硫化曲线
橡胶硫化曲线

橡胶硫化曲线橡胶硫化曲线橡胶硫化是指将天然橡胶或合成橡胶中的双键与硫黄反应,形成交联结构,从而使橡胶具有弹性和耐热性的过程。
在橡胶生产中,硫化曲线是评价橡胶硫化程度的重要指标之一。
本文将介绍橡胶硫化曲线的定义、影响因素以及应用。
一、定义1.1 概念橡胶硫化曲线是指在一定条件下,测量不同时间内橡胶样品的硬度变化,并绘制出的曲线。
1.2 测量方法通常使用万能试验机或热压机进行测量。
在测量过程中,将样品放置在试验机或热压机中,在一定时间内加热并施加压力,测量样品不同时间点的硬度值,并绘制出相应时间和硬度值之间的曲线。
二、影响因素2.1 硫化剂种类和用量不同种类和用量的硫化剂对橡胶硫化速率和程度都有影响。
使用过多的硫会导致过交联,硫化速率过快,形成硬而脆的橡胶;而使用过少的硫则会导致交联不足,橡胶弹性差。
2.2 硫化温度和时间硫化温度和时间也是影响橡胶硫化曲线的重要因素。
通常情况下,较高的温度和较长的时间可以促进橡胶的交联反应,提高硫化程度。
但过高的温度和时间会导致橡胶老化、劣化等问题。
2.3 混炼工艺混炼工艺对橡胶硫化曲线也有一定影响。
在混炼过程中加入助剂可以改善橡胶的加工性能和耐热性能,但同时也可能影响硫化反应速率和程度。
三、应用3.1 评价橡胶品质通过测量橡胶样品在不同时间内的硬度变化并绘制出相应曲线,可以评价橡胶的硫化程度和品质。
通常情况下,合格的橡胶样品应该具有较平缓且充分的硫化曲线,并且在一定时间内硬度值应该稳定。
3.2 指导生产橡胶硫化曲线也可以用于指导橡胶生产过程中的操作。
通过对不同硫化条件下的硫化曲线进行比较,可以确定最佳的硫化温度、时间和硫化剂种类和用量等参数,从而提高橡胶生产效率和品质。
3.3 研究交联反应机理橡胶硫化曲线还可以用于研究交联反应机理。
通过对不同时间点的橡胶样品进行分析,可以了解交联反应的速率和程度,并探索交联反应的机理。
这对于深入了解橡胶材料的性质和优化橡胶生产工艺都具有重要意义。
硫化曲线t10和t90

硫化曲线t10和t90硫化曲线是用来研究橡胶硫化过程的一种实验方法,通过观察硫化曲线的变化,可以了解橡胶硫化的速度、硫化程度以及最佳硫化条件等信息。
在硫化曲线中,t10和t90是两个重要的参数,它们分别表示橡胶硫化开始和结束的时间点。
本文将深入探讨硫化曲线中的t10和t90参数的意义,以及它们在橡胶硫化过程中的应用。
第一部分:硫化曲线的定义和意义硫化曲线是用来描述橡胶硫化过程中硫化程度随时间的变化。
通常,硫化曲线的横轴表示时间,纵轴表示硫化程度,硫化程度通常用硫化度或者硬度来表示。
硫化曲线的形状和特征可以反映出橡胶硫化的速度和程度,对橡胶的性能和质量有重要的影响。
t10和t90是硫化曲线中的两个重要时间点。
t10表示橡胶开始硫化的时间点,通常也称为10%硫化时间;t90表示橡胶硫化完成的时间点,通常也称为90%硫化时间。
这两个时间点对于研究橡胶硫化过程的速度和程度具有重要的意义。
第二部分:t10和t90在橡胶硫化过程中的应用1.硫化速度的评估t10和t90可以用来评估橡胶的硫化速度。
硫化速度快的橡胶,t10和t90的数值会比较小,反之则较大。
通过比较不同橡胶的t10和t90数值,可以了解不同橡胶的硫化速度的差异,进而选择最适合的橡胶材料。
2.硫化程度的控制t10和t90还可以用来控制橡胶的硫化程度。
通过控制硫化曲线中的t10和t90参数,可以调整橡胶的硫化程度,从而满足不同产品对橡胶硫化程度的要求。
例如,对于一些需要较高硫化程度的橡胶制品,可以通过延长t90时间来提高硫化程度。
3.工艺条件的优化t10和t90还可以用来优化橡胶硫化的工艺条件。
通过调整硫化曲线中的t10和t90参数,可以确定最佳的硫化温度、硫化时间和硫化剂用量等工艺条件,以获得最佳的硫化效果。
第三部分:如何测试t10和t90要测试橡胶的t10和t90参数,通常可以采用动态硫化曲线分析仪进行实验。
在实验中,先将橡胶样品置于硫化机中,然后加入硫化剂和促进剂,在一定的温度和时间条件下进行硫化。
eva硫化曲线
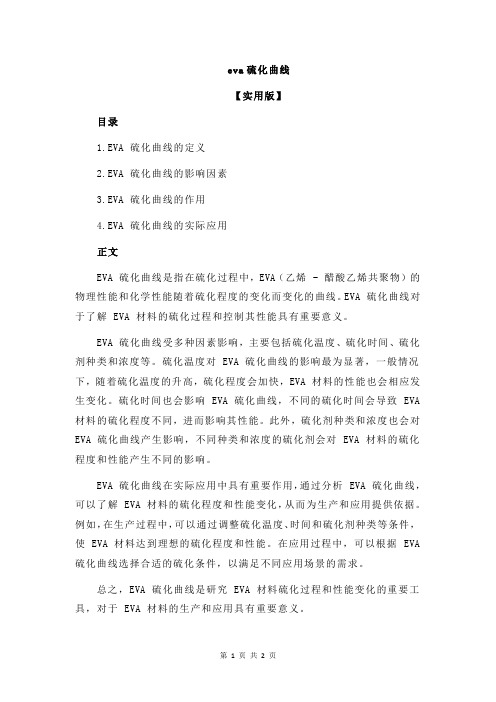
eva硫化曲线
【实用版】
目录
1.EVA 硫化曲线的定义
2.EVA 硫化曲线的影响因素
3.EVA 硫化曲线的作用
4.EVA 硫化曲线的实际应用
正文
EVA 硫化曲线是指在硫化过程中,EVA(乙烯 - 醋酸乙烯共聚物)的物理性能和化学性能随着硫化程度的变化而变化的曲线。
EVA 硫化曲线对于了解 EVA 材料的硫化过程和控制其性能具有重要意义。
EVA 硫化曲线受多种因素影响,主要包括硫化温度、硫化时间、硫化剂种类和浓度等。
硫化温度对 EVA 硫化曲线的影响最为显著,一般情况下,随着硫化温度的升高,硫化程度会加快,EVA 材料的性能也会相应发生变化。
硫化时间也会影响 EVA 硫化曲线,不同的硫化时间会导致 EVA 材料的硫化程度不同,进而影响其性能。
此外,硫化剂种类和浓度也会对EVA 硫化曲线产生影响,不同种类和浓度的硫化剂会对 EVA 材料的硫化程度和性能产生不同的影响。
EVA 硫化曲线在实际应用中具有重要作用,通过分析 EVA 硫化曲线,可以了解 EVA 材料的硫化程度和性能变化,从而为生产和应用提供依据。
例如,在生产过程中,可以通过调整硫化温度、时间和硫化剂种类等条件,使 EVA 材料达到理想的硫化程度和性能。
在应用过程中,可以根据 EVA 硫化曲线选择合适的硫化条件,以满足不同应用场景的需求。
总之,EVA 硫化曲线是研究 EVA 材料硫化过程和性能变化的重要工具,对于 EVA 材料的生产和应用具有重要意义。
eva硫化曲线

eva硫化曲线
EV A(乙烯-醋酸乙烯共聚物)是一种常用的热塑性弹性体材料,它具有良好的耐候性、耐化学腐蚀性和机械性能。
硫化是指通过加入硫化剂将EV A材料中的双键交联成三维网络结构,从而增加其强度和耐热性。
硫化曲线是描述EV A材料硫化过程中物理性质变化的曲线图。
