压铸件质量控制
压铸车间质量管理方案

压铸车间质量管理方案压铸车间是生产压铸件的重要场所,质量管理在压铸车间中尤为重要。
良好的质量管理方案能够确保产品质量稳定,提高生产效率,降低生产成本,增强企业竞争力。
本文将从流程控制、设备维护、员工培训和质量监控四个方面,探讨如何建立一套有效的压铸车间质量管理方案。
一、流程控制压铸车间的生产流程是影响产品质量的关键因素之一。
为确保产品质量稳定,应建立科学、规范的生产工艺流程,并制定详细的作业指导书。
作业指导书应包括每个工序的具体操作步骤、操作要点、质量要求和质量检验方法等内容,以确保每个工序的操作符合质量要求。
同时,应加强对生产工艺流程和作业指导书的培训,提高员工对流程的理解和执行能力。
二、设备维护设备是保证产品质量的基础。
为确保设备正常运行,应建立完善的设备维护制度。
制定设备维护计划,按照计划进行定期保养、维修和更换备件,确保设备的可靠性和稳定性。
同时,建立设备维护记录,记录设备维护情况和故障处理过程,以便分析设备故障原因,采取相应措施预防故障的发生。
三、员工培训员工是质量管理的重要一环。
为提高员工的职业素质和技术水平,应加强员工培训。
培训内容包括质量意识培养、工艺知识培训、操作技能培训和质量管理知识培训等。
培训形式可以采取内部培训、外部培训和岗位轮换等方式,使员工全面掌握所需的知识和技能,提高工作效率和质量水平。
四、质量监控质量监控是质量管理的核心环节。
建立有效的质量监控体系,可以及时发现和纠正质量问题,确保产品质量符合要求。
质量监控包括原材料检验、过程控制和成品检验等环节。
原材料检验应严格按照标准进行,确保原材料质量稳定可靠;过程控制要加强对关键工序和关键参数的监控,及时调整工艺参数,防止质量问题的发生;成品检验要建立完善的检验方法和标准,对产品进行全面检测,确保产品质量符合要求。
以上是建立一套有效的压铸车间质量管理方案的主要内容。
通过科学的流程控制、设备维护、员工培训和质量监控,能够有效提高产品质量,确保压铸车间的生产效率和竞争力。
压铸件缺陷的产生及控制
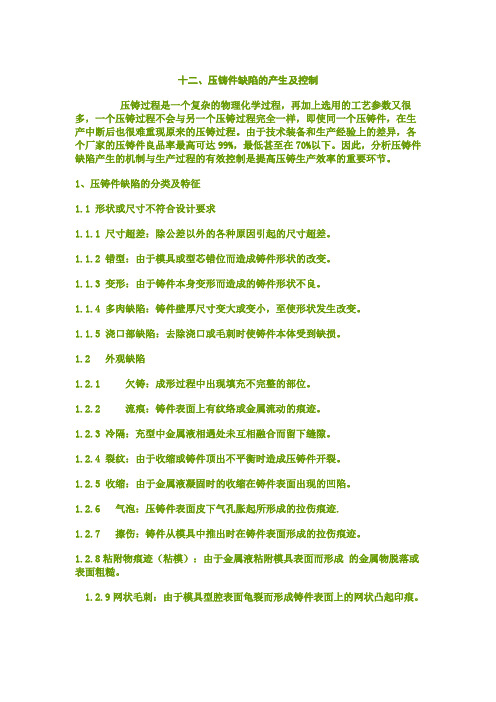
顶杆痕迹过深
1、铸件冷却时间不够
2、部分壁过厚
1、模具需充分冷却
2、延长保压时间和冷却时间,待充分凝固后再推出
3、改变铸件形状使壁厚均匀或者改变推杆位置
由于留有残屑造成铸件缺肉
1、模具清理不干净
2、镶块或滑块配合不好
3、表面状况较差
1、把模具表面和滑块处的残渣的残渣清除彻底后再压铸
1.2.7擦伤:铸件从模具中推出时在铸件表面形成的拉伤痕迹。
1.2.8粘附物痕迹(粘模):由于金属液粘附模具表面而形成的金属物脱落或表面粗糙。
1.2.9网状毛刺:由于模具型腔表面龟裂而形成铸件表面上的网状凸起印痕。
1.2.10模具侵蚀印痕:由于模具被侵蚀造成的网状凸起或多肉(尤其在浇口附近)。
1.2.11针孔:在铸件表面形成的小孔。
8、去除模具表面的热裂纹
9、去掉粘在模具表面的碎屑
粘附物痕迹(粘模)
1、模具和浇口设计及铸件结构不合理
2、模具维修不良
1、增加内浇口厚度
2、修理浇口的位置和方向
3、加强粘模部位的冷却
4、选择合适的脱模剂,充分喷涂
5、调整铁含量
6、调整压射速度
7、改变铸件结构以使充型良好
8、经常去除粘附在型腔表面的碎屑
5、调整模具的温度、铸件的形状、压射速度和金属液流动状态以使热中心处于厚壁的中心
6、改进浇口使流态更佳
7、改变工艺使流态更佳
气泡
1、压铸工艺不合理,尤其是模温过高
2、铸件结构不合理
3、铸件表面存在气体
1、降低模具表面温度
2、调整凝固时间
3、改进模具设计以便获得好的流态,特别是保证足够大的溢渣包和排气道
压铸件产品技术规范标准

压铸件产品技术规范标准1. 引言压铸件是一种具有高精度、高强度和高复杂性的金属铸件,广泛应用于汽车、电子、航空航天等行业。
为了确保压铸件产品质量的稳定和一致性,制定了一系列的技术规范标准,以规范压铸件的生产和质量控制过程。
本文将介绍压铸件产品技术规范标准的主要内容,包括材料要求、尺寸和形状公差、表面处理、硬度要求、力学性能要求等方面。
2. 材料要求压铸件的材料选择对产品的质量和性能具有重要影响。
根据不同的应用领域和要求,压铸件常用的材料包括铝合金、锌合金、镁合金等。
2.1 铝合金铝合金是最常用的压铸件材料之一,具有良好的流动性、加工性能和机械性能。
常用的铝合金包括ADC12、A380等,其化学成分和物理性能应符合相应的标准。
2.2 锌合金锌合金是另一种常用的压铸件材料,具有良好的液态流动性和冷却收缩性能。
常用的锌合金有Zamak 3、Zamak 5等,其化学成分和物理性能应符合相应的标准。
2.3 镁合金镁合金具有重量轻、比强度高等特点,适用于要求重量轻、高强度的产品。
常用的镁合金有AZ91D、AM60B等,其化学成分和物理性能应符合相应的标准。
3. 尺寸和形状公差为了保证压铸件的尺寸精度和形状一致性,对其尺寸和形状设定了公差要求。
公差的选择应根据产品的具体要求和应用领域来确定。
4. 表面处理压铸件在生产过程中常常需要进行表面处理,以提高其耐腐蚀性、耐磨性和装饰性。
常见的表面处理方法包括喷漆、电镀、阳极氧化等。
