德马输送辊筒产品选用手册-详细版样本2012 V2
Ultra-Tow 1000 Lb. Trailer Winch 产品说明书

Trailer Winch – 1000 Lb. CapacityOwner’s ManualWARNING: Read carefully and understand all ASSEMBLY AND OPERATION INSTRUCTIONS before operating. Failure to follow the safety rules and other basic safety precautions may result in serious personal injury.Items #52802 #52807 #52809Thank you very much for choosing an Ultra-Tow™ product!For future reference, please complete the owner’s record below:Serial Number/Lot Date Code: ________________________________ Purchase Date: ____________________________________________ Save the receipt, warranty, and this manual. It is important that you read the entire manual to become familiar with this product before you begin using it.This winch is designed for certain applications only. Northern Tool & Equipment is not responsible for issues arising from modification or improper use of this product such as an application for which it was not designed. We strongly recommend that this product not be modifiedand/or used for any application other than that for which it was designed. For technical questions, please call 1-800-222-5381.Intended Use (4)Technical Specifications (4)Important Safety Information (5)Specific Operation Warnings (6)Winch Mounting and Cable Attachment (7)Main Parts of Winch (8)Assembly Instructions (8)Before Each Use (9)Operating Instructions (9)Moving or Tensioning Loads (9)After Each Use (10)Maintenance (10)Troubleshooting (10)Parts Diagram (11)Parts List (11)Replacement Parts (12)Limited Warranty (13)The Ultra-Tow Trailer Winch is designed for safer, easier boat loading and unloading. Pulling winches are best suited for boat trailers and other horizontal pulling applications which require the freewheeling feature of ratchet type winches.∙The winch is designed to be attached to a mounting plate or structure capable of supporting the load that is intended to pull (lift). Mounting location and hardware must support your Winch and load.∙For maximum strength and safety, this winch should be mounted with three 3 ⁄8" or M10 bolts, washers, and lock washers (not included, sold separately). The bolt should attach the winch to the mounting structure utilizing the outside rear holes or slots. The third bolt should be insertedthrough the winch frame and mounting structure in a manner to utilize the foremost remaining frame slot (hole).∙Select a winch line with breaking strength at least 1-1 ⁄2 times the winch rating and a hook 1-1 ⁄2 times stronger than the line.∙CABLE REPLACEMENT: Use extreme care when replacing cable, it is secured under tension by the cable clamp, and may spring back forcefully.a. Put pawl in reel out position. Reel the old cable all the way out by turning handle counterclockwise.b. Loosen the nut and remove the old cable from underneath the cable clamp.c. Remove the old cable.d. Route new cable end over bushing and through the hole to the outside of the drum.e. Install the cable under the cable clamp.f. Tighten the nut securely.g. Put pawl in reel in position, then reel the new cable onto drum by turning the handle clockwise,being careful not to allow kinking.h. Test winch for proper operation.∙If nylon strap is used, it should have a loop sewn in one end and be attached using a 3 /8" x 3" or1 /4" x 2-3/4" long bolt and locknut. Use a locknut, not a nut and lock the washer. Insert boltthrough slots in both reel side plates so that nut is on gear side.∙Tighten only until snug with bolt in bottom of slot next to reel hub.Insert handle and secure with a lock nut.Winding/unwinding the cable without load1. Place the ratchet lever in the center position.2. The cable reel now moves freely in both directions.3. Pull the steel cable at the fixed hook until the hook can be attached to the load to be moved.4. Wind back the excessive cable by turning the crank clockwise.Winding up the cable under load (towing, loading)1. Hold the crank firmly and push gently to relieve the ratchet lever2. Place the ratchet lever at position.3. Turn the crank clockwise to evenly wind up the steel cable.Unwinding the cable under load (lowering, unloading)1. Hold the crank firmly and push gently to relieve the ratchet lever.2. Place the ratchet lever at position.3. The steel cable should be fully retracted again after use.Ratchet switch1. There are 3 positions for the ratchet switch: The higher position is for pulling, the lower position isfor releasing, the middle position is for both pulling and releasing, but can only be used when the winch is loaded. Hold the crank handle tightly if you want to change the switch position.2. Before using, install the winch on a firm and flat surface. To install it, put the ratchet switch on themiddle position and pull the cable out until the holes on the bottom of the base are visible. Then use at least 3 sets of 3/8 inch bolts and locking nuts, in a triangular pattern, to affix the base to the surface. Use an extra metal or hardwood board when necessary.3. Then install the crank handle to the axis bolt with nut.4. Put the ratchet switch on the higher position and turn the crank handle clockwise to pull. Place theratchet switch on the lower position and turn the crank handle counterclockwise to release.5. When finished, attach the hook to the paw bushing.∙Wipe external surfaces of the winch with a clean cloth.∙Periodically, lubricate the wire rope with light oil. Lubricate the gear with gear grease.∙This winch has been fully lubricated at the factory; but, for continued smooth performance and increased life, occasional greasing of gears and reel shaft and an occasional drop of oil on drive shaft bearings are recommended.∙Inspect periodically all parts, steel cable, accessories and replace them if damaged or used.∙Have damaged parts replaced by an authorized service center.∙Check the nuts periodically and tighten them if they are loose.∙Keep winch in good working order. Damaged or severely-worn parts create unnecessary dangers and could result in personal injury or property damage.∙Always lock up product and keep out of children.Maintain the winch by adopting a program of conscientious repair and maintenance in accordance with the following recommended procedures. It is recommended that the general condition of any tool be examined before it is used. Keep your tool in good repair.The following chart is based on a normal operation schedule.∙For replacement parts and technical questions, please call Customer Service at 1-800-222-5381. ∙Not all product components are available for replacement. The illustrations provided are a convenient reference to the location and position of parts in the assembly sequence.∙When ordering parts, the following information will be required: item description, item model number, item serial number/item lot date code, and the replacement part number.∙The distributor reserves the rights to make design changes and or improvements to product lines and manuals without notice.Northern Tool and Equipment Company, Inc. ("We'' or '"Us'') warrants to the original purchaser only ("You'' or “Your”) that the Ultra-Tow product purchased will be free from material defects in both materials and workmanship, normal wear and tear excepted, for a period of one year from date of purchase. The foregoing warranty is valid only if the installation and use of the product is strictly in accordance with product instructions. There are no other warranties, express or implied, including the warranty of merchantability or fitness for a particular purpose. If the product does not comply with this limited warranty, Your sole and exclusive remedy is that We will, at our sole option and within a commercially reasonable time, either replace the product or product component without charge to You or refund the purchase price (less shipping). This limited warranty is not transferable.Limitations on the WarrantyThis limited warranty does not cover: (a) normal wear and tear; (b) damage through abuse, neglect, misuse, or as a result of any accident or in any other manner; (c) damage from misapplication, overloading, or improper installation; (d) improper maintenance and repair; and (e) product alteration in any manner by anyone other than Us, with the sole exception of alterations made pursuant to product instructions and in a workmanlike manner.Obligations of PurchaserYou must retain Your product purchase receipt to verify date of purchase and that You are the original purchaser. To make a warranty claim, contact Us at 1-800-222-5381, identify the product by make and model number, and follow the claim instructions that will be provided. The product and the purchase receipt must be provided to Us in order to process Your warranty claim. Any returned product that is replaced or refunded by Us becomes our property. You will be responsible for return shipping costs or costs related to Your return visit to a retail store.Remedy LimitsProduct replacement or a refund of the purchase price is Your sole remedy under this limited warranty or any other warranty related to the product. We shall not be liable for: service or labor charges or damage to Your property incurred in removing or replacing the product; any damages, including, without limitation, damages to tangible personal property or personal injury, related to Your improper use, installation, or maintenance of the product or product component; or any indirect, incidental or consequential damages of any kind for any reason.Assumption of RiskYou acknowledge and agree that any use of the product for any purpose other than the specifieduse(s) stated in the product instructions is at Your own risk.Governing LawThis limited warranty gives You specific legal rights, and You also may have other rights which vary from state to state. Some states do not allow limitations or exclusions on implied warranties or incidental or consequential damages, so the above limitations may not apply to You. This limited warranty is governed by the laws of the State of Minnesota, without regard to rules pertaining to conflicts of law. The state courts located in Dakota County, Minnesota shall have exclusive jurisdiction for any disputes relating to this warranty.Distributed by:Northern Tool & Equipment Company, Inc.Burnsville, Minnesota 55306Made in China。
Yaohua XK3101M2可移动调验增量指示器货物运输轮胎重量检测手册说明书

Yaohua XK3101-M2 Protable WIM Indicator user and calibration ManualXK3101M2 Portable WIM IndicatorOperator’s ManualOperator’s Manual of XK3101M2 Portable WIM Indicator for Axle Overload Detection 1. IntroductionWIM (weigh-in-motion) is the top technology in weighing field. Our company has long been engaged in the research, development and production of the axle load WIM system. In 2000, we developed the XK3101 indicator, which has the function of axle testing. And,due to its high reliability and precision in WIM, it gained the acceptance of most customers. And also our company is one of the few firms who have the intellectual property right of their own. This system (XK3101M2) was improved on the base of XK3101B; it is more reliable and more precise and can be used in portable vehicle scales and other axle load WIM systems.2. Features◆Excellent weighing function and high precision;◆Backlight lattice LCD, Clear both in daytime and nighttime;◆Can conveniently input full vehicle license number with letters;◆Can put in the name of the testing organization and operators;◆Built-in high speed printer to print the whole testing report form;◆Can store as many as 1300 vehicle testing records;◆mature inquiry and statistic function;◆AC/DC, real time battery capacity indicating. The battery can be used for 40 hours on end. Automatic shut off;◆The auto power supply system can be used for providing electricity and charging;◆The instrument can work independently. And it also can upload testing data to computers.3. Main Technical Index• (1)full-scale temperature coefficient: 5ppm/℃• (2) inner resolution: 24 bits(3) Sampling speed: 200 times/sec• (4) the speed of display renewal: 12.5times/sec• (5) system non-linearity <0.01%• (6) impulse source of sensor: DC 5V±2%• (7) operating temperature range: 0℃--40℃1This is a “Table of Contents preview” for quality assuranceThe full manual can be found at /estore/catalog/ We also offer free downloads, a free keyboard layout designer, cable diagrams, free help andsupport. : the biggest supplier of cash register and scale manuals on the net。
IronMan210 单相MIG沿用包说明书

