履带式全液压坑道钻机技术交流
履带式液压锚杆钻机安全技术交底模板

一、交底对象1. 钻机操作人员2. 钻机维修保养人员3. 钻机管理人员二、交底时间[填写具体日期]三、交底内容一、设备概述1. 履带式液压锚杆钻机是一种用于煤矿巷道支护的机械设备,具有自动化程度高、操作简便、安全性好等特点。
2. 钻机主要由行走部、机体部、钻机部、升降机构、液压系统、动力部、工作平台等组成。
二、安全操作规程1. 操作人员必须经过专业培训,取得相应操作资格。
2. 操作前应认真检查钻机各部件是否完好,液压系统是否正常,安全防护装置是否齐全有效。
3. 操作过程中应保持注意力集中,严禁酒后操作或疲劳作业。
4. 钻进前,应对钻孔位置进行安全检查,确保顶板和煤帮稳定。
5. 钻进过程中,严禁用手或戴手套触摸旋转的钻杆,禁止单手操作。
6. 开孔时,支腿应缓慢伸出,避免钻杆变形折断或钻头损坏。
7. 钻机突然加载时,操作者应保持正确的站位,防止扭伤。
8. 使用本钻机进行顶板超高钻孔时,应由使用单位制定特殊的安全措施。
三、安全注意事项1. 操作人员应熟悉钻机各部件的功能和操作方法,了解设备的技术参数和安全性能。
2. 钻机作业区域应设置安全警示标志,并采取隔离措施,防止无关人员进入。
3. 钻机操作过程中,应保持良好的通风,防止有害气体积聚。
4. 钻机作业现场应配备消防器材,确保一旦发生火灾能够迅速扑救。
5. 钻机维修保养时,应切断电源,防止误操作造成人身伤害。
四、紧急处理措施1. 钻机出现故障时,应立即停止作业,并通知维修人员进行检查和处理。
2. 钻机操作过程中,如发现顶板和煤帮不稳定,应立即停止作业,采取临时支护措施。
3. 发生火灾时,应立即切断电源,使用灭火器进行扑救,并迅速撤离现场。
4. 发生人员受伤事故时,应立即采取急救措施,并及时拨打急救电话。
五、总结1. 履带式液压锚杆钻机操作过程中,必须严格遵守安全操作规程,确保操作人员的人身安全和设备的安全运行。
2. 定期对操作人员进行安全教育培训,提高安全意识,减少安全事故的发生。
下梨园煤业履带式全液压钻机维修技术规范(1)
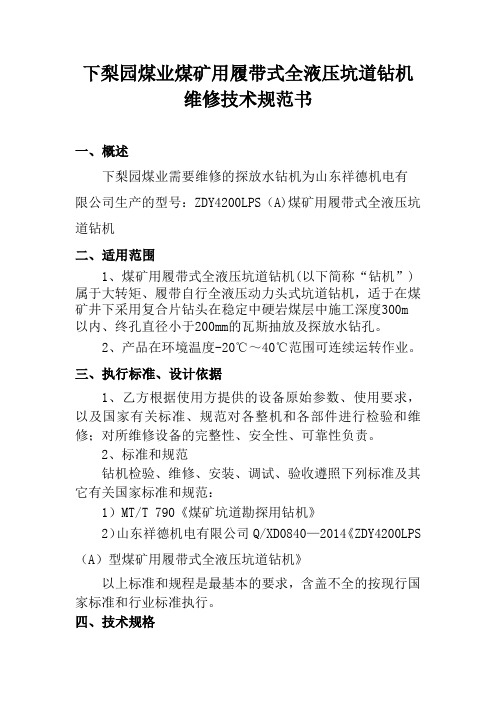
下梨园煤业煤矿用履带式全液压坑道钻机维修技术规范书一、概述下梨园煤业需要维修的探放水钻机为山东祥德机电有限公司生产的型号:ZDY4200LPS(A)煤矿用履带式全液压坑道钻机二、适用范围1、煤矿用履带式全液压坑道钻机(以下简称“钻机”)属于大转矩、履带自行全液压动力头式坑道钻机,适于在煤矿井下采用复合片钻头在稳定中硬岩煤层中施工深度300m 以内、终孔直径小于200mm的瓦斯抽放及探放水钻孔。
2、产品在环境温度-20℃~40℃范围可连续运转作业。
三、执行标准、设计依据1、乙方根据使用方提供的设备原始参数、使用要求,以及国家有关标准、规范对各整机和各部件进行检验和维修;对所维修设备的完整性、安全性、可靠性负责。
2、标准和规范钻机检验、维修、安装、调试、验收遵照下列标准及其它有关国家标准和规范:1)MT/T 790《煤矿坑道勘探用钻机》2)山东祥德机电有限公司Q/XD0840—2014《ZDY4200LPS (A)型煤矿用履带式全液压坑道钻机》以上标准和规程是最基本的要求,含盖不全的按现行国家标准和行业标准执行。
四、技术规格1、主要技术参数《ZDY4200LPS(A)煤矿用履带式全液压坑道钻机》使用说明书(山东祥德机电有限公司生产)2、技术要求1)检修内容要求根据现场考察和使用情况分析,在保证使用可靠性和安全性为前提下,对未有报损和前期使用未发现异常的液压电器等元件不列入维修更换明细当中(因为在未接电和试机前无法判定,包括行走部和驱动马达等)。
乙方通电试机后,如出现新的维修项目,需通知甲方到场共同鉴定是否进行维修。
乙方保证缺损件的更换和尽可能的利用修复技术,保证设备的正常使用寿命。
具体内容如下:3、整机技术要求1)整机的外观表面整洁,主机除操作手柄、按钮、标志牌、油标玻璃板及外配合表面不涂漆外,各注、放油塞及防爆标志涂原油漆。
3)钻机验收合格交付使用之日起半年内,在使用方遵守使用、保养、安装、运输规则条件下,确因质量不良而发生损坏或不能正常工作时(易损件除外),乙方应免费为用户修理或更换。
ZDY6000L钻机使用说明书(1)

说明:
本钻机在煤矿井下使用时,必须选用YBK2-280S-4型矿用隔爆型三相异步电动机。所用隔爆型三相异步电动机、液压支架胶管总成应有安全标志。
钻机出厂之前,系统工作压力已调定,用户在使用过程中不得擅自超调,否则,出现任何责任事故,我院概不负责。
钻机液压系统工作介质为矿物油,不得在渗漏状态下工作,对泄漏在工作场所的矿物油,应及时清理掩埋。
13.钻机安标受控件明细20
1.
