日产3000吨水泥熟料窑尾预热器与分解炉系统设计
日产3000吨水泥熟料窑尾预热器与分解炉系统设计

1前言1.1水泥产业发展概述我国是水泥生产大国,水泥工业是我国国民经济建设的重要基础材料产业,在国民经济可持续发展中具有举足轻重的地位。
随着现代化建设的持续、稳定发展,我国水泥工业正面临着更好更快地发展、完善自身、节能环保的重任[1]。
水泥生产过程中,最重要的工艺环节是将化学成分合格的生料煅烧成既定矿物组成的熟料的过程[2]。
此过程所使用的设备包括旋风筒预热器、分解炉、回转窑和篦冷机等,这些设备即为构成窑尾系统的主要设备。
伴随着水泥工业生产技术的发展,熟料煅烧设备经历了立窑、干法中空窑、湿法窑、立波尔窑、预热器窑以及预分解窑的变化。
对于水泥工业窑炉,国内外主要研究机构均依据水泥熟料形成热、动力学机制,研究水泥窑炉工艺过程,并对各设备子系统工作机理和料气运动、换热规律进行探讨[3]。
通过建立单级和多级粉体悬浮热交换器热力学理论模型和分解炉系统热稳定性理论模型,建立全系统的热效率模型,系统研究了悬浮预热器和分解炉的热效率及其影响因素、悬浮预热器系统特性组合流程、流场、温度场、浓度场的合理分布和碳酸盐分解及固液相反应动力学特性,并以此为理论指导,开发出新型干法水泥熟料生产技术装备[4]。
1.2国内外研究现状天津水泥工业设计研究院有限公司开发的TDF分解炉,具有三喷腾和碰顶效应、湍流回流作用强、固气停留时间比大、温度场及浓度场均匀、物料分散及换热效果好、阻力系数低等特点[5]。
交叉料流型预分解法在保证全系统固气比不变的前提下,可使每级预热器单体的固气比提高,从而提高系统的热效率。
采用这种生产方法可提高生料入窑分解率,降低预热器出口气体温度及分解炉操作温度[6]。
整个系统在相对低温下操作可以减少钾、钠、氯盐及一些低熔点矿物形成,有利于系统稳定操作,减少预热器及分解炉结皮堵塞。
如西安建筑科技大学徐德龙院士团队发明的悬浮态高固气比预热分解技术[7]。
以Prepol和Pyro⁃clon型炉[8]为代表的管道式分解炉,主要依靠“悬浮效应”加强气固换热,炉内湍流强度较小,一般以增大炉容为主要措施,保证分解炉的功效发挥,故其单位容积热负荷及单位容积产量相对其他炉型来说,都是比较小的。
日产3000吨水泥熟料窑尾预热器与分解炉系统设计
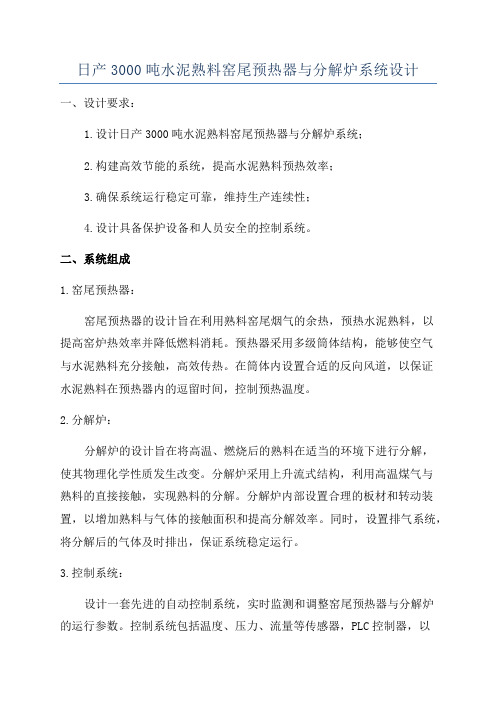
日产3000吨水泥熟料窑尾预热器与分解炉系统设计一、设计要求:1.设计日产3000吨水泥熟料窑尾预热器与分解炉系统;2.构建高效节能的系统,提高水泥熟料预热效率;3.确保系统运行稳定可靠,维持生产连续性;4.设计具备保护设备和人员安全的控制系统。
二、系统组成1.窑尾预热器:窑尾预热器的设计旨在利用熟料窑尾烟气的余热,预热水泥熟料,以提高窑炉热效率并降低燃料消耗。
预热器采用多级筒体结构,能够使空气与水泥熟料充分接触,高效传热。
在筒体内设置合适的反向风道,以保证水泥熟料在预热器内的逗留时间,控制预热温度。
2.分解炉:分解炉的设计旨在将高温、燃烧后的熟料在适当的环境下进行分解,使其物理化学性质发生改变。
分解炉采用上升流式结构,利用高温煤气与熟料的直接接触,实现熟料的分解。
分解炉内部设置合理的板材和转动装置,以增加熟料与气体的接触面积和提高分解效率。
同时,设置排气系统,将分解后的气体及时排出,保证系统稳定运行。
3.控制系统:设计一套先进的自动控制系统,实时监测和调整窑尾预热器与分解炉的运行参数。
控制系统包括温度、压力、流量等传感器,PLC控制器,以及人机界面。
通过自动控制系统,实现燃烧过程的自动调整,提高系统的稳定性和能耗效率。
系统还要具备报警和安全保护装置,确保设备及人员的安全。
三、系统工作原理1.窑尾预热器工作原理:熟料窑尾的高温废气通过窑尾预热器进入多级筒体结构,与水泥熟料进行热交换。
同时,预热器内通过设置合适的反向风道,控制水泥熟料在预热器内的逗留时间和热风向上的流动方向。
通过热交换,把窑尾烟气中的余热传递给水泥熟料,使得水泥熟料的温度逐渐升高。
2.分解炉工作原理:经过窑尾预热器预热的水泥熟料进入分解炉内,在高温煤气的作用下完成分解过程。
分解炉内的高温煤气直接与水泥熟料进行接触,通过热量传导和导流作用,使水泥熟料中的矿物质发生分解反应,生成新的物质,提高熟料的活性和可磨性。
四、系统优势1.高效节能:通过窑尾预热器利用余热和分解炉的高温煤气,实现废热回收,提高熟料的热效率,降低能源消耗;2.环保节能:废气经过预热器与分解炉的处理,减少高温废气的排放;3.连续生产:系统能够保证稳定运行,实现连续生产;4.自动控制:系统设有自动控制装置,能够实现自动监测和调整参数,提高系统的稳定性和能耗效率。
日产5000t水泥熟料预分解窑窑尾工艺设计说明书

日产5000t水泥熟料预分解窑窑尾工艺设计说明书5000t/d水泥分解窑窑尾(低氮氧化合物排放)工艺设计摘要:水泥是社会经济发展最重要的建筑材料之一,在今后几十年甚至是上百年之内仍然是无可替代的基础材料,对人;低氮排放;工艺设计The Process Design of the Back End ofPrecalciner Kiln for 5000T/D CementClinker(Low Nitrogen OxideEmissions)Abstract:Cement is one of the most important building materials of the social and economic development, within the coming decades or even a century,Cement is still no substitute for basic materials, the importance of human civilization is self-evident.calciner kiln as the representatives has become leading technology and the most advanced technology of the cement industry. It has many advantages, such as high throughput, a high degree of auto mation, high quality products, low energy consumption, low emissions of harmful substances, etc.In the production process of cement will release a number of harmful substances,particularly nitrogen oxides,according to the requirement of this design,the design uses a range of methods to reduce the concentration of nitrogen oxide .Based on the design of new dry cement production technology in today's design requirements, the main task is the back-end part of the process design, including the production of cement raw materials, fuel quality requirements, the design of ingredients and ingredients, the material balance calculation , the main auxiliarybalance and equipment selection, calculation and storage back-end process design.Key words: 5000T / D, Low Nitrogen Emissions, Process Precalciner kiln, Design目录第1章绪论........................................................... ..11.1 引言 (1)1.2设计简介 (1)第2章建厂基本资料 (3)2.1设计题目 (3)2.2建厂条件 (3)2.3原料质量要求 (3)2.3.1水泥原料质量要求 (3)2.3.2石膏和混合材质量要求 (4)2.4燃料品质要求 (5)2.5熟料热耗的选择 (6)2.6生产方法和窑型的选择 (6)第3章配料计算与物料和主机平衡 (8)3.1配料计算 (8)3.1.1原料 (24)3.3主机平衡与选型 (24)3.3.1车间工作制度确定 (24)3.3.2主机选型 (25)3.3.3主机平衡表 (32)第4章储库计算 (33)4.1各种物料储存期的确定 (33)4.2各种原料储存设施的计算 (34)4.2.1石灰石、原煤、联合预均化堆场、石膏、矿渣预均化堆场计算 (34)4.2.1.1石灰石预均化堆场计算 (34)4.2.1.2原煤预均化堆场计算 (35)4.2.1.3联合储库计算 (36)4.2.1.4石膏、矿渣预均化堆场计算 (36)4.3各种物料的储存设施计算 (37)4.3.1生料配料站.............................................. ... .374.3.2生料均化库............................................. .... .394.3.3熟料库.................................................. ... .404.3.4熟料配料站 (40)4.4水泥库计算 (41)4.5储库一览表 (42)第5章物料和热平衡计算 (43)5.1原始资料................................................... . (43)5.2物料平衡与热平衡计算 (44)5.2.1 物料平衡计算 (44)5.2.2 热平衡计算 (50)5.3物料平衡表与热平衡表的编制................................... ..54 第6章窑外分解系统的设计计算.. (56)6.1原始资料..................................................... ..566.2相关参数的设定 (56)6.3单位烟气的 (61)6.7分解炉结构尺寸计算........................................... ..63 6.8旋风筒设计方案选择. (66)6.9旋风筒结构尺寸计算 (68)6.10分解炉与旋风筒尺寸汇总表 (75)第7章窑尾设备的 (91)致谢................................................................. .. .92 参考文献.......................................................... .. .. ..93第一章绪论1.1引言我国氮氧化合物的排放量年增长5%-8%,如果不采取进一步的的减排措施,到2030年我国氮氧化合物排放量将达到3540吨,如此巨大的排放量讲给公众健康和生态环境带来灾难家有着明显差距,同时水泥行业排污严重的情况下,为了使我国水泥工业实现可持续发展,必须加大发展新型干法水泥生产技术和水泥产业结构调整的力度,同时通过对各种设备的改进达到低碳低氮氧化合物排放的目标。
日产5000t水泥熟料NSP窑的设计(说明书)

洛阳理工学院课程设计说明书课程名称:新型干法水泥生产技术与设备设计课题:5000t/d水泥熟料NSP窑的设计专业:无机非金属材料工程班级:学号:姓名:成绩:指导教师(签名):年月日课程设计任务书设计课题:5000t/d水泥熟料NSP窑的设计一、课题内容及要求:1.物料平衡计算2.热平衡计算3.窑的规格计算确定4.主要热工技术参数计算5.NSP窑初步设计:工艺布置与工艺布置图(窑中)二、课题任务及工作量1.设计说明书(不少于1万字,打印)2.NSP窑初步设计工艺布置图(1号图纸1张,手画)三、课题阶段进度安排1.第15周:确定窑规格、物料平衡与热平衡计算、主要热工参数计算2.第16周:NSP窑工艺布置绘图四、课题参考资料李海涛. 新型干法水泥生产技术与设备[M].化学工业出版社严生.新型干法水泥厂工艺设计手册[M].中国建材工业出版社金容容.水泥厂工艺设计概论[M].武汉理工大学出版社2011.5.3设计原始资料一、物料化学成分(%)二、煤的工业分析及元素分析三、热工参数1. 温度a. 入预热器生料温度:50℃;b. 入窑回灰温度:50℃;c. 入窑一次风温度:20℃;d. 入窑二次风温度:1100℃;e. 环境温度:20℃;f. 入窑、分解炉燃料温度:60℃;g. 入分解炉三次风温度:900℃;h. 出窑熟料温度:1360℃;i. 废气出预热器温度:330℃;j. 出预热器飞灰温度:300℃;2. 入窑风量比(%)。
一次风(K1):二次风(K2):窑头漏风(K3)=10:85:5;3. 燃料比(%)。
回转窑(Ky ):分解护(KF)=40:60;4. 出预热器飞灰量:0.1kg/kg熟料;5. 出预热器飞灰烧失量:35.20%;6. 各处过剩空气系数:窑尾αy =l.05;分解炉出口αL=1.15;预热器出口αf=1.40;7.入窑生料采用提升机输送;8.漏风:预热器漏风量占理论空气量的比例K4=0.16;分解炉及窑尾漏风(包括分解炉一次空气量),占分解炉用燃料理论空气量的比例K6=0.05;9. 袋收尘和增湿塔综合收尘效率为99.9%;10. 熟料形成热:根据简易公式(6-20)计算;11. 系统表面散热损失:460kJ/kg熟料;12. 生料水分:0.2%;13. 窑的设计产量:5000t/d(或208.33t/h)。
日产3000吨熟料预分解窑的分解炉设计
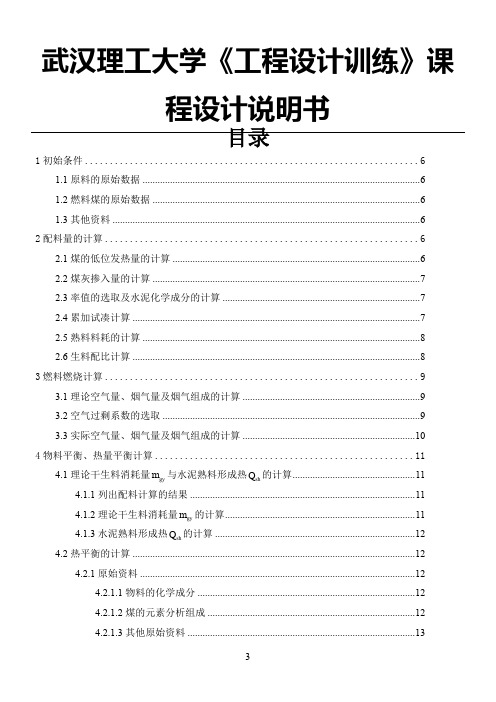
程设计说明书目录1初始条件 (6)1.1原料的原始数据 ............................................................................................................... 6 1.2燃料煤的原始数据 ........................................................................................................... 6 1.3其他资料 ........................................................................................................................... 6 2配料量的计算 (6)2.1煤的低位发热量的计算 ................................................................................................... 6 2.2煤灰掺入量的计算 ........................................................................................................... 7 2.3率值的选取及水泥化学成分的计算 ............................................................................... 7 2.4累加试凑计算 ................................................................................................................... 7 2.5熟料料耗的计算 ............................................................................................................... 8 2.6生料配比计算 ................................................................................................................... 8 3燃料燃烧计算 (9)3.1理论空气量、烟气量及烟气组成的计算 ....................................................................... 9 3.2空气过剩系数的选取 ....................................................................................................... 9 3.3实际空气量、烟气量及烟气组成的计算 ..................................................................... 10 4物料平衡、热量平衡计算 . (11)4.1理论干生料消耗量gy m 与水泥熟料形成热sh Q 的计算 (11)4.1.1列出配料计算的结果 .......................................................................................... 11 4.1.2理论干生料消耗量gy m 的计算 ............................................................................ 11 4.1.3水泥熟料形成热sh Q 的计算 ................................................................................ 12 4.2热平衡的计算 .. (12)4.2.1原始资料 (12)4.2.1.1物料的化学成分 ....................................................................................... 12 4.2.1.2煤的元素分析组成 ................................................................................... 12 4.2.1.3其他原始资料 . (13)程设计说明书4.2.2确定平衡系统与平衡计算的依据 (14)5设备尺寸的计算 ........................................... 错误!未定义书签。