T he IronMan™210 is a powerful welding package Array that is versatile and easy to use. It is equippedwith many outstanding features.Welds 22 gauge up to 3/8 in steel.Excellent aluminum welding with optionalSpoolmate 3035 spool gun.Six-tap voltage control allows for a smooth,easy-to-control arc.Infinite wire feed speed control for preciseadjustment of penetration and weld bead shape.Comes complete with gun and built-in runninggear/cylinder rack.Handles wire spools up to 12 in—wire feedspeed adjusts from 90 to 750 IPM.Built-in thermal overload protects the unit.Reversible drive rolls: two grooves for three wiresizes on one drive roll. Decreases spare partsand changeover time.Hinged door for easy access to wire drivesystem for spool and drive roll changes.Certified to both the Canadian and U.S. Standards for welding equipment.2(Order from Hobart Service Parts.)Contact TipsContact Tip Adapter #169 716 Replacement Liners Nozzle #169 7151/2 in (13 mm) diameter orifice.Spot Nozzles#176 237#176 239#176 241Reversible V-Groove Drive Rollsfor Mild Steel Wire#202 925.023 and .030/.035 in (0.6 and 0.8/0.9 mm)Spoolmate™3035 #195 016Includes 20 ft (6 m) cable. When combinedwith the IronMan™210, this spool gun welds.023, .030 and .035 in (0.6, 0.8 and 0.9 mm)wires on 14 gauge to 1/4 in thick aluminum.#207 642 Switch and Gas Diverter required.3Litho in USAThe IronMan ™210 comes complete with:Constant-voltage DC power source Built-in wire feeder10 ft, M-10 MIG welding gun Regulator/flow gauge 5 ft gas hoseSample spool of solid welding wire 7 ft primary input cable with plug Dual groove drive roll – .023 and .030/.035 in10 ft work cable with clamp Extra contact tipsBuilt-in running gear/cylinder rack Weld, set-up and parts information chart。
VMI精品轮胎机械产品样本
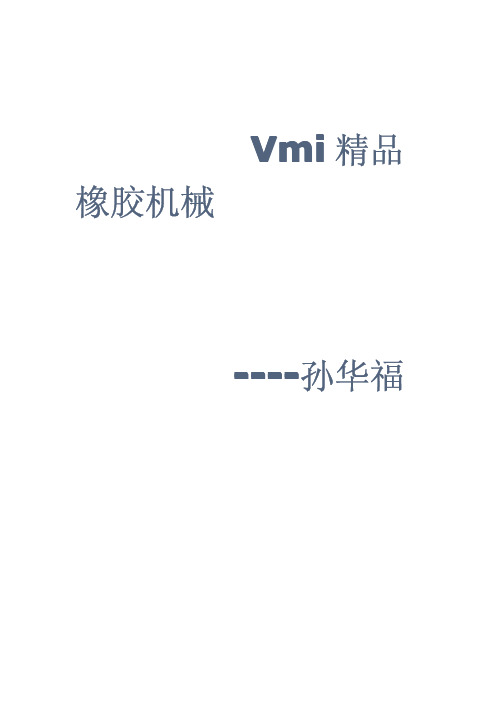
VMI 是子午线轮胎胶部件如带束层、钢丝胎体帘布层、纤维胎体帘布层的裁断和接头系统的主要供应商。 所有的机器都是采用最先进的技术设计并制造,使您在生产高质量终端产品时更快捷,性能更可靠,保证 每班每天生产更多里程的材料。总之,我们的裁断和接头系统的主要特点有:
• 为客户定制的解决方案灵活、模块化的机器设计允许我们根据最终用户的特殊要求来生产我们的 机器。附加的功能如:额外的卷取装置模块、纵裁机和胶条贴合器都是可以添加的。 • 高精确性 裁断和接头精确高,产生废料少,浪费小。 • 每天生产出更多里程的材料。 该机器比目前市场上任何现有的机器都具有更高的产成品量. • 易于操作我们机器备具有便于操作的可触摸控制界面,只需要一个操作者来操作。只要按一下按 钮,就可以轻松调节原材料的宽度和角度。用于工字轮或小车的导开和卷取能够快速更换。 • 终身服务 所有机器都易于维修,并且由全球的 VMI 服务组织支持。
Top
子午线乘用轮胎成型系统,VMI248-2
虽然一次法技术是领先的,但是我们也生产第二段成型机。例如,VMI-248-2第二段轮胎成型机,它就是 VMI-248-SL 一次法 机器模型的精简版本,它们都是运用了相同成熟的设计原理。该机器能够利用在一个单独的第一段成型机 上制作的胎体半成品和两个带束层,冠带条和胎面完成一个生胎。
The VMI248-SL • 高的贴合准确性 • 高产量 • 可靠和准确的胶部件贴合 • 与客户生产物流的密切配合 • 用户化的解决方案
图片中为子午线乘用胎的一次法成型机,型号为:VMI-248-SL. 因为所有的联合动作是优化和均衡的,所以一次法成型机具有非常短的周期时间。它是专门设计来最大限 度地减少停机时间,并且适应性强,可根据工装来有效地更换导开料卷和与轮胎规格有关的工装。现代化 的控制系统是菜单驱动的,自动化的机器设置能够使材料的宽度、类型和角度更换更快更准确,从而使 VMI248-SL 也能适用于小批量的生产. 该机器配备快速更换的单/双导开系统,以满足轮胎成型供料配置。按照您的要求选择工字轮、卷轴或者小 车、自动生胎移除系统和自动料卷更换系统,所有的这些我们都将按照您的要求来定制成型机. 在行业中 轮胎的设计是不同的,但是随着我们按照客户要求订制的纤维或钢丝子口供料架和贴合头,胎圈包布、胶 条(也适用于跑气保用轮胎)的供料架和贴合器的提供,我们可以满足您的轮胎技术.
2NWG2024辊式喂料机说明书2

3
版权说明
本说明书的版权仍归本公司所有。 本设备开发设计的技术所有权归中材装备集团有限公司南京分公司所有。 4 工作原理及结构
4.1 工作原理 本机是一种多辊式输送机械, 各辊子均具有特殊设计的辊齿, 当各辊子同向转动时, 将托在其上的物料由一端强制送到另一端。相邻辊子上的异形耐磨板形成的空隙可以使碎 料漏下,间隙的大小与产品要求相适应。 本设备上游为其他喂料设备,一般为板式喂料机,下游接破碎机。本设备由多组辊子 组成,承载面积和筛隙面积较大,当物料经板喂机喂进本机后,较大物料被异形耐磨板输 送进破碎机,较小成品物料通过各缝隙落至下料溜子,被输送皮带运走。这样既提高了破 碎系统的生产能力,又减轻了破碎机的负荷,也延长了破碎设备易损件的寿命。该系统的 整体负荷由板喂机电机的变频调速来实现,而本机辊子均以较高的转速运转,以便及时输 送或筛下物料。 在破碎作业车间采用本机输送物料,在系统同等产量下,电耗较低;在同样电耗下, 系统产量提高较多,尤其在来料小块所占比例较大的情况下更为明显。因此,采用本机用 于破碎作业输送物料是比较经济、节能的方案。
2
修改版号:
NCW312-AM
中材装备集团南京分公司
2
保证及责任 原则上,按照双方已签订的相关合同条款执行。 当由于以下原因而造成人员及财产损害时,我方不承担任何责任:
安全设施不完善或安全保护设施被拆除的情况下运行机器。 设备在不当介质中运输、储存、安装、启动、运行。 不当的、不规范的运行和维护运行机器。 不正确使用机器。 错误的喂料和卸料工况。 未经我方允许对机器进行结构更改。 未经我方允许对驱动参数(功率和转速)进行更改。 异物进机以及不可抗力所造成的损害。 使用非本公司产品的备品备件。
2002 Whelen Engineering Lightbar产品说明书

©2002 Whelen Engineering Company Inc.Form No.13719A (053007)A u t o m ot ive : For warranty information regarding this product, visit /warranty•Proper installation of this product requires the installer to have a good understanding of automotive electronics, systems and procedures.•Whelen Engineering requires the use of waterproof butt splices and/or connectors if that connector could be exposed to moisture.•Any holes, either created or utilized by this product, should be made both air- and watertight using a sealant recommended by your vehicle manufacturer.•Failure to use specified installation parts and/or hardware will void the product warranty.•If mounting this product requires drilling holes, the installer MUST be sure that no vehicle components or other vital parts could be damaged by the drilling process. Check both sides of the mounting surface before drilling begins. Also de-burr the holes and remove any metal shards or remnants. Install grommets into all wire passage holes.•If this manual states that this product may be mounted with suction cups, magnets, tape or Velcro®, clean the mounting surface with a 50/50 mix of isopropyl alcohol and water and dry thoroughly.•Do not install this product or route any wires in the deployment area of your air bag. Equipment mounted or located in the air bag deployment area will damage or reduce the effectiveness of the air bag, or become a projectile that could cause serious personal injury or death. Refer to your vehicle owner’s manual for the air bag deployment area. The User/Installer assumes full responsibility to determine proper mounting location, based on providing ultimate safety to all passengers inside the vehicle.•For this product to operate at optimum efficiency, a good electrical connection to chassis ground must be made. The recommended procedure requires the product ground wire to be connected directly to the NEGATIVE (-) battery post (this does not include products that use cigar power cords).•If this product uses a remote device for activation or control, make sure that this device is located in an area that allows both the vehicle and the device to be operated safely in any driving condition. •Do not attempt to activate or control this device in a hazardous driving situation.•This product contains either strobe light(s), halogen light(s), high-intensity LEDs or a combination of these lights. Do not stare directly into these lights. Momentary blindness and/or eye damage could result.•Use only soap and water to clean the outer lens. Use of other chemicals could result in premature lens cracking (crazing) and discoloration. Lenses in this condition have significantly reduced effectiveness and should be replaced immediately. Inspect and operate this product regularly to confirm its proper operation and mounting condition. Do not use a pressure washer to clean this product.•It is recommended that these instructions be stored in a safe place and referred to when performing maintenance and/or reinstallation of this product.•FAILURE TO FOLLOW THESE SAFETY PRECAUTIONS AND INSTRUCTIONS COULD RESULT IN DAMAGE TO THE PRODUCT OR VEHICLE AND/OR SERIOUS INJURY TO YOU AND YOUR PASSENGERS!Warnings to Installers Whelen’s emergency vehicle warning devices must be properly mounted and wired in order to be effective and safe. Read and follow all of Whelen’s written instructions when installing or using this device. Emergency vehicles are often operated under high speed stressful conditions which must be accounted for when installing all emergency warning devices. Controls should be placed within convenient reach of the operator so that they can operate the system without taking their eyes off the roadway. Emergency warning devices can require high electrical voltages and/or currents. Properly protect and use caution around live electrical connections.Grounding or shorting of electrical connections can cause high current arcing, which can cause personal injury and/or vehicle damage, including fire. Many electronic devices used in emergency vehicles can create or be affected by electromagnetic interference. Therefore, after installation of any electronic device it is necessary to test all electronic equipment simultaneously to insure that they operate free of interference from other components within the vehicle. Never power emergency warning equipment from the same circuit or share the same grounding circuit with radio communication equipment. All devices should be mounted in accordance with the manufacturer’s instructions and securely fastened to vehicle elements of sufficient strength to withstand the forces applied to the device. Driver and/or passenger air bags (SRS) will affect the way equipment should be mounted. This device should be mounted by permanent installation and within the zones specified by the vehicle manufacturer, if any. Any device mounted in the deployment area of an air bag will damage or reduce the effectiveness of the air bag and may damage or dislodge the device. Installer must be sure that this device, its mounting hardware and electrical supply wiring does not interfere with the air bag or the SRS wiring or sensors. Mounting the unit inside the vehicle by a method other than permanent installation is not recommended as unit may become dislodged during swerving; sudden braking or collision. Failure to follow instructions can result in personal injury. Whelen assumes no liability for any loss resulting from the use of this warning device. PROPER INSTALLATION COMBINED WITH OPERATOR TRAINING IN THE PROPER USE OF EMERGENCY WARNING DEVICES IS ESSENTIAL TO INSURE THE SAFETY OF EMERGENCY PERSONNEL AND THE PUBLIC.Warnings to Users Whelen’s emergency vehicle warning devices are intended to alert other operators and pedestrians to the presence and operation of emergency vehicles and personnel. However, the use of this or any other Whelen emergency warning device does not guarantee that you will have the right-of-way or that other drivers and pedestrians will properly heed an emergency warning signal. Never assume you have the right-of-way. It is your responsibility to proceed safely before entering an intersection, driving against traffic, responding at a high rate of speed, or walking on or around traffic lanes. Emergency vehicle warning devices should be tested on a daily basis to ensure that they operate properly. When in actual use, the operator must ensure that both visual and audible warnings are not blocked by vehicle components (i.e.: open trunks or compartment doors), people, vehicles, or other obstructions. It is the user’s responsibility to understand and obey all laws regarding emergency warning devices. The user should be familiar with all applicable laws and regulations prior to the use of any emergency vehicle warning device. Whelen’s audible warning devices are designed to project sound in a forward direction away from the vehicle occupants. However, because sustained periodic exposure to loud sounds can cause hearing loss, all audible warning devices should be installed and operated in accordance with the standards established by the National Fire Protection Association.Safety First This document provides all the necessary information to allow your Whelen product to be properly and safely installed. Before beginning the installation and/or operation of your new product, the installation technician and operator must read this manual completely. Important information is contained herein that could prevent serious injury or damage.Installation Guide:Option Kit KDCRLED Centurion™ Lightbar Steady ID Light 51 Winthrop Road Chester, Connecticut 06412-0684Phone: (860) 526-9504Internet: Salese-mail:*******************CustomerServicee-mail:*******************®ENGINEERING COMPANY INC.IMPORTANT! The lightbar should be located a minimum of 16" Array from any radio antennas!Installation:1.Remove the two Torx head screws that secure the end cap to thebase. (Fig. 1)2.Slide the lens sections off the end of the base and remove thedividers so you may gain access to the lightbar base. (Fig. 2) Besure to note the order in which the lenses were installed on thelightbar.Note:You will notice that the lenses are seated verytightly into the lens divider gaskets to preventleaks. You will need to insert a screwdriver at eachcorner (between the black endcap and aluminumbase) and gently pry the lens out to break it freefrom the dividers. Pry each side out just a little at atime, alternating from one side to the other untilthe lens slides out easily. Before reassembling,apply a very small amount of liquid dish detergentto the sides of the rubber gaskets to help themslide in easier and obtain a better seal.3.Measure the length of the lightbar base to find the exact centerand mark it with a pencil or marker. (See next page)4.Place the lighthead assembly onto thecenter of the lightbar base.Be sure to insert the lip on the end of the take-down assembly,into the slot in the base as shown in figure 3. Secure the assembly to the channel in the lightbar base, using two of the 3/8” hexhead screws provided.Wiring:1.Secure the ground lug for the filter assembly (the BLACK wire) to the channel in the lightbar base using the 1/4” hex headscrews provided as indicated. (Fig. 4)2.Connect the provided extension with the faston connectors, to the RED wire coming from the filter assembly. Run the extensionalong the lightbar base and connect the other end it to the GREY wire (or any unused wire) in the lightbar wiring harness. Note:The cable exiting the lightbar must be fused. (Refer to Fuse & Switch Information below.)3.Neatly dress and place any loose wires under the cable clamps to avoid interference with moving parts, then replace andsecure all domes.WARNING! All customer supplied wires that connect to the positive terminal of the battery must be sized to supply at least 125% of the maximum operating current and FUSED at the battery to carry that load. DO NOT USE CIRCUIT BREAKERS WITH THIS PRODUCT!WARNING!The outer surfaces of this product may be cleaned with mild soap and water. Use of any other chemicals may void product warranty. Do not use a pressure washer.。
DEL(DEM)皮带秤(定量给料机)使用手册

