焊缝探伤检测全集
焊缝的检验方法

焊缝的检验方法嘿,咱今儿个就来唠唠焊缝的检验方法!你说这焊缝啊,就好比是一座建筑的关节,要是这关节不牢固,那整座“大厦”不就危险啦!先来说说外观检查。
这就像是给焊缝来个“全身扫描”,看看它表面有没有啥缺陷呀,比如裂缝啦、气孔啦、咬边啦之类的。
这可不能马虎,得瞪大了眼睛仔细瞧,就像咱挑水果似的,得挑个“光鲜亮丽”的不是?然后呢,有个很重要的方法叫无损检测。
这可神奇啦!就好像给焊缝做了个“透视”,不用破坏它就能知道里面的情况。
像什么超声检测呀,它能发出声波,通过声波的反射来判断焊缝有没有问题。
这就好比是蝙蝠在黑暗中靠声波来“看”路一样,厉害吧!还有射线检测,能拍出焊缝内部的“照片”,有啥毛病一目了然。
还有磁粉检测呢!它能让焊缝上的微小缺陷“现形”,就像孙悟空的火眼金睛,啥妖魔鬼怪都逃不过。
渗透检测也不错,能把那些细小的裂纹都给找出来,就像个细心的侦探在寻找线索。
这些检验方法各有各的用处,一个都不能少哇!你想想,如果没有好好检验焊缝,那在使用的时候出了问题可咋办?那后果可不堪设想啊!所以啊,咱可不能小瞧了这焊缝的检验。
每次看到那些技术人员认真地用各种方法检验焊缝,我就忍不住感叹,这是多么重要的工作呀!他们就像守护焊缝质量的卫士,一丝不苟地确保焊缝的安全可靠。
这可真是个技术活,也是个良心活呀!咱再想想,要是大桥上的焊缝没检验好,那车走在上面多危险;要是飞机上的焊缝有问题,那可不得了啦!所以说呀,焊缝的检验方法那是至关重要的,一点都不能含糊!总之,焊缝的检验方法那是多多益善,每一种都有它独特的作用和价值。
咱得重视起来,让焊缝质量过硬,这样我们的生活才能更安全、更有保障呀!你说是不是这个理儿呢?。
各类型焊缝的可用无损检测方法汇总表
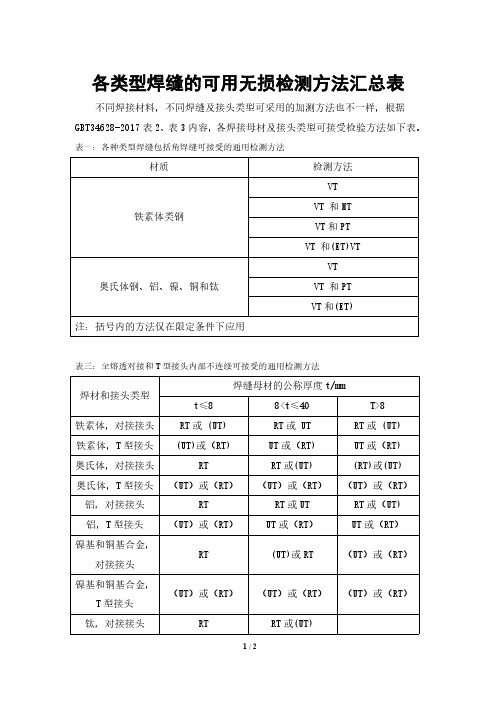
各类型焊缝的可用无损检测方法汇总表
不同焊接材料,不同焊缝及接头类型可采用的加测方法也不一样,根据GBT34628-2017表2、表3内容,各焊接母材及接头类型可接受检验方法如下表。
表一:各种类型焊缝包括角焊缝可接受的通用检测方法
材质检测方法
铁素体类钢
VT
VT和MT
VT和PT VT和(ET)VT
奥氏体钢、铝、镍、铜和钛
VT
VT和PT VT和(ET)
注:括号内的方法仅在限定条件下应用
表三:全熔透对接和T型接头内部不连续可接受的通用检测方法
焊材和接头类型
焊缝母材的公称厚度t/mm
t≤88<t≤40T>8
铁素体,对接接头RT或(UT)RT或UT RT或(UT)
铁素体,T型接头(UT)或(RT)UT或(RT)UT或(RT)
奥氏体,对接接头RT RT或(UT)(RT)或(UT)奥氏体,T型接头(UT)或(RT)(UT)或(RT)(UT)或(RT)铝,对接接头RT RT或UT RT或(UT)铝,T型接头(UT)或(RT)UT或(RT)UT或(RT)镍基和铜基合金,
对接接头
RT(UT)或RT(UT)或(RT)镍基和铜基合金,
T型接头
(UT)或(RT)(UT)或(RT)(UT)或(RT)钛,对接接头RT RT或(UT)
钛,T型接头(UT)或(RT)UT或(RT)注:括号内的方法仅在限定条件下应用。
钢结构焊缝探伤检测方案及对策钢结构检测方法

钢结构焊缝探伤检测方案及对策钢结构检测方法目录一、现场探伤方案 (5)二、现场安装无损检测人员须知 (2)三、现场射线无损检测安全操作管理规程 (2)四、现场辐射事故应急预案 (2)五、无损检测专用工艺规程 (19)现场射线探射方案编制人:批准人:一、探伤内容本工程为XXXXX,根据设计及规范要求需进行射线探伤。
二、探伤方案及时间本次探伤采用便携式X射线探伤设备进行,从20XX年X月XX日起每天22:00~23:00;00:30~6:00三、管理方案1.目的在进行X射线探伤工作时,射线对周围人员身体造成一定伤害,为了避免X 射线造成对人体的伤害,特制定本管理方案。
2.措施2.1因施工需要在施工现场进行X射线探伤时,要采取以下措施:a).探照前要设置防护区(以作业地点问为半径30m至40m)并经射线报警检测合格。
c).安全圈外的通道处,要设专人警戒,并设置报警装置。
d).由于是夜间现场探伤.设有红灯警示。
e).射线探伤人员和操作必须在安全圈外,或具备防护措施的操作室内操作。
f).由于道路在防护区以内,进出人员与车辆在专人的引导下通过。
2.2X射线设备和参数选用时应尽量避开施工人员集中的时间进行2.3在施工现场探伤应尽量避开施工人员集中的时间进行2.4射线操作人员持证上岗2.5射线探伤时,操作人员应在安全区域内进行操作2.6射线探伤完毕后,拆除隔离,进行正常生产活动3.职责项目经理;XX探伤人员:XX监护人员:XX四、作业区域详见示意图:现场射线无损检测安全操作管理规程受控状态编号 EO/JLYR.10.11-2010发布日期 XX实施日期 XX编制:XXX 审核:XXX 批准:XXX现场射线无损检测安全操作管理规程为了确保现场(野外)辐射场所专业人员和放射装置的安全,根据国家《放射性同位素与射线装置安全和防护条列》及国家卫生部发布的《放射工作卫生防护管理办法》和国家环保局批发的《放射性同位素与射线装置安全许可管理办法》等的相关规定,特制定本规程。
焊缝超声波探伤检验规程

焊缝超声波探伤检验规程1 目的指导本公司无损探伤人员工作,规范无损探伤的检验过程。
2 范围本程序适用于公司钢结构产品制造(包括外包外协件)中的无损检验工作。
3 职责3.1品保部探伤员Ⅰ、Ⅱ、Ⅲ级人员负责探伤工作的实施。
3.2品保部探伤员Ⅱ、Ⅲ级人员负责检验规程的编制、现场检测技术指导。
3.3品保部负责无损探伤的质量控制工作,对无损探伤中有争议的问题做出裁决。
3.4品保部负责自检报告的签发。
4 检验规程4.1探伤准备工作a) 距离一波幅曲线:利用RB-1或RB-2试块测试距离一波幅曲线,评定线、定量线和判废线满足GB11345-89标准中9.2.1的B级要求。
b) 探伤灵敏度:不低于评定线,扫查灵敏度在基准敏度上提高6dB。
