经典的物流布局资料
物流公司仓库布局规划方案,仓库功能区域划分与平面图

一、仓库背景资料新友情物流公司是一家第三方物流企业,成立于2003年,主营仓储业务。
随着企业的不断开展,新友情的业务也由单一的成品仓储,拓展到了连锁零售业的配送、运输等领域,并同几家连锁零售企业建立了稳定的业务关系。
由于原有的仓储面积已不能满足业务的需要,新友情公司一段时间靠租赁仓库来弥补仓储面积的缺乏。
经过核算,该公司投资新建库房一间,用于连锁超市商品的仓储及配送。
为了保证建成后的高效作业,仓库经理决定好好设计该库房的布局,并选购相应的仓储设备。
为此,经理对外发布通告,征求设计方案。
该仓库的状况如下:面积1000平米〔长40米,宽25米〕,高10米,该仓库建筑的地面额定载荷为5吨,拟存储的主要货物包括生活电器、生活用纸张、日用化学品。
二、仓库布局规划方案1.仓库功能区域划分〔1〕功能区域名称:储货区、行政商务区〔办公室〕、作业工具区、收发货区、发货缓冲区、整理区、通道〔2〕功能区域的面积:储货区:195平方米长:15m宽:13m拆零拣货区:234平方米长:18m宽:13m行政商务区〔办公室〕:入库办公室:18平方米长:6m宽:3m出库办公室:18平方米长:6m 宽:3m作业工具区:24平方米长:8m宽:4m收货区:48平方米长:8m宽:6m发货区:50平方米长:10m宽:5m发货缓冲区:45平方米长:15m宽:3m整理区:65平方米长:5m宽:13m通道:宽:5米〔3〕功能区域的作用:储货区:储货拆零拣货区:拣货行政商务区〔办公室〕:办公作业工具存放区:存储作业工具收货区:收货发货区:发货发货缓冲区:存储待发货物整理区:整理待存储货物2. 仓库内通道规划:主通道W5m3. 货区货架的布局:货架种类:横梁式货架、流利式货架横列或纵列布局:纵列布局画出货架布局图:4. 仓库支持的业务量:存储货位的数量〔上架〕: 横梁式货架:共8列共8排共5层共320个货位拣货位数量(品种数): 流利式货架:共12列共4排共4层共192个货位5.作业动线:货物上架动线、补货动线、拣货动线〔作业方式〕6. 仓库设备参数:叉车参数:额定载荷:1600kg前悬距:395mm轴距:1380mm自重:3050kg总长:3205mm车体宽:1100mm可起上升度:6000mm转弯半径:1900mm托盘尺寸:L1000×W1200×H160货位尺寸:横梁式货架:L2300×W900×H1230〔mm〕双货位流利式货架:L1400×W1800×H400〔mm〕双货位拣货工具:电子标签、周转箱、滚筒式输送机、叉车、托盘、三、仓库布局规划图。
物流中心布局规划

24
2)流程图法
15年11月27日星期五
中转流程——国际中转国际 旅客下机进入T1一层→安全检查→中转柜台办理手续→上至 T1二层国际出发候机厅→登机
25
2.顾客需求分析
产品分类,进行ABC分析:关键的少数、次要的多数
1)按分类依据将物品从大到小进行排序
如图,其中P代表物料种类,Q代表订购数量。根据每一种物料Pi (i=l,2…,n)其对应点Qi,即可画出由直方图表示的P-Q图( 见图1)。 2)按分类标准,选择断点进行群组分类。3~5个
27
15年11月27日星期五
设 施 设 计
15年11月27日星期五
(一)设施定位阶段 主要目的:
解决两个问题;规划的物流中心“是”扮演什么角色, 或“不是”扮演什么角色? 案例:一批发市场,因年代老旧,想全部拆除重建为现代化多楼
层物流中心,提供批发、零售和生鲜食品的物流作业,改建前, 高级管理者因非技术方面压力的原因,将底层规划与零售摊贩使 用,而将物流中心规划至三楼与四楼,并要求大型货车可直接上 下楼层。由于在实际作业中,零售摊贩业的小型货车对与车辆进 出便利性的要求程度多不及物流中心和批发作业的大型货车严格 ,使得之后规划工作出现问题。
A 31-1-10 29-1-9 30-1-6
22-1-8 20-1-1 21-1-7 21-2-4 18-1-6 15-1-1 16-1-6 21-3-7 21-4-4 21-5-7
11-1-8 6-1-1 7-1-2 8-1-1 9-1-3 9-2-4 9-3-5
1-1-1
2-1-1
a-b-c表示第a个部件的第b道工序在第c个班组进行装配 a: 1-通风器 2-回油泵 3-前机匣 4-双速传动 5-油气分离器 6-滑油附件 7-附件机匣 8-中支承 9-低压压气机转子 10-子装配体① 11-子装 配体② 12-子装配体③ 13-处理机匣 14-高压压气机转子 15-后机匣 16-燃油总管 17-子装配体④ 18-点火器 19-子装配体⑤ 20-燃烧室 21-Ⅰ级导 向器 22-子装配体⑥ 23-Ⅰ级涡轮 24-Ⅱ级导向器 25-子装配体⑦ 26-Ⅱ级涡轮 27-子装配体⑧ 28-扩散器 29-可调喷口 30-电气附件 31-总装 配体 c: 1-前后机匣班 2-附件机匣班 3-装配班 4-机加班 5-平衡班 6-加力班 7-机匣导向班 8-传装班 9-钣焊班 10-总装班 某型号航空发动机装配树形结构图 15年11月27日星期五