ZDY6000L型煤矿用履带式全液压坑道钻机属于自行式、低转速、大转矩类型,适于采用复合片钻头施工深度约600 m的大直径钻孔,也可采用孔底动力机钻进,主要用于煤矿井下施工近水平长距离瓦斯抽放钻孔。
回转器采用卡槽式连接安装在给进装置的拖板上,借助给进油缸带动拖板沿机身导轨往复运动,实现钻具的给进或起拔。回转器主轴结构为通孔式,使用钻杆的长度不受钻机给进行程的限制。
4.2.2夹持器
夹持器固定在给进装置机身的前端,用于夹持孔内钻具,还可配合回转器实现机械拧卸钻杆。卡瓦由螺钉固定在卡瓦座上,卡瓦座靠挡边与销轴实现轴向固定。将两根销轴抽出即可从一侧取出卡瓦座,使夹持器通孔扩大,以便通过粗径钻具。在夹持器与给进机身的连接处设有两组调整垫片,用于调整夹持器卡瓦组的中心高,使之与回转器主轴中心高相一致。
额定压力/MPa 26
额定流量/L/min 148
C给进装置
主轴倾角/°-10~20
最大给进/起拔力/kN 180
给进/起拔行程/mm 1000
给进/起拔速度/m/s起下钻工况0~0.25
钻进工况0~0.05
额定压力/MPa 21
额定流量/L/min起下钻工况148
ZYL-1200LS型履带式全液压坑道钻机

ZDY-1200LPS型履带式全液压坑道钻机安全操作规程一、井下安装1、使用前的准备工作(1)钻机安装前,首先清理好钻场,钻场周围的岩石应安全可靠,且具有足够的空间,通风良好。
(2)配有与钻机相适应的水源(供水量Q>200L/min,供水压力>1Mpa) 或压风(需压风排渣风压>0.6Mpa),电源及相应的配套设备。
(3)按液压系统图连接各油管。
连接油管时应检查快换接头的动作灵活性和清洁度,连接应正确、牢固可靠。
(4)经空气滤清器油网加入46#抗磨液压油至油位计上标位,开机试车后油位会下降,应及时补油至上标位。
(5)连接电源,电动机连接电压等级应与电源电压等级相符合,电动机的旋转方向应与油泵标注的箭头方向一致。
(6)调定工作压力: 将动力头马达进出油管和推进油管2 对快换接头拔下,松开泵站上的大、小泵溢流阀,旋紧多路换向阀组上的各过载阀(3 个)。
开机后将旋转手把前推至正转位置,缓慢调节操纵台上大泵的溢流阀,使油压逐渐上升,当操纵台右边压力表指示为18Mpa 时,锁紧该过载阀,此压力为旋转油路总压力;调节该阀片上方过载阀压力,当操纵台右边压力表指示为16Mpa 时,锁紧该过载阀,此压力为动力头正转工作压力;将旋转手把向后拉至反转位置,调节总回油阀片下方过载阀压力,当操纵台右边压力表指示为17Mpa 时,锁紧该过载阀,此压力为动力头反转工作压力;将旋转手把打回中位,此时旋转油路上各工作压力调定完毕。
将争创进退手把向后拉至正常后退位置(注意最后为浮动位,即卸钻杆螺纹位置),缓慢调节操纵台上小泵的溢流阀,使油压逐渐上升,当操纵台左边压力表指示为16Mpa 时,锁紧该溢流阀,此压力为推进油路总压力,即加持器加紧和松开、卡盘松开压力、给进油缸的后退(起拔)压力、履带车行走压力、履带车抬升压力;将推进手把向前推至正常前进位置,调节正常进退阀片,此压力为推进压力。
将推进手把置于中位,各工作压力调定完毕。
履带液压钻机操作方法
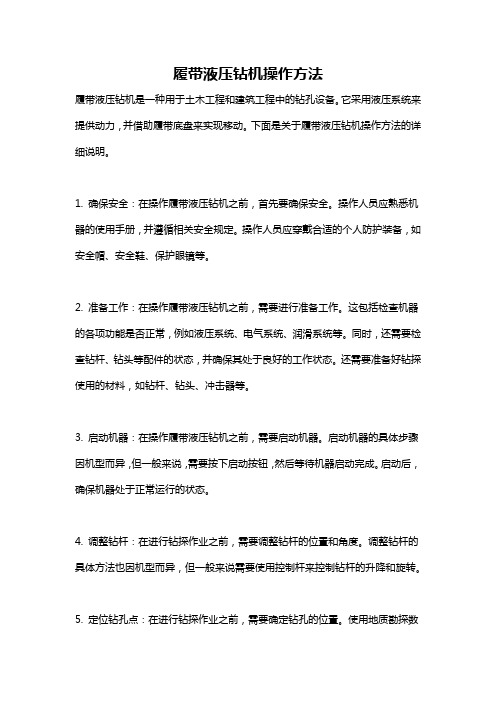
履带液压钻机操作方法履带液压钻机是一种用于土木工程和建筑工程中的钻孔设备。
它采用液压系统来提供动力,并借助履带底盘来实现移动。
下面是关于履带液压钻机操作方法的详细说明。
1. 确保安全:在操作履带液压钻机之前,首先要确保安全。
操作人员应熟悉机器的使用手册,并遵循相关安全规定。
操作人员应穿戴合适的个人防护装备,如安全帽、安全鞋、保护眼镜等。
2. 准备工作:在操作履带液压钻机之前,需要进行准备工作。
这包括检查机器的各项功能是否正常,例如液压系统、电气系统、润滑系统等。
同时,还需要检查钻杆、钻头等配件的状态,并确保其处于良好的工作状态。
还需要准备好钻探使用的材料,如钻杆、钻头、冲击器等。
3. 启动机器:在操作履带液压钻机之前,需要启动机器。
启动机器的具体步骤因机型而异,但一般来说,需要按下启动按钮,然后等待机器启动完成。
启动后,确保机器处于正常运行的状态。
4. 调整钻杆:在进行钻探作业之前,需要调整钻杆的位置和角度。
调整钻杆的具体方法也因机型而异,但一般来说需要使用控制杆来控制钻杆的升降和旋转。
5. 定位钻孔点:在进行钻探作业之前,需要确定钻孔的位置。
使用地质勘探数据和工程设计图纸,确定钻孔位置,并使用标尺等工具标记出钻孔点。
6. 开始钻探:确定钻孔位置后,可以开始进行钻探。
具体的钻探方法因工程要求而异,一般有回转钻探和往复钻探两种。
回转钻探是通过旋转钻杆来进行钻探,可以快速钻入较深的地层。
往复钻探是通过上下往复运动来进行钻探,适用于钻孔较浅或需要打下孔的情况。
7. 监控钻探过程:在进行钻探作业过程中,需要监控钻探的各项参数。
这包括钻进速度、钻进压力、转速等。
通过监控这些参数,可以及时调整钻探机器的工作状态。
