筒节制作工艺
筒节制造工序过程卡
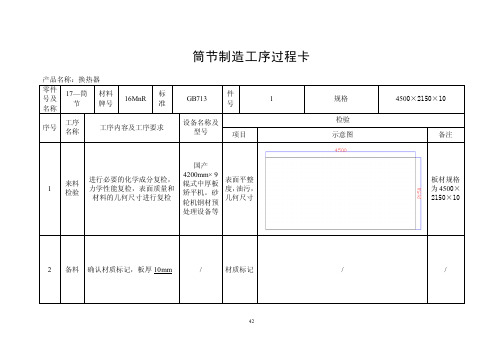
表面平整 度,油污, 几何尺寸
处理设备等
4500×2150×10
备注
板材规格 为 4500× 2150×10
2 备料 确认材质标记,板厚 10mm
/
材质标记
/
/
42
筒节制造工序过程卡
产品名称:换热器
零件 号及 名称
17-筒节
材料 牌号
16MnR 标准
GB713
件 号
1
序号
工序 名称
工序内容及工序要求
零件 号及 17—筒节 名称
材料 牌号
16MnR
标 准
序号
工序 名称
工序内容及工序要求
筒节制造工序过程卡
件
GB713
号
1
设备名称 及型号
项目
规格
检验 示意图
在筒体上的循环水出口、入口,
10
开孔 工序
工艺介质出口、入口,放空口, CG1-30 型
排净口处划线并开设孔,乙炔 半自动火
火焰切割
焰切割机
孔径,圆 度
16MnR 标准
GB713
件 号
1
序号 5
工序名 称
工序内容及工序要求
设备名称及 型号
边缘加 将工件的边缘或 端面加工成符 B8160A/1 型
工 合工艺要求的形状和尺寸精度
刨边机
项目
形状和尺 寸精度
6
环、纵 缝坡口 加工
按坡口加工图在刨边机上加工 出纵缝焊接坡口
B8160A/1 型 刨边机
坡口尺寸
设备名称 及型号
项目
规格
检验 示意图
3
划线
按筒节展开尺寸 4497 划线,移 直尺等划
加氢反应器收口筒节锻造新工艺研究
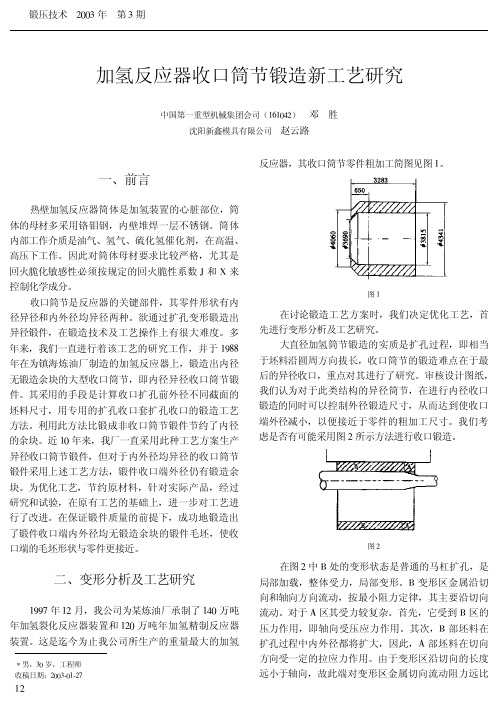
在讨论锻造工艺方案时,我们决定优化工艺,首 先进行变形分析及工艺研究。 大直径加氢筒节锻造的实质是扩孔过程,即相当 于坯料沿圆周方向拔长,收口筒节的锻造难点在于最 后的异径收口,重点对其进行了研究。审核设计图纸, 我们认为对于此类结构的异径筒节,在进行内径收口 锻造的同时可以控制外径锻造尺寸,从而达到使收口 端外径减小,以便接近于零件的粗加工尺寸。我们考 虑是否有可能采用图 " 所示方法进行收口锻造。
在图 " 中 . 处的变形状态是普通的马杠扩孔,是
二、变形分析及工艺研究
%,,) 年 %" 月,我公司为某炼油厂承制了 %’# 万吨 年加氢裂化反应器装置和 %"# 万吨年加氢精制反应器 装置。这是迄今为止我公司所生产的重量最大的加氢
#男,$# 岁,工程师 收稿日期:"##$(#%(")
局部加载,整体受力,局部变形。. 变形区金属沿切 向和轴向方向流动,按最小阻力定律,其主要沿切向 流动。对于 / 区其受力较复杂。首先,它受到 . 区的 压力作用,即轴向受压应力作用。其次,. 部坯料在 扩孔过程中内外径都将扩大,因此,/ 部坯料在切向 方向受一定的拉应力作用。由于变形区沿切向的长度 远小于轴向,故此端对变形区金属切向流动阻力远比
%"
轴向方向小。同时,由于收口套上锻件的接触面呈圆 弧形,有利于金属沿切向流动。因此,! 部坯料的内 外径也随扩孔的进程而变大。同时由于受单向载荷, 其变形程度不如 " 区强烈。锻造完成后,会形成一个 自然的收口形状。以达到锻造内外异径筒节的目标。 这种成形思路从表面上看很简单,但仔细分析问题很 多。同时由于最后收口端的尺寸全凭实际操作时收口 端和本体两部分金属变形量的不同来保证,因此容易 因为计算和操作失误造成收口端长度变长,延续到锻 件非收口部分,使锻件本体直径不够。在操作方面, 要有经验的高级技术人员指挥才能实现这一新的工艺 方法。无论对工艺设计人员,还是对操作技工,都是 有难度的。因此,必须事先周密计算好在收口锻造前 一火扩孔所应达到的内外径尺寸,将收口端扩孔长大 量考虑进去,从而保证锻出满足实际需要的锻件尺寸。 经过多次运算比较,设计出了改进后的新工艺,即内 外径均无锻造余块工艺方案。
锅炉汽包压制筒节的制造工艺
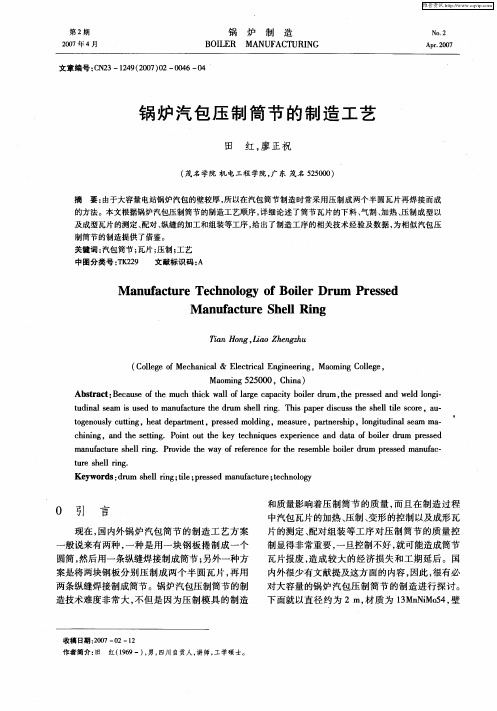
( o eeo ca i l Eetc n ier g Mami ol e C l g f l Meh nc & l r a E gn e n , o n C l g , a ci l i g e Mam n 2 0 0, hn ) o ig5 5 0 C ia
维普资讯
第 2期
田 红 , : 炉汽包压制筒节 的制造工艺 等 锅
・ 7・ 4
厚 为 15m 的 锅 炉 汽 包 为 例 , 行 锅 炉 汽包 压 4 m 进 制 筒节 的制 造工 艺分 析 。
