大型铸钢件用醇基锆英粉
大型铸钢件用醇基锆英粉涂料的研制与应用

大型铸钢件用醇基锆英粉涂料的研制与应用陈展飞;田秀成;费长正;刘文瑞;刘健【摘要】介绍了大型铸钢件用醇基锆英粉涂料的组成、生产工艺路线及其工艺性能特征,研究了醇基铸造涂料的选材、生产工艺等对涂料性能的影响.该涂料抗粘砂能力强,悬浮性、刷涂性、流平性优异,一次刷涂所得涂层厚度高,适用于各种铸钢件尤其是大型铸钢件的生产,可有效地防止粘砂等缺陷,获得表面质量优良的铸件.【期刊名称】《大型铸锻件》【年(卷),期】2006(000)004【总页数】3页(P17-19)【关键词】锆英粉;大型铸钢件;涂料;悬浮;流平性【作者】陈展飞;田秀成;费长正;刘文瑞;刘健【作者单位】德阳立达化工公司,四川,618000;德阳立达化工公司,四川,618000;德阳立达化工公司,四川,618000;德阳立达化工公司,四川,618000;德阳立达化工公司,四川,618000【正文语种】中文【中图分类】TG21 前言随着铸造业的不断发展,必将对各种铸件的表面质量提出越来越高的要求。
在砂型(芯)工作表面施涂铸造涂料是造型工艺中一道非常重要的工序,铸造涂料的作用主要有:降低铸件的表面粗糙度,防止或减少铸件粘砂、夹砂、砂眼缺陷,调整铸件表面成分和表面组织,提高铸件落砂和清整效率等。
铸造涂料质量的高低,直接影响着铸件的表面质量水平。
当前国内虽有众多的铸造涂料生产企业,但其产品技术质量水平与国外先进产品尚存在着较大的差距,不能满足铸件尤其是大型铸件生产对铸造涂料的质量要求,目前各大型铸钢件生产企业使用的铸造涂料主要依赖进口。
针对这种现状,我们以国外先进的铸造涂料产品作参照,通过多次反复实验,研制出了各项工艺性能与国外同类产品水平相当,可完全满足大型铸钢件浇铸工艺要求的优质醇基锆英粉涂料。
2 大型铸钢件用醇基涂料的组成醇基铸造涂料的成分主要有耐火填料、悬浮剂、粘结剂、有机溶剂、附加剂等。
涂料原辅材料的选择和配比是影响涂料性能的决定性因素,因此,原辅材料品种及配比的确定是本产品研制过程中最关键的环节。
铸造涂料配方技术

锆英粉的主要成分是ZrO2、SiO2,即正硅酸锆。
它的耐火度高,是目前用于消失模铸造最好的一种抗粘砂材料。
浇注铸钢件和大型铸铁件时多采用这种耐火材料,可以减少铸件的清理工作量,获得表面光洁的铸件。
醇基铸造涂料优点:1、涂刷点燃后,型、芯表面的涂料层可自行烘干,不用进烘干窑;2、使用方便,生产周期短;3、可应用水玻璃砂的型、芯。
铸件粘砂是因为涂料没有有效起到阻挡隔离作用,或涂料与高温金属液体发生化学反映。
1.涂料附着力差:填砂震动时造成涂料剥落,引起铸件粘砂,2.涂料膨胀系数大:与高温金属液体接触时涂料受热体积膨胀脱离铸型导致铸件粘砂。
3.高温液体金属被氧化与涂料和铸型发生化学反应生成金属氧化物,对涂料和型砂都有极强的粘结性,能够将型砂牢固粘附在铸件表面上形成一系列的低熔点化合物〔在铸件厚壁及转角处等,低熔点物更多,粘砂层更后),造成铸件粘砂,有时虽未产生粘砂,但在铸件表面粘附上一层难以清除的涂料,及产生粘灰。
铸件砂眼:1、铸型内有掉入的砂子。
2、涂料强度低,耐火差,经不住高温金属液体的冲刷,型砂被卷入铸件。
铸件气孔产生的原因很多,总之一句话就是因为铸型中存在较多发气量大的物质,发气速度快,涂料或被砂透气性差,气体未及时排除所致。
普通铸造涂料只是在铸件和铸型中间起到阻挡隔离作用,达到防粘砂目的,但普通铸造由于涂料附着力差、强度低、耐火差、发气量大,容易造成铸件产生粘砂、砂眼、气孔、碳渣等缺陷。
新型铸造涂料是在传统铸造涂料基础上加以改进,调整,能有效防止高温液体金属氧化,与铸型和高温液体金属接触过程中不起化学反应。
并且能吸收消化含氮、硫、碳等气体。
从而彻底解决: 铸件粘砂,铸件砂眼,铸件粗糙,铸件气孔,铸件夹杂〔渣〕,球磨铁变异,铸钢渗硫裂纹,增碳缺陷等。
铸造用的树脂砂一般是呋喃树脂砂;呋喃树脂砂又分为:糠醇呋喃树脂、脲醛呋喃树脂、酚醛呋喃树脂等铸造用树脂都要求控制甲醛的含量,游离甲醛在造型、造芯时会刺激人的眼、鼻、喉等器官,而且树脂砂在浇铸时发气量大。
铸造用锆砂、粉

行业标准《铸造用锆砂、粉》解读1 标准概况在铸造生产中,锆砂主要用于大型厚壁铸钢件、铸铁件的型(芯)砂,锆粉主要用于型砂铸造用涂料。
目前,伴随我国铸造行业的快速发展,对铸件质量要求的提高,铸件尺度的增大,使用铸造用锆砂、粉的需求量有不断增大的趋势。
新修订的标准有效解决了标龄老化问题,缩短铸造用锆砂、粉技术指标与国际先进水平的差距,有力推动我国造型材料的发展。
