压气机叶片磁粉探伤
航空燃气轮机叶片损伤检测与诊断
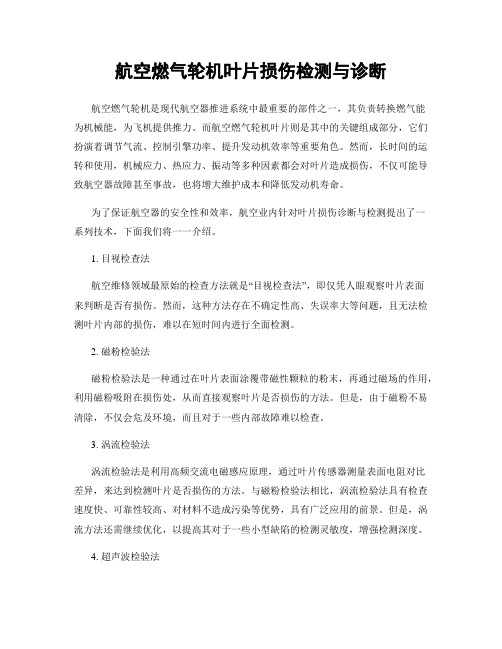
航空燃气轮机叶片损伤检测与诊断航空燃气轮机是现代航空器推进系统中最重要的部件之一,其负责转换燃气能为机械能,为飞机提供推力。
而航空燃气轮机叶片则是其中的关键组成部分,它们扮演着调节气流、控制引擎功率、提升发动机效率等重要角色。
然而,长时间的运转和使用,机械应力、热应力、振动等多种因素都会对叶片造成损伤,不仅可能导致航空器故障甚至事故,也将增大维护成本和降低发动机寿命。
为了保证航空器的安全性和效率,航空业内针对叶片损伤诊断与检测提出了一系列技术,下面我们将一一介绍。
1. 目视检查法航空维修领域最原始的检查方法就是“目视检查法”,即仅凭人眼观察叶片表面来判断是否有损伤。
然而,这种方法存在不确定性高、失误率大等问题,且无法检测叶片内部的损伤,难以在短时间内进行全面检测。
2. 磁粉检验法磁粉检验法是一种通过在叶片表面涂覆带磁性颗粒的粉末,再通过磁场的作用,利用磁粉吸附在损伤处,从而直接观察叶片是否损伤的方法。
但是,由于磁粉不易清除,不仅会危及环境,而且对于一些内部故障难以检查。
3. 涡流检验法涡流检验法是利用高频交流电磁感应原理,通过叶片传感器测量表面电阻对比差异,来达到检测叶片是否损伤的方法。
与磁粉检验法相比,涡流检验法具有检查速度快、可靠性较高、对材料不造成污染等优势,具有广泛应用的前景。
但是,涡流方法还需继续优化,以提高其对于一些小型缺陷的检测灵敏度,增强检测深度。
4. 超声波检验法超声波检验法是利用高频超声波探头,通过对叶片材料的声波传递生成的信号进行反射和漏声检测,从而达到诊断叶片损伤的目的。
该方法具有检测准确度高、参数控制容易等优势,可以应用于广泛范围的叶片材质,也被众多企业所采用。
但是,这种方法的缺点在于需要专业人员操作,以确保正确使用探头,从而避免少量损伤未被检测到。
总之,目前的科技手段还无法完全解决燃气轮机叶片损伤检测的问题,但各种方法各有所长,面对不同损伤类型,只有综合运用多种检测方法,才能更为准确、全面地发现、诊断叶片损伤。
汽轮机动叶片磁粉探伤伪磁痕现象分析

探 伤 结 果
探 伤 结 果
经事后 分析 , 述事件 为典 型 的伪磁 痕 现象 。 上
就 此 问题 , 者结 合 在动 叶片 磁 粉探 伤 检测 中 笔
出现 的具体情 况作 了分析 。
2 原因分析
将 上述 两类 事 件 分别 以 A、 B表 示 。从 原 材 料 人手加 以分 析 、 论 。首先 , A、 讨 从 B两 种 叶 片 中取
作 者 简 介 : 淑 秋 ( 9 6一) 女 , 川 内 : , 黄 16 , 四 l 主要 从 事 材 料 技 术 质 量 控 制 丁 作 。 人
维普资讯
第 1 期 1
黄淑秋 : 汽轮机动叶片磁粉探伤伪磁痕现象分析
・1 5・
分析 , 再从 两种 叶片 的工 艺 方 面 进 行 分 析 。分 析 结 果如 下 : ( )磁 痕显示部 位 金相分 析 1
汽轮机动叶 片磁粉探伤伪磁痕现象分析
黄 淑秋
( 州 汽 轮 机 股 份 有 限 公 司 , 江 杭 州 30 2 ) 杭 浙 10 2
摘 要 : 汽轮机 动 叶片磁粉 探 伤过程 中 出现的 特殊磁 痕 现 象进 行 了分析 , 出了产生伪 磁痕 的原 对 找
因, 过热 处理 工 艺消除 了特 殊磁 痕现 象 。 通 关键词 : 汽轮 机 动叶 片 ; 特殊磁 痕 分析 ; 伪磁 痕 ; 消除
( a gh uSe m T rieC , Ld , a g h u 3 0 2 ,C ia H n z o t ub o , t. H n zo 0 2 hn ) a n 1
Absr c t a t:Th p ca g e i ma e i h g ei n pe t n o ta t r i eblde sa ay e e s e ilma n tc i g n t e ma n tci s ci fse m u b n a swa n lz d,t a s to ft e o hec u ain o h fk g e i s d s o ee a e ma n tc wa ic v r d.i wa lmi t d i by h a r amen e hn c . t s ei nae t e tte t tt c i s
CFM56-7B航空燃气涡轮发动机叶片典型损伤模型建立、外来物损伤分析、检测方法及修复方式研究
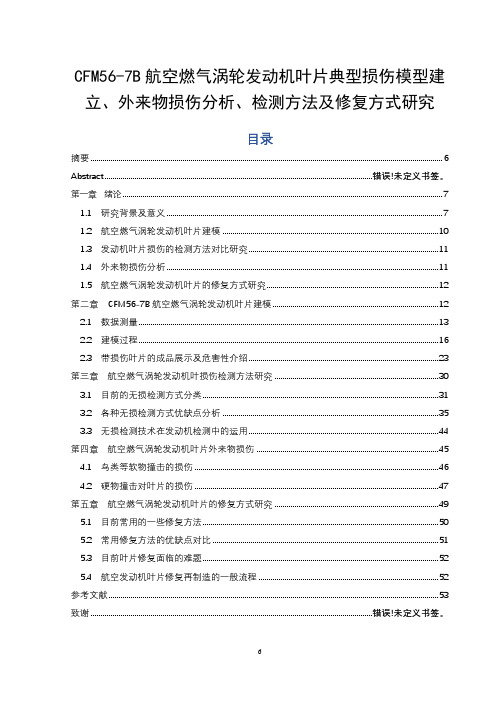
