车架通用技术条件
简述车架的功用及对车架的要求
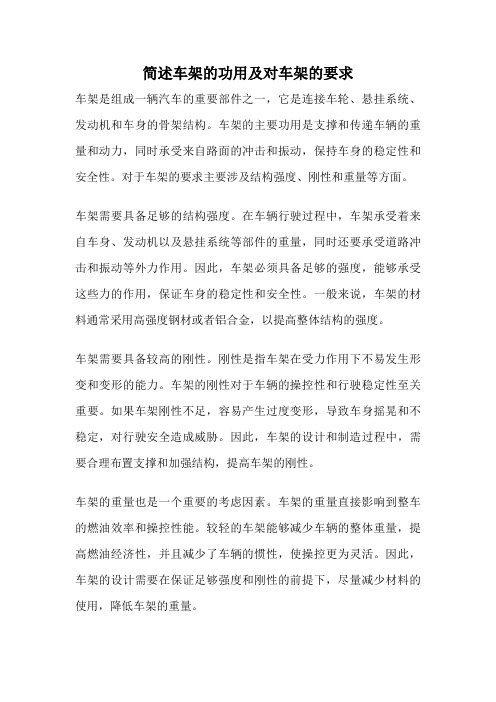
简述车架的功用及对车架的要求车架是组成一辆汽车的重要部件之一,它是连接车轮、悬挂系统、发动机和车身的骨架结构。
车架的主要功用是支撑和传递车辆的重量和动力,同时承受来自路面的冲击和振动,保持车身的稳定性和安全性。
对于车架的要求主要涉及结构强度、刚性和重量等方面。
车架需要具备足够的结构强度。
在车辆行驶过程中,车架承受着来自车身、发动机以及悬挂系统等部件的重量,同时还要承受道路冲击和振动等外力作用。
因此,车架必须具备足够的强度,能够承受这些力的作用,保证车身的稳定性和安全性。
一般来说,车架的材料通常采用高强度钢材或者铝合金,以提高整体结构的强度。
车架需要具备较高的刚性。
刚性是指车架在受力作用下不易发生形变和变形的能力。
车架的刚性对于车辆的操控性和行驶稳定性至关重要。
如果车架刚性不足,容易产生过度变形,导致车身摇晃和不稳定,对行驶安全造成威胁。
因此,车架的设计和制造过程中,需要合理布置支撑和加强结构,提高车架的刚性。
车架的重量也是一个重要的考虑因素。
车架的重量直接影响到整车的燃油效率和操控性能。
较轻的车架能够减少车辆的整体重量,提高燃油经济性,并且减少了车辆的惯性,使操控更为灵活。
因此,车架的设计需要在保证足够强度和刚性的前提下,尽量减少材料的使用,降低车架的重量。
除了上述要求之外,车架还需要考虑其他因素。
例如,车架的设计应该符合车辆的使用环境和需求。
对于越野车或者运输车等重载车型,车架需要更加坚固和耐用,以应对恶劣的路况和重负荷的工作。
而对于轿车和跑车等高性能车型,则需要更加注重车架的轻量化和刚性,以提供更好的操控性能和驾驶体验。
车架作为汽车的骨架结构,具备支撑和传递重量和动力的功能,对于车架的要求主要涉及结构强度、刚性和重量等方面。
车架需要具备足够的强度和刚性,以保证车身的稳定性和安全性。
同时,车架的重量也需要尽量减少,以提高整车的燃油经济性和操控性能。
除此之外,车架的设计还需要考虑车辆的使用环境和需求,以满足不同车型的要求。
半挂车通用技术条件
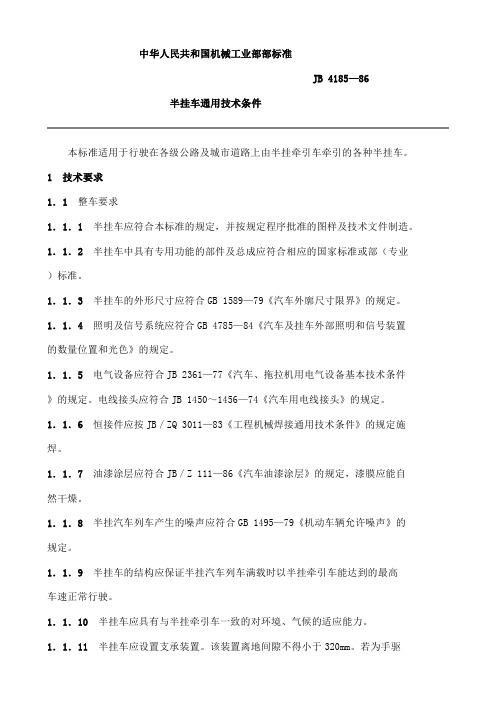
中华人民共和国机械工业部部标准JB 4185—86半挂车通用技术条件本标准适用于行驶在各级公路及城市道路上由半挂牵引车牵引的各种半挂车。
1 技术要求1.1 整车要求1.1.1 半挂车应符合本标准的规定,并按规定程序批准的图样及技术文件制造。
1.1.2 半挂车中具有专用功能的部件及总成应符合相应的国家标准或部(专业)标准。
