湿型砂
5. 第1章 湿型砂

铸造用硅砂分级:
根据国家标准GB/T9442—1998的规定,铸造用硅砂 按SiO2含量可分为五级。
表1-1 铸造用硅砂按SiO2含量分级
分级代号
98
96
93
90
85
w(SiO2)(%) ≥98
≥96
≥93
≥90
≥85
分级代号
0.2
0.3
0.5
1.0
2.0
w泥分(%)
≤0.2
≤0.3
≤0.5
≤1.0
3.湿型铸造法
基本特点:型(芯)无需烘干,不存在硬化过程。 主要优点:
生产灵活,效率高,成本低,周期短; 易实现机械化和自动化; 省烘干设备、燃料、电力及空间; 砂箱使用寿命长; 容易落砂。 主要缺点:易夹砂结疤、粘砂、气孔、砂眼、胀砂等。 应用范围:流水生产和手工造型 500Kg以下的铸件 。
4.表干型铸造法
• 影响因素:拉应力、受力破碎前的变形量。
• 变形量:在测定型砂抗拉强度时,试样破碎前的变形, 一般很小。
韧性:型砂的湿压强度(MPa)×变形量(cm)×乘
1000。它表示了型砂由于塑性变形而能吸收能量的性质。
• 韧性的测定 • 落球法:标准抗压试样、
φ50mm,510克钢球,12.7mm 的筛。 • 破碎指数:留在筛网上的型 砂质量占试样质量的比值。 • 表示在冲击条件下的韧性 • 高,表示型砂的起模性好, 过高,流动性差,不够致密。
• 2.1 水分、最适宜干湿程度和紧实率
• (1)水分: 型砂中含水质量百分数
• 测定:称50g型砂,红外烘干105-110℃,4-8min至恒重, 称量质量变化。
•
X=(G-G1)/G×100%
砂型铸造--湿砂铸造

砂型铸造——湿型砂的选用及其检测组员:余柏松、罗凯贤、陈卡、何桂景砂型铸造是最普通的制造,其工艺特点:适用性广,技术灵活性大,生产准备工作相对简单,铸件主要为铸铁;但铸件精度及其表面粗糙度较差,对环境污染比较大。
优点:1、可以铸造外形和内腔十分复杂的毛坯。
如:各种箱体、床身、机架等。
2、适用性广泛,从几克到几百吨的铸件都可以。
3、原材料来源广泛,成本低廉。
如可以熔化铁屑。
4、铸件形状与零件尺寸比较接近,减少切削加工余量。
缺点:1、工序较多,一些工序质量难以保证。
质量不稳定,容易形成废品。
2、铸件中容易出现缩孔和气孔,性能不如锻件,因此对于承载较大载荷的重要零件一般不用铸件。
砂型铸造所包含的范围很广,而砂型是这种铸造工艺的基础,只有把基础搞好,上层建筑才会稳固。
砂型铸造的优缺点很多都与砂型的好坏有关。
比如,砂型铸造所产生粘砂、表面粗糙度等也与砂型的结构,原砂的选用有关,下面要讨论的主要是最基本的湿砂铸造:砂型铸造中使用最多的是粘土砂型。
而粘土砂型可分为湿型、干砂型和表面烘干砂型。
三者之间的主要差别在于:湿型是造好的砂型不经烘干,直接浇入高温金属液体;干砂型是在合箱和浇注前将整个砂型送入窑中烘干;表面烘干砂型只在浇注前对型腔表层用适当方法烘干一定深度(一般5~10mm,大件20mm 以上)。
目前,湿型砂是使用最广泛的、最方便的造型方法,大约占所有砂型使用量的60~70%,但是这种方法还不适合很大或很厚实的铸件。
湿型铸造特点:湿型铸造法的基本特点是砂型(芯)无需烘干,不存在硬化过程。
其主要优点是生产灵活性大,生产率高,生产周期短,便于组织流水生产,易于实现生产过程的机械化和自动化;材料成本低;节省了烘干设备、燃料、电力及车间生产面积;延长了砂箱使用寿命等。
但是,采用湿型铸造,也容易使铸件产生一些铸造缺陷,如:夹砂、结疤、鼠尾、粘沙、气孔、砂眼、胀砂等。
湿型砂用原材料:湿型砂是由原砂、粘土、附加物及水按一定配比组成的。
常用型砂种类

机器造 )’ %’&()*& &.,/&.&.* * — ,.-/*.+ — 2&/)+& ’-/%& +.— — 型活化砂, 铸造机床 铸件
・ 2&, ・
第三篇
造型材料
配 比 (!) 碳酸钠 煤 粉 (以膨润 其他 土为基) 含水量紧实率 ( ! )( ! ) 性 湿 压 热湿拉 透气性 强 度 强 度 能 含泥量 用 其 他 途
%
—
.,/ + -,. &’’ + )’’ %0 + 11 —
0
—
1’(&-’
&’’
1,%
—
—
—
.,% + -,’
2 &’’
%’ + 1% —
1
—
1’(&-’
&’’
-,%
—
—
煤粉 ) + - .,’ + -,’
2 /’
%’ + 1’ —
表.5)5序 号 旧 砂 新 砂
工厂有色合金铸件湿型砂配方及性能实例
第三篇
造型材料
配 比 ( !) 他 含水量 ( !) 性 透气性 能 湿压 紧实 用 途 强度 率 ( !) ("#$) 小型铸 钢件 3 &’’"4 碳 钢件 3 &’’"4 耐 热钢件
序 号 旧 砂
新 砂 膨润土 碳酸钠 糊 精 其 粒度组别 加入量 &’’()’’ &’’ * + && ’,) ’,) + ’,—
震击造 %* *( ,( 0/()-/( — — ./()2/( — !’( 2*)*0 — — — 型背砂, 铸 造灰铸铁 缸体 黏土 0( 2( 0(+.( -( &)’ — %)0 木屑 手工造 2/.)&/. — 1 ,.( &()*( — ,(),. — 型, 铸造灰 铸铁大件
铸造工艺学第二章湿型

第二节 湿型砂性能要求、检测原理及检测方法
• 二、透气性 • 透气性:紧实的型砂能让气体透过而逸出的能力。 • 测定原理:测出气钟内的空气在压力下通过试样 的时间,计算其透气性。
V—通过试样的空气体积;H—试样高度;
S—试样截面积;p—试样前压力(mmH2O); t—2000cm3空气通过试样的时间
第三节 湿型砂用原材料及其质量要求
原砂的质量要求 1. 含泥量
• 原砂的含泥量—指原砂中直径小于0.02mm的细小颗粒的含量。
• 含泥量对湿型砂的性能的影响 ① 原砂中泥分增多,孔隙半径减小,透气性降低。 ② 原砂中泥分增多,湿态抗压强度提高,达到最适宜干湿状态的型砂含水量也提高。 ③ 若原砂的泥分中不含粘土矿物,则 原砂中含泥量增多会使型砂变脆,起模性能变坏。
第二节 湿型砂性能要求、检测原理及检测方法
一、水分、最适宜干湿度和紧实率 • 判断型砂的干湿程度的几种方法
1.
