铜阳极泥中回收碲的方法试验
从铜阳极泥处理分铜后液中回收硒和碲
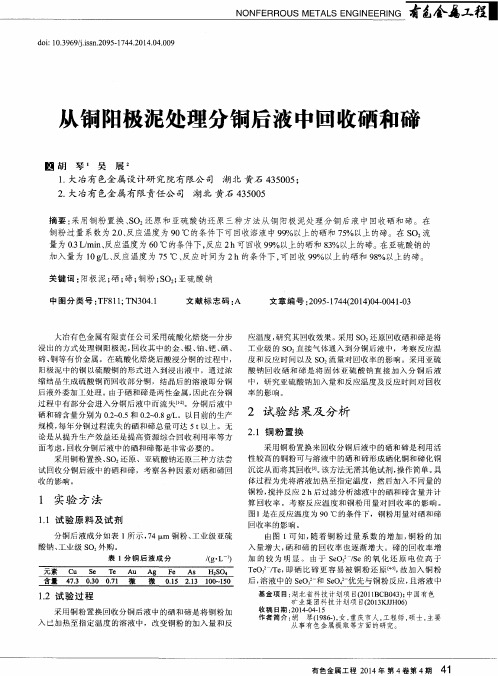
d o i : 1 0 . 3 9 6 9 d . i s s n . 2 0 9 5 — 1 7 4 4 . 2 0 1 4 . 0 4 . 0 0 9
从铜 阳极泥处理 分铜后液 中回收硒和碲
髓 胡 琴 吴 展 1 . 大冶有 色金 属设计研 究院有 限公 司 湖北 黄石 4 3 5 0 0 5 ; 2 . 大冶有 色金 属有 限责任公 司 湖北 黄石 4 3 5 0 0 5
率 的影 响 。
硒和碲含量分别 为 0 . 2 ~ 0 . 5和 0 . 2 ~ 0 . 8 L 。以 目前 的生产 规模 , 每年分铜过 程流失的硒和碲 总量可达 5 t 以上 。无
论 是 从 提 升 生 产 效 益 还 是 提 高 资 源 综 合 回 收 利 用 率 等 方 面考虑 , 回 收 分 铜 后 液 中 的硒 和 碲 都 是 非 常 必 要 的 。 采用铜粉置换 、 S O : 还 原 、 亚硫 酸 钠 还 原 三 种 方 法 尝 试 回 收 分 铜 后 液 中 的硒 和 碲 ,考 察 各 种 因 素对 硒 和 碲 回 收 的影 响 。
摘要: 采用 铜粉 置换 、 S O : 还原和亚硫酸钠 还原三种方 法从 铜 阳极泥处理分铜后 液 中回收硒 和碲。在 铜粉过量 系数为 2 . 0 、 反应温度为 9 0 ℃的条件下可 回收溶液 中 9 9 %以上的硒和 7 5 %以上的碲 。在 S O : 流 量为 0 - 3 L / mi n 、 反应温度为 6 0 ℃的条件下, 反应 2 h可回收 9 9 %以上 的硒和 8 3 %以上的碲。在亚硫酸钠的 加入量为 1 0 g / L、 反应温度为 7 5 ℃、 反应时间为 2 h的条件下 , 可回收 9 9 %以上的硒和 9 8 %以上的碲 。 关键词 : 阳极 泥; 硒; 碲; 铜粉 ; S O 2 ; 亚硫 酸钠
从碲化亚铜渣中回收碲
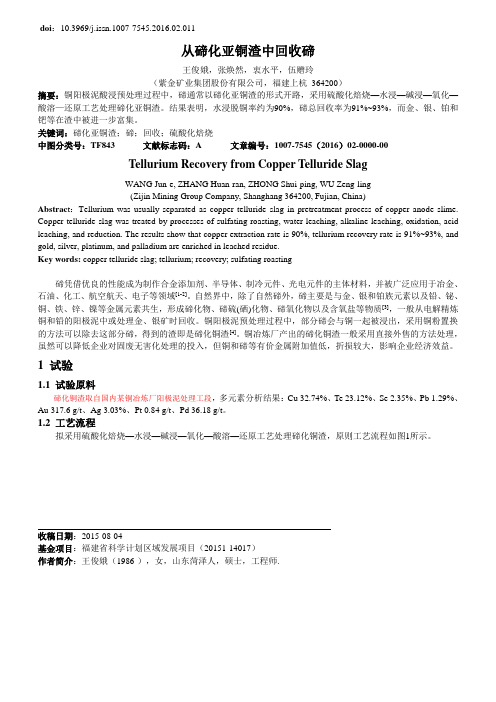
doi:10.3969/j.issn.1007-7545.2016.02.011从碲化亚铜渣中回收碲王俊娥,张焕然,衷水平,伍赠玲(紫金矿业集团股份有限公司,福建上杭364200)摘要:铜阳极泥酸浸预处理过程中,碲通常以碲化亚铜渣的形式开路,采用硫酸化焙烧—水浸—碱浸—氧化—酸溶—还原工艺处理碲化亚铜渣。
结果表明,水浸脱铜率约为90%,碲总回收率为91%~93%,而金、银、铂和钯等在渣中被进一步富集。
关键词:碲化亚铜渣;碲;回收;硫酸化焙烧中图分类号:TF843 文献标志码:A 文章编号:1007-7545(2016)02-0000-00Tellurium Recovery from Copper Telluride SlagWANG Jun-e, ZHANG Huan-ran, ZHONG Shui-ping, WU Zeng-ling(Zijin Mining Group Company, Shanghang 364200, Fujian, China)Abstrac t:Tellurium was usually separated as copper telluride slag in pretreatment process of copper anode slime. Copper telluride slag was treated by processes of sulfating roasting, water leaching, alkaline