窑尾预热器与分解炉的功能及作用
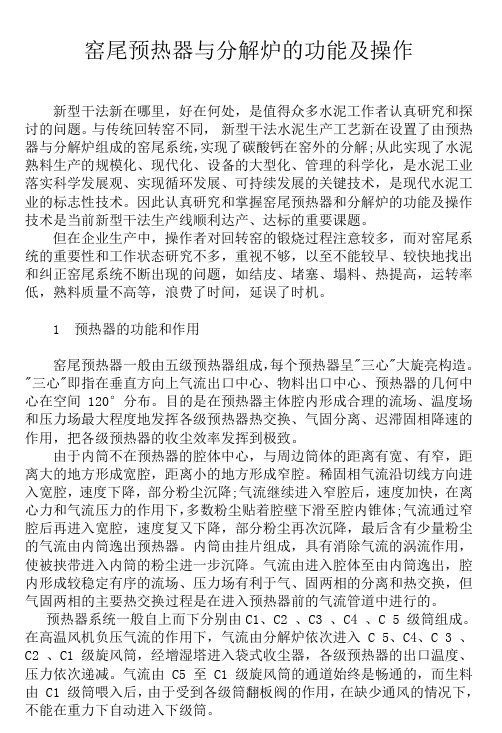
如C1、C2、C3、C4,C5级筒的收尘效率下降,将使本级筒内已进行充分热交换的生料又返回上级筒与低温稀固相气流混合,造成热量的损失和浪费。所以各级预热器的收尘效率是影响窑尾系统正常、高效运行的重要参数。从理论上讲各级预热器的收尘效率应当是越高越好,但追求过高的收尘效率将使系统阻力增加,导致过多的压力损失,窑尾风机功率的增加,同样是一种能量的损失。设计中已对预热器系统的阻力和风机功率进行了恰当配置保持收尘效率设计参数的稳定是十分必要和重要的。在正常生产中,影响各级预热器收尘效率的因素主要是内筒的长短,挂片的完好程度以及翻板阀的工作状态等,此外风量的变化,给料量的变化也都对收尘效率有或多或少的影响,因此提高操作水平,保持各级预热器较高的收尘效率是水泥企业生产管理上的一个重要课题。在预热器设计参数确定之后,内筒尺寸长短的变化将决定预热器的收尘效率。一般说,内筒长度不变,收尘效率不变,由于磨损、烧失,长度变短,收尘效率将随之呈线性下降,挂片磨损、烧失,部分进口气流易从出口短路,收尘效率则有较大的下降。
由于内筒不在预热器的腔体中心,与周边筒体的距离有宽、有窄,距离大的地方形成宽腔,距离小的地方形成窄腔。稀固相气流沿切线方向进入宽腔,速度下降,部分粉尘沉降;气流继续进入窄腔后,速度加快,在离心力和气流压力的作用下,多数粉尘贴着腔壁下滑至腔内锥体;气流通过窄腔后再进入宽腔,速度复又下降,部分粉尘再次沉降,最后含有少量粉尘的气流由内筒逸出预热器。内筒由挂片组成,具有消除气流的涡流作用,使被挟带进入内筒的粉尘进一步沉降。气流由进入腔体至由内筒逸出,腔内形成较稳定有序的流场、压力场有利于气、固两相的分离和热交换,但气固两相的主要热交换过程是在进入预热器前的气流管道中进行的。
日产4000吨水泥熟料新型干法生产线窑尾系统工艺设计精品
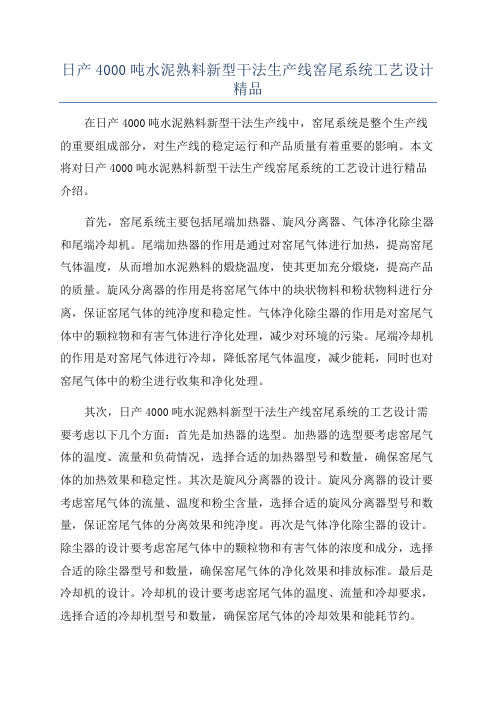
日产4000吨水泥熟料新型干法生产线窑尾系统工艺设计精品在日产4000吨水泥熟料新型干法生产线中,窑尾系统是整个生产线的重要组成部分,对生产线的稳定运行和产品质量有着重要的影响。
本文将对日产4000吨水泥熟料新型干法生产线窑尾系统的工艺设计进行精品介绍。
首先,窑尾系统主要包括尾端加热器、旋风分离器、气体净化除尘器和尾端冷却机。
尾端加热器的作用是通过对窑尾气体进行加热,提高窑尾气体温度,从而增加水泥熟料的煅烧温度,使其更加充分煅烧,提高产品的质量。
旋风分离器的作用是将窑尾气体中的块状物料和粉状物料进行分离,保证窑尾气体的纯净度和稳定性。
气体净化除尘器的作用是对窑尾气体中的颗粒物和有害气体进行净化处理,减少对环境的污染。
尾端冷却机的作用是对窑尾气体进行冷却,降低窑尾气体温度,减少能耗,同时也对窑尾气体中的粉尘进行收集和净化处理。
其次,日产4000吨水泥熟料新型干法生产线窑尾系统的工艺设计需要考虑以下几个方面:首先是加热器的选型。
加热器的选型要考虑窑尾气体的温度、流量和负荷情况,选择合适的加热器型号和数量,确保窑尾气体的加热效果和稳定性。
其次是旋风分离器的设计。
旋风分离器的设计要考虑窑尾气体的流量、温度和粉尘含量,选择合适的旋风分离器型号和数量,保证窑尾气体的分离效果和纯净度。
再次是气体净化除尘器的设计。
除尘器的设计要考虑窑尾气体中的颗粒物和有害气体的浓度和成分,选择合适的除尘器型号和数量,确保窑尾气体的净化效果和排放标准。
最后是冷却机的设计。
冷却机的设计要考虑窑尾气体的温度、流量和冷却要求,选择合适的冷却机型号和数量,确保窑尾气体的冷却效果和能耗节约。
总之,日产4000吨水泥熟料新型干法生产线窑尾系统的工艺设计需要综合考虑加热器、旋风分离器、气体净化除尘器和冷却机等组成部分的选型和设计,确保窑尾气体的加热、分离、净化和冷却效果,以及对环境的污染和能耗的控制,进一步提高水泥熟料生产线的稳定运行和产品质量。
日产7000吨熟料预分解窑的分解炉设计精品

日产7000吨熟料预分解窑的分解炉设计精品日产7000吨熟料预分解窑的分解炉设计1 原料配比计算1.1煤的低位发热量计算1.1.1燃料煤的原始资料1.1.2低位发热量计算. 3391030109()25 =33962.59+1030 4.20-109-0.31-25 1.01=24667.5(kJ/kg-)net ad ad ad ad ad adQ C H O S M =+---(8.12)煤1.2煤灰掺入量计算根据参考文献[1]中p175相关知识,取水泥熟料的实际形成热q = 2900kJ/kg -熟料,取煤灰沉落率%100 =S ,可知:100290022.6110010024667.52.66%ad A net adqA SG Q =??=?=,1.3配料方案原始数据1.3.1率值、热耗预设查阅参考文献[1] 中p174相关信息,预设:KH = 0.90,SM = 2.30,IM = 1.70,∑=97.5%1.3.2熟料成分预算23100%(2.81)(1) 2.65 1.3597.50100%(2.80.901)(1.701) 2.30 2.65 1.7 1.353.52%Fe O KH IM SM IM ∑=?++++=??+?+?+?+=2323 () 1.7 3.52% 5.98%Al O IM Fe O ==?= 22323 () 2.2(5.98% 3.52%) 21.85%SiO SM Al O Fe O =+=?+= 22323 () 97.50%(21.85%+5.98%+3.52%) 66.15%CaO SiO Al O Fe O =∑-++=-= 1.4递减试凑求配合比过程1.4.1原料的原始资料1.4.2递减试凑过程及核算熟料化学成分与率值根据参考文献[1]中176页的相关知识,利用递减配料计算如下:表1-3 递减法配料计算表(以100kg 熟料为基准)1.4.3配合比计算 1.4.3.1干物料配比及烧失量计算根据上表可求煅烧100kg 熟料所需各种干原料用量为:石灰石 = 121.12kg 粘土 = 27.15kg 铁粉 = 2.52kg各种原料配合比为:121.12100%121.1227.15 2.5280.32%=?++=石灰石 27.15100%121.1227.15 2.5218.01%=?++=粘土2.52100%121.1227.15 2.521.67%=?++=铁粉干生料烧失量Ls=?∑各原料所占百分比该原料的烧失量=80.32%43.13%18.01% 4.32% 1.67% 1.25%=35.44%?+?+?1.4.3.2湿物料配比及水分计算各种湿生料用量=1-各种干生料用量各种湿生料含水率湿生料总含水率Ws=*∑各原料所占百分比该原料的含水率=80.28%×1.0%+18.00%×1.0%+1.72%×4.0%=1.052%各种物料损失均按3%计算,所以不影响各组分的含量。
日产4000吨分解炉课程设计

课程设计说明书日产4000吨熟料现代化干法生产水泥厂设计(重点车间:分解炉)学院:材料科学与工程学院课程名称:制品机械设备课程设计专业班级:无机非金属材料工程班学生姓名:学号:指导教师:摘要水泥是社会经济发展最重要的建筑材料之一,在今后几十年甚至是上百年之内仍然是无可替代的基础材料,对人类生活文明的重要性不言而喻。
现代最先进的水泥生产技术就是新型干法预分解窑。
预分解窑是在悬浮预热器与回转窑之间增设分解炉,在分解炉中加入占总用量50%-60%的燃料,使燃料燃烧的过程与生料碳酸盐分解的吸热过程在悬浮状态或沸腾状态下迅速进行,从而使入窑生料的分解率从悬浮预热窑的30%-40%提高到85%-90%,使窑的热负荷大为减轻,窑的寿命延长,而窑的产量却可成倍增长。
与悬浮预热器窑相比,在单机产量相同的条件下,预分解窑具有:窑的体积小,占地面积减小,制造、运输和安装较易,基建投资较低,且由于一半以上的燃料是在温度较低的分解炉内燃烧,,产生有害气体NOx较少,减少了对大气的污染。
为了符合当今水泥行业的发展需求同时也是对大学本科四年所学知识的考查,我选择了“日产4000吨熟料现代化干法生产水泥厂初步设计”这个课题作为我的毕业设计课题。
设计范围主要是分解炉,通过配料计算、工艺平衡计算等得出结果,并结合实际对主机及附属设备进行选型,进而对各种设备进行工艺布置,对全厂的设备进行简单规划。
关键词:水泥;新型干法预分解窑;分解炉设计任务书第一节设计目的此次课程设计是进入大学以来的第一次设计课程,也是在参加了生产实习后的一次总结。
基于在学习了《制品机械设备课程设计》,并结合本专业的发展特色而开设的一项重要的实践学习环节。
其目的在于通过课程设计的锻炼,树立正确的设计思想,培养我们认真的科学态度和严谨求实的工作作风。
在设计过程中培养我们学生掌握绘图、计算、研究等科学设计方法,提高工程设计计算,锻炼我们分析解决实际问题的能力。
第二节设计原则与指导思想1.根据任务书规定产品品种、质量、规模进行设计;2.选择技术先进、经济合理的工艺流程和设备;3.主要设备的能力应与生产规模相适应;4.满足工艺要求,确保工艺畅通;5.充分考虑安全因素,确保安全生产。
课程设计--日产3200吨熟料预分解窑的分解炉设计
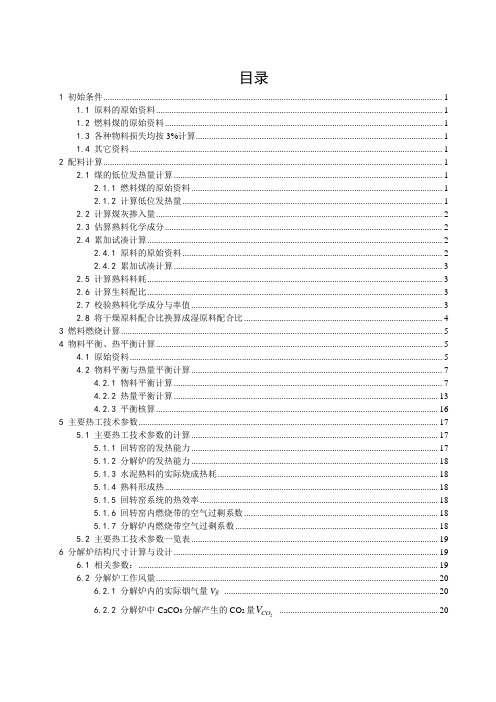