2. 3.
水分(含水量或湿度)--最常用
手捏感觉--经验 紧实率--很多工厂列其为最经常性检 验性能的项目之一 紧实率:锤击后试样体积的压缩程度
紧实率=[(筒高-紧实距离)/筒高] ×100%
第三节 湿型砂用原材料及其质量要求
一、石英质原砂 原砂的分类:
山砂;海砂;湖砂;河砂;风积砂。
成份及形成过程: • 天然硅砂—小颗粒,是由岩石风化形成的。 • 石英砂岩—沉积的石英颗粒被胶体的二氧化硅或氧化铁、碳酸钙等物胶结成块状。 • 石英岩—经过变质而形成的坚固整体的岩石。 • 人造石英砂—坚固岩石经过人工破碎、筛分。
但是,原砂是众多形状和重量各异的砂粒组成的集合,要确定出与其相对应的 假想圆球的直径就成为计算原砂理论比表面积的关键。
1.2 湿砂型
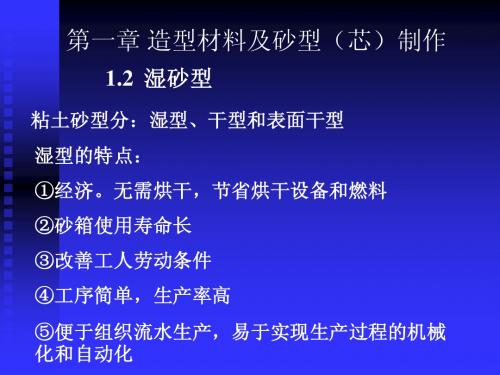
1.2 湿砂型
1.2.1 湿型砂用原材料及质量要求 1. 原砂 2. 粘土 ①分类 ②粘土的表面电荷和交换性阳离子 ③粘土的吸附水分及湿态粘结机理 ④粘土对型砂性能的影响
1.2.1 湿型砂用原材料及质量要求 1. 原砂 2. 粘土: 由细小结晶质 的粘土矿物组 成,化学成分 都是含水的铝 硅酸盐。
1.2 湿砂型
1.2.2 湿型砂性能要求及检测原理 1. 水分、最适宜干湿程度(适宜湿度)和紧实率 最适宜干湿程度的判断方法: ① 水分(含水量) ② 手感法 ③ 紧实率:湿型砂在一定紧实力作用下体积变 化的百分数
1. 水分、最适宜干湿程度(适宜湿度)和紧实率 最适宜干湿程度的判断方法: ③ 紧实率
图1.5 紧实率测定法示意图
一般:手工和机器造型用型砂, 紧实率接近50%;高压造 型和冲击造型,40%~45 %;挤压造型,35%~40 %。
1.2.2 湿型砂性能要求及检测原理 1. 水分、最适宜干湿程度(适宜湿度)和紧实率 2. 透气性 :型砂能让气体透过而逸出的能力
图1.6 透气性测定仪示意图 1-气钟; 2-水筒; 3-三通阀; 4-试样座; 5-试样筒; 6- 标准试样; 7-微压表; 8-阻流孔
1.2.1 湿型砂用原材料及质量要求 1. 原砂 2. 粘土 ③粘土的吸附水分 及湿态粘结机理
图1.4 膨润土的湿态强度(表面联结强度和 桥联结强度之和)与水分含量的关系
1.2 湿砂型
1.2.1 湿型砂用原材料及质量要求 1. 原砂 2. 粘土 ①分类 ②粘土的表面电荷和交换性阳离子 ③粘土的吸附水分及湿态粘结机理 ④粘土对型砂性能的影响
1.2.2 湿型砂性能要求及检测原理 3. 湿态强度
图1.8 型砂强度试验方法示意图 强度的定量表示:用标准 试样在受外力作用下 遭破坏时的应力值表 示。
一、湿型砂的性能

一、湿型砂的性能前言为了保证湿型铸件具有良好的表面质量,必须使用良好性能的型砂。
本文将介绍高质量湿型砂的性能要求、工厂实际应用实例,并分析型砂性能与铸件质量之间的关系。
一般认为使用造型紧实压力150~400kPa的普通震压式造型机,砂型平面硬度才只有70~80度,垂直面下端硬度可能只有50~60度,铸件局部极易产生缩孔、缩松、胀砂和粘砂缺陷。
由于砂型平均密度仅1.2~1.3 g/cm3,称为低密度造型或低压造型。
为了克服上述缺点,出现了气动微震造型机,在压实的同时增添了震动作用,改善了砂型紧实时型砂的流动性能,使压实比压几乎提高了一倍,达到400~700kPa左右,砂型平面硬度大约为80~90度,平均密度可能在1.4~1.5g/cm3范围内。
密度比较均匀,减少了局部缩松、胀砂和粘砂缺陷。
近代化造型机的压实比压有可能提高到700kPa或稍高,所得到砂型表面硬度大约为90~95度,平均密度可达1.5~1.6g/cm3,称为高密度造型方法。
高密度造型的生产效率高、铸件尺寸精度高,机械加工余量少。
应用多触头高压、气冲、挤压(即垂直分型无箱射压造型)、射压、静压等造型机制成砂型都可能达到上述的紧实密度,因而国内外应用日益普遍。
为了具体说明湿型砂的性能和控制范围,本文数据搜集大部分取自上世纪90年代末期及本世纪初中外公开发行刊物。
还有一部分数据是由国内各工厂的工程师提供的,凡属未正式发表过的都不注明工厂名称,所列举数据只是当时情况,并不代表目前实际状况。
本文中列举的各种性能数据,除特殊注明以外,都是从造型处直接取样测得的。