leaching, oxidation, acid leaching, and reduction. The results show that copper extraction rate is 90%, tellurium recovery rate is 91%~93%, and gold, silver, platinum, and palladium are enriched in leached residue.Key words: copper telluride slag; tellurium; recovery; sulfating roasting碲凭借优良的性能成为制作合金添加剂、半导体、制冷元件、光电元件的主体材料,并被广泛应用于冶金、石油、化工、航空航天、电子等领域[1-2]。
从铜阳极泥分铜渣碱浸液中回收碲

Vol. 40 No. 2(Sum. 176)ApG .2021第40卷第2期(总第176期)2021牟4月湿法冶金 .HydGometa l uGgyofChina从铜阳极泥分铜渣碱浸液中回收y廖春发,邹耕,彭珊,邹建柏,周迅(江西理工大学材料冶金化学学部,江西赣州341000)摘要:研究了以Na^SOs 预还原,NaS 除铅、铜,调pH 水解法从铜阳极泥分铜渣超声强化氧化碱浸液中回收确。
结果表明:在NaSO 3用量为理论量的1. 0倍、还原时间9 min 、还原温度70 b 条件下,确还原率为 92.27% ;在NaA 添加量为理论量的1.0倍、反应时间10 min 、温度60 b 条件下,还原液中Pb 2+、Cu 2+脱除率分别为86.8%、95.7% ;除杂液调整pH 为4.0左右,在反应时间10 min 、反应温度90 b 条件下,确水解为 TeO —水解率达9& 44%,所得TeO :粉末纯度为89. 69% +关键词:含确溶液;还原;除杂;水解;沉淀*希中图分类号:TF803. 2;TF811 文献标识码:A 文章编号:1009-2617(2021)02-0120-05DOI : 10. 13355/j. cnki. sfyj. 2021. 02. 007自然界中,确的独立矿床较少,主要伴生于其 他金属矿[12]中+工业上主要从冶金副产物[34]中回收确,其中铜阳极泥是回收确的主要原料,所生 产的确占总产量的90%左右目前,从含确溶 液中分离提取确的方法有置换法6、SO :还原 法7或NaSOs 还原法8、沉淀分离法9等。
置换法采用铜粉还原溶液中的确,确以Cu z Te 形式 回收[1011],此法环境友好,确回收率高,但对铜粉 需求大,成本较高。
采用SO :或NaSOs 还原溶液中确,确以单质形式沉淀。
相较而言,以Na SOs 作还原剂,对环境污染小,确沉淀时间短8 +中和沉淀分离法是通过调节溶液pH,使 确以TeO :形式沉淀析出,但此法所得中和渣含较多杂质,需除杂[1213] +试验针对铜阳极泥分铜渣超声强化氧化碱浸含确溶液-14,用NaSOs 将溶液中+ 6价确预还+4, 用 Na 2S , 调液pH ,使确以TeO :形式沉淀。
阳极泥及碲回收物料中高含量碲的测定

13 — 4 —
维普资讯
第 2期
岩 矿 测 试 ht:/ k cia ur ntL t】/ y h i r 【 no  ̄ e 1 1
第 2 卷 1
2 结果与讨论
2 1 最佳溶样介质的选择 . 阳极 泥 的 主 要 成 分 及 台 量 ( 0 ) : u t√1 是 c
一
定量 的 T ( ) 准 溶 液, 稀 释 至 i0mL左 eⅣ 标 水 0
右, 以下测 定 同实验 方法 , 计算 出 L
12 实验方法 .