加 热 到 80℃ ~ 9 C, 2 90o 则可 以不 再 正火 , 必 须 但 高温 回火 处 理 。 1M NM 5 3 n i o4钢 板 , 常 正 火 温 正 度 为 90℃ ~90℃ , 此 温 度 对 压 制 成 形 来 说 0 4 但 温 度较 低 , 片成 形 不 好 。工 艺上 把 加 热 温 度 提 瓦 高 到 90±1 8 0℃ , 求 偏 上 限 加 热 。在 试 样 分 析 要 中没有 发 现 晶粒 粗 大 , 机械 性 能 , 织结 构并 无 对 组 影 响 , 温及 均 热 时 间按 35小 时 计 。 由于 考 虑 升 . 炉温 与 工件 实 际温 度 有 差 异 , 了使 工 件 尽 量烧 为
关键词 : 汽包筒节 ; 瓦片 ; 压制 ; 工艺 中图分 类号 :K 2 T 29 文献标识码 : A
M a u a t r c n l g fBo l r Dr m e s d n f c u e Te h o o y o i u Pr s e e
M a u a t r h l Ri g n f c u e S el n
压力容器筒节纵缝组对工艺规程指导书

压力容器筒节纵缝组对工艺规程指导书工艺编号:1组对时,坡口间隙、错边量、棱角度等应符合规定。
具体尺寸允差见附表一。
2组对时尽量使用F枪、手位葫芦等,少用工卡具,以避免机械损伤。
不锈钢、Cr-Mo钢、低温钢及σs≥490Mpa 的高强钢所用工卡具拆除后,母材经补焊后打磨平滑用永久记号笔做好标记,以进行磁粉或着色检测。
3工卡具、吊耳、引熄弧板等须统一设置,与筒体同材质,引(熄)弧板的长度要求不短于150mm其厚度要求为筒节厚度的2/3并保证外表面平齐以免造成焊缝两端与整条焊缝的不一致性。
4组对时须严格控制错边、间隙,并保证错边、间隙的均匀一致性。
5立位焊接的筒体及分片到货的锥段、椭圆封头、球形封头纵缝组对须在经找正水平的平台上(或拼接的钢板)上进行,以保证圆度及端面不平度。
锥段组对纵缝间隙允许有2 mm的不一致性。
6封头组对时,保证瓜瓣下口平齐,控制理论拱高,组对间隙均匀2~3mm。
7严禁强力组对,点固焊缝间距和厚度要符合规定,严禁对材料表面进行烧烤。
8焊接接头拘束度大时,推荐采用抗裂性能更好的焊条施焊。
9点固焊缝不得有裂纹,否则应清除重焊。
如存在气孔、夹渣时亦应去除。
10熔入永久焊缝内的定位焊缝两端应便于接弧,否则应予修整。
11有预后热要求时,严格执行工艺。
纵缝点焊预后热采用氧—乙炔火焰加热,时间不得少于3min,保证温度,保证点焊焊缝长度≥150mm和厚度12mm~16mm,间距400mm~500mm,防止焊前开裂。
12无法或回床困难的筒体纵缝组对时须预留反变形。
13临时工卡具、吊耳的焊接须采用和筒体相同的焊接工艺及焊材。
附表一特殊技术要求:1.此工艺规程同时适用于筒体、封头、裙座筒体、锥段、卷制接管。
2.复合钢板纵缝组对错边量要求在1mm以内,焊接时基层全部焊接到位,过渡层与面层焊接时在两端各留出约50mm 不焊,待环缝复层焊接时一并施焊。
筒节的制造

(2)使工件在矫正曲率下多次滚卷,并着重于焊缝区的矫正,使圆筒曲率均匀一致。经测量,直到合乎要求为止。
(3)逐渐卸除载荷,并使工件在逐渐卸除载荷的过程中多次滚卷。
10、无损检验:焊缝进行100%无损检测,超声波探伤按JB/1730-94规定Ⅰ级为合格,射线探伤按JB/1730-94规定不低于Ⅱ级为合格。
板料预弯后放入卷板机上下辊之间进行辊卷前必须使板料的母材与辊的轴线平行使板料的纵向中心线与辊的轴线保持相互垂直即对中其目的是防止钢板在滚卷过程中产生扭斜变形
1、钢板的复检
2、钢材的表面预处理
钢材表面预处理是钢材进入划线、号料或下料工序之前的一道必经工序。由于钢材表面的油污、锈蚀和氧化皮等都会影响产品的制造质量。因此,在进行材料划线。下料之前必须先进行表面预处理。钢材的表面预处理对于提高产品质量、延长产品寿命、减少环境污染具有重要意义。钢材的表面预处理方法主要有机械除锈法和化学除锈法两种。
(3)卷圆钢板对中后,即可用上辊压住板料并使之产生一定弯曲,开动机床进行滚卷。
每滚卷一次行程,便适当下调上辊一次,这样经过多次滚卷就可将板料弯曲成所要求的曲率。在滚卷过程中要注意:随时用卡样板测量,看是否达到曲率要求,不可过卷量太多,因为过卷要比曲率不足难以修正,且易使金属性能变坏。在冷卷时要考虑到回弹的影响,必须施加一定的过卷量。当卷制达到曲率要求时,还应在此曲率下多卷几次,以使其变形均匀和释放内应力,减少回弹。WCF-62钢回弹量较大,需要在最终成形之前进行一次退火。卷板机辊子的位置关系如图下图所示。
须在筒体上开1个Ф530mm、1个Ф32mm、1个Ф57mm、1一个Ф89mm、3个Ф38mm以及3个Ф25mm的孔。先要进行划线、打标记来确定孔中心的位置,如总焊接结构总图所示。对于Ф530mm采用气体火焰切割割孔,其余小孔径孔可用冲压机床进行冲孔或进行钻孔。
亚临界锅炉锅筒筒节制造工艺路线探讨
