加工余量一览表
板材加工余量表
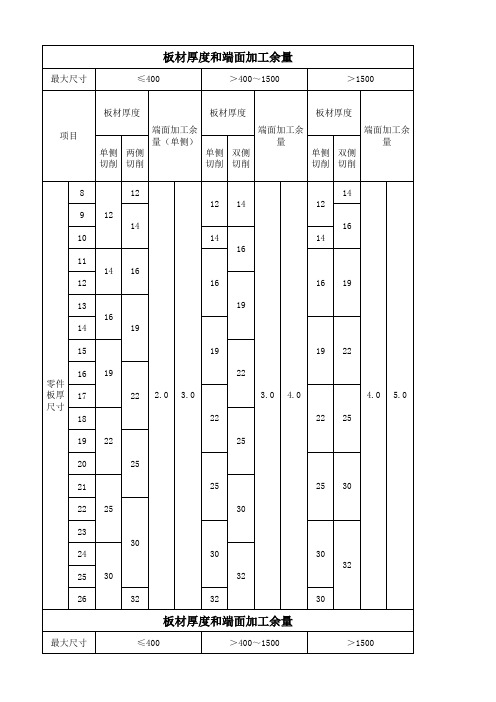
最大尺寸 ≤400 >400~1500 >1500
板材厚度 项目 单侧 两侧 切削 切削 8 9 10 11 14 12 13 16 14 15 16 零件 板厚 尺寸 17 18 19 20 21 22 23 30 24 25 26 30 32 25 22 25 19 22 2.0 3.0 19 16 12 14 12 端面加工余 量(单侧)
板材厚度 端面加工余 量 单侧 双侧 切削 切削
板材厚度 端面加工余 量 单侧 双侧 切削 切削 14
12
14
12 16
14 16
14
16 193.0 22 25 4.0
19
22
4.0 22 25
5.0
25 30
25
30
30 32 32
30 32
30
板材厚度和端面加工余量
最大尺寸 ≤400 >400~1500 >1500
端面加工余 量
47 48 49
50 55
55 55 50 51 52 零件 板厚 尺寸 53 60 54 55 65 56 57 58 65 59 65 60 厚度70~250mm 单侧 双侧 切削 切削 2~3 4~5 单侧 双侧 400~ 切削 切削 1000 3~4 6~7 单侧 双侧 1000 切削 切削 ~ 1500 4~5 7~8 65 70 65 70 60 60 65 2.0 3.0 4.0 5.0 60 5.0 6.0 55 60 60
板材厚度和端面加工余量
最大尺寸 ≤400 >400~1500 >1500
板材厚度 项目 端面加工余 量(单侧)
板材厚度 端面加工余 量
板材厚度 端面加工余 量
项目 单侧 两侧 切削 切削 46
毛坯加工余量表
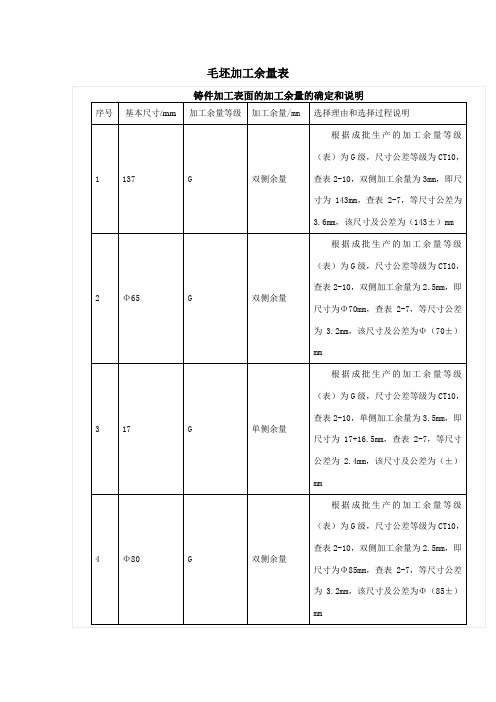
4
4
5
5
6
6
11-25
4
4
5
5
6
6
26-50
4
5
5
6
7
7
51-100
5
5
6
7
7
7
101-200
5
5
7
7
8
8
201-300
6
7
7
8
8
9
301-450
7
7
8
8
9
9
451-600
8
8
9
9
10
10
8
Φ47
H
双侧余量
根据成批生产的加工余量等级(表)为H级,尺寸公差等级为CT10,查表2-10,双侧加工余量为3mm,即尺寸为Φ41mm,查表2-7,等尺寸公差为2.8mm,该尺寸及公差为Φ(41±)mm
9
Φ32
H
双侧余量
根据成批生产的加工余量等级(表)为H级,尺寸公差等级为CT10,查表2-10,双侧加工余量为3mm,即尺寸为Φ26mm,查表2-7,等尺寸公差为2.6mm,该尺寸及公差为Φ(26±)mm
(毫米)
工件直径(D)
工 件 长 度 L
车刃的割刀量和车削二端面的余量(每件)
<70
71-120
121-200
201-300
301-450
直 径 上 加 工 余 量
≤32
1
2
2
3
4
5-10
33-60
2
3
3
4
5
4-6
61-100
3
4
加工余量参数表

附录三加工余量参数表表 1 粗车、半精车外圆的加工余量(单位:mm)注:加工带凸台的零件时,其加工余量要根据零件的全长和最大直径来确定。
表 2 精车外圆的加工余量(单位:mm)1.舍五入)。
这时的粗车外圆的公差等级为14 级。
2. 决定加工余量用轴的长度计算与装夹方式有关。
3. 粗车外圆的公差带相当于h12~h13。
注:1. 在单件或小批生产时,本表的余量值应乘上系数,并化成一位小数,如×=,采用(四舍五入)。
2. 决定加工余量用轴的长度计算与装夹方式有关。
3. 磨前加工公差相当于h11。
表 4 精车端面的加工余量(单位:mm)1. d2. 表中的公差系指尺寸L 的公差。
表 5 磨端面的加工余量(单位:mm)注: 1. 加工有台阶的轴时,每台阶的加工余量应根据该台阶的d 及零件的全长分别选用。
2. 表中的公差系指尺寸L 的公差。