本标准是对JB/T 9223-1999《铸造用锆砂》的修订,由苏州兴业材料科技股份有限公司(原苏州市兴业铸造材料有限公司)负责起草,2012年10月由全国铸造标委会造型材料分技术委员会在苏州组织行业专家对送审稿进行审查,对标准送审稿作了进一步的修改、整理和完善,形成了标准报批稿。
2 新旧标准主要内容差异2.1 名称将JB/T 9223-1999《铸造用锆砂》改名为《铸造用锆砂、粉》,锆砂在铸造生产中作为原砂的应用量并不多,但在型砂铸造用涂料中却大量应用。
因此,新标准中增加了锆粉的内容,不仅增加标准的适用性,扩大了标准的适用范围,而且对行业发展更具有现实的指导意义。
2.2 范围本标准规定了铸造用锆砂、粉的术语和定义,分级、分组及牌号,技术要求,试验方法,检验规则以及包装、标志、运输、贮存和质量证明书。
本标准适用于铸造生产造型(芯)用锆砂、粉。
2.3 规范性引用文件新标准中引用了7项国家和行业标准,全部为非注日期引用,比旧标准增加了GB/T 4984《含锆耐火材料化学分析方法》、GB/T 5611《铸造术语》、GB/T 9442《铸造用硅砂》、GB 11743《土壤中放射性核素的γ能谱分析方法》及JB/T 9156《铸造用试验筛》等5个引用标准,比旧标准查询更方便。
2.4 术语和定义旧标准中只规定峰值含量、酸耗值二个定义,新标准中增加了除GB/T 5611《铸造术语》中界定的术语和定义外,还有铸造用锆砂、粉,含水量,含泥量,原砂细度,细粉含量五个术语及定义;删除了峰值含量定义。
锆英砂、锆英粉、硅酸锆、氧化锆浅析

2硅酸锆
• 硅酸锆(ZrSiO4)俗称矽酸锆,是由天然锆英石经 超细粉碎,除铁,钛加工,表面改性处理等工艺加 工而成。其产品属于化工产品类,主要用作陶瓷坯 釉的乳浊剂。
• 我们的研究以为,硅酸锆在陶瓷坯釉料主要有如下 作用:①乳浊(避光)、增白;②加强坯体强度; ③增强抗水解性;④增强硬度和耐磨度 。 • 值得强调的是,硅酸锆之所以被应用是因为它能同 时起到以上四种作用,在我们的研究中,且不要只 强调其一,而忽略其他。
锆英砂、锆英粉、硅酸锆、化 学锆、锆陶瓷结构件浅析
山东金澳科技新材料有限公司 +86-0543-2518008 2012.12.10
1、天然锆族矿物
• 锆英石:为正方晶系,常呈短小柱状出现,颜色有白色、黄色、暗褐色 到黑色等,具有金刚光泽。锆英石为正硅酸锆,一般分子式为ZrSiO4, 但在锆英石中,总含有百分之零点几到百分之几的铪,所以正确的应当 写成(Zr、Hf)SiO4。锆英石一般为非磁性,非导体,但也有些含铁质 多一些的变种锆英石呈弱磁性。 • • 斜锆石:为单斜晶系,常呈板状晶体,其颜色有白色、褐色、黄色和黑 色等。具有玻璃和油脂光泽,呈非磁性。斜锆石的分子式为ZrO2,有时 含有铪、铁、钛等杂质,在最纯的斜锆石中含ZrO2可达98%,一般的含 ZrO2为75%—83%。
• 现在工业上对锆英石砂矿的要求为含ZrO2> 0.5%(矿物量为>3公斤/米3)。国外锆英石 的储量为3.282万吨。主要在美国、印度、澳 大利亚、巴西等国。锆英石精矿一般要求 ZrO2为65%左右。
2、锆英砂、锆英粉、硅酸锆
• 他们三个的化学式都是ZrSiO4(硅酸锆),结构表达式为 ZrO2•SiO2。但是正是因为锆英石这种东西,其晶体结构有较 高的天然结晶强度,使得它在不同的度范围内有不同的用途, 而且用于不同的行业。例如,锆英砂是锆英石的天然形状,它 主要是有含锆英石的海砂中经选矿而成,我们在市场上称之为 锆英砂精矿。锆英粉用于耐火材料,精密铸造等行业,硅酸锆 用于陶瓷中。并且随着磨矿技术的提高,所用量比例也在于发 生着变化,例如,硅酸锆的用量,近几年随着陶瓷行业的大量 应用,而占到了整个锆砂供应量的50%。因此锆英砂、锆英粉、 硅酸锆的种类均已客观存在,并在同行业的人所熟知,反应了 他们适用的广泛性,但化学组成和矿物组成结构是一种物质, 即锆英石或ZrSiO4(硅酸锆),下面以图示简述这一过程:
铸钢用新型醇基涂料的研制与应用
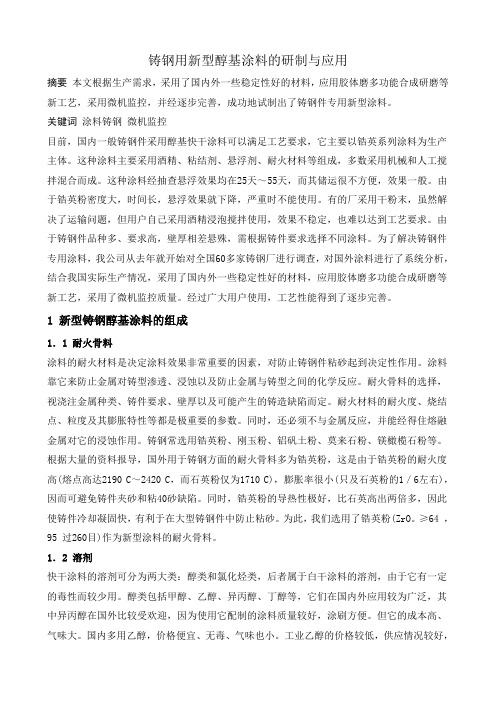
铸钢用新型醇基涂料的研制与应用摘要本文根据生产需求,采用了国内外一些稳定性好的材料,应用胶体磨多功能合成研磨等新工艺,采用微机监控,并经逐步完善,成功地试制出了铸钢件专用新型涂料。
关键词涂料铸钢微机监控目前,国内一般铸钢件采用醇基快干涂料可以满足工艺要求,它主要以锆英系列涂料为生产主体。
这种涂料主要采用酒精、粘结剂、悬浮剂、耐火材料等组成,多数采用机械和人工搅拌混合而成。
这种涂料经抽查悬浮效果均在25天~55天,而其储运很不方便,效果一般。
由于锆英粉密度大,时间长,悬浮效果就下降,严重时不能使用。
有的厂采用干粉末,虽然解决了运输问题,但用户自己采用酒精浸泡搅拌使用,效果不稳定,也难以达到工艺要求。
