微裂纹的分形分布及损伤演化过程的分形机理考虑一弹性体包含NT条相互
断裂理论基础
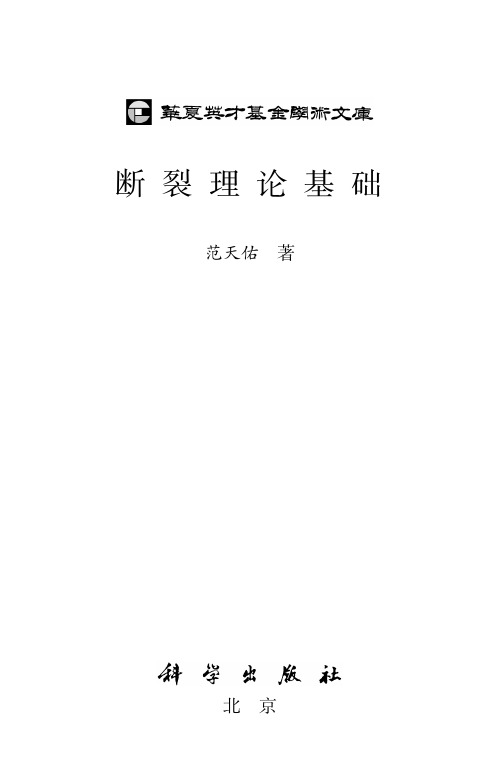
· ii · 前 言
它是在当时生产实践问题的强烈推动下 ,在经典 Griffith 理论的基 础上发 展起 来 的 .上世纪 60 年代是其大发展时期 .从 1965 年下半年开始国内出现特殊的形势 , 上面提到的我国老一辈学者开创的断裂学科的较好势头也就丧失了 ,因而同国外 的差距进一步拉大 .在 20 世纪 70 年代初 ,受我国航空工业部门的委托 ,冶金部钢 铁研究总院物理研究室陈箎同志领导的小组从材料断裂韧性测试开始 ,在十分困 难的条件下 ,率先在我国开展了断裂力学的工作 .显然 ,我国断裂力学工作起步至 少比国外大约晚了 20 多年 .1972 年 ,在敬爱的周恩来总理关怀下 ,包括力学在内 的自然科学各基础学科举行了赶超世界先进水平的规划座谈会 .当时力学学科的 规划座谈会的预备会的纪要就引用了恩格斯的一句名言 :“一个民族要想站在世界 的高峰 ,就一刻也不能停止理论思维 。”同时指出断裂力学是一门新学科 ,在理论上 和实践上具有重要意义 ,建议尽快在我国开展该领域的工作 .在冶金部钢铁研究总 院物理研究室陈箎同志等工作和力学学科规划座谈会预备会纪要的激励下 ,尤其 是众多实际问题需要的推动下 ,我国一些单位和科技工作者逐步开展了断裂力学 的研究和应用工作 .著者当时是作为一名业余爱好者参加到这项工作中去的 .著者 在当学生时 ,受到董铁宝教授的指导 ,读过一点经典断裂理论的文献 ,当时也得到 王仁教授 、张兴钤教授和钱临照教授的指教 .在经过将近 10 年中断并重新回到教 学工作岗位时 ,获悉经典断裂理论已经发展成断裂力学这门新学科时 ,很振奋 ,但 深感已经落后得太远了 .枟断裂力学基础枠是著者学习断裂力学笔记整理出来的 .当 时著者对断裂力学的认识还很初步 .该书出版至今已经超过了 20 年 ,探索断裂现 象规律的工作已从力学扩充到更广泛和深入的领域 .考虑到这些情况的变化 ,需要 对该书加以改写 .
岩石破坏过程中的声发射分布规律及其分形特征
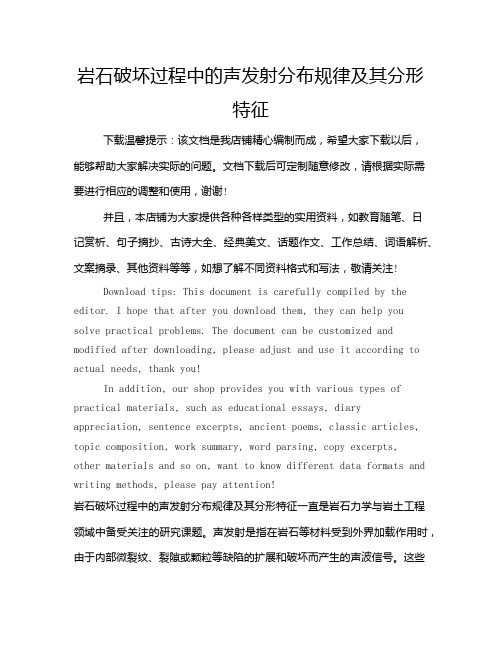
岩石破坏过程中的声发射分布规律及其分形特征下载温馨提示:该文档是我店铺精心编制而成,希望大家下载以后,能够帮助大家解决实际的问题。
文档下载后可定制随意修改,请根据实际需要进行相应的调整和使用,谢谢!并且,本店铺为大家提供各种各样类型的实用资料,如教育随笔、日记赏析、句子摘抄、古诗大全、经典美文、话题作文、工作总结、词语解析、文案摘录、其他资料等等,如想了解不同资料格式和写法,敬请关注!Download tips: This document is carefully compiled by the editor. I hope that after you download them, they can help yousolve practical problems. The document can be customized and modified after downloading, please adjust and use it according to actual needs, thank you!In addition, our shop provides you with various types of practical materials, such as educational essays, diary appreciation, sentence excerpts, ancient poems, classic articles, topic composition, work summary, word parsing, copy excerpts,other materials and so on, want to know different data formats and writing methods, please pay attention!岩石破坏过程中的声发射分布规律及其分形特征一直是岩石力学与岩土工程领域中备受关注的研究课题。
基于微米力学实验的页岩I型断裂韧度表征

基于微米力学实验的页岩I型断裂韧度表征韩强;屈展;叶正寅;董广建【摘要】页岩断裂韧度(KIC)是页岩气储层水力压裂设计的基础参数之一,由于组成的非均质性,常规宏观力学测量方法存在制样困难、力学解释参数不连续、精度偏低等问题.如何及时获取页岩的断裂特性,确保安全高效的工程施工,是当前面临的一大问题.因此,提出了基于微米力学实验的页岩Ⅰ型断裂韧度分析方法,可用于页岩微裂纹起裂、发育直至形成宏观裂纹的机理研究,进行页岩宏观Ⅰ型断裂韧度预测.基于页岩多尺度组成分析,开展了维氏压头和玻氏压头的页岩微米力学实验,分析了页岩残余压痕与压头间的相似关系、有效测试载荷以及压头参数的优化与选择.分析了不同压入载荷下的页岩细观断裂韧度分布特征,开展了宏观巴西圆盘实验,验证页岩微米力学测试方法的适用性.研究结果表明,在有效载荷范围内的页岩细观Ⅰ型断裂韧度波动性较小,当压入载荷过大时,由于岩样压痕区域出现局部剥落导致断裂韧度测量值偏小.与宏观实验的比对分析显示,微米力学实验的KIC平均值为0.86 MPa· √m,直槽切缝巴西圆盘实验得到的K IC平均值为0.92 MPa· √m,两类方法的统计平均值较为接近,页岩局部组成的非均质性使得微米力学测量结果较宏观测试更为分散.研究结果可用于页岩宏观Ⅰ型断裂韧度预测,为有效解决页岩气储层水力压裂参数评价提供新的思路和方法.【期刊名称】《力学学报》【年(卷),期】2019(051)004【总页数】10页(P1245-1254)【关键词】页岩;微米力学测试;影响因素;Ⅰ型断裂韧度【作者】韩强;屈展;叶正寅;董广建【作者单位】西安石油大学石油工程学院/博士后创新基地,西安 710065;西安石油大学陕西省油气井及储层渗流与岩石力学重点实验室,西安 710065;西北工业大学航空学院/博士后科研流动站,西安 710072;西安石油大学石油工程学院/博士后创新基地,西安 710065;西安石油大学陕西省油气井及储层渗流与岩石力学重点实验室,西安 710065;西北工业大学航空学院/博士后科研流动站,西安 710072;西北工业大学航空学院/博士后科研流动站,西安 710072;西南石油大学石油与天然气工程学院,成都 610500【正文语种】中文【中图分类】TE135引言岩气储层岩石具有低渗透、天然裂缝发育等特征,页岩气井水平段由于水力压裂施工的岩石裂纹发育,裂纹扩展的模式主要为Ⅰ型、Ⅱ型断裂或复合型断裂[1−6].通过页岩断裂韧度、脆性指数等参数的综合分析,可以为页岩气储层水力压裂设计及支撑剂选型提供科学依据[7−8].作为准脆性材料,页岩内部会存在裂缝、空隙、夹杂等天然微缺陷,其破坏特征表现为断裂的突发性,在裂缝扩展前不存在明显的裂尖塑性区,通过微裂隙的扩展最终连通形成宏观裂缝.如何在钻井、开采发生早期,超前或及时获取页岩断裂行为并准确做出异常情况预警,确保工程施工的安全和高效,是当前岩石力学面临的一大难题.目前对岩石起裂的室内研究主要参照岩石物理与力学特性关系,通过宏观实验获取力学属性[9−10].陈勉等[11−12]围绕砂岩储层进行了大量宏观实验研究,分析了砂岩断裂韧度受单轴抗拉、抗压强度等的影响规律.陈建国等[13]通过巴西圆盘实验分析了页岩Ⅰ型和Ⅱ型断裂韧度,并结合测井资料拟合了断裂韧度预测模型.该类方法虽然可以得到页岩的基本力学特征,但可能会存在制样困难、力学解释参数不连续、精度偏低等问题[14].测井仪器因井下空间制约或测试范围受限,常会导致测井解释资料品质不高、测量误差较大[15].在基础理论方面,通过开展裂纹尖端应力与裂纹扩展规律分析,描述裂纹扩展的有效判据和裂纹对自身结构的影响因素,分析裂缝的形成、发育、扩展等特征,建立了宏观损伤演化本构关系[16].但是,传统的宏观唯象模型没有考虑页岩内部的非均质性对宏观破坏的响应特征.页岩是典型的非均匀材料,由纳米级的多孔黏土、微米级非黏土夹杂和裂纹、孔洞、位错等组成复杂的微结构,页岩的弹性、硬度和变形破坏等都与组成有关[17].唐春安等[18−19]根据Weibull分布假设提出了岩石显微尺度分析,认为细观非均匀性是造成材料宏观非线性的内在原因.王士民等[20]通过非均匀性对宏观破坏形式的研究,指出材料坡度参数越小,其破坏形式越具有随机性.页岩的断裂破损本质上是微裂纹的产生、发育、扩展、直到贯通为宏观裂纹,使其失稳破坏的过程.该过程可分为3个阶段:某些孤立点产生应力集中,开裂后可以达到平衡态的起裂过程;随着载荷的增大介质沿开裂面产生相对滑移,裂纹扩展稳定阶段;当微裂纹相互贯通形成控制强度的宏观裂纹时,进入不稳定扩展阶段,逐渐失去承载能力. 现代力学按研究内容、尺度大小,将研究范畴划分为微观力学、细观力学和宏观力学.其中细观力学分析作为连接微观和宏观的桥梁,不仅可以研究料力学属性的形成机理,还可以评价和预测宏观尺度的有效性能[21−23].张泰华等[24−25]通过纳米力学测试技术,分析了金属、薄膜等材料的显微力学特性.近些年来,该技术逐渐被用于生物材料、晶体硅、水泥石等材料的微观力学评价[26−28].根据Ulm对页岩组成的尺度划分方法,可以将页岩按尺寸属性划分为单晶黏土矿物,微观多孔黏土介质(尺度为10−8~10−6m),细观多孔黏土夹杂复合介质 (尺度为10−5~10−4m)和尺寸大于10−3m 的宏观岩样 [29].基于页岩多尺度组成分布,本文通过微米力学实验讨论页岩细观断裂特性,研究一种适用于测量页岩细观Ⅰ型断裂韧度参数的新方法,开展测试参数影响因素评价,并与宏观巴西圆盘实验进行比对分析,为页岩显微断裂评价提供新的思路.1 分析方法微米力学测试仅需要满足测试表面的平整性,对样品形状和尺寸几乎无限制,实验压入深度在微米级,对材料属于微损测试.测试区域的应力场分布受压头几何形状的影响,在实际测量过程中会根据不同目的选用合适类型的压头,常用的棱锥压头有维氏压头和玻氏压头.1.1 维氏压头维氏压头为正四棱锥状,相对棱面夹角136◦、等效半锥角70.3◦,底面棱长与深度之比为4.95,投影面积为24.5h2,压痕形状产生的径向裂纹如图1所示.图中a 为压痕半径,c是径向裂纹长度,l是压痕点尖端距裂纹尖端的长度.图1 维氏压头产生径向裂纹示意图Fig.1 Schematic diagram of radial crack with Vickers indenter维氏压头与材料通过接触作用产生的裂纹可分为两类,一种是贯穿样品内部呈轴对称的半饼状裂纹,另一类是在试样表面产生的径向裂纹(图2).基于实验结果分析和量纲函数的拟合,给出适用维氏压头的材料裂纹沿径向充分扩展经验模型[30]式中,KIC为断裂韧度,;HIT为压入硬度,MPa;EIT为弹性模量,MPa;c为样品表面压痕中心点到裂纹端部的距离,mm;a为压痕半对角线长度,mm;φ为约束因子,取值3.图2 韦氏压头产生裂纹面类型Fig.2 Crack type produced by Vickers indenter 式(1)虽然给出了材料断裂韧度与弹性模量、硬度等参数的定性关系,但是半饼状裂纹的形成机理并不明确.将加载过程中的弹性应力场分解为卸载阶段的弹性可恢复功和因塑性变形的不可逆功进行讨论,Lawn等[31]提出了弹/塑性压入断裂模型.根据该模型,维氏压头在材料表面的应力场被简化为弹性应力场和塑性残余应力场的叠加问题.对核心塑性区的应力场作如下假设:初始状态为无应力弹性半空间,材料由于压入作用产生的塑性变形量可以通过单位体积的变化来表征.将裂纹充分扩展条件下的塑性区对弹性区的作用,简化为垂直作用于裂纹面中并使其张开的一对集中力Fr式中,b为塑性区半径,mm;Ψ为压头的相对棱边半夹角,(◦);Fm 为压入载荷,N.根据内嵌圆盘裂纹应力强度因子的解析解[32],并考虑半空间自由表面的影响,压头卸载后半饼状裂纹前段的应力强度因子可表示为式中,f(φ)为应力强度因子修正系数,无因次.