热模锻工艺及模具设计
第十二章 压力机模锻工艺及模具设计

(2)锻件图的制订 确定锻件图的原则和内容与锤上模锻相同,不同点如下: 1)热模锻压力机有顶出装置,锻件能方便地从深型腔内取出,分模面可 以灵活地选择。 2)锻件拔模斜度一般比锤上模锻件小一级。外斜度为3°~7°,内斜度 为7°~10°,或视孔的相对深度而定。当h>0.75d时,采用两级拔模 斜度。
5)飞边槽的型式与锤上模锻相似,不同之处在于 仓部是开通的。如图12-4
图12-4 飞边槽的形式 a) 用于形状较复杂锻件 b)用于形状较简单锻件
(2)预锻工步设计:预锻工步设计原则与锤上模锻相似。设计时应着 重考虑以下几点:
1)预锻工步图的高度尺寸相应要比终锻大2~5mm,宽度尺寸比 终锻要小0.5~1mm,对高筋和凸出部分,取较大差值。
之比大于1.6~2时,应增加压扁工步。 (2)对断面有一定变化的锻件:断面变化不超过10%~15%时,采用压
肩~终锻或压肩~预锻~终锻。 (3)对截面变化大的锻件:采用其它设备制坯(辊锻、平锻、楔横轧、
空气锤等)或采用成型毛坯。 (4)对弯曲类锻件,是否需要采用弯曲工步与锤上模锻相同。 在热模锻压力机上模锻质量和尺寸较小的锻件时,可以采用多件模锻。
图12-18 整体式模锻
组合式锻模或镶块锻模结构,便于实现模具零件的标准化,中小批 量的生产多用此种形式。
图12-19 镶块式锻模
图12-20 用楔紧固模块
摩擦压力机上模锻,上下模的导向方式见图12-21、图12-22。
图12-21用导销导向
图12-22 凸凹模导向的结构型式 a) 圆柱面导向 b) 圆锥面导向 c) 喇叭形导向
(1)终锻工步设计:根据热锻件图设计的。与锤 上模锻相似,不同之处有以下几点:
1)上下模充满的难易程度差别不大,应考虑锻件 的定位和取出方便。
锻造工艺与模具设计-模锻成形工序分析

● 金属充满模膛后,多余金属由桥口流出,此 为第Ⅲ阶段。
13
一、开式模锻变形过程
●
第Ⅰ阶段:由开始模压到金属与模具侧壁接触为止
14
一、开式模锻变形过程
●
第Ⅱ阶段:第Ⅰ阶段结束到金属充满模膛为止
15
一、开式模锻变形过程
●
第Ⅲ阶段:金属充满模膛后,多余金属由桥口流出
16
二、开式模锻各阶段的应力应变分析
32
小飞边模锻
对某些形状的锻件,在模锻最后阶段,变形区集中 分布在分模面附近,远离分模面的部分不容易充满。
33
楔形飞边槽
主要依靠桥口斜面产生的水平分力阻止金属外 流,飞边部分金属消耗减少一倍;这种飞边与锻件 连接处较厚,切边较困难
34
扩张型飞边槽
在模锻的第一第二阶段,桥口部分对金属外流有一定阻力作用;而最 后阶段,对多余金属的外流无阻碍作用,可以较大程度的减小变形力,使 上下模压靠。
42
18
二、开式模锻各阶段的应力应变分析
●
第Ⅱ阶段
19
二、开式模锻各阶段的应力应变分析
第Ⅲ阶段: 主要是将多余金属排入飞边。此时流动界面已不存 在,变形仅发生在分模面附近的一个区域内,其它部位 则处于弹性状态;多于金属由桥口流出时阻力很大,使 变形抗力急剧增大
●
20
二、开式模锻各阶段的应力应变分析
6
控制金属的流动方向
各质点向着阻力最小方向移动, 因此依靠不同的工具,采取不同的加载方式在变形 体内建立不同的应力场实现对金属流动物体内方向的控 制
7
控制塑性变形区
主要靠利用不同工具在坯料内产生不同的应力状态, 使部分金属满足屈服准则,另一部分金属不满足屈服准 则,达到控制变形区的目的
锻造工艺过程及模具设计

锻造工艺过程及模具设计1. 引言锻造是一种通过对金属材料施加压力,使其产生塑性变形,从而得到所需形状和性能的工艺方法。
锻造工艺及模具设计在制造业中具有广泛的应用。
本文将介绍锻造的工艺过程和模具设计的基本原理和方法。
2. 锻造工艺过程2.1 热锻工艺热锻是指在高温下进行的锻造工艺。
其基本过程包括预热、装料、锻造和冷却四个步骤。
2.1.1 预热预热是将锻造原料加热至一定温度,以提高其塑性和降低锻造压力。
预热温度的选择取决于材料的类型和要求。
2.1.2 装料装料是将预热好的原料放置在锻造模具上,以准备进行下一步的锻造操作。
装料时需要考虑材料的定位和固定,确保锻造过程中的准确性和一致性。
2.1.3 锻造锻造是通过对装料施加压力,使其发生塑性变形,从而得到所需形状和性能的过程。
在锻造过程中,需要控制加压力、防止材料裂纹和变形等问题。
2.1.4 冷却冷却是将锻件从锻造中取出后,使其慢慢冷却,以缓解残余应力和提高材料的硬度和强度。
2.2 冷锻工艺冷锻是指在室温下进行的锻造工艺。
与热锻相比,冷锻可以更好地控制材料的性能和形状,并且不需要进行预热和冷却,节约能源。
2.2.1 材料的选择冷锻对材料的要求较高,一般选用具有良好塑性和变形能力的材料,如铝、铜等。
2.2.2 模具的设计冷锻模具的设计需要考虑以下几个方面:模具材料的选择、模具结构的设计、模具的可制造性和可维修性等。
3. 模具设计3.1 模具的分类模具按照其所用材料的不同可以分为金属模具、木模具和塑料模具等。
其中金属模具是最常用的一种,具有强度高、耐磨性好的特点。
3.2 模具结构的设计模具的结构设计包括上模、下模和侧模的设计。
上模是与锻件上表面接触的模具,下模是与锻件下表面接触的模具,侧模用于锻造中需要有孔的部位。
3.3 模具材料的选择模具材料的选择需要考虑模具的使用寿命、成本和性能要求等。
常用的模具材料有工具钢、合金钢和铸铁等。
3.4 模具的制造工艺模具制造工艺包括模具的加工和装配过程。
热锻模具工艺及其要点

热锻模具加工工艺及其要点1:下料根据生产指令按规定材料及尺寸下料。
要点:检查原材料1)外表应无压伤、疤痕、深度划伤、夹皮等缺陷。
2)内部应无裂纹、皮下气泡、夹层等缺陷。
2:自由锻根据生产指令按规定尺寸锻造。
要点:1)加热:快速加热,但应烧透且应加热温度均匀;加热中翻动2~3次;工件间隙≥原始圆形毛坯直径d(或原始方形毛坯边长a);加热时间按d(或a)min,注:d为原始圆形毛坯直径(a为原始方形毛坯边长),即每1㎜加热1min;避免与不同材料的毛坯同炉加热。
