TPS学习心得报告
TPS学习心得体会

TPS学习心得体会第一篇:TPS学习心得体会看了《致新员工书》和《xx的冬天》,大家对任总的为人都非常的肯定,也非常钦佩与感动!其实我们每个人都是爱国的,只是程度不同,所以xx人的崇高目标与理想也是我们全体中国人,甚至全球华人的美好愿望!当老师问大家为什么选择xx时,有些同学坦率地说出了自己的求职经历。
一些著名的跨国it公司给员工的待遇和福利比xx更丰厚,工作环境也比xx轻松自由一点,所以他们更仰慕这类公司,遗憾的是只有xx选择了他们!这是人之常情,可以理解,同学们是诚实的。
当然,有一些同学是怀着与xx人一样产业报国的目标与理想来到这里的,也有部分同学是被任总闪亮伟大的人格魅力所吸引。
总之,无论如何,我们今天都已经相聚!来到这里,我们每个人都有一种期待:通过奋斗来实现自我价值,同时获得合理公平的回报。
绝对公平是没有的,但如果失去了基本的公平,一个团队就不可能团结,分崩瓦解只是迟早的问题。
不过这一点,请大家放心。
xx民主决策和权威管理的经营管理体制可以有效地保证利益分配的相对公平性,以绩效为核心的考核方法可能会一时让你遭受一些委屈,但金子始终会发光的,烧不死的鸟才叫凤凰!xx的文化是开放的、包容和不断发展的,所以只要我们继承这种文化,并将其发扬光大,集体团结一致共同奋斗,我们有理由相信公司的明天会更好!在一个企业里,只有企业的发展得到有效保障,内部员工才能不断地成长,彼此的利益才能得到可靠的保证。
优胜劣汰,是自然界的规律。
事实上,一个企业要活下去是件多么不容易的事情,要想发展就更加艰难。
现在各行各业的竞争都非常激烈,每年都会有许多公司倒掉。
企业要想长期生存,就要寻求活下去的理由和活下去的价值,而活下去的基础是不断提高核心竞争力。
客户是企业的衣食父母,所以xx文化的核心是以客户服务为导向的。
有了好的目标,企业的发展还需要有好的管理体系与执行流程来保证。
公司管理体系与流程的制定是以聚焦客户为中心,服从组织、团队合作、责任敬业、诚实守信和自我批判等的企业价值观和文化为依据的。
TPS体会
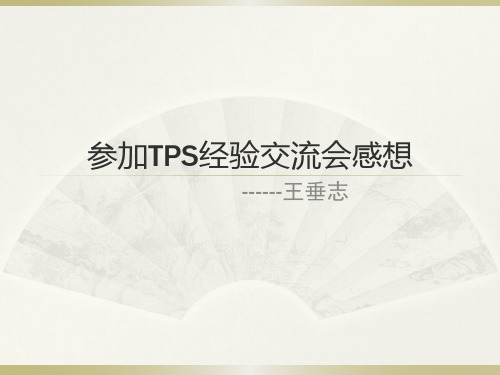
六:推行TIE的基本要求
改善基于需求,以现实现地现物为基础, 目标清楚.评价体系清楚. 不仅要做能做的事,还要向应该做的事挑 战. 作业人员共同参与,作业人员最熟悉现状. 问五次为什么.
推行TIE的基本要求
想到就马上行动,巧迟拙速(坐而言不如 起而行),在不能判定时先试着做。 做设备改善前先进行作业改善。 策略做出后先考虑质量和安全。
四:标准作业
指以人为中心,决定没有浪费的顺序,安 全且高效的生产高品质的产品. 目的:制造方法规则的明确化和进行持续 改进的基础.没有标准的地方就没有改善. 以人为中心和反复的作业. 标准作业的三要素:节拍时间.作业顺序.标 准在制品数量
五:标准作业和改善的步骤
Байду номын сангаас
改善需求的明确化(目标). 首先将现状的作业做成表格图标,即基于 现状的标准化. 以现状为基础找出问题(发现浪费). 改善. 新标准作业票的形成
会议内容
在7月3-4日的会议中,宁良实业的负责人 主要讲解了企业推行TIE的过程,方法;及 推行过程中的心得体会,并进行了推行前 后的对比。参会人员进行了现场参观。 随后全体与会人员进行了讨论,中国汽车 工业协会领导,和滤清器行业协会的领导 对活动进行了总结。
宁良实业推行精益生产一年来取得 的效果
有些内容对我们认为早已经是“过去时”了, 但国外正相反。 欧美和日本管理学家认为,“鞍钢宪法” 的精神实质是“后福特主义”,即对福特式僵 化、以垂直命令为核心的企业内分工理论的挑 战。用眼下流行术语来说,“两参一改三结合” 就是“团队合作”。美国麻省理工学院管理学 教授L· 托马斯明确指出,“鞍钢宪法”是“全 面质量”和“团队合作”理论的精髓,它弘扬 的“经济民主”恰是增进企业效率的关键之一。
企业中层干部学习丰田TPS管理方式的心得体会

企业中层干部学习丰田TPS管理方式的心得体会任何一个企业的生存和发展都离不开管理,所谓管理出效益。
丰田tps管理方式之所以能取得成功,关键在于这种管理方式是科学的,而且对丰田来说是行之有效的。
用管理控制经营,而不是用经营控制管理。
因此在管理和工艺技术方面,提高创新改造的概念,用技术创新来突破传统,用管理创新来增强执行力和执行效果。
管理创新的过程也是一次培养干部,锻炼提高干部素质,淘汰落伍干部的一个过程,通过提高干部的管理能力和素质,从而带动全员提高。
因此干部是决定企业生存和发展的一个关键因素,干部的管理能力提高了才能做好经营工作。
企业要生存和发展就要盈利,盈利的前提就是产品的销售价格问题,既然销售价格不是企业能左右的,那么只有通过降低成本,杜绝浪费,才能使产品具有市场竞争力。
所以我们华尔润公司就应该向丰田,只有不断降低成本,才能使我们的玻璃产品稳稳地占领市场。