物流仓库布局规划
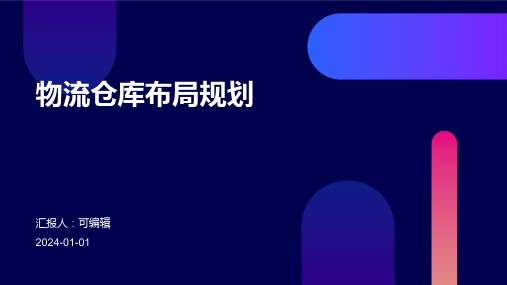
存储物流动线规划
存储物流动线规划是仓库布局的 核心环节,主要考虑货物的存储 位置、存储方式、存储区域的划
分等因素。
规划合理的存储物流动线,可以 最大化利用仓库空间,提高存储
作业效率,降低存储成本。
存储物流动线应与仓库的建筑结 构、货物特性、作业流程等因素 相匹配,以确保存储作业的顺畅
仓库管理系统介绍
仓库管理系统(WMS)是一种用于 管理仓库运作的系统,它结合了信息 技术和仓库管理实践,以提高仓库运 作效率和准确性。
WMS的主要功能包括库存管理、订单 处理、货物追踪和仓库布局优化等, 它能够实现自动化和智能化的仓库管 理,减少人工错误和提升效率。
条形码技术应用
条形码技术是一种自动识别技术,通过使用不同长度的条形符号来表示数字或字 母,实现快速、准确的识别。
02
仓库布局的目的是提高仓库作业 效率、降低运营成本、提升仓储 管理水平和满足客户需求。
仓库布局的目标和原则
仓库布局的目标包括
提高作业效率、降低运营成本、提高 仓储管理水平和满足客户需求等。
仓库布局的原则包括
合理规划空间、优化作业流程、提高 作业效率、保证作业安全和便于管理 等。
仓库布局的影响因素
业。
装卸作业安全措施
03
采取必要的安全措施,如设置安全警示标识、配备04
仓库物流动线规划
进货物流动线规划
进货物流动线规划是仓库布局的重要环节,主要考虑货物的进货方向、进 货车辆的停放位置、进货作业区的划分等因素。
规划合理的进货物流动线,可以减少货物在仓库内的搬运距离和次数,提 高进货作业效率。
物流中心合理布局

物流中心规划与运作管理
6
一物流中心合理布局应考虑的问题
➢区域内应设置的物流中心的数目 ➢物流中心的地理位置 ➢各物流中心的规模吞吐能力 ➢各物流中心的进货与供货关系;即从哪些资
源厂进货向哪些用户供货 ➢计划区域内中转供货与直达供货的比例
物流中心规划与运作管理
7
二物流中心的选址
➢税收政策的稳定性
税收政策的稳定性也是影响物流中心成本 和效益的重要因素 特别是在物流中心的发 展初期;由于初期资金投入大;许多物流中心 往往是负债运营的;在这种情况下如果政府 没有税收上的支持或者税收政策不稳定;对 于物流中心的正常运营和发展无疑是雪上 加霜 因此;所在区域政府税收政策的稳定性 也应该成为物流中心区域选择所必须考虑 的因素
物流中心规划与设计
物流中心规划与运作管理
1
第二章 物流中心的合理布局
➢物流中心合理布局概述
– 物流中心合理布局的意义 – 合理布局的主要内容 – 物流中心布局的常用方法
➢一元网点布局 ➢多元网点布局 ➢几种常用的物流中心布局方法
物流中心规划与运作管理
2
第一节 物流中心合理布局概述
物流中心的合理布局是物流系统中具有 战略意义的投资决策问题 物流中心布局是 否合理;将对整个系统的物流合理化和商品 流通的社会效益有着决定性的影响
34
➢与机场衔接程度
随着顾客对运输服务时间性要求的不断增 加;与机场衔接的程度也逐渐成为物流中心 选址的重要影响因素 特别是对于以贵重商 品快递为主要业务的物流中心而言;邻近机 场将会极大的减少运输的时间;提高运送的 速度;满足顾客的需求
物流中心规划与运作管理
35
➢竞争性标准
某物流行业仓库布局及运营策划方案

WMS系统的功能与特点
货物追踪
实时追踪货物位置,提高物流效率。
数据分析
提供数据分析和报告,帮助企业做出更好的决策。
WMS系统的功能与特点
灵活性
可根据企业需求进行定制,满足不同仓 库的特殊需求。
VS
高效性
自动化和智能化的管理方式,提高仓库运 营效率。
WMS系统的功能与特点
可靠性
系统稳定可靠,可保证仓库的正常运营。
仓库布局的常见类型
根据货物流转模式
单向流:货物从入库到出库沿单一方 向流动,适用于货物品种较少、批量
较大的情况。
双向流:货物在入库和出库方向上均 流动,适用于货物品种较多、批量大 小不一的情况。
根据货物存储方式
货架式存储:货物存放在货架上,适 用于大量中小型货物存储的情况。
平面存储:货物直接堆放在地面上, 适用于大型货物或不规则形状货物的 存储。
根据实际库存情况,设置合理的 库存预警线,避免出现缺货或积 压现象。
库存调整
02
03
库存优化
根据市场变化和销售情况,适时 调整库存结构,保持合理的库存 水平。
通过科学的库存管理方法,如 ABC分类法、实时盘点等,优化 库存结构,提高库存周转率。
安全管理
仓库消防安全
定期检查消防设施的完好性,确保消防通道畅通无阻,提高仓库整 体的消防安全水平。
货物防盗
采取有效的防盗措施,如安装监控摄像头、使用货架锁等,确保货 物安全无虞。
作业安全
制定严格的作业安全规章制度,要求员工在操作过程中遵守安全规程 ,防止意外事故的发生。
04