2)火次:五火十锻。
3)温度:加热温度:1120~1150。
始锻温度:1070~1100℃。
终锻温度:850~900℃。
4)打击力度:始锻开锤轻击以清除加热氧化皮,确保成形后锻坯有良好的表面质量;拔长或镦粗时均匀进给,锤击轻重一致,避免温共5页第1页度过低时猛烈锻打或进行大变形量锻击而产生裂纹。
成形锻坯结束锻造时终锻温度可取终锻温度下限或更低一些,但只限于最后锻坯的修整、校形,以轻击为主,低温下,碳化物较脆、易碎,在许用终锻温度下,锻打有益,但操作危险应注意安全。
5)锻造比以大于2的锻造比进行变向反复镦拔。
6)冷却成型锻坯堆放冷却时,保证地面干净整洁,严禁在潮湿的地面上放置。
7)加工余量成型锻坯应保证端面单边有效加工余量3㎜,径向单边有效加工余量5㎜。
3:退火采用完全退火,用以消除应力,降低硬度,改善切削加工性能。
温度:840~860℃。
保温时间:2~3小时。
缓慢冷却至500℃以下时出炉,空冷至室温。
确保硬度:≤HB2294:车加工(粗车)根据图纸按规定尺寸加工。
要点:1)各部加工余量不应低于1.0~1.5㎜。
2)加工外表面粗糙度在Ra3.2以内,内表面粗糙度在Ra3.2 以内。
3)粗车毛坯不允许有尖角,尖角处在保证加工余量的前体下均以R3~6过渡。
5:铣削及标识按规定铣标识平面,表面粗糙度不应低于Ra3.2。
标识应清晰可辨,保证配模后能够完全保留标识字迹。
锻模设计(含实例)

继续压缩至上下模接触即打靠。
变形仅发生在分模面附近的区域内
,处于最强的三向压应力状态,变
形抗力也最大。此阶段的H 压下量小
16
于2mm,它消耗的能量却占总能量
H
17
二、终锻模膛设计
1、模膛尺寸计算
热锻件图依据冷锻件图绘制。
热锻件图上尺寸比冷锻件图
中尺寸加大一个收缩率,
即 Ll(1%)
式中:δ—终锻温度下的
主要内容是绘制热锻件图和确定飞 边槽形式与尺寸。
边槽主要起排泄和容纳多余金属
作用。
充填模膛的阻力作用相对次要。
锻件高度由压机行程保证。上下分 模面间保留一定间隙,不发生碰撞 。
间ቤተ መጻሕፍቲ ባይዱ大小根据飞边槽高度而定。
H
47
2)预锻工步设计
预锻工步图根据终锻工步图设计。总的原则是使预锻后
的坯料尽可能以镦粗方式进行。
dmin —计算毛坯的最小直径; d拐 —杆部与头部交接处的直径:
说明:
d拐1.13h拐M
α 值越大,流向头部的金属体积越多;
β 值越大,金属沿轴向流动的距离越长;
K 值越大,表明杆部锥度大,小头和杆部金属过剩;
G 值越大,制坯难度加大。
H
36
(4) 根据繁重系数确定制坯工序的初步 方案
长轴类锻件可根据计 算出的繁重系数在右示 经验图表中查出制坯工 序的初步方案,再依据 生产试验修改确定。
H
43
东风汽车公司锻造厂用的热模锻压力机吨 位主要有1200、800、400、200MN(1MN =106 N)等。
2、平锻机吨位 经验公式:
F = 57.5kA,kN 。
式中
k —材料系数。 取 k = 1.0~1.3;
热锻工艺与模锻设计四弯曲型腔的设计ppt实用版
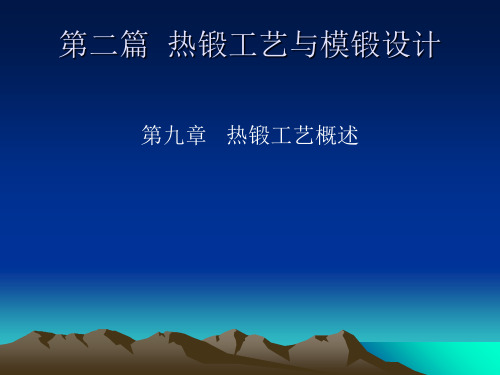
温度可高达1350 ℃以上。
• 优点:对毛坯加热的适应范围较大,便于实现加热机械化 自动化,也可用保护气体进行少无氧化加热。
• 缺点:加热温度受到电热体的限制,热效率比其他电加热 法低。
三、钢在加热中的常见缺陷
• 1、氧化:钢料加热到高温时,其表层中的Fe元素与氧化性 气 体 (O2 、 CO2 、 H20 、 SO2) 发 生 化 学 反 应 , 使 钢 坯 表 层 形成氧化皮的现象称为氧化(或烧损)。
2、终锻型腔与预锻型腔的排列
否则,塑性显著降低,变形抗力增大,加工硬化现象严重,容易产生锻造裂纹。
在锻压生产中,以中频感应电加热应用最多。 镶块底面距型腔最深处厚度s应不小于(0.
3、确定模锻所需工步,进行工步设计和型腔设计,其顺序
是:先设计终锻型腔,然后设计预锻型腔和制坯型腔;
优点:加热速度快,加热质量好,温度控制准确,金属烧损少。 当进料比Ln-1/an-1 小时, 大,即在同样的相对压缩程度
3、目前我国锻造行业的任务
• ⑴、提高大型锻件与合金钢锻件的质量和锻造生产的 模锻工序在锻件成形过程中不是最后工序:
挤压成形时,坯料在三向压应力作用下产生一向伸长双向压缩变形。
机械化与自动化程度; ②、裂纹:低塑性材料开式冲孔时常易在侧表面和内孔园角处产生纵向裂纹。
锻造工艺过程及模具设计

锻造工艺过程及模具设计锻造是一种通过对金属材料进行加热和塑性变形来制造零件的工艺。
它广泛应用于航空航天、汽车制造、机械制造等领域。
锻造工艺过程中,模具设计起着至关重要的作用。
本文将介绍锻造工艺的基本过程,并探讨模具设计的要点和技巧。
一、锻造工艺过程锻造工艺过程通常包括以下几个步骤:材料准备、加热、装料、锻造、冷却和后处理。
1. 材料准备:选择合适的金属材料是成功进行锻造的关键。
常用的锻造材料有碳钢、不锈钢、铜合金等。
在材料准备阶段,需要对材料进行清洁和切割,以便于后续的加工操作。
2. 加热:将金属材料加热至适当的温度,使其达到塑性变形的状态。
不同的金属材料需要加热到不同的温度范围,以确保其具有足够的可塑性。
3. 装料:将预热好的金属材料放入模具中。
模具是用来限制和塑性变形金属材料的工具,它的设计和制造直接影响着锻造零件的质量和形状。
4. 锻造:在加热和装料后,施加压力使金属材料发生塑性变形。
锻造可以分为冷锻和热锻两种方式。
冷锻适用于低碳钢等硬度较低的金属材料,热锻适用于高碳钢等硬度较高的金属材料。
5. 冷却:锻造完成后,将锻造件从模具中取出,进行冷却。
冷却的目的是使锻造件快速降温,以增加其强度和硬度。
6. 后处理:锻造件经过冷却后,还需要进行后处理。