③环境污染要求:安装环境不允许有导电性粉尘和腐蚀性气体存在;应根据 仪表或变频器外壳防护等级要求,将控制柜安装在空气流通、清洁的环境。
④、环境震动要求:控制柜应安装在无震动环境,如必须安装在震 动比较大的场合,应采取有效隔震措施。
⑵、环带的负载调整:环带的负载调整必须在空载调整完成后进行。环带 载料后,若仍出现跑偏现象,重复上述空载调整过程。
第十八页,共33页。
DEL/DEM系列定量给料机使用手册
㈡、电气控制部分的调试要求及步骤 定量给料机能否实现计量准确、运行稳定,标定调试是关键。
1控制柜接电源:按图纸要求正确接线确认无误后,给控制柜上电,控 制柜内部各部分通电正常后,控制柜断电;
DEL/DEM系列定量给料机主要由两部分组成,即:电气控制部 分和机械部分。其中,电气控制部分主要由控制柜(控制箱)、称 重控制仪表、变频器、称重传感器、速度传感器等部件组成;机械 部分包括驱动装置、秤体、秤底座、主动滚筒、从动滚筒、环形胶 带、带荷测量装置、带速测量装置、环带涨紧装置、清扫装置、承 重托辊、布料器、集尘罩等部分。
㈡、定量给料机的安装要求和步骤
定量给料机由电气控制和机械两大部分组成,一般先进行机械 部分的安装再进行电气控制部分的安装,也可以机械部分和电气控 制部分同时安装。特殊情况例外。
第十一页,共33页。
DEL/DEM系列定量给料机使用手册
1、机械部分的安装 ⑴、安装空间要求: 设备安装空间,在铅垂方向上的尺寸应比设备总高 度大20~30mm。在水平方向,秤体无减速机侧至少有1.5倍环带宽度的 空间,便于以后检修设备和更换环带。 ⑵、安装基础要求:定量给料机应安装在稳固、坚实的基础上,基础为混 凝土或钢结构均可,要有足够的强度保证。 ⑶、就位前装配:定量给料机就位前,先将秤体(含序号2~6,8,13, 14各部件,见图2-1~3)与秤底座、集尘罩支架、集尘罩按图2-1~3所示 装配在一起,保证集尘罩下料口中心与主动滚筒距离符合随机图纸尺寸。 ⑷、现场测量:测量现场料仓口法兰离地高度,计算料仓法兰离地高度与 设备总高的高度差△H;测量现场料仓口中心与下一级落料口间的距离是 否与定量给料机的进出料口中心距相对应;根据现场测量结果确定设备准 确位置和安装顺序。
Ironton 工业级大型拖车货沿说明书
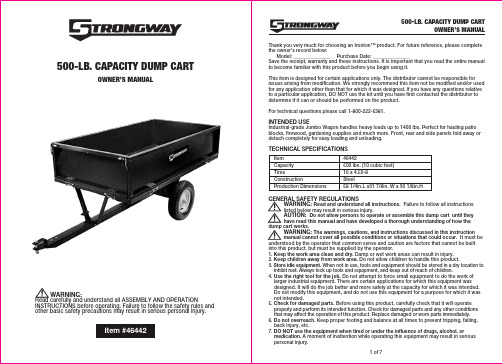
OWNER’S MANUAL
WARNING: Read carefully and understand all ASSEMBLY AND OPERATION INSTRUCTIONS before operating. Failure to follow the safety rules and other basic safety precautions may result in serious personal injury.
dump cart works. WARNING: The warnings, cautions, and instructions discussed in this instruction manual cannot cover all possible conditions or situations that could occur. It must be
understood by the operator that common sense and caution are factors that cannot be built into this product, but must be supplied by the operator. 1. Keep the work area clean and dry. Damp or wet work areas can result in injury. 2. Keep children away from work area. Do not allow children to handle this product. 3. Store idle equipment. When not in use, tools and equipment should be stored in a dry location to
ROLAND M-200i说明书V1

电池面板螺丝及任何您可能会取下的推子 旋钮等。
118e
请小心进行接地操作 ● 如果您要从接地终端上移除螺丝,请小心放置,
以免儿童接触发生意外。当重新安装时,请拧 紧螺丝。
120
使用幻像供电的注意事项 ●除了连接电容话筒外,请关闭幻像供电再连接
360
● 由于放置设备之处的表面材质和温度等缘故,本设备的橡胶 脚垫可能发生褪色或表面破裂。您可以在脚垫下垫一块毡毯 或布料来防止此类现象发生。但要注意确保不要使设备滑落 或意外移动。
361
● 请不要将盛有水的容器 (如花瓶等)置于设备上。同样,请 避免将杀虫剂、香水、酒精、指甲油或喷雾罐等置于设备上 方。如有液体洒落于设备上,请使用柔软的干布将其擦干。
• 变压器、电源线或插头破损 • 冒烟或发出异味 • 有异物掉入或液体渗入设备 • 设备遭到雨淋 (或其它方式被打湿) • 设备操作不正常或表现出明显的变化
..............................................................................................................
存储备份
501b
● 本设备内置电池,保证关机情况下为内部存储供电。当电池 电量即将耗尽时屏幕上会有提示信息。当您看到此信息后, 请尽快更换新的电池避免数据丢失。关于更换电池的信息, 请查看本说明书第 16 页 “ 关于内置电池 ”。
其它注意事项
551
● 请注意设备发生故障时内部存储的数据会丢失。为了避免发 生重要数据丢失,建议您将数据保存至 U 盘。
放置场所
351
● 将本设备放在靠近后级功率放大器(或其它含有大型电源转 换电路的设备)旁边可能会产生嗡音等噪声。要缓和这种噪 音,请改变机器的方向或是放置到较远的地方以避免干扰。
(word完整版)德国布朗卢比PowerMon 中文操作手册