本文中各种性能排列顺序基本上按照日常检验的顺序和常用性。
有关型砂检测方法另有专门文章介绍。
1.紧实率和含水量型砂的手感干湿程度是极为重要的性能,它反映型砂是否处于最适宜的造型状态。
直到1969年才找到用紧实率衡量型砂干湿程度的方法。
湿型砂不可太干,紧实率不可过低,因为型砂中膨润土未被充分润湿,性能较为干脆,起模困难,砂型易碎,表面的耐磨强度低,铸件容易生成砂孔和冲蚀缺陷。
(1)湿型砂的性能要求
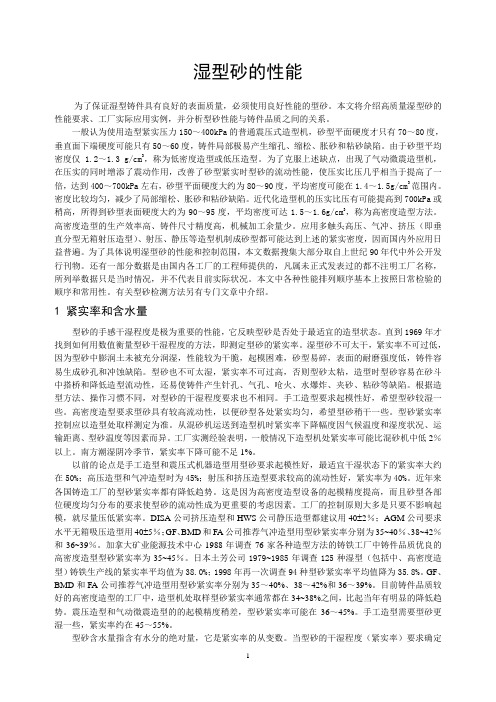
湿型砂的性能为了保证湿型铸件具有良好的表面质量,必须使用良好性能的型砂。
本文将介绍高质量湿型砂的性能要求、工厂实际应用实例,并分析型砂性能与铸件品质之间的关系。
一般认为使用造型紧实压力150~400kPa的普通震压式造型机,砂型平面硬度才只有70~80度,垂直面下端硬度可能只有50~60度,铸件局部极易产生缩孔、缩松、胀砂和粘砂缺陷。
由于砂型平均密度仅1.2~1.3 g/cm3,称为低密度造型或低压造型。
为了克服上述缺点,出现了气动微震造型机,在压实的同时增添了震动作用,改善了砂型紧实时型砂的流动性能,使压实比压几乎相当于提高了一倍,达到400~700kPa左右,砂型平面硬度大约为80~90度,平均密度可能在1.4~1.5g/cm3范围内。
密度比较均匀,减少了局部缩松、胀砂和粘砂缺陷。
近代化造型机的压实比压有可能提高到700kPa或稍高,所得到砂型表面硬度大约为90~95度,平均密度可达1.5~1.6g/cm3,称为高密度造型方法。
高密度造型的生产效率高、铸件尺寸精度高,机械加工余量少。
应用多触头高压、气冲、挤压(即垂直分型无箱射压造型)、射压、静压等造型机制成砂型都可能达到上述的紧实密度,因而国内外应用日益普遍。
为了具体说明湿型砂的性能和控制范围,本文数据搜集大部分取自上世纪90年代中外公开发行刊物。
还有一部分数据是由国内各工厂的工程师提供的,凡属未正式发表过的都不注明工厂名称,所列举数据只是当时情况,并不代表目前实际状况。
本文中各种性能排列顺序基本上按照日常检验的顺序和常用性。
有关型砂检测方法另有专门文章中介绍。
1 紧实率和含水量型砂的手感干湿程度是极为重要的性能,它反映型砂是否处于最适宜的造型状态。
直到1969年才找到如何用数值衡量型砂干湿程度的方法,即测定型砂的紧实率。
湿型砂不可太干,紧实率不可过低,因为型砂中膨润土未被充分润湿,性能较为干脆,起模困难,砂型易碎,表面的耐磨强度低,铸件容易生成砂孔和冲蚀缺陷。
湿型砂

1.粘土砂的紧实率是指湿态的型(芯)砂在一定的紧实力的作用下其体积变化的百分比,用试样紧实前后高度变化的百分比来表示,用湿型砂锤击制样机上三锤紧实。
有效高度120mm.紧实率=紧实距离/筒高(100%)紧实率CB:32%2.含水量:粘土砂的含水量是指在105-110℃烘干能去除的水分含量,以试样烘干后失去的质量与原试样质量的比(%)表示。
检验方法一般采用烘干称重法,仪器主要为红外线快速干燥器。
含水量:3.2%3.用型砂的紧实率%和含水量的比值来衡量一种型砂的含水量是否合适。
10-12.小于10,含泥量偏多型砂韧性差,大于12,含泥量偏少,对水分敏感性增大,而且透气性也偏高,易粘砂。
4.粘土湿型砂的透气性是指紧实后的砂样允许气体通过的能力。
透气性越高表明沙粒间孔隙过大,金属液易于渗透入沙粒。
透气性:1105.湿态抗压强度:110-140KPA 湿态抗拉强度:>11 KPA 抗劈强度:>17 KPA 5.表面强度表面耐磨性表面安定性>85%湿型砂应当具有足够高的表面强度,能够经受起模轻吹下芯浇注金属液等过程的擦磨作用。
6.型砂含泥量指的都是颗粒直径小于0.02mm的组分质量分数。
含泥量有两部分组成,第一部分活性组分,有效膨润土和有效煤粉。
第二部分灰分,失效膨润土煤粉和杂质。
用适量的α-淀粉降低型砂对含水量的敏感性。
型砂含泥量全粘土12-13%7.型砂粒度直接影响透气性和铸件表面粗糙度。
型砂粒度是将测量过含泥量的型砂用筛分法测定得到。
58±2. 50-65(相当于50/140---140/50筛号)8.MB 活性膨润土量6---9%9.有效煤粉量。
通过测定灼烧减量即燃损值和挥发量,含碳量,固定碳含量等参数作为推测有效煤粉量的参考。
灼烧减量即燃损值为3.5---5%。
砂型铸造-湿型铸造.

