涟钢炼钢、轧制生产工艺流程
炼钢生产工艺流程-概述说明以及解释

炼钢生产工艺流程-概述说明以及解释1.引言1.1 概述炼钢生产工艺流程是指钢铁制造过程中的一系列步骤和工艺,旨在将生铁转化为高品质的钢材。
这个过程通常包括炼铁和炼钢两个主要阶段。
炼铁是将铁矿石经过冶炼和还原等多个步骤,从中提取出生铁的过程。
生铁是含有较高碳含量的铁合金,一般还含有一些杂质,需要进行炼钢进一步提纯。
炼钢是在特定条件下,通过控制温度、压力、氧气流量等参数,对生铁进行加工和熔炼,以去除杂质并调整钢材的成分和性能。
炼钢生产工艺流程在各个钢铁企业和工厂可能存在差异,但通常包括以下几个关键步骤:配料、炼钢炉装料、炉前处理、溶解炼炉、精炼、铸钢、连铸以及后续的淬火、热处理和表面处理等工序。
在配料阶段,各种原材料,包括铁矿石、废钢、合金等,按照一定比例混合,以满足最终产品的技术要求。
接下来是炼钢炉装料,将配料装入炼钢炉中,并控制好加热和冶炼条件。
炉前处理是指在进入炼钢炉之前对原料进行预处理,以去除杂质和调整成分。
这一步通常包括破碎、磁选、筛分等物理处理和烧结、还原等化学处理。
溶解炼炉是炼钢的关键过程,原料在高温下熔化,各种杂质被氧化、还原或浮渣分离的方式去除。
精炼是对溶解炼炉的产物进行进一步处理,通过吹氧、渣化反应等技术手段,去除残余杂质,调整成分组成和温度。
接下来是铸钢阶段,将精炼后的钢液倒入连铸机中,通过结晶器冷却凝固,形成连续块或板。
这些块或板可用于制造各种钢材产品,如钢板、钢管、钢坯等。
炼钢生产工艺流程的最后几个过程是后续处理,包括淬火、热处理和表面处理。
通过这些工序,钢材的性能、硬度、韧性、耐腐蚀性等可以得到进一步改善和优化,以满足特定应用需求。
总的来说,炼钢生产工艺流程是一个复杂且关键的过程,需要合理的工序安排、严格的质量控制和先进的技术手段。
它不仅影响到钢材质量和性能,也对钢铁企业的生产效率和经济效益产生重大影响。
1.2 文章结构文章结构部分的内容应该是对整篇文章的组成部分进行简要介绍。
钢铁企业基本工艺作业流程

钢铁企业工艺步骤钢铁生产工艺步骤大致分为:选矿,烧结,焦化,炼铁,炼钢,连铸,轧钢等过程;辅助系统有:制氧/制氮,循环水系统,烟气除尘及煤气回收等。
原煤粉状含铁原料铁矿原料物料流线能源流线钢成品1选矿1.1工艺介绍选矿是冶炼前准备工作,从矿山开采下来矿石以后,首先需要将含铁、铜、铝、锰等金属元素高矿石甄选出来,为下一步冶炼活动做准备。
1.2工艺步骤选矿通常分为破碎、磨矿、选别三部分。
其中,破碎又分为:粗破、中破和细破;选别依方法不一样也可分为:磁选、重选、浮选等。
1.3原料原矿石。
1.4产物铁精矿。
1.5设备矿石破碎设备:颚式破碎机、锤式破碎机。
磨矿工艺设备:球磨机、螺旋分级机。
选别工艺设备:浮选机、磁选机。
2烧结2.1工艺介绍为了确保供给高炉铁矿石中铁含量均匀,而且确保高炉透气性,需要把选矿工艺产出铁精矿制成10-25mm块状原料。
铁矿粉造块现在关键有两种方法:烧结法和球团法。
铁矿粉造块目标:◆去除有害杂质,回收有益元素,保护环境;◆综合利用资源,扩大炼铁用原料种类;◆改善矿石冶金性能,适应高炉冶炼对铁矿石质量要求。
2.2工艺步骤2.2.1烧结法烧结是钢铁生产工艺中一个关键步骤,它是将铁矿粉、粉(无烟煤)和石灰、高炉炉尘、轧钢皮、钢渣按一定配比混匀。
经烧结而成有足够强度和粒度烧结矿可作为炼铁熟料。
烧结矿生产步骤:烧结料准备,配料和混合,烧结和产品处理。
精矿粉石灰石碎焦高炉灰结矿热烧结矿电2.2.2 球团法球团是把细磨铁精矿粉或其它含铁粉料添加少许添加剂混合后,在加水润湿条件下,经过造球机滚动成球,再经过干燥焙烧,固结成为含有一定强度和冶金性能球型含铁原料。
球团矿生产步骤:原料准备、配料、混合、造球、干燥和焙烧、冷却、成品和返矿处理铁精粉精矿粉膨润土电2.3原料含铁原料:含铁量较高、粒度<5mm矿粉,铁精矿,高炉炉尘,轧钢皮,钢渣等。
通常要求含铁原料品位高,成份稳定,杂质少。
熔剂:要求熔剂中有效CaO含量高,杂质少,成份稳定,含水3%左右,粒度小于3mm占90%以上。
钢厂的工艺流程
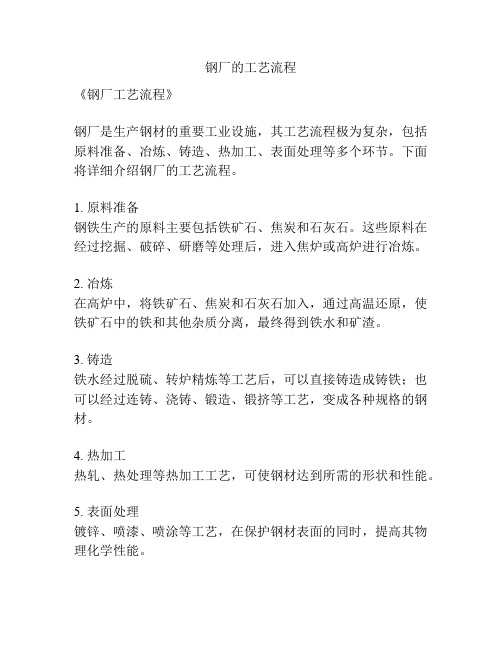
钢厂的工艺流程
《钢厂工艺流程》
钢厂是生产钢材的重要工业设施,其工艺流程极为复杂,包括原料准备、冶炼、铸造、热加工、表面处理等多个环节。
下面将详细介绍钢厂的工艺流程。
1. 原料准备
钢铁生产的原料主要包括铁矿石、焦炭和石灰石。
这些原料在经过挖掘、破碎、研磨等处理后,进入焦炉或高炉进行冶炼。
2. 冶炼
在高炉中,将铁矿石、焦炭和石灰石加入,通过高温还原,使铁矿石中的铁和其他杂质分离,最终得到铁水和矿渣。
3. 铸造
铁水经过脱硫、转炉精炼等工艺后,可以直接铸造成铸铁;也可以经过连铸、浇铸、锻造、锻挤等工艺,变成各种规格的钢材。
4. 热加工
热轧、热处理等热加工工艺,可使钢材达到所需的形状和性能。
5. 表面处理
镀锌、喷漆、喷涂等工艺,在保护钢材表面的同时,提高其物理化学性能。
以上就是钢厂的主要工艺流程,整个流程需要高度的自动化设备和严格的生产管理,以确保钢材的质量和生产效率。
随着技术的不断进步,钢厂的工艺流程也在不断完善,以满足市场对钢材品质和多样化需求。
炼钢生产流程详解

钢铁生产工艺要紧包括:炼铁、炼钢、轧钢等流程。
〔1〕炼铁:确实是基本把烧结矿和块矿中的铁复原出来的过程。
焦炭、烧结矿、块矿连同少量的石灰石、一起送进高炉中冶炼成液态生铁〔铁水〕,然后送往炼钢厂作为炼钢的原料。