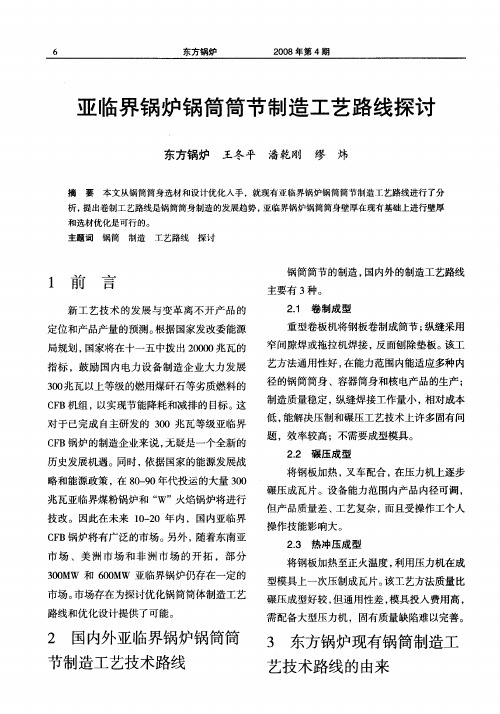
2 国内外 亚临界锅炉锅筒筒 3 东方锅炉现有锅筒制造工 节制造工艺技术路线 艺技术 路线 的 由来
东方锅炉
20 0 8年第 4期
7
东方锅炉生产第一台亚临界 3 O万千瓦锅 炉确定的工艺技术路线是采用热冲成型方法 。 根据 C E引进技术 , 锅筒筒身用钢板壁厚选用
6= 4 mm、 材 料 牌 号 为 D WA 5 (3 N 15 I 3 31 Mn i
口后 焊 接 组合 。受 当时 的历 史 条 件 限制 , 当 在
老化 , 设备能力已经严重下降且每年均有较长
时间的大修 ,严重影响正常生产。
6 )制约设 计 优化
时时间紧、 任务量不大且初投资几十万即可生
产 的情况 下 , 是一 种 不得 已而为 之 的方法 。另
一
锅筒筒身的优 化设计 多年来 由于受模具 尺寸的限制且模具投资费用大 、 制造周期长等
4 1 利 于设计 优 化 .
冲压成 型后 的瓦片在热态 即放人冷却支 座上 自然冷却 , 常常出现配对 困难 , 筒节也常 常出现大小头现象 ,引起装配错边 。
3)装 配筒 节 时 的工艺 缺 陷难 以改 变
和选 材优化是可行 的。 主题词 锅筒 制造 工艺路线 探讨
锅 筒筒 节 的制造 , 国内外 的制 造工 艺路线
1 刚 舌
新 工艺 技 术 的发 展 与变 革 离 不 开 产 品 的 定位 和产 品产量 的预 测 。 根据 国家 发改委 能源 局规 划 , 国家将在 十一 五 中拨 出 200兆 瓦 的 00
备 负荷 严 重超 载且 制造 周 期长 , 以满
9 0年代 已经改为采用卷制工艺技术路线 ,这 证 明卷制是锅筒筒身制造的成熟 、可靠且先 进 、实用的工艺技术路线 。 从长远发展看 , 锅筒筒节的生产工艺技术
单个筒节卷制形成形的工艺过程

单个筒节卷制形成形的工艺过程
一种筒体卷制工艺,包括如下步骤: (1)按净尺寸下料; (2)将得到的板材放到卷板机上,保证板材的横向端面与卷板机的上辊轴线平行,以确保板材在卷制完成后对缝整齐; (3)利用上辊使板材的两个横向端面端弯曲; (4)滚弯; (5)焊接:从卷板机上取下筒体,按照焊接工艺的要求对焊缝进行焊接; (6)滚圆成型:把焊接完成的筒体重新装入卷板机,对焊缝两侧的直边段实施局部滚圆,待该处曲率与中间段曲率接近后,对筒体做整体滚圆,反复多次后,达到筒体圆度的要求; (7)从卷板机上卸下卷制好的筒体,按照焊接工艺对焊缝进行盖面焊接.本发明不但能够避免材料浪费,而且省去预弯模具及相关设备的投入,从而大大节约成本,提高工作效率.
根据筒体的直径乘3。
14得周长,根据筒体的高度拼板,然后放置三心轧辊上加工,两支轧辊在板下,一支轧辊在板上,上轧辊位于两下轧辊中间,板放进之后,开始下压上轧辊,并来回滚动轧辊,将板一点一点压出弧度,随着下压的深度增加,弧度也随着增加,直到将板压成对角相接的整圆。
点焊接后,复验尺寸,修正后再焊接,然后上轧辊压对焊口处进行修圆。
尿素合成塔主要零部件的制造工艺流程设计_图文(精)
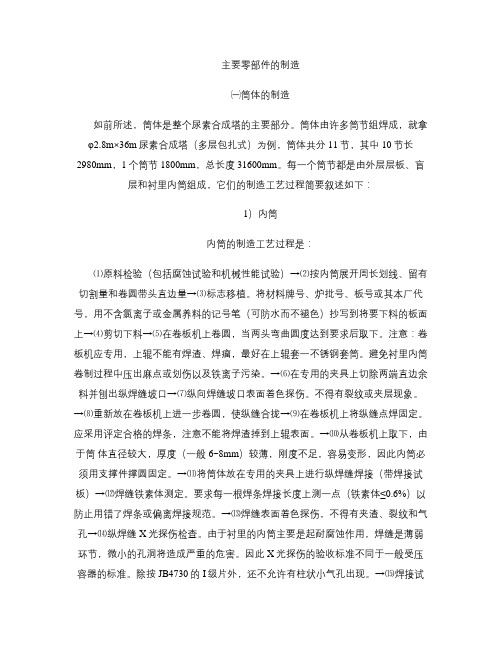
主要零部件的制造㈠筒体的制造如前所述,筒体是整个尿素合成塔的主要部分。
筒体由许多筒节组焊成,就拿φ2.8m×36m尿素合成塔(多层包扎式)为例,筒体共分11节,其中10节长2980mm,1个筒节1800mm,总长度31600mm。
每一个筒节都是由外层层板、盲层和衬里内筒组成,它们的制造工艺过程简要叙述如下:1)内筒内筒的制造工艺过程是:⑴原料检验(包括腐蚀试验和机械性能试验)→⑵按内筒展开周长划线、留有切割量和卷圆带头直边量→⑶标志移植。
将材料牌号、炉批号、板号或其本厂代号,用不含氯离子或金属养料的记号笔(可防水而不褪色)抄写到将要下料的板面上→⑷剪切下料→⑸在卷板机上卷圆,当两头弯曲圆度达到要求后取下。
注意:卷板机应专用,上辊不能有焊渣、焊瘤,最好在上辊套一不锈钢套筒。
避免衬里内筒卷制过程中压出麻点或划伤以及铁离子污染。
→⑹在专用的夹具上切除两端直边余料并刨出纵焊缝坡口→⑺纵向焊缝坡口表面着色探伤。
不得有裂纹或夹层现象。
→⑻重新放在卷板机上进一步卷圆,使纵缝合拢→⑼在卷板机上将纵缝点焊固定。
应采用评定合格的焊条,注意不能将焊渣掉到上辊表面。
→⑽从卷板机上取下,由于筒体直径较大,厚度(一般6~8mm)较薄,刚度不足,容易变形,因此内筒必须用支撑件撑圆固定。
→⑾将筒体放在专用的夹具上进行纵焊缝焊接(带焊接试板)→⑿焊缝铁素体测定。
要求每一根焊条焊接长度上测一点(铁素体≤0.6%)以防止用错了焊条或偏离焊接规范。
→⒀焊缝表面着色探伤,不得有夹渣、裂纹和气孔→⒁纵焊缝X光探伤检查。
由于衬里的内筒主要是起耐腐蚀作用,焊缝是薄弱环节,微小的孔洞将造成严重的危害。