CFM56-7B航空燃气涡轮发动机叶片典型损伤模型建立、外来物损伤分析、检测方法及修复方式研究目录摘要 (6)Abstract ...................................................................................................................................... 错误!未定义书签。
第一章绪论. (7)1.1 研究背景及意义 (7)1.2 航空燃气涡轮发动机叶片建模 (10)1.3 发动机叶片损伤的检测方法对比研究 (11)1.4 外来物损伤分析 (11)1.5 航空燃气涡轮发动机叶片的修复方式研究 (12)第二章CFM56-7B航空燃气涡轮发动机叶片建模 (12)2.1 数据测量 (13)2.2 建模过程 (16)2.3 带损伤叶片的成品展示及危害性介绍 (23)第三章航空燃气涡轮发动机叶损伤检测方法研究 (30)3.1 目前的无损检测方式分类 (31)3.2 各种无损检测方式优缺点分析 (35)3.3 无损检测技术在发动机检测中的运用 (44)第四章航空燃气涡轮发动机叶片外来物损伤 (45)4.1 鸟类等软物撞击的损伤 (46)4.2 硬物撞击对叶片的损伤 (47)第五章航空燃气涡轮发动机叶片的修复方式研究 (49)5.1 目前常用的一些修复方法 (50)5.2 常用修复方法的优缺点对比 (51)5.3 目前叶片修复面临的难题 (52)5.4 航空发动机叶片修复再制造的一般流程 (52)参考文献 (53)致谢............................................................................................................................................. 错误!未定义书签。
磁粉探伤方法和工艺简介精选文档

磁粉探伤方法和工艺简介精选文档TTMS system office room 【TTMS16H-TTMS2A-TTMS8Q8-磁粉探伤方法和工艺简介射阳县德阳电子有限公司一.剩磁法和连续法1.剩磁法指先将工件磁化,再将磁粉或磁悬液施加到工件表面以检查工件缺陷的方法。
适用于经淬火,调质处理等增强强度或硬度的热处理后的高碳钢和合金钢,不适用于低碳钢和经退火处理或热变形钢材,马氏体不锈钢用剩磁法效果不如连续法。
剩磁法特别适用于批量小件的探伤,此时生产效率高。
2.连续法又称外加法,系指在外加磁场的作用下,将磁粉或磁悬液施加到工件上去进行探伤的方法。
目前该法比较流行的工艺是,先喷洒磁悬液,接着磁化(通电1-3秒),此时仍继续浇注磁悬液,停止浇注后再通电数次,每次秒,中断磁化后观察缺陷,最后退磁。
连续法适用于所有铁磁性材料。
教科书中推荐优先使用剩磁法,实际中多采用连续法。
二.直流磁化和交流磁化1.直流磁化目前已很少采用纯直流电,而采用单相半波或全波,三相半波或全波整流电。
2.交流磁化一般采用工频交流电。
交流磁化时,起作用的是电流的峰值,但一般标示的电流值是有效值。
交流磁化和直流磁化都能检测表面和近表面缺陷,交流磁化对表面缺陷的检测灵敏度高,直流磁化检测表面下的缺陷的能力强一些。
一般说来,电流中包含的脉动成份越大,探测内部缺陷的能力越弱。
直流磁化用于剩磁法时剩磁稳定,交流磁化则剩磁不够稳定,加断电相位控制器可解决此问题(采用过零点断电的方法叫断电相位控制,以防止对工件形成退磁作用)。
直流磁化退磁困难,交流磁化退磁容易。
目前一般推荐使用交流磁化,且多采用连续法,此时一般也加断电相位控制。
使用交流连续磁化,设备结构简单,成本低,磁化效果一般都能满足要求。
也有使用交直流混合磁化的,此时,交流磁化在前,直流磁化在后,以利于退磁。
三.磁化方法1.周向磁化。
指给工件直接通电,或者使电流流过贯穿工件中心孔的导体,旨在工件中建立一个环绕工件的并与工件轴垂直的闭合磁场。
汽轮机叶片叶身的无损检测技术探析
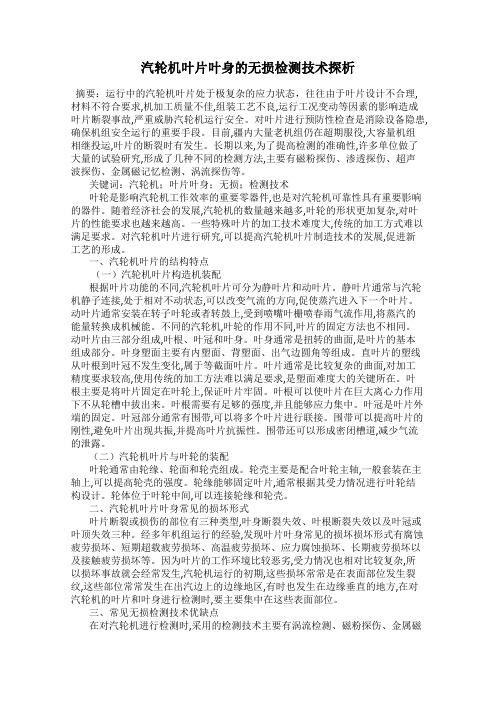
汽轮机叶片叶身的无损检测技术探析摘要:运行中的汽轮机叶片处于极复杂的应力状态,往往由于叶片设计不合理,材料不符合要求,机加工质量不佳,组装工艺不良,运行工况变动等因素的影响造成叶片断裂事故,严重威胁汽轮机运行安全。
对叶片进行预防性检查是消除设备隐患,确保机组安全运行的重要手段。
目前,疆内大量老机组仍在超期服役,大容量机组相继投运,叶片的断裂时有发生。
长期以来,为了提高检测的准确性,许多单位做了大量的试验研究,形成了几种不同的检测方法,主要有磁粉探伤、渗透探伤、超声波探伤、金属磁记忆检测、涡流探伤等。
关键词:汽轮机;叶片叶身;无损;检测技术叶轮是影响汽轮机工作效率的重要零器件,也是对汽轮机可靠性具有重要影响的器件。