8. 钻头更换:当钻头磨损或需要更换时,需要停止钻探作业,将钻杆抽出地面。
然后,打开钻头所在位置的卡子,将旧钻头取出,再将新钻头安装好,最后将钻杆重新插入地面。
9. 结束钻探作业:当完成钻探任务或需要暂停钻探作业时,需要将机器停止。
ZDY4000LS型煤矿用履带式全液压坑道钻机的研制
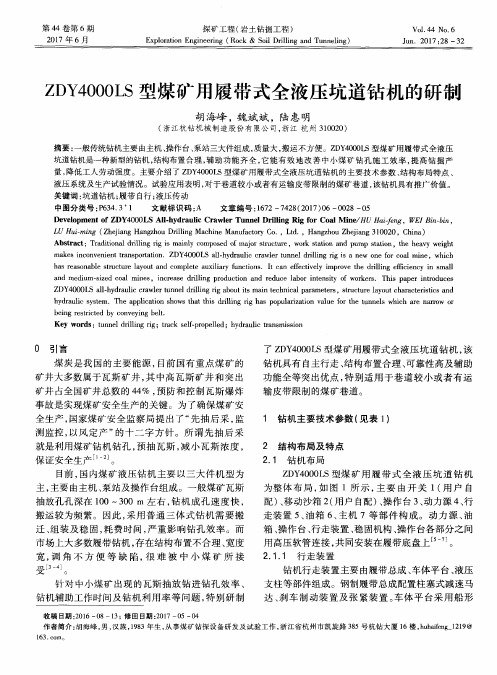
探 矿 工 程 (岩 土 钻 掘 工 程 )
Exploration Engineer ing (Rock & Soil Drilling and Tunneling)
Vo1.44 No.6 Jun.2017:28 —32
ZDY4000LS型 煤 矿 用 履 带 式全 液 压 坑 道 钻 机 的研 制
胡 海峰 ,魏 斌 斌 ,陆 惠 明
(浙江杭钻机械制造股份 有限公 司,浙江 杭 州 310020)
摘要 :一般传统钻机 主要 由主机 、操作台 、泵站三大件组成 ,质量大 ,搬运不 方便 。ZDY4OOOLS型煤矿用履带式全 液压 坑道 钻机是一种新型的钻机 ,结构布置合理 ,辅 助功 能齐 全 ,它能 有效 地改 善 中小煤矿 钻孔 施 工效率 ,提高钻 掘产 量 ,降低工人 劳动强 度。主要 介绍 了 ZDY4000LS型煤矿 用履 带式全液压坑道钻机 的主要技术参数 、结构布局特点 、 液压系统及生产试验情况 。试验应用表 明 ,对于巷道较小 或者有运输皮带 限制 的煤 矿巷道 ,该钻 机具 有推广价值 。 关键词 :坑 道钻 机 ;履带 自行 ;液压传动 中图 分 类 号 :P634.3 1 文 献 标 识 码 :A 文 章 编 号 :1672—7428(2017)06—0028—05 Development of ZDY4000LS All-hydraulic Crawler Tunnel Drilling Rig for Coal M ine/HU Hai-厂eng,WEI Bin—bin, LU Hui—ruing(Zhejiang Hangzhou Drilling Machine Manufactory Co.,Ltd.,Hangzhou Zhejiang 3 10020,China) Abstract:Traditional drilling rig is main1y composed of major structure,work station and pump station,the heavy weight
我矿使用ZDY4000L型煤矿用履带式全液压坑道钻机的先进设备技术优点

SGZ—ⅢA型钻机:
钻进深度:300米;钻孔开孔直径:150毫米;钻孔终孔直径:91毫米
ZDY4000L型煤矿用履带式全液压坑道钻机:
施工深度350m以内、终孔直径小于200mm的近水平瓦斯抽放钻孔。
1、从钻进深度
2、钻孔开孔直径
SGZ—ⅢA型钻机
25
60
2842是来自ZDY4000L型钻机25
60
18
0
否
3、钻孔终孔直径
三个方面比以前有很大的改观
瓦斯钻孔抽采治理
钻机型号
钻孔施工长度m
施工时间
h
钻头直径
mm
抽放量m3/min
SGZ—ⅢA型钻机
120
17
94
0.45
ZDY4000L型钻机
120
12
114
0.65
瓦斯抽放钻孔施工安全方面
钻机型号
钻孔倾角
(度)
钻孔施工长度m
施工时间
h
钻杆下滑次数
(次)
是否使用专用工具拆卸钻杆
钻机常见故障.ppt

故障及现象
可能原因
排除方法
副泵系统压力小
按上述方法排除
给进压力太小
增大给进压力
给进装置
给进起拔力 小或不动作
背压阀(节流阀)关闭
顺时针旋转手轮, 打开背压阀
拖板与导轨卡死
松动拖板两侧螺 钉
给进油缸活塞密封损坏, 内部漏油
检修给进油缸
2020/4/27
ZDY6000LD(A)履带式全液压坑道钻机技术交流
清洗压力表头部通孔
压力表指针摆动或失 灵
泵液力端某一吸入球 阀被泥团碎渣压住不
工作
清洗积存在吸入阀周 边的泥团碎渣
压力表损坏
更换压力表
2020/4/27
ZDY6000LD(A)履带式全液压坑道钻机技术交流
15
泥浆泵常见故障及排除方法
故障
可能原因
排除办法
曲轴箱内润滑油过多, 大大超过规定的液面
高度
检查并泄油至规定高 度;
回转器
主泵系统压力小 按上述方法排除
马达磨损(马达泄油 量大)
维修或更换马达
回转无力
配油套上的密封圈 (孔用Yx型密封圈 D18)损坏(齿轮箱
回油量过大)
更换密封圈
主轴或配油套磨损 (齿轮箱回油量大)
检修或更换
2020/4/27
ZDY6000LD(A)履带式全液压坑道钻机技术交流
9
钻机常见故障及排除方法
10
钻机常见故障及排除方法
故障及现象
可能原因
排除方法
压力表
无显示
压力表损坏
更换新压力表
系统回油阻力大
清洗回油滤油器
(回油阻力大于0.6MPa)
滤芯
浅析履带式液压潜孔钻机在预裂钻孔工艺中的应用

