塑料碗-模具设计
塑料碗注射模具设计

天津大学(高等教育自学考试)本科生毕业设计(论文)任务书机械工程学院办学点模具设计与制造专业10丁班设计(论文)题目:塑料碗注射模具设计完成期限:三个月自2012年11月20日至2013年3月10日止指导教师史清卫办学单位负责人刘伯伟批准日期2012、11、20 学生杨阳接受任务日期2012、11、20注:1. 本任务书一式两份,一份院或系留存,一份发给学生,任务完成后附在说明书内。
2.“检查人签名”一栏和“指导教师批准日期”由教师用笔填写,其余各项均要求打印。
一、设计(论文)原始依据(资料)1.设计题目:塑料碗注射模具设计2.原始数据:1)塑料制品材质:ABS2)生产批量:10 万件3)塑件的收缩率:0.5%4) 塑件表面光洁平整、无飞边毛刺及明显的熔接痕和其它斑痕5)零件图如下:二、设计(论文)内容和要求:(说明书、专题、绘图、试验结果等)1.设计内容:塑件工艺分析:1)塑件名称:塑料碗注射模具设计2)塑件材质:ABS3)塑件精度要求:该塑件尺寸中等,整体结构较简单.多数都为曲面特征,故选一般精度等级:5级2.模具结构及成型零件的设计:1)分型面的选择:分型面是决定模具结构形式的重要因素,它与模具的整体结构和模具的制造艺有密切关系,并且直接影响着塑料熔体的流动特性及塑料的脱模。
2)成型零件设计:本设计本应该按照一模一件的传统做法,但考虑到有内该产品带有简易的面结构,于是采用了顶出结构法,所以要用到顶出机构和块件。
而块件的选择用材和结构上要严密和精准,考虑了针对模架需要具高弹性有回复能力和耐磨性选用了45#钢为材料,配合顶出结构和动模固定板的运动、导柱导套的导向功能、复位杆及弹簧的回复功能进行开模脱模。
3)型腔数目的确定和浇注系统设计该塑件结构较简单,体积适中,所以采用一模一件结构。
浇注系统由主流道、分流道、进料浇口和冷料穴组成。
4)脱模结构的设计及导向、定位结构的确定采用推杆推出结构导向机构采用导柱、导套定位机构主要采用定位板、复位杆等5)冷却系统的设计6)注射机的选择7)绘制注射模具的装配图、成型零件图和其他标准需要补充加工的零件图:3.设计说明书1)制品如上图所示2)相关计算a.成型尺寸的计算b.制品体积重量计算c.注射机注射容量计算附:设计进度计划表天津大学高等教育自学考试本科生毕业设计(论文)开题报告模具的发展越来越多的被人们所重视,它凝聚了各类高新技术,能快速精密的直接把材料成型、焊接、装配成零部件、组件或产品,其效率、精度、流线、超微型化、节能、环保,以及产品的性能、外观等,都是传统工艺方法所望尘莫及的。
塑料碗注塑模具设计

塑料碗注塑模具设计
塑料碗注塑模具设计需要考虑以下几个方面:
1. 确定碗的形状和尺寸:根据要生产的塑料碗的规格要求,确
定碗的形状和尺寸,包括碗的口径、高度、底部半径等。
2. 碗的结构和壁厚:根据碗的规格和要求,设计碗的结构和壁厚。
一般情况下,塑料碗的底部比较厚,边缘比较薄,可以考虑采
用不均匀壁厚注塑技术。
3. 碗的材质:根据生产要求,选择合适的塑料材料,如聚丙烯、聚苯乙烯等,进行模具设计。
4. 模具的结构:根据碗的形状和结构设计模具的拆模方式、模
具的夹紧方式、模具的注射系统、模具的冷却系统、模具的排气系
统等。
5. 模具的材料和加工工艺:选择适合的模具材料,如优质的模
具钢,通过精细加工、CNC加工等工艺,制造出精确的模具。
6. 模具的功能和寿命:确定模具的使用寿命和工作效率,确保
模具可以持续稳定地生产出高质量的塑料碗。
以上是塑料碗注塑模具设计的一些基本要点,需要根据具体情
况进行细致的设计和调整。
碗注塑模具设计毕业设计说明书

碗的注射模具设计说明书设计题目:碗的注射模具设计指导老师:xx设计者:xxx系别:信息控制与制造系班级:xx学号:xx绪论{一} 【模具在加工工业中的地位】模具是利用其特定形状去成型具有一定的形状和尺寸制品的工具。
在各种材料加工工业中广泛的使用着各种模具。
例如金属铸造成型使用的砂型或压铸模具、金属压力加工使用的锻压模具、冷压模具等各种模具。
对模具的全面要求是:能生产出在尺寸精度、外观、物理性能等各方面都满足使用要求的公有制制品。
以模具使用的角度,要求高效率、自动化操作简便;从模具制造的角度,要求结构合理、制造容易、成本低廉。
模具影响着制品的质量。
首先,模具型腔的形状、尺寸、表面光洁度、分型面、进浇口和排气槽位置以及脱模方式等对制件的尺寸精度和形状精度以及制件的物理性能、机械性能、电性能、内应力大小、各向同性性、外观质量、表面光洁度、气泡、凹痕、烧焦、银纹等都有十分重要的影响。
其次,在加工过程中,模具结构对操作难以程度影响很大。