当φ取90◦时为1.半饼状裂纹径向扩展的平衡条件为将式(4)代入式(5)可得到断裂韧度的表达式为式中,δ为与压头几何形状有关的系数,通过实验确定.对于一些脆性材料,在维氏压头的作用下并不出现半饼状裂纹,而是在材料表面产生径向裂纹.根据不规则裂缝应力强度因子判据[33],径向裂纹尖端与半饼状裂纹尖端的应力强度因子满足关系式中,KR为径向裂纹尖端的应力强度因子;KRP为半圆状裂纹尖端的应力强度因子.在此基础上通过满足边界条件的模型推导[34],得到径向裂纹断裂韧度表达式为式中,δL为待定系数,取值范围在0.014 6~0.015 4.在裂纹扩展充分的条件下,两种裂纹形态下的断裂韧度的计算值接近,这说明裂纹充分扩展时,其具体形态变化对断裂韧度的影响不大.1.2 玻氏压头玻氏压头为三棱锥形状,侧面棱边与中心线夹角77.05◦、棱面与中心线夹角65.3◦、等效半锥角与维氏压头相同,为70.3◦,底面棱边与深度比值为7.531 5,投影面积24.56h2,产生的径向裂纹参数如图3所示.图3 玻氏压头产生径向裂纹示意图Fig.3 Schematic diagram of radial crack with Berkovich indenter星型裂纹应力强度因子分析表明,对于一次出现任意不多于9条裂纹的断裂问题,维氏压头与玻氏压头的断裂韧度满足一次函数的关系,且维氏压头大约是玻氏压头的1.073倍[35].给出玻氏压头的断裂韧度表达式为值得注意的是,当满足径向裂纹充分扩展条件时,式(6)同样可适用于玻氏压头,对应的玻氏压头δ值约为0.016.2 页岩细观断裂测试2.1 测试设备页岩细观断裂力学测试选用集成声发射检测技术、摩擦力检测微米位移测量技术及微机自控技术的MFT-4000型多功能表面性能测试仪.该仪器的主要技术参数:加载范围0.5~300 N、加载精度0.5 N、加载速率 5~100 N/min、位移测量范围0.5~200µm.通过控制最大载荷与加载速度,获取载荷–位移数据,具有载荷、位移和仪器的自校准功能.2.2 测试样品页岩样品选自四川盆地龙马溪组地层,质地坚硬,颜色以灰、黑色为主,部分层理发育;X衍射结果显示,页岩中石英含量 20%~65%,方解石含量15%~35%,少见正长石和斜长石,黏土矿物含量16%~60%,属于一种典型的硬脆性页岩[36].试样尺寸为50 mm×25 mm×15 mm,上下表面的平行度小于0.3◦、侧面与压入表面垂度小于0.3◦.为了消除试样表面粗糙度对压入深度的影响,对试样进行二次精心细抛光处理,然后进行烘干、密封待用.2.3 测试流程单次测试主要包括3个阶段:加载阶段、保持阶段和卸载阶段(见图4).首先将压头与岩样表面接触,按确定的最大载荷和加载速率压入岩样表面;当达到最大载荷达后保持一定时间,消除测量误差;然后按照一定的卸载速率在规定时间内卸载至0,最后将压头从岩样表面提升移至下一个待测试点.图4 典型压痕加载响应与压痕变化Fig.4 Typical load response and indentation根据Delesse准则,非均质材料各相介质表面分布百分数可等效为体积百分数,对目标岩样表面的显微力学实验分析可以近似表征块体样的力学属性.同时,由于页岩组成的非均质性,使得单次压入测试不足以表征表面的宏观断裂韧度特征.本文采用网格化压入测试并进行统计分析,减小因压入区域某一组分集中产生的局部效应.根据ISO 14577的标准[37],确定页岩的相邻压入点间距不小于2 mm、压入点距岩样边界7 mm,排除相邻测试点的应力场干扰和页岩边界效应的影响.对于微/纳米范围的压入力学实验,压入测试数量应不小于15次,以便提高测量平均值的可靠性和重复性.3 测试影响因素分析3.1 压头选型针对龙马溪组页岩试样,分别选用维氏压头和玻氏压头开展显微断裂测试.图5给出了维氏压头在不同压入载荷(40 N,50 N,60 N,80 N)条件下的典型细观压痕.不难看出,维氏压头在页岩压痕表面会产生微小的凹点和局部剥落,且压头与压痕间的自相似性较差.此外,载荷–深度曲线表现出明显的不规则凸起.因此,由维氏压头较难得到径向裂纹和半对角压痕的长度参数.造成这种现象的主要原因是维氏压头尖端加工横刃结构和页岩非均质组成共同作用的结果.图5 维氏压头在页岩表面的残余压痕Fig.5 The residual indentation of shale surface produced by Vickers indenter图6 玻氏压头在页岩表面的残余压痕Fig.6 The residual indentation of shale surface produced by Berkovich indenter图6(a)和图6(b)给出了玻氏压头在不同最大载荷(60 N,80 N)条件下的典型细观压痕结果.不难看出,玻氏压头与压痕点的相似性较好,当压入载荷达到页岩细观破裂阈值60 N时,实验压入深度介于55~75µm,在岩样表面产生微裂纹.当压入载荷达到80 N,压入深度会达到78~90µm,裂纹发育较为明显.通过比对分析,常规的维氏压头不能满足页岩细观Ⅰ型断裂韧度的测量要求,建议采用玻氏压头开展页岩评价.实验中还发现,页岩与金属、陶瓷、薄膜等材料一样,存在有效裂纹产出率较低的问题,需要通过大量的压入实验获取.3.2 有效载荷与加载速率压入断裂韧度测试的有效载荷分析,目前仅见于陶瓷、金属等复合材料,对于组成的非均匀页岩尚无名明确的确定方法.通过对页岩弹性模量和硬度参数的细观力学测试分析,已知最大载荷在50 N时多数压入点与玻氏压头的自相似性较好,未出现破裂[38].当加载速率为10 N/min,压入载荷为60 N的压入点表面沿压头棱锥端部裂纹开始发育.载荷为90 N的部分压痕点沿棱面出现不规则剥落,当载荷达到100 N时,压痕点周边出现明显剥落(图6(c)和图6(d)).因此,岩样断裂韧度测试的有效载荷最好小于90 N.在加载速率为 100 N/min时,上述载荷的压痕点周边区域都会出现不同程度的剥落,这是由于过快加载会使压头向页岩表面产生一个冲击力,引起压痕点表面应力场的复杂变化.考虑到 MFT-4000型测试仪的加载精度,建议选取10 N/min开展测试.3.3 压头参数应用微米力学测试方法求解中间参量(弹性模量和硬度)过程中,假设了压头为理想尖端,即不存在曲率半径.然而,由于加工水平、使用磨损等影响,真实压头尖端曲率半径有可能会对弹性模量和硬度产生的影响.通过对式(9)中自变量参数弹性模量和硬度测量的影响,压头参数进而影响到断裂韧度求解的精确度.在相同条件下,通过理想压头和存在曲率半径压头的弹性模量比值和硬度的分析发现,当压头尖端真实曲率半径为20µm时,弹性模量和压入硬度随压入位移的减小,测量误差开始逐渐增大;当曲率半径达到50µm,此时的压头已不适用于页岩细观力学测试(图7、图8).因此测试前,需要检测压头曲率半径是否在有效范围.图7 不同曲率半径下岩样弹性模量关系(ER为是压头曲率半径R下岩样的弹性模量,E0为理想压头下的岩样弹性模量,hc为压入深度)Fig.7 The relationship between the radius of indenter and the test results of elastic modulus(ERis the elastic modulus of sample when the radius of indenter is R,E0is the elastic modulus under ideal condition,hcis indentation depth)图8 不同曲率半径下岩样硬度关系(HR为是压头曲率半径R下岩样的弹性模量,H0为理想压头下的岩样弹性模量))Fig.8 The relationship between the radiusof indenter and the test results of hardness(HRis the hardness of sample when the radius of indenter is R,H0is the hardness under ideal condition)4 结果与讨论图9给出了采用玻氏压头的页岩典型载荷–位移曲线和残余压痕表面形貌特征,结果显示裂纹面沿压痕角点扩展.表1给出了由微米力学实验,得到的KIC随不同压入载荷的变化关系.在有效载荷范围内,KIC随载荷的增加波动较小.当载荷过大导致压入表面出现局部剥落,KIC会随之缓慢降低.对于玻氏压头,有效载荷范围内测量得到的页岩试样表面径向裂纹长度介于1~3 mm,该小尺寸裂纹的测量准确与否,直接会导致断裂韧度的测量精度.与维氏压头相比,玻氏压头的尖端更为锋利,对页岩微断裂开启具有关键作用.需要注意的是,在对中间参数——弹性模量和硬度,需要在试样表面未发生破裂的情况下另行开展实验和分析计算,保证参数获取的准确性,参数的求解采用Oliver-Pharr方法.图9 页岩微米力学测试曲线和压痕表面形貌Fig.9 Typical micro-indentation load-depth curve of shale and the surface topography of indentation表1 玻氏压头的页岩细观Ⅰ型断裂韧度与压入载荷关系Table 1 The relationship between fracture toughness typeⅠand load at meso-scale by Berkovich indenterFm/NKIC/(MPa·√m)60 0.91 65 0.89 70 0.88 80 0.76 90 0.72由于页岩细观Ⅰ型断裂韧度求解是基于微米力学测试理论,需要与常规宏观测试结果进行比对分析,才能确定该方法对页岩的适用性.这里,通过将巴西圆盘实验测定的页岩宏观Ⅰ型断裂韧度作为约定真值,对细观测试结果进行分析评价.巴西圆盘实验选用WDW-D200型微机控制电子万能实验机,岩样加工为半圆柱状并进行切片处理,采用水力刀切割成预制缝(图10).实验载荷与预制缝的夹角为0度,岩样出现明显的拉伸破坏.巴西圆盘试件测试I型断裂韧度的计算公式为[39]式中,F为径向加载载荷,N;Rc为圆盘半径,mm;B为圆盘厚度,mm;ac为预制裂缝长度,mm;N为无因次强度因子.当ac/R 60.3时,无因次强度因子近似满足图10 页岩巴西圆盘测试试件Fig.10 Test sample of Brazilian disc test图11 页岩Ⅰ型断裂韧度的实验对比结果Fig.11 Comparison of experimental results of fracture toughness图11给出了页岩微米力学实验和巴西圆盘实验的断裂韧度测试结果.玻氏压头实验方法的KIC 介于,平均值为,25%~75%的分布偏差小于0.27.巴西圆盘实验得到的KIC介于0.76~1.21 MPa·m,平均值为0.92 MPa·m,25%~75%的分布偏差小于0.18.不难看出,微米压入测量法和宏观常规实验的统计平均值较为接近,可以进行页岩宏观Ⅰ型断裂韧度的预测.同时,微米压入的KIC分布较常规测量更为分散,这主要是由页岩局部矿物组分的异所产生的.5 结论本文在页岩多尺度组成分析的基础上,开展了维氏压头和玻氏压头的细观断裂实验,进行了实验参数的影响因素评价,分析了页岩细观Ⅰ型断裂韧度的基本特征,并与宏观实验结果进行比对分析,验证了方法的合理性.得出以下结论:(1)维氏压头由于自身构型和页岩的非均匀组成,导致压痕与压头的自相似性不理想,多数压痕表面出现剥落;对于玻氏压头,当载荷达到破裂阈值60 N后,沿棱锥的径向裂纹逐渐发育.在实验开始前,需要明确有效压入载荷和加载速率参数,减小因载荷加载过大、过快导致岩样表面崩落,对弹性模量、硬度等测量参数的影响.(2)在有效测试条件下,页岩细观I型断裂韧度受压入载荷增加的影响较小.当载荷过大时,因岩样表面崩落或重复压入导致应力场复杂化,页岩细观I型断裂韧度随压入载荷的增加而逐渐减小.通过对比宏观巴西圆盘实验和微米力学测试结果,分析宏观、细观页岩性断裂韧度.不难看出,通过微米力学测试可以有效表征岩样的Ⅰ型断裂韧度,当获取宏观实验岩样困难时,该技术可作为快速获取页岩断裂属性的一种新方法.