取一 定量 的 TeⅣ ) 准溶 液 于 30mL烧 杯 ( 标 0
中, 加人 2 0mI 浓 HC , [用水 稀 释 至 1 0nI左 右。 0 l J
(0 0 、 e 5 1 ) A ( 0 1 ) P ( 0 5 、 1 -2 ) S ( ~ 0 、 g 1 ~ 5 、 b 2 ~2 ) A ( ~1 、 ( ~7 、 e ~ 3 、 ( ~0 3 ; s0 5 ) S 5 )T ( )Au O 2 ) 另
定至淡黄色后, 加入 3 ~4滴 5 / L的二苯胺磺酸 g
钠指示 剂 , 续 用 ( H42 e s ) 标 准 溶 液滴 定 继 N )F (q 2 至紫 色消 失即为 终点 。
作者简 介:王冬珍(9 9一)女. 16 , 山西省临猗县人, 高级工程师, 长期从事分 析化 验工作 。
些 问题 。本 文 通 过实 验 , 论 了最 佳溶 样 介质 、 讨
杂质元 素 的消除 及 允许 量 、 重铬 酸钾 的用 量 、 应 反
加 人 1 n 5 / 0IL 20gL的 S C,溶液, 沸且保 持 9 nI 微 0 mi, 单 体 碲 凝 聚 完全 , 下 冷 却。 用 慢 速 滤纸 n使 取 过滤, 2 UI 00 4mo HC 溶 液洗 涤烧杯及 沉淀 5 I ~7 次, 水洗 3 ~5次 。将沉 淀连 同滤纸 移人 原烧杯 中, 加 入 1) L浓 Ha, (n r 3滴 w , 3低 温加 热溶解。加  ̄ , o 入8 0m1热水 、 , 下 表皿 , 4g脲 取 微沸 5mi, n 取下
从铜阳极泥中回收碲研究现状
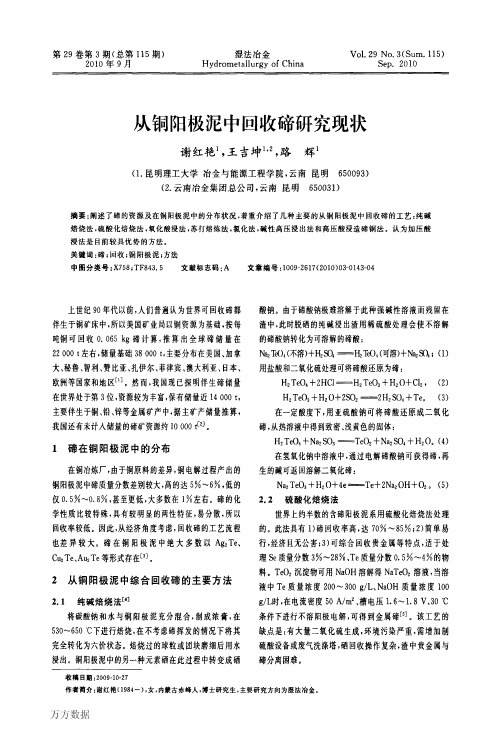
在氢氧化钠中溶液中,通过电解碲酸钠可获得碲,再 生的碱可返回溶解二氧化碲:
Na2Te03+H20+4e=—一Te+2N820H+02。(5) 2.2 硫酸化焙烧法
世界上约半数的含碲阳极泥系用硫酸化焙烧法处理 的。此法具有1)碲回收率高,达70%~85%;2)简单易 行,经济且无公害;3)可综合回收贵金属等特点,适于处 理Se质量分数3%~28%、Te质量分数O.5%~4%的物 料。Te0。沉淀物可用Na0H溶解得NaTe0:溶液,当溶 液中Te质量浓度200~300 g/L、Na0H质量浓度100 g/L时,在电流密度50 A/m2、槽电压1.6~1.8 V、30℃ 条件下进行不溶阳极电解,可得到金属碲∞]。该工艺的 缺点是:有大量二氧化硫生成,环境污染严重,需增加制 硫酸设备或废气洗涤塔,硒回收操作复杂,渣中贵金属与 碲分离困难。
刘建华等[73采用氧化酸浸法,对某铜冶炼厂铜阳极 泥回收碲过程中产生的碱浸渣、净化渣、碲电积阳极泥的 混合渣料进行了富集提取碲的研究。结果表明:采用氧 化酸浸法,在浸出温度80℃、液固体积质量比10:1、每 50 g物料加氧化剂A l g、残酸浓度3.6 mol/L、浸出时间 5 h条件下,碲浸出率达到90.09%,铜浸出率为97.8l%, 浸出液町进一步提取碲。
氧化为二氧化碲,其反应式为:
N包R+8Kf、n一2Me()+4K20+8N02+1爸02。(7)
二氧化碲比较稳定,但易挥发,所以须在加入硝石的 同时加入苏打,使二氧化碲一经形成就立即与碳酸钠作 用生成亚碲酸盐:
Te()2+Na2 C03===一Na2 Te03+C02十。 (8) 生成的亚碲酸钠进入渣中。苏打造渣技术的关键是 把握好时间并控制好温度。 物料中所含的可溶性碲主要以亚碲酸钠和二氧化碲 形式存在,须用一定浓度的碱溶液溶解。但碱的浓度不 宜过高,否则,杂质铅、二氧化硅等也随之溶解。游离碱 可使溶液保持一定碱度,避免已溶解的亚碲酸钠水解。 浸出液中含有铅、铜、硒、砷、锑等杂质,严重影响电解碲 的质量,必须通过反复中和去除。净化后的溶液送中和 槽加稀硫酸中和沉淀,当pH为5~5.5时即到终点:
铜阳极泥渣中浸出碲的试验研究

p r t r f7 ℃ ,t ed s g fp t s i m e m a g n t f0 8 a d p 1 6 h e l ru l a h n a e e a u e o 0 h o a e o o a su p r n a a e o . n H . ,t et l i m e c i g r t u
2 Gux m et r in i pp rGr u . iiS le ,Ja gx Co e o p,Guii 5 4,Ja g 。Chi ) x 42 33 in xi na
Ab t a t Th x r c i n c n ii n ft l r u we e d s u s d wih t l r u b a i g r s d e fo c p e s r c : e e t a to o d to so e l i m r i c s e t e l i m— e rn e i u r m o p r u u a o e s i sr w t ra s n d l me a a ma e il .Th fe to a h n i ,t m p r t r ,d s g fp t s i m e m a g n t ee f c fl c i g tme e e a u e o a e o o a su p r n a a e e
铜阳极泥处理过程中中和渣中碲的提取与制备

铜阳极泥处理过程中中和渣中碲的提取与制备采用硫酸浸出−二氧化硫还原方法从中和渣中制取单质碲。
研究表明:采用硫酸浸出中和渣,当反应温度为30 ℃、反应时间为0.5 h、硫酸浓度为53.9 g/L、硫酸用量为理论用量的 1.5 倍时,碲浸出率为99.99%;采用亚硫酸钠还原酸浸液中碲时,碲(Ⅳ)发生水解生成二氧化碲;采用二氧化硫还原酸浸液中碲时,当反应温度为75℃、反应时间为2 h、盐酸浓度为3.2 mol/L、二氧化硫流量为0.4 L/min 时,碲回收率达到99.84%。
X 射线衍射(XRD)分析表明二氧化硫还原得到的产物为单质碲,电感耦合等离子体发射光谱(I CP)分析表明,碲粉中碲含量为98.27%。
扫描电子显微系统(SEM)分析表明,碲粉的形态为针形1782 年,科学家发现了碲。
在20世纪30 年代,随着碲在工业上的广泛应用,碲的生产才发展起来。
目前,碲用途广泛,有工业味精的美誉,把碲加入钢和铜中可以改善其机械加工性能和抗腐蚀性能,在铅里加入少量碲可显著提高其抗腐蚀性、抗磨性及机械强度。
在橡胶工业中碲的用量也很大,它可增加橡胶的可塑性,提高橡胶的抗热、抗氧化和耐磨性能。
高纯碲用于制造化合物半导体,如碲化镉、碲化铝、碲化铋等。
在国防、航空航天、能源等高新领域有其重要的应用。
碲虽然用途巨大,但是资源稀缺,大部分的碲伴生在铜、铅、金、银的矿物中,在四川石棉县境内的大水沟发现了世界唯一的一处独立碲矿。
铜电解精炼过程中产生的阳极泥是现今提取碲的主要原料,80%的碲从中提取。
目前,从阳极泥中回收碲的方法很多,有氧化焙烧−硫酸浸出、硫酸化焙烧−碱法浸出和氧化焙烧−碱浸法等。
由铜阳极泥回收铂钯后的中和渣提取碲,其中的碲含量较低,经硫酸浸出后,一般采用铜作为还原剂,将碲置换成碲化铜,进行富集回收。
根据反应物的电极电位,在催化剂存在的条件下,二氧化硫能还原硫酸浸出液中的碲。
本文作者采用硫酸浸出和二氧化硫还原的工艺,以盐酸作为催化剂,从铜阳极泥中回收铂钯后的中和渣中提取制备碲粉。
铜阳极泥中碲的回收

Ke wo d :C p e n d l ; l ru ; camig y r s o p ra o es me Tel im Reli n i u