由于铸钢件品种多、要求高,壁厚相差悬殊,需根据铸件要求选择不同涂料。
为了解决铸钢件专用涂料,我公司从去年就开始对全国60多家铸钢厂进行调查,对国外涂料进行了系统分析,结合我国实际生产情况,采用了国内外一些稳定性好的材料,应用胶体磨多功能合成研磨等新工艺,采用了微机监控质量。
经过广大用户使用,工艺性能得到了逐步完善。
1 新型铸钢醇基涂料的组成1.1 耐火骨料涂料的耐火材料是决定涂料效果非常重要的因素,对防止铸钢件粘砂起到决定性作用。
涂料靠它来防止金属对铸型渗透、浸蚀以及防止金属与铸型之间的化学反应。
耐火骨料的选择,视浇注金属种类、铸件要求、壁厚以及可能产生的铸造缺陷而定。
耐火材料的耐火度、烧结点、粒度及其膨胀特性等都是极重要的参数。
同时,还必须不与金属反应,并能经得住熔融金属对它的浸蚀作用。
铸钢常选用锆英粉、刚玉粉、铝矾土粉、莫来石粉、镁橄榄石粉等。
根据大量的资料报导,国外用于铸钢方面的耐火骨料多为锆英粉,这是由于锆英粉的耐火度高(熔点高达2190 C~2420 C,而石英粉仅为1710 C),膨胀率很小(只及石英粉的1/6左右),因而可避免铸件夹砂和粘40砂缺陷。
同时,锆英粉的导热性极好,比石英高出两倍多,因此使铸件冷却凝固快,有利于在大型铸钢件中防止粘砂。
铸造涂料方法用途
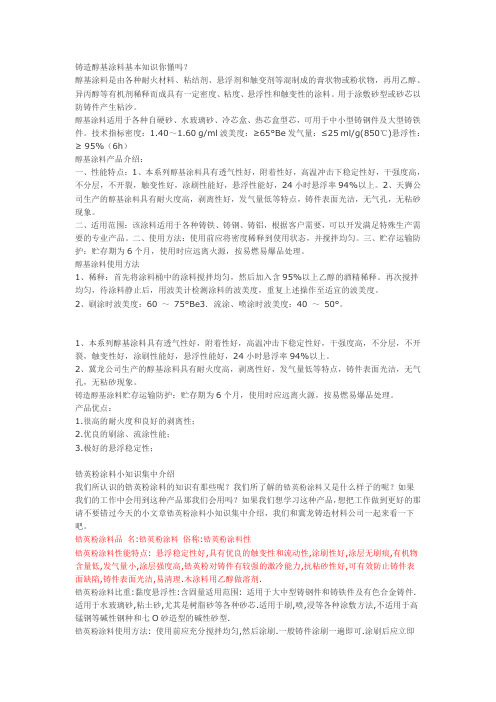
铸造醇基涂料基本知识你懂吗?醇基涂料是由各种耐火材料、粘结剂、悬浮剂和触变剂等混制成的膏状物或粉状物,再用乙醇、异丙醇等有机剂稀释而成具有一定密度、粘度、悬浮性和触变性的涂料。
用于涂敷砂型或砂芯以防铸件产生粘沙。
醇基涂料适用于各种自硬砂、水玻璃砂、冷芯盒、热芯盒型芯,可用于中小型铸钢件及大型铸铁件。
技术指标密度:1.40~1.60 g/ml波美度:≥65°Be发气量:≤25 ml/g(850℃)悬浮性:≥ 95%(6h)醇基涂料产品介绍:一、性能特点:1、本系列醇基涂料具有透气性好,附着性好,高温冲击下稳定性好,干强度高,不分层,不开裂,触变性好,涂刷性能好,悬浮性能好,24小时悬浮率94%以上。
2、天狮公司生产的醇基涂料具有耐火度高,剥离性好,发气量低等特点,铸件表面光洁,无气孔,无粘砂现象。
二、适用范围:该涂料适用于各种铸铁、铸钢、铸铝,根据客户需要,可以开发满足特殊生产需要的专业产品。
二、使用方法:使用前应将密度稀释到使用状态,并搅拌均匀。
三、贮存运输防护:贮存期为6个月,使用时应远离火源,按易燃易爆品处理。
醇基涂料使用方法1、稀释:首先将涂料桶中的涂料搅拌均匀,然后加入含95%以上乙醇的酒精稀释。
再次搅拌均匀,待涂料静止后,用波美计检测涂料的波美度,重复上述操作至适宜的波美度。
2、刷涂时波美度:60 ~75°Be3.流涂、喷涂时波美度:40 ~50°。
1、本系列醇基涂料具有透气性好,附着性好,高温冲击下稳定性好,干强度高,不分层,不开裂,触变性好,涂刷性能好,悬浮性能好,24小时悬浮率94%以上。
2、冀龙公司生产的醇基涂料具有耐火度高,剥离性好,发气量低等特点,铸件表面光洁,无气孔,无粘砂现象。
铸造醇基涂料贮存运输防护:贮存期为6个月,使用时应远离火源,按易燃易爆品处理。
产品优点:1.很高的耐火度和良好的剥离性;2.优良的刷涂、流涂性能;3.极好的悬浮稳定性;锆英粉涂料小知识集中介绍我们所认识的锆英粉涂料的知识有那些呢?我们所了解的锆英粉涂料又是什么样子的呢?如果我们的工作中会用到这种产品那我们会用吗?如果我们想学习这种产品,想把工作做到更好的那请不要错过今天的小文章锆英粉涂料小知识集中介绍,我们和冀龙铸造材料公司一起来看一下吧。
铸件技术要求[1]
![铸件技术要求[1]](https://img.taocdn.com/s3/m/2e7ce220aaea998fcc220ea7.png)
铸件技术要求及各主要工序的控制要点一.铸件技术要求1.铸件重量3.1吨;浇冒口重量2吨;箱重5.1吨。
金属收得率61%。
2.冒口12只。
其中保温冒口4只;普通暗冒口4只;明冒口4只(按原来的不变)。
3.增加成型冷铁8块;原来每只侧法兰外端面的6块冷铁该为3块方冷铁,其余冷铁按原来的排放不变。
4.浇注系统均由陶管排出。
5.砂箱高度:上箱总高度≥800MM;下箱总高度≥700MM。
6..冷铁需喷丸除锈。
表面无污物、粘砂等。
7..型砂采用面、背砂。
外模表面覆盖50-100MM厚度的新砂,其余用旧砂。
8.出气棒直径为30MM。
二.各主要工序的控制要点1.型砂1)型砂抗压强度2.8—3.2MPa;表面稳定性≥90%,型砂可使用时间5-10分钟。
2)需测定树脂、固化剂以及砂的流量(作好现场记录)。
配比准确后才可造型、制芯。
