质(高密度固体微粒)与水配制成具有一定密度呈悬状的两相流体。
当原煤给入充满这种悬浮液分选机后,小于悬浮液密度的煤上浮,大于悬浮液密度的矸石(或中煤)下沉,实现按劳取酬密度分选。
重液选煤因介质腐蚀性大,回收难,成本高,工业上未能应用。
目前,生产中广泛应用的是重悬浮液选煤,通称重介质选煤。
按分选条件不同,重介质选可分为在重力场中分选和在离心力场中分选2大类。
前者主要用于选块煤(大于是13mm),在重个质分选机内实与分选,后者多用于分选末,用重介质旋流器实现分选。
特点: 重介质选煤是目前分选效率最高的选煤方法, 其特占是:①分选精确度高;②分选密度调节范围宽; 易实现自动调控;③对入选原煤的数量和质量波动适应性强;④分选粒度范围宽, 块煤分选机入料粒度一般为300~13mm, 旋流器入料粒度通常为13~0.15mm;⑤生产中必须添加重要质, 工艺流程中要有介质制备和净化回收系统;⑥设备磨损较严重, 溜槽、管道要采用耐磨材质,以减少维修量。
影响重介选煤厂介耗的因素分析摘要:从重介选煤生产方面阐述了影响介耗的主要因素有:磁铁矿粉质量,重介悬浮液的粘度和固相体积浓度,合格悬浮液的循环量,弧形筛、脱介筛的脱介效果,进入磁选机的分流量,磁选机的分选效率,磁铁矿粉的添加方式,从重介系统中向外排放的介质量等,同时提出了降低介耗应注意的主要环节和措施。
关键词:重介质选煤;磁铁矿粉质量;介耗;影响因素一、我矿业选煤厂介质损耗现状在重介选煤过程中,重介悬浮液加重质(磁铁矿粉)的损耗是避免不了的。
而介质损耗一直是重介选煤厂一项重要的技术评价指标。
通常分选块煤的介耗要比分选末煤时低,用低密度悬浮液时比用高密度悬浮液时低。
第四章 重介质选矿

第四章 重介质选矿4.4.1 概述重介质选矿:指矿粒在重介质中进行分选的过程。
重介质 :是指密度大水的重液或重悬浮液流体 ,即密度大于1.0的重液或中悬浮流体,在重力选矿过程中,通常都采用密度低于入选矿粒密度的水或空气作为分选介质 。
原理:重介质选矿法是当前最先进的一种重力选矿法,它的基本原理是阿基米德原理,即浸在介质里的物体受到的浮力等于物体所排开的同体积介质的重量。
物体在介质中所受重力G 0的大小与物体的体积、物作与介质间的密度差成正比;G 0的方向只取决于(δ-ρzj )值的符号。
凡密度大于分选介质密度的矿粒, 为正值,矿粒在介质中下沉;反之 为负值,矿粒即上浮。
在重介分选机中,物料在重介质作用下按密度分选为两种产品,分别收集这两种产品,即可达到按密度选矿的目的。