一是强调现场的管理,如果企业生产现场一塌糊涂,卫生极差,操作人员在这种环境下也不会生产出好的产品;二是对生产现场异常情况或生产出不合格品时,能得到及时的发现和处理,减少损失。
如我公司油泵房向油罐卸油时,就是现场没有人及时发现溢油,导致几十吨重油外溢,给公司造成一定的经济损失,因此各个部门都要从中吸取教训,确保生产现场在发生意外时能及时发现和处理。
所以管理就是先管好人(引导和教育),中层干部没有管好,就不能带动员工,员工没有管好就不能按操作规程操作,就不能生产出合格的产品,其它工作也不能做好,就会给企业带来损失。
因此企业的管理思想(即企业文化)是最根本的,没有企业正确的管理思想,用任何现代化管理手段都会失败的,这就要求员工有一种自觉性,管理人员在不在都应该一个样,所以要使每位员工有这种自觉性,就需要我们中层干部加大对员工的思想教育,加大跟踪、考核力度。
同时,中层干部要不断改革和创新,通过改革和创新,使全体干部员工共享改革和创新的成果。
即要求我们管理人员要尊重员工 ___,激发员工的积极性,提升员工的能力,那么就要求我们多与员工面对面的沟通,倾听他们___,不断改善工作和生活条件,使他们能安心地工作。
TPS推进考察学习体会

--TPS推进考察学习体会
夏立新 2010年9月
前 言
2010年9月13日-19日,公司组织一行11人,赴日本进行 TPS综合研修,此次研修采取现场调研、参观及沟通等形式,
通过参观日本丰田元町工厂、爱信精机丰田核心子公司、欧
德克斯、中势橡胶、日本精工等丰田公司核心零部件供应商 参观调研,并听取丰田公司出身的平井胜利、大西匡两位专 家“企业人和组织活力提升”及“从企业经营全局角度认识 TPS本质及应用”为主题的讲座,现将此次课题研修收获、亮
3、好夸夸其谈,不愿意埋头做事,不脚
踏实地; 4、不愿意自责,专挑别人的问题(他 责),不敢暴露问题,不能正视问题。
四、重新审视“体系”和“改善”的关系
不能为了建“体系”而建“体系”,适合企业自身的
体系才是最好的体系。 通过此次考察,我切身感受到日本的企业改善无处不 在,有现场的改善,有管理的改善,有经营的改善,改善 的标准化过程本身就是“体系”的构建过程,“改善”本 身就是在建“体系”,那种认为改善不能够构建体系的认 识是极其错误的。 全员改善是根本,必须长期坚持,不能动摇。
产 品 经 营
产品订单改善
商 品 经 营
商品订单改善
2、现有小团队活动主要是在基层开展,
不能够推动业务的改善; 3、仅通过14种QC工具不足以支撑职 能部门的业务改善(T-PK)。
(小团队活动、成果发表会机制、改善提案)
群众性自主改善活动
图:现有TPS推进体系
4、对策:全面引进TQM体制
1)TQM(Total Quality management)定义: 是为了做到人与组织活力及工作质量的提升,并创 建能够柔性(灵活)对应经营环境变化的企业体质而 开展的改善、革新活动。Total包括三个方面,即全员、 全部门、全过程。
丰田模式(TPS)学习心得
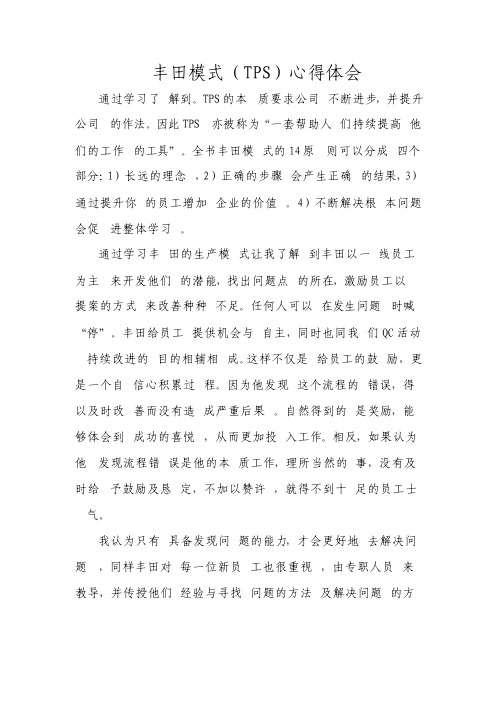
丰田模式(TPS)心得体会通过学习了解到。
TPS的本质要求公司不断进步,并提升公司的作法。
因此TPS亦被称为“一套帮助人们持续提高他们的工作的工具”。
全书丰田模式的14原则可以分成四个部分:1)长远的理念,2)正确的步骤会产生正确的结果,3)通过提升你的员工增加企业的价值。
4)不断解决根本问题会促进整体学习。
通过学习丰田的生产模式让我了解到丰田以一线员工为主来开发他们的潜能,找出问题点的所在,激励员工以提案的方式来改善种种不足。
任何人可以在发生问题时喊“停”。
丰田给员工提供机会与自主,同时也同我们QC活动持续改进的目的相辅相成。
这样不仅是给员工的鼓励,更是一个自信心积累过程。
因为他发现这个流程的错误,得以及时改善而没有造成严重后果。
自然得到的是奖励,能够体会到成功的喜悦,从而更加投入工作。
相反,如果认为他发现流程错误是他的本质工作,理所当然的事,没有及时给予鼓励及恳定,不加以赞许,就得不到十足的员工士气。
我认为只有具备发现问题的能力,才会更好地去解决问题,同样丰田对每一位新员工也很重视,由专职人员来教导,并传授他们经验与寻找问题的方法及解决问题的方法。
当然,首先要学会独立,不能依靠他人来完成自己的事,若是这样永远不会成长。
丰田非常重视方法。
无论是生产还是在原物料上,他们都会想方设法去降低一切能降低的成本。
如:丰田帮助供应商找到流程的上错误,来降低自己的原物料成本。
不但降低了供应商自己的成本,也降低了自己的成本。
大多企业都不会去做这样的事情,认为我帮他来解决问题降低成本谁为帮我解决问题降低成本啊?而丰田却相反主动极枳去帮助供应商解决问题来达到降低自己的原物料成本。
丰田重视过程管理。
让生产设备具有发现问题并能立即停止生产的能力。
2023年最新丰田tps培训心得,ps培训感想优质(五篇)