加工孔直径钻用车刀 扩孔钻粗铰精铰的直径第一次第二次镗以后3- - - - 3H7 4- - - - 4H7 5-- - - 5H7 6- - --6H7 8-- -8H7 10- --10H712--12H7 13- -13H7 14--14H715- -15H7 16--16H718- -18H7 20-20H7 22-22H724-24H7 25-25H726-26H7 28-28H7302830H7 3232H7 3535H73838H7 4040H74242H7 4545H74848H7 5050H760 3060H7 70 3070H780 3080H790 30-90H7 100 30-100H7120 30-120H7 140 30-140H716030-160H7 180 30-180H7注: 1. 在铸铁上加工直径到 15mm 的孔时,不用扩孔钻扩孔。
2. 在铸铁上加工直径为 30 到 32mm 的孔时,仅用直径为 28 与 30mm 的钻头钻一次。
加工余量表

表1轴类调质余量单位:mm
表2齿轮调质余量单位:mm
表3齿圈调质余量单位:mm
表4轴类热处理后外圆磨前半精车(磨削余量)(调用)单位:mm
(2)对于淬火的零件,淬火前半精加工余量应为表中数值乘以1.25;
(3)磨前粗糙度不大于Ra6.3;
表5 渗碳、淬火齿面内外圆(非渗表面涂防渗剂)加工余量(mm)表(试用)
表6渗碳,淬火前齿轮半精车:内孔及端面磨削余量与公差(mm)(一分厂试用)
表7渗碳淬火后精车齿轮:内孔及端面磨削余量与公差(mm)(一分厂试用)
表8 渗碳、淬火齿轮粗滚齿公法线余量(mm) (一分厂试用)
表9渗碳、淬火齿轮粗滚齿公法线余量(mm) (三分厂试用)
表10渗碳、淬火齿轮粗滚齿公法线余量(mm) (四分厂试用)
表11软齿面及中硬齿面粗滚齿余量单位:mm
表12中硬齿面Mn>12热处理(调质)前粗滚齿及齿外圆余量(试用)单位:mm
表13
渗碳淬火弧齿锥齿轮磨前铣齿:齿厚留磨量与公差(mm)(试用)
技术中心工艺室2009-2-27
表14分箱面焊接箱体粗加工后人工时效余量(试用)单位:mm
表15 分箱面焊接箱体粗加工后振动时效余量(试用)单位:mm
表16铸铁箱体(平行轴)粗加工后人工时效余量单位:mm。
机械加工余量选择表
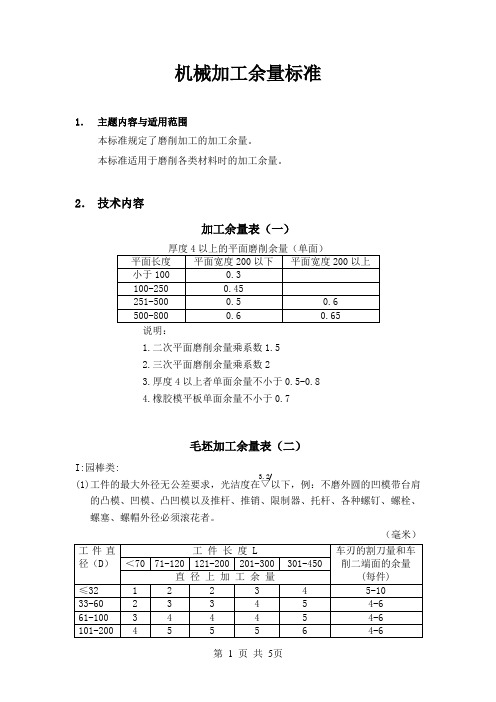
机械加工余量标准1. 主题内容与适用范围本标准规定了磨削加工的加工余量。
本标准适用于磨削各类材料时的加工余量。
2. 技术内容加工余量表(一)说明:1.二次平面磨削余量乘系数1.52.三次平面磨削余量乘系数23.厚度4以上者单面余量不小于0.5-0.84.橡胶模平板单面余量不小于0.7毛坯加工余量表(二)I:园棒类:(1)的凸模、凹模、凸凹模以及推杆、推销、限制器、托杆、各种螺钉、螺栓、螺塞、螺帽外径必须滚花者。
(毫米)当D <36时并不适应于调头夹加工,在加工单个工件时,应在L 上加夹头量10-15。
(2)凹模,挡料销、肩台须磨加工的凸模或凸凹模等。
当D <36时,不适合调头加工,在加工单个零件时,应加夹头量10-15。
毛坯加工余量表(三)(1)例如:固定板、退料板等。
注:表中的加工余量为最小余量,其最大余量不得超过厂规定标准。
毛坯加工余量表(四)Ⅲ:矩形锻件类:表内的加工余量为最小余量,其最大余量不得超过厂规定标准。
平面、端面磨削加工余量表(五)一、平面二、端面注:20-40% 如需磨两次的零件,其磨量应适当增加10-20%环形工件磨削加工余量表(六)注:φ50以下,壁厚10以上者,或长度为100-300者,用上限 φ50-φ100,壁厚20以下者,或长度为200-500者,用上限 φ100以上者,壁厚30以下者,或长度为300-600者,用上限 1.3 0.5φ6以下小孔研磨量表(七)注:本表只适用于淬火件当长度e 小于15毫米时,表内数值应加大20-30%导柱衬套磨削加工余量表(八)镗孔加工余量表(九)附注:当一次镗削时,加工余量应该是粗加工余量加工精加工余量。
毛坯加工余量表
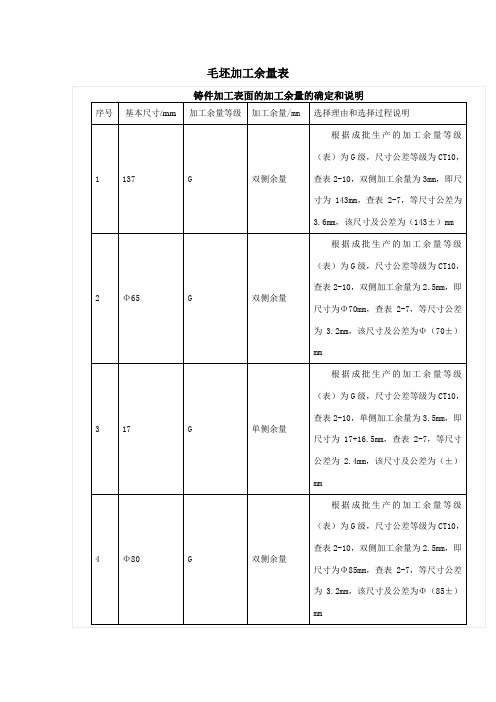
3
4
4
5
6
5-10
33-60
4
4
5
6
6
5-8
61-100
5
5
5
6
7
5-8
101-200
6
6
6
