工艺铁氧体法共22页
永磁铁氧体生产工艺

永磁铁氧体生产工艺永磁铁氧体是一种具有高磁性和高温稳定性的磁性材料,广泛应用于电机、发电机、传感器等领域。
永磁铁氧体的生产工艺一般包括以下几个步骤:1. 原料准备:永磁铁氧体的主要原料是氧化铁、氧化钡、氧化钴等化合物,需要按照一定的比例进行配料,同时还需要添加一定的助磁剂和其他添加剂。
配料完成后,将原料送入球磨机进行混合研磨,以提高混合度和颗粒粒度的均匀性。
2. 造粒压制:将研磨后的混合粉末送入造粒机进行压制成形。
常用的造粒方法有干压造粒和湿压造粒两种。
干压造粒是将混合粉末在模具中进行压制,形成预定形状的颗粒;湿压造粒则是在添加一定的液体和黏结剂的情况下进行造粒,然后通过干燥将颗粒固化。
3. 烧结和烧结控制:将压制成形的颗粒送入高温炉进行烧结。
在烧结过程中,由于高温作用,颗粒之间的颗粒间结合力增强,形成致密的材料,颗粒内部排列有序。
烧结温度和时间的控制对于材料的性能具有重要影响,需要进行精确控制。
4. 后处理:烧结后的材料还需要通过一些后处理工艺来进一步提高其性能。
常见的后处理方法包括磁化处理、热处理和磁场处理等。
磁化处理是将材料置于强磁场中进行磁化,以提高材料的磁性能;热处理则是利用高温进行退火或淬火等处理,以改变材料的晶体结构和性能;磁场处理则是利用磁场对材料进行预处理,提高材料的磁性能。
5. 检验和包装:经过上述工艺步骤后,对生产出的永磁铁氧体进行质量检验,包括磁性能测试、密度测试、外观检查等。
合格的产销售前,还需要进行包装和存储,以保证产品的质量和使用寿命。
以上是永磁铁氧体的基本生产工艺,不同厂家和产品可能会有所差异,但总体上都是通过原料准备、造粒压制、烧结和后处理等环节来完成材料的制备。
随着技术的不断发展,工艺也在不断改进和优化,以提高材料的性能和生产效率。
铁氧体生产工艺技术
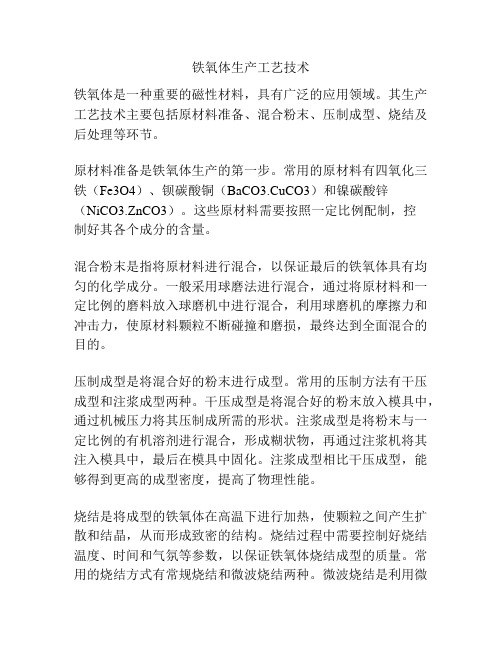
铁氧体生产工艺技术铁氧体是一种重要的磁性材料,具有广泛的应用领域。
其生产工艺技术主要包括原材料准备、混合粉末、压制成型、烧结及后处理等环节。
原材料准备是铁氧体生产的第一步。
常用的原材料有四氧化三铁(Fe3O4)、钡碳酸铜(BaCO3.CuCO3)和镍碳酸锌(NiCO3.ZnCO3)。
这些原材料需要按照一定比例配制,控制好其各个成分的含量。
混合粉末是指将原材料进行混合,以保证最后的铁氧体具有均匀的化学成分。
一般采用球磨法进行混合,通过将原材料和一定比例的磨料放入球磨机中进行混合,利用球磨机的摩擦力和冲击力,使原材料颗粒不断碰撞和磨损,最终达到全面混合的目的。
压制成型是将混合好的粉末进行成型。
常用的压制方法有干压成型和注浆成型两种。
干压成型是将混合好的粉末放入模具中,通过机械压力将其压制成所需的形状。
注浆成型是将粉末与一定比例的有机溶剂进行混合,形成糊状物,再通过注浆机将其注入模具中,最后在模具中固化。
注浆成型相比干压成型,能够得到更高的成型密度,提高了物理性能。
烧结是将成型的铁氧体在高温下进行加热,使颗粒之间产生扩散和结晶,从而形成致密的结构。
烧结过程中需要控制好烧结温度、时间和气氛等参数,以保证铁氧体烧结成型的质量。
常用的烧结方式有常规烧结和微波烧结两种。
微波烧结是利用微波能量对铁氧体进行加热,其烧结速度和效果都比常规烧结要好。
烧结后的铁氧体还需要进行后处理,主要包括磁场处理和涂层处理两个环节。
磁场处理是将铁氧体置于特定强度和方向的磁场中进行处理,以提高其磁化强度和磁化方向。
涂层处理是在铁氧体表面涂层一层耐腐蚀、耐磨损或具有特定功能的材料,以增加其使用寿命和性能。
总之,铁氧体生产工艺技术是一个复杂而严谨的过程。
只有掌握好每个环节的工艺要点和参数,才能够生产出质量优良的铁氧体产品,满足不同领域的需求。
随着科技的不断发展,铁氧体生产技术也在不断创新,提高生产效率和材料性能,推动着铁氧体产业的发展。
铁氧体生产工艺技术

❖ 单晶的制备,是物质的结晶过程,是物质从 液相到固相的转变过程。
❖ 采取的措施:在坩埚底放一块生长方向平行 于器壁的小单晶叫仔晶,以后的结晶沿仔晶 生长。
❖ 常用制单晶的方法:
❖ 一、 熔融固化法
❖ 二、 熔剂法。
❖ 新课教学:
❖ 第六章 粘结永磁
❖ 粘结永磁:是将制备好的永磁粉末加入塑料、 橡胶等粘结剂进行充分混合,然后经压延成型、 挤出成型、注射成型、压缩成型等工艺制得的 永磁体。
❖ 同性和异性:粘结永磁根据在制造工艺中是否 取向分为同性和异性(日本称为等方性和异方 性),其电磁性能明显不一样
❖ 粘结永磁的优点:
❖ 1、 具有较高的永磁性能和粘合剂的物理性能, 如柔性、弹性等;
❖ 2、 可以制备形状复杂、薄壁型的产品; ❖ 3、 产品一致性好,尺寸精度高;
❖ 4、 磁体的比重(密度)小,重量轻,有利于 器件、整机的轻量化;
❖ 1、 有良好的机械加工性能,可进行车、钳、铣、刨、 磨剪切、叠压、卷饶、扭转等;