目录1 初始条件 (1)1.1 原料的原始资料 .................................................................................................................................. 1 1.2 燃料煤的原始资料 .............................................................................................................................. 1 1.3 各种物料损失均按3%计算 ................................................................................................................ 1 1.4 其它资料 .............................................................................................................................................. 1 2 配料计算 . (1)2.1 煤的低位发热量计算 (1)2.1.1 燃料煤的原始资料 .................................................................................................................. 1 2.1.2 计算低位发热量 ...................................................................................................................... 1 2.2 计算煤灰掺入量 .................................................................................................................................. 2 2.3 估算熟料化学成分 .............................................................................................................................. 2 2.4 累加试凑计算 .. (2)2.4.1 原料的原始资料 ...................................................................................................................... 2 2.4.2 累加试凑计算 .......................................................................................................................... 3 2.5 计算熟料料耗 ...................................................................................................................................... 3 2.6 计算生料配比 ...................................................................................................................................... 3 2.7 校验熟料化学成分与率值 .................................................................................................................. 3 2.8 将干燥原料配合比换算成湿原料配合比 .......................................................................................... 4 3 燃料燃烧计算 .................................................................................................................................................. 5 4 物料平衡、热平衡计算 . (5)4.1 原始资料 .............................................................................................................................................. 5 4.2 物料平衡与热量平衡计算 (7)4.2.1 物料平衡计算 .......................................................................................................................... 7 4.2.2 热量平衡计算 ........................................................................................................................ 13 4.2.3 平衡核算 .. (16)5 主要热工技术参数 (17)5.1 主要热工技术参数的计算 (17)5.1.1 回转窑的发热能力 ................................................................................................................ 17 5.1.2 分解炉的发热能力 ................................................................................................................ 18 5.1.3 水泥熟料的实际烧成热耗 .................................................................................................... 18 5.1.4 熟料形成热 ............................................................................................................................ 18 5.1.5 回转窑系统的热效率 ............................................................................................................ 18 5.1.6 回转窑内燃烧带的空气过剩系数 ........................................................................................ 18 5.1.7 分解炉内燃烧带空气过剩系数 ............................................................................................ 18 5.2 主要热工技术参数一览表 ................................................................................................................ 19 6 分解炉结构尺寸计算与设计 (19)6.1 相关参数: ........................................................................................................................................ 