c) 探伤时机:碳素结构钢应在焊缝冷却到环境温度,低合金结构钢应在完成焊接24小时后进行探伤;另外,探测要经过打磨,外观检验合格后进行探伤。
d) 探伤方式和扫查方式:探伤方式见:扫查方式有锯齿形扫查、前后、左右、环绕、转角扫查等几种方式。
e) 检查部位:检查部位根据GB50205-2001《钢结构工程施工质量验收规范》及设计文件、工艺文件。
f) 抽检率:当设计和合同未对抽检率做出规定时,按GB50205-2001《钢结构工程施工质量验收规范》表5.2.4,当设计和合同对抽检率做出规定时,按设计和合同执行。
4.2探伤方法4.2.1平板对接焊缝a) 探头选择探头的K值选择如表1。
表1 探头的K值根据厚度不同按下表选择图1 平板对接焊缝的超声波探伤4.3.2 T型接头焊接的检验按T型焊缝的特点及GB11345-89标准要求,选择以下三种探伤方式组合实施检验。
4.3.2.1焊缝内部缺陷检测a) 探头选择见(表2)b) 根据不同检验等级要求选择探伤面,探伤面如图1所示。
表2 探头的K值根据腹板厚度不同按下表选择b) 探测位置c) 对所有反射波幅超过定量线的缺陷,均应确定其位置,最大反射波幅所在区域和缺陷指示长度。
焊缝实验

钢轨焊缝探伤知识一、钢轨焊缝的分区探测图.钢轨焊缝各部位扫查方式对钢轨焊缝进行探伤时,一般是将焊缝化分为四个区域,如图所示,以采用不同的方式进行扫查,其中:1区:轨腰及其延伸部分。
一般采用串列式进行扫查,在焊轨厂或焊轨基地,若轨底允许放置探头时,也可采用K型扫查。
2区:轨底部分。
一般采用K型扫查。
3区:轨底角部分。
一般用单探头法进行扫查,用一次波扫查轨底角下部,二次波扫查轨底角上部。
4区:轨头部分。
可从轨头两侧用K型方式进行扫查,也可用70°探头按探测核伤的方式进行单探头法扫查。
附录A GHT型钢轨焊缝超声波探伤对比试块单位为毫米a) GHT-1a 双探头试块b) GHT-1b双探头试块技术要求:1 试块用60kg/m钢轨制作。
平底孔深:≥40mm;平底孔底部至试块另一端长度:≥450mm。
2 不同试块上同一位置平底孔的反射波高相差不超过±2dB。
图A-1 GHT-1型双探头试块单位为毫米a) GHT-5试块分区示意图b) GHT-5试块0°探头区(A区)c)GHT-5试块轨头和轨腰探头区(B区)d) GHT-5试块轨底探头区(C区)技术要求:1 试块用60kg/m钢轨制作。
为加工人工缺陷方便,轨头和轨底可部分切除。
2 不同试块上同一位置横孔或竖孔的反射波高相差不超过±1.5dB。
图A-2 GHT-5型单探头试块探伤灵敏度校准双探头探伤轨腰部位(1). K型扫查将GHT-1a试块上距踏面90mm的3号平底孔反射波高调整到满幅度的80%,如图3-10所示,然后根据探测面情况进行适当表面耦合补偿,一般2dB~6dB,作为轨腰部位的探伤灵敏度。
图轨腰K型扫查探伤灵敏度校准(2).串列式扫查将GHT-1a试块上距轨底40mm的4号平底孔反射波高调整到满幅度的80%,如图3=11所示,然后根据探测面情况进行适当表面耦合补偿,一般2dB~6dB,作为轨腰部位的探伤灵敏度。
焊缝质量检测方法

焊缝质量检测方法1.目测检测方法目测是最简单常用的焊缝质量检测方法之一、通过肉眼直接观察焊缝外观,检查有无裂纹、孔洞、咬边等缺陷。
目测检测可以快速判断焊缝的表面质量和形状。
2.放射检测方法放射检测是利用放射性同位素或X射线对焊缝进行检测。
放射检测分为射线摄影和射线透射两种。
射线摄影通过将射线照射到焊缝上,然后在感光材料上观察形成的曝光图像,根据图像的密度和缺陷形态来判断焊缝的质量。
射线透射是将射线穿过焊缝,通过检测器接收射线,根据接收到的射线强度来判断焊缝的质量。
3.超声波检测方法超声波检测是利用超声波在材料中传播的特性,来进行焊缝质量检测。
超声波的传播速度和焊接缺陷之间存在关联,当焊接缺陷存在时,超声波的传播速度会发生变化。
通过超声波传感器的发射和接收,可以检测焊缝中的缺陷,如裂纹、孔洞、夹杂物等。
4.磁粉检测方法磁粉检测是利用液体磁粉或磁性颗粒在磁场作用下在焊缝表面产生磁化,然后观察磁粉或磁性颗粒的分布情况,从而检测焊缝中的裂纹、疲劳断裂等表面缺陷。
5.渗透检测方法渗透检测是通过将渗透剂涂在焊缝表面,然后在一定时间后将渗透剂清洗掉。
如果焊缝有裂纹或其他缺陷,渗透剂会渗入缺陷处,形成可见的痕迹。
通过观察渗透剂的渗透情况,可以判断焊缝的质量。
以上方法是常用的焊缝质量检测方法,不同的方法适用于不同的焊接方法和焊缝类型。
在进行具体的焊缝质量检测时,需要根据实际情况选择合适的方法,并进行相应的测试和分析。
同时,为了保证焊缝质量的可靠性,应该配合使用多种检测方法进行综合评估和判定。
焊缝探伤试验步骤UT

采用CTS-22 型模拟机对焊缝进行探伤的基本操作步骤:1.根据给定的试板厚度确定灵敏度:板厚在15mm以上:评定线①1x6-9 dB,定量线①1x6-3 dB , 判废线①1x6+5 dB。
2.测定探头的前沿距离和K 植:探头置于CSK-IA 试块上。
对准R100 圆弧面,前后移动探头,找到最高反射回波,量出此时探头至试块边缘的距离X ,则探头前沿L0=100-X mm。
例如:量出探头至试块边缘的距离X为90mm,则前沿距离为L0=100-90=10mm。
然后将探头对准CSK-IIIA 试块上埋深为30mm 的① 1x6 孔,前后左右移动探头,找到最高回波,量出探头至试块边缘的距离Y,, 则探头的K 值为:K =(Y+L 0-40)/30。
3•假设焊缝试样T=20mm,采用CSK-IA、IIIA试块,K2探头。
<1>按水平1:1 调节扫描速度(1)将始波前沿对准零位,探头置于CSK-IIIA 试块上,选定深度分别为20mm, 40mm 的横孔,先将探头对准深度d=20mm 的横孔, 探头前沿到试块边缘的距离定为80-L。
,找到最高回波,用[微调]将其前沿调至水平刻度50处。
用[水平]旋扭将回波前沿调至40mm处。