7
7
5-8
当D<36时,不适合调头加工,在加工单个零件时,应加夹头量10-15。
Ⅱ:圆形锻件类(不需锻件图)
(1)不淬火钢表面粗糙度在▽以下无公差配合要求者,例如:固定板、退料板等。
(毫米)
工件直径(D)
(毫米)
工件直径(D)
工 件 长 度 L
车刃的割刀量和车削二端面的余量(每件)
<70
71-120
121-200
201-300
301-450
直 径 上 加 工 余 量
≤32
1
2
2
3
4
5-10
33-60
2
3
3
4
5
4-6
61-100
3
4
4
4
5
4-6
101-200
4
5
5
5
6
4-6
当D<36时并不适应于调头夹加工,在加工单个工件时,应在L上加夹头量10-15。
工 件 长 度 L
<10
11-20
21-45
46-100
101-250
直径上加工余量 长度方向上余量
150-200
5 5
5 5
5 5
5 6
5 7
201-300
5 6
5 6
5 6
5 7
6 8
加工余量和切削参数表
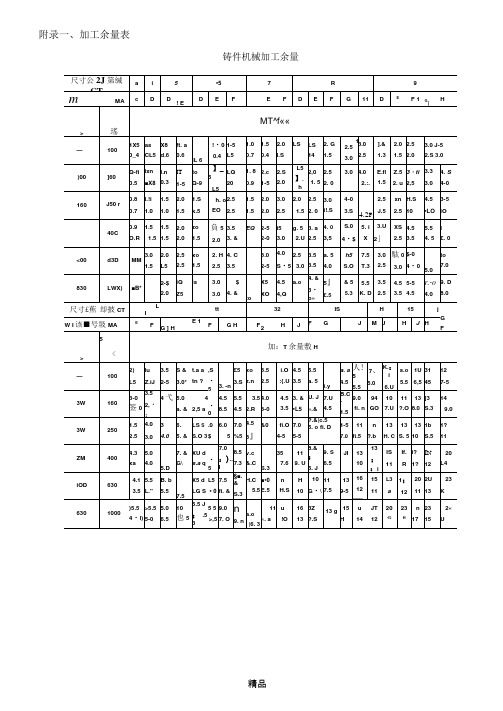
附录一、加工余量表铸件机械加工余量表磨孔余量ft 4-29平面租刨后精诜的加工余■/mm/mm表脣30铳平面的加工余・寬度冬200 寬度>200〜400 宽直M200 «« >200-400加工表面不同长度下的加工余・*8-31 ■平面的加工余・/mm魚处理后«8-33绩面的加工余■/mm« 879各种加工方法所能达到的表面粗糙度/pm 加工方法&值1 加工方法R•值车削外圆10 〜80 圜柱优刀半精车 2. 5 〜10 2. 5 〜20 精车1・25〜10 精饶0. 63〜5.细车0・16〜1・25 细饶0. 32〜1. 25 车削端面-一 - .................粗丰5〜20 aft 2. 5—20 半精车 2. 5〜10 0. 32 〜5 精车】・25〜10 细饶0.167 25 细车“0. 327 25 髙速饶IW车削割槽和切斷粗铳手炉“・・0. 63〜2・5 一次行程10〜20 0. 16~0・ 63 二次行程 2.5-10 刨削僮孔5〜20 粗僅5〜20 精刨1・25〜10 半箱桃2・5〜10 细刨(光»mi)0・16〜1・25 梢铿0・63〜5 槽的表面 2. 5 〜10 细蚀(金刚键床贰孔〉0・16〜1・25 插削 2. 5〜20钻孔 1.25 〜20 拉削扩孔精拉0. 32-2. 5 粗扩(有毛面)5〜20 细拉0. 08〜0・ 32 梢扩 1.25-10 推削储孔•倒角1・25〜5 精推0.16〜1・ 25 较孔细推0. 02〜0・ 63 • 一次较孔嫖纹加工钢2・5〜10 |用板牙、丝傩•自动张开式板牙头0. 63~5附录二、切削***、/ » 8-50碘质合蚩及髙連解车刀粗车外■和■面时的进给■注,1. 1JUT斷续表面及肓冲击时.表内的进给■应象票数K・0・75〜0.85.2. 加工酚热制及其合金不采用大于1.0mm/r的进给*.3. 加工淬缺钢时.我内进给it应桑系数K・0・8 (当材料硬度为44〜56HHC)或K-0. 5《当竇度为57〜62HRC时).表8・52切断及切槽的进给■注,1 •在直径大于60mm 的实心村料上切断时•当切刀接近峯件轴线0・5倍半径时・表中进给量应减小40% 〜50%.2.加工淬理钢时.表内进给量应橄小30% (当现度小于50HRC 时)或50% (当硬度大于50HRC 时).» 8-55切断和切槽时的切削用■/ft 8-57外圓切削速度參考袁,1・6090min.2.车孔切削速度要比车外圆时低10%〜20%.衰8・69高連•祸钻头钻孔时的进给■估头直径几/mm钢 %/MPa铸铁、铜、铝合金硬度<800800〜1000>1000<200HBS>200HBS进给 就//mm •◎0. 05 〜0・ 0§ . 0. 04 〜0・ 05 - 0. 03〜0・04・ 0. 09 〜0・ 11 0. 05—0. 07 >2〜4 0. 08-0.10 0. 06—0. 08 0. 04 〜0・ 06 0. 18 〜0・ 22 •0.11-0.13 >4〜6 0・14〜0・10 0・10〜0・12 0. 