仓库管理系统
WMS系统的功能与特点
库存管理
实时跟踪库存量,实现库存预警和补货提醒。
物流管理-仓库布局规划

物流管理-仓库布局规划 知识目标熟悉仓库的种类;掌握仓库的总体构成;掌握仓库内部规划设计的基本方法;掌握仓储设施设备的基础知识;熟悉仓储作业安全的各项要求。
能力目标能准确计算仓容;能够根据仓库类型进行仓库布局;能够对仓库布置和储位划分提出合理化的建议;能够选择合适的设施设备;能够复述安全措施。
本项目知识结构图职业标准与岗位要求任务一仓库平面布局一、影响仓库平面布局的因素(一)仓库的专业化程度(二)仓库的规模和功能二、仓库平面布局的要求(一)仓库平面布置要适应仓储作业过程的要求,有利于仓储作业的顺利进行。
1.仓库平面布置时,物品流向应该是单一的流向。
2.最短的搬运距离。
根据作业方式、仓储物品品种、地理条件等,合理安排库房、专用线与主干道的相对位置,尽量减少迂回运输。
3.最少的装卸环节。
4.最大限度地利用空间。
(二)仓库平面布局要有利于提高仓储经济效益要因地制宜,充分考虑地形、地址条件,利用现有资源和外部协作条件,根据设计规划和库存物品的性质能够更好地选择和配置设施设备,最大限度地发挥其效能。
(三)仓库平面布置要有利于保证安全和职工的健康仓库建设时严格执行《建筑设计防火规范》的规定,留有一定的防火间距,并有防火防盗安全设施,作业环境的安全卫生标准要符合国家的有关规定,有利于职工的身体健康。
三、仓库的种类(一)按保管目的可划分为:1.配送中心(流通中心)型仓库——具有发货、配送和流通加工的功能。
2.存储中心型仓库——以储存为主的仓库。
3.物流中心型仓库——具有储存、发货、配送、流通加工等功能的仓库。
(二)按建筑形态可划分为:1.平房型仓库平房仓库结构比较简单,建筑费用便宜,人工操作比较方便。
2.二层楼房型仓库3.多层楼房型仓库二层楼房仓库和多层楼房仓库可以统称为楼房仓库,它可以减少土地的占用面积,其物品上下移动作业复杂,进去库作业可采用机械化或半机械化,楼房隔层间可依靠垂直运输机机械联系,也可以坡道相连。
物流配送中心布局与优化

物流配送中心布局与优化一、引言物流配送中心是供应链管理中不可或缺的重要环节,其布局与优化对于提高物流效率、降低成本和满足客户需求至关重要。
本文将就物流配送中心布局与优化进行探讨。
二、物流配送中心布局1. 选址与规划物流配送中心选址考虑因素包括交通便利程度、物流网络覆盖范围、附近的供应商和客户位置以及劳动力资源等。
在选址确定后,需进行规划,包括中心建筑物、存储区域、道路与停车区域、设备与设施等。
2. 存储与集货区域物流配送中心的存储区域需要根据产品特点、存储需求和货物流动性考虑。
一般可分为常用商品储存区、临时商品储存区和大件商品储存区。
集货区域则是将从供应商处到达的物流货物进行整合、归类和分拣的区域。
3. 拣选与包装区域拣选与包装区域是物流配送中心的核心环节,需根据订单特点和产品属性合理规划。
拣选区域应具备高效的拣选设备和技术,以提高拣选速度和准确度。
包装区域则需要考虑包装方式、器具和材料,以确保货物安全发运。
4. 公共设施与办公区域物流配送中心还需要设置公共设施和办公区域,包括员工休息区、管理办公区、会议室和培训室等。
这些区域的布局要注重员工的工作舒适度和效率。
三、物流配送中心优化1. 信息系统优化实施高效的物流信息系统是物流配送中心优化的核心。
通过实时监控货物流动、订单履约情况和仓库库存等信息,可以及时调整物流配送中心的运营流程和策略,提高物流效率。
2. 仓储库存优化仓储库存优化是保证物流配送中心高效运作的重要环节。
采用合理的库存管理策略,如ABC分类法、批量订货和定期清理过期产品等,可以减少库存积压和资金占用,提高库存周转率。
3. 运输路线优化运输路线优化可以降低物流配送中心的运输成本和时间,并提高服务质量。
通过运输路线规划和优化算法,可以最大程度地减少运输距离和时间,提高交通效率。
4. 人员培训与管理优化物流配送中心的人员是其运作的关键。
进行系统的人员培训和管理,提高员工的素质和技能,使其能够适应日益复杂的物流环境和工作要求,对优化物流配送中心至关重要。
物流中心布局规划
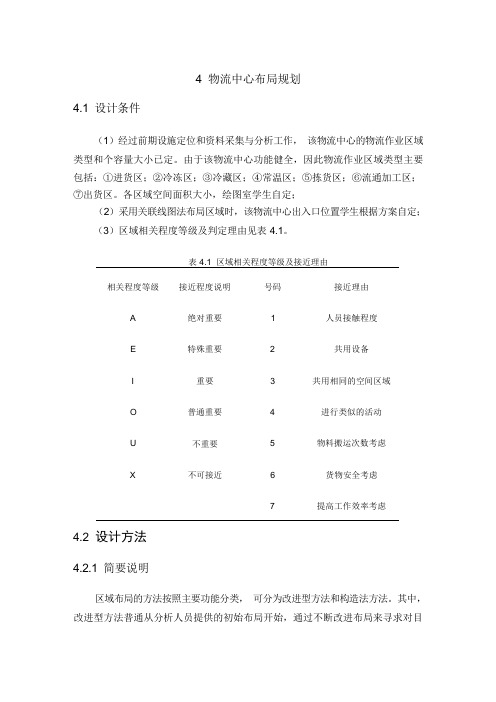
4 物流中心布局规划4.1 设计条件(1)经过前期设施定位和资料采集与分析工作,该物流中心的物流作业区域类型和个容量大小已定。
由于该物流中心功能健全,因此物流作业区域类型主要包括:①进货区;②冷冻区;③冷藏区;④常温区;⑤拣货区;⑥流通加工区;⑦出货区。
各区域空间面积大小,绘图室学生自定;(2)采用关联线图法布局区域时,该物流中心出入口位置学生根据方案自定;(3)区域相关程度等级及判定理由见表4.1。