它通常以硫化时间为横坐标,以物理性质(如硬度、拉伸强度等)为纵坐标,展示了随着硫化时间的增加,EV A材料的性能变化情况。
一般来说,硫化曲线可以分为以下几个阶段:
1. 潜伏期(Induction Period):在开始硫化时,材料的物理性质并不明显改变,此阶段也被称为潜伏期。
在这个阶段,硫化剂与EV A材料中的双键发生反应,形成临时交联点。
2. 加速期(Acceleration Period):随着硫化时间的增加,临时交联点逐渐增多,材料开始出现明显的物理性质变化。
此阶段的硫化速度较快,材料的硬度和强度迅速提高。
3. 稳定期(Plateau Period):当临时交联点达到一定数量时,EV A材料的硬度和强度开始趋于稳定。
此阶段的硫化速度减缓,材料的物理性质变化不再明显。
4. 过硫化期(Overcure Period):如果硫化时间过长,材料可能会出现过硬化现象,导致物理性质下降。
这个阶段需要注意控制硫化时间,避免过度硫化。
需要注意的是,不同的EV A材料和硫化条件下的曲线形状可能有所差异。
因此,在具体的应用中,根据需要选择适当的硫化条件,以获得所需的物理性能。
1。
促进剂的硫化曲线

促进剂的硫化曲线
硫化曲线指的是在橡胶硫化过程中,不同时间和温度下橡胶中硫化程度的变化曲线。
硫化是橡胶加工工艺中非常重要的步骤,通过硫化可以使橡胶获得优良的弹性、耐热、耐腐蚀等性能。
在硫化曲线中,通常可以分为几个阶段:
1. 延迟期(t0到t1):橡胶在橡胶-硫混合物中,尚未出现硫
化反应,此时橡胶材料保持弹性。
2. 加速期(t1到t2):在此阶段,橡胶中的硫化反应开始加速,硫化速度逐渐增加,橡胶材料的硫化程度也逐渐增加。
橡胶开始变得发硬。
3. 高速期(t2到t3):硫化反应在此阶段达到最高速度,橡
胶材料的硫化程度迅速增加。
此时橡胶开始形成网络结构,整体硬化。
4. 减速期(t3到t4):硫化反应速度开始减慢,硫化程度的
增加趋于平缓。
橡胶变得更加耐磨和耐热。
5. 稳定期(t4到t5):硫化反应基本结束,硫化程度变化很小。
橡胶材料的硫化程度达到最高水平。
不同类型的橡胶和硫化体系会有不同的硫化曲线特征,这取决于使用的促进剂、硫化温度和时间等因素。
硫化曲线的了解有助于合理选择硫化条件,以获得符合要求的橡胶制品。
图2-1 硫化曲线(Curing curve
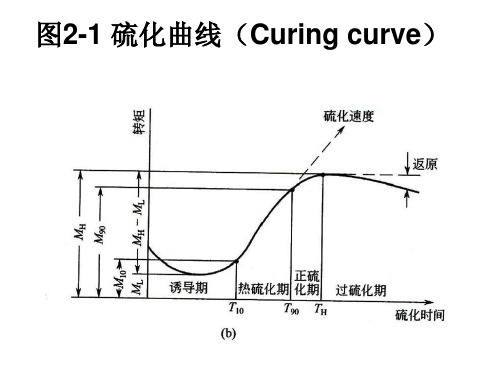
2.2橡胶的无促进剂硫黄硫化 橡胶的无促进剂硫黄硫化
一、硫黄的品种及用量 (一)品种 一 品种 1、粉末硫黄 、 硫黄在橡胶中的溶解度随温度升高而增大。 硫黄在橡胶中的溶解度随温度升高而增大。
配合剂在胶料的 配合量超过了它的 溶解度达到过饱和, 溶解度达到过饱和, 就从胶料内部析出 到表面上, 到表面上,形成一 层白 霜。
CH3 CH2 C CH CH CH2 Sx R
CH3 C CH CH2 CH2
CH3 C CH CH CH
CH3 C CH CH2
• 五.硫黄硫化胶的结构与性能 硫黄硫化胶的结构与性能
• 1.结构 硫黄硫化橡胶时,硫黄在橡胶大分子间 结构 硫黄硫化橡胶时, 形成单S键、双硫键或多硫键,同时还生成大分 形成单 键 双硫键或多硫键, 子内部的单硫键或多硫键,但以多硫交联键最多。 子内部的单硫键或多硫键,但以多硫交联键最多。 • 2.性能 多硫交联键不稳定,易分解重排,所以硫 性能 多硫交联键不稳定,易分解重排, 化胶的耐热性较差。 化胶的耐热性较差。
硫化曲线( 图2-1 硫化曲线(Curing curve) )
硫化曲线( 图2-1 硫化曲线(Curing curve) )
(二)硫化历程图 二 硫化历程图
• 根据硫化历程分析,可将硫化曲线分成四个阶段: 根据硫化历程分析,可将硫化曲线分成四个阶段: • 焦烧阶段 热硫化开始前的延迟作用时间,反映 焦烧阶段: 热硫化开始前的延迟作用时间, 了加工安全性。 了加工安全性。该阶段取决于促进剂的品种和用 量。 • 热硫化阶段: 硫化反应的交联阶段,逐渐产生网 热硫化阶段 硫化反应的交联阶段, 络结构, 络结构,该阶段斜率的大小反映了硫化速度的快 慢。 • 平坦硫化阶段 交联反应基本完成。硫化平坦期的 平坦硫化阶段:交联反应基本完成。 交联反应基本完成 长短取决于胶料配方。 长短取决于胶料配方。 • 过硫化阶段 相当于硫化反应阶段中网构形成的后 过硫化阶段:相当于硫化反应阶段中网构形成的后 期。
硫化曲线t10和t90

硫化曲线t10和t90硫化曲线是用来描述橡胶在硫化过程中的变化规律的一项重要指标。
其中,t10和t90分别表示橡胶硫化过程中10%和90%硫化完成所需的时间。
本文将对硫化曲线中的t10和t90进行详细探讨,旨在帮助读者深入了解橡胶硫化的过程和特点。
1. 硫化曲线简介硫化曲线是通过在一定温度下跟踪记录橡胶硫化过程中的硫化度变化而得到的一条曲线。
它可以帮助我们了解橡胶在硫化过程中的行为和性能变化。
2. t10的意义与描述t10是硫化曲线中的一个重要参数,它表示橡胶硫化过程中10%硫化完成所需的时间。
一般来说,t10的数值越小,说明橡胶硫化速度越快,反之则表示硫化速度较慢。
3. t90的意义与描述t90是硫化曲线中的另一个重要参数,它表示橡胶硫化过程中90%硫化完成所需的时间。
与t10相似,t90的数值越小,说明橡胶硫化速度越快,反之则表示硫化速度较慢。
4. 影响t10和t90的因素橡胶硫化的过程受多种因素的影响,这些因素也会对硫化曲线中的t10和t90产生影响。
主要的影响因素包括硫化剂种类和用量、硫化温度、硫化时间等。
5. t10和t90的应用由于t10和t90可以反映出橡胶硫化速度的快慢,因此在橡胶制品的生产过程中具有重要的应用价值。
生产者可以通过控制硫化剂和硫化条件,合理调整t10和t90的数值,以满足不同用途橡胶制品的要求。
6. 硫化曲线的优化通过优化硫化剂的选择和合理控制硫化条件,可以有效提高硫化曲线中的t10和t90数值,进而改善橡胶制品的性能。