因此,在重介质选矿过程中,介质的性质(主要是密度)是选到的最重要的因素。
gV F G G zj )(0ρδ-=-=发展: 1858年有人提出用锰、钡、钙的氯化物溶液作为分选介质进行选煤,但因介质难于回收,致使成本昂贵,未能获得推广使用。
1917年出现使用水砂混合物作为重介质分选煤炭,但效果受到局限,一般仅用于选分易选的动力煤。
1926年苏联工程师E·A·斯列普诺夫首先提出使用稳定悬浮液的重介质选煤法。
以后,重介质选矿法便开始逐渐获得广泛应用。
至今,除重介质选煤是选煤的重要方法之外,也可应用于金属矿石、黑色金属矿石、贵金属矿石、稀有金属矿石及其它物料的分选。
特点:优点:1)分选效率和分选精度都高于其它选煤方法。
块煤:ηmax = 99.5% ,E可达0.02~0.03;末煤:ηmax = 99%,E可达0.05。
2)分选密度调节范围宽跳汰:一般,1.45~1.9;重介:1.35~1.9 , 重介质旋流器:1.3~2.0。
3)分选粒度范围宽块煤:1000~6 mm末煤旋流器:50~0.15 mm4)适应性强对精煤质量变化时,灰分可按要求变。
重介质选矿以及常用的重介质
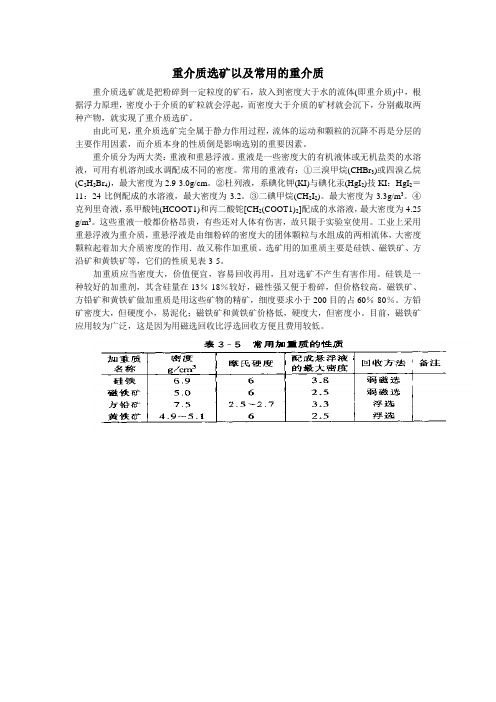
重介质选矿以及常用的重介质重介质选矿就是把粉碎到一定粒度的矿石,放入到密度大于水的流体(即重介质)中,根据浮力原理,密度小于介质的矿粒就会浮起,而密度大于介质的矿材就会沉下,分别截取两种产物,就实现了重介质选矿。
由此可见,重介质选矿完全属于静力作用过程,流体的运动和颗粒的沉降不再是分层的主要作用因素,而介质本身的性质倒是影响选别的重要因素。
重介质分为两大类:重液和重悬浮液。
重液是一些密度大的有机液体或无机盐类的水溶液,可用有机溶剂或水调配成不同的密度。
常用的重液有:①三溴甲烷(CHBr3)或四溴乙烷(C2H2Br4),最大密度为2.9-3.0g/cm。
②杜列液,系碘化钾(KI)与碘化汞(HgI2)技KI:HgI2=11:24比例配成的水溶液,最大密度为3.2。
③二碘甲烷(CH2I2)。
最大密度为3.3g/m3。
④克列里奇液,系甲酸钝(HCOOT1)和丙二酸铊[CH2(COOT1)2]配成的水溶液,最大密度为4.25 g/m3。
这些重液一般都价格昂贵,有些还对人体有伤害,故只限于实验室使用。
工业上采用重悬浮液为重介质,重悬浮液是由细粉碎的密度大的团体颗粒与水组成的两相流体,大密度颗粒起着加大介质密度的作用.故又称作加重质。