19 6.2 分解炉工作风量 .. (20)6.2.1 分解炉内的实际烟气量V fl (20)6.2.2 分解炉中CaCO 3分解产生的CO 2量2CO V (20)6.2.3窑气量V k (20)6.2.4通过分解炉的工作态气体量V Ff (21)6.3分解炉直筒部位的有效截面积A F与有效内径D F (21)6.4分解炉的有效高度H (21)6.5分解炉锥体部位的有效高度H2 (21)6.6分解炉直筒部位的有效高度H1 (21)6.7分解炉锥体下端口直径d F (21)6.8入分解炉三次风管直径d i (21)6.9入分解炉三次风管进风口宽度a和高度b (22)6.10分解炉生料进料口直径d s (22)6.11分解炉燃料进口直径d r (22)6.12分解炉主要结构尺寸一览表 (22)7耐火材料选材计算与散热计算 (23)7.1耐火衬料的设计理念 (23)7.2材料的主要参数 (23)7.2.1粘土砖的部分性质 (23)7.2.2碳钢的部分性质 (23)7.3厚度计算 (23)7.3.1已知参数 (23)7.3.2厚度计算 (24)7.4散热量计算 (24)7.5耐火材料厚度对分解炉筒体尺寸的修正 (25)8设计评述 (25)9参考资料 (26)日产3200吨熟料预分解窑的分解炉设计1初始条件1.1原料的原始资料表1.1 原料与煤灰的化学成分(%)项目物料烧失量SiO2 Al2O3 Fe2O3 CaO MgO SO3K2O Na2O H2O 石灰石43.05 1.79 0.64 0.71 53.10 0.71 1.00 粘土 4.74 65.47 16.94 5.99 4.04 0.91 1.01 0.7 1.00 铁粉 1.02 38.01 2.05 52.97 3.95 1.99 4.05 煤灰57.11 27.15 9.11 3.41 1.26 2.311.2燃料煤的原始资料表1.2 煤的元素分析数据C ad H ad N ad O ad S ad A ad M ad65.5 5.1 1.1 6.0 0.4 20.5 1.41.3各种物料损失均按3%计算1.4其它资料:本设计工厂有自己的矿山,其它条件均符合建厂要求,工厂气象条件符合设计要求。
日产熟料5000t水泥厂窑尾工艺设计l计算书
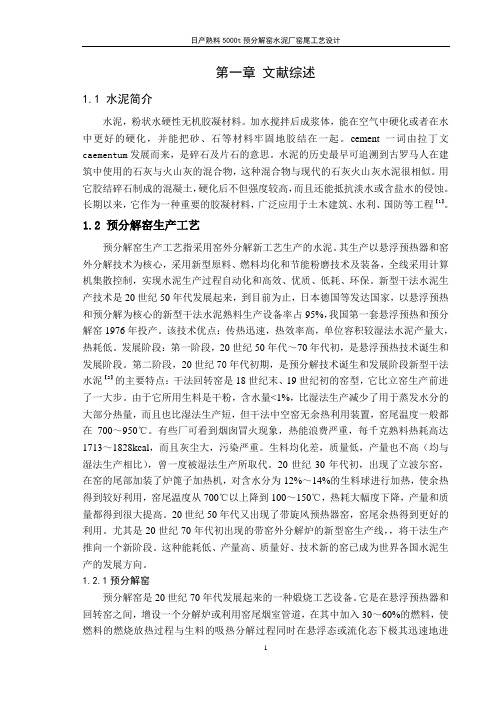
第一章文献综述1.1 水泥简介水泥,粉状水硬性无机胶凝材料。
加水搅拌后成浆体,能在空气中硬化或者在水中更好的硬化,并能把砂、石等材料牢固地胶结在一起。
cement一词由拉丁文caementum发展而来,是碎石及片石的意思。
水泥的历史最早可追溯到古罗马人在建筑中使用的石灰与火山灰的混合物,这种混合物与现代的石灰火山灰水泥很相似。
用它胶结碎石制成的混凝土,硬化后不但强度较高,而且还能抵抗淡水或含盐水的侵蚀。
长期以来,它作为一种重要的胶凝材料,广泛应用于土木建筑、水利、国防等工程【1】。
1.2 预分解窑生产工艺预分解窑生产工艺指采用窑外分解新工艺生产的水泥。
其生产以悬浮预热器和窑外分解技术为核心,采用新型原料、燃料均化和节能粉磨技术及装备,全线采用计算机集散控制,实现水泥生产过程自动化和高效、优质、低耗、环保。
新型干法水泥生产技术是20世纪50年代发展起来,到目前为止,日本德国等发达国家,以悬浮预热和预分解为核心的新型干法水泥熟料生产设备率占95%,我国第一套悬浮预热和预分解窑1976年投产。
该技术优点:传热迅速,热效率高,单位容积较湿法水泥产量大,热耗低。
发展阶段:第一阶段,20世纪50年代~70年代初,是悬浮预热技术诞生和发展阶段。
第二阶段,20世纪70年代初期,是预分解技术诞生和发展阶段新型干法水泥【2】的主要特点:干法回转窑是18世纪末、19世纪初的窑型,它比立窑生产前进了一大步。
由于它所用生料是干粉,含水量<1%,比湿法生产减少了用于蒸发水分的大部分热量,而且也比湿法生产短,但干法中空窑无余热利用装置,窑尾温度一般都在700~950℃。
有些厂可看到烟囱冒火现象,热能浪费严重,每千克熟料热耗高达1713~1828kcal,而且灰尘大,污染严重。
生料均化差,质量低,产量也不高(均与湿法生产相比),曾一度被湿法生产所取代。
20世纪30年代初,出现了立波尔窑,在窑的尾部加装了炉篦子加热机,对含水分为12%~14%的生料球进行加热,使余热得到较好利用,窑尾温度从700℃以上降到100~150℃,热耗大幅度下降,产量和质量都得到很大提高。
日产5200吨熟料预分解窑的预热器系统设计解析
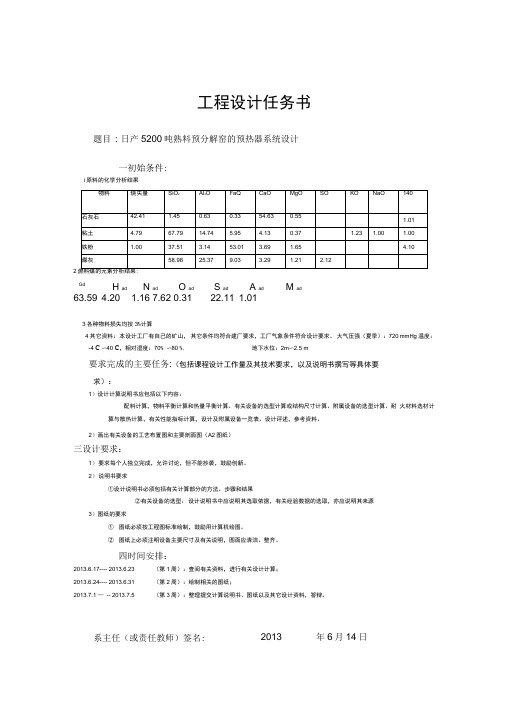
工程设计任务书题目:日产5200吨熟料预分解窑的预热器系统设计一初始条件:i原料的化学分析结果2Gd H ad N ad O ad S ad A ad M ad63.59 4.20 1.16 7.62 0.31 22.11 1.013各种物料损失均按3%计算4其它资料:本设计工厂有自己的矿山,其它条件均符合建厂要求,工厂气象条件符合设计要求。
大气压强(夏季):720 mmHg 温度:-4 C 〜40 C,相对湿度:70% 〜80 %, 地下水位:2m〜2.5 m要求完成的主要任务:(包括课程设计工作量及其技术要求,以及说明书撰写等具体要求):1)设计计算说明书应包括以下内容:配料计算,物料平衡计算和热量平衡计算、有关设备的选型计算或结构尺寸计算、附属设备的选型计算、耐火材料选材计算与散热计算,有关性能指标计算,设计及附属设备一览表、设计评述,参考资料。
2)画出有关设备的工艺布置图和主要剖面图(A2图纸)三设计要求:1)要求每个人独立完成,允许讨论,但不能抄袭,鼓励创新。
2)说明书要求①设计说明书必须包括有关计算部分的方法、步骤和结果②有关设备的选型,设计说明书中应说明其选取依据,有关经验数据的选取,亦应说明其来源3)图纸的要求①图纸必须按工程图标准绘制,鼓励用计算机绘图。
②图纸上必须注明设备主要尺寸及有关说明,图面应清洁、整齐。
四时间安排:2013.6.17---- 2013.6.23 (第1周):查阅有关资料,进行有关设计计算;2013.6.24---- 2013.6.31 (第2周):绘制相关的图纸;2013.7.1 —-- 2013.7.5 (第3周):整理提交计算说明书、图纸以及其它设计资料,答辩。
系主任(或责任教师)签名: 2013 年6月14日指导教师签名: 2013年6月14日目录1 •配料计算 ................................................................. 1..1.1计算煤灰掺入量 ..................................................... 1.1.1.1煤的低位发热量.............................................. 1.1.1.2煤灰的掺入量................................................. 1.1.2根据熟料率值,估算熟料化学成分 (2)1.3累加试凑过程........................................................2.1.4配比结果............................................................2.2. 燃烧计算..................................................................3..3. 物料与热量平衡计算........................................................4.3.1物料平衡........................................................... .5..3.1.1收入项目...................................................... 5.3.1.1.1燃料总消耗量............................................. 5.3.1.1.2生料消耗量............................................... 5.3.1.1.3入窑系统空气量.......................................... 7.3.1.2支出项目...................................................... 9.3.1.2.1 熟料...................................................... 9.3.1.2.2出预热器废气量.......................................... 9.3.1.2.3出预热器飞灰量 (12)3.2热量平衡计算 (12)3.2.1收入项目.................................................... 1.23.2.1.1燃料燃烧生成热 (12)3.2.1.2燃料带入物理热 (12)3.2.1.3生料带入物理热 (12)3.2.1.4入窑回灰带入热量........................................ 1.33.2.1.5空气带入热量 (13)3.2.2支出项目.................................................... 1.43.2.2.1熟料形成热 (14)3.2.2.2蒸发生料中水分耗热量.................................... 1.43.2.2.3废气带走的热量 (14)3.2.2.4出窑熟料带走热量 (15)3.2.2.5出预热器飞灰带走热量.................................... 