产品缺陷名称分类汇编
产品缺陷等级分类表

糊金
烫金压力过重/温度过高导致糊版
※
D15
28
烫击穿纸 击凹/烫金过程中导致穿纸
※
D16
29
压纹浅 产品表面效果浅/样品不一致
※
D17
30 浮雕/击凸浅 产品表面效果浅/样品不一致
※
D18
31
短坑/超坑 裱坑见坑纸与面纸位置造成
※
D19
32
甩坑
裱纸干后容易撕开/分层/脱落
※
D20
33 裱纸上下粘连 裱纸胶水粘到上下物料造成粘坏粘烂
※
D8
21
丝印飞油 丝印油墨飞溅到印张其他地方
※
D9
22
丝印糊版 丝印图文模糊变粗
※
D10
23 丝印套位不准 过程中位置不准≥0.5mm
※
D11
24
金纸色差 烫金纸颜色与样品颜色不一致
※
D12
25
掉金/沙眼 烫金面掉金或颗粒状掉金
※
D13
26 烫金套位不准 烫金过程中位置不准≥0.5mm
※
D14
27
※
C6
7
水干/水大 印张水墨失衡导致
※
C7
8
水墨杠/鬼影 印张表面有杠印/花印
※
C8
9
擦花/拖花 印张表面有刮擦/拖擦痕迹/油墨花
※
C9
10
过底粘花 印张下面一张油墨带起粘到上面一张
※
C10
11
错字/缺字 印张残字/字体错误等
※
C11
12
皱纸/烂纸 印张有皱烂
※
C12
13
覆错膜 光膜/哑膜/触感膜等使用错误
产品缺陷的概念和种类

产品缺陷的概念和种类概念产品缺陷指的是产品在设计、制造或售后服务过程中出现的错误或缺陷。
它可能导致产品无法正常使用、功能不完善或存在安全隐患等问题。
产品缺陷在市场经济中非常常见,消费者购买产品后发现问题时,他们常常会寻求售后维权或者要求退货。
产品缺陷的种类1. 设计缺陷:设计缺陷指的是产品在设计阶段就存在的问题,导致产品无法满足消费者需求或者容易出现故障。
设计缺陷可能源自于设计师对产品功能的理解错误、抄袭他人设计或者不同厂家间技术差异等。
比如,某个家电公司生产的电饭锅在设计时忽略了实际需求,导致加热不均匀或者小心烧焦食物。
2. 制造缺陷:制造缺陷指的是产品在制造过程中出现的错误,导致产品无法正常工作或者存在安全隐患。
制造缺陷可能来自于工艺不当、原材料选择有误、生产设备老化或者操作失误等。
比如,某个汽车制造商在生产过程中没有严格控制质量,导致汽车零部件容易断裂或者接缝易开裂。
3. 包装缺陷:包装缺陷指的是产品在包装过程中出现的问题,导致产品容易损坏或者影响产品使用。
包装缺陷可能产生于包装材料的质量问题、包装设计的不合理或者包装过程中的操作失误等。
比如,某个食品生产企业在包装产品时使用了低质量的塑料袋,导致产品在运输过程中易破裂,影响食品的安全性。
4. 表示缺陷:表示缺陷指的是产品在市场营销过程中表述失误或者虚假宣传等问题,导致消费者对产品性能、功能或者质量有误解。
表示缺陷可能来自于企业在广告宣传中的夸大其词、销售人员对产品性能的不正确说明或者标签贴错等。
比如,某个化妆品公司在产品广告中宣称可以即时祛皱,吸引了很多消费者购买,但实际效果却非常有限。
5. 效能缺陷:效能缺陷指的是产品在正常使用时无法满足消费者的期望或者功能不完善的问题。
效能缺陷可能源自于产品设计时对市场需求的误判、制造工艺的不完善或者未发现的技术难题等。
比如,某个电子公司生产的智能手机屏幕显示效果不清晰,导致用户体验差。
6. 安全缺陷:安全缺陷指的是产品在使用过程中存在安全隐患或者对用户造成伤害的问题。
质量缺陷分类

质量缺陷分类
1. 设计缺陷!你看啊,就像一个房子设计的时候把窗户开得特别小,导致采光不足,这多闹心啊!比如你买个杯子,把手设计得特别别扭,拿起来都费劲,这就是设计缺陷呀!
2. 材料缺陷那可太要命啦!好比你做蛋糕用了过期的面粉,能好吃吗?像有的衣服,没用多久就破了洞,这就是材料不行导致的材料缺陷嘛!
3. 制造缺陷真的很烦人唉!就好像工厂生产玩具,结果有个零件没安好,玩着玩着就坏了,这不就是制造的时候没弄好嘛!比如一辆车,某些地方装配得很粗糙,这就是制造缺陷的例子呀!
4. 包装缺陷也不容忽视呀!你想想,一个精美的礼物,结果包装一塌糊涂,心情是不是都变差啦?像有的食品,包装密封有问题,这不就容易坏嘛,这就是包装缺陷呀!
5. 标识缺陷也挺坑人的呢!比如说一个药瓶,上面的使用说明写得模模糊糊,让人怎么用呀?就跟有的电器,标识不清不楚,让人弄不清怎么操作,这就是标识缺陷的表现呀!
6. 性能缺陷真的很影响使用体验呀!就仿佛一部手机,总是卡顿,这多烦人!比如一台电视,画面效果不好,这就是性能上有缺陷呗!
7. 寿命缺陷有时候真让人无语呀!好比一个灯泡,没用多久就坏了,这寿命也太短了吧!像有的工具,很快就磨损不能用了,就是寿命缺陷的例子呀!
8. 服务缺陷也是个大问题哟!要是你买了个东西,售后爱答不理的,你气不气?比如去修车,工作人员态度极差,这就是服务缺陷嘛!
我觉得呀,质量缺陷的分类真的很重要,我们得重视起来,不然会给我们的生活带来很多麻烦和不愉快呢!。
72-产品缺陷分类

WI-QC-017(A)
核准:
审核:
制表:李申媚
NO
不良项目
1
外观刮花2外观黑来自/杂质3外观缺料
4
不熟/过硫
4
外观批锋
5 包装方式不符合
6 包装数量不符合
7
冲型缺陷
8 外箱标签不符合
9 型号标签不符合
10
关键尺寸
11
拉力测试
12
咬力测试
13
VOC/M测试
14
老化测试
东莞市印象科技有限公司
产品缺陷分类
级别
A级
B级
C级
备注
A级为严重缺陷(CR):1.0重金属含量严重超标. 2.0不符合法律法规的要求.3.0对安全有隐患. 阐述 B级为主要缺陷(MAJ)直接影响产品的使用和销售.
