万吨直馏柴油加氢精制装置简介
直馏柴油加氢装置掺炼催化柴油的技术改进
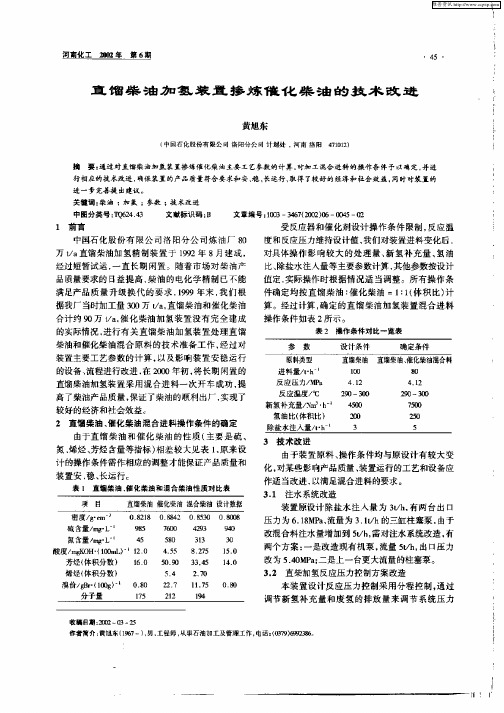
据我厂当时加工量 30 0 万 a直馏柴油和催化柴油 , 合计约 9 万 a催 化柴油加氢装置没有完全建成 0 , 的实 际情 况 , 进行 有 关 直馏 柴油 加氢 装 置处 理直 馏 柴油和催化柴油混合原料的技术准备工作, 经过对
算。经过计算 , 确定的直馏柴油加氢装置混合进料 操作条件如表 2 所示。 表2 操作条件对比一览表 参 数 设 计条 件
1 0 0
确定条 件
装置主要工艺参数的计算, 以及影响装置安稳运行
的设备 、 流程进行改 进 , 20 在 00年初 , 长期 闲置 的 将
——
面———
溴价 g ‘ 0 ) B ( 0 r1g
08 . 2 7 1. 08 0 2 15 7 - 0
本装置设计反应压力控制采用分程控制 2 ( 0 —2 /
!
调节 新氢补充量和废氢的排放量来调节系统压力
作者简介 : 黄旭东( 6 一 , 工程师 . 1 7 ) 男, 9 从事石油加工及管理工作 . 电话 : 3969 3 。 ( 7 ) ". 0 9zm
维普资讯
河 南化 工
抛
年
第 6期
直 馏 柴 油 加 氢 装 置 掺 炼 催 化 柴 油 的 技 术 改 进
黄旭东
( 中国石化股份有 限公司 洛阳分公 司 计划处 , 河南 洛阳 4 11) 702
摘
要: 通过对直馏柴 油加氢装 置掺炼催化 柴油主要 工艺参数的计算 , 对加工混合进料的操作条件 子烈璃定 , 井进
“ 边收边 放” 的方法 ; 为保证 反应 压力控 制平稳 , 调节 及时 , 分程控制 为单 回路 控制 ( 图 2 , 改 见 )将更 加灵
加氢装置介绍

加氢裂化装置原理、流程及特点
加氢裂化是将大分子的重质油转化为广泛使用的小分子 的轻质油的一种加工手段。可加工直馏柴油、催化裂化循环 油、焦化馏出油,也可用脱沥青重残油生产汽油、航煤和低 凝固点柴油。加氢裂化装臵是炼油厂最重要的的生产装臵之 一,在高温、高压、临氢状态下操作。 加氢裂化装臵的工艺流程主要有三种类型方法: ⑴ 一次通过法:所产尾油不参加循环。 ⑵ 部分循环法:所产尾油一部分参加循环,一部分排出 装臵。 ⑶ 全部循环法:所产尾油全部参加循环,不排尾油。 加氢裂化装臵主要设备有加氢精制反应器、加氢裂化反 应器、加热炉、高压热交换器、高压空冷器、高、低压分离 器、高温高压临氢管道、高温阀门等。详见图1、图2、图3、 图4。
2013-8-17 12
H1
H2
H3
凸台
H4
H5
s-k H6
1
图5
2013-8-17
热壁加氢反应器
13
加氢裂化装置常用材料
设备名称
加氢精制、裂化反应器 (设计温度≤ 450 ℃/设 计压力8~20MPa) 高压热交换器(温度≤ 260 ℃)
选用材质
板2.25Cr-1Mo(SA387Gr22CL2) +6.5mm(Tp309+347) 堆焊层 或+4mm(TP347)单层浅熔深堆焊 锻2.25Cr-1Mo(SA336F22CL2) + 6.5mm(Tp309+347) 堆焊层或+4mm(TP347)单层浅熔深堆焊 管程:反应流出物:管箱(碳钢、碳钼钢+4~6mm CA;铬钼钢+3mm CA)管板(碳钢、碳钼钢、铬钼钢 + 8mmTP309+347) 壳程:循环氢、原料:壳体(碳钢、碳钼钢、铬钼 钢+ 3mm CA) 管程:反应流出物:管箱(铬钼钢+3mm 1Cr18Ni9Ti 复合板 或 +6.5mm Tp309+347堆焊层 或 +4mmTP347) 管板(铬钼钢+8mmTP309+347或铬 钼钢+8mmTP410) 壳程:循环氢、原料:壳体(铬钼钢+4mm CA;或 +3mm 1Cr18Ni9Ti 复合板;或+4mmTP347;或 +6.5mm Tp309+347堆焊层) 14