❖ 2、 耐冲击震动,不易碎; ❖ 3、 可嵌入金属、非金属等全体零件整体成型; ❖ 4、 可以制造成全径向(全辐射)取向的磁体; ❖ 5、 废料可以重新回收使用; ❖ 6、 磁体的Hcj高。
❖ 粘结永磁的缺点:
❖ 由于粘结剂是非磁性物质,制造的磁体产品其 电磁性能(Br、Hcb、(BH)max)只有该类 烧结磁体的50~70%。
❖ 粘结永磁的用途:
❖ 1、 传动方面 ❖ 2、 音响设备方面; ❖ 3、 通讯设备方面; ❖ 4、 磁性密封; ❖ 5、 其它方面。
❖ 粘结永磁发展概况:
❖ 粘结永磁的发展,国际上起步与60年代,中国起步于 70年代。
铁氧体工艺流程
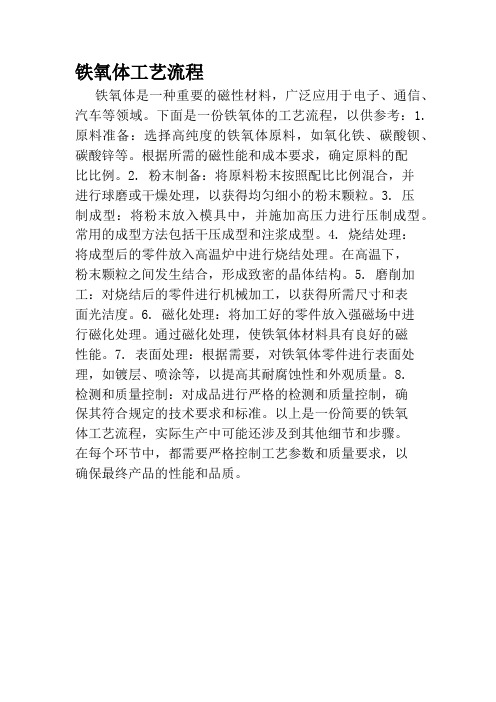
铁氧体工艺流程
铁氧体是一种重要的磁性材料,广泛应用于电子、通信、汽车等领域。
下面是一份铁氧体的工艺流程,以供参考:1. 原料准备:选择高纯度的铁氧体原料,如氧化铁、碳酸钡、碳酸锌等。
根据所需的磁性能和成本要求,确定原料的配
比比例。
2. 粉末制备:将原料粉末按照配比比例混合,并
进行球磨或干燥处理,以获得均匀细小的粉末颗粒。
3. 压
制成型:将粉末放入模具中,并施加高压力进行压制成型。
常用的成型方法包括干压成型和注浆成型。
4. 烧结处理:
将成型后的零件放入高温炉中进行烧结处理。
在高温下,
粉末颗粒之间发生结合,形成致密的晶体结构。
5. 磨削加工:对烧结后的零件进行机械加工,以获得所需尺寸和表
面光洁度。
6. 磁化处理:将加工好的零件放入强磁场中进
行磁化处理。
通过磁化处理,使铁氧体材料具有良好的磁
性能。
7. 表面处理:根据需要,对铁氧体零件进行表面处理,如镀层、喷涂等,以提高其耐腐蚀性和外观质量。
8.
检测和质量控制:对成品进行严格的检测和质量控制,确
保其符合规定的技术要求和标准。
以上是一份简要的铁氧
体工艺流程,实际生产中可能还涉及到其他细节和步骤。
在每个环节中,都需要严格控制工艺参数和质量要求,以
确保最终产品的性能和品质。
铁氧体磁铁制造工艺流程

铁氧体磁铁制造工艺流程铁氧体磁铁制造工艺流程一、概述铁氧体磁铁是一种常见的永磁材料,具有高磁能积、高矫顽力、高稳定性等优点,广泛应用于电机、声学器件、传感器等领域。
本文将介绍铁氧体磁铁的制造工艺流程。
二、原材料准备1. 铁氧体粉末:选择适当的铁氧体粉末是制造高质量铁氧体磁铁的关键。
常用的粉末有SrFe12O19、BaFe12O19等。
2. 粘结剂:粘结剂可以增加粉末之间的黏着力,提高成型后的强度和韧性。
常用的粘结剂有聚乙烯醇(PVA)、聚乙烯(PE)等。
3. 溶剂:溶剂用于稀释粘结剂,使其易于涂覆在粉末表面。
常用的溶剂有水、丙酮等。
4. 添加剂:添加剂可以改善材料性能,如增加导电性能或防腐蚀性能。
常用的添加剂有氧化铁、钛酸酯等。
三、成型1. 压制:将铁氧体粉末和粘结剂混合均匀后,采用压制工艺将其压成所需形状的坯料。
压制时需要控制压力和温度,以确保坯料的致密性和稳定性。
2. 烧结:将压制好的坯料置于高温炉中进行烧结。
烧结过程中,粉末颗粒之间会发生化学反应,形成致密的晶体结构。
同时,粘结剂也会被热分解并挥发出去。
烧结温度和时间需要根据具体材料而定。
四、加工1. 切割:将烧结好的铁氧体坯料切割成所需尺寸的小块。
2. 磨削:对切割好的小块进行表面处理和修整,以获得平整光滑的表面。
3. 磁化:通过电流或强磁场对铁氧体磁铁进行磁化处理。
在这个过程中,材料内部会产生一定方向上的自发极化,并形成一个稳定的磁场。
五、检测和质量控制1. 磁性检测:通过磁性测试仪器检测铁氧体磁铁的磁场强度、剩磁、矫顽力等指标。
2. 外观检测:对铁氧体磁铁进行外观检查,检查是否有裂纹、毛刺等缺陷。
3. 包装和贮存:将合格的铁氧体磁铁进行包装,并在干燥、无尘的环境中储存。
同时,要注意避免与其他磁性物品接触,以免影响其性能。
六、结语以上就是铁氧体磁铁制造工艺流程的详细介绍。
在实际生产中,需要根据具体情况进行调整和改进,以确保产品质量和生产效率。
永磁铁氧体的制备工艺
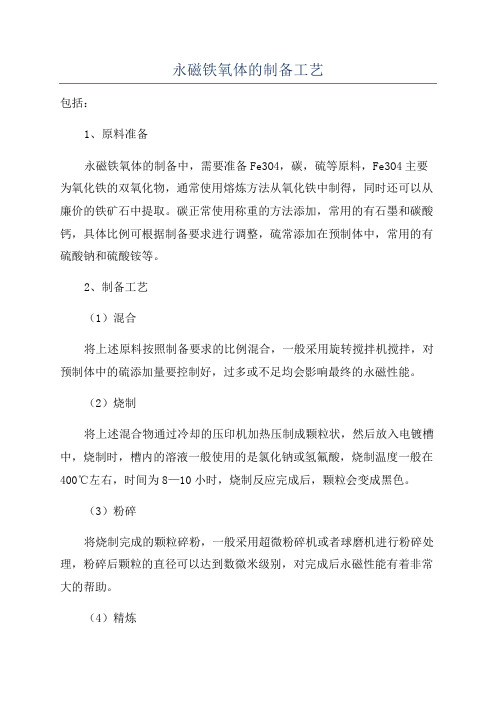
永磁铁氧体的制备工艺
包括:
1、原料准备
永磁铁氧体的制备中,需要准备Fe3O4,碳,硫等原料,Fe3O4主要为氧化铁的双氧化物,通常使用熔炼方法从氧化铁中制得,同时还可以从廉价的铁矿石中提取。
碳正常使用称重的方法添加,常用的有石墨和碳酸钙,具体比例可根据制备要求进行调整,硫常添加在预制体中,常用的有硫酸钠和硫酸铵等。
2、制备工艺
(1)混合
将上述原料按照制备要求的比例混合,一般采用旋转搅拌机搅拌,对预制体中的硫添加量要控制好,过多或不足均会影响最终的永磁性能。
(2)烧制
将上述混合物通过冷却的压印机加热压制成颗粒状,然后放入电镀槽中,烧制时,槽内的溶液一般使用的是氯化钠或氢氟酸,烧制温度一般在400℃左右,时间为8—10小时,烧制反应完成后,颗粒会变成黑色。
(3)粉碎
将烧制完成的颗粒碎粉,一般采用超微粉碎机或者球磨机进行粉碎处理,粉碎后颗粒的直径可以达到数微米级别,对完成后永磁性能有着非常大的帮助。