产 品 缺 陷 分 级 表

番核
确认
作成
刘睿
产 品 缺 陷 分 级 表
作成日:2012.11.28 产品分类 缺点分类 轻微 冲压件 严重 致命 轻微 螺丝 严重 致命 轻微 轴芯 严重 致命 轻微 铆钉 严重 致命 轻微 车削件 严重 致命 不 良 现 象
外观不良,刮花,伤痕,电镀水印,毛边,色差,掉漆,流油,电镀不良等 尺寸不良,变形,缺料,功能不良,盐雾实验NG等 RoHS不符,材质不符,信赖性实验NG等 外观不良,爆模,伤痕,毛刺,毛边,台阶不饱满,牙底不光滑等 尺寸不良,断角,断冲针,斜牙,烂牙,环规NG,光钉等 锤击实验NG,信赖性实验NG,RoHS不符,材质不符等 外观不良,伤痕,多料,毛边,电镀不良等 尺寸不良,漏车槽,变形,盐雾实验NG等 锤击实验NG,信赖性实验NG,RoHS不符,材质不符等 外观不良,伤痕,多料,毛边,电镀不良等 尺寸不良,变形,盐雾实验NG等 信赖性实验NG,RoHS不符,材质不符等 外观不良,伤痕,多料,毛边,电镀不良等 尺寸不良,变形,漏工序,粗糙度NG,盐雾实验NG等 信赖性实验NG,RoHS不符,材质不符等
处理办法:各个检验单位发现不良,应立即标识并隔离,按我司不合格品处理办法和程序作出相应的处理。 如客户有特殊要求,按客户要求处理。
ቤተ መጻሕፍቲ ባይዱ
变更时间
2007.04.26 2012.11.28
变更内容 作成 增加不良现象,处理办法
承认 XXX XXX
确认
变更者 XXXX XXXX
WI-QC-20/2007.04.26
产品缺陷等级分类表

序号 缺陷名称
定义
功能
严重缺陷 一般缺陷
1 磁性 无磁性、磁性不足
※
2 开合 不能正常开合
※
3 规格 规格错误
※
材质
1 纸板克重错误 克重选用与要求不一致
※
2 皮革材质不符 皮革材质与要求不一致
※
3 绒布错误
绒布材质与要求不一致
※
外观
1 缺损
产品有不正常缺口或少部件
※
2 开胶
胶水粘合不牢产生的产品部件分离
※
3 内盒歪斜
内盒两端距边不一致
※
4 包装错误
装箱数量或包装方式与订单不一致
※
5 少数
装箱数量比要求数量少
※
6 起泡
胶水未粘合产生的问题
※
7 破皮
产品表面破损
※
8 间隙
产品不吻合,边缘间隙过大
※
9 露铁皮
皮料包边不到位产生露铁皮
※
10 露纸板
皮料包边不到位产生露纸板
※
11 软边
折边不到位产生的问题
※
12 LOGO
LOGO歪斜、破损、不清晰、错误等
※
13 胶水
产品表面有块状或颗粒状胶水
14 磁铁歪斜
放磁铁时不到位产生的位置偏差
15 绒布起皱
材料不良或操作不当产生的问题
16 绒布歪斜
两边或两端距边缘距离不一致
17 箱唛错误
箱唛与订单不一致
18 凸点
产品表面或内里有凸起现象
19 露底布
内盒配合不到位露材料底布
严重缺陷:凡对产品构成致命缺陷,对人生安全有伤害,丧失产品主要功能,严重影响产品使用性 能。 一般缺陷:未对产品构成致命性缺陷,对产品使用功能没有影响,但会严重影响其外观。
产品缺陷名称分类汇编

产品缺陷名称分类汇编邵东铝业二00三年十月铸轧、板带产品缺陷分类汇编,主要参照兄弟工厂的有关资料,结合本公司的具体情况编写而成的,主要是为了加强质量管理,统一缺陷代号,为生产及技术培训提供指导,并便于质量的统计分析工作。
由于此编写容尚未与本公司的生产实践进行很好的结合,可能有不当之处,望提宝贵意见,以便于今后进行充实,修改完善。
板、带系列产品缺陷编号1、热带产生原因:⑴前箱温度偏高、液面偏低;⑵铸轧速度过快;⑶供料咀局部发生堵塞。
消除办法:⑴降低前箱温度,控制液面高度;⑵降低铸轧速度;⑶提速、跑渣或更换供料咀。
2、气道产生原因:⑴熔体中氢含量偏高;⑵供料咀潮湿;⑶供料咀局部堵塞或唇部破损。
消除办法:⑴加强精炼、除气,使含氢弹量隆到0.13ml/100克、铝以下;⑵供料咀使用前要加热烘干、保温。
⑶提速、跑渣或更换供料咀。
3、裂纹产生原因:⑴熔体过热;⑵熔体保温时间过长;⑶铸轧速度过快,供料咀唇局部破裂。
消除办法:⑴适当增加Al—Ti—B细化晶粒。
⑵缩短熔体保温时间;⑶降低铸轧速度,及时更换供料咀。
4、裂边产生原因:⑴铸轧区过大;⑵供料咀边部有金属凝块;消除办法:⑴缩小铸轧区;⑵及时更换供料咀。
5、尺寸超差产生原因:⑴供料咀规格不符;⑵铸轧辊辊缝超差;⑶设备液压系统发生故障。
消除办法:⑴及时更换供料咀;⑵调整铸轧辊辊缝;⑶保证设备工作稳定。
6、同板差超差产生原因:⑴铸轧辊辊型不对称;⑵铸轧辊两侧辊缝不一致;⑶铸轧机设备发生故障。
消除办法:⑴保证铸轧辊辊型符合要求;⑵调整两侧辊缝的距离;⑶保证铸轧机设备工作稳定。
7、粘辊产生原因:⑴铸轧速度过快;⑵冷却强度低;⑶烧火喷烟润滑出故障。