因此X光探伤的验收标准不同于一般受压容器的标准。
除按JB4730的I级片外,还不允许有柱状小气孔出现。
→⒂焊接试板的晶间腐蚀倾向试验和选择性腐蚀检查及金相检查。
其方法按HG/T3172和HG/T3173、HG/T3174验收标准按GB9842或工程标准的规定。
筒节制作流程

1
塑料瓶处理工艺流程
塑料瓶处理工艺流程简述如下:
原料钢板→①切割下料:使用等离子或火焰切割机将钢板切割成所需尺寸;→②边缘加工:对切好的钢板边缘进行坡口处理,以便焊接;→③卷板成型:将处理好的钢板送入卷板机卷制成圆筒状;→④对接准备:筒节两端准备焊接,清洁并定位;→⑤环缝焊接:内外环缝进行自动或手工焊接;→⑥焊缝检测:利用X射线或超声波检测焊接质量;→⑦矫正与整形:对焊接后的筒节进行矫正,保证几何形状准确;→⑧表面处理:喷砂除锈,涂装防腐;→⑨最终检验:检查尺寸、外观及内在质量;→⑩包装入库:合格产品进行包装并入库待用。
1。
锥形封头与筒节焊接形式

锥形封头与筒节焊接形式1.引言1.1 概述:锥形封头与筒节焊接形式是一种常见的工程焊接技术,用于连接锥形封头与筒节两者之间。
锥形封头是一种具有锥状几何形状的零件,通常用于容器、压力容器、储罐等设备的顶部或底部封闭部分。
而筒节则是锥形封头下方形状较为规则的部分,常用于连接锥形封头与系统中的其余部分。
锥形封头与筒节焊接形式的基本原理是通过熔化焊条或电弧加热,将锥形封头与筒节的接触面加热至熔点,借助表面张力使其自然融合在一起。
这种焊接方式可以产生较强的焊缝,确保连接部位的密封性和机械强度。
锥形封头与筒节焊接形式广泛应用于许多工程领域,包括石油化工、化学工业、能源工业等。
在石油化工行业中,锥形封头与筒节的焊接被广泛用于制作压力容器、反应器等设备。
在化学工业中,锥形封头与筒节的焊接形式常用于气体储罐、化工设备等。
而在能源工业中,锥形封头与筒节的焊接形式则常用于核电厂的核容器焊接等重要工程。
锥形封头与筒节焊接形式具有许多优势。
首先,它可以确保连接部位的完全密封,有效防止液体或气体泄漏。
其次,焊接强度高,可以承受较大的压力和载荷。
此外,该焊接形式可以灵活地适应不同尺寸和形状的焊接需求,具有较高的适用性。
最后,随着技术的进步和应用领域的扩大,锥形封头与筒节焊接形式的发展趋势将越来越多地注重环保、安全和节能等方面的需求。
综上所述,锥形封头与筒节焊接形式是一种重要且广泛应用的工程焊接技术,它的优势和发展潜力使得它在许多行业中得到了广泛的应用和推广。
在接下来的部分中,我们将更详细地探讨锥形封头与筒节焊接形式的基本概念、应用领域、优势以及发展趋势等方面。
1.2 文章结构文章结构文章将按照以下结构展开对锥形封头与筒节焊接形式的探讨。
首先,引言部分将提供对本文主题的概述,介绍锥形封头和筒节焊接形式的基本概念,并阐明本文的目的。
接下来,正文部分将详细介绍锥形封头与筒节焊接形式的基本概念,包括其定义、构成要素等。
同时,将探讨锥形封头与筒节焊接形式在不同领域的应用情况,包括工业、建筑等方面。
加氢反应器筒体制造
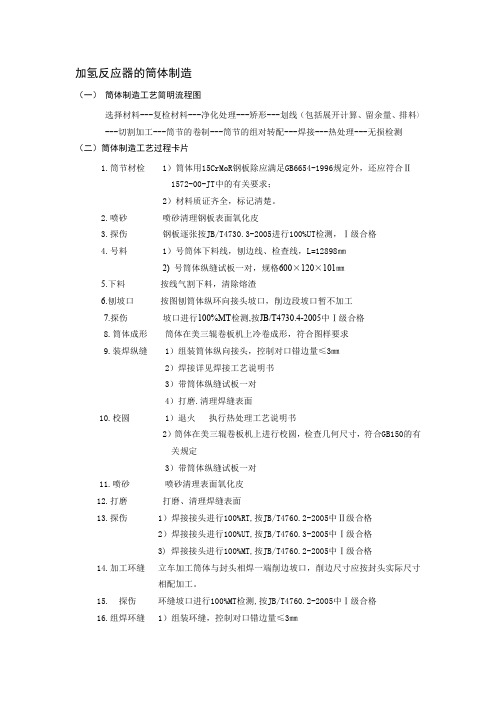
加氢反应器的筒体制造(一)筒体制造工艺简明流程图选择材料---复检材料---净化处理---矫形---划线(包括展开计算、留余量、排料)---切割加工---筒节的卷制---筒节的组对转配---焊接---热处理---无损检测(二)筒体制造工艺过程卡片1.筒节材检1)筒体用15CrMoR钢板除应满足GB6654-1996规定外,还应符合Ⅱ1572-00-JT中的有关要求;2)材料质证齐全,标记清楚。
2.喷砂喷砂清理钢板表面氧化皮3.探伤钢板逐张按JB/T4730.3-2005进行100%UT检测,Ⅰ级合格4.号料1)号筒体下料线,刨边线、检查线,L=12898㎜2)号筒体纵缝试板一对,规格600×120×101㎜5.下料按线气割下料,清除熔渣6.刨坡口按图刨筒体纵环向接头坡口,削边段坡口暂不加工7.探伤坡口进行100%MT检测,按JB/T4730.4-2005中Ⅰ级合格8.筒体成形筒体在美三辊卷板机上冷卷成形,符合图样要求9.装焊纵缝1)组装筒体纵向接头,控制对口错边量≤3㎜2)焊接详见焊接工艺说明书3)带筒体纵缝试板一对4)打磨.清理焊缝表面10.校圆1)退火执行热处理工艺说明书2)筒体在美三辊卷板机上进行校圆,检查几何尺寸,符合GB150的有关规定3)带筒体纵缝试板一对11.喷砂喷砂清理表面氧化皮12.打磨打磨、清理焊缝表面13.探伤1)焊接接头进行100%RT,按JB/T4760.2-2005中Ⅱ级合格2)焊接接头进行100%UT,按JB/T4760.3-2005中Ⅰ级合格3)焊接接头进行100%MT,按JB/T4760.2-2005中Ⅰ级合格14.加工环缝立车加工筒体与封头相焊一端削边坡口,削边尺寸应按封头实际尺寸相配加工。