(4)精炼。
永磁铁氧体的制备工艺

永磁铁氧体的制备工艺一、原料选取1.氧化物原料:通常使用Fe2O3、Fe3O4作为铁源,Co3O4作为钴源。
2.氮化物原料:一般使用氮化铁作为氮源。
3.稀土原料:利用稀土元素的高磁晶各向异性,常使用氧化稀土和相应的稀土钴化合物作为稀土源。
二、配料1.按照化学计量比例将各种原料精细研磨,并通过筛网分选得到均匀的粉末。
2.将各种原料粉末按照一定比例进行混合,通常由铁源、稀土源和钴源组成。
三、烧结1.将混合粉末充分搅拌均匀,并进行压片成坯。
通常采用等静压方法,在模具中施加一定压力,使混合粉末在模具中成型。
2.将坯体进行预烧处理,去除一部分有机物质,并形成初步的金属氧化物。
3.进行烧结处理,将坯体加热至一定温度下,使金属氧化物发生化学反应,形成金属间化合物和磁性颗粒。
4.控制烧结温度和时间,以保证产生足够的磁晶各向异性和颗粒尺寸的增长。
四、后处理1.针对烧结后的材料进行磨削、超声清洗等处理,以去除表面的污染物和不良颗粒。
2.进行磁化处理,通过外加磁场将材料磁化,使其具有永久磁性。
3.进行磁性能测试,进行磁感强度、矫顽力和剩余磁感应强度等性能测试,并根据需要对材料进行优化。
永磁铁氧体的制备工艺繁多,其中最常用的是传统的陶瓷工艺和后来发展起来的粉末冶金工艺。
陶瓷工艺制备的永磁铁氧体具有较高的矫顽力和剩余磁感应强度,但磁晶各向异性较低;而粉末冶金工艺制备的永磁铁氧体具有较高的磁晶各向异性,但矫顽力和剩余磁感应强度较低。
目前,研究人员正在努力寻找新的制备工艺,以获得更优异的永磁铁氧体性能。
综上所述,永磁铁氧体的制备工艺包括原料选取、配料、烧结和后处理等步骤。
这些工艺在生产过程中需要严格控制参数和条件,以获得理想的微观结构和磁性能。
随着技术的不断发展,相信永磁铁氧体的制备工艺还会不断创新和改进,以满足不同领域对其性能的需求。
铁氧体制造工艺流程

铁氧体制造工艺流程一、原料准备。
铁氧体制造呢,原料是很关键的一步。
这就好比咱们做菜,得先把食材准备好。
一般来说,铁氧体的主要原料是铁的氧化物,像三氧化二铁这种。
还得加上一些其他的金属氧化物,比如说氧化锌、氧化镍之类的。
这些原料的纯度可得把控好,要是杂质太多,就像做饭的时候食材不新鲜,那做出来的铁氧体质量肯定不咋地。
而且不同用途的铁氧体,原料的配比那也是不一样的。
就像做不同的菜需要不同的调料比例一样,有的铁氧体可能需要多一点三氧化二铁,有的则需要更多的氧化锌,这都是有讲究的。
二、混合研磨。
原料准备好之后呢,就到了混合研磨这一步。
这一步就像是把食材搅和在一起,不过可不像咱们平时随便搅搅就行。
得用专门的设备,把那些原料磨得细细的,混合得特别均匀。
要是混合不均匀,就像炒菜的时候盐巴没撒匀,有的地方咸死,有的地方没味。
在这个过程中,还得注意控制研磨的时间和力度。
研磨时间太短,原料颗粒可能还是比较大,不利于后续的反应;研磨时间太长呢,又可能会引入一些不必要的杂质。
而且这个力度也要恰到好处,就像按摩一样,太轻没效果,太重可能就把原料给弄坏了。
三、预烧。
混合研磨之后,就迎来了预烧环节。
这预烧啊,就像是给原料来个热身运动。
把混合好的原料放到高温炉里去烧一下,这个温度那也是很关键的。
温度低了,原料之间的反应不完全,就像跑步没跑够距离,没达到效果。
温度高了呢,又可能会出现一些其他的问题,比如说原料可能会被过度烧结,变得特别硬,不利于后续的加工。
预烧的目的就是让原料之间初步发生反应,形成一些小的铁氧体颗粒,为后面的正式烧结做准备。
四、二次研磨。
预烧完了之后,又要进行二次研磨啦。
为啥还要研磨呢?因为预烧之后的原料可能会结块,颗粒大小也不均匀。
这时候再研磨一次,就能让原料更加细腻,颗粒大小更加均匀。
这就像咱们把面团揉了一次之后,再揉一次,会让面团更加光滑一样。
二次研磨的设备和方法跟第一次研磨可能会有些不同,毕竟经过预烧之后原料的性质有点变化了。
铁氧体生产工艺流程
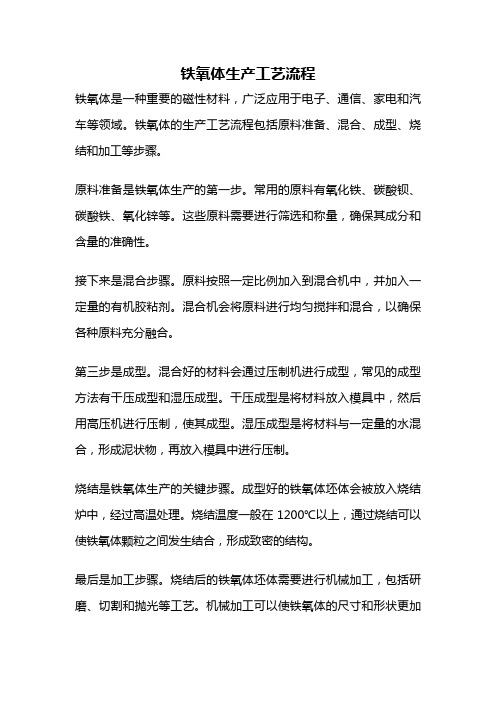
铁氧体生产工艺流程铁氧体是一种重要的磁性材料,广泛应用于电子、通信、家电和汽车等领域。
铁氧体的生产工艺流程包括原料准备、混合、成型、烧结和加工等步骤。
原料准备是铁氧体生产的第一步。
常用的原料有氧化铁、碳酸钡、碳酸铁、氧化锌等。
这些原料需要进行筛选和称量,确保其成分和含量的准确性。
接下来是混合步骤。
原料按照一定比例加入到混合机中,并加入一定量的有机胶粘剂。
混合机会将原料进行均匀搅拌和混合,以确保各种原料充分融合。
第三步是成型。
混合好的材料会通过压制机进行成型,常见的成型方法有干压成型和湿压成型。
干压成型是将材料放入模具中,然后用高压机进行压制,使其成型。
湿压成型是将材料与一定量的水混合,形成泥状物,再放入模具中进行压制。
烧结是铁氧体生产的关键步骤。
成型好的铁氧体坯体会被放入烧结炉中,经过高温处理。
烧结温度一般在1200℃以上,通过烧结可以使铁氧体颗粒之间发生结合,形成致密的结构。
最后是加工步骤。
烧结后的铁氧体坯体需要进行机械加工,包括研磨、切割和抛光等工艺。