表4.1 区域相关程度等级及接近理由相关程度等级接近程度说明号码接近理由A 绝对重要 1 人员接触程度E 特殊重要 2 共用设备I 重要 3 共用相同的空间区域O 普通重要 4 进行类似的活动U 不重要 5 物料搬运次数考虑X 不可接近 67货物安全考虑提高工作效率考虑4.2 设计方法4.2.1 简要说明区域布局的方法按照主要功能分类,可分为改进型方法和构造法方法。
其中,改进型方法普通从分析人员提供的初始布局开始,通过不断改进布局来寻求对目标函数值得提高。
构造型方法普通从零开始来做布局方案,它可以进一步分为两 类:建造物尺寸已给定的和未给定的。
第一类构造型方法合用于物流中心搬到已 有的空厂房的情况;第二类构造型方法合用于“空地”的情况。
关联线图法是一种 构造型的布局方法,其具体步骤如图 4.1 所示。
绘 制 活 动 关 系 图制作 关 联线图工 作 表制作 方块膜 片 图构建 膜片拼 排 图产生区域布局 图绘制 关 连线 图图 4.1 关联线图法步骤图4.2.2 详细步骤(1) 绘制活动关系图。
①确定设施具体包含哪些部门,将所有的逐一列出:进货区,出货区,常温 区,冷藏区,冷冻区,拣货区,流通加工区,暂存区,信息处理中心和行政办公 区等。
②将列出的所有部门中类似(如属于同一监督管理系统)的群组化(将所有 区域群组化后得到进出货区,常温区,冷藏冷冻区,拣货区,流通加工区行政部 门和暂存区, 避免后期分析时部门数过多,增加分析难度。
运输服务的物流网络设计仓储和配送中心的布局
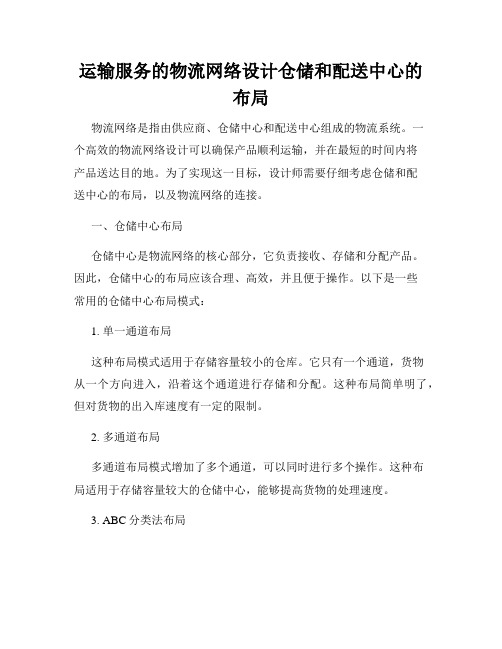
运输服务的物流网络设计仓储和配送中心的布局物流网络是指由供应商、仓储中心和配送中心组成的物流系统。
一个高效的物流网络设计可以确保产品顺利运输,并在最短的时间内将产品送达目的地。
为了实现这一目标,设计师需要仔细考虑仓储和配送中心的布局,以及物流网络的连接。
一、仓储中心布局仓储中心是物流网络的核心部分,它负责接收、存储和分配产品。
因此,仓储中心的布局应该合理、高效,并且便于操作。
以下是一些常用的仓储中心布局模式:1. 单一通道布局这种布局模式适用于存储容量较小的仓库。
它只有一个通道,货物从一个方向进入,沿着这个通道进行存储和分配。
这种布局简单明了,但对货物的出入库速度有一定的限制。
2. 多通道布局多通道布局模式增加了多个通道,可以同时进行多个操作。
这种布局适用于存储容量较大的仓储中心,能够提高货物的处理速度。
3. ABC分类法布局ABC分类法是一种按照产品重要性进行分类的方法。
根据销售情况和重要性程度,将产品分为A、B、C类。
A类产品需要放置在最便捷的位置,以便快速分配;B类产品次之,C类产品放置在最边缘的位置。
二、配送中心布局配送中心是物流网络中将产品从仓储中心送达客户的关键环节。
以下是一些常用的配送中心布局模式:1. 集中式布局集中式布局模式将所有的配送活动集中在一个中心,从这里将产品送达各个目的地。
这种布局模式适用于产品分布范围较小、目的地数量较少的情况。
2. 分散式布局分散式布局模式将配送活动分散在多个中心,从各个中心将产品送达目的地。
这种布局模式适用于产品分布范围广泛、目的地数量较多的情况。
它可以减少运输距离和时间,并提高配送效率。
三、物流网络连接为了实现高效的物流运输,物流网络的连接至关重要。
以下是一些常用的物流网络连接方法:1. 直达运输直达运输是指将产品直接从供应商送达目的地,中间不经过任何中转。
这种运输方式快捷高效,适用于产品配送范围有限的情况。
2. 中转运输中转运输是指将产品从供应商送达仓储中心,然后再从仓储中心运输到配送中心,最后送达目的地。
物流中心合理布局

➢区域经济政策的稳定性 区域经济政策的稳定性是指物流中心所在
区域的宏观经济发展政策、物流业发展政 策、对物流业发展的优惠支持政策的稳定 性和一致性。物流业涉及到多种行业,因 此经济政策的稳定性以及政府对于发展物 流业的政策对物流业的发展是至关重要的。
27
➢税收政策的稳定性 税收政策的稳定性也是影响物流中心成本
18
➢经济合理性标准
物流服务需求情况 现有物流设施的利用程度 土地资源的可得性 劳动力资源的可得性 成本效益合理性
19
➢ 物流服务需求情况
物流服务是物流中心的核心业务,因此物流中心 所在区域的物流需求状况将影响物流中心的进一 步发展。如果有效需求不足,不仅会造成物流中 心设施设备能力的浪费,而且会影响到物流总行 经营效益的好坏。目前我国的物流市场中普遍存 在有效需求不足的情况,因此在筹建物流中心之 前对物流中心所在区域物流服务需求现状、潜在 的需求以及会对需求造成影响的因素进行调研和 分析是非常必要的。在明确了物流服务需求的现 状的基础上,制定相应的物流中心建设和发展策 略,以免造成资金的浪费。
37
➢各物流中心的经营费用:物流中心在经营过 程中发生的费用,如进出库费、保管维护费 等,它是与经营状态直接相关的费用,与物 流中心的经营规模有关。
24
➢政策环境稳定性标准
政治政策稳定性 区域经济政策的稳定性 税收政策的稳定性
25
➢政治政策稳定性 所谓的政治稳定性是指物流中心所在区域