辽化装置介绍
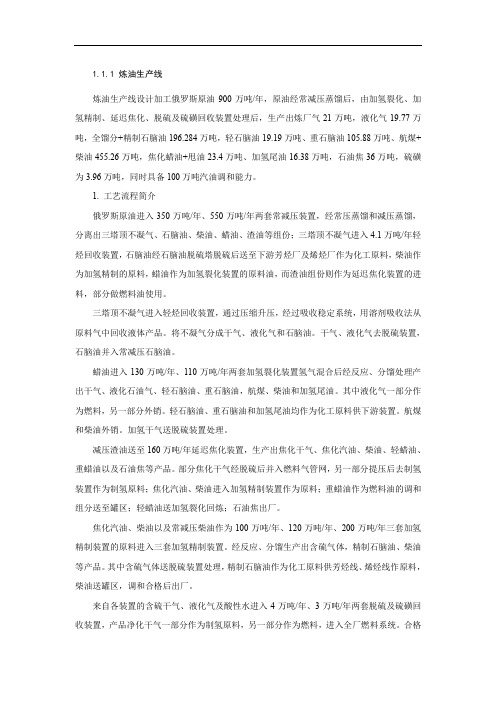
1.1.1 炼油生产线炼油生产线设计加工俄罗斯原油900万吨/年,原油经常减压蒸馏后,由加氢裂化、加氢精制、延迟焦化、脱硫及硫磺回收装置处理后,生产出炼厂气21万吨,液化气19.77万吨,全馏分+精制石脑油196.284万吨,轻石脑油19.19万吨、重石脑油105.88万吨、航煤+柴油455.26万吨,焦化蜡油+甩油23.4万吨、加氢尾油16.38万吨,石油焦36万吨,硫磺为3.96万吨,同时具备100万吨汽油调和能力。
1. 工艺流程简介俄罗斯原油进入350万吨/年、550万吨/年两套常减压装置,经常压蒸馏和减压蒸馏,分离出三塔顶不凝气、石脑油、柴油、蜡油、渣油等组份;三塔顶不凝气进入4.1万吨/年轻烃回收装置,石脑油经石脑油脱硫塔脱硫后送至下游芳烃厂及烯烃厂作为化工原料,柴油作为加氢精制的原料,蜡油作为加氢裂化装置的原料油,而渣油组份则作为延迟焦化装置的进料,部分做燃料油使用。
三塔顶不凝气进入轻烃回收装置,通过压缩升压,经过吸收稳定系统,用溶剂吸收法从原料气中回收液体产品。
将不凝气分成干气、液化气和石脑油。
干气、液化气去脱硫装置,石脑油并入常减压石脑油。
蜡油进入130万吨/年、110万吨/年两套加氢裂化装置氢气混合后经反应、分馏处理产出干气、液化石油气、轻石脑油、重石脑油,航煤、柴油和加氢尾油。
其中液化气一部分作为燃料,另一部分外销。
轻石脑油、重石脑油和加氢尾油均作为化工原料供下游装置。
航煤和柴油外销。
加氢干气送脱硫装置处理。
减压渣油送至160万吨/年延迟焦化装置,生产出焦化干气、焦化汽油、柴油、轻蜡油、重蜡油以及石油焦等产品。
部分焦化干气经脱硫后并入燃料气管网,另一部分提压后去制氢装置作为制氢原料;焦化汽油、柴油进入加氢精制装置作为原料;重蜡油作为燃料油的调和组分送至罐区;轻蜡油送加氢裂化回炼;石油焦出厂。
焦化汽油、柴油以及常减压柴油作为100万吨/年、120万吨/年、200万吨/年三套加氢精制装置的原料进入三套加氢精制装置。
1.2Mt/a柴油加氢装置开工及运行分析
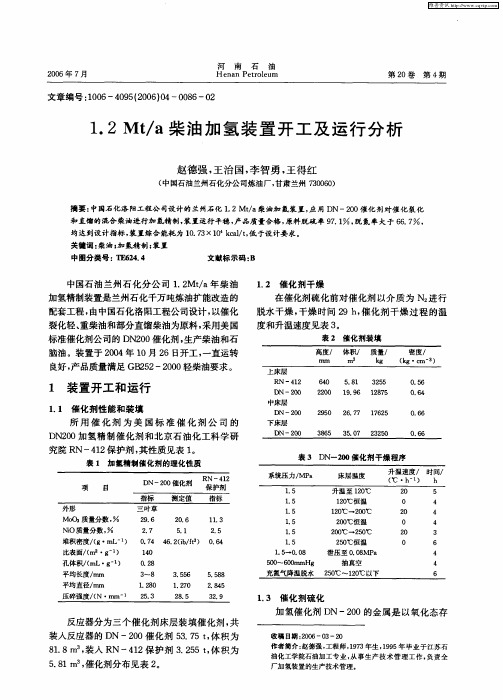
系统存 硫/ g l 【
上硫率 ,
由表 5可见上硫率达 9 . 1 , 8 6 满足加氢催 化 剂 的流化 要求 。
表 8 原 料和产品性质 ( 第二次标定 )
2 装置运行和标定
2 1 装置 运行 .
装置 20 0 4年 1 0月 2 日开 工 , 2 0 6 到 0 6年 2 月底已累计加工量达到 16 23 1t其 中加工催 5 7 , 化柴 油 10 010t直 馏柴 油 5 0 1t焦 化柴 油 2 3 、 88 7 、
o2 .8
3 ~8 12 0 .8
356 .5 120 .7 2. 85 558 . 8 285 . 4 3 9 2.
压碎强度/ N ・ 2 一 ( n l1 n 2 . Βιβλιοθήκη 31 3 催化 剂硫化 .
加氢催化剂 D N一 0 2 0的金 属是 以氧化态存 反应器分为三个催化剂床层装填催化剂 , 共 装入反应器的 D N一20催化剂 5. 5t体积为 0 3 7 , 8 . 。装入 R 18m , N一42保护剂 3 25t体积为 1 . 5 ,
1 2 催 化剂 干燥 .
在催化剂硫化前对催化剂 以介质 为 N 进行 2 脱水 干燥 , 干燥时间 2 , 9h 催化剂干燥过程 的温 度和升温速度见表 3 。
表 2 催化剂装填
良好 , 品质量满足 G 2 2 0 0 产 B 5 —20 轻柴油要求 。
1 装置 开工和 运行
1 1 催化剂性能和装填 .
4 7 。每千克催化剂处理原料 3 .4t 410t 07 。
2 2 装 置标定 结果 .
