火灾爆炸指数法用于加氢厂房的安全评价(新编版)
道化学火灾爆炸危险指数评价法

道化学火灾爆炸危险指数评价法
道化学火灾爆炸危险指数评价法,简称Dow Fire and E某plosion Inde某,是美国陶氏化学公司在20世纪60年代开发的一种火灾爆炸危险指数评价方法,主要用于评估场所化学品储存和生产过程中的火灾和爆炸危险性。
Dow指数评估方法,通过对化学品的物理化学性质、储存条件、装置安全性等进行评估,计算火灾和爆炸危险指数,并根据指数分类确定预防工作的方案和措施。
Dow指数评估方法包括以下几个方面:
1.物理化学性质评估:包括物质燃烧、闪点、熔点、汽化等物理化学性质的评估。
2.储存条件评估:包括储存容器的材料、储存方式、存放时间等的评估。
3.装置安全性评估:包括操作人员的技术水平、设备的安全性、操作过程中的风险等评估;
通过以上评估,可以得出Dow指数评估值,这个数值越高,该化学品的危险性就越高,防火灭火和安全防范就需要更多的防火设施和安全预防措施。
Dow指数评估方法的优点在于,可以对化学品的不同性质进行评估, 从而提高预防措施的精细化,指导场所做好防火工作和制定应急预案;并且按照不同危险等级,对应不同的应急预案,让企业在火灾或爆炸发生时更有应对的措施。
但Dow指数评估方法也有缺点,计算过程较为繁琐复杂,需要大量的
物理化学数据和实验结果,依赖数据的准确性确保评估结果的准确性和可
靠性。
总之,Dow指数评估方法能对化学品的危险等级进行评估,是一种科
学的、实用性强的评估方法,对企业做好防火工作和应急预案非常有帮助。
道化学火灾、爆炸指数评价法
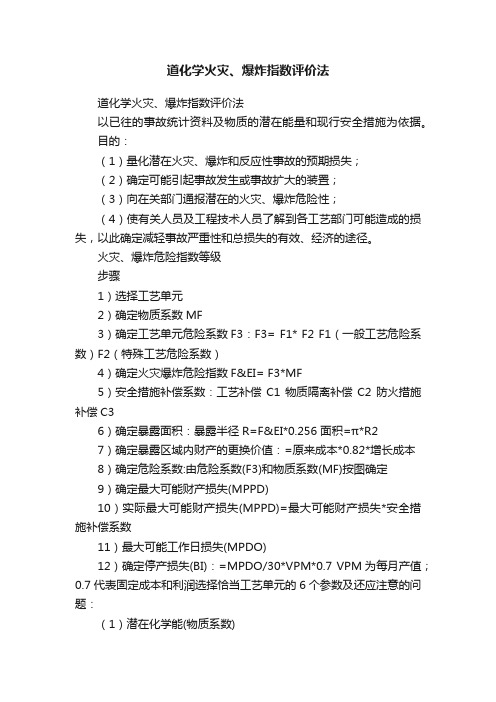
道化学火灾、爆炸指数评价法道化学火灾、爆炸指数评价法以已往的事故统计资料及物质的潜在能量和现行安全措施为依据。
目的:(1)量化潜在火灾、爆炸和反应性事故的预期损失;(2)确定可能引起事故发生或事故扩大的装置;(3)向在关部门通报潜在的火灾、爆炸危险性;(4)使有关人员及工程技术人员了解到各工艺部门可能造成的损失,以此确定减轻事故严重性和总损失的有效、经济的途径。
火灾、爆炸危险指数等级步骤1)选择工艺单元2)确定物质系数MF3)确定工艺单元危险系数F3:F3= F1* F2 F1(一般工艺危险系数)F2(特殊工艺危险系数)4)确定火灾爆炸危险指数F&EI= F3*MF5)安全措施补偿系数:工艺补偿C1物质隔离补偿C2防火措施补偿C36)确定暴露面积:暴露半径R=F&EI*0.256 面积=π*R27)确定暴露区域内财产的更换价值:=原来成本*0.82*增长成本8)确定危险系数:由危险系数(F3)和物质系数(MF)按图确定9)确定最大可能财产损失(MPPD)10)实际最大可能财产损失(MPPD)=最大可能财产损失*安全措施补偿系数11)最大可能工作日损失(MPDO)12)确定停产损失(BI):=MPDO/30*VPM*0.7 VPM为每月产值;0.7代表固定成本和利润选择恰当工艺单元的6个参数及还应注意的问题:(1)潜在化学能(物质系数)(2)工艺单元中危险物质的数量(3)资金密度(每平方米美元数)(4)操作压力和操作温度(5)导致火灾、爆炸事故的历史资料(6)对装置起关键作用的单元还应注意的问题:1)所处理的量至少为454kg或0.454m32)设备串联布置且相互间未有效隔离,要仔细考虑如何划分3)要仔细考虑操作状态及操作时间,对F&EI有影响的异常状况,判别选择个操作阶段还是几个阶段来确定重大危险4)在决定哪些设备具有最大潜在火灾爆炸危险时,可请教工程技术人员或专家物质系数的确定:由N F(燃烧性)、N R(化学性)决定。
道化学火灾、爆炸指数评价法在危化企业安全评价中的应用研究

道化学火灾、爆炸指数评价法在危化企业安全评价中的应用研究一、本文概述随着化工行业的快速发展,危险化学品生产企业的安全问题日益突出,火灾和爆炸事故时有发生,给人民生命财产安全带来了严重威胁。
因此,对危化企业进行科学、有效的安全评价显得尤为重要。
道化学火灾、爆炸指数评价法作为一种常用的安全评价方法,已经在全球范围内得到了广泛应用。
本文旨在探讨道化学火灾、爆炸指数评价法在危化企业安全评价中的应用,以期为提高危化企业的安全管理水平和降低事故风险提供理论支持和实践指导。
本文将首先介绍道化学火灾、爆炸指数评价法的基本原理和计算方法,分析其在危化企业安全评价中的适用性和优势。
接着,通过案例分析,详细阐述道化学火灾、爆炸指数评价法在危化企业安全评价中的具体应用步骤和注意事项。
在此基础上,本文还将探讨如何结合危化企业的实际情况,对评价结果进行解读和应用,提出针对性的安全改进措施和建议。
本文的研究不仅有助于深化对道化学火灾、爆炸指数评价法的理解和应用,也为危化企业的安全管理和风险防控提供了有益参考。
通过本文的研究,希望能够为危化企业的安全评价工作提供更加科学、有效的方法和工具,推动危化行业的安全生产水平不断提升。
二、道化学火灾、爆炸指数评价法概述道化学火灾、爆炸指数评价法,简称道化学法,是一种广泛应用于危化企业安全评价的定量风险评估方法。
该方法起源于20世纪60年代的美国道化学公司,旨在通过一系列的计算和评估,对化工生产过程中的潜在火灾、爆炸等危险进行量化分析,从而为企业的安全管理提供科学依据。
道化学法以物质系数为基础,结合工艺单元的危险性系数、操作条件系数、一般工艺危险系数和特殊工艺危险系数等,通过特定的数学模型计算得到火灾、爆炸指数。
这一指数不仅能够反映物质本身的危险性,还能够体现工艺过程和操作条件对安全的影响。
通过对比标准值,可以判断生产过程的安全水平,进而制定相应的安全措施和管理对策。
道化学法的核心在于其科学性和实用性。
美国道化学公司火灾爆炸指数评价法

美国道化学公司⽕灾爆炸指数评价法美国道化学公司⽕灾爆炸指数评价法(1)选择评价单元:应⽤“美国道化学公司⽕灾爆炸指数评价法”针对性评价制A/B车间、仓库A/B/C/D。
(2)物质系数(MF)的确定:单元内存在的物质为⼆甲苯等成分。
根据评价指南的规定,应选取⽕灾危险性较⼤或储运量较⼤的物质作为代表性物质,故代表物质选定为⼆甲苯,其物质系数MF为16。
(3)⼀般⼯艺危险系数(F1):制A/B车间:基本系数为1.00。
①放热反应:酯化反应属于中等放热反应,系数为0.50。
②吸热反应:⽆。
③物料处理与输送:易燃物料在连接管线上装卸,同时存在⼈⼯加料,系数为0.50。
④封闭单元或室内⼯艺单元:本单元为开放式单元。
⑤通道:具有合格的消防、救援通道。
⑥排放和泄漏控制:本单元周围为⼀可排放泄漏液的平坦地,⼀旦失⽕,会引起⽕灾,系数为0.50。
⼀般⼯艺危险系数F1 = 2.50仓库A/B/C/D:基本系数为1.00。
①放热反应:⽆。
②吸热反应:⽆。
③物料处理与输送:易燃物料在连接管线上装卸,系数为0.50。
④封闭单元或室内⼯艺单元:本单元为开放式单元。
⑤通道:具有合格的消防、救援通道。
⑥排放和泄漏控制:本单元周围为⼀可排放泄漏液的平坦地,⼀旦失⽕,会引起⽕灾,系数为0.50。
⼀般⼯艺危险系数F1 = 2.00(4)特殊⼯艺危险系数(F2):制A/B车间:基本系数为1.00。
①毒性物质:毒性物质的危险系数为0.2NH。
⼆甲苯的NH=2,系数为0.40。
②负压操作:有负压操作,此处不取系数。
③爆炸极限范围内或其附近的操作:反应釜冷却时可能吸⼊空⽓,系数为0.50。
④粉尘爆炸:⽆。
⑤压⼒释放:反应釜内常压操作。
⑥低温:⽆。
⑦易燃物质和不稳定物质的数量:制A/B车间总容量为63.4/63m3,折合约50500kg,系数约为1.09。