浅析履带式液压潜孔钻机在预裂钻孔工艺中的应用摘要:履带式液压潜孔钻机因钻孔角度灵活、行动方便、操作简单、作业效率高在大体积钻爆施工领域受到广泛的喜爱和应用,若用履带式液压潜孔钻机进行预裂孔钻孔施工,将解放很大一部分劳动力,并大大提高钻机设备的利用率和工作效率。
关键词:履带式液压潜孔钻机;工艺流程;技术要点;质量控制措施。
在预裂钻孔施工过程中一般使用YQ-100B型潜孔钻机进行造孔,首先需要搭建一个钻架平台,再将钻机与钻架平台用扣件连接固定,通过控制钻架平台的角度和稳定性,以达到控制钻孔精度的目的。
此钻孔工艺能够达到较高的钻孔精度,特别适合于混凝土结构面等质量控制要求较高的开挖任务,但也存在操作工艺复杂、钻机移动不便、投入人力较多、不便于主爆孔钻孔、钻机利用率低等诸多弊端。
而履带式液压潜孔钻机因钻孔角度灵活、行动方便、操作简单、作业效率高而受到广泛的喜爱和应用,用履带式液压潜孔钻机进行预裂孔钻孔,将解放一部分劳动力,并大大提高钻机设备的利用率和工作效率。
1.履带式液压潜孔钻机预裂钻孔的要点1.钻机稳定性的控制钻孔施工前做好部位的清理和平整,清理应尽量达到基岩面,对准开孔点,不断调整钻机位置,使其达到一个最佳的作业姿势,将钻机滑架与基岩面充分接触并靠紧,利用钻机自身制动满足钻机稳定性要求。
1.开孔精度的控制将钻头中心对准开孔点,调整钻杆角度和方向,使其达到设计要求,再次检查钻头中心与开孔点的位置,若偏离,则微调钻头位置,检查钻杆角度和方向,如此反复使得钻机在设计的角度和方向下精确对准开孔点,满足开孔要求。
1.钻孔角度的控制钻孔角度的精度直接决定了结构面开挖的超欠情况,如何控制钻孔角度使其恰好等于设计角度值,是履带式液压潜孔钻机预裂钻孔的一个难点。
对准开孔点后利用罗盘或者坡度尺测量角度,将坡度尺固定在钻杆上,上下调整钻杆位置至所需角度值即可。
当开孔点位、开孔方向和角度同时满足要求时可进行钻孔。
开孔时先用低风压冲击钻孔,入岩20cm时,用坡度尺复测角度,若有偏差则进行调整;调整完毕后打开旋转继续钻孔至入岩100cm,第三次用坡度尺检测角度,若有偏差则调整,若无偏差则适当增大风压继续钻孔,入岩200cm后采用正常风压进行钻孔,每次更换钻杆时检测角度,若有偏差及时调整。
探水钻机入井的安全技术措施
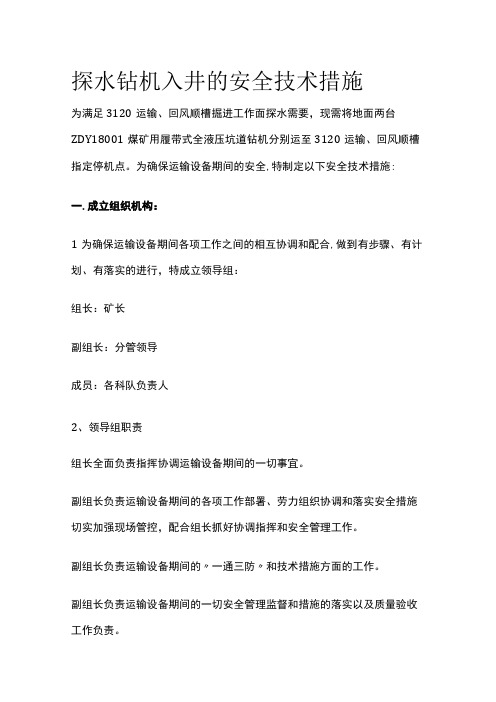
探水钻机入井的安全技术措施为满足3120运输、回风顺槽掘进工作面探水需要,现需将地面两台ZDY18001煤矿用履带式全液压坑道钻机分别运至3120运输、回风顺槽指定停机点。
为确保运输设备期间的安全,特制定以下安全技术措施: 一.成立组织机构:1为确保运输设备期间各项工作之间的相互协调和配合,做到有步骤、有计划、有落实的进行,特成立领导组:组长:矿长副组长:分管领导成员:各科队负责人2、领导组职责组长全面负责指挥协调运输设备期间的一切事宜。
副组长负责运输设备期间的各项工作部署、劳力组织协调和落实安全措施切实加强现场管控,配合组长抓好协调指挥和安全管理工作。
副组长负责运输设备期间的〃一通三防〃和技术措施方面的工作。
副组长负责运输设备期间的一切安全管理监督和措施的落实以及质量验收工作负责。
副组长负责运输设备期间机电、机运方面的管理、组织、指挥工作。
副组长负责协助总工程师做好运输设备期间的〃一通三防〃方面的工作,并具体安排落实通风瓦斯管理方面工作。
副组长负责协助总工程师做好运输设备期间的安全技术措施的制定和补充完善及贯彻学习工作。
副组长协助安全矿长抓好运输设备期间的一切安全管理监督、措施的落实和质量验收工作。
副组长负责协助机电副矿长做好今次运输设备期间的工作,具体负责梭车、动力线路、信号、照明、机电设备、探水钻机的运输、调试和电缆等设备的安全管理工作。
副组长负责协助总工程师做好运输设备期间的〃一通三防〃方面的工作,并具体安排落实通风瓦斯管理方面工作。
各成员负责本业务范围内的相关工作,对本责任区内的安全生产工作负责,并协助各分管领导做好本业务范围内的工作。
3、成立现场领导组主要负责人:下料队队长现场负责人:当班班组长安全监督人:由当班专职安全员全面负责4、现场领导组职责:主要负责人:全面负责本次探水钻机运输及运输路线各作业场所的劳动组织和具体协调安排工作。
现场主要负责人:负责现场对探水钻机运输工作进行全面安排,是探水钻机运输工作的现场责任人,并做好运输各区段作业人员的安排和协调工作。
履带式液压潜孔钻机工作原理

履带式液压潜孔钻机工作原理
履带式液压潜孔钻机是一种专门用于岩土工程施工中进行岩土
钻探的设备。
它采用液压系统驱动,具有强大的动力和稳定性。
履带式液压潜孔钻机的工作原理主要分为以下几个步骤:
1. 钻杆设定:首先,将钻杆连接到钻机上,并通过液压系统将
钻杆推入地面。
钻杆一般由钢筋材料制成,具有足够的强度和刚
度来应对施工中的高强度作业。
2. 钻进操作:液压系统通过电动泵将压力传递到液压缸,从而
推动钻杆向下旋转。
这时,钻机的钻头将会旋转并向下钻进地下。
液压系统还能够通过调节液压缸的压力来控制钻进速度和转速,