工业 生产 的碲元 素 主要来 源 于铜 电解 精炼 工艺
中的 阳 极 泥 , 常 含 碲 2 ~ 1 %, 大 多 数 以 通 % 0 绝 A 2 eC 2 e AuTe等 形 式 存 在 。 由 于各 铜 冶 炼 gT 、 uT 、 2 厂采用 的铜 原料 不 同 , 阳极 泥 的碲 含 量 有较 大差 铜 异 , 的可 达 5 ~6 , 的仅 0 5 ~0 8 , 高 % % 低 .% . % 甚
维普资讯
有色 金属 ( 冶炼部 分 ) 2 0 0 6年 2期
・3 ・ 3
铜 阳极 泥 中碲 的 回收
张博 亚 , 吉坤 , 王 彭金 辉
( 昆明理 工大 学材料 与冶金 工程 学院 , 南 昆明 6 0 9 ) 云 5 0 3
摘 要 : 绍 碲 元 素 在铜 阳极 泥 中存 在 的形 式 , 点 阐述 从铜 阳 极 泥 中 回 收碲 的方 法 。 介 重
Z HANG oy ,W ANG i u B —a J— n,P k ENG Jn h i i — u
( a ut o tr l a d Mea u g a En ie r g u migUnv ri f c n ea dTeh o g . n a , n nn 。6 0 9 ,C ia Fcl f y Maei s n tl r i l g ei ,K n n i s yo i c n c n l y Yu n n Ku r i a l c n n e t Se o g 5 0 3 hn )
种产 物 中 , 一般 选 择 碱 浸 法 。 阳 极 泥 含 量小 于 2 % 时 , 般选择 苏打 造渣 法 , 一 采用在 分银 炉氧化 精炼 的
从铜阳极泥中回收硒_碲新技术

从铜阳极泥中回收硒、碲新技术梁刚舒万艮蔡艳荣郑诗礼(中南工业大学化学系,长沙410083)提出了从铜阳极泥中回收硒、碲的新技术:以H2O2作氧化剂,在弱酸性溶液中氧化硒和碲,固液分离后调节pH分离硒和碲,在盐酸酸化下用Na2SO3还原硒和碲。
硒和碲回收率分别为99%和98%,纯度均可达99%。
关键词:硒碲回收铜阳极泥1前言从铜电解阳极泥中回收提纯硒、碲的方法较多,有苛性碱氧化加压浸出[1]、氧化焙烧高温浸出[2]、低温氧化焙烧、稀硫酸浸出等[3,4],硒、碲还原大都采用二氧化硫还原、铜还原的方法[5,6]。
由于采取预先焙烧氧化的方法,存在设备较复杂,动力设备维修费用高,二氧化硫气体对人体和环境危害较大,硒、碲回收率和纯度不高等缺点。
经小型试验和工业试验改进了现有工艺,提高了硒、碲的回收率和纯度,降低了生产成本。
2试验211原料试验原料为大冶金属公司电解铜阳极泥,其化学成分见表1。
表1铜阳极泥化学成分元素Au Ag Cu Se Te Pb As 成分/%0.912.0823.4 6.7 3.1 4.3 1.19212方法21211硫酸预浸除铜铜阳极泥中铜含量高对硒、碲和贵金属回收不利。
必须首先对阳极泥进行预处理。
采用3mol/L H2SO4浸出,浸出温度40e,时间2h,使阳极泥中铜含量降至1%~3%,碲和银部分浸出。
银可加入氯化钠或盐酸优先沉淀回收,碲可用铜粉还原。
21212硒、碲氧化在pH=3~4的H2SO4和NaCl体系中加入10%H2O2(理论计算量的200%),温度75e,氧化时间6h,将硒、碲氧化成亚硒酸盐和亚碲酸盐,贵金属留于渣中,然后固液分离。
21213硒、碲分离用10%NaOH调至pH6,使碲形成亚碲酸盐沉淀物,过滤分离硒、碲。
21214硒、碲还原将亚硒酸钠溶液以3mol/L H Cl酸化第21卷第4期稀有金属1997年7月后,用Na2SO3溶液还原成元素硒。