20 05年 4月 7日至 1 0日对装置 进行 了标 定, 标定的原料为 8 的催化裂化柴油和 2 的 0 0
汽柴油加制氢介绍.ppt
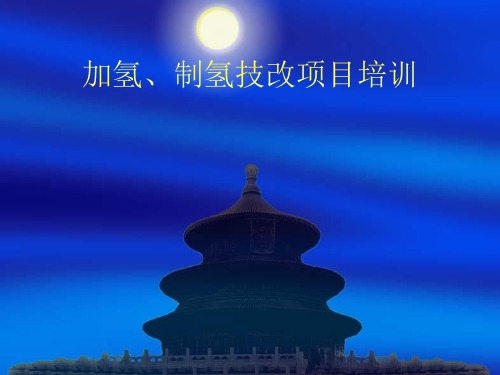
2) 产品氢气压力
≥2.4 MPa.G
3) 产品氢温度
≤40 ℃
4) PSA部分解吸气排气压力
≥0.03 MPa
5) PSA部分氢气回收率(设计值) ≥83 %
3、30万吨/年催化汽油加氢装置 该装置设计点为28.80万吨/年催化汽油,最大加工量为36万吨/年,最小加工量为20
万吨/年。装置主要原料为催化汽油,其主要性质为 :
产品设计目标为: 1) 加氢后汽油产品硫含量<150PPm(主要由专利商保证)。 2) 加氢处理RON损失≯1.5个单位(主要由专利商保证)。 3) 重汽油加氢单元C5+以上液体收率>99.6 m %。 三套装置与一期项目装置共用一套公用工程,并在此基础上新增2台1000m3原料调合罐, 以保证装置进料的平稳性;新上10000m3气柜一台,以缓解火炬系统的压力,并能达到合 理利用装置废气的目的。
该装置设计点为38.56万吨/年,其中直馏柴油、催化柴油、直馏汽油的比例分别为 57.05%、35.17%、7.78%,最大加工量为46万吨/年,最小加工量为26万吨/年。装置原 料主要性质为:
装置产品设计目标为:
1) 精制柴油硫含量: 2) 精制汽油(石脑油)干点: 3) 精制柴油闪点:
≤350ppm ≤200℃ ≥55℃
2 、生产流程简述 1) 生产流程简述 ①反应部分
自罐区来的原料油,按预期的原料比例,首先进入原料调合罐进行调和,然
后在原料油缓冲罐(V3001)液面和流量控制下混合,经原料油脱水器 (SW3001)脱水(保证原料水含量低于350ppm),再通过原料油过滤器(FI3001) 滤去原料中大于25微米的颗粒,然后进入原料油缓冲罐(V3001)。原料油缓冲 罐采用燃料气进行保护。来自原料油缓冲罐(V3001)的原料油经加氢进料泵 (P3001A,B)增压至9.2MPa(G),在流量控制下,经反应流出物/原料油换热器 (E3003A,B)换热后,与混合氢混合进入反应流出物/反应进料换热器(E3001A、B、 C),然后经反应进料加热炉(F3001)加热至反应所需温度,进入加氢精制反应 器(R3001)。该反应器设置三个催化剂床层,床层间设有注急冷氢设施。来自 加氢精制反应器(R3001)的反应流出物,经反应流出物/反应进料换热器 (E3001A、B)、反应流出物/低分油换热器(E3002)、反应流出物/反应进料 换热器(E3001C)、反应流出物/原料油换热器(E3003A、B)依次与反应进料、 低分油、原料油换热,然后经反应流出物空冷器(A3001)冷却至50℃,最后经 反应流出物水冷器(E3011)冷却至45℃进入高压分离器(V3002)。为了防止 反应流出物中的铵盐在低温部位析出,通过注水泵(P3002A、B)将除盐水注至 反应流出物空冷器(A3001)上游侧的管道中。
柴油加氢装置
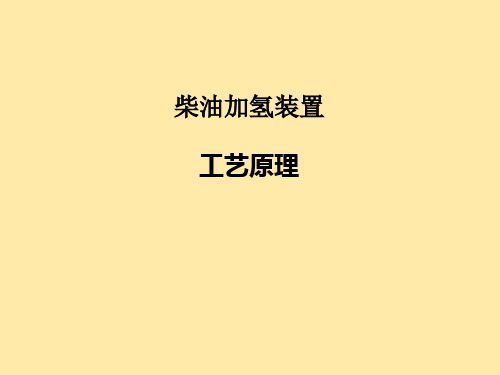
精制反应器内发生的反应
含硫有机物
催化剂
H2
烃类
含氮有机物
H2
催化剂
烃类
含氧有机物
H2
催化剂
烃类
金属有机物
H2
催化剂
烃类
烯烃
催化剂
H2
烷烃
H2S NH3 H2O 金属单质
与重整精制反应不同有:烃类碳数不同,杂质含量不同。 与重整精制反应相同有:均为放热反应,体积缩小反应。
低 分 罐
精制油去分馏塔 污水
在改质反应器内发生的主要反应第1、2步反应,
十六烷值为零
十六烷值约20以上
非柴油组分
想避免第3步反应的发生,就要控制好反应深度,即反应 温度、反应压力、反应空速、氢油比等。
新氢 原料泵
柴油加氢精制装置反应系统工艺流程
循环氢压缩机 冷却器
排放氢
加热炉
1
2
高
低分气
分
罐
低
高 分 罐
污水
冷氢
低分气
低 分 罐
精制油去分馏塔 污水
高分罐分离的是油、水、氢气三相的。
新氢 原料泵
柴油加氢精制装置反应系统工艺流程
循环氢压缩机 冷却器
排放氢
加热炉
1
2
高
低分气
分
罐
低
污水
分 罐
精制反应器
改质反应器
冷氢
精制油去分馏塔 污水
排除的污水中,含有H2S、NH3,这是物 理方法第一次脱除S、N、O元素。
催化剂
烯烃
催化剂
H2
烃类 烃类 烃类 烃类 烷烃
柴油加氢装置(汽柴油生产技术课件)
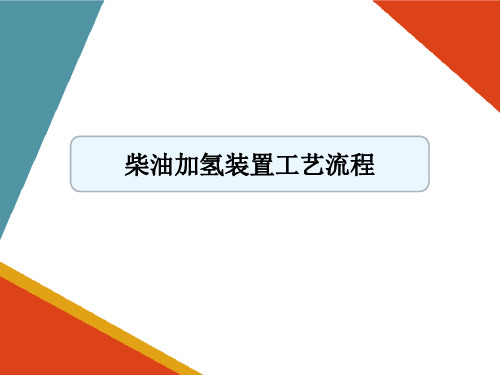
高分罐
LIC 排污
循环氢
LI 低分罐
图5—9 高分罐液位控制示意图
高分罐液位是油相液面高度。偏
高油相和气相分离效果将下降,偏低易形 成高压串低压导致分馏塔操作紊乱。
高分罐界位是水相与油相的界面
高度。偏高油带水,偏低水带油。
高分罐液位的影响因素:
1、高分罐与低分罐压差变化; 2、原料泵出口流量变化; 3、高分罐温度变化。
精制柴油十六烷值偏低,说明反应没有达到部分达到了第2步反应, 也即反应深度不够工艺要求。
1、反应温度偏低; 2、反应压力偏低;
3、催化剂活性偏低; 4、空速偏大。
1、塔顶压力偏 低; 2、塔顶温度偏 高;
精制油从低分罐来 原料泵
回流罐 粗汽油
分 馏 塔
粗汽油干点偏高?
柴油出装置
塔底的轻组分没有气化 上升到塔顶:
低分气
高
分
罐
低
分
分
馏
罐
塔
图5—10 低分罐压力控制示意图
低分罐的作用,一是分担些分馏塔
顶负荷,再是环节高压直接到低压而导致 分离塔的操作紊乱。
低分罐压力的影响因素:
1、高分罐压力变化; 2、分馏塔压力变化; 3、低分罐顶气体出口流量变化; 4、低分罐出口换热器的压降变化。
低分气
从高分罐来 低分罐
石脑油去催化重整装置
分
馏
塔
精制柴油溴价不合格的原
因?
柴油出装置
精制油从低分罐来 原料泵
回流罐
石脑油去催化重整装置
分馏Βιβλιοθήκη 塔精制柴油硫含量超标?