〔2〕炼钢:是把原料〔铁水和废钢等〕里过多的碳及硫、磷等杂质往掉并参加适量的合金成分。
〔3〕连铸:将钢水经中间罐连续注进用水冷却的结晶器里,凝成坯壳后,从结晶器以稳定的速度拉出,再经喷水冷却,待全部凝固后,切成指定长度的连铸坯。
〔4〕轧钢:连铸出来的钢锭和连铸坯以热轧方式在不同的轧钢机轧制成各类钢材,形成产品。
炼钢工艺总流程图炼焦生产流程:炼焦作业是将焦煤经混合,破裂后参加炼焦炉内经干馏后产生热焦碳及粗焦炉气之制程。
烧结生产流程:烧结作业系将粉铁矿,各类助熔剂及细焦炭经由混拌、造粒后,经由布料系统参加烧结机,由点火炉点燃细焦炭,经由抽气风车抽风完成烧结反响,高热之烧结矿经破裂冷却、筛选后,送往高炉作为冶炼铁水之要紧原料。
高炉生产流程:高炉作业是将铁矿石、焦炭及助熔剂由高炉顶部参加炉内,再由炉下部鼓风嘴鼓进高温热风,产生复原气体,复原铁矿石,产生熔融铁水与熔渣之炼铁制程。
转炉生产流程:炼钢厂先将熔铣送前处理站作脱硫脱磷处理,经转炉吹炼后,再依订单钢种特性及品质需求,送二次精炼处理站(RH真空脱气处理站、LadleInjection盛桶吹射处理站、VOD真空吹氧脱碳处理站、STN搅拌站等)进行各种处理,调整钢液成份,最后送大钢胚及扁钢胚连续铸造机,浇铸成红热钢胚半成品,经检验、研磨或烧除外表缺陷,或直截了当送下游轧制成条钢、线材、钢板、钢卷及钢片等成品。
连铸生产流程:连续铸造作业乃是将钢液转变成钢胚之过程。
上游处理完成之钢液,以盛钢桶运送到转台,经由钢液分配器分成数股,分不注进特定外形之铸模内,开始冷却凝固成形,生成外为凝固壳、内为钢液之铸胚,接着铸胚被引拔到弧状铸道中,经二次冷却接着凝固到完全凝固。
钢厂工艺流程介绍

钢厂工艺流程介绍钢厂工艺流程是指将炼钢生产过程划分为不同的步骤,每个步骤都有特定的工艺流程,以确保生产过程的顺利进行和钢材质量的稳定。
钢厂工艺流程一般包括原料准备、炼钢工艺、炼钢设备和产品制造等环节。
首先是原料准备环节。
钢铁的主要原料是铁矿石、焦炭和石灰石。
在炼钢前需要对这些原料进行筛分、洗涤和质量检验等处理,以确保原料的质量和适用性。
其次是炼钢工艺环节。
炼钢工艺是指将铁矿石经过冶炼和还原等过程制得纯铁的方法和步骤。
传统的炼钢工艺包括高炉法、碱性炼钢法和电弧炉法等。
近年来,随着技术的进步,采用了先进的连铸、轧钢和热处理等工艺,以提高钢材的质量和生产效率。
炼钢工艺的选择主要取决于炼钢厂的规模、技术水平和经济性等因素。
然后是炼钢设备环节。
炼钢设备是指进行炼钢工艺的设备,包括高炉、转炉、电弧炉、连铸机和轧钢机等。
这些设备具有不同的功能和特点,可以满足不同工艺流程的需求。
例如,高炉是用于将铁矿石冶炼成铁水的设备,转炉是用于转炉法炼钢的设备,电弧炉是用于电弧炉法炼钢的设备,连铸机是用于将炼钢产生的铁水浇铸成坯料的设备,轧钢机是用于将坯料轧制成钢材的设备。
最后是产品制造环节。
产品制造是指将炼钢产生的坯料或热轧钢材进行加工、冷镦、锻打、热处理、表面处理和检验等过程,最终生产出符合规格和质量要求的钢材产品。
这些加工工序依次进行,每个工序都有特定的工艺流程和设备要求。
总之,钢厂工艺流程是炼钢生产过程中的重要环节,通过合理的工艺流程和先进的设备,可以确保钢材质量的稳定和生产效率的提高。
随着科技的进步,钢厂工艺流程也在不断完善和创新,以满足不断变化的市场需求。
涟钢实习报告

涟钢实习报告涟钢实习报告1一、实习目的通过自己的观察学习,对涟钢一炼轧厂和冷轧板厂车间的构造组成、生产线的布置、生产工艺流程和工艺参数有个初步了解。
在实习过程中培养自己调查研究,搜集、整理资料,分析问题和解决问题的能力。
二、实习内容1.一炼轧厂1.1工艺流程及主要设备与csp生产线匹配的转炉公称容量为100 t,钢水100%经过lf处理。
工艺流程如下:图1.1 工艺流程炉后主要设备及其特点如下。
lf:采用回转臂形式,设有钙处理(软吹氩)和精炼两个工位。
变压器额定容量18 mva,电极直径φ450mm,极心圆直径φ700mm。
精炼过程加料、吹氩、加热等采用数模控制。
连铸机:机型为立弯式,两铸机间距26 m。
铸坯厚度55~70 mm,设计拉速2.8~6.0m/min,铸机冶金长度9.705 m。
辊底式均热炉:位于摆动剪后,长度为291m,具有加热、均热、储坯(缓冲)、摆动过渡等功能。
采用低nox快速烧嘴,燃烧介质为混合煤气。
板坯入炉温度825~1060℃,出炉温度 1 150±10℃。
单坯长35.3~44.9 m;采用半无头轧制时,板坯长度可达269m(a线)。
精轧机组:由7架4辊不可逆轧机组成,轧制力f1~f2为44 000 kn,f3~f4为42 000kn,f5~f7为32 000 kn,主电机功率为10 000 kw。
层流冷却及卷取:高速飞剪用于半无头轧制,剪切力1 950 kn,带钢温度大于500℃,带钢速度约21m/s。
带钢冷却后经地下卷取机卷取,3个液压助卷辊,有自动踏步控制功能。
平整机:单机架4辊平整机,工作辊φ550~500mm,支撑辊φ1000~910mm。
热卷平整最大延伸率为3%,最大厚度为6.5mm,最大屈服强度为500mpa。
1.2采用的新技术涟钢csp生产线除采用了传统csp的成熟技术外,采用的新技术有电磁制动(embr)、等温结晶器冷却系统(iso)、液芯压下(lcr)、半无头轧制、动态变规格轧制(fgc)等。
钢材生产工艺流程
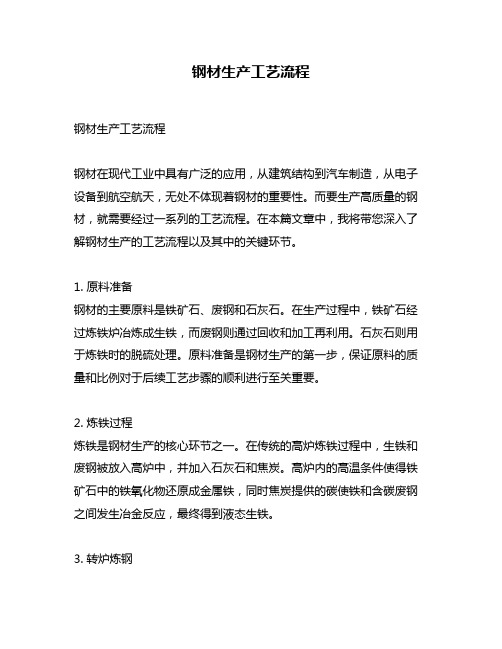