消除办法:⑴降低铸轧速度;⑵提高冷却强度;⑶保证喷烟润滑正常工作。
8、非金属压入产生原因:⑴供料咀损坏,其颗粒进入铸轧板;⑵喷烟润滑,其烟量过大,黑烟粉粘在辊面上;消除办法:⑴及时更换供料咀;⑵控制好喷烟量及烟雾颗粒。
9、大晶粒产生原因:⑴熔体温度高,局部过热;⑵熔体保温时间过长;⑶轧辊冷却强度低。
产品缺陷编码表
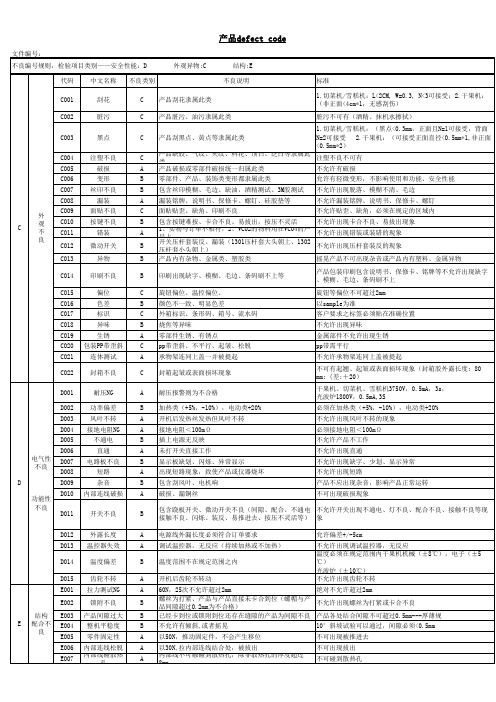
产品缺胶、气纹、夹纹、料花、顶白、泛白等隶属此 注塑不良不可有 类 产品破损或零部件破损统一归属此类 不允许有破损 零部件、产品、装饰类变形都隶属此类 包含丝印模糊、毛边、缺油,酒精测试、3M胶测试 漏装铭牌、说明书、保修卡、螺钉、硅胶垫等 面贴贴歪、缺角、印刷不良 允许有轻微变形,不影响使用和功能、安全性能 不允许出现脱落、模糊不清、毛边 不允许漏装铭牌、说明书、保修卡、螺钉 不允许贴歪、缺角,必须在规定的区域内
产品defect code
文件编号: 不良编号规则,检验项目类别——安全性能:D 代码 C001 C002 C003 C004 C005 C006 C007 C008 外 观 不 良 C009 C010 C011 C012 C013 C014 C015 C016 C017 C018 C019 C020 C021 C022 D001 D002 D003 D004 D005 D006 电气性 不良 D 功能性 不良 D007 D008 D009 D010 D011 D012 D013 D014 D015 E001 E002 E 结构 配合不 良 E003 E004 E005 E006 E007 中文名称 刮花 脏污 黑点 注塑不良 破损 变形 丝印不良 漏装 面贴不良 按键不良 错装 微动开关 异物 印刷不良 偏位 色差 标识 异味 生锈 包装PP带歪斜 连体测试 封箱不良 耐压NG 功率偏差 风叶不转 接地电阻NG 不通电 直通 电路板不良 短路 杂音 内部连线破损 开关不良 外露长度 温控器失效 温度偏差 齿轮不转 拉力测试NG 锁附不良 产品间隙过大 整机平稳度 零件固定性 内部连线松脱 内部线碰散热 孔 不良类别 C C C C A B B A C B A B B B C B C B A C A C A B A A B A B A B A B A A B A A B B B A A A 产品刮花隶属此类 产品脏污、油污隶属此类 产品刮黑点、黄点等隶属此类 外观异物:C 结构:E 不良说明 标准 1.切菜机/雪糕机:L<2CM, W=0.3, N<3可接受;2.干果机: (非正面<4cm*1,无感刮伤) 脏污不可有(酒精、抹机水擦拭) 1.切菜机/雪糕机:(黑点<0.3mm,正面且N=1可接受,背面 N=2可接受 2.干果机:(可接受正面直径<0.5mm*1,非正面 <0.5m绝对不允许超过2mm 螺丝为打紧、产品与产品直接未卡合到位(螺帽与产 不允许出现螺丝为打紧或卡合不良 品间隙超过0.2mm为不合格) 已经卡到位或锁附到位还存在缝隙的产品为间隙不良 产品各处结合间隙不可超过0.5mm---厚薄规 不允许有倾斜,或者摇晃 以50N,推动固定件,不会产生移位 以30N,拉内部连线结合处,被拔出 内部线不可触碰到散热孔,除非散热孔的厚度超过 8mm 10°斜坡试验可以通过,间隙必须<0.5mm 不可出现被推进去 不可出现拔出 不可碰到散热孔
产品缺陷名称解释
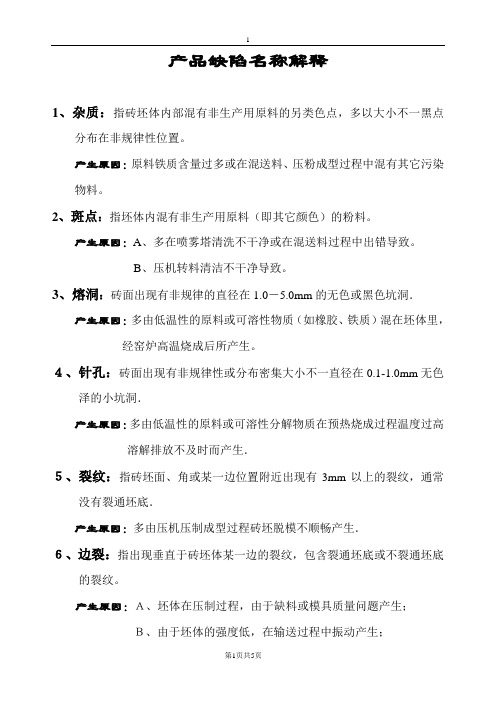
产品缺陷名称解释1、杂质:指砖坯体内部混有非生产用原料的另类色点,多以大小不一黑点分布在非规律性位置。
产生原因:原料铁质含量过多或在混送料、压粉成型过程中混有其它污染物料。
2、斑点:指坯体内混有非生产用原料(即其它颜色)的粉料。
产生原因:A、多在喷雾塔清洗不干净或在混送料过程中出错导致。
B、压机转料清洁不干净导致。
3、熔洞:砖面出现有非规律的直径在1.0-5.0mm的无色或黑色坑洞.产生原因:多由低温性的原料或可溶性物质(如橡胶、铁质)混在坯体里,经窑炉高温烧成后所产生。
4、针孔:砖面出现有非规律性或分布密集大小不一直径在0.1-1.0mm无色泽的小坑洞.产生原因:多由低温性的原料或可溶性分解物质在预热烧成过程温度过高溶解排放不及时而产生.5、裂纹:指砖坯面、角或某一边位置附近出现有3mm以上的裂纹,通常没有裂通坯底.产生原因:多由压机压制成型过程砖坯脱模不顺畅产生.6、边裂:指出现垂直于砖坯体某一边的裂纹,包含裂通坯底或不裂通坯底的裂纹。
产生原因:A、坯体在压制过程,由于缺料或模具质量问题产生;B、由于坯体的强度低,在输送过程中振动产生;C、由于干燥或入窑烧成温度控制不合理产生。