后处理可以包括修整、抛光、热处理等工序,以进一步提高锻造件的性能和表面质量。
二、模具设计要点和技巧模具是锻造工艺中不可或缺的工具,其设计和制造直接关系到锻造件的质量和形状。
以下是一些模具设计的要点和技巧:1. 合理选材:模具的材料应具有足够的硬度和耐磨性,以承受锻造过程中的高温和高压。
常用的模具材料有合金工具钢、合金铸钢等。
2. 结构简单:模具的结构应尽可能简单,便于制造和维修。
过于复杂的结构会增加制造难度,降低模具的使用寿命。
3. 合理布局:模具的布局应合理,使得锻造过程中的力分布均匀。
同时,还要考虑模具的强度和刚度,以避免变形和破坏。
4. 充分利用材料:在模具设计中,应尽量减少废料的产生,充分利用材料。
模锻工艺与模具设计实用手册模锻工艺与模具设计实用手册
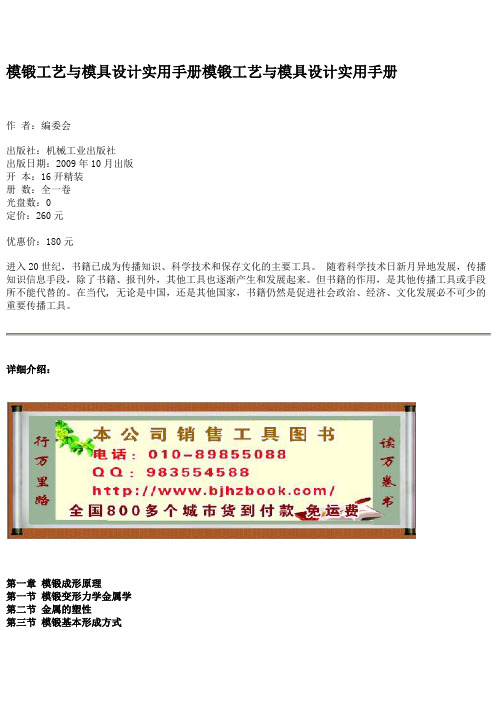
模锻工艺与模具设计实用手册模锻工艺与模具设计实用手册作者:编委会出版社:机械工业出版社出版日期:2009年10月出版开本:16开精装册数:全一卷光盘数:0定价:260元优惠价:180元进入20世纪,书籍已成为传播知识、科学技术和保存文化的主要工具。
随着科学技术日新月异地发展,传播知识信息手段,除了书籍、报刊外,其他工具也逐渐产生和发展起来。
但书籍的作用,是其他传播工具或手段所不能代替的。
在当代, 无论是中国,还是其他国家,书籍仍然是促进社会政治、经济、文化发展必不可少的重要传播工具。
详细介绍:第一章模锻成形原理第一节模锻变形力学金属学第二节金属的塑性第三节模锻基本形成方式第四节模锻变形流动的控制第二章模锻变形前工序第一节模锻原毛坯的制备第二节加热的目的、方法和质量第三节锻造加热规范第四节少无氧化加热第五节火焰加热炉与加热温度测量第三章模锻基本设备第一节锤类模锻设备第二节热模锻压力机第三节平锻机第四节螺旋压力机第五节模锻液压机第四章锤上模锻第一节锤上模锻概述第二节模锻件图设计第三节模锻模膛设计第四节制坯模膛设计第五节原毛坯计算与设备吨位第六节锤锻模结构设计第七节设计实例第五章其它设备上模锻第一节热模压力机上模锻第二节螺旋压力机上模锻第三节平锻机上模锻第六章模锻变形后工序第一节锻件冷却第二节切边和冲孔第三节模锻热处理第四节校正第五节精压第六节表面清理第七节模锻件质量检验第七章特殊金属模锻第一节不透钢的模锻第二节铝台金模锻第三节铜合金模锻第四节钛合金的模锻第五节高温合金的模锻第六节镁合金的模锻第八章特殊模锻第一节精密模锻第二节挤压第三节高速模锻第四节锟压锻第五节模轧第六节环形件辗压第七节径向锻造第八节粉末锻造第九节摆动辗压第十节液态模锻第十一节高温模锻第十二节超塑性模锻第九章模锻生产优化技术第一节模锻机械化与自动化第二节模锻成形过程模拟仿真第三节锻模cAD/CAM技术模锻工艺与模具设计实用手册模锻工艺与模具设计实用手册模锻工艺与模具设计实用手册模锻工艺与模具设计实用手册模锻工艺与模具设计实用手册模锻工艺与模具设计实用手册第一章模锻成形原理第一节模锻变形力学金属学第二节金属的塑性第三节模锻基本形成方式第四节模锻变形流动的控制第二章模锻变形前工序第一节模锻原毛坯的制备第二节加热的目的、方法和质量第三节锻造加热规范第四节少无氧化加热第五节火焰加热炉与加热温度测量第三章模锻基本设备第一节锤类模锻设备第二节热模锻压力机第三节平锻机第四节螺旋压力机第五节模锻液压机第四章锤上模锻第一节锤上模锻概述第二节模锻件图设计第三节模锻模膛设计第四节制坯模膛设计第五节原毛坯计算与设备吨位第六节锤锻模结构设计第七节设计实例第五章其它设备上模锻第一节热模压力机上模锻第二节螺旋压力机上模锻第三节平锻机上模锻第六章模锻变形后工序第一节锻件冷却第二节切边和冲孔第三节模锻热处理第四节校正第五节精压第六节表面清理第七节模锻件质量检验第七章特殊金属模锻第一节不透钢的模锻第二节铝台金模锻第三节铜合金模锻第四节钛合金的模锻第五节高温合金的模锻第六节镁合金的模锻第八章特殊模锻第一节精密模锻第二节挤压第三节高速模锻第四节锟压锻第五节模轧第六节环形件辗压第七节径向锻造第八节粉末锻造第九节摆动辗压第十节液态模锻第十一节高温模锻第十二节超塑性模锻第九章模锻生产优化技术第一节模锻机械化与自动化第二节模锻成形过程模拟仿真第三节锻模cAD/CAM技术作者:编委会出版社:机械工业出版社出版日期:2009年10月出版开本:16开精装册数:全一卷光盘数:0定价:260元优惠价:180元本店订购简单方便,可以选择货到付款、汇款发货、当地自取等方式全国货到付款,满200元免运费,更多请登陆文成图书。
锻造工艺与模具设计-锻前加热、锻后冷却与热处理

第二篇锻造工艺与模具设计锻造:以锭料或棒料为原材料时,称为锻造,在锻造加工中,坯料发生明显的塑性变形,有较大量的塑性流动。
自由锻:只用简单的通用性工具,或在锻造设备的上、下砧间直接使坯料变形而获得所需的几何形状及内部质量锻件的方法。
模锻:利用模具使毛坯变形而获得锻件的锻造方法。
锻压生产过程•锻压的生产过程包括成形前的锻坯下料、锻坯加热;成形;成形后工件的热处理、清理、校正和检验。
法兰生产工艺流程主导产品——大型铸锻件:电站锻件、船用锻件等亚临界汽轮机缸体、超临界缸体、亚临界汽轮机(600MW及600MW以下)高中压转子、中压主轴、超纯转子、高低压联合转子、低压转子、叶轮等火力发电机组(300MW及300MW以下)铸锻件;大型船用铸锻件等。
300MW发电机转子300MW缸体1-1 锻前加热的目的及方法1 目的:提高金属塑性,降低变形抗力,即增加金属的可锻性,从而使金属易于流动成形,并使锻件获得良好的锻后组织和力学性能。
1-1 锻前加热的目的及方法2 方法:金属坯料的加热方法,按所采用的热源不同,可分为:¾燃料加热:¾电加热:[1] 燃料(火焰)加热燃料加热是利用固体(煤、焦炭等)、液体(重油、柴油等)或气体(煤气、天然气等)燃料燃烧时所产生的热量对坯料进行加热。