08 〜0・ 10 0. 27 〜0・ 33 0. 18-0. 22 >6〜8 0. 18 〜0・ 22 0・13〜0・15 0. 11-0. 13 0. 36〜0・ 44 0. 22 〜0・ 26 >8 〜10 0. 22 〜0・ 28 0.17-0.21 0. 13 〜0・ 17 0. 47〜0・ 57 0. 28 〜0・ 34 >10 〜13 0. 25 〜0・ 31 0.19-0. 23 0. 15 〜0. 19 0. 52〜0・ 64 0・3】〜0・39 >13~160・31〜0・37 0. 22 〜0・ 28 0・】8〜0・22 0.61-0. 75 0. 37 〜0・ 45 >】6〜200. 35〜0・ 43 0. 26 〜0・ 32 0.21-0. 25 0. 70〜0・ 86 0. 43〜0・ 53 >20 〜250. 39〜0.47 0. 29〜0・ 35 0. 23 〜0・ 29 0. 78-0. 96 0. 47〜0・ 57 >25 〜30 0・45〜0・55 0. 32〜0・ 40 0. 27 〜0・ 33 0. 9〜1・1 0. 54〜0・ 66 >30 〜600. 60〜0・ 700. 40〜0・ 500. 30〜0・ 401・0〜1・20. 70 〜0・ 80tt钻头直径必/mm工艺婴 求分类InIn进给 最 //mm •严0. 22*0. 280.8r 0・ 22 0.】8〜0. 22 Q. 13-0.17 >8~12 0. 20〜0・ 36 0. 22 〜0・ 28 0. 25 〜30 0.18〜0・ 22 >12 〜160. 25〜0・ 40 0. 25 〜0・ 30 0・ 28 〜0. 24 0. 20〜0・ 25 1>16 〜20 0. 40〜0・ 48 0. 27〜0・ 33 0. 32〜0・ 28 0・23〜0・28、 >20 〜24 0. 45~0・ 55 0. 33〜0・ 38 0. 38〜0. 43 0. 27〜0・ 32 >24 〜26 0. 50〜0・ 60 0. 37〜0・ 41 0・ 40〜0. 46 0. 32~0・ 28 >20 〜300. 55 〜0・ 650. 40〜0・ 500. 45 〜0. 500. 36〜0・ 44>200HBS復质合金YG8钻头鮎灰铸铁时的进给■/m-1丧8・99各种常用工件材料的饶剤琼度推荐范BI如有侵权请联系告知删除,感谢你们的配合!。
加工余量参数表
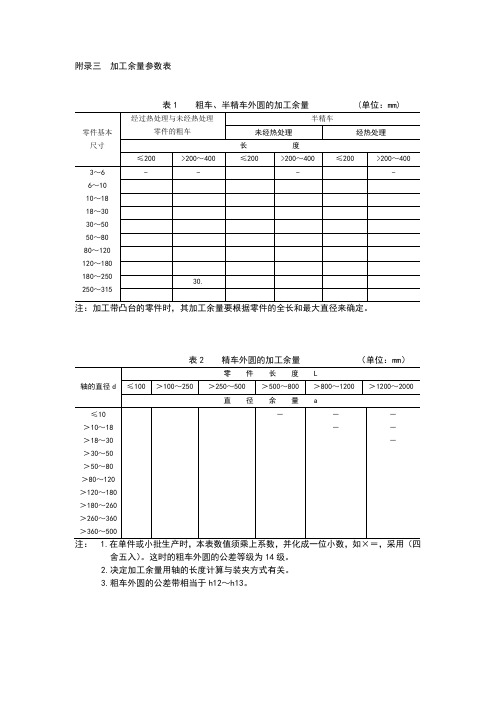
附录三加工余量参数表表1 粗车、半精车外圆的加工余量 (单位:mm)注: 1.在单件或小批生产时,本表数值须乘上系数,并化成一位小数,如×=,采用(四舍五入)。
这时的粗车外圆的公差等级为14级。
2.决定加工余量用轴的长度计算与装夹方式有关。
3.粗车外圆的公差带相当于h12~h13。
表3 磨削外圆的加工余量 (单位:mm)舍五入)。
2.决定加工余量用轴的长度计算与装夹方式有关。
3.磨前加工公差相当于h11。
注:1.加工有台阶的轴时,每台阶的加工余量应根据该台阶的d及零件的全长分别选用。
2.表中的公差系指尺寸L的公差。
表5 磨端面的加工余量 (单位:mm)注:1.加工有台阶的轴时,每台阶的加工余量应根据该台阶的d及零件的全长分别选用。
2.表中的公差系指尺寸L的公差。
2.在铸铁上加工直径为30到32mm的孔时,仅用直径为28与30mm的钻头钻一次。
3.用磨削作为孔的最后加工方法时,精镗以后的直径根据表1-23查得。
4.用金刚石细镗作为孔的最后加工方法时,精镗以后的直径根据表1-24查得。
5.如仅用一次铰孔,则铰孔的加工余量为本表中粗铰与精铰的加工余量总和。
2.在铸铁上加工直径为30、32mm的孔时,仅用直径为28、30mm的钻头钻一次。
3.用磨削作为孔的最后加工方法时,精镗以后的直径根据表1-23查得。
4.用金刚石细镗作为孔的最后加工方法时,精镗以后的直径根据表1-24查得。
5.如仅用一次铰孔,则铰孔的加工余量为本表中粗铰与精铰的加工余量总和。
注:1.当加工在热处理极易变形的、薄的轴套及其他零件时,应将表中的加工余量数值乘以。