机械加工可以使铁氧体的尺寸和形状更加精确,并且提高其表面质量。
除了以上主要的工艺步骤外,还有一些辅助工艺需要注意。
例如,在混合材料时,需要控制搅拌时间和速度,以确保混合均匀;在成型过程中,需要控制压力和模具的温度,以保证成型品的质量;在烧结时,需要控制炉内气氛和烧结时间,以避免产生氧化和杂质。
铁氧体的生产工艺流程复杂且精细,每个步骤都需要严格控制和操作。
只有在每个环节都做好质量控制,才能保证生产出优质的铁氧体产品。
总结一下,铁氧体的生产工艺流程包括原料准备、混合、成型、烧结和加工等步骤。
每个步骤都有其特定的要求和注意事项,需要严格控制和操作。
铁氧体的生产工艺需要高温、高压和精密的设备,以及严格的质量控制措施。
通过这些工艺流程,可以生产出质量优良、性能稳定的铁氧体产品,满足不同领域的需求。
随着科技的发展,铁氧体的生产工艺也在不断创新和改进,以适应市场需求和技术发展。
铁氧体生产工艺
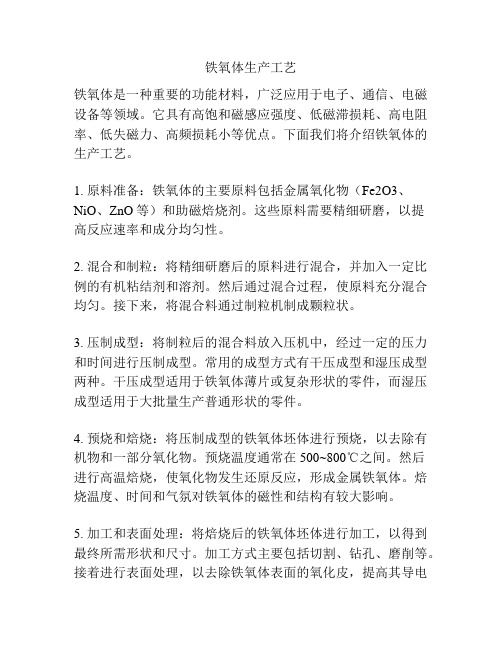
铁氧体生产工艺铁氧体是一种重要的功能材料,广泛应用于电子、通信、电磁设备等领域。
它具有高饱和磁感应强度、低磁滞损耗、高电阻率、低失磁力、高频损耗小等优点。
下面我们将介绍铁氧体的生产工艺。
1. 原料准备:铁氧体的主要原料包括金属氧化物(Fe2O3、NiO、ZnO等)和助磁焙烧剂。
这些原料需要精细研磨,以提高反应速率和成分均匀性。
2. 混合和制粒:将精细研磨后的原料进行混合,并加入一定比例的有机粘结剂和溶剂。
然后通过混合过程,使原料充分混合均匀。
接下来,将混合料通过制粒机制成颗粒状。
3. 压制成型:将制粒后的混合料放入压机中,经过一定的压力和时间进行压制成型。
常用的成型方式有干压成型和湿压成型两种。
干压成型适用于铁氧体薄片或复杂形状的零件,而湿压成型适用于大批量生产普通形状的零件。
4. 预烧和焙烧:将压制成型的铁氧体坯体进行预烧,以去除有机物和一部分氧化物。
预烧温度通常在500~800℃之间。
然后进行高温焙烧,使氧化物发生还原反应,形成金属铁氧体。
焙烧温度、时间和气氛对铁氧体的磁性和结构有较大影响。
5. 加工和表面处理:将焙烧后的铁氧体坯体进行加工,以得到最终所需形状和尺寸。
加工方式主要包括切割、钻孔、磨削等。
接着进行表面处理,以去除铁氧体表面的氧化皮,提高其导电性和表面光洁度。
6. 检测和筛选:对铁氧体产品进行磁性、电学和物理性能的检测。
检测内容包括磁感应强度、磁滞回线、矫顽力、电阻率、介电常数等。
根据产品质量要求,对合格产品进行筛选和分级。
7. 包装和储存:对合格的铁氧体产品进行包装和标识,并存放在干燥、通风的仓库中。
在储存过程中要防止产品受潮、受尘和受污染,以保证其性能不受影响。
以上就是铁氧体的生产工艺,生产铁氧体需要精细的原料准备、混合和制粒、压制成型、预烧和焙烧、加工和表面处理、检测和筛选、以及包装和储存等步骤。
通过这些工艺步骤的合理配合,可以制得具有优良性能的铁氧体产品。
永磁铁氧体的制备工艺

1.3 永磁铁氧体磁粉的合成工艺及原理永磁铁氧体的性能取决于两个方面,一是相成份,与配方,以及原材料的理化性能有很密切关系,对剩磁有重要影响。
二是微结构,合成的工艺往往对产物微结构的起决定作用,不同的合成方法,所生产的永磁铁氧体的微结构差异很大对矫顽力有重要影响。
因此研究铁氧体生产工艺,深入认识其内在规律,可以有效的控制永磁铁氧体的性能,对生产的指导意义巨大。
根据铁氧体磁粉制备方式的不同,可以把永磁铁氧体的生产分为干法合成和湿法合成两类,之后制备磁体的工艺包括成型和烧结基本相同。
干法生产采用氧化物作原料,活性较差,反应程度难以完全,但是工艺简单,应用较为普遍;湿法生产虽然工艺复杂,但由于原料的化学活性较高,铁氧体的磁性能较好,而且还能充分利用各种工业副产品,便于提高质量,降低成本,很有发展前途。
1.3.1 传统的固相合成方法(氧化物法)图1-1 传统固相合成工艺流程图Fig.1-1 The conventional solid phase synthesis process process 目前工业生产中主要以氧化铁,氧化锶为原料,在远低于反应物的熔点或它们低共熔点的温度下以分子扩散的形式,达到离子或者原子的重排,生成新的固溶物即锶铁氧体。
反应的温度以及保温时间应该根据原料的特性比如原材料的粒度,纯度,来源进行控制,预烧温度太高或保温时间太长都容易造成合成的铁氧体异常晶粒长大,产生显著的磁畴壁,降低矫顽力,使磁性能恶化;温度太低可能使扩散不充分,铁氧体化过程不完全,通常的反应温度在1220~1280℃之间。
因为固相反应的原料活性较低,通常把第一次合成称为预烧阶段,之后进行球磨,成型和二次烧结,在成型阶段进行充磁。
因为高温固相法合成永磁铁氧体具有工艺简单,产量大等优点,是当今企业生产永磁铁氧体的最主要方法。