钢材生产工艺流程钢材生产工艺流程钢材在现代工业中具有广泛的应用,从建筑结构到汽车制造,从电子设备到航空航天,无处不体现着钢材的重要性。
而要生产高质量的钢材,就需要经过一系列的工艺流程。
在本篇文章中,我将带您深入了解钢材生产的工艺流程以及其中的关键环节。
1. 原料准备钢材的主要原料是铁矿石、废钢和石灰石。
在生产过程中,铁矿石经过炼铁炉冶炼成生铁,而废钢则通过回收和加工再利用。
石灰石则用于炼铁时的脱硫处理。
原料准备是钢材生产的第一步,保证原料的质量和比例对于后续工艺步骤的顺利进行至关重要。
2. 炼铁过程炼铁是钢材生产的核心环节之一。
在传统的高炉炼铁过程中,生铁和废钢被放入高炉中,并加入石灰石和焦炭。
高炉内的高温条件使得铁矿石中的铁氧化物还原成金属铁,同时焦炭提供的碳使铁和含碳废钢之间发生冶金反应,最终得到液态生铁。
3. 转炉炼钢转炉炼钢是一种常用的钢材生产工艺。
在这个过程中,将液态生铁转化为钢液。
转炉是一个类似于大锅的设备,可以容纳大量的液态金属。
炉内会注入氧气,使生铁中的碳等杂质被氧化和吹除,同时可以根据需要添加合金元素,以调整钢液的成分和性能。
这一过程通过反复地吹氧、冶炼和采样来进行,直到得到所需的钢液成分。
4. 连铸法浇铸连铸法是钢材成形的关键步骤之一。
通过连续浇注钢液,使其在冷却过程中逐渐凝固成坯料。
连铸机通常由一个铸模和一系列的冷却装置组成。
铸模内的钢液通过上升或下降的连续运动,经过一系列冷却水管的作用,形成钢坯。
连铸法能够高效地生产大量的钢坯,并拥有较好的外观和内部组织。
5. 热轧和冷轧经过连铸成型的钢坯可以通过热轧或冷轧工艺进行进一步加工。
热轧是将钢坯加热至高温,然后通过辊轧机械将其压制成所需的形状,如板材、型材等。
热轧工艺具有高效和快速的特点,但在成品表面质量和尺寸精度上有一定的限制。
冷轧则是将钢坯在室温下经过辊轧机械加工,可以获得更高的表面质量和尺寸精度。
冷轧还可以通过控制温度和轧制力度来调节钢材的力学性能。
涟钢炼钢、轧制生产工艺流程

涟钢炼钢、轧制生产工艺流程
七机架精轧机组具有 自动宽度控制、自动厚 度控制、自动平直度控 制、凸度控制技术,辊 缝润滑系统,可使带钢 尺寸精度达到国际先进 水平。
涟钢炼钢、轧制生产工艺流程
冷轧辊
涟钢炼钢、轧制生产工艺流程
五、涟钢概况与主要产品
一)、涟钢概况
中南地区重要精 品板材基地。
1、在华菱的布局
涟钢
湘钢
以专用板为主导的宽厚板。 以工业加工用材为主导的 线、棒材。
衡钢
涟钢炼钢、轧制生产工艺流程
系全球大型无缝钢管 生产企业,中国第二 大专业化无缝钢管生 产企业。
涟钢炼钢、轧制生产工艺流程
层流冷却
用途: 控制冷却速度,保证卷取
温度以确保产品质量和性能。
冷却带钢厚度: 1.2~25.4 mm
冷却带钢宽度:900~2130 mm
终轧温度: 870~900℃
卷取温度: 200~800℃
冷却水温度:
35℃
冷却段长度:超快冷段:9.12m
常规段:94.62 mm
冷却组数:
T403- 2超
HMD4-2 T404-2超 T405-2超
1 2 3 4 5 6 7 8 9 10 11 12 13 14 15
16 17 18
:超超超超超超
:超超超超超超 :超超超超超超
:超超超超超超超超超超 :超超超超 :超超
:超超超超 :超超超
图 1 轧后冷却系统设备布置图
涟钢炼钢、轧制生产工艺流程
总结钢铁产品工艺流程
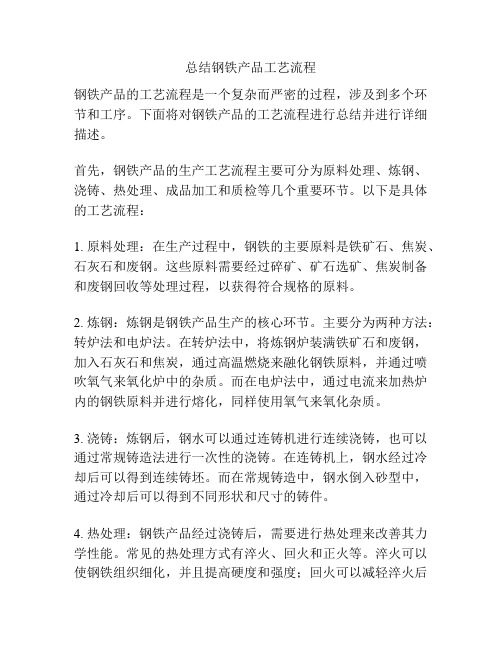
总结钢铁产品工艺流程钢铁产品的工艺流程是一个复杂而严密的过程,涉及到多个环节和工序。
下面将对钢铁产品的工艺流程进行总结并进行详细描述。
首先,钢铁产品的生产工艺流程主要可分为原料处理、炼钢、浇铸、热处理、成品加工和质检等几个重要环节。
以下是具体的工艺流程:1. 原料处理:在生产过程中,钢铁的主要原料是铁矿石、焦炭、石灰石和废钢。
这些原料需要经过碎矿、矿石选矿、焦炭制备和废钢回收等处理过程,以获得符合规格的原料。
2. 炼钢:炼钢是钢铁产品生产的核心环节。
主要分为两种方法:转炉法和电炉法。
在转炉法中,将炼钢炉装满铁矿石和废钢,加入石灰石和焦炭,通过高温燃烧来融化钢铁原料,并通过喷吹氧气来氧化炉中的杂质。
而在电炉法中,通过电流来加热炉内的钢铁原料并进行熔化,同样使用氧气来氧化杂质。
3. 浇铸:炼钢后,钢水可以通过连铸机进行连续浇铸,也可以通过常规铸造法进行一次性的浇铸。
在连铸机上,钢水经过冷却后可以得到连续铸坯。
而在常规铸造中,钢水倒入砂型中,通过冷却后可以得到不同形状和尺寸的铸件。
4. 热处理:钢铁产品经过浇铸后,需要进行热处理来改善其力学性能。
常见的热处理方式有淬火、回火和正火等。
淬火可以使钢铁组织细化,并且提高硬度和强度;回火可以减轻淬火后的脆性,提高韧性;正火可以消除淬火后的应力。
5. 成品加工:经过热处理的钢铁产品需要进行进一步的加工,例如锻造、轧制、切割、焊接和冲压等。
这些加工工序可以对钢铁产品进行形状和尺寸的调整,以满足不同的需求。
6. 质检:在整个工艺流程中,质检是一个必不可少的环节。
对钢铁产品的质量进行把关,确保其符合相关标准和要求。
常见的质检方法有化学分析、物理性能测试和外观检查等。
总结来说,钢铁产品的工艺流程包括原料处理、炼钢、浇铸、热处理、成品加工和质检等环节。
这些环节相互配合,一环扣一环,确保了钢铁产品的质量和性能。
