品质改善活动的改善案例
品质精益改善案例

品质精益改善案例
嘿,朋友们!今天我要给你们讲讲一个超棒的品质精益改善案例!
咱就说有这么一家汽车制造工厂,之前那生产线上时不时就出点小毛病。
比如呀,有个工人老张总是抱怨:“哎呀,这零件安装起来咋这么费劲呢!”这可不行啊,生产效率上不去,质量也让人揪心。
(这里通过老张的抱怨体现出之前的问题)
于是呢,工厂的管理团队就决定搞一次大变革。
他们把大家召集起来,说:“咱得想办法改进啊,不然这可咋整!”(通过这句话展现管理团队的决心和对现状的思考)大家都积极响应。
他们从每个细节入手,就像给病人做全面检查一样。
比如说,调整了生产流程,让各个环节衔接得更顺畅,不再像之前那样磕磕绊绊。
这就好比是给一条路修得更平坦宽敞,车子开起来那叫一个爽!(用修路来类比流程调整带来的顺畅)
然后呢,还加强了对零件的质量检测。
每个零件都得过好几道关,力求做到完美无瑕。
这就跟挑选精兵强将一样,得是最棒的才能上战场!(用挑选精兵强将来隐喻对零件质量的严格把控)
经过一段时间的努力,哇塞,效果那叫一个明显!生产线上的问题大大减少,产量提高了,质量也蹭蹭往上涨。
工人们都高兴坏了,老张也不再抱怨啦,反而笑着说:“嘿,现在干起活来可带劲了!”
你们说,这品质精益改善是不是太厉害啦?这就是一个活生生的例子,告诉我们只要用心去做,没有什么是不能改变的!品质精益改善,真的能带来巨大的好处,咱都得重视起来,好好去实践啊!。
iqc品质改善提案案例大全

iqc品质改善提案案例大全品质改善是企业持续发展的关键所在。
IQC(Incoming Quality Control)即进料质量控制,是产品质量管理中的一项重要环节。
以下是一些IQC品质改善提案案例,以供参考。
1.提高供应商的质量管理水平:提案目标:提高进料质量,减少不合格品数量。
方案:与供应商建立战略合作伙伴关系,共同建立质量管理体系,包括质量标准制定、制程控制、质量培训等。
同时对供应商进行定期评估,及时反馈问题并共同解决。
2.引入自动化检测设备:提案目标:提高检测效率,降低人工误差。
方案:引入自动化检测设备,例如光学比对仪、三坐标测量仪等。
通过自动化检测设备可以实现高精度的测量和比对,提高了检测效率,并降低了人工误差。
3.加强原材料供应商的审核:提案目标:确保原材料质量符合要求。
方案:将审核流程纳入到原材料供应商的合同中,定期对原材料供应商进行现场审核,验证其质量管理体系的有效性。
执掌纠正措施,确保原材料质量符合要求。
4.实施良品率追踪:提案目标:减少不良品数量,提高产品质量。
方案:建立良品率追踪系统,实时监测产品的良品率,并对低良品率的产品进行分析。
找出问题的原因,并采取相应措施进行改善,以提高产品质量。
5.提高员工质量意识:提案目标:通过培训和激励,提高员工对质量的重视程度。
方案:开展质量培训,包括产品知识、工艺流程、质量标准等,提高员工的专业技能和质量意识。
同时设立质量奖励机制,鼓励员工积极参与质量改善活动。
6.建立质量跟踪系统:提案目标:及时发现并解决质量问题。
方案:建立质量跟踪系统,实时记录和跟踪产品质量问题的发生和处理过程。
通过对质量问题的跟踪和分析,及时发现潜在问题,并采取相应措施解决,以避免质量问题对产品质量的影响。
7.推行供应商自检:提案目标:减少供应商对企业的不良品投诉。
方案:要求供应商自行开展自检工作,并提供自检报告。
同时对供应商进行监督和指导,确保其自检工作的有效性。
精益现场改善案例

精益现场改善案例
精益现场改善是一种基于精益生产理念的改善方法,旨在通过减小浪费、提高生产效率和品质,从而提高企业的竞争力。
下面是一个关于如何精益现场改善的案例:
某汽车零部件制造公司的生产线在生产过程中出现了很多浪费,如零部件运输过程中长时间的等待、物料的过度处理、无价值的运动等。
这些问题导致了生产效率低下、品质不稳定和成本增加。
为了解决这些问题,该公司采取了精益现场改善的方法。
首先,该公司进行了价值流分析,明确了产品从原材料到最终成品的生产流程,并找出了其中的浪费。
他们发现,运输、等待和处理环节占据了大部分的时间和资源,因此决定从这些环节入手进行改善。
接下来,他们采用了一系列的精益工具和方法,如Kanban系统、5S整理、单点设备保养等。
通过Kanban系统,他们建立
了一个可视化的物料运输系统,能够准确地控制物料的数量和运输时间。
通过5S整理,他们将工作区域做了优化,保持了
一定的整洁度和有序性,减少了运动浪费。
通过单点设备保养,他们定期对设备进行保养和维修,减少了因设备故障而停工的时间。
改善后,该公司的生产线的效率得到了明显提高,产品的品质也得到了保证。
运输时间和等待时间明显减少,减少了人员的
浪费和资源的浪费。
整个改善过程中,该公司注重对员工的培训和参与,使他们对改善目标和方法有了更好的理解并积极参与其中。
通过精益现场改善,该公司成功地解决了生产线上存在的问题,提高了生产效率和产品品质,降低了成本,提升了企业的竞争力。
品质改善活动的改善案例

现状分析—年度数据
不良个数最高为:
1.颜色异常1044个 多工序检查,品管抽检,无法全数管控 2.标签错误599个 多工序检查,品管可管控 3.产品混装245个 多工序检查,品管抽检,无法全数管控
不良件数最高为:
1.颜色不良5件 多工序检查,品管抽检,无法全数管控 2.寸法不良5件 成形组立工程检查,品管无法管控 3.产品混装4件 多工序检查,品管抽检,无法全数管控 4.连接不良4件 多工序检查,品管抽检,无法管控 5.操作不良4件 多工序检查,品管抽检,无法管控