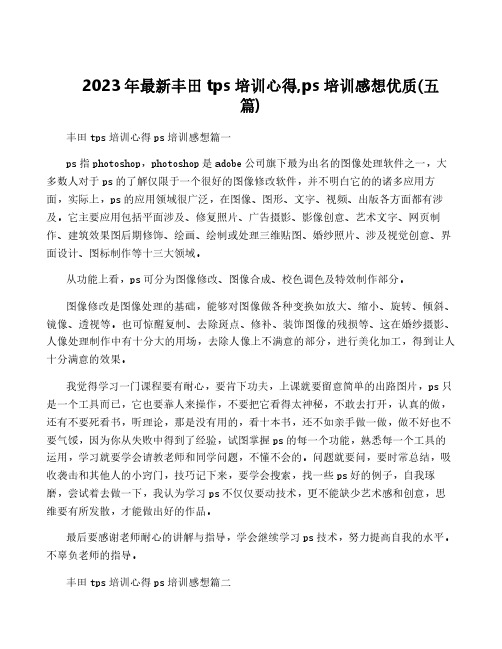
2023年最新丰田tps培训心得,ps培训感想优质(五篇)丰田tps培训心得ps培训感想篇一ps指photoshop,photoshop是adobe公司旗下最为出名的图像处理软件之一,大多数人对于ps的了解仅限于一个很好的图像修改软件,并不明白它的的诸多应用方面,实际上,ps的应用领域很广泛,在图像、图形、文字、视频、出版各方面都有涉及。
它主要应用包括平面涉及、修复照片、广告摄影、影像创意、艺术文字、网页制作、建筑效果图后期修饰、绘画、绘制或处理三维贴图、婚纱照片、涉及视觉创意、界面设计、图标制作等十三大领域。
从功能上看,ps可分为图像修改、图像合成、校色调色及特效制作部分。
图像修改是图像处理的基础,能够对图像做各种变换如放大、缩小、旋转、倾斜、镜像、透视等。
也可惊醒复制、去除斑点、修补、装饰图像的残损等、这在婚纱摄影、人像处理制作中有十分大的用场,去除人像上不满意的部分,进行美化加工,得到让人十分满意的效果。
我觉得学习一门课程要有耐心,要肯下功夫,上课就要留意简单的出路图片,ps只是一个工具而已,它也要靠人来操作,不要把它看得太神秘,不敢去打开,认真的做,还有不要死看书,听理论,那是没有用的,看十本书,还不如亲手做一做,做不好也不要气馁,因为你从失败中得到了经验,试图掌握ps的每一个功能,熟悉每一个工具的运用,学习就要学会请教老师和同学问题,不懂不会的。
问题就要问,要时常总结,吸收袭击和其他人的小窍门,技巧记下来,要学会搜索,找一些ps好的例子,自我琢磨,尝试着去做一下,我认为学习ps不仅仅要动技术,更不能缺少艺术感和创意,思维要有所发散,才能做出好的作品。
最后要感谢老师耐心的讲解与指导,学会继续学习ps技术,努力提高自我的水平。
不辜负老师的指导。
丰田tps培训心得ps培训感想篇二photoshop是科学与艺术的结合,但最终看的是艺术效果。
美术功底扎实与否是影响您将来平面作品水平高低的重要因素,photoshop只是一个得力的工具。
学习丰田生产方式的心得体会

Remember, only your smile can make you find light in the endless darkness.(页眉可删)学习丰田生产方式的心得体会学习丰田生产方式的心得体会1日本的产品在世界上一向以简洁小巧、精致、质量好、功能先进等优点著称。
为了持续产品竞争力的不断提升,务必降低产品价格,同时保证产品品质持续原有水平,甚至超越原有产品,因此想方设法降低成本、提高科技含量,成为了日本公司重点研究的课题。
对于大批量制造,从流水线上生产出的产品而言,原材料成本和管理成本构成了日本产品的主要成本。
由于日本资源有限,产品的原材料大多进口,成本不容易控制,因此如何控制管理成本是决定产品价格能否下降的主要因素。
"即使是干燥的毛巾,如果动脑筋也能让它挤出水",这句名言出自丰田汽车工业社长丰田英二。
多数企业在谈到如何改善管理提高效率时总以人员配备合理、生产效率已经很高等等的理由来表示公司的效率已没有能够提升的空间。
然而用丰田的生产方式来对照企业现有的生产方式仍然能够发现有许多不足,似乎还有许多"水分"能够拧出。
消除浪费是丰田生产方式的唯一目的。
消除浪费是降低成本的有效手段。
在制造过程成本中,丰田总结了7种浪费。
生产过剩的浪费、制造不良品的浪费、停工等活的浪费、动作上的浪费、搬运的浪费、加工本身的浪费、库存的浪费。
丰田将浪费的定义范围扩大化,把只使成本增加而不产生附加价值的作业都称为浪费,以上7种浪费即是"干毛巾中的水分".丰田认为控制并改善这些浪费就能提高效率并且高品质的生产。
丰田生产实现消除浪费的两大支柱是,及时化与自化。
及时化是指在需要的时候按照需要的量生产需要的产品供给各工序。
多数企业认为机器及员工在8小时内不停工作,生产商品就是机器利用率以及人工效率最大化了。
丰田则认为这样会生产出很长一段时间销售不出去的产品,这样的结果有两个缺点:1、流动资金占用率提高了。
【最新文档】丰田模式,原则9,学习体会-推荐word版 (10页)

本文部分内容来自网络整理,本司不为其真实性负责,如有异议或侵权请及时联系,本司将立即删除!== 本文为word格式,下载后可方便编辑和修改! ==丰田模式,原则9,学习体会篇一:丰田模式(TPS)学习心得丰田模式(TPS)心得体会通过学习了解到。
TPS的本质要求公司不断进步,并提升公司的作法。
因此TPS 亦被称为“一套帮助人们持续提高他们的工作的工具”。
全书丰田模式的14原则可以分成四个部分:1)长远的理念,2)正确的步骤会产生正确的结果,3)通过提升你的员工增加企业的价值。
4)不断解决根本问题会促进整体学习。
通过学习丰田的生产模式让我了解到丰田以一线员工为主来开发他们的潜能,找出问题点的所在,激励员工以提案的方式来改善种种不足。
任何人可以在发生问题时喊“停”。
丰田给员工提供机会与自主,同时也同我们QC活动持续改进的目的相辅相成。