燃料在燃料炉内燃烧产生高温炉气(火焰),通过炉气对流、炉围(炉墙和炉顶)辐射和炉底传导等传热方式,使金属坯料得到热量而被加热。
在低温(650℃以下)炉中,金属加热主要依靠对流传热,在中温(650~1000℃)和高温(1000℃以上)炉中,金属加热则以辐射方式为主。
在普通高温锻造炉中,辐射传热量可占到总传热量的90%以上。
[1] 燃料(火焰)加热优点:燃料来源广泛,炉子建造容易,加热费用低,对坯料适应范围广等。
缺点:劳动条件差,金属氧化烧损严重,加热质量难以控制等。
目前,该方法仍是锻造加热的主要方法,广泛用于自由锻、模锻时的对各种大、中、小型坯料的加热。
模锻成形工艺及模具设计特点

模锻成形工艺及模具设计特点锻锤的优点在于打击速度快,因而模具接触时间短,适合要求高速变形来填充模具的场合。
由于其快速、灵活的操作特性,其适应性非常强,有人成为“万能”设备,因而特别适用于多品种、小批量的生产。
模锻锤属于力大能小,能量可以累积,强冲击负荷和没有固定下死点的定能设备,锻锤的强冲击负荷和多次锻击成形特点,使金属在高度方向流动和填充良好,特别适用于生产薄平带筋的锻件。
锤锻主要工作特点(1)靠冲击力使金属变形,锤头在行程的最后,速度约4-9m/s(2)受力系统不是封闭的,冲击力通过下砧传给基础(3)单位时间内的打击次数多(1~10t模锻锤为40~100次/min)(4)锤头行程不固定(5)承受偏载能力和导向精度均较差(6)无顶出装置模锻工艺和模具设计特点(1)金属在各模膛中的变形是锤头的打击下逐步完成的,锤头的打击速度虽然快,但在打击中每一次的变形量较小(2)由于考冲击力使金属变形,可以利用金属的流动惯性,有利于金属填充模膛。
锻件上难充满的部分应尽量放在上模(3)在锤上可实现多种模锻工步,特别是对长轴类锻件进行滚压,拔长等制坯工步非常方便(4)由于模锻锤的导向精度不太高,工作时的冲击性质和锤头行程不固定等,因此模锻件的尺寸不太高(5)由于无顶出装置,锻件起模较困难,模锻斜度应适当大些(6)由于冲击力使金属变形,模具一般采用整体结构(7)由于靠冲击力使金属变形和锤头行程速度快,通常才用锁扣装置导向,较少采用导柱导套。
典型的锤模锻经过6个工序①镦粗:用来以减小坯料高度,增大横截面积(图中无镦粗工序)。
②拔长:将坯料绕轴线翻转并沿轴线送进,用来减小坯料局部截面,延长坯料长度。
③滚压:操作时只翻转不送进,可使坯料局部截面聚集增大,并使整个坯料的外表圆浑光滑。
④弯曲:用来改变坯料轴线形状。
⑤预锻:改善锻件成形条件,减少锻模膛的磨损。
⑥终锻:使锻件最终成形,决定锻件的形状和精度。
毕业设计锻造工艺分析与模具设计

毕业设计锻造工艺分析与模具设计引言:锻造是一种常用的金属成形工艺,通过将金属材料加热至一定温度后,施加压力使其发生塑性变形,从而得到有一定形状和性能要求的零件。
锻造工艺及其模具设计对于产品质量和生产效率具有重要影响。
本文将通过对锻造工艺的分析以及模具的设计,来提高锻造工艺的可靠性和效率。
一、锻造工艺分析:1.工件材料选择:锻造材料应具有良好的塑性和延展性,常用的锻造材料有钢、铝合金、铜等。
2.工件形状:锻造可以制造出各种形状的零件,包括轴类零件、板类零件、环件、齿轮等。
根据不同工件形状选择合适的锻造工艺和模具。
3.工艺流程:锻造的工艺流程主要包括预加工、加热、锻造和冷却四个步骤,其中加热和冷却步骤对于工件的质量和机械性能影响较大。
二、模具设计:1.模具材料选择:模具的材料应具有高强度、高硬度和耐磨性,一般选择优质的合金钢或高速钢。
2.模具结构设计:根据工件的形状和要求设计模具的结构,包括模座、上模板、下模板、合模机构等部分。
合理的模具结构能够提高锻造的生产效率和产品质量。
3.模具的制造与使用:模具的制造需要严格按照设计要求进行工艺加工,包括切割、铣削、磨削等工序。
在使用过程中,要注意模具的保养和维护,以延长模具的使用寿命。
三、锻造工艺改进:1.工艺参数调整:通过对锻造工艺参数的优化调整,可以改善工件的质量和机械性能,如锻造温度、锻造速度、锻造压力等。
2.工装夹具设计:合理设计工装夹具能够提高生产效率和工件的一致性,减少工人的劳动强度。
3.自动化生产:采用自动化设备进行锻造,可以减少人力投入,提高生产效率和产品质量。
结论:通过对锻造工艺的分析和模具的设计,可以提高锻造工艺的可靠性和效率,同时改善产品的质量和机械性能。
随着科技的不断进步,锻造工艺将更加高效、精确和自动化。
在实际应用中,我们应根据具体情况进行灵活运用,并不断探索新的锻造工艺和模具设计方法,以满足不断变化的市场需求。
第十二章 压力机模锻工艺及模具设计PPT课件

写在最后
经常不断地学习,你就什么都知道。你知道得越多,你就越有力量 Study Constantly, And You Will Know Everything. The More
You Know, The More Powerful You Will Be
谢谢大家
荣幸这一路,与你同行
图12-7 封闭式毛坯型腔
2)开启式镦粗:在两个平面内进行镦粗,为便于在预锻时定位,在镦粗平面 上做成一定的凹槽。(如图12-8所示)能清除坯料侧面的氧化皮。
一般多采用开启式镦粗。
图12-8 敞开式毛坯模槽
六、确定坯料尺寸
与锤上模锻相同(参照锤上模锻)。
七、锻模结构
(一)模架(夹持器)
模架:是通用的,由上下模板﹑导柱﹑导套、顶出装置、以及安装 (紧固)调整镶块用的零件等组成。 有两种模架形式:
(1)终锻工步设计:根据热锻件图设计的。与锤 上模锻相似,不同之处有以下几点:
1)上下模充满的难易程度差别不大,应考虑锻件 的定位和取出方便。
2)压机在一次行程中充满型腔,在型腔的深处, 需设计排气孔,孔径约为1.2~2mm。
3)压机有顶杆装置,顶杆与金属接触部分起型腔 的作用。
4)直径小于26mm的孔,一般不冲出。需冲孔时, 连皮厚度通常取S=6~8mm。