9
102
1 12
1
0
0
GA-1标G签A-错2产误G品C-混1G异装C-品3组组装装G位CG-异C6-连常8组接装不部良G位D-欠1外品G观D-破2G外损DG-观D3-有变4打瑕形磨疵G或打D-颜痕5表色面不处良G理DG-不D8-外良9其观他缩外水G观E-异1操常G作E-不2性良G能E-不4异良G音E-不7回良转G不F-良1G未F-加2尺工GG寸FF--不94加形良工状时异G其常Z-他9其不他良不良项
不良数 不良比率
500
112233445050505050500000000000
56.1% 386 43.3%
2 0.2%
1 0.1%
1 0.1%
60.0% 50.0% 40.0% 30.0% 20.0% 1 10.0% 0.1% 0.0%
标签与实物不符 外观不良 露底不良 寸法不良 组装不良 性能不良
分析现状—异常分析图
09年度纳入不良明细
不良个数 不良件数
1200
9
1000
10448
不良发生时个数较多
8
7
800
不
良
品质改善活动的改善案例ppt课件

1
选定主题—选择
异常原因分析和对策中必备项:
1.生产不良 制造原因只有在产品生产时发生及对策
2.流出不良 流出原因在制造过程和检查过程都会 产生。并如在出货检查时防止异常流出, 可达成客户要求的标签与实物不符不良 不良件数“0”目标
2
选定主题—定案
减少客户投诉中多数量不良,达成客户 PPM目标。 理由是: *客户每年都有相关联络,要求各供应商 减少标签与实物不符的异常。 *品管检查作业方法中可以对应。
件
10月份纳入不良个数明细
不良数 不良比率
500
112233445050505050500000000000
56.1% 386 43.3%
2 0.2%
1 0.1%
1 0.1%
60.0% 50.0% 40.0% 30.0% 20.0% 1 10.0% 0.1% 0.0%
标签与实物不符 外观不良 露底不良 寸法不良 组装不良 性能不良
作业台
人
培训不足 标准不了解
未按照作业标 准实施
线上配料异常
料
工作时间太 长,疲惫
人员工作时精 神不集中
个人原因
流
出
不
良
原
因
分
析
来料错误
来料错误时,受入检查 和工程中的生产前确认 可发现,需提前预防。
8
喔哦~
原因分析—分析结论说明
NO
不良项目
原因
对策
人
1.培训后向受训人确认培
为 因
训内容是否理解;
6
设定目标
来来来,一 起来改善!
出货检查流程及方法: 1.制造完成品检查
(全数检查)
品质改善分段控制案例

品质改善分段控制案例家电公司是一家专注于生产和销售电视机的企业,由于市场竞争激烈,品牌知名度较低,公司决定通过提升产品质量来赢得市场份额。
他们采取了品质改善分段控制的方法来逐步提高产品的品质和服务水平。
首先,公司对产品进行了全面的品质分析。
他们从产品设计、制造过程、原材料、配件等多个方面进行了详细的调研和分析,找出了当前产品存在的问题和不足之处。
通过品质分析,公司确定了需要改进和提高的关键指标,例如产品的分辨率、色彩还原度、屏幕亮度等。
接下来,公司制定了一套具体的品质改善控制计划。
他们根据产品分析结果,将品质改善目标分阶段确定。
在第一阶段,公司将集中精力改善产品外观和基本功能,以提高用户的第一印象。
在第二阶段,公司将着重改善产品的核心技术和性能,以提高产品的品质竞争力。
在第三阶段,公司将关注产品的细节和用户体验,以打造高品质的产品和服务。
在实施过程中,公司采取了一系列措施来控制品质改善的进程。
首先,他们加强了对供应商的管理和合作,选择优质的原材料和配件供应商,以确保产品的材料质量。
其次,公司加强了对生产过程的监控,采用先进的生产设备和技术,建立了一套严格的品质控制流程,确保产品的加工和制造过程符合标准。
此外,公司还加强了对产品的检测和测试,建立了一套完善的品质检测体系,确保产品的功能和性能符合预期。
最后,公司注重了对用户反馈和投诉的收集和分析,通过不断改善产品和服务,逐步提高用户满意度。
经过一段时间的努力,公司逐步实现了品质改善,并取得了显著的效果。
首先,产品的外观和基本功能得到了大幅改善,用户对产品的第一印象有了明显的提升,销量和市场份额逐步增加。
其次,产品的核心技术和性能也得到了大幅提升,产品在市场上与竞争对手的差距逐步缩小,用户满意度和品牌知名度不断提高。
最后,产品的细节和用户体验也得到了改善,用户反馈和投诉数量明显减少,公司形象得到了进一步塑造。
综上所述,品质改善分段控制是一种有效的管理方法,可以帮助企业逐步提高产品和服务的品质水平。
品质改善QCC活动成果报告案例

伍、现状调查三
(一)改善前数据收集,5~6月份TR-377绒布不良数统计 如下表:
收 集 人:张金枝
收集日期: 09.5~09.6
数据来源: 品质异常退料单 物品报废申请单
日期 项目 不良数
5/1~5/20 5/21~6/106/11~6/30 合计 10.3 2.4 7.6 20.3 18.7 4.8 10.1 33.6 64.2 93.2 27.2 34.4 13.5 31.2 104.9 158.8 3842.5米
D C A P
叁、主题选定(二)
降低MN/ZP绒布不良率
选题理由:
1.解决品管工作中实际困扰; 2.减少生产线抱怨,以利生产; 3.3~5月绒布进料不良数比率大; 4.提升品管事务效率.