1.3.2 溶胶-凝胶法(Sol-Gel)溶胶-凝胶法也是目前合成永磁铁氧体使用较多的工艺,按照目前对醇盐水解过程的理解,溶胶的形成过程被概念性的描述如下:即以醇盐为原料,在温和条件下进行水解和缩聚反应,而随着缩聚反应的进行以及溶剂的蒸发,具有流动性的Sol逐渐变粘成为略显弹性的固体Gel,然后再在比较低的温度下烧结成为所合成的材料。
永磁铁氧体加工工艺和方法
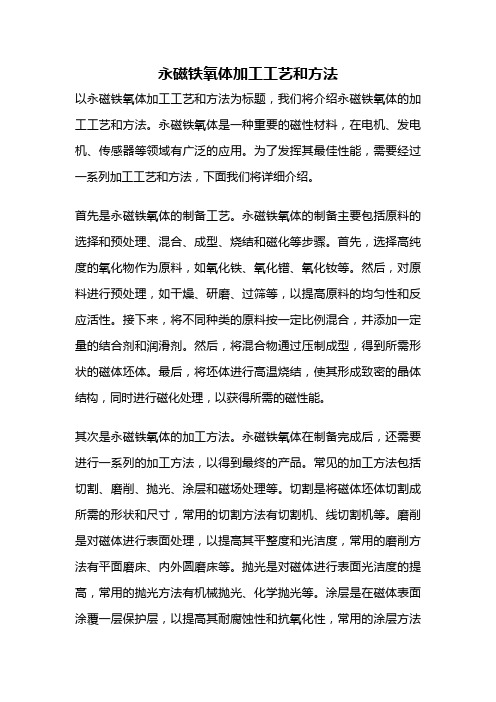
永磁铁氧体加工工艺和方法以永磁铁氧体加工工艺和方法为标题,我们将介绍永磁铁氧体的加工工艺和方法。
永磁铁氧体是一种重要的磁性材料,在电机、发电机、传感器等领域有广泛的应用。
为了发挥其最佳性能,需要经过一系列加工工艺和方法,下面我们将详细介绍。
首先是永磁铁氧体的制备工艺。
永磁铁氧体的制备主要包括原料的选择和预处理、混合、成型、烧结和磁化等步骤。
首先,选择高纯度的氧化物作为原料,如氧化铁、氧化镨、氧化钕等。
然后,对原料进行预处理,如干燥、研磨、过筛等,以提高原料的均匀性和反应活性。
接下来,将不同种类的原料按一定比例混合,并添加一定量的结合剂和润滑剂。
然后,将混合物通过压制成型,得到所需形状的磁体坯体。
最后,将坯体进行高温烧结,使其形成致密的晶体结构,同时进行磁化处理,以获得所需的磁性能。
其次是永磁铁氧体的加工方法。
永磁铁氧体在制备完成后,还需要进行一系列的加工方法,以得到最终的产品。
常见的加工方法包括切割、磨削、抛光、涂层和磁场处理等。
切割是将磁体坯体切割成所需的形状和尺寸,常用的切割方法有切割机、线切割机等。
磨削是对磁体进行表面处理,以提高其平整度和光洁度,常用的磨削方法有平面磨床、内外圆磨床等。
抛光是对磁体进行表面光洁度的提高,常用的抛光方法有机械抛光、化学抛光等。
涂层是在磁体表面涂覆一层保护层,以提高其耐腐蚀性和抗氧化性,常用的涂层方法有喷涂、浸渍等。
磁场处理是通过施加外部磁场,对磁体进行磁化处理,以提高其磁性能,常用的磁场处理方法有直流磁场处理、交变磁场处理等。
在进行永磁铁氧体加工工艺和方法时,还需要注意一些关键技术。
首先是原料的选择和配比,不同种类和比例的原料会影响磁体的磁性能。
其次是成型工艺的控制,包括压制力、压制速度和保压时间等参数的控制,这些参数会影响磁体的致密度和形状。
再次是烧结工艺的控制,包括烧结温度、烧结时间和气氛等条件的控制,这些条件会影响磁体的晶体结构和磁性能。
最后是磁场处理的控制,包括磁场强度、磁化时间和磁化方向等参数的控制,这些参数会影响磁体的磁化程度和磁性能。
软磁铁氧体的生产工艺

软磁铁氧体的生产工艺1.材料准备:软磁铁氧体主要由铁氧体粉末和绝缘材料组成。
首先需要选用高纯度的铁氧体粉末和绝缘材料,然后对这些原料进行粉碎和筛分,以获得所需的颗粒大小范围。
2.混合:将铁氧体粉末和绝缘材料按一定比例混合。
混合的目的是将两种原料充分均匀地混合在一起,以提高磁性能和绝缘性能。
3.成型:将混合后的材料进行成型。
常用的成型方法包括压制和注射成型。
压制是将混合后的材料放入一个模具中,然后通过外力压制成所需形状。
注射成型是将混合后的材料放入一个注射机中,然后通过高压将材料注射到模具中,形成所需的形状。
4.烧结:将成型后的材料进行烧结。
烧结是指将材料加热到一定温度,并在一定的时间内保持该温度,使颗粒间发生结合。
在烧结过程中,材料中的绝缘材料会融化,填充在铁氧体粉末之间,起到增强绝缘性能和控制颗粒间磁耦合的作用。
5.后处理:在烧结后,还需要对软磁铁氧体进行一些后处理。
一般包括退火和表面处理。
退火是指将烧结后的材料再次加热到一定温度,并在一定的时间内保持该温度,以消除内部应力和改善材料的磁性能。
表面处理是指对软磁铁氧体进行抛光、喷涂等处理,以提高其外观和尺寸精度。
软磁铁氧体的生产工艺还会根据具体应用领域的需求进行一些调整和优化。
例如,在电动机领域,可能会采用精密成型和表面镀层的工艺,以提高材料的导磁率和耐腐蚀性。
在电感器领域,可能会采用高压注射成型和高温烧结的工艺,以获得更高的磁感应强度和稳定性。
总之,软磁铁氧体的生产工艺主要包括材料准备、混合、成型、烧结和后处理等步骤。
每个步骤的具体操作和参数设置都会对最终产品的性能和质量产生影响,因此需要严格控制每个步骤的工艺参数,以保证产品的稳定性和一致性。
工艺——铁氧体法

生成铁氧体的机理:
废水中其他金属离子取代铁氧 体晶格中的二价铁离子和三价 铁离子,进入晶体的八面体位 或四面体位,构成晶体的组成 部分,因此不易溶出。由此, 使溶解于水中的重金属离子进 入铁氧体晶体中,生成复合的 铁氧体。
铁氧体法和亚硫酸盐法工艺对比
工艺方案分析
我 们 de 工 艺——铁氧体法
调节池
混凝反应池
斜板斜管沉淀池
铁氧体制作槽Leabharlann 板框压滤池工艺方案分析
• 1. 设计规模
• 总处理水量(日平均流量)Q=300m3/d
• 2.废水水质
• 根据当地环保部门水质监测及其他同类废水水质类比调查, 确定设计水质为:
• 3.处理要求
工艺方案分析
工艺流程图
工艺方案分析
调节池
• 主要用来调节流量和PH,均化水质,同时也能除去车间排水带 出的油类等物质。 • 采用长方体调节池,底面积75m² ,实际高度2.5m • 1)、搅拌设备