7、心裂:指砖体面部在中间任何位置有长5mm以上的裂纹.产生原因:A、坯体在压制过程压力不够或模具质量问题产生;B、由于坯体强度低,在输送过程由于输送带或干燥辊棒高低不平稳所产生。
8、分层:指砖体出现有夹层现象,通常出现在砖面、砖边和砖底产生夹层。
产生原因:由于压机压制排气过程设定的数据不适应原料颗料的水份变化造成。
9、变形:指砖面水平线由于中心弯曲度或边弯曲度超出指定的控制标准。
产生原因:A、微粉砖(二次布料)基料与粉料烧成收缩上下不级配产生;B、烧成温度曲线控制不合理或辊棒太弯和棒钉等造成;C、砖体抛光深度过深砖坏了砖面结构,形成砖面致密度跟砖底不一致造成。
(多指幻彩砖)。
10、有机质:砖体表面呈现密集的点,分布局部或大面积灰黑色状态。
缺陷分类标准
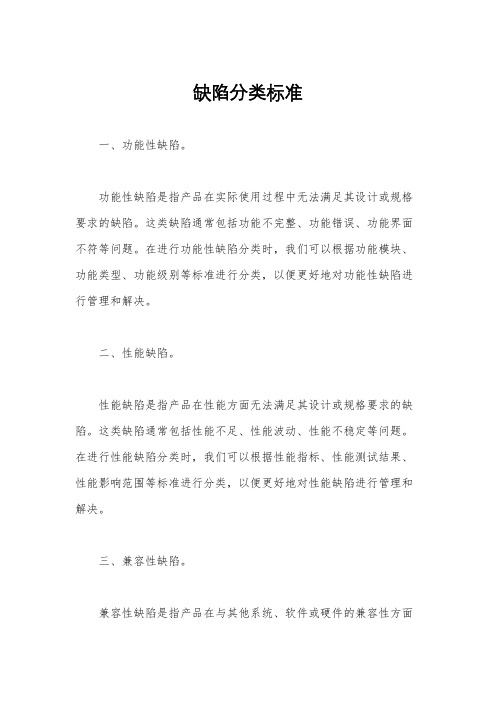
缺陷分类标准一、功能性缺陷。
功能性缺陷是指产品在实际使用过程中无法满足其设计或规格要求的缺陷。
这类缺陷通常包括功能不完整、功能错误、功能界面不符等问题。
在进行功能性缺陷分类时,我们可以根据功能模块、功能类型、功能级别等标准进行分类,以便更好地对功能性缺陷进行管理和解决。
二、性能缺陷。
性能缺陷是指产品在性能方面无法满足其设计或规格要求的缺陷。
这类缺陷通常包括性能不足、性能波动、性能不稳定等问题。
在进行性能缺陷分类时,我们可以根据性能指标、性能测试结果、性能影响范围等标准进行分类,以便更好地对性能缺陷进行管理和解决。
三、兼容性缺陷。
兼容性缺陷是指产品在与其他系统、软件或硬件的兼容性方面存在问题的缺陷。
这类缺陷通常包括与特定平台不兼容、与特定浏览器不兼容、与特定设备不兼容等问题。
在进行兼容性缺陷分类时,我们可以根据兼容性范围、兼容性影响、兼容性测试结果等标准进行分类,以便更好地对兼容性缺陷进行管理和解决。
四、安全性缺陷。
安全性缺陷是指产品在安全性方面存在问题的缺陷。
这类缺陷通常包括数据泄露、权限不足、漏洞利用等问题。
在进行安全性缺陷分类时,我们可以根据安全风险等级、安全漏洞类型、安全漏洞影响范围等标准进行分类,以便更好地对安全性缺陷进行管理和解决。
五、可靠性缺陷。
可靠性缺陷是指产品在可靠性方面存在问题的缺陷。
这类缺陷通常包括系统崩溃、数据丢失、功能异常等问题。
在进行可靠性缺陷分类时,我们可以根据可靠性影响程度、可靠性测试结果、可靠性故障率等标准进行分类,以便更好地对可靠性缺陷进行管理和解决。
综上所述,缺陷分类标准在产品开发和测试过程中起着非常重要的作用。
通过对缺陷进行分类,我们可以更好地理解和管理产品中的问题,从而及时有效地解决缺陷,提高产品质量,满足用户需求。
因此,我们需要在实际工作中充分利用各种缺陷分类标准,以便更好地进行缺陷管理和解决。
塑料件缺陷汇总

表面冷料
B
未充分塑化或经过流道, 喷嘴时急剧冷却的材料 进入模腔,与周围的材 料熔合不良而形成制件 表面的缺陷
缺陷图片
产生原因
解决方法
1、熔料塑化不均匀 2、模具温度太低
均匀塑化 增加模温
3、熔料内混入难熔的杂料
使用干净原料
4、热嘴温度太低
提高热嘴温度
5、无冷料穴或冷料穴尺寸不合理
增加冷料穴/更改冷料穴尺寸
换料/降低模温/降低料温/降低注射压力
调整模具,重新研配贴合不紧部位/清除杂物 调整模具,减小型腔和型芯部分滑动零件间 隙 烧焊过切部位,重新加工研配
7、模具强度或刚性差
增大模板厚度/增加模板或补加支撑柱
8、模具各承接面平行度差
修整模具,使各承接面间相互平行
9、模具安装时未被压紧
重新安装模具
缺陷名称 缺陷等级
产生原因
缺陷图片
1、浇口尺寸小
2、注射速度过快
3、模温低
解决方法
增大浇口尺寸 适当降低注射速度 提高模温
4、注射压力过大
合理控制注射压力
5、浇口位置不当
更改浇口位置
缺陷名称 缺陷等级
缺陷释义
熔接线
B
注射成型时,熔料汇合 处产生的细线称为熔接 线
缺陷图片
模具类型 塑料模
产生原因
1、注射压力低,注射速度慢 2、模温低 3、脱模剂使用不合理 4、模具排气不良 5、熔料温度低
6、注射速度过快或过慢
调整注射速度
缺陷名称 表面光泽度不良、阴影
缺陷等级 缺陷释义
A
熔料流动时受阻,改变方向而 在制件表面形成的光泽不一致 现象
缺陷图片
模具类型
产生原因
(精编)产品质量缺陷分级