图12-13镶块中顶出器的配置 a) 顶在飞边上 b) 顶在连皮上 c)采用两个顶出器顶出 d) 顶在锻件本体上
(四)排气孔
1、在终锻型腔中应开有排气孔。 2、孔径:一般φ1.2~φ2mm,孔深为20~30mm,与直径为φ8~20mm的 孔相连直至镶块底部。
3、位置:在金属最后充填的地方。
第二节 摩擦压力机模锻艺及模具设计
热模锻工艺介绍 180813
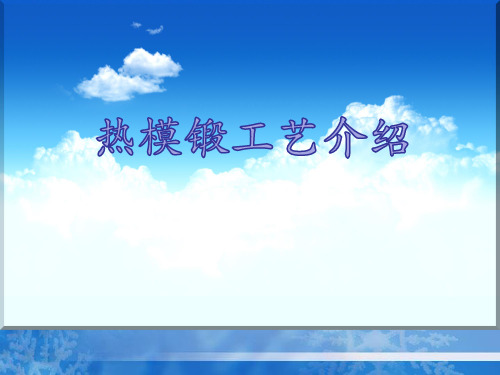
1)模锻锤: G=(3.5~6.3)KF(公斤) 2)热模锻压力机 P=(6.3~7.4)F(吨) 圆形锻件:P=8(1-0.001D)(1.1+20/D)2 FБbt 非圆形:P=8(1-0.001D)(1.1+20/D)2 (1+0.1 )FБbt 3)平锻机 P=5(1-0.001D)(D+10)2Бbt 4)螺旋压力机 P=KБbtF
热模锻压力机 (曲柄压力机)
和同样能力的模锻锤相比, 热模锻压力机的初次投资 大,但维护费用低,动力 消耗小。
和摩擦压力机模锻相比, 生产率较高,便于自动化。
热模锻压力机结构复杂, 制造条件要求高。
螺旋压力机种类:
摩擦螺旋压力机 电动螺旋压力机 离合器螺旋压力机 液压传动螺旋压力机
1、摩擦压力机靠飞轮积蓄 的能量工作,原则上可多次打击 干大活。实际有效打击次数不超 过3次。
键块分别紧固在锤头和下模座
的燕尾槽中。
•
燕尾使模块固定在锤头
(或砧座)上,使燕尾底面与
锤头(或砧座)底面紧密贴合。
•
楔铁使模块在左右方向定
位。键块使模块在前后方向定
位。
热模锻压力机与模锻锤相比,其 工作特性为: (1)静压成形,无震动和噪音; (2)机架和曲柄连杆机构的刚性 大,工作时弹性变形小; (3)滑块行程一定,每一模锻工 步只要一次行程完成; (4)导向精度和承受偏载的能力 强; (5)有上下顶件装置,便于锻件 脱模。
部分汽车件产品
转向系统 Steering System
制动系统 Braking System
传动系统 Drive System
➢ 转向系统 Components of Steering System
锻造工艺及模具设计第一章

(二)锻造生产的发展趋势
1) 总趋势是使锻件形状、尺寸和表面质量 最大限度地与产品零件相接近,以达到少 、无切削加工的目的,为此应逐步发展和 完善精密成形新技术,发展高效精密的锻 压设备。
2) 为适应大批量生产的需要,应发展专业 化的连续生产线,建立地区性的专门化锻 造中心,如齿轮精锻中心、连杆锻造中心 、标准件锻造中心等,以利于进行技术改 造及采用最新设备和先进工艺。
20世纪初期,随着汽车开始大量生产,热模锻迅 速发展,成为锻造的主要工艺。
➢锻压经过100多年的发展,今天已成为一 门综合性学科。
➢它以塑性成形原理、金属学、摩擦学为 理论基础,同时涉及传热学、物理化学、 机械运动等相关学科,以锻造、冲压等为 技术,与其它学科一起支撑机器制造业。
我国的锻造生产与世界先进国家的水平相比
还有一定差距。
表现在:1) 工业发达国家的模锻件已占全部锻件的 70%以上,而我国尚不足30%。
2) 国外有成千条锻造自动生产线,大型自由锻 造水压机普遍配备了锻造操作机等。而我国在这些 方法还很薄弱。
3) 精锻技术和大型锻件的生产水平与一些工业发 展国家相比较低,一些航空产品上的精锻件和重 要的大型自由锻件还常常需从国外进口。
锻造工艺及模具设计第一章
第一章 绪 论
压力加工设备欣赏
什么是锻造?——金属塑性加工方法之一
锻造的定义:
利用锻压机械对金属坯料施 加压力,使其产生塑性变形以 获得具有一定机械性能、一定 形状和尺寸锻件的加工方法。
为了使金属材料在高塑性下成型,通常锻造是在热态下 进行,因此锻造也称为热锻。
今天,锻造生产率提高,其锻件精度也愈来愈高,可以达到 甚至超过机械加工的一般精度水平,如各种冷温挤压标准件 、精锻齿轮、精锻叶片、精锻轴类件等。
锻造工艺过程及模具设计第7章模锻工艺

第7章
模锻工艺过程
4.联合模锻件 根据锻件的形状、 尺寸,采用其它设备 制坯、平锻机上成形; 或者平锻机上制坯、 其它设备成形;或采 用不同设备成形锻件 的不同部位。
第7章
模锻工艺过程
7.3 模锻件图设计
模锻件图是模锻生产过程、模锻工艺 过程规范制订、锻模设计、锻模检验及锻 模制造的依据。
模锻件图是根据产品图设计的,分为 冷锻件图和热锻件图两种。
第7章
模锻工艺过程
采用带导柱的组合模,能锻出精度较 高的锻件。 采用带镶块的组合模具,可节约大量 模具钢。 切边模也可以装在同一副模架上。
第7章
模锻工艺过程
7.1.3 螺旋压力机及其工艺过程特征
目前 国内用得 较多的螺 旋压力机 是摩擦压 力机。图 7-4为摩擦 压力机的 传动系统
简图。
图7.4摩擦压力机传动系统简图 1-电机 2-传送带 3、5-摩擦盘 4-轴 6-飞轮 7、10-连接杆 8-螺母9-螺杆 11-挡块 12-滑块 13-手柄
第7章
模锻工艺过程
热模锻压力机模锻工艺过程具有下列特点: 1、对于横截面形状复杂、分模面接近圆形或方形 的锻件(例如薄辐齿轮),必须正确设计预锻工步。 2、对于截面相差很大的长毛坯,一般需要用其它 设备制坯。 3、最好使用电加热及其它少无氧化加热,或在热 坯料送进压力机前有效清除氧化皮。 4、热模锻压力机导向精度较高,工作方式和普通 冲床相近。
第7章
模锻工艺过程
7.1.2 热模锻压力机及其工艺过 程特征
热模锻压力机的机构和工作原理如图7.3 所示。 和锤上模锻相比,可以认为属于静压。 振动小、噪音小、劳动条件好、操作安全, 对操作工人技术要求低,便于实现机械化和 自动化。
热锻模热处理工艺设计报告

热锻模热处理工艺设计报告一、背景介绍热锻技术是一种通过热加工和塑性变形的方式对金属材料进行形状改变和强化的方法。
热锻模是热锻工艺中的重要组成部分,对热锻产品的质量和性能起着关键作用。
为了保证热锻模具具有良好的耐用性和工艺性能,需要进行适当的热处理。