1.1.3 半挂车的外形尺寸应符合GB 1589—79《汽车外廓尺寸限界》的规定。
1.1.4 照明及信号系统应符合GB 4785—84《汽车及挂车外部照明和信号装置的数量位置和光色》的规定。
1.1.5 电气设备应符合JB 2361—77《汽车、拖拉机用电气设备基本技术条件》的规定。
电线接头应符合JB 1450~1456—74《汽车用电线接头》的规定。
1.1.6 恒接件应按JB/ZQ 3011—83《工程机械焊接通用技术条件》的规定施焊。
1.1.7 油漆涂层应符合JB/Z 111—86《汽车油漆涂层》的规定,漆膜应能自然干燥。
1.1.8 半挂汽车列车产生的噪声应符合GB 1495—79《机动车辆允许噪声》的规定。
1.1.9 半挂车的结构应保证半挂汽车列车满载时以半挂牵引车能达到的最高车速正常行驶。
1.1.10 半挂车应具有与半挂牵引车一致的对环境、气候的适应能力。
1.1.11 半挂车应设置支承装置。
该装置离地间隙不得小于320mm。
若为手驱动时,在半挂车满载情况下,施于手柄的力不得超过196N(特重型半挂车由用户与制造厂另行商定)。
1.1.12 半挂车的最小离地间隙不得小于半挂牵引车的最小离地间隙(特重型半挂车和特种半挂车由用户与制造厂另行商定)。
1.1.13 半挂车使用的润滑油和工作液应与半挂牵引车一致。
1.1.14 半挂车前口转半径(见图1)R=2040mm (最大值)对一般方头半挂车S=1600mm(最大值)对于通道式集装箱半挂车,S的最大值为914mm,不包括安装集装箱闭锁装置或类似装置的前横梁。
车架铆接通用技术要求

精品资料车架铆接通用技术要求发布精品资料前言车架铆接通用技术要求1 范围本标准规定了我公司客车车架总成及其零部件的铆接技术要求。
本标准适用于公司产品设计、工艺设计、操作与质量检验。
2 引用标准QJ/DD04.3.01-2010 切削加工件通用技术条件3 一般要求3.1 铆钉对应的铆钉孔直径及偏差按表1执行。
表1 单位为毫米3.2 铆钉孔间距偏差按QJ/DD04.3.01-2010执行。
3.3 铆钉、铆接零件表面应清洁,不得有锈层、油垢,铆钉孔不得有毛刺。
3.4 铆接零件装配应相互紧贴,可采用螺栓、定位销或夹子紧固被铆接零件,不允许采用焊接(点焊)的方法紧固。
3.5 铆接操作时,上、下铆头和铆钉应同心,以保证铆钉成形准确。
3.6 车架及其零部件采用冷铆铆接。
当技术文件有明确要求时,可采用热铆铆接。
3.7 热铆铆钉加热温度为800℃~900℃,并在500℃以上完成铆接过程。
3.8 热铆铆钉在装入铆钉孔前,必须清除氧化皮,对烧损、烧细、烧坏的铆钉不允许使用。