铁氧体法
铁氧体处理法
基本原理
铁氧体法是在硫酸亚铁处理法的基础上发展起 来的一种新型处理方法。其机理是使废水中的 各种金属离子形成铁氧体晶粒一起沉淀析出, 从而使废水得到净化。
优点
硫酸亚铁货物广,价格低,处理设备简单, 处理后水能达到排放标准,污泥不会引起二次 污染。
缺点
试剂投加量大,产生的污泥量也大
我国农业发展对氮肥的需要量很大,在氮肥生产的合成氨 工艺上要使用大量的催化剂,利用含铬污泥可以制作合 成氨中的变催化剂。
3、还可以制作红色抛光膏
Thank you
• 采用专用搅拌设备进行搅拌,可以防止水中悬浮物的沉积、使 水质均匀。 • • 2)、提升泵 • 调节池的集水坑安装2台自动搅匀潜污泵,一用一备。
福州铁氧体生产工艺
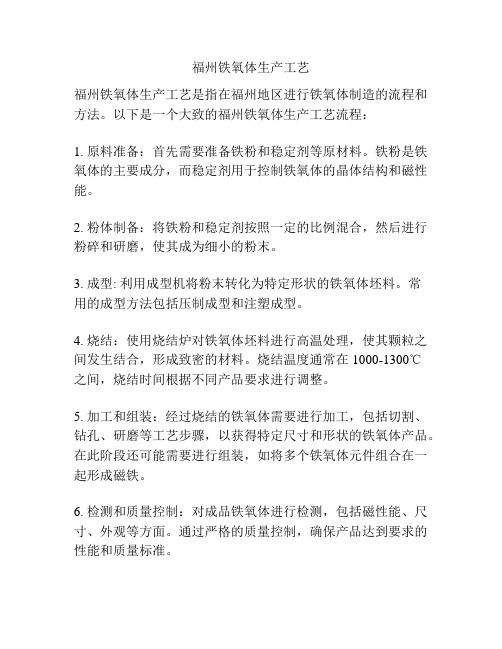
福州铁氧体生产工艺
福州铁氧体生产工艺是指在福州地区进行铁氧体制造的流程和方法。
以下是一个大致的福州铁氧体生产工艺流程:
1. 原料准备:首先需要准备铁粉和稳定剂等原材料。
铁粉是铁氧体的主要成分,而稳定剂用于控制铁氧体的晶体结构和磁性能。
2. 粉体制备:将铁粉和稳定剂按照一定的比例混合,然后进行粉碎和研磨,使其成为细小的粉末。
3. 成型: 利用成型机将粉末转化为特定形状的铁氧体坯料。
常
用的成型方法包括压制成型和注塑成型。
4. 烧结:使用烧结炉对铁氧体坯料进行高温处理,使其颗粒之间发生结合,形成致密的材料。
烧结温度通常在1000-1300℃
之间,烧结时间根据不同产品要求进行调整。
5. 加工和组装:经过烧结的铁氧体需要进行加工,包括切割、钻孔、研磨等工艺步骤,以获得特定尺寸和形状的铁氧体产品。
在此阶段还可能需要进行组装,如将多个铁氧体元件组合在一起形成磁铁。
6. 检测和质量控制:对成品铁氧体进行检测,包括磁性能、尺寸、外观等方面。
通过严格的质量控制,确保产品达到要求的性能和质量标准。
7. 包装和出货:将合格的铁氧体产品进行包装,一般采用防潮、防震等措施,最后进行出货。
福州铁氧体生产工艺可根据具体产品的要求进行调整和优化,以满足不同客户的需求。
铁氧体生产工艺技术——铁氧体的烧结(一)
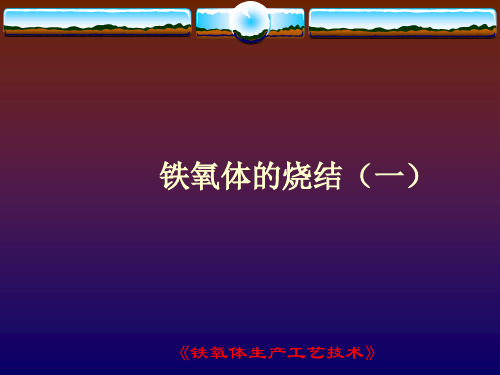
《铁氧体生产工艺技术》
烧结温度曲线
《铁氧体生产工艺技术》
烧结窑炉
《铁氧体生产工艺技术》
烧结窑炉
《铁氧体生产工艺技术》
❖ 2、烧结推动力 ❖ (1)致密化与瓶颈形成的推动力与机制 ❖ 物质由曲率半径小处向曲率半径较大处传递,同一颗
粒内物质传递的结果导致所谓的颗粒“球化”;不同 颗粒接触时,物质将由小颗粒向大颗粒传递,促使颗 粒“粗化”。 ❖ (2)晶体生长的驱动力——界面能 ❖ 晶界移动对晶粒生长的贡献取决于初始的颗粒尺寸比。 ❖ 三、晶粒长大与二次再结晶现象 ❖ 1、晶粒生长与致密化的关系
❖ 复习——讲授——小结—生产工艺技术》
❖ 复习上次课重点: ❖ 烧结的概念,将成型好的坯件在常压或加压下,在空
气中(或保护气体中)高温(T<T熔点=加热,使颗 粒相互结合,排除颗粒间的气孔,提高材料的机械强 度,使之充分铁氧体化(充分固相反应)。
❖ 二、烧结过程分为烧结初期、烧结中期、烧结后期三 个阶段。不同颗粒接触时,物质将由小颗粒向大颗粒 传递,促使颗粒“粗化”,晶界移动对晶粒长大的贡 献取决于初始颗粒的尺寸比。
❖ 这里有一个容易混淆的问题:是否是由于晶粒 长大的结果才导致了烧结体的致密化呢?
《铁氧体生产工艺技术》
❖ 烧结初、中期表面扩散是最有可能的致密化及 粗化的物质传输途径或至少是其中之一,而烧 结后期只有晶界或体积扩散是可能的机制。
❖ 表面扩散传质可同时导致颗粒列阵的收缩和晶 粒生长,
❖ 并且传质过程对颗粒列阵收缩的贡献远大于晶 粒生长导致烧结重新启动(颗粒间二面角的重 新形成)所引起的收缩。
《铁氧体生产工艺技术》
❖ 对于所有气孔均符合热力学收缩密度有所不同 的磁体,初始密度对烧结密度的影响是不大的。 但如果初始密度过低,热力学稳定,致密化将 受明显影响,初始密度高,R小,σp大,有利 于致密化。
铁氧体磁铁生产工艺
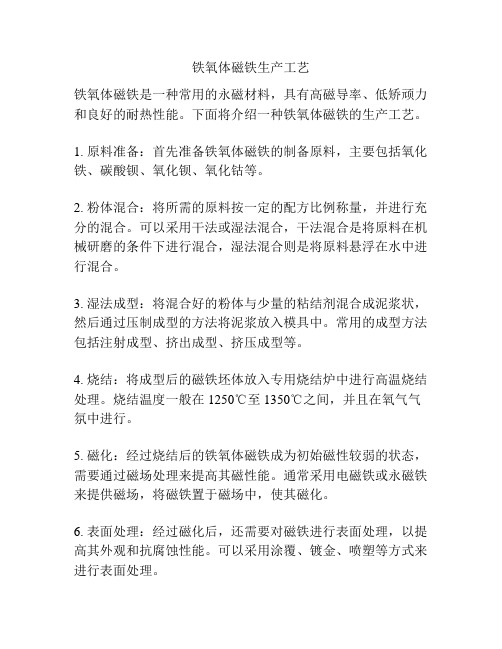
铁氧体磁铁生产工艺铁氧体磁铁是一种常用的永磁材料,具有高磁导率、低矫顽力和良好的耐热性能。
下面将介绍一种铁氧体磁铁的生产工艺。
1. 原料准备:首先准备铁氧体磁铁的制备原料,主要包括氧化铁、碳酸钡、氧化钡、氧化钴等。
2. 粉体混合:将所需的原料按一定的配方比例称量,并进行充分的混合。
可以采用干法或湿法混合,干法混合是将原料在机械研磨的条件下进行混合,湿法混合则是将原料悬浮在水中进行混合。
3. 湿法成型:将混合好的粉体与少量的粘结剂混合成泥浆状,然后通过压制成型的方法将泥浆放入模具中。
常用的成型方法包括注射成型、挤出成型、挤压成型等。
4. 烧结:将成型后的磁铁坯体放入专用烧结炉中进行高温烧结处理。