柴油出装置
循环氢压缩机
2、高分罐排污力度 不够工艺要求
新氢
柴油加氢技术总结

柴油加氢技术总结2#柴油加氢装置开工总结宋火军1.开工前的准备1.1 学习装置理论知识生产低硫、低芳烃、低密度、高十六烷值得清洁柴油是今后世界范围内的柴油生产总趋势。
如何满足符合日趋苛刻的车用柴油标准,生产出符合环保要求的清洁柴油将成为炼油技术进步的一个重要课题。
柴油燃料质量升级的趋势与汽油类似,最主要的是对于硫含量的控制,同时对于柴油产品指标中的十六烷值、芳烃含量、冷流动性、密度等也提出了更为严格的要求。
二次加工的柴油含有相当多的硫、氮及烯烃类物质,油品质量差,安定性不好,储存过程容易变质,对直馏柴油而言,由于原油中硫含量升高,环保法规日趋严格,已经不能直接作为产品出厂,也需要经过加氢精制处理。
柴油加氢精制的生产原理就是在一定温度、压力、氢油比、空速条件下,借助加氢精制催化剂的作用,有效的使油品中的硫、氮、氧、非烃类化合物转化为响应的烃类和H2S、NH3和H2O。
另外,少量的重金属则截留在催化剂中,同时使烯烃和部分芳烃饱和,从而得到安定性、燃烧性、情节性都较好的优质柴油产品和粗汽油(裂解料)。
本装置中大量循环氢的存在能保证气相为连续相,液相为分散相,被气相打散的液相在固定床催化剂上从上至下以液滴的形态流过催化剂床层,从而发生一系列的加氢反应。
循环氢在其中的关键作用是:(1)维持反应所需的氢分压,用来维系气相中的氢气向油相溶解的推动力。
(2)控制催化剂床层的温升。
(3)稀释反应物流杂质的浓度,促进深度脱杂质的反应。
1.2 学习开工方案在开工前两个月,车间开始组织操作人员学习开工方案,让每个人对开工都心里有数,了解每一个步骤,提高了操作人员的操作水平,为这次成功的开工打下了基础。
1.3 联系调度,提供合格氮气,在系统催化剂干燥时能满足供应。
1.4 硫化剂与试车用直馏柴油准备充足。
2.催化剂干燥催化剂在包装、储运和装填中,都难免吸附一定水分,吸附水会降低催化剂的活性和强度。
因此催化剂要在预硫化前进行脱水。
制氢装置简介
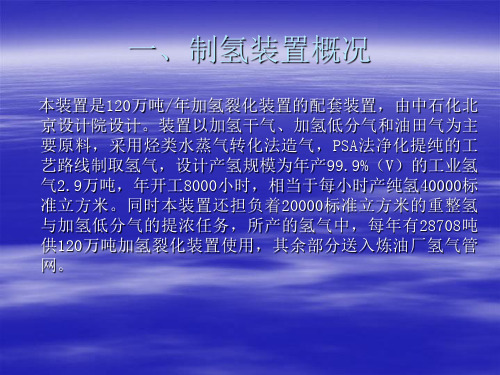
中压蒸汽
锅炉给水、发生并 过热蒸汽部分
中变冷 却分液
制氢PSA 部分
中压蒸 汽外送
低分气湿法 脱硫部分
重整氢 PSA
氢气
十、制氢工艺流程简述(一)
自装置外来的50℃,2.2MPa(G)的加氢裂化低分气 进入加氢裂化低分气冷却器(E-1102)壳层冷却后, 进入加氢低分气分液罐(D-1102)分液,从加氢低 分气脱硫塔(C-1102)底进入,在塔中与来自硫磺 回 收 装 置 的 甲 基 二 乙 醇 胺 ( MDEA ) 贫 液 逆 流 接 触 (MDEA浓度25%wt),脱除气体中的硫化氢,脱硫后 的低分气送本装置中重整氢提浓PSA单元,MDEA溶液 送回硫磺回收装置再生。
水蒸汽 合计
公斤/小时 5937.50 5952.97 43800.00 55690.47
吨/日 142.50 142.87 1051.20 1336.57
万吨/年 4.75 4.76 35.04 44.55
工业氢
3628.46 87.08 2.90
出
PSA尾气
27941.00 670.58 22.35
十五、制氢工艺流程简述(六)
自中变反应器出来的变换气依次经过中变气/原料气换热器 (E-1201)温度降至367℃和中变气/脱氧水换热器(E1202A/B)温度降至156.5℃后,进入中变气第一分液罐(D1203)分出凝液,然后在中变气除盐水换热器(E-1203)与 除盐水换热到137.8℃后进入中变气第二分液罐(D-1204), 分出凝液后,进入中变气空冷器(A-1201)冷却到60℃,再 经中变气第三分液罐(D-1205)分液后,进入中变气水冷器 (E-1204),水冷到40℃的中变气经中变气第四分液罐(D1206)分液后进入中变气PSA提纯单元。
柴油加氢装置节能降耗设备方面措施
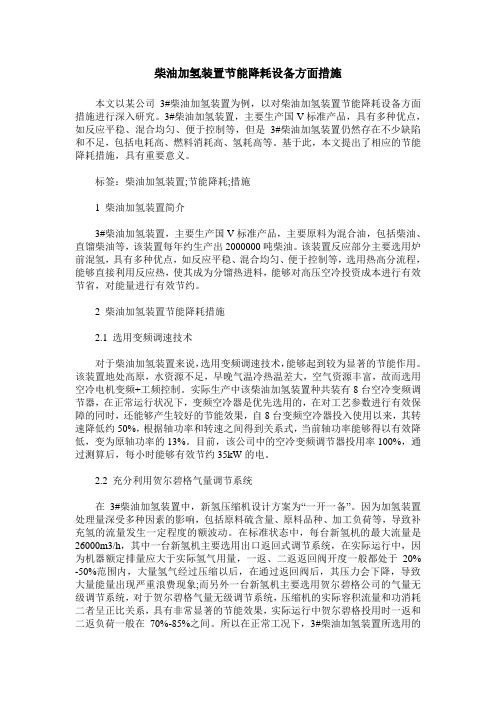
柴油加氢装置节能降耗设备方面措施本文以某公司3#柴油加氢装置为例,以对柴油加氢装置节能降耗设备方面措施进行深入研究。
3#柴油加氢装置,主要生产国V标准产品,具有多种优点,如反应平稳、混合均匀、便于控制等,但是3#柴油加氢装置仍然存在不少缺陷和不足,包括电耗高、燃料消耗高、氢耗高等。
基于此,本文提出了相应的节能降耗措施,具有重要意义。
标签:柴油加氢装置;节能降耗;措施1 柴油加氢装置简介3#柴油加氢装置,主要生产国V标准产品,主要原料为混合油,包括柴油、直馏柴油等,该装置每年约生产出2000000吨柴油。
该装置反应部分主要选用炉前混氢,具有多种优点,如反应平稳、混合均匀、便于控制等,选用热高分流程,能够直接利用反应热,使其成为分馏热进料,能够对高压空冷投资成本进行有效节省,对能量进行有效节约。