这样不仅是给员工的鼓励,更是一个自信心积累过程。
因为他发现这个流程的错误,得以及时改善而没有造成严重后果。
自然得到的是奖励,能够体会到成功的喜悦,从而更加投入工作。
相反,如果认为他发现流程错误是他的本质工作,理所当然的事,没有及时给予鼓励及恳定,不加以赞许,就得不到十足的员工士气。
我认为只有具备发现问题的能力,才会更好地去解决问题,同样丰田对每一位新员工也很重视,由专职人员来教导,并传授他们经验与寻找问题的方法及解决问题的方法。
当然,首先要学会独立,不能依靠他人来完成自己的事,若是这样永远不会成长。
丰田非常重视方法。
无论是生产还是在原物料上,他们都会想方设法去降低一切能降低的成本。
如:丰田帮助供应商找到流程的上错误,来降低自己的原物料成本。
不但降低了供应商自己的成本,也降低了自己的成本。
大多企业都不会去做这样的事情,认为我帮他来解决问题降低成本谁为帮我解决问题降低成本啊?而丰田却相反主动极枳去帮助供应商解决问题来达到降低自己的原物料成本。
丰田重视过程管理。
让生产设备具有发现问题并能立即停止生产的能力。
物流公司学习丰田TPS管理心得体会

物流公司学习丰田TPS管理心得体会物流公司学习丰田tps管理心得体会学习丰田tps管理,让我想到的最多的一个是:tps能给我们带来什么。
丰田的tps管理方式,依靠它独特的管理理念、成本理念、可视化的管理方式、自主的管理方式、尊重人性的管理方法、中层驱动的执行理念这一整套的管理方式,构筑了丰田自律的神经控制。
丰田依靠它的tps管理方式,造就了它规模世界第三,产量世界第二、而其利润世界第一的骄人成绩。
纵观整个tps管理方式,从宏观的角度,从企业的角度讲,我们华尔润要学习它先进的管理方式,就要先弄清楚差距在那里?最大的差距有两点:第一,管理是绝对的。
第二,中层驱动的执行理念。
丰田认为,真正持久决定企业价值的是企业的内部管理,我一直推崇的观念是攘外必先安内,要想在激烈的市场竞争中占有一席之地,就必须抓好内部管理,自下而上的一整套执行链是企业提高执行力的关键,只有做了这点,才能一致对外。
历史上封建社会每一个鼎盛朝代的衰落甚至灭亡,无外乎都是由一个因素引起的——内忧外患,在外强劲敌的吞噬下,朝延内部又发生内争。
就算是衰落或者灭亡,也不能把责任全部都推到那些ceo的身上,明崇祯帝朱由检是一个很好的例子,人说:“明朝灭亡,不亡于崇祯,而亡于万历”崇祯是想振兴大明,也有能力振兴大明,但他没有从根本上解决内部问题。
集团内部的腐蚀让他这个本身应该很英明的皇帝成了断送大明江山的耻徒,最终只求得煤山一吊。
所以,真正成功的企业变革,一定要从中层发起。
由面及点,从微观的角度,从部门的角度讲,在物流科的管理过程中,它更是一套适合物流科管理方式。
我们要学tps的很多。
做好部门管理工作首先是做好内部管理,实施分级管理,平衡协调内部关系,体现人性化管理,最终才能成为劲往一处使的实干团体。
不能依靠erp系统提高成品库管理水平,更主要是以个人为管理单位,以班组为管理对象,体现以我为主的管理方式。
真正实现管理出效益。
其二、成本制胜,丰田的“成本论”指出:企业利润是市场价格减去成本,产品的售价是市场决定,而非企业决定,企业要获得更多的利润,必须无止境的降低成本,用丰田的另一句话是:无止境的消除浪费。
学习丰田“TPS”管理心得体会

学习丰田“TPS”管理心得体会丰田生产方式,也被称为丰田生产系统(Toyota Production System,简称“TPS”)。
自20世纪50年代起,丰田开始研究如何通过优化生产流程,降低成本、提升质量并提高效率。
这些实践不仅让丰田企业变成业内赫赫有名的企业,还成为了全球范围内的管理范例。
我对丰田“TPS”进行了深入的研究,并通过实践体验来领悟这个管理系统的核心思想,以下是我个人的体会和心得。
1. KPI的重要性“KPI”是丰田生产方式中至关重要的一环。
KPI全称为“Key Performance Indicator”,直译为“关键绩效指标”。
这是一种衡量工作表现的方法,在丰田生产方式中,每个岗位的KPI不同。
KPI会被定期评估和监控,以确保流程和工作能够控制和改善。
在丰田生产方式中,每个岗位的工作职责和KPI都明确而具体。
KPI会反映工作的量化指标和效果。
同时,员工会对自己的KPI进行自我评估,这些评估结果也会通过演练等各种形式被反馈和纠正。
这些KPI考核不单单是对员工工作表现的量化,更是推动公司整体运营的关键因素。
通过KPI,丰田可以明确条理地了解企业的发展状况,并一步一步提高运营效率。
对于企业及员工来说,KPI的实施能够提高整个企业的竞争力。
2. 精益生产和严密监控丰田试图通过“精益生产”的概念来概括他们的生产方式。
此概念涉及到简化和最大化工作流程、减少废品产量以及避免生产过程中的浪费,该思想从而受惠于企业和消费者。
“严密监控”是融入于“精益生产”的重要概念。