15.探伤环缝坡口进行100%MT检测,按JB/T4760.2-2005中Ⅰ级合格16.组焊环缝1)组装环缝,控制对口错边量≤3㎜2)焊接详见焊接工艺说明书3)打磨、清理焊缝表面4)按热处理工艺进行炉外消氢处理17.打磨打磨、清理焊缝表面18.探伤1)焊接接头进行100%RT,按JB/T4760.2-2005中Ⅱ级合格2)焊接接头进行100%UT,按JB/T4760.3-2005中Ⅰ级合格3)焊接接头进行100%MT,按JB/T4760.2-2005中Ⅰ级合格19.堆焊过渡层1)堆焊过渡层,详见焊接工艺说明书2)按热处理工艺进行炉外消氢处理3)打磨、清理过渡层20.探伤过渡层进行100%PT检测,按JB/T4730.5-2005中Ⅰ级合格21.堆焊筒体表层1)堆焊表层,详见焊接工艺说明书2)测铁素体数3)打磨、清理表层22.筒体探伤1)表层进行100%PT检测,按JB/T4730.5-2005中Ⅰ级合格2)堆焊层及熔合面进行100%UT,符合Ⅱ1572-00-JT中的有关要求3)堆焊层进行厚度检测,符合图纸要求(三)、筒体制造工艺流程具体内容1、选择材料此加氢反应器筒体材料选择15CrMoR。
尿素合成塔主要零部件的制造工艺流程设计
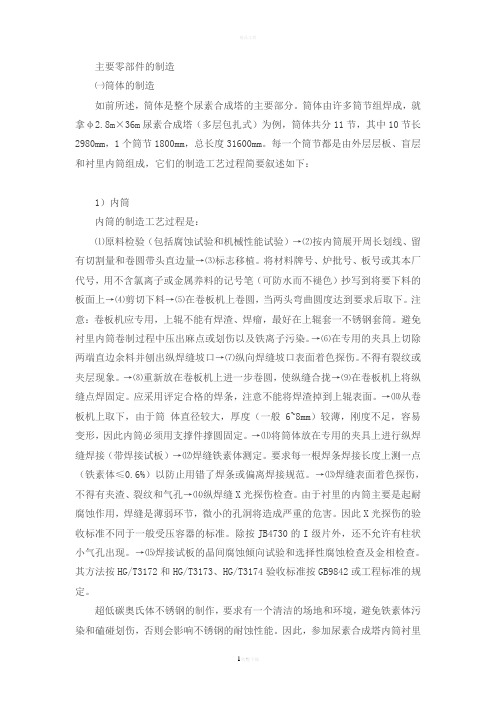
主要零部件的制造㈠筒体的制造如前所述,筒体是整个尿素合成塔的主要部分。
筒体由许多筒节组焊成,就拿φ2.8m×36m尿素合成塔(多层包扎式)为例,筒体共分11节,其中10节长2980mm,1个筒节1800mm,总长度31600mm。
每一个筒节都是由外层层板、盲层和衬里内筒组成,它们的制造工艺过程简要叙述如下:1)内筒内筒的制造工艺过程是:⑴原料检验(包括腐蚀试验和机械性能试验)→⑵按内筒展开周长划线、留有切割量和卷圆带头直边量→⑶标志移植。
将材料牌号、炉批号、板号或其本厂代号,用不含氯离子或金属养料的记号笔(可防水而不褪色)抄写到将要下料的板面上→⑷剪切下料→⑸在卷板机上卷圆,当两头弯曲圆度达到要求后取下。
注意:卷板机应专用,上辊不能有焊渣、焊瘤,最好在上辊套一不锈钢套筒。
避免衬里内筒卷制过程中压出麻点或划伤以及铁离子污染。
→⑹在专用的夹具上切除两端直边余料并刨出纵焊缝坡口→⑺纵向焊缝坡口表面着色探伤。
不得有裂纹或夹层现象。
→⑻重新放在卷板机上进一步卷圆,使纵缝合拢→⑼在卷板机上将纵缝点焊固定。
应采用评定合格的焊条,注意不能将焊渣掉到上辊表面。
→⑽从卷板机上取下,由于筒体直径较大,厚度(一般6~8mm)较薄,刚度不足,容易变形,因此内筒必须用支撑件撑圆固定。
→⑾将筒体放在专用的夹具上进行纵焊缝焊接(带焊接试板)→⑿焊缝铁素体测定。
要求每一根焊条焊接长度上测一点(铁素体≤0.6%)以防止用错了焊条或偏离焊接规范。
→⒀焊缝表面着色探伤,不得有夹渣、裂纹和气孔→⒁纵焊缝X光探伤检查。
由于衬里的内筒主要是起耐腐蚀作用,焊缝是薄弱环节,微小的孔洞将造成严重的危害。
因此X光探伤的验收标准不同于一般受压容器的标准。
除按JB4730的I级片外,还不允许有柱状小气孔出现。
→⒂焊接试板的晶间腐蚀倾向试验和选择性腐蚀检查及金相检查。
其方法按HG/T3172和HG/T3173、HG/T3174验收标准按GB9842或工程标准的规定。
筒节组装工艺过程卡-改

备注
施工班组:
班长:
项目名称 产品编号 筒节编号
青 岛 山 泰 钢 结 构 有 求 工序号 工序名称 工 艺方法或 要 求 1 法兰组装 组对法兰时,对法兰尺寸进行检查,然后按排板图及图纸要求,间隔90°调出四条度数线。筒体 法兰与平台间隙≤1mm 纵缝的位置应按排板图组对。组对前塔体及法兰坡口内及其两侧各20mm用磨光机打磨,以除 错边量不超过1mm, 去铁锈、油污等杂质。组对时采用在平台上倒拨筒体无间隙组对。筒体与法兰组对前必须先将 纵缝位置偏移量≤5mm 筒体端部椭圆度调整合格,可采用筒内打支撑的方法调节端部椭圆度,椭圆度≤5mm。 2 环缝组对 在组对胎具上进行卧式组对,外径对齐。组对时要严格按照排版图进行,并保证筒节 长度方向误差要求±2mm 对角线之差不大于3mm。 环缝编号 的总长度和四个角度的对角线尺寸符合公差要求。为减少外侧打磨量, 组对间隙0~1mm 错边量不超过1.5mm, 要求在筒体的内侧组对,筒体外侧不允许焊刀把,打卡子,筒外定位无打火现象。 3 环缝焊接 在托滚上进行焊接。焊接时要注意引弧和收弧,保证焊缝成型,严格按焊接工艺卡进行。 余高0~2;宽窄差≤2; 焊缝表面凹凸150mm内≤2.5mm 环缝编号 先焊接内侧,焊完后外侧清根,同时用磨光机进行清理干净,严禁焊后清理。外观质量好坏与 咬边0.05t且≤0.5mm 焊接外口前是否对整个坡口及两侧用磨光机打磨光滑,以去除焊接内口时留下的药皮等杂物, 无飞溅和焊瘤、气孔、弧孔 有直接关系。对此要严格执行该工艺纪律。 4 碰大口 组对时,划线要求准确,以保证扭曲在公差范围。整段塔筒组对完后,要检查平行度 四个象限差值在3mm内 法兰平面度等见表1 编号 法兰平面度、长度、扭曲度。 长度之差不超过3mm 上下法兰扭曲≤10mm 5 焊接 同上 同上 6 UT/RT 焊后进行无损检测,按无损检测工艺进行 7 整体尺 组焊完后进行检验。 同3 寸检验 A1 备注