以适应不同地层条件。
3. 提钻操作:当需要提取钻杆时,液压系统将会逆向运行,通
过液压缸的活塞向上移动,从而提起钻杆。
这样就能够将地下岩
石带至地面,为后续的分析与研究提供样本。
4. 夹紧和传递岩心:在钻进过程中,当钻头钻进一定深度后,
钻机会通过液压系统夹紧岩芯,防止其掉落或损坏。
然后,通过
提钻操作,将夹紧的岩心传输到地面。
5. 深度显示:履带式液压潜孔钻机还配备了深度显示装置,可
以实时监测钻探的深度情况,并记录在数据采集仪中。
这样,工
程人员可以根据深度信息进行钻探数据的分析和处理。
履带式液压潜孔钻机的工作原理主要依靠液压系统的驱动,通
过合理控制液压系统的压力和流量,实现钻探的深入和提取。
它
具有高效、稳定的特点,在岩土工程中起着重要的作用。
履带式钻机安全技术交底模板

一、交底目的为确保履带式钻机在施工过程中的安全使用,预防事故发生,特进行履带式钻机安全技术交底。
二、适用范围本交底适用于所有参与履带式钻机操作、维护及管理人员。
三、交底内容1. 钻机简介履带式钻机是一种主要用于基础施工、地基处理等工程的大型机械。
它具有稳定性好、移动方便、操作简单等特点。
2. 操作人员要求(1)操作人员必须具备一定的机械操作经验,熟悉钻机的基本结构、性能和操作规程。
(2)操作人员应持有相关操作证书,并经过专业培训。
3. 安全操作规程(1)作业前检查1)检查钻机各部件是否完好,液压系统、电气系统是否正常。
2)检查钻杆、钻头、钻具等是否完好,无裂纹、磨损等缺陷。
3)检查钻机基础是否牢固,防止倾覆。
(2)作业中注意事项1)作业时,操作人员应严格遵守操作规程,不得擅自更改操作步骤。
2)操作钻机时,严禁超载、超速、超行程。
3)作业过程中,注意观察钻机运行状态,发现异常情况立即停机检查。
4)钻机运行过程中,禁止在钻杆、钻头等部位进行维修、更换。
5)钻机作业时,应保持施工现场整洁,不得堆放杂物。
(3)作业后处理1)作业结束后,关闭钻机电源,检查各部件是否有损坏。
2)清理施工现场,确保无安全隐患。
4. 钻机维护保养(1)定期检查钻机各部件,发现问题及时更换。
(2)定期对液压系统、电气系统进行保养,确保系统正常运行。
(3)定期对钻杆、钻头、钻具等进行检查,确保其完好。
5. 应急处理(1)发生故障时,立即停机,切断电源,防止事故扩大。
(2)在确保安全的前提下,及时排除故障。
(3)如遇紧急情况,立即启动应急预案,确保人员安全。
四、交底人及日期交底人:(姓名)交底日期:(年月日)五、接受人(姓名)(职务)(部门)六、备注1. 本交底应妥善保管,确保相关人员熟悉掌握。
2. 操作人员应严格遵守本交底规定,确保施工安全。
3. 如有疑问,请及时向交底人咨询。
ZDY6000LD(A)型履带式全液压定向钻机及其应用
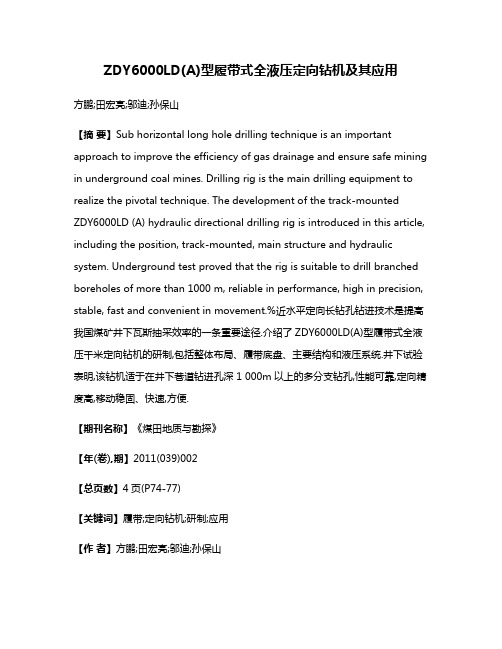
ZDY6000LD(A)型履带式全液压定向钻机及其应用方鹏;田宏亮;邬迪;孙保山【摘要】Sub horizontal long hole drilling technique is an important approach to improve the efficiency of gas drainage and ensure safe mining in underground coal mines. Drilling rig is the main drilling equipment to realize the pivotal technique. The development of the track-mounted ZDY6000LD (A) hydraulic directional drilling rig is introduced in this article, including the position, track-mounted, main structure and hydraulic system. Underground test proved that the rig is suitable to drill branched boreholes of more than 1000 m, reliable in performance, high in precision, stable, fast and convenient in movement.%近水平定向长钻孔钻进技术是提高我国煤矿井下瓦斯抽采效率的一条重要途径.介绍了ZDY6000LD(A)型履带式全液压千米定向钻机的研制,包括整体布局、履带底盘、主要结构和液压系统.井下试验表明,该钻机适于在井下巷道钻进孔深 1 000m以上的多分支钻孔,性能可靠,定向精度高,移动稳固、快速,方便.【期刊名称】《煤田地质与勘探》【年(卷),期】2011(039)002【总页数】4页(P74-77)【关键词】履带;定向钻机;研制;应用【作者】方鹏;田宏亮;邬迪;孙保山【作者单位】中国煤炭科工集团西安研究院,陕西,西安,710077;中国煤炭科工集团西安研究院,陕西,西安,710077;中国煤炭科工集团西安研究院,陕西,西安,710077;中国煤炭科工集团西安研究院,陕西,西安,710077【正文语种】中文【中图分类】P634煤矿井下定向钻进技术是煤矿瓦斯治理和保障高效生产的一项关键技术,也一直是国内倍受关注和积极发展的关键技术。