A B C D 1 封口三率低于标准要求(√)√2彩印脱落(√)√3二重卷边假封、大塌边、快口、跳封、断封等√(√)4空罐导电率超标√5硫酸铜实验不合格√6表面划伤严重√7图形或标认错误√8图案色差√9内涂面有油污√10封口擦伤严重√11盖子埋头度不足√12焊缝不良等√(√)13盖子刻线泄漏 √14酸度明显低于规定下限√15净含量平均不足√16BRIX偏差超过内控标准√17滋气味有明显异味√18滋气味有轻微异味,不明显√19有明显肉眼可见的外来杂质√20产品色泽明显偏深或偏浅√21错装、漏装产品、产品无标识,数额较大√22包装标识品种、规格不清晰,包装损坏严重√23包装轻微污染或擦伤√(√)24杀菌时间和温度低于标准要求√25真空度不足但不漏气√(√)26拉环不能正常开启√(√)27慢性泻漏√28成品罐体凹瘪变形(√)(√)√2930B级:立刻停机,隔离产品.知会生产部与工程部, 在找到原因并排除故障前不得重新投入生产. 原材料退货.C级:隔离产品.知会生产部与工程部,排除故障继续生产.原材料投诉.D级:在生产空隙进行调整;或边生产边调整.原材料投诉.注意: 缺陷等级栏内标记一项以上的,分别适用于该项缺陷程度的轻重不同时,或不同品种具体要求。
由于生产情况复杂,各种缺陷由于某种原因可能会转化.现场控制时要求灵活运用,控制标准只能采用更严一级,严禁使用下一级!品检部2006年1月12日附: 产品缺陷分级评定参考表序号缺 陷 情 况缺 陷 等 级针对不同等级的缺陷采相应的处理措施并每半年检讨一次,以便及时纠正完善:A级:立刻停机,隔离产品,并上报公司领导,在找到原因并排除故障前不得重新投入生产.重新投 入生产后必须得到公司领导的同意.原材料退货.。
不良品分类和缺点程度区分一览表
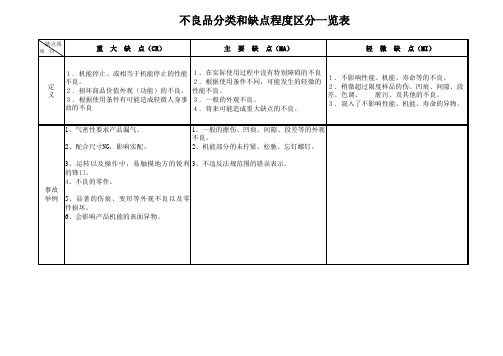
1.不影响性能、机能、寿命等的不良。 2.稍微超过限度样品的伤、凹痕、间隙、段 差、色调、 脏污、及其他的不良。 3.混入了不影响性能、机能、寿命的异物。
1、气密性要求产品漏气。 2、配合尺寸NG,影响实配。
1、一般的擦伤、凹痕、间隙、段差等的外观 不良。 2、机能部分的未拧紧、松驰、忘钉螺钉。
事故 举例
不良品分类和缺点程度区分一览表
缺点项 项 目
重 大 缺 点(CR)
主 要 缺 点(MA)
轻 微 缺 点(MI)
定 义
1.机能停止、或相当于机能停止的性能 不良。 2.损坏商品价值外观(功能)的不良。 3.根据使用条件有可能造成轻微人身事 故的不良
1.在实际使用过程中没有特别障碍的不良 2.根据使用条件不同,可能发生的轻微的 性能不良。 3.一般的外观不良。 4.将来可能造成重大缺点的不良。
3、运转以及操作中,易触摸地方的锐利 3、不违反法规范围的错误表示。 的锋口。 4、不良的零件。
5、显著的伤痕、变形等外观不良以及ቤተ መጻሕፍቲ ባይዱ 件损坏。 6、会影响产品机能的表面异物。
不良缺陷一览表

道的部位及薄壁处,缺陷周缘圆滑光亮。其浇 注系统 是未充满的,浇道和
注系统是充满的。
冒口顶面基本上与铸件上表面
齐平。
铸件上部残缺,残缺部分边角呈圆形,浇注系 肉眼外观检查。注意与浇 不 统未充满,直浇道和冒口与铸件上表面齐平 到相区别
1.跑火:铸件分型面以上部分严重残缺,残缺 表面凹陷。有时沿型腔壁形成类似飞翅的残 片,在铸件 分型面处有时有飞翅。2.型漏(漏 箱)存在于铸件内的严重的空壳状残缺。有时 铸件 外形虽较完整,但内部金属已漏空,铸件 完全呈坚守岗位状,铸型底部残留有多余金属 。
孔或渣缩孔。渣气孔(渣缩孔)出现的部位与 渣、渣气孔、渣缩孔与内渗物
夹渣相同,表现形式有夹渣内含气孔(缩孔或 和外渗物的区别是:前者形状
缩松)、气孔(缩孔)内含夹渣及夹渣外气孔 不规则呈大片状或斑点状分
(缩松)成群分布三种。在铸件断面上,夹渣 布,无金属光泽;后者呈豆粒
、渣气孔、渣缩孔均无金属光泽。
称为表面气孔;位于铸件表皮下的腰圆形分散
性气孔称为皮下气孔;分散分布在铸件内部、
状如针头的气孔称为针孔;成群分布在铸件表
层、状如针头的气孔称为表面针孔。气孔壁一 铸件内部的气孔采用超声检验
般较光滑。气孔常与夹渣或缩松并存。气孔按 或射线检验,在铸件表层的气
形成原因可以分为卷入气孔、侵入气孔、反应 孔采用渗透液或磁粉检验。各
生的疤片状金属突起物,其表面粗糙边缘锐
区别。
利,和一小部分金属与铸件本体相连,疤片与
铸件之间夹有砂层。通常发生在铸件的下表面
和下表面上。
肉眼外观检查。注意其与未浇
铸件残缺,轮廓不完整,或轮廓虽完整,但边 满的区别。浇不到铸件 的浇
、棱、角圆钝。常出现在型腔上表面或远离 浇 注系统是充满的;未浇满的浇
产品缺陷分类标准
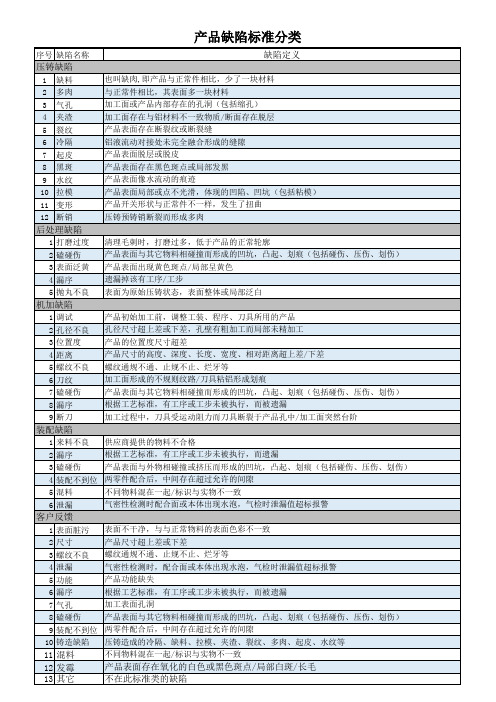
2 磕碰伤
产品表面与其它物料相碰撞而形成的凹坑,凸起、划痕(包括碰伤、压伤、划伤)
3 表面泛黄 产品表面出现黄色斑点/局部呈黄色
4 漏序
遗漏掉该有工序/工步
5 抛丸不良 表面为原始压铸状态,表面整体或局部泛白