砂型铸造-湿型铸造1 概述粘土砂型可分为湿型、干砂型和表面烘干砂型。
三者之间的主要差别在于:湿型是造好的砂型不经烘干,直接浇入高温金属液体;干砂型是在合箱和浇注前将整个砂型送入窑中烘干;表面烘干砂型只在浇注前对型腔表层用适当方法烘干一定深度(一般5~10mm,大件20mm以上)。
目前,湿型砂是使用最广泛的、最方便的造型方法,大约占所有砂型使用量的60~70%,但是这种方法还不适合很大或很厚实的铸件。
表面烘干型与干型比,可节省烘炉,节约燃料和电力,缩短生产周期,所以曾在中型和较大型铸铁件的生产中推广过。
通常采用较粗砂粒(使有高的透气性),加入较多粘土和水分,有时还在型砂中加1~2%的木屑(提高抗夹砂结疤能力),其型腔表面必须涂敷涂料。
干型主要用于重型铸铁件和某些铸钢件,为了防止烘干时铸型开裂,一般在加入膨润土的同时还加入普通粘土。
干型主要靠涂料保证铸件表面质量。
其型砂和砂型的质量比较容易控制,但是砂型生产周期长,需要专门的烘干设备,铸件尺寸精度较差,因此,近些年的干型,包括表面烘干的粘土政型已大部分被化学粘结的自硬砂型所取代。
2 湿型铸造2.1湿型铸造特点湿型铸造法的基本特点是砂型(芯)无需烘干,不存在硬化过程。
其主要优点是生产灵活性大,生产率高,生产周期短,便于组织流水生产,易于实现生产过程的机械化和自动化;材料成本低;节省了烘干设备、燃料、电力及车间生产面积;延长了砂箱使用寿命等。
但是,采用湿型铸造,也容易使铸件产生一些铸造缺陷,如:夹砂、结疤、鼠尾、粘沙、气孔、砂眼、胀砂等。
随着铸造科学技术的发展,对金属与铸型相互作用原理的理解更加深刻;对型砂质量的控制更为有效;加上现代化砂处理设备使型砂质量得到了一定保证;先进的造型机械使型砂紧实均匀,起模平稳,铸型的质量较高,促进了湿型铸造方法应用范围的扩大。
例如汽车、拖拉机、柴油机等工业中,质量在300~500kg 以下的薄壁铸铁件,现都已成功地采用湿型铸造。
湿型砂性能参数概要

湿型砂性能参数概要1.粘土砂的紧实率是指湿态的型(芯)砂在一定的紧实力的作用下其体积变化的百分比,用试样紧实前后高度变化的百分比来表示,用湿型砂锤击制样机上三锤紧实。
有效高度120mm.紧实率=紧实距离/筒高(100%)紧实率CB:32%2.含水量:粘土砂的含水量是指在105-110℃烘干能去除的水分含量,以试样烘干后失去的质量与原试样质量的比(%)表示。
检验方法一般采用烘干称重法,仪器主要为红外线快速干燥器。
含水量:3.2%3.用型砂的紧实率%和含水量的比值来衡量一种型砂的含水量是否合适。
比值为10-12比较合适.小于10,含泥量偏多型砂韧性差,大于12,含泥量偏少,对水分敏感性增大,而且透气性也偏高,易粘砂。
4.5.粘土湿型砂的透气性是指紧实后的砂样允许气体通过的能力。
透气性越高表明沙粒间孔隙过大,金属液易于渗透入沙粒。
透气性:1105. 湿态抗压强度:110-140KPA 湿态抗拉强度:>11 KPA 抗劈强度:>17 KPA6.表面强度表面耐磨性表面安定性>85%湿型砂应当具有足够高的表面强度,能够经受起模轻吹下芯浇注金属液等过程的擦磨作用。
7.型砂含泥量指的都是颗粒直径小于0.02mm的组分质量分数。
含泥量有两部分组成,第一部分活性组分,有效膨润土和有效煤粉。
第二部分灰分,失效膨润土煤粉和杂质。
用适量的α-淀粉降低型砂对含水量的敏感性。
型砂含泥量全粘土12-13%比较合适8.型砂粒度直接影响透气性和铸件表面粗糙度。
型砂粒度是将测量过含泥量的型砂用筛分法测定得到。
58±2. 50-65(相当于50/140---140/50筛号)9.MB 活性膨润土量6---9%10.有效煤粉量。
通过测定灼烧减量即燃损值和挥发量,含碳量,固定碳含量等参数作为推测有效煤粉量的参考。
灼烧减量即燃损值为3.5---5%汇总:孙科2018.11.18。
湿型砂原材料质量测定方法(4)

猛烈降低型砂流动性 , 不适合机器造型使用。
目前 市 面上 有 几种 仪 淀粉 商 品供 应 ,选购 一
收 稿 日期 :0 9 1一 O 2 0 — l 1 修 定 日期 :0 0 O — 3 2 1一 1 1
一
仅化 度 反 映 出从 普 通 淀 粉 ( 一 粉 ) 化 为 B淀 转 淀 粉 的程 度 。标 准 法测 定 化度 的操作 步 骤 较 为复杂 , 少采 用 。 易法 即膨 润度测 定法 , 较 简 操
前 自行检 验其 质量 和性 能情 况是 必要 的 。 淀粉 的
性能 和质 量指 标如 下 。 41 含水 量 . 在 1 5 1 0℃烘 干箱 内烘 干 ,测 定含 水 量 。 0 ~ 1
普通 淀粉 和糊 精 的水分 大约 在 5 1%, 一 粉 %~ 5 仪 淀 含有 的水 分都 不超 过 85 .%。
作者简介 : 于震宗( 9 4 2 2 1. . ) 男, 1 2 . — 0 01 2 , 教授 , 1 25 博士生导师。
作 步骤是 :
2l/ 代 铁 l5 o14现 铸 8
湿型砂原材料质量测定方法 ) ( 4
( 华大学 清 机械工程系 , 京 北 10 8 ) 0 0 4
_ ห้องสมุดไป่ตู้