2.如被加工孔在以后必须作为基准孔时,其公差应按7级公差来制定。
3.在单件、小批生产时,本表的数值应乘以,并化成一位小数。
例如×=,采用(四舍五入)。
表9 平面加工余量 (单位:mm)注:1.如几个零件同时加工时,长度及宽度为装置在一起的各零件长度或宽度及各零件间的间隙之总和。
加工余量表

表1轴类调质余量单位:mm
表2齿轮调质余量单位:mm
表3齿圈调质余量单位:mm
表4轴类热处理后外圆磨前半精车(磨削余量)(调用)单位:mm
(2)对于淬火的零件,淬火前半精加工余量应为表中数值乘以1.25;
(3)磨前粗糙度不大于Ra6.3;
表5 渗碳、淬火齿面内外圆(非渗表面涂防渗剂)加工余量(mm)表(试用)
表6渗碳,淬火前齿轮半精车:内孔及端面磨削余量与公差(mm)(一分厂试用)
表7渗碳淬火后精车齿轮:内孔及端面磨削余量与公差(mm)(一分厂试用)
表8 渗碳、淬火齿轮粗滚齿公法线余量(mm) (一分厂试用)
表9渗碳、淬火齿轮粗滚齿公法线余量(mm) (三分厂试用)
表10渗碳、淬火齿轮粗滚齿公法线余量(mm) (四分厂试用)
表11软齿面及中硬齿面粗滚齿余量单位:mm
表12中硬齿面Mn>12热处理(调质)前粗滚齿及齿外圆余量(试用)单位:mm
表13渗碳淬火弧齿锥齿轮磨前铣齿:齿厚留磨余量与公差(mm)(三分厂试用)
表14分箱面焊接箱体粗加工后人工时效余量(试用)单位:mm
表15 分箱面焊接箱体粗加工后振动时效余量(试用)单位:mm
表16铸铁箱体(平行轴)粗加工后人工时效余量单位:mm。
加工余量参数表
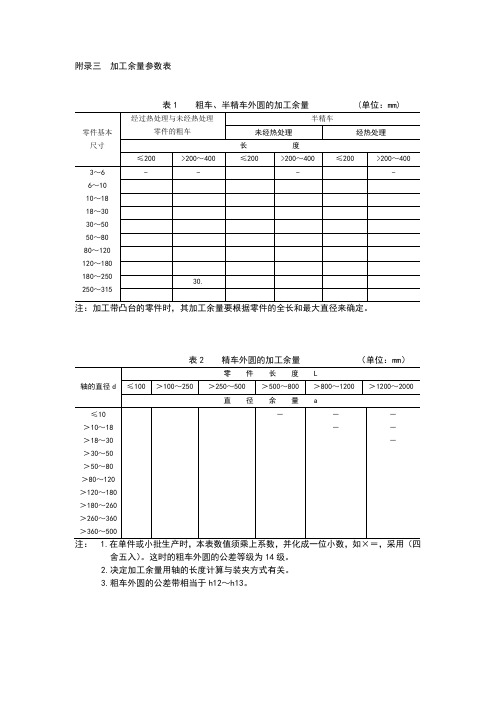
附录三加工余量参数表表1 粗车、半精车外圆的加工余量 (单位:mm)注: 1.在单件或小批生产时,本表数值须乘上系数,并化成一位小数,如×=,采用(四舍五入)。
这时的粗车外圆的公差等级为14级。
2.决定加工余量用轴的长度计算与装夹方式有关。
3.粗车外圆的公差带相当于h12~h13。
表3 磨削外圆的加工余量 (单位:mm)舍五入)。
2.决定加工余量用轴的长度计算与装夹方式有关。
3.磨前加工公差相当于h11。
注:1.加工有台阶的轴时,每台阶的加工余量应根据该台阶的d及零件的全长分别选用。
2.表中的公差系指尺寸L的公差。
表5 磨端面的加工余量 (单位:mm)注:1.加工有台阶的轴时,每台阶的加工余量应根据该台阶的d及零件的全长分别选用。
2.表中的公差系指尺寸L的公差。
2.在铸铁上加工直径为30到32mm的孔时,仅用直径为28与30mm的钻头钻一次。
3.用磨削作为孔的最后加工方法时,精镗以后的直径根据表1-23查得。
4.用金刚石细镗作为孔的最后加工方法时,精镗以后的直径根据表1-24查得。
5.如仅用一次铰孔,则铰孔的加工余量为本表中粗铰与精铰的加工余量总和。
2.在铸铁上加工直径为30、32mm的孔时,仅用直径为28、30mm的钻头钻一次。
3.用磨削作为孔的最后加工方法时,精镗以后的直径根据表1-23查得。
4.用金刚石细镗作为孔的最后加工方法时,精镗以后的直径根据表1-24查得。
5.如仅用一次铰孔,则铰孔的加工余量为本表中粗铰与精铰的加工余量总和。
注:1.当加工在热处理极易变形的、薄的轴套及其他零件时,应将表中的加工余量数值乘以。
2.如被加工孔在以后必须作为基准孔时,其公差应按7级公差来制定。
3.在单件、小批生产时,本表的数值应乘以,并化成一位小数。
例如×=,采用(四舍五入)。
表9 平面加工余量 (单位:mm)注:1.如几个零件同时加工时,长度及宽度为装置在一起的各零件长度或宽度及各零件间的间隙之总和。
毛坯加工余量表
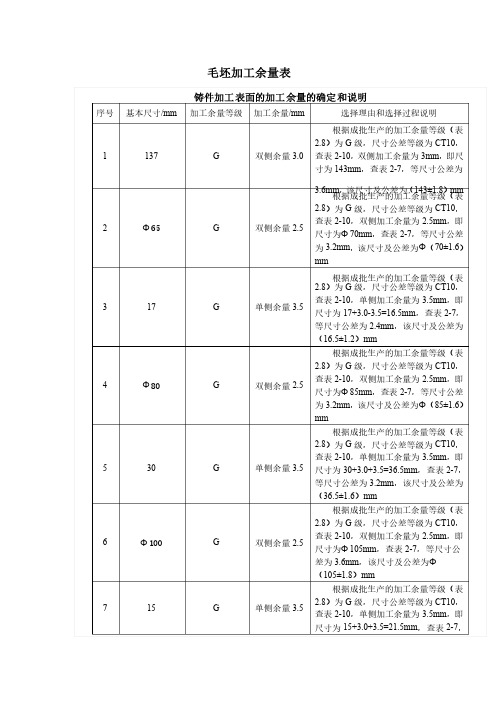