3.9 根据设备要求,合理选择铆接压力,保证铆钉成形质量。
3.10 铆接后,不符合要求的铆钉应铲去重铆;铲去铆钉时,不应损坏母体金属及相邻铆钉,其铲入深度不得超过0.5 mm。
3.11 铆接质量技术要求3.11.1 铆接后被铆零件应在铆钉四周3倍铆钉杆直径范围内紧密贴合,其间隙不得超过0.05 mm。
3.11.2 成形铆钉头按附录A《铆接缺陷产生原因分析及缺陷检查表》及铆钉预制头要求执行。
3.11.3 其余铆接质量技术要求按附录A《铆接缺陷产生原因分析及缺陷检查表》执行。
附录A 铆接缺陷产生原因分析及缺陷检查表单位为毫米铆接缺陷简图允许偏差缺陷原因检查方法铆钉头与母材贴合不紧密不允许1、铆钉头与铆钉杆连接处有凸起地方2、铆接时,顶具未顶紧1、外部检查2、用锤敲击3、用0.05 mm塞尺检查铆钉头歪斜不允许1、铆接时粗心大意2、顶具放置偏斜1、外部检查2、用0.05 mm 塞尺检查铆钉头有裂纹不允许1、铆钉材质低劣2、铆钉加热过度外部检查铆钉杆在铆钉孔内弯曲不允许铆钉孔大且铆钉杆长敲击钉头铆钉在铆合件内断开不允许1、零件间有间隙2、装配不正确3、压的不紧敲击铆缝用手锤敲打时,铆钉头振荡或活头不允许1、铆接件压的不紧2、铆钉杆在孔内不严密用手锤敲打两面铆钉头铆钉头有凹痕b≤2但在重要地方不允许顶具松动或疏忽而形成外部检查铆钉头周围有帽缘b≤1.51、铆钉杆长2、铆钉模小外部检查铆钉头中心与铆钉杆中心偏移b≤1.51、铆接时粗心大意2、顶具放置偏斜外部检查铆钉头边缘缺肉b+d≤2c≤1.51、铆钉杆短2、铆钉模大外部检查和用样板检查铆钉头过小b≤0.1d1、铆钉杆短2、铆钉模小外部检查和用样板检查铆钉头周围有硬伤(母材上)h≤11、铆钉模大2、铆钉模安放不正外部检查埋头铆钉的钉头突出h≤0.5时允准许用砂轮磨去1、铆钉杆长2、埋头锥边小外部检查埋头铆钉的钉头凹进h≤0.5铆钉杆长度不够埋头锥边大外部检查_________________________________。
汽车卡车车架设计标准是什么
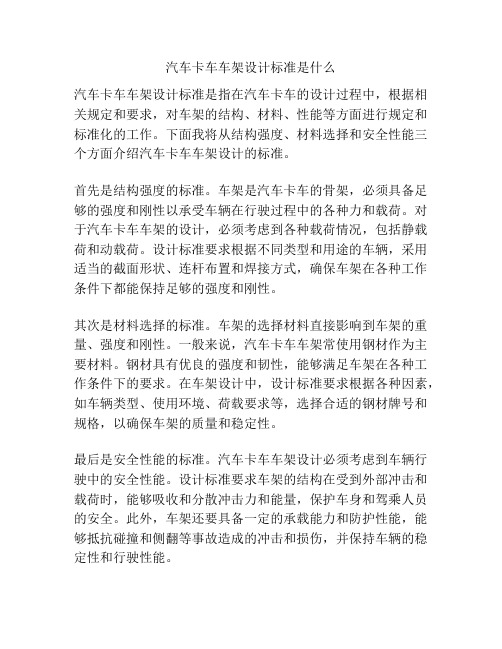
汽车卡车车架设计标准是什么
汽车卡车车架设计标准是指在汽车卡车的设计过程中,根据相关规定和要求,对车架的结构、材料、性能等方面进行规定和标准化的工作。
下面我将从结构强度、材料选择和安全性能三个方面介绍汽车卡车车架设计的标准。
首先是结构强度的标准。
车架是汽车卡车的骨架,必须具备足够的强度和刚性以承受车辆在行驶过程中的各种力和载荷。
对于汽车卡车车架的设计,必须考虑到各种载荷情况,包括静载荷和动载荷。