编者按 : 粘土湿型砂 主要用来 生产中小铸铁件和铸铝件 以及 少量小型铸钢 件 , 特别 是汽车 、 拖拉机 的关键铸件 , 如 气缸体 、 气缸盖 、 曲轴 、 动盘 等 , 制 其铸件质量往往 与湿型砂性能有关 。作者根 据 G / 6 4 2 0 BT2 8— 0 9铸造用砂及混合料试 验 方法 、 BT 2 2 20 G / 1 — 0 1煤 的工 业分 析 方法 、BT 9 2 — 9 9铸 造 用湿 型砂 有 效膨 润 土及 有效 煤 粉试 验方 法 、BT J / 2 1 1 9 J / 9 2 — 0 8湿型铸造用煤粉 、BT9 2 — 9 9铸造用膨润土和粘土 、BT9 4 — 9 8铸造用硅砂 、 BT 0 7 — 0 7膨润 2220 J / 2 7 19 J / 4 2 19 G /2 9 3 2 0 土, 同时参照 了美 国砂 型和砂芯试验手册 ( F l adC r T s H n bo , r dt , A SMo n oe et ad ok 3dE i)系统地介绍 了湿型砂性能检测 d . 和湿 型砂原材料质量测定方面 的国家标准和机械行业标准 以及最新 的检测仪器 , 更重要 的是还根据其他参考资料 以及 自己参 加的科研和操作实践 , 补 充说 明” 以“ 的形式 给出了湿 型砂性能检测 技巧和湿型砂原 材料质量检测方法 , 并针对 国内外相应 的检测方法和检测仪器性能提 出了自己的见解 。 “ 湿型砂性能检测 技术” 一文包 括湿 型砂取样方法 , 含水 量检测 , 紧实率 、 透气性 、 湿态强度 、 韧性 、 可紧实性 和流 动 性、 含泥量 、 砂粒粒度 、 有效膨润土量 、 有效煤粉和发气量 、 热湿拉强度等型砂性能 的测量方法 和注 意事项共 1 2节 内容 , 刊登在本 刊 2 1 0 0年第 15期 ;湿型砂原材料质量的测定方法” - “ 一文包括原砂 ( 指硅砂 )膨润土 、 、 煤粉 、 淀粉 等湿 型砂 原 材 料的质量判定标准 和检测方法共 4节 内容 , 刊从 2 1 年第 1 本 01 期起连载刊登 。
湿型砂的配方是怎样定的

湿型砂的配方是怎样定出的?■清华大学于震宗一. 前言要想生产出优良品质的湿砂型铸件,必须使用优秀性能的湿型砂。
湿型砂性能的获得,除了要使用优质的原材料和良好的混制工艺以外,还需要有一个合理的配方。
同一种造型方法、同一种类型铸件和同样的品质要求,国内外的湿型砂性能要求是基本类似的,可以互相参考借鉴。
例如国内外稳定生产中小灰铸铁件单一砂的型砂性能都基本上符合下表所示。
各项性能都是从造型处取样的测定结果。
含泥量是指型砂而言;有效膨润土量是指5.00g型砂用0.20%浓度试剂纯亚甲基蓝溶液的滴定量[mL];有效煤粉量是指1.00g 型砂900℃的发气量[mL]。
性能的波动范围根据铸件大小、厚薄和结构、以及清理方法不同而异,一般情况可取中间值。
至于混砂配方的确定则各工厂可能有较大出入。
铸铁湿型砂批料配方的最主要组成物是旧砂,此外还补充加入原砂、水、膨润土、煤粉。
在生产中旧砂和新砂加入量的比例并不经常变化,通常将旧砂和新砂量之和做为100%。
膨润土、煤粉和水的加入量可能随时调整,因此将这三种材料加入量按超过100%计算。
下表为某些工厂生产中等大小灰铸铁件的单一砂批料配方的例子。
原材料为内蒙砂、优质膨润土、优质煤粉;砂铁比5~7;落砂时树脂砂芯混入旧砂中约占旧砂量的0.5~2%;无旧砂除尘冷却装置;铸件经抛丸清理。
型砂干湿程度根据手捏的感觉或紧实率检测值,含水量为参考值。
2版)第103~104页的表格中列举了国內9家著名大型铸造工厂的铸铁单一湿型砂。
膨润土加入量有的为2~4%,还有极个别的高达5%。
煤粉加入量有的为0.75~2%,也有的高达3~4%。
至于民营中小铸造工厂的批料加入量可能有更大差异。
混砂加水量取决于型砂的干湿程度。
并不给出具体加入量。
以下将讨论其他几种批料的加入量是如何确定的。
二. 膨润土的批料加入量在生产中都是根据型砂试样的湿压强度来确定膨润土加入量是否足够。
补加膨润土的目的是补充膨润土被烧损的损失,另一方面,新加入材料如新砂、混入芯砂和煤粉也需要靠加入膨润土进行黏结使具有足够强度。
(2)湿型砂材料

湿型砂材料湿型铸造用型砂的组成物除了旧砂、新砂以外,还加入水、膨润土、煤粉等材料。
此外还有可能加入其它附加物如糊精、 -淀粉、重油液、纸浆废液、糖浆、木粉等。
膨润土和其它附加物与水形成粘稠糊状膜包覆在砂粒表面上形成湿型砂所要求的强度、塑性、韧性等特性。
目前我国有些中、小铸造工厂的湿型铸件表面品质不良和废品率高的主要原因之一大多是原材料选用不当,又不对购入原材料进行严格的检验。
本文中将介绍一些国内外铸造工厂所用湿型砂材料的实际情况,所列举的一些数据只是当时取样检测得到的,或是引自国内外文献,或是当时从个别商品中取样测定的结果,并不代表目前该地区产品的质量状况。
国内原材料产地仅用县或市名,不具体说明生产工厂的名称和地址。
本文写作中参照了几种国家标准和机械行业标准:GB/T 2684-2009 铸造用原砂及混合料试验方法;GB/T 212-2001 煤的工业分析方法;JB/T 9221-1999 铸造用湿型砂有效膨润土及有效煤粉试验方法;JB/T 9222-2008 湿型铸造用煤粉;JB/T 9227-1999 铸造用膨润土和粘土;JB/T 9442-1998铸造用硅砂。
1 原砂(新砂)1.1 引言砂粒是型砂的最主要组成物,每次混制湿型砂时都要向回用砂中补充一些砂粒。
加入原砂(新砂)的目的是:①在铸造过程中,有些砂粒破碎成为微细颗粒和粉尘而被除尘系统排除,还有些粘附在铸件表面而被清理掉。
另外,如果旧砂的落砂和破碎设备效果差,旧砂团块会随铸件跑掉或被筛掉。
因而必须添加新原砂以补充砂粒损失和保持砂系统的总砂量不变。
②旧砂泥分的主要组分是膨润土和煤粉,也还含一些灰分(包括膨润土和煤粉受热而被部分地烧损变成的死粘土和死煤粉,以及混砂加入的原砂、膨润土和煤粉带入的惰性粉尘)。
在回用旧砂砂处理和运输过程中,一部分泥分(包括灰分)被除尘系统清除出去,但仍然有一部分残留下来,并且进入新混制的型砂中而影响型砂性能。