5. 硬度要求压铸件的硬度是其材料和工艺的重要指标之一,对产品的强度、耐磨性、耐腐蚀性等性能有直接影响。
硬度测试应按照相应的标准进行,测试结果应符合规定的要求。
6. 力学性能要求压铸件的力学性能包括抗拉强度、屈服强度、延伸率等指标。
根据产品的具体要求和应用领域,制定了相应的力学性能要求。
力学性能测试应按照相应的标准进行,测试结果应符合规定的要求。
7. 检验和质量控制为了确保压铸件产品的质量稳定和一致性,需要进行严格的检验和质量控制。
铝合金压铸件控制计划

铝合金压铸件控制计划1.引言2.原材料采购选择优质的铝合金原料对于保证产品质量至关重要。
首先,要选择有良好信誉的供应商,并与之建立长期合作关系。
其次,要对进货的铝合金原料进行全面的物理与化学性能检测,确保其符合产品要求。
最后,在采购过程中,要严格控制原材料的质量、规格和数量,防止出现偷工减料等问题。
3.生产工艺控制3.1铝液的准备铝液是压铸件的原材料,其温度、成分和纯度直接影响产品的质量。
在铝液的准备过程中,应确保炉温达到设定温度,并在加工过程中定期检测铝液的成分和纯度,以及温度的稳定性。
3.2模具的设计与制作模具是铸造过程中的关键因素之一,其设计和制作需要经验丰富且具有高精度的技术人员。
在模具设计和制作过程中,要根据产品的要求和工艺要求,选择合适的材料和加工工艺。
同时,在模具加工过程中,要进行严格的检测和测量,确保模具的精度和质量。
3.3压铸过程控制压铸是铝合金压铸件的成型过程,在压铸过程中,要严格控制铝液的温度、压力和铸造时间。
同时,还要监控压铸机的工作状态,确保其正常运行。
3.4后处理在铝合金压铸件的后处理过程中,包括去除余脱模剂、清洗、修整和热处理等环节。
这些环节需要严格按照工艺要求进行操作,并进行必要的质量检测和测量,以确保产品的精度和质量。
4.设备检测设备的检测是压铸件质量控制的重要环节。
首先,要定期对压铸机进行维护和保养,确保其正常运行。
其次,在每一批产品生产之前,要对压铸机进行调试和校验,确保其精度和稳定性。
同时,还要对成品进行抽样检测和测量,对不合格品进行追踪和整改。
5.质量管理体系为了提高铝合金压铸件的质量,应建立完善的质量管理体系。
首先,要制定详细的工作操作规范和质量检测标准,确保每个环节的工作都按照规定进行。
其次,要建立质量跟踪和评价机制,对每一批产品进行质量检测和评估,及时发现问题并采取措施进行改进。
6.结论。
压铸件常见缺陷及改善对策(1)

压铸件常见缺陷及改善对策(1)压铸件常见缺陷及改善对策压铸件是汽车、电器、机械等行业生产的重要部件,具有成本低、成型形状复杂、尺寸精度高等优点,但在生产过程中,常出现一些缺陷,影响产品的质量和性能。
本文将介绍压铸件常见缺陷及改善对策。
一、缺陷分类(一)表面缺陷1.气孔:表面或内部存在大小不一的圆形或椭圆形小孔。
2.夹渣:表面或内部存在小颗粒或纤维杂质。
3.闪亮:表面出现暗角或光亮,且材料表面的形状失真。
(二)内部缺陷1.开裂:铸件内部存在一定大小、方向和数量的开裂,导致铸件强度下降。
2.气孔:铸件内部存在大小不一、分布不均匀的空隙,导致铸件强度下降。
3.缩松:铸件灌注过程中未完全充实、冷却时出现局部收缩,导致铸件强度下降。
二、改善对策(一)工厂加工环境1.密闭铸造室:确保铸造工艺的真空、氩气气氛、风机循环扇等工作环境的洁净度和稳定性。
2.温度控制:在铸件铸造、冷却、急冷和退火等多个环节,控制温度变化。
3.砂芯制作环境和温度:砂芯质量直接影响铸件内部缺陷情况,制作时要确保环境稳定、温度协调。
(二)工艺改善1.铸造压力:适当增加铸造压力可降低铸造缺陷的比例。
2.浇注速度:适当调整铸造流速,避免在铸造过程中产生气泡。
3.铸造温度:根据铸造材料的特性,调整铸造温度。
4.铸模制作:铸模是决定铸件质量的关键,铸模制作过程需加强工艺控制和质量监管。
结论压铸件是一种重要的制造工艺,其质量直接影响到产品的性能和寿命。
本文简要介绍了压铸件常见缺陷分类及改善对策,提供一定的参考与借鉴。
工厂要加强工艺改进,在生产过程中增加检测措施,提高生产过程中的整体质量控制水平。
压铸铝合金控制计划
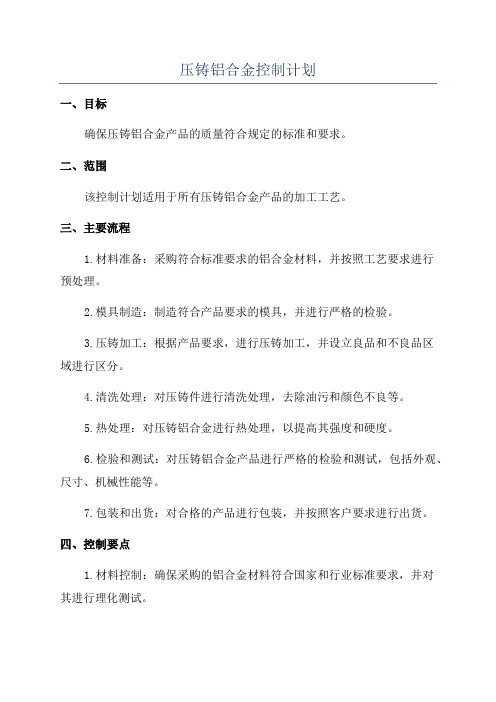
压铸铝合金控制计划一、目标确保压铸铝合金产品的质量符合规定的标准和要求。
二、范围该控制计划适用于所有压铸铝合金产品的加工工艺。
三、主要流程1.材料准备:采购符合标准要求的铝合金材料,并按照工艺要求进行预处理。
2.模具制造:制造符合产品要求的模具,并进行严格的检验。
3.压铸加工:根据产品要求,进行压铸加工,并设立良品和不良品区域进行区分。
4.清洗处理:对压铸件进行清洗处理,去除油污和颜色不良等。
5.热处理:对压铸铝合金进行热处理,以提高其强度和硬度。
6.检验和测试:对压铸铝合金产品进行严格的检验和测试,包括外观、尺寸、机械性能等。
7.包装和出货:对合格的产品进行包装,并按照客户要求进行出货。
四、控制要点1.材料控制:确保采购的铝合金材料符合国家和行业标准要求,并对其进行理化测试。
2.模具控制:制造模具时,确保其尺寸和质量符合产品要求,并进行定期维护和检修。
3.工艺控制:对压铸加工过程中的参数进行控制,包括压力、温度、时间等,以确保产品质量的稳定性。