沉淀的硒用水淋洗并干燥。
- 1、下载文档前请自行甄别文档内容的完整性,平台不提供额外的编辑、内容补充、找答案等附加服务。
- 2、"仅部分预览"的文档,不可在线预览部分如存在完整性等问题,可反馈申请退款(可完整预览的文档不适用该条件!)。
- 3、如文档侵犯您的权益,请联系客服反馈,我们会尽快为您处理(人工客服工作时间:9:00-18:30)。
铜阳极泥中回收碲的方法试验一,概述铜的用途非常广泛,在我国铜冶炼企业很多,冶炼工艺技术大同小异,如今铜矿山资源的较贫乏,从大量的废弃物,电子垃圾,电子产品中回收有价金属,是很多冶炼铜企业的研究方向,在铜冶炼工艺过程中,生产出来的冰铜是一种中间产品,冰铜经过阳极炉或转炉冶炼,得到另外的铜冶炼的中间产品粗铜,铜冶炼企业通常处理粗铜的方法是采用电解方法,通过粗铜电解,得到电解铜,既阴极铜,在粗铜电解过程中大量的杂质元素,有价金属,如:铜、铅、锡、金、银、铂、钯、硒、碲等贵金属和稀有金属,都以铜电解阳极泥的形式沉淀富集,本方法试验是属于有色金属的湿法冶金,试验原料是一种高杂质铜阳极泥,来源于广东铜冶炼公司,本铜阳极泥中回收碲的方法试验,属于稀散金属的湿法冶金,具体步骤是首先向沥干水分后的铜阳极泥中加入浓度为50~400g/L的硫酸调浆,得到铜阳极泥浆料,控制铜阳极泥浆料中铜阳极泥的重量浓度在1~30%,将所得的铜阳极泥浆料置于微波反应炉中,向铜阳极泥浆料中通入或加入氧化剂,调节微波频率为2450MHz,微波加热功率为100~900w,在常压下浸出反应1~20min后出料,进行固液分离,得到含碲的浸出液。
本发明的技术方案缩短了铜阳极泥的处理时间,加大了处理量,提高了碲的浸出率,使铜阳极泥中其他有价金属走向合理且集中,有利于综合回收,既降低了能耗,又不需要特殊的高压装备,同时具有较快的浸出速度。
二、基本技术原理铜阳极泥中回收碲的方法试验属于稀散金属的湿法冶金,特别涉及一种微波酸浸从铜阳极泥中回收碲的方法。
碲属于稀散金属,是一种冶金工业中广泛使用的合金添加剂,石油化学工业中的催化剂和硫化剂,电子和电气工业中重要的半导体和光学器件原料,是当代高技术新材料的支撑材料。
碲以其在现代高科技工业、国防与尖端技术领域中所占有的重要地位,越来越受到人们的重视,应用范围也越来越广,对国民经济的发展的影响到越来越大。
世界上大部分可回收碲都伴生于铜矿床和碲化物型金银矿床中。
工业生产碲的主要来源是铜电解精炼过程中产生的阳极泥。
铜在电解精炼时,在直流电作用下阳极上的铜和电位较负的贱金属溶解进入溶液,而正电性金属,如金、银和铂族金属它们在阳极上不进行电化学溶解,而以极细的分散状态落入槽底成为铜阳极泥。
铜阳极泥含有大量的贵金属和稀有元素,是提取稀贵金属的重要原料。
由于阳极泥中通常都含有较多的铜、硒、碲及银等,因此从铜阳极泥中回收提取碲的工艺都较复杂。
对于从铜阳极泥回收碲,目前国内外采用较多的方法是硫酸化焙烧-碱浸法、氧化酸浸法、苏打熔炼法等。
硫酸化焙烧-碱浸法是应用较广的传统工艺,目前为国内外大多数工厂所采用,基本流程为:“铜阳极泥→硫酸化焙烧蒸硒→稀酸分铜→碱浸分碲→电解制备金属碲”,该工艺的缺点是:(1)能耗高、操作环境差;(2)有大量二氧化硫生成,环境污染严重;(3)硒回收操作复杂,渣中贵金属与碲分离困难,碲、硒回收率低。
氧化酸浸法过程可以不产生二氧化硫,但由于氧化法的反应温度不能很高(最高不超过90℃),因此反应强度较弱、反应时间较长,需要6小时甚至更长时间完成浸碲的任务,并且铜、碲、硒浸出率都很低。
为了解决常压酸浸反应速度慢,效率低,耗时长的问题,高温加压酸浸工艺逐渐受到关注,此工艺具有处理时间短,处理量大,浸出速度快等优点,但同时也存在着能耗高、设备要求高等缺点。