加入新砂可使型砂中的含泥量保持平衡和和冲淡型砂中的灰分。
铸造湿型砂的检测要求与质量控制

湿型砂检测项目1、含水量型砂含水量高,铸件的针孔、气孔、呛火、胀砂、夹砂、水爆炸粘砂等缺陷增加。
在保证型砂的使用性能的前提下,应尽可能降低水分。
一般在造型机处含水量在2.5~4.0%之间,手工造型可以再放宽一点,紧实率/含水量的比率应控制在10~12:1。
型砂的含水量只是型砂中所含自由水的绝对数量,并不反映型砂的干湿程度。
如果型砂含有大量吸水粉尘,那么含水量高达5%,可能型砂还会显得太干,起模困难,这在许多中小型铸造企业都存在这种情况,一方面是没有人去管理,有些企业型砂反复使用10多年,连简单的除尘都不做,一方面是因为用的原材料不好,原砂是就近购买,膨润土和煤粉也没有什么要求。
2、紧实率型砂的干湿程度可以用紧实率来表示。
无论型砂的粉尘含量多少,它都有一个适宜的紧实率,只是含水量不同。
一般手工造型紧实率控制在46%左右,射压、挤压、静压造型紧实率控制在30~40%,夏季略高一点。
型砂检测一般宜在造型机处取样,在混砂机处取样应补偿运输和储存过程中的水分流失。
有些高压造型或气冲造型的砂型,3次锤击的试样并不能代表实际生产情况,有时候可能需要经过10次之多的锤击制样,具体应做对比确定次数,由此制作的试样其他方面的数据也会有明显变化。
3、透气率型砂必须具有良好的透气能力,以免浇注过程中发生呛火和铸件产生气孔缺陷。
透气能力也不能过高,否则会造成铸件表面粗糙和机械粘砂。
大多数型砂要求透气率在80~140,手工使用的面砂透气率可以低至60。
4、湿压强度目前国内的试样筒工作表面粗糙,耐磨性差,较易磨损,使测得强度值偏低,透气率偏高,制样器不宜放置在木桌上,在水泥台上也需垫上6mm以上的橡胶板,否则测得的湿压强度可能会偏低25%左右。
有条件的可以自己制作试样筒,工作表面硬度HRC65~70,表面粗糙度Ra≤0.20μm。
具体造型时需要的湿压强度,丹麦DISA挤压线推荐200±20Kpa,德国BMD和瑞士GF推荐180~220 Kpa,东久公司推荐无箱射压110~140 Kpa,新东公司水平无箱射压推荐80~140 Kpa,具体还得根据铸件的厚薄程度作适当调整。
粘土湿型砂

粘土湿型砂及其质量控制一粘土湿型砂的特点湿型砂主要由原砂、膨润土、附加物(煤粉、淀粉等)和水组成。
造型过程中,型砂捣实并达到一定紧实度后,形成砂型。
粘土湿型砂的结构示意图通常使用的硅砂,来源广,便宜,耐火度高。
另一方面,原砂砂粒能为砂型(芯)提供众多孔隙,保证型、芯具有一定的透气性,在浇注时,使型内产生的大量气体顺利逸出。
湿型砂按在造型时的情况,可分为面砂、背砂和单一砂。
二粘土湿型砂用的原材料1 硅砂1)硅砂种类及其SiO2含量天然硅砂河砂、湖砂、、海砂(牟平)、风积砂(大林、围场)。
人工硅砂由硅石岩、硅砂岩采矿、清洗、破碎、筛选加工而成。
硅砂的SiO2含量及不同用途铸铁用砂SiO2≥85%;铸钢用砂SiO2≥95%。
2)石英的结构转变特性石英为硅氧四面体,相变温度:573℃时产生体积膨胀,易夹砂。
870℃时也产生相变,故烧过此温度后,用于复膜砂。
3)硅砂的杂质长石、云母、氧化铁、碳酸盐及粘土,均降低(1)耐火度。
4)硅砂的含泥量原砂含有的直径小于0.02mm的颗粒,其质量分数称为原砂的含泥量。
5)硅砂的粒度和表示方法例如:三筛>75%,40/70;四筛>85%,50/1406)硅砂的颗粒形状和角形因数颗粒较圆(角形因数小)的砂粒,型砂的流动性好,紧实密度较高,透气性好。
2膨润土粘土的主要成分是水化硅酸铝(mAl2O3.SiO2.xH2O)。
晶体结构有两层型(高岭土,即普通粘土),三层型(蒙脱石,即膨润土)。
和普通粘土相比,膨润土有较大的吸水膨胀性、胶体分散性、、吸附性、离子交换性和湿态粘结性能。
故多用于湿型砂。
膨润土在500-700℃时失去结构水,加热到800℃以上时,晶格破坏,失去粘结作用。
膨润土分钙基膨润土和钠基膨润土,钠基膨润土在水分较高时仍有较好的强度,即具有较高的热湿拉强度和抗夹砂能力。
铸造用膨润土按工艺试样湿压强度值分为4级,,热湿拉强度值也分为4级。
(2)各种牌号的铸造用膨润土,其吸附亚甲基蓝量每100克至少应在20克以上;水分不大于12%,膨润土的95%应通过200号铸造用试验筛。
型砂的成分及制备

型砂的成分及制备
型砂在反复使用过程中型砂成分将发生变化,如粘土和煤粉的烧损、 泥分的增加等。
所以,型砂每回用一次(或几次),就要补加一定量的新砂、粘土和 煤粉,以保证型砂性能不变,
即要 控制型砂成分。
1. 湿型砂的成分 (1) 有效粘土
湿型砂中的粘土
有效粘土 失效粘土
起粘结作用的粘土 未起粘结作用的粘土
成分 铸铁件
原砂SiO2 有效粘土 有效煤粉
(%)
< 92
6~8 4~8
含泥量 12 ~16
铸钢件 > 96
6~8
0
8 ~14
含水量
4.5 ~ 6 4~5
性能 铸铁件
紧实率
%
45 ~ 55
铸钢件 45 ~ 55
透气性
< 100 < 120
湿压强度 热湿拉强度 破碎指数
MPa
kPa
%
0.06~0.1 1.0 ~2.5 70 ~ 90
2. 湿型砂的制备 (3) 砂处理工艺流程
面砂、单一砂
面砂、单一砂
单一砂、背砂
混砂工艺(以碾轮式为例):
a).湿混:砂 部分水 混匀 粘土 煤粉 混1-2分钟水
b).干混:砂 粘土 煤粉
混1-2分钟 水
混至要求紧实率出碾 调匀 松砂 造型机
2. 湿型砂的制备
混砂效率
起粘结作用的粘土量 有效粘土含量