⑥腐蚀和磨损:本单元的腐蚀和磨损可忽略。
⑨泄漏——连接头和填料处:泵、法兰连接处产⽣正常的⼀般泄漏,系数为0.30。
道化学公司火灾爆炸危险指数评价法
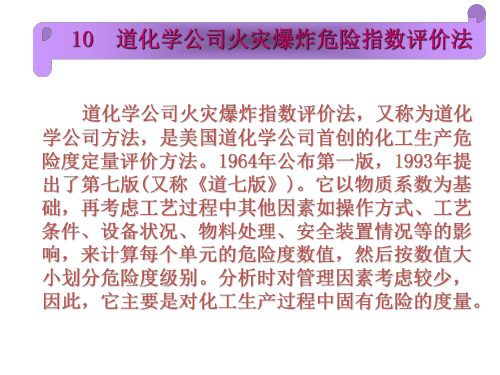
储存中总能量/Btu × 109 A - 液化气;B.- 1类易燃液体(闪点<37.8℃=;C - 2类可燃液体(37.8'℃<闪点
<60℃)Байду номын сангаас
图10-4储存中的液体和气体
物质总量/Ib×106(1lb = 0.454kg) 图10-5 储存中的可燃固体/工艺中的粉尘
10.3.4.1 火灾爆炸危险指数的计算
① 应急电源,0.98
② 冷却,0.97~0.99 ③ 抑爆,0.84~0.98
④ 紧急停车装置,0.96~0.99
⑤ 计算机控制设置了在线计算机以帮助操作者,但它 不直接控制关键设备或经常不用计算机操作时,系数 为0.99;具有失效保护功能的计算机直接控制工艺操 作时,系数为0.97;采用下列三项措施之一者,系数 为0.93
面积小于上述数值时,要分析它对 通道的要求,如果通道不符合要求,影响 消防活动时,系数可取0.20。
① F&EI计算表中排放量按以下原则确定: ② 系数选取原则:
压力/(Ib/in2)(表压,1 Ib/in2=6.895Pa) 10-2 易燃、可燃液体的压力危险系数图
工艺中总能量 / Btu ×109 (1 Btu=1.055 ×103J) 图10-3工艺中的液体和气体
随着单元危险系数和物质系数的增大,二次 事故变得愈加严重。火灾、爆炸危险指数(F&EI) 是单元危险系数(F3)和物质系数(MF)的乘 积。它与暴露半径有关。
表10-11是F&EI值与危险程度之间的关系, 它使人们对火灾、爆炸的严重程度有一个相对的 认识。
(1)工艺控制补偿系数(C1) (2)物质隔离补偿系数(C2) (3)防火措施补偿系数(C3)
⑥ 惰性气体保护,0.94 ~ 0.9 ⑦ 操作指南或操作规程,0.91 ~ 0.99 ⑧ 活性化学物质检查,0.91 ~ 0.98 ⑨ 其他工艺过程危险分析,0.91 ~ 0.98表10-12
火灾爆炸指数法用于加氢厂房的安全评价(新编版)

( 安全论文 )单位:_________________________姓名:_________________________日期:_________________________精品文档 / Word文档 / 文字可改火灾爆炸指数法用于加氢厂房的安全评价(新编版)Safety is inseparable from production and efficiency. Only when safety is good can we ensure better production. Pay attention to safety at all times.火灾爆炸指数法用于加氢厂房的安全评价(新编版)加氢试验厂房是中国石化抚顺石油化工研究院投资最大、装置最集中的场所,是防火重点部位,做好它的安全评价可以使管理者了解事故隐患和薄弱环节,全面掌握该部位的安全状况,不断改进、完善安全防灾体系与设施,也可据此确定系统是否需要改进设计或增加安全措施,明确改进后的危险性是否达到可以接受的程度,以预防事故发生,实现系统最佳安全的目的。
由于加氢试验厂房中均为小型试验装置,故在评价中有别于工业装置,部分选项视情况可以忽略不计。
1安全评价方法选择现在国内外以开发出许多种安全评价法,按指标量化的体系可分为两大类,即风险率法和相对法。
但风险率评价法需要精确的统计数据,其评价结果的准确率才比较高;而往往由于缺乏故障由于液氯生产系统承担着氯气液化、贮存、气化、精制和包装等关键生产过程,设备服役运行多年,生产过程的各工艺控制参数要求苛刻,一旦超概率数据,应用起来有一定的困难。
目前应用较多的是相对法,也称指数法或评点法,这类方法是根据过去经验或有关资料,采用一系列相对数值来度量危险性的大小,经综合评价,确定系统安全程度。
本文采用的评价方法为美国道化学公司火灾爆炸指数评价法[1],该评价法是以工艺过程中使用、生产物质的理化特性为基础,结合工艺条件、物料量等因素求取火灾爆炸指数。
火灾爆炸指数法用于加氢厂房的安全评价

火灾爆炸指数法用于加氢厂房的安全评价
加氢试验厂房是中国石化抚顺石油化工研究院投资最大、装置最集中的场所,是防火重点部位,做好它的安全评价可以使管理者了解事故隐患和薄弱环节,全面掌握该部位的安全状况,不断改进、完善安全防灾体系与设施,也可据此确定系统是否需要改进设计或增加安全措施,明确改进后的危险性是否达到可以接受的程度,以预防事故发生,实现系统最佳安全的目的。
由于加氢试验厂房中均为小型试验装置,故在评价中有别于工业装置,部分选项视情况可以忽略不计。
加油站道化学火灾爆炸指数法评价00

道化学火灾爆炸指数法评价一、确定评价单元及危险物质(一)评价单元根据生产的特点和危险程度将选取生产储存单元中最具危险的、起关键作用的部分划分为更小的评价单元,具体划分的小单元如下:汽油储罐。
(二)危险物质各单元内危险物质及物质系数及特性见表5-4-1和表5-4-2。
表5-4-1 评价单元及危险物质表5-4-2 物质系数和特性表二、火灾爆炸危险指数评价(一)固有危险程度评价按照单元的工艺条件,并结合工艺特点,选取各评价单元的工艺危险系数,计算火灾、爆炸危险指数,确定单元固有危险程度。
结果见表5-4-3。
表5-4-3 火灾爆炸危险指数表注:储存中的液体或气体的计算方法步骤:物质的质量吨数×103/0.4536=?×103(磅)燃烧热:18.8×104(BTU/1b)。
总热值=?×103×18.8×104=X×109( BTU)再根据公式:lgY=-0.403115+0.378703 (lgX)-0.046402(lgX)2-0.015379(lgX)3求Y(二)安全补偿系数根据工艺单元内设置的安全防范设施情况,确定各评价单元的安全补偿系数如表5-4-4。
表5-4-4 安全补偿系数表(三)最终评价用求取的安全补偿系数乘以各工艺单元的固有火灾、爆炸危险指数,可求得补偿后的火灾、爆炸危险指数(F&EⅠ)′,进而可以确定各工艺单元的暴露区域半径或暴露区域面积。
计算结果见表5-4-5。
表5-4-5 补偿火灾、爆炸危险指数及暴露区域半径计算表从火灾、爆炸危险指数评价结果中可以看出:初期评价中,汽油储罐单元的火灾、爆炸危险等级为“中等”。
综上所述,经过安全补偿后,各评价单元的火灾、爆炸危险指数均不超过“很大”,即项目可以达到安全使用的基本要求。
因此,在项目进行初步设计或施工图设计过程中,应将评价过程中涉及的安全补偿措施落实到设计文件中,确保项目建成后的安全生产109103。
火灾爆炸指数法用于加氢厂房的安全评价
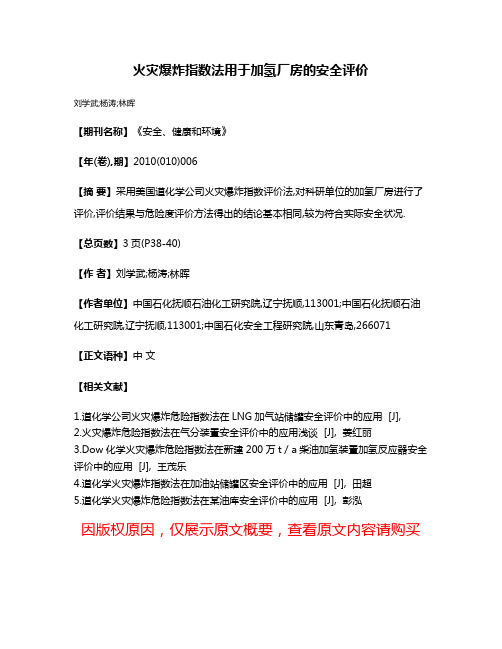
火灾爆炸指数法用于加氢厂房的安全评价
刘学武;杨涛;林晖
【期刊名称】《安全、健康和环境》
【年(卷),期】2010(010)006
【摘要】采用美国道化学公司火灾爆炸指数评价法,对科研单位的加氢厂房进行了评价,评价结果与危险度评价方法得出的结论基本相同,较为符合实际安全状况.【总页数】3页(P38-40)
【作者】刘学武;杨涛;林晖
【作者单位】中国石化抚顺石油化工研究院,辽宁抚顺,113001;中国石化抚顺石油化工研究院,辽宁抚顺,113001;中国石化安全工程研究院,山东青岛,266071
【正文语种】中文
【相关文献】
1.道化学公司火灾爆炸危险指数法在LNG加气站储罐安全评价中的应用 [J],