每个环节都有严格的要求和控制,对于钢铁生产企业来说,需要科学合理地进行生产计划和管理,以提高产品质量和生产效率。
钢铁生产工艺流程(连铸之前部分)

钢铁生产工艺流程(连铸之前部分)钢铁生产工艺是一个复杂而庞大的系统,包括多个阶段和环节。
在连铸之前的部分,主要包括原料准备、炼钢和铸造等工序。
首先,原料准备是钢铁生产的第一步。
主要原料包括铁矿石、废钢和焦炭等。
先将铁矿石进行破碎和磨矿,得到粒度较小的矿石。
然后将矿石与焦炭、石灰石等混合,形成一定比例的炉料。
废钢也会被回收利用,通过磁选、焙烧等工序进行预处理,并与铁矿石混合。
接下来是炼钢过程。
炼钢有两种主要方法:基本氧化法(BOF)和电弧炉法。
在BOF法中,炉子先预热,然后加入预热过的废钢和矿石。
通过吹氧,氧与废钢反应生成氧化物,并产生大量的热量。
炉子内的氧气不断被吹入,从而将废钢中的杂质氧化,最终得到合格的钢水。
而在电弧炉法中,焦炭和废钢被放入电弧炉中,并通过电流产生的电弧进行加热,达到熔化的目的。
接下来是铸造过程。
将炼钢炉中获得的钢水倒入连铸机中,经过连铸机的结晶器冷却,形成一条长条形的坯料。
连铸是一种高效、连续的浇铸工艺,在这个阶段可以根据需要进行不同形状和尺寸的坯料生产。
通过连铸机的拉拔力和冷却水的喷射,使得钢水逐渐凝固并形成坯料。
在整个连铸之前的工序中,还伴随着一系列的辅助工作。
首先是钢水的取样分析,用来检测钢水的化学成分、温度等参数,以确保钢水质量符合要求。
同时,还要对连铸设备进行维护和保养,确保设备的正常运行。
此外,还有坯料的切割和打糙等处理,以及废水和废渣的处理,以保证生产环境的安全和卫生。
总结来说,钢铁生产工艺流程的连铸之前的部分主要包括原料准备、炼钢和铸造等工序。
在这些工序中,通过破碎、磨矿等步骤准备原料,然后通过炼钢过程将原料加热、熔化,最终得到合格的钢水。
接着通过连铸机将钢水冷却成坯料。
在整个过程中,还伴随着钢水的取样分析、设备的维护和保养,以及废水和废渣的处理等辅助工作。
这些工序紧密配合,共同完成钢铁生产的连铸之前阶段。
炼钢工艺流程中的19个工序,全了

炼钢工艺流程中的19个工序,全了1、造渣调整钢、铁生产中熔渣成分、碱度和粘度及其反应能力的操作。
目的是通过渣——金属反应炼出具有所要求成分和温度的金属。
例如氧气顶吹转炉造渣和吹氧操作是为了生成有足够流动性和碱度的熔渣,以便把硫、磷降到计划钢种的上限以下,并使吹氧时喷溅和溢渣的量减至最小。
2、出渣电弧炉炼钢时根据不同冶炼条件和目的在冶炼过程中所采取的放渣或扒渣操作。
如用单渣法冶炼时,氧化末期须扒氧化渣;用双渣法造还原渣时,原来的氧化渣必须彻底放出,以防回磷等。
3、熔池搅拌向金属熔池供应能量,使金属液和熔渣产生运动,以改善冶金反应的动力学条件。
熔池搅拌可藉助于气体、机械、电磁感应等方法来实现。
4、电炉吹风通过置于炉底的喷嘴将N2、Ar、CO2、CO、CH4、O2等气体根据工艺要求吹入炉内熔池以达到加速熔化,促进冶金反应过程的目的。
采用底吹工艺可缩短冶炼时间,降低电耗,改善脱磷、脱硫操作,提高钢中残锰量,提高金属和合金收得率。
并能使钢水成分、温度更均匀,从而改善钢质量,降低成本,提高生产率。
5、熔化期炼钢的熔化期主要是对平炉和电炉炼钢而言。
电弧炉炼钢从通电开始到炉料全部熔清为止、平炉炼钢从兑完铁水到炉料全部化完为止都称熔化期。
熔化期的任务是尽快将炉料熔化及升温,并造好熔化期的炉渣。
6、氧化期和脱碳期普通功率电弧炉炼钢的氧化期,通常指炉料溶清、取样分析到扒完氧化渣这一工艺阶段。
也有认为是从吹氧或加矿脱碳开始的。
氧化期的主要任务是氧化钢液中的碳、磷;去除气体及夹杂物;使钢液均匀加热升温。
脱碳是氧化期的一项重要操作工艺。
为了保证钢的纯净度,要求脱碳量大于0.2%左右。
随着炉外精炼技术的发展,电弧炉的氧化精炼大多移到钢包或精炼炉中进行。
7、精炼期炼钢过程通过造渣和其他方法把对钢的质量有害的一些元素和化合物,经化学反应选入气相或排、浮入渣中,使之从钢液中排除的工艺操作期。
8、还原期普通功率电弧炉炼钢操作中,通常把氧化末期扒渣完毕到出钢这段时间称为还原期。
涟钢BOF_LF_CSP工艺生产冷轧基料用板卷

涟钢BOF-LF-CSP工艺生产冷轧基料用板卷吴光亮1,3,郑柏平1,焦国华1,温德智1,康永林2,孙彦辉2(1. 涟源钢铁集团有限公司,湖南 娄底417009; 2.北京科技大学,北京100083; 3.钢铁研究总院,北京100081)摘要: 通过成分设计和工艺控制,利用高炉—转炉—LF炉—CSP连铸连轧工艺实现了CQ、DQ级冷轧冲压用热轧板卷的工业规模生产。
试验结果表明:钢水成分[C]、[Si]、[Als]、[N]、[O]、[S]的精确控制是该工艺生产冷轧冲压用钢的关键;B含量在0.003-0.007%范围内,可使板卷的屈服强度降低20-30MPa;CSP连铸采用轻压下工艺铸坯厚度从70mm降低到55mm,板卷屈服强度可降低30-45MPa;板坯的出炉温度升高可降低板卷屈服强度;在一定温度区间内,终轧温度和卷取温度升高,可降低板卷屈服强度。