4.清洗控制:确保清洗过程中使用的清洗剂符合要求,并对清洗效果进行定期检验。
5.热处理控制:根据产品要求,对压铸铝合金进行热处理,确保其物理性能满足要求。
6.检验控制:严格按照检验标准对产品进行检验,确保不合格产品不流入市场。
7.包装控制:对合格产品进行包装,确保其在运输过程中不受到损坏。
五、质量控制方法1.抽样检验:根据国家和行业标准,制定抽样检验方案,并定期进行抽样检验。
2.巡检:对压铸加工过程中的关键环节进行巡检,及时发现问题并进行纠正。
3.符合性评估:对每个工序的合格率进行统计,并及时分析不合格品的原因,采取措施进行改进。
4.培训:对操作人员进行培训,确保他们对工艺要求、产品质量标准等有清晰的认识。
六、责任及权限1.生产部门负责生产过程的具体实施,包括材料准备、加工、清洗、热处理等。
2.质量部门负责制定和执行控制计划,对产品质量进行监督和管理。
3.技术部门负责对工艺进行优化和改进,并对相关参数进行监控和调整。
压铸不良原因与措施

压铸不良原因与措施压铸是一种常见的金属加工方法,用于制造各种各样的金属零件。
然而,在压铸过程中常常会出现一些不良情况,导致产品质量下降或无法使用。
以下是一些常见的压铸不良原因及相应的措施。
1.缩孔(针眼)原因:高温熔融金属凝固时,金属液缩小所形成的孔洞。
措施:-控制材料的熔点和凝固温度,避免温度过高。
-提高注入压力和速度,确保金属充实完全。
-控制铸造工艺参数,如浇注温度、压力和速度,减少气体夹杂物。
2.气孔原因:熔融金属中混入空气或水分,冷凝成孔洞。
措施:-净化材料,确保金属液没有杂质。
-增加浇注温度,减少金属和气体冷凝。
-提高注入速度,使气体远离金属液。
3.热裂纹原因:金属在凝固过程中,由于残余应力、金属浓缩和组织缺陷等原因引起的开裂。
措施:-优化铸造工艺,减少或消除金属残余应力。
-控制金属的凝固速度,避免快速凝固造成应力集中。
-添加合适的合金元素,改善金属组织结构。
4.狭长缺陷原因:熔融金属填充模腔的过程中,金属液流动不均匀,形成局部过渡缩小的缺陷。
措施:-设计合理的铸造模具,确保金属液能够均匀填充模腔。
-调整铸造工艺参数,如入口和出口位置、浇注温度和速度,改善金属液流动状态。
-使用合适的流道和浇口设计,使金属流动更加均匀。
5.长气孔原因:金属液注入模腔的过程中,气体无法顺利排出,形成长而突出的孔。
措施:-增大出口尺寸,提高气体排出的通道。
-调整浇注顺序,避免气泡在金属液中积聚。
-使用适当的排气装置,确保顺畅排出气体。
6.表面不良原因:压铸件表面出现裂纹、气孔、疤痕等缺陷。
措施:-增加模具的冷却系统,提高金属液凝固速度。
-优化模具表面处理,减少摩擦和热传导。
-控制铸造工艺参数,如浇注温度和速度,减少金属液与模具的接触时间。
总之,压铸不良的原因和措施是多种多样的,需要根据不同情况采取相应的措施。
通过优化材料、设计模具、调整工艺参数等方法,可以有效地减少压铸不良,提高产品质量。
压铸件检验规范
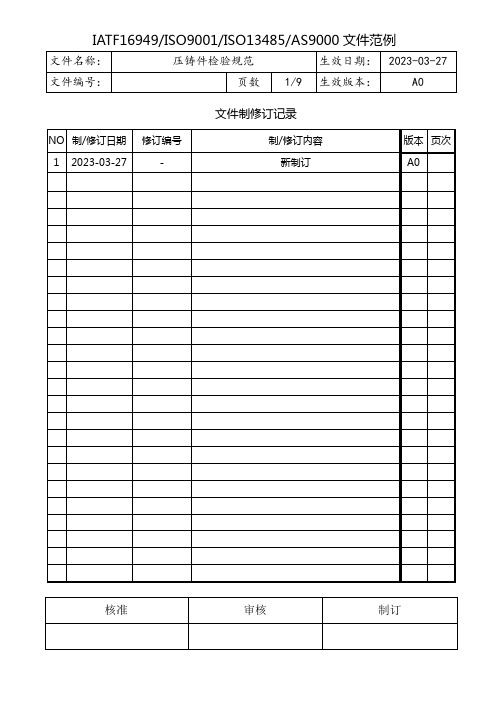
文件制修订记录1、目的:为了对压铸车间生产之产品进行有效地控制,其品质符合国标,行业及客户要求,特制定本规定;2、适用范围:本公司压铸车间均属之;3、职责:品质部负责压铸车间产品首件及巡检,压铸车间负责产品自检互检。
4、不合格品控制:按《不合格控制程序执行》。
原因分析部门:压铸车间,品质部,技术部。
5、引用标准:国家标准,工程图纸;样板;MIL-STD-105E;不良图示。
6、定义:致命缺陷(Critical):单件物料质量特性极严重不符合规定或影响到安全性能时,定义为致命缺陷;严重缺陷(Major):单件物料质量特性严重不符合规定或单件物料重要质量特性不符合规定时,定义为严重缺陷;轻微缺陷(Minor):单件物料质量特性轻微不符合规定或单件物料一般质量特性不符合规定时,定义为轻微缺陷;7、检验内容:一、铸件所需材料及化学成分应符合要求。
二、每批次铸件的机械性能应符合要求。
三、量检具测量铸件尺寸,尺寸公差符合GB/T 6414-1999《铸件尺寸公差与机械加工余量》及工程图纸要求。
四、齿轮类产品,必要时跳动测试仪检测跳动度,符合工程图纸要求。
(双齿轮类产品可分别测试大小齿轮跳动度)五、表面粗糙度可按GB/T 6060.1-1997《表面粗糙度比较样块铸造表面》评级。
六、外观质量:(不良图片见附件)1. 铸件上不允许有冷隔、裂纹、穿透性缺陷及严重的残缺类缺陷(浇不到、未浇满、机械损伤等)的存在.2. 在金属型铸件的非加工表面上,允许铸件有分型、顶杆及排气塞等痕迹。
但凸出表面不大于0.3mm或凹下表面不超过0.4mm,且布局合理协调。
3. 非加工表面的浇冒口,应清理到与铸件表面齐平;待加工表面的浇冒口残留量应不大于3 mm。
4. 铸件上作为基准用的部位应平整,不允许存在任何凸起痕迹,装饰面上不允许有推杆痕迹。
5. 非加工表面上,不允许有麻面和有色斑点。
6. 铸件待加工表面上,允许有经加工可去掉的任何缺陷。
铝合金压铸件的重力铸造工艺控制
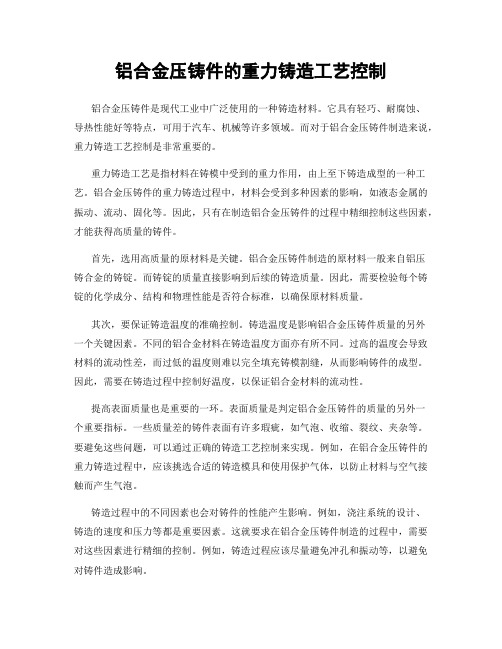