2.火灾爆炸危险指数法在气分装置安全评价中的应用浅谈 [J], 姜红丽
3.Dow化学火灾爆炸危险指数法在新建200万t/a柴油加氢装置加氢反应器安全评价中的应用 [J], 王茂乐
4.道化学火灾爆炸指数法在加油站储罐区安全评价中的应用 [J], 田超
5.道化学火灾爆炸危险指数法在某油库安全评价中的应用 [J], 彭泓
因版权原因,仅展示原文概要,查看原文内容请购买。
(完整版)道化学火灾爆炸危险指数评价法
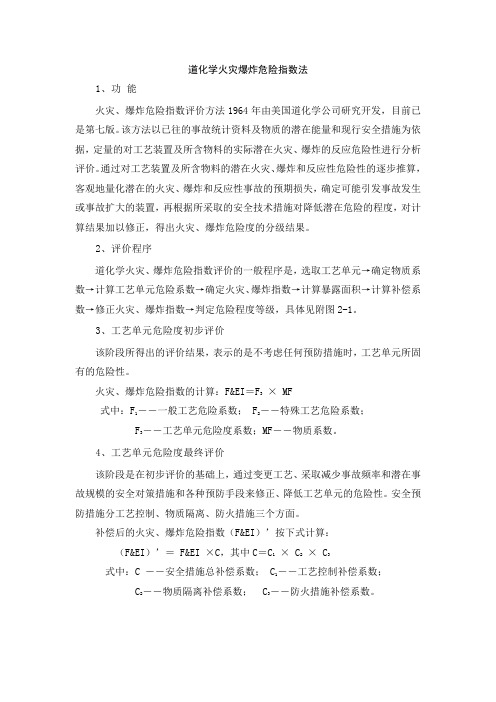
道化学火灾爆炸危险指数法1、功能火灾、爆炸危险指数评价方法1964年由美国道化学公司研究开发,目前已是第七版。
该方法以已往的事故统计资料及物质的潜在能量和现行安全措施为依据,定量的对工艺装置及所含物料的实际潜在火灾、爆炸的反应危险性进行分析评价。
通过对工艺装置及所含物料的潜在火灾、爆炸和反应性危险性的逐步推算,客观地量化潜在的火灾、爆炸和反应性事故的预期损失,确定可能引发事故发生或事故扩大的装置,再根据所采取的安全技术措施对降低潜在危险的程度,对计算结果加以修正,得出火灾、爆炸危险度的分级结果。
2、评价程序道化学火灾、爆炸危险指数评价的一般程序是,选取工艺单元→确定物质系数→计算工艺单元危险系数→确定火灾、爆炸指数→计算暴露面积→计算补偿系数→修正火灾、爆炸指数→判定危险程度等级,具体见附图2-1。
3、工艺单元危险度初步评价该阶段所得出的评价结果,表示的是不考虑任何预防措施时,工艺单元所固有的危险性。
火灾、爆炸危险指数的计算:F&EI=F3× MF式中:F1――一般工艺危险系数; F2――特殊工艺危险系数;F3――工艺单元危险度系数;MF――物质系数。
4、工艺单元危险度最终评价该阶段是在初步评价的基础上,通过变更工艺、采取减少事故频率和潜在事故规模的安全对策措施和各种预防手段来修正、降低工艺单元的危险性。
安全预防措施分工艺控制、物质隔离、防火措施三个方面。
补偿后的火灾、爆炸危险指数(F&EI)’按下式计算:(F&EI)’=F&EI ×C,其中C=C1× C2× C3式中:C ――安全措施总补偿系数; C1--工艺控制补偿系数;C 2――物质隔离补偿系数; C3――防火措施补偿系数。
附图2-1 道化学火灾、爆炸危险指数评价程序5、危险等级的确定附表3-4 危险等级分级表本评价方法的最终目的是得到可靠的评价结论,并根据评价结论提出相应的补偿措施;一般来说,只有工程中所有单元的补偿火灾、爆炸危险度均小于“Ⅳ”级,工程装置才可以通过安全设计,从而达到安全生产的基本要求。
道化学火灾爆炸指数评价法

道化学火灾、爆炸指数评价法1 目的美国道化学公司自1964年开发“火灾、爆炸危险指数评价法”第一版以来,历经29年,不断修改完善;在1993年推出了第七版,以已往的事故统计资料及物质的潜在能量和现行安全措施为依据,定量地对工艺装置及所含物料的实际潜在火灾、爆炸和反应危险性行分析评价,可以说更趋完善、更趋成熟;其目的是:1量化潜在火灾、爆炸和反应性事故的预期损失;2确定可能引起事故发生或使事故扩大的装置;3向有关部门通报潜在的火灾、爆炸危险性;4使有关人员及工程技术人员了解到各工艺部门可能造成的损失,以此确定减轻事故严重性和总损失的有效、经济的途径;2 评价计算程序评价计算程序如下:火灾、爆炸危险指数评价法风险分析计算程序如图1所示;图1 风险分析计算程序3 火灾、爆炸危险指数及补偿系数火灾、爆炸危险指数及补偿系数见表1、表2、表3及表4;表1 火灾、爆炸指数F&EI表4 DOW方法计算说明4.1 选择工艺单元确定评价单元:进行危险指数评价的第一步是确定评价单元,单元是装置的一个独立部分,与其他部分保持一定的距离,或用防火墙;定义:工艺单元——工艺装置的任一主要单元;生产单元——包括化学工艺、机械加工、仓库、包装线等在内的整个生产设施;恰当工艺单元——在计算火灾、爆炸危险指数时,只评价从预防损失角度考虑对工艺有影响的工艺单元,简称工艺单元;选择恰当工艺单元的重要参数有下列6个;一般,参数值越大,则该工艺单元就越需要评价;1潜在化学能物质系数;2工艺单元中危险物质的数量;3资金密度每平方米美元数;4操作压力和操作温度;5导致火灾、爆炸事故的历史资料;6对装置起关键作用的单元;选择恰当工艺单元时,还应注意以下几个要点:1由于火灾、爆炸危险指数体系是假定工艺单元中所处理的易燃、可燃或化学活性物质的最低量为2268kg或2.27m3,因此,若单元内物料量较少,则评价结果就有可能被夸大;一般,所处理的易燃、可燃或化学活性物质的量至少为454kg或0.454m3,评价结果才有意义;2当设备串联布置且相互间未有效隔离,要仔细考虑如何划分单元;3要仔细考虑操作状态如开车、正常生产、停车、装料、卸料、填加触媒等及操作时间,对F&EI有影响的异常状况,判别选择一个操作阶段还是几个阶段来确定重大危险;4在决定哪些设备具有最大潜在火灾、爆炸危险时,可以请教设备、工艺、安全等方面有经验的工程技术人员或专家; 4.2 物质系数的确定物质系数MF是表述物质在燃烧或其他化学反应引起的火灾、爆炸时释放能量大小的内在特性,是一个最基础的数值;物质系数是由美国消防协会规定的NF 、NR分别代表物质的燃烧性和化学活性决定的;通常,NF 和NR是针对正常温度环境而言的;物质发生燃烧和反应的危险性随着温度的升高而急剧加大,如在闪点之上的可燃液体引起火灾的危险性就比正常环境温度下的易燃液体大得多,反应的速度也随着温度的升高而急剧加大,所以当温度超过60℃,物质系数要修正,其内容见物质系数修正表;附表中提供了大量的化学物质系数,它能用于大多数场合;附表中未列出的物质,其NF 、NR可以根据NFPA325M或NFPA49加以确定,并依照温度修正后,由表9—7确定其物质系数;对于可燃性粉尘而言,确定其物质系数时用粉尘危险分级值Sc而不是NF;1表外的物质系数在求取附表、NFPA49和NFPA325中未列出的物质、混合物或化合物的物质系数时,必须确定其可燃性等级NF 或可燃性粉尘等级St,必须首先确定有表5左栏中的参数,液体和气体的NF由闪点求得,粉尘或尘雾的St值由粉尘爆炸试验确定;可燃固体的NF值则依其性质不同在表5左栏中分类标示;表5 物质系数取值表物质、混合物或化合物的反应性等级NR根据其在环境温度条件下的不稳定性或与水反应的剧烈程度,按NFPA704确定;NR=0:在燃烧条件下仍保持稳定的物质,通常包括以下物质:①不与水反应的物质;②在温度>300~500℃时用差热扫描量热计DSC测量显示温升的物质;③用DSC试验时,在温度≤500℃时不显示温升的物质;NR=1:稳定,但在加温加压条件下成为不稳定的物质,一般包括如下物质:①接触空气、受光照射或受潮时发生变化或分解的物质;②在>150~300℃时显示温升的物质;=2:在加温加压条件下发生剧烈化学变化的物质:NR①用DSC做试验,在温度≤150℃时显示温升的物质;②与水剧烈反应或与水形成潜在爆炸性混合物的物质;=3:本身能发生爆炸分解或爆炸反应,但需要强引发源或引发前必须在密闭状态下加热的物质:NR①加温加热时对热机械冲击敏感的物质;②加温加热时或密闭,即与水发生爆炸反应的物质;=4:在常温常压下易于引爆分解或发生爆炸反应的物质;NR注意:反应性包括自身反应性不稳定性和与水反应性;物质的NR指标由差热分析仪DTA或差示扫描量热计DSC分析其温升的最低峰值温度来判断,按表6分类:几个附加限制条件是:1若该物质为氧化剂,则NR再加1但不超过4;2对冲击敏感性物质,NR为3或4;3如得出的NR值与物质的特性不相符,则应补做化学品反应性试验;一旦求出并确定NF 