苏打熔炼法也是一种广泛用于从阳极泥中回收硒、碲的方法。
此工艺的缺点是:(1)工艺流程较复杂,浸出对渣的要求较高;(2)能耗高,环境污染严重;(3)碲回收操作复杂。
三、方法试验目的针对现有技术存在的问题,本发明提供一种微波酸浸从铜阳极泥中回收碲的方法,目的是缩短铜阳极泥的处理时间,加大处理量,提高碲的浸出率,使铜阳极泥中其他有价金属走向合理且集中,有利于综合回收,既降低了能耗,又不需要特殊的高压装备,同时具有较快的浸出速度。
实现铜阳极泥中回收碲的方法试验目的的技术方案按照以下步骤进行:(1)向铜阳极泥中加水进行粗调浆,筛去颗粒直径大于5mm 的沙粒类杂质,沥干水分,向沥干水分后的铜阳极泥中加入浓度为50~400g/L的硫酸调浆,得到铜阳极泥浆料,控制铜阳极泥浆料中铜阳极泥的重量浓度在1~30%;(2)将所得的铜阳极泥浆料置于微波反应炉中,向铜阳极泥浆料中通入或加入氧化剂,调节微波频率为2450MHz,微波加热功率为100~900w,在常压下浸出反应1~20min后出料,进行固液分离,得到含碲的浸出液。
加入的氧化剂为压缩空气、工业纯氧、富氧空气或H2O2中的一种或两种;采用H2O2时,H2O2的用量为0.05~5molH2O2/L浆料。
四、方法试验结论本铜阳极泥中回收碲的方法试验原理是利用电流使磁控管产生微波,通过波导传输到加热器中。
由于带电粒子的传导和介电质极化,微波场中物质分子偶极化响应速率与微波频率相当,然而在微波作用下导致的电介质偶极极化往往又滞后于微波频率,使微波场能量损耗并转化为热能。
处于加热器中的物料,吸收微波功率后,本身分子的运动在高频交变电磁厂中受到干扰和阻碍,使离子导热并且分子的偶极子发生旋转,产生了类似摩擦的作用,温度也随之升高。
在一般条件下,微波可方便地穿透如玻璃、陶瓷、某些塑料等材料。
传统浸取方法中矿物加热浸出一定时间后,浸出反应产生的较致密物质会包裹未反应矿核,使浸出反应受阻。
而采用微波强化浸取配有相应添加物的矿石,使矿粒间产生热应力裂纹和孔隙或与添加物反应,不断更新反应界面,将有助于改善浸出效果,由于微波的特性以及微波的热效应和非热效应,使得微波加热相对于传统加热具有很多无可比拟的优点。
以硫酸和双氧水为介质,对铜阳极泥进行微波酸浸实验,该法具有反应速度快,浸出率高等特点。
本方法可能涉及到的主要化学反应方程式如下:Cu2Te +2O2+2H2SO4=2CuSO4+H2TeO3+H2OH2TeO3+0.5O2= H2TeO4Cu2Te+4H2O2+2H2SO4=2CuSO4+H2TeO3+5H2OAg2Te+3H2O2+H2SO4=Ag2SO4+H2TeO3+3H2OSO2+H2O2=H2SO4本铜阳极泥中回收碲的方法试验达到的技术经济指标:碲浸出率94.5~99.6%。
与现有工艺相比存在如下优点:(1)加热均匀。
常规加热是物质表面先发热,然后通过热传导把热量传到物质内部。
使用微波辅助铜阳极泥的浸出过程,微波加热是从物质的内部加热,具有自动平衡的性能,因而加热均匀,可避免常规加热过程中容易引起的表面硬化和不均匀现象。
(2)反应速率快,浸出率高。
避免了同类型浸出中较长的浸出时间和大部分情况下较低的浸出率,较同等条件下未经过微波处理的浸出率提高了15~35%以上。
(3)微波加热速度快。
只需常规方法的百分之一到千分之一的时间就可完成加热过程。
这是因为微波能够渗入到物料内部,对被加热物料直接发热,而不是依靠物料本身的热传导,因而克服了常规加热方法加热慢的缺点,因此浸出时间大幅度降低。
(4)热效率高,节约能源。
由于微波加热是微波直接对物料加热,除了有限的微波传输损耗外,几乎没有其它的额外损耗,所以微波加热十分省电节能。
(5)反应灵敏。
常规的加热方法,不论是电热、蒸汽、热空气等要达到一定温度,都需要一定的预热时间。