烧结温度一般在1250℃至1350℃之间,并且在氧气气氛中进行。
5. 磁化:经过烧结后的铁氧体磁铁成为初始磁性较弱的状态,需要通过磁场处理来提高其磁性能。
通常采用电磁铁或永磁铁来提供磁场,将磁铁置于磁场中,使其磁化。
6. 表面处理:经过磁化后,还需要对磁铁进行表面处理,以提高其外观和抗腐蚀性能。
可以采用涂覆、镀金、喷塑等方式来进行表面处理。
7. 检验和包装:对于磁铁的质量进行检验,主要包括外观检验和性能测试。
外观检验主要是检查磁铁的外观是否完好,没有明显的缺陷和损坏。
性能测试则是通过磁力计等设备来测试磁铁的磁性能。
合格的磁铁将进行包装,通常采用塑料袋、泡沫箱等包装材料。
以上是一种常见的铁氧体磁铁生产工艺,不同厂家和产品可能会有所不同。
生产工艺的优化对于提高产品的质量和性能至关重要,随着技术的不断进步,铁氧体磁铁的制备工艺也在不断创新和改进。
铁氧体制备方法

铁氧体制备方法嘿,朋友们!今天咱就来聊聊铁氧体制备方法。
这铁氧体啊,就像是个神奇的小魔术,能变出各种奇妙的性质和用途呢!要制备铁氧体,首先得有合适的原料。
就好比做菜得有食材一样,没有好的原料可不行。
一般常用的有铁的化合物、氧的化合物等等。
然后呢,把这些原料按照一定的比例混合在一起,就像调鸡尾酒似的,得掌握好那个度。
接下来就是关键步骤啦!得进行热处理。
这热处理就像是给铁氧体“蒸桑拿”,让它们在合适的温度下发生反应,逐渐形成我们想要的铁氧体结构。
你说神奇不神奇?就这么烤一烤、烧一烧,就有新东西出来啦!在这个过程中,温度的控制可太重要啦!温度太高,可能就烤糊啦,那可就前功尽弃;温度太低呢,反应又不完全,达不到我们想要的效果。
这就好比烤面包,火候得恰到好处,面包才能香喷喷、软绵绵的。
还有哦,反应的时间也得把握好。
时间太短,铁氧体还没成型呢;时间太长,又可能会有一些不必要的变化。
这就像跑步比赛,跑太快可能会摔倒,跑太慢又拿不到好名次。
制备铁氧体的方法有很多种呢,不同的方法就像是不同的烹饪技巧,做出来的菜味道也不一样。
比如有些方法能让铁氧体的磁性更强,有些方法能让它的导电性更好。
这多有趣呀!咱再想想,这铁氧体在我们生活中可到处都是呢!像那些电子设备里、磁性材料里,都有它的身影。
没有铁氧体,好多东西可都没法正常工作啦!你说这铁氧体制备是不是很有意思?就像一个小小的魔法世界,充满了惊喜和未知。
我们通过不断地尝试和探索,就能创造出各种性能优良的铁氧体。
所以啊,朋友们,可别小看了这铁氧体制备方法。
它可是开启无数可能性的钥匙呢!让我们一起在这个神奇的领域里探索吧,说不定还能发现新的宝藏呢!这难道不让人兴奋吗?难道你不想亲自试试吗?。
钡铁氧体制备工艺

钡铁氧化体制备摘要钡铁氧体由于其独特的结构及性能,在传感元件、光电材料和磁敏光记录材料、颜料、脱氢催化剂等许多方面得到了广泛应用。
本论文主要以Fe2O3、BaCO3 为原料,采用正交实验在不同的配比、烧结温度、保温时间条件下制备六角硬磁钡铁氧体,分析研究了六角硬磁钡铁氧体的制备工艺(原料配比、烧结温度、保温时间)对材料性能的影响,并对不同的影响因素得到不同制备条件下的钡铁氧体进行研究。
实验中采用激光粒度仪对混合后的原料进行粒度分析,混合后的原料粒度在0.20μm-2.00μm范围内,混合粒度越小,比表面积越大,固相反应速度越快。
最后用X射线衍射(XRD)对预烧后得到的粉料进行物相分析,图谱结果表明除了有钡铁氧体BaFe12O19外,还有部分Fe2O3,这是由于BaO与Fe2O3的原料配比分别为1:6和1:5.6,Fe2O3的摩尔浓度比较大,在高温预烧后一部分与BaO形成六角型钡铁氧体,其余部分为Fe2O3。
此现象说明本实验选择的原料配比不能够生成六角硬磁钡铁氧体。
此实验结果为以后钡铁氧体制备研究提供了理论基础与实验依据。
关键词:磁性材料;铁氧体;钡铁氧体Preparation Technical Study of Barium FerriteAbstractBarium ferrite due to its unique structure and performance,the sensing components,optoelectronic materials and magnetic optical recording materials,pigments,and many other aspects of dehydrogenation catalyst has been widely applied. In this paper,mainly Fe2O3,BaCO3as raw material,the use of orthogonal experiment in different ratio,sintering temperature,holding time under the conditions of preparation of hexagonal ferrite hard magnetic barium,analysis of the hexagonal ferrite