在大批量生产塑料制品时,应尽量减少开模、合模的过程和取制件过程中的手工劳动,为此,常采用自动开合模自动顶出机构,在全自动生产时还要保证制品能自动从模具中脱落。
另外模具对制品的成本也有影响。
当批量不大时,模具的费用在制件上的成本所占的比例将会很大,这时应尽可能的采用结构合理而简单的模具,以降低成本。
现代生产中,合理的加工工艺、高效的设备、先进的模具是必不可少是三项重要因素,尤其是模具对实现材料加工工艺要求、塑料制件的使用要求和造型设计起着重要的作用。
高效的全自动设备也只有装上能自动化生产的模具才有可能发挥其作用,产品的生产和更新都是以模具的制造和更新为前提的。
由于制件品种和产量需求很大,对模具也提出了越来越高的要求。
因此促进模具的不断向前发展[二] 【模具的发展趋势】近年来,模具增长十分迅速,高效率、自动化、大型、微型、精密、高寿命的模具在整个模具产量中所占的比重越来越大。
从模具设计和制造角度来看,模具的发展趋势可分为以下几个方面:(1)加深理论研究在模具设计中,对工艺原理的研究越来越深入,模具设计已经有经验设计阶段逐渐向理论技术设计各方面发展,使得产品的产量和质量都得到很大的提高。
塑料碗注塑模具毕业设计(全套图纸)

目录一、塑料的工艺性 (1)(1)、注塑模工艺 (3)(2)、化学和物理特征 (3)(3)、塑件的尺寸与公关差 (4)1、塑件的尺寸与公关差 (4)2、塑件尺寸公差标准 (4)3、塑料的表面质量 (4)二、注射成型机的选择 (4)三、型腔布局与分型面设计 (5)(1)、型腔数目的确定 (5)(2)、型腔的布局 (5)(3)、分型面的设计 (5)四、浇注系统设计 (6)(1)、主流道设计 (6)(2)、主流道衬套的固定 (7)(3)、分流道的设计 (8)(4)、浇口的设计 (10)五、成型零件的设计 (12)(1)、成型零件的结构设计 (12)1、凹模结构设计 (12)2、型芯结构设计 (12)(2)、成型零件工作尺寸计算 (13)1、外型尺寸 (14)2、内腔尺寸 (15)六、合模导向机构设计 (16)(1)、导柱结构 (17)(2)、导套结构 (17)七、脱模机构的设计 (18)(1)、脱模机构的设计的总体原则 (18)(2)、推杆设计 (18)1、推杆的形状 (19)2、推杆的位置与布局 (19)(3)、推件板设计的要点 (19)(4)、开模行程与推出机构的校核 (20)(5)、浇注系统凝料脱模机构 (20)八、模具工作原理简述 (20)工艺卡 (22)参考文献 (23)一、塑料的工艺性(1)、注塑模工艺干燥处理:如果储存适当则不需要干燥处理。
熔化温度:220~275℃,注意不要超过275℃。
模具温度:40~80℃,建议使用50℃。
结晶程度主要由模具温度决定。
注射压力:可大到1800bar。
注射速度:通常,使用高速注塑可以使内部压力减小到最小。
如果制品表面出现了缺陷,那么应使用较高温度下的低速注塑。
流道和浇口:对于冷流道,典型的流道直径范围是4~7mm。
建议使用通体为圆形的注入口和流道。
所有类型的浇口都可以使用。
典型的浇口直径范围是1~1.5mm,但也可以使用小到0.7mm的浇口。
对于边缘浇口,最小的浇口深度应为壁厚的一半;最小的浇口宽度应至少为壁厚的两倍。
塑料碗注射模具设计实施方案

塑料碗注射模具设计实施方案清晨的阳光透过窗帘的缝隙,洒在图纸上的那一刻,我的大脑就像被启动的机器,开始运转起来。
塑料碗,这个日常生活中最常见的物品,其背后的注射模具设计,却是一门不简单的技术活。
我就用这10年的经验,给大家详细解析一下这个“塑料碗注射模具设计实施方案”。
一、市场调研与需求分析我们要了解市场现状。
市场上的塑料碗种类繁多,材质、大小、用途各不相同。
这就需要我们进行深入的市场调研,了解消费者的需求。
比如,家庭使用的塑料碗更注重实用性,而餐饮业则更看重美观和耐用性。
二、模具设计原则1.符合工艺要求:模具设计要满足塑料碗的生产工艺,包括注塑、冷却、脱模等环节。
2.结构优化:模具结构要简洁、合理,便于加工和维护。
3.耐用性:模具材料要选择耐磨、耐腐蚀的材质,保证模具的使用寿命。
4.安全性:模具设计要考虑到操作者的安全,避免出现意外伤害。
三、模具设计流程1.初步设计:根据市场需求,绘制塑料碗的二维图纸,确定模具的基本结构。
2.三维建模:利用CAD软件,对模具进行三维建模,细化每一个部分。
3.模具分解:将模具分解成多个部件,便于加工和组装。
4.模具加工:根据三维模型,进行模具的加工制作。
四、关键环节解析1.注塑成型:这是模具设计中的核心环节,要确保塑料熔体在模具中的流动顺畅,避免产生气泡、缩水等缺陷。
2.冷却系统:冷却系统设计要合理,保证塑料碗在冷却过程中均匀收缩,避免变形。