毛坯加工余量表铸件加工表面的加工余量的确定和说明序号序号 基本尺寸/mm 加工余量等级加工余量等级 加工余量/mm 选择理由和选择过程说明选择理由和选择过程说明1 137 G 双侧余量3.0 根据成批生产的加工余量等级(表2.8)为G 级,尺寸公差等级为CT10,查表2-10,双侧加工余量为3mm ,即尺寸为143mm ,查表2-7,等尺寸公差为3.6mm ,该尺寸及公差为(143±143±1.81.8)mm 2 Φ6565 G 双侧余量2.5 根据成批生产的加工余量等级(表2.8)为G 级,尺寸公差等级为CT10,查表2-10,双侧加工余量为2.5mm ,即尺寸为Φ70mm ,查表2-7,等尺寸公差为3.2mm ,该尺寸及公差为Φ(70±70±1.61.6)mm 3 17 G 单侧余量3.5 根据成批生产的加工余量等级(表2.8)为G 级,尺寸公差等级为CT10,查表2-10,单侧加工余量为3.5mm ,即尺寸为17+3.0-3.5=16.5mm ,查表2-7,等尺寸公差为2.4mm ,该尺寸及公差为(16.5±16.5±1.21.2)mm 4 Φ8080 G 双侧余量2.5 根据成批生产的加工余量等级(表2.8)为G 级,尺寸公差等级为CT10,查表2-10,双侧加工余量为2.5mm ,即尺寸为Φ85mm ,查表2-7,等尺寸公差为3.2mm ,该尺寸及公差为Φ(85±85±1.61.6)mm 5 30 G 单侧余量3.5 根据成批生产的加工余量等级(表2.8)为G 级,尺寸公差等级为CT10,查表2-10,单侧加工余量为3.5mm ,即尺寸为30+3.0+3.5=36.5mm ,查表2-7,等尺寸公差为3.2mm ,该尺寸及公差为(36.5±36.5±1.61.6)mm 6 Φ100100 G 双侧余量2.5 根据成批生产的加工余量等级(表2.8)为G 级,尺寸公差等级为CT10,查表2-10,双侧加工余量为2.5mm ,即尺寸为Φ105mm ,查表2-7,等尺寸公差为3.6mm ,该尺寸及公差为Φ(105±105±1.81.8)mm 7 15 G 单侧余量3.5 根据成批生产的加工余量等级(表2.8)为G 级,尺寸公差等级为CT10,查表2-10,单侧加工余量为3.5mm ,即尺寸为15+3.0+3.5=21.5mm ,查表2-7,等尺寸公差为2.4mm ,该尺寸及公差为(21.5±21.5±1.21.2)mm 8 Φ4747 H 双侧余量3.0 根据成批生产的加工余量等级(表2.8)为H 级,尺寸公差等级为CT10,查表2-10,双侧加工余量为3mm ,即尺寸为Φ41mm ,查表2-7,等尺寸公差为2.8mm ,该尺寸及公差为Φ(41±41±1.41.4)mm 9 Φ3232 H 双侧余量3.0 根据成批生产的加工余量等级(表2.8)为H 级,尺寸公差等级为CT10,查表2-10,双侧加工余量为3mm ,即尺寸为Φ26mm ,查表2-7,等尺寸公差为2.6mm ,该尺寸及公差为Φ(26±26±1.31.3)mm 10 Φ6060 H 双侧余量3.0 根据成批生产的加工余量等级(表2.8)为H 级,尺寸公差等级为CT10,查表2-10,双侧加工余量为3.0mm ,即尺寸为Φ54mm ,查表2-7,等尺寸公差为2.8mm ,该尺寸及公差为Φ(54±54±1.41.4)mm 11 78 G 单侧余量3.5 根据成批生产的加工余量等级(表2.8)为G 级,尺寸公差等级为CT10,查表2-10,单侧加工余量为3.5mm ,即尺寸为78+3.0-3.5=77.5mm ,查表2-7,等尺寸公差为3.2mm ,该尺寸及公差为(77.5±77.5±1.61.6)mm 12 Φ155155 G 双侧余量3.0 根据成批生产的加工余量等级(表2.8)为G 级,尺寸公差等级为CT10,查表2-10,双侧加工余量为4mm ,即尺寸为Φ161mm ,查表2-7,等尺寸公差为4.0mm ,该尺寸及公差为Φ(161±161±2.02.0)mm I :I:圆棒类: (1)工件的最大外径无公差要求,光洁度在▽3.2以下,例:不磨外圆的凹模带台肩的凸模、凹模、凸凹模以及推杆、推销、限制器、托杆、各种螺钉、螺栓、螺塞、螺帽外径必须滚花者。
机械加工余量标准最新版

机械加工余量标准最新版本标准适用于磨削各类材料时的加工余量。