、NR,就可以用表5确定物质系数;2混合物工艺单元内混合物物质应按“在实际操作过程中所存在的最危险物质”原则来确定;发生剧烈反应的物质,如氢气和氯气在人工条件下混合、反应,反应持续而快速,生成物为非燃烧性、稳定的产物,则其物质系数应根据初始混合状态来确定;混合溶剂或含有反应性物质溶剂的物质系数,可通过反应性化学试验数据求得;若无法取得时,则应取组分中最大的MF作为混合物MF的近似值最大组分浓度≥5%;对由可燃粉尘和易燃气体在空气中能形成爆炸性的混合物,其物质系数必须用反应性化学品试验数据来确定;3烟雾易燃或可燃液体的微粒悬浮于空气中能形成易燃的混合物,它具有易燃气体—空气混合物的一些特性;易燃或可燃液体的雾滴在远远低于其闪点的温度下,能像易燃蒸汽—空气混合物那样具有爆炸性;因此,防止烟雾爆炸的最佳有效防护措施是避免烟雾的形成,特别是不要在封闭的工艺单元内使可燃液体形成烟雾;如果会形成烟雾,则需将物质系数提高1级,并请教有关专家;4物质系数的温度修正如果物质闪点小于60℃或反应活性温度低于60℃,则该物质系数不需要修正;若工艺单元温度超过60℃,则对MF应作修正,见表7;4.3 工艺单元危险系数F3工艺单元危险系数F3包括—般工艺危险系数F1和特殊工艺危险系数F2,对每项系数都要恰当地进行评价;计算工艺单元危险系数F3中各项系数时,应选择物质在工艺单元中所处的最危险的状态,可以考虑的操作状态有:开车、连续操作和停车;计算F&EI时,一次只评价一种危险,如果MF是按照工艺单元中的易燃液体来确定的,就不要选择与可燃性粉尘有关的系数,即使粉尘可能存在于过程中的另一段时间内;合理的计算方法为:先用易燃液体的物质系数进行评价,然后再用可燃性粉尘的物质系数评价,只有导致最高的F&EI和实际的可能的最大财产损失的计算结果才需要报告;一个重要的例外是混合物,如果某种混杂在一起的混合物被视作最高危险物质的代表,则计算工艺单元危险系数时,可燃性粉尘和易燃蒸气的系数都要考虑;一般工艺危险性一般工艺危险是确定事故损害大小的主要因素,共有6项;根据实际情况,并不是每项系数都采用,各项系数的具体取值参见以下方面:1放热化学反应若所分析的工艺单元有化学反应过程,则选取此项危险系数,所评价物质的反应性危险已经为物质系数所包括:1轻微放热反应的危险系数为0.3,包括加氢、水合、异构化、磺化、中和等反应;2中等放热反应系数为0.5,包括:①烷基化——引入烷基形成各种有机化合物的反应;②酯化——有机酸和醇生成酯的反应;③加成——不饱和碳氢化合物和无机酸的反应,无机酸为强酸时系数增加到0.75;④氧化——物质在氧中燃烧生成CO2,H2O的反应,或者在控制条件下物质与氧反应不生成CO2,H2O的反应,对于燃烧过程及使用氯酸盐、硝酸、次氯酸、次氯酸盐类强氧化剂时,系数增加到1.00;⑤聚合——将分子连接成链状物或其他大分子的反应;⑥缩合——两个或多个有机化合物分子连接在一起形成较大分子的化合物,并放出H2O和HCl的反应;3剧烈反应——指—旦反应失控有严重火灾、爆炸危险的反应,如卤化反应,取1.00;4特别剧烈的反应,系数取1.25,指相当危险的放热反应;2吸热反应反应器中所发生的任何吸热反应,系数均取0.25;1煅烧——加热物质除去结合水或易挥发性物质的过程,系数取为0.40;2电解——用电流离解离子的过程,系统为0.20;3热解或裂化——在高温、高压和触媒作用下,将大分子裂解成小分子的过程,当用电加热或高温气体间解加热时,系数为0.20;直接火加热时,系数为0.4;3物料处理与输送本项目用于评价工艺单元在处理、输送和贮存物料时潜在的火灾危险性;1所有Ⅰ类易燃或液化石油气类的物料在连接或未连接的管线上装卸时的系数为0.5;2采用人工加料,且空气可随时加料进入离心机、间歇式反应器、间歇式混料器设备内,并且能引起燃烧或发生反应的危险,不论是否采用惰性气体置换,系数均取0.5;3可燃性物质存放于库房或露天时的系数为:①对NF =3或NF=4的易燃液体或气体,系数取0.85,包括桶装、罐装、可移动挠性容器和气溶胶罐装;②对表9—7中所列NF=3的可燃固体,系数取0.5;③对表中所列NF=2的可燃性固体,系数取0.4;④对闭杯闪点大于37.8℃并低于60℃的可燃性液体,系数取0.25;若上述物质存放于货架上且未安设洒水装置时,系数要加0.20,此处考虑的范围不适合于一般贮存容器;4封闭单元或室内单元处理易燃液体和气体的场所为敞开式,有良好的通风,以便能迅速排除泄漏的气体和蒸气,减少了潜在的爆炸危险;粉尘捕集器和过滤器也应放置在敞开区域并远离其他设备;封闭区域定义为有顶且三面或多面有墙壁的区域,或无顶但四周有墙封闭的区域;封闭单元内即使专门设计有机械通风,其效果也不如敞开式结构,但如果机械通风系统能收集所有的气体并排出去的话,则系数可以降低;系数选取原则如下:1粉尘过滤器或捕集器安置在封闭区域内时,系数取0.50;2在封闭区域内,在闪点以上处理易燃液体时,系数取0.3;如果处理易燃液体量>4540kg,系数取0.45;3在封闭区域内,在沸点以上处理液化石油气或任何易燃液体量时,系数取0.6;若易燃液体的量大于4540k8,则系数取0.90;4若已安装了合理的通风装置时,1、3两项系数减50%;5通道生产装置周围必须有紧急救援车辆的通道,“最低要求”是至少在两个方向上设有通道,选取封闭区域内主要工艺单元的危险系数时要格外注意;至少有一条通道必须是通向公路的,火灾时消防道路可以看做是第二条通道,设有监控水枪并处于待用状态;整个操作区面积大于925m2,且通道不符合要求时,系数为0.35;整个库区面积大于2315m2,且通道不符合要求时,系数为0.35;面积小于上述数值时,要分析它对通道的要求;如果通道不符合要求,影响消防时,系数取0.20;6排放和泄漏控制此项内容是针对大量易燃、可燃液体溢出危及周围设备的情况,不合理的排放设计已成为造成重大损失的原因;该项系数仅适用于工艺单元内物料闪点60℃或操作温度大于其闪点的场合;为了评价排放和泄漏控制是否合理,必须估算易燃、可燃物总量以及消防水能否在事故时得到及时排放;1F&EI计算表中排放量按以下原则确定:①对工艺和贮存设备,取单元中最大储罐的贮量加上第二大储罐10%的贮量;②采用30min的消防水量;将上述①、②两项之和填入F&EI计算表中一般工艺危险的F&EI;2系数选取的原则:①设有堤坝防止泄漏液流入其他区域,但堤坝内所有设备露天放置时,系数取0.5;②单元周围为一可排放泄漏液的平坦地,一旦失火,会引起火灾,系数为0.5;③单元的三面有堤坝,能将泄漏液引至蓄液池的地沟,并满足以下条件,不取系数:·蓄液池或地沟的地面斜度不得小于下列数值:土质地面为2%,硬质地面为1%;·蓄液池或地沟的最外缘与设备的之间的距离至少小于15m,如果没有防火墙,可以减少其距离;·蓄液池的贮液能力至少等于1中①与②之和;④如蓄液池或地沟处设有公用工程管线或管线的距离不符合要求,系数取0.5;简而言之,有良好的排放设施才可以不取危险系数;特殊工艺危险性特殊工艺危险是影响事故发生概率的主要因素,特定的工艺条件是导致火灾、爆炸事故的主要原因;特殊工艺危险有下列12项;1毒性物质毒性物质能够扰乱人们机体的正常反应,因而降低了人们在事故中制定对策和减轻伤害的能力;毒性物质的危险系数为0.2×NH,对于混合物,取其中最高的NH值;N H 是美国消防协会在NFPA704中定义的物质毒性系数,其值在NFPA 325 M或NFPA49中已列出;附表中给出了许多物质的NH值;对于新物质,可请工业卫生专家帮助确定;NFPA704对物质的NH分类为:NH=0 