PowerMon OERATION MANUALKOLORIMETERSILIKOMETERIONOMETERNATRIOMETERTITROMETER在安装或开始运行系统时,请仔细阅读本手册。
Bran+Luebbe公司不对由不遵守说明书而造成的损坏负责,并且质保期也会随之失效.使用非Bran+Luebbe原装的配件也会导致质保期的失效。
本说明书中的内容可以由Bran+Luebbe公司单方面更改而无需另行通知。
未经Bran+Luebbe公司的书面许可,本手册的任何部分都不允许以任何方式——电子地或机械地——被复制,传播.即便本手册被译为多种语言的版本,德文的版本为原始版本.目录1 介绍 (4)1.1 本手册的惯例 (4)2 安全建议 (5)3 运行操作 (6)3.1 概述 (6)3.2 触摸屏 (6)3.2.1 初始化 (7)3.2.2 PowerMon 的结构和布局 (8)3.3 结果 (8)3.3.1 表格 (9)3.3.2 图表 (10)3.3.3 信息 (10)3.4菜单 (11)3.4.1 系统 (11)3.4.2 传感器列表 (12)3.4.3 参数列表 (17)3.4.4应用 (17)3.4.5 服务 (23)3.4.6 帮助 (34)3.5 操作模式 (35)3.5.1 测量模式 (36)3.5.2 校准模式 (36)3.5.3 停止模式 (36)3.5.4 错误模式 (37)4 报错信息 (38)4.1 概述 (38)4.2 报错信息概述 (38)1 介绍Bran+Luebbe公司的PowerMon系列分析仪表是新一代完全自动化的在线分析仪表的。
他们用湿化学的方法,可以连续不断地测量液体样品中的多种成分的浓度。
本手册说明了以下两种分析仪表:· POWERMON KOLORIMETER·POWERMON SILIKOMETER·POWERMON LONOMETER·POWERMON NATRIOMETER·POWERMON TITROMETER操作人员需要有一定的基础技术知识.在安装调试前请仔细阅读本手册.将手册一直放在系统的附近,以方便查阅。
德马工业输送辊筒选型手册中文版
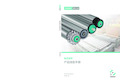
1800 系列 无动力输送辊筒 ……………………… 28
2214/2224 系列 塑钢单 / 双链输送辊筒 ………… 52 2411/2421 系列 钢制单 / 双链输送辊筒 ………… 56 2311/2321 系列 钢制单 / 双链输送辊筒 ………… 60
积放输送辊筒产品系列
66-75
3214/3224 系列 塑钢单 / 双链积放辊筒 ………… 68
铝合金
与钢管、不锈钢相比,铝合金的强度只有它们的1/3,但 它重量轻,只有钢管的36%,并且不怕水、不生锈,适合 某些需要辊筒轻量或水淋的应用,并且在特定行业(如橡 胶业)中广泛使用。
PVC
PVC管(聚氯乙烯)的承载能力远低于普通钢管,但由 于其自身的独特性能,在某些领域有着广泛的应用: 1.防腐蚀,良好的化学稳定性; 2.容易清洁; 3.重量轻,启动性能好; 4.运行噪音低,良好的防震性能。
辊筒标准代号(订货代号)的说明 ………………… 11
参数化图纸下载 …………………………………… 12
更多设计信息 ……………………………………… 13
无动力输送辊筒产品系列
14-33
1900 系列 轻型输送辊筒 ………… …………………… 18
1200 系列 泛用型输送辊筒 ……………………… 23
材料
304
J4-200
导磁性
不导磁
耐腐蚀性 对碱溶液及大部分有机 酸亦具有良好的耐腐蚀 能力。
耐腐蚀性一般,在没有 氯化物污染或潮湿的一 般大气腐蚀环境中,能 够长期工作,基本上保 持无锈蚀。
主要用途 厨房器具,汽车零件, 建筑材料,食品生产设 备,医院用具等。
主要用作装饰,或在某 些有高温要求时代替钢 管镀锌使用。
输送线皮带操作及维护说明书

菜鸟惠阳项目(皮带输送机)维护及操作指南说明书浙江德马科技股份有限公司目录1绪言 (4)2维修人员安全指导 (5)2.1清洁系统与模块 (6)2.2机械维护安全 (6)2.3电气维护安全 (7)2.4安全准则 (8)2.5运行安全 (9)2.6狭窄空间 (9)2.7防护罩 (10)2.8端部防护罩 (10)2.9底部防护罩 (11)2.10安全标签 (11)2.11本地安全考虑 (13)3技术规格 (14)3.1环境条件 (14)3.2输送速度 (14)4竣工系统总体介绍 (15)4.1水平皮带输送机 (15)4.1.2尾部 (19)4.1.3机身 (21)4.1.4侧板 (21)4.2转弯皮带机 (24)5更换零部件 (26)5.1尾部的维修 (26)5.1.1尾部滚筒的拆装 (26)5.2驱动部的维修 (27)5.2.1驱动的构成 (27)5.2.2改向滚筒的更换 (29)5.2.3张紧滚筒的更换 (29)5.2.4驱动滚筒的更换 (30)5.3转弯部滚筒的更换 (31)6设备维护与保养 (32)6.1常见故障及原因 (32)6.2皮带跑偏 (33)6.2.1皮带跑偏的危害 (33)6.2.2皮带跑偏的原因 (34)6.2.3皮带跑偏的处理 (34)6.3系统维护 (36)6.3.1总则 (36)6.3.2设备安全检查措施 (36)6.3.3设备检查人员安全措施 (37)6.3.4机械设备检查措施 (37)6.3.5工具,准备和材料要求 (37)6.3.6日常性维护及保养 (38)6.4链条的维护及保养 (39)6.4.1影响链条使用寿命的因素及磨损点 (39)6.4.2链条的维护 (40)6.4.3链条润滑方法的选择 (40)6.5润滑 (41)6.5.1润滑注意事项 (41)6.5.2润滑说明 (41)6.6带座轴承的维护 (42)6.6.1带座轴承的结构 (42)6.6.2带座轴承拆装方法 (43)6.6.3维护保养(定期检查) (44)6.6.4润滑脂的补充 (45)6.6.5润滑脂补充间隔时间 (45)6.6.6润滑脂的补充方法 (46)6.6.7轴承的更换 (48)7常见问题解答 (49)1 绪言此菜鸟惠阳项目是浙江德马集团与菜鸟(集团)双方经过多次技术交流、实地勘查、讨论、结合以前提供给菜鸟其他项目输送机相关案例进行的设计、制造,为贵公司量身定做的一套半自动化输送系统。
输送设备操作手册

焦作瑞丰纸业有限公司废弃物焚烧供热系统工程输送设备操作手册(第一版)编制:审核:批准:焦作瑞丰纸业有限公司动力车间2009年6月17日输送设备操作规程一、燃料输送工艺流程1.1 燃料输送系统1.1.1输煤系统的范围包括:从干煤棚至锅炉的卸煤、储煤、上煤全部系统。
1.1.2燃料输送系统及运行制式燃料输送系统采用单路皮带机,分时段输煤和输送废木渣。
输煤时皮带机出力Q=30t/h,带宽B=500mm,带速v=1.0m/s。
按1台15t/h锅炉100%MCR纯燃煤,采用3班制,每班运行约0.5小时。
按1台15t/h锅炉100%MCR混烧工况,运煤采用一班制,每班运行约1小时。
运废木渣采用间歇运行方式,每班运行约0.5小时,每天7次。
1.2燃料输送工艺流程1.2.1输煤流程自卸汽车来煤→煤堆(干煤棚)→ZL50型装载机→受煤斗→电磁振动给料机→1#皮带机→除铁器→2#皮带机(配电子皮带称)→炉前煤仓1.2.2输废木渣流程厂内车辆来废木渣→生物质堆(生物质棚)→ZL50型装载机→往复式给料机→1#皮带机→犁式卸料器→炉侧生物质仓(储存)→螺旋给料机→星型给料阀1.3燃料输送设备性能1.3.1电磁振动给煤机1) 设备位号:2012) 型号:GZ-43) 数量:1台4) 给料量:30t/h5) 废木渣粒度:小于50×30×5mm6) 给煤粒度:≤50mm7) 电机功率:0.45kW8) 电压:380V9) 频率:50Hz10) 防护等级:IP5411) 绝缘等级:F级12) 接线方式:Y21.3.2 1# 带式输送机1) 设备位号:2022) 型号:TD753) 数量:1台4) 给料量:30t/h5) 带宽:B=500mm6) 带速:v=1.0m/s7) 水平长度:Lh=63.7m8) 输送高度:H=16.3m9) 电机功率:7.5kW10) 电压:380V11) 频率:50Hz12) 防护等级:IP5413) 绝缘等级:F级14) 接线方式:Y21.3.3 2# 带式输送机1) 设备位号:2032) 型号:TD753) 数量:1台4) 给料量:30t/h5) 带宽:B=500mm6) 带速:v=1.0m/s7) 水平长度:Lh=8.4m8) 电机功率:3.0kW9) 电压:380V10) 频率:50Hz11) 防护等级:IP5412) 绝缘等级:F级13) 接线方式:Y21.3.4 螺旋给料机1) 设备位号:2042) 型号:LS-4003) 数量:1台4) 给料量:0~5t/h5) 螺旋直径:400mm6) 螺旋形式:等距螺旋7) 带速:v=1.0m/s8) 输送距离:7500mm9) 变频电机功率:5.5kW10) 电压:380V11) 频率:50Hz12) 防护等级:IP5413) 绝缘等级:F级14) 接线方式:Y21.3.5 炉前星型给料器1) 设备位号:1022) 数量:1台3) 给料量:0~5t/h4) 出口尺寸:400mmx400mm5) 变频电机功率:2.2kW6) 电压:380V7) 频率:50Hz8) 防护等级:IP549) 绝缘等级:F级10) 接线方式:Y21.3.6 电子皮带秤1) 设备位号:2052) 数量:1台3) 带宽:500mm4) 精度:±0.5%5) 螺旋形式:变距螺旋6) 带速:v=1.0m/s7) 输送距离:7500mm8) 电机功率:0.1kW9) 电压:220V10) 频率:50Hz1.3.7 电动双侧犁式卸料器1) 设备位号:2062) 数量:1台3) 适用带宽:500mm4) 适用带速:v=1.0m/s5) 电机功率:0.75kW6) 电压:380V7) 频率:50Hz8) 防护等级:IP549) 绝缘等级:F级10) 接线方式:Y21.3.8 悬挂式永磁除铁器1) 设备位号:2072) 型号:RCYB-53) 数量:1台4) 适用带宽:500mm5) 适用带速:v=1.0m/s6) 电机功率:0.75kW7) 电压:380V8) 频率:50Hz9) 防护等级:IP5410) 绝缘等级:F级11) 接线方式:Y2二、开车应具备的条件所有与输送系统相关的设备已经安装完成;所有设备已经具备通电条件;所有润滑点已经加注润滑油(脂);皮带连接已经达到强度要求;三、开车方法和步骤3.1 固定式皮带输送机3.1.1螺旋输送机试运转前,应符合下列要求:3.1.1.1润滑油(脂)的名称、型号、主要性能和加注的数量应符合螺旋输送机技术文件的规定。
EMAGE-2D使用说明书