1.53.2.2.6系统表面散热损失........................................ 1.53.3主要热工技术参数 (15)3.4物料平衡表........................................................ 1.63.5热量平衡表........................................................ 1.64 •悬浮预热器的尺寸计算 (17)4.1旋风筒尺寸........................................................ 1.74.1.1各级旋风筒处理的气体量...................................... 1.74.1.2旋风筒的直径和高度 (18)4.1.3旋风筒进风口尺寸 (19)4.2排气管(内筒)尺寸 (19)4.3旋风筒其他相关尺寸 (20)4.4旋风筒结构尺寸表 (20)5. 耐火材料选材与散热计算 (21)5.1耐火材料的设计理念 (21)5.2耐火材料的主要参数 (21)5.3材料的厚度计算 (22)5.3.1已知参数 (22)5.3.2材料厚度计算 (22)5.3.2.1热流密度q的计算 (22)5.3.2.2厚度计算 (23)5.3.3散热量计算 (24)6. 预热器尺寸修正 (25)7. 设计评述与体会 (26)8 •参考资料 (26)日产5200吨熟料预分解窑的预热器系统设计1 •配料计算1.1计算煤灰掺入量1.1.1煤的低位发热量Q net.ar=339C ar+1030H ar~109(O ar-S ar)-25M ar (kJ/kg)Q net.ar=339 X 0.6359+10300.042-109 >(0.0762-0.0031)-25X).0101 =25060.97(kJ/kg) 1.1.2煤灰的掺入量100kg熟料中煤灰掺入量可按下式近似计算:尸_ qA ar S _ PA ar S(J —--------式中Ga——熟料中煤灰掺入量,%;q――单位熟料热值,kJ/kg熟料,选3350; Qnet,ar ----- 煤的热值,kJ/kg;Aar ---- 煤的空气干燥基灰分含量,%;S ---- 煤灰沉落率,%,可选100%;P――熟料烧成的煤耗,kg/kg熟料;qA ar S 100 Q net , arKH CaO T.65AI2O3 - 0.35Fe2O32.8SiO266.445-1.65 5.533- 0.35 3.1162.8 22.379二0.897SMSiOAl 2O 3 Fe 2 O 322 .3795.533 3.116二2.588IMAl 2 O 3 _ 5 .533Fe 2 O 3 3.1161 .776竺22 100冷96%100 25060 .971.2根据熟料率值,估算熟料化学成分已知KH=0.9, SM=2.6, IM=1.7,刀=97.5%熟料化学成分计算如下:Fe2O3 3.19 %(2.8KH +1)(IM +1)SM +2.65IM +1.35AbO3=IM(Fe2O3)=5.42%SiQ=SM(A2O3+Fe2O3)=22.39%CaO=-(SiQ+A bO3+Fe s O3)=66.5%1.3累加试凑过程计算率值:将验证得的率值与题意要求目标值相比,可以看出各率值的误差: △KH=0.90-0.897=0.003 < 0.01△SM=2.6-2.588=0.012 < 0.1△IM=1.776-1.7=0.076 < 0.1;其误差值均在要求的范围之内且较小,即配料结果符合要求。
本科毕业论文---日产4000吨水泥熟料预分解窑熟料粉磨系统的初步设计正文

毕业论文(设计)论文题目4000t/d水泥熟料预分解窑熟料粉磨系统的初步设计学院年级专业学生姓名学号指导教师毕业论文(设计)论文题目4000t/d水泥熟料预分解窑熟料粉磨系统的初步设计学院材料科学与工程年级专业无机非金属材料工程学生姓名学号指导教师摘要水泥粉磨是水泥成品制备的重要工艺过程,它直接影响水泥质量的好坏,因此水泥粉磨车间的设计在整个的水泥厂的设计中是很重要的一个环节。
本论文就4000 t/d(日产4000吨)吨硅酸盐水泥工厂水泥粉磨车间进行设计,根据相关文献以及对产量要求对水泥的配料方案、三大平衡(物料平衡、主机平衡、储库平衡)和水泥粉磨车间系统设备的选型进行设计与计算,并据此对水泥粉磨车间的主要粉磨设备以及其相关的附属设备(选粉机、收尘器等)的型号进行了选择。
本次设计秉着力求使产品达到“优质、环保、节能”的原则,对生产工艺技术方案以及粉磨车间设备进行了仔细的斟酌与取舍,并做出了生产总体布置平面图和水泥粉磨系统工艺布置图。
关键词:水泥,工厂设计,4000t/dAbstractCement plant design is a very important aspect. This thesis on 4000 t / d (Nissan 4000 tons) tons of Portland cement factory cement grinding plant design, according to the relevant literature as well as production req Cement grinding is finished cement important preparation process, which directly affects the quality of cement is good or bad, so the design of cement grinding plant in the whole of the uirements for cement batching scheme, the three balance (material balance, the host balancing reservoir balance) and cement grinding plant equipment selection system design and calculation, and accordingly cement grinding plant on the main grinding equipment and its associated ancillary equipment (separator, dust collector, etc.) models were selection. This design holds strive to make products to achieve "quality, environmental protection, energy conservation," the principle of the production technology programs and grinding workshop equipment were carefully consider the trade-offs, and make the overall layout of the production plan and cement grinding system process layout.Keywords: cement, plant design, 4000t/d;目录摘要 (I)Abstract (II)目录 (III)第1章绪论 (1)1.1引言 (1)1.2国内外现状 (1)1.3目前世界水泥行业的先进技术和发展 (3)1.4生产需求状况 (4)1.5设计特点 (5)第2章原料与燃料 (10)2.1原料的质量要求 (10)2.1.1 水泥原料(普通硅酸盐水泥) (10)2.1.2 混合材及石膏 (11)2.2燃料的质量要求 (12)2.2.1 煤 (12)2.2.2 熟料热耗的选择 (13)第3章配料计算与物料平衡 (14)3.1配料计算 (14)3.1.1 原料选择 (14)3.1.2 率值及率值确定 (14)3.1.3 水泥配料方案 (15)3.2物料平衡计算 (19)3.2.1 烧成车间生产能力和工厂生产能力的计算 (19)3.2.2 原、燃料消耗定额 (20)3.2.3 烧成系统和工厂的生产能力 (23)3.2.4 全厂物料平衡表 (23)第4章主机平衡计算及选型 (25)4.1车间工作制度的确定 (25)4.2主机选型 (25)4.2.1 破碎机的选型 (25)4.2.2 生料磨的选型 (26)4.2.3 窑系统 (26)4.2.4 煤磨的选型 (27)4.2.5 水泥磨的选型 (28)4.2.6 包装机的选型 (29)4.3主机平衡表 (29)第5章储库计算 (30)5.1确定各种物料储存期 (30)5.2堆场计算 (30)5.2.1 石灰石预均化堆场 (31)5.2.2 原煤预均化堆场 (32)5.2.3 联合预均化堆场 (33)5.3储库计算 (35)5.3.1 生料配料站 (35)5.3.2 熟料库 (39)5.3.3 水泥配料站 (41)5.3.4 水泥库 (44)5.4储库一览表 (45)第6章水泥制成车间设计计算 (46)6.1水泥制成车间介绍 (46)6.1.1 水泥粉磨的功能和意义 (46)6.1.2 现代水泥粉磨技术发展的特点 (46)6.1.3 水泥粉磨流程发展情况 (48)6.1.4 辊压机粉磨系统的发展 (49)6.1.5 辊压机水泥粉磨工艺方案 (49)6.1.6 本设计工艺流程 (51)6.2制成车间选型计算 (52)6.2.1 球磨机的设计计算 (52)6.2.2 水泥球磨机的热平衡计算 (58)6.3辊压机系统选型计算 (61)6.3.1 辊压机选型计算 (61)6.3.2 V型选粉机、旋风筒选型及其他设备选型 (62)6.4其他附属设备的选型计算 (64)6.4.1 O-SEPA选粉机 (64)6.4.2 收尘器 (65)6.4.3 喂料计量设备 (65)6.4.4 配料装置设计 (66)6.4.5 输送设备 (67)第7章水泥制成车间工艺布置 (70)第8章全厂平面工艺布置 (71)8.1全厂总平面设计的基本原则 (71)8.2全厂工艺平面布置说明 (72)结论 (74)致谢 (75)参考文献 (76)第1章绪论1.1引言新型干法水泥生产自问世以来倍受世界各国的关注,特别是上世纪80 年代以来得到了突飞猛进的发展,国际水泥工业以预分解技术为核心,将现代科学技术和工业化生产的最新成果广泛应用于水泥生产的全过程,形成了一套具有现代高科技为特征和符合优质、高效、节能、环保以及大型化、自动化的现代生产方法。