火灾时除一般可燃物的危险外,短期接触没有其他危险的物质;NH=1 短期接触可引起刺激,致人轻微伤害的物质,包括要求使用适当的空气净化呼吸器的物质;NH=2 高浓度或短期接触可致人暂时失去能力或残留伤害的物质,包括要求使用单独供给空气的呼吸器的物质;N=3 短期接触可致人严重的暂时或残留伤害的物质,包括要求全身防护的物质;H=4 短暂接触也能致人死亡或严重伤害的物质;NH注:上述毒性系数NH值只是用来表示人体受害的程度,它可导致额外损失;该值不能用于职业卫生和环境的评价;2负压操作本项内容适用于空气泄入系统会引起危险的场合;当空气与湿度敏感性物质或氧敏感性物质接触时可能引起危险,在易燃混合物中引入空气也会导致危险;该系数只用于绝对压力小于500mmHg66661Pa的情况;系数为0.50;如果采用了本项系数,就不要再采用下面“燃烧范围内或其附近的操作”和“释放压力”中的系数,以免重复;大多数汽提操作,一些压缩过程和少许蒸馏操作都属于本项内容;表压=绝对压力—大气压3燃烧范围或其附近的操作某些操作导致空气引入并夹带进入系统,空气的进入会形成易燃混合物,进而导致危险;本条款将讨论以下有关情况:1NF =3或NF=4的易燃液体贮罐,在贮罐泵出物料或者突然冷却时可能吸入空气,系数取0.50;打开放气阀或在负压操作中未采用惰性气体保护时,系数为0.50;贮有可燃液体,其温度在闭杯闪点以上且无惰性气体保护时,系数也为0.50;如果使用了惰性化的密闭蒸汽回收系统,且能保证其气密性则不用选取系数;2只有当仪表或装置失灵时,工艺设备或贮罐才处于燃烧范围内或其附近,系数为0.30;任何靠惰性气体吹扫,使其处于燃烧范围之外的操作,系数为0.30,该系数也适用于装载可燃物的船舶和槽车;若已按“负压操作”选取系数,此处不再选取;3由于惰性气体吹扫系统不实用或者未采取惰性气体吹扫,使操作总是处于燃烧范围内或其附近时,系数为0.80;4粉尘爆炸粉尘最大压力上升速度和最大压力值主要受其粒径大小的影响;通常,粉尘越细,危险性越大;这是由于细尘具有很高的压力上升速度和极大压力伴生;本项系数将用于含有粉尘处理的单元,如粉体输送、混合粉碎和包装等;所有粉尘都有一定的粒径分布范围;为了确定系数,采用10%粒径,即在这个粒径处有90%粗粒子,其余10%为细粒子;根据表8确定合理的系数;除非粉尘爆炸试验已经证明没有粉尘爆炸危险,否则都要考虑粉尘系数;5释放压力操作压力高于大气压时,由于高压可能会引起高速率的泄漏,因此要采用危险系数;是否采用系数,取决于单元中的某些导致易燃物料泄漏的构件是否会发生故障;例如:己烷液体通过6.5cm2的小孔泄漏,当压力为517kPa表压时,泄漏量为272kg/min;压力为2069kPa表压时,泄漏量为上述的2.5倍即680kg/min;用释放压力系数确定不同压力下的特殊泄漏危险潜能,释放压力还影响扩散特性;由于高压使泄漏可能性大大增加,所以随着操作压力提高,设备的设计和保养就变得更为重要;系统操作压力在20685kPa表压以上时,超出标准规范的范围美国机械工程师学会非直接火加热压力容器规范中第八章第一节;对于这样的系统,在法兰设计中必须采用透镜垫圈、圆锥密封或类似的密封结构;参见图2,根据操作压力确定初始危险系数值;下列方程适用于压力为0~6895kPa表压时危险系数Y的确定;译者注:直接引用原文公式,故公式中的压力即X值的单位应为“磅/英寸2”;Y=0.16109+1.61503X/1000-1.42879X/10002+0.5172X/10003图2 易燃、可燃液体的压力危险系数图表9可确定压力为0~6895kPa表压的易燃、可燃液体的压力系数也包括图2在内;用图2中的曲线能直接确定闪点低于60℃的易燃可燃液体的系数;对其他物质可先由曲线查出初始系数值,再用下列方法加以修正:1焦油、沥青、重润滑油和柏油等高粘性物质,用初始系数乘以0.7作为危险系数;2单独使用压缩气体或利用气体使易燃液体压力增至103kPa表压以上时,用初始系数值乘以1.2作为危险系数;3液化的易燃气体包括所有在其沸点以上贮存的易燃物料,用初始系数值乘以1.3作为危险系数;确定实际压力系数时,首先由图2查出操作压力系数,然后求出释放装置设定压力系数,用操作压力系数除以设定压力系数得出实际压力系数调整系数,再用该调整系数乘以操作压力系数求得实际压力系数;这样,就对那些具有较高设定压力和设计压力的情况给予了补偿;注意调节释放压力使之接近于容器设计压力是非常有利的;例如,对于使用易挥发溶剂,特别是气态的反应,可以通过调节反应中释放的温度并根据反应物质及有关动力学数据,用计算机模拟来确定是否需要释放压力;但是在一些反应系统中并不需要释放压力;在一些特定场合,增加压力容器的设计压力以降低释放的可能性是有利的,在有些场合也许能达到容器的最大允许压力;6低温本项主要考虑碳钢或其他金属在其展延或脆化转变温度以下时可能存在的脆性问题;如经过认真评价,确认在正常操作和异常情况下均不会低于转变温度,则不用系数;测定转变温度的一般方法是对加工单元中设备所用的金属小样进行标准摆锤式冲击试验,然后进行设计,使操作温度高于转变温度;正确设计应避免采用低温工艺条件;系数给定原则为:1采用碳钢结构的工艺装置,操作温度等于或低于转变温度时,系数取0.30;如果没有转变温度数据,则可假定转变温度为10℃;2装置为碳钢以外的其他材质,操作温度等于或低于转变温度时,系数取0.20;切记,如果材质适于最低可能的操作温度,则不用给系数;7易燃和不稳定物质的数量易燃和不稳定物质数量主要讨论单元中易燃物和不稳定物质的数量与危险性的关系;分为3种类型,用各自的系数曲线分别评价;对每个单元而言,只能选取一个系数,依据是已确定为单元物质系数代表的物质;1工艺过程中的液体或气体;该系数主要考虑可能泄漏并引起火灾危险的物质数量,或因暴露在火中可能导致化学反应事故的物质数量;它应用于任何工艺操作,包括用泵向贮罐送料的操作;该系数适用于下列已确定作为单元物质系数代表的物质:①易燃液体和闪点低于60℃的可燃液体;②易燃气体;③液化易燃气;④闭杯闪点大于60℃的可燃液体,且操作温度高于其闪点时;=2,3或4;⑤化学活性物质,不论其可燃性大小NR确定该项系数时,首先要估算工艺中的物质数量kg;这里所说的物质数量是在10min内从单元中或相连的管道中可能泄漏出来的可燃物的量;在判断可能有多少物质泄漏时要借助于一般常识;经验表明,取下列两者中的较大值作为可能泄漏量是合理的:a.工艺单元中的物料量;b.相连单元中的最大物料量;紧急情况时,通过遥控关闭阀门,使相连单元与之隔离的情况不在考虑之列;在正确估计工艺中物质数量之前,要回答的问题是“什么是最大可能的泄漏量”当你熟悉了工艺后,做出判断的结果与上述估算有较大差异时,只要确信你的结果可靠,就应当采用它;记住:凭借你对工艺的熟悉和良好的判断,总能使你得到更为符合实际的估算值;但要注意:如果泄漏物具有不稳定性化学反应性时,泄漏量一般以工艺单元内的物料量为准;例:加料槽、缓冲罐和回流罐是与单元相连的一类设备,它们可能装有比评价单元更多的物料;可是,如果这些容器都配备遥控切断阀,则不能把它们看做是“与工艺单元相连的设备”;在火灾、爆炸指数计算表的特殊工艺危险的“G”栏中的有关空格中填写易燃或不稳定物质的合适数量;使用图3时,将求出的工艺过程中的可燃或不稳定物料总量乘以燃烧热HcJ/kg,得到总热量J;燃烧热Hc可以从附表或化学反应试验数据中查得;对于NR =2或NR值更大的不稳定物质,其Hc值可取6倍于分解热或燃烧热中的较大值;分解热也可从化学反应试验数据中查得;在火灾、爆炸指数计算表的特殊工艺危险“G”栏有关空格处填入燃烧热HcJ/kg值;。