(2)移动探头,将探头对准深度d=40mm 的横孔,探头前沿到试块边缘的距离定为120-L。
,找到最高回波,若此回波前沿所对的水平刻度值为y,应求出x=80-y。
当x为0时,正好是水平1:1 ;当x 为正时,用[微调]将回波向大读数移动到y+2| x|处;当x为负时,用[微调]将回波向小读数移动到y-2|x|处。
(3)用[水平]将回波前沿调至水平刻度80处。
(4)再将探头对准深度d=20mm的横孔,探头前沿到试块边缘的距离定为80-L。
,看反射波的位置是否正好在40处。
如果是,调整完毕;如果不是,按上述方法重复调节。
<2>测距-波曲线:探头对准d=10m⑪1x6,把[增益]旋扭调至最大,[粗调衰减器]调至20dB处,找到最高反射波,调[微调衰减器],当回波靠近80% 波高时,调[增益],使其最大回波达到80%然后固定[增益],调[衰减器],分别使d=20, 30, 40mm勺①1x6最高反射回波达到80%记录相应的衰减器的读数于下表中,并作出相应的距离-波幅曲线。
焊缝探伤检测方法

焊缝探伤检测方法焊缝探伤检测是焊接质量控制中非常重要的一环,它可以有效地发现焊接缺陷,保证焊接质量,提高焊接工艺的可靠性。
在焊接工程中,焊缝探伤检测方法的选择和应用对于焊接质量的保证至关重要。
本文将介绍几种常见的焊缝探伤检测方法。
首先,我们来介绍一下常见的焊缝探伤检测方法之一——X射线探伤。
X射线探伤是利用X射线穿透物体的原理,通过对物体吸收和散射X射线的不同特性进行检测,从而发现焊接缺陷。
X射线探伤方法可以对焊缝进行全面、立体的检测,适用于各种类型的焊接工艺和焊接材料。
但是X射线探伤设备成本较高,操作需要专业人员,并且对环境有一定的辐射影响。
其次,超声波探伤是另一种常见的焊缝探伤检测方法。
超声波探伤利用超声波在材料中传播的特性,通过检测超声波在焊接部位的传播情况,来判断焊接部位是否存在缺陷。
超声波探伤方法具有灵敏度高、分辨率高、操作方便等优点,适用于各种材料的焊缝检测。
但是超声波探伤需要对焊接工件进行耦合剂处理,且对焊接工件的几何形状和表面质量要求较高。
另外,磁粉探伤是一种简单有效的焊缝探伤方法。
磁粉探伤利用磁场对材料的磁性特性进行检测,通过在焊接部位涂覆磁粉,再施加磁场,从而发现焊接缺陷。
磁粉探伤方法操作简单,成本较低,适用于各种形状的焊缝检测。
但是磁粉探伤方法对环境要求较高,且只能检测表面缺陷,对于深层缺陷的检测能力较弱。
最后,涡流探伤是一种适用于导电材料的焊缝探伤方法。
涡流探伤利用交变磁场在导电材料中产生涡流的原理,通过检测涡流的变化来发现焊接缺陷。
涡流探伤方法对材料的电导率和磁导率要求较高,适用于金属材料的焊缝检测。
但是涡流探伤方法只能检测表面缺陷,对于深层缺陷的检测能力较弱。
综上所述,不同的焊缝探伤检测方法各有优缺点,选择合适的方法取决于具体的焊接工艺和焊接材料。
在实际应用中,可以根据需要综合利用多种探伤方法,以提高焊接质量的保证。
焊缝探伤检测方法的选择和应用对于焊接质量的保证至关重要,希望本文介绍的几种方法能够对焊接工程实践提供一定的参考和帮助。
焊缝探伤检测方法
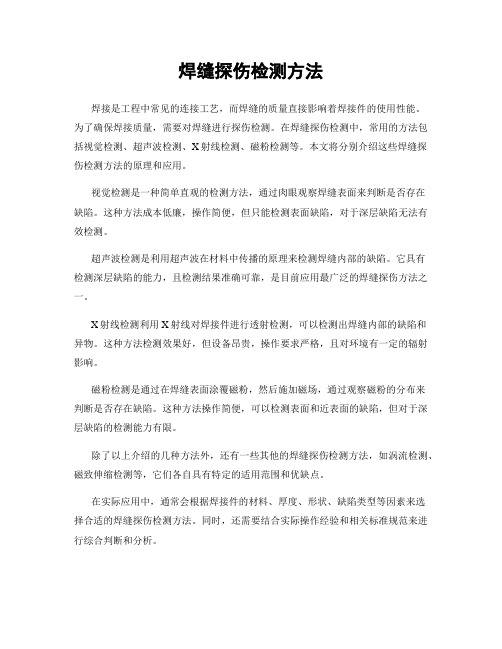
焊缝探伤检测方法焊接是工程中常见的连接工艺,而焊缝的质量直接影响着焊接件的使用性能。
为了确保焊接质量,需要对焊缝进行探伤检测。
在焊缝探伤检测中,常用的方法包括视觉检测、超声波检测、X射线检测、磁粉检测等。
本文将分别介绍这些焊缝探伤检测方法的原理和应用。
视觉检测是一种简单直观的检测方法,通过肉眼观察焊缝表面来判断是否存在缺陷。
这种方法成本低廉,操作简便,但只能检测表面缺陷,对于深层缺陷无法有效检测。
超声波检测是利用超声波在材料中传播的原理来检测焊缝内部的缺陷。
它具有检测深层缺陷的能力,且检测结果准确可靠,是目前应用最广泛的焊缝探伤方法之一。
X射线检测利用X射线对焊接件进行透射检测,可以检测出焊缝内部的缺陷和异物。
这种方法检测效果好,但设备昂贵,操作要求严格,且对环境有一定的辐射影响。
磁粉检测是通过在焊缝表面涂覆磁粉,然后施加磁场,通过观察磁粉的分布来判断是否存在缺陷。
这种方法操作简便,可以检测表面和近表面的缺陷,但对于深层缺陷的检测能力有限。
除了以上介绍的几种方法外,还有一些其他的焊缝探伤检测方法,如涡流检测、磁致伸缩检测等,它们各自具有特定的适用范围和优缺点。
在实际应用中,通常会根据焊接件的材料、厚度、形状、缺陷类型等因素来选择合适的焊缝探伤检测方法。
同时,还需要结合实际操作经验和相关标准规范来进行综合判断和分析。
总的来说,焊缝探伤检测是焊接质量控制中至关重要的一环,选择合适的检测方法并进行准确可靠的检测,对于确保焊接件的质量和安全具有重要意义。
希望本文介绍的焊缝探伤检测方法能够对相关人员有所帮助,提高焊接质量,确保工程安全。
焊缝检测方法

焊缝检测方法1.焊缝的外观检查(1)焊缝质量的外观检查,应按设计文件规定的标准在焊缝冷却后进行,梁柱构件以及厚板焊接件,应在完成焊接工作24h后,对焊缝及热影响区是否存在裂缝进行复查;(2)焊缝表面应均匀、平滑,无折皱、间断和未满焊,并与基本金属平缓连接,严禁有裂纹、夹渣、焊瘤、烧穿、弧坑、针状气孔和熔合性飞溅等缺陷;(3)所有焊缝均应进行外观检查,当发现有裂纹疑点时,可用磁粉探伤或着色渗透探伤进行复查,(4)对焊缝上出现的间断、凹坑、尺寸不足、弧坑、咬边等缺陷,应予补焊,补焊焊条直径不宜大于4mm.(5)修补后的焊缝应用砂轮进行修磨,并按要求重新进行检查.2.焊缝的超声波探伤检查(1)图纸和技术文件要求全熔透的焊缝,应进行超声波探伤检查;(2)超声波探伤检查应在焊缝外观检查合格后进行,焊缝表面不规则及有关部位不清洁的程度,应不妨碍探伤的进行和缺陷的辨认,不满足上述要求时事前应对需探伤的焊缝区域进行铲磨和修整;(3)全熔透焊缝的超声波探伤检查数量,应按设计文件要求,当发现有超过标准的缺陷时,应全部进行超声波检查;(4)超声波探伤检查应根据设计文件规定的标准进行;超声波探伤的检查等级按《钢焊缝手工超声波检验方法和探伤结果分级》GB11345-89规定进行验收。