参考文献【相关文献】1 陈勉,葛洪魁,赵金洲等.页岩油气高效开发的关键基础理论与挑战.石油钻探技术,2015,43(5):7-14(Chen Mian,Ge Hongkui,Zhao Jinzhou,et al.The key fundamentals for the efficient exploitation of shale oil and gas and its related challenges.Petroleum Drilling Techniques,2015,43(5):7-14(in Chinese))2 李庆辉,陈勉,金衍等.页岩脆性的室内评价方法及改进.岩石力学与工程学报,2012,31(8):1680-1685(Li Qinghui,Chen Mian,Jin Yan,et al.Indoor evaluation method for shale brittleness and improvement.Chinese Journal of Rock Mechanics and Engineering,2012,31(8):1680-1685(in Chinese))3 Lyu Q,Long XP,Ranjith PG,et al.Experimental investigation on the mechanical properties of a low-clay shale with different absorption times in sub-/super-criticalCO2.Energy,2018,147:1288-12984 Lyu Q,Long XP,Ranjith PG,et al.Experimental investigation on the mechanical behaviours of a low-clay shale under water-based fluids Engineering Geology,2018,233:124-1385 孙可明,张树翠.含层理页岩气藏水力压裂裂纹扩展规律解析分析.力学学报,2016,48(5):1229-1237(Sun Keming,Zhang Shucui.Hydraulic fracture propagation in shale gas bedding reservoir analytical analysis.Chinese Journal of Theoretical and AppliedMechancis,2016,48(5):1299-1237(in Chinese))6 张财贵,曹富,李炼等.采用压缩单裂纹圆孔板确定岩石动态起裂、扩展和止裂韧度.力学学报,2016,48(3):624-635(Zhang Caigui,Cao Fu,Li Lian,et al.Determination of dynamic fracture initiation,propagation,and arrest toughness of rock using SCDC specimen.Chinese Journal of Theoretical and Applied Mechanics,2016,48(3):624-635(in Chinese))7 郑哲敏.关于中国页岩气持续开发工程科学研究的一点认识.科学通报,2016,61(1):34-35(Zheng Zhemin.A little understanding of the scientifiresearch on the continuous development of shale gas in China.Science Bulletin,2016,61(1):34-35(in Chinese))8 谢和平,高峰,鞠杨等.页岩气储层改造的体破裂理论与技术构想.科学通报,2016,61(1):36-46(Xie Heping,Gao Feng,Ju Yang,et al.Volume fracture theory and technical conception of reforming shale gas reservoir.Science Bulletin,2016,61(1):36-46(in Chinese))9 Farrokhrouz M,Asef MR,Kharrat R.Empirical estimation of uniaxial compressive strength of shale formations.Geophysics,2014,79(4):227-23310 韩铁林,师俊平,陈蕴生等.轴、侧向同卸荷下砂岩力学特性影响的试验研究.力学学报,2016,48(4):936-943(Han Tielin,Shi Junping,Chen Yunsheng,et al.Experimental study on mechanics characteristics of sandstone under axial unloading and radial unloading path.Chinese Journal of Theoretical and Applied Mechanics,2016,48(3):936-943(in Chinese))11 陈勉,金衍,袁长友.围压条件下岩石断裂韧性的实验研究.力学与实践,2001,23(4):32-35(Chen Mian,Jin Yan,Yuan Changyou.Study on the experiment for fracture toughness under confinin pressure.Mechanics in Engineering,2001,23(4):32-35(in Chinese))12 陈治喜,陈勉.岩石断裂韧性与声波速度相关性的试验研究.石油钻采工艺,1997,19(5):56-60(Chen Zhixi,Chen Mian.Experimental study on the relationship between rock fracture toughness and acoustic velocity.Oil Drilling and Production Technology,1997,19(5):56-60(in Chinese))13 陈建国,邓金根,袁俊亮等.页岩储层I型和II型断裂韧性评价方法研究.岩石力学与工程学报,2015,34(6):1101-1105(Chen Jianguo,Deng Jinggen,Yuan Junliang,et al.Determination of fracture toughness of modes I and II of shale formation.Chinese Journal of Rock Mechanics and Engineering,2015,34(6):1101-110(in Chinese))14 陈勉,金衍,张广清.石油工程岩石力学.北京:科学出版社,2008(Chen Mian,Jin Yan,Zhang Guangqing.Petroleum Engineering Rock Mechanics.Beijing:Science Press,2008(in Chinese)) 15 HengS,GuoYT,YangCH,etal.Experimental and theoretical study of the anisotropic properties of shale.International Journal of Rock Mechanics and MiningSciences,2015,74(1):58-6816 Liang L,Xiong J,Liu X.Experimental study on crack propagation in shale formations considering hydration and wettability.Journal of Natural Gas Science and Engineering,2015,23:492-49917 何金钢,康毅力,游利军等.矿物成分和微结构对泥质岩储层应力敏感性的影响.天然气地球科学,2012,23(1):129-134(He Jingang,Kang Yili,You Lijun,et al.Effects of mineral composition and microstructure on stress-sensitivity of mudrocks.Natural GasGeoscience,2012,23(1):129-134(in Chinese))18 夏英杰,李连崇,唐春安等.储层砂岩破坏特征与脆性指数相关性影响的试验及数值研究.岩石力学与工程学报,2017,36(1):10-28(Xia Yingjie,Li Lianchong,Tang Chunan,et al.Experiment and numerical research on failure characteristic and brittleness index for reservoir sandstone.Chinese Journal of Rock Mechanics and Engineering,2017,36(1):10-28(in Chinese))19 唐春安,刘红元,秦四清等.非均匀性对岩石介质中裂纹扩展模式的影响.地球物理学报,2000,43(1):116-121(Tang Chunan,Liu Hongyuan,Qin Siqing,et al.Influenc of heterogeneity on crack propagation modes in brittle rock.Chinese Journal of Geophysics,2000,43(1):116-121(in Chinese))20 王士民,朱合华,冯夏庭等.细观非均匀性对脆性岩石材料宏观破坏形式的影响.岩土力。
短裂纹扩展规律及分析方法整理

一、材料疲劳裂纹扩展研究现状许多领域对于材料的疲劳性能有着特殊的要求,以航空、船舶及发动机材料为例,高温抗疲劳性能是关系到可靠性和寿命的一项非常重要的性能指标。
工程实践及理论研究表明,疲劳是导致材料、构件失效的重要因素之一。
据统计,机械零件破坏的50% ~90%为疲劳破坏,而材料约90% 的疲劳损伤寿命都是消耗在裂纹萌生及扩展阶段,因此建立一种既能应用于损伤容限分析,也能应用于耐久性分析的疲劳全寿命预测方法,必须了解其在短裂纹阶段的行为。
二、短裂纹的定义短裂纹的定义有两种其一,从力学角度,将不满足线弹性断裂力学( linear elasticfracture mechanics LEFM) 有效性条件的裂纹统称为短裂纹;其二,从物理学角度,短裂纹是指裂纹长度不超过应力、应变场范围,或者说与塑性区同一数量级的裂纹。
疲劳短裂纹行为具体地可划分为尺度与微观结构特征相当的微观组织短裂纹( microstructure shortcrack,MSC) 行为和脱离微观结构束缚的物理短裂纹( physical short crack,PSC) 行为。
主要涉及短裂纹萌生与扩展机理、寿命预测和短裂纹行为模拟三方面内容。
三、短裂纹萌生机理关于短裂纹的形成有三种解释:第一种解释认为,在疲劳过程中由于材料微观结构的非均匀性,会引起材料力学性能的持续硬化现象,对于微观屈服强度低的晶粒,其循环硬化速率高且饱和值大; 而对于微观屈服强度高的晶粒,其循环硬化速率低、饱和值小。
当某一或某些表面晶粒由于循环硬化而使塑性耗尽时,该晶粒开裂而产生短裂纹。
第二种观点认为,疲劳过程首先由滑移开始。
金相观察发现,在一定循环载荷下,滑移带在较大铁素体晶粒内出现,且载荷越大,有滑移带形成的铁素体晶粒越多,同时个别滑移带逐渐加深或变宽,之后在缺口正表面形成一条或几条在高放大倍数显微镜下看到的细小疲劳裂纹。