设计标准要求根据不同类型和用途的车辆,采用适当的截面形状、连杆布置和焊接方式,确保车架在各种工作条件下都能保持足够的强度和刚性。
其次是材料选择的标准。
车架的选择材料直接影响到车架的重量、强度和刚性。
一般来说,汽车卡车车架常使用钢材作为主要材料。
钢材具有优良的强度和韧性,能够满足车架在各种工作条件下的要求。
在车架设计中,设计标准要求根据各种因素,如车辆类型、使用环境、荷载要求等,选择合适的钢材牌号和规格,以确保车架的质量和稳定性。
最后是安全性能的标准。
汽车卡车车架设计必须考虑到车辆行驶中的安全性能。
设计标准要求车架的结构在受到外部冲击和载荷时,能够吸收和分散冲击力和能量,保护车身和驾乘人员的安全。
此外,车架还要具备一定的承载能力和防护性能,能够抵抗碰撞和侧翻等事故造成的冲击和损伤,并保持车辆的稳定性和行驶性能。
总结起来,汽车卡车车架设计的标准主要涉及结构强度、材料选择和安全性能三个方面,以确保车架在各种工作条件下都具备足够的强度、重量和安全性能。
这些标准是保障汽车卡车质量和安全的重要依据,对于汽车卡车制造厂商和设计工程师来说,是设计和生产高质量车辆的基础。
车架铆接通用技术要求

QJ/DD 03.3.05-2001 车架铆接通用技术要求发布QJ/DD 03.3.05-2001 前言1 范围本标准规定了我公司客车车架总成及其零部件的铆接技术要求。
本标准适用于公司产品设计、工艺设计、操作与质量检验。
2 引用标准QJ/DD04.3.01-2010 切削加工件 通用技术条件 3 一般要求3.1 铆钉对应的铆钉孔直径及偏差按表1执行。
表1 单位为毫米3.2 铆钉孔间距偏差按QJ/DD04.3.01-2010执行。
3.3 铆钉、铆接零件表面应清洁,不得有锈层、油垢,铆钉孔不得有毛刺。
3.4 铆接零件装配应相互紧贴,可采用螺栓、定位销或夹子紧固被铆接零件,不允许采用焊接(点焊)的方法紧固。
3.5 铆接操作时,上、下铆头和铆钉应同心,以保证铆钉成形准确。
3.6 车架及其零部件采用冷铆铆接。
当技术文件有明确要求时,可采用热铆铆接。
3.7 热铆铆钉加热温度为800℃~900℃,并在500℃以上完成铆接过程。
3.8 热铆铆钉在装入铆钉孔前,必须清除氧化皮,对烧损、烧细、烧坏的铆钉不允许使用。
3.9 根据设备要求,合理选择铆接压力,保证铆钉成形质量。
3.10 铆接后,不符合要求的铆钉应铲去重铆;铲去铆钉时,不应损坏母体金属及相邻铆钉,其铲入深度不得超过0.5 mm 。
3.11 铆接质量技术要求3.11.1 铆接后被铆零件应在铆钉四周3倍铆钉杆直径范围内紧密贴合,其间隙不得超过0.05 mm 。