(5)超声波检查应做详细记录,并写出检查报告;(6)经检查发现的焊缝不合格部位,必须进行返修,并应按同样的焊接工艺进行补焊,再用同样的方法进行质量检查;(7)当焊缝有裂纹、未焊透和超标准的夹渣、气孔时,必须将缺陷清除后重焊。
清除可用碳弧气刨或气割进行;(8)焊缝出现裂纹时,应由焊接技术负责人主持进行原因分析,制定出措施后方可返修。
当裂纹界限清楚时,应从裂纹两端加长50mm处开始,沿裂纹全长进行清除后再焊接。
(9)低合金结构钢焊缝返修,在同一处返修次数不得超过2次。
对经过2次返修仍不合格的焊缝,则要更换母材,或由责任工程师会同设计和专业质量检验部门协商处理。
焊缝检测方法
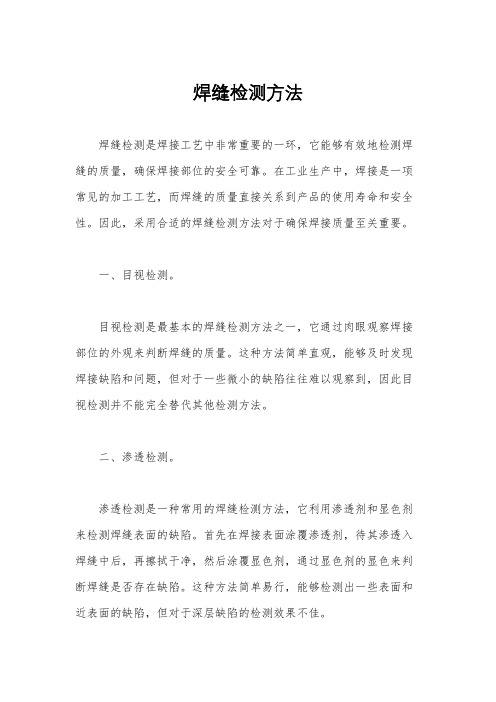
焊缝检测方法焊缝检测是焊接工艺中非常重要的一环,它能够有效地检测焊缝的质量,确保焊接部位的安全可靠。
在工业生产中,焊接是一项常见的加工工艺,而焊缝的质量直接关系到产品的使用寿命和安全性。
因此,采用合适的焊缝检测方法对于确保焊接质量至关重要。
一、目视检测。
目视检测是最基本的焊缝检测方法之一,它通过肉眼观察焊接部位的外观来判断焊缝的质量。
这种方法简单直观,能够及时发现焊接缺陷和问题,但对于一些微小的缺陷往往难以观察到,因此目视检测并不能完全替代其他检测方法。
二、渗透检测。
渗透检测是一种常用的焊缝检测方法,它利用渗透剂和显色剂来检测焊缝表面的缺陷。
首先在焊接表面涂覆渗透剂,待其渗透入焊缝中后,再擦拭干净,然后涂覆显色剂,通过显色剂的显色来判断焊缝是否存在缺陷。
这种方法简单易行,能够检测出一些表面和近表面的缺陷,但对于深层缺陷的检测效果不佳。
三、超声波检测。
超声波检测是一种非接触式的焊缝检测方法,它通过超声波在材料中传播的速度和衰减程度来检测焊缝的质量。
这种方法能够检测出焊缝内部的各种缺陷,如气孔、夹杂、裂纹等,对于焊接质量的评估非常准确。
但是,超声波检测设备价格较高,操作技术要求较高,需要专业人员进行操作和解读结果。
四、X射线检测。
X射线检测是一种常用的焊缝检测方法,它通过照射焊接部位并记录X射线透射图像来判断焊缝的质量。
这种方法能够检测出焊缝内部的各种缺陷,对于厚壁焊接件的检测效果尤为明显。
但是,X射线检测设备较为昂贵,操作技术要求较高,需要专业人员进行操作和解读结果。
综上所述,焊缝检测是确保焊接质量的重要环节,不同的检测方法各有优劣。
在实际生产中,应根据具体情况选择合适的检测方法,以确保焊接质量和产品安全可靠。
同时,对于焊接人员来说,应加强对焊缝检测方法的学习和实践,提高自身的检测能力和水平,为工业生产的安全和发展贡献自己的力量。
焊缝检查规则参照下表进行

项目
说明
探伤范围
按单面单侧0~1跨距范围内
检查方法
初始探伤
Z形扫查、左右扫查、前后扫查、斜平行扫查
规定探伤
左右扫查、前后扫查、首振扫查及必要的斜平行扫查
测定范围(时间轴)
δ≤30mm时为200mm
30mm<δ≤40mm时为250mm
探头
5P9×9K2.5或5Z10×10A70
耦合剂
化学浆糊或75%以上的甘油
装置调用标准试验片
CSK-IK,RB-2
探伤灵敏度(感度)调整用
标准试验片
RB-2
距离波幅校正曲线(DAC)的绘制
按RB-2的Φ3孔
灵敏度及检出水平
判废线:-4dB,定量线:-10dB,评定线:-16dB
检测比例
一级焊缝100%
二级焊缝20%
检测时机
焊后24小时
焊缝探伤举例--用斜探头扫查25mm厚钢板的焊缝(图示)
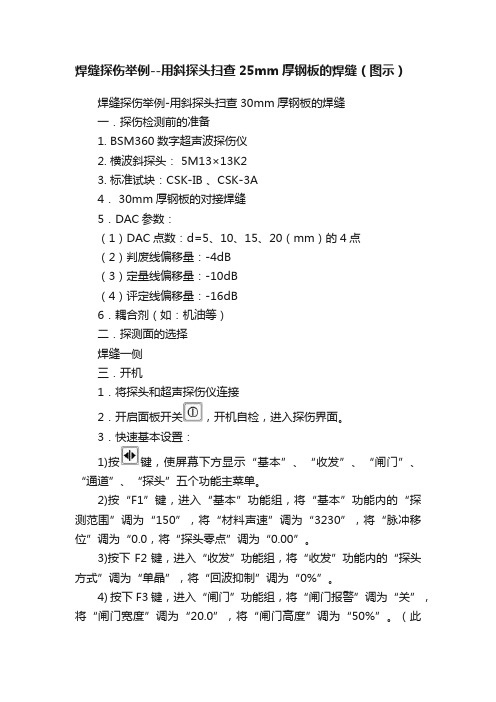
焊缝探伤举例--用斜探头扫查25mm厚钢板的焊缝(图示)焊缝探伤举例-用斜探头扫查30mm厚钢板的焊缝一.探伤检测前的准备1. BSM360数字超声波探伤仪2. 横波斜探头:5M13×13K23. 标准试块:CSK-IB 、CSK-3A4. 30mm厚钢板的对接焊缝5.DAC参数:(1)DAC点数:d=5、10、15、20(mm)的4点(2)判废线偏移量:-4dB(3)定量线偏移量:-10dB(4)评定线偏移量:-16dB6.耦合剂(如:机油等)二.探测面的选择焊缝一侧三.开机1.将探头和超声探伤仪连接2.开启面板开关,开机自检,进入探伤界面。
3.快速基本设置:1)按键,使屏幕下方显示“基本”、“收发”、“闸门”、“通道”、“探头”五个功能主菜单。
2)按“F1”键,进入“基本”功能组,将“基本”功能内的“探测范围”调为“150”,将“材料声速”调为“3230”,将“脉冲移位”调为“0.0,将“探头零点”调为“0.00”。
3)按下F2键,进入“收发”功能组,将“收发”功能内的“探头方式”调为“单晶”,将“回波抑制”调为“0%”。
4) 按下F3键,进入“闸门”功能组,将“闸门报警”调为“关”,将“闸门宽度”调为“20.0”,将“闸门高度”调为“50%”。
(此条内容的调整可根据使用者的习惯而定)。
5)按下F4键,进入“通道”功能组,将“探伤通道”调为所需的未存储曲线的通道,如“No.1”,此时“设置调出”、“设置保存”和“设置删除”均默认显示为“关”。
6)按下F5键,进入“探头”功能组,将“探头K值”调为“0.00”,将“工件厚度”调为“50.0”,将“探头前沿”调为“0.00”,将“标度方式”调为“声程”。
7)按一下键,使屏幕下方显示“增益”、“DAC1”、“ DAC2”“AVG1”“AVG2”五个功能主菜单。
8)按下F1键,进入“增益”功能组,将全部内容均调为“关”。
9)按下F2键,进入“DAC1”功能组,将“DAC曲线”调为“开”,将“DAC标定点”调为“0”,将“显示标定”调为“开”。
焊缝探伤仪及探头测试方法

焊缝探伤仪及探头测试方法焊缝探伤仪及探头测试方法1、探伤灵敏度余量:A、直探头:a、用2.5MHz、φ20直探头CS-1-5或DB-PZ20-2型标准试块。
b、连接探头并将仪器灵敏度置最大,即发射置强,抑制置零或关,增益置最大。