铝合金压铸件的重力铸造工艺控制铝合金压铸件是现代工业中广泛使用的一种铸造材料。
它具有轻巧、耐腐蚀、导热性能好等特点,可用于汽车、机械等许多领域。
而对于铝合金压铸件制造来说,重力铸造工艺控制是非常重要的。
重力铸造工艺是指材料在铸模中受到的重力作用,由上至下铸造成型的一种工艺。
铝合金压铸件的重力铸造过程中,材料会受到多种因素的影响,如液态金属的振动、流动、固化等。
因此,只有在制造铝合金压铸件的过程中精细控制这些因素,才能获得高质量的铸件。
首先,选用高质量的原材料是关键。
铝合金压铸件制造的原材料一般来自铝压铸合金的铸锭。
而铸锭的质量直接影响到后续的铸造质量。
因此,需要检验每个铸锭的化学成分、结构和物理性能是否符合标准,以确保原材料质量。
其次,要保证铸造温度的准确控制。
铸造温度是影响铝合金压铸件质量的另外一个关键因素。
不同的铝合金材料在铸造温度方面亦有所不同。
过高的温度会导致材料的流动性差,而过低的温度则难以完全填充铸模割缝,从而影响铸件的成型。
因此,需要在铸造过程中控制好温度,以保证铝合金材料的流动性。
提高表面质量也是重要的一环。
表面质量是判定铝合金压铸件的质量的另外一个重要指标。
一些质量差的铸件表面有许多瑕疵,如气泡、收缩、裂纹、夹杂等。
要避免这些问题,可以通过正确的铸造工艺控制来实现。
例如,在铝合金压铸件的重力铸造过程中,应该挑选合适的铸造模具和使用保护气体,以防止材料与空气接触而产生气泡。
铸造过程中的不同因素也会对铸件的性能产生影响。
例如,浇注系统的设计、铸造的速度和压力等都是重要因素。
这就要求在铝合金压铸件制造的过程中,需要对这些因素进行精细的控制。
例如,铸造过程应该尽量避免冲孔和振动等,以避免对铸件造成影响。
最后,需要做好质量控制和检验工作。
铝合金压铸件制造完成后,需要进行精密的检验工作。
这个过程包括化学成分分析、金相分析、比重测量和硬度测量等等。
这些检验流程能够有效地验证铝合金压铸件制造过程中的质量控制措施的效果,发现质量问题并及时进行修复。
影响压铸件质量的主要因素及控制方法
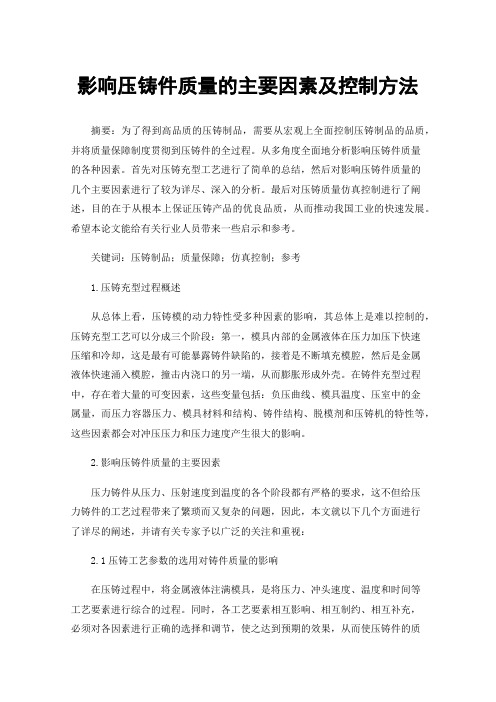
影响压铸件质量的主要因素及控制方法摘要:为了得到高品质的压铸制品,需要从宏观上全面控制压铸制品的品质,并将质量保障制度贯彻到压铸件的全过程。
从多角度全面地分析影响压铸件质量的各种因素。
首先对压铸充型工艺进行了简单的总结,然后对影响压铸件质量的几个主要因素进行了较为详尽、深入的分析。
最后对压铸质量仿真控制进行了阐述,目的在于从根本上保证压铸产品的优良品质,从而推动我国工业的快速发展。
希望本论文能给有关行业人员带来一些启示和参考。
关键词:压铸制品;质量保障;仿真控制;参考1.压铸充型过程概述从总体上看,压铸模的动力特性受多种因素的影响,其总体上是难以控制的,压铸充型工艺可以分成三个阶段:第一,模具内部的金属液体在压力加压下快速压缩和冷却,这是最有可能暴露铸件缺陷的,接着是不断填充模腔,然后是金属液体快速涌入模腔,撞击内浇口的另一端,从而膨胀形成外壳。
在铸件充型过程中,存在着大量的可变因素,这些变量包括:负压曲线、模具温度、压室中的金属量,而压力容器压力、模具材料和结构、铸件结构、脱模剂和压铸机的特性等,这些因素都会对冲压压力和压力速度产生很大的影响。
2.影响压铸件质量的主要因素压力铸件从压力、压射速度到温度的各个阶段都有严格的要求,这不但给压力铸件的工艺过程带来了繁琐而又复杂的问题,因此,本文就以下几个方面进行了详尽的阐述,并请有关专家予以广泛的关注和重视:2.1压铸工艺参数的选用对铸件质量的影响在压铸过程中,将金属液体注满模具,是将压力、冲头速度、温度和时间等工艺要素进行综合的过程。
同时,各工艺要素相互影响、相互制约、相互补充,必须对各因素进行正确的选择和调节,使之达到预期的效果,从而使压铸件的质量得到改善。
本文着重论述了压力和模具温度对铸造工艺的影响。
在铸造过程中,压力是保证铸件组织致密、外形清楚的关键。
在压铸工艺中,压射压力可分为两类:压射力和压射比压。
在压铸机的压射机构中,压射力是一种压力作用于压射活塞的力量。
压铸件常见缺陷及改善对策-V1

压铸件常见缺陷及改善对策-V1
压铸件是一种常见的工业制品,由于生产过程中可能存在各种因素,会导致压铸件出现各种缺陷,影响产品性能和质量。
本文将介绍一些常见的压铸件缺陷及改善对策。
一、表面缺陷
常见的表面缺陷包括气孔、氧化皮、气泡等。
主要原因是压铸件未能完全充填模具或模具表面质量不好,而且模具温度、金属液温度等可能有偏差。
改善对策包括提高模具温度,保证金属液温度稳定,采用优质钢材制造模具,以及增加压力和时间等措施。
二、尺寸偏差
尺寸偏差是指制品与设计要求值之间存在的误差,会影响零部件的配合、装配和使用。
主要原因是模具和设备的磨损,温度控制不精确,以及金属液流动不均匀等。
改善对策包括定期维护模具,保证设备工作正常,加强温度控制,优化金属液流动情况,以及采用精密仪器检测尺寸等。
三、瘤等内部缺陷
瘤是一种内部缺陷,通常出现在薄壁部分或不易充填的区域。
瘤的产生与模具的设计、金属液的配比、铸造工艺等因素有关。
改善对策包括优化模具设计、调整金属液比例,控制铸造工艺参数以及加强质量检测等。
四、内部卷边