随着经济社会的发展,汽轮机的数量越来越多,叶轮的形状更加复杂,对叶片的性能要求也越来越高。
一些特殊叶片的加工技术难度大,传统的加工方式难以满足要求。
对汽轮机叶片进行研究,可以提高汽轮机叶片制造技术的发展,促进新工艺的形成。
一、汽轮机叶片的结构特点(一)汽轮机叶片构造机装配根据叶片功能的不同,汽轮机叶片可分为静叶片和动叶片。
静叶片通常与汽轮机静子连接,处于相对不动状态,可以改变气流的方向,促使蒸汽进入下一个叶片。
动叶片通常安装在转子叶轮或者转鼓上,受到喷嘴叶栅喷春雨气流作用,将蒸汽的能量转换成机械能。
不同的汽轮机,叶轮的作用不同,叶片的固定方法也不相同。
动叶片由三部分组成,叶根、叶冠和叶身。
叶身通常是扭转的曲面,是叶片的基本组成部分。
叶身塑面主要有内塑面、背塑面、出气边圆角等组成。
直叶片的塑线从叶根到叶冠不发生变化,属于等截面叶片。
叶片通常是比较复杂的曲面,对加工精度要求较高,使用传统的加工方法难以满足要求,是塑面难度大的关键所在。
叶根主要是将叶片固定在叶轮上,保证叶片牢固。
叶根可以使叶片在巨大离心力作用下不从轮槽中拔出来。
叶根需要有足够的强度,并且能够应力集中。
叶冠是叶片外端的固定。
叶冠部分通常有围带,可以将多个叶片进行联接。
V2500发动机高压压气机叶片损伤检查

V2500发动机高压压气机叶片损伤检查崔宗辉,苏金波郑攀忠(山东太古飞机工程有限公司,济南 250107)(GE 检测控制技术,上海201203)摘要:压气机叶片是航空发动机中的重要零件,在高温、高压、振动以及巨大的离心力等恶劣的工作环境下,易产生腐蚀、疲劳裂纹甚至断裂等故障。
如果不能及时发现这些损伤,会造成发动机空中停车,危及飞行安全。
本文所介绍的超声波检查HPC 4级叶片榫头,是一种有效杜绝安全隐患的方法。
关键词:超声波检测;叶片;裂纹;缺陷评估, GE USN52ULTRASONIC INSPECTION OF V2500 ENGINE HIGH PRESSURE COMPRESSOR BLADE FOR DAMAGECUI Zong-hui,SU Jin-bo(Taikoo [Shandong] Aircraft Engineering Co.Ltd, Jinan 250107, China)ZHENG Pang-zhong(GE Measurement & Control, Shanghai 201203,China ) Abstract:Compressor vanes are the important parts of the aero-engine. Erosion, fatigue cracking and even fracture might be found on compressor vanes frequently. If cannotbe detected adequately, the damage could lead to in-flight shut down and affectthe flight safety of the aircraft. The ultrasonic inspection of HPC stage 4 bladeroots was introduced. It is an effective method for preventive safety events. Keywords:Ultrasonic testing; Blades; Cracks; Defect analysis , GE USN52 V2500发动机是IAE公司研制的轴流式、双转子、高涵道比涡轮风扇发动机,它有A5/D5两大系列,该发动机被广泛应用于A321、A320、A319和MD90等中型民用飞机上。
航空发动机高压涡轮叶片损伤检测策略

航空发动机高压涡轮叶片损伤检测策略随着航空工业的发展,航空发动机的性能要求越来越高。
其中,高压涡轮叶片作为发动机中重要的部件之一,其工作环境恶劣,容易受到损伤。
因此,高压涡轮叶片的损伤检测策略成为了航空工程领域的研究热点之一。
本文将从不同的角度探讨航空发动机高压涡轮叶片损伤检测策略,包括传统方法和新兴技术。
传统的航空发动机高压涡轮叶片损伤检测方法主要基于人工检查和非破坏性检测技术。
人工检查需要专业技术人员对叶片进行目视检查,通过检查叶片表面的裂纹、磨损和腐蚀等情况来判断叶片是否损坏。
这种方法虽然简单,但受限于人工经验和操作技巧的局限,容易出现漏检和误判的情况。
非破坏性检测技术包括磁粉探伤、涡流探伤和超声波检测等,这些技术可以通过对叶片进行表面或内部缺陷的检测来判断叶片是否存在损坏。
然而,非破坏性检测技术需要专业设备和操作人员,并且对叶片进行检测需要拆卸发动机,对航空公司和运营商来说是一个复杂的操作。