2造型、制芯1)树脂,固化剂加入混砂机料捅时必须镇静10分钟,待其沉淀;气体逸出后才可开机工作。
、2)造型、制芯之前按图纸检查模型、冒口、冷铁、出气棒、浇注陶管等是否符合要求。
3)混砂机停机后、开机前必须丢掉头砂、尾砂。
4)造型、制芯时,开机放砂前必须将冒口、冷铁;出气棒;芯骨、浇注陶管等准确排放。
模型表面,冷铁、活块,出气棒根部的型砂必须拍紧实,模型、冒口深凹处的型砂要捣紧实,上述操作必须在型砂可使用时间内完成。
5)每节浇注陶管必须准确对接,避免陶管之间的型砂被钢水冲刷到型腔中。
(可用胶带纸将各陶管连接,作好造型前的准备工作)6)保证砂型,坭芯的气眼通畅。
3.涂料1)起模2小时后上第一次涂料.,涂料前需吹扫砂型、坭芯上的浮砂。
2)采用锆英粉醇基涂料,浓度适当,涂刷2-3遍。
3)涂刷均匀,气眼、字板处防止涂料堆积。
4..配模、合箱1)砂型,坭芯需用喷灯烘烤。
2)坭芯落入下箱中,需检查壁厚是否均匀。
上箱的出气孔必须通畅。
型腔内尖角砂、浇注陶管内的浮砂等夹杂物吹扫干净。
3)合箱后检查型内是否有错边,夹杂物等,明冒口覆盖报纸防止落入杂物。
铸造用涂料的分类及配比
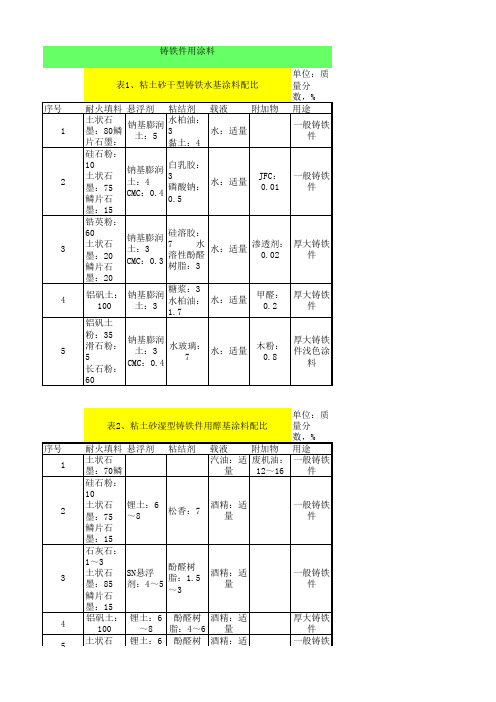
序号 1 2
3 4 5 6
序号
1 2
3 4 5 6 7 8
土状石 锂基膨润 酚醛树脂:4 乙醇:适量 黏土:2 一般铸铁件 墨:80鳞 土:3 硅石粉:70 有机膨润 松香:6 乙醇:适量 氧化铁:5 一般铸铁件 土状石墨:20 土:4 鳞片石墨:10 PVB:0.5 硅石粉:60 有机膨润 酚醛树 乙醇:适量 铁白粉:0.5 厚大铸铁件 土状石墨:20 土:3 脂:3 鳞片石墨:20 PVB:0.4 锆英粉: 锂基膨润 酚醛树脂:3 乙醇:适量 厚大铸铁件浅色涂料 100 土:3 铝矾土:80 锂基膨润土:3 香:3 乙醇:适量 松 厚大铸铁件 鳞片石墨:20 镁橄榄石:60 凹凸棒 酚醛树 乙醇:适量 氧化铁:4 一般铸铁件 土状石墨:20 土:4 脂:3 鳞片石墨:20 HPC:0.5 硅石粉:80 有机膨润土:3 PVB:0.5 乙醇:适量 松香:6 一般铸铁件浅色涂料 长石粉:20 鳞片石墨:10 锂基膨润 酚醛树 乌洛托品:0.2 一般铸铁件 硅石粉:25 土:5 脂:3 叶蜡石粉:65
序号 1 2 3 4 5 6 7
铸铁件用涂料 表1、粘土砂干型铸铁水基涂料配比 单位:质量分数,% 耐火填料 悬浮剂 粘结剂 载液 附加物 用途 土状石 水柏油:3 钠基膨润土:5 水:适量 一般铸铁件 墨:80鳞 黏土:4 硅石粉:10 钠基膨润 白乳胶: 水:适量 JFC:0.01 一般铸铁件 土状石墨:75 土:4 3 鳞片石墨:15 CMC:0.4 磷酸钠: 锆英粉:60 钠基膨润 硅溶胶: 渗透剂:0.02 厚大铸铁件 土状石墨:20 土:3 7 水 水:适量 鳞片石墨:20 CMC:0.3 溶性酚醛 糖浆:3 铝矾土:100 钠基膨润土:3 水:适量 甲醛:0.2 厚大铸铁件 水柏油:1.7 铝矾土粉:35 钠基膨润 厚大铸铁 滑石粉:5 土:3 水玻璃:7 水:适量 木粉:0.8 件浅色涂 CMC:0.4 料 长石粉:60
锂基膨润土在醇基快干锆英粉涂料中的应用试验

20 0 2年第 3期
20 0 2年 6月
・
铸
Hale Waihona Puke 造设备研
究
Jn 0 2 N3 ue2 0 0
R S A C T D E N F U D Y E U P N E E R H S U ISO O N R Q IME T
应 用研 究 ・
锂 基 膨 润 土 在 醇 基 快 干 锆 英 粉 涂 料 中的应 用 试 验
贾 永泽 ( 原矿 山机 器厂 , 太 山西 太原
摘
0 00 ) 3 09
要: 为了提 高铸钢件表 面光洁度 , 满足 国外客 户对毛坯 表 面的 高质量要 求。我们 分 别采 用钠 基膨 润
土, 钙基膨 润 土及锂 基膨润 土作 为悬浮 剂在 醇基快 干锆 英粉 涂料 中进 行 了应 用, 过对其 悬 浮性进行 比较 性 通 试 验 , 定锂基膨润 土悬浮稳 定性 最好 。本 文详细 阐述 了锂 基膨润 土的 原土 的悬浮性 , 认 活化 处理后 的悬浮性 及锂 基膨 润土醇基快 干锆 英粉涂料 的组成 , 各项性 能。并通过 生产 验证 , 用该涂料 , 应 铸件表 面令人 满意。
为满 足 出 口产 品对 铸 钢件 的 高 质 量 要 求 , 用 选 了一种 人 工合 成 的 锂基 膨 润土 , 以它作 为 悬 浮剂 , 并 配 制成 了醇基 快 干锆 英 粉 涂 料 。 该 涂 料 质 量 稳 定 ,