ZDY6000LD钻机操作规程

ZDY6000LD型履带式全液压坑道钻机操作规程中煤科工集团西安研究院20011年3月、钻机性能介绍1.1适用范围ZDY6000LD煤矿用履带全液压钻机,属于自行式、低转速、大扭矩类型,适于采用复合片钻头施工大直径钻孔,主要用于煤矿井下施工近水平长距离瓦斯抽放钻孔,也可用于地面和坑道近水平工程钻孔的施工。
1.2型号含义Z D Y 6000 L DI—主轴定位________ 履带式_______________________ 最大额定转矩 N.m 液压传动___________________________________ 动力头式钻机1.3主要技术参数回转装置:额定转矩N.m 6000~1800额定转速r/min 50T90油马达型号A6V160MA油马达排量ml/r 46~160钻杆直径mm 73/89主轴通孔直径mm 95给进装置:最大给进/起拔力kN 180给进速度m/s I泵给进0〜0.25U泵给进0〜0.05 起拔速度m/s 0〜0.25给进/起拔行程mm 1000主轴倾角-10° ~20°泵站:液压系统额定压力MPa I /u油泵26/2I泵型号I泵排量ml/rU泵型号U泵排量ml/r油箱有效容积L电动机型号电动机功率kW整机:适用钻孔深度m外形尺寸(长x宽x高)mm钻机质量kg PVT470 〜100PV100 〜20.6240YBK2-280S-4756003380X 1450X 1800约70001.4钻机结构1•履带车体2•泵站3•主机4•操纵台图1钻机结构示意图钻机为整体式布局(见图1),由履带车体、主机、泵站和操纵台四大部分组成,主机、泵站、操纵台之间用高压胶管连接,共同安装在履带车体之上,结构紧凑,便于井下搬迁运输。
、钻机操作方法2.1各操作手把、手轮的位置(见图2)和功能2.1.1操作手把a.马达回转操作手把(1)——用以改变马达的转向。
手把向前推,回转器正转;手把往后拉,回转器反转;手把置于中间位置,回转器停转,马达浮动。
钻神ZSL100A型全液压履带式工程钻机性能简介

0-360
动力头输出转速(rpm)
38;70(可根据施工情况调整)
动力头输出最大扭拒(N·m)
5800
动力头最大行程(mm)
3400;2800(可根据工地情况选配)
副轨道行程(mm)
1000
动力头最大提升力(KN)
1、Hydraulic control rig, its holes fast, accurate, adjust the angle auxiliary time is short, low labor intensity; equipped with hydraulic landing legs to protect the rig stable operation, hole angle precision.
6、钻机通过风冷散热,全液压系统散热性能效果好、安全可靠;通过大油缸倍速给进,具有强劲的拉拔力与给进力,加上其长行程,可以有效地提高钻进效率;采用大扭矩液压双马达输入结构的旋转动力头,尤其解决了对含卵石的粘土钻孔时无法钻孔或偏孔的问题,且效率高。
7、钻机适用于多种钻进工艺:深孔跟管钻进、大口径潜孔锤钻进、麻花钻螺旋钻进等。亦可配置不同规格的动力头来供用户选择,可以满足不同钻进工法的要求,使设备的使用范围更广。
4、钻机钢制履带引进日本小松和美国卡特彼勒技术,其承载能力强、牵引力大、噪音低;底盘配有内藏式低速大扭矩行走马达,具有高通过性能;履带驱动轮齿采用合金钢并经淬火处理,耐磨性好,使用寿命长。
5、钻机结构系统简练紧凑,坚固的设计和优化的运动学体系,符合欧洲联盟严格的安全特性和健康标准,其生产遵守ISO9001质量管理体系的要求。
7、Technology for a variety of drilling rig: drilling hole with the tube, large diameter hole hammer drilling, drilling and other spiral twist. Power of different specifications can also be configured for the user to select the head to meet the different requirements of drilling engineering methods to make wider use of equipment.