伍、现状调查一
1.活动主题作业流程
货车运输
进料检验
入库
发料裁片
生产
发料至生产线
缴库
裁片
TR-377绒布表 面柔软、光滑 无花纹
(一)活动目标:TR-378绒布由18247PPMB降至100PPM,
TR-377绒布由41327PPM降至100PPM.
六、目标设定
不 良 率 P P M
1.达成公司04年进 料不良率100PPM↓
41,327
30,000 20,000 10,000
TR-378绒布 TR-377绒布
41,327
4,328 1,254 TR-377 TR-378 100 目标
拾、对策实施 五-Ⅱ
问题点:7月底确认绒布线痕仍然存在, 我们检讨后后实施二次对策.
皱折
对策实施:在卷筒纸上贴附一层牛皮纸, 责任人:刘财强 实施日期:09.8.16
品格提升项目优秀案例

品格提升项目优秀案例精益生产二期项目品质提升组选取订单稳定,客户端质量表现不佳及厂内废品率较高的SHTY01/02/09及HYWK03进行专题改善,从“降低客户端PPM”、“降低产品废品率”、“提高产品直通率”、“难题解决”四个方面进行品质提升。
改善小组由相应产品项目组成员组合而成,充分拉动项目资源进行产品质量提升,避免了改善小组与项目组的工作重复。
在难题攻关时充分拉动各部门资深工程师以及工程中心同事共同商讨,寻求问题解决的最佳方法。
团队的成功源于大家的共同努力。
小组每周定期举行周例会,回顾过去一周所开展的工作,并且讨论下一步的工作计划,让每个人都能清醒的认识到小组的现状以及团队的目标,不断为之努力。
各小组按照“月月有主题,周周有活动”的活动方针,每周举行相应的质量提升活动,让改善意识深入人心,让品质提升落实到现场。
团队的成长同时带动了成员能力的提升。
本期改善项目,品质提升小组总共开展了23次审核,涉及18个专题。
共审核出137个问题点。
发现了问题,我们还需要解决问题。
小组按照问题分析八步法总共输出了9份A3报告以及26份点改善报告。
小组成员在发现问题以及解决问题在这过程中不断的提升。
但远不止这些。
现场活动的组织锻炼了组织能力,每周报告的编写锻炼了书面总结能力,大小例会的现场展示提升了演讲口才。
在活动开展过程中,组员的能力在潜移默化的改变着。
精益改善项目的开展,不仅仅是降低废品率,提高了客户满意度。
更让大家对于精益生产思想有了更深刻的了解与认知,让每个人都参与到改善的活动中。
精益生产二期项目的成功源于大家的共同努力,希望在精益生产三期项目中,品质提升组将再接再厉,做出更好的成绩。
iqc品质改善提案案例大全

iqc品质改善提案案例大全随着市场竞争日益激烈,企业的品质改善变得越来越重要。
为了帮助企业提升产品质量和客户满意度,以下是一些IQC品质改善提案案例。
1.设立质量评估小组首先,企业可以设立一个质量评估小组,由专业人员组成,负责监督和评估生产过程中的质量控制。
小组可以定期检查产品,发现问题并提出解决方案。
此外,小组还可以负责收集顾客反馈和投诉,并制定改善计划。
2.实施供应商考核制度很多时候,产品质量的问题源于供应商提供的原材料或零部件。
因此,企业可以实施供应商考核制度,对供应商进行定期考核和评估。
只有具备一定质量保证能力的供应商才能成为合作伙伴。
同时,企业应建立与供应商之间的良好合作关系,共同努力提高产品质量。
3.引入先进的质量检测设备有效的检测设备是保证产品质量的关键。
企业可以投资购买先进的质量检测设备,以提高产品检测的准确性和效率。
这样可以更早地发现产品质量问题,避免不符合客户要求的产品流入市场。
4.培训和教育员工员工是企业的核心资源,对他们进行系统培训和教育是提高产品质量的重要手段。
企业可以组织员工参加质量管理培训,提高他们的质量意识和技能。
此外,企业还可以建立员工奖励制度,激励员工参与质量改进活动。
5.实施全员质量管理质量不仅仅是质检部门的责任,而是每个员工的责任。
企业可以实施全员质量管理,让每个员工都参与到质量控制的过程中。
这不仅可以发现并解决问题,还可以改善企业的工作流程和组织文化。
6.树立品质文化品质是企业的核心竞争力之一,企业应树立品质文化,让品质成为每个员工的重要价值观。
企业可以定期组织品质文化培训和沙龙活动,鼓励员工分享质量改进的经验和故事,从而增强员工的质量意识和认同感。
7.建立和改进质量管理体系企业可以建立质量管理体系,如ISO9001等标准,并不断改进和优化体系。
质量管理体系可以帮助企业规范质量管理流程,减少缺陷和错误,并提高产品质量。
8.加强与客户的沟通与合作与客户的良好沟通和合作是提高产品质量的重要因素。
工厂质量改善案例
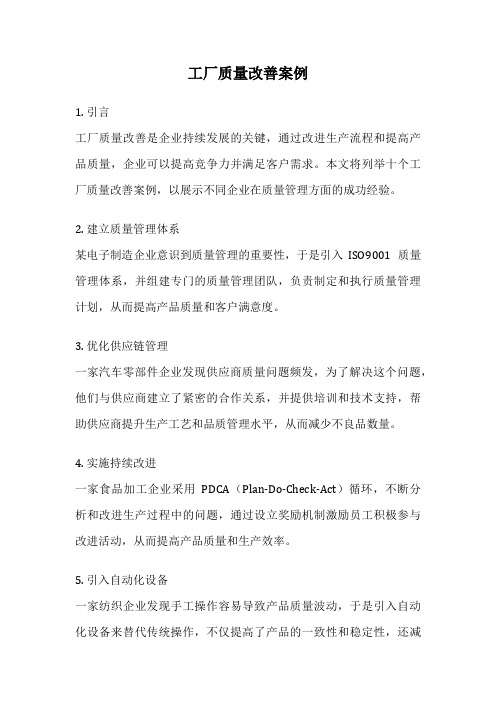
工厂质量改善案例1. 引言工厂质量改善是企业持续发展的关键,通过改进生产流程和提高产品质量,企业可以提高竞争力并满足客户需求。