选矿用的加重质主要是硅铁、磁铁矿、方沿矿和黄铁矿等,它们的性质见表3-5。
加重质应当密度大,价值便宜,容易回收再用,且对选矿不产生有害作用。
硅铁是一种较好的加重剂,其含硅量在13%-18%较好,磁性强又便于粉碎,但价格较高。
磁铁矿、方铅矿和黄铁矿做加重质是用这些矿物的精矿,细度要求小于200目的占60%-80%。
方铅矿密度大,但硬度小,易泥化;磁铁矿和黄铁矿价格低,硬度大,但密度小。
目前,磁铁矿应用较为广泛,这是因为用磁选回收比浮选回收方便且费用较低。
重介质选矿实施方案
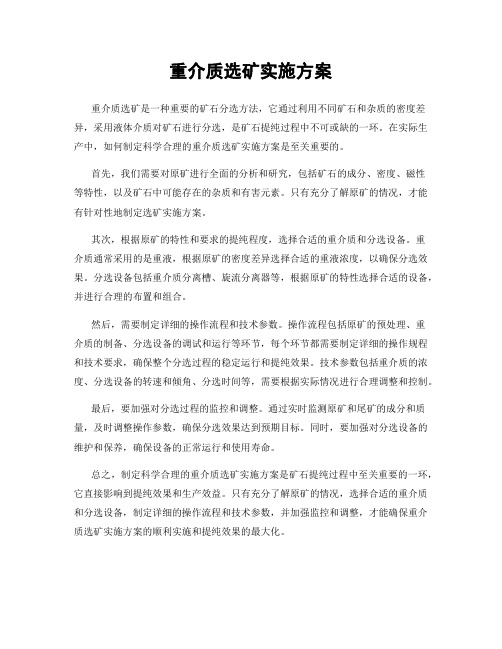
重介质选矿实施方案
重介质选矿是一种重要的矿石分选方法,它通过利用不同矿石和杂质的密度差异,采用液体介质对矿石进行分选,是矿石提纯过程中不可或缺的一环。
在实际生产中,如何制定科学合理的重介质选矿实施方案是至关重要的。
首先,我们需要对原矿进行全面的分析和研究,包括矿石的成分、密度、磁性
等特性,以及矿石中可能存在的杂质和有害元素。
只有充分了解原矿的情况,才能有针对性地制定选矿实施方案。
其次,根据原矿的特性和要求的提纯程度,选择合适的重介质和分选设备。
重
介质通常采用的是重液,根据原矿的密度差异选择合适的重液浓度,以确保分选效果。
分选设备包括重介质分离槽、旋流分离器等,根据原矿的特性选择合适的设备,并进行合理的布置和组合。
然后,需要制定详细的操作流程和技术参数。
操作流程包括原矿的预处理、重
介质的制备、分选设备的调试和运行等环节,每个环节都需要制定详细的操作规程和技术要求,确保整个分选过程的稳定运行和提纯效果。
技术参数包括重介质的浓度、分选设备的转速和倾角、分选时间等,需要根据实际情况进行合理调整和控制。
最后,要加强对分选过程的监控和调整。
通过实时监测原矿和尾矿的成分和质量,及时调整操作参数,确保分选效果达到预期目标。
同时,要加强对分选设备的维护和保养,确保设备的正常运行和使用寿命。
总之,制定科学合理的重介质选矿实施方案是矿石提纯过程中至关重要的一环,它直接影响到提纯效果和生产效益。
只有充分了解原矿的情况,选择合适的重介质和分选设备,制定详细的操作流程和技术参数,并加强监控和调整,才能确保重介质选矿实施方案的顺利实施和提纯效果的最大化。
常用的重介质有哪些?
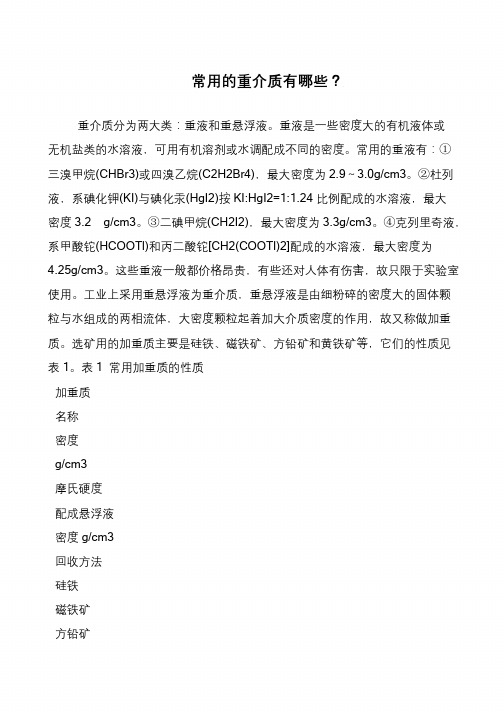
书山有路勤为径,学海无涯苦作舟
常用的重介质有哪些?