道化学火灾爆炸指数评价法在合成氨装置转化工序安全性评价中的应用
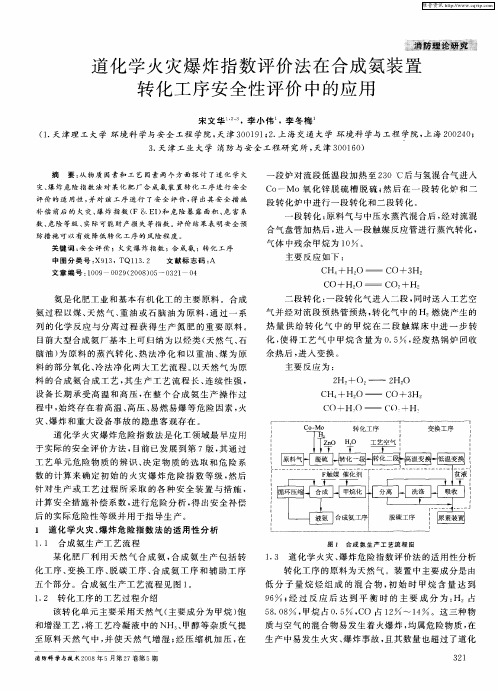
一
段 炉对 流段低 温段加 热至 2 0 C后 与氢混 合气进 入 3
灾、 炸 危 险 指数 法 对 某 化 肥 厂 合 成 氨 装 置 转 化 工序 进 行 安 全 爆
C —Mo氧化 锌脱 硫 槽 脱硫 ; 后 在一 段 转 化炉 和 二 o 然 段转 化炉 中进行一 段转化 和二 段转化 。
后 的实 际危险性 等级并 用 于指导生 产 。 1 道 化 学 火 灾 、 炸 危 险 指 数 法 的 适 用 性 分 析 爆
1 1 合成 氨生 产工艺 流程 . 某化 肥 厂利 用 天然 气 合成 氨, 合成 氨 生产 包 括 转
l 合 成 氦 生 严 工 艺 流 程 图
1 3 道 化 学 火 灾 、 炸 危 险 指 数 评 价 法 的 适 用 性 分 析 . 爆
低分子量烷烃组成 的混合物 , 初始 时 甲烷 含 量 达 到
9 ; 过 反 应 后 达 到平 衡 时 的 主 要 成 分 为 : 6 经 H。占
5.8 , 8 0 甲烷 占0 5 , O 占 1 ~1 。这三 种物 . C 2 4
质与空 气 的混 合物 易发生 着火爆 炸 , 均属 危 险物质 , 在 生 产 中易发生 火灾 、 炸事故 , 其数量也 超过 了道化 爆 且
料 的 部 分 氧 化 、 法 净 化 两 大 工 艺 流 程 。 天 然 气 为 原 冷 以
料 的合 成氨合 成 工艺 , 生 产工 艺 流程 长 、 其 连续 性 强 , 设 备长期 承 受高 温 和高 压 , 整 个 合成 氨 生产 操 作过 在 程中, 始终存 在着 高温 、 高压 、 易燃 易爆 等 危险 因素 , 火 灾 、 炸和重 大设备 事故 的隐患 客观存 在 。 爆 道 化学火 灾爆 炸危 险指数 法是化 工领域 最早 应用 于实 际的安全 评价方 法 , 目前 已发展 到第 7版 , 其通 过 工艺 单元 危险 物 质的辨 识 、 定物 质 的选 取 和危 险系 决 数 的计算 来确 定 初始 的火 灾 爆炸 危 险指 数 等级 , 后 然 针对 生产 或工 艺过 程所 采 取 的各 种安 全装 置与 措 施 , 计算安全 措施 补偿系 数 , 进行 危 险分析 , 出安全补偿 得
道化学火灾、爆炸指数评价法
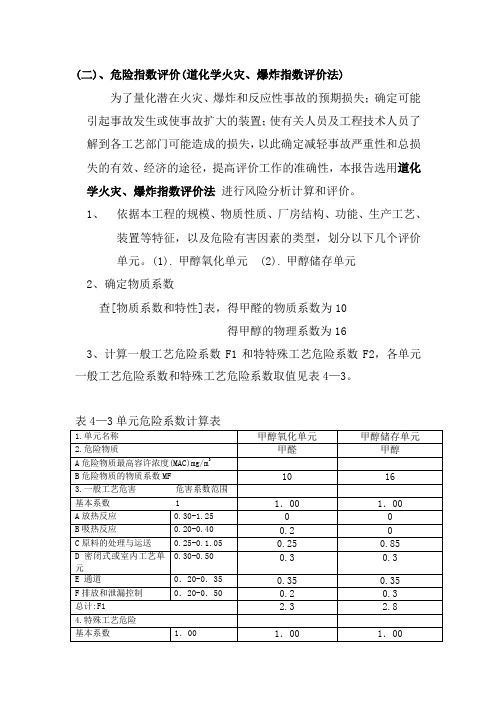
(二)、危险指数评价(道化学火灾、爆炸指数评价法)为了量化潜在火灾、爆炸和反应性事故的预期损失;确定可能引起事故发生或使事故扩大的装置;使有关人员及工程技术人员了解到各工艺部门可能造成的损失,以此确定减轻事故严重性和总损失的有效、经济的途径,提高评价工作的准确性,本报告选用道化学火灾、爆炸指数评价法进行风险分析计算和评价。
1、依据本工程的规模、物质性质、厂房结构、功能、生产工艺、装置等特征,以及危险有害因素的类型,划分以下几个评价单元。
(1). 甲醇氧化单元 (2). 甲醇储存单元2、确定物质系数查[物质系数和特性]表,得甲醛的物质系数为10得甲醇的物理系数为163、计算一般工艺危险系数F1和特特殊工艺危险系数F2,各单元一般工艺危险系数和特殊工艺危险系数取值见表4—3。
表4—3单元危险系数计算表4.火灾爆炸指数F&EIF&EI=MF×F1 ×F2式中:MF —物质系数F1 —一般工艺危险性系数F2 —特殊工艺危险性系数5.评价危险等级单元危险性等级划分情况见表4—4表4—4 F&Ei及危险等级6.单元危险性排序法评价结果分析见表4—5从单危险性排序法评价结果可知甲醇氧化、储存单元的火灾爆炸指数(F&EI)接近61,充装单元超过96,危险等级分别为较轻和中等。
为了降低风险,企业采取了一定的安全措施进行补偿,见补偿后的火灾、爆炸危险等级表。
7、安全措施补偿系数后的火灾、爆炸危险等级见表4-6企业通过从工艺控制、物质隔离、防火防爆等措施,大大降低了火灾、爆炸危险等级,使危险单元处于基本安全状态。
反之危险性很大。
因此,企业仍应引起高度注意,严格按照国家有关安全法律法规,继续巩固和保持已采取的工艺控制、物质隔离、防火防爆等措施,制订更有效的安全控制措施,进一步降低火灾、爆炸危险等级。
火灾爆炸指数法用于加氢厂房的安全评价

加氢 试验 厂房 内 4 0套小 型加 氢 装置 , 工艺 流
程 基本 相 同 , 故选 取 整个 厂房 为 评价 单元 。 加氢 厂
房 概 况如 下 。
加 氢厂 房为 钢筋 混凝 土排 架结 构 , 度 2 跨 4m,
长 度 6 1屋面 设 9m跨 天 窗 , 火 等 级 为二 级 , 01, 3 耐 设 两 个 安 全 疏 散 口 , 散 距 离 为 2 厂 房 建 筑 疏 7m, 面积 1 7 t, 11 容积 1 0 1, 房采 用 侧 窗 、 4 T 0001 厂 3 天
窗 、 屋 面 泄 压 , 压 面 积 9 31 , 压 面 积 与 厂 及 泄 3 1 泄 1
房容 积 比值 为 005 满 足 防火规 范要 求 。 .7 ,
收 稿 日期 :0 0 0 — 3 2 1 — 4 2
现 在 国 内外 以 开发 出许 多 种 安 全评 价 法 , 按
指标 量 化 的体 系可分 为 两大 类 ,即风 险率 法 和相 对法 。 风 险率 评价 法需 要 精确 的 统计 数据 , 评 但 其 价结 果 的准确 率才 比较 高 ;而往 往 由于缺 乏 故 障
放 热 反 应 吸热 反 应 物料储运和输送
31 确 定 物质 系数 ( F . ) 在 加 氢 过程 中 , 气 是 引起 火 灾 、 炸 的最 危 氢 爆
后 在高温 ( 于 4 0 ) 压 ( 于 1 a 条件 下 , 小 5℃ 高 小 7MP )
工 艺概 况 :该 厂 房 现 有小 型加 氢 装 置 4 0套 ,
主要 部 件 由美 国引 进 ,配 备 有先 进 的计 算 机 控 制 系统 , 过 计 算机 可完 成 整套 装 置 的监 控 操 作 , 通 具
火灾、爆炸危险指数评价法
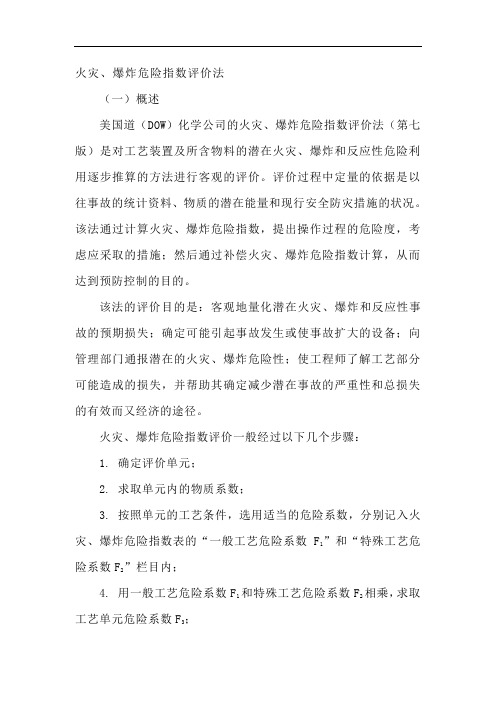
火灾、爆炸危险指数评价法(一)概述美国道(DOW)化学公司的火灾、爆炸危险指数评价法(第七版)是对工艺装置及所含物料的潜在火灾、爆炸和反应性危险利用逐步推算的方法进行客观的评价。
评价过程中定量的依据是以往事故的统计资料、物质的潜在能量和现行安全防灾措施的状况。
该法通过计算火灾、爆炸危险指数,提出操作过程的危险度,考虑应采取的措施;然后通过补偿火灾、爆炸危险指数计算,从而达到预防控制的目的。
该法的评价目的是:客观地量化潜在火灾、爆炸和反应性事故的预期损失;确定可能引起事故发生或使事故扩大的设备;向管理部门通报潜在的火灾、爆炸危险性;使工程师了解工艺部分可能造成的损失,并帮助其确定减少潜在事故的严重性和总损失的有效而又经济的途径。
火灾、爆炸危险指数评价一般经过以下几个步骤:1. 确定评价单元;2. 求取单元内的物质系数;3. 按照单元的工艺条件,选用适当的危险系数,分别记入火灾、爆炸危险指数表的“一般工艺危险系数F1”和“特殊工艺危险系数F2”栏目内;4. 用一般工艺危险系数F1和特殊工艺危险系数F2相乘,求取工艺单元危险系数F3;5. 将工艺单元危险系数F3与物质系数相乘,求出火灾、爆炸危险指数(F&EⅠ),根据火灾、爆炸危险指数及危险等级表确定单元的危险程度,完成单元危险度的初期评价;6. 根据单元内配备的安全设施,选取各项系数,求出安全补偿系数;7. 利用安全补偿系数,求取补偿火灾、爆炸危险指数(F&EⅠ)′;8. 按照补偿火灾、爆炸危险指数(F&EⅠ)′,确定补偿后的单元危险程度,计算单元的暴露区域半径和暴露面积。