的社会治安稳定性、恶性犯罪事件发生的 频率或者物流中心所在国家发生政变、暴 乱的可能性等。这些因素作为物流中心正 常运营的外部环境将会影响到物流中心长 期正常的运转以及利润目标的实现。因此, 政治政策稳定性是物流中心选址的标准之 一。
072-物流配送中心布局规划

五、区域配置
1、区域配置逻辑
(1)内围式程序 先决定厂房(或厂区)模板面积的大小与长宽比例, 然后在此范围内配置各相关作业区域。 (2)外张式程序 先配置各作业区域的相邻关系,完成可行的面积组 合型式,再框出外部厂房(或厂区)的面积范围, 并进行各区域面积的局部调整,以完成各区域面 积的配置。
2、配置方法
(2)ABC分析
依产品别进行年出货量及平均出货天数的出货量ABC 分析,并定出出货量高、中、低的等级及范围。
在后续规划设计阶段,可针对高、中、低类的产品 组作进一步的物性分析,以适当的分类及分组。 可依照出货高、中、低类别,制定不同类别产品的 存量水平,再乘以各类别的产品品项数,即可求 得拣货区储运量的初估值。
(2)商品送货频率估计法
①年运转量计算:将各类产品依单元负载单位换算 成相同单位的年储运总量。 ②估计年出货天数:即为工作天数,依各类产品别 估计年出货天数。 ③计算平均出货单日的储运量:将各产品年运转量 除以年出货天数。 ④估计送货频率:依产品别估计厂商送货频率。 ⑤估算库容量:以平均单日储运量乘以送货频率, 库容量=平均单日储运量×送货频率 ⑥估计安全系数:估计仓储运转的变动弹性,以估 算的库容量乘以安全系数,求出规划库容量,以 满足高峰时期的高运转需求。
(3)ABC交叉分析
针对年出货量及平均出货天数出货量的高、中、低 分类,进行组合交叉分析,则可得到九组出货类 型组,依其出货特性作适当的归并,再作不同存 量水平的规划。
(4)ABC组合交叉分析
出货特性的分析过程,如有足够的分析数据并配合计算机化 的作业进行,可建议将各类产品出货天数加入平均单日出 货量及年出货量,三项因素综合考虑,进行交叉分析与综 合判断,以更有效掌握产品出货特性。
快递布局规划书

快递布局规划书1. 引言本文档将详细介绍快递布局规划的重要性和目标,并提供了一些建议和指导原则,以帮助快递公司进行有效的布局规划。
2. 背景随着电子商务的快速发展,快递业务也呈现出蓬勃的增长势头。
为了满足市场需求,快递公司需要注重布局规划,以提高运输效率、降低成本,并为客户提供更好的服务体验。
3. 布局规划目标快递布局规划的主要目标是实现以下几个方面的提升:3.1 运输效率通过合理的布局规划,可以缩短货物的运输路径和时间,提高运输效率。
可以考虑以下布局策略:•将仓库和配送中心设置在战略地理位置,以便更好地服务不同地区的客户。
•根据货物流量和运输距离,合理划分货物配送区域,并设置相应的中转站,以减少车辆的行驶距离。
3.2 成本控制布局规划还应着重降低运输成本,包括以下方面:•降低人力成本:通过合理分配人力资源、自动化设备等,减少人工操作和劳动力成本。
•减少能源消耗:合理规划仓库和配送中心的位置和设施,以降低能源消耗。
3.3 顾客满意度快递布局规划应着眼于提升客户满意度,包括以下方面:•缩短快递时效:通过布局规划,减少货物在途时间,提高送达速度。
•提供便捷的服务:在客户密集地区设置自提点,方便客户自取快递。
4. 布局规划建议根据上述目标,本文提供以下一些建议和指导原则,以帮助快递公司进行布局规划:4.1 地理位置选择选择仓库和配送中心的地理位置很重要。
建议考虑以下几个因素:•快递公司的覆盖范围和目标客户群体。
•附近的交通便利程度,包括高速公路、铁路、公交车站等。
•人口密度和经济发展情况。
4.2 仓库布局设计仓库布局设计需要考虑以下几个方面:•合理划分不同功能区域,如货物存储区、包装区、分拣区等。
•最大限度地利用仓库空间,采用高架货架、自动化存储设备等,提高存储密度。
•合理设计货物流通路径,降低货物搬运距离和时间。
4.3 配送中心布局设计配送中心布局设计需要考虑以下几个方面:•合理划分货物配送区域,并设置相应的中转站点。
物流仓库 平面布局

连续输送 自动控制和检测 投资中等
3)AGV方式 配置: AGV+巷内输送机 特点:
柔性好 自动控制和管理 投资最大
4)穿梭车方式 配置: 有轨小车+巷内输送机+进出货
输送机/出入库台 特点:
柔性好 自动控制和管理 投资中等
货物单元出、入高层货架的形式
贯通式
同端出入式
旁流式
各自特点
物流模式
出入库口的布置
特点
同层端 同端出入式 多层同端
贯通式
巷道两端
旁流式
从巷道一端入、侧面出
能缩短出入库周期
便于管理、保养 效率稍降 空间利用率下降 可两条线路同时搬运 搬运效率高
仓库货区布局
(一)仓库货区布局的基本要求
1.适应仓储作业过程的要求,有利于仓储业务的顺利进行。 (1)单一的物流方向 (2)应尽量减少储存物资在库内的搬运距离,避免任何迂回运输。 (3)最少的装卸环节 (4)最大程度地利用空间