2 柴油加氢装置节能降耗措施2.1 选用变频调速技术对于柴油加氢装置来说,选用变频调速技术,能够起到较为显著的节能作用。
该装置地处高原,水资源不足,早晚气温冷热温差大,空气资源丰富,故而选用空冷电机变频+工频控制。
实际生产中该柴油加氢装置种共装有8台空冷变频调节器,在正常运行状况下,变频空冷器是优先选用的,在对工艺参数进行有效保障的同时,还能够产生较好的节能效果,自8台变频空冷器投入使用以来,其转速降低约50%,根据轴功率和转速之间得到关系式,当前轴功率能够得以有效降低,变为原轴功率的13%。
目前,该公司中的空冷变频调节器投用率100%,通过测算后,每小时能够有效节约35kW的电。
2.2 充分利用贺尔碧格气量调节系统在3#柴油加氢装置中,新氢压缩机设计方案为“一开一备”。
因为加氢装置处理量深受多种因素的影响,包括原料硫含量、原料品种、加工负荷等,导致补充氢的流量发生一定程度的额波动。
在标准状态中,每台新氢机的最大流量是26000m3/h,其中一台新氢机主要选用出口返回式调节系统,在实际运行中,因为机器额定排量应大于实际氢气用量,一返、二返返回阀开度一般都处于20% -50%范围内,大量氢气经过压缩以后,在通过返回阀后,其压力会下降,导致大量能量出现严重浪费现象;而另外一台新氢机主要选用贺尔碧格公司的气量无级调节系统,对于贺尔碧格气量无级调节系统,压缩机的实际容积流量和功消耗二者呈正比关系,具有非常显著的节能效果,实际运行中贺尔碧格投用时一返和二返负荷一般在70%-85%之间。
柴油加氢精制装置节能减排措施
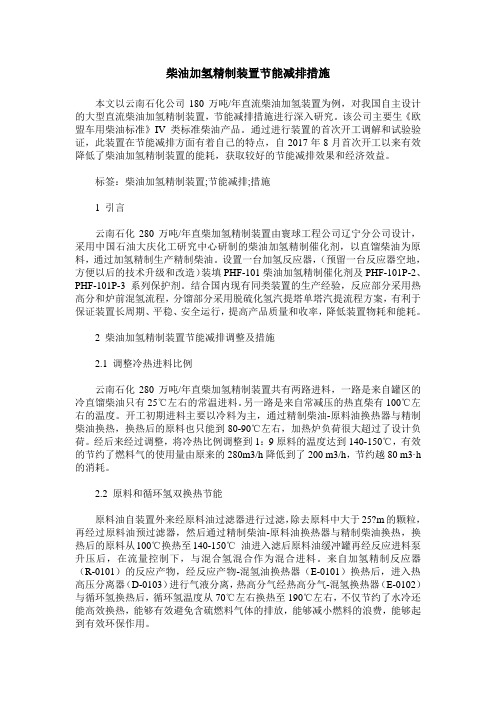
柴油加氢精制装置节能减排措施本文以云南石化公司180万吨/年直流柴油加氢装置为例,对我国自主设计的大型直流柴油加氢精制装置,节能减排措施进行深入研究。
该公司主要生《欧盟车用柴油标准》IV类标准柴油产品。
通过进行装置的首次开工调解和试验验证,此装置在节能减排方面有着自己的特点,自2017年8月首次开工以来有效降低了柴油加氢精制装置的能耗,获取较好的节能减排效果和经济效益。
标签:柴油加氢精制装置;节能减排;措施1 引言云南石化280万吨/年直柴加氢精制装置由寰球工程公司辽宁分公司设计,采用中国石油大庆化工研究中心研制的柴油加氢精制催化剂,以直馏柴油为原料,通过加氢精制生产精制柴油。
设置一台加氢反应器,(预留一台反应器空地,方便以后的技术升级和改造)装填PHF-101柴油加氢精制催化剂及PHF-101P-2、PHF-101P-3系列保护剂。
结合国内现有同类装置的生产经验,反应部分采用热高分和炉前混氢流程,分馏部分采用脱硫化氢汽提塔单塔汽提流程方案,有利于保证装置长周期、平稳、安全运行,提高产品质量和收率,降低装置物耗和能耗。
2 柴油加氢精制装置节能减排调整及措施2.1 调整冷热进料比例云南石化280万吨/年直柴加氢精制装置共有两路进料,一路是来自罐区的冷直馏柴油只有25℃左右的常温进料。
另一路是来自常减压的热直柴有100℃左右的温度。
开工初期进料主要以冷料为主,通过精制柴油-原料油换热器与精制柴油换热,换热后的原料也只能到80-90℃左右,加热炉负荷很大超过了设计负荷。
经后来经过调整,将冷热比例调整到1:9原料的温度达到140-150℃,有效的节约了燃料气的使用量由原来的280m3/h降低到了200 m3/h,节约越80 m3·h 的消耗。
2.2 原料和循环氢双换热节能原料油自装置外来经原料油过滤器进行过滤,除去原料中大于25?m的颗粒,再经过原料油预过滤器,然后通过精制柴油-原料油换热器与精制柴油换热,换热后的原料从100℃换热至140-150℃油进入滤后原料油缓冲罐再经反应进料泵升压后,在流量控制下,与混合氢混合作为混合进料。
柴油加氢精制工艺
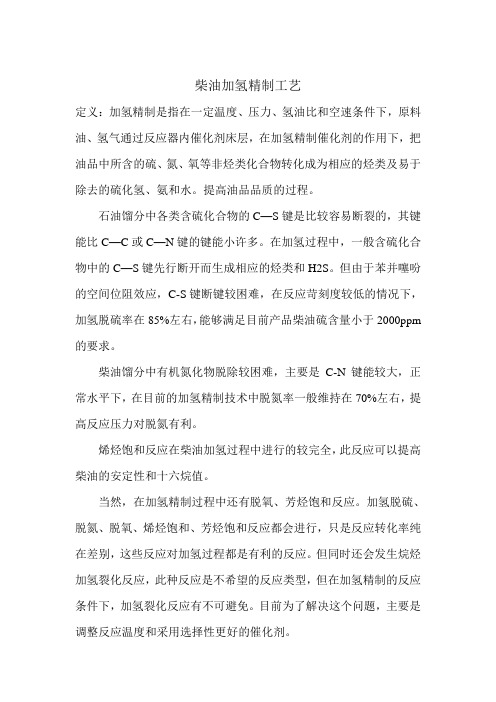
柴油加氢精制工艺定义:加氢精制是指在一定温度、压力、氢油比和空速条件下,原料油、氢气通过反应器内催化剂床层,在加氢精制催化剂的作用下,把油品中所含的硫、氮、氧等非烃类化合物转化成为相应的烃类及易于除去的硫化氢、氨和水。
提高油品品质的过程。
石油馏分中各类含硫化合物的C—S键是比较容易断裂的,其键能比C—C或C—N键的键能小许多。
在加氢过程中,一般含硫化合物中的C—S键先行断开而生成相应的烃类和H2S。
但由于苯并噻吩的空间位阻效应,C-S键断键较困难,在反应苛刻度较低的情况下,加氢脱硫率在85%左右,能够满足目前产品柴油硫含量小于2000ppm 的要求。
柴油馏分中有机氮化物脱除较困难,主要是C-N键能较大,正常水平下,在目前的加氢精制技术中脱氮率一般维持在70%左右,提高反应压力对脱氮有利。
烯烃饱和反应在柴油加氢过程中进行的较完全,此反应可以提高柴油的安定性和十六烷值。
当然,在加氢精制过程中还有脱氧、芳烃饱和反应。
加氢脱硫、脱氮、脱氧、烯烃饱和、芳烃饱和反应都会进行,只是反应转化率纯在差别,这些反应对加氢过程都是有利的反应。