“严密监控”主要是调节生产过程中的异常情况,确保产量与产品质量的高度一致。
这包括了针对整个企业的生产流程的制定,以及对每个生产岗位的严格控制和管理。
通常来说,严密监控可以用标准化来实现。
这种标准化的重要性在于确保所有员工都能在同样的标准下工作,而达成更好地生产效率和产品品质。
3. 思考纪律在丰田生产方式,一个非常重要的概念是“思考纪律”。
TPS学习心得

TPS学习心得第一篇:TPS学习心得TPS推进本质及方法学习心得5月21日上午我非常有幸地参加了深加工事业部组织的TPS推进本质及方法的培训课程,非常感谢深加工事业部领导对这次培训活动的组织及主讲老师一上午的辛劳,我过这次学习收益颇深,学到了很多像生产排计划这样很多对实际非常有作用的知识,下面是我的学习心得:丰田生产方式最早萌芽于1947年。
当时,创始人大野耐一听到美军总司令部说美国人的生产效率是日本的8倍,他就想到人的能力不该有8倍的差别,是不是制造方法不同呢?观察一下车间,他发现公司车床上干活的工人总是抄着手等在那儿,就开始让这个工人再干一台机床。
从使人和机器适当地配合生产开始,丰田公司逐步创造出了1974年公布于众的TPS.TPS是一种以通过消除所有环节上的浪费来缩短产品从生产到客户手中时间从而提升企业竞争力的生产方式。
一般认为,TPS有两大支柱。
其一为Just In Time(JIT)准时生产。
它不采取预测性或计划性的生产,仅在接到客户的订单之后才开始依照订单产品样式、数量及在适当的交货时间之前组织原料进行生产,以降低库存资金积压及呆滞品库存增加的风险。
另一支柱为“人字边的自动化(Jidoka)”—自働化--。
与传统追求“高速度、大产量、多用机”的自动化截然不同,它是以最低的成本制造出“适速化、专用化、小型化”的自动机器,以使不仅大批量而且小批量的产品都能够快速合格地被制造出来。
围绕着这两大支柱的是TPS已经总结出的一系列独特的改善技法,比如“看板化生产”、“后补充生产”“一人工”等等。
其实这些技法还嫌粗放,TPS要求工人在更细的细节上实现这种技法,由此提出了“改善(Kaizen)和连续改善”的基础理念,以把看得见的浪费最大程度地消灭,同时把看不见的浪费也最大程度地消灭。
但是在实际的运用中,许多公司仅仅从形式上去效仿某个方面比如看板管理,而这往往是不能成功的。
TPS是一个系统管理,是一个全员参加的、思想统一的、不断改进的降低成本的系统过程。
最新实践的心得体会 tps心得体会s心得体会(通用7篇)

最新实践的心得体会tps心得体会s心得体会(通用7篇)心得体会是我们在经历一些事情后所得到的一种感悟和领悟。
那么我们写心得体会要注意的内容有什么呢?以下是我帮大家整理的最新心得体会范文大全,希望能够帮助到大家,我们一起来看一看吧。
实践的心得体会篇一TPS,即“丰田生产方式”,是世界上著名的生产管理模式之一。
它的核心是通过消除浪费,优化生产流程,提高生产效率,从而提高产品质量。
在实施TPS过程中,我深感到这种方式对企业的重要性和卓越的价值。
以下是我对TPS 的心得体会。
首先,TPS的核心在于消除浪费。
浪费是造成企业效率低下的根本原因之一。
通过TPS的实施,企业能够在生产过程中挖掘出各种形式的浪费,如等待时间、废品、过程不稳定等,并针对性地进行改进。
在我所在的企业实施TPS 后,我们发现了许多以前忽视的浪费点,并通过改进解决了其中的问题。
例如,我们重新规划了生产流程,通过精确分工和合理的生产安排,大幅减少了物料在生产线上的等待时间,提高了生产效率和产品质量。
其次,TPS要求企业优化生产流程。
生产流程的优化对于企业的发展至关重要。
经过TPS的实施,我们重新审视了整个生产流程,找出了其中繁琐和重复的环节,并进行了相应的优化。
通过简化流程、提高生产效率和减少浪费的最小化,我们成功地提高了产品质量和企业竞争力。
例如,在以前的生产流程中,我们需要多次手动操作,而经过TPS优化后,许多环节可以通过自动化完成,大大提高了生产效率和产品质量。
再次,TPS能够有效提高生产效率。
生产效率是企业的生命线,也是企业竞争力的重要体现。
在我们企业实施TPS后,我们通过各种改进措施,有效提高了生产效率。
例如,我们采用了“车间自动化”系统,将生产过程中的许多环节自动化处理,提高了生产效率和品质稳定性;我们还引进了“零库存”管理模式,减少了库存超额和产能浪费,提高了资金利用率。
这些措施的实施使我们企业的生产效率得到了极大的提升。
另外,TPS也强调员工参与和持续改进。
丰田利润模式心得体会
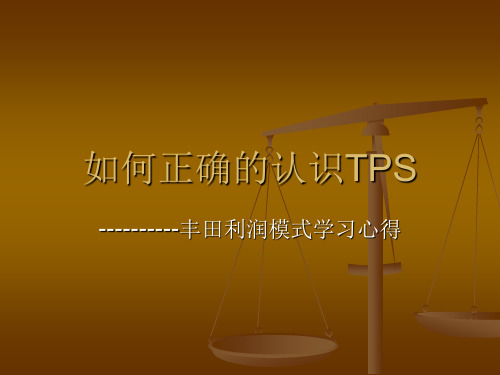
二车间3.12---15号改善的课题: 上粉肉串20g沾浆器具的改善
改善前: 车间在生产上粉肉串20克 时,沾浆用的小盒是小塑 料盒,高度仅有8cm左右, 而串的长度10cm左右,沾 浆时串需要一定的斜度, 方能全部沾好浆。这样就 造成了动作的浪费。 串上粉上浆的速度每人 200支/h
在座的你有如何感想呢?