Lih um — b s nt n t ti — a e Be o ie
JA o gz I Y n -e
∞
舳 加 ∞
( aya T i nMii u nn gMahnr l tTiu n0 0 0 C i ) c i yPa ,aya 30 9, hn e n a
大型铸钢件铸造工艺技术

大型铸钢件铸造工艺技术大型铸件生产周期长、工序复杂,一般要经历众多工序(如图2—1所示),合理设置其铸造过程中各项工艺是决定铸件最终成功铸造的关键要素。
图2—1大型铸钢件铸造工艺流程2.1大型铸钢件造型用砂铸钢件尤其是大型铸钢件大都采用自硬砂地面造型。
大型铸钢件通常具有厚大断面和高的金属静压头、浇注时间较长,加上铸件凝固过程中金属液体与砂型之间的热作用、机械作用、化学反应非常强烈;铸件表面,尤其在砂芯或砂型凹陷及转角处极易产生金属渗透粘砂,易造成铸件尺寸稳定性差和表面缺陷。
因而大型铸钢件对砂型的高温力学性能、型砂材料的抗粘砂能力要求非常高。
目前国内重机行业用于大型铸钢件的造型用砂主要有水玻璃砂(C02吹气硬化和有机醋自硬化)、树脂自硬砂〔峡喃树脂自硬砂、碱酚醛树脂自硬砂)国内一些主要大型铸件生产企业已逐步完成使用自硬砂铸造工艺的技术改造。
大型铸钢件的面砂一般采用铬铁矿砂等特种砂,这些原砂比硅砂的价格高出很多。
因此,对于旧砂再生系统中铬铁矿砂与石英砂的分离技术也是一项合理利用资源及降低成本的关键性技术。
2.2 铬铁矿砂在造型中的应用2.2.1铬铁矿呋喃树脂砂面砂应用实例(见表2—1)222 铬铁矿砂成份及选择铬铁矿砂属于铬尖晶石。
一般以(FeMg 0・(CrAIFe)2Q形式存在,其中杂质主要为CaO MnQ SiO2、TQ2等金属氧化物和碳酸盐化合物。
铬铁矿砂的比重为(4.4〜4.5 )3 3kg/cm,堆积比重为(2.0〜2.7 )kg/cm ,耐火度为2000土25C,熔融触点2040C。
铬铁矿砂的选择主要依据需要配制的型(芯)砂后的工艺参数、铸件质量以及旧砂再生回收率的高低来不断摸索确定。
铬铁矿砂的化学成分及质量分数(%见表2—1。
表2—1 铬铁矿砂的化学成分及质量分数(%2.2.2.1 酸耗值我们在采用呋喃树脂砂工艺时其催(固)化剂为磺酸、苯磺酸之类酸性固化剂硬化,要求原砂呈中性,如存在诸如滑石粉的碱性化合物,固化剂的消耗必然要加大,从而砂型固化慢甚至不能硬化。
高锰钢铸件生产工艺汇编 (2)
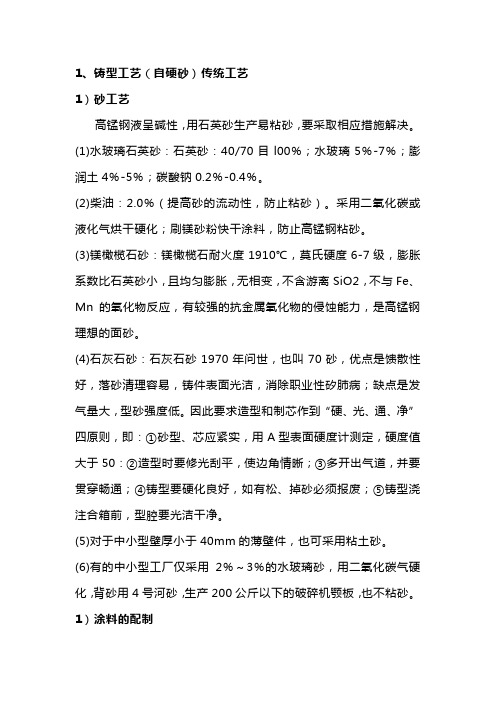
1、铸型工艺(自硬砂)传统工艺1)砂工艺高锰钢液呈碱性,用石英砂生产易粘砂,要采取相应措施解决。
(1)水玻璃石英砂:石英砂:40/70目l00%;水玻璃5%-7%;膨润土4%-5%;碳酸钠0.2%-0.4%。
(2)柴油:2.0%(提高砂的流动性,防止粘砂)。
采用二氧化碳或液化气烘干硬化;刷镁砂粉快干涂料,防止高锰钢粘砂。
(3)镁橄榄石砂:镁橄榄石耐火度1910℃,莫氏硬度6-7级,膨胀系数比石英砂小,且均匀膨胀,无相变,不含游离SiO2,不与Fe、Mn的氧化物反应,有较强的抗金属氧化物的侵蚀能力,是高锰钢理想的面砂。
(4)石灰石砂:石灰石砂1970年问世,也叫70砂,优点是馈散性好,落砂清理容易,铸件表面光洁,消除职业性矽肺病;缺点是发气量大,型砂强度低。
因此要求造型和制芯作到“硬、光、通、净”四原则,即:①砂型、芯应紧实,用A型表面硬度计测定,硬度值大于50:②造型时要修光刮平,使边角情晰;③多开出气道,并要贯穿畅通;④铸型要硬化良好,如有松、掉砂必须报废;⑤铸型浇注合箱前,型腔要光洁干净。
(5)对于中小型壁厚小于40mm的薄壁件,也可采用粘土砂。
(6)有的中小型工厂仅采用2%~3%的水玻璃砂,用二氧化碳气硬化,背砂用4号河砂,生产200公斤以下的破碎机颚板,也不粘砂。
1)涂料的配制(1)快干涂料:先将松香溶于无水酒精中,形成松香酒精溶液,再将镁砂粉陶土混入,建议用200~320目细镁砂粉。
(2)水基镁砂涂料:将镁砂粉、陶土按比例配好,在混砂机中干混10分钟,加水柏油混4小时20分钟,再分批加入清水混碾1小时30分钟,碾成膏状,装入铁桶内加少量清水复盖,如室温超过24度,涂料超过24小时,易发生水化,将重新回混碾3小时。
2、高锰钢铸件(传统铸造)浇注系统的设计(1)高锰钢线收缩率:小件2.4%~3.2%,大件2.0%~2.5%。
在砂型铸造条件下一般铸造线收缩率(缩尺)选择2.5%~2.7%,不同铸件不同部位不同方向线收缩率不同。
锆英粉与耐火材料
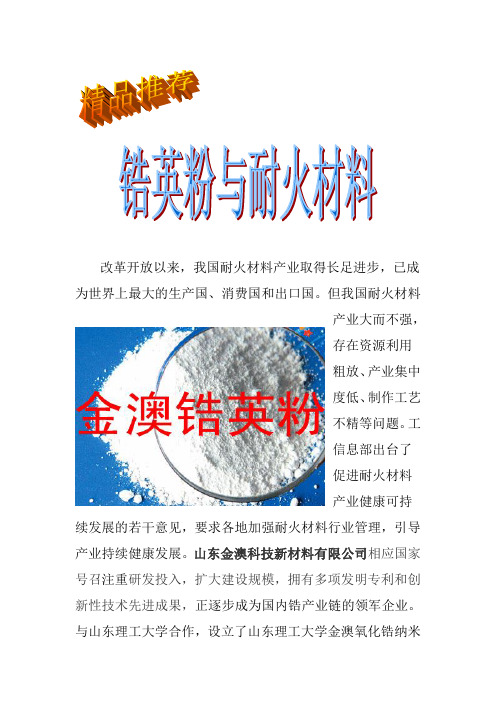
改革开放以来,我国耐火材料产业取得长足进步,已成为世界上最大的生产国、消费国和出口国。