若此时仪器和探头噪声电平(不含始脉冲处的多次声反射)高于满幅度的10%,则调整衰减或增益,使噪声电平等于满幅度的10%。
记下此时衰减器的读数S0。
c、将探头置于试块端面上探测200mm处φ2平底孔,移动探头使φ2平底孔反射波幅度最高,用衰减器将该波调至满幅度的50%,记下此时衰减器的读数S1,则该探头的相对灵敏度(探伤灵敏度余量)S为:S=S1-S0(dB)。
B、斜探头:连接被测探头并将仪器灵敏度置最高,既发射置强、抑制置零或关、增益置最大。
按直探头的方法测量噪声电平S0,然后将探头置于CSL-1A试块上探测R100园弧面,耦合良好并保持声束方向与试块侧面平行,前后移动探头,使R100园弧面回波幅度最高,调节衰减器将其调至满幅度的50%,设此时衰减器的读数为S2。
则斜探头的灵敏度余量S为:S=S2-S0(dB)。
C、组合阵列探头灵敏度相对偏差:各子探头(各晶片)灵敏度的最大偏差即为组合或阵列探头的灵敏度相对偏差。
2、垂直线性误差:a、连接直探头并在试块上探测任一反射波(一般声程大于50mm)作为参照波,调节探伤仪灵敏度,使参照波的幅度恰为垂直满刻度的100%,且增益或衰减器至少有30dB的调节余量。
测试时允许使用探头压块。
b、用增益或衰减器降低参照波的幅度,并依次记下每衰减2dB时参照波幅度的读数,直至衰减26dB以上。
然后将参照波幅度实测值与表中的理论值相比较,取最大偏差d(+)与最大负偏差d(-),则垂直线性误差为:Δ(+)(-)C、在工作频率范围内,改用不同频率的探头,重复a和b的测试。
3、动态范围:a、连接直探头并在试块上探测任一反射波(一般声程大于50mm)作为参照波。
(完整版)AWSD1.1焊缝超声波探伤-精华(快速学成-最新版)
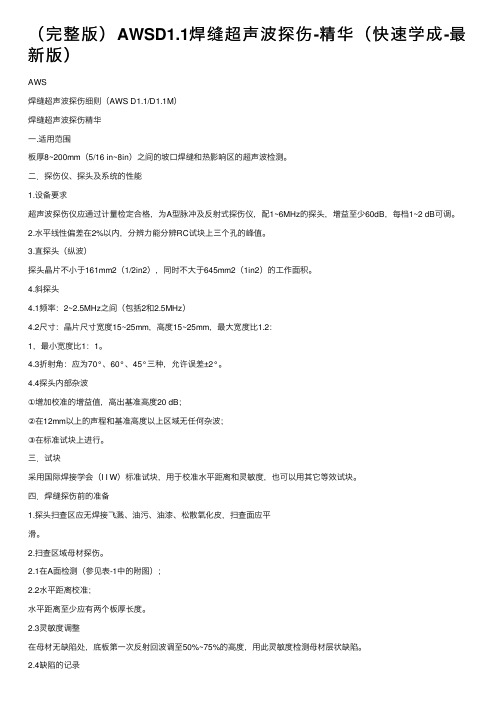
(完整版)AWSD1.1焊缝超声波探伤-精华(快速学成-最新版)AWS焊缝超声波探伤细则(AWS D1.1/D1.1M)焊缝超声波探伤精华⼀.适⽤范围板厚8~200mm(5/16 in~8in)之间的坡⼝焊缝和热影响区的超声波检测。
⼆.探伤仪、探头及系统的性能1.设备要求超声波探伤仪应通过计量检定合格,为A型脉冲及反射式探伤仪,配1~6MHz的探头,增益⾄少60dB,每档1~2 dB可调。
2.⽔平线性偏差在2%以内,分辨⼒能分辨RC试块上三个孔的峰值。
3.直探头(纵波)探头晶⽚不⼩于161mm2(1/2in2),同时不⼤于645mm2(1in2)的⼯作⾯积。
4.斜探头4.1频率:2~2.5MHz之间(包括2和2.5MHz)4.2尺⼨:晶⽚尺⼨宽度15~25mm,⾼度15~25mm,最⼤宽度⽐1.2:1,最⼩宽度⽐1:1。
4.3折射⾓:应为70°、60°、45°三种,允许误差±2°。
4.4探头内部杂波①增加校准的增益值,⾼出基准⾼度20 dB;②在12mm以上的声程和基准⾼度以上区域⽆任何杂波;③在标准试块上进⾏。
三.试块采⽤国际焊接学会(I I W)标准试块,⽤于校准⽔平距离和灵敏度,也可以⽤其它等效试块。
四.焊缝探伤前的准备1.探头扫查区应⽆焊接飞溅、油污、油漆、松散氧化⽪,扫查⾯应平滑。
2.扫查区域母材探伤。
2.1在A⾯检测(参见表-1中的附图);2.2⽔平距离校准;⽔平距离⾄少应有两个板厚长度。
2.3灵敏度调整有如下情况影响(⼲扰)需记录;a. 底部反射全部消失;b. 缺陷波⾼等于或⼤于底部反射波⾼。
有以上缺陷应记录其尺⼨⼤⼩、位置和距A⾯的深度。
五.焊缝探伤1.斜探头的选择:1.1探头频率:2~2.5MHz1.2探头尺⼨:宽15~25mm,⾼15~20mm1.3折射⾓度选择(见表-1)检测⾓度选择(表-1)⼯艺卡材料厚度in.[mm]焊缝类型5/16[8]~≤1-1/2[38]>1-1/2[38]~≤1-3/4[45]>1-3/4[45]~≤2-1/2[60]>2-1/2[60]~≤3-1/2[90]>3-1/2[90]~≤4-1/2[110]>4-1/2[110]~≤5[130]>5[130]~≤7[180]>7[180] ~≤8[200] * ** ** ** **对接 1 0 1 F 1G 或4F1G或5F6或7F8或10F9或11F12或13F 12 FT型 1 0 1F或XF4或XF7F或XF10F或XF11F或XF13F或XF- -⾓接 1 0 1 F或XF1G或4F或XF1G6或7F或XF8或10F或XF9或11F或XF13或14F或XF- -⽓电焊和电渣焊1 0 1 0 1G或P1或P3 6或7P3 11或15 P3 11或15 P3 11或15 P3 11或15**P3符号说明:X —从“C”⾯检验。
焊缝质量检测方法

一外观检验用肉眼或放大镜观察是否有缺陷,如咬边、烧穿、未焊透及裂纹等,并检查焊缝外形尺寸是否符合要求。
二密封性检验容器或压力容器如锅炉、管道等要进行焊缝的密封性试验。
密封性试验有水压试验、气压试验和煤油试验几种.1水压试验水压试验用来检查焊缝的密封性,是焊接容器中用得最多的一种密封性检验方法。
2气压试验气压试验比水压试验更灵敏迅速,多用于检查低压容器及管道的密封性.将压缩空气通入容器内,焊缝表面涂抹肥皂水,如果肥皂泡显现,即为缺陷所在。
3煤油试验在焊缝的一面涂抹白色涂料,待干燥后再在另一面涂煤油,若焊缝中有细微裂纹或穿透性气孔等缺陷,煤油会渗透过去,在涂料一面呈现明显油斑,显现出缺陷位置。
三焊缝内部缺陷的无损检测1 渗透检验渗透检验是利用带有荧光染料或红色染料的渗透剂的渗透作用,显示缺陷痕迹的无损检验法,常用的有荧光探伤和着色探伤。
将擦洗干净的焊件表面喷涂渗透性良好的红色着色剂,待渗透到焊缝表面的缺陷内,将焊件表面擦净。
再涂上一层白色显示液,待干燥后,渗入到焊件缺陷中的着色剂由于毛细作用被白色显示剂所吸附,在表面呈现出缺陷的红色痕迹。
渗透检验可用于任何表面光洁的材料。
2 磁粉检验磁粉检验是将焊件在强磁场中磁化,使磁力线通过焊缝,遇到焊缝表面或接近表面处的缺陷时,产生漏磁而吸引撒在焊缝表面的磁性氧化铁粉.根据铁粉被吸附的痕迹就能判断缺陷的位置和大小。