Users’ Manual for EMAGE-2D Laurel Industrial Company, Inc.Table of ContentsChapter 1 System Overview (3)1.1 Brief Description of Main Features of EMAGE-2D (3)1.2 Requirement for Computer System (4)1.3 Install and Run EMAGE-2D (4)Chapter 2 Data Manipulation and Analysis (7)2.1 Data Input (7)2.2 Brief Description about Data Manipulation Toolbar (10)2.3 Viewing Data (11)2.4 Data Manipulation (17)2.5 Saving Data (27)Chapter 3 RRI 2-D Inversion (31)3.1 Choose Data for RRI Inversion (31)3.2 Initial Model Construction (32)3.3 Set RRI Inversion Parameter (35)3.4 Save RRI files (39)3.5 Run RRI Inversion (40)3.6 Retrieve Inversion Result (41)Chapter 4 RM2D Inversion (44)4.1 Brief Description about Model Manipulation Toolbar (44)4.2 Data Selection for RM2D Inversion (46)4.3 Set RM2D Starting Model (47)4.4 Model Display and Modification (49)4.5 Set RM2D Inversion Parameters (52)4.6 Save RM2D Files (53)4.7 Run RM2D Inversion (55)4.8 Retrieve Inversion Result (56)Chapter 5 PW2D Forward (58)5.1 Introduction to Finite Element Modeling (58)5.2 Frequency Definition (61)5.3 Mesh Initialization (61)5.4 Model Display and Manipulation (62)5.5 Set Model 1-D Background (63)5.6 Boundary Extension (63)5.7 Set Site Location (64)5.8 Clear Current Model (65)5.9 Save PW2D Files (65)5.10 Run PW2D Forward (66)5.11 Retrieve PW2D Forward Result (67)Appendix: Software Document for RM2D inversion (68)References (78)Disclaimer (79)Chapter 1 System Overview1.1 Brief Description of Main Features of EMAGE-2DEMAGE-2D is a MT/AMT data processing and modeling software package, which can be divided into four modules including Data Manipulation and Analysis, RRI Inversion, RM2D Inversion and PW2D Forward. Below is a brief introduction to the major features of each module.1.Data Manipulation and Analysis∙Viewing data parameters such as apparent resistivity, impedance phase, coherency, skew, strike, polar diagram, Bostick transform etc. ∙Impedance rotation∙Data interpolation∙Frequency and site selection∙TE/TM mode definition∙Static shift analysis and correction∙Duplicate site handle2.RRI Inversion∙Data selection for inversion∙Starting model construction∙Set inversion parameters∙Save RRI files and run RRI∙Retrieve and display inversion result3.RM2D Inversion∙Data selection for inversion∙Starting model construction∙Model manipulation∙Set inversion parameters∙Save RM2D files and run RM2D∙Retrieve and display inversion result4.PW2D Forward∙Frequency selection for forward problem∙Model construction and manipulation∙Auto padding for the extension of model boundary∙Save PW2D files and run PW2D∙Retrieve and display forward calculation result1.2 Requirement for Computer SystemEMAGE-2D is a window application that can be run on Window 95/98, Window NT 4.0. It is recommended to run EMAGE-2D on a high performance computer because of the computational intensity of 2-D inversion and forward algorithm.1.Minimum RequirementCPU: Pentium 200Memory: 32 megabytesHard Disk: 100 megabytes free spaceDisplay: support 800X600 resolution under 256-color mode2.Recommended RequirementCPU: Pentium-II 400Memory: 128 megabytesHard Disk: 500 megabytes free spaceDisplay: support 1024X768 resolution under 16 bites color mode1.3 Install and Run EMAGE-2DEMAGE-2D InstallationInsert the EMAGE-2D CDROM into your computer‟s CDROM drive, then run the file setup.exe so the installation wizard will be launched. It will guide you through the entire installation procedure.When you begin the setup program, you will be presented the Choose Destination Location dialog (figure 1.1) which gives you chance to specify which folder to install EMAGE-2D.EMAGE-2D executable and all other supported files will be automatically copied into this folder by installation wizard. The default folder isC:\EMAGE-2D. If you hope to change it, click Browse button, then the Choose Folder dialog (figure 1.2) will be displayed on the screen. You can specify the EMAGE-2D installation folder on it, then click OK button to return Choose Destination Location dialog in which you can click Next button to begin to copy files.Figure 1.1 Choose Destination Location DialogFigure 1.2 Choose Folder DialogIf your operation system is Window NT, you also need run ntdrv.exe under subfolder “NTDRV” in the EMAGE-2D folder to install dongle driver on your machine.Run EMAGE-2DEMAGE-2D can only be run on the machine on which the hardware key (dongle) supplied with EMAGE-2D is installed. In order to install dongle, it is better shut down your computer first, then attach the dongle to the parallel printer port of your computer. You can attach the 25-pin connector of the printer to the other end of the key. After making sure the dongle is installed properly, click EMAGE-2D item on the Program submenu of Start menu on your computer to launch EMAGE-2D. You also can double click EMAGE-2D.EXE in the directory where EMAGE-2D is installed to run it.Chapter 2 Data Manipulation and Analysis2.1 Data InputEMAGE-2D supports Z file format of EH4, RES file format of MT-1 and the output of PW2D forward output as input data at present time.1.EH4 Data InputFor EH4 data, there are two ways to prepare input data. Below is step by step description about how to input EH4 data into EMAGE-2D.1)Using @(or @l)File as Input DataFigure 2.1 Open EH4 @ Files Dialog(1)Create a working directory in your hard disk.(2)For high frequency data, copy @ file and the impedance files (the files preceded by Z) of your survey data from your EH4 instrument into the working directory; For low frequency data copy @l and the impedance files (the files preceded by W) into the working directory. (3)Select Open EH4 @ file…in File menu, then Open EH4 @ file dialog (figure 2.1) will be popup on the screen. When Auto Selectcheckbox is checked, EMAGE-2D will determine whether the data is high or low frequency data according to the file name. Sometime you may rename @ or @l file for some reasons. In this case, EMAGE-2D has no idea about the data type, so you need set it manually. High Freq and Low Freq radio button will be enabled after Auto Check is unchecked. If the data to be input is high frequency data, High Freq should be checked, otherwise, Low Freq should be checked.(4)Click OK button on the dialog to begin inputting data.(5)When an impedance file in @ or @l does not exist in the current directory, a warning message will be given to indicate that this file does not exist in the current directory and inquire whether to continue without it or quit to check the data.2)Edit EH4 line definition file (EH4 File) as input data.Figure 2.2 Open EH4 File Dialog(1)Create a working directory in the hard disk, then copy the impedance files preceded by Z or W into the working directory.(2)Use text editor such as Notepad in Windows or Edit on Dos promptmode to create a line definition file with an extension of EH4. If you use word processor such as Word to create line definition file, be sure save it as pure text format. Below is an example to demonstrate the format of EH4 line definition file.Line 1 Format: EH4Line 2 This is an example of line definition file for EH4 dataLine 3 There are three sites in the data setLine 4 Data:Line 5 Ztest.001 X: 0 Y: 0 Z: 0Line 6 Ztest.002 X: 30 Y: 0 Z: 0Line 7 Ztest.003 X: 60 Y: 0 Z: 0Line 1 always is “Format: EH4”, indicating that the input data is EH4 data. After that, you can write any number of comment lines (such line 2 and line 3 in above example). The “Data:” line (line 4 in above example) after comment lines indicates the lines below are the data lines that will be taken as input by EMAGE-2D. Each site takes one line consisting of the impedance file name and coordinates for the site.(3)Click Open EH4 File in File menu to popup Open EH4 File dialog (figure 2.2). Open EH4 data line definition file to input data.2.MT-1 Data Input(1)Create a working directory in the hard disk, then copy the RES files output by MT-1 processing program into the working directory.(2)Use text editor such as Notepad in Windows or Edit on Dos prompt mode to create a line definition file with an extension of MT1. If you use word processor such as Word to create line definition file, be sure save it as pure text format. Below is an example to demonstrate the format of MT-1 data line definition file.Line 1 Format: MT-1Line 2 This is an example of line definition file for MT-1 dataLine 3 Data:Line 4 Demo1.res X: 0 Y: 0 Z: 400Line 5 Demo2.res X: 1000 Y: 0 Z: 510Line 6 Demo3.res X: 2000 Y: 0 Z: 450Line 1 always is “Format: MT-1”, indicating that the input data is MT-1 data. After that, you can write any number of comment lines (line 2 in above example). The “Data:” line (line 3 in above example) after comment lines indicates the lines below are the data lines that will be taken as input by EMAGE-2D. Each site takes one line, consisting of the impedance file name and coordinates for the site.Figure 2.3 Open MT-1 File Dialog(3)Click Open MT-1 File in File menu then popup Open MT-1 File dialog (figure 2.3). Open MT-1 data line definition file to input data. 3.PW2D Forward Calculation Data InputDetailed description about how to input PW2D data is discussed in Chapter 5.2.2 Brief Description about Data Manipulation ToolbarFigure 2.4 Data Manipulation ToolbarIn order to edit and display the input data, user need to access the controls on the Data Manipulatio n Toolbar (figure 2.4). When data input has been done, the toolbar will be enabled. Below are brief descriptions about themain functions of the controls from left to right in the toolbar.Plot Button:Click it to refresh the content in plot area.Edit Button:Any graphical edit operation cannot be functioned unless this button is checked.Mask Button:This button is used to control whether or not to display the disabled frequencies. When it is checked , the disabled frequencies will not be displayed, otherwise, the disabled frequencies will be displayed in gray color.Static Shift Button:This button is used control to display the data without static shift correction or corrected data. If it is unchecked, the displayed data will be raw data without static correction, otherwise, corrected data will be displayed. Another function of this button is for static correction operation. Static shift correction operation is allowed only if the button is checked. Interpolation Button:It is used to control if display raw data or interpolated data. If this button is unchecked, raw data will be displayed, otherwise you can view and edit the interpolated data.Switch Button:When this button is checked, you can switch XY and YX mode impedance (rotate±90 °) frequency by frequency.Plot Type Selection List Box:Can be used to select different parameters to view and edit.Site Selection List Box:Set the selected site as current site, so you can view and edit the parameters of the current site.2.3 Viewing DataEMAGE-2D can display twenty-first type of parameter about the data set (figure 2.5)1.Site Location MapSelect this item to display Site Location Map. After data input is completed, EMAGE-2D will display Site Location Map in plot area(figure 2.6). A triangle sign represents each site. The impedance file name of the site taken as site name is displayed above or below it. If you hope not to display site name on the map, click Show Site Name in Site Location Map in Data Manipulation menu to uncheck it.Figure 2.5 Plot Type In Selection List BoxFigure 2.6 Site Location Map2.Apparent Resistivity CurveThe apparent resistivity curve of current site will be displayed in plot area when user selects Apparent Resistivity item in Plot Type Selection list box (figure 2.7). For raw data, XY and YX mode are represented as rectangle and triangle signs respectively. If interpolated data is displayed, XY and YX model will be shown by red and blue dot respectively. Mask, Static Shift and Interpolation button on the Data Manipulation toolbar can be used to control the display mode of apparent resistivity curve.∙When Mask button is checked, the disabled frequencies will not be shown, otherwise, the disabled frequencies will be displayed in gray color.∙When Static Shift button is checked, the data after static shift correction will be displayed, otherwise the uncorrected data will be shown.∙When Interpolation Button is checked, the interpolated data will be displayed, otherwise the raw data will be shown.Figure 2.7 Apparent Resistivity Curve3.Impedance Phase CurveThe impedance phase curve of current site will be displayed in plot areawhen you select Impedance Phase item in Plot Type Selection list box. For raw data, XY and YX mode are represented as rectangle and triangle signs respectively. If the interpolated data is displayed, XY and YX model will be shown by red and blue dot respectively. The display mode of impedance phase curve controlled by Mask and Interpolation button is the same as that of apparent resistivity.4.StrikeThe strike curve of current site will be displayed in plot area when you select Strike item in Plot Type Selection list box. The display mode of strike curve controlled by Mask and Interpolation button is the same as that of apparent resistivity.5.SkewThe skew curve of current site will be displayed in plot area when you select Skew item in Plot Type Selection list box. The display mode of skew curve controlled by Mask button is the same as that of apparent resistivity.6.CoherencyThe coherency curve of current site will be displayed in plot area when you select Mult Coh (E, H) item in Plot Type Selection list box. The data of XY mode and YX mode is represented as rectangle and triangle signs respectively. The display mode of coherency curve controlled by Mask button is the same as that of apparent resistivity.There is no coherency data in the MT-1‟s RES file, so EMAGE-2D set them to 1 in order to be compatible with EH-4 data.7.Polar DiagramThe polar diagram of current site will be displayed in the plot area when you select Polar Diagram item in Plot Type Selection list box (figure 2.8). The polar of each frequency is contained in a rectangle where the frequency value is printed on upper part of the rectangle. Red polar and blue polar are principal impedance and auxiliary impedance components respectively.Figure 2.8 Polar Diagram8.Bostick TransformThe relation between impedance and frequency can be transformed to the relation between resistivity and depth by Bostick transform, roughly reflecting the earth resistivity distribution versus depth.The Bostick transform curve of current site will be displayed in plot area when you select Bostick Transform item in Plot Type Selection list box. For raw data, XY and YX mode are represented as rectangle and triangle signs respectively. If the interpolated data is displayed, XY and YX model will be shown by red and blue dot respectively. The display mode of Bostick transform curve controlled by Static Shift and Interpolation button is the same as apparent resistivity.Cross SectionsIn order to view cross section of the data, you need to define profile first. If you want to show the cross section of TM or TE mode data, you shoulddefine the mode of each site also. A detailed description about how to define profile and TM/TE mode is presented later in this manual. EMAGE-2D can show twelve types of cross sections (table 2.1).Table 2.1 The type of cross section Item in the listbox of plot typeApparent resistivity in XY mode App. Resistivity Freq Section-RhoXY Impedance phase in XY mode Phase Freq Section-PhsXYApparent resistivity in YX mode App. Resistivity Freq Section-RhoYX Impedance phase in YX mode Phase Freq Section-PhsYXApparent resistivity in TM mode App. Resistivity Freq Section-RhoTM Impedance phase in TM mode Phase Freq Section-PhsTMApparent resistivity in TE mode App. Resistivity Freq Section-RhoTE Impedance phase in TE mode Phase Freq Section-PhsTEBostick resistivity in XY model Bostick Depth Section-BostXYResBostick resistivity in YX model Bostick Depth Section-BostYXResBostick resistivity in TM model Bostick Depth Section-BostTMResBostick resistivity in TE model Bostick Depth Section-BostTERes Static shift and Interpolation buttons on Data Manipulation toolbar can be used to control display manner of cross section. When Static Shift button is checked, the data you have seen is statically corrected data, otherwise uncorrected data is shown. Interpolation button acts similar way, checked for interpolated data, unchecked for raw data.EMAGE-2D will create default color scale for each type of cross section according to data value. If you want set it manually, click Set Color Scale For Contour in Data Manipulation menu and popup Set Color Scale For Contour dialog (figure 2.9). Double-click any item in Scale List box, the scale value will appear in Enter Color Scale Value so you can modify it manually. Default Color Scale checkbox gives you the option to use default color scale or not. If you check Blank No Data Area, the area without data will be blanked.Static Correction Reference CurveIn order to display static correction reference curve, you need also define profile first. After that, click Static Correction Reference Curve to display it. Please refer to Static Shift Correction section later in this manual for thedetailed discussion about it.Figure 2.9 Set Color Scale For Contour Dialog2.4 Data ManipulationMost of data edit operation will need to access Data Manipulation menu and Data Manipulation toolbar. If no explicit indication, submenu mentioned in this chapter refers to the item in Data Manipulation menu and toolbar is taken for Data manipulation toolbar.1.Duplicate Sites HandleIf there are duplicates sites whose X and Y coordinates are same, Check Duplicate Sites submenu will be enabled. Select it and popup Check Duplicate Sites modeless dialog (figure 2.10). When the dialog is displayed on the screen, you can do other operation outside the dialog so it is convenient to check duplicate sites‟ data quality while dealing with them.The first group of duplicate sites found by EMAGE-2D will be appear in Duplicate Sites list box when you open the dialog first time. EMAGE-2D will search another group of duplicate sites if there are ones when you click Find Next button. Select Restart will search duplicate sites again from very beginning. If you decide delete some site, highlight the site name in list box, then click Delete button to delete it. Sometime it may bebetter to combine duplicate sites into a new site. Click Combine… button to bring Input Combined Site Name dialog (figure 2.11) up. Put site name in Combined Site Name as the name of the new site. If you hope to delete the old sites after combination, please check Delete Old Sites checkbox. After click OK button, the combined site will display in Duplicate Site list box of Check Duplicate Sites dialog. It is recommended to disable bad frequencies of duplicate sites before doing combination.Figure 2-10 Check Duplicate Sites DialogFigure 2-11 Input Combined Site Name Dialog2.Fix ImpedanceIn MT/AMT theory, the impedance is calculated under right-handed coordinate system. If the orientation of electrical or magnetic sensors isnot set this way, the calculation of skew and polar will be incorrect, the auxiliary impedance component of polar and skew will be anomaly big. If the orientation of some site is suspected not being set properly, EMAGE-2D will fix it automatically. Sometime EMAGE-2D will make wrong decision because of the noise in the data and the complexity of the earth. In this case, you need fix it manually by check the skew and polar diagram. When the skew and auxiliary impedance component is too big, you can click Fix Impedance submenu to fix it.3.Vector Versus Tensor Data of EH4Vector impedance is not stable as the polarizing direction of incident electromagnetic field varies with time. This is the very reason why we often use tensor impedance for data interpretation in MT. When the measure time is short such as EH4 survey, the polarization may not change too much. It may be acceptable to use vector data for interpretation. In field survey, it is not unusual to have good data in one direction but bad in another direction due to culture noise. It maybe causes both XY and YX mode data noisy if you use tensor impedance data because the calculation of tensor data will use both direction data. As for vector impedance data, you only need electrical field in one direction and magnetic field in the perpendicular direction to get vector data in this direction. In this case, you may get good data in one direction for interpretation. This is why both vector and tensor data are contained in impedance file of EH4 data. It is recommended to use tensor impedance if the data of both directions is good.You can switch between tensor and vector data by click Show EH4Vector Data submenu. If vector data is being used, a check sign will appear on the left of the submenu. By the way, if you have done rotation on the data, the data will be tensor because there is no way to rotate vector data.4.Site and Frequency Selection(1)Site SelectionThere are two ways to select sites into current data set.Figure 2.12 Data Selection DialogThe first one is to select sites on Data Selection dialog. Select Data Selection submenu to bring up Data Selection dialog (figure 2.12). A site will be selected into the current data set if you highlight it in Site Name list box, unhighlight it will delete it from the current data set. Clicking site name in the list box will switch between selection and deletion. You can select or delete all sites by clicking Select All Sites button. If all sites are already selected, clicking Select All Sites button will delete all sites, otherwise all sites will be selected. Actually, deleted sites will not be considered it in data analysis, display and interpretation process. You can include it later by reselecting it.The second way for site selection can be done though Site Location Map.A triangle sign represents each site. When Site location Map is shown, check Edit button on the toolbar first. Clicking the site sign will switch between selection and deletion. The selected sites are printed in blue color,deleted ones in gray color.(2)Frequency SelectionThere are three ways to select frequency.The first one is to do it in Data Selection dialog that is similar to site selection. Highlight a frequency in Frequency list box of the dialog (figure 2.12) to enable it, unhighlight it to disable it. Every frequency contained in any site will be listed in Frequency list box. It is not necessary to have all sites have same frequencies. If you enable or disable any frequency in the list box, this frequency will be enabled or disabled from the sites that have the data of this frequency. Select All Freq button can also be used to enable or disable all frequencies in the way which is similar to Select All Sites button for site selection.Figure 2-13 Frequency Auto-Selection DialogThe second way is to select frequencies automatically in Frequency Auto-Selection dialog. Selecting Frequency Auto-Selection submenu to popup Frequency Auto-Selection dialog (figure 2.13). Input cut-off value in Select Freq. By Coh(>=)so the frequencies will be disable automatically when their coherencies are below this value. Similarly, the frequencies will also be disabled when their skews are greater than the value in Select Freq. By Skew (<=).In other hand, you are provided an option to select frequencies for the current site or all sites in Site Selection radio button group and to select frequencies for which mode data in ModeSelection radio button group.The third way is to select frequencies on apparent resistivity, impedance phase and coherency curves. Interpreter normally needs to analyze data site by site during interpretation process and delete bad frequencies. Below are some suggestions for frequency selection.∙Coherency: It is recommended to delete the frequencies which coherency is below 0.6.∙Skew: Theoretically speaking, skew is a measure of the three dimensionality of the resistivity distribution near the site. But the noise in data will also make it big. When the skew of one frequency is much bigger than that of the rest, it is possible to be caused by noise and need to be deleted.∙Smoothness: Apparent resistivity and impedance should be smooth and continuous for high quality data. The outliers should be deleted before interpretation.To select frequencies this way, you need check Edit button on the toolbar first, then click left and right buttons of mouse to enable or disable frequencies XY and YX mode data respectively.5.Profile DefinitionIn order to display cross section, calculate static shift correction reference and prepare data for 2D inversion, you need define profile first. There are two methods to define profile in EMAGE-2D.(1)Define Profile in Data Selection DialogSelect beginning and ending site of the profile in Starting Site and Ending Site respectively in Data Selection dialog (figure 2.12), then click OK to complete profile definition. After that, a black line will be plotted in Site Location Map to indicate the orientation of the profile.(2)Define Profile in Site Location MapCheck Edit button in the toolbar and hold down Ctrl key in your computer keyboard, then click at the starting position of the profile on the map andmove mouse cursor while keeping left button of the mouse down. When the cursor has been moved to the ending position of the profile you hope to put, release mouse button to finish profile definition.6.Impedance RotationThe impedance of XY and YX mode will be same if the geology is one-dimensional. For non-1D geology, the data of XY and YX mode will be different. The impedance tensor can be rotated mathematically to any other orthogonal axis orientation. If the geology is truly two-dimensional this rotation will reach an angle such that auxiliary impedance become zero and the principal impedance becomes the principal impedance. This angle yields the impedance strike once it has been determined which of the XY or YX components reflects the impedance for the electrical field which is parallel to the strike. When we can rotate impedance so that X direction is perpendicular to the strike of the structure. The XY and YX components are defined as TM and TE mode respectively. If we undertake 1-D interpretation, it is better use the data of TE mode because 1-D inversion result of TE data is closer to the real geology than that of TM data. For 2-D inversion, usually it is best to use the combination of TE and TM data. If you choose one direction of data to do 2-D interpretation, it is widely argued that in 2-D model the goal should to match the TM curve, as it has higher lateral resolution and is less affected by 3-D distortions then the TE mode.There are five types of rotation implemented in EMAGE-2D(1)Analytic RotationImpedance can be rotated to principal axes, which is a related but different concept from the strike of structure, by analytic rotation. In two-dimensional geology, both strike and tip of structure are principal axes. Interpreter should refer to the geology and other kind information to determine if impedance is rotated to strike or tip.(2)Zxy Maximum RotationRotate impedance to one of two principal axes so that the apparent resistivities of X direction (ρx y) are always greater than those of Y direction (ρy x).。
输送机产品样本