但我国耐火材料
产业大而不强,
存在资源利用
粗放、产业集中
度低、制作工艺
不精等问题。
工
信息部出台了
促进耐火材料
产业健康可持续发展的若干意见,要求各地加强耐火材料行业管理,引导产业持续健康发展。
山东金澳科技新材料有限公司相应国家号召注重研发投入,扩大建设规模,拥有多项发明专利和创新性技术先进成果,正逐步成为国内锆产业链的领军企业。
与山东理工大学合作,设立了山东理工大学金澳氧化锆纳米
陶瓷研发中心,与武汉理工大学初步建立科研合作协议,筹建省级规模研发实验室。
耐火材料是建材、机械等高温工业发展不可或缺的基础材料,也是铸造消失模涂料的骨料成分,耐火材料的品种很多,其中锆英粉是目前用于消失模铸造最好的一种抗粘砂材料。
锆英粉主要成分是ZrO2、SiO2,它的耐火温度不小于2 550℃,颗粒度325目,是浇注铸钢件和大型铸铁件时采用的耐火材料,可以减少铸件的清理工作量,获得表面光洁的铸件。
锆英粉在精密铸造作为耐火材料的应用目前尚无替代品出现,山东金澳科技新材料有限公司生产的金澳牌锆英粉拥有:氧化锆的含量高(不低于66%),耐火度高,含其他氧化物杂质少,化学性能好,结合均匀度高,乳着效果佳,铸造件在灌浆时模具就不会熔化且易脱模等性能和化学优势,被广泛应用于精密铸造的制壳阶段和消失模涂料的耐火骨料中,国内国际众多耐火材料企业均使用金澳牌锆英粉,凭借自身实力和价格实惠、质量上乘的优势,赢得了国际国内企业的一致好评,成为国际第一品牌!。
铸造涂料配方及作用
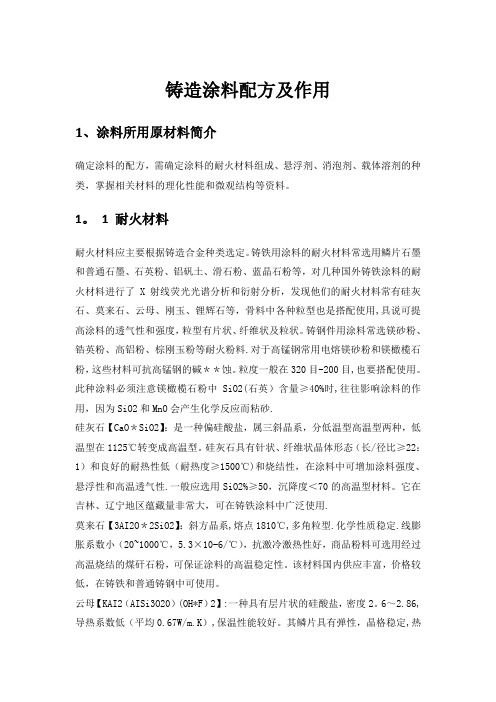
铸造涂料配方及作用1、涂料所用原材料简介确定涂料的配方,需确定涂料的耐火材料组成、悬浮剂、消泡剂、载体溶剂的种类,掌握相关材料的理化性能和微观结构等资料。
1。
1 耐火材料耐火材料应主要根据铸造合金种类选定。
铸铁用涂料的耐火材料常选用鳞片石墨和普通石墨、石英粉、铝矾土、滑石粉、蓝晶石粉等,对几种国外铸铁涂料的耐火材料进行了X射线荧光光谱分析和衍射分析,发现他们的耐火材料常有硅灰石、莫来石、云母、刚玉、锂辉石等,骨料中各种粒型也是搭配使用,具说可提高涂料的透气性和强度,粒型有片状、纤维状及粒状。
铸钢件用涂料常选镁砂粉、锆英粉、高铝粉、棕刚玉粉等耐火粉料.对于高锰钢常用电熔镁砂粉和镁橄榄石粉,这些材料可抗高锰钢的碱**蚀。
粒度一般在320目-200目,也要搭配使用。
此种涂料必须注意镁橄榄石粉中SiO2(石英)含量≥40%时,往往影响涂料的作用,因为SiO2和MnO会产生化学反应而粘砂.硅灰石【CaO*SiO2】:是一种偏硅酸盐,属三斜晶系,分低温型高温型两种,低温型在1125℃转变成高温型。
硅灰石具有针状、纤维状晶体形态(长/径比≥22:1)和良好的耐热性低(耐热度≥1500℃)和烧结性,在涂料中可增加涂料强度、悬浮性和高温透气性.一般应选用SiO2%≥50,沉降度<70的高温型材料。
它在吉林、辽宁地区蕴藏量非常大,可在铸铁涂料中广泛使用.莫来石【3AI2O*2SiO2】:斜方晶系,熔点1810℃,多角粒型.化学性质稳定.线膨胀系数小(20~1000℃,5.3×10-6/℃),抗激冷激热性好,商品粉料可选用经过高温烧结的煤矸石粉,可保证涂料的高温稳定性。
该材料国内供应丰富,价格较低,在铸铁和普通铸钢中可使用。
云母【KAI2(AISi3O20)(OH*F)2】:一种具有层片状的硅酸盐,密度2。
6~2.86,导热系数低(平均0.67W/m.K),保温性能较好。
其鳞片具有弹性,晶格稳定,热化学稳定性较好.该材料熔点较低(1270~1330℃),用于铸铁涂料时易于粘砂。
- 1、下载文档前请自行甄别文档内容的完整性,平台不提供额外的编辑、内容补充、找答案等附加服务。
- 2、"仅部分预览"的文档,不可在线预览部分如存在完整性等问题,可反馈申请退款(可完整预览的文档不适用该条件!)。
- 3、如文档侵犯您的权益,请联系客服反馈,我们会尽快为您处理(人工客服工作时间:9:00-18:30)。
性能 比重 ( & ’ & ()* ) +, 值 粘度 & ( - 涂 . / 号杯) %! 0 悬浮性 (1 ) 发气量 ( & )2 & ’) ( # 333 4 ) %)56) 曝热抗裂性 ( # %33 4 , 指标 %" 3/* 7 7" 8 *% 98 #9" 7 !级
表 !" 大型铸钢件用醇基锆英粉涂料的最佳配比 #$%&’( !" #)’ *+,-./. .$,0)-12 3$,-* *4 ,)’ $&0*)*&5%$6’7 8-30*1 +*97’3 0*$,-12 4*3 ,)’ )’$:; 6,’’& 0$6,-12