本文将列举十个工厂质量改善案例,以展示不同企业在质量管理方面的成功经验。
2. 建立质量管理体系某电子制造企业意识到质量管理的重要性,于是引入ISO9001质量管理体系,并组建专门的质量管理团队,负责制定和执行质量管理计划,从而提高产品质量和客户满意度。
3. 优化供应链管理一家汽车零部件企业发现供应商质量问题频发,为了解决这个问题,他们与供应商建立了紧密的合作关系,并提供培训和技术支持,帮助供应商提升生产工艺和品质管理水平,从而减少不良品数量。
4. 实施持续改进一家食品加工企业采用PDCA(Plan-Do-Check-Act)循环,不断分析和改进生产过程中的问题,通过设立奖励机制激励员工积极参与改进活动,从而提高产品质量和生产效率。
5. 引入自动化设备一家纺织企业发现手工操作容易导致产品质量波动,于是引入自动化设备来替代传统操作,不仅提高了产品的一致性和稳定性,还减少了人为错误的发生,提高了生产效率。
6. 加强员工培训一家制药企业意识到员工技能对产品质量的影响,于是投入大量资源培训员工,包括生产技能、质量控制知识等,提高员工的专业水平和责任意识,从而降低产品质量问题的发生率。
7. 制定标准作业程序一家化工企业发现生产操作缺乏标准化,容易导致质量问题,于是制定了标准作业程序,并进行培训和监督,确保员工按照标准操作,从而提高产品质量和生产效率。
8. 引进先进检测设备一家机械制造企业购买了先进的检测设备,能够对产品进行全面的检测和分析,从而及时发现问题并采取措施,提高产品质量和可靠性。
9. 强化质量意识一家家具制造企业通过举办质量月活动、组织质量培训等方式,提高员工对质量的重视程度,鼓励员工自觉参与质量管理活动,从而不断改进产品质量。
10. 客户投诉管理一家家电企业建立了客户投诉管理系统,及时响应客户的反馈并进行分析,从根本上解决问题,提升客户满意度和忠诚度。
QCC小组活动改善案例

D
C
改善前
A
改善后
八、对策实施(四)
现状分析:海汽部分铁件制程不良。如:4T01之锁扣总成不良率高。
对策拟定:确定不良原因为锁扣总成之零件主轮纳入不良,临时处理 委外线切割
对策实施:1、临时对策:对现有不良品进行委外,品保物管做好库存管制。 2、永久对策:开立设变单,与主机厂协调对产品进行更改。 对策处置:依设变后标准生
43 28 17 88
43 27 16 86
50 28 18 96
39 28 18 85
45 22 17 84
35 15 18 68
50 25 18 93
45 24 15 84
45 22 17 84
48 15 8 71
三、现状把握(二)
400 单 位 : 分 300 200 100 0 一汽 金杯 丰田 江森 龙兴 全海 全福 联泓 富士兴
100 80
单 位 : 分
60
40
20
0
长春一汽 沈阳金杯 天津丰田 北京江森 哈尔滨龙兴
哈尔滨龙兴
全兴海南
天津双协
天津夏利
天津丰铁
全兴无锡
全兴福州
福州联泓
富士兴
评核项目
配分 50 30 20 100
长春一汽 沈阳金杯 天津丰田 北京江森
全兴海南 天津双协 天津夏利 天津丰铁 全兴无锡 全兴福州 福州联泓
19 15 16 50
判 定
X
担当
计划 完成日
为 收料人员 何 未点收 客 服务 客诉结果 户 营业未追 满 踪 意 包装箱未 度 做防尘防 差 品质 锈处理
制程不稳 定
可行性 可 尚可 差
生产计划 交期 安排不合 理
品质改善之QCC活动改善案例发表模式

革新小组成员
小组组长
小组组员
发表担当
Hale Waihona Puke 小组号令发表协力2
1.出场
1.1 在上一组发表结束前在指定地方列队准备; 1.2 听到司议”请ⅹⅹ小组出场; 1.3 全组成员快速围成一圈,伸出右手搭在一起,小组
号令同时高呼”品质改善”,全员随后一起高呼” 加油,加油,加油!” 并迅速恢复队列跑步至发表席; 1.4 快至发表席指定地方时,号令”看齐(齐音要拉 长)”,全员左手衬腰,向右看齐;号令”好”(短促 有力),全员左手放下,面向观众呈立正姿势站立; 1.5 号令”注意”,(意音落时)全员左右手臂同时抬 高30CM后再用力拍响大腿----号令”敬礼”,全 员”请多指教”---敬礼.
6
5.发表完毕
5.1 内容发表完后,发表担当”以上,发表完毕!; 全员迅速恢复出场队形;
5.2 司仪”下面是提问时间,请各位提问”; 5.3 如果有人提问,组内熟悉该问题的人要左脚
跨出一步,右脚跟上合并”谢谢您的提问, 这个问题由我来回答……以上”,回答完 毕快速退回原位;
7
6.发表结束
6.1 司仪”还有没有人提问”,稍顿”如果 没有提问,***组发表结束”,号令”注 意”---全员两手同时抬高30CM再用力 拍响大腿---号令”敬礼”,全员”谢谢指 教”---敬礼---号令”向右转”---全员同 时向右转并跑步快速退场.