机加缺陷
1 调试
产品初始加工前,调整工装、程序、刀具所用的产品
2 孔径不良 孔径尺寸超上差或下差,孔壁有粗加工而局部未精加工
9 断刀
加工过程中,刀具受运动阻力而刀具断裂于产品孔中/加工面突然台阶
装配缺陷
1 来料不良 供应商提供的物料不合格
2 漏序
根据工艺标准,有工序或工步未被执行,而遗漏
3 磕碰伤
产品表面与外物相碰撞或挤压而形成的凹坑,凸起、划痕(包括碰伤、压伤、划伤)
4 装配不到位 两零件配合后,中间存在超过允许的间隙
11 混料
不同物料混在一起/标识与实物不一致
12 发霉
产品表面存在氧化的白色或黑色斑点/局部白斑/长毛
13 其它
不在此标准类的缺陷
产品缺陷标准分类
序号 缺陷名称
缺陷定义
压铸缺陷
1 缺料
也叫缺肉,即产品与正常件相比,少了一块材料
2 多肉
与正常件相比,其表面多一块材料
3 气孔
加工面或产品内部存在的孔洞(包括缩孔/断面存在脱层
5 裂纹
产品表面存在断裂纹或断裂缝
6 冷隔
铝液流动对接处未完全融合形成的缝隙
3 位置度
产品的位置度尺寸超差
4 距离
产品尺寸的高度、深度、长度、宽度、相对距离超上差/下差
5 螺纹不良 螺纹通规不通、止规不止、烂牙等
6 刀纹
加工面形成的不规则纹路/刀具粘铝形成划痕
产品审核缺陷目录

超出公差范围
浙江海中天橡塑有限公司
文件编号:QA/YJJD030805-004-0
版本:A 页码:2/2 分发日期:2006/02/01 分发编号:
标题:产品审核缺陷目录
序 号
缺陷描述 缺陷名称
关键缺陷
没有供应商的检验合格
主要缺陷
次要缺陷
705
材料检验
证书\没有原材料检验规 范
检验不合格的原材料未 经验证就让步放行
0mm处小于3处385带楔缺陷带楔形不正常405图纸无顾客图纸或遗失自绘图纸未经确认410产品特殊特性未加识别415尺寸检验特殊特性值不符普通特性值不符505游标卡尺检验游标卡尺零位不准未经检定不在使用有效期内510测长机检验未经检定不在使用有效期内515投影仪检验未经检定不在使用有效期内520高低温箱未经检定不在使用有效期内525疲劳寿命试验机未经检定不在使用有效期内530拉力机未经检定不在使用有效期内535硬度计未经检定不在使用有效期内605皮带硬度超出公差范围610拉伸强度小于标准值615线抽出强度小于标准值620布剥离强度小于标准值625参考力伸长率小于标准值630齿剪切强度小于标准值缺陷名称浙江海中天橡塑有限公司文件编号
标题:产品审核缺陷目录
本作业指导书列出了公司三大类产品的常见缺陷,影响品级及产生此缺陷的工序和原因: 1、目的: 了解产品的质量状况,提供原始数据,有利于针对性地做出纠正预防措施。 2、范围: 公司的各种产品(包括新产品和常规产品)的产品质量审核。 3、引用文件: 无。 4、术语和定义: 4.1 关键缺陷:预见到会对人身造成危险和不安全的缺陷; 4.2 主要缺陷:非关键缺陷,预计会影响使用性,不能完全按照规定的用途使用; 4.3 次要缺陷:预计按照规定的用途使用不会受到多大影响,或与适用的标准有偏差,但对设备、装置的 使用、操作、运行等有轻微影响的缺陷。 5、主要内容:
- 1、下载文档前请自行甄别文档内容的完整性,平台不提供额外的编辑、内容补充、找答案等附加服务。
- 2、"仅部分预览"的文档,不可在线预览部分如存在完整性等问题,可反馈申请退款(可完整预览的文档不适用该条件!)。
- 3、如文档侵犯您的权益,请联系客服反馈,我们会尽快为您处理(人工客服工作时间:9:00-18:30)。
产品缺陷名称分类汇编邵东铝业有限公司二00三年十月铸轧、板带产品缺陷分类汇编,主要参照兄弟工厂的有关资料,结合本公司的具体情况编写而成的,主要是为了加强质量管理,统一缺陷代号,为生产及技术培训提供指导,并便于质量的统计分析工作。
由于此编写内容尚未与本公司的生产实践进行很好的结合,可能有不当之处,望提宝贵意见,以便于今后进行充实,修改完善。
板、带系列产品缺陷编号1、热带产生原因:⑴前箱温度偏高、液面偏低;⑵铸轧速度过快;⑶供料咀局部发生堵塞。
消除办法:⑴降低前箱温度,控制液面高度;⑵降低铸轧速度;⑶提速、跑渣或更换供料咀。
2、气道产生原因:⑴熔体中氢含量偏高;⑵供料咀潮湿;⑶供料咀局部堵塞或唇部破损。
消除办法:⑴加强精炼、除气,使含氢弹量隆到0.13ml/100克、铝以下;⑵供料咀使用前要加热烘干、保温。
⑶提速、跑渣或更换供料咀。
3、裂纹产生原因:⑴熔体过热;⑵熔体保温时间过长;⑶铸轧速度过快,供料咀唇局部破裂。
消除办法:⑴适当增加Al—Ti—B细化晶粒。
⑵缩短熔体保温时间;⑶降低铸轧速度,及时更换供料咀。
4、裂边产生原因:⑴铸轧区过大;⑵供料咀边部有金属凝块;消除办法:⑴缩小铸轧区;⑵及时更换供料咀。