磁粉检验仅适用于检验铁磁性材料表面或近表面处的缺陷。
3 射线检验射线检验有X射线和Y射线检验两种.当射线透过被检验的焊缝时,如有缺陷,则通过缺陷处的射线衰减程度较小,因此在焊缝背面的底片上感光较强,底片冲洗后,会在缺陷部位显示出黑色斑点或条纹。
X射线照射时间短、速度快,但设备复杂、费用大,穿透能力较Y射线小,被检测焊件厚度应小于30mm.而Y射线检验设备轻便、操作简单,穿透能力强,能照投300mm的钢板。
透照时不需要电源,野外作业方便.但检测小于50mm以下焊缝时,灵敏度不高。
EN 1714 焊缝无损探伤检验-焊缝超声波探伤UT(中文)
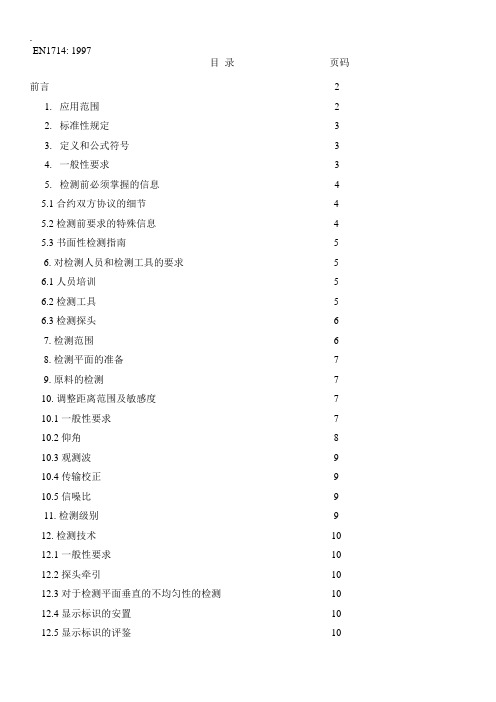
在检测焊缝之前,检测员必须了解以下重要信息:
-如有要求,需有书面检测说明 (见5.3)
-原材料种类及加工方式 (如铸、锻或辗压)
-检测时间 (考虑工作状态,包括热处理因素)
-焊接完之后的热处理时间及范围
-焊缝预处理及测量
-对上表面的要求
-焊接要求及焊接过程中的重要信息
-对检测报告的要求
6.3.3 探头与弯曲检测面之间的配合
检测面与探头底部之间的缝隙不能超过0.5mm。只要满足以下等式 D≥15a(其中D指检测物的直径,单位mm;a为检测方向上的探头底部的长度),圆柱形及球形的上表面一般来说都能达到该要求,若不符合要求,探头底部就必须与上表面的弯曲相配合,灵敏度及范围相应地也要作一定调整。
检测面必须平整,且无妨碍耦合的脏物(如锈、铁渣、焊接时的飞溅物,缺口及波纹)检测面的波纹度须达到一定的要求,即不能使探头和检测面之间的缝隙超过0.5mm。若出现此类情况,检测面就要着焊缝边缘的地方可能与探头之间存在1mm的缝隙)只有在这种条件下才是允许的:即至少附加一个入射角从这一边进行检测,因为彼此间过大的缝隙而导致检测范围受限,因而这项附加检测是必要的。
频率为1MHz的声波可以用于长波程及普通的波衰减情况下的焊缝检测。
6.3.2 入射角
检测过程中若使用横波,且波束是由对面的上表面反射而来的,那么波束的入射角务必大于或等于350,且最好不大于700。若有多个入射角,那么至少要有一个角探头符合该条件。此外,至少有一个入射角尽可能与焊缝侧面成直角,如果检测中要求使用两个或更多的入射角,额定入射角之间相差至少100,如果焊缝呈弯曲状,探头和对面反射面的入射角大小可以借助横截面图或按照 prEN 583-2中所说的方法加以确定,如果入射角不能按上述标准确定的话,务必在检测报告中简要介绍一下入射条件,未检测范围及出现的困难与问题。
焊缝探伤检测全集

焊缝探伤检测全集焊缝探伤检测全集物理探伤就是不产生化学变化的情况下进展无损探伤。
一、什么是无损探伤?答:无损探伤是在不损坏工件或原材料工作状态的前提下,对被检验部件的外表和部质量进展检查的一种测试手段。
二、常用的探伤方法有哪些?答:常用的无损探伤方法有:*光射线探伤、超声波探伤、磁粉探伤、渗透探伤、涡流探伤、γ射线探伤、萤光探伤、着色探伤等方法。
三、试述磁粉探伤的原理?答:它的根本原理是:当工件磁化时,假设工件外表有缺陷存在,由于缺陷处的磁阻增大而产生漏磁,形成局部磁场,磁粉便在此处显示缺陷的形状和位置,从而判断缺陷的存在。
四、试述磁粉探伤的种类?1、按工件磁化方向的不同,可分为周向磁化法、纵向磁化法、复合磁化法和旋转磁化法。
2、按采用磁化电流的不同可分为:直流磁化法、半波直流磁化法、和交流磁化法。
3、按探伤所采用磁粉的配制不同,可分为干粉法和湿粉法。
五、磁粉探伤的缺陷有哪些?答:磁粉探伤设备简单、操作容易、检验迅速、具有较高的探伤灵敏度,可用来发现铁磁材料镍、钴及其合金、碳素钢及*些合金钢的外表或近外表的缺陷;它适于薄壁件或焊缝外表裂纹的检验,也能显露出一定深度和大小的未焊透缺陷;但难于发现气孔、夹碴及隐藏在焊缝深处的缺陷。
六、缺陷磁痕可分为几类?答:1、各种工艺性质缺陷的磁痕;2、材料夹渣带来的发纹磁痕;3、夹渣、气孔带来的点状磁痕。
七、试述产生漏磁的原因?答:由于铁磁性材料的磁率远大于非铁磁材料的导磁率,根据工件被磁化后的磁通密度B =μH来分析,在工件的单位面积上穿过B根磁线,而在缺陷区域的单位面积上不能容许B根磁力线通过,就迫使一局部磁力线挤到缺陷下面的材料里,其它磁力线不得不被迫逸出工件外表以外出形成漏磁,磁粉将被这样所引起的漏磁所吸引。
八、试述产生漏磁的影响因素?答:1、缺陷的磁导率:缺陷的磁导率越小、则漏磁越强。
2、磁化磁场强度〔磁化力〕大小:磁化力越大、漏磁越强。
3、被检工件的形状和尺寸、缺陷的形状大小、埋藏深度等:当其他条件一样时,埋藏在外表下深度一样的气孔产生的漏磁要比横向裂纹所产生的漏磁要小。
工业管道焊缝外部质量检验
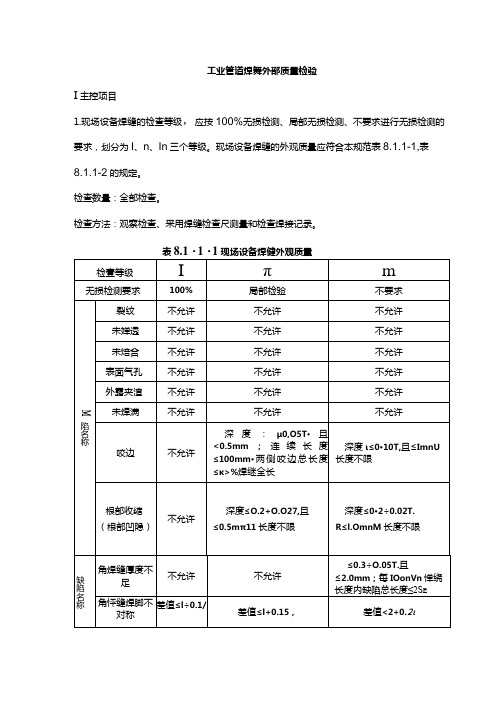
工业管道焊舞外部质量检验I主控项目1.现场设备焊缝的检查等级,应按100%无损检测、局部无损检测、不要求进行无损检测的要求,划分为I、n、In三个等级。
现场设备焊缝的外观质量应符合本规范表8.1.1-1,表8.1.1-2的规定。
检查数量:全部检查。
检查方法:观察检查、采用焊缝检查尺测量和检查焊接记录。
注:1当咬边经磨削修整并平滑过渡时,可按焊缝一侧较薄母材最小允许厚度值评定。
2角焊缝焊脚不对称在特定条件下要求平缓过渡时,不受本规定限制。
3除注明角焊缝缺陷外,其余均为对接、角接焊缝通用。
4表中T为母材厚度;t为设计焊缝厚度。
5表中公式的常量单位为mmβ2、管道焊缝的检查等级,应按现行国家标准《工业金属管道工程施工质量验收规范》GB50184的规定划分为I、n、m、IV、V五个等级。
管道焊缝的外观质量应符合本规范表8.1.2-1、表8.1.2-2的规定。
检查数量:全部检查。
检查方法:观察检查、采用焊缝检查尺测量和检查焊接记录。