DTⅡ型固定式带式输送机
DTII 型带式输送机整体结构见下图,主要部件如下:输送带,驱动装置(电机、减速机、液力 偶合器、制动器、联轴器、逆止器)或电动滚筒,传动滚筒,改向滚筒,托辊,拉紧装置,清扫器, 卸料器,机架,漏斗,导料槽,安全保护装置等。
5
6
7
4
8
9
10
11
3
1
2
15
14
13
Байду номын сангаас
12
20
19
18 17 16
15 14 13
12 11 10 9 8
5 B
13
19
20
21
22
B1
1、传动滚筒 5、槽型托辊 9、改向滚筒 13、下托辊 17、头架 21、卸料车
2、头罩 6、缓冲托辊 10、尾架 14、中间架 18、弹簧清扫器 22、车式拉紧装置
3、输送带 7、导料槽 11、空段清扫器 15、中间支腿 19、垂直拉紧装置
不能单侧卸料。 二、DT75 型重型卸料车:适用于输送容重为 2.5t/m3 的物料。
带宽 B(mm) 托辊间距 T(mm)
轮距 P(mm) 轨距 F(mm) 外形长 L(mm)
图号
1000 1100 3500 1540 8015 DT4F7-II(III)
1200 1100 3500 1840 8664 DT5F7-II(III)
输送设备产品样本
编制日期:2008 年 5 月
DT75 型通用带式输送机
一、 用途 DT75 型通用固定式带式输送机(以下简称 DT75 型)具有输送量大、
结构简单、维护方便、成本低、通用性强等优点,广泛应用在冶金、煤炭、 交通、水电等部门,用来输送散状物料或成件物品。根椐输送工艺的要求, 可以单机输送,也可以多台或与其它输送机组成水平或倾斜的输送系统。 二、 技术特征和主要参数
德马输送辊筒产品选用手册-详细版样本2012 V2