但同时还会发生烷烃加氢裂化反应,此种反应是不希望的反应类型,但在加氢精制的反应条件下,加氢裂化反应有不可避免。
目前为了解决这个问题,主要是调整反应温度和采用选择性更好的催化剂。
下面以我厂100万吨/年汽柴油加氢精制装置为例,简单介绍一下工艺流程:60万吨柴油加氢精制催化汽油选择性加氢脱硫醇技术(RSDS技术)催化汽油加氢脱硫醇装置的主要目的是拖出催化汽油中的硫含量,目前我国大部分地区汽油执行国三标准,硫含量要求小于150ppm,烯烃含量不大于30%,苯含量小于1%。
在汽油加氢脱硫的过程中,烯烃极易饱和,辛烷值损失较大,针对这一问题,石科院开发了RSDS技术。
本技术的关键是将催化汽油轻重组分进行分离,重组分进行加氢脱硫,轻组分碱洗脱硫。
采取轻重组分分离的理论基础是,轻组分中烯烃含量高,可达到50%以上,通过直接碱洗,辛烷值几乎不损失。
柴油加氢精制装置运行情况分析

中国石化燕山石化公司(简称燕山石化)是北京地区唯一千万吨级炼化企业,油品质量升级始终走在国内前列,执行着国内最严格的汽柴油标准,2016年底率先推出京VI油品。
燕山石化有一套120万吨/年柴油加氢装置,以直馏柴油掺炼焦化汽油、焦化柴油和催化柴油,生产满足京VI标准车用柴油的调和组分。
1 装置简介燕山石化柴油加氢精制装置由反应部分(包括压缩机、循环氢脱硫)、分馏部分、循环氢脱硫及公用工程等部分组成。
装置原设计加工能力100万吨/年,2001年7月28日一次开车成功,2008 年通过扩能改造,增上了第二反应器,加工能力提高至120万吨/年。
该装置上周期(2017年12月9日—2020年6月)采用石油化工科学研究院(简称石科院)研制开发、中国石化催化剂长岭分公司生产的RS-2100/ RS-2110催化剂。
2020年8月,该装置在检修期间对加氢催化剂进行了再生并在第二反应器补充了部分活性稳定性更好的RS-3100催化剂。
2 装置上周期运行情况柴油加氢精制装置上周期加工的原料硫含量接近10000μg/g、密度在860 kg/m3左右、终馏点接近360℃。
装置运行初期,产品硫含量稳定控制低于10μg/g。
2.1 催化剂装填数据装置上周期催化剂装填数据详见表1。
表1 催化剂装填数据装填物质实际装填量堆密度/体积/m3重量/t(kg·m-3)一反上床层RG-1保护剂10.9 6.4585RS-2100催化剂(普通)17.514.8844一反中床层RS-2100催化剂(普通)30.225.3839一反下床层RS-2100催化剂(部分密相)44.542.9965二反RS-2100新鲜剂(普通)24.920.9840RS-2110新鲜剂(密相)44.047.51079由此可见,装置合计装填主精制催化161.1m3,合计151.4t。
其中,RS-2100催化剂普通装填堆密度在840kg/m3左右,密相装填堆密度达到980kg/m3;而RS-2110催化剂的装填堆密度较RS-2100高10%左右。
(120万吨)柴油加氢精制装置操作规程
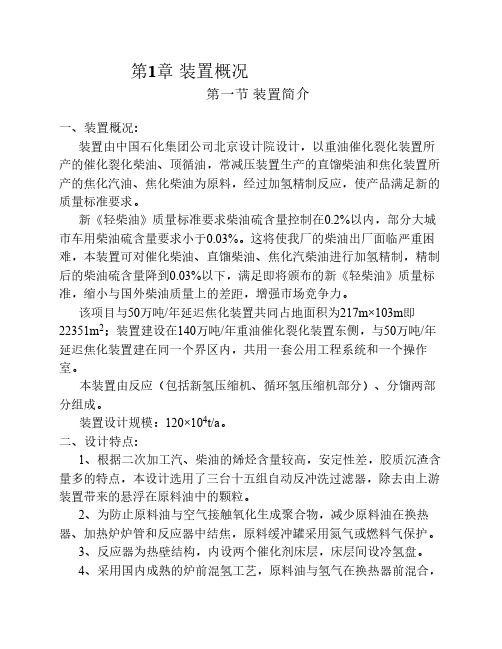
第一节 装置简介
一、装置概况: 装置由中国石化集团公司北京设计院设计,以重油催化裂化装置所
产的催化裂化柴油、顶循油,常减压装置生产的直馏柴油和焦化装置所 产的焦化汽油、焦化柴油为原料,经过加氢精制反应,使产品满足新的 质量标准要求。
新《轻柴油》质量标准要求柴油硫含量控制在0.2%以内,部分大城 市车用柴油硫含量要求小于0.03%。这将使我厂的柴油出厂面临严重困 难,本装置可对催化柴油、直馏柴油、焦化汽柴油进行加氢精制,精制 后的柴油硫含量降到0.03%以下,满足即将颁布的新《轻柴油》质量标 准,缩小与国外柴油质量上的差距,增强市场竞争力。
0.467 0.122 0.015 0.01 0.008 0.004 8.279 91.903
C5+液收
100.19
化学耗氢
0.85
备注:数据由石油化工科学研究院提供。
100.182 0.81
表5 柴油加氢精制产品主要性质
柴油产品要求
S<150ppm
方案一
方案二
主要产品
汽油 柴油 汽油 柴油
馏分范围
反应入口氢分压 MPa
进料量
t/h
体积空速
h-1
催化剂装填量 m3
上床层
下床层
反应温度 ℃
上床层:入口温度
方案一
方案二
RN-10
S<150ppm
6.4
150
1.83
1.82
96.79 32.26 64.53
307
315
出口温度 温升 下床层:入口温度
出口温度
温升
床层平均反应温度 ℃
反应器总温升 ℃ 反应器入口氢油比 床层间冷氢量 Nm3/h 催化剂运转周期 二、高压分离器: 操作压力 MPa(G) 温度 ℃ 三、低压分离器: 操作压力 MPa(G) 温度 ℃ 四、新氢压缩机: 入口温度 ℃ 40 入口压力 MPa(G) 出口压力 MPa(G) 五、循环氢压缩机: 入口温度 ℃ 50 入口压力 MPa(G) 出口压力 MPa(G) 六、汽提塔: 塔顶压力 MPa(G) 进料温度 ℃