为了弥补传统方法的不足,新兴技术逐渐应用于航空发动机高压涡轮叶片损伤检测。
其中,机器学习和无人机技术是最常见的方法之一。
机器学习使用大量的数据训练算法模型,通过识别叶片的不同状态来判断叶片是否损坏。
这种方法基于大数据分析和模式识别,可以提高叶片损伤检测的准确性和效率。
无人机技术可以通过无人机搭载的高清相机或红外热像仪对叶片进行拍摄和监测,通过图像处理和数据分析来检测叶片的损伤情况。
这种方法不需要拆卸发动机,可以实时监测叶片的状态,减少了维修和检测的成本。
另外,纳米技术作为一种新型材料应用技术,也被广泛研究用于航空发动机高压涡轮叶片损伤检测。
纳米材料具有超高的比表面积和优异的电学、光学、磁学等特性,可以用于检测叶片表面的微小损伤。
例如,纳米传感器可以通过吸附在叶片表面的方式来实时监测叶片的应力和温度变化,从而判断叶片是否存在损伤。
此外,纳米材料还可以用于涂覆叶片表面,形成一层保护膜,提高叶片的抗损伤性能。
车辆无损检测技术—磁粉探伤的原理及方法

线圈
电流
缺陷
纵向 磁化
磁场
缺陷 电源
横向 磁化
5.磁粉探伤的不足之处
对于金属内部较深的裂纹与缺陷,采用电磁 探伤是不大容易发现的。
这时虽然磁力线遇到缺陷而弯曲,但由于缺陷与 外表的距离较远,磁力线不可能泄漏到外表面, 以致工件表面各处的磁力线密度相差不大,磁粉 不会集中。
它是一种车辆轮对车轴表面探伤的专用设备。 它设置了纵向和横向联合磁化装置,采用磁悬液荧光磁粉显示,在操作机械化和探伤灵敏
度等方面比较先进,并便于实现流水作业。
6.车辆磁粉探伤的设备
全磁探 伤机磁 悬液喷 洒、回 收装置
1-液泵 5-喷头
2-搅拌器 6-回收槽
3-输液管 7-换向阀
4-输液管 8-贮液槽
C ATA L O G
02 PART
显示方法
PART 03 磁粉
PART 04 零件磁化
PART 05 磁粉探伤的不足之处
PART 06 车辆磁粉探伤的设备
SN SN
SN
一、磁粉探伤的工作原理
SN SN
SN
SN
SN
SN
磁化漏磁场Leabharlann 吸附磁粉二、显示方法
磁粉 聚集在漏磁场附近,可以从磁粉聚集的形状判断出裂纹的深度和长度。
1.裂纹的磁痕特征一般为锯齿形,两端呈尖角状,磁粉 聚集的图像不规则,清晰、密集。
2.发纹的磁痕特征呈直的或微弯的细线,磁粉聚集图像 呈细长、平直。
3.伪磁痕的磁痕特征是绝大部分的磁粉聚集图像都比较散 乱,再次磁化检查时,一般复现状况不好或完全不复现。
磁粉探伤的操作方法
磁粉探伤在汽轮机叶片质量检测中的应用

磁粉探伤在汽轮机叶片质量检测中的应用一、磁粉探伤技术简介磁粉探伤技术是一种利用磁性粉末检测材料内存在的表面和近表面缺陷的非破坏性检测方法。
磁粉探伤根据检测对象的不同可分为湿法磁粉探伤和干法磁粉探伤两种方法。
湿法磁粉探伤是通过在被检测件表面涂覆磁性粉末,在施加磁场后,通过粉末的吸附性把磁场分布的不均匀呈现出来,形成磁极,用肉眼、放大镜或显微镜观察,直接得出缺陷位置和形状;而干法磁粉探伤是将磁性粉末直接喷洒在被检测的物体表面,在作用磁场时,磁粉堆积的地方就可以观察到缺陷的位置和形状。
磁粉探伤技术能有效地检测到叶片表面和近表面的裂纹、疤痕、孔洞等缺陷。
二、汽轮机叶片的质量检测要求汽轮机叶片作为汽轮机的核心组成部分之一,其质量直接关系到汽轮机的工作效率和安全运行。
由于汽轮机叶片在工作过程中承受着高温、高压、高速等复杂工况的作用,因此其质量检测要求十分严格。
汽轮机叶片的质量检测主要包括表面缺陷检测、腐蚀检测和内部缺陷检测。
表面缺陷主要包括裂纹、疤痕、孔洞等,这些缺陷会导致叶片的损坏,降低汽轮机的工作效率,并可能引发事故。
对于汽轮机叶片的质量检测必须十分严格,确保叶片的质量和安全运行。
三、磁粉探伤技术在汽轮机叶片质量检测中的应用1. 汽轮机叶片的表面缺陷检测磁粉探伤技术能够有效地检测汽轮机叶片表面的裂纹、疤痕、孔洞等缺陷。
通过涂覆磁性粉末或直接喷洒磁性粉末,在施加磁场后,可以观察到叶片表面的缺陷情况,及时发现并修复叶片的表面缺陷。
这对于确保叶片的质量和延长汽轮机的使用寿命起到了重要作用。
2. 汽轮机叶片的腐蚀检测磁粉探伤技术还可以用于检测汽轮机叶片的腐蚀情况。
在施加磁场后,如果叶片表面存在腐蚀,利用磁粉探伤技术可以及时发现叶片的腐蚀部位,从而及时进行修复和保养,防止腐蚀扩大,确保汽轮机叶片的质量和安全运行。
2. 高精度:磁粉探伤技术能够对叶片的表面和近表面进行精确检测,能够清晰地显示出缺陷的位置和形状,确保叶片的质量检测结果准确可靠。
磁粉探伤在汽轮机叶片质量检测中的应用

磁粉探伤在汽轮机叶片质量检测中的应用
磁粉探伤是一种无损检测技术,其应用于汽轮机叶片质量检测也表现出了良好的检测效果。