风电塔筒通常制造工艺标准
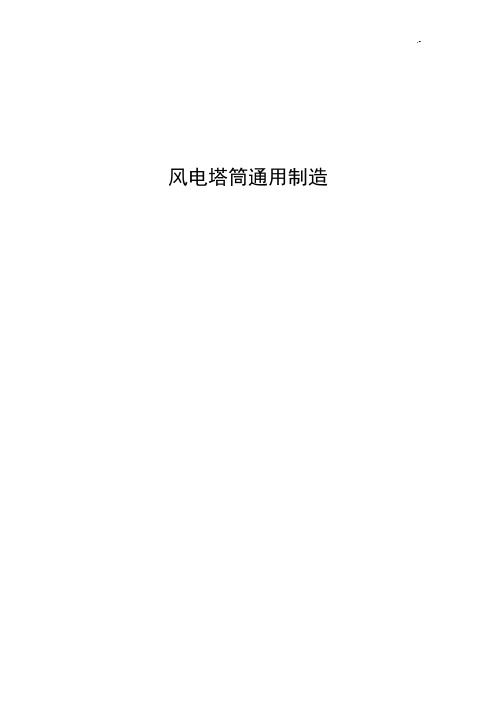
风电塔筒通用制造目录1.塔筒制造工艺流程图2.制造工艺3.塔架防腐4.吊装5.运输注:本工艺与具体项目的技术协议同时生效,与技术协议不一致时按技术协议执行一.塔架制造工艺流程图(一)基础段工艺流程图1.基础筒节:H原材料入厂检验→R材料复验→R数控切割下料(包括开孔)→尺寸检验→R加工坡口→卷圆→R校圆→100%UT检测。
2.基础下法兰:H原材料入厂检验→R材料复验→R数控切割下料→R法兰拼缝焊接→H拼缝100%UT检测→将拼缝打磨至与母材齐平→热校平(校平后不平度≤2mm)→H拼缝再次100%UT检测→加工钻孔→与筒节焊接→H角焊缝100%UT检测→校平(校平后不平度≤3mm)→角焊缝100%磁粉检测。
3.基础上法兰:外协成品法兰→H入厂检验及试件复验→与筒节组焊→100%UT 检测→H平面检测。
4.基础段组装:基础上法兰与筒节部件组焊→100UT%检测→H平面度检测→划好分度线组焊挂点→整体检验→喷砂→防腐处理→包装发运。
(二)塔架制造工艺流程图1.筒节:H原材料入厂检验→R材料复验→钢板预处理→R数控切割下料→尺寸检验→R加工坡口→卷圆→R组焊纵缝→R校圆→100%UT检测。
2.顶法兰:成品法兰→H入厂检验及试件复验→与筒节组焊→100%UT检测→平面度检测→二次加工法兰上表面(平面度超标者)。
3.其余法兰:成品法兰→H入厂检验及试件复验→与筒节组焊→100%UT检测→平面度检测。
4.塔架组装:各筒节及法兰短节组对→R检验→R焊接→100%UT检测→R检验→H划出内件位置线→H检验→组焊内件→H防腐处理→内件装配→包装发运。
二、塔架制造工艺(一)工艺要求:1.焊接要求(1)筒体纵缝、平板拼接及焊接试板,均应设置引、收弧板。
焊件装配尽量避免强行组装及防止焊缝裂纹和减少内应力,焊件的装配质量经检验合格后方许进行焊接。
(2)塔架筒节纵缝及对接环缝应采用埋弧自动焊,应采取双面焊接,内壁坡口焊接完毕后,外壁清根露出焊缝坡口金属,清除杂质后再焊接,按相同要求制作筒体纵缝焊接试板,产品焊接试板的厚度范围应是所代表的工艺评定覆盖的产品厚度范围,在距筒体、法兰及门框焊约50mm处打上焊工钢印,要求涂上防腐层也能清晰看到;(3)筒节纵环焊缝不允许有裂纹、夹渣、气孔、未焊透、未融合及深度>0.5mm 的咬边等缺陷,焊接接头的焊缝余高h应小于焊缝宽度10%;(4)筒节用料不允许拼接,相邻筒节纵焊缝应尽量错开180度,筒节纵焊缝置于法兰两相邻两螺栓孔之间。
回转窑筒节整环挖补工艺

年 1 号窑 大修 中得 到 了验证 , 效果 良好 , 它使整环挖 补 几 乎 同 整 节 简 体 更 换 达 到 同 样 技 术 效 果 。 保 证 简 可 体 的检 修 质 量 。
( 辑 编 王艳 丽 )
CEM EN T 2 o . . 2 0 2 No 1
见 图 1 每 段 弧 板 两 边 都 进 行 加 固 和 支 撑 。加 固板 厚 , 6=3 hm, L=1 0 r 宽 H=3 0 m , 4块 × 0i 长 2 0 m, a 0r a 共 3=1 2块 ; 撑 槽 钢 [6 , L =2 0 rm, 2根 × 支 1a 长 0 2 a 共
度 找 正 , 后 焊 好 3条 纵 缝 。 然 8 )未 焊 一 侧 同其 它 更换 筒 节 一 起 进 行 动 态 精 找
正 , 至 径 向 跳 动 值 达 到 检 修 技 术 要 求 ,最 后 焊 好 环 直
缝。
9 拆 除 所 有 支撑 及 筋 板 , 把 焊 疤 、 渣 打 磨 干 ) 并 焊
4 效 果
此 挖 补 方 法 在 我 厂 19 9 9年 5号 窑 大 修 和 2 0 00
4 将 其 中 1块 弧 板 吊 装 对 接 找 正 , 板 加 固 。注 ) 筋
意 与 相 邻 筒 节 纵 缝 错 开 8 0 m 以上 , 边 量 ≤2 m, 0r a 错 a r 环 缝 ≤3 m, 术 要 求 同整 体 筒 节 更 换 对 接 一 样 。 a r 技
3:6根 .