第三种说法是,疲劳损伤起因于沿晶短裂纹,高温可以促进晶界滑动,晶界滑移聚集又会促进晶界孔洞的集结和局部扩散的发生,而局部扩散又会促进孔洞成长,因此高温下易于形成沿晶裂纹。
2.3--Griffith微裂纹强度理论

孔洞两个端部的应力几 乎取决于孔洞的长度和 端部的曲率半径,而与 孔洞形状无关。
(孔洞)裂纹 长度2c
平板弹性体孔洞端部的受力情况
A—孔洞端部应力;—外加应力
a—原子间距;
—曲率半径
A = [1+2(c/)1/2]
若为扁平的锐裂纹,则c>> ,c/将很大,略去‘1’,得:
1. 若能控制裂纹长度和原子间距在同一数量级, 则材料可以达到理论强度。(很难做到) 2. 制备高强度材料:E和要大,裂纹尺寸尽可能小。
(P45实例)
这一理论能说明脆性断裂的本质—微裂纹扩展,能解 释强度的尺寸效应。应用于玻璃等脆性材料上很成功, 但在金属与非晶体聚合物时有了很大的误差,即实验 值比计算值大得多。
大于c=(2E/πc)1/2
可以引入扩展单位面积裂纹所需的塑性功p来描述延性 材料的断裂(与前面假设的考虑方向相反,即增加了新生表面 能)。
c=[E(+p)/πc)]1/2
通常p>>,因此,对于金属和陶瓷材料,当E和c相 同的情况下,其临界裂纹长度相差103数量级。(P46)
因此,塑性是阻止裂纹扩展的一个重要因素。
c为断裂应力
前面只考虑了裂纹端部一点的应力,实际上裂纹端部 的应力状态是很复杂的。
Griffith从能量的角度上分析了裂纹扩展的条件:物体 内储存的弹性应变能的降低大于等于开裂形成两个新 表面所需的表面能。反之,前者小于后者,裂纹不会 扩展。因此,物体内储存的弹性应变能的降低是裂纹 扩展的动力。
将单位厚度的薄板拉长至l+∆l,然后固定两端。此时板中储 存的弹性应变能为 ½(F·∆l)。
2.3 Griffith微裂纹强度理论
Griffith(格里菲斯)认为,实际材料中存在许多细小的裂 纹或缺陷。在外力作用下,这些裂纹和缺陷附近产生应 力集中现象。当应力达到一定程度时,裂纹开始扩展而 导致断裂。所以,断裂不是两部分晶体沿整个晶面拉断, 而是裂纹扩展的结果。
☆☆☆带微裂纹物体的有效断裂韧性
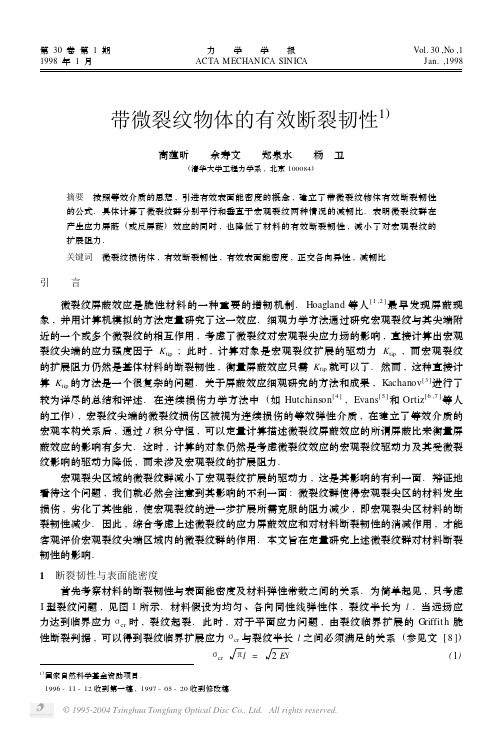
带微裂纹物体的有效断裂韧性1)1)国家自然科学基金资助项目.1996-11-12收到第一稿,1997-05-20收到修改稿.高蕴昕 余寿文 郑泉水 杨 卫(清华大学工程力学系,北京100084)摘要 按照等效介质的思想,引进有效表面能密度的概念,建立了带微裂纹物体有效断裂韧性的公式.具体计算了微裂纹群分别平行和垂直于宏观裂纹两种情况的减韧比.表明微裂纹群在产生应力屏蔽(或反屏蔽)效应的同时,也降低了材料的有效断裂韧性,减小了对宏观裂纹的扩展阻力.关键词 微裂纹损伤体,有效断裂韧性,有效表面能密度,正交各向异性,减韧比引 言微裂纹屏蔽效应是脆性材料的一种重要的增韧机制.Hoagland 等人[1,2]最早发现屏蔽现象,并用计算机模拟的方法定量研究了这一效应.细观力学方法通过研究宏观裂纹与其尖端附近的一个或多个微裂纹的相互作用,考虑了微裂纹对宏观裂尖应力场的影响,直接计算出宏观裂纹尖端的应力强度因子K tip ;此时,计算对象是宏观裂纹扩展的驱动力K tip ,而宏观裂纹的扩展阻力仍然是基体材料的断裂韧性,衡量屏蔽效应只需K tip 就可以了.然而,这种直接计算K tip 的方法是一个很复杂的问题.关于屏蔽效应细观研究的方法和成果,Kachanov [3]进行了较为详尽的总结和评述.在连续损伤力学方法中(如Hutchinson [4],Evans [5]和Ortiz [6,7]等人的工作),宏裂纹尖端的微裂纹损伤区被视为连续损伤的等效弹性介质,在建立了等效介质的宏观本构关系后,通过J 积分守恒,可以定量计算描述微裂纹屏蔽效应的所谓屏蔽比来衡量屏蔽效应的影响有多大.这时,计算的对象仍然是考虑微裂纹效应的宏观裂纹驱动力及其受微裂纹影响的驱动力降低,而未涉及宏观裂纹的扩展阻力.宏观裂尖区域的微裂纹群减小了宏观裂纹扩展的驱动力,这是其影响的有利一面.辩证地看待这个问题,我们就必然会注意到其影响的不利一面:微裂纹群使得宏观裂尖区的材料发生损伤,劣化了其性能,使宏观裂纹的进一步扩展所需克服的阻力减少,即宏观裂尖区材料的断裂韧性减少.因此,综合考虑上述微裂纹的应力屏蔽效应和对材料断裂韧性的消减作用,才能客观评价宏观裂纹尖端区域内的微裂纹群的作用.本文旨在定量研究上述微裂纹群对材料断裂韧性的影响.1 断裂韧性与表面能密度首先考察材料的断裂韧性与表面能密度及材料弹性常数之间的关系.为简单起见,只考虑I 型裂纹问题,见图1所示.材料假设为均匀、各向同性线弹性体,裂纹半长为l .当远场应力达到临界应力σcr 时,裂纹起裂.此时,对于平面应力问题,由裂纹临界扩展的Griffith 脆性断裂判据,可以得到裂纹临界扩展应力σcr 与裂纹半长l 之间必须满足的关系(参见文[8])σcr πl =2E γ(1)第30卷第1期1998年1月力 学 学 报ACTA MECHAN ICA SIN ICA Vol.30,No ,1Jan.,1998其中E为材料的Y oung模量,γ为材料的表面能密度或单位表面张力(对不同材料可在物理手册中查到).另一方面,应力强度因子理论给出了含2l长裂纹的无限大平板的应力强度因子K I;从而可知,与式(1)等价的脆性断裂准则为K I=σπl=K IC(2)其中K IC为材料的断裂韧性(对不同材料可从材料手册中查到).综合(1)和(2)式即得K IC=2Eγ(3)图1 I型裂纹问题Fig11 Mode I crack problem 对于一般二维各向异性问题,文[8]给出了材料断裂韧性和表面能密度及弹性常数之间类似于(3)式的一般关系.对于正交各向异性弹性平面应力问题,其本构关系为ε1=1E1(σ1-υ12σ2)ε2=1E2(-υ21σ1+σ2)ε12=12G12σ12(4)其中,E1,E2,υ12,υ21,G12为材料弹性常数,且满足:υ12/E1=υ21/E2. 这里材料的正交主轴与图1所示坐标轴重合.利用文[8]给出的结果,可以得到K IC=2E2γ1-υ212+E24G12面:-1/2(5) 式(3)和(5)给出了材料的断裂韧性与材料的弹性常数和表面能密度之间的关系.下文将会看到,这些关系提供了确定微裂纹固体有效断裂韧性的一个基础.2 微裂纹体的有效断裂韧性考察一个基体材料为各向同性的弹性体,其中含大量的微裂纹.下面将具体确定该微裂纹体的断裂韧性.按照等效介质的概念,在宏观平均的意义下,这样一个微裂纹体等效于一个均匀弹性体,简称为有效体.微裂纹的不同分布,一般导致有效体的平均或所谓的有效弹性性质呈现出不同的各向异性.当微裂纹完全随机分布时,有效体是各向同性的.考虑I型裂纹平面应力问题,此时其有效材料参数仍满足(3)式所示的关系^K IC=2^E^γ(6)其中符号上方加“^”表示有效体的材料参数,如^E IC,^E,^γ分别表示有效断裂韧性、有效弹性模量和有效表面能密度,下文均采用相同的记法.011力 学 学 报1998年第30卷对于平行分布的微裂纹体,有效体是正交各向异性的.此时,其有效材料参数满足(5)式所示的关系^K IC =2^E 2^γ1-^υ212+^E 24^G 12=-1/2(7) 从(6)和(7)式可以看出,要确定微裂纹体的有效断裂韧性,只需确定微裂纹体的有效弹性常数和有效表面能密度.至此,我们将确定微裂纹体的有效断裂韧性的问题转化为确定其有效弹性常数和有效表面能密度的问题.关于微裂纹有效弹性常数的确定,细观力学已给出许多结果[9],本文将直接引用有关结果.对于包含平行分布(垂直于x 1轴)微裂纹群的二维体,其有效弹性性质为正交各向异性,文[10]给出了考虑微裂纹相互作用二阶效应的有效弹性常数,如下式所示E E 1=1+2ρ+0.373ρ2, υ^υ12=1+2ρ+0.373ρ2G ^G 12=1+11+υ(ρ+0.077ρ2), ^E 2=E , ^υ21=υυ(8)其中ρ为微裂纹密度.图2 微裂纹串接示意图Fig 12 The sketch of connected microcracks 3 有效表面能密度关于有效表面能密度的概念,作者未见前人报导.下面说明这个量的物理意义和确定方法.考察一个含微裂纹群的单位厚度的二维体,其中含一条宏观裂纹.从宏观尺度看,该宏观裂纹是一条直线裂纹,它的表观直线长度为2l ;但是从细观尺度(微裂纹的尺度)看,它实际是一条串接了一些微裂纹的弯折线裂纹(如图2示意),它的实际长度为弯折线的长度,记为2l r ,因此它的实际裂纹面面积为4l r .但是,在单位宽度微裂纹体中形成这个宏观裂纹所产生的新表面面积并不一定是4l r ;因为形成这个宏观裂纹面时,串接过一些微裂纹,即宏观裂纹面中包含着一些与它重合的微裂纹面,设这些微裂纹的长度总和为2l 0.那么,形成这个宏观裂纹所产生的新表面面积为4(l r -l 0).其中这些微裂纹面的表面积4l 0是早在产生宏观裂纹之前就已存在,所以不包括在新表面积中.当2l 0=0时,意味这个宏观裂纹没有串接过任何微裂纹.按照等效介质的概念,上述问题等效于一个有效体中包含着一个相同宏观裂纹的问题.这个宏观裂纹是直线裂纹,有效体是均匀连续的,在其中产生一个宏观裂纹所产生的新表面积为4l .这里有必要指出,有效体为不同于基体的材料,它的表面能密度与基体材料的不同,称为有效表面能密度,用^γ表示.当分别在有效体和微裂纹体中产生一个表观相同的宏观裂纹时,由于问题是等价的,要求消耗相同的能量,因此有4l^γ=4(l r -l 0)γ(9)上式定义了微裂纹体的有效表面能密度为^γ=γl r -l 0l hn (10)111第 1 期高蕴昕等:带微裂纹物体的有效断裂韧性从式(10)可以看出,确定有效表面能密度的关键是确定l r 和l 0,而它们都依赖于宏观裂纹弯折线的路径.在宏观尺度下,这条路径依然是一条表观直线;在细观尺度下确定这条弯折线的路径是困难的,尤其当微裂纹分布较复杂时更难.由于裂纹总是沿阻力最小的路径扩展;所以,在表观路径为直线的前提下,选择使得(l r -l 0)取最小值的路径为实际路径.显然,这个问题需要进一步深入研究,本文仅提出了有效断裂韧性的基本概念,讨论了简单情况.应当注意,当有效性质为各向异性时,有效表面能密度和有效断裂韧性也呈现出各向异性,它们是宏观裂纹取向的函数.下节将通过两个简单例子,说明确定上述有效材料参数的具体方法.4 算 例现在考察微裂纹平行分布的情况,设a 为微裂纹的统计平均半长;d 为沿平行微裂纹方向、相邻微裂纹中心之间距离的统计平均值;hd 为沿垂直微裂纹方向、相邻微裂纹之间距离的统计平均值;如图3所示.此时,先讨论含平行分布微裂纹群(垂直于x 1轴方向,参见图4(a ))的物体,其有效体为正交各向异性弹性体,有效弹性常数如式(8)所示.假设上述描述微裂纹分布规律的参数给定,则微裂纹密度为ρ=πa 2hd 2(11)这里应注意到,为了限制相邻微裂纹间本身没有串接,必须要求:d >2a ,考虑到上式,亦要求:ρ<π/(4h ).图3 微裂纹体及微裂纹分布参数的统计平均值图4(a ) 情况a 图4(b )情况b Fig.3 The microcracked body and the statistical averageFig.4(a )Case a Fig.4(b ) Case bvalue of the parameters for microcrack distribution 当所考察宏观裂纹(长度为2l )的走向与微裂纹平行时,如图4(b )所示.此时,在平行裂纹的方向,单位长度上微裂纹数目的可能最大值为1/d ,最小值为零,取其平均作为平行裂纹方向微裂纹数目的统计平均值,其值为1/(2d ).因此,与宏观裂纹重合的微裂纹的总长度的统计平均值为2l 0=2l ・12d ・2a (12)考虑到上述情况下,宏观裂纹不发生弯折,即l r =l ,并将(12)式代入(10)式得^γ=γ1-a b 面的(13)考虑到式(11)得^γ=γ(1-ρhπ纹没(14)211力 学 学 报1998年第30卷 当所考察宏观裂纹的走向与微裂纹垂直时,如图4(a )所示.