火灾、爆炸危险指数分析计算程序如图4-3-2。
图4-3-2 火灾、爆炸危险指数分析计算程序(二)评价过程1. 工艺单元选择工艺单元是指工艺装置的任一主要单元,仓库也可以作为一个工艺单元。
多数工厂是由多个单元组成,但在计算火灾、爆炸指数时,只选择那些从损失预防角度来看对工艺有影响的工艺单元进行评价,这些单元称为恰当工艺单元,简称工艺单元。
火灾、爆炸危险指数评价

火灾、爆炸危险危险指数评价(道化法)目前国际上比较通用的是美国道化学公司的火灾爆炸危险指数评价方法。
(第七版)(以下简称道七版),通过计算火灾、爆炸危险指数,划分危险等级,并进行采取安全对策措施加以补偿的最终危险指数评价,判定危险度是否可以接受。
对工程进行安全评价时,只有工程中所有单元的补偿火灾、爆炸危险等级均不超过“高”,才可以通过,说明达到了安全生产的基本要求。
否则,应对工程修改完善或增加安全防护措施,直至重新评价通过为止。
适用范围:火灾爆炸指数是对工业装置及所含物料的实际潜在火灾、爆炸和反应性危险进行按步推算的客观评价。
主要用于评价贮存、处理、生产易燃、可燃、活性物质的操作过程,也可用于评价污水处理设施、公用工程系统、管道、整流器、变压器、锅炉等单元的潜在损失。
其中,易燃或活性化学物质的最小处理量为454k9左右的单元。
1、评价程序评价程序2、确定评价单元单元是装置或部位的相对独立部分,与其它部分保持一定的距离。
通常也可把危险性潜能类似的单元归并为一个较大的单元。
3、单元危险度的初期评价(表示的是不考虑任何预防措施时,单元所固有的火灾爆炸危险性)3、1 计算火灾爆炸危险指数,按下式计算:F ﹠EI=F 3×MF式中:MF----物质系数F 3------工艺单元危险系数;F3=F1×F2 F1------一般工艺危险系数; F2------特殊工艺危险系数。
3、2 确定暴露区域半径(R )R=0.84×0.3048×F ﹠EI (单位:米) 3、3 确定暴露区域面积 (S )S=3.14×R2 (m2)4、单元危险度的最终评价(补偿措施后的火灾爆炸危险指数)(F﹠EI)'=F﹠EI×C式中:(F﹠EI)'------补偿火灾爆炸危险指数F﹠EI----------- 固有的火灾爆炸危险指数C----------------安全措施总补偿系数,C= C1×C2×C3式中:C1----工艺控制补偿系数C2-------物质隔离补偿系数C3-------防火措施补偿系数补偿系数取值分别按《道七版》所确定的原则选取。
火灾爆炸指数

火灾爆炸指数评价法简介1概念定量分析。
① 量化潜在火灾、爆炸和反应性事故的预期损失;② 确定可能引起事故发生或使事故扩大的装置;③ 向有关部门通报潜在的火灾、爆炸危险性;④ 使有关人员及工程技术人员了解到各工艺部门可能造成的损失,以此确定减轻事故严重性和总损失的有效、经济的途径。
2基本方法介绍基本程序见下图1)选择工艺单元选择恰当工艺单元的重要参数有下列六个:① 潜在的化学能(物质系数);② 工艺单元中危险物质的数量;③ 资金密度(每平方米美元数);④ 操作压力和操作温度;⑤ 导致火灾、爆炸事故的历史资料;⑥ 对装置起关键作用的单元。
一般参数值越大,则该工艺单元就越需要评价。
该方法是假定工艺单元中所处理的易燃、可燃或化学活性物质的最低量为2270千克或2.27立方米。
因此,若单元内物料较少,则评价结果有可能被夸大。
一般,所处理的易燃、可燃或者化学活性物质的量至少为454千克或0.454立方米,评价结果才有意义。
3)评价计算① 火灾、爆炸危险指数(F&EI)a.物质系数(MF)的选取物质系数是表述物质在燃烧或其他化学反应引起火灾、爆炸时释放能量大小的内在特性,是一个最基础的数值。
它是由美国消防协会规定的NF、NR(分别代表物质的燃烧性和化学活性)决定的。
b.一般工艺危险系数(F1)的选取选取项包括“基本系数、放热化学反应、吸热反应、物料处理与输送、封闭式或室内工艺单元、通道、排放、泄漏控制”等7个取值项。
基本系数取1.00,其它6项根据实际情况具体取值,无危险时系数用0.00。
一般工艺危险系数为7项取值之和。
c.特殊工艺危险系数(F2)的选取选取项包括“基本系数、毒性物质、负压操作、接近易燃范围的操作、粉尘爆炸、压力、低温、物质的量和燃烧热、腐蚀与磨损、泄漏、使用明火设备、热油热交换系统、传动设备”等13个取值项。
基本系数取1.00,其它12项根据实际情况具体取值,无危险时系数用0.00。
- 1、下载文档前请自行甄别文档内容的完整性,平台不提供额外的编辑、内容补充、找答案等附加服务。
- 2、"仅部分预览"的文档,不可在线预览部分如存在完整性等问题,可反馈申请退款(可完整预览的文档不适用该条件!)。
- 3、如文档侵犯您的权益,请联系客服反馈,我们会尽快为您处理(人工客服工作时间:9:00-18:30)。
( 安全论文 )单位:_________________________姓名:_________________________日期:_________________________精品文档 / Word文档 / 文字可改火灾爆炸指数法用于加氢厂房的安全评价(新编版)Safety is inseparable from production and efficiency. Only when safety is good can we ensure better production. Pay attention to safety at all times.火灾爆炸指数法用于加氢厂房的安全评价(新编版)加氢试验厂房是中国石化抚顺石油化工研究院投资最大、装置最集中的场所,是防火重点部位,做好它的安全评价可以使管理者了解事故隐患和薄弱环节,全面掌握该部位的安全状况,不断改进、完善安全防灾体系与设施,也可据此确定系统是否需要改进设计或增加安全措施,明确改进后的危险性是否达到可以接受的程度,以预防事故发生,实现系统最佳安全的目的。
由于加氢试验厂房中均为小型试验装置,故在评价中有别于工业装置,部分选项视情况可以忽略不计。
1安全评价方法选择现在国内外以开发出许多种安全评价法,按指标量化的体系可分为两大类,即风险率法和相对法。
但风险率评价法需要精确的统计数据,其评价结果的准确率才比较高;而往往由于缺乏故障由于液氯生产系统承担着氯气液化、贮存、气化、精制和包装等关键生产过程,设备服役运行多年,生产过程的各工艺控制参数要求苛刻,一旦超概率数据,应用起来有一定的困难。
目前应用较多的是相对法,也称指数法或评点法,这类方法是根据过去经验或有关资料,采用一系列相对数值来度量危险性的大小,经综合评价,确定系统安全程度。
本文采用的评价方法为美国道化学公司火灾爆炸指数评价法[1],该评价法是以工艺过程中使用、生产物质的理化特性为基础,结合工艺条件、物料量等因素求取火灾爆炸指数。
2确定评价单元加氢试验厂房内40套小型加氢装置,工艺流程基本相同,故选取整个厂房为评价单元。
加氢厂房概况如下。
加氢厂房为钢筋混凝土排架结构,跨度24m,长度60m,屋面设9m跨天窗,耐火等级为二级,设两个安全疏散口,疏散距离为27m,厂房建筑面积1471m2,容积10000m3,厂房采用侧窗、天窗、及屋面泄压,泄压面积933m2,泄压面积与厂房容积比值为0.075,满足防火规范要求。