锆英粉 ,(( 复合悬浮剂 ( 固体) *+ & ) &+ ( 特种粘结剂 *+ ( ) .+ ( 混合溶剂 $& ) $6 附加剂 (+ (& ) (+ ,
《 大型铸锻件》 BS)TU @Байду номын сангаасD&VR’ )R, POW’VR’
R/G L R/-+1:+= (%%"
大型铸钢件用醇基锆英粉 涂料的研制与应用
陈展飞! 田秀成! 费长正! 刘文瑞! 刘! 健
( 德阳立达化工公司, 四川 "#$%%% ) 摘要: 介绍了大型铸钢件用醇基锆英粉涂料的组成、 生产工艺路线及其工艺性能特征, 研究了醇基铸造涂 料的选材、 生产工艺等对涂料性能的影响。该涂料抗粘砂能力强, 悬浮性、 刷涂性、 流平性优异, 一次刷涂所得 涂层厚度高, 适用于各种铸钢件尤其是大型铸钢件的生产, 可有效地防止粘砂等缺陷, 获得表面质量优良的铸 件。 关键词: 锆英粉; 大型铸钢件; 涂料; 悬浮; 流平性 中图分类号: &’((#! ! 文献标识码: )
收稿日期: (%%" —%K —((
?> 大型铸钢件用醇基涂料的组成 醇基铸造涂料的成分主要有耐火填料、 悬浮 剂、 粘结剂、 有机溶剂、 附加剂等。涂料原辅材料 的选择和配比是影响涂料性能的决定性因素, 因 此, 原辅材料品种及配比的确定是本产品研制过 程中最关键的环节。 (G #! 原辅材料的选择 (G #G #! 耐火填料 耐火填料又称耐火粉料, 是铸造涂料的主要 组分, 对涂料的抗粘砂能力起决定性作用, 其作用 在于隔离型、 芯与金属液, 改进金属液与型、 芯的 界面作用。选择耐火粉料时应综合考虑以下性 质: 耐火性能要与金属液的浇注温度一致, 良好的 高温化学稳定性, 不与型砂起不良反应, 不损害铸 件的化学成分及性能, 适当的细度。厚大铸钢件 宜选用锆英粉作耐火填料。锆英粉耐火度高, 熔 具有良好的高温化学惰性, 热膨胀 点为 ( LM% N , 率小。锆英粉的耐火度受其 <=O( 含量影响, <=O( 含量偏低, P+( OM 等杂质含量偏高, 其耐火度将降 #Q
78+ . 789:2;:" $((%
《 大型铸锻件》 <=>4? @>ABC7D >7E F#GDC7D
低, 从而降低涂料的抗粘砂能力。为保证大型铸 钢件浇铸对涂料耐火性的要求, 锆英粉中 !"#$ 的 含量应大于 %&’ 。锆英粉的细度对涂料的性能 有重要影响, 粒度过粗, 锆英粉易在运输和贮存过 程中沉淀板结, 使涂料的施工性能下降; 粒度过 细, 涂料点燃后涂层易开裂。实验表明, 锆英粉的 细度在 $&( ) *$& 目之间时, 可较好地平衡涂料的 悬浮性和抗开裂性。 $+ ,+ $- 悬浮剂 悬浮剂的作用在于防止或减缓涂料中的耐火 填料下沉, 避免涂料形成 “ 硬底” 。醇基涂料常用 的悬浮剂有锂基膨润土、 凹凸棒土、 累托石、 有机 膨润土等。由于锆英粉比重较大 ( .+ % / 0 12 ) , 在 以乙醇为主要载体的醇基涂料体系中极易沉淀。 锂基膨润土、 凹凸棒土、 累托石等属于无机悬浮 剂, 它们都需要先用适量的水活化才能发挥悬浮 功效, 涂料中的粘结剂是有机组分, 遇水将降低其 流动性甚至析出; 有机膨润土属于有机粘结剂, 需 用气味较大并具有一定毒性的甲苯或二甲苯引 发, 若甲苯或二甲苯加入量较少, 有机膨润土不能 充分膨胀, 加入到含有大量乙醇的涂料体系中将 导致其收缩甚至析出, 甲苯或二甲苯加入量过多, 一方面使涂料气味大, 另一方面导致涂料点燃后 产生大量 “ 黑烟” , 降低涂 层 性 能 并 恶 化 施 工 环 境, 故无论是选用上述无机悬浮剂还是有机悬浮 剂, 涂料体系中总是存在与之性质相排斥的组分, 都将导致涂料成为一个不稳定体系。提高涂料的 悬浮性也不能单靠调整悬浮剂的加入量来解决, 悬浮剂加入量低, 将使涂料的悬浮率不够, 悬浮剂 加入量高, 可提高涂料的悬浮率, 但由于悬浮剂与 涂料中某些组分性质相互排斥, 涂料的流动性、 刷 涂性等性能将降低。因此, 提高醇基锆英粉涂料 的悬浮性是一个很难解决的问题。通过大量实 验, 我们找到了一种主要成分为硅酸铝镁, 在水性 和油性体系中均具有良好触变增稠效果的悬浮剂 及一种比表面积特别大的纳米级触变增稠剂, 将 它们与适量的锂基膨润土配合使用, 并通过适当 的加工工艺, 制得了一种复合悬浮剂。使用该复 合悬浮剂, 使涂料体系的稳定性提高, 从而可制得 触变性强、 悬浮性特别优异但不影响其它性能的 醇基锆英粉涂料。 $+ ,+ *- 粘结剂 粘结剂的作用是在涂料涂覆后将耐火填料等 固体成分粘结在一起, 使涂层具有一定的强度和 耐磨性, 并使涂层附着于砂型表面上。醇基涂料 ,6
*