例如,使用高效硫化体系和适当的硫化温度,可在保持硫化速度的同时,避免橡胶材料受到过度硫化而引起的性能变化。
7. 硫化曲线的测试方法硫化曲线的测试是通过在实验室中使用硫化仪进行的。
根据硫化曲线测试结果,可以计算得到t10和t90的数值,进而进行相关的分析和判断。
总结:硫化曲线中的t10和t90是描述橡胶硫化过程的重要指标,通过对其数值的分析和研究,可以帮助我们更好地了解橡胶硫化的过程和特点。
硫化曲线

NBR/AT 硫化曲线
配方
硫化配方:ZnO 5g SA 1g DM 1.5g TT 0.5g S 2g 4010NA 1g 硫化工艺:145℃×T 90
0.0
0.2
0.4
0.6
0.8
1.0
1.2
1.4
扭矩/N .M
时间/min
硫化曲线ML——最低转矩,N/m(kgf/cm)
硫化曲线MH——到达规定时间之后仍然不出现平坦曲线或最高转矩的硫化曲线,所达到的最高转矩N/m(kgf/cm)
硫化曲线TS1——从实验开始到曲线由最低转矩上升0.1 N/m(kgf/cm)时所对应的时间,MIN
硫化曲线TS2——从实验开始到曲线由最低转矩上升0.2 N/m(kgf/cm)时所对应的时间,MIN
硫化曲线TC(x)——试样达到某一硫化程度所需要的时间,即试样转矩达到ML+X (MH-ML)时
所对应的时间,MIN(注:如X取值0.5,即TC50,X取.9,即TC90)
3.4.硫检参数的意义:
硫化曲线ML:表示胶料的流动性,ML越低,流动性越好,反之,越差。
硫化曲线MH:表征胶料的胶料的剪切模数、硬度、定伸强度和交联密度,一般MH越低,硬度越低,MH越高,硬度越高。
橡胶信息网,
硫化曲线TS2:表征胶料的操作安全性,TS2越短,表示胶料越容易发生死料,产品在生产时容易产生缺料不良。
反之,TS2越长,虽然操作安全性提高,但是产效会变低,成本会增加很多,故TS2对胶料的加工、配方设计具有很重要的意义。
硫化曲线TC90:主要用来评估胶料在成型生产时的一次加硫条件,TC90过长表示硫化速度偏慢,会导致产品硬度低,产效低。
橡胶硫化曲线
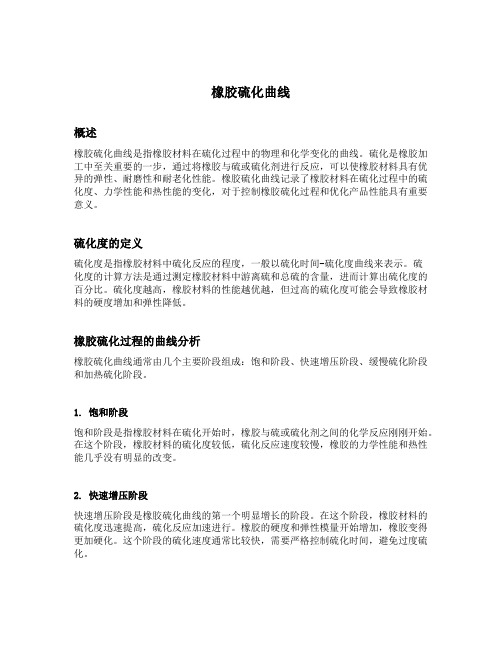
橡胶硫化曲线概述橡胶硫化曲线是指橡胶材料在硫化过程中的物理和化学变化的曲线。
硫化是橡胶加工中至关重要的一步,通过将橡胶与硫或硫化剂进行反应,可以使橡胶材料具有优异的弹性、耐磨性和耐老化性能。
橡胶硫化曲线记录了橡胶材料在硫化过程中的硫化度、力学性能和热性能的变化,对于控制橡胶硫化过程和优化产品性能具有重要意义。
硫化度的定义硫化度是指橡胶材料中硫化反应的程度,一般以硫化时间-硫化度曲线来表示。
硫化度的计算方法是通过测定橡胶材料中游离硫和总硫的含量,进而计算出硫化度的百分比。
硫化度越高,橡胶材料的性能越优越,但过高的硫化度可能会导致橡胶材料的硬度增加和弹性降低。
橡胶硫化过程的曲线分析橡胶硫化曲线通常由几个主要阶段组成:饱和阶段、快速增压阶段、缓慢硫化阶段和加热硫化阶段。
1. 饱和阶段饱和阶段是指橡胶材料在硫化开始时,橡胶与硫或硫化剂之间的化学反应刚刚开始。
在这个阶段,橡胶材料的硫化度较低,硫化反应速度较慢,橡胶的力学性能和热性能几乎没有明显的改变。
2. 快速增压阶段快速增压阶段是橡胶硫化曲线的第一个明显增长的阶段。
在这个阶段,橡胶材料的硫化度迅速提高,硫化反应加速进行。
橡胶的硬度和弹性模量开始增加,橡胶变得更加硬化。
这个阶段的硫化速度通常比较快,需要严格控制硫化时间,避免过度硫化。
3. 缓慢硫化阶段缓慢硫化阶段是橡胶硫化曲线的第二个增长缓慢的阶段。
在这个阶段,橡胶材料的硫化度继续提高,但速度相对较慢。
橡胶的硬度和弹性模量继续增加,但增速变得较低。
这个阶段的硫化时间较长,有助于橡胶的硫化反应更加完全,提高产品的性能。
4. 加热硫化阶段加热硫化阶段是橡胶硫化过程的最后一个阶段。
在这个阶段,橡胶材料的硫化度趋于饱和,硫化反应几乎停止。
橡胶的硬度和弹性模量基本稳定,橡胶材料达到最终的硫化状态。
这个阶段的硫化时间较长,可以进一步提高橡胶的性能稳定性。
橡胶硫化曲线的应用橡胶硫化曲线的研究对于优化橡胶制品的性能具有重要意义。
硫化曲线t10和t90
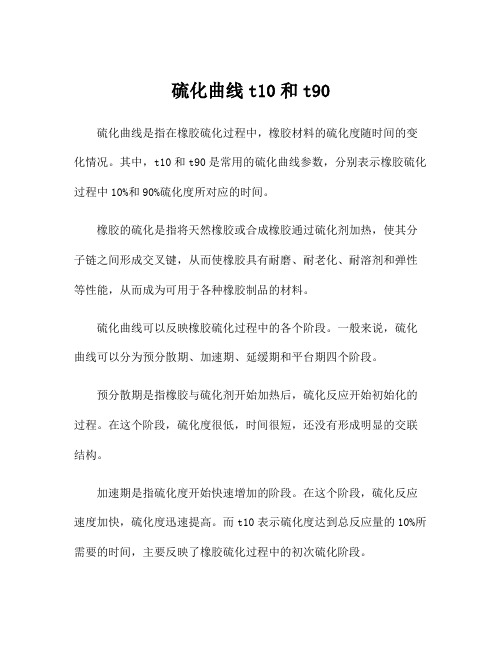
硫化曲线t10和t90硫化曲线是指在橡胶硫化过程中,橡胶材料的硫化度随时间的变化情况。
其中,t10和t90是常用的硫化曲线参数,分别表示橡胶硫化过程中10%和90%硫化度所对应的时间。
橡胶的硫化是指将天然橡胶或合成橡胶通过硫化剂加热,使其分子链之间形成交叉键,从而使橡胶具有耐磨、耐老化、耐溶剂和弹性等性能,从而成为可用于各种橡胶制品的材料。
硫化曲线可以反映橡胶硫化过程中的各个阶段。
一般来说,硫化曲线可以分为预分散期、加速期、延缓期和平台期四个阶段。
预分散期是指橡胶与硫化剂开始加热后,硫化反应开始初始化的过程。
在这个阶段,硫化度很低,时间很短,还没有形成明显的交联结构。
加速期是指硫化度开始快速增加的阶段。
在这个阶段,硫化反应速度加快,硫化度迅速提高。
而t10表示硫化度达到总反应量的10%所需要的时间,主要反映了橡胶硫化过程中的初次硫化阶段。
延缓期是指硫化度的增加开始变缓的阶段。
在这个阶段,橡胶的硫化速度逐渐减慢,硫化反应的进展变得缓慢。
平台期是指硫化度基本上停滞在某个数值的阶段。
在这个阶段,橡胶硫化基本上已经完成,硫化反应进一步进行的速度很慢,硫化度的变化不明显。
而t90表示硫化度达到总反应量的90%所需要的时间,主要反映了橡胶硫化过程中的最后硫化阶段。
在橡胶制品的生产过程中,橡胶硫化的质量和性能对制品的质量和使用寿命有着重要的影响。
硫化曲线的形状和参数可以帮助生产者了解和控制橡胶硫化过程,以获得符合要求的制品。
对于不同的橡胶材料和硫化剂,硫化曲线的形状和参数也会有所不同。
一些橡胶材料在硫化过程中可能存在缩小、损失热和硫化剂流失等现象,这些会对硫化曲线的形状产生影响。