100 %
测定方法:
型砂预定混碾时间的抗 压强度 型砂预定混碾时间延长 5分钟的抗压强度 100 %
1. 湿型砂的成分 (4) 泥分
型砂中直径 < 22μm 的物质。 原砂中泥分 + 有效粘土 + 有效煤粉 + 有害成分
- 1、下载文档前请自行甄别文档内容的完整性,平台不提供额外的编辑、内容补充、找答案等附加服务。
- 2、"仅部分预览"的文档,不可在线预览部分如存在完整性等问题,可反馈申请退款(可完整预览的文档不适用该条件!)。
- 3、如文档侵犯您的权益,请联系客服反馈,我们会尽快为您处理(人工客服工作时间:9:00-18:30)。
半型砂箱基本简介高密度造型方法(或称高紧实度造型,包括多触头高压、气冲、挤压、射压、静压、真空吸压等造型方法)的生产效率高、铸件品质较好,因而国内应用日益普遍。
高密度造型对型砂品质的要求比较严格。
本文用表格仅列举出作者搜集的一些比较典型的国内外铸造工厂实际应用的和部分设备公司推荐的高密度砂型的型砂性能,并在以下段落中加以评论。
受纸张宽度限制,只在表格中列出几种主要的和经常测定的性能。
数据搜集来源一部分为近年来中外公开发行刊物,在表格最右侧注明刊物名称和出版年月或期号。
另一部分是由各公司或工厂的工程师最近提供的。
在表中只标明数据获得日期而不具体注明工厂名称。
所列举数据只是当时情况,并不代表目前的实际状况。
表中工厂编号A、B、C分别代表国外工厂(或外资厂)、合资厂、本国厂。
符号中―○‖—造型机处取样;―●‖—混砂机处取样;―□‖—型砂含泥量;―*‖—旧砂含泥量。
1、紧实率和含水量湿型砂不可太干,否则膨润土未被充分润湿,起模困难,砂型易碎,表面的耐磨强度低,铸件容易生成砂孔和冲蚀缺陷。
型砂也不可太湿,过湿型砂易使铸件产生针孔、气孔、呛火、水爆炸、夹砂、粘砂等缺陷,而且型砂太粘、型砂在砂斗中搭桥、造型流动性降低,砂型的型腔表面松紧不均,还可能导致造型紧实距离过大和压头陷入砂箱边缘以内而损伤模具和砂型吃砂量过小。
表明型砂干湿状态的参数有两种:紧实率和含水量。
附表中国内各厂的紧实率和含水量除特别注明外,取样地点可能都在混砂机处。
但是型砂紧实率和含水量的控制应以造型处取样测定为准。
从混砂机运送到造型机时紧实率和含水量下降幅度因气候温度和湿度状况、运输距离、型砂温度等因素而异。
如果只根据混砂机处取样检测结果控制型砂的湿度,就要增多少许以补偿紧实率和水分的损失。
多年前的观点认为手工造型和震压式机器造型造型机处最适宜干湿状态的紧实率约在45~50%;高压造型和气冲造型为40~45%;挤压造型要求流动性好,紧实率为35~40%。
由表中可以看出铸件品质较好的工厂的高密度造型的型砂紧实率通常在25~45%范围内,比起当年有明显降低。
这是由于高密度造型设备的起模精度提高,而且砂型各部位硬度均匀分布的要求使型砂的流动性成为重要因素。
工厂的控制原则大多是只要能够保证起模,就尽量降低紧实率。
比较理想的造型机处型砂紧实率集中于34~38%之间,不可高于40%,也避免低于32%。
从减少铸件气孔缺陷的角度出发,要求最适宜干湿状态下型砂的含水量尽可能低。
高强度型砂的膨润土加入量多,型砂中含有多量灰分,所购入煤粉和膨润土的品质低劣而需要增大加入量,混砂机的加料顺序不良、揉捻作用不强、刮砂板磨损、混砂时间太短,以致型砂中存在多量不起粘结作用的小粘土团块,都会提高型砂的含水量。
根据资料,世界各国高密度造型工厂造型机处的型砂含水量基本上都是分布在2. 5~4.2%之间,比较集中于2.8~3.5%。
如果生产的铸件具有大量树脂砂芯(如发动机铸件),型砂含水量大多偏于下限,这是由于大量树脂砂芯溃散后混入型砂使含泥量下降和型砂吸水量降低。
我国有些铸造工厂的型砂含水量很高:如表中C-8厂实测高达5.0%,可能与旧砂含泥量高达16.7~1 8.0%有关。
型砂的(紧实率)/(含水量)比值可表示每1%型砂含水量能够形成多少紧实率,最好在10~12。
由几家外商独资或合资企业的检验结果计算比值大多在10~12.7范围内。
曾测定三家乡镇铸造厂的比值只有5.0~8.5之间,说明型砂中吸水物质过多。
2、透气率砂型的透气率不可过低以免浇注过程中发生呛火和铸件产生气孔缺陷。
但是绝对不可理解为型砂的透气性能―越高越好‖。
因为透气率过高表明砂粒间孔隙较大,金属液易于渗入而造成铸件表面粗糙,还可能产生机械粘砂。
所以湿型用面砂和单一砂的透气性能应控制在一个适当的范围内。
对湿型砂透气率的要求需根据浇注金属的种类和温度、铸件的大小和厚薄、造型方法、是否分面砂与背砂、型砂的发气量大小、有无排气孔和排气冒口、是否上涂料和是否表面烘干等等各种因素而异。
用单一砂生产中小铸件时,型砂透气性能的选择必须兼顾防止气孔与防止表面粗糙或机械粘砂两个方面。
高密度造型的砂型排气较为困难,要求型砂的透气率通常稍高些。
从附表可以看出较为适当的高密度造型型砂透气率大多在100~140之间。
如果型砂透气率在160以上或更高,除非在砂型表面喷涂料,否则铸件表面会出现粗糙甚至有局部机械粘砂。
附表中A-2的透气率实测结果竟达250,上、下型都需喷醇基涂料。
另一外资工厂的透气率不作为控制项目,偶尔测得透气率大约为200~280。
观察其铸件表面相当粗糙,原因是型砂中混入大量20/40目粗粒溃碎砂芯。
实际上,有很多生产发动机的铸造厂都遇到溃碎砂芯混入旧砂而使型砂透气率偏高的问题。
C-13的铸件表面并不粗糙,而测得的透气率高达230~240,是仪器的通气塞孔洞尺寸过大所致。
3、湿态强度如果型砂湿态强度不足,在起模、搬运砂型、下芯、合型等过程中,砂型有可能破损和塌落;浇注时砂型可能承受不住金属液的冲刷和冲击,而造成砂孔缺陷甚至跑火(漏铁水);浇注铁水后石墨析出会造成型壁移动而导致铸件出现疏松和胀砂缺陷。