一般选用有机粘结剂, 常用的有: 酚醛树脂、 松香、 聚乙烯醇缩丁醛 ( 345 ) 、 硅酸乙酯等。上述粘结 剂均具有亲油憎水性, 与前述的无机悬浮剂中加 入的活化水不相容, 二者混合后, 粘结剂的溶解性 将受到不良影响甚至导致其从溶剂中析出, 从而 降低涂料的流动性、 流平性、 刷涂性等性能。我们 运用有机物溶解理论并通过大量实验, 找到了一 种既能溶于水又能溶于乙醇等有机溶剂的特殊粘 结剂, 使用该粘结剂避免了体系中出现不相容成 分相互混杂、 相互排斥的情况, 从而大大提高了涂 料的流动性, 使涂料在较高的粘度状态下也容易 刷涂。毛刷每蘸一次涂料反复刷涂多次后, 涂料 仍可自动流平, 得到平整光滑、 无刷痕的涂层, 因 此, 该粘结剂在本体系中还发挥了流平剂的功效。 $+ ,+ .- 溶剂 溶剂的作用在于将涂料中的固、 液体料分散 或溶解于其中, 使涂料成为便于涂覆的浆状体或 膏状体。乙醇是醇基涂料最常用的溶剂。由于乙 醇挥发速度较快, 当涂料一次性刷涂面积较大而 点火间隔时间稍长时, 涂料就不易点燃。因此, 我 们选择以乙醇为主, 配合适量挥发速度适中的辅 助溶剂的混合溶剂体系, 该溶剂体系可保证涂料 一次刷涂较大面积仍可点燃。 $+ ,+ &- 附加剂 附加剂是为了改善涂料的某些性能或消除其 某种缺陷而添加的少量附加物, 在涂料中起类似 “ 味精” 的作用, 但它不是涂料的必加组分, 而是 视对各类涂料的具体性能要求而酌情加入。醇基 涂料的附加剂有润湿剂、 消泡剂、 流平剂、 偶联剂 等。本涂料中加入了一种金属氧化物作附加剂来 增强纳米触变剂的触变增稠效果。 $+ $- 涂料的基本配比 通过大量实验, 我们优化出的大型铸钢件用 醇基锆英粉涂料的最佳配比范围如表 , 所示。
<" 生产设备及工艺 涂料的生产设备主要有: 搅拌机、 齿轮泵、 胶 体磨。搅拌机的作用在于将固体粉料和液体料混 合均匀, 齿轮泵对配好的浆料起输送转移作用, 胶
《 大型铸锻件》 ,CDEF GDH<I?J D?K LMNJI?J
?B" ! ?BOP)QPR %33/
体磨则通过其摩擦、 挤压、 剪切、 研磨作用将耐火 填料中的团聚粒子打开成为更细小的次级粒子而 被悬浮剂和粘结剂充分包裹, 形成稳定的分散体。 生产工艺对涂料的性能有重大影响。通过大 量试验, 我们确定大型铸钢件用醇基涂料的基本 生产工艺流程为: 在一种悬浮剂中加入活化剂, 静 置活化%加入其它悬浮剂、 附加剂、 溶剂%高速搅 拌%研磨%制得复合悬浮剂 % 加入耐火填料、 粘 结剂、 溶剂%高速搅拌 % 研磨 % 大型铸钢件用醇 基锆英涂料。按此工艺流程制得的涂料各项工艺 性能良好, 可达到预期的技术指标。 !" 主要技术指标和工艺性能特征 !" #$ 主要技术指标 按前述配方及工艺制得的涂料, 其主要技术 指标如表 % 所示。
45678&,7 : &*6; 4=367.+ *4; 5+;7=6:+5 3*+ 7/10/;636/2 /8 3*+ 4.7/*/.9:4;+5 E6=7/2 0/?5+= 7/4362A 8/= 3*+ *+4-C ;3++. 74;362A 425 3*+ 0=/5F736/2 0=/7+;; =/F362+ 4; ?+.. 4; 3*+ 0=/7+;; 0=/0+=3C 7*4=473+=6;367,1+42?*6.+ 3*+ +88+73; /8 3*+ 143+=64. ;+.+736/2 425 3*+ 0=/5F736/2 0=/7+;; /8 3*+ 7/4362A /2 63; 0=/0+=3C *4-+ :++2 =+;+4=7*+5G &*+ =+;F.3 ;*/?+5 3*43 3*+ 7/4362A 0=/7+;;+; +H7+..+23 :F=29/2 =+;6;3427+ 7404:6.63C 425 A//5 0=/0+=36+; /8 ;F;0+2;6/2,0462362A 425 .+-+.9 62A 4; ?+.. 4; 3*67I+= 7/43 ?63* /27+ 0462362A, ?*67* 6; ;F634:.+ 8/= -4=6/F; I625; /8 ;3++. 74;362A; 0=/5F736/2, +;0+764..C 8/= 3*+ *+4-C ;3++. 74;362A :+74F;+ 3*+ :F=29/2 425 /3*+= 5+8+73; 7/F.5 :+ +88+736-+.C 0=+-+23+5,62 3*6; ?4C 3*+ 74;362A ?63* A//5 ;F=847+ JF4.63C 7/F.5 :+ 0=/5F7+5G 9#: ;<826: E6=7/2 0/?5+=;*+4-C ;3++. 74;362A;7/4362A;;F;0+2;6/2;.+-+.62A