与宏观裂纹重合的微裂纹的总长度为2l 0=0,故此时微裂纹体的有效表面能密度就是基体的表面能密度,即^γ=γ(15) 有了上面的准备,就可以确定微裂纹体的有效断裂韧性了.当宏观裂纹与微裂纹垂直时,此时微裂纹垂直于x 1轴,将(8)和(15)式代入(7)式,就得到垂直于微裂纹方向的有效体的有效断裂韧性^K IC ⊥为^K IC ⊥=K IC (22+ρ+0.077ρ2说明1/4≈(1-0.125ρ+0.029ρ2)K IC (16) 当宏观裂纹与微裂纹平行时,此时微裂纹平行x 1轴,将(8)式中有效弹性常数各分量的下标“1”和“2”进行对调,然后和(14)式一起代入(7)式,就得到平行于微裂纹方向的有效体的有效断裂韧性^K IC ||为^K IC ||=K IC 1-ρhπ(1/2(1-0.875ρ+1.015ρ2)(17)图5 情况a 和情况b 下的减韧比Fig 15 The k IC in case a and case b 上文表明,微裂纹体的有效断裂韧性依赖于各向同性基体材料的断裂韧性K IC 及表征微裂纹分布规律的统计参数h 和微裂纹密度ρ.为了图示方便起见,本文规定:微裂纹群垂直和平行于宏观裂纹的两种情况分别称为情况a 和情况b.另外,我们定义有效断裂韧性与基体断裂韧性的比值:k IC =^K IC /K IC 为减韧比,它是一个无量纲量,描述了微裂纹群对材料断裂韧性消减的程度,减韧比越小,有效断裂韧性越小.式(16)和(17)的结果,如图5所示,微裂纹垂直于宏观裂纹情况下的有效断裂韧性明显大于平行情况.5 讨 论1)首先讨论一宏观裂纹嵌含在与其分别垂直和平行分布的两种微裂体中的问题,如图4(a ),(b )所示.按照等效介质概念,上述微裂纹体等效为两种均匀的有效体,然后计算有效体中主裂纹的应力强度因子,发现两种情况的应力强度因子相同,与微裂纹的取向无关[11].此时,如果认为材料的裂纹扩展阻力是基体材料的断裂韧性,那么上述两种情况就会同时起裂,这显然与实际不符.但是,如果同时考虑到微裂纹对断裂韧性的影响,本文结果表明,垂直情况的有效断裂韧性明显大于平行情况,定量结果见图5所示;因此,垂直情况下的宏观裂纹就相对不容易起裂,与实际情况符合.2)如本文前言所述,许多研究表明宏观裂纹尖端区域的微裂纹群会产生应力屏蔽效应,而本文研究表明这个微裂纹群同时会降低裂尖区材料的有效断裂韧性.因此,要客观评价微裂311第 1 期高蕴昕等:带微裂纹物体的有效断裂韧性图6 情况a 和情况b 下的屏蔽比Fig 16 The k I in case a and case b 纹群的影响,必须同时综合考虑其上述两个方面的作用.以I 型静止裂纹平面应力问题为例,本文定量评价微裂纹的减韧和屏蔽效应.当微裂纹垂直于宏观裂纹时,参照文[12]的结果,不难求得屏蔽比为k I ⊥=(1+2.188ρ)-1/2;当微裂纹平行于宏观裂纹时,同理可求得屏蔽比为k I||=(1-0.188ρ)-1/2.上面两种情况的屏蔽比如图6所示,表明垂直情况有较好的屏蔽效果,而平行情况有所谓的反屏蔽效应.比较图5和图6可以看出,宏观裂纹尖端的平行微裂纹群十分有害,大大地降低了裂尖区材料的断裂韧性;而垂直情况下,减韧作用和屏蔽效应综合的结果仍是增韧的,但其增韧效果比不考虑减韧作用有所降低.参 考 文 献1Hoagland RG ,Hahn GT ,Rosenfield AR.Influence of microstructure on the fracture propagation in rock.Roc Mech ,1973,5:77~1062Hoagland RG ,Embury JD.A treatment of inelastic deformation around a crack tip due to microcracking.J A m Cera Soc ,1980,63:404~4103K achanov M.Elastic solids with many cracks and related problem.In :Advances in Applied Mechanics (Edited by Huctchinson J W ,Wu TW ).Academic Press ,New Y ork ,1993,30:259~4284Hutchinson J W.Crack tip shielding by microcracking in brittle solids.Acta Metall ,1987,35:1605~16195Evans A G ,Faber KT.Crack -growth resistance of microcracking brittle materials.J A m Cera Soc ,1984,67:255~2606Ortiz M.A continuum theory of crack shielding in ceramics.J A ppl Mech ,1987,54:54~587Ortiz M ,G iannakopoulos AE.Maximal crack tip shielding by microcracking.J A ppl Mech ,1989,56:279~2838Г.П.切列帕诺夫著.脆性断裂力学.黄克智等译.北京:科学出版社,1990(Cherepanov GP.Mechanics of Brittle Frac 2ture.Mc Graw -Hill ,New Y ork ,1979)9K achanov M ,Tsukrov I ,Shafiro B.Effective properties of cracked solids :critical review of some basic concepts.A ppl Mech Rev ,1992,45:304~33510J u J W ,Chen T -M.Effective elastic moduli of two -dimensional brittle solids with interacting microcracks.Part I :Basic formu 2lations.J A ppl Mech ,1994,61:349~35711杨卫.固体破坏理论的若干问题.见:杨卫,郑泉水,靳征谟主编.走向21世纪的中国力学.北京:清华大学出版社,1996.1~10(Y ang W.Some problems of failure theory of solids ,in :Mechanics in China Facing 21st Century ,eds by Y ang W ,et al.,Beijing :Tsinghua University Press ,1996.1~10(in Chinese ))12冯西桥.脆性材料的细观损伤理论和损伤结构的安定分析.博士论文.北京:清华大学,1995(Feng XQ.Micro -failuretheory for brittle materials and shakedown analysis of structures with damage ,Ph. D.Thesis.Department of Engineering Me 2chanics ,Beijing :Tsinghua University ,1995(in Chinese ))411力 学 学 报1998年第30卷THE EFFECTIVE FRACTURE TOUGHNESSOF MICROCRACKED BODIES 1)1)1)The project supported by the N ational N atural Science Found ation of China.G ao Yunxin Yu Shouwen Zheng Quanshui Yang Wei(Depart ment of Engineering Mechanics ,Tsinghua U niversity ,Beijing 100084,China )Abstract The driving force for the propagation of the macrocrack is reduced by the microcrack zone around the crack tip region of the macrocrack ,meanwhile ,damage is occurred in the macrocrack tip region ,in which the materials is weakened by microcrack damage.Then the fracture toughness of the materials in the macrocrack tip region is decreased.The evaluation of the effect of the microc 2rack damage on the mechanical behavior must take into account both the stress -shield effect and the decreasing effect of the fracture toughness of the materials in the macrocrack tip region.In this pa 2per the effect of microcrack damage on the fracture toughness of the materials are quantitatively in 2vestigated.By considering the microcracked solid as an effective medium and introducing the concept of effective surface energy density ,we derive the formula for the effective fracture toughness of a microcracked body.As an application ,the toughness -reduction ratios are given in the case that all the microcracks are normal to the macrocrack and the case that all the microcracks are parallel to the macrocrack ,respectively.It is shown that the shielding effect functions in the above two cases and the toughness -reduction effect of distributed microcrack are remarkable.K ey w ords microcracked body ,effective fracture toughness ,effective surface energy density ,or 2thotropic elasticity ,toughness -reduction ratio511第 1 期高蕴昕等:带微裂纹物体的有效断裂韧性。
用分数维研究裂纹扩展过程的演化方程
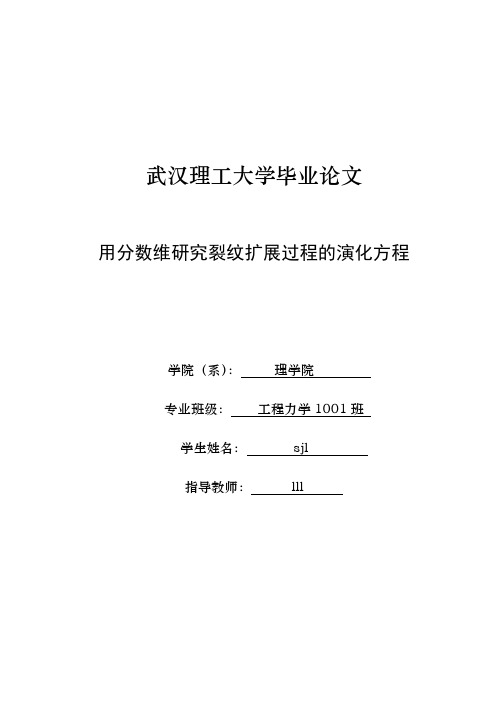
由上述内容可见,对裂纹扩展状况的研究不仅可以充分发挥材料的性能,不造成浪费,减轻地球负担。而且可以对材料性能有更准确的了解,这样就便于人们发现更多新型材料应用于航空航天等各个领域,促进我国科技的发展。由此可见,研究裂纹扩展问题意义重大。
大量实验证明,大部分材料的裂纹并不是平直扩展的。这就表明现在断裂力学中的理论都存在一定的误差。大量结果表明:裂纹扩展存在分形效应。应用分形理论研究裂纹的扩展问题,使得研究结果更具准确性,也为工程应用提供了准确的依据。