8
7.敬礼要领
➢ 眼睛始终平视前方 ➢ 下半身/头/双手不动 ➢ 翘屁股 ➢ 上半身向前倾30度
9
8.发表基本功
➢ 士气高 ➢ 速度快 ➢ 动作齐
10
11
4
3.发表
3.1 全员介绍完后,号令”发表开始”,全员快速移 动至对应位置:
品质改善案例
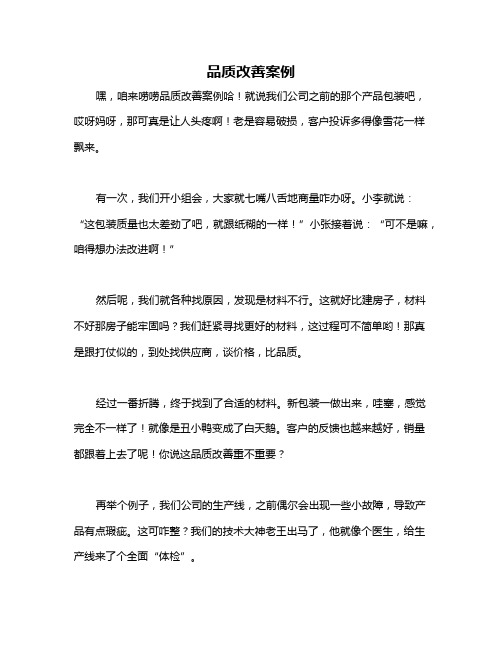
品质改善案例
嘿,咱来唠唠品质改善案例哈!就说我们公司之前的那个产品包装吧,哎呀妈呀,那可真是让人头疼啊!老是容易破损,客户投诉多得像雪花一样飘来。
有一次,我们开小组会,大家就七嘴八舌地商量咋办呀。
小李就说:“这包装质量也太差劲了吧,就跟纸糊的一样!”小张接着说:“可不是嘛,咱得想办法改进啊!”
然后呢,我们就各种找原因,发现是材料不行。
这就好比建房子,材料不好那房子能牢固吗?我们赶紧寻找更好的材料,这过程可不简单哟!那真是跟打仗似的,到处找供应商,谈价格,比品质。
经过一番折腾,终于找到了合适的材料。
新包装一做出来,哇塞,感觉完全不一样了!就像是丑小鸭变成了白天鹅。
客户的反馈也越来越好,销量都跟着上去了呢!你说这品质改善重不重要?
再举个例子,我们公司的生产线,之前偶尔会出现一些小故障,导致产品有点瑕疵。
这可咋整?我们的技术大神老王出马了,他就像个医生,给生产线来了个全面“体检”。
他带着几个徒弟,没日没夜地研究,终于找到了问题所在,然后对症下药。
嘿,你还别说,生产线立马变得稳稳当当的,生产出来的产品那叫一个精致!这不就是像人身体好了,干啥都有力气嘛!
所以说啊,品质改善真的是太重要啦!它就像是给企业注入了活力,让企业能跑得更快、更远!大家一定要重视起来呀,可别不当回事哟!。
iqc品质改善提案案例大全
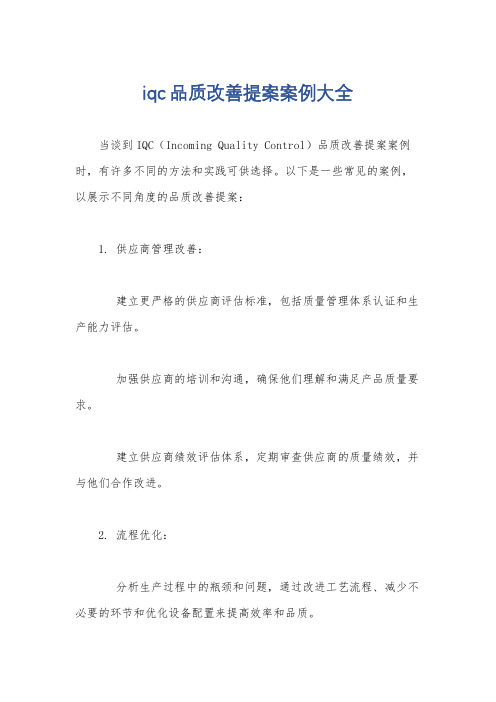
iqc品质改善提案案例大全当谈到IQC(Incoming Quality Control)品质改善提案案例时,有许多不同的方法和实践可供选择。
以下是一些常见的案例,以展示不同角度的品质改善提案:1. 供应商管理改善:建立更严格的供应商评估标准,包括质量管理体系认证和生产能力评估。
加强供应商的培训和沟通,确保他们理解和满足产品质量要求。
建立供应商绩效评估体系,定期审查供应商的质量绩效,并与他们合作改进。
2. 流程优化:分析生产过程中的瓶颈和问题,通过改进工艺流程、减少不必要的环节和优化设备配置来提高效率和品质。
引入自动化技术和设备,减少人为因素对产品质量的影响。
实施持续改进的方法,如六西格玛和精益生产,以减少浪费和缺陷。
3. 质量培训和教育:建立培训计划,提供员工关于质量管理、产品检验和问题解决的培训。
培养员工的质量意识,鼓励他们主动参与质量改进活动,并提供奖励和认可。
建立知识共享平台,促进不同部门之间的沟通和合作,以解决质量问题。
4. 数据分析和统计控制:收集和分析大量的生产数据,以识别潜在的质量问题和趋势。
应用统计方法,如过程能力指数和控制图,监控和控制生产过程的稳定性和一致性。
利用数据分析结果,制定改进措施和预防措施,以提高产品的一致性和稳定性。
5. 客户反馈和投诉管理:建立有效的客户反馈渠道,及时收集和处理客户反馈和投诉。
分析客户反馈和投诉的原因和模式,找出根本原因并采取纠正措施。
与客户进行积极的沟通和合作,解决问题并改进产品质量。
这些案例只是品质改善提案的一小部分,实际上还有许多其他方法和实践可供选择。
每个组织的情况和需求都不同,因此需要根据具体情况制定适合的品质改善提案。
品质改善提案案例大全

品质改善提案案例大全在当今激烈的市场竞争中,品质改善已成为企业发展的关键因素之一。
为了提高产品和服务的质量,许多企业都在不断探索和实践。
下面我们将介绍一些品质改善提案的案例,希望能够为您的企业提供一些借鉴和启发。
首先,我们来看一个关于产品质量改善的案例。
某家电子产品制造企业在生产过程中,发现了产品在高温环境下容易出现故障的问题。