2.有利于提高仓库的经济效益 (1)货区布局应充分考虑地形、地质条件,因地制宜 (2)平面布置与竖向布置相适应 (3)货区布局能充分和合理地利用我国目前普遍使用的门式、桥式起
重机等固定设备 3.有利于保证安全生产和文明生产
(二)仓库货区布局的基本形式 1.货区布置的基本思路 (1)根据物品特性分区分类储存,将特性相近的物品集中存放; (2)将单位体积大、单位质量大的物品存放在货架底层,并且靠近出库
区和通道; (3)将周转率高的物品存放在进出库装卸搬运最便捷的位置; (4)将同一供应商或者同一客户的物品集中存放,以便于进行分拣配货
作业。 2.货区布置的形式 (1)垂直式布局:横列式布局、纵列式布局和纵横式布局。
物流中心内部布局课件

通过课程学习和实践操作,学生在物流中心内部布局设计、设备选 型和运营策略制定等方面的实践能力得到提升。
学习成果展示
学生可以将自己设计的物流中心内部布局方案进行展示,并接受老师 和同学的点评和建议。
THANKS
感谢观看
拣选区等。
设备配置
针对不同区域的特点,配置相应 的拣选设备,如电子标签、RF手 持终端、自动化拣选系统等,提
高拣选效率。
货架设计
合理设计货架高度、层数和间距 ,确保员工能够方便、安全地进
行拣选作业。
拣选效率提升方法
采用先进的拣选技术
如重力式货架、流利式货架等,实现快速、 准确的拣选作业。
实施波次拣选
内部布局原则与策略
内部布局原则
流程顺畅原则
确保物流中心内部各功能区域 之间的流程顺畅,减少不必要 的迂回和交叉,提高物流效率
。
空间充分利用原则
合理规划物流中心内部空间, 提高空间利用率,降低运营成 本。
灵活性原则
物流中心内部布局应具备一定 灵活性,以适应市场变化和业 务需求调整。
安全与环保原则
确保物流中心内部布局符合安 全与环保要求,保障员工人身 安全和健康,降低对环境的负
设备选型及配置方案制定
设备选型
根据作业需求和设备性能,选用合适的物流设备,如叉车、输送线、货架等,以 提高作业效率和质量。
配置方案制定
根据设备选型和作业流程,制定合理的设备配置方案,包括设备数量、布局和操 作流程等,以确保设备的充分利用和协调运作。
空间利用率提升举措
1 2
合理规划空间
根据物流中心内部布局和业务需求,合理规划各 功能区的空间大小和位置,以提高空间利用率。
几种常用的物流中心布局方法
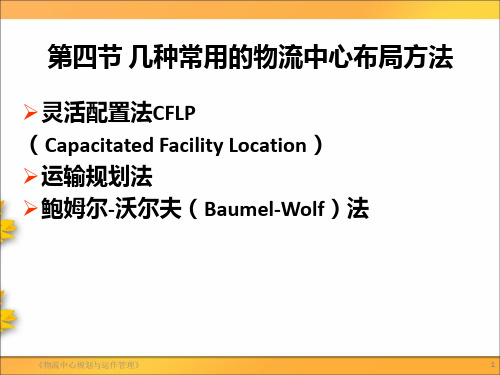
《物流中心规划与运作管理》
28
二、运输规划法
基本思想:以整数规划 模型为基础,不考虑网 点建设投资资本,从而 避免复杂计算,转化为 一个转运问题,以运输 规划方法求解。
《物流中心规划与运作管理》
29
※多元单品种物流网点布局j 1 i 1 k 1 k 1 j 1 i 1 k 1 i 1 不考虑网点建设投资
变成零的变量退出基成为非基变量,原来 的非基变量成了基变量。每次调整完后, 基变量发生了变化,所有非基变量的检验 数都要重新计算一次,如此反复进行直到 所有非基变量的检验数大于或等于零为止。
《物流中心规划与运作管理》
15
一、CFLP
针对具有若干企业的经济区域,欲在这些企业中寻 找若干个企业设立物流中心,分别为其周围的企业 进行物流服务。 CFLP法的基本思想是:首先假定网点布局方案已经 确定,即给出一组初始网点设置地址。根据初始方 案按运输规划模型求出各初始网点的供货范围,然 后在各供货范围内分别移动网点到其他备选地址上, 以使各供货范围内的总成本下降,找到各供货范围 内总成本最小的新网点设置地址,再将新网点设置 地址代替初始方案,重复上述过程直至各供货范围 内总成本不能再下降时为止。
《物流中心规划与运作管理》 8
《物流中心规划与运作管理》
9
(二)求检验数
如图示: 顶点→(1) 非基变量
(2) 基变量 (3) 基变量
(1)闭回路法
(4) 基变量 (6) (5) 基变量 基变量 非基变量的检验数就等于闭回路上说有奇数顶点 (顶点(1)、(3)、(5))对应的单位运价之 和减去所有偶数顶点(顶点(2)、(4)、(6)) 对应的单位运价之和。
C
jJ1
1j
X 1 j f1,1 0 1* 4 6 * 2 7 * 3 4 * 2 10 55
物流系统规划与设计第三章--物流中心的合理布局

CFLP法的基本思想是:首先假定网点 布局方案已经确定,即给出一组初始网点 设置地址。根据初始方案按运输规划模型 求出各初始网点的供货范围,然后在各供 货范围内分别移动网点到其他备选地址上, 以使各供货范围内的总成本下降,找到各 供货范围内总成本最小的新网点设置地址, 再将新网点设置地址代替初始方案,重复 上述过程直至各供货范围内总成本不能再 下降时为止。
(5)物流中心布局的常用方法
1.解析方法
它是通过数学模型进行物流中心网 点布局的方法。采用这种方法,首先根 据问题的特征、外部条件和内在联系建 立起数学模型或图解模型,然后对模型 求解获得最佳布局方案。
2.模拟方法