3.11.2 成形铆钉头按附录A 《铆接缺陷产生原因分析及缺陷检查表》及铆钉预制头要求执行。
3.11.3 其余铆接质量技术要求按附录A 《铆接缺陷产生原因分析及缺陷检查表》执行。
附录A 铆接缺陷产生原因分析及缺陷检查表 单位为毫米 车架铆接通用技术要求_________________________________。
车架铆接通用技术要求
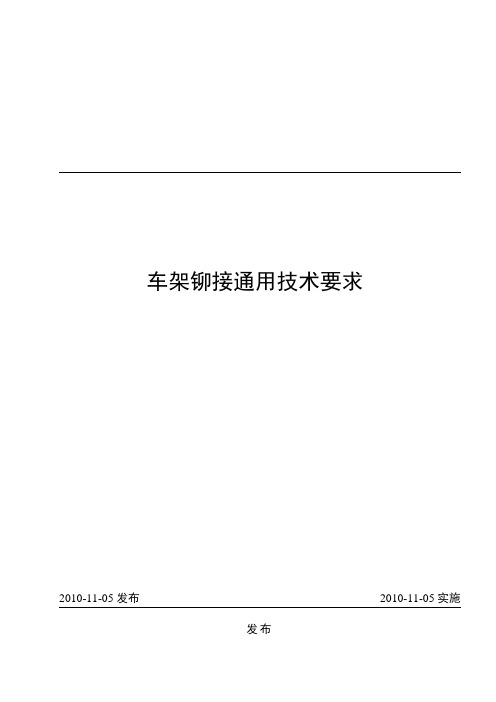
车架铆接通用技术要求发布前言车架铆接通用技术要求1 范围本标准规定了我公司客车车架总成及其零部件的铆接技术要求。
本标准适用于公司产品设计、工艺设计、操作与质量检验。
2 引用标准QJ/DD04.3.01-2010 切削加工件通用技术条件3 一般要求3.1 铆钉对应的铆钉孔直径及偏差按表1执行。
表1 单位为毫米3.2 铆钉孔间距偏差按QJ/DD04.3.01-2010执行。
3.3 铆钉、铆接零件表面应清洁,不得有锈层、油垢,铆钉孔不得有毛刺。
3.4 铆接零件装配应相互紧贴,可采用螺栓、定位销或夹子紧固被铆接零件,不允许采用焊接(点焊)的方法紧固。
3.5 铆接操作时,上、下铆头和铆钉应同心,以保证铆钉成形准确。
3.6 车架及其零部件采用冷铆铆接。
当技术文件有明确要求时,可采用热铆铆接。
3.7 热铆铆钉加热温度为800℃~900℃,并在500℃以上完成铆接过程。
3.8 热铆铆钉在装入铆钉孔前,必须清除氧化皮,对烧损、烧细、烧坏的铆钉不允许使用。
3.9 根据设备要求,合理选择铆接压力,保证铆钉成形质量。
3.10 铆接后,不符合要求的铆钉应铲去重铆;铲去铆钉时,不应损坏母体金属及相邻铆钉,其铲入深度不得超过0.5 mm。
3.11 铆接质量技术要求3.11.1 铆接后被铆零件应在铆钉四周3倍铆钉杆直径范围内紧密贴合,其间隙不得超过0.05 mm。
3.11.2 成形铆钉头按附录A《铆接缺陷产生原因分析及缺陷检查表》及铆钉预制头要求执行。
3.11.3 其余铆接质量技术要求按附录A《铆接缺陷产生原因分析及缺陷检查表》执行。
附录A铆接缺陷产生原因分析及缺陷检查表单位为毫米_________________________________。
车架通用技术条件
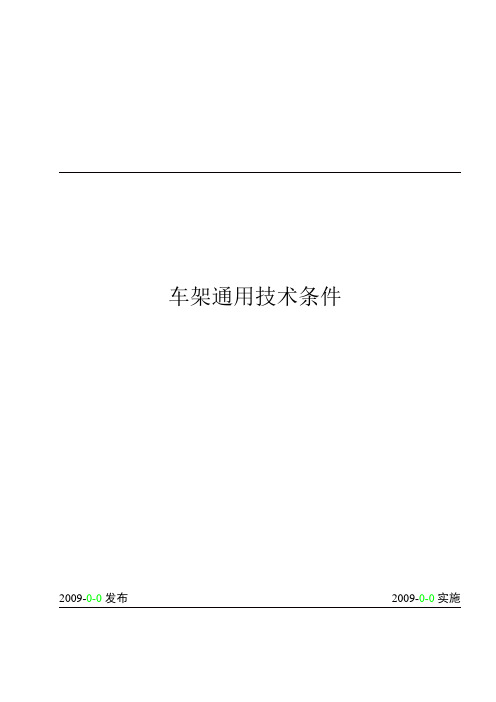
车架通用技术条件前言车架通用技术条件1前言本技术条件是公司车架通用的基本要求,适用于公司车架设计及检验。
2引用标准QJ/DD04.3.23-87 铆接工艺通用技术条件QJ/DD04.3.50-2010 焊接件通用技术条件QJ/DD04.16-2009 客车油漆涂层QJ/DD09.8.10-2009 装配通用技术条件3技术要求3.1车架铆接要求3.1.1铆接要求按QJ/DD04.3.23-87铆接工艺通用技术条件执行。