正确的认识自我与改善
学习时有个同学说回去后马上去做,说了那么多的想法,恨不得立竿见影的出效果, 是的我们学习后确实对各种浪费有了新的认识,对现状有了很多的想法,但不能急于 求成,要考虑到改善后的残留问题,因为改善是一个长期工作是一步一个脚印,用十 二分的辛苦才换取的成绩。(丰田的“看板管理”推了九年) 应正确的对待改善,从自我做起,在改变别人之前先改变自己,以身作则,身先士卒 改善先从小的地方做起,从模仿做起,尽可能先做花钱少的改善。 改善要立即去做而不是三分钟的热血,关键在于持之以恒,并把困难的事情简单 做,简单的事情重复做。
最后与大家分享一下丰田魔鬼十训比较好的几个内容: 创造一个智慧的环境,不要让过去的经验阻碍了今天的智慧 你就是成本,消除无用的浪费,否则就没有提升 先接受任务,再去思考完成的方法 失败的经验需要改善,成功的经验也需要改善 记住-------现状永远是最差的
谢谢大家 盖文波 2012年3月23日
Βιβλιοθήκη 改善后: 沾浆用的是不锈钢小盆,直径 25cm,高度10cm左右,沾浆时 串不需要一定的斜度,直接沾 浆即可。 目的:减少动作的浪费提高 沾浆的速度 效果:串上粉上浆的速度为每 人250支/h。 投入:不锈钢盆20元/个*20个共 需400 元左右。 效率提高了25% 每人每天可节约2小时。 改善人:辛逢春 唐松家
TPS心得——精选推荐
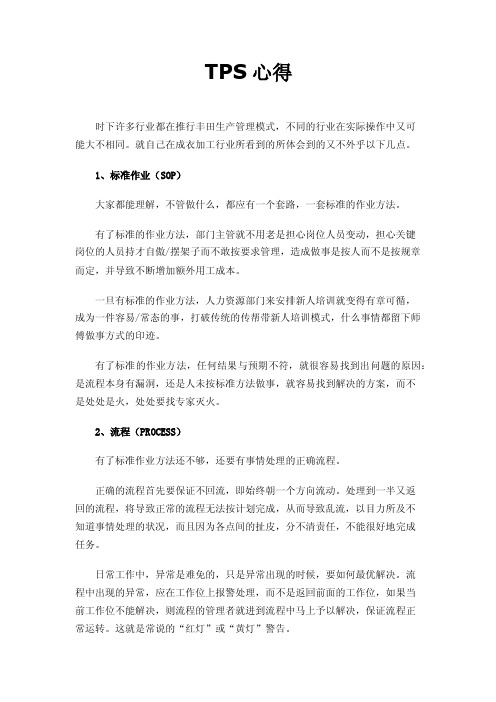
TPS心得时下许多行业都在推行丰田生产管理模式,不同的行业在实际操作中又可能大不相同。
就自己在成衣加工行业所看到的所体会到的又不外乎以下几点。
1、标准作业(SOP)大家都能理解,不管做什么,都应有一个套路,一套标准的作业方法。
有了标准的作业方法,部门主管就不用老是担心岗位人员变动,担心关键岗位的人员持才自傲/摆架子而不敢按要求管理,造成做事是按人而不是按规章而定,并导致不断增加额外用工成本。
一旦有标准的作业方法,人力资源部门来安排新人培训就变得有章可循,成为一件容易/常态的事,打破传统的传帮带新人培训模式,什么事情都留下师傅做事方式的印迹。
有了标准的作业方法,任何结果与预期不符,就很容易找到出问题的原因:是流程本身有漏洞,还是人未按标准方法做事,就容易找到解决的方案,而不是处处是火,处处要找专家灭火。
2、流程(PROCESS)有了标准作业方法还不够,还要有事情处理的正确流程。
正确的流程首先要保证不回流,即始终朝一个方向流动。
处理到一半又返回的流程,将导致正常的流程无法按计划完成,从而导致乱流,以目力所及不知道事情处理的状况,而且因为各点间的扯皮,分不清责任,不能很好地完成任务。
日常工作中,异常是难免的,只是异常出现的时候,要如何最优解决。
流程中出现的异常,应在工作位上报警处理,而不是返回前面的工作位,如果当前工作位不能解决,则流程的管理者就进到流程中马上予以解决,保证流程正常运转。
这就是常说的“红灯”或“黄灯”警告。
3、节奏时间(TIMING)即流程中需时最多的那个工作位的作业时间,因此如果流程中每个工作位的作业时间相差较大时,就会导致较大的人工浪费。
原则上每个工作位的作业时间应相同,才能保证整条线都按同一节奏作业。
实际运作中,因为人员的技能度,熟练度,以及工序本身的难易度不同,导致即使按标准作业时间都一样排出的流程,也不能保证大家的实际作业时间完全一样。
因此任何流程,都应测试,即在大货生产前要做产前培训。
TPS学习心得体会报告

看板是实现Just In Time生产的工具
2019/4/1 14
TPS
看板管理(案例:3C卖场)
货物摆放1台 至货架供客人 观赏&选定,货 物前用小型看 板标示出货物 相关资料
2019/4/1
15
TPS
看板管理(案例:3C卖场)
根据货物的实 际库存摆放对 应数量的小看 板,客人确定 购买时,拿取 需求数量的小 看板至柜台结 帐,且领取货 物。
人才是人财 培养能够 为公司做 贡献的人才
2019/4/1
10
TPS
GPS生产方式的基本
『基本是5S』 标准化 维持
问题表面化
改善
2019/4/1
消除浪费
11
TPS
JIT---缓冲
前工序 ● ● ● ● ● ● ● A 主生产线 B
有缓冲的情况
●●●●●
缓冲是…线与线之间 【连接部分(汇合点)存在 一定的库存】
課程
考核達 成率
100%
I1
新進員工
I
1 -3 個月員工
80%
L
3 -6 個月員工
70%
U
6 個月以上員工
30%
全技能
2019/4/1 25
TPS
2019/4/1
26
TPS
七种浪费
3、生产过剩的浪费----掩盖其他的浪费, 阻碍改善
物
5、搬运的浪费
6、库存的浪费 7、加工本身的浪费 人 2、等待的浪费 1、动作的浪费 质量
TPS
知識管理 / 知識經濟
知識的四層次與八向度 Dimension of Knowledge
智慧 Wisdom 知識 Knowledge 技巧 Know-how 經驗 Experience
TPS学习心得体会
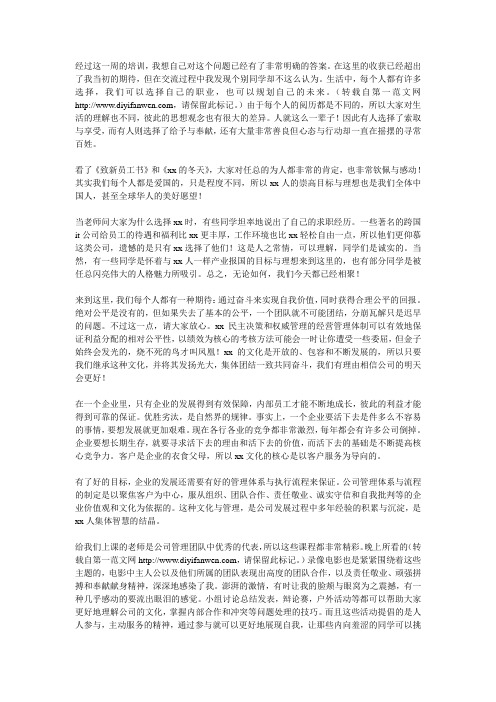
经过这一周的培训,我想自己对这个问题已经有了非常明确的答案。