关键词: BOF-LF-CSP工艺;冷轧用钢;热轧板卷Study on Producing Hot-Rolled Strip for Cold Rolling Using in BOF-LF-CSP of Lianyuan SteelWU Guang-liang1,ZHENG Bai-Ping1, JIAO Guo-hua1,WEN De-zhi1,KANG Yong-lin2, SUN Yan-hui2(1 Lianyuan Iron and steel Group Co.Ltd.Loudi Hunan 417009;2 University of Science and Technology Beijing.100083;3 Institute for Structural Materials of CISRI, Beijing 100081)Abstract: In order to produce cold rolling pressing steel in BOF-LF-CSP process, there is an attempt to design the component of steel and co n trol the process for producing cold rolling pressing steel on commercial size. The test results showed that the steel component [C] [Si] [Als] [N] [O] [S] accurate co n trolling is the key of producing cold rolling pressing steel using BOF-LF-CSP process. The yield strength reduced 20-30MPa when B content is 0.003-0.007%. The yield strength reduced 30-45MPa when the thickness of casting blank was reduced from 70mm to 55mm by liquid-core depress in CSP casting process. The yield strength reduced when heating the temperature of casting blank set up, and when finishing roll and batching the temperature set up in the scope.Key words: BOF-LF-CSP process;cold rolling using steel;hot roll bending1989年第一条薄板坯连铸连轧生产线在美国纽柯克拉兹维莱厂(Nucor Steel Corp. Craw fordsville)投产,给以“电炉+精炼+连铸+连轧”四位一体的“小钢厂”带来了无限生机,大幅度提升了该类钢厂的竞争能力,也为该技术在钢铁制造领域规模应用开辟了广阔的前景。
轧钢工艺流程(1)
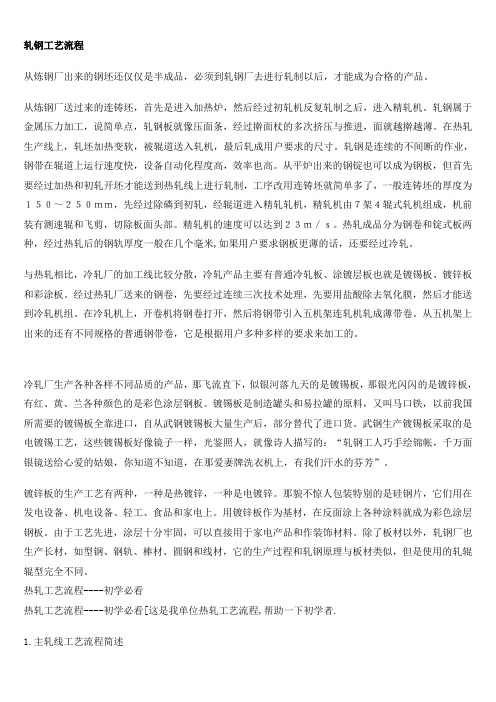
轧钢工艺流程从炼钢厂出来的钢坯还仅仅是半成品,必须到轧钢厂去进行轧制以后,才能成为合格的产品。
从炼钢厂送过来的连铸坯,首先是进入加热炉,然后经过初轧机反复轧制之后,进入精轧机。
轧钢属于金属压力加工,说简单点,轧钢板就像压面条,经过擀面杖的多次挤压与推进,面就越擀越薄。
在热轧生产线上,轧坯加热变软,被辊道送入轧机,最后轧成用户要求的尺寸。
轧钢是连续的不间断的作业,钢带在辊道上运行速度快,设备自动化程度高,效率也高。
从平炉出来的钢锭也可以成为钢板,但首先要经过加热和初轧开坯才能送到热轧线上进行轧制,工序改用连铸坯就简单多了,一般连铸坯的厚度为150~250mm,先经过除磷到初轧,经辊道进入精轧轧机,精轧机由7架4辊式轧机组成,机前装有测速辊和飞剪,切除板面头部。
精轧机的速度可以达到23m/s。
热轧成品分为钢卷和锭式板两种,经过热轧后的钢轨厚度一般在几个毫米,如果用户要求钢板更薄的话,还要经过冷轧。
与热轧相比,冷轧厂的加工线比较分散,冷轧产品主要有普通冷轧板、涂镀层板也就是镀锡板、镀锌板和彩涂板。
经过热轧厂送来的钢卷,先要经过连续三次技术处理,先要用盐酸除去氧化膜,然后才能送到冷轧机组。
在冷轧机上,开卷机将钢卷打开,然后将钢带引入五机架连轧机轧成薄带卷。
从五机架上出来的还有不同规格的普通钢带卷,它是根据用户多种多样的要求来加工的。
冷轧厂生产各种各样不同品质的产品,那飞流直下,似银河落九天的是镀锡板,那银光闪闪的是镀锌板,有红、黄、兰各种颜色的是彩色涂层钢板。
镀锡板是制造罐头和易拉罐的原料,又叫马口铁,以前我国所需要的镀锡板全靠进口,自从武钢镀锡板大量生产后,部分替代了进口货。
武钢生产镀锡板采取的是电镀锡工艺,这些镀锡板好像镜子一样,光鉴照人,就像诗人描写的:“轧钢工人巧手绘锦帐,千万面银镜送给心爱的姑娘,你知道不知道,在那爱妻牌洗衣机上,有我们汗水的芬芳”。
镀锌板的生产工艺有两种,一种是热镀锌,一种是电镀锌。
炼钢工艺流程.doc
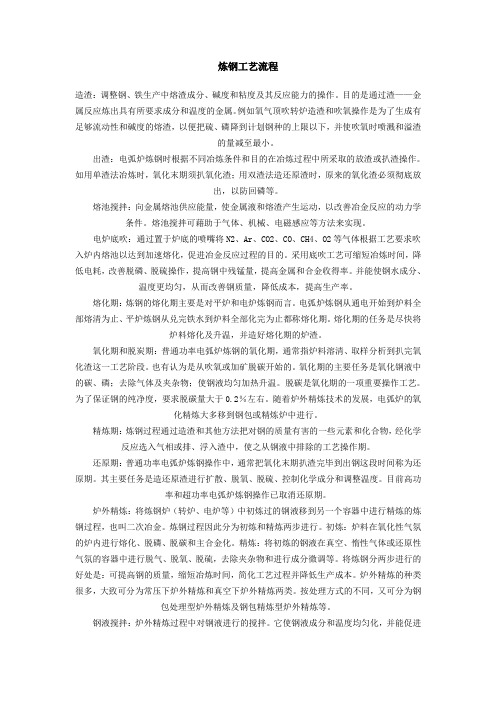
炼钢工艺流程造渣:调整钢、铁生产中熔渣成分、碱度和粘度及其反应能力的操作。
目的是通过渣——金属反应炼出具有所要求成分和温度的金属。
例如氧气顶吹转炉造渣和吹氧操作是为了生成有足够流动性和碱度的熔渣,以便把硫、磷降到计划钢种的上限以下,并使吹氧时喷溅和溢渣的量减至最小。
出渣:电弧炉炼钢时根据不同冶炼条件和目的在冶炼过程中所采取的放渣或扒渣操作。
如用单渣法冶炼时,氧化末期须扒氧化渣;用双渣法造还原渣时,原来的氧化渣必须彻底放出,以防回磷等。