2.技术内容加工余量表(一)厚度4以上的平面磨削余量(单面)平面长度平面宽度200以下平面宽度200以上小于1000.3100-2500.45251-5000.50.6500-8000.60.65说明: 1.二次平面磨削余量乘系数1.52.三次平面磨削余量乘系数23.厚度4以上者单面余量不小于0.5-0.84.橡胶模平板单面余量不小于0.7毛坯加工余量表(二)3.2I:园棒类:(1)工件的最大外径无公差要求,光洁度在▽以下,例:不磨外圆的凹模带台肩的凸模、凹模、凸凹模以及推杆、推销、限制器、托杆、各种螺钉、螺栓、螺塞、螺帽外径必须滚花者。
(毫米)工件直径(D)工件长度L车刃的割刀量和车削二端面的余量(每件)<7071-120121-200201-300301-450直径上加工余量≤32122345-1033-60233454-661-100344454-6101-200455564-61.6当D<36时并不适应于调头夹加工,在加工单个工件时,应在L上加夹头量10-15。
(2)工件的最大外径有公差配合要求,光洁度在▽以上,例如:外圆须磨加工的凹模,挡料销、肩台须磨加工的凸模或凸凹模等。
(毫米)工件直径(D)工件长度L车刃的割刀量和车削二端面的余量(每件)<5051-8081-150151-250251-420直径上加工余量≤15334455-1016-32344565-1033-60445665-861-100555675-8101-200666775-8当D<36时,不适合调头加工,在加工单个零件时,应加夹头量10-15。
毛坯加工余量表(三)3.2Ⅱ:圆形锻件类(不需锻件图)(1)不淬火钢表面粗糙度在▽以下无公差配合要求者,例如:固定板、退料板等。
(毫米)工件直径(D)工件长度L<1011-2021-4546-100101-250直径上加工余量长度方向上余量150-2005555555657201-3005656565768301-4005757576889401-50078586879910501-6007868687101011注:表中的加工余量为最小余量,其最大余量不得超过厂规定标准。
加工余量查询

表7-1模具经常使用加工办法的加工余量、加工精度、概略粗糙度之五兆芳芳创作注:经济加工余量是指本道工序的比较公道、经济的加工余量.本道工序加工余量要视加工根本尺寸、工件资料、热处理状况、前道工序的加工结果等具体情况而定.1. 加工总余量的确定(1)加工总余量和工序余量加工总余量(毛坯余量)—毛坯尺寸与零件图设计尺寸之差.工序余量—相邻两工序的工序尺寸之差.某个概略加工余量Z∑为该概略各加工工序的工序余量Zi之和,即式中n—该概略的加工工序数.(2)影响加工余量的因素1)加工概略上的概略粗糙度和概略缺陷层深度.2)加工前或上工序的尺寸公役.3)加工前或上工序各概略相互位置的空间偏差.4)本工序加工时的装夹误差.(3)查表法确定机械加工余量,总余量和半精加工、精加工工序余量可参考有关尺度或工艺手册查得,并应结合实际情况加以修正.粗加工工序余量减去半精加工和精加工工序余量而得到.2. 工序尺寸及公役计较对于各类工序的定位基准与设计基准重应时的概略的多次加工(如外圆和内孔的加工),工序尺寸可由后续加工的工序尺寸加工上(对被包涵面)或减去(对包涵面)公称工序余量而求得;工序尺寸公役按所用加工办法的经济精度选定.图4-2 暗示外圆加工时加工余量、工序尺寸及其公役的散布,图中Z1、Z2、Z3为粗加工、半精加工、精加工的公称余量;To为毛坯公役.T1 、T2、T3为粗加工、半精加工、精加工的工序尺寸公役.当各工序的公称余量和公役确定后,卡按下面顺序计较每一工序的工序尺寸;终加工(精加工)工序尺寸A3,公役T3由零件图规则.半精加工的工序尺寸A2=A3+ Z3,公役为T2.粗加工的工序尺寸A1= A2+ Z2,公役为T1.毛坯尺寸Ao= A1+Z2.公役为To.工序尺寸的公役一般应按“入体原则”标注,而在毛坯的根本尺寸上一般都注以双向偏差.当基准不重应时,或零件在加工进程中需要多次转换工序基准,或工序尺寸尚需在持续加工的概略上标注时,有关工序的工序尺寸及其公役,则需通过尺寸链的阐发,计较得到.3. 机床及工艺装备的选择(1)机床的选择1)机床的加工尺寸规模应与工件的外廓尺寸相适应.2) 机床的任务精度应与工序要求的精度想适应.3)机床的生产率应与工件的生产类型相适应.4)机床的选择应考虑工场的现有设备条件.