重介质分为两大类:重液和重悬浮液。
重液是一些密度大的有机液体或
无机盐类的水溶液,可用有机溶剂或水调配成不同的密度。
常用的重液有:①
三溴甲烷(CHBr3)或四溴乙烷(C2H2Br4),最大密度为2.9~3.0g/cm3。
②杜列液,系碘化钾(KI)与碘化汞(HgI2)按KI:HgI2=1:1.24 比例配成的水溶液,最大
密度3.2 g/cm3。
③二碘甲烷(CH2I2),最大密度为3.3g/cm3。
④克列里奇液,系甲酸铊(HCOOTl)和丙二酸铊[CH2(COOTl)2]配成的水溶液,最大密度为
4.25g/cm3。
这些重液一般都价格昂贵,有些还对人体有伤害,故只限于实验室使用。
工业上采用重悬浮液为重介质,重悬浮液是由细粉碎的密度大的固体颗
粒与水组成的两相流体,大密度颗粒起着加大介质密度的作用,故又称做加重质。
选矿用的加重质主要是硅铁、磁铁矿、方铅矿和黄铁矿等,它们的性质见
表1。
表1 常用加重质的性质
加重质
名称
密度
g/cm3
摩氏硬度
配成悬浮液
密度g/cm3
回收方法
硅铁
磁铁矿
方铅矿。
重介质粉国家化验标准

重介质粉国家化验标准重介质粉是一种常见的工业原料,广泛应用于建筑材料、化工、冶金等行业。
为了保证重介质粉的质量和安全性,国家制定了一系列的化验标准,以便对重介质粉进行质量监管和检测。
本文将对重介质粉国家化验标准进行详细介绍,以便相关行业从业人员和监管部门了解相关标准。
首先,重介质粉国家化验标准主要包括外观、化学成分、颗粒度、水分含量、杂质含量等方面的检测要求。
外观检测主要包括颜色、形状、表面光洁度等指标,化学成分检测则包括主要元素含量、有害元素含量等指标。
颗粒度检测是指对重介质粉颗粒大小和分布进行检测,水分含量和杂质含量则是对重介质粉的纯度和干燥程度进行检测。
这些检测项目的设立,旨在保证重介质粉的质量和稳定性,以及对使用者的安全保障。
其次,重介质粉国家化验标准的制定是基于相关法律法规和行业标准的要求,旨在规范生产企业的生产行为,保障产品质量,维护消费者权益。
在实际操作中,生产企业需要严格按照国家化验标准进行生产,并委托有资质的检测机构对产品进行检测,确保产品符合国家标准要求。
同时,监管部门也会对生产企业进行定期检查和抽样检测,以确保产品质量和安全性。
此外,重介质粉国家化验标准的实施对于行业发展和产品质量提升具有重要意义。
一方面,严格的化验标准可以促使企业加强生产管理,提高产品质量,增强企业竞争力。
另一方面,化验标准的实施可以保障产品质量,增强消费者信心,促进市场健康发展。
因此,重介质粉国家化验标准的制定和实施对于行业和消费者都具有积极的意义。
总之,重介质粉国家化验标准的制定和实施是为了保障产品质量和消费者权益,促进行业健康发展。
相关行业从业人员和监管部门应当加强对化验标准的理解和执行,共同维护产品质量和市场秩序。
希望本文对重介质粉国家化验标准有所帮助,谢谢阅读!。
- 1、下载文档前请自行甄别文档内容的完整性,平台不提供额外的编辑、内容补充、找答案等附加服务。
- 2、"仅部分预览"的文档,不可在线预览部分如存在完整性等问题,可反馈申请退款(可完整预览的文档不适用该条件!)。
- 3、如文档侵犯您的权益,请联系客服反馈,我们会尽快为您处理(人工客服工作时间:9:00-18:30)。
4.3.1.4 影响重悬浮液性质的因素
影响重悬浮液性质的因素主要包括悬浮液的固体 体积分数、加重质的密度、粒度和颗粒形状等。 固体体积分数影响重悬浮液的密度和粘度,悬浮 液的粘度随固体体积分数的增加而增加,存在临 界固体体积分数。