在这里的收获已经超出了我当初的期待,但在交流过程中我发现个别同学却不这么认为。
生活中,每个人都有许多选择,我们可以选择自己的职业,也可以规划自己的未来。
(转载自第一范文网,请保留此标记。
)由于每个人的阅历都是不同的,所以大家对生活的理解也不同,彼此的思想观念也有很大的差异。
人就这么一辈子!因此有人选择了索取与享受,而有人则选择了给予与奉献,还有大量非常善良但心态与行动却一直在摇摆的寻常百姓。
看了《致新员工书》和《xx的冬天》,大家对任总的为人都非常的肯定,也非常钦佩与感动!其实我们每个人都是爱国的,只是程度不同,所以xx人的崇高目标与理想也是我们全体中国人,甚至全球华人的美好愿望!当老师问大家为什么选择xx时,有些同学坦率地说出了自己的求职经历。
一些著名的跨国it公司给员工的待遇和福利比xx更丰厚,工作环境也比xx轻松自由一点,所以他们更仰慕这类公司,遗憾的是只有xx选择了他们!这是人之常情,可以理解,同学们是诚实的。
当然,有一些同学是怀着与xx人一样产业报国的目标与理想来到这里的,也有部分同学是被任总闪亮伟大的人格魅力所吸引。
总之,无论如何,我们今天都已经相聚!来到这里,我们每个人都有一种期待:通过奋斗来实现自我价值,同时获得合理公平的回报。
绝对公平是没有的,但如果失去了基本的公平,一个团队就不可能团结,分崩瓦解只是迟早的问题。
不过这一点,请大家放心。
xx民主决策和权威管理的经营管理体制可以有效地保证利益分配的相对公平性,以绩效为核心的考核方法可能会一时让你遭受一些委屈,但金子始终会发光的,烧不死的鸟才叫凤凰!xx的文化是开放的、包容和不断发展的,所以只要我们继承这种文化,并将其发扬光大,集体团结一致共同奋斗,我们有理由相信公司的明天会更好!在一个企业里,只有企业的发展得到有效保障,内部员工才能不断地成长,彼此的利益才能得到可靠的保证。
- 1、下载文档前请自行甄别文档内容的完整性,平台不提供额外的编辑、内容补充、找答案等附加服务。
- 2、"仅部分预览"的文档,不可在线预览部分如存在完整性等问题,可反馈申请退款(可完整预览的文档不适用该条件!)。
- 3、如文档侵犯您的权益,请联系客服反馈,我们会尽快为您处理(人工客服工作时间:9:00-18:30)。
30
TPS
根据需求量来定T.T (Tack Time)
生产一个或者一辆必须要用几分钟或者几秒钟 (每月更新一次)
每班工作时间(固定)
TACK TIME=
需求量(每班的生产数量) 每班工作时间(固定)+超时工作时间
实际 TACK=
需求量(每班的生产数量)
Cycle Time (C.T)
2013-7-22
品質是藉由 “ DIRFT” * 來控制
*Do it right first time
第一次就做好
★“Up-stream Action” “ 源流管理” ★ “Self Control by Cell System” “Cell Group別自律管理 ”
2013-7-22 21
TPS
导入:自我品质保证
<第1領域>
重 要
Ex :資材不良&遅延対応 Ex :工程Trouble対応 Ex.:事故対応
Ex.:Skill訓練
Ex.:新Process開発
<第3領域> 不 重 要
Ex.:突然的訪問者
Ex.:飛び込み電話応対 Ex.:無意味な付き合い
2013-7-22
<第4領域>
Ex.・暇潰し Ex.・雑談・お喋り
品質穩 安全 人員管理 人力向上 交期准 日常管理 成本低 知识管理 創造性思考 工作方法 (JM) ECRS:消除﹑結 合﹑更換﹑簡化 自律管理
5
管 理 目 標
物料管理 時間管理 數據 工作教導 (JI)
作业标准化
作業流程
問題解決技能 (JL)
基 本 技 能
2013-7-22
報告技巧 開會和討論 自我品质 管理
課程
考核達 成率
100%
I1
新進員工
I
1 -3 個月員工
80%
L
3 -6 個月員工
70%
U
6 個月以上員工
30%
全技能
2013-7-22 25
TPS
2013-7-22
26
TPS
七种浪费
3、生产过剩的浪费----掩盖其他的浪费, 阻碍改善
物
5、搬运的浪费
6、库存的浪费 7、加工本身的浪费 人 2、等待的浪费 1、动作的浪费 质量
初期Cell线 分时段上料, 减少作业现场 物料堆放。
2013-7-22
42
TPS
物料供料系统转换
物料供料目标:送料到站
推动物料JIT 且物料于仓库 完成分料,并以 定时的量分发 至各站
2013-7-22
43
TPS
2013-7-22
44
2013-7-22
8
TPS
自己實現力~成果和成長循環的力量
體驗/ 在意
C 反省
成果 與 成長
教訓/ 智慧
D 學習
問題當 寶山
A 向上心
自信/ 新的挑戰
P 細心
基本技能
基本人格
成長
自助努力的精神
2013-7-22
成果
9
自己實現力
TPS
GPS→TPS+人才培养
JIT+自働化+追求一人工
Just In Time *在需要的时候,按照需要的量来生产, 搬运需要的东西。 自働化 *机器运作+人类的智慧 *发生异常状况,机器自动停止运作 追求一人工 *均衡工作量,提供实质的工作[均衡化]
多能 工作
拉式 系統 全方位 改善