为了解决这一问题,企业决定对生产工艺进行调整,采用更高温度下的测试,以确保产品在极端条件下依然能够正常运行。
经过一段时间的努力,产品质量得到了显著提升,客户投诉率明显下降,市场反响也非常积极。
其次,我们来看一个关于服务质量改善的案例。
某家餐饮企业在市场调研中发现,顾客对其服务态度和效率提出了不少负面评价。
为了改善这一问题,企业决定对员工进行培训,提升他们的服务意识和专业水平。
同时,还引入了一套新的点餐系统,以提高服务效率。
经过一段时间的努力,顾客对餐厅的评价明显提升,客流量也有了明显的增长。
再次,我们来看一个关于流程质量改善的案例。
某家制造企业在生产流程中存在着许多低效率和浪费的问题,导致成本居高不下。
为了改善这一问题,企业引入了精益生产的理念,对生产流程进行了全面优化。
通过价值流分析和精益工具的运用,企业成功地简化了流程,减少了浪费,提高了生产效率,降低了成本。
最后,我们来看一个关于管理质量改善的案例。
某家企业在管理层面存在着决策缓慢、沟通不畅、目标不明确等问题,导致了组织运转效率低下。
为了改善这一问题,企业进行了管理团队的重组和培训,建立了更加科学的绩效考核体系,加强了内部沟通和协作。
经过一段时间的努力,企业的管理质量得到了显著提升,组织运转效率明显提高,整体绩效也有了明显的改善。
以上就是一些品质改善提案的案例,这些案例充分展现了企业在不同领域如何通过改善质量来提升竞争力。
希望这些案例能够给您带来一些启发,也希望您的企业能够在品质改善的道路上不断前行,取得更大的成功。
企业质量改进案例
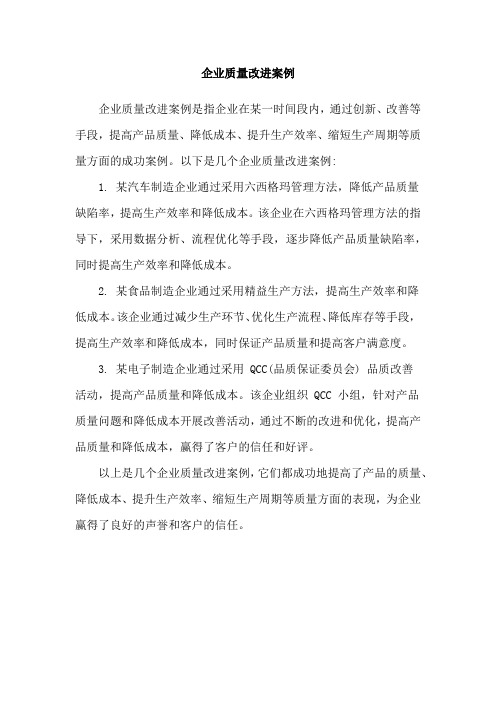
企业质量改进案例
企业质量改进案例是指企业在某一时间段内,通过创新、改善等手段,提高产品质量、降低成本、提升生产效率、缩短生产周期等质量方面的成功案例。
以下是几个企业质量改进案例:
1. 某汽车制造企业通过采用六西格玛管理方法,降低产品质量
缺陷率,提高生产效率和降低成本。
该企业在六西格玛管理方法的指导下,采用数据分析、流程优化等手段,逐步降低产品质量缺陷率,同时提高生产效率和降低成本。
2. 某食品制造企业通过采用精益生产方法,提高生产效率和降
低成本。
该企业通过减少生产环节、优化生产流程、降低库存等手段,提高生产效率和降低成本,同时保证产品质量和提高客户满意度。
3. 某电子制造企业通过采用 QCC(品质保证委员会) 品质改善
活动,提高产品质量和降低成本。
该企业组织 QCC 小组,针对产品
质量问题和降低成本开展改善活动,通过不断的改进和优化,提高产品质量和降低成本,赢得了客户的信任和好评。
以上是几个企业质量改进案例,它们都成功地提高了产品的质量、降低成本、提升生产效率、缩短生产周期等质量方面的表现,为企业赢得了良好的声誉和客户的信任。
生产线制程品质生产效率改善案例

生产线制程品质生产效率改善案例在制造业中,保证生产线制程品质和生产效率的改善是非常重要的。
本文将以公司的生产线制程品质和生产效率改善案例为例,详细介绍该公司在此方面的改进措施和取得的成果。
公司是一家生产汽车零部件的制造企业,其主要产品包括发动机零部件、传动系统零部件等。
由于市场竞争日益激烈,客户对产品的质量和交货时间要求越来越高,因此该公司决定对生产线制程品质和生产效率进行改进。
首先,该公司进行了生产线的现状分析和问题定位。
经过调研和数据分析,发现该生产线存在以下问题:一是制程品质不稳定,产品中出现了一定比例的次品率;二是生产效率较低,生产周期长,无法满足客户的需求。
针对问题一,该公司采取了多项措施来提高制程品质。
首先,引进了先进的质量检测设备,以提高产品的检测精度和准确性。
其次,对员工进行了质量培训,强调质量意识和细节要求,提高员工的质量意识和责任感。
此外,还加强了供应商的质量管理和协作,提前对进货物料进行检验和筛选,减少次品率。
对于问题二,该公司着重优化了生产流程和管理系统,提高生产效率。