加重质的密度影响重悬浮液的密度,颗粒粒度 和形状影响悬浮液的粘度和稳定性。
分选:
介质回收:
介质的净化与再生:
从分选原理来看,重介质分选只和密度有关, 与粒度、形状无关,实际中与颗粒的密度有较 大关系。 主要是细粒级
用重介质分选煤时,给料的下限为3-6mm,上 限为300-400mm。用重介质分选金属矿石时, 给料的下限为1.5-3.0mm,上限为50-150mm, 若用重介质旋流器分选,给料粒度下限可以降 低到0.5-1.0mm。
优点:结构简单、运转可靠、便于操作,介 质循环量小。 缺点:分选面积小。
4.3.2.3 重介质振动溜槽
4.3.2.4
重介质旋流器
旋转重介质流 重介质流的快速旋转,加重质颗粒受到了相当大 的离心力场作用,使得加重质颗粒中密度较高、 粒度较粗的颗粒,在离心力作用下向器壁及底部 沉降,因而悬浮液受到了浓缩作用,导致了悬浮 液其密度在整个旋流器内呈不均匀分布。 分布规律是:悬浮液密度由中央向外随半径的增 加而增高;若旋流器正立安置,由上而下,则悬 浮液密度的分布是由小到大。
4.3重介质分选
重介质分选:在密度大于1000kg/m3的介质中进行的 分选过程。 加重质:加到水中用于加大介质密度的高密度固体微 粒。
加重质的要求:密度适宜、价格低廉、便于回收。
工业上使用的加重质主要有:
硅铁(6800kg/m3)、方铅矿(7500kg/m3)、磁铁 矿(5000)、黄铁矿(4900-5100)、毒砂(砷黄铁 矿,5900-6200)
4.3.1 重悬浮液的性质
4.3.1.1 重悬浮液的粘度
非均质两相流体,粘度不是定值,而且明显比 分散介质大。
原因主要有以下3方面:
a 悬浮液流动时,由于固体颗粒的存在,既增 加了摩擦面积,又增加了流体层间的速度,从 而导致流动时摩擦阻力增加。
b 固体体积分数较高时,因固体颗粒间的摩 擦、碰撞,使得悬浮液的流动变形阻力增大。
悬浮液的稳定性和粘度的关系。
4.3.2 重介质分选设备 重介分选机种类很多,要求应满足下列条件: (1)构造简单、体积小,但要保证物料在分 选机中有充分的分选分层时间。故要求重介分 选机单位面积处理能力大、运动部件少、运转 可靠、操作及维修方便。 (2)在分选机内全部悬浮液密度保持均匀稳 定。保证物料在分选机内能够精确的按已确定 的分选密度进行分选。分选机内应避免造成过 大的涡流,上升或下降水流速度不应太大,以 减少粒度和形状对分选效果的影响。
4.旋流器锥角 当旋流器直径已定,锥角大小对处理能力及分选 效果的影响与分级用旋流器相似。分选效果将随 锥用的增大而降低,为了获得良好的分选效果, 重介质旋流器应选用较小锥角,我国选煤生产中 所使用的重介质旋流器,锥角多为20°。
5. 溢流口和沉砂口的大小 旋流器溢流口和沉砂口的大小,是影响旋流器工 作的最主要因素。溢流口和底流口的大小对旋流 器处理能力的影响,与分级用水力旋流器相同。
c 由于加重质表面积大,容易自发联结,形 成一种局部或整体的空间网状结构物,以降 低表面能,这种现象称为悬浮液的结构化。
结构化的悬浮液的突出特点:有一定的初始 切应力,外力破坏这一初始切应力后,悬浮 液才开始流动。
4.3.1.2 重悬浮液的密度 密度: 重悬浮液的密度: ρsu=φδ+(1-φ)ρ φ=ρc/(δ(1-c)+ρc) φ容积浓度 c重量浓度
4.3.2.5 重介质涡流旋流器
4.3.2.5 荻纳型重介质涡流旋流器
4.3.2.6 Tri-Flo 型重介质涡流旋流器
4.3.2.7 三产品重介质涡流旋流器
4.3.2.8 斜轮重介质涡流旋流器