3.脱模机构:脱模机构要设计得巧妙,确保塑料碗在脱模过程中不会损坏。
五、模具验收与改进模具设计完成后,要进行严格的验收。
验收合格后,进入批量生产阶段。
在批量生产过程中,要不断收集反馈,对模具进行改进,以适应市场需求的变化。
六、后期维护与服务模具的后期维护和服务同样重要。
我们要定期对模具进行检查,发现问题及时解决,确保模具的稳定运行。
1.调研别走马观花市场调研不能只看表面,要深入到消费者的使用习惯和偏好里去。
别以为塑料碗就那回事,一调研才发现,有的人喜欢轻便的,有的人偏好厚实的。
【完整版】碗注塑模具设计毕业设计说明书

碗的注射模具设计说明书设计题目:碗的注射模具设计指导老师:xx设计者:xxx系别:信息控制与制造系班级:xx学号:xx绪论{一} 【模具在加工工业中的地位】模具是利用其特定形状去成型具有一定的形状和尺寸制品的工具。
在各种材料加工工业中广泛的使用着各种模具。
例如金属铸造成型使用的砂型或压铸模具、金属压力加工使用的锻压模具、冷压模具等各种模具。
对模具的全面要求是:能生产出在尺寸精度、外观、物理性能等各方面都满足使用要求的公有制制品。
以模具使用的角度,要求高效率、自动化操作简便;从模具制造的角度,要求结构合理、制造容易、成本低廉。
模具影响着制品的质量。
首先,模具型腔的形状、尺寸、表面光洁度、分型面、进浇口和排气槽位置以及脱模方式等对制件的尺寸精度和形状精度以及制件的物理性能、机械性能、电性能、内应力大小、各向同性性、外观质量、表面光洁度、气泡、凹痕、烧焦、银纹等都有十分重要的影响。
其次,在加工过程中,模具结构对操作难以程度影响很大。
在大批量生产塑料制品时,应尽量减少开模、合模的过程和取制件过程中的手工劳动,为此,常采用自动开合模自动顶出机构,在全自动生产时还要保证制品能自动从模具中脱落。
另外模具对制品的成本也有影响。
当批量不大时,模具的费用在制件上的成本所占的比例将会很大,这时应尽可能的采用结构合理而简单的模具,以降低成本。
现代生产中,合理的加工工艺、高效的设备、先进的模具是必不可少是三项重要因素,尤其是模具对实现材料加工工艺要求、塑料制件的使用要求和造型设计起着重要的作用。
高效的全自动设备也只有装上能自动化生产的模具才有可能发挥其作用,产品的生产和更新都是以模具的制造和更新为前提的。
由于制件品种和产量需求很大,对模具也提出了越来越高的要求。
因此促进模具的不断向前发展[二] 【模具的发展趋势】近年来,模具增长十分迅速,高效率、自动化、大型、微型、精密、高寿命的模具在整个模具产量中所占的比重越来越大。
从模具设计和制造角度来看,模具的发展趋势可分为以下几个方面:。
最新塑料盘子注塑模具设计课程设计

塑料盘子注塑模具设计课程设计注塑模具设计课程设计课程名称:盘子注塑模具设计姓名:郭光平指导教师:刘元义学院:机械工程学院专业班级:材料成型及控制工程–模具1002班日期:2014年1月目录摘要 (4)前言 (5)1 工艺分析 (6)1.1材料特性分析--------------------------------------------------------------------------------------------------- 61.2材料的参数------------------------------------------------------------------------------------------------------ 61.3注射参数--------------------------------------------------------------------------------------------------------- 6 1.4塑件制作数据 --------------------------------------------------------------------------------------------------- 71.4.1塑件的尺寸 ------------------------------------------------------------------------------------------- 71.4.2塑件尺寸公差标准 --------------------------------------------------------------------------------- 111.4.3塑件的表面质量 ------------------------------------------------------------------------------------ 