15世纪,杰出的艺术家、工程师达·芬奇在实验的过程中发现:直径一定的情况下,铁丝所能承受的断裂载荷与其长度呈反比。这在当时并未给出合理的解释。
1913年,Inglis给出了含有椭圆孔,且无限大的平板的弹性力学精确解。当板受各向均匀应力时,椭圆孔长轴端的最大应力为[2]:
(1.1)
当板受垂直于长轴的单向拉伸时,椭圆孔长轴端的最大应力为:
3. 型裂纹(撕开型裂纹):这类裂纹承受出平面的剪力,裂纹在其自身平面内做平行于裂纹前缘的滑动。
在实际情况中,由于构件所受载荷及构件本身的不对称性,实际裂纹扩展不单单是上述三种情况的某一种情况,而是三种类型的组合,如 - 型、 - 型裂纹等。
1.1.2.2 断裂力学的发展
断裂力学作为固体力学的一个分支,其产生和发展经历了漫长的过程,现对其发展过程进行概述:
(1.4)
其中, 代表材料的表面能, 是裂纹长度, 是材料的弹性模量。Griffith所得出的理论对脆性材料比较合适,但对金属材料却存在着很大的误差。
疲劳与断裂综述

论文题目:疲劳与断裂综述院(系)材料与化工学院专业材料工程姓名学号目录1 绪论 (3)1.1 疲劳及断裂力学发展............................................. 3..1.2 疲劳与断裂力学的关系............................................ 3..1.3 疲劳设计方法4...2 疲劳现象及特点4...2.1 变动载荷和循环应力.............................................. 4..2.2 疲劳现象及特点................................................. 5...2.3 疲劳断口宏观特征................................................ 5..3 疲劳过程及机理6...3.1 疲劳裂纹萌生过程及机理........................................... 6..3.2 疲劳裂纹扩展过程及机理.......................................... 7..4 疲劳影响因素及应对措施................................................ 8..4.1 疲劳强度影响因素................................................. 8..4.2 提高疲劳强度的措施.............................................. 9..5 结束语............................................................. 1..0.1 绪论1.1 疲劳及断裂力学发展日内瓦的国际标准化组织(ISO)在1964年发表的报告《金属疲劳试验的一般原理》中给疲劳下了一个描述性定义:“金属材料在应力或应变的反复作用下所发生的性能叫疲劳” 。
岩石微结构与微裂纹的损伤演化特征
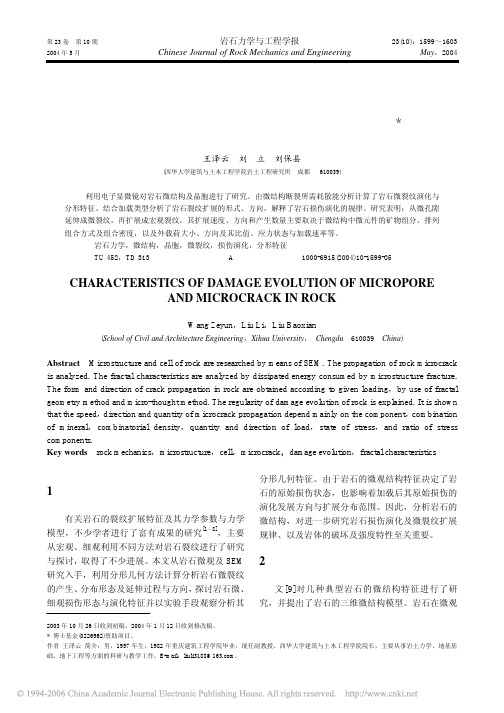
系可从下面的分析计算得知: (26) (27) (28) 将前述石灰岩圆形试件端面的裂纹扩展分布抽 象为图 6 所示的分形模型:试件的裂纹根据实验观 察,主要是径向,而切向较少,且从外周边向内发 展。故分形模型简化为径向裂纹形式。至于少数切 向裂纹则折合入径向裂纹中。该分形模型的源多边 形为图 6(a)所示, 圆中由 3 条裂纹将截面一分为三, 然后再将其中的部分一分为三,如此继续下去,任 意多条裂纹依次类推。因此,当第 1 次出现 3 条裂 纹时,所切割试件外周边相似比为
CHARACTERISTICS OF DAMAGE EVOLUTION OF MICROPORE AND MICROCRACK IN ROCK
Wang Zeyun,Liu Li,Liu Baoxian
(School of Civil and Architecture Engineering,Xihua University, Chengdu 610039 China)
d f −1 d f −1 d f −1
N =5,r = = 2 × ( 2 3 ) 0.115 8 rs = 2.309 5rs (7) df =
1 4
(11) (12)
ln 5 = 1.160 9 ln 4
而沿 1-2′ -3-4-5-6b 和沿 1-2-3-4-5-6a = 2(3.605 6) 0.080 9 rs = 2.218 6rs (8) 与沿 1-2-3-4′ -5-6a 扩展裂纹所具有的分形 维数是相等的,其裂纹扩展所需耗散能为 Gcrit = 2( 4.358 9) 0.093 2 rs = 2.294 1rs = 2(3) 0.261 8 rs = 2.666 5rs (9) (13)
N =5,
损伤土力学-第一三章_完成版
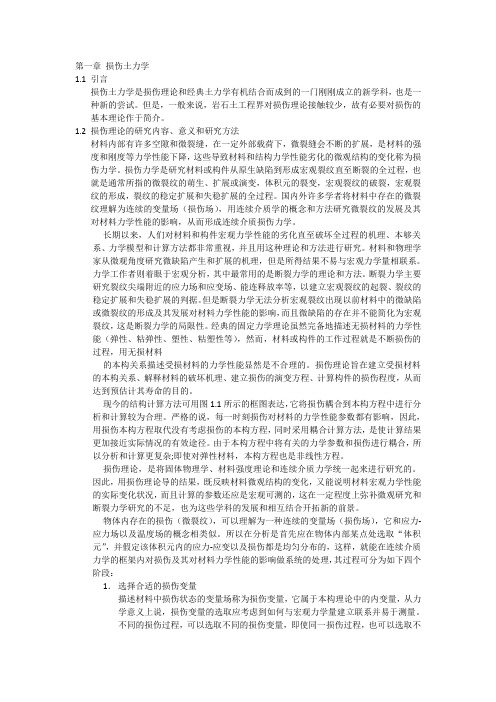
第一章损伤土力学1.1引言损伤土力学是损伤理论和经典土力学有机结合而成到的一门刚刚成立的新学科,也是一种新的尝试。
但是,一般来说,岩石土工程界对损伤理论接触较少,故有必要对损伤的基本理论作于简介。
1.2损伤理论的研究内容、意义和研究方法材料内部有许多空隙和微裂缝,在一定外部载荷下,微裂缝会不断的扩展,是材料的强度和刚度等力学性能下降,这些导致材料和结构力学性能劣化的微观结构的变化称为损伤力学。
损伤力学是研究材料或构件从原生缺陷到形成宏观裂纹直至断裂的全过程,也就是通常所指的微裂纹的萌生、扩展或演变,体积元的裂变,宏观裂纹的破裂,宏观裂纹的形成,裂纹的稳定扩展和失稳扩展的全过程。
国内外许多学者将材料中存在的微裂纹理解为连续的变量场(损伤场),用连续介质学的概念和方法研究微裂纹的发展及其对材料力学性能的影响,从而形成连续介质损伤力学。
长期以来,人们对材料和构件宏观力学性能的劣化直至破坏全过程的机理、本够关系、力学模型和计算方法都非常重视,并且用这种理论和方法进行研究。
材料和物理学家从微观角度研究微缺陷产生和扩展的机理,但是所得结果不易与宏观力学量相联系。
力学工作者则着眼于宏观分析,其中最常用的是断裂力学的理论和方法。
断裂力学主要研究裂纹尖端附近的应力场和应变场、能连释放率等,以建立宏观裂纹的起裂、裂纹的稳定扩展和失稳扩展的判据。
但是断裂力学无法分析宏观裂纹出现以前材料中的微缺陷或微裂纹的形成及其发展对材料力学性能的影响,而且微缺陷的存在并不能简化为宏观裂纹,这是断裂力学的局限性。
经典的固定力学理论虽然完备地描述无损材料的力学性能(弹性、粘弹性、塑性、粘塑性等),然而,材料或构件的工作过程就是不断损伤的过程,用无损材料的本构关系描述受损材料的力学性能显然是不合理的。
损伤理论旨在建立受损材料的本构关系、解释材料的破坏机理、建立损伤的演变方程、计算构件的损伤程度,从而达到预估计其寿命的目的。
现今的结构计算方法可用图1.1所示的框图表达,它将损伤耦合到本构方程中进行分析和计算较为合理。
02--断裂力学-I-II-III裂尖场
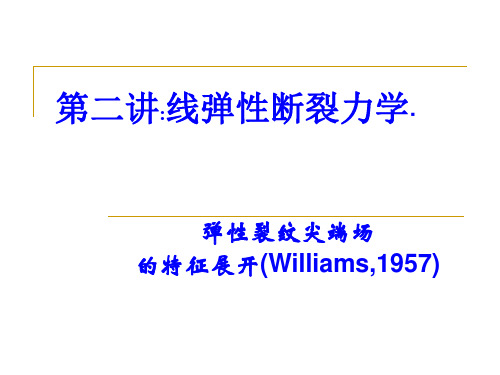
研究内容
1、断裂力学分类 线弹性断裂力学、弹塑性断裂力学、微观断裂力学 2、裂纹的分类
3、断裂发生破坏的几个阶段与断裂力学应用
主要应力分量 位移
xz , yz ;
u 0 , v 0 , w w x, y
III 型反平面剪切问题
复变函数方法在求解裂纹尖端时是相当有效的。 根据复变函数理论,任何解析函数的实部和虚 部都满足Laplace方程,它们构成共轭的调和 函数。 如果知道一个调和函数,则可以由柯西-黎曼 方程求出与之共轭的调和函数。
该方程组有非零解得条件是:
(当 0 时,裂尖位移奇异,当 0 时, 代表刚体位移)
解的一般形式表示为 :
cos 4 1,
1 2
即
3 2
n , 2
n 1, 2,3
z C11 z C12 z C13 z , z C21 z C22 z C23 z .
II 1
Ⅰ型和Ⅱ型裂纹问题
在某些情况下,应力、应变式中的第二项也对 材料的断裂起明显影响,考虑前两项时的应力 场和位移场为:
KI K I II % % + T1 1 + II , 2 r 2 r iK r I I % iu2 II % u1 2 2 r 1 1 II II % iu2 i z % T z T z u1 2 8 4
KI u1 iu2 2
第二项对应着刚体转动 和均 匀的横向应立场 T 的叠加效应
T 在文献中称为T应力,所以
上式中的裂尖场又称为K-T场
线弹性断裂力学
裂纹的基本类型 I型——张开型(opening mode) II型——滑开型(sliding mode) III型——撕开型(anti-plane shear mode)
浅谈岩石损伤力学
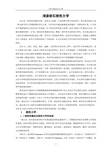
浅谈岩石损伤力学岩石是一种典型的脆性材料,表现出与金属、合金和聚合物不同的特性,根本原因就是它是一种内部含有许多微裂隙的多孔介质。
当外界对其施加能量或者荷载时,其裂纹的扩展、汇合将会严重影响到岩石的宏观力学效能,对工程应用带来重大困难。
而岩石损伤力学就是针对这一问题从微裂纹萌生、扩展、演化到宏观裂纹形成、断裂、破坏的全过程进行研究,旨在通过建立岩土损伤本构模型和损伤演化方程,评价岩土体的损伤程度,进而评估其稳定性。
伴随着大规模的岩石工程建设,损伤力学理论取得了丰硕成果,本文仅对损伤力学在国内外研究现状做一个简要综述。
在矿山、水利、交通、国防、能源、人防等众多的岩体工程中,如何评价岩体的稳定性,进行合理的支护决策,以保证工程的安全建设和营运,是岩土力学领域的一个重要课题。
而岩体工程的失稳大多是由断层和裂隙扩展促成的,在岩土工程中随处可见,例如在地下工程中由于开采引起顶板上覆盖层破坏、围岩松动、里层的形成都是岩体中的微裂隙扩展造成的。
然而岩石是自然界的产物,是由多种矿物晶粒、孔隙和胶结物组成的混杂体。
经过亿万年的地质演变和多期复杂的构造运动,使岩石含有不同阶次随机分布的微观孔隙和裂纹。
在宏观尺度上天然岩体又为多种地质构造面(节理、断层和弱面等)所切割。
这些重要特征表征岩石是一种很特殊很复杂的材料,它不是离散介质(因为它是结晶材料),也不是连续介质,因存在着宏、细、微观的不连续性。
岩石材料实质上是似连续又非完全连续,似破断又非完全破断的介质。
所以岩石材料是极其复杂的非连续和非均质体,它的力学属性具有非线性、各向异性及随时间变化的流变特性。
岩石的变形和破坏特性不但和岩石的复杂结构相关,而且还受温度、围压、孔隙水等环境因素的影响。
然而如何才能将岩石的微裂隙影响和细观断裂机理与岩石宏观力学宏观结合起来,把强度和断裂理论建立于微裂纹演化的细观动力学基础上,从而导出宏观的力学量,更好的解决岩石的稳定和强度问题?成为啦广大岩土工作者必须急待解决的课题,从而岩土理论也取得啦前所未有的发展,通过对岩土介质从微裂纹萌生、扩展、演化到宏观裂纹形成、断裂、破坏的全过程进行研究,通过建立岩土损伤本构模型和损伤演化方程,评价岩土体的损伤程度,进而评估其稳定性。
岩石微裂纹演化的分岔混沌与自组织特征
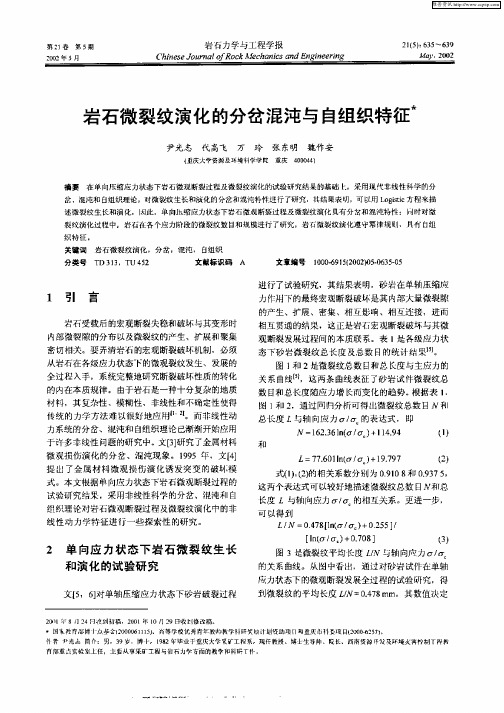
关键词 分类号
岩石5 D 3 3 u4 2 文蘸标识码 A 文章编号 10 -9 2 0 )50 3 ・5 0 06 I(0 20 -6 50 5
进行 了试验 研究 ,其 结果表 明,砂岩在 单轴压缩 应
1 引
言
Ma 2 0 v 02
岩 石 微 裂纹 演化 的分岔 混沌 与 自组 织特 征
尹光志 代 高飞 万 玲 张东明 魏作安
重庆 4 04 ) 0 04 < 庆大 学资源 及环 境科 学 学院 重
摘要
在 单向压缩 应力状态下岩石微观断裂过程及微裂纹演化的试验研究结果 的基础 t,采用现代非线性科学 的分 - .