4.3.2.9 立轮重介质涡流旋流器
立轮重介质分选机
4.3.3
重介质分选工艺
重介质分选一般包括原料准备、介质制备、 分选、介质回收与再生。 原料准备:破、磨、筛分、分级、洗矿、脱 水 介质制备:加重质的破碎、磨碎
(3)能够迅速地将已经分层的产品从分选机中排 出。不同产物排放不及时,将影响分选机的分选 效果和处理量。
(4)能分选粒级比较宽的物料。因为这样将简化 整个工艺系统,经济上是有利的。 (5)悬浮液的循环量要少。悬浮液的循环量是指 每小时进入分选机的悬浮波总的体积(包括随原 矿加入的及其它地方加入的悬浮液)。因为悬浮 液的数量越大,动力消耗、加重质回收工作量及 加重质的损失量都要增高。
也就是说,入料悬浮液密度虽然不同,但经适当 调节,完全可以达到按同一分选密度进行分选。
因此,当要求的分选密度一定时,生产过程中对 入料悬浮液密度的要求并不十分严格。当然,入 料悬浮液密度如能保持稳定值,生产中可使调整 工作大为减少。
3.入料中矿石与悬浮液的体积比
入料中矿石和悬浮液的体积比,直接影响旋流器 的处理能力和分选效果。 当矿石和悬浮液的体积比增大时,旋流器按矿石 计算的生产能力也增大,但分选效果相应下降。 这是因为体积比增大,旋流器内矿石层增厚,分 层阻力加大,分层速度降低,导致轻、重矿粒易 相互混淆。经研究,从分选效果来看,矿石和悬 浮液的体积比,以1:8为宜,但此时生产能力 较低;为了要保持一定的处理能力 在一般情况下,应采用1:4-1:6为佳。
硅铁:是硅和铁的合金,含硅13-18%最适 合。可用于配制密度3200-3500kg/m3的重 悬浮液,磁选回收。 方铅矿:常用浮选生产的精矿,可配制密度 为3500kg/m3的重悬浮液,浮选回收。 磁铁矿:采用铁品位在60%以上的铁精矿, 可配制的最大密度为2500kg/m3的重悬浮液, 磁铁矿加重质可以磁选回收。
影响重介质旋流器工作的因素 影响重介质旋流器工作的因素,在很多方面与分 级用水力旋流器相似,主要有下列几个方面: 1.进料压力 进料压力高,旋流器的处理能力也大。此外,随 着进料压力的增大,离心力也大,故在一定程度 上,增大进料压力,可使分选过程加速,提高了 分选效果。 如果压力过大,反而对分选不利。
颗粒下沉时 ρef﹥ρsu+ρq
颗粒上升时
ρef﹤ρsu-ρq 介于两项有效密度之间的颗粒,既不能上浮 也不能下沉,得不到有效分选。细小的不规 则形状颗粒更明显。
4.3.1.3 重悬浮液的稳定性
悬浮液的稳定性是指悬浮液保持自身密度、粘 度不变的性能。 通常用加重质颗粒在悬浮液中的沉降速度的倒 数来描述悬浮液的稳定性,称为悬浮液的稳定 性指标,Z=1/v。
4.3.2.1 圆锥型重介质分选机
给料粒度5-50mm,适合处理低密度含量高 的物料。
优点:分选面积大、工作稳定、分离精确度 高。 缺点:需要微细粒加重质,介质循环量大, 需要配置空气压缩装置。
4.3.2.2 鼓型重介质分选机
给料粒度6-150mm,搅动强烈,可以用粒度 较粗的加重质,不适合处理细物料。
因为随着进料压力的加大,旋流器的浓缩作用加强,一方 面实际分选密度增高,另一方面由于悬浮液密度分布更不 均匀,导致分选效果降低。从这个意义上看:增大进料压 力,对分选是不利的。
2.悬浮液密度 悬浮波密度越高,旋流器内物料的实际分选密度 也就越大。 在一般情况下,悬浮液密度可比实际分选密度低 200-400kg/m3,随着要求的分选密度越高,这种 差别也就越大。 在实际生产过程中,入料悬浮液密度与实际分选 密度间的差值,可通过改变给料压力及沉砂口直 径的大小进行调节。