物流中心网点布局的模拟方法,是将 实际问题用数学方程和逻辑关系的模型表 示出来,然后通过模拟计算和逻辑推理确 定最佳布局方案。这种方法较之数学模型 找解析解简单。
物流中心是组织物流活动的基础条 件。由于商品资源的分布、需求状况、 运输条件和自然条件等因素的影响,使 得在同一计划区域内的不同地方,设置 不同规模的物流中心,划定不同的供货
范围,其整个物流系统和全社会的经济效 益是不同的,有时差别甚至很大。那么, 在已有的客观条件下,如何设置物流中心, 才能使物流费用最少,社会经济效益最佳, 对用户的服务质量最好呢?这就是物流中 心的合理布局问题。
* 方便用户
物流中心的服务对象是商品的供需双 方,而且主要是商品的需求用户。因此应 使物流中心网点尽量靠近用户一些,特别 应在用户比较集中的地方设置网点(工矿 企业集中的地方设点)。
第2章 物流中心的合理布局
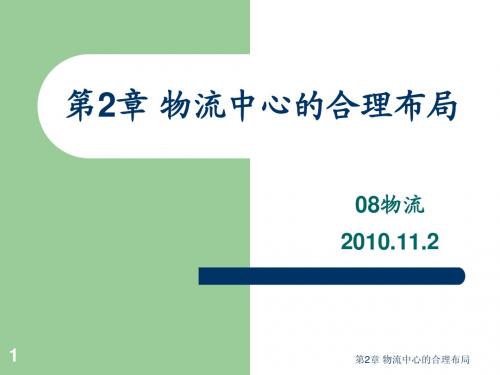
28
第2章 物流中心的合理布局
2、微分法
微分法举例:
五个企业的资料
企业 坐标(xi,yi)(公里) 物流量(吨) 运价ci (元/吨公里) A B C (2,5) 2500 0.75 D E
(3,8) (8,2) 2000 0.5 3000 0.5
(6,4) (8,8) 1000 0.75 1500 0.75
18
第2章 物流中心的合理布局
1、重心法
重心的特点是其质量等于所有各个质点质量的总和, 其重力矩等于各个质点重力矩之和。根据求平面中物 体系统重心的方法有:
n n x C j Wj C j WjX j j1 j1 n n y C W C j WjYj j j j1 j1
40
60 A 10 70 20
50 40 90 30 50 20 30 P 10
110
B
10
C
12
第2章 物流中心的合理布局
2.2.1 一元网点布局的图解法
优点:对费用函数为非线性情况的处理是方便 的;不仅可以找出最优解,而且还能给出最优 点附近的各种总成本等位线。 缺点:对大规模问题感到困难,在资源点和需 求点较多的情况下运用此方法时计算工作非常 复杂。
整理后得
19
第2章 物流中心的合理布局
重心法求解结果
由各个质点的质量和它们的坐标可求出重心坐标和重心 质量:
实际求得的(x, y)的值即为所求物流中心网点 位置的坐标,记为 (x,y) 。
20
第2章 物流中心的合理布局
重心法例题
某计划区域内资源点与需求点的分布情况,如下图所示, 各点资源量、需求量和运费率,如下表2-1所示。需在该 地区设置一个物流网点D,只考虑运输费用,求D的最佳 位置。 图中:
- 1、下载文档前请自行甄别文档内容的完整性,平台不提供额外的编辑、内容补充、找答案等附加服务。
- 2、"仅部分预览"的文档,不可在线预览部分如存在完整性等问题,可反馈申请退款(可完整预览的文档不适用该条件!)。
- 3、如文档侵犯您的权益,请联系客服反馈,我们会尽快为您处理(人工客服工作时间:9:00-18:30)。
1-4:区块式布置便成例
组装工厂(工程) 零件加工工厂(工程)
冲床工厂(工程)
出货场
模具进料
事务所
正门 停 车 场
完 成 品 置 场
检查区
完
成 组装工程 品
置 场
另件置场
次组装
焊接工程
另件置场
试验室
零件
零件进料
冲 模具
压 件
置场
置
场
模具 维护场
冲压工程
冲压工程
材料 置场
材料进料
工厂墙壁、窗等 全部设为通路带。 此外,要设定主 通路。
▪ 有效编排设备与工作区域的整合,使制程是直线流动, 生产一贯化。
▪ 使物料运搬的距离最短,避免有交叉重复现象发生。
▪ 维持生产作业与制程编排的弹性化,以利必要性之改 善调整。
▪ 使原物料在制程中能快速流动,避免堆积存放,造成 资金积压。
▪ 以合理有效的制程规划,减少对设备投资之重复。
▪ 建筑空间的有效利用规划。
• 节拍时间(T/T) • 作业顺序 • 标准中间库存数
目视管理
看板方式 ·搬运·备料·店面构成
自动化
100%不良品 1. 品质在工程
内做好 2. 省人化
异常会停止 异常会知道
〉设备
·灯号表示·避错装置
人的工作与机械的 工作要分开
2.丰田生产方式
2-3.『浪费』的定义
NO 浪费的种类 1 多做的浪费
2 *无附加价值之作业
15 3工程组装作业
18
16 放入完成品箱
3
17 回1工程
2 *步行之浪费
84 领取零件
365 *无附加价值之作业
85 领取通箱
217 *无附加价值之作业
2.丰田生产方式
2-3-2.『浪费』的恐怖
为何多做是浪费?
1.问题点·隐藏〖改善的需求〗
2.产生新的浪费(2次的浪费)
① 材料、零件先用 ② 电力、压气等能源之浪费 ③ 垫板、通箱需增加 ④ 运搬具、推高机等需增加
④TPS活动之变迁 19世
纪 产业革命
(工业的急速进步) 管理方式:泰勒方式 (科学的管理法)
扩大至其他业界
1913
年 大量生产方式
(输送带方式)
石油危机 .