日产4000吨水泥预分解窑烧成系统的初步设计
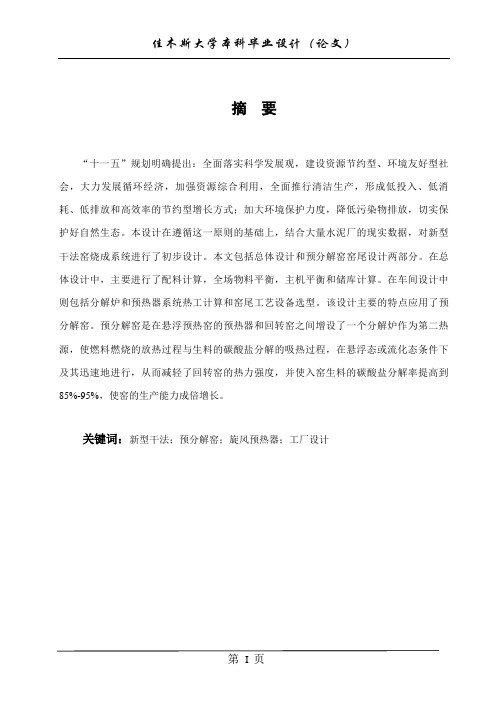
摘要“十一五”规划明确提出:全面落实科学发展观,建设资源节约型、环境友好型社会,大力发展循环经济,加强资源综合利用,全面推行清洁生产,形成低投入、低消耗、低排放和高效率的节约型增长方式;加大环境保护力度,降低污染物排放,切实保护好自然生态。
本设计在遵循这一原则的基础上,结合大量水泥厂的现实数据,对新型干法窑烧成系统进行了初步设计。
本文包括总体设计和预分解窑窑尾设计两部分。
在总体设计中,主要进行了配料计算,全场物料平衡,主机平衡和储库计算。
在车间设计中则包括分解炉和预热器系统热工计算和窑尾工艺设备选型。
该设计主要的特点应用了预分解窑。
预分解窑是在悬浮预热窑的预热器和回转窑之间增设了一个分解炉作为第二热源,使燃料燃烧的放热过程与生料的碳酸盐分解的吸热过程,在悬浮态或流化态条件下及其迅速地进行,从而减轻了回转窑的热力强度,并使入窑生料的碳酸盐分解率提高到85%-95%,使窑的生产能力成倍增长。
关键词:新型干法;预分解窑;旋风预热器;工厂设计Abstract“Eleveth Five-year Plan” made clear:the full implementation of the scientif ic development concept and building a resource-saving and environment-friendly society;vigorously develop the circular economy and strengthen the comprehensive utilization of resources,the full implementatiom of clean production,the formation of low-input,low consumption,low emissions and efficient-saving mode of growth;intensify environmental protection,and reduced pollutant emissions,and effectively protect the natural ecology.In this paper, including the design and pre-kiln back-end design in two parts. In the overall design, the main ingredients for the calculation, the material balance of the audience, the host computing balance and storage. Design in the workshop include preheater and calciner system thermal calculation and back-end process equipment selection. The design of the main features of the application of the pre-kiln. Precalciner kiln is preheated in the suspension preheater kilns and between the addition of a rotary kiln calciner as a second heat source, so that the exothermic fuel combustion process and raw materials endothermic carbonate decomposition process, in the suspended state or fluidization conditions and rapid manner, so as to reduce the heat intensity of the rotary kiln.Raw materials into the kiln and the carbonate decomposition rate to 85 % -95%, so the kiln production capacity doubled.Key words:NSP; Suspension preheater; Cyclone preheater ;Plant design目录摘要 (I)Abstract (II)第1章绪论 (1)1.1水泥工业及水泥行业形势 (1)1.2国内外烧成技术现状 (2)1.2.1 国际烧成技术现状 (2)1.2.2 国内烧成系统现状 (3)1.2.3 新型节能烧成系统 (4)1.3烧成系统发展趋势 (5)1.4本设计的意义 (7)第2章物料平衡计算 (9)2.1水泥熟料成分设定 (9)2.2物料平衡的计算 (10)2.2.1 物料平衡计算 (10)2.2.2 原料消耗定额 (11)2.2.3 烧成用干煤的消耗定额 (11)2.3全厂物料平衡计算 (12)2.3.1 相关参数的确定 (12)2.3.2 计算步骤及计算公式 (14)2.3.3 全厂物料平衡表 (16)第3章主机平衡 (18)第4章烧成系统热平衡计算 (19)4.1原始资料 (19)4.2物料平衡计算 (20)4.3热量平衡计算 (21)第5章主要设备及设备的选型 (25)5.1主机设备选型 (25)5.1.1 石灰石破碎机选型 (25)5.1.2 生料粉磨系统选型 (27)5.1.3 预热器及分解炉选型 (28)5.1.4 回转窑 (29)5.1.5 篦冷机选型 (31)5.1.6 煤磨 (32)5.1.7 水泥磨 (34)5.1.8 包装机 (35)5.2预分解窑主要设备的设计计算 (36)5.2.1 回转窑规格的确定 (36)5.2.2 回转率所需功率 (36)5.2.3 电机功率 (37)5.2.4 回转窑内物料运动速度 (37)5.2.5 窑内物料负荷率 (37)第6章回转窑的规格设计及附属设备的选型计算 (38)6.1确定各段窑长 (38)6.2回转窑厚度 (38)6.3回转窑的技术性能 (38)6.3.1 回转窑的技术性能 (38)6.3.2 分解炉规格的确定 (39)6.3.3 熟料篦冷却机的选型计算 (40)6.4附属设备的选型计算 (40)6.4.1 旋风筒的设计计算 (40)6.4.2 风机的计算及选型 (41)6.4.3 入分解炉专用风管直径(三次风管) (41)6.4.4 烟囱的设计计算 (42)6.4.5 增湿塔的设计计算 (42)6.4.6 电收尘器 (42)6.4.7 煤粉制备系统的计算 (42)致谢 (43)参考文献 (44)附录1 (1)附录2 (2)附录3 ............................................................................................................ 错误!未定义书签。
- 1、下载文档前请自行甄别文档内容的完整性,平台不提供额外的编辑、内容补充、找答案等附加服务。
- 2、"仅部分预览"的文档,不可在线预览部分如存在完整性等问题,可反馈申请退款(可完整预览的文档不适用该条件!)。
- 3、如文档侵犯您的权益,请联系客服反馈,我们会尽快为您处理(人工客服工作时间:9:00-18:30)。
1前言1.1水泥产业发展概述我国是水泥生产大国,水泥工业是我国国民经济建设的重要基础材料产业,在国民经济可持续发展中具有举足轻重的地位。
随着现代化建设的持续、稳定发展,我国水泥工业正面临着更好更快地发展、完善自身、节能环保的重任[1]。
水泥生产过程中,最重要的工艺环节是将化学成分合格的生料煅烧成既定矿物组成的熟料的过程[2]。
此过程所使用的设备包括旋风筒预热器、分解炉、回转窑和篦冷机等,这些设备即为构成窑尾系统的主要设备。
伴随着水泥工业生产技术的发展,熟料煅烧设备经历了立窑、干法中空窑、湿法窑、立波尔窑、预热器窑以及预分解窑的变化。
对于水泥工业窑炉,国内外主要研究机构均依据水泥熟料形成热、动力学机制,研究水泥窑炉工艺过程,并对各设备子系统工作机理和料气运动、换热规律进行探讨[3]。