磁粉探伤技术在汽轮机叶片质量检测中的应用主要体现在以下三个方面。
首先,磁粉探伤具有良好的快速性。
在汽轮机叶片质量检测中,磁粉探伤可以在较短的时间内完成全面的质量检测。
一份汽轮机叶片探伤报告仅需要几小时时间便可完成,这大大减少了汽轮机叶片探伤的成本。
其次,磁粉探伤技术具有可靠性和可操纵性。
磁粉探伤技术具有高灵敏度、可重复性和可操纵性,用磁屏蔽的汽轮机叶片可以很容易地检测出尺寸小或深度大的缺陷,可以大大改善汽轮机叶片的质量。
最后,磁粉探伤技术的操作简单,安全性高。
采用磁粉探伤技术对汽轮机叶片进行检测时,无需将叶片从机体上拆下,也不需要使用危险物质,当不进行操作时也没有任何隐患,很安全。
综上所述,磁粉探伤技术在汽轮机叶片质量检测方面具有诸多优良性能,可大大提高汽轮机叶片质量检测的效率、可靠性和安全性,值得在实践中深入研究和应用。
磁粉探伤机在产学研合作中的应用案例

磁粉探伤机在产学研合作中的应用案例磁粉探伤机是一种非破坏性检测设备,能够有效地检测材料中的裂纹、缺陷等隐患。
在制造业中广泛应用,以确保产品质量和安全性。
产学研合作在磁粉探伤机的应用中起到了重要的推动作用。
本文将介绍一些磁粉探伤机在产学研合作中的应用案例,以展示其在实际生产中的重要性和价值。
案例一:航空发动机叶片的磁粉探伤航空发动机是航空器的核心部件,其质量和性能直接影响到飞机的安全性和可靠性。
然而,由于叶片工作在恶劣的高温高压环境下,易受到外界冲击或热应力的影响,因此经常出现裂纹或疲劳现象。
为了确保航空发动机的可靠性,研究人员与航空制造企业合作,采用磁粉探伤技术对航空发动机叶片进行定期检测。
在研究中,研究人员首先需要了解叶片的材料特性和工作环境,然后确定适合该材料和环境的磁粉探伤方法。
通过采集一定数量的叶片样品,研究人员进行了一系列的实验和分析。
最终,他们成功地开发出了一套适用于航空发动机叶片的磁粉探伤机。
该设备可以快速准确地检测叶片中的微小裂纹和缺陷,确保叶片的安全性和可靠性。
案例二:汽车零部件的磁粉探伤汽车是人们生活中最常见的交通工具之一,其零部件的质量和性能直接关系到行车安全和乘坐舒适度。
为了保证汽车零部件的质量,汽车制造企业与研究机构合作,开展磁粉探伤技术的研究和应用。
以发动机缸体为例,这是汽车发动机中最重要的零部件之一。
在生产过程中,由于工艺限制或材料缺陷等原因,缸体很容易出现裂纹或其他隐患。
为了有效地检测缸体的质量问题,研究人员与汽车制造企业合作,建立了一个针对缸体的磁粉探伤系统。
该系统利用磁粉探伤机器对缸体进行全面的非破坏性检测。
通过大量实验和数据分析,研究人员不断优化磁粉探伤机的参数设置和操作方法,以提高缸体检测的准确性和效率。
最终,他们成功地研发出一套可靠的磁粉探伤技术和设备,能够在汽车生产中广泛应用。
案例三:铁路轨道的磁粉探伤铁路轨道是铁路交通系统中最重要的部件之一,直接关系到列车的运行安全和平稳性。
磁粉探伤机在航天工业中的应用

磁粉探伤机在航天工业中的应用航天工业是一项高度复杂和关键性的领域,对于飞行器和宇宙航行器的安全性和可靠性提出了高要求。
在航天器的制造和维修过程中,磁粉探伤技术被广泛应用,以确保航天器的质量和可靠性。
磁粉探伤机作为一种非破坏性检测设备,在航天工业中发挥着至关重要的作用。
磁粉探伤技术基于电磁感应的原理,通过在已磁化的材料表面施加磁粉,然后观察和检测材料表面上可能存在的裂纹、缺陷和不均匀性。
磁粉探伤机利用磁粒子在磁场作用下的特性,通过观察和分析磁粒子在材料表面的分布和聚集情况,来判断材料是否存在缺陷。
在航天工业中,磁粉探伤机的应用非常广泛。
首先,在航天器的制造过程中,磁粉探伤技术可以用于检测和识别材料的缺陷和裂纹。
航天器的结构和材料要能够承受各种极端环境条件和载荷,因此对于材料的质量和可靠性有着极高的要求。
通过使用磁粉探伤技术,可以对航天器的关键零部件和结构进行全面的检测和评估,确保其符合设计要求,并能够在极端环境下正常工作。
其次,在航天器的维修和维护过程中,磁粉探伤技术也扮演着重要的角色。
航天器在使用过程中可能会受到撞击、高温、高压等因素的影响,导致结构出现裂纹和缺陷。
这些缺陷如果不能及时发现和修复,可能会导致航天器在飞行中出现故障,甚至发生事故。
通过使用磁粉探伤技术,可以检测和识别航天器结构中的潜在问题,及早采取修复措施,确保航天器的正常工作和使用寿命。
此外,磁粉探伤技术还可以应用于航天器发动机和推进系统的检测和评估。
航天器的发动机是其最核心的部件之一,其工作性能直接关系到航天器的安全和可靠性。
通过使用磁粉探伤技术,可以对航天器发动机的叶片、涡轮和其他关键零部件进行全面的检测和评估,确保其工作良好,并在飞行中不会出现故障。