维普资讯
第2 卷 】
第 5期
20 0 2年 5月
岩 石力 学与工 程学报 C iee ora ok ca i n n ier g hns unlfR c hnc adE gnei J o Me s n
2 () 65 6 9 I :3 ̄ 3 5
2 单 向 应 力 状 态 下 岩 石 微 裂 纹 生 长 和 演 化 的试 验研 究
文【,6对单轴压缩应力状态下砂岩破裂过程 5 ]
201 8闩 2 0 年 4同收 到韧 稿 ,20 年 【 0【 0月 2 9日收 到修 改稿 。
・ 国家 教育 部 J点些盘 (O 06 】5、高 等学 校优 秀青 年教 师教 学科研 装恸 l 一 2 00 1】】 十剧资助项 E和 重庆 市} 蚕项 R 2 O-2 7, l : } (O O6 ) 5 们 着 光忠 简介 : 男,3 9岁 .博十 , 【驼 年毕 业于 重庆太 学来 矿工 程泵 ,现任 教授 、博士 生 导帅 院 长、西 南 资源 开敏 厦环境 炎 害控 制T 程 9 育 部 重点 实验 室土 任 .土要 从事 采矿 工程 与岩 石力 学方 而的 教学 和科研 T佧
失效分析裂纹分析技术

•裂纹的宏观形貌
常见的裂纹宏观形貌有
龟裂纹 线裂纹 环形裂纹 周向裂纹 辐射状裂纹 弧形裂纹
① 龟裂纹外观形貌类似于龟壳网络状分布的一类 裂纹。龟裂纹一般是一种表面沿晶裂纹,深度不大。 由于零件表面(或晶界)的成分、组织、性能 及应力状态与中心(或晶内)不一致,在制造过程或 使用过程中使晶界成为薄弱环节,并产生很大的组 织应力和热应力等内应力,从而使晶界开裂,形成 龟裂纹。龟裂纹按其形成条件,可分为铸造表面龟 裂纹、锻造表面龟裂纹、热处理表面龟裂纹、焊接 龟裂纹、磨削龟裂纹和使用龟裂纹。
金属的表面缺陷,如夹砂、斑疤、划痕、 折迭、氧化、脱碳和粗晶环等 金属的内部缺陷,如缩孔、气泡、疏橙、 偏析、夹杂物、白点、过热、过烧和发纹 等 不仅本身直接破坏金属的连续性,降低材 料的强度和韧性,而且往往在这些缺陷周 围造成很大的应力集中,使得材料在很低 的平均应力下产生裂纹。
②零件形状因素原因引起的裂纹
(3)裂纹分叉法 机械零件在断裂的过程中,出现一条裂纹后,往 往会引伸出多条分支裂纹或分叉裂纹,如图9所示。 裂纹的扩展方向为从主裂纹向分叉或分支裂纹方 向,分叉或分支裂纹汇集的裂纹为主裂纹。 A为主裂纹;BCD为二次裂纹。
(4)断面氧化颜色法 金属零件如暴露在环境介质或高温下会被腐蚀和氧 化,而且腐蚀和氧化的程度会随时间的增加而加重。 主裂纹较次裂纹形成时间早,主断面较次断面暴露 在环境中的时间长,腐蚀与氧化程度严重,腐蚀产 物多、氧化颜色深。 (5)疲劳裂纹长度法 当同一零件上出现多条疲劳裂纹时,一般可根据疲 劳扩展区的长度、疲劳弧线和疲劳条带间距的大小 来判断主裂纹。疲劳裂纹长、疲劳弧线或疲劳条带 间距小的为主裂纹。
一般情况下,疲劳裂纹的末端是尖锐的; 拉痕、发裂纹的末端圆秃; 磨削裂纹一般细又浅,呈龟裂状或规则直 线排列。 由于过热、过烧引起的锻造或热处理裂纹, 往往晶粒粗大,并常在晶界处伴有析出物。
损伤演化路径

损伤演化路径损伤演化路径是指材料在受到外界力量作用下,逐渐发生变化和破坏的过程。
它是材料破坏过程中的重要研究内容,对于材料的设计和使用具有重要的指导意义。
损伤演化路径的研究可以帮助我们了解材料在不同应力条件下的破坏机制,为材料的强度和可靠性分析提供依据。
损伤演化路径可以分为三个阶段:起始阶段、扩展阶段和破坏阶段。
在起始阶段,材料受到外界力量的作用,开始出现微小的损伤。
这些损伤通常是微裂纹、孔洞或晶界处的位错等微观缺陷。
在这个阶段,损伤的形成和扩展速度较慢,材料的强度和刚度基本上不受影响。
随着外界力量的增加,材料进入扩展阶段。
在这个阶段,损伤开始扩展并相互连接,形成更大的裂纹。
这些裂纹会进一步削弱材料的强度和刚度。
材料的应力集中和应变集中效应会加剧裂纹的扩展,导致材料的破坏速度加快。
最终,材料进入破坏阶段。
在这个阶段,裂纹扩展到一定程度后,材料无法再承受外界力量而发生不可逆的破坏。
这时,材料会发生断裂或塑性变形,失去原有的功能。
损伤演化路径的研究可以通过实验和数值模拟等手段进行。
实验可以通过应力-应变曲线、断口形貌等来观察材料的破坏过程。
数值模拟可以使用有限元方法等来模拟材料的应力分布和损伤演化过程。
损伤演化路径的研究对于材料工程和结构设计具有重要意义。
首先,它可以帮助我们了解材料在不同应力条件下的破坏机制,为材料的强度和可靠性分析提供依据。
其次,它可以指导材料的设计和制备,以提高材料的耐久性和使用寿命。
此外,损伤演化路径的研究还可以为工程结构的维修和改进提供参考。
总之,损伤演化路径是材料破坏过程中的重要研究内容,对于材料工程和结构设计具有重要意义。
通过深入研究损伤演化路径,我们可以更好地理解材料的破坏机制,并提出相应的改进措施,以提高材料的性能和可靠性。
金属内部微裂纹愈合内变量及其演化分析

第16卷第2期2004年4月钢铁研究学报JOU RNA L OF IRON AN D ST EEL RESEAR CHV ol.16,N o.2A pr.2004基金项目:国家自然科学基金资助项目(59889101)作者简介:张永军(1969-),男,博士生,讲师; 收稿日期:2002-11-18; 修订日期:2003-03-31金属内部微裂纹愈合内变量及其演化分析张永军, 韩静涛, 韦东滨(北京科技大学材料科学与工程学院,北京100083)摘 要:裂纹愈合是一个不可逆的热力学过程。
笔者在连续介质热力学框架内,由热力学第二定律推导出裂纹愈合耗散不等式,定义了描述金属材料内部裂纹愈合过程的热力学内变量H 。
以铜单晶为例,依据分子动力学模拟结果对铜单晶内部微裂纹愈合过程中愈合内变量的演化趋势进行了定量分析。
关键词:微裂纹;愈合;内变量;演化;金属中图分类号:T G111.9 文献标识码:A 文章编号:1001-0963(2004)02-0059-04Inner Variable of Micro Crack Healing in Metal and Its EvolvementZHANG Yong -jun, HAN Jing -tao, WEI Dong -bin(University of Science and T echnolog y Beijing ,Beijing 100083,China)Abstract:T he crack healing is a t hermodynamic nonreversible process.A dissipation inequation for crack -healing is giv en based on the ther modynamics of continuous medium and second law of thermodynamics.A definit ion of inner var iable to describle the cr ack -healing process is put forw ard.Based on the molecular dy namic simulation,the evolv ement of inner variable of micro crack healing o f pure copper is analysed quantitatively.Key words:micro cr ack;crack -healing;inner variable;evolvement;metal近期的一些研究工作[1~6]初步表明,过去认为只有智能材料才能具有的损伤愈合及性能恢复等能力在金属材料中也有体现。
断口的宏观形貌、微观形态及断裂机理

断口的宏不雅描写.微不雅形态及断裂机理按断裂的门路,断口可分为穿晶断裂和沿晶断裂两大类.穿晶断裂又分为穿晶韧性断裂和穿晶解理断裂(个中包含准解理断裂).沿晶断裂也分为沿晶韧性断裂和沿晶脆性断裂.下面分别加以评论辩论.(1)穿晶韧窝型断口断裂穿过晶粒内部,由大量韧窝的成核.扩大.衔接而形成的一种断口.宏不雅描写:在拉伸实验情形下,老是先塑性变形,引起缩颈,然后在缩颈部位裂纹沿与外力垂直的偏向扩大,到必定程度后掉稳,沿与外力成45°偏向快速成长至断裂.众所周知,这种断口称为杯锥状断口.断口概况光滑不服,无金属光泽,故又称为纤维状断口.微不雅形态:在电子显微镜和扫描电镜下不雅察,断口平日是由大量韧窝衔接而成的.每个韧窝的底部往往消失着第二相(包含非金属搀杂)质点.第二相质点的尺寸远小于韧窝的尺寸.韧窝形成的原因一般有两种形成情形:1)韧窝底部有第二相质点的情形.因为第二相质点与基体的力学机能不合(别的,还有第二相质点与基体的联合才能.热膨胀系数.第二相质点本身的大小.外形等的影响),所以在塑性变形进程中沿第二相质点鸿沟(或穿过第二相质点)易形成微孔裂纹的焦点.在应力感化下,这些微孔裂纹的焦点逐渐长大,并跟着塑性变形的增长,显微孔坑之间的衔接部分逐渐变薄,直至最后断裂.图3-41是微孔穿过第二相质点的示意图.若微孔沿第二相点鸿沟成核.扩大形成韧窝型裂纹后,则第二相质点留在韧窝的某一侧.2)在韧窝的底部没有第二相质点消失的情形.韧窝的形成是因为资估中本来有显微孔穴或者是因为塑性变形而形成的显微孔穴,这些显微孔穴随塑性变形的增大而不竭扩大和互相衔接,直至断裂.这种韧窝的形成往往须要进行很大的塑性变形后才干够实现.是以,在这类断口上往往只有少量的韧窝或少量变外形韧窝,有的甚至经很大的塑性变形后仍见不到韧窝.当变形不大时,断口呈波浪状或蛇形名堂,而当变形很大时,则为无特点的平面.韧窝的外形与应力状况有较大关系.因为试样的受力情形可能是垂直应力.切应力或由弯矩引起的应力,这三种情形下韧窝的外形是不一样的.(2)解理与准解理断口1)解理断口.断裂是穿过晶粒.沿必定的结晶学平面(即解理面)的分别,特殊是在低温或快速加载前提下.解理断裂一般是沿体心立方晶格的{100}面,六方晶格的{0001}面产生的.宏不雅描写:解理断裂的宏不雅断口叫法很多,例如称为“山脊状断口”.“结晶状断口”.以及“萘状断口”等(见图片3-53).山脊状断口的山脊指向断裂源,可依据山脊状正交曲线群剖断断裂起点和断裂偏向.萘状断口上有很多取向不合.比较滑腻的小平面,它们象条晶体一样闪闪发光.这些取向不合的小平面与晶粒的尺寸相对应,反应了金属晶粒的大小.微不雅形态:在电子显微镜下不雅察时,解理断口呈“河道名堂”和“舌状名堂”.2)准解理断口.这种断口在低碳钢中最罕有.前述的结晶状断口就是准解理断口,它在宏不雅上相似解理断口.准解理断口的微不雅形态主如果由很多准解理小平面.“河道名堂”.“舌状名堂”及“扯破岭”构成.沿晶断口是沿不合取向的晶粒鸿沟产生断裂.其产生的重要原因是因为晶界弱化,使晶界强度显著低于晶内强度而引起的.造成晶界弱化的原因很多,例如,锻造进程中加热和塑性变形工艺不当引起的轻微粗晶;高温加热时氛围中的C.H等元素浓渡过高以及炉中残存有铜,渗人晶界;过烧时的晶界融化或氧化;加热及冷却不当造成沿晶界析出第二相质点或脆性薄膜;合金元素和搀杂偏析造成沿晶界的富集;别的沿晶界的化学腐化和应力腐化等等,都可以造成晶界弱化,产生沿晶断口.(1)沿晶韧窝型断口若第二相质点沿晶界析出的密度很高,或因有必定密度的第二相质点再加上晶粒粗大,都邑产生沿晶韧窝型断裂.沿晶韧窝形成的原因与穿晶韧窝雷同.这种断裂的显微裂纹是沿着或穿过第二相质点成核的.显微裂纹的扩大和衔接,陪同随必定量的微不雅塑性变形.在断口概况可看到很多位向不合.无金属光泽的“小棱面”或“小平面”.