压铸件内部卷边是指制品的边缘有一定程度的拱形或曲度,通常出现
在加强部位或边缘区域。
主要原因是模具设计不合理,金属液充填不
充分或充填不均匀等。
改善对策包括优化模具结构,充分充填金属液,增加压力和时间等。
综上所述,良好的压铸件质量得到保障需要生产各环节掌控的精细化、全面化。
压铸件企业应高度重视成品缺陷的发现与分析,全面推进生
产设备、工艺、材料的控制管理,确保完美制品的生产。
压铸质量控制与检验标准

1.压铸生产的质量控制1.压铸生产的质量控制1.1环境铸造生产中涉及的主要工作场地、空间和厂房凡影响铸件质量的主要因素均属环境控制范围。
不同工艺方法或不同铸件材料之间凡不能交叉生产的工作场地应分开或隔离。
如压力铸造和熔模铸造、砂型铸造、有色金属和黑色金属、铝合金和镁合金、真空和非真空熔化浇铸之间的工作场地等。
铸造厂房和工作场地的温度,一般不低于10℃。
新设计的铸造厂房应符合TJ16的TJ36规定。
工作间或厂房内的光照度应不低于75LX。
工作间或厂房内的噪声应符合GBJ87规定.熔化和浇铸场地,地面不允许有积水。
厂房应保持良好的通风,有污染的操作区,应按有关规定进行处理。
压铸生产中释放的有害物质见表9—1其有害物质的毒理特性及极聚允许浓度见表9—2。
1.2设备、仪表和工装铸造过程中直接影响铸件质量的主要设备、仪表和工装应进行质量控制。
应控设备、仪表和工装的目录由技术部门会同使用部门提出,并规定检定项目和周期.其使用、维护、保养和管理的质量控制,工厂应规定通用量具、衡器具的使用管理控制,工厂应有计量管理规范。
设备、仪表和工装应有检定合格证,合格证应注明检定日期、有效期和责任者。
不合格者应停用或作待修等标记.生产现场不准使用未经检定合格或超过检定有效周期的器具、设备、仪表和工装。
精密、关键和贵重的仪表、设备和模具,应建立使用登记和履历本。
铸造机械设备每年应进行一次技术指标检查,技术指标应不低于工艺要求。
熔炼浇注设备每年应进行一次技术指标检查,如设备的熔化功率和熔化速度。
铸造用加热炉的类别应符合有关标准规定。
铸件热处理加热炉,按铸件材料相应的热处理技术标准规定控制。
用于重要的测温与控温的仪表最好配有温度显示自动记录装置。
安全自动报警装置。
复验报告应存档备查,材料发往生产车间时,应附有质量证明及复验报告。
使用单位对主要材应分类存放,妥善保管,防止混批混料、锈蚀和污染。
浇冒口和废铸件等回炉料应及时处理,分类存放,放置标志,严防混料。
1.压铸产品质量缺陷分析及解决对策

第5页,共65页。
3 气孔类缺陷 气孔类缺陷是压铸件最常见的一类缺陷,在薄壁件上主要表现为
表面气泡和不可见的微孔,当对压铸件进行抛光、涂镀时,会引起涂 镀层起泡;在厚壁件上主要表现为深部气孔,严重时会有疏松、缩孔 现象存在。产生气孔类缺陷的原因很多,其中最主要的是充型时的 排气不畅和裹气。控制和预防这类缺陷时,主要是要保证压铸模 排气系统合理、畅通,消除或减少充填型腔时多股合金液流的相 互撞击。
MA离壳表面拉伤
第11页,共65页。
拉伤: 沿开模方向铸件表面呈现条状的拉伤痕迹,有一定深度,严重时为一面状伤痕。 另一种是金属液与模具产生焊合、粘附而拉伤(粘铝拉伤),以致铸件表面多肉或缺肉。
产生的原因: 1、 型腔表面有损伤、凹坑 2、 出模方向斜度太小或倒斜 3、 顶出时偏斜 4、 浇注温度过高或过低,模温过高导致合金液产生粘附 5、 脱模剂使用效果不好,喷涂不好 6、 铝合金成分含铁量低于0.6% 7、 冷却时间过长或过短
第24页,共65页。
TU5JP4进排气浇口直冲型芯有被冲凹陷的立即进行更换以减少变形
第25页,共65页。
上模时压铸机上的4根推杆一定要长度一样,公差 在0.5mm内,以保证顶出平稳
第26页,共65页。
开模后静模弹簧推杆没有出来,说明已经卡死不起作用了,需修模
第27页,共65页。
DUG:977机框下抽芯
离壳3#孔外形上有裂纹
第19页,共65页。
裂纹:
1. 铸件表面有呈直线状或波浪形的纹路,狭小而长,在外力作用下有发展趋势 2. 冷裂-开裂处金属没有被氧化 3. 热裂-开裂处金属已经被氧化
压铸铝合金制件的质量控制

1 压铸 铝合金制件原材料的质量控制
为保证压铸件质量, 提高一次压铸合格率 , 在
收稿 日期 :0 5—1 8 20 1—2
料头 、 边皮、 切屑、 品的 回炉 利用也是供 给 废
的原料之一 , 对该 回炉料 , 应严格归类 、 清理 , 去除
作者简介 : 赵爱萍 (91 ) 女 。 16 一 , 云南昆明人 , 高级工程师 , 主要从 事机械制造技术方 面的教学与研 究
针状组织存在于合金组织中 , 对压铸件危害最大, 是造成合金流动性差 、 压铸件产生热裂纹、 抗冲击性 和塑性下降的主要原因. 但铁含量过少, 又易产生粘 模、 脱模困难. 因此, 铁含量应控制在 06 一 .%. .% 12
铜可提 高合 金 的流动性 、 压铸件 的强度和硬 度. 但含量超过 0 8 .%时 , 铸件热裂倾 向增加 , 且塑
表 1 各种缺 陷在压铸废 品中所 占的E 率 匕
缺陷形式 气孔 裂纹 缩孔 表面疏松 浇铸不足 其他
性下降, 对后续 机加工也不利 , 具磨损较快. 刀 因
此, 铜含量应 ≤O 6 . %.