需要指出的是,磁粉探伤技术在航天工业中的应用还需要结合其他非破坏性检测技术和手段来进行综合评估。
例如,超声波检测、X射线检测等技术可以与磁粉探伤技术相结合,以提高对航天器结构和零部件的检测精度和准确性。
浅谈燃气轮机检修中的检查工作

浅谈燃气轮机检修中的检查工作摘要:近年来全国天然气发电行业火速发展,更新更大的燃气轮机发电厂在各地落户。
燃气轮机的检修对于机组的经济性和安全性至关重要。
在燃机检修中主要的技术工作包括计划、检查、测量和记录。
其中检查各种措施和文件、新旧部件状态、孔探检查和探伤检查是每日最频繁的技术工作之一。
大唐国际北京高井热电厂作为亚洲首个9FB燃机电厂,在2016年进行了三台燃机本体首次检修工作。
本文对现场检修中的检查工作做了详细梳理,希望能为今后检修工作及其他燃机电厂检修提供借鉴参考。
关键词:燃气轮机;检修;措施文件;部件状态;孔探和探伤在北京高井热电厂9FB燃机检修中,检查工作主要包括九方面工作:(1)开工检查表、两票(2)系统隔离措施、(3)顶缸支撑高度、(4)拆下的旧部件检查、(5)新部件安装前检查、(6)叶片检查、(7)孔探检查、(8)无损探伤检查、(9)旧零件收集清点。
1开工检查表、两票在现场检修开始之前,需要逐项检查开工检查表上的事项,确认各项准备工作已经完成,满足开工条件。
由现场工程师和工长签名、确认后方可开工。
开工检查表上需要检查确认的主要内容包括:安全计划、备品备件、现场布置图、进度图、现场施工工艺手册、隔离措施等。
检修开始前,需要检查两票,确认工作票内容已经覆盖检修中的所有内容并且各项措施正确。
2隔离措施燃机检修现场隔离保护措施共两种,两票和挂牌上锁隔离措施。
两票由运行人员实施,将相关设备断电、关闭等。
挂牌上锁隔离措施是燃机现场检修团队做的第二道保护措施,将所需隔离系统的盘柜、阀门等挂牌上锁。
需要隔离的系统包括:天然气燃料系统、LCI励磁变、冷却密封系统、启动系统、润滑油系统、液压油系统、冷却水系统、火灾保护系统、水洗系统。
钥匙由燃机检修人员保管,防止误操作等问题。
挂牌上锁完成后,对照清单逐项检查措施是否已经完成,并由现场工程师和工长确认签字。
3检查缸体支撑顶起高度。
在本体检修中,需要拆卸燃烧器和揭透平缸上缸,在拆卸中缸体会发生张口和变形。
压气机叶片根部原位检测传感器的设计与制作

在带有磁芯的线圈上通以交流电,轴线上的磁感应强度可根据毕奥-萨伐尔-拉普拉斯定律[5]得到
(2)
式中:μ0为真空磁导率;I为激励电流;r为磁芯线圈的半径;x为轴线上某点M到线圈平面的距离。
通过设置不同的磁芯尺寸对比,在保持被测体与探头距离不变的情况下,设置不同的磁芯尺寸。
【期刊名称】《无损检测》
【年(卷),期】2018(040)010
【总页数】6页(P10-15)
【关键词】叶片根部;涡流传感器;设计与制作
【作 者】龚模辉;胡博;于润桥;于瑞栋
【作者单位】南昌航空大学 无损检测教育部重点实验室,南昌 330063;南昌航空大学 无损检测教育部重点实验室,南昌 330063;南昌航空大学 无损检测教育部重点实验室,南昌 330063;南昌航空大学 无损检测教育部重点实验室,南昌 330063
(1)
式中:f为激励频率;Bm为饱和磁感应强度;d为磁芯的直径;ρ为磁芯材料电阻率;D为磁芯材料的密度。
从式(1)可知,要使涡流损耗最低,应该尽可能地使用较低的饱和磁通密度和电导率,以最大程度地减少磁通衰减。另外,考虑到磁芯中电磁感应的存在会不断地产生焦耳热,因此磁芯材料需要具有较高的居里温度Tc。
图6 栅极回路LC并联电路结构和频率与电流的关系曲线
谐振频率计算公式为
(4)
式中:L为线圈电感;C为电容。
根据工作频率f与谐振频率f0,选取合适的并联电容与线圈电感,使谐振频率达到工作频率。通过重复试验得到,线圈电感为15~35 μH,线圈匝数为20~30。
1.5 传感器磁芯的加工设计
图7 叶片根部检测位置的不规则曲面
锰锌和镍锌材料铁氧体都具有较低的饱和磁通密度和电阻率,能够最大程度地减小磁场的衰减;且由于镍锌材料电阻率较高,适合在频率较高的环境下工作。根据检测的压气机叶片材料可知,激励频率不宜过高,在频率低于2 MHz时,锰锌材料的性能明显好一些。锰锌材料的初始磁导率高于镍锌材料的,在达到磁饱和前将得到更高的磁通密度[8]。因此,传感器选择锰锌材料作为磁芯的材料,以最大程度地减少磁场的衰减,提高检测灵敏度。
磁粉探伤机
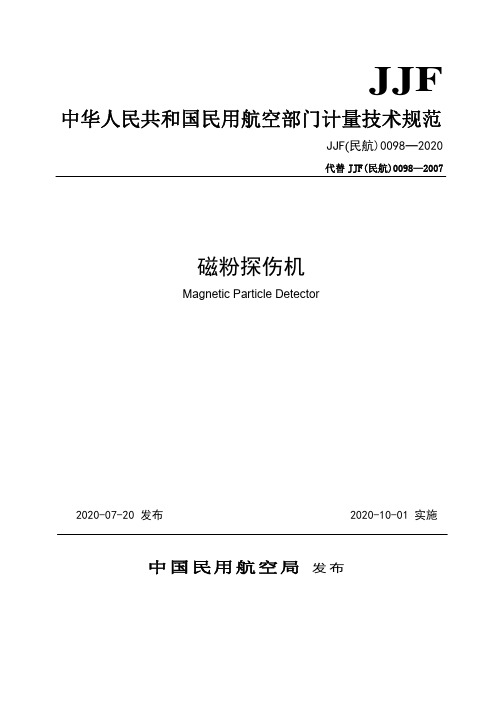
校准规范
JJF(民航) 0098-2020
Calibration Specification for
代替 JJF(民航) 0098—2007
Magnetic Particle Detector