ZDY6000LD钻机操作规程

ZDY6000LD(F)型煤矿用履带式全液压坑道钻机操作规程一、适用范围第1条本技术操作规程适用于贵州黔西能源开发有限公司青龙煤矿ZDY6000LD(F)型煤矿用履带式全液压坑道钻机施工各类钻孔的操作。
第2条 ZDY6000LD(F)型煤矿用履带式全液压坑道钻机(以下简称“钻机”)属于自行式、低转速、大转矩类型,在煤矿井下稳定中硬煤层中,既适于采用孔口动力及复合片钻头施工大直径钻孔,也可采用孔底动力机具钻进定向钻孔。
能够满足钻进各种用途钻孔的需要,如高位钻孔、地质勘探孔、探放水钻孔、抽采瓦斯孔,注水孔及其它工程用孔也可用于地表工程施工。
二、上岗条件第3条 ZDY6000LD(F)型煤矿用履带式全液压坑道钻机的操作人员必须经过钻机操作知识的专业技术培训,考试合格,取得钻机操作证后,方可上岗。
第4条上岗条件及职责:a. 必须熟悉钻机的工作原理,定向钻机轨迹控制,掌握ZDY6000LD(F)型钻机的操作要领、维护保养及排除故障的知识和事故处理办法。
b. 了解本矿井发生煤与瓦斯突出的预兆和规律,掌握施工区域的通风系统和避灾路线。
c. 掌握抽采钻孔、测压钻孔、探放水钻孔等钻孔的封孔工艺方法。
d. 了解“一通三防”基础知识。
三、安全规定第5条操作人员必须经过培训才可使用本钻机。
第6条操作人员使用钻机必须详细阅读说明书。
第7条操作人员随身衣物应合身并束紧,以免缠上钻机的运动部件而对肢体造成损伤。
第8条钻机工作时,钻机锚固必须牢固,防止倒下伤人。
第9条严格按照说明书要求调定钻机工作压力。
第10条启动钻机前,操作人员应通知所有人员注意安全,在确认人员和设备都安全后,方可启动钻机运转。
第11条严禁非专业维修人员调整钻机系统压力,专业维修人员对钻机系统压力进行调整时,必须严格按照随机说明书限定压力进行调整,系统压力不得超调,且调整系统压力时必须停止钻机运行并停电将开关手把打到零位;调整钻机转速及推进速度时,必须确保钻机四周人员或物料与钻机间有足够安全距离,必须先调整钻机转速后调整钻机推进速度。
- 1、下载文档前请自行甄别文档内容的完整性,平台不提供额外的编辑、内容补充、找答案等附加服务。
- 2、"仅部分预览"的文档,不可在线预览部分如存在完整性等问题,可反馈申请退款(可完整预览的文档不适用该条件!)。
- 3、如文档侵犯您的权益,请联系客服反馈,我们会尽快为您处理(人工客服工作时间:9:00-18:30)。
回油
油 缸
3.泵站 3.泵站
液压油泵采用进口件, 液压油泵采用进口件, 性能先进,可靠性高; 性能先进,可靠性高;弹联 轴器采用梅花型,寿命长; 轴器采用梅花型,寿命长; 冷却装置采用并联三片板 翘式结构,冷却效果明显, 翘式结构,冷却效果明显, 提高了系统效能
a.卡转联动:回转器正、反转时,回转油路中的部分 a.卡转联动:回转器正、反转时, 卡转联动 高压油通过单向阀进入液压卡盘, 高压油通过单向阀进入液压卡盘,使卡盘自动卡紧 钻杆
b.卸扣联动:反转时, b.卸扣联动:反转时,部分高压油进入夹持器的 卸扣联动 副油缸,以增加夹持器的夹紧能力, 副油缸,以增加夹持器的夹紧能力,防止打滑
四.液压系统
1.行走马达 3.回转马达 4.卡盘 5.夹持器 6.给油缸 1.行走马达 2. 液控先导手动阀 3.回转马达 4.卡盘 5.夹持器 6.给油缸 8.支撑油缸控制阀 9.负载敏感泵 7. 四联比例多路换向阀 8.支撑油缸控制阀 9.负载敏感泵 10. 恒压变量泵
液压原理示意图
Ⅰ泵循环原理图
一.研制背景
瓦斯抽放是防治煤矿瓦斯灾害事故的治本 性措施,钻孔抽放是瓦斯抽放的基本手段 性措施, 煤矿安全高效的生产要求,使煤炭采掘与 煤矿安全高效的生产要求, 瓦斯钻孔施工速度的矛盾日益突出, 瓦斯钻孔施工速度的矛盾日益突出,对成 孔速度提出了更高要求
目前制约成孔速度主要有两大因素
1.钻机搬迁拆装等辅助时间长(MK- 型钻机使用统计) 1.钻机搬迁拆装等辅助时间长(MK-7型钻机使用统计) 钻机搬迁拆装等辅助时间长(MK
下面内容
一.研制背景 二.主要技术参数 三.钻机结构 四.液压系统 五.创新点
五.创新点
具有定向钻进主轴制动功能, 具有定向钻进主轴制动功能, 可 同时满足孔口回转和孔底马达回 转两种钻进工艺 在国内坑道钻机中首次采用负载 敏感控制系统 单泵和压力补偿控制两片履带, 单泵和压力补偿控制两片履带, 具备直线行走及原地转向功能 带伸缩补偿装置的稳固调角装置 多路阀采用先导压力控制
搬迁拆装 2.分体式钻机经常拆装, 液压系统易污染, 2.分体式钻机经常拆装, 液压系统易污染,故障率提 分体式钻机经常拆装 高,油液损失严重
a.采用履带自行,解决搬迁费时、 a.采用履带自行,解决搬迁费时、劳动 采用履带自行 强度大的问题 b.采用整体式结构,油管不拆装, b.采用整体式结构,油管不拆装,系统不 采用整体式结构 污染, 污染,工作可靠性高
孔口回转钻进: 孔口回转钻进: 回转器带动钻杆 和钻头旋转钻进 孔底马达钻进: 孔底马达钻进: 钻杆不转, 钻杆不转,孔底 马达带动钻头旋 转钻进
五.创新点
浮动装 置 进油
回油
油 缸
液压系统特点
双泵供油独立工作 负载敏感泵+ 负载敏感泵+负载敏感多路阀组 无压力、 合, 无压力、溢流损失 多种执行机构联动功能,同时各 多种执行机构联动功能, 机构有独立工作机能 多路阀带有压力补偿功能, 多路阀带有压力补偿功能,多联 阀同时工作各自所需的流量和 压力互不影响 履带半坡驻车自锁, 履带半坡驻车自锁,过载自动保 护 先导控制 系统启动瞬间流量特性曲线 流量特性曲线
三.钻机结构