图 2 弧 板 初 焊 不 蒽
6 转 窑 1 3 用 同样 方 法 挖 补第 二 、 ) /, 三块 ? 意 割 注 口后 先 校 圆 , 样 只 焊 一 侧 ( 同 一 侧 ) 留 另一 侧 : 同 且 ,
筒节滚圆、校圆工艺
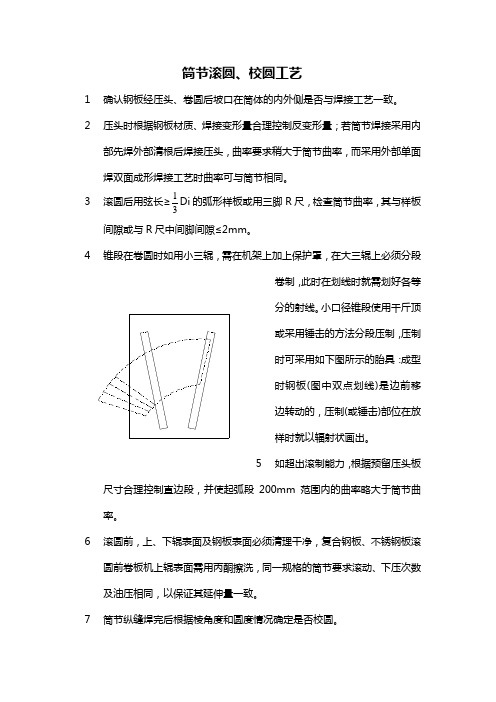
筒节滚圆、校圆工艺1确认钢板经压头、卷圆后坡口在筒体的内外侧是否与焊接工艺一致。
2 压头时根据钢板材质、焊接变形量合理控制反变形量;若筒节焊接采用内部先焊外部清根后焊接压头,曲率要求稍大于筒节曲率,而采用外部单面焊双面成形焊接工艺时曲率可与筒节相同。
3 滚圆后用弦长≥31Di 的弧形样板或用三脚R 尺,检查筒节曲率,其与样板间隙或与R 尺中间脚间隙≤2mm 。
4 锥段在卷圆时如用小三辊,需在机架上加上保护罩,在大三辊上必须分段卷制,此时在划线时就需划好各等分的射线。
小口径锥段使用千斤顶或采用锤击的方法分段压制,压制时可采用如下图所示的胎具:成型时钢板(图中双点划线)是边前移边转动的,压制(或锤击)部位在放样时就以辐射状画出。
5 如超出滚制能力,根据预留压头板尺寸合理控制直边段,并使起弧段200mm 范围内的曲率略大于筒节曲率。
6 滚圆前,上、下辊表面及钢板表面必须清理干净,复合钢板、不锈钢板滚圆前卷板机上辊表面需用丙酮擦洗,同一规格的筒节要求滚动、下压次数及油压相同,以保证其延伸量一致。
7筒节纵缝焊完后根据棱角度和圆度情况确定是否校圆。
8 校圆前筒节上的试板、(熄)引弧板必须采用切割方法取下,不得用锤击方法取下,校圆时控制圆度:对于普通容器、塔器其圆度≤筒体内径的1%,且≤25mm(卷制接管≤1%Di,且≤5mm),对于刚性不大的筒节只需对棱角度进行校正(棱角≤1/10δs +2mm,且≤3mm)。
对于换热器壳体,要求其圆度≤0.5%Di且当Di≤1200mm时圆度≤5mm、Di≥1200mm时圆度≤7mm。
此工艺规程同时适用于筒体、裙座筒体、锥段、卷制接管。
- 1、下载文档前请自行甄别文档内容的完整性,平台不提供额外的编辑、内容补充、找答案等附加服务。
- 2、"仅部分预览"的文档,不可在线预览部分如存在完整性等问题,可反馈申请退款(可完整预览的文档不适用该条件!)。
- 3、如文档侵犯您的权益,请联系客服反馈,我们会尽快为您处理(人工客服工作时间:9:00-18:30)。
筒节制作工艺
1、工程技术准备
1.1熟悉图纸及技术要求。
1.2按照相关标准进行焊接工艺评定。
1.3编制工序工艺文件和质量验收文件。
2、工程生产准备
2.1所有材料进厂后要按照制作图纸及技术条件的要求进行复检并要有生产厂家的产品质量证明书和合格证,凡无不符合要求的,一律不得使用。
2.2焊丝、焊剂、焊条的发放和烘烤由专人执行,并做好发放、烘烤记录。
3、卷板工序技术要求
3.1卷制准备工作:
3.1.1检测钢板两对角线是否等长,且符合技术、工艺要求。
3.1.2检测钢板两直边是否等长,且是否呈直线。
3.1.3检查钢两直边上是否有缺陷、毛刺等,否则进行相应的填补和打磨处理。
3.1.4清洁钢表面的灰尘、铁锈和油漆等异物。
3.2压制弧头
3.2.1转动卷板机压制,送出钢板50—75㎝(弧头长)。
用样板检验弧头弧度。
要保证弧头足够长,否则在卷制时,弧头末尾与卷制起始位衔接不上而出现直段。
3.2.2第一次的压制不能保证弧度,应后退钢板至初始位,少量上提压制侧辊继续压制。
应尽量在最少的压制次数内保证压制质量,以免造成钢板的严重变形(会出现波浪形)。
3.2.3由于钢板(扇板)卷成筒后,两筒口的直径不同,所以在压制弧头时,侧辊的两端做相应的高度差别处理。
3.3筒节卷制。
3.3.1在钢板一端的大弧边上进行测量后,划出小弧边角相对应的位置记号。
以作为卷制时校对钢板两直边中点的连线与辊垂直的基准。
3.3.2当卷制过半时,为避免因扇板过长由于自重下落而产生破坏性变形。
必须用吊车吊住钢板,并随着卷制做曲线跟随运动。
当一圈卷完后,清除钢板上因卷
压而剥落的铁锈、灰尘等异物,此时必须关闭设备,防止意外原因使设备转动而造成人员伤害。
3.3.3在卷制的过程中,用样板检验小弧边弧度,但不能完全依赖样板,如果弧边弧度和样板弧度完全吻合,这样的筒卷出来较多会出现焊缝凹头的现象,要使弧边弧度略小于样板弧度为易。
3.4合边:合边前转动卷扳机使两直边处于操作人员能及的范围,用吊车吊住上面的一端缓慢下放,大弧边的两角先接触,使用接边槽形工装(自行制作)固定大弧边的两角,调整好距离、角度后,点焊连接。
3.5滚制筒体时,用焊缝检验规和150mm钢板尺(或焊缝检验尺)检查控制筒体对接间隙≤2mm,错边量不大于1.5mm,错口量不大于1mm,然后定位焊,定位焊长度不小于20mm.