德马输送辊筒产品选用手册-详细版样本2012 V21.引言在德马输送辊筒产品选用手册中,我们将提供详细的产品选用指导。
本手册旨在帮助用户了解德马输送辊筒产品的特点和适用范围,以便更好地根据工程需求进行选择。
2.产品概述2.1 产品分类本章节将介绍德马输送辊筒产品的分类,包括驱动辊筒和非驱动辊筒、重载辊筒和轻载辊筒、防尘辊筒和防水辊筒等。
2.2 产品特点与性能本章节将详细介绍德马输送辊筒产品的特点和性能,包括承载能力、转动阻力、运行平稳性等关键指标。
3.选择指南3.1 工程背景本章节将介绍进行辊筒选用时应考虑的工程背景信息,包括输送物料特性、环境条件、工作方式等。
3.2 选用步骤本章节将提供德马输送辊筒产品的选用步骤和依据,包括确定工作负荷、计算辊筒数量和间距、选择适配器和安装方式等。
4.产品型录在本章节中,我们将提供德马输送辊筒产品的完整型录,包括各类辊筒的规格尺寸、技术参数、适用范围等详细信息,以供用户参考。
5.安装与维护本章节将提供德马输送辊筒产品的安装和维护指南,包括安装步骤、注意事项、维护周期等,以确保产品的正常使用和延长使用寿命。
6.附件在本文档的附录部分,将提供相关附件,包括德马输送辊筒产品的技术图纸、安装示意图、维护记录表等,以供用户参考和使用。
7.法律名词及注释7.1 法律名词本章节将本文档中涉及的法律名词,并提供相应的解释和定义,以确保对相关法律概念的准确理解。
7.2 注释本章节将提供本文档中涉及的其他重要名词和概念的注释和解释,以帮助读者更好地理解和使用本文档。
【文档结尾】本文档涉及附件:1.德马输送辊筒产品型录2.德马输送辊筒技术图纸3.德马输送辊筒安装示意图4.德马输送辊筒维护记录表本文所涉及的法律名词及注释:1.法律名词:定义和解释清楚在文档中涉及的法律术语。
2.注释:提供其他名词和概念的注释和解释,以帮助读者更好地理解文档内容。
2x150-700(32MJ)说明书071206

MG2×150/700–WD型交流电牵引采煤机说明书鸡西煤矿机械有限公司2007年10月MG2×150/700-WD 型交流电牵引采煤机鸡西煤矿机械有限公司1M G 2×150/700-W D 型电牵引采煤机三维数字样MG2×150/700-WD 型交流电牵引采煤机鸡西煤矿机械有限公司2前 言为了方便用户使用采煤机,确保对采煤机的正确操作、安全使用和维修保养,延长采煤机使用寿命,提高采煤机生产效率,我们编制了这本采煤机使用说明书。
说明书重点对MG2×150/700-WD 型采煤机的适用范围、结构特点、工作原理和维护保养做了较为详尽的介绍和说明。
希望用户在使用该采煤机前要认真阅读说明书,掌握工作原理和使用方法,并根据本单位实际情况,制定相应的采煤机使用、维护、保养岗位责任制。
因为采煤机使用范围不断扩展,以及随着科学技术的发展,本产品局部结构和外购配套件等,也需不断采用新材料和新技术,在不影响整体和主要件互换性的情况下,也有相应的持续改进;所以本说明书只限于采煤机的使用说明,供用户参考,不能作为订购采煤机备件的依据。
要掌握采煤机的详尽结构或采购备件,请参阅该采煤机的随机出厂图册。
本说明书的编制得到了有关用户的关心和支持,实际使用中还可能存在一些问题和不足,欢迎广大用户给予批评和指正。
鸡西煤矿机械有限2007年5月16日MG2×150/700-WD 型交流电牵引采煤机鸡西煤矿机械有限公司3目 录第一章概 述 (4)第一节 概述..............................................................................4 第二节 整机组成及工作原理.........................................................4 第三节 主要技术参数及配套设备...................................................7 第四节 采煤机的主要特点 (13)第二章 牵引部 ……………………………………………………………………15 第三章 截割部 ……………………………………………………………………22 第四章调高液压传动系统 (32)第五章 冷却喷雾系统 ..................................................................39 第六章 采煤机电控系统及其工作原理 (42)第一节 采煤机电控系统的结构......................................................42 第二节 系统的特点.....................................................................44 第三节 系统组成及功能...............................................................45 第四节 采煤机电气操作...............................................................47 第五节 电控系统的工作原理.........................................................49 第六节 采煤机的操作及维护.........................................................51 第七节 电控系统部件及组件明细表................................................53 第八节 采煤机电气图 (54)第七章 辅助系统………………………………………………………………… 59 第八章采煤机的使用与维护 (61)第一节 采煤机的井上检查与试运转…………………………………………61 第二节 采煤机的操作…………………………………………………………61 第三节 采煤机的注油…………………………………………………………63 第四节采煤机的维护 (65)附录一安标配套件明细............................................................... ...67 售后服务 .................................................................................... (68)MG2×150/700-WD 型交流电牵引采煤机鸡西煤矿机械有限公司4第一章 概述第一节 概述MG2×150/700-WD 型交流电牵引采煤机是采用多电机驱动、横向布置,用以开采较薄煤层的无链电牵引采煤机,机面高度低,装机功率大,具备截割硬煤、夹矸和爬坡的能力和过断层能力。
Vulcan-Hart VHD系列重型食品保温运输柜安装与使用手册说明书