5、尺寸超差产生原因:⑴供料咀规格不符;⑵铸轧辊辊缝超差;⑶设备液压系统发生故障。
消除办法:⑴及时更换供料咀;⑵调整铸轧辊辊缝;⑶保证设备工作稳定。
6、同板差超差产生原因:⑴铸轧辊辊型不对称;⑵铸轧辊两侧辊缝不一致;⑶铸轧机设备发生故障。
消除办法:⑴保证铸轧辊辊型符合要求;⑵调整两侧辊缝的距离;⑶保证铸轧机设备工作稳定。
7、粘辊产生原因:⑴铸轧速度过快;⑵冷却强度低;⑶烧火喷烟润滑出故障。
消除办法:⑴降低铸轧速度;⑵提高冷却强度;⑶保证喷烟润滑正常工作。
8、非金属压入产生原因:⑴供料咀损坏,其颗粒进入铸轧板;⑵喷烟润滑,其烟量过大,黑烟粉粘在辊面上;消除办法:⑴及时更换供料咀;⑵控制好喷烟量及烟雾颗粒。
9、大晶粒产生原因:⑴熔体温度高,局部过热;⑵熔体保温时间过长;⑶轧辊冷却强度低。
消除办法:⑴严格控制熔体温度;⑵缩短熔体保温时间,提高轧辊冷却强度;⑶控制好Al—Ti—B细化剂使用量。
10、腐蚀产生原因:⑴铸轧卷存放时遇酸、碱、水等介质发生腐蚀;⑵铸轧卷在潮湿的环境中长期存放。
消除办法:⑴铸轧卷存放时避免与水等介质接触;⑵铸轧卷不适于长期存放,尽快使用。
11、化学成份不合格产生原因:⑴配料时计算错误;⑵炉料(如复化锭、废料混料)成份不合格;⑶合金转炉时洗炉不净。
消除办法:⑴准确配料;⑵使用成份合格的炉料;⑶快速分析不合格,要即时增加金属添加剂或补充纯铝锭。
⑷合金转炉时要充分洗炉。
12、松树枝状产生原因:⑴轧制时压下量过大,金属在辊间由于磨擦力大来不及流动而产生滑移;⑵轧制油粘度不适宜;⑶轧制时张力过小。
消除办法:⑴合理分配压下量;⑵对轧制油进行定期分析、检查;⑶轧制时控制好张力。
13、气泡产生原因:⑴铸轧区液体穴中含有氢气;⑵铸轧速度偏快;⑶氮气量不足,旋转除气装置故障,除氢效果不佳。
消除办法:⑴加强熔炼精炼除气;⑵适当降低铸轧速度;⑶保证氮气流量及纯洁度;⑷及时检查和清理除气装置。
14、压过划痕产生原因:⑴轧制前,铝板表面产生擦划伤;⑵轧制过程中,由于设备、导路造成擦划伤;⑶来料波浪大;⑷轧制时张力不稳定,使铝卷层间产生错动。
消除办法:⑴轧制过程中,精心操作,尽量避免铝卷与设备、导路碰撞;⑵控制好张力;⑶保证来料质量。
15、性能不符产生原因:⑴没有正确执行热处理工艺;⑵热处理设备工作不稳定;⑶仪表温差大,热电偶不良或测温位置不正确;⑷轧制工艺制度不合理,变形量不够;⑸铸轧板冶金组织不合格。
消除办法:⑴严格执行热处理工艺;⑵定期检修设备,使之处于稳定工作状态;⑶调整轧制工艺,保证足够的变形量;⑷及时修正仪表误差;⑸保证来料冶金组织符合要求。
16、印痕产生原因:⑴轧辊粘有金属残渣或工作辊面有缺陷,在板带上产生有规律的印痕;⑵牵引辊、压紧辊有缺陷或粘有金属屑;⑶产品表面有金属物带入轧辊内造成印痕。
消除办法:⑴及时清理导路,保持辊面洁净;⑵及时换辊。
17、油痕产生原因:⑴冷轧用轧制油粘度大或轧制油中混入机油;⑵空气清板器出现故障,轧制油未吹净;⑶退火温度使用不合格,除油工艺未用好,油未充分挥发。
消除办法:⑴调整轧制油添加剂的用量,保证粘度适宜;⑵减少轧制油中的机油含量,保证轧机润滑设备少漏机油。
⑶调准空气清板器的角度和流量;⑷定期更换轧制油。
18、过薄产生原因:⑴压下量调整不及时;⑵测厚仪系统发生故障;⑶厚度显示仪表有误差。
消除办法:⑴及时调整压下量;⑵定期检修测厚仪装置及仪表。
19、毛刺产生原因:⑴切边时剪刃不锐利;⑵切边时剪刃间隙调整的不合理;⑶切边时润滑不好。
消除办法:⑴及时更换剪刃;⑵合理调整剪刃间隙;⑶加强润滑。
20、金属压入产生原因:⑴轧制时金属屑进入铝板表面;⑵轧制时轧辊粘铝,然后又压入铝板内;⑶切边质量不好,边部毛刺压入铝板内;⑷清辊器发生故障。
消除办法:⑴保证来料表面清洁;⑵及时清理轧辊和导路;⑶提高切边质量,减少毛刺;⑷及时修理清辊器。
21、波浪产生原因:⑴辊缝调整不平衡,辊型不合理;⑵润滑冷却不均;⑶压下量分配不合理;⑷来料质量不好,同板差超标;⑸卷取时张力不均;⑹拉弯矫直时,延伸率选择不合理。
消除办法:⑴合理调整辊缝;⑵正确使用弯辊,控制辊型;⑶合理分配压下量;⑷保证来料同板差合格;⑸控制好卷取张力;⑹注意使用拉弯矫直时的延伸率。
22、划伤产生原因:⑴板带生产时与导路内突出物相互磨擦;⑵板片之间相互移动时,造成相互划伤。
消除办法:⑴生产前及时清理导路;⑵尽量避免生产时板带与硬物接触。
23、折伤产生原因:⑴板片包装时用力不均,产生折伤。
消除办法:⑴包装时用力均匀。
24、过厚产生原因:⑴压下量调整不及时;⑵测厚系统发生故障;⑶厚度显示仪表有误差。
消除办法:⑴及时调整压下量;⑵定期检查测厚仪装置及仪表。