通过建立单级和多级粉体悬浮热交换器热力学理论模型和分解炉系统热稳定性理论模型,建立全系统的热效率模型,系统研究了悬浮预热器和分解炉的热效率及其影响因素、悬浮预热器系统特性组合流程、流场、温度场、浓度场的合理分布和碳酸盐分解及固液相反应动力学特性,并以此为理论指导,开发出新型干法水泥熟料生产技术装备[4]。
1.2国内外研究现状天津水泥工业设计研究院有限公司开发的TDF分解炉,具有三喷腾和碰顶效应、湍流回流作用强、固气停留时间比大、温度场及浓度场均匀、物料分散及换热效果好、阻力系数低等特点[5]。
交叉料流型预分解法在保证全系统固气比不变的前提下,可使每级预热器单体的固气比提高,从而提高系统的热效率。
采用这种生产方法可提高生料入窑分解率,降低预热器出口气体温度及分解炉操作温度[6]。
整个系统在相对低温下操作可以减少钾、钠、氯盐及一些低熔点矿物形成,有利于系统稳定操作,减少预热器及分解炉结皮堵塞。
如西安建筑科技大学徐德龙院士团队发明的悬浮态高固气比预热分解技术[7]。
以Prepol和Pyro⁃clon型炉[8]为代表的管道式分解炉,主要依靠“悬浮效应”加强气固换热,炉内湍流强度较小,一般以增大炉容为主要措施,保证分解炉的功效发挥,故其单位容积热负荷及单位容积产量相对其他炉型来说,都是比较小的。
三菱公司设计的N一MFC预分解系统所用的旋风筒则采用了出口内筒加装导向叶片的方式,以减少循环气体量,从而在不降低收尘效率的前提下降低旋风筒阻力损失。
由于采用了这种低阻旋风筒,其五级旋风预热器的阻力损失相当于或略低于四级旋风预热器的水平[9]。
南京化工学院近年来开发的SWP 喷旋预热器是通过轴流取代折流而使阻力损失降至普通旋风筒的三分之一左右。
采用半椭圆截面结构,利用旋流板产生气流旋转,并通过加装弧形挡板使旋流空间与沉料空间分开。
宇部型旋风筒的出风内筒呈靴形结构,在其进口装设导流板,从而使循环气流量及“缩流”减少,大大降低了旋风筒阻力损失[10]。
天津水泥工业设计研究院在燕山水泥厂窑尾系统采用类似结构的旋风筒,使五级筒和分解炉全系统的阻力损失低于4500Pa ,达到了比较优异的指标。
神户制钢公司的KoLBoc 筒为例,加装导向叶片,使旋风筒阻力损失降低了近30%,并且能适当改善分离效果[11]。
为了降低阻力损失,川崎型旋风筒采用一种顶部呈锥形、进口按一定水平角倾斜下降的结构,其阻力损失仅为洪堡型旋风筒的65%左右,分离效率可以满足作为中间级旋风筒的要求[12]。
我国新型干法技术的发展已经处于比较完善的时期,但国产装备的能耗、控制水平、运转率及可靠性仍有待提高。
结合我国国情来看,水泥工业无疑是重污染行业。
2013年,河北省因雾霾问题压减了钢铁、水泥、玻璃等工业的产量。
所以,水泥行业务必朝着节能减排的方向发展,加快产业结构调整步伐,大力推广新型干法水泥生产工艺的节能技术。
1.3本次设计的内容及特点本次毕业设计的内容,是依据给定的建厂条件,设计日产3000吨水泥熟料的水泥厂。
水泥生产工艺设计是工厂建设的基础,是设计是工厂设计的主要环节,是决定全局的关键。
本次毕业设计的有以下几个任务:第一,参照同类型厂家进行数据的选择,包括适当的率值,热耗,进行配料计算。
第二,根据配料计算进行全厂工艺平衡计算,具体内容包括:根据产量计算回转窑尺寸、标定产量,然后参考同类型厂家选择回转窑窑型;进行全场物料平衡计算;根据计算出的物料平衡进行主机平衡计算,并选择出主要设备的规格和型号;根据全厂物料平衡计算出储库和堆场的尺寸。
第三,根据配料计算和全厂工艺平衡计算设计全厂工艺布置和工艺流程图。
第四,根据全厂工艺平衡进行重点车间的设计计算:包括烧成车间的工艺流程、窑尾系统的物料平衡计算、窑尾系统的热量平衡计算、窑尾系统的烟气平衡计算、窑尾系统预热器与分解炉的选型及尺寸确定。
最后依据以上内容完成毕业设计说明书及毕业设计图纸。
水泥工业每年要消耗大量的石灰石、粘土等天然资源, 排放大量的2CO 、2SO 及粉尘等有害物质,对环境造成污染。
而粘土本身水分含量高,需要加设烘干设备,增加煤耗;铁粉的成本比较高,使用铁粉作为配合省料是一种资源的浪费[13]。
所以本次设计利用砂岩和硫酸渣分别代替粘土和铁粉。
一方面减小水泥生产的成本,减少煤耗和燃煤排放的污染物;另一方面,硫酸渣是工业废渣,在水泥生产中得到了利用和处理,可以减少固体工业垃圾的排放,此做法也是按照国家节能减排的要求,走可持续发展之路[14]。
本次毕业设计,旨在让学生整合大学期间所学习的专业知识,同时参阅资料掌握国内外发展研究现状,与生产实践有机的结合起来。
通过这次实际的训练,使学生进一步了解水泥生产从原料配合、工艺平衡、设备选型、堆场储库计算到熟料烧成、水泥产出的整个过程,提高学生运用知识、查阅资料、处理数据和识图、绘图技术水平,加强优化方案、统筹安排的能力;结合生产实际,提高分析和解决问题的能力。
同时掌握所学专业的发展前景及就业前景,为将来的的自身发展和提升打下坚实的基础。
2 设计基础2.1 原料化学成分生产水泥熟料所用的原料、燃料的成分如下:表2.1 原料与煤灰的化学成分(%)名称 Loss∑ 其他 石灰石 39.52 7.20 1.30 0.46 48.54 1.56 98.58 1.42 砂岩 11.52 57.61 11.50 4.64 10.60 0.88 96.75 3.25 铁铝土 9.80 30.52 37.38 15.49 1.55 0.30 95.04 4.96 硫酸渣 6.91 20.40 6.38 48.54 9.33 3.80 95.36 4.64 煤灰50.6829.854.397.392.6094.915.092.2 原、燃料水分生产水泥熟料所用的原料、燃料水分如下表2.2 原、燃料的操作水分(%)物料 石灰石 砂岩 铁铝土 硫酸渣 煤 水分33.520462.3 燃料的元素分析和工业分析生产水泥熟料所用的燃料的元素及工业分析如下表2.4 燃料的元素分析(%)67.484.080.251.1910.921.1429.2020.0649.6025616.002.4 建厂条件2.4.1 建厂地点及自然条件(1)建厂地点:某市郊区、靠国道 (2)厂区地形:厂区地势较平坦,(3)交通情况:便利,附近有公路、铁路等,有利于原料、水泥等运输。
2SiO 32O Al 32O Fe CaO MgO(4)气温:最高40℃,最低10℃,月平均25℃(5)降雨量:年总降雨量800mm,最大日降雨量100mm(6)主导风向:东北风,平均风速1.5m/s(7)地耐力:17.5吨/平方米,压力:750mm汞柱2.4.2 建厂的原燃料条件(1)石灰石:工厂自备矿山,储量丰富,火车运入(2)砂岩:外运,储量丰富,火车运入(3)铁铝土:外运,储量丰富,火车运入(4)硫酸渣:某钢厂供应,汽车运入(5)石膏:石膏矿供应,成分稳定,汽车运入(6)混合材:某钢厂供应,汽车运入(7)烟煤:煤矿供应,火车运入3 配料计算配料计算,顾名思义就是在配合生料之前,先进行配合比的计算。
在水泥生料生产过程中,配料计算为各种生料的配合,提供基础的理论依据。
只有准确的的配料计算,才能配合出合格的生料,从而煅烧出质量合格的熟料。
而生料的有效化学成分或者说能够提供出的所需矿物百分比以及三率值,则是配料计算主要影响因素。
配料计算首先要确定率值,率值的确定方法将会在下文中提到。
其次是根据建厂的原、燃料条件,通过确定好的率值,计算出配合比。
由于燃煤的沉落率为100%,所以在原料配合中要考虑煤灰的成分和掺入量;由于生料配合不是一次就能既符合熟料成分要求,又符合率值的要求,所以本次设计中配合干生料的计算运用了试凑法,即在理论值的基础上变动很小的幅度,重新计算出配合料比例,最终得到既符合熟料成分要求,又符合率值的要求的配比。
3.1 率值确定率值是水泥熟料中各主要氧化物含量之间的比例关系,包括石灰饱和系数(KH )、硅率(SM )、铝率(IM )。
石灰饱和系数是熟料中总的CaO 含量减去饱和32O Al 和32O Fe 所需的氧化钙,与2SiO 化合的CaO 的含量,比上2SiO 全部化合成S C 3所需的CaO 的含量,即2SiO 被CaO 饱和成S C 3的程度。
从实际的熟料成分来说,它表示的了S C 3和S C 2的百分含量比例。
石灰饱和系数值越大,即硅酸盐矿物中的S C 3的含量越多,则熟料的强度就越大;然而,石灰饱和系数过高的话,熟料的煅烧过程就必须时间要长,因为这个值偏高会使熟料煅烧变得困难,否则游离氧化钙就会出行,从而影响产量和窑内工作条件。
所以,石灰饱和系数的值需要提高,担忧不能过高,实际生产中一般规定在0.84~0.92之间。
硅率,又称硅酸率。
它反映了熟料中2SiO 含量和32O Al 与32O Fe 相加的和的比值,反映了熟料中硅酸盐矿物与熔剂矿物的相对含量。
硅率值偏低,熔剂矿物所占比例大导致液相量较大,易结大块,煅烧过程变得困难;硅率值偏低,则与上述情况相反,同样会使煅烧过程困难,所以,硅率必须有适当的取值范围,一般为1.8~2.5.铝率,又称铁率,表示熟料中32O Al 和32O Fe 含量的比值。
它反映了熟料中A C 3和AF C 4的相对含量。
铝率值偏大,也就是A C 3含量偏多,会使S C 3的形成变得困难;铝率值偏小,虽然有助于S C 3的形成,但同样易结大块,对窑造成损害。
因此,实际生产中一般取0.9~1.8。
本次设计参考同类型水泥生产厂家,取值如下[15]:02.087.0±=KH 1.050.2±=SM1.060.1±=IM3.2 熟料热耗和掺入煤灰量3.2.1 熟料热耗熟料热耗是指烧成每千克熟料索要消耗的热量。
新型干法生产线熟料热耗约为)(2969kg kJ q =,不超过)(3200kg kJ 。