二、热处理工艺设计1. 确定热处理方式根据热锻模具的材料和结构特点,我们选择了淬火和回火的热处理方式。
淬火可以使模具表面形成高硬度的马氏体组织,提高模具的硬度和耐磨性;回火可以消除淬火过程中产生的内应力,提高模具的韧性和抗拉强度。
2. 确定热处理参数根据热锻模具的材料和要求,我们制定了以下热处理参数:- 淬火温度:800- 淬火介质:水- 回火温度:500- 回火时间:2小时3. 热处理过程(1)淬火过程:将热锻模具加热至800并保持一段时间,使其均匀受热。
然后迅速将模具放入预先准备好的水中进行冷却。
水的冷却速度较快,可以使模具表面迅速形成马氏体组织。
(2)回火过程:将淬火后的模具加热至500并保持2小时,让模具内部的残余应力逐渐释放,同时马氏体转变为较为稳定的回火组织。
之后,将模具缓慢冷却至室温。
4. 检测和表征完成热处理后,需要对热锻模具进行检测和表征,以确保其达到设计要求。
常用的方法包括金相显微镜观察、硬度测试和力学性能测试等。
三、预期效果和改进措施经过以上热处理过程,预期热锻模具能够具备以下效果:- 表面硬度提高,耐磨性能增强- 内部应力得到释放,模具韧性提高- 样品组织均匀,无明显缺陷然而,热处理过程中也可能出现一些问题,如表面开裂、变形等。
为了避免这些问题的发生,我们采取了以下改进措施:- 严格控制热处理温度和时间,避免温度过高或时间过长导致变形和开裂。
- 选择合适的冷却介质,确保冷却速度适中,避免产生过多的应力和变形。
- 加强对模具的预处理,如去除氧化物和表面锈蚀等,减少表面缺陷的产生。
四、结论热锻模热处理工艺设计是确保热锻模具具有良好工艺性能和耐用性的重要环节。
锻造工艺过程及模具设计第7章模锻工艺
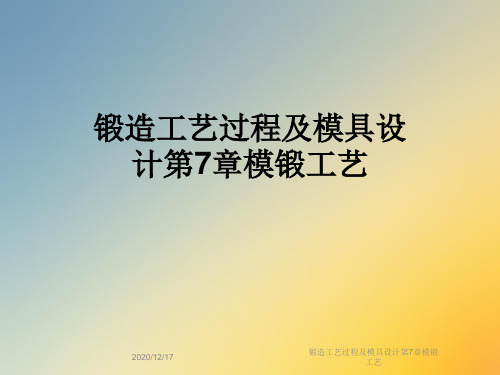
锻造工艺过程及模具设计第7章模锻 工艺
(3)对头部尺寸较大的长轴类锻件可以折线 分模,使上下模膛深度大致相等,使尖角处易于 充满,如7.9所示。
图7.9 上下模膛深度大致相等易充满
锻造工艺过程及模具设计第7章模锻 工艺
(4)当圆饼类锻件H≤D时,应采取径向分
模,不宜采用轴向分模(图7.10)。
四、和垂直分模平锻机相比,水 平分模平锻机在操作上的优点:
1.夹紧力大,可利用夹紧滑块作为模锻变 形机构,扩大了应用范围,提高了锻件 精度。
2.模锻时坯料沿水平方向传送,易于实现 机械化和自动化。
锻造工艺过程及模具设计第7章模锻 工艺
五、和垂直分模平锻机相比,水平分模平 锻机有如下缺点:
1.曲柄连杆式的夹紧机构,夹紧保持时间 有限,不宜进行深冲孔和管坯端部镦锻成形。
模锻件图是根据产品图设计的,分为 冷锻件图和热锻件图两种。
锻造工艺过程及模具设计第7章模锻 工艺
冷锻件图即为锻件图。 冷锻件图用于最终锻件的检验和校正 模的设计,也是机械加工部门制定加工 工艺过程,设计加工夹具的依据。 热锻件图用于锻模设计和加工制造。 热锻件图是对冷锻件图上各尺寸相应地 加上热胀量而绘制的。
锻造工艺过程及模具设计第7章模锻 工艺
采用带导柱的组合模,能锻出精度较 高的锻件。
采用带镶块的组合模具,可节约大量 模具钢。
切边模也可以装在同一副模架上。
锻造工艺过程及模具设计第7章模锻 工艺
7.1.3 螺旋压力机及其工艺过程特征
目前 国内用得 较多的螺 旋压力机 是摩擦压 力机。图 7-4为摩擦 压力机的 传动系统
3、摩擦压力机设备制造成本低,劳动条件好。 4、摩擦压力机的缺点是生产率低、传动效率 低、抗偏载能力差。
热模锻_精品文档
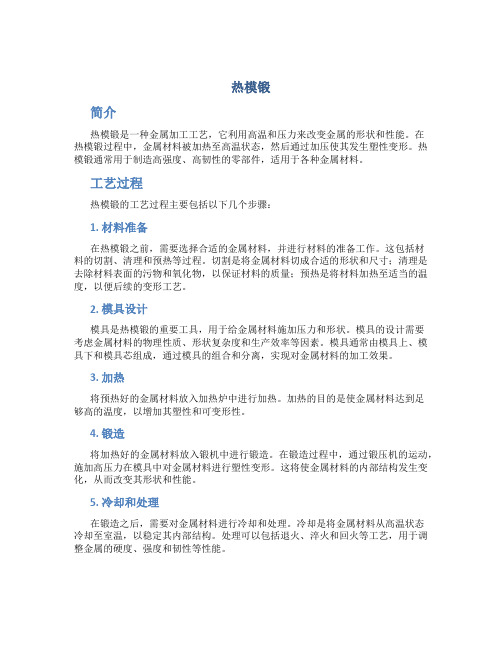
热模锻简介热模锻是一种金属加工工艺,它利用高温和压力来改变金属的形状和性能。
在热模锻过程中,金属材料被加热至高温状态,然后通过加压使其发生塑性变形。
热模锻通常用于制造高强度、高韧性的零部件,适用于各种金属材料。
工艺过程热模锻的工艺过程主要包括以下几个步骤:1. 材料准备在热模锻之前,需要选择合适的金属材料,并进行材料的准备工作。
这包括材料的切割、清理和预热等过程。
切割是将金属材料切成合适的形状和尺寸;清理是去除材料表面的污物和氧化物,以保证材料的质量;预热是将材料加热至适当的温度,以便后续的变形工艺。
2. 模具设计模具是热模锻的重要工具,用于给金属材料施加压力和形状。
模具的设计需要考虑金属材料的物理性质、形状复杂度和生产效率等因素。
模具通常由模具上、模具下和模具芯组成,通过模具的组合和分离,实现对金属材料的加工效果。
3. 加热将预热好的金属材料放入加热炉中进行加热。
加热的目的是使金属材料达到足够高的温度,以增加其塑性和可变形性。
4. 锻造将加热好的金属材料放入锻机中进行锻造。
在锻造过程中,通过锻压机的运动,施加高压力在模具中对金属材料进行塑性变形。
这将使金属材料的内部结构发生变化,从而改变其形状和性能。
5. 冷却和处理在锻造之后,需要对金属材料进行冷却和处理。
冷却是将金属材料从高温状态冷却至室温,以稳定其内部结构。
处理可以包括退火、淬火和回火等工艺,用于调整金属的硬度、强度和韧性等性能。
优点及应用领域热模锻具有以下几个明显的优点:1.提高材料性能:热模锻能够改善金属材料的结晶状态和力学性能,使其具有更高的强度、韧性和抗疲劳性。
2.制造高品质零部件:热模锻可以制造复杂形状和高精度的零部件,满足各种工业领域的需求。
3.节约材料成本:热模锻可以减少材料的浪费,提高材料的利用率,降低制造成本。
热模锻广泛应用于航空航天、汽车制造、电力设备、石油化工、冶金等领域,例如制造飞机引擎、汽车曲轴、液压缸体等高负荷和高耐久性零部件。
模具设计与制造—— 热锻工艺概述
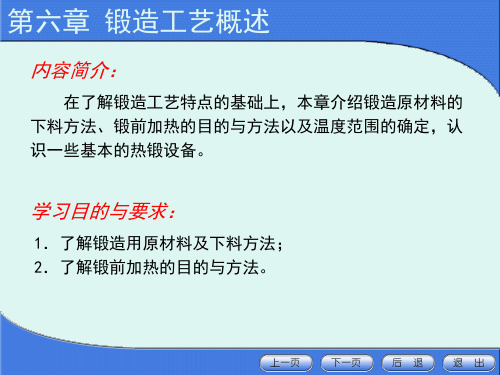
内容简介:
在了解锻造工艺特点的基础上,本章介绍锻造原材料的 下料方法、锻前加热的目的与方法以及温度范围的确定,认 识一些基本的热锻设备。
学习目的与要求:
1.了解锻造用原材料及下料方法; 2.了解锻前加热的目的与方法。
第六章 锻造工艺概述
第一节 锻造工艺特点
一、锻造生产的重要性
锻造是塑性加工的重要分支,它是利用材料的塑性,对材 料施加外力使之发生塑性变形,从而得到所需形状、尺寸、 组织和性能的锻件。
第六章 锻造工艺概述
第二节 锻造用材料及下料方法-锯切法
锯床下料极为普遍,虽效率低,锯口损耗大,但下料长 度准确,锯割断面平整,是一种主要的下料方法。有圆盘锯、 带锯、弓形锯等。
圆盘锯是由电动机带动带齿的锯盘旋转并移动,将棒料 切断。
弓形锯是由电动机带动带齿的锯条作往复移动,将棒料 切断。
第六章 锻造工艺概述
加热时间:毛坯从开始加热至始锻温度时所需的时间。不包括毛 坯在始锻温度下的保温时间。
第六章 锻造工艺概述
第六节 少无氧化加热
通常称金属烧损量在0.5%以下的锻造加热为少氧化加热。 称金属烧损量在0.1%以下的锻造加热为无氧化加热。 少无氧化加热除了可减少金属氧化、脱碳外,还可显著提高
锻件表面质量和尺寸精度,减少模具磨损等;是实现精密锻造必 不可少的配套技术。
快速加热 利用介质保护加热
少无氧化火焰加热
第六章 锻造工艺概述
第六节 少无氧化加热-炉气
第六章 锻造工艺概述
第六节 少无氧化加热-快速加热
包括:火焰炉中的辐射快速加热和对流快速加热,感应电加热和 接触电加热等。
理论依据:采用技术上可能的加热速度加热金属时,坯料内部产 生的温度应力、留存的残余应力和组织应力叠加的结果,不足以 引起坯料产生裂纹。
热模锻工艺及模具设计

SGMDYPT-FF 2009.04
1.DYPT热模锻齿轮毛坯生产工艺流程
钢棒剪切下料 *:端面角度/毛刺
中频感应棒料加热 *:温度
四工步锻压成型 *:尺寸/表面质量
等温退火热处理 *:温度曲线/金相组织
抛丸处理 *:表面氧化皮残留物
质量检验 *:尺寸/表面质量
SGMDYPT-FF 2009.04
强化抛丸 Short Blasting
磁粉探伤 Magnetic Detection
终检入库 Final Acceptance
SGMDYPT-FF 2009.04
工步示意图:
辊锻制坯 镦粗压扁
预锻
终锻 冲孔 切边
机械手 夹爪爪 夹持端
辊锻工步(4)
SGMDYPT-FF 2009.04
工艺比较: 1.采用涨断加工的连杆减少了工艺切口和调质费 用,(材料为非调钢); 2.从原材料和加工费用较拉断连杆都有优势; 3.从机械性能讲涨断连杆的机械性能好于拉断连杆 在国外涨断连杆是一种较成熟的工艺,所以德国许多 汽车公司(包括大众汽车和奔驰汽车)基本都采用 锻造连杆. 而在美国和日本,粉末冶金连杆采用的较多.
基准尺寸相同 或预锻比终锻单边小 此部位多 不充满
SGMDYPT-FF 2009.04
二.模具结构设计(闭式) - 预锻模腔
2.3镦粗坯料定位: 由于镦粗坯料端面圆角与侧面多为大 圆弧过渡,坯料定位于下模接近坯料 直径的凹腔内,如图示区域; 2.4镦粗坯料放置: 坯料由送料同步器夹持到达位置后, 坯料与模具成型面多有一定高度差, 坯料放置与成型后顶出,需要保证其 运动过程中的平稳性; 多采用浮动下模结构,利用浮动顶出 机构来接、送坯料,有利于运动平稳 性和坯料定位准确。
- 1、下载文档前请自行甄别文档内容的完整性,平台不提供额外的编辑、内容补充、找答案等附加服务。
- 2、"仅部分预览"的文档,不可在线预览部分如存在完整性等问题,可反馈申请退款(可完整预览的文档不适用该条件!)。
- 3、如文档侵犯您的权益,请联系客服反馈,我们会尽快为您处理(人工客服工作时间:9:00-18:30)。
强化抛丸 Short Blasting
磁粉探伤 Magnetic Detection
终检入库 Final Acceptance
SGMDYPT-FF 2009.04
工步示意图:
辊锻制坯 镦粗压扁
预锻
终锻 冲孔 切边
机械手 夹爪爪 夹持端
辊锻工步(4)
SGMDYPT-FF 2009.04
工艺比较: 1.采用涨断加工的连杆减少了工艺切口和调质费 用,(材料为非调钢); 2.从原材料和加工费用较拉断连杆都有优势; 3.从机械性能讲涨断连杆的机械性能好于拉断连杆 在国外涨断连杆是一种较成熟的工艺,所以德国许多 汽车公司(包括大众汽车和奔驰汽车)基本都采用 锻造连杆. 而在美国和日本,粉末冶金连杆采用的较多.
下模浮 动顶出
镦粗圆饼状坯料 落入本区域
SGMDYPT-FF 2009.04
二.模具结构设计(闭式) - 预锻模腔 设计要点: 2.5预防终锻成型时产生错差/折叠:
1)因热模锻压力机为多工位进级方式, 很难保证使模腔布局于压力机工作压 力中心位置,并且因各个工位金属流 动变形量不同,产生变形抗力也不同, 各个工位变形所需要的设备压力也不 同。 2)在实际生产中压力机负载工作状况总 是存在偏载现象; 3)偏载现象与模具制造、装配等累积误 差必然影响到锻件的错差,工步间错 差过大,后续锻压易出现折叠。 4)在模座导柱导向之外,增加预锻工步 与终锻工步的模具结构导向。 依靠合模初期,上下模外衬啮合,对 工步模具起导向作用,右图示
该尺寸考虑冲孔影响 一档从动齿轮 终锻成型工步示意图
SGMDYPT-FF 2009.04
2.2)四工步锻压成型工艺 - 预锻成型
预锻成型工艺要点: 1. 直径:便于预锻件放置于终锻模腔内,单 边间隙0.8-1.2mm为易。 2. 高度:目前热模锻齿轮终锻多采用类似镦 粗的方式,高度降低,直径增加,为利于 终锻金属较易流动,多采用预锻件高度较 终锻件高1.5-2.5mm为易。 3. 圆周/内孔 圆弧过渡: 预锻件在此部位成形太好(充满),终锻时 金属不易流动,易形成折叠,预锻件该部 位多采用大圆弧过渡,内孔处多增加凸出 高度。 4. 连皮:厚度多比终锻成型厚度高2mm以上, 以利于内孔上边缘终锻成型 5. 锻件上小的凸部与凹坑,预锻工步进行简 化不做或转化为圆滑形状.