3.1.2不同心的铆钉孔,允许采用同径铰刀铰孔后铆接。
3.1.3铆接后,不合要求但又在允许偏差范围内的铆钉数,不超过总数的10%,单件上不超过1个。
3.1.4纵梁铆接完成后,对纵梁上下翼面及腹面出现的孔不同心现象,按原孔尺寸引钻。
3.2车架定位焊要求3.2.1槽型梁腹面前后面、上下翼面各焊一段,异型管梁前后腹面各焊一~二段,其余小件每件焊至少两段,每段焊缝长约10 mm,焊角高低于板厚,该焊缝在后续焊接中应被覆盖上。
3.3车架焊接要求3.3.1焊接标准按QJ/DD04.3.50-2010焊接件通用技术条件执行。
3.3.2焊接采用CO2气体保护焊,焊角高度与所焊零件板厚相同。
3.3.3焊接顺序:先焊纵梁联接处→横梁→立柱→其余各支撑梁、小件;焊接中要求由内向外,由中间向前后逐步、对称、交错进行。
3.3.4纵梁搭接、联接处及关键联接件在焊夹具上完成焊接。
3.3.5联接板的塞焊孔≤30mm时,塞焊孔焊平;塞焊孔>30mm时,塞焊孔焊一周;板周边在两孔间断续焊,焊缝长同孔径,焊角高均同板厚。
3.3.6焊接过程中,车架应处于平整状态。
3.4车架检查、修正要求3.4.1车架平面度技术要求3.4.1.1专用焊夹具上生产的老车型车架,平面度≤8mm。
3.4.1.2其余车架平面度≤6mm,每2米≤2mm;带落差车架平面度要求相同,公差按各落差面积分布。
3.4.1.3带行李仓车架在X方向直线度:纵梁≤6mm,每2米≤2mm;支撑梁端头处≤3mm。
中华人民共和国国家标准汽车车架修理技术条件
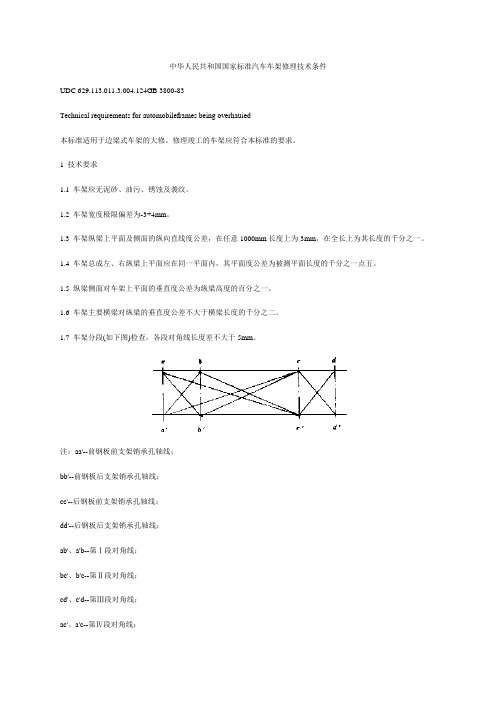
中华人民共和国国家标准汽车车架修理技术条件UDC 629.113.011.3.004.124GB 3800-83Technical requirements for automobileframes being overhauied本标准适用于边梁式车架的大修。
修理竣工的车架应符合本标准的要求。
1 技术要求1.1 车架应无泥砂、油污、锈蚀及袭纹。
1.2 车架宽度极限偏差为-3+4mm。
1.3 车架纵梁上平面及侧面的纵向直线度公差,在任意1000mm长度上为3mm,在全长上为其长度的千分之一。
1.4 车架总成左、右纵梁上平面应在同一平面内,其平面度公差为被测平面长度的千分之一点五。
1.5 纵梁侧面对车架上平面的垂直度公差为纵梁高度的百分之一。
1.6 车架主要横梁对纵梁的垂直度公差不大于横梁长度的千分之二。