这些“小棱面”或“小平面”的尺寸与晶粒尺寸相对应(假如晶粒渺小,则断口概况上的“小棱面”或“小平面”用肉眼就不克不及看到或不显著).在电子显微镜下不雅察“小校面”或“小平面”,它是由大量韧窝构成的,韧窝底部往往消失有第二相质点(或薄膜).石状断口和棱面断口都是沿晶韧窝型断口.别的,偏析线也是一种沿晶韧窝型断口.(2)沿晶脆性断口在沿晶脆性断口上,几乎没有塑性变形的陈迹或仅看到少少的韧窝.例如,过烧后的断口,就是沿晶界氧化物薄膜产生的一种沿晶脆性断裂.别的,18-8奥氏体不锈钢沿晶界大量析出碳化物后,也易产生沿晶脆断;沿晶界化学腐化和应力腐化(包含氢脆)后产生的断口,也都是沿晶脆性断口.属于这类断口的还有层状断口和撕痕状断口等.上面介绍的断口微不雅形态,是按照断裂的门路来分类的.而现实临盆中见到的断口有时往往是由几种类型并存的混杂断口.例如,石状断口中,假如“小棱面”或“小平面”不是贯串全部断面,断口经常是沿晶和穿晶混杂断口.在现实临盆中依据缺点断口的宏不雅描写和微不雅形态就可以断定出缺点的类型.缺点产生的原因和应采纳的对策.例如某厂临盆的迫击炮炮尾,在试炮时经常产生折断的情形,经断面实验发明是石状断口,经选区电子衍射剖析确认韧窝底部的析出相颗粒是MnS再联合现场查询拜访以为该缺点产生的原因是终锻前的加热温渡过高,终锻时的变形程渡过小造成的.因为加热温度高,使奥氏体晶粒粗大,并使MnS大量溶入基体,锻后冷却时,MhS 沿粗大的奥氏体晶界析出,造成晶界轻微弱化所致,后来转变预制坯的尺寸以增大终锻的变形量,并下降终锻前的加热温度,问题就美满地解决了.又例如某厂临盆的Cr—Ni—Mo—V钢某种大型轴类锻件,在运行中产生的脆性断裂,经断口磨练发明:此类锻件消失有棱面断口.该锻件用的钢是在5t碱性电弧炉顶用氧化法冶炼的,锭重2.2t,锻造加热温度为1180~1200℃,保温3h以上,锻后立刻送热处理炉进行退火.扩氢处理,然落后行粗加工和调质处理.调质后在两头切取试片,作纵向断口磨练,发明有棱面断口,棱面断口大多出如今大型锻件的心部,而锻件边部仍为正常的纤维状断口,金相组织中有沿原粗大奥氏体晶界的析出相的链状收集.棱面断口的微不雅形态,韧窝内的析出相为不规矩的四边形,呈薄片状,经选区电子衍射肯定为AlN.由AlN的等温析出曲线可见,在约900℃迟缓冷却时,将有大量的AlN析出.依据上述磨练成果剖析以为:1)该Cr—Ni—Mo—V钢大型轴类锻件,其棱面断口主如果在锻造加热时温度较高,保温时光过长,在锻后缓冷进程中,固溶入基体的大量AlN呈薄片状沿粗大的奥氏体晶界呈链状收集析出,造成微孔聚合型沿晶断裂而形成的.奥氏体晶粒越粗大,析出相密度愈高,晶界弱化愈轻微.2)锻造高温加热的时光越长,固溶人基体的AlN越多,随后缓冷进程中形成校面断口的偏向越大,是以恰当掌握锻造加热规范是很重要的.3)因为AlN在奥氏体区析出峰值的温度约为900℃,其析出相随保温时光的延伸而增长.是以,采纳下降待料温度,增长一次过冷工艺,则能加速锻后冷却速度,削减锻件在奥氏体区 AlN析出峰值温度的逗留时光,因而就能克制AlN沿粗大奥氏体晶界的析出.临盆实践证实,这是防止Cr—Ni—Mo—V钢锻件产生棱面断口的有用措施.。
第三章-断裂的微观机制

第三章
断裂的微观机制
3.1 微裂纹形核方式
3.2 位错发射和无位错区
3.3 韧脆判据及韧脆转变的位错理论
第3章 断裂的微观机制
3.1 微裂纹形核方式
在绝大多数情况下,材料的断裂是由微裂纹的形成
和发展引起的。
微裂纹的形核以位错的发射、增值和运动(局部塑
性变形)为先导,是局部塑性变形发展到临界状态的必
第3章 断裂的微观机制
3.1 微裂纹形核方式
3.1.2 微孔聚合形成微裂纹
微孔成核与长大的位错模型:第二相的强度高不可变形
第3章 断裂的微观机制
3.1 微裂纹形核方式
3.1.2 微孔聚合形成微裂纹
微孔形成并逐渐长大后,微孔与微孔之间的横截面面积减小,使得
材料所受的应力增大。
这将促进变形的进一步发展,加快微孔的长大,直至聚合。
同时,材料所受的应力大,促使塑性变形进一步发展,材料产生形
变硬化而强化。
因此,基体材料的形变强化指数越高,形变强化的作用越大,则微
孔长大的过程就越慢,材料的塑性和韧性就越好。
第3章 断裂的微观机制
3.1 微裂纹形核方式
3.1.3 空位聚合成空洞形成微裂纹
对高纯度的金属材料或单相合金,在拉伸断裂也呈现韧窝断口,材
致原子键断裂从而使微裂纹形核。
第3章 断裂的微观机制
3.1 微裂纹形核方式
3.1.6 应力集中使原子键断裂形成微裂纹
金属材料(金属间化合物)拉伸时裂尖首先发射位错,即裂尖前方
存在一个屈服区,其中最大应力(它就等于有效屈服应力σys ):
m ax y s Q s
考虑加工硬化,Q也不会大于5,故可认为:
第十二章微裂纹的演化

第⼗⼆章微裂纹的演化第⼗⼆章微裂纹的演化显微观察表明,岩⽯的破坏不是⼀下⼦从原始状态就突然发⽣的,它要经历微裂纹的萌⽣、发育、成核等⼀系列演化过程。
§1.2所提到的岩⽯的不连续结构有许多是在原始形成时就存在的。
形成这些不连续结构的机理⾮常复杂。
例如,在冷却过程中因各局部膨胀系数不同就可能形成部分缺陷和微裂纹。
§12.1 热缺陷与热激活在⼀定环境下,微破裂从分⼦尺度,从分⼦键的尺度开始,形成热缺陷。
这种理论被称之为热激活理论。
根据热⼒学和统计物理,分⼦运动速度的最可⼏分布为波⽿兹曼分布。
根据量⼦理论,对于⼀个由N 个原⼦组成的晶体体系的热运动来说,这个体系相当于⼀个由3N 个质量为m , 弹⼒为f 的独⽴的单维简谐振⼦组成的体系,晶体中分布在能级)v (∈上的单维简谐振⼦数为kT e QN n /)v (3)v (∈-=(12.1) 其中k 为波⽿兹曼常数,T 为绝对温度, )v (∈为这些处于量⼦状态的能量或振⼦的能谱νh )21v ()v (+=∈ = ,2 ,1 ,0v (12.2) 式中h 为普朗克常数,ν为为简谐振⼦的基本频率,Q 为配分函数∑∈-=j kT e Q /)v (∑+=j kT h e/)21v (νkT h kT h e e //211νν---= (12.3) 根据量⼦理论,即使在低能级下,也总有⼀定概率的原⼦能通过隧道效应,“渗透”过原有势阱,形成缺陷。
产⽣缺陷的原因,除原⼦空间的⽆序和不成对电⼦⾃旋取向分布的⽆序以外,晶体中还可以出现偏离点阵周期性的缺陷。
晶体的缺陷可以分为点缺陷和和线缺陷等。
线缺陷的主要形式是位错。
点缺陷⼀般指空位和填隙原⼦等缺陷,⽽这样的缺陷在达成平衡的晶体中是按照热⼒学规律的要求形成和增减的,我们称之为热缺陷。
我们可以引⼊似化学平衡法,将晶体中有序-⽆序转化过程和缺陷的⽣成过程模拟为⼀个似化学反应。
根据阿累尼乌斯⽅程和过渡理论,这种似化学反应基本过程的速度常数为∈-=KT A k N*1exp ? (12.4) 其中1∈?为活化能,A 为指数前因⼦或频率因⼦。
- 1、下载文档前请自行甄别文档内容的完整性,平台不提供额外的编辑、内容补充、找答案等附加服务。
- 2、"仅部分预览"的文档,不可在线预览部分如存在完整性等问题,可反馈申请退款(可完整预览的文档不适用该条件!)。
- 3、如文档侵犯您的权益,请联系客服反馈,我们会尽快为您处理(人工客服工作时间:9:00-18:30)。
微裂纹的分形分布及损伤演化过程的分形机理
考虑一弹性体包含N T条相互平行、半长为c、宽为W的椭圆型微裂纹,并承受边界应力σ(见图1)。
假设由微裂纹之间相互作用而引起的弹性能可以忽略不计,这N T个体积单元中的微裂纹是彼此独立的困。
这样对应于损伤区发育初期,由这N T条裂纹构成的裂纹群所引起的自由能变化为:
ΔF = N T W ( -B2 σ2 <c2 > + 4γ <c>)(1a)
对应于每个裂纹单元的平均自由能为:
< ΔF > = W ( -B2 σ2 <c2> + 4γ <c>)(1b)
式中E,y—杨氏模量,单位面积表面能B2=π/E
作为二维问题,对应于相互平行的椭圆型拉伸裂纹,总损伤体积可定义为:V d =πN T W<c2>总裂纹面积:A d =4N T W<c>,<c>表示裂纹半长在(c0,c1)范围内其概率分布的数学期望值。
这里c0为最小的裂
纹半长(假设为常量),c l为最大裂纹半长。
以<Ac>表示单一裂纹面积,由方程(1),取,可得到同一表达式:
(2)
这个方程只有当<c2>与<c>彼此互为函数关系时才有意义,因此无一般解。
但对于常值c0,微裂纹分布为分形分布时,(2)式能有解析解。
类似于Griffith应变能释放率,定义分形微裂纹群的应变能释放率(对应N T条裂纹群情况)
(3)
则动态破坏准则为了G,>G c=2γ。
这里U为整个系统的应变能,正比于损伤体积。
数学期望<·>表示每个裂纹单元内参量的平均值,这样当裂纹趋于1时,G/就还原到单裂纹体的应变能释放率G0在裂纹群损伤演化过程中,微小裂纹对损伤断裂的影响应当受到重视,特别是在流体和固体相互作用的应力腐蚀环境中。
假设在区域(G0,G c)内应力腐蚀将引起稳定的裂纹损伤演化。
G0为应变能释放的最小值,它对应于亚临界裂纹扩展的起始点。
当G<G0时裂纹发生愈合,因此c Q 对应为给定外应力σ下由于应力腐蚀而引起扩展的最小裂纹尺寸。
这种应力腐蚀现象的存在导致了一个稳定的自由能最小值,因为在应力低于动态破坏强度以下,附加了在裂尖以应力腐蚀反应为形式的流体和固体相互作用所对应的自由能的(负)贡献。
如果这种流固相互作用仅发生在裂纹表面上,那么这种效应可由物理化学释放率y,来反映(替代y)。
当裂纹扩展速率增加到动态扩展速率时,裂尖流体的扩散速率就抑制住应力腐蚀。
这时机械能支配裂纹扩展,y,_y。
如没有应
力腐蚀的影响,则最大(主)裂纹控制整个材料破坏。
Griffith忽略了这种现象,只考虑机械自由能,也就忽略了大量更小的裂纹对材料损伤破坏的贡献。
然而实验室和现场资料(特别是岩石材料)都证实了这些小裂纹的重要性,尤其是在损伤初期。
图2给出了单一扩展裂纹从亚临界到临界状态的转化示意图。
图2 单一扩展裂纹从压临界到临界状态的转化示意图
类似于Griffith准则,方程(2)和(3)允许在自由能不变的条件下,材总的损伤面积仍可增加,对于常值N T,亚临界裂纹的扩展条件可改写为:
(4)
这样G,同时反映了由于力学和化学的共同作用而产生的总裂纹面积及损伤体积的变化程度。
从方程(4)可以看到这样一个事实:机械能贮存于体积中,但在裂纹扩展过程中而释放于表面上。
由方程(3)知,G,的确定得先已知裂纹长度分布的一阶和二阶矩,即<c>和<c2>。
大量研究已发现材料损伤演化过程中微裂纹长度满足分形分布,即裂纹半长的概率分布为:
P (c ≥ x)=( c / c0 )-D(5)
当D∈(0,3)为裂纹分布的分维,根据方程(5),可计算出裂纹半
长为i的矩阵(i≠D)
(6a)
当i=D时
(6b)
应当注意到,当D>1时<c>和总损伤面积A d主要由大量的小裂纹支配。
而D<1时Ad主要是大(主)裂纹的贡献,因为裂纹长度增加后产生应力集中。
这样D=1体现了从稳定态向失稳态过渡的临界点。
稳态状况下,大量小裂纹的贡献在于使裂纹总面积的增加(D>1),而当D<l时,由于损伤演化导致宏观裂纹的应力集中,使得最大裂纹产生新的裂纹面积,引起非稳定态断裂。
当假定微裂纹分布是自相似分形分布,则D为常数,N T可以变化。
这样由方程(3)可以确定修正德Griffith能量释放率:
(7)
由方程(6)可知,当D≠1,2时
(8)
当D=2时
(9)
当D=1时
(10)
式中x=c1/c0。
图3给出了由方程(7)定义的对于不同N T值的修正Griffith能量释放率G,/G。
的平方根(定义。
C=-1)与分维D的相关曲
线,可以看到材料的断裂韧度负相关于微裂纹布的分维D。