INSTALLATION &OPERATION MANUAL VHD SERIESHEAVY DUTYHOLDING & TRANSPORTATION CABINETSMODELS:VHD8 ML-138090VHD15ML-138091IMPORTANT FOR YOUR SAFETYTHIS MANUAL HAS BEEN PREPARED FOR PERSONNEL QUALIFIED TO INSTALL ELECTRICAL EQUIPMENT, WHO SHOULD PERFORM THE INITIAL FIELD START-UP AND ADJUSTMENTS OF THE EQUIPMENT COVERED BY THIS MANUAL.FOR YOUR SAFETYDO NOT STORE OR USE GASOLINE OR OTHERFLAMMABLE VAPORS OR LIQUIDS IN THEVICINITYOF THIS OR ANY OTHER APPLIANCE.Improper installation, adjustment,alteration, service, or maintenance cancause property damage, injury, or death.Read the installation, operating andmaintenance instructions thoroughlybefore installing or servicing equipment.IN THE EVENT OF A POWER FAILURE,DO NOT ATTEMPT TO OPERATE THIS DEVICETABLE OF CONTENTSIMPORTANT FOR YOUR SAFETY . . . . . . . . . . . . . . . . . . . . . . . . . . . . . . . . . . . . . . . . 1 GENERAL . . . . . . . . . . . . . . . . . . . . . . . . . . . . . . . . . . . . . . . . . . . . . . . . . . . . . . . . . . . 3 INTRODUCTION . . . . . . . . . . . . . . . . . . . . . . . . . . . . . . . . . . . . . . . . . . . . . . . . . 3 INSTALLATION . . . . . . . . . . . . . . . . . . . . . . . . . . . . . . . . . . . . . . . . . . . . . . . . . . 3 ELECTRICAL REQUIREMENTS . . . . . . . . . . . . . . . . . . . . . . . . . . . . . . . . . . . . . 4 OPERATION . . . . . . . . . . . . . . . . . . . . . . . . . . . . . . . . . . . . . . . . . . . . . . . . . . . . . . . . . 5 CONTROLS . . . . . . . . . . . . . . . . . . . . . . . . . . . . . . . . . . . . . . . . . . . . . . . . . . . . . 5 OPERATING INSTRUCTIONS . . . . . . . . . . . . . . . . . . . . . . . . . . . . . . . . . . . . . . 6 SHUTDOWN . . . . . . . . . . . . . . . . . . . . . . . . . . . . . . . . . . . . . . . . . . . . 6 CLEANING . . . . . . . . . . . . . . . . . . . . . . . . . . . . . . . . . . . . . . . . . . . . . . . . . . . . . . 7 STAINLESS STEEL CARE . . . . . . . . . . . . . . . . . . . . . . . . . . . . . . . . . . . . . . . . . 7 MAINTENANCE . . . . . . . . . . . . . . . . . . . . . . . . . . . . . . . . . . . . . . . . . . . . . . . . . . 8 TROUBLESHOOTING . . . . . . . . . . . . . . . . . . . . . . . . . . . . . . . . . . . . . . . . . . . . . . . . . . 9 SERVICE & PARTS INFORMATION . . . . . . . . . . . . . . . . . . . . . . . . . . . . . . . . . . . . . . . 9 SPECIFICATIONS . . . . . . . . . . . . . . . . . . . . . . . . . . . . . . . . . . . . . . . . . . . . . . . . . . . . 10 PAN CAPACITY . . . . . . . . . . . . . . . . . . . . . . . . . . . . . . . . . . . . . . . . . . . . . . . . . 10 WIRING DIAGRAM . . . . . . . . . . . . . . . . . . . . . . . . . . . . . . . . . . . . . . . . . . . . . . . . . . . 11 WARRANTY . . . . . . . . . . . . . . . . . . . . . . . . . . . . . . . . . . . . . . . . . . . . . . . . . . . . . . . . . 12GENERALVulcan-Hart Holding & Transport Cabinets are produced with quality workmanship and material. Proper installation, usage, and maintenance of your cabinet will result in many years of satisfactory performance.It is suggested that you thoroughly read this entire manual and carefully follow all of the instructions provided.The VHD Series Holding & Transport Cabinets are “Heavy Duty” and designed for tough transportationoperations. Before installing, verify that the electrical service agrees with the specifications on the rating plate located on the lower back corner of the cabinet. (Fig.1) If the supply and equipment requirements do not agree, do not proceed with unpacking and installation. Contact your Vulcan-Hart Customer Service Department immediately.UNPACKING:The Cabinet was inspected before leaving the factory. The transportation company assumes full responsibility for safe delivery upon acceptance of the shipment. Immediately after unpacking, check for possible shipping damage to the cabinet.If the cabinet is found to be damaged, save the packaging material andcontact the carrier within 15 days of delivery.Carefully unpack and place in a work accessible area as near the installation position as possible. 1. Open the door and carefully remove any packaging materials. 2. Peel off vinyl protection film. 3. Remove adjustable tray slides from bottom of cabinet. 4. Install tray slides in the cabinet. Make sure the hook on the end of the tray slide is up.CLEANING:The cabinet should be thoroughly cleaned prior to putting into service.Use a mild soap and water solution to clean the interior of the unit. Never use harsh chemicals or abrasive pads to clean the unit. Refer to cleaning instructions in this manual.LOCATION:For efficient cabinet operation, choose a location that will provide easy loading and unloading without interfering with the final assembly of food orders.The installation location must allow adequate clearances for servicing and proper operation.ELECTRICAL CODES & STANDARDS:The cabinet must be installed in accordance with:In the United States of America:1. State and Local Codes.2. National Electrical Code, ANSI/NFPA-70 (latest edition.) Copiesmay be obtained from: TheNational Fire ProtectionAssociation, 1Batterymarch Park,Quincy, MA 02269.1-617-770-3000 In Canada:1. Local Codes.2. Canadian Electrical Code, CSAC22.1 (latest edition.) Copiesmay be obtained from: TheCanadian Standard Association.www.csa.caELECTRICAL CONNECTIONS:The cabinet is factory wired for 120 volt single phase operation. The cabinet is equipped with an 8 foot cord and a NEMA 5-15 plug as standard equipment. Refer to wiring diagrams inthe back of this manual.The cord and plug supplied is a suitable durable cord with a molded three-prong plug, and is provided with a heavy-duty strain relief.All cabinets are equipped with a three-prong plug. Itis imperative that this plug must be connected into a properly grounded three-prong receptacle. If the receptacle is not the proper grounding type, contact an electrician. Do not remove the grounding prong from this plug.Verify that the power source matches the Serial Data Plate located on the lower back corner of the cabinet and the plug configuration before the connection is made. (Fig.1)SERIAL DATA PLATE(Fig.1)OPERATIONThe Cabinet and its partsare hot. Be very careful when operating, cleaning, or servicing the cabinet.ON / OFF POWER FULL-RANGEHEAT INDICATOR LIGHTPower Indicator Light:The Red Power Indicator Light indicates the cabinet is plugged in.Heat Indicator Light:The Amber Heat Indicator Light indicates the heating element(s) are heating. The amber light will stay lit as long as the heating element(s) are engaged. Once the predetermined temperature is achieved, the heating element(s) will begin to cycle. During this period, the amber light will turn on and off.ON / OFF Switch:The ON / OFF Switch turns on the cabinet. The cabinet will not operate unless the switch is in the ON position.Thermometer:The Thermometer indicates the interior temperature of the cabinet.Thermostat:The Thermostat turns power on to the heating element(s). The thermostat setting is from 1 to 10. The greater the thermostat setting number, the higher the temperature. (Fig. 2)Fig. 2It is recommended that prior to placing the cabinet in operation, that it be preheated at the highest temperature setting for a period of 30 to 45 minutes .The Cabinet and its parts are hot. Be very careful when operating, cleaning, or servicing the cabinet.Once the cabinet has been connected to the appropriate power source, the cabinet is ready for operation.1. Switch the ON/OFF Switch to On.2. Turn the thermostat dial to thenumber 5. This will cause theheating element to start heating.Once the red light is lit, thethermostat dial can be turned tothe desired setting. (Fig.2)3. Wait approximately 25 minutesfor the cabinet to preheat.4. Load hot food pans with hotcooked food into cabinet.This cabinet is not intended to reheat or cook food. Food must be cooked and at a safe serving temperature prior to being placed in the cabinet.The operator should always monitor the food product to insure that it remains at a proper temperature.The Cabinet and its parts are hot. Be very careful when operating, cleaning, or servicing the cabinet.1. Turn the thermostat to the Offposition.2. Switch the ON/OFF switch to theoff position. 3. Allow cabinet to cool downcompletely.4. Unplug power cord.5. Clean cabinet according toinstructions in this manual.The Cabinet and its parts are hot. Be very careful when operating, cleaning, or servicing the cabinet.Always unplug electrical power supply before cleaning.DAILY:1. Unplug electrical power supply.2. Allow warmer to cool beforecleaning.3. Clean the interior of the cabinetwith a mild soap and water.Never use harsh chemicals orabrasive pads to clean the cabinet. 4. Rinse and dry with a soft drycloth.5. Clean the exterior of the cabinetwith a clean damp cloth.HEAVY-DUTY CLEANING:For heavy-duty cleaning, use warm water, a degreaser, and a plastic, stainless steel, or Scotch-Brite pad. Never rub in a circular motion -- rub gently in the direction of the steel grain.Always rinse thoroughly.CLEANING:Stainless Steel contains 70 – 80% iron, which will rust if not properly maintained. Stainless Steel also contains 12 – 30% chromium, which forms an invisible passive, protective film that shields against corrosion. If the protective film remains intact, the stainless steel will remain intact. However, if the film is damaged, the stainless steel can break down and rust. PREVENTIVE CARE:To prevent stainless steel break-down, follow these steps:1. Never use any metal tools,scrapers, files, wire brushes,or scouring pads (except forstainless steel scouring pads,)which will mar the surface.2. Never use steel wool– whichwill leave behind particles that willrust.3. Never use acid-based orchloride containing cleaningsolutions – which will breakdown the protective film.4. Never rub in a circular motion.Always rub gently in the directionof the steel grain.5. Never leave any food productsor salt on the surface. Manyfoods are acidic. Salt containschloride.PRESERVING & RESTORING:Special stainless steel polishing cleaners can preserve and restore the protective film.Preserve the life of stainless steel with a regular application of a high-quality stainless steel polishing cleaner, as a final step to daily cleaning.If signs of breakdown appear, restore the stainless steel surface. First, thoroughly clean, rinse, and dry the surface. Then, on a daily basis, apply a high-quality stainless steel polish according to manufacturer’s instructions.HEAT TINT:Darkened areas, called “heat tint,” may appear on stainless steel exposed to excessive heat. Excessive heat causes the protective film to thicken. This is unsightly, but is not a sign of permanent damage.To remove heat tint, follow the routine cleaning procedure. Stubborn heat tint will require heavy-duty cleaning.To reduce heat tint, limit the exposure of equipment to excessive heat. The Cabinet and itsparts are HOT . Be very careful when operating, cleaning, or servicing the cabinet.Always unplugelectrical power supply before cleaning or servicing the cabinet.TROUBLESHOOTINGTo obtain Service and Parts information concerning this model, contact Vulcan-Hart Service Department at the address listed on the front cover of this manual or refer to our website: for a complete listing of Authorized Service and Parts depots.Customer Service 1-800-814-2028Technical Service 1-800-814-2028Service Parts 1-800-814-2028When calling for service, have the model number and serial number available.Vulcan VHD Series heavy duty transport cabinets are designed for the toughest transportation operations. The blower motor distributes a gentle and even temperature throughout the cabinet. The cabinet is heliarc welded, fully insulated, 20 gauge stainless steel double pan construction with support channels welded at base, with integral dual layer fully welded corner posts (all four corners.) It has a full perimeter bumper and 5” super duty polyurethane casters (2 swivel with brakes and 2 rigid.) 12 gauge hinges are welded to both the cabinet frame and door and 12 gauge lockable transport latches, magnetic closures, and welded push/pull handles. Recessed control panel features dual indicator lights, a thermometer, and a full range thermostat for temperatures up to 190⁰F (88⁰C). Holding and Transport Capacity: VHD88 ea. 18”x26” sheet pans16 ea. 12”x20”x2½” pansOr a combination of both on 1½” centers.4 pairs of universal tray slides includedVHD1515 ea. 18”x26” sheet pans30 ea. 12”x20”x2½” pansOr a combination of both on 1½” centers.12 pairs of universal tray slides includedWIRE DIAGRAM。
Miller Feeder Drive Roll Kits 及 Wire Guide 说明书
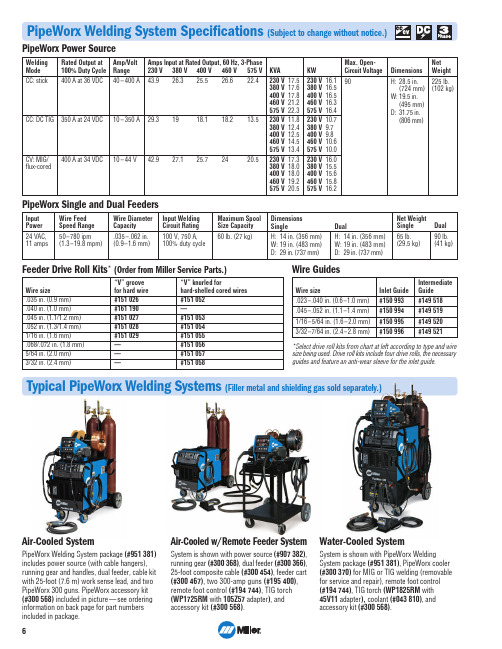
Feeder Drive Roll Kits *(Order from Miller Service Parts.)6“V” groove “V” knurled forWire size for hard wire hard-shelled cored wires .035 in. (0.9 mm) #151 026 #151 052.040 in. (1.0 mm) #161 190 —.045 in. (1.1/1.2 mm) #151 027 #151 053.052 in. (1.3/1.4 mm) #151 028 #151 0541/16 in. (1.6 mm) #151 029 #151 055.068/.072 in. (1.8 mm) — #151 0565/64 in. (2.0 mm) — #151 0573/32 in. (2.4 mm) — #151 058*Select drive roll kits from chart at left according to type and wire size being used. Drive roll kits include four drive rolls, the necessary guides and feature an anti-wear sleeve for the inlet guide.Intermediate Wire size Inlet Guide Guide .023–.040 in. (0.6–1.0 mm) #150 993 #149 518.045–.052 in. (1.1–1.4 mm) #150 994 #149 5191/16–5/64 in. (1.6–2.0 mm) #150 995 #149 5203/32–7/64 in. (2.4–2.8 mm) #150 996 #149 521Wire GuidesPipeWorx Single and Dual FeedersPipeWorx Power SourceTypical PipeWorx Welding Systems (Filler metal and shielding gas sold separately.)Air-Cooled w/Remote Feeder SystemSystem is shown with power source (#907 382),running gear (#300 368), dual feeder (#300 366),25-foot composite cable (#300 454), feeder cart (#300 467), two 300-amp guns (#195 400),remote foot control (#194 744), TIG torch (WP1725RM with 105Z57adapter ), and accessory kit (#300 568).Water-Cooled SystemSystem is shown with PipeWorx Welding System package (#951 381), PipeWorx cooler (#300 370)for MIG or TIG welding (removable for service and repair), remote foot control (#194 744), TIG torch (WP1825RM with 45V11adapter ),coolant (#043 810), and accessory kit (#300 568).Air-Cooled SystemPipeWorx Welding System package (#951 381)includes power source (with cable hangers),running gear and handles, dual feeder, cable kit with 25-foot (7.6 m) work sense lead, and two PipeWorx 300 guns. PipeWorx accessory kit (#300 568)included in picture —see ordering information on back page for part numbers included in package.。