而利用微波加热,开机即可正常运转,调整微波输出功率,物料加热情况立即无惰性地随着改变,便于自动控制。
五、方法试验下面结合实施例对本发明做进一步说明。
实施例中所用的铜阳极泥由广东铜冶炼公司提供,所用铜阳极泥的成分如表1:表1 铜阳极泥的成分元素Au Ag Cu Ni Se Te重量含量172.9g·t-12.60% 12.11% 47.36% 3.22% 0.369%试验例1(1)向铜阳极泥中加水进行粗调浆,筛去颗粒直径大于5mm 的沙粒类杂质,沥干水分,向沥干水分后的铜阳极泥中加入浓度为400g/L的硫酸调浆,控制铜阳极泥浆料中铜阳极泥的重量浓度在30%;(2)将所得的铜阳极泥浆料置于微波反应炉中,向铜阳极泥浆料中入氧化剂H2O2,调节微波频率为2450MHz,微波加热功率为100w,在常压下浸出反应10min出料,进行固液分离,得到含碲的浸出液。
H2O2的用量为2.5molH2O2/L 浆料。
浸出结束后经过化学分析碲的浸出率为94.5%(表2)。
试验例2(1)向铜阳极泥中加水进行粗调浆,筛去颗粒直径大于5mm 的沙粒类杂质,沥干水分,向沥干水分后的铜阳极泥中加入浓度为50g/L的硫酸调浆,控制铜阳极泥浆料中铜阳极泥的重量浓度在1%;(2)将所得的铜阳极泥浆料置于微波反应炉中,向铜阳极泥浆料中入氧化剂H2O2,调节微波频率为2450MHz,微波加热功率为500w,在常压下浸出反应4min出料,进行固液分离,得到含碲的浸出液。
H2O2的用量为5molH2O2/L浆料。
浸出结束后经过化学分析碲的浸出率为98.9%(表2)。
试验例3(1)向铜阳极泥中加水进行粗调浆,筛去颗粒直径大于5mm 的沙粒类杂质,沥干水分,向沥干水分后的铜阳极泥中加入浓度为250g/L的硫酸调浆,控制铜阳极泥浆料中铜阳极泥的重量浓度在20%;(2)将所得的铜阳极泥浆料置于微波反应炉中,向铜阳极泥浆料中入氧化剂H2O2,调节微波频率为2450MHz,微波加热功率为300w,在常压下浸出反应6min出料,进行固液分离,得到含碲的浸出液。
H2O2的用量为0.05molH2O2/L 浆料。
浸出结束后经过化学分析碲的浸出率为99.1%(表2)。
试验例4(1)向铜阳极泥中加水进行粗调浆,筛去颗粒直径大于5mm 的沙粒类杂质,沥干水分,向沥干水分后的铜阳极泥中加入浓度为350g/L的硫酸调浆,控制铜阳极泥浆料中铜阳极泥的重量浓度在15%;(2)将所得的铜阳极泥浆料置于微波反应炉中,向铜阳极泥浆料通入氧化剂压缩空气,调节微波频率为2450MHz,微波加热功率为700w,在常压下浸出反应1min出料,进行固液分离,得到含碲的浸出液。
浸出结束后经过化学分析碲的浸出率为98.2%(表2)。
试验例5(1)向铜阳极泥中加水进行粗调浆,筛去颗粒直径大于5mm的沙粒类杂质,沥干水分,向沥干水分后的铜阳极泥中加入浓度为150g/L的硫酸调浆,控制铜阳极泥浆料中铜阳极泥的重量浓度在10%;(2)将所得的铜阳极泥浆料置于微波反应炉中,向铜阳极泥浆料通入氧化剂富氧空气,调节微波频率为2450MHz,微波加热功率为900w,在常压下浸出反应20min出料,进行固液分离,得到含碲的浸出液。
浸出结束后经过化学分析碲的浸出率为99.6%(表2)。
试验例6(1)向铜阳极泥中加水进行粗调浆,筛去颗粒直径大于5mm 的沙粒类杂质,沥干水分,向沥干水分后的铜阳极泥中加入浓度为100g/L的硫酸调浆,控制铜阳极泥浆料中铜阳极泥的重量浓度在8%;(2)将所得的铜阳极泥浆料置于微波反应炉中,向铜阳极泥浆料通入氧化剂压缩空气和工业纯氧,调节微波频率为2450MHz,微波加热功率为600w,在常压下浸出反应15min 出料,进行固液分离,得到含碲的浸出液。