目視管理
JIT的認知
平均化平准化 流動生產
執行力 燈光顯示板 革新 少人化 同步工程
設備人力生 產方力 5S 信任
消除七大浪費
零件標准化
防呆裝置 設備的轉換
團隊合作
2013-7-22
構思的轉換
以身作責
4
TPS
制造管理之屋-技能
目標方針
2013-7-22
16
TPS
看板管理(案例:3C卖场)
小看板没有代 表已售完,客 人看到「售完」 看板后,可选择 其他商品,销 售员也可根据 「售完」看板 进行补货
2013-7-22
17
TPS
运用看板的条件
前工序 (供应商)
货期 数量 质量 相互信任 遵守100% 的原则 严格做到 均衡化生产 (标准±10%)
Self-Quality Assurance
作业0缺失
Zero Defects Workmanship
22
2013-7-22
TPS
談問題,講真相(象)
2013-7-22
23
TPS
基本技能-工作進行的方法
•現狀把握 •課程找出 •目標設定 •檢討進行方式 •計劃作成 •從日常中實行 •每天循環PDCA
后工序 (客户)
2013-7-22
18
TPS
2013-7-22
19
TPS
It's not the BIG that eat the SMALL …
It’s the FAST that eat the SLOW
2013-7-22
20
TPS
TPI Project <
2.“品質 戦略/ Quality Strategy” >
2013-7-22 33
TPS
解决问题的方式
目标 (goal)
问题 (gap)
实际状况 (current siuation)
2013-7-22
34
TPS
问题的三种时间序列类型
经营层 设定型
管理层
探索型
基层
发生型
2013-7-22
35
TPS
问题的三种时间序列类型
原因导向 目标导向
过去
现在
未来
1.已发生型问题 2.探索型问题 3.未来设定预测问题
TPS心得报告
2013-7-22
1
TPS
2013-7-22
2
TPS
从战术的角度研讨
TPS
2013-7-22 3
TPS
TPS成功关键
TPS是TOP-down的方式 由管理階層帶領員工
目標 方針 TPS 自働化 JIT 看板 方式 現場 中心 標准化 多樣 少量 工作的 概念 以人 為中心
TPS的特征
人才是人财 培养能够 为公司做 贡献的人才
2013-7-22
10
TPS
GPS生产方式的基本
『基本是5S』 标准化 维持
问题表面化
改善
2013-7-22
消除浪费
11
TPS
JIT---缓冲
前工序 ● ● ● ● ● ● ● A 主生产线 B
有缓冲的情况
●●●●●
缓冲是…线与线之间 【连接部分(汇合点)存在 一定的库存】
看板是实现Just In Time生产的工具
2013-7-22 14
TPS
看板管理(案例:3C卖场)
货物摆放1台 至货架供客人 观赏&选定,货 物前用小型看 板标示出货物 相关资料
2013-7-22
15
TPS
看板管理(案例:3C卖场)
根据货物的实 际库存摆放对 应数量的小看 板,客人确定 购买时,拿取 需求数量的小 看板至柜台结 帐,且领取货 物。
2013-7-22
36
TPS
现状问题分析「技能(skill)不足」
对现状问题分析的 二个障碍
能力不足 (Skill)
意愿不足 (Will)
2013-7-22
37
TPS
对问题组织的两种不同思路看法
传统思路(第一种 approach)
问题
原因
对策
新思路(第二种 approach)
原因
问题
对策
2013-7-22
P
計劃的作成
D
計劃的實行
A
計劃的修正
C
進度的確認
2013-7-22
•防止問題的再發 •日程、目標的修正
•確認有無延遲 •進度延遲或其他問題點的原因 •查明原因及處理對策
24
TPS
全技能培训(I、L、U阶)
受訓對象 課程內容
1 .環境認識 2 .禮儀講解 3 . SO P认 识 4 . ESD 5 . R O H S基 本 介 紹 1 .零件識別 2 . 電 動 起 子 基 本认 识 & 操 作 3 . 烙 鐵 基 本认 识 & 操 作 1 . 半 成 品 /目 視 檢 驗 規 范 2 .切板機操作 3 .插件技巧 4 .功能測試 5 .組包裝技巧 1 .生產干部管理職掌 2 . 生 產 日 報 K EY I N 3 .QC七大手法 4 . I E技 能 訓 練 5 .現場管理的核心持續 6 .無駝
2013-7-22
改善的突破口
4、次品、修补的浪费
27
TPS
对浪费的认识--操作工的动作
2013-7-22
28
TPS
对效率的认识
需求量 100个/天
2013-7-22
29
TPS
時間管理Matrix
Productivity 21/ 製造革新
緊
急
不緊急
<第2領域>
Ex.:Manual作り Ex.:“Poka-Yoke” Ex.:予防保全処置 Ex.:改善活動
生产一个或者一辆用了几分钟或者 几秒钟的实测时间
31
TPS
知識管理 / 知識經濟
有效運用知識, 創造競爭優勢 K=(P+I)
S
K=知識 Knowledge
P=人們 People
I=資訊 Information