锰能使合金中铁的片状和针状组织变为细密
的晶体形状 , 减少铁 的有 害影 响 , 含量在 04 以 .% 下时还可增加铸件 的塑性. 但锰含量过高 , 会引起 偏析. 锰含量应控制在 0 6 . %以下. 锌可提高合金的流动性、 铸件的切削加工性. 同 时铸件的热裂倾向也增加了. 锌含量应≤ Q3 %. 硅是 合金 中的主要组成成 分 , 硅能提 高合 金 高温下的造型性 , 减少收缩 率 , 热裂倾 向. 无 但组 织粗大 , 机加工 效果 差. 含量应 控 制在 1% 一 硅 0
维普资讯
第2卷 6
压铸件品质管理

力学性能达不到规定要求会降低承载能力,影响压铸件的正常使用。尤其对于有保安特性要求 的部件,如果力学性能达不到要求,铸件只能按报废处理。 评价:通过力学性能试验机检验 13、硬质点 铸件上有硬度高于金属基体的细小质点或块状物,加工后常常显示出不同的亮度。 铸件中的硬质点主要给机械加工带来问题,可使刀具磨损严重或损坏,加工过程不稳定,严重 时无法加工。 评价:主要原因是金属液中混入杂质。一般通过机械加工或金相检验。 14、渗漏 铸件达不到密封性要求,发生漏水或漏气现象。 对有特殊要求的压铸件,渗漏影响它的正常使用,如社内的左、右箱体等。 评价:渗漏主要是由于铸件内部组织疏松,存在气孔、缩孔等铸造缺陷造成的。一般通过压力检 测确认。压检不合格可通过修补解决。
3、无损探伤检验 无损探伤是对压铸件缺陷进行非破坏性检查,主要包括渗透检验、放射性检验(X射线)、电磁检验(磁 粉检验、涡流检验)、声波检验等。目前社内使用较多的是渗透检验,确认产品的缺陷大小。
4、耐压试验 对有耐压要求的压铸件要采用耐压试验来检查压铸件的密闭性。试验方法是将压铸件用夹具夹紧并呈密闭 状态,向其中通入压缩空气,并浸入水中,观察是否有气泡出现。试验的参数根据相应技术条件设定。 耐压试验一般在专门的设备上进行(压检机) 5、耐腐烛试验 常用的有盐雾腐蚀试验。盐雾腐蚀试验方法是将压铸件清理干净称重后,放于盐雾腐蚀试验机中进行腐蚀, 经过一段时间后取出压铸件。将压铸件清洗干净并烘干表面,再次测量压铸件的质量,通过腐蚀前后压 铸件的质量变化判定铸件的腐蚀程度。
镁合金压铸生产过程中的质量控制

镁合金压铸生产过程中的质量控制摘要:在我国的资源储备中,具有丰富的镁储备,有关统计表明,我国的镁储备量约占据世界储备总量的 1/3。
同其他的合金相比较,镁合金的强度更高、密度较小,加上其具备良好的散热性,得到了广泛的应用。
但在镁合金压铸件的实际生产中,往往会因复杂的生产工艺造成镁合金性能差强人意,因此,需要对镁合金压铸生产进行有效控制,保障镁合金压铸件的生产质量。
总而言之,若想推动合金压铸行业发展,必须要强化生产过程中的质量控制。
本文主要在镁合金锭的融化准备以及镁合金压铸生产中的有效控制进行分析,希望能够推动镁合金压铸行业的进一步发展。
关键词:镁合金压铸;融化;质量控制1融化准备1.1入库复检镁合金锭自身条件是保证镁合金压铸件质量的基本,压铸企业在对镁合金锭进行采购之前,应该对供应商提供的镁合金锭进行少量试用,检查其镁合金锭的成分、力学性能等条件,在保证镁合金锭完全符合生产要求的前提下,在签订合同批量进货。
如果需要的货物供应量大,压铸企业选择了两个或者以上的供应商,就要做好详细的记录,将各个供应商的镁合金锭分开存储。
1.2融化前的分级处理首先,融化镁合金锭之前,需要对回料炉进行有效清理,主要清理炉中的油污、沙子等杂质,对于成分不合格的铸件,禁止回炉处理。
在处理完毕后,将回炉料放到明确指定区域,随即做好标记;其次,针对报废铸件的回收处理工作,在进入回料炉之前,也要对报废件进行清理,去除其铸件表面的杂质;最后要对飞边、切屑等废料进行有效处理,要注意废料不可回炉。
1.3融化前工具和防护措施的准备首先,在镁合金锭融化前,所使用的工具中不能含有桐、硅、镍等金属元素,更不能使用有锈蚀的操作工具,只有这样才能够保证压铸质量。
其次要做好相应的防护措施,在融化镁合金锭之前,在融化炉以及保温炉旁设置好干燥黄砂箱,同时对于灭火器的配备类型也要进行有效选择,不能选择含水灭火器以及与含与镁液发生化学反应元素的灭火器。
2镁合金压铸生产过程中的质量控制2.1注意化学元素的影响和作用在镁合金压铸生产过程中,应注意合金元素的影响。
影响压铸件质量的主要工艺参数

影响压铸件质量的主要工艺参数影响压铸件质量的主要工艺参数包括:1. 压铸工艺温度:压铸件在铸造过程中需要加热熔化金属材料,温度是影响铸件质量的重要因素。
如果温度过高,会导致熔融金属过热,容易产生气孔、缩松等缺陷;如果温度过低,会使铸件成型不完全,表面质量差,容易出现可见缺陷。
2. 压铸压力:压铸压力直接影响到铸件的密度和凝固过程。
过高的压力会使得铸件的细小部分压缩不够,导致铸件中出现气孔、缩松等缺陷;过低的压力则会造成铸件形状不完美,容易产生气孔、翘曲等问题。
3. 注射速度:注射速度是指金属材料进入模具中的速度。
过快的注射速度会导致金属材料冲击力大,易引起气门过冲、表面润色不均等问题;过慢的注射速度则会导致凝固时间过长,容易产生热裂、夹杂等缺陷。
4. 冷却时间:冷却时间是指铸件在模具中冷却至一定温度的时间。
冷却时间过短会导致铸件内部温度分布不均,容易产生热裂、夹杂等缺陷;冷却时间过长则会使生产率降低,成本增加。
5. 模具温度:模具温度直接影响到铸件的凝固速度和整体质量。
模具温度过高会导致金属熔化过快,铸件表面质量较差;模具温度过低则会导致凝固时间延长,生产效率低下。
6. 浇注系统设计:浇注系统包括喷嘴、导槽、浇注口等部分,直接影响到金属材料进入模具的流动性和冷却性能。