SGMDYPT-FF 2009.04
1.DYPT热模锻齿轮毛坯生产工艺流程
钢棒剪切下料 *:端面角度/毛刺
中频感应棒料加热 *:温度
四工步锻压成型 *:尺寸/表面质量
等温退火热处理 *:温度曲线/金相组织
抛丸处理 *:表面氧化皮残留物
质量检验 *:尺寸/表面质量
SGMDYPT-FF 2009.04
Cutting the Stick
Stick Induction Heating
辊锻制坯 (4工步) Roller Foundry (4 Steps)
锻压成型(5工步) Forging Pressing (5 Steps)
可控风冷 Controllable Wind Cooler
精压 Accurate Pressing
二.模具结构设计(开式) - 终锻模腔 设计出热锻件图,下一步要 考虑的是: -飞边槽的确定,(根据设备确 定) (飞边槽的作用: -增加金属流动阻力,便于充满; -容纳多余金属) -排气孔 针对较深的腔,在金属最后充 满处钻出排气孔,(直径Ф 1~ 2,深度5-15mm);如模腔底部 有顶出器或其它排气的缝隙 时,不需开排气孔.
好控制锻件高度公差;但不便于进行制坯. 冲孔;模具结构复杂,初次投资大.
- 大尺寸工作台面,可多工位布局,如:镦粗/预锻/终锻/ - 设备有顶料机构, 实现自动化生产,生产效率高 - 模具模块可按工步单独设计/制造/安装,调整/更换/
维修方便.
- 热模锻压力机因各个工位金属流动变形量不同,产
生变形抗力不同,各个工位变形所需要的设备压力也不 同;在实际生产中压力机负载工作状况总是存在偏载现 象
基准尺寸相同 或预锻比终锻单边小 此部位多 不充满
SGMDYPT-FF 2009.04
二.模具结构设计(闭式) - 预锻模腔
2.3镦粗坯料定位: 由于镦粗坯料端面圆角与侧面多为大 圆弧过渡,坯料定位于下模接近坯料 直径的凹腔内,如图示区域; 2.4镦粗坯料放置: 坯料由送料同步器夹持到达位置后, 坯料与模具成型面多有一定高度差, 坯料放置与成型后顶出,需要保证其 运动过程中的平稳性; 多采用浮动下模结构,利用浮动顶出 机构来接、送坯料,有利于运动平稳 性和坯料定位准确。
原材料进厂检验 Raw Material
棒料剪切
Cutting the Stick
棒料感应加热
Stick Induction Heating
辊锻制坯(4工步) Roller Foundry (4 Steps) 抛丸处理 Ball Blast
淬火回火 Quenching Temperature
精压 Accurate Pressing
SGMDYPT-FF 2009.04
二.模具结构设计(开式) - 终锻模腔 -终锻模腔按热锻件图设计: 加工面机加工余量及工艺余量(需与机加工厂协商) 例如:拉断连杆(T200)需考虑连杆体和连杆盖断开的加工余量, 而涨断连杆(GEN3)不需考虑. 考虑收缩率,对钢锻件,收缩率一般取1%~1.5%;考虑后续工序 (如校正或压印),收缩率取为1%~1.5% . 同时还应考虑:
SGMDYPT-FF 2009.04
. 举例
T200连杆与L850连杆工艺比较:
T200
L850
SGMDYPT-FF 2009.04
1. 工艺流程 Process
1)S200连杆毛坯锻造生产工艺流程 Forging Process of S200 Connecting Rod Production 锻压成型 (5工步) Forging Pressing (5 Steps) 磁粉探伤 Magnetic Detection
课程主要内容:
一.热模锻般工艺特点 -热模锻齿轮毛坯生产工艺流程
-四工步锻压成型工艺特点 二. 热模锻模具设计 -闭式模锻模具设计(以齿坯为例) -开式模锻模具设计(以连杆为例)
三.涨断连杆与拉断连杆工艺对比
SGMDYPT-FF 2009.04
一.热模锻一般工艺特点 (和锤上模锻相比)
- 压机滑块行程固定,载荷为静压力,锻件精度高,能较
SGMDYPT-FF 2009.04
二.模具结构设计(开式) - 预锻模腔
设计要点: 1.高度尺寸比终锻工步尺寸图相应大2-5mm,而宽度尺寸适当 减小,并使预锻件的截面面积稍大于终锻件相应的横截面积; 2.严格控制预锻件各部分的体积,使终锻时多余的金属能合理 地流动,避免产生金属回流,折叠等缺陷; 3.预锻件在终锻模腔的定位.预锻件图的某些部位的形状和尺 寸应与终锻件基本吻合; 4.预锻件的圆角半径和模锻斜度设计原则与锤上模锻相同.
二.模具结构设计(闭式) - 终锻模腔 设计要点:
2.3冲孔连皮设计: 冲孔连皮的设计多跟锻件的内孔形状/内孔深度与直径等因素有关, 目前我们热模锻齿轮的冲孔连皮有两种结构模式。 (预锻模腔的连皮形式多跟终锻模腔形式接近)
图a 图b
图 a 结构有:一档从动齿轮/三四档从动结合齿/五档从动齿轮/倒档惰轮 图 b 结构有:其他零件
合模时, 上下模 啮合面
SGMDYPT-FF 2009.04
二.模具结构设计(闭式) - 终锻模腔 1.终锻模腔:
DYPT热模锻齿轮均为闭式模锻,即为无飞边锻造, 因此终锻模腔设计较为简单,仅须考虑热态锻件 尺寸,无需考虑飞边槽设计。
2.设计要点:
2.1缩比及尺寸调整: 在没有类似参考及相关经验的前提下,终锻模腔 可以根据锻件材料缩比系数(1.2-1.5%)进行 设计。 根据最终锻件成品进行调整终锻模腔相关尺寸。 2.2预锻件放置及定位: 因终锻模腔与锻件成品有直接关联,终锻模腔不 易采用浮动接送料的方式,且终锻模腔是各个工 步中变形受力最大的工步,下模多采用热态紧配 合,改善模具受力状态,以增强抗打击能力; 预锻件的放置完全依靠自由落体进入模腔, 预锻件靠其与终锻模腔相近的下模外形定位. SGMDYPT-FF 2009.04
冷态锻 件图设计
缩比
Байду номын сангаас
热态锻 件图设计
变形量(高 / 瘦 ) 可靠定位
选 材
镦粗比 减少钢棒的 规格(直径)
镦粗制坯
圆周定位
预锻成型 毛坯设计
SGMDYPT-FF 2009.04
2.1)四工步锻压成型工艺 - 终锻成型
终锻成型工艺要点: 1. 缩比(热收缩率): 高温锻件尺寸的热收缩率多采用 1.0-1.5%; 2. 模锻: 多采用内孔3~5°,外周1-3°; 3. 锻件外形尺寸: 考虑后续冲孔工序对局部尺寸的 变形影响,调整局部缩比。 4. 冲孔连皮设计: 基于金属流动、锻打压力和模具 寿命等因素考虑,厚度多采用710mm
图b
模具下压,坯 料产生变形抗 力不均匀
SGMDYPT-FF 2009.04
二.模具结构设计(闭式) - 预锻模腔 1.预锻模腔:
预锻模腔改善金属在终锻模腔内的成 形条件,尽可能减少变形量使金属易 于充满终锻模腔,可以改善终锻模具 使用寿命并尽可能减少压力偏载;
预锻模腔
终锻模腔
2.设计要点:
2.1模锻角度: 复杂形状模锻斜度,预锻比终锻斜度 大1-2°,右上图示 2.2封闭模腔容积: 预锻模腔容积较终锻模腔大10-20%, 预锻模腔过渡处多为较大R,预锻毛坯 外圆周和内孔边缘以成型圆鼓状为好, 预锻毛坯不要求充满模腔。 如右下图示
模具下压, 坯料产生变 形抗力
SGMDYPT-FF 2009.04
2.4)镦粗制坯