1.7 车架分段(如下图)检查,各段对角线长度差不大于5mm。
注:aa'--前钢板前支架销承孔轴线;bb'--前钢板后支架销承孔轴线;cc'--后钢板前支架销承孔轴线;dd'--后钢板后支架销承孔轴线;ab'、a'b--第Ⅰ段对角线;bc'、b'c--第Ⅱ段对角线;cd'、c'd--第Ⅲ段对角线;ac'、a'c--第Ⅳ段对角线;1.8 左右钢板弹簧固定支架销孔应同轴,其同轴度公差为φ2.0mm(按GB 1958-80《形状和位置公差检测规定》检测方法5-1进行检测)。
前后固定支架销孔轴线间的距离左、右相差:轴距在4000mm及其以下的应不大于2mm,轴距在4000mm以上的应不大于3mm。
1.9 车架的焊接应符合焊接规范。
焊缝应平整、光滑、无焊瘤、弧坑,咬边深度不大于0.5mm,咬边长度不大于焊缝长度的百分之十五,并不得有气孔、夹渣等缺陷。
1.10 车架挖补或截修的焊缝方向,除特殊车架外,不允许与棱线垂直、重叠;焊缝及其周围基体金属上,不应有裂纹。
- 1、下载文档前请自行甄别文档内容的完整性,平台不提供额外的编辑、内容补充、找答案等附加服务。
- 2、"仅部分预览"的文档,不可在线预览部分如存在完整性等问题,可反馈申请退款(可完整预览的文档不适用该条件!)。
- 3、如文档侵犯您的权益,请联系客服反馈,我们会尽快为您处理(人工客服工作时间:9:00-18:30)。
车架通用技术条件
前言
车架通用技术条件
1前言
本技术条件是公司车架通用的基本要求,适用于公司车架设计及检验。
2引用标准
QJ/DD04.3.23-87 铆接工艺通用技术条件
QJ/DD04.3.50-2010 焊接件通用技术条件
QJ/DD04.16-2009 客车油漆涂层
QJ/DD09.8.10-2009 装配通用技术条件
3技术要求
3.1车架铆接要求
3.1.1铆接要求按QJ/DD0
4.3.23-87铆接工艺通用技术条件执行。
3.1.2不同心的铆钉孔,允许采用同径铰刀铰孔后铆接。
3.1.3铆接后,不合要求但又在允许偏差范围内的铆钉数,不超过总数的10%,单件上不超过1个。
3.1.4纵梁铆接完成后,对纵梁上下翼面及腹面出现的孔不同心现象,按原孔尺寸引钻。
3.2车架定位焊要求
3.2.1槽型梁腹面前后面、上下翼面各焊一段,异型管梁前后腹面各焊一~二段,其余小件每件焊至少两段,每段焊缝长约10 mm,焊角高低于板厚,该焊缝在后续焊接中应被覆盖上。
3.3车架焊接要求
3.3.1焊接标准按QJ/DD0
4.3.50-2010焊接件通用技术条件执行。
3.3.2焊接采用CO2气体保护焊,焊角高度与所焊零件板厚相同。