如果浇注系统设计不合理,易产生气孔、错流、夹杂等缺陷。
总之,以上主要工艺参数都会对压铸件的质量产生重要影响。
为了获得高质量的压铸件,需要在生产过程中合理控制这些参数,并确保每个参数都处于最佳范围内。
影响压铸件质量的主要工艺参数是压铸生产中非常重要的一环。
通过合理控制这些参数,可以有效地提高压铸件的质量,确保其达到设计要求。
首先,压铸工艺温度是影响压铸件质量的关键参数之一。
合适的温度可以保证金属材料完全熔化,使金属液体顺利流入模具中,并在合适的速度冷却凝固,从而获得高密度、无缺陷的铸件。
如果温度过高,会使金属液体过热,容易产生气孔、缩松等缺陷;相反,如果温度过低,会导致铸件成型不完全,表面质量差,容易出现可见缺陷。
- 1、下载文档前请自行甄别文档内容的完整性,平台不提供额外的编辑、内容补充、找答案等附加服务。
- 2、"仅部分预览"的文档,不可在线预览部分如存在完整性等问题,可反馈申请退款(可完整预览的文档不适用该条件!)。
- 3、如文档侵犯您的权益,请联系客服反馈,我们会尽快为您处理(人工客服工作时间:9:00-18:30)。
压铸件质量控制压铸作为一种特殊铸造方法,与其他铸造方法相比,其基本的特征是将液态金属以高速高压对模具进行填充充型,但是,由于压铸方法固有的充型造成的喷射以及金属模具快速冷却和高的生产效率对模具的损害,使压铸件不可避免的产生很多缺陷,一些缺陷是与压铸方法与之俱来的,一些则是可以避免的,一些缺陷不会影响压铸件的性能,所以不会造成铸件废品,而另外一些缺陷则可能会影响铸件的性能而成为废品。
质量是企业的生命线,是提高企业竞争能力的重要支柱,是提高企业经济效益的重要条件,因此,提高压铸件质量,无论对于压铸企业的经济利益,还是减少资源浪费的社会效益,都是非常有利的。
压铸件质量包括外观质量、内在质量和使用质量,外观质量是指铸件表面的粗糙度、表面质量、尺寸公差、形位公差和质量偏差等;内在质量是指铸件的化学成分、物理和力学性能、金相组织以及在铸件内部存在的孔洞、夹杂物和裂纹等;使用质量是指铸件能满足各种使用要求和工作性能,如耐磨性、耐蚀性、和切削性、焊接性等。
产生压铸件缺陷的直接原因可以归纳为以下几个方面1)压铸件结构设计不合理2)模具和压铸方案不正确3)材料及熔炼不正确4)压铸机以及压铸工艺条件不正确5)压铸操作不适当(手动操作)除此之外由于管理方面的原因,如生产组织、现场管理质量管理等不够完善,操作者玩忽职守、不负责任也是产生压铸缺陷的间接原因。
一.压铸件结构设计压铸件结构设计是压铸工作的第一步,设计的合理性和工艺适应性将会影响到后续工作的顺利进行,如模具结构及制造难易、铸件精度保证、缺陷的种类等,都会以压铸件本身的工艺性的优劣为前提。
为了从根本上防止压铸件的质量缺陷,并以低成本高效率的持续生产出高质量铸件,必须是压铸件的结构适合于压铸工艺。
压铸件的结构设计就是使铸件的机构、形状在满足其工艺要求的前提下尽量符合压铸工艺、压铸模具的各种要求。
压铸件结构的工艺性:1.尽量消除铸件内部侧凹,使模具结构简单2.尽量使铸件壁厚均匀,可利用肋减少壁厚,避免铸件产生气孔、缩孔、变形等缺陷3.尽量消除铸件上的深孔、深腔。
因为细小型芯易弯曲、折断。
深腔处充填和排气不良4.设计的铸件要便于脱模、抽芯二.模具设计和压铸方案对压铸件的质量影响1.浇注系统设计的好坏直接影响到金属液的充填状态、压铸件成型、表面质量和内部质量金属液在压铸过程中的充型状态是由压力、速度、时间、温度、气体等因素综合作用形成,因而浇注系统与压力传递、合金流速、填充时间、凝固时间、模具温度、排气条件有着密切关系。
压力传递一方面要保证内浇口处金属液以高压、告诉充填型腔,另一方面又要保证在流道和内浇口截面的金属液不先凝固,以保证传递的最终增压压力。
这就需要最佳的流道和内浇口设计,最小的压力损失。
内浇口面积过大和过小都会影响填充过程,当压射条件一定时,过大的内浇口使充填速度低,金属液早凝固,甚至充填不足,过小的内浇口又会使喷射加剧,增加热量损失,产生漩涡并卷入过多气体,模具易损。
设计原则:使金属液能有效地、平稳的流动充填型腔,避免气体混入2.分型面的选择影响压铸件的外形及模具加工的难易1)对同心度要求高的外形或内孔,应尽可能设在同一个半型内,否则在模具制造时不易保证精度,而在使用时因导柱导套的磨损,而误差逐渐增大,容易造成铸件废品;对与分型面平行的高度尺寸,在精度要求较高时也应设在同一个型腔内。
2)分型面应当考虑减少金属液对滑块抽芯机构的压力,因为滑块受力过大,容易影响尺寸精度和造成意外事故3)分型面应当考虑到开模后的出模距离,在动、定模内,应当尽量避免过深的型腔,这样不但有利于金属填充,有利于排气及上涂料,同时也可不使模具过厚过重4)分型面应当考虑到铸件的美观和容易去飞边,分型面应当尽可能避免在平面内的中间,更应当避免无法抛光的分型方法。
5)分型面应当尽量简化模具结构的复杂性,使模具制造方便,对各种不同的曲折分型面的零件,分型面尽可能取在同一个平面内6)分型面上的压力应当小于合模力,在铸件投影面积较大,而在分型面上的投影面积大于额定面积时,就应设法选择低于合模力的铸件投影面积为分型面7)分型面及内浇口的位置和方向应当尽量使液流进入型腔通顺,没有撞击,不会产生漩涡,否则会造成成型不好8)有活动侧抽芯,应尽可能放在动模内,有螺纹型芯也尽可能放在动模内,因为这样可以保证铸件随动模移动3.冷却系统的布置影响模具温度的控制,从而影响铸件的充填、凝固状态;能使模具温度均衡,铸件凝固时冷却速度一致,减少铸件中的气孔和缩孔;模温调节,凝固时间缩短,提高生产效率;模温能正确控制,有利于稳定铸件之尺寸精度和机械性能;热量扩散正常,减少模具应力,延长模具寿命注意事项:1)同一模具尽量采用较少的冷却水道和水嘴的规格,以免增加设计和制造的复杂性2)冷却水道的直径一般为6~14mm。