硫化曲线的形状和参数对于研究橡胶的硫化机理和调控硫化过程非常重要。
例如,加速期的长度可以反映橡胶硫化速度的快慢,而延缓期的长度可以反映硫化反应的稳定性和均匀性。
通过对硫化曲线的观察和分析,可以优化橡胶硫化工艺,改善橡胶制品的质量和性能。
硫化曲线介绍精编

硫化曲线介绍精编 Document number:WTT-LKK-GBB-08921-EIGG-22986一. 流变仪之各种曲线之原理:1. S*粘弹曲线的原理:根据转子或转盘转动时,因胶料架桥作用所产生之扭矩变化曲线。
S*= S’2+S”2δ=ab-ac2. S’弹性曲线的原理:S’=S* X cosδ,S’ 可得到相关之加硫条件参数。
3. S”粘性曲线的原理:S”=S* X sinδ ,S” 可得到相关之粘性参数。
粘性曲线可看出橡胶之加工性。
4. Loss Angle 动的损失角曲线的原理:δ=ab-ac5. tan δ粘弹性比值曲线:tan δ=S”/S’6. 上、下模温度曲线:测试进行中温度变化记录曲线。
7. 硫化速率曲线:架桥过程中相邻两点间之斜率值之曲线。
8. 粘弹综合曲线:S*= S’2+S”2二. 流变仪图形及数据之判读及运用:流变仪之标准硫化曲线如下:S* S’S ” δab ac δ a c b其中共分为三大区:1. 第一区为加工区:在此一时间内橡胶具有可塑性。
此段时间愈长愈易于加工,但产能将降低,扭力值愈低橡胶流动性愈好。
2. 第二区为硫化区:在此一时间内为架桥过程。
以相同的材料而言此段时间愈长,物性通常会较佳。
3. 第三区为物理性质区:此一区段可判读成品之物理性质。
由曲线中可得数据说明如下:时间扭力1.焦烧时间(TS – Time of Scorch):一般而言国人的习惯此数据取2,这个时间通常称之为加工安全时间,也就是超过此时间橡胶已架桥失去了流动性,这是衡量模内流动时间的尺度,在低温下,它是衡量加工性能的指数,它与门尼焦烧相似。
事实上,如果流变仪和门尼试验的温度相同时,流变仪的TS2和门尼的TS35有密切关系。
以TS2为例,其定义为最低扭力值加2个单位所对应的时间:MS2=ML+2 ?此点所对应的时间(TS)2.硫化时间(TC – Time of Curing):一般而言国人的习惯此数据取90,这个时间通常称之为最适加硫时间,也就是说当加硫至此一时间就可自模具中将成品取出,其定义为加硫至90%所需之时间,其计算公式为:MC90=(MH-ML)*90%+ML?此点所对应之时间(TC)3.最低扭力值(ML – Min Torque):此数据可作为加工特性之参考。
eva硫化曲线

eva硫化曲线摘要:一、引言二、EVA 硫化曲线的定义和作用三、EVA 硫化曲线的类型1.高温硫化曲线2.常温硫化曲线3.低温硫化曲线四、EVA 硫化曲线的应用领域1.橡胶制品行业2.塑料制品行业3.涂料行业五、EVA 硫化曲线对制品性能的影响1.硬度2.强度3.耐磨性4.耐老化性六、EVA 硫化曲线的测量方法1.实验方法2.计算方法七、EVA 硫化曲线的调整与优化1.调整硫化温度2.调整硫化时间3.添加硫化剂八、结论正文:一、引言EVA(乙烯- 醋酸乙烯酯共聚物)是一种具有广泛应用的塑料材料,具有良好的柔韧性、耐磨性、耐老化性和透明性。
硫化是EVA 材料加工过程中的一个重要环节,通过硫化,可以改善EVA 材料的性能,使其更适合各种应用场景。
EVA 硫化曲线是描述硫化过程中EVA 材料性能变化的重要参数,对EVA 材料的性能和应用有着重要影响。
二、EVA 硫化曲线的定义和作用EVA 硫化曲线是指在硫化过程中,EVA 材料的硬度、强度、耐磨性等性能随硫化时间变化的曲线。
它反映了EVA 材料在硫化过程中的性能变化规律,为EVA 材料的加工提供了重要的参考依据。
三、EVA 硫化曲线的类型根据硫化温度的不同,EVA 硫化曲线可以分为高温硫化曲线、常温硫化曲线和低温硫化曲线。
1.高温硫化曲线:硫化温度一般在150℃以上,这种硫化曲线可以使EVA 材料具有更高的硬度和强度,但耐磨性和耐老化性较差。
2.常温硫化曲线:硫化温度一般在60-120℃,这种硫化曲线可以使EVA 材料具有较好的综合性能,广泛应用于橡胶制品和塑料制品行业。
3.低温硫化曲线:硫化温度一般在40-60℃,这种硫化曲线可以使EVA 材料具有较好的柔韧性和耐老化性,但硬度和强度较低。
四、EVA 硫化曲线的应用领域EVA 硫化曲线在橡胶制品、塑料制品和涂料等行业有着广泛的应用。
通过调整EVA 硫化曲线,可以满足不同制品的性能要求,提高制品的质量和使用寿命。
硫化曲线t10和t90
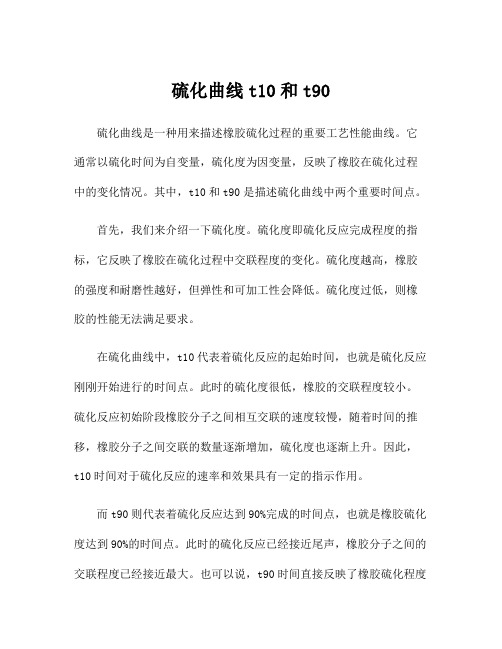
硫化曲线t10和t90硫化曲线是一种用来描述橡胶硫化过程的重要工艺性能曲线。
它通常以硫化时间为自变量,硫化度为因变量,反映了橡胶在硫化过程中的变化情况。
其中,t10和t90是描述硫化曲线中两个重要时间点。
首先,我们来介绍一下硫化度。
硫化度即硫化反应完成程度的指标,它反映了橡胶在硫化过程中交联程度的变化。
硫化度越高,橡胶的强度和耐磨性越好,但弹性和可加工性会降低。
硫化度过低,则橡胶的性能无法满足要求。
在硫化曲线中,t10代表着硫化反应的起始时间,也就是硫化反应刚刚开始进行的时间点。
此时的硫化度很低,橡胶的交联程度较小。
硫化反应初始阶段橡胶分子之间相互交联的速度较慢,随着时间的推移,橡胶分子之间交联的数量逐渐增加,硫化度也逐渐上升。
因此,t10时间对于硫化反应的速率和效果具有一定的指示作用。
而t90则代表着硫化反应达到90%完成的时间点,也就是橡胶硫化度达到90%的时间点。
此时的硫化反应已经接近尾声,橡胶分子之间的交联程度已经接近最大。
也可以说,t90时间直接反映了橡胶硫化程度的快慢与充分性。
通常情况下,t90时间越短,说明橡胶的硫化反应速率快且充分,橡胶材料的性能也会相应提升。
硫化曲线的形状通常可分为四个阶段:橡胶化、股化、稳态硫化和过硫化。
在橡胶化阶段,曲线可以近似看作是一条直线,此时的硫化度较低。