100万吨年柴蜡油加氢精制装置操作规程
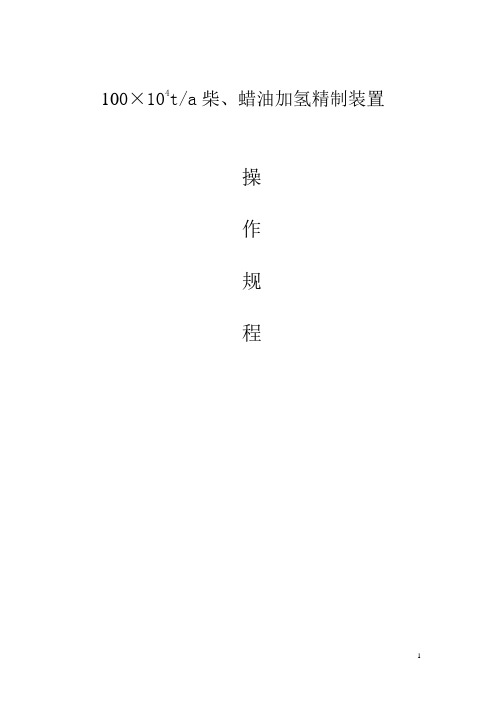
100×104t/a柴、蜡油加氢精制装置操作规程第一章装置概述第一节加氢工艺简介……………………………………………………4页第二节装置概况…………………………………………………………5页第二章加氢精制工艺原理第一节加氢工艺原理……………………………………………………7页第二节加氢精制反应机理………………………………………………8页第三章生产工艺过程第一节装置工艺流程简述………………………………………………12页第二节装置物料平衡及工艺操作条件…………………………………14页第三节催化剂性质及技术规格…………………………………………18页第四章装置生产工艺技术指标第一节原材料及产品质量………………………………………………20页第二节生产过程气体性质………………………………………………23页第三节装置消耗、能耗指标……………………………………………24页第四节装置生产控制分析………………………………………………27页第五章装置正常操作(岗位操作法)第一节氢气压缩机操作法………………………………………………28页第二节加热炉操作法……………………………………………………37页第三节反应系统操作法…………………………………………………43页第四节分馏系统操作法…………………………………………………50页第五节装置循环流程操作法……………………………………………54页第六节机泵操作法……………………………………………………57页第六章装置正常开工第一节装置的大检查…………………………………………61页第二节水电汽风引进装置……………………………………63页第三节装置试压与气密………………………………………65页第四节临氢系统升温干燥……………………………………70页第五节催化剂装填……………………………………………71页第六节催化剂预硫化…………………………………………74页第七节分馏系统引油升温循环………………………………77页第八节反应投料………………………………………………79页第七章装置正常停工…………………………………82页第八章装置主要控制及联锁自保……………………83页第一节装置主要控制回路……………………………………83页第二节装置联锁自保…………………………………………86页第九章装置事故处理…………………………………87页第一节装置停电紧急处理预案………………………………87页第二节装置停风紧急处理预案………………………………90页第三节装置停水紧急处理预案………………………………92页第四节装置停蒸汽紧急处理预案……………………………94页第五节装置停瓦斯紧急处理预案……………………………95页第六节重大工艺设备问题处理………………………………97页第十章环境保护…………………………………………102页第十一章劳动安全卫生…………………………………103页第十二章操作技术问答…………………………………108页附图:工艺流程设备平面图附表:设备一览表第一章加氢精制装置概述第一节加氢工艺简介催化剂加氢对于提高原油加工深度,合理利用石油资源,改善产品质量,提高轻质油收率以及减少大气污染都具有重要意义。
柴油加氢精制装置长周期运行
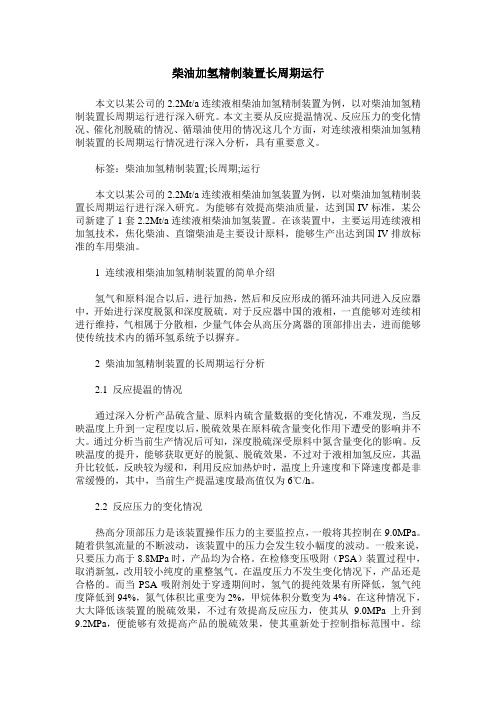
柴油加氢精制装置长周期运行本文以某公司的2.2Mt/a连续液相柴油加氢精制装置为例,以对柴油加氢精制装置长周期运行进行深入研究。
本文主要从反应提温情况、反应压力的变化情况、催化剂脱硫的情况、循環油使用的情况这几个方面,对连续液相柴油加氢精制装置的长周期运行情况进行深入分析,具有重要意义。
标签:柴油加氢精制装置;长周期;运行本文以某公司的2.2Mt/a连续液相柴油加氢装置为例,以对柴油加氢精制装置长周期运行进行深入研究。
为能够有效提高柴油质量,达到国IV标准,某公司新建了1套2.2Mt/a连续液相柴油加氢装置。
在该装置中,主要运用连续液相加氢技术,焦化柴油、直馏柴油是主要设计原料,能够生产出达到国IV排放标准的车用柴油。
1 连续液相柴油加氢精制装置的简单介绍氢气和原料混合以后,进行加热,然后和反应形成的循环油共同进入反应器中,开始进行深度脱氮和深度脱硫。
对于反应器中国的液相,一直能够对连续相进行维持,气相属于分散相,少量气体会从高压分离器的顶部排出去,进而能够使传统技术内的循环氢系统予以摒弃。
2 柴油加氢精制装置的长周期运行分析2.1 反应提温的情况通过深入分析产品硫含量、原料内硫含量数据的变化情况,不难发现,当反映温度上升到一定程度以后,脱硫效果在原料硫含量变化作用下遭受的影响并不大。
通过分析当前生产情况后可知,深度脱硫深受原料中氮含量变化的影响。