3.3.3焊接顺序:先焊纵梁联接处→横梁→立柱→其余各支撑梁、小件;焊接中要求由内向外,由中间向前后逐步、对称、交错进行。
3.3.4纵梁搭接、联接处及关键联接件在焊夹具上完成焊接。
3.3.5联接板的塞焊孔≤30mm时,塞焊孔焊平;塞焊孔>30mm时,塞焊孔焊一周;板周边在两孔间断续焊,焊缝长同孔径,焊角高均同板厚。
3.3.6焊接过程中,车架应处于平整状态。
3.4车架检查、修正要求
3.4.1车架平面度技术要求
3.4.1.1专用焊夹具上生产的老车型车架,平面度≤8mm。
3.4.1.2其余车架平面度≤6mm,每2米≤2mm;带落差车架平面度要求相同,公差按各落差面积分布。
3.4.1.3带行李仓车架在X方向直线度:纵梁≤6mm,每2米≤2mm;支撑梁端头处≤3mm。
3.4.2支撑梁间距尺寸:公称尺寸±3 mm。
3.4.3横梁、支撑梁与纵梁不垂直度允差4:1000。
3.4.4车架左、右纵梁上,发动机左右悬置最近的对称两孔间对角线允差≤5mm。
3.4.5车架前悬挂前支架(前推力杆座)孔中心线,至后悬挂前支架(后推力杆座)孔中心线,两对角线应相等,允差≤5mm。
3.4.6车架前悬挂前支架(前推力杆座)孔中心线,至后悬挂前支架(后推力杆座)孔中心线,同侧轴距应相等,允差≤2 mm。
3.4.7乘客门支撑梁间距尺寸(mm):公称尺寸(+4,0)。
3.4.8前、后悬挂支架处纵梁宽度允差:公称尺寸±1 mm;其余位置左右纵梁宽度允差:公称尺寸±2 mm。
3.4.9车架各段落差允差(mm):公称尺寸(+1,-2)。
3.4.10非六面体(车身无过渡连接件)车架,同侧支撑梁外端直线度≤2 mm。
3.5车架装配悬挂支架要求
3.5.1对不同心悬挂支架孔,允许采用同径铰刀铰孔。
3.5.2悬挂支架螺栓扭矩按QJ/DD09.8.10-2009装配通用技术条件中机械性能10.9级螺栓扭矩执行。
3.6车架涂黑漆要求
3.6.1车架表面涂黑漆,涂层性能指标符合QJ/DD0
4.16-2009客车油漆涂层标准。
3.6.2涂黑漆技术要求
3.6.2.1涂黑漆前要求车架表面打磨均匀,无浮漆、油污、锈蚀、灰尘,焊缝表面无药皮及焊渣等杂质。
3.6.2.2车架焊缝处及表面涂膜损伤处,需补涂防锈底漆,再补涂防腐黑漆。
3.6.2.3车架所有表面、腔体内部及板厚端面等部位均涂黑色防腐面漆,无漏涂、露底。
3.6.3悬挂装配孔及装配面须保护,不得有漆。
3.7车架移工、存放要求
3.7.1车架实行单台移工,移工支撑在车架前后轴附近,并且处于正车状态。
3.7.2车架存放中,要求处于平整状态,支撑点支撑在前后轴中心线±200 mm范围内,单台存放。