采用数条直径小的水道冷却效果要比采用一条大直径的水道好3)注意水道之间的距离和水道与型腔之间的距离4)采用隔板式水道时,应在隔板螺栓上作出隔板位置标记,以便在安装时保持其正确位置。
5)注意水道与模具其他结构之间的距离4.模具加工的精度影响铸件表面的粗糙度及尺寸精度5.溢流槽、排气槽设计的位置、大小直接影响铸件外观质量和是否产生气体缺陷;开设位置:1)金属液最先流到的地方;2)在突出位型芯的背面;3)多股液流汇合之处;4)由于铸件形状出现涡流的地方;5)金属液最后流道的部位;6)浇口两侧充型不到的死角位置;7)大平面上易产生收缩的区域;8)一般铸件温度较低的区域;9)料位厚而易产生收缩的区域;10)难于排气的部位;11)做顶出平台用;12)需引流而不使分型面过早封闭的部位。
6.顶杆布置影响压铸件能否顺利脱模剂不产生变形三.材料及熔炼压铸合金的化学成分、熔炼控制直接影响压铸间的质量,对于硬点、气孔、机械性能产生直接的影响,因为合金液中的成分含有杂质,既影响机械性能,切削性能及其后的热处理性能,又大大影响到铸造性、铸造表面、硬点等。
还因为氧化物,非金属杂质物关系到硬点的产生,气体关系到气孔,耐压性等,不严格控制就会出现问题。
有关材料及熔炼操作问题归纳一下共有1.回炉材料管理问题在熔炼车间应设置回收料分类存放的料场,并有清晰的标记,还应规定往料场集聚回收料的方法2.回炉料和合金锭的配比问题新料与回炉料搭配时,回炉料不超过35%,合理控制投料量、投料时间、料块大小。
3.铝锭熔化保温问题熔炼温度控制在670°~760°范围内。
过高温度会发生氧化或吸氢,过低温度不易分离炉渣,利用熔剂对铝液进行精炼、除气、除渣,熔炼过程中保持液面平衡,精炼温度要求达到720±20°,合理控制出料温度、时间、减少保温时间。
4.装入和倒出合金液的问题出料斗要保持干燥、干净并要经常在料斗内壁涂刷保护涂料,对每一斗的铝料进行清理,扒出氧化物及不熔物。
四.压铸机以及压铸工艺条件压铸机是压铸生产的核心,压铸机性能的优劣以及对模具、压铸工艺的适应范围对压铸件质量保证有决定性影响,压铸生产中压铸工艺参数的设定和调节直接影响产品的质量。
主要参数设定:1.射料时间:射料时间大小与铸件壁厚成正比,对于铸件质量比较大,压射速度比较慢且所需时间较长时,射料时间可适当加大。
2.开模时间:较厚的压铸件比薄的压铸件的开模时间要长,结构复杂的的模具比结构简单的模具开模时间要长,调节开始时可以略长一点时间,然后再缩短。
3.顶出延时时间:在保证产品充分凝固成型切不粘模的前提下,尽量减短顶出延时时间。
4.顶回延时时间:在保证能顺利取出铸件的前提下尽量减短顶回延时时间5.储能时间:在设定时操作机器作自动循环运动,观察储能时间结束时,压力是否能够达到设定值,在能达到设定压力值得前提下尽量缩短储能时间6.顶针次数:根据模具要求来设定顶针次数7.压力参数设定:在保证机器能正常工作,铸件产品质量能合乎要求的前提下,尽量减小压力。
8.压射速度的设定:压射速度分为慢压射速度、快压射速度、增压运动速度。
慢压射速度通常在0.1~0.8m/s范围内选择,快压射速度与内浇口速度成正比,一般从低向高调节,在不影响铸件质量的前提下,以较低的快压射速度为宜;增压运动所占时间极短,它的目的是压实金属,是铸件组织致密;一般观察射料压力表的压力示值在增压运动中成一斜线均匀上升,压铸产品无疏松就可。
9.慢速、快速转换位置设置:慢速、快速运动转换应该在压射冲头通过压室浇注口后进行,对于薄壁小铸件,一般慢速较短、快速较长;对于厚壁大铸件,一般慢速较长,快速较短,同时应根据铸件的质量调节转换位置。
10.铝合金液温度设定:根据压铸合金不同结构的产品,其壁厚铸件比薄壁铸件浇注温度要低,一般温度保持在620°~660°11.模温的控制:一般以合金凝固温度的1/2为限,在压铸生产过程中最重要的就是模具工作温度的稳定和平衡,它是影响压铸件制件和压铸效率的重要因素之一。
五.压铸操作(手工操作)这里主要指手动喷涂及吹干,合理的喷涂操作是保证铸件质量、压铸模具寿命、生产效率的一个重要因素,涂料的作用:使液态金属充填流畅,有利于成型,防止粘模,使铸件获得光亮、光滑、平整的表面质量;保护模具,避免高温液态金属对模具表面的冲刷,减低模具的导热率和模温,延长模具寿命;开模时,有利于铸件顺利脱出;减少对冲头、顶杆、活动部位的摩擦和磨损;喷涂时应注意1.喷涂动作迅速、喷涂均匀,喷射距离为100~200mm2.喷涂部位不能有水分存在,如有水分制品产生气孔冷隔缺陷3.热点部位应重点喷涂,喷涂少容易粘模,产生裂纹4.用脱模剂喷枪从上到下迅速吹干脱模剂。
六.车间管理1.根据工种、技术水平进行岗位优化组合、合格上岗,严格遵守劳动纪律和操作规程;2.对压铸机、模具、工具必须保证完好、齐全,做好日常保养;3.材料保证供应,保质、保量,铸件堆放有序,,防止碰伤、划伤、4.品种、数量一般以生产计划要求按时生产,同时要考虑生产连续性5.质量控制就是要对重点工艺加强质量管理,工序的质量控制要严格遵守工艺纪律和操作规程6.在车间内部营造一个安全、文明、舒适、美好的工作环境7.生产过程中的质量控制:1)建立质量管理体系、明确质量管理目标2)严格执行工艺记录,搞好均衡生产和文明生产3)做好原材料、压铸件的技术检查工作4)建立质量信息系统,做好产品质量记录、统计、分析和反馈5)实行工序质量控制,特别是关键、重点工序的质量控制6)加强不合格品的管理7)严格执行设备保养制度,正确使用设备、模具,保证生产质量■。