生产较大铸件的高密度砂型所用砂箱没有箱带,高强度型砂可以避免塌箱、胀箱和漏箱。
无箱造型的砂型在造型后缺少砂箱支撑也需要具有一定的强度。
挤压造型时顶出的砂型要推动其它造好砂型向前移动,更对型砂的强度提出了较高要求。
但是,强度也不宜过高。
因为高强度的型砂需要加入更多的膨润土,不但影响型砂的水分和透气性能,还会使铸件生产成本增加,而且给混砂、紧实和落砂等工序带来困难。
以下文章中各种型砂强度的单位均为kPa,不再逐个标明。
3.1湿压强度一般而言,欧洲铸造行业对铸铁用高密度造型型砂的的湿压强度值要求较高。
欧洲造型机供应商推荐的湿压强度值范围在130~250之间,集中于180~220。
有些日本铸造工厂对型砂湿压强度的要求偏低。
除表上所列的丰田上乡和三菱川崎强度较高以外,很多工厂只有80~180。
北美铸造行业的型砂强度似乎介于欧洲于日本之间。
例如福特汽车厂Cleveland铸造厂排气管高压造型型砂为172,万国收割机公司Loisville铸造厂生产拖拉机缸体高压型砂为134~156。
有人认为欧洲铸造工厂的型砂湿压强度比美、日两国工厂高的原因之一是由于欧洲铸铁用原砂含SiO2较高,型砂中必须加入大量膨润土才能避免铸件产生夹砂结疤缺陷。
我国工厂高密度造型的型砂湿压强度比较接近美洲和日本工厂,对于铸铁件而言,除个别铸造厂以外,高密度造型的湿压强度大多在120~200范围内,比较集中在140~180。
湿压强度控制值较低的优点之一是即使所使用的振动落砂机破碎效果不好,也不致有大砂块随铸件跑掉。
而且很多铸造工厂所选用膨润土的品质较差,宁愿型砂的湿压强度稍低些,就无需加入大量膨润土,型砂含水量也可低些。
高密度湿型铸钢需要防止铸件生成热裂缺陷,因而所用型砂的湿压强度大多在70~130之间,以降低对铸件收缩阻力。
3.2湿拉强度和湿劈强度从材料力学角度来看,抗压强度除代表型砂粘结强度以外,也还受砂粒之间摩擦阻力的影响,而抗拉强度无此缺点。
通常要求湿拉强度>20kPa。
但是测定型砂的湿态抗拉强度必须使用特制的试样筒和试验机,所以很多中小铸造工厂不测定型砂的抗拉强度。
有人按照混凝土试验中曾使用过的办法将圆柱形标准试样横放,使它在直径方向受压应力,就可以得出近似抗拉强度的湿态劈裂强度值。
我国几家工厂的要求在30~50范围内。
DISA公司推荐的湿劈强度是30~34,还给出了用劈裂强度估算抗拉强度的近似公式:湿拉强度=湿劈强度×0.65。
3.3湿剪强度湿剪强度比湿压强度较能表明型砂的粘结力而且容易测定。
国外设备公司建议的高密度造型线型砂的湿剪强度值为30~50(剪切力作用在标准试样的两端平面上)。
A-5实测为52,B-1实测为38~55。
另一种较新的测试方法,剪切力作用在试样圆周面上。
这种仪器可以同时测出抗剪强度和剪切断裂时的变形量。
两种湿剪强度数值是一致的。
通常生产用型砂的变形量多在0.40~0.70mm范围内。
例如A-6测得挤压造型型砂的剪切强度约为60kPa,变形量约在0.50mm。
3.4表面强度(表面耐磨性)湿砂型应当具有足够高的表面强度,能够经受起模、清吹、下芯、浇注金属液等过程的擦磨作用。
否则型腔表面砂粒受外力作用下容易脱落,可能造成铸件的表面粗糙、砂孔、粘砂等缺陷。
在有些铸造工厂中,从起模到合箱之间砂型敞开放置较长时间,以致铸型表面水分不断蒸发,即―风干现象‖,可能会导致表面耐磨性急剧下降。
间隔时间长,天气干燥,型砂温度较高时,风干现象尤其严重。
美国Dietert公司推荐利用测定造型性的圆筒筛,将两只圆柱标准试样并列放置其中,转动1min后称量掉落的砂量,用来代表型砂表面耐磨性。
日本较多使用的方法是将标准试样放置在6目筛上,在震摆式筛砂机上震动6 0s,以震摆前、后试样重量的比率称为―表面安定度(SSI)‖。
例如东久公司推荐水平分型无箱射压线的型砂试样湿态即时表面安定度为>88%。
该公司调查6家铸造厂的表面安定度都在88.9~91.0%范围内。
土芳公司调查8家静压和气冲线在77.6~86.6%范围内,平均82.5%。
我国A-1实测结果在70~89范围内;A-4实测结果是89.9~90.6%。
在湿砂型喷涂表面稳定剂或涂料和在型砂中加入淀粉材料都能提高表面耐磨性。
为了避免表面安定度试验的试样在筛上出现不规则的颠簸翻滚,而使掉落砂量波动。
清华大学研制出的耐磨性测定装置使用钢丝针布对试样施加100g正压力刷磨表面,称量1min的磨下量即可代表湿型砂试样的表面耐磨性。
用内蒙精选砂100%,天然钠基膨润土或钙基膨润土8%,α淀粉量0~1%配制型砂,紧实率按45%控制。
不加α淀粉的钠基膨润土空白试样,即时磨损量约为8g,风干2h后磨损量即已增加到40g以上。
加入α淀粉1%的钠基膨润土试样即时磨损量降为0.37g,风干2h后磨损量仅约为2g左右。
钙基膨润土试样即时磨损量高达16g,加入α淀粉后即时磨损量降为1. 8g。
4、型砂含泥量型砂和旧砂的泥分是由有效的膨润土、煤粉以及无效的灰分组成的。
一般型砂比旧砂的泥分含量多出0. 5~3.0%。
型砂的含泥量直接地影响型砂的各种性能的因素,旧砂的含泥量只是供参考之用。
所以应当以型砂含泥量的检测和控制为主。
附表中含泥量除专门注明外大概都是指旧砂而言。
大多数铸造厂的型砂和旧砂含泥量过高的原因可能是所使用的原砂、膨润土和煤粉品质不良,旧砂缺乏有效地除尘处理造成的。
还有些发动机铸造工厂的型砂出现含泥量过低的现象,是旧砂中混入大量溃碎树脂砂芯造成的,以致型砂适宜含水量太低,透气率太高,性能难以控制。