熔池搅拌:向金属熔池供应能量,使金属液和熔渣产生运动,以改善冶金反应的动力学条件。
熔池搅拌可藉助于气体、机械、电磁感应等方法来实现。
电炉底吹:通过置于炉底的喷嘴将N2、Ar、CO2、CO、CH4、O2等气体根据工艺要求吹入炉内熔池以达到加速熔化,促进冶金反应过程的目的。
采用底吹工艺可缩短冶炼时间,降低电耗,改善脱磷、脱硫操作,提高钢中残锰量,提高金属和合金收得率。
并能使钢水成分、温度更均匀,从而改善钢质量,降低成本,提高生产率。
熔化期:炼钢的熔化期主要是对平炉和电炉炼钢而言。
电弧炉炼钢从通电开始到炉料全部熔清为止、平炉炼钢从兑完铁水到炉料全部化完为止都称熔化期。
熔化期的任务是尽快将炉料熔化及升温,并造好熔化期的炉渣。
氧化期和脱炭期:普通功率电弧炉炼钢的氧化期,通常指炉料溶清、取样分析到扒完氧化渣这一工艺阶段。
也有认为是从吹氧或加矿脱碳开始的。
氧化期的主要任务是氧化钢液中的碳、磷;去除气体及夹杂物;使钢液均匀加热升温。
脱碳是氧化期的一项重要操作工艺。
为了保证钢的纯净度,要求脱碳量大于0.2%左右。
随着炉外精炼技术的发展,电弧炉的氧化精炼大多移到钢包或精炼炉中进行。
精炼期:炼钢过程通过造渣和其他方法把对钢的质量有害的一些元素和化合物,经化学反应选入气相或排、浮入渣中,使之从钢液中排除的工艺操作期。
还原期:普通功率电弧炉炼钢操作中,通常把氧化末期扒渣完毕到出钢这段时间称为还原期。
轧钢工艺流程
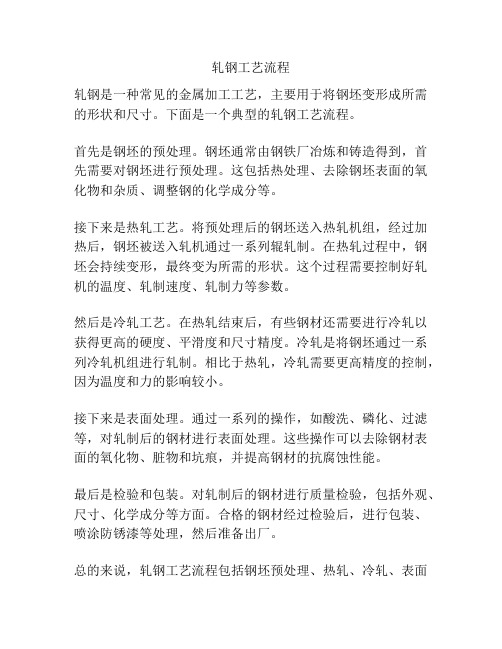
轧钢工艺流程
轧钢是一种常见的金属加工工艺,主要用于将钢坯变形成所需的形状和尺寸。
下面是一个典型的轧钢工艺流程。
首先是钢坯的预处理。
钢坯通常由钢铁厂冶炼和铸造得到,首先需要对钢坯进行预处理。
这包括热处理、去除钢坯表面的氧化物和杂质、调整钢的化学成分等。
接下来是热轧工艺。
将预处理后的钢坯送入热轧机组,经过加热后,钢坯被送入轧机通过一系列辊轧制。
在热轧过程中,钢坯会持续变形,最终变为所需的形状。
这个过程需要控制好轧机的温度、轧制速度、轧制力等参数。
然后是冷轧工艺。
在热轧结束后,有些钢材还需要进行冷轧以获得更高的硬度、平滑度和尺寸精度。
冷轧是将钢坯通过一系列冷轧机组进行轧制。
相比于热轧,冷轧需要更高精度的控制,因为温度和力的影响较小。
接下来是表面处理。
通过一系列的操作,如酸洗、磷化、过滤等,对轧制后的钢材进行表面处理。
这些操作可以去除钢材表面的氧化物、脏物和坑痕,并提高钢材的抗腐蚀性能。
最后是检验和包装。
对轧制后的钢材进行质量检验,包括外观、尺寸、化学成分等方面。
合格的钢材经过检验后,进行包装、喷涂防锈漆等处理,然后准备出厂。
总的来说,轧钢工艺流程包括钢坯预处理、热轧、冷轧、表面
处理、检验和包装等环节。
这些环节需要精确的控制和操作,以确保钢材具备所需的性能和质量,满足用户的要求。
同时,这也是一个能耗较高、环境污染较大的工艺,需注意环保措施的落实。
钢铁生产工艺流程
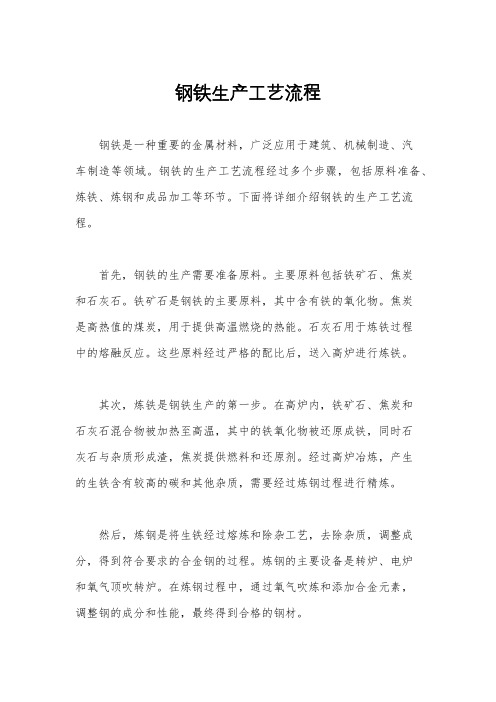
钢铁生产工艺流程钢铁是一种重要的金属材料,广泛应用于建筑、机械制造、汽车制造等领域。
钢铁的生产工艺流程经过多个步骤,包括原料准备、炼铁、炼钢和成品加工等环节。
下面将详细介绍钢铁的生产工艺流程。
首先,钢铁的生产需要准备原料。
主要原料包括铁矿石、焦炭和石灰石。
铁矿石是钢铁的主要原料,其中含有铁的氧化物。
焦炭是高热值的煤炭,用于提供高温燃烧的热能。
石灰石用于炼铁过程中的熔融反应。
这些原料经过严格的配比后,送入高炉进行炼铁。
其次,炼铁是钢铁生产的第一步。
在高炉内,铁矿石、焦炭和石灰石混合物被加热至高温,其中的铁氧化物被还原成铁,同时石灰石与杂质形成渣,焦炭提供燃料和还原剂。
经过高炉冶炼,产生的生铁含有较高的碳和其他杂质,需要经过炼钢过程进行精炼。
然后,炼钢是将生铁经过熔炼和除杂工艺,去除杂质,调整成分,得到符合要求的合金钢的过程。
炼钢的主要设备是转炉、电炉和氧气顶吹转炉。
在炼钢过程中,通过氧气吹炼和添加合金元素,调整钢的成分和性能,最终得到合格的钢材。
最后,成品加工是将炼钢后的钢坯进行轧制、锻造、拉拔等加工,得到各种规格的钢材和铁合金产品。
成品加工是钢铁生产的最后一个环节,也是直接面向市场和用户的环节,其质量和效率直接影响到钢铁企业的经济效益。
总的来说,钢铁的生产工艺流程包括原料准备、炼铁、炼钢和成品加工等环节,每个环节都有其特定的工艺和设备。
钢铁生产是一个复杂的系统工程,需要各个环节紧密配合,确保产品质量和生产效率。
随着技术的不断进步,钢铁生产工艺也在不断优化和改进,以适应市场的需求和环境的变化。
希望通过本文的介绍,能够让读者对钢铁生产工艺有更深入的了解。
轧钢生产工艺流程介绍

轧钢生产工艺流程介绍1、棒材生产线工艺流程钢坯验收→加热→轧制→倍尺剪切→冷却→剪切→检验→包装→计量→入库(1)钢坯验收〓钢坯质量是关系到成品质量的关键,必须经过检查验收。
①、钢坯验收程序包括:物卡核对、外形尺寸测量、表面质量检查、记录等。
②、钢坯验收依据钢坯技术标准和内控技术条件进行,不合格钢坯不得入炉。
(2)、钢坯加热钢坯加热是热轧生产工艺过程中的重要工序。
①、钢坯加热的目的钢坯加热的目的是提高钢的塑性,降低变形抗力,以便于轧制;正确的加热工艺,还可以消除或减轻钢坯内部组织缺陷。
钢的加热工艺与钢材质量、轧机产量、能量消耗、轧机寿命等各项技术经济指标有直接关系。
②、三段连续式加热炉所谓的三段即:预热段、加热段和均热段。