股化阶段是曲线的斜率逐渐减小的阶段,此时的硫化度随时间的增长而逐渐上升。
稳态硫化阶段是指曲线呈现出平缓的状态,此时橡胶的硫化度已经接近最大值。
过硫化阶段是曲线开始出现下降趋势,此时橡胶的硫化度开始下降,原因往往是交联程度过高导致橡胶断裂。
通过观察硫化曲线的t10和t90时间,可以评估硫化反应的速率和完成程度。
通常来说,t10时间越短,说明橡胶的硫化反应速率快;而t90时间越短,说明橡胶的硫化程度充分。
因此,对于某些特定的应用领域,我们可以根据t10和t90时间的要求来优化橡胶材料的硫化工艺。
总结起来,硫化曲线中的t10和t90时间点是描述橡胶硫化过程的重要参数。
硫化曲线

如何解读硫化仪测得的硫化曲线硫化仪测定未硫化胶料硫化特性的原理:将未硫化胶料试样放入一个完全密封或几乎完全密封的模腔内,并使之保持在设定的试验温度下。
模腔有上、下两个部分,其中一部分以微小的摆角振荡。
振荡使试样产生剪切应变,测定试样对模腔的反作用转矩(力)。
此转矩(力)取决于胶料在硫化过程中产生的、随硫化时间长短而连续变化的剪切模量。
从胶料入模开始,硫化仪便自动记录反映胶料产生剪切应变的转矩的数值。
于是,便得到了一条转矩与时间的关系曲线,即硫化曲线。
其形状与设定的试验温度和胶料的特性有关。
(有的硫化仪用FL):最小转矩或力(N.m或N);(有的硫化仪用Fmax):在规定时间内达到的平坦、最大、最高转矩或力(N.m或N);(有的硫化仪用t10):也叫焦烧时间,即转矩达到ML+(MH-ML)*10%时所对应的时间;(有的硫化仪用t90): 也叫正硫化时间,即转矩达到ML+(MH-ML)*90%时所对应的时间,称为工艺正硫化时间。
硫化历程分为四个阶段:硫化诱导阶段,热硫化阶段,硫化平坦阶段和过硫化阶段。
什么是橡胶硫化压力?硫化压力在橡胶成型过程中起什么作用?橡胶件硫化的三大工艺参数是:温度、时间和压力。
其中硫化温度是对制品性能影响最大的参数,硫化温度对橡胶制品的影响的研究也比比皆是。
但对硫化压力比较少进行试验。
硫化压力是指,橡胶混炼胶在硫化过程中,其单位面积上所承受的压力。
一般情况下,除了一些夹布件和海绵橡胶外,其他橡胶制品在硫化时均需施加一定的压力。
橡胶硫化压力,是保证橡胶零件几何尺寸、结构密度、物理机械的重要因素,同时也能保证零件表面光滑无缺陷,达到橡胶制品的密封要求。
作用主要有以下几点:防止混炼胶在硫化成型过程中产生气泡,提高制品的致密性;提供胶料的充模流动的动力,使胶料在规定时间内能够充满整个模腔;提高橡胶与夹件(帘布等)附着力及橡胶制品的耐曲绕性能;4)提高橡胶制品的物理力学性能。
硫化压力的选取需要考虑如下几个方面的因素:1)胶料的配方;2)胶料可塑性的大小;3)成型模具的结构形式(模压,注压,射出等);4)硫化设备的类型(平板硫化机,注压硫化机,射出硫化机,真空硫化机等);5)制品的结构特点。
橡胶的硫化曲线分析

橡胶的硫化反应历程硫化历程是橡胶大分子链发生化学交联反应的过程包括橡胶分子与硫化剂及其他配合剂(主要是活性剂、促进剂)之间发生的一系列化学反应以及在形成网状结构时伴随发生的各种副反应。
硫化仪无转子硫化仪的结构示意图硫化曲线分成四个阶段,即1)焦烧阶段:热硫化开始前的延迟时间2)热硫化阶段:硫化反应的交联阶段,其斜率代表反应速度3)平坦硫化阶段:交联反应基本结束,熟化阶段(短化、重排、裂解),性能最佳4)过硫化阶段:胶料硫化在此阶段,可能出现三种形式1、焦烧期(ab段)焦烧期(诱导期):从胶料放入模具至出现轻微硫化的整个过程所需要的时间叫硫化诱导期,又称为焦烧时间。
焦烧(scorch):加有硫化剂的混炼胶在加工或停放过程中产生的早期硫化现象。
焦烧现象本质是硫化,胶料局部交联。
胶料焦烧后,流动性明显变差,甚至不能流动,后续加工工序无法正常进行。
诱导期反应了胶料的加工安全性。
诱导期短,加工安全性差;诱导期太长,会降低生产效率。
表征参数ts1——焦烧时间(scorchtime),从开始加热起,至胶料的转矩由最低值上升0.1N.m所需要的时间。
tc10——焦烧时间,从开始加热起,至胶料的转矩由最低值上升10个单位所需要的时间。
焦烧时间又分为操作焦烧时间:胶料在加工或停放过程中由于热积累效应所消耗的焦烧时间;剩余焦烧时间:胶料在模具内保持流动的时间。
操作焦烧时间长,剩余焦烧时间就短2、热硫化期(BC段)由焦烧点到工艺正硫化点(C点)所经历的阶段,即硫化反应过程的交联反应期。
曲线快速上升。
热硫化期特性参数:tc90——工艺正硫化时间,从开始加热起,至胶料的转矩由最低值上升90个单位所需要的时间。
斜率k——反映胶料硫化速度快慢,斜率越大,硫化速度越快CRI——加硫指数【CRI=100/(tc90—ts1)】,min-1,反映胶料硫化速度快慢,CRI值大,硫化速度快。
3、平坦硫化期(cd段)曲线保持水平所经历的时间长短,反映胶料在硫化过程中性能稳定性的高低。
eva硫化曲线
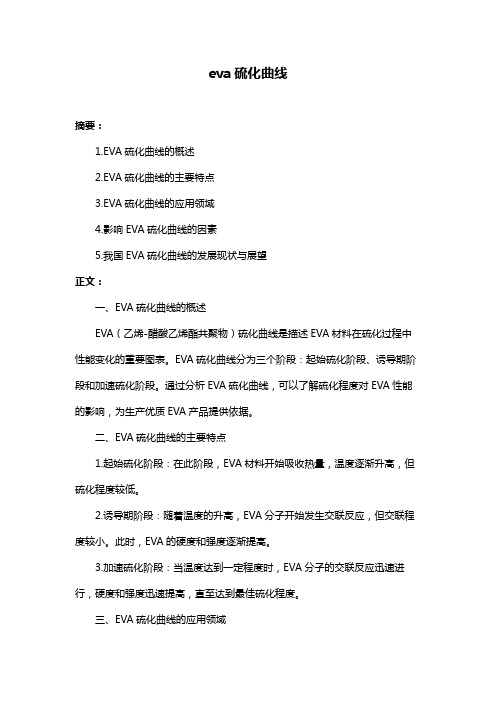
eva硫化曲线摘要:1.EVA硫化曲线的概述2.EVA硫化曲线的主要特点3.EVA硫化曲线的应用领域4.影响EVA硫化曲线的因素5.我国EVA硫化曲线的发展现状与展望正文:一、EVA硫化曲线的概述EVA(乙烯-醋酸乙烯酯共聚物)硫化曲线是描述EVA材料在硫化过程中性能变化的重要图表。
EVA硫化曲线分为三个阶段:起始硫化阶段、诱导期阶段和加速硫化阶段。
通过分析EVA硫化曲线,可以了解硫化程度对EVA性能的影响,为生产优质EVA产品提供依据。
二、EVA硫化曲线的主要特点1.起始硫化阶段:在此阶段,EVA材料开始吸收热量,温度逐渐升高,但硫化程度较低。
2.诱导期阶段:随着温度的升高,EVA分子开始发生交联反应,但交联程度较小。
此时,EVA的硬度和强度逐渐提高。
3.加速硫化阶段:当温度达到一定程度时,EVA分子的交联反应迅速进行,硬度和强度迅速提高,直至达到最佳硫化程度。