在生产流程方面,通过对生产线进行布局调整和工艺优化,减少了生产环节和工序的数量,缩短了生产周期。
在管理系统方面,该公司引入了先进的工业互联网技术,实现了设备的智能化和信息的实时传递。
此外,还采用了生产线平衡和产能规划技术,实现了生产资源的最优配置和生产进度的有效控制。
通过以上改进措施的实施,该公司取得了明显的改善效果。
首先,制程品质得到了显著提升。
产品的次品率明显下降,满足了客户对品质的要求,提高了客户满意度。
其次,生产效率得到了大幅度的提高。
生产周期缩短,大大提高了生产线的产能,减少了生产成本,提高了企业的利润率。
此外,还改善了员工的工作环境和工作质量,提高了员工的工作满意度。
综上所述,通过对生产线制程品质和生产效率的改进,该公司取得了显著的成果。
然而,改进工作并不是一次性任务,而是一个持续改进的过程。
该公司将继续关注生产线的制程品质和生产效率,不断改善和优化,以适应市场和客户的需求,提高企业的竞争力。
质量改善案例模板.ppt

生产科/ 技术品 管科
程兴/何 永华
2011.1.16
Y
追求技术创新,铸造完美品质
质量问题 ,我去解决
请领导批评指正!
追求技术创新,铸造完美品质
Hale Waihona Puke 5改善后此产品胶口位置已改动, 产品质量问题稳定
对比
追求技术创新,铸造完美品质
品质改善专项工作汇报
质量问题 ,我去解决
3、下周改善工作计划:
问题描述 原因分析
改善对策
责任部 门
责任人
计划完成 实际完 状 态 时间 成时间 G/Y/R
备注
J48副仪表 板本体调 试时报废 过多
机床、工艺不 稳定
召集汽车件车间相 关技术人员共同讨 论各工序的控制。
品质改善专项工作汇报
质量问题 ,我去解决
2、改善工作成果展示:
改善1: 改善前:客户多次投诉产品胶口处未修平,导致主机厂焊接有缝隙。 改善后:根据客户样件要求,工程科对模具进行改进,现客户已认可,产品质量处
于稳定状态。 见下图:
改善前
工程科见产品封样件的要 求整改
此位置有5个胶口需要对其胶口改位置
目录
质量问题 ,我去解决
一、品质改善专项工作汇报
1、上周改善专项工作内容 2、改善工作成果展示(最好以数据说话) 3、下周改善工作计划
追求技术创新,铸造完美品质
品质改善专项工作汇报
1、上周改善专项工作内容:
质量问题 ,我去解决
客户多次投诉产品胶口处维修平,导致主 机厂焊接有缝隙
追求技术创新,铸造完美品质
- 1、下载文档前请自行甄别文档内容的完整性,平台不提供额外的编辑、内容补充、找答案等附加服务。
- 2、"仅部分预览"的文档,不可在线预览部分如存在完整性等问题,可反馈申请退款(可完整预览的文档不适用该条件!)。
- 3、如文档侵犯您的权益,请联系客服反馈,我们会尽快为您处理(人工客服工作时间:9:00-18:30)。
总结—课题
不良测试做法需一直持续实施。 下一年度计划导入扫描确认的方式,
采取扫描枪确认番号,纳期等信息。 以求加强保证异常流出
谢谢大家的聆听, 我们会持续改善以 求提高!
感谢下 载
原因分析—鱼骨图分析 怎么办
呢?
另附资料说明
法
检查指示书在正式 使用前会做检查前 培训,如有疑问或 后续有疑问时也可 资料难懂 提出,视情况可追 加项目。
作业指示书说 明不足
作业区域无法调 整,到再增产或 有必要时,开两 班检查
作业区域小,人 员作业位置小
作业环境不够 亮,无法检出
每月进行灯管 确认,750露 克斯以上,可 对应
培训不足
培训后不理解
2.正式作业前对受训人做 作业观察,并确认其检查
素
后的产品(班组长); 3.做不定期的不良测试
原
1.随着客户增产的趋势,生 1.控制加班时间,每天加
因 分 析
产线也随着产量提升,检查 班不超过3小时,每周有一
2
工作时间长,
量也增加;
天休息;
易疲劳
2.因前生产线中少部品项 2.需要前工序等相关部门
结果分析—不良说明 郁闷
革命还未成功,
ing
我们还需努力!