表8.1.2・1管道焊缝外观质量表管道焊缝外观质量(余高和根部凸出注:对于铝及铝合金的根部凸出,当母材厚度小于或等于2mm时,根部凸出应小于或等于1.5mm;当母材厚度为2mm〜6mm时,根部凸出应小于或等于2.5mm o3、钛及钛合金、错及错合金的焊缝表面应在焊后清理前进行色泽检查。
钛及钛合金焊缝的色泽检查结果应符合表8.1.3的规定。
错及错合金的焊筑表面应为银白色,当出现淡黄色时应予以清除。
检查数量:全部检查。
检查方法:观察检查和检查焊接检查记录。
者为低温氧化,除不掉者为高温氧化。
11一般项目4、焊缝外观应成形良好,不应有电弧擦伤;焊道与焊道、焊道与母材之间应平滑过渡;焊渣和飞溅物应清除干净。
检查数量:全部检查。
检查方法:观察检查。
5、管道对接焊筵处的角变形(图8.1.5)应符合下列规定:1当管子公称尺寸小于100mm时,允许偏差为2mm;2当管子公称尺寸大于或等于100mm时,允许偏差为3mm o图8.1.5管道焊接接头的角变形I-钢板尺;a-角变形(平直度)偏差检查数量:全部检查。
- 1、下载文档前请自行甄别文档内容的完整性,平台不提供额外的编辑、内容补充、找答案等附加服务。
- 2、"仅部分预览"的文档,不可在线预览部分如存在完整性等问题,可反馈申请退款(可完整预览的文档不适用该条件!)。
- 3、如文档侵犯您的权益,请联系客服反馈,我们会尽快为您处理(人工客服工作时间:9:00-18:30)。
焊缝探伤检测全集焊缝探伤检测全集物理探伤就是不产生化学变化的情况下进行无损探伤。
一、什么是无损探伤?答:无损探伤是在不损坏工件或原材料工作状态的前提下,对被检验部件的表面和内部质量进行检查的一种测试手段。
二、常用的探伤方法有哪些?答:常用的无损探伤方法有:X光射线探伤、超声波探伤、磁粉探伤、渗透探伤、涡流探伤、γ射线探伤、萤光探伤、着色探伤等方法。
三、试述磁粉探伤的原理?答:它的基本原理是:当工件磁化时,若工件表面有缺陷存在,由于缺陷处的磁阻增大而产生漏磁,形成局部磁场,磁粉便在此处显示缺陷的形状和位置,从而判断缺陷的存在。
四、试述磁粉探伤的种类?1、按工件磁化方向的不同,可分为周向磁化法、纵向磁化法、复合磁化法和旋转磁化法。
2、按采用磁化电流的不同可分为:直流磁化法、半波直流磁化法、和交流磁化法。
3、按探伤所采用磁粉的配制不同,可分为干粉法和湿粉法。
五、磁粉探伤的缺陷有哪些?答:磁粉探伤设备简单、操作容易、检验迅速、具有较高的探伤灵敏度,可用来发现铁磁材料镍、钴及其合金、碳素钢及某些合金钢的表面或近表面的缺陷;它适于薄壁件或焊缝表面裂纹的检验,也能显露出一定深度和大小的未焊透缺陷;但难于发现气孔、夹碴及隐藏在焊缝深处的缺陷。
六、缺陷磁痕可分为几类?答:1、各种工艺性质缺陷的磁痕;2、材料夹渣带来的发纹磁痕;3、夹渣、气孔带来的点状磁痕。
七、试述产生漏磁的原因?答:由于铁磁性材料的磁率远大于非铁磁材料的导磁率,根据工件被磁化后的磁通密度B =μH来分析,在工件的单位面积上穿过B根磁线,而在缺陷区域的单位面积上不能容许B根磁力线通过,就迫使一部分磁力线挤到缺陷下面的材料里,其它磁力线不得不被迫逸出工件表面以外出形成漏磁,磁粉将被这样所引起的漏磁所吸引。
八、试述产生漏磁的影响因素?答:1、缺陷的磁导率:缺陷的磁导率越小、则漏磁越强。
2、磁化磁场强度(磁化力)大小:磁化力越大、漏磁越强。
3、被检工件的形状和尺寸、缺陷的形状大小、埋藏深度等:当其他条件相同时,埋藏在表面下深度相同的气孔产生的漏磁要比横向裂纹所产生的漏磁要小。
九、某些零件在磁粉探伤后为什么要退磁?答:某些转动部件的剩磁将会吸引铁屑而使部件在转动中产生摩擦损坏,如轴类轴承等。
某些零件的剩磁将会使附近的仪表指示失常。
因此某些零件在磁粉探伤后为什么要退磁处理。
十、超声波探伤的基本原理是什么?答:超声波探伤是利用超声能透入金属材料的深处,并由一截面进入另一截面时,在界面边缘发生反射的特点来检查零件缺陷的一种方法,当超声波束自零件表面由探头通至金属内部,遇到缺陷与零件底面时就分别发生反射波来,在萤光屏上形成脉冲波形,根据这些脉冲波形来判断缺陷位置和大小。
十一、超声波探伤与X射线探伤相比较有何优的缺点?答:超声波探伤比X射线探伤具有较高的探伤灵敏度、周期短、成本低、灵活方便、效率高,对人体无害等优点;缺点是对工作表面要求平滑、要求富有经验的检验人员才能辨别缺陷种类、对缺陷没有直观性;超声波探伤适合于厚度较大的零件检验。
十二、超声波探伤的主要特性有哪些?答:1、超声波在介质中传播时,在不同质界面上具有反射的特性,如遇到缺陷,缺陷的尺寸等于或大于超声波波长时,则超声波在缺陷上反射回来,探伤仪可将反射波显示出来;如缺陷的尺寸甚至小于波长时,声波将绕过射线而不能反射;2、波声的方向性好,频率越高,方向性越好,以很窄的波束向介质中辐射,易于确定缺陷的位置。
3、超声波的传播能量大,如频率为1MHZ(100赫兹)的超生波所传播的能量,相当于振幅相同而频率为1000HZ(赫兹)的声波的100万倍。
十三、超生波探伤板厚14毫米时,距离波幅曲线上三条主要曲线的关系怎样?答:测长线Ф1 х 6 -12dB定量线Ф1 х 6 -6dB判度线Ф1 х 6 -2dB十四、何为射线的“软”与“硬”?答:X射线穿透物质的能力大小和射线本身的波长有关,波长越短(管电压越高),其穿透能力越大,称之为“硬”;反之则称为“软”。
十五、用超生波探伤时,底波消失可能是什么原因造成的?答:1、近表表大缺陷;2、吸收性缺陷;3、倾斜大缺陷;4、氧化皮与钢板结合不好。
十六、影响显影的主要因素有哪些?答:1、显影时间;2、显影液温度;3、显影液的摇动;4、配方类型;5、老化程度。
十七、什么是电流?答:电流是指电子在一定方向的外力作用下有规则的运动;电流方向,习惯上规定是由电源的正极经用电设备流向负极为正方向,即与电子的方向相反。
十八、什么是电流强度?答:电流强度是单位时间内通过导体横截面的电量,电流有时也作为电流强度的简称,可写成I =Q \ T 式中I 表示为电流强度Q 为电量,T 为时间。