三、EVA硫化曲线的应用领域EVA硫化曲线在EVA制品生产中具有广泛的应用,如:橡胶制品、塑料制品、电缆绝缘层等。
通过研究EVA硫化曲线,可以优化生产工艺,提高产品质量。
四、影响EVA硫化曲线的主要因素1.硫化剂种类和用量:不同硫化剂的活性不同,对EVA硫化曲线形状有影响;硫化剂用量过多或过少,都会导致硫化不完全。
2.温度:温度对EVA硫化速率有很大影响,温度过高或过低都会导致硫化不完全。
3.压力:压力对EVA硫化也有一定影响,适当增加压力有利于提高硫化程度。
4.制品形状和结构:不同形状和结构的EVA制品,其硫化曲线可能有所不同。
五、我国EVA硫化曲线的发展现状与展望近年来,我国EVA产业得到了快速发展,技术水平不断提高。
在研究EVA 硫化曲线方面,我国已经取得了一定的成果,但与发达国家相比,仍有一定差距。
未来,我国应继续加大EVA硫化曲线研究力度,提高硫化技术水平,以满足日益增长的市场需求。
总之,EVA硫化曲线在EVA制品生产中具有重要意义。
硫化曲线

实验室中我最喜欢的仪器就是硫化仪了,简直就是一做配方的神器。
下面说的有一个前提,那就是每次测试的时候都要用一样的硫化温度,比如150度,再把NM轴的数值刻度固定住,比如NM的区间是0-35KG.CM。
一定要这么做,不然数据不具有可比性可重复性,你也不太可能从中间看出来什么。
(温度和扭矩数值自己根据自己工厂的需要设,这个很灵活的)1.硫化曲线上可以看焦烧和硫化时间,呵呵,地球人都知道。
2.硫化曲线可以看出活化体系有没有问题。
从硫化曲线的瞬时加速度的偏移可以看出活化体系是不足还是过量(硫化曲线的瞬时加速度=NM/该点时间),但是硫化曲线的瞬时加速度和活化体系关系不大,我说的是偏移,你也可以理解为加速度的加速度(其实可以用一个微积分的术语表达,这会儿一时想不起了),当偏移的变化很小或者几乎无变化的时候,活化剂不足。
3.硫化曲线可以看出硫化体系有没有问题,可以看出硫化剂是不是相对促进剂少了----会有剧烈的硫化返原;硫化剂少了交联度可能达不到,NM比较小。
促进剂多少可以从硫化曲线的瞬时加速度看出来,一般来说当T10-T60时间段瞬时加速度越大说明交联越快,但是当大到一定程度的时候,比如角度接近90度了,这样的胶料就有促进剂过多的嫌疑了。
促进剂过多会造成橡胶产品因为交联速度太快橡胶分子来不及顺应压力而舒展(形变滞后效应)进而内部因此凝聚了内应力,内应力的存在会造成产品带有变形,容易破裂,不耐老化等缺陷。
促进剂少了硫化慢,这个一般都能看出来的,但是硫化慢不一定是促进剂少了,这和胶料PH,添加的不正确防老剂(有的会吸收自由基)有关系。
4.可以看出防护体系有无问题。
呵呵,很多人在达到正硫化区间后就不会做下去了,很可惜,因为硫化曲线的硫化返原和橡胶的老化有一定的关系,一般来说正硫化区间越长越耐老化。
如果不是缺少硫化剂的原因,硫化返原越大,就是NM变化越大说明防老体系越不足,需要加防老剂了-----我甚至觉得看习惯了这个甚至都可以省略做70度X100HRS老化试验了,特别样品很急的时候。
硫化曲线

硫化曲线vulcanization curve;curing curve在某一温度下测定橡胶在硫化过程中某一物理性能与硫化时间关系的曲线。
一般情况下,用硫化胶的拉伸强度、扯断伸长率、定伸应力和硬度等分别对硫化时间作图,就可以得到硫化曲线。
目前通常用硫化仪直接绘出硫化曲线,由硫化曲线可以观察胶料硫化的整个过程,按橡胶交联情况的不同可分为:硫化诱导期、热硫化阶段、平坦硫化阶段和过硫阶段。
从硫化曲线可以求得胶料焦烧性能、硫化速率、最佳硫化时间、硫化平坦性以及抗过硫返原性能等。
优肯科技股份有限公司《橡胶工艺原理》杨清芝主编硫化曲线上的参数、硫化的各个阶段及其它们之间的关系见图2-8。
由田可见,在硫化温度下,开始转矩下降,也就是粘度下降,到最低点后又开始上升,这表示硫化的开始,随着硫化的进行,转矩不断上升并达到最大值。
从图2—o的硫化曲线上可见下列参数:ML(最小转矩);MH(最大转矩);TH(理论正硫化时间);M10:ML十(MH—ML)X 10%,T10(焦烧时间);M90:ML十(MH—ML)X 90%,T9O(工艺正硫化时间)。
图2—8中曲线上的各硫化阶段:诱导期,热硫化期,正硫化期,过硫化期。
在硫化反应开始前,胶料必须有充分的迟延作用时间以便进行混炼、压延、压出、成型及模压时充满模型。
一旦硫化开始,反应要迅速。
因此,硫化诱导期对橡胶加工生产安全至关重要.是生产加工过程的一个基本参数。
在热硫化阶段,橡胶与硫磺的交联反应迅速进行,曲线的斜率即硫化速率与交联键生成速度基本一致,并符合一级反应方程式。
从硫化时间对交联密度关系可得下列方程式,式中Vut——硫化时间为,时的交联密度;K ——交联反应速度常数;t ——硫化时间;ti ——硫化诱导时间;Vu ——交联密度;Vu∞——最大交联密度。
按照式(2—1)将Vut。
对硫化时间进行标绘.可得到图2—9所示的交联反应的动力学曲线,它与图2—8的热硫化段的硫化曲线相同。
光伏胶膜 硫化曲线
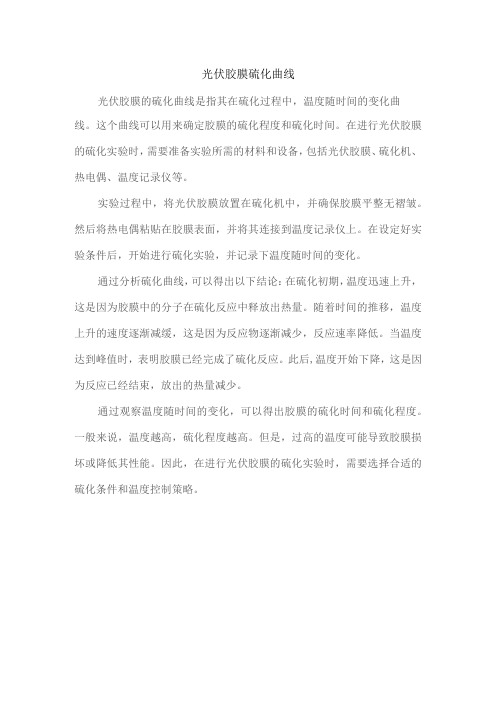
光伏胶膜硫化曲线
光伏胶膜的硫化曲线是指其在硫化过程中,温度随时间的变化曲
线。
这个曲线可以用来确定胶膜的硫化程度和硫化时间。
在进行光伏胶膜的硫化实验时,需要准备实验所需的材料和设备,包括光伏胶膜、硫化机、热电偶、温度记录仪等。
实验过程中,将光伏胶膜放置在硫化机中,并确保胶膜平整无褶皱。
然后将热电偶粘贴在胶膜表面,并将其连接到温度记录仪上。
在设定好实验条件后,开始进行硫化实验,并记录下温度随时间的变化。
通过分析硫化曲线,可以得出以下结论:在硫化初期,温度迅速上升,这是因为胶膜中的分子在硫化反应中释放出热量。
随着时间的推移,温度上升的速度逐渐减缓,这是因为反应物逐渐减少,反应速率降低。
当温度达到峰值时,表明胶膜已经完成了硫化反应。
此后,温度开始下降,这是因为反应已经结束,放出的热量减少。
通过观察温度随时间的变化,可以得出胶膜的硫化时间和硫化程度。