钻机为整体式布局,结构紧凑, 钻机为整体式布局,结构紧凑,便于井下搬迁运输
泵站 主机 操纵台
履带 车体
1.履带车体 1.履带车体
行走装置 车体平台 稳固调角油缸
行走装置
履带:采用四轮一带组件, 履带:采用四轮一带组件,计专 用结构与钻机车体连接 行走马达:内藏式定量马达, 行走马达:内藏式定量马达,具 有驻车自锁功能
b.液压卡盘的回油由液控单向阀与节流阀联合控制, b.液压卡盘的回油由液控单向阀与节流阀联合控制, 液压卡盘的回油由液控单向阀与节流阀联合控制 即卡紧时单向阀关闭,松开时单向阀打开, 即卡紧时单向阀关闭,松开时单向阀打开,卡盘中的 液压油直接回到油箱。 液压油直接回到油箱。卡盘松开的速度可通过节流阀 调节
2.主机 2.主机
回转 器 夹持 器 给进装 置
给进装置为两根双杆双作用缸直接驱动, 给进装置为两根双杆双作用缸直接驱动,带动拖板 和回转器沿机身导轨移动,整体钢性好 钢性好, 和回转器沿机身导轨移动,整体钢性好,可靠性高
回转器
设计有主轴制动功 设计有主轴制动功 主轴制动 能的液控抱紧装置
胶囊式液压卡盘 胶囊式液压卡盘 主轴为通孔式结构 主轴为通孔式结构 通孔式
4.操纵台 4.操纵台
油路设计功能模块化, 油路设计功能模块化, 集成式油路板设计 操纵习惯与ZDY系列钻 操纵习惯与ZDY系列钻 ZDY 机一致 管件接头全部采“ 管件接头全部采“C” 型接头, 型接头,锥面机械硬密 封,密封可靠
下面内容
一.研制背景 二.主要技术参数 三.钻机结构 四.液压系统 五.创新点
最大额定转矩 /N.m 主轴制动扭矩 /N.m 额定转速 /r/min 最大给进/ 最大给进/起拔力 /kN 主轴倾角 电动机功率 /kW 行走速度 /km/h 最大爬坡能力 6000 1500 5~250 210 -10o~20o 75 0~ 5 20° 20°
下面内容
一.研制背景 二.主要技术参数 三.钻机结构 四.液压系统 五.创新点
Ⅰ泵调试
• 初次运转前要从Ⅰ泵泄油口或高压出口加液 压油,边加油边拨转联轴器 • 初始压力调至(1.5~2) MPa;泵压调至26 MPa
Ⅱ泵循环原理图
Ⅱ泵调试
• 初次运转前要从 Ⅱ泵泄油口或高 压出口加液压油, 边加油边拨转联 轴器 • 泵压调至21 MPa
1.液压联动回路 1.液压联动回路
车体平台
用来安装固定操纵台、主机、 用来安装固定操纵台、主机、泵站等各部分结构
稳固调角油缸
位置、数量:在车体四角位置,设有四对 位置、数量:在车体四角位置, 特点:缸尾两两对接, 特点:缸尾两两对接,动作可单独控制 具备液压锁紧, 具备液压锁紧,可有效保压 应用:车体稳固、机身调角方便可靠, 应用:车体稳固、机身调角方便可靠,适 应性强
ZDY6000LD履带式 ZDY6000LD履带式 全液压坑道钻机技术交流
煤科总院西安研究院 钻探技术与装备研发中心
ZDY6000LD履带式全液压坑道钻机 ZDY6000LD履带式全液压坑道钻机
主要内容: 主要内容:
研制背景 主要技术参数 钻机结构 液压系统 创新点
下面内容
一.研制背景 二.主要技术参数 三.钻机结构 四.液压系统 五.创新点
夹持器(复合式) 夹持器(复合式)
特点:结构紧凑,夹持力大, 特点:结构紧凑,夹持力大,自动对中 难点: 难点:承压面积大小与其他机构的配合关系
给进装置
采用矩壳箱式机身结构, 采用矩壳箱式机身结构,双杆双作用油缸并 列布局,钻机能力大。 列布局,钻机能力大。机身结构易于实现钻机大 倾角调整 浮动装 油缸浮动装置
下面内容
一.研制背景 二.主要技术参数 三.钻机结构 四.液压系统 五.创新点
二.主要技术参数
该机研制主要针对施工600m以内近水平大直径瓦斯 该机研制主要针对施工600m以内近水平大直径瓦斯 600m 抽放孔。为适应用户对精确定向钻进的需求,设计了孔 抽放孔。为适应用户对精确定向钻进的需求, 底动力钻进时主轴制动装置,主要技术性能参数如下: 底动力钻进时主轴制动装置,主要技术性能参数如下:
c.为防止心轴卡死后, c.为防止心轴卡死后,因回转马达转动而损坏机件的 为防止心轴卡死后 事故,在马达回转油路设计特殊油路装置, 事故,在马达回转油路设计特殊油路装置,由抱紧装 置油路进行控制, 置油路进行控制,从而避免了因误操纵所出现的事故
d.油缸浮动装置:钻杆拧卸丝扣时, d.油缸浮动装置:钻杆拧卸丝扣时,仅克服回转器托 油缸浮动装置 板浮动移动阻力,不须克服液压系统阻力, 板浮动移动阻力,不须克服液压系统阻力, 从而有 效避免钻杆丝扣被拉伤或挤坏, 效避免钻杆丝扣被拉伤或挤坏,提高钻杆使用寿命
c.夹转联动:可实现正转时卡盘卡紧、 c.夹转联动:可实现正转时卡盘卡紧、夹持器自动 夹转联动 松开,停止回转后,夹持器自动卡紧, 松开,停止回转后,夹持器自动卡紧,防止因误 操作引起滑杆事故
d.起下钻联动: d.起下钻联动:在起钻或下钻工况下实现给进油缸与卡 起下钻联动 夹持器之间的联动。由于卡盘、 盘、夹持器之间的联动。由于卡盘、夹持器自身工作原 理不同,可保证实现“先卡紧,后松开”的特殊要求。 理不同,可保证实现“先卡紧,后松开”的特殊要求。 当该阀处于中位时取消联动,可单独使给进油缸运动, 当该阀处于中位时取消联动,可单独使给进油缸运动, 增加其机动性
2.特殊功能回路 2.特殊功能回路
a.在起钻油路中串一个液控双向节流阀, a.在起钻油路中串一个液控双向节流阀,通调节 在起钻油路中串一个液控双向节流阀 阀的开度改变系统压力, 阀的开度改变系统压力,协调给进油缸与夹持器的 动作, 动作,避免起下钻时因系统压力过低夹持器不能完 全张开, 全张开,造成钻杆擦伤