3.6滚圆合格,同时进行单节筒体的纵缝合缝。
纵焊缝定位焊,间距200mm,点焊长度100~200mm。
3.7检查单节筒体组对质量,重点检查纵缝对接间隙≤2mm,错边量≤1.5mm,错口量不大于1mm及定位焊质量.合格方可转入下序。
4、焊接工序技术要求
4.1焊接坡口及其母材内外壁用角向磨光机清理出金属光泽,清理范围手工焊每侧各为10~20mm,埋弧焊每侧各为20mm。
并检查母材无裂纹、重皮、毛刺、缺口等缺陷,如有缺陷需及时消除。
4.2焊接对口情况检查,看是否做到中径对齐;焊接对口的局部间隙过大时,应设法修整到要求尺寸,严禁在间隙内加填塞物。
4.3在露天作业时,焊接场所应采取搭设防风、雨棚等措施;要求相对湿度<90%,风速<10m/s;焊接环境温度应大于0℃(低于0℃时,应在坡口两侧100㎜范围内加热到15℃以上)。
4.4焊接方法及要求
4.4.1筒节焊缝采用埋弧自动焊法,每节卷制后先焊内缝,外部清根。
清根时采用碳弧气刨,选用较大电流防止夹碳。
4.4.2筒节壁厚在14㎜以下(含14mm),埋弧自动焊时不开坡口;筒节厚度在14㎜以上,焊接时根据图纸要求开坡口,图纸无要求时,根据焊接工艺规范要求
进行。
4.4.3进行焊接时,特别要保证起弧、收弧的质量,需加引弧、收弧板,去除引弧、收弧时,必须注意去除部位必须保证平整,并用直尺靠平检验,不允许出现凹进、凸出等缺陷。
4.4.4在焊接筒节中应按批次做产品焊接试板。
每种厚度规格的板材做一种,记录焊接参数。
4.4.5点固焊
4.4.
5.1点固焊时焊工必须持有相应位置的焊工合格证。
所有焊条、预热温度、焊接工艺应与正式施焊时相同。
4.4.
5.2严禁在被焊工件表面乱点乱焊或随意焊接临时支撑物,若对口时采用加楔对口,则不应伤损母材,且将残留焊疤打磨平整。
4.4.
5.3点焊时焊点尽量做到长度相同,间距均匀相等。
塔体点固焊在外侧,以便电弧气刨清除。
4.4.
5.4点固焊后应对点固焊缝,特别是收弧、引弧处进行斜坡式打磨,并仔细检查各焊点无缺陷,如有缺陷应立即清除,重新进行点固焊。
4.4.
5.5点固焊完毕后工件不得移动或用力敲击,以防变形或产生裂纹。
4.4.6打底焊及层间焊接
4.4.6.1打底焊时应对点固焊处进行检查,如有缺陷消除后再行施焊。
4.4.6.2焊层厚度以不超过5 mm为准。
摆动宽度不大于所用焊条直径的1.5倍。
4.4.6.3焊接时应分层分道焊接,每层焊接完毕后应清理干净,并检查有无缺陷,消除缺陷后再进行次层焊接。
4.5对接焊缝外形尺寸:
注:b:对接间隙 g:坡口宽度
(1)任意连续300mm长度内。
(2)低于50mm长度内。
(3)任意25mm长度内。
4.6焊缝外观质量
4.6.1焊缝不允许有裂纹、夹渣、气孔、漏焊、烧穿、弧坑、未熔合及深度〉0.5mm 的咬边。
4.6.2焊缝和热影响区表面不得有裂纹、气孔、夹渣、未熔合及低于焊缝高度的弧坑。
4.6.3熔渣、毛刺等应清除干净。
4.6.4焊缝外形尺寸超出规定值时,应进行修磨,局部补焊,返修后应合格。
5、无损检测技术要求
5.1无损检测需在焊缝外观检验合格后进行。
5.2焊缝无损检测均按压力容器无损探伤检验标准JB/T4730执行。
5.3无损探伤检验检验内容及标准。
5.4所有筒节端头处均布片射探,其余选择最薄弱焊缝处布片射探。
5.5无损探伤人员必须持有Ⅱ级以上证书。
6、校圆技术要求
6.1回圆:由于在埋弧焊接的过程中,受环境、焊接参数、操作不规范、操作人
员素质等诸多因素的影响,造成焊缝出现凹头和凸头的现象,需要对筒节焊缝进行回圆处理。
6.2纵缝焊完后,用钢卷尺、钢板尺、样板等检查筒节尺寸符合要求,对超差筒体进行回圆.
6.2.1筒节对接纵缝处环向棱角的要求:用1000mm样板检查,筒体环向棱角≤3 mm 6.2.1筒体任意切断面圆度公差应为:dmax-dmin≤5‰D.。