本规范经中国民用航空局2020年07月20日批准,并自2020年10月 01日起施行。
归口单位:中国民用航空局航空器适航审定司 起草单位:北京飞机维修工程有限公司
本规范技术条文由起草单位负责解释。
JJF(民航) 0098-2020
本规范起草人: 周 博 (北京飞机维修工程有限公司) 姜 威 (北京飞机维修工程有限公司) 丁 政 (北京飞机维修工程有限公司) 陈 成 (北京飞机维修工程有限公司) 于荣浩 (北京飞机维修工程有限公司)
JJF(民航) 0098-2020
注:安匝为输出电流与线圈匝数的乘积。
6.8.3.3 按压充磁按钮,检查电压峰值读数,将读数填入附录A表A.8中。 7 校准结果
经校准的磁粉探伤机出具校准证书,校准证书记录格式见附录 A,校准证书 内容见附录 B,测量不确定度评定方法见附录 C,不确定度评定示例见附录 D。 8 复校时间间隔
磁粉探伤机的复校时间间隔一般不超过 6 个月,必要时可随时校准。
5 校准项目
校准项目如下: a) 通用技术要求检查; b) 绝缘电阻的检查; c) 纵向磁化电流的校准; d) 周向磁化电流的校准; e) 磁化时间的校准; f) 磁场快断的检查。
6 校准方法
6.1 通用技术要求检查 磁粉探伤机应无影响正常工作的机械损伤,各旋钮开关应操作灵活、接触可
靠、定位准确。夹持装置,接线端等不应有松动现象。 被校磁粉探伤机的附件及文件应齐全。
6
附录 A
2Cr13汽轮机叶片裂纹磁粉检测工艺选择与应用__

硬化区
13mm 进 汽 侧 端 部
正常母材区
裂纹源点
电火花强化
图 1 某电厂 #1 机 低 压 末 级 叶 片 内 弧 进 汽 侧 裂 纹渗透检测形貌
图 3 某 电 厂 #1 机 低 压 末 级 叶 片 横 截 面 进 汽 侧端部硬化区域
硬化区和正常母材区在组织和晶粒大小上有明显 的区别, 硬化区组织明显细小, 见图 4、图 5 所示
MATERIAL S CIENCE 材料科学
出磁粉探伤试片所能模拟的缺陷特征, 而叶片现场磁粉 检测一般采用黑磁粉便携式磁轭法检测, 无法满足检测 灵敏度要求, 故检测工艺应该重新考虑。因为现场叶片 无法拆卸, 而便携式磁粉检测设备不能满足要求, 所以 选 用 CJX6000 移 动 式 磁 粉 检 测 设 备 , 采 用 绕 电 缆 法 进 行磁化, 磁化电流采用交流电, 磁化电流根据缠绕圈数 和叶片宽度进行确定, 磁粉选用荧光磁粉, 记录采用临 摹草图法。
河南科技 2007.2 上
35
MATERIAL S CIENCE 材料科学
2Cr13 汽轮机叶片裂纹磁粉 检测工艺选择与应用
河南电力试验研究院 王朝华
一 、前 言 2004 年 起 , 某 汽 轮 机 厂 制 造 的 N135- 13.24 / 535 / 535 型 135MW 机组, 低压末级叶片频繁出现裂纹, 最严 重时正级末级 105 片叶片有 96 片存在裂纹, 个别裂纹 可以肉眼观察。汽轮机叶片为高速转动部件, 运行环境 和受力状况复杂, 是发电厂重要的金属监督对象。低压 末级叶片具有较大的体积和质量, 如果叶片断裂, 不仅 会损坏其它叶片, 还可能因为断叶片卡阻, 破坏转子的 动平衡, 导致轴系失稳, 成为重大事故的诱发因素。 二 、叶 片 裂 纹 特 点 这些机组投运时间均在 2003 年, 低压末级叶片发现 裂纹时间均为机组投运后第一次大修, 低压末级叶片, 正、反级均发现裂纹叶片( 正级较多) , 低压末级叶片裂 纹位于叶片进汽侧内弧面, 在距叶顶约 100~200mm 范围 内, 呈横向密集、平行分布, 裂纹长度(进汽至出汽侧方向) 约为 1~12mm, 低压末级叶片裂纹起始于叶片内弧面与 进汽侧端部拐角处, 沿内弧面向外弧面和出汽侧方向扩 展。在此种叶片检测时, 检测结果对比发现渗透检测对小 裂纹的检出率明显高于磁粉检测( 见图 1- 图 2) 。
汽轮机叶片叶身的无损检测

汽轮机叶片叶身的无损检测
徐茂琦
【期刊名称】《军民两用技术与产品》
【年(卷),期】2017(000)008
【摘要】运行中的汽轮机叶片往往由于叶片制造工艺不良,设计不科学,材料不符合要求等因素的影响造成叶片断裂事故的发生,严重威胁着汽轮机的运行安全.同时,工作在高温、高压蒸汽恶劣环境下的汽轮机叶片承受着高的离心力和复杂的激振力.如果叶身内部存在裂纹等缺陷,高速运行后就会出现机械性能差,极易导致大事故.因此,对叶片进行预防性检查是确保机组安全运行的重要手段.为了提高检测的准确性,许多单位做了大量的试验研究,形成了几种不同的检测方法,主要有:渗透探伤、磁粉探伤、超声波检测、金属磁记忆检测、涡流探伤等.无损检测技术对汽轮机的安全性与经济性具有重大的意义.本文概述了无损检测技术,阐述了汽轮机叶片叶身的无损检测技术.