一般来说,温度越高,硫化程度越高。
但是,过高的温度可能导致胶膜损坏或降低其性能。
因此,在进行光伏胶膜的硫化实验时,需要选择合适的硫化条件和温度控制策略。
硫化曲线介绍

一. 流变仪之各种曲线之原理:1. S*粘弹曲线的原理:根据转子或转盘转动时,因胶料架桥作用所产生之扭矩变化曲线。
S*= S’2+S”2 δ=ab-ac2. S’弹性曲线的原理:S’=S* X cos δ,S’ 可得到相关之加硫条件参数。
3. S”粘性曲线的原理:S”=S* X sin δ ,S” 可得到相关之粘性参数。
粘性曲线可看出橡胶之加工性。
4. Loss Angle 动的损失角曲线的原理:δ=ab-ac5.tan δ粘弹性比值曲线:tan δ=S”/S’6. 上、下模温度曲线:测试进行中温度变化记录曲线。
7. 硫化速率曲线:架桥过程中相邻两点间之斜率值之曲线。
8. 粘弹综合曲线:S*= S’2+S”2 二. 流变仪图形及数据之判读及运用:流变仪之标准硫化曲线如下:其中共分为三大区:1. 第一区为加工区:在此一时间内橡胶具有可塑性。
此段时间愈长愈易于加工,但产能将降低,扭力值愈低橡胶流动性愈好。
2. 第二区为硫化区:在此一时间内为架桥过程。
以相同的材料而言此段时间愈长,物性通常会较佳。
3. 第三区为物理性质区:此一区段可判读成品之物理性质。
由曲线中可得数据说明如下:S* S’ S” δ ab ac δa cb 扭力 時間1. 焦烧时间(TS – Time of Scorch):一般而言国人的习惯此数据取2,这个时间通常称之为加工安全时间,也就是超过此时间橡胶已架桥失去了流动性,这是衡量模内流动时间的尺度,在低温下,它是衡量加工性能的指数,它与门尼焦烧相似。
事实上,如果流变仪和门尼试验的温度相同时,流变仪的TS2和门尼的TS35有密切关系。
以TS2为例,其定义为最低扭力值加2个单位所对应的时间:MS2=ML+2 →此点所对应的时间(TS)2. 硫化时间(TC – Time of Curing):一般而言国人的习惯此数据取90,这个时间通常称之为最适加硫时间,也就是说当加硫至此一时间就可自模具中将成品取出,其定义为加硫至90%所需之时间,其计算公式为:MC90=(MH-ML)*90%+ML →此点所对应之时间(TC)3. 最低扭力值(ML – Min Torque):此数据可作为加工特性之参考。
- 1、下载文档前请自行甄别文档内容的完整性,平台不提供额外的编辑、内容补充、找答案等附加服务。
- 2、"仅部分预览"的文档,不可在线预览部分如存在完整性等问题,可反馈申请退款(可完整预览的文档不适用该条件!)。
- 3、如文档侵犯您的权益,请联系客服反馈,我们会尽快为您处理(人工客服工作时间:9:00-18:30)。
硫化曲线图参数详细说明(2008-12-16 13:57:59)标签:硫化曲线说明参数杂谈分类:橡胶技术论文硫变仪以及硫化曲线的介绍1. 橡胶硫化测试仪,简称为硫变仪,是指在橡胶硫化过程中连续测定胶料硫化性能的全部变化,并具有较高的测试精度的仪器,生产橡胶制品的厂家可以用它进行橡胶的均匀性、重现性、稳定性的测试。
并且进行橡胶配方设计和检测,目前主要应用于批量生产橡胶硫化特性的检测和管控。
2.分类:2.1根据其有无转子分为:有转子流变仪、无转子流变仪.2.2有转子流变仪及无转子流变仪的主要区别:2.2.1有转子流变仪测试时试样温度达到稳定所需要时间长;而无转子则较快。
2.2.2有转子的转子与胶料产生的磨擦力也计入胶料剪切模量的数据中,而无转子则避免此摩擦力的影响。
3、硫化曲线3.1实验原理从流变学的观点可以说,迄今为止,各种流变仪所采用的原理本质上是一致的,即模压在模腔内的试样连续的承受恒定的小振幅和低频率的正弦剪切变形,由测力传感器测定剪切应力,以转矩单位表示,即胶料的剪切模量,当试样规格、厚度、振幅角和实验温度一定时,所测定的剪切应力与交联点密度成正比关系,记录下的剪切应力—时间的曲线便是硫化曲线。
3.2.硫化曲线ML——最低转矩,N•m(kgf•cm)MH——到达规定时间之后仍然不出现平坦曲线或最高转矩的硫化曲线,所达到的最高转矩N•m(kgf•cm)TS1——从实验开始到曲线由最低转矩上升0.1 N•m(kgf•cm)时所对应的时间,MINTS2——从实验开始到曲线由最低转矩上升0.2 N•m(kgf•cm)时所对应的时间,MINTC(x)——试样达到某一硫化程度所需要的时间,即试样转矩达到ML+X(MH-ML)时所对应的时间,MIN(注:如X取值0.5,即TC50,X取.9,即TC90)3.4.硫检参数的意义:ML:表示胶料的流动性,ML越低,流动性越好,反之,越差。
MH:表征胶料的胶料的剪切模数、硬度、定伸强度和交联密度,一般MH越低,硬度越低,MH越高,硬度越高。
TS2:表征胶料的操作安全性,TS2越短,表示胶料越容易发生死料,产品在生产时容易产生缺料不良。
反之,TS2越长,虽然操作安全性提高,但是产效会变低,成本会增加很多,故TS2对胶料的加工、配方设计具有很重要的意义。
TC90:主要用来评估胶料在成型生产时的一次加硫条件,TC90过长表示硫化速度偏慢,会导致产品硬度低,产效低。
4. 流变仪的试验影响因素4.1试验温度硫化既然是一种化学反应过程,无疑温度对反应速度是一个重要因素。
随着温度提高其诱导期缩短,硫化速度加快.当温度相当高时配方中原材料变量的信息受到掩盖. 胶料硫化过程是一个在一定温度和压力作用下受力的过程。
如果温度或压力稍有变化,就会对测量的硫化曲线产生很大影响。
目前,压力一般较容易控制。
通过带有压力表的硫化仪就可以达到稳定的压力。
供给硫化仪的气压必须在任何时候都高于硫化仪所设定的额定气压。
而温度控制是各厂家一直强调的主要技术指标。
我厂硫化仪采用进口温控表,模腔温度波动≤±0.1℃,温度恢复时间≤2min。
4.2 硫化仪的测量频率:大部分国内使用的硫化仪都采用100转/分钟的转动频率。
转动速度对硫化仪的影响主要是使得测量的过程加快。