25、擦伤产生原因:⑴铝卷层与层之间产生错动造成擦伤;⑵生产时与设备、导路接触造成擦伤;⑶轧制时张力控制不好。
消除办法:⑴开卷和卷取张力尽量一致;⑵控制好张力,保证张力合适、均匀;⑶包装、运输、存放过程中避免擦伤;⑷及时消除设备、导路中的凸起物。
26、过窄产生原因:⑴切边时,剪刀间距过小;⑵切边时,设备发生震动造成过窄;⑶园盘剪间距指示不准确。
消除办法:⑴切边时,准确调整剪刀间距;⑵及时检修设备及仪表。
板带材工艺废品种类及产生原因——摘自铝合金及其加工手册1.贯穿气孔熔铸品质不好2.表面气泡铸锭含氢量高组织疏松;铸块表面凹凸不平的地方有脏东西,装炉前没有擦净;蚀洗后,铸块与包铝板表面有蚀洗残留痕迹;加热时间过长或温度过高,铸块表面氧化;第一道焊合轧制时,乳液嘴没有闭严,乳液流到包铝板下面。
3.铸块开裂热轧时压下量过大,从铸锭端头开裂;铸块加热温度过高或过低。
4.力学性能不合格没有正确执行热处理制度或热处理设备不正常,空气循环不好;淬火时装料量大,盐浴槽温度不够时装炉,保温时间不足,没有达到规定温度即出炉;试验室采用的热处理制度或试验方法不正确;试样规格形状不正确,试样表面被破坏。
5.铸锭夹渣熔铸品质不好,板内夹有金属或非金属残渣。
6.撕裂润滑油成分不合格或乳液太浓,板片与轧辊间产生滑动,金属变形不均匀;没有控制好变形铝合金的状态代号1.范围本标准规定了变形铝合金的状态代号。
本标准适用于铝及铝加工产品。
2.基本原则2.1基础状态代号用一个英文大写字母表示。
2.2细分状态代号采用基础状态代号后跟一位或多位阿拉伯数字表示。
2.3基本状态代号基本状态分为5种,如表达式所示3.细分状态代号3.1 H的细分状态在字母H后面添加两位阿拉伯数字(称作HXX状态),或三位阿拉伯数字(称作HXXX状态)表示H的细分状态。
3.1.1 HXX状态3.1.1.1 H后面的第1位数字表示获得该状态的基本处理程序,如下所示:H1—单纯加工硬化处理状态。
适用于未经附加热处理,只经加工硬化即获得所需强度的状态。
H2—加工硬化及不完全退火的状态。
适用于加工硬化程度超过成品规定要求后,经不完全退火,使强度降低到规定指标的产品。
对于室温下自然时效软化的合金,H2与对应的H3具有相同的最小极限抗拉强度值;对于其它合金,H2与对应的H1具有相同的最小极限抗拉强度值,但延伸率比H1稍高。
H3—加工硬化及稳定化处理的状态。
适用于加工硬化后经热处理或由于加工过程中受热作用致使其力学性能达到稳定的产品。
H3状态仅适用于在室温下逐渐时效软化(除非经稳定化处理)的合金。
H4—加工硬化及涂漆处理的状态。
适用于加工硬化后,经涂漆处理导致了不完全退火的产品。
3.1.1.2 H后面的第2位数字表示产品的加工硬化程度。
数字8表示硬状态。
通常采用O状态的最小抗拉强度与表2 规定的强度差值之和,来规定HX8的最小抗拉强度值。
对于O(退火)和HX8状态之间的状态,应在HX代号后分别添加从1到7的数字来表示,在HX后添加数字9表示比HX8加工硬化程度更大的超硬状态,各种HXX细分状态代号及对应的加工硬化程度如表3所示:表2 HX8状态与O状态的最小抗拉强度差值表3 HXY细分状态代号与加工硬化程度HXXX状态代号如下所示:a) H111适用于最终退火后又进行了适量的加工硬化,但加工硬化程度又不及H11状态的产品。
b)H112适用于热加工成型的产品。
该状态产品的力学性能有规定要求。
c)H116适用于镁含量≥4.0%的5XXX系合金制成的产品。
这些产品具有规定的力学性能和抗剥落腐蚀性能要求。
d)花纹板的状态代号花纹板的状态代号和其对应的、压花前的板材状态代号如表4所示:在字母T后面添加一位或多位阿拉伯数字表示T的细分状态。
3.2.1 TX状态在T后面添加0~10的阿拉伯数字,表示细分状态(称作TX状态)如表5所示。
T后面的数字表示对产品的茶杯处理程序。
在TX状态代号后面再添加一位阿拉伯数字(称作TXX状态),或添加两位阿拉伯数字(称作TXXX状态),表示经过了明显改变产品特性(如力学性能、抗腐蚀性能等)的特定工艺处理的状态,如表6所示。
在上述TX或TXX或TXXX状态代号后面添加“51”、或“510”、或“511”或“52”或“54”表示经历了消除应力处理的产品状态代号,如表7所示。
正如T的消除应力状态代号表示方法,可在W状态代号后面添加相同的数字(51、52、54),以表示不稳定的固溶热处理及消除应力状态。
附录A(提示的附录)1.点腐蚀点腐蚀又称为孔腐蚀,是在金属上产生针尖状、点状、孔状的一种为局部的腐蚀形态。
点腐蚀是阳极反应的一种独特形式,是一种自催化过程,即点腐蚀孔内的腐蚀过程造成的条件既促进又足以维持腐蚀的继续进行。