丰田生产方式
(1彻97底0) 排除浪费
•及时化 •自动化
2.丰田生产方式
•作了就可卖岀的时代
(卖方是优势的时代)
第1次 第2次
石油危机
• 只买高品质低价格的 时代
浪费就是不会贡献给「附 加价值」的一切事物
·正味加工工时
正 味作 作业 业时
间
作业者 的动作
无 意 义 作 业
浪 费
无附加价值的作业
•作业时零件的取 出 •作业时工具的取 出 •工程间步行 •装箱 •品质点检
•机械作动 时间之等 待 •通箱取用 •材料之领 取 •不良品之 修正 •因欠零件 之等待 •因机械故 障之等待
7 取出1工程材料
5 *无附加价值之作业
8 步往2工程机械
2 *步行之浪费
9 将材料固定于2工程机械,再起动
18
10 等待2工程加工完了
62 *等待
11 取出2工程材料
7 *无附加价值之作业
12 走行至3工程组装工程
2 *步行之浪费
13 3工程:取组装零件
2 *无附加价值之作业
14 3工程:取起子工具
(买方是优势的时代) ① 低成长时代 ② 关税保护之废止 ③ 国际竞争之激烈化 ④ 市场全球化
2-1.成本主义与低减成本
成本主义
低减成本
概 利益 念 图
提高售价,利 益也会提升
利益
售 成价 本
降低成本, 会提升利益
售 价 成 本
•成本加利益来决定售价
想 (需要>生产)=卖方市场 法 售价=成本+利益
1.公司展望与工厂建设
1-3:区块式布置的想法
①标准的生产流程
模具置场 维护
原
材检 料 查 素材成型工程 进
库 存 素材加工工程
料
冲压、塑胶成形,
压铸成形等
机械加工, 二次组装等
进料零件 检查 保管
库 存表面处理工程
电镀、涂装、 热处理等
库 存 完成品加工工程
机械加工, 二次组装等
完
库 存
成 品 出
▪ 人、设备、物流、放置方式考量原则,并充分提升人 力绩效。
1-1-1设施布置的方向与目的
▪ 设布施置布方向置需要作长期规划。 ▪ 设施布置对产品生产成本有重大的影响、
要周详规划。 ▪ 设施布置需要由日常生产活动中不断的
改善,寻找最佳化的布置。
布置目的
将工厂的各种作业和附属设施、依照制造程序作最 适当的编排与布置。(设备、物流动线、在库区、 通路等)
交 货
货
②区块式布置的想法
检讨此一区块的物流会成为整流,人的动作, 检讨步骤 运搬会顺畅,中间库存是最少的设备配置。
① 包括未来,要生产那些制品,有多少量 ② 上述各制品的那些工程要内制 ③ 外周即工厂内主要通路带区块工厂内窗边,墙壁边的区域为通路 ④ 材料,零件的进料区块 ⑤ 交货及支给协力厂物品的进料区块 ⑥ 可工程顺序配置的工程与不可的工程要区分,工厂内生产之工程
4. 如另页所示,置场应以适当库存量为准,可收纳全制品为条件
(*5)工程顺序中工程配置例
区分
内容
设备列
工程顺序配置 一般加工 容易移动 一般加工机,低价设备,
可能
设备
之设备
制品专用加工机等
工程顺序配置 大型设备 移动困难 大型冲床,铸造设备,涂
不可能
装置工业 的设备
装,电镀装置等
1.公司展望与工厂建设
1-1-2基本生产线布置形态
在一般生産繫統設計中,存在着下列四 種不同的基本佈置形態:
▪ 以産品佈置 ▪ 以製程佈置 ▪ 以固定位置佈置 ▪ 以群組佈置
綜閤以上四種基本佈置形態,來探討『如何佈置工厰的 生産綫』。
1.公司展望与工厂建设 1-2:依据未来计划的生产线计划
①工厂建设阶段的检讨 1. 展望10年后,20年后之检讨 • 那些商品,每月要生产多少?要检讨 • 制品别内外工程区分的检讨(自己工
区块要定出 ⑦ 考量物量、运搬效率的置场区块 各制品、工程区每1件都要置场 ⑧ 检查、模具置场、保全等区块
③注意事项
1. 装置工业(热处理、电镀、涂装)等投资金额大,如为少量生 产则不算,故常是外包。
2. 墙壁边,窗边常成不用的小巷,被放置不用品,成为4S的大患
3. 做工程区块的检讨时,配置其内之设备,其大小应可容纳。
•以设备的泛 用化提升设备 家动率(投资 减少) •适合多种少 量能源费
•削减设备台 数以紧排方式 减少能源费 •作业动作浪 费之排除 •省人化 •以协力厂 TPS活动减少 购入费
材料不良低减
3-2.制造方法改善例
〈原来的生产方式〉
计 划 No1 生
No2
No3
生产流程
产 方
库存
库存
库存
库存
式 •物:每一工程都得要保持库存
厂内生产『工程区分』之检讨) 2. 工厂建设之空间:生产线空间、公用
设备、附带空间之检讨 • 对展望变更,可『临机应变对应』的
工厂建设空间也要考量。
②检讨内容
一、 『物流,人的动作,设备物品的放置方法』之
最适性检讨一
a) 包括将来要生产『那些 制品』多少量
各制品别有哪些工程,需 哪些设备
b) 原材料、零件,制品置 场的空间需要多少
•人:配置3名作业者
〈依TPS的生产方式〉
节
拍 时
No1
②
No2
③
间 库存① 生
产
•物:工程为一个流
•人:库存 ·作业者减至1/3
No3
④
⑤ 库存
2.丰田生产方式
基本的想法
1. 不降低成本、就无 法提高利益
2. 以制造方法改变成 本
3. 彻底排除浪费 4. 追求真正的效率
*1(更低成本做 出良好品质的商品)
•异常问题点不会表面化 •有库存则发生异常也不会紧张
•会增加用人数目 •会增加仓库空间或仓库
为何会产生多做?
1. 过度对应机械故障,品质不良,欠勤 2. 为了对应后工程领取时的差异 3. 误读的提升稼动率,提升虚有效率的结果 4. 停线是不好的罪恶感 5. 作业者太多 6. 生产架构准备做得不好
进行工作所必须的最少物料以外因生产 及运搬架构所发生的库存
对附加价值有直接贡献以外的动作
做不良品或修正品之浪费,加上要修整 的浪费
问题点
•会隐藏问题点及改善之需求 •材料、零件先用掉,又发生通箱、运搬 增加等新的浪费 •库存空间的增加 •作业工时的浪费
•运搬工时的浪费(装载、整理、移动等 之时间) •临时置场之浪费
如何布置生产线
物流及放置物品的最佳布置
工厂建设及设备布置应整体 性的企划与检讨。 因为工厂与工厂内部之设备 布置会在日常及每天的生产 活动中被利用到的。 为此:在工厂的布置时应考 量下列三项 ▪ 物(原材料、零件、制品、 模具、治工具、通箱等等) 的『物流』应单纯。 ▪ 人(作业者、运搬者等等) 的『动作/作业』应顺畅。 ▪ 物品的『放置方法/置放方式』 应容易了解。 将以上事项充分检讨后,再 做『工厂建设及设备』的布 置是较妥当的。
进料、交货的卡 车由外围通路顺 畅流动
零件、完成品置场 需全部制品点数都 有。再者,置场的 大小是以能保管的 「适当库存」为准
制品的流程是 「整流」,将设 备工程配置成不 停滞的顺流
2.丰田生产方式