相对于最早3转/分钟的设备来说,100转/分钟在测量时更加适用于高温快检等方面使用。
各种频率测量的硫化数据结果不同,但都可以用于橡胶硫化的检测。
4.3硫化仪的摆动角度:按照标准,有转子硫化仪的摆角应为1°或3°;无转子硫化仪的摆动角度应为1°或0.5°,初配置均为1°。
摆动角度对于硫化数据的影响和频率相似,各种角度测量的硫化数据结果不同,但都可以用于橡胶硫化的检测。
角度越大,施加于胶样上的扭矩就越大,测量得到的数据就越大。
对于特别软的橡胶易采用大角度的摆动。
反之,硬胶采用小一些的摆动角度就可。
总之,选用不同摆角的目的都是为了能更清楚的显示测量数据。
现在所有数据都是计算机或单片机计算,数据再小也可以分辨,对于一般橡胶硫化来说,变化角度的实用性不大,标配角度足以适用于所有橡胶。
硫化仪数据解析ML——最低转矩,N•m(kgf•cm)MH——到达规定时间之后仍然不出现平坦曲线或最高转矩的硫化曲线,所达到的最高转矩N•m(kgf•cm)TS1——从实验开始到曲线由最低转矩上升0.1 N•m(kgf•cm)时所对应的时间,MINTS2——从实验开始到曲线由最低转矩上升0.2 N•m(kgf•cm)时所对应的时间,MINTC(x)——试样达到某一硫化程度所需要的时间,即试样转矩达到ML+X(MH-ML)时所对应的时间,MIN(注:如X取值0.5,即TC50,X取.9,即TC90)3.4.硫检参数的意义:ML:表示胶料的流动性,ML越低,流动性越好,反之,越差。
MH:表征胶料的胶料的剪切模数、硬度、定伸强度和交联密度,一般MH越低,硬度越低,MH越高,硬度越高。
TS2:表征胶料的操作安全性,TS2越短,表示胶料越容易发生死料,产品在生产时容易产生缺料不良。
反之,TS2越长,虽然操作安全性提高,但是产效会变低,成本会增加很多,故TS2对胶料的加工、配方设计具有很重要的意义。
TC90:主要用来评估胶料在成型生产时的一次加硫条件,TC90过长表示硫化速度偏慢,会导致产品硬度低,产效低。
硫化曲线vulcanization curve;curing curve在某一温度下测定橡胶在硫化过程中某一物理性能与硫化时间关系的曲线。
一般情况下,用硫化胶的拉伸强度、扯断伸长率、定伸应力和硬度等分别对硫化时间作图,就可以得到硫化曲线。
目前通常用硫化仪直接绘出硫化曲线,由硫化曲线可以观察胶料硫化的整个过程,按橡胶交联情况的不同可分为:硫化诱导期、热硫化阶段、平坦硫化阶段和过硫阶段。
从硫化曲线可以求得胶料焦烧性能、硫化速率、最佳硫化时间、硫化平坦性以及抗过硫返原性能等。
优肯科技股份有限公司《橡胶工艺原理》杨清芝主编硫化曲线上的参数、硫化的各个阶段及其它们之间的关系见图2-8。
由田可见,在硫化温度下,开始转矩下降,也就是粘度下降,到最低点后又开始上升,这表示硫化的开始,随着硫化的进行,转矩不断上升并达到最大值。
从图2—o的硫化曲线上可见下列参数:ML(最小转矩);MH(最大转矩);TH(理论正硫化时间);M10:ML十(MH—ML)X 10%,T10(焦烧时间);M90:ML十(MH—ML)X 90%,T9O(工艺正硫化时间)。
图2—8中曲线上的各硫化阶段:诱导期,热硫化期,正硫化期,过硫化期。
在硫化反应开始前,胶料必须有充分的迟延作用时间以便进行混炼、压延、压出、成型及模压时充满模型。
一旦硫化开始,反应要迅速。
因此,硫化诱导期对橡胶加工生产安全至关重要.是生产加工过程的一个基本参数。
在热硫化阶段,橡胶与硫磺的交联反应迅速进行,曲线的斜率即硫化速率与交联键生成速度基本一致,并符合一级反应方程式。
从硫化时间对交联密度关系可得下列方程式,式中Vut——硫化时间为,时的交联密度;K ——交联反应速度常数;t ——硫化时间;ti ——硫化诱导时间;Vu ——交联密度;Vu∞——最大交联密度。
按照式(2—1)将Vut。
对硫化时间进行标绘.可得到图2—9所示的交联反应的动力学曲线,它与图2—8的热硫化段的硫化曲线相同。
从图2—9曲线可见,交联反应自ti开始,交联密度近似直线增加,最后达最大值。
从理论上,胶料达到最大交联密度时的硫化状态称为正硫化,它与图2—8中的对应点是硫化仪中的最大转矩MH。
所以正硫化时间是指胶料达到最大交联密度时所需要时间。
显然,由交联密度来确定正硫化是比较合理的,它是现代各种硫化测量技术的理论基础。
(四)理想的橡胶硫化曲线较为理想的橡胶硫化曲线应满足下列条件:(1)硫化诱导期要足够长,充分保证生产加工的安全性;(2)硫化速度要快,提高生产效率.降低能耗;(3)硫化平坦期要长。
要实现上述条件,必须正确选择硫化条件和硫化体系。
目首比较理想的是迟效性的次磺酰胺类促进剂的硫化体系。
理想的硫化曲线如图2—10所示。
硫化仪数据解析ML——最低转矩,N•m(kgf•cm)MH——到达规定时间之后仍然不出现平坦曲线或最高转矩的硫化曲线,所达到的最高转矩N•m(kgf•cm)TS1——从实验开始到曲线由最低转矩上升0.1 N•m(kgf•cm)时所对应的时间,TS2——从实验开始到曲线由最低转矩上升0.2 N•m(kgf•cm)时所对应的时间,TC(x)——试样达到某一硫化程度所需要的时间,即试样转矩达到ML+X(MH-ML)时所对应的时间,MIN(注:如X取值0.5,即TC50,X取0.9,即TC90)ML:表示胶料的流动性,ML越低,流动性越好,反之,越差。
MH:表征胶料的胶料的剪切模数、硬度、定伸强度和交联密度,一般MH越低,硬度越低,MH越高,硬度越高。
TS2:表征胶料的操作安全性,TS2越短,表示胶料越容易发生死料,产品在生产时容易产生缺料不良。
反之,TS2越长,虽然操作安全性提高,但是产效会变低,成本会增加很多,故TS2对胶料的加工、配方设计具有很重要的意义。
TC90:主要用来评估胶料在成型生产时的一次加硫条件,TC90过长表示硫化速度偏慢,会导致产品硬度低,产效低。
Vc1,Vc2即硫化速度指数.由式;Vc=100/(t90-tsx)得出. ts 1,ts 2即初始硫化时间.即从试验开始到曲。