hard magnetic Preparation of barium ( ratio of raw materials,sintering temperature,holding time) on the material properties and the impact of different factors under different conditions of preparation of barium ferrite research. Experiments using laser particle size analyzer on the mixture of raw materials for particle size analysis,particle size of raw materials mixed in the range of 0.20μm-2.00μm,mixed-grain size smaller than the surface area the greater the faster solid-state reaction. Finally,X-ray diffraction (XRD) after pre-burn phase of the powder for analysis,mapping results show that in addition to spinel ferrite BaFe12O19,there are parts of Fe2O3,which is due to BaO and Fe2O3,respectively,for the 1:6 ratio of raw materials and 1:5.6,Fe2O3 molar concentration of relatively large,high-temperature burn-in the latter part of the formation and BaO spinel-type barium ferrite,for the rest of the Fe2O3. This phenomenon indicates choice in this experiment the ratio of raw materials can not be hard to generate hexagonal ferrite magnetic barium. After the results of this experiment for preparation of barium ferrite research provides a theoretical basis and experimental evidence.Keywords: magnetic materials; ferrite; barium ferrite目录1绪论 (1)1.1铁氧体的特征 (1)1.2铁氧体制备工艺 (3)1.2.1成分配比 (3)1.2.2预烧工艺 (4)1.2.3制粉和成型工艺 (4)1.2.4二次烧结工艺 (4)1.3 铁氧体制备的几种方法 (4)1.3.1 热分解法 (5)1.3.2 化学共沉淀法 (5)1.3.3 电解共沉淀法 (5)1.3.4 喷雾法 (5)1.3.5 自蔓延高温合成法 (6)1.3.6 氧化物法 (6)1.4 铁氧体的晶体结构 (7)1.4.1 尖晶石型铁氧体 (7)1.4.2 磁铅石型铁氧体 (9)1.4.3石榴石型铁氧体 (10)1.5 铁氧体的发展现状 (10)1.5.1铁氧体的发展方向 (10)1.5.2钡铁氧体的应用及其发展方向 (11)1.6本课题研究的目的、内容和意义 (11)2 实验原理 (12)2.1 固相—固相平衡的晶体生长 (12)2.1.1 形变再结晶理论 (12)2.2焙烧动力学及微观分析 (16)2.2.1动力学原理 (17)2.2.2钡铁氧体烧结原理 (18)2.2.3铁氧体的烧结阶段内部结构变化 (19)2.3 扩散原理 (19)2.3.1扩散机构 (19)2.3.2 扩散二种简单的基本模型 (20)2.3.3 扩散的影响因素 (21)3 实验内容及结果分析 (23)3.1 实验原料 (26)3.2 实验设备 (26)3.3 实验方法 (27)3.3.1 配料 (28)3.3.2 研磨 (29)3.3.3 预烧 (30)3.3.4 样品表征 (30)3.4 实验结果分析 (31)3.4.1 粒度分析 (31)3.4.2 试样的X线衍射分析 (31)3.5 实验影响因素 (24)3.5.1 原料的选取 (24)3.5.2 预烧 (24)3.5.3 保温时间 (25)3.5.4 掺杂 (25)4.结论 (36)致谢 ...................................................................................................... 错误!未定义书签。