反映温度的提升,能够获取更好的脱氮、脱硫效果,不过对于液相加氢反应,其温升比较低,反映较为缓和,利用反应加热炉时,温度上升速度和下降速度都是非常缓慢的,其中,当前生产提温速度最高值仅为6℃/h。
2.2 反应压力的变化情况热高分顶部压力是该装置操作压力的主要监控点,一般将其控制在9.0MPa。
随着供氢流量的不断波动,该装置中的压力会发生较小幅度的波动。
一般来说,只要压力高于8.8MPa时,产品均为合格。
在检修变压吸附(PSA)装置过程中,取消新氢,改用较小纯度的重整氢气。
炼油厂工艺简介
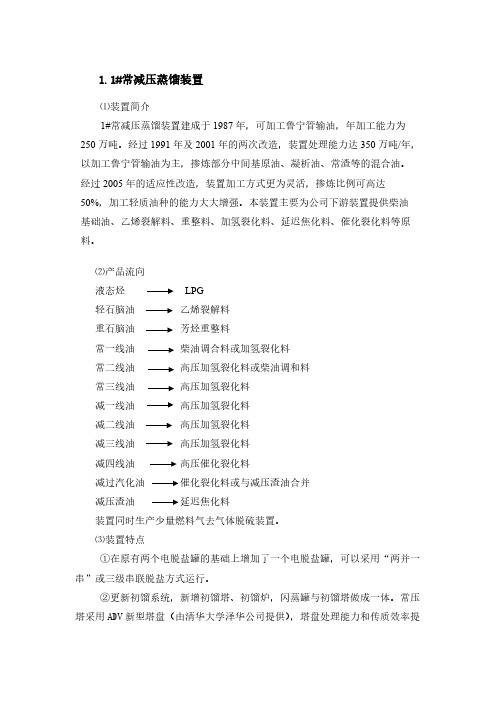
1.1#常减压蒸馏装置⑴装置简介1#常减压蒸馏装置建成于1987年,可加工鲁宁管输油,年加工能力为250万吨。
经过1991年及2001年的两次改造,装置处理能力达350万吨/年,以加工鲁宁管输油为主,掺炼部分中间基原油、凝析油、常渣等的混合油。
经过2005年的适应性改造,装置加工方式更为灵活,掺炼比例可高达50%,加工轻质油种的能力大大增强。
本装置主要为公司下游装置提供柴油基础油、乙烯裂解料、重整料、加氢裂化料、延迟焦化料、催化裂化料等原料。
⑵产品流向液态烃LPG轻石脑油乙烯裂解料重石脑油芳烃重整料常一线油柴油调合料或加氢裂化料常二线油高压加氢裂化料或柴油调和料常三线油高压加氢裂化料减一线油高压加氢裂化料减二线油高压加氢裂化料减三线油高压加氢裂化料减四线油高压催化裂化料减过汽化油减压渣油装置同时生产少量燃料气去气体脱硫装置。
⑶装置特点①在原有两个电脱盐罐的基础上增加了一个电脱盐罐,可以采用“两并一串”或三级串联脱盐方式运行。
②更新初馏系统,新增初馏塔、初馏炉,闪蒸罐与初馏塔做成一体。
常压塔采用ADV新型塔盘(由清华大学泽华公司提供),塔盘处理能力和传质效率提高。
③减压塔填料更换为高效规整填料ZUPAK,采用槽式分布器取代原喷头,进料部位采用流线式快速分布器(天津大学天久公司)。
④加热炉采用LGH-L/Q高效燃烧器(洛阳科恒公司)。
⑤装置增加轻烃回收系统,生产液化气、轻石脑油和重整料。
⑥减压系统采用三级蒸汽抽真空,残压达2.0Kpa以下。
2.2#常减压蒸馏装置⑴装置简介2# 常减压蒸馏装置建成于1995年,该装置主要加工高硫、轻质原油,加工能力为250万吨/年。
2002年装置经过改造,加工能力达450万吨/年,设计加工沙特轻质油、沙特中质混合原油。
800万吨/年炼油改造完成以后,主要以加工沙轻、阿曼等高(含)硫油为主,适当安排部分低硫原油,总硫控制在1.5%左右。
装置主要产品有液化气、乙烯料、重整料、柴油调和基础料、加氢裂化、加氢精制料、催化料、焦化料。
柴油加氢装置掺炼催化柴油试验总结

柴油加氢装置掺炼催化柴油试验总结总结了中国石油哈尔滨石化公司柴油加氢装置掺炼催化柴油试验期间,装置的氢气消耗及产品质量情况。
本次试验,考核了催化剂在原料性质发生变化的时的应用。
标签:加氢;掺炼;催化柴油1.装置简介中国石油哈尔滨石化公司100万吨/年柴油加氢装置2013年7月开始建设,2014年8月工程中交,由中国石化工程设计有限公司(SEI)设计,中油第一建设公司建设。
装置以来自上游常减压装置的常一线和常二线柴油为原料,在高温高压、氢气以及催化剂的作用下脱除原料中的硫、氮等杂质,生产出优质的航煤及柴油产品。
装置采用石油化工科学研究院(RIPP)和中国石化工程建设公司(SEI)联合开发的连续液相加氢(SLHT)技术。
100万吨/年柴油加氢精制装置催化剂采用RS-1100超深度脱硫催化剂和配套的RG-1保护剂。
2016年9月装置进行了第一次检修,对反应器催化剂进行器外再生,并补充部分新鲜催化剂,2016年9月26日装置开车成功。
2.掺炼催化柴油背景本次检修开工后,柴油加氢装置共进行了两次催化柴油掺炼,第一次在10月11日至10月15日期间,由于公司催化柴油原料罐存压力比较大,加氢改质装置处理能力有限,因此公司决定将催化柴油原料按比例引入柴油加氢装置进行试验;第二次在11月6日,装置引入催化柴油直供料进行掺炼,运行2小时后切除。
在掺炼催化柴油直供料之前,对柴油加氢装置原料流程进行改造,改造如下图所示:(1)图中加粗部分流程为新增流程。
(2)掺炼催化柴油过程中,阀(1)、(3)、(4)打开,阀(2)关闭。
(3)通过阀(1)控制催化柴油比例。
3.原料比較催化柴油与直馏柴油性质对比4.掺炼比例及调整过程10月11日至10月15日期间,按催化柴油原料比例10%、15%、20%引入装置,产品质量按普通柴油方案生产,反应器压力控制9.5MPa。
在催化柴油各种比例下观察R-101各床层温度、温升及氢耗情况。
确保反应器床层总温升不大于20℃,反应器床层温升通过以下手段控制:(1)开大E-101冷旁路调节阀TV11207,降低反应器入口温度;(2)调节P-104变频,将循环比提至2;(3)开大E-204管程跨线调节阀TV10402,降低原料油温度;(4)关闭E-203管程跨线阀,降低原料油温度。