预热段的作用:利用加热烟气余热对钢坯进行预加热,以节约燃料。
(一般预加热到300~450℃)加热段的作用:对预加热钢坯再加温至1150~1250℃,它是加热炉的主要供热段,决定炉子的加热生产能力。
均热段的作用:减少钢坯内外温差及消除水冷滑道黑印,稳定均匀加热质量。
③、钢坯加热常见的几种缺陷a、过热钢坯在高温长时间加热时,极易产生过热现象。
钢坯产生过热现象主要表现在钢的组织晶粒过分长大变为粗晶组织,从而降低晶粒间的结合力,降低钢的可塑性。
过热钢在轧制时易产生拉裂,尤其边角部位。
轻微过热时钢材表面产生裂纹,影响钢材表面质量和力学性能。
为了避免产生过热缺陷,必须对加热温度和加热时间进行严格控制。
b、过烧钢坯在高温长时间加热会变成粗大的结晶组织,同时晶粒边界上的低熔点非金属化合物氧化而使结晶组织遭到破坏,使钢失去应有的强度和塑性,这种现象称为过烧。
过烧钢在轧制时会产生严重的破裂。
因此过烧是比过热更为严重的一种加热缺陷。
过烧钢除重新冶炼外无法挽救。
避免过烧的办法:合理控制加热温度和炉内氧化气氛,严格执行正确的加热制度和待轧制度,避免温度过高。
c、温度不均钢坯加热速度过快或轧制机时产量大于加热能力时易产生这种现象。
- 1、下载文档前请自行甄别文档内容的完整性,平台不提供额外的编辑、内容补充、找答案等附加服务。
- 2、"仅部分预览"的文档,不可在线预览部分如存在完整性等问题,可反馈申请退款(可完整预览的文档不适用该条件!)。
- 3、如文档侵犯您的权益,请联系客服反馈,我们会尽快为您处理(人工客服工作时间:9:00-18:30)。
四辊粗轧机
用途:与E立辊轧机一起经 5-7道次轧制。 型式:四辊可逆。 轧制压力:55000 KN 主电机功率:11000KW 轧制速度:0-3.25-6.5 m/s 最大压下量:50 mm 压下速度:0-40 mm/s 压下方式:电动APC+液压 HGC 工作辊尺寸: Ф1250/Ф1150×2250 mm 工作辊材质:高鉻钢 工作辊磨辊:可带箱磨辊
●钢板(或板带钢)按轧制温度分为热轧钢板和冷轧钢板;
按用途分为桥梁板、锅炉板、造船板、汽车板、电工板 ●钢板是应用最为广泛的钢材之一,用厚×宽来表示。
0.2~3mm的钢板称为薄板,热轧薄板(包括带钢)在工 业发达国家中已占钢板总量的80%左右,占钢材总产量 的50%以上,因而在现代轧钢生产中占有重要地位。
6、板材认证
序号 1 认证产品 管线钢 牌号 认证机构
X80及X80以下 国家质检总局 HP295 HP325 LGNS1
2 3
气瓶钢 耐硫酸露点腐蚀钢
国家质检总局 中国烟草总公司
4
船板用钢
A、B级
CCS
5
火车车厢板
09CuPCrNiA Q450NQR1
■ 型钢可分为大型材、中型材和小型材等。 接和镀层等钢材; 低合金钢等等;
■ 根据加工方式分为热轧材、冷轧、冷拔、 锻压、焊
■ 根据钢的材质或性能分为:优质钢、普通钢、合金钢、
■ 根据钢材的用途分为:造船板、锅炉板、油井管、油
气输送管、电工用钢等等。
三) 轧制的基本概念 ●轧钢是利用金属的塑性使金属在两个旋转的轧辊之间 受到压缩产生塑性变形,从而得到具有一定形状、尺寸和 性能的钢材的加工过程。 ●被轧制的金属叫轧件;使轧件实现塑性变形的机械设 备叫轧钢机;轧制后的成品叫钢材。 ●经加工变形后的金属中,随着温度的增加,其晶体组 织有出现重新改组为新晶粒的现象,称为金属的再结晶。 ●金属进行再结晶的最低温度称为金属的再结晶温度。 T再=(0.35-0.40)TM TM:金属的熔点,以绝对温度K表示。
七机架精轧机组具有 自动宽度控制、自动厚 度控制、自动平直度控
制、凸度控制技术,辊
缝润滑系统,可使带钢
尺寸精度达到国际先进
水平。
多功能仪
在精轧机F7出口,安装
有多功能仪,它能即时和
连续地测量中心 线、横截 面厚度、温度、剖面、宽 度、 边缘温降和热轧出口 时的板型。从测量得到的
一系列过程控制和质量保
打包机 打包机布置在步进梁 旁,采用两台双头全 自动有扣式打包机,
可针对不同钢种对打
包道次的不同要求而
实现打包过程。
四、冷轧工艺流程
退火
酸轧联机
冷轧卷
罩 式 炉
平整机
镀锌机组 冷轧硬卷
彩涂机组
板 卷 加 工 及 销 售
酸洗轧机联合机组
酸洗-轧机联合技术是世界上目前最先进的冷轧技术之一,自80
年代问世以来,国内外已建设的酸洗-轧机联合机组已达30余套之 多;我国已有5套(包括本钢1套、宝钢1420和1550冷轧各1套、鞍钢新 轧2套)机组正在运行,正在建设和改造的还有多套。二十年来的国 内外生产经验证明,这种一体化生产工艺与常规的串列式冷轧机或 无头轧制相比,具有工序简单、生产周期短、操作人员少、节约投 资、减少占地面积、产品质量好、成材率高等优点。 本机组引进日本三菱-日立公司技术,轧机压下控制采用直动式 伺服阀;工作辊和中间辊换辊通过换辊小车直接过跨在磨辊间装卸 轧辊;轧机主传动采用单传动;配有自动厚度控制AGC、液压焊缝 控制HGC、动态变规格控制FGC、自动板形控制ASC等。
取机(2台)---钢卷入库
涟 钢 热 轧 薄 板 生 产 线
立辊轧机
涟钢薄板坯连铸连轧生产线既采用了传统的CSP技
术,又采用了如等温结晶器冷却系统、结晶器电磁制动、
液芯压下、短流程控制技术、半无头轧制、动态变规格
技术、超快冷等目前最先进的CSP技术。
2、 一炼轧厂CSP线的特色 ★ 成功轧制出厚度仅0.78mm的世界最薄的热轧板卷,创 造了钢铁工业CSP生产线的奇迹;
热卷箱