如果工件尺寸太大,精度要求太高,没有相应设备可供选择时,就需改装设备或设计专用机床.(2)工艺装备的选择1)夹具的选择,在单件小批生产中,应尽量选用通用夹具或组合夹具,在大批大量生产中,应按照工序要求设计专用高效夹具.2)刀具的选择,主要取决于工序所采取的加工办法,加工概略的尺寸,工件资料,所要求的加工精度和概略粗糙度、生产率及经济性等,一般应尽量选用尺度刀具.3)量具的选择,主要按照生产类型和要求查验的精度.在单件小批生产中,应尽量采取通用量具量仪,在大批大量生产中,应采取各类极限量规或高生产率的查抄量仪.4. 时间定额及缩减单件时间的措施(1)时间定额及其组成,时间定额是在一定的生产条件下,规则生产一件产品或完成一道工序所消耗的时间,用td暗示.按照时间定额可以安插作业筹划.进行成本核算.确定设备设备数量和人员编制,筹划生产面积.因此,时间定额是工艺规程中的重要组成部分.时间定额主要利用经过实践而堆集的统计资料及进行部分计较来确定.时间定额由以下部分组成:1)根本时间定额tj 直接改动生产对象的形状、尺寸、相对位置、概略状态或资料性能等工艺进程所消耗的时间.根本时间定额通常可用计较的办法求出,具体计较公式详见各加工办法章节.2)帮助时间定额tf 为实现工艺进程所必须进行的各类帮助动作所消耗的时间.帮助时间定额可按照统计资料来确定,也可以按根本时间的百分数来预算.根本时间定额与帮助时间定额的总和称为作业时间定额.3)安插任务地时间定额tb 为使加工正常进行,工人照管任务地(如改换刀具、润滑机床、清理切屑、收拾东西等)所消耗的时间.安插任务地时间定额一般按作业时间的百分数计较.4)休息与生理需要时间定额tx 工人在任务班内为恢复体力和满足生理上的需要所消耗的时间.休息与生理需要时间一般也按作业时间的百分数预算.5)准备与终结时间定额tz 工人为生产一批数量为N的产品或零、部件,进行准备和结束任务所消耗的时间.成批生产时的时间定额:td=tj+tf+tb+tx+ tz:/N大量生产时的时间定额:td=tj+tf+tb+tx(2)缩减单件时间的措施1)缩减根本时间tj的措施,提高切削用量,削减加工余量,缩短刀具的任务行程,采取多刀多刃和多轴机床加工,或采取其他新工艺,新技巧.2)缩减帮助时间tf的措施,尽量使帮助动作实现机械或自动化,如采取先进夹具,提高机床的自动化程度;使帮助时间与根本时间部分地域或全部地重叠起来,如采取多位夹具或多位任务台,采取主动丈量或数字显示自动丈量装置.3)缩减安插任务地时间tb的措施,采取耐用度较高的刀具或砂轮,采取各类快换刀夹、刀具微调装置,专用对刀样板和样件以及自动换刀装置.4)缩减准备与终结时间的措施,采取成组工艺生产组织形式,使夹具和刀具的调整通用化,采取准备终结时间较短的先进设备及工艺装备.。
轴在粗车外圆后,精车外圆的加工余量
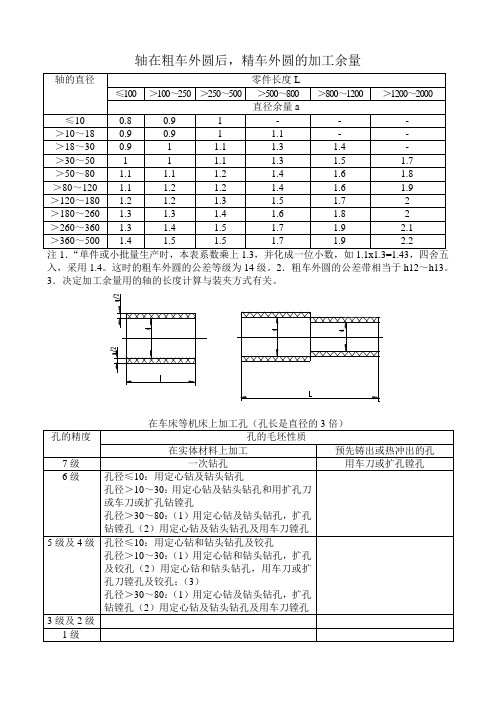
1.1
1.2
1.4
1.6
1.8
>80~120
1.1
1.2
1.2
1.4
1.6
1.9
>120~180
1.2
1.2
1.3
1.5
1.7
2
>180~260
1.3
1.3
1.4
1.6
1.8
2
>260~360
1.3
1.4
1.5
1.7
1.9
2.1
>360~500
1.4
1.5
1.5
1.7
1.9
2.2
注1.“单件或小批量生产时,本表系数乘上1.3,并化成一位小数,如1.1x1.3=1.43,四舍五入,采用1.4。这时的粗车外圆的公差等级为14级。2.粗车外圆的公差带相当于h12~h13。
≤18
>18~50
>50~120
>120~260
>260~500
>500
余量a
≤30
0.5
0.6
0.7
0.8
1ቤተ መጻሕፍቲ ባይዱ
1.2
>30~50
0.5
0.6
0.7
0.8
1
1.2
>50~120
0.7
0.7
0.8
1
1.2
1.2
>120~260
0.8
0.8
1
1
1.2
1.4
>260~500
1
1
1.2
1.2
1.4
1.5
>500
轴在粗车外圆后,精车外圆的加工余量
轴的直径
零件长度L
≤100