10月份标签与实物不符1件:
原因分析为:检查人员检查遗漏,异常品在出货检查时, 有发现同品番的产品有标签与实物不符,检查员认为已 经选别,应不会有异常的心态下造成流出。(推定)
针对检查人员调查结果:该检查员日常检查时比较认真, 做不良测试时也能检出,并及时将异常提出。(以往) *可参照不良测试实绩统计(唐晚妹)
件
10月份纳入不良个数明细
不良数 不良比率
500
112233445050505050500000000000
56.1% 386 43.3%
2 0.2%
1 0.1%
1 0.1%
60.0% 50.0% 40.0% 30.0% 20.0% 1 10.0% 0.1% 0.0%
标签与实物不符 外观不良 露底不良 寸法不良 组装不良 性能不良
多,导致生产延迟,出货时
协助对应;
间不更改,紧急对应品增多 3 . 做不定期的不良测试
及
日常生活中都有心情 唯有提高检查员的警惕
对 策
3
个人原因,精 烦闷之时,所以无法 神不集中 避免会有开小差的事
性,并了解产品的重要性 后,认真对待检查品
*做不定期的不良测试,
情
提升检查员的警惕性
原因分析– 补充
对策实施
哇唔..改善 ,改善…
对应点:减少多个数不良流出
11..作作成计计划划
2.实施2.实施
措施:做不定期不良测试,提
项目:1.标签与实物不符,
高检查员的警惕性,以防流出不良。
2.左右混入,3.少数
作成:HANDLE 李治平/ KEY-SET 谢江
4.异品混入
对象人员:所有出货检查员
10月份开始
现状分析—年度数据
不良个数最高为:
1.颜色异常1044个(多工序检查,品管抽检,无法全数管控) 2.标签错误599个(多工序检查,品管可管控) 3.产品混装245个(多工序检查,品管抽检,无法全数管控)
不良件数最高为:
1.颜色不良5件(多工序检查,品管抽检,无法全数管控) 2.寸法不良5件(成形组立工程检查,品管无法管控) 3.产品混装4件(多工序检查,品管抽检,无法全数管控) 4.连接不良4件(多工序检查,品管抽检,无法管控) 5.操作不良4件(多工序检查,品管抽检,无法管控)
22 2
2
22
200
2 7 13 2 25 6 18
1 1 4 1 11 5 29 35 11 2
9
102
1 12
1
0
0
GA-1标G签A-错2产误G品C-混1G异装C-品3组组装装G位CG-异C6-连常8组接装不部良G位D-欠1外品G观D-破2G外损DG-观D3-有变4打瑕形磨疵G或打D-颜痕5表色面不处良G理DG-不D8-外良9其观他缩外水G观E-异1操常G作E-不2性良G能E-不4异良G音E-不7回良转G不F-良1G未F-加2尺工GG寸FF--不94加形良工状时异G其常Z-他9其不他良不良项
QCC改善活动资料
选定主题—选择
异常原因分析和对策中必备项:
1.生产不良 制造原因只有在产品生产时发生及对策
2.流出不良 流出原因在制造过程和检查过程都会 产生。并如在出货检查时防止异常流出, 可达成客户要求的标签与实物不符不良 不良件数“0”目标
选定主题—定案
减少客户投诉中多数量不良,达成客户 PPM目标。 理由是:
*经过调查发现,该检查员在异常发生品检查时,因为个 人因素导致确认时未确认到(个人隐私,不记入)。 (实际)
总结—反省
经过短暂的一个月时间测试,不能体现很明显的效 果额,需要长时间的坚持,将检查员的警惕性提高 才能达到客户所设定的“标签与实物不符异常件数 为0”的目标。
经过这次测试,也让检查人员了解到作业有疏忽时, 异常随时有可能流出给客户,对客户造成不必要的 麻烦,严重时会导致客户停线危机。
期间:10月~
PD
44..实实施施结结果果
AC
3.确认
测试结果:HANDLE有24人,
10月份标 签与实物 不良再发1
件
不合格有2人
KEY-SET有5人,
未达成
不合格为0
2010年HDL能力调查总结.xls
2010年受入检查与KEY-SET出货检查能力
对策实施—图表
郁闷 ing
10月份标 签与实物 不良再发1
设定目标
来来来,一 起来改善!
出货检查流程及方法: 1.制造完成品检查
(全数检查)
☆本次对应改善的工程 为出货检查区域,检 查人员的警惕性提升, 标签与实物不符为0
挑中你 了~~
2.品管出货检查 (初期流动品和海外向的全 检, 其他的抽检)
3.制造出库后入生管仓库 (入库品不可再开箱和换标签)
4.按照日期出货
检查方法说明:
1.待检区推部品,同时需要确认整车产品品番、纳期一致 2.推到检查区后确认检查用的资料与待检品,须一致 3.检查时按照《检查作业手顺书》检查,盖章(异常时联络班组长确认处理) 4.检查完成后再次确认整车产品品番、纳期一致 5.确认完成后推到检查完成品放置区
*检查方法没有问题,如按照检查基准实施可防止异常流出
*客户每年都有相关联络,要求各供应 商减少标签与实物不符的异常。
*品管检查作业方法中可以对应。
分析现状—异常分析图
09年度纳入不良明细
不良个数 不良件数
1200
9
1000
10448
不良发生时个数较多
8
7
800
不
良
599
个 600
4
4
数
5 4
6 不
5
5良
4件 数
400 3
3
3
3
245 2
22 2 2
作业台
人
培训不足 标准不了解
未按照作业标 准实施
线上ห้องสมุดไป่ตู้料异常
料
工作时间太 长,疲惫
人员工作时精 神不集中
个人原因
流
出
不
良
原
因
分
析
来料错误
来料错误时,受入检查 和工程中的生产前确认 可发现,需提前预防。
喔哦~
原因分析—分析结论说明
NO
不良项目
原因
对策
人
1.培训后向受训人确认培
为 因
训内容是否理解;
1
分析图中异常项目说明
不良项目依次为:
GA-1标签错误,GA-2产品混装, GC-1异品组装,GC-3组装位异常, GC-6连接不良, GC-8组装部位欠品, GD-1外观破损, GD-2外观变形, GD-3有瑕疵打痕, GD-4打磨或颜色不良,GD-5表面处理不良, GD-8外观缩水,
GD-9其他外观异常, GE-1操作不良, GE-2性能不良, GE-4异音不良, GE-7回转不良, GF-1未加工, GF-2尺寸不良, GF-4形状异常, GF-9加工时其他不良, GZ-9其他不良项