中间坯厚度30-45mm 宽度:900-2130 mm
温度:900-1150℃
内径 Φ600-Φ650mm 外径Max.φ2150 mm
穿带速度: 3.5 m/s 最大卷曲速度: 6.5 m/s
最大开卷速度:2.5 m/s
钢卷质量:38 T
单位宽度卷重: Max.22 Kg/mm
切头飞剪 用途:切掉中间坯的头尾。 型式:转鼓式切头飞剪。 剪切带坯断面:50×2130mm(X70) 剪切温度:≥ 900℃ 剪切应力:140 N/mm2 剪切力:14700KN 剪刃布置型式:双剪刃90º 切头长度:≤500 m 主传动减速机速比:17.56 主传动电机: AC2 x 1600 Kw 600 r/min 3.5倍过载10秒。
酸轧机组布置图
主要工艺流程及设备
入口步进梁→双上开卷→直头机→双层切断剪→焊接→1#入口活 套→破鳞拉矫→浅槽紊流酸洗→漂洗→烘干→2#活套→剪边→3# 活套→事故剪→四机架6辊UCM冷轧→分断剪→卡伦塞卷取→卸卷 →打包→标识→钢卷运输
冷轧辊
五、涟钢概况与主要产品 一)、涟钢概况
中南地区重要精 品板材基地。
等;按表面特征分为镀锌板、镀锡板、涂塑板和复合板等。
二、CSP工艺流程(一炼轧厂) 1、主要工艺流程 薄板坯连铸连轧与传统热轧带钢生产工艺相比,具有 流程短、投资省、生产成本低和自动化程度高等优势。 它的主要工艺流程为: 100t转炉(3座)---105tLF(3座)---CSP连铸机(2台)---辊底 式均热炉(2座)---7机架精轧机组---层流冷却---地下卷
CCR HCR DHCR
热卷箱
辊道 二次高压水除鳞
保温坑
清理
精轧机组
加热炉
层流冷却
地下卷取机 高压水除鳞 打捆、打印、称重
粗轧机组
热轧钢卷库
直发卷 平整分卷线 热剪 热处理 横切线 至冷轧
外发
3、主体设备
蓄热式步进炉
粗轧除鳞机
用 途:除去板坯表面加热 过程中产生的一次氧化铁皮 喷嘴前水压力: 20 MPa 喷嘴与板坯角度:15° 喷嘴与板坯距离:130 mm 喷射有效宽度:2263.79 mm 集水管数量:2对 喷嘴数量:4×37个(喷嘴间 距61mm) 总流量:9501.6L/min 上喷嘴高度可调节
新入厂员工培训教材 (轧钢生产系统及生产品种) 目录 一、轧钢基础知识 二、CSP工艺系统流程(一炼轧厂) 三、2250热轧板工艺流程 四、冷轧工艺流程 五、钢概况及主要产品
一、轧钢的基础知识
一)轧钢生产工艺流程
二)轧制产品的种类、规格
■ 钢材根据断面形状,可以分为板、管、型、丝四大类。
■ 根据板带钢厚来分,有特厚板、中厚板、薄板;
●将金属加热到再结晶温度以上进行轧制叫热轧。
热轧的优点:可以消除加工硬化,能使金属的强度、
硬度、脆性降低,塑性和韧性增加,而易于加工; 缺点:高温下钢件表面易生成氧化铁皮,使产品表面粗 糙度增大、尺寸不够精确。 碳钢热轧温度一般在850-1200℃。
●金属在再结晶温度以下进行的轧制叫冷轧。
冷轧的优缺点与热轧相反。
立棍轧机
用途:与R四辊水平轧机一 起,经5-7道次轧制。 型式:吸附型、上传动式 (不可逆轧制)。 轧制温度:1150℃ 轧制压力:7000 KN 轧制速度:0-2.6-6.5m/s 开口度: 880 mm-2250 mm 最大压下量:单侧50 mm(厚 度230 mm) 侧压方式:全液压AWC 轧辊尺寸: Ф1200/Ф1100×650 mm 轧辊材质:锻钢辊
超快速冷却+常规层流冷却组合: 200~650℃; 常规层流冷却:450~650℃
超快速冷却 HMD1-1 T401-1 HMD1-2 T401-2 T402-1上 T402-2下
粗冷段
层流冷却 加密强化冷却段
精冷段 T403-1上 T403-2下 HMD4-1 T404-1高 T405-1低 HMD4-2 T404-2高 T405-2低
层流冷却
用途: 控制冷却速度,保证卷取 温度以确保产品质量和性能。 冷却带钢厚度: 1.2~25.4 mm 冷却带钢宽度:900~2130 mm 终轧温度: 卷取温度: 870~900℃ 200~800℃
冷却水温度: 35℃ 冷却段长度:超快冷段:9.12m
常规段:94.62 mm 冷却组数: 18组
如:30CrMo 、LGNS1、65Mn、LG600等 ◆管线用钢。 如:X60、X65等系列
工 作 辊 换 棍 机
Main drives(主驱动器)
Hydraulic looper(液压活套)
三/2250热轧板工艺流程 1、工艺流程图
2、产品流程图
连铸合格坯料 外购坯 切头飞剪 板坯库
冷却
车轮 用钢
冷成 形用 钢
门业 板
汽车 及家 电板
5、质量保证
公司已通过: ISO9001质量管理体系 IS010012计量管理体系 ISO/TS16949 汽车质量体系认证 ISO14001 环境管理体系 OSHMS18001 职业安全健康管 理体系认证 TS16949 汽车板体系认证
优化剪切系统现场设备位置
头尾形状分类和剪切原理
精轧除鳞机 精轧除鳞机用来清
除板坯上的二次氧化
铁皮,并将板坯送入 精轧机中。 精轧除鳞机高压水 压力为20MPa,前后
夹送辊辊缝可调。
精轧前。
轧制压力为 1500 KN,
单侧压下量为5 mm , 主传动电机为AC370 W2台。
★ 半无头轧制技术的工业化、批量化应用;
★ 钛板的多次成功轧制;
★ 薄规格(h≤2.0)批量化生产。
3、生产的主要产品 ◆ 建筑、桥梁、车辆、船舶用结构钢; 如:Q235,Q345,LG510L,16MnL等