【总页数】1页(P110)
【作者】徐茂琦
【作者单位】哈尔滨汽轮机厂有限责任公司,哈尔滨 150046
【正文语种】中文
【相关文献】
1.汽轮机叶片叶身超声导波检测技术研究 [J], 靳峰;汪毅;李世涛;张武能
2.汽轮机叶片叶身及围带的涡流检测 [J], 刘金秋;夏晓涛;冯翌轩;尚伟
3.汽轮机叶片叶身的无损检测 [J], 高荣刚
4.叶身裂纹对汽轮机叶片振动特性影响的研究 [J], 李兴华;关淳;关明臣;李宇峰;曹登庆;马义良
5.汽轮机叶片叶身的涡流检测 [J], 张华宇;魏晓壮;张鑫;谢凤芹;周彦龙
因版权原因,仅展示原文概要,查看原文内容请购买。
- 1、下载文档前请自行甄别文档内容的完整性,平台不提供额外的编辑、内容补充、找答案等附加服务。
- 2、"仅部分预览"的文档,不可在线预览部分如存在完整性等问题,可反馈申请退款(可完整预览的文档不适用该条件!)。
- 3、如文档侵犯您的权益,请联系客服反馈,我们会尽快为您处理(人工客服工作时间:9:00-18:30)。
压气机叶片磁粉探伤方法
1.范围
本标准规定了汽轮机叶片的湿法磁粉探伤。
本标准适用于检测叶片表面及近表面的裂纹、发纹及其他缺陷。
2 引用标准
下列标准所包含的条文,通过在本标准中引用而构成为本标准的条文。
本标准出版时,所示版本均
为有效。
所有标准都会被修订,使用本标准的各方应探讨使用下列标准最新版本的可能性。
G B / T 9 4 4 5 - 1 9 8 8 无损检测人员技术资格鉴定通则
G B / T 1 2 6 0 4 . 5 -1 9 9 0 无损检测术语磁粉检测
J B / T 8 2 9 0 - 1 9 9 8 磁粉探伤机
3 定义
本标准所用的术语定义符合 G B / T 1 2 6 0 4 . 5 中的有关规定
4 检测人员要求
4 . 1 磁粉检测人员应按 G B / T 9 4 4
5 规定取得技术资格证书
4 . 2 磁粉检测应由具有磁粉探伤I 级以上资格证书者进行磁粉探伤,由具有磁粉探伤I 级以上资格证
书者签发检测报告,以保证探伤结果的可靠性。
5 检测设备
5 . 1 叶片探伤用磁粉探伤机应符合J B / T 8 2 9 。
中的技术要求。
推荐采用固定式磁粉探伤机。
对被检
叶片,按本标准 8 . 1 - 8 . 7 的规定,该机应能产生足够强的磁场。
5 . 2 磁粉探伤机应安装周向磁化电流和纵向磁化安匝数等指示表,指示误差不得超过示值的上 5 写,每
年至少校准指示表一次。
5 . 3 具有何种方式的磁化装置,则应具有相应方式的退磁装置
5 . 4 磁粉撒布装置应包括储液箱及喷洒机构,储液箱应安装搅拌器。
5 . 5 应具有剩磁检查仪。
5 .
6 应安装照明灯,被检区域的光照度不得低于 3 5 0 I x
5 . 7 当采用荧光法检测时,在暗室内观察磁痕,暗室内其可见光照度应不大于 2 0 I x ,所使用的紫外线
灯在工件表面的紫外线强度应不低于 1 0 0 0 p W / c m ` , 紫外线波长应在0 . 3 2 ^ - 0 . 4 0 p m 范围内。
6 叶片的表面准备
6 . 1 被检叶片的表面应干燥、无污物和锈斑等。
6 . 2 被检叶片表面的表面粗造度 R a 最大允许值为 1 . 6 0 K m .
6 . 3 如果要对叶片进行表面处理( 如电镀、喷涂等) ,磁粉探伤应在表面处理前进行。
6 . 4 如果必须在表面处理后进行磁粉探伤,可由供需双方协商解决。
但用直接通电法时,须保证通电
触点处露出金属本底,确保通电良好
7 磁粉及其磁悬液
叶片磁粉探伤允许采用荧光磁粉或非荧光磁粉。
7 . 1 应选择与叶片表面有高反差色泽的非荧光磁粉
7 . 2 推荐使用的非荧光磁粉和荧光磁粉粒度为 4 5 f m ( 3 2 0目 ) 。
7 . 3 磁悬液浓度要求如下 :
7 . 3 . 1 新配制的磁悬液中非荧光磁粉的浓度应为 1 2 ^ - 2 5 g / L , 荧光磁粉的浓度为。
. 5 ^ - 2 . 0 g / 。
一
般磁悬液都应具备如下性能 ; 无刺激性气味,对皮肤无刺激性,在工作状态下磁悬液的运动乳度不高于
1 0 m m ' / s 。
水磁悬液对叶片表面应具有良好的润湿性,对叶片无腐蚀作用,磁粉分散性好油磁悬液
闪点不得低于 6 0 0 C .
7 . 3 . 2 在正常情况下,油磁悬液半月测定一次,水磁悬液一周测定一次。
当气候炎热干燥时,要适当增
加对水磁悬液的测定次数,在 1 0 0 m L 磁悬液抽样中,荧光磁粉的推荐沉淀容积值为。
1 - 0 . 5 m l - ,非
荧光磁粉的沉淀容积值为 L 2 ^ - 2 . 4 m l 。
7 . 3 . 3 磁悬液浓度一般采用梨形离心沉淀管测量沉淀容积值的方法来测定,对荧光磁悬液,使用管茎
1 m l的试管( 刻度 0 . 0 5 m L ) ,对非荧光磁悬液,使用管茎为 1 . 5 m L 的试管( 刻度。
1 M I , ) ,抽样前磁悬
液在循环系统中至少要流动 3 0 m i n ,以保证可能沉淀在液槽中筛网,侧壁和槽底的磁粉完全混合从
软管中或喷嘴取 1 0 0 m L 磁悬液,并使其沉淀 3 0 m i n ,沉淀在管底的容积值就是槽液中磁粉的浓度。
7 . 3 . 4 如果磁悬液浓度太低或太高,可加人适当的磁粉或载液,使其达到所要求的浓度。
7 . 3 . 5 如果沉淀的磁粉出现松散的团聚现象,而不是密实的磁粉层,则应作第二次取样测定,如果仍然
如此,说明磁粉可能已被磁化,应更换磁悬液。
7 . 4 推荐如下配方方法 :
7 . 4,水磁悬液: 水磁悬液是在水中加人磁粉、表面润湿剂、防锈剂、消饱剂直接配制而成。