十九、什么是电阻?答:指电流在导体内流动所受到的阻力,在相同的温度下,长度和截面积都相同的不同物质的电阻,差别往往很大;电阻用“R”表示,单位为欧姆,简称欧,以Ω表示。
二十、什么是电压?答:指在电源力的作用下,将导体内部的正负电荷推移到导体的两端,使其具有电位差,电压的单位是伏特,简称伏,用符号“V”表示。
二十一、什么是交流电,有何特点?答:交流电指电路中电流、电压、电势的大小和方向不是恒定的,而是交变的,其特点是电流、电压、电势的大小和方向都是随时间作作周期性的变化;工矿企业设备所用的交流电动机、民用照明、日常生活的电器设备都是以交流电作为电源;交流电有三相和单相之分,其电压380伏和220伏。
二十二、什么是直流电,有何特点?答:指在任何不同时刻,单位时间内通过导体横截面的电荷均相等,方向始终不变的电流;其特点是电路中的电流、电压、电势的大小和方向都是不随时间变化而变化,而是恒定的;直流电机、电镀、电机励磁、蓄电池充电、半导体电路等。
二十三、什么是欧姆定律?答:欧姆定律反映了有稳恒电流通过的电路中电阻、电压和电流相互关系;欧姆定律指出,通过电路中的电流与电路两端电压成正比,与电路中的电阻成反比;即I =V \ R。
二十四、什么是电磁感应?答:通过闭合回路的磁通量发生变化,而在回路中产生电动势的现象称为电磁感应;这样产生电动势称为感应电动势,如果导体是个闭合回路,将有电流流过,其电流称为感生电流;变压器,发电机、各种电感线圈都是根据电磁感应原理工作。
二十五、简述超生波探伤中,超生波在介质中传播时引起衰减的原因是什么?答:1、超声波的扩散传播距离增加,波束截面愈来愈大,单位面积上的能量减少。
2、材质衰减一是介质粘滞性引起的吸收;二是介质界面杂乱反射引起的散射。
二十六、CSK-ⅡA试块的主要作用是什么?答:1、校验灵敏度;2、校准扫描线性。
二十七、影响照相灵敏度的主要因素有哪些?答:1、X光机的焦点大小;2、透照参数选择的合理性,主要参数有管电压、管电流、曝光时间和焦距大小;3、增感方式;4、选用胶片的合理性;5、暗室处理条件;6、散射的遮挡等。
二十八、用超生波对饼形大锻件探伤,如果用底波调节探伤起始灵敏度对工作底面有何要求?答:1、底面必须平行于探伤面;2、底面必须平整并且有一定的光洁度。
二十九、超声波探伤选择探头K值有哪三条原则?答:1、声束扫查到整个焊缝截面;2、声束尽量垂直于主要缺陷;3、有足够的灵敏度。
三十、超声波探伤仪主要有哪几部分组成?答:主要有电路同步电路、发电路、接收电路、水平扫描电路、显示器和电源等部份组成。
三十一、发射电路的主要作用是什么?答:由同步电路输入的同步脉冲信号,触发发射电路工作,产生高频电脉冲信号激励晶片,产生高频振动,并在介质内产生超声波。
三十二、超声波探伤中,晶片表面和被探工件表面之间使用耦合剂的原因是什么?答:晶片表面和被检工件表面之间的空气间隙,会使超声波完全反射,造成探伤结果不准确和无法探伤。
三十三、JB1150-73标准中规定的判别缺陷的三种情况是什么?答:1、无底波只有缺陷的多次反射波。
2、无底波只有多个紊乱的缺陷波。
3、缺陷波和底波同时存在。
三十四、JB1150-73标准中规定的距离――波幅曲线的用途是什么?答:距离――波幅曲线主要用于判定缺陷大小,给验收标准提供依据它是由判废线、定量线、测长线三条曲线组成;判废线――判定缺陷的最大允许当量;定量线――判定缺陷的大小、长度的控制线;测长线――探伤起始灵敏度控制线。
三十五、什么是超声场?答:充满超声场能量的空间叫超声场。
三十六、反映超声场特征的主要参数是什么?答:反映超声场特征的重要物理量有声强、声压声阻抗、声束扩散角、近场和远场区。
三十七、探伤仪最重要的性能指标是什么?答:分辨力、动态范围、水平线性、垂直线性、灵敏度、信噪比。
三十八、超声波探伤仪近显示方式可分几种?答:1、A型显示示波屏横座标代表超声波传递播时间(或距离)纵座标代表反射回波的高度;2、B型显示示波屏横座标代表超声波传递播时间(或距离),这类显示得到的是探头扫查深度方向的断面图;3、C型显示仪器示波屏代表被检工件的投影面,这种显示能绘出缺陷的水平投影位置,但不能给出缺陷的埋藏深度。
三十九、超声波探头的主要作用是什么?答:1、探头是一个电声换能器,并能将返回来的声波转换成电脉冲;2、控制超声波的传播方向和能量集中的程度,当改变探头入射角或改变超声波的扩散角时,可使声波的主要能量按不同的角度射入介质内部或改变声波的指向性,提高分辨率;3、实现波型转换;4、控制工作频率;适用于不同的工作条件。
四十、磁粉探头的安全操作要求?答:1、当工件直接通过电磁化时,要注意夹头间的接触不良、或用了太大的磁化电流引起打弧闪光,应戴防护眼镜,同时不应在有可能燃气体的场合使用;2、在连续使用湿法磁悬液时,皮肤上可涂防护膏;3、如用于水磁悬液,设备须接地良好,以防触电;4、在用茧火磁粉时,所用紫外线必须经滤光器,以保护眼睛和皮肤。
四十一、什么是分辨率?答:指在射线底片或荧光屏上能够识别的图像之间最小距离,通常用每1毫米内可辨认线条的数目表示。
四十二、什么是几何不清晰度?答:由半影造成的不清晰度、半影取决于焦点尺寸,焦距和工件厚度。
四十三、为什么要加强超波探伤合录和报告工作?答:任何工件经过超声波探伤后,都必须出据检验报告以作为该工作质量好坏的凭证,一份正确的探伤报告,除建立可靠的探测方法和结果外,很大程度上取决于原始记录和最后出据的探伤报告是非常重要的,如果我们检查了工件不作记录也不出报告,那么探伤检查就毫无意义。
四十四、磁粉探伤中为什么要使用灵敏试片?答:使用灵敏试片目的在于检验磁粉和磁悬液的性能和连续法中确定试件表面有效磁场强度和方向以及操作方法是否正确等综合因素。
四十五、什么叫定影作用?答:显影后的胶片在影液中,分影剂将它上面未经显影的溴化银溶解掉,同时保护住黑色金属银粒的过程叫定影作用。
四十六、着色(渗透)探伤的基本原理是什么?答:着色(渗透)探伤的基本原理是利用毛细现象使渗透液渗入缺陷,经清洗使表面渗透液支除,而缺陷中的渗透残瘤,再利用显像剂的毛细管作用吸附出缺陷中残瘤渗透液而达到检验缺陷的目的。