2HAZOP分析由于液氯生产系统承担着氯气液化、贮存、气化、精制和包装等关键生产过程,设备服役运行多年,生产过程的各工艺控制参数要求苛刻,一旦操作或控制失误,将会对整个氯碱生产系统造成严重威胁,甚至发生容器爆炸,造成氯大量外泄,给职工、周围居民乃至社会造成极大危害。
限于篇幅,以下仅对危险性最大的液氯贮槽进行HAZOP分析。
2.1分析单元液氯贮槽主要控制的工艺参数:液氯贮槽的温度、液位、压力。
分析单元(节点)为液氯输送泵1的进口阀门至液氯输送泵2的进口阀门,如图1所示。
2.2分析结果及讨论仅以液氯贮罐液位的HAZOP分析为例加以说明,HAZOP分析结果见表1。
引导词偏差原因后果已采取的安全措施建议措施NONE(空白)无液位1)液氯进口阀关闭2)进口管线堵塞3)进口阀门盲板未拆4)液化器相连管线断裂5)液位变送器指示错误6)液氯输送泵无流量或憋压7)去包装的液氯管线泄漏8)设备或管线保温腐蚀,穿孔泄漏1)无液位即罐内无液氯2)液氯(或液氯汽化后)泄漏1)系统所有阀门处于受控状态2)严格执行盲板管理规定,按照盲板图挂牌、装拆、消项,专人管理3)设置了液位低低报联锁停车报警系统;现场设置双液位检测4)液位控制阀定期检验保养5)控制系统设置了冗余系统,并定期保养6)现场安装了有毒气体报警仪探头7)可以把液氯转送到另外的贮槽。
用两个贮槽液面指示的减增来判断失常的液面计8)随时检查液位上升情况9)调节阀失常时,转换到备用系统10)与液氯精制器压力控制联锁1)选择符合材质要求的阀门2)所有阀门设有打开的标志,并有书面确认程序3)按照规范增设有毒气体报警仪数量,信号引至中央控制室4)加强现场巡检5)增设固定碱液喷淋设施,使得喷淋面积覆盖整个贮槽6)事故氯吸收系统扩容,增加1台事故氯气吸收塔;并优化运行工艺,吸收塔负压操作7)对操作工加强培训,严格执行操作规程和安全技术规程8)现有厂房门窗关闭不严,改为塑钢门窗9)定期进行设备强检MORE(过量)液位偏高1)后续系统故障2)后续系统阀门关闭或开度不够3)现场液位计与控制室DCS液位指示有偏差,仪表指示故障1)安全阀起跳2)液化器液位升局3)导致后续系统压力上升I)液氯贮罐本体设置安全阀,排放管线并人事故氯吸收装置2)安全阀根阀必须处于全开状态并锁定3)建立液化器定期排污制度。
并做好确认记录。
加强分析样品的检验及审查1)加强巡检,发现故障及时处理2)相连两罐之间手动阀门改为远程控制阀门,且在紧急状态下能够自动切换3)液氯输送泵的进口管线设置紧急切断阀引导词偏差原因后果已采取的安全措施建议措施4)安全阀根阀没有打开5)液位变送器的根阀和各计量仪器的信号变送器的根阀关闭6)系统温度偏高7)后续系统盲板未拆除8)出口管线堵塞9)出口阀门关闭或开度不够10)去事故氯排放系统堵塞11)去液氯精制器的液位阀门调节阀坏12)与废氯槽连接的压力调节器故障13)液氯受槽的液位调节阀坏14)泵出口未安装止逆阀4)液化器发生爆炸5)氯大量泄漏,造成人员中毒和环境污染6)引起流量升高7)法兰、阀门密封性能下降8)泵的能力下降4)加强巡检5)设置了液位高、低报警及联锁停车6)设置了压力高、低联锁报警及联锁停车7)现场安装了有毒气体报警仪探头8)严格执行盲板管理规定9)控制系统设置了冗余系统,并定期保养10)安全阀定期检验,并建立台账17)制定了应急操作程序,并定期演习4)罐体液位计改用雷达式液位计5)增设固定碱液喷施,使得喷淋面积覆盖整个槽6)事故氯吸收系统扩容,增加1台事故氯气吸塔7)按照规范增设有毒气体报警仪数量,信号引至中央控制室;同时,设置现场视频监控,实施24h连续监控8)加强培训,严格执行操作规程和安全技术规程9)现有厂房门窗关闭不严,改为塑钢门窗工0)完善应急操作程序,增加演练次数和效果11)定期进行设备强检12)严格限制液氯日常贮存月巨LESS(减量)液位偏低1)液氯进口阀关闭2)进口管线堵塞3)进口阀门盲板未拆4)液化器相连管线断裂5)液位变送器指示错误6)液氯输送泵1无流量或憋压7)去包装的液氯管线泄漏8)设备或管线保温腐蚀,穿孔泄漏1)后续系统流量不足2)前系统压力波动3)操作困难4)氯泄漏,造成人员伤害、环境污染1)所有阀门处于受控状态2)严格}}4}1T育板管理规定3)设置了液位低低报联锁停车报警系统4)对液位控制阀定期检验保养5)控制系统设置了冗余系统,并定期保养6)可以把液氯转送到另外的贮槽,用两个贮槽的液面指示的减增来判断失常的液面计7)随时检查液位上升情况8)调节阀失常时,转换到备用系统9)与液氯精制器压力控制联锁1)选择符合材质要求的阀门2)所有阀门设有打开的标志,并有书面确认程序3)按照规范增设有毒气体报警仪数量,信号引至中央控制室4)加强现场巡检5)增设固定碱液喷淋设施,使得喷淋面积覆盖整个贮槽6事故氯吸收系统扩容,增加1台事故氯气吸收塔7)加强培训,严格执行操作规程和安全技术规程8)现有厂房门窗关闭不严,改为塑钢门窗OTHERTHAN(异常)液氯泄漏至空气中1)管道破裂或穿孔2)法兰连接处密封不良3)阀门密封不良1).人员中毒,环境污染2)系统压力降低1)设置了有毒气体报警系统2)设置了液位高、低报警联锁系统3)设置压力高、低报警联锁系统1)加强巡检,发现故障及时处理2)定期进行反事故演习3)及时查找隐患4)增加事故氯吸收单元的能力从以上对液氯贮罐的液位进行HAZOP分析可以看出,存在的主要偏差有液氯贮罐液位偏高、偏低或无液位以及液氯泄漏等,为了控制偏差的发生,企业制定了一系列的措施,有些措施是原设计就有的,有些是后来技术改造增加的安全措施,如液位报警、流量报警、紧急切断阀、并联安全阀、备用电源、充氮气保护、设置有毒气体报警仪、按照要求定期进行三氯化氮排放等,对事故的发生起到一定阻止和减缓作用,基本上能满足安全生产需要,但尚存部分事故隐患;从企业HSE管理角度考虑,并考虑到液氯大量泄漏后的灾难性后果,已有的措施不能很好地满足现有装置的应急处理要求,如液氯贮罐破裂,大量液氯泄漏,仅用现有的事故氯单元进行处理远远不够,因此,需要增加一些安全控制措施。
3安全措施与建议a)增加有毒气体报警仪数量。
按GB50493-2009《石油化工可燃气体和有毒气体检测报警设计规范》关于有毒气体检测点与释放源的距离不宜大于2}n的要求,还应增加9台有毒气体报警仪。
b)液氯贮罐罐体之间连接阀、事故风机的进出口阀要实行远程控制。
c)增设液氯贮罐的紧急喷淋设施主要包括碱液贮罐、输送泵、废液收集池、废液输送泵以及相应的管线、阀门。
应保证喷淋面积覆盖整个贮槽。
d)液氯罐体液位计改用雷达式液位计,提高装置本质安全化水平。
e)在液氯输送泵的回流线上设置远程控制阀门。
f)增加三氯化氮的排污次数,并加强管理。
排污物中的三氯化氮含量要小于60g/L,大于80g/L时,要增加排污次数或连续排污,并加强监测。
大于100g/L时,要采取停止加料等紧急措施并查找原因。
g)对事故氯气吸收系统进行改造,增大事故氯吸收能力。
主要内容包括:①事故氯气处理工艺由一段吸收改为两段吸收;②事故氯气吸收塔由正压操作改为微负压操作;③在氯气干燥和压缩系统主流程上设置部分手阀和仪表控制阀,以控制氯气泄漏;④将原有风机移至厂房外。
h)加强日常安全管理,开展经常性的隐患排查、整改活动;认真做好装置开停车、检维修等作业活动前的危害识别和风险评价工作;实行未遂事件报告制度等。
4结语通过对液氯贮槽液位进行的HAZOP分析可以看出,主要存在的问题有液氯贮罐缺少紧急事故状态下的碱喷淋系统,液氯贮罐的液位计读数偏差较大,液氯输送泵进口管线没有安装紧急切断阀,有毒气体报警仪的数量不足,事故氯单元吸收能力不足。
因此,应落实相应的对策措施,以提高氯碱生产系统的安全可靠性。
云博创意设计MzYunBo Creative Design Co., Ltd.。