111.5确定注射机---------------------------------------------------------------------------------------------------- 122 模具结构设计 (14)2.1分型面选择---------------------------------------------------------------------------------------------------- 142.2浇口设计------------------------------------------------------------------------------------------------------- 162.3流道设计------------------------------------------------------------------------------------------------------- 162.4浇口套设计---------------------------------------------------------------------------------------------------- 173 排气系统和冷却系统设计 (19)3.1排气系统设计------------------------------------------------------------------------------------------------- 193.2冷却系统的设计 --------------------------------------------------------------------------------------------- 194.1脱模机构设计的总体原则 --------------------------------------------------------------------------------- 214.2推件力的计算------------------------------------------------------------------------------------------------- 224.2.1脱模力 ------------------------------------------------------------------------------------------------ 225 底板设计 (23)5.1凹模尺寸设计------------------------------------------------------------------------------------------------- 235.1.1凹模的径向尺寸计算------------------------------------------------------------------------------- 235.2凸模尺寸设计------------------------------------------------------------------------------------------------- 245.2.1凸模的径向尺寸计算------------------------------------------------------------------------------- 245.2.2凹模的高度尺寸计算------------------------------------------------------------------------------- 25 7 导柱设计 (28)7.1导柱------------------------------------------------------------------------------------------------------------- 287.2导套 ------------------------------------------------------------------------------------------------------------ 287.3推杆的选择---------------------------------------------------------------------------------------------------- 298 材料选择 (30)8.1凹凸模材料的选择 ------------------------------------------------------------------------------------------ 309 注射机校核 (31)9.1注射量---------------------------------------------------------------------------------------------------------- 319.2注射压力------------------------------------------------------------------------------------------------------- 319.3锁模力---------------------------------------------------------------------------------------------------------- 319.4开模行程------------------------------------------------------------------------------------------------------- 3110 小结 (33)参考文献 (34)摘要本设计针对分析盘子的塑件图,完成其造型设计,根据分析盘子的塑件的特点完成其注射模设计,本文主要阐述了塑料盘子注塑成型的基本原理,注射模具的结构设计方法及过程。
基于Moldflow的塑料碗注塑模设计
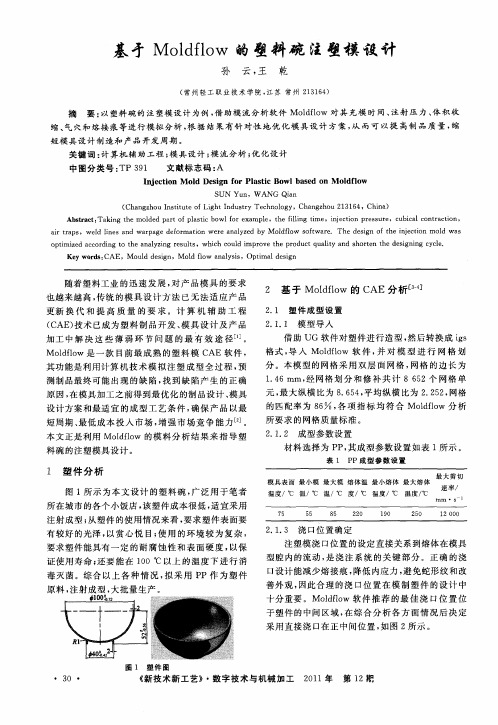
Ab ta tTa ig t emod d p r fpa t o o x mp e h iig t ,ijcin p es r ,c bc l o ta t n, src : kn h le a to lsi b wlfre a l,t ef l i c l n me n t r su e u ia n rci e o c o
o tmie c o dn o t e a a y i g r s ls p i z d a c r i g t h n l zn e u t ,wh c o l mp o e t e p o u tq aiy a d s o t n t e d sg i g c c e ih c u d i r v h r d c u l n h r e h e i n n y l. t Ke r s CAE,M o l e i n,M o d f w n l ss y wo d : u d d sg l l o a a y i ,Op i ld sg t ma e i n
arta s i r p ,wed l e n r a ed f r t n we ea ay e y Mod lw o t r.Th ein o h ne t n mod wa l i sa d wa p g eo mai r n lz d b lfo s fwae n o ed sg ft eijci l s o
表 1 P P成 型 参 数 设 置
1 塑 件分 析
图 1所示 为 本文 设 计 的塑 料 碗 , 广泛 用 于 笔者 所 在城 市 的各个小 饭店 , 塑件成本 很 低 , 宜采用 该 适
- 1、下载文档前请自行甄别文档内容的完整性,平台不提供额外的编辑、内容补充、找答案等附加服务。
- 2、"仅部分预览"的文档,不可在线预览部分如存在完整性等问题,可反馈申请退款(可完整预览的文档不适用该条件!)。
- 3、如文档侵犯您的权益,请联系客服反馈,我们会尽快为您处理(人工客服工作时间:9:00-18:30)。
¥塑料模具设计说明书项目名称:塑料碗注射模具设计系别:机电系专业:机械设计制造及其自动化组长:学号::组员:学号:学号:学号:学号:学号:指导教师:)二OO九年四月目录一、塑料碗的零件图 (4)1.塑料碗的3D模型(SolidWorks造型) (4)二、塑料碗制品的结构特点 (5))三、选择的塑料及其性能、成型条件 (6)1.选择的塑料 (6)塑料的性能 (6)的成型条件 (6)四、确定型腔数、排列方式和分型面 (7)1、型腔数目的确定 (7)2、型腔的排列方式 (7)3、分型面的设计 (8)…五、选择注射机和注射机参数 (9)1 、注射机的组成 (9)2.锁模力的校核 (11)3. 注射量的校核 (11)4. 核膜机构的尺寸的校核 (11)六、模具型腔和型芯尺寸计算 (12)1、型腔的内形尺寸计算 (12)2、型腔的深度尺寸计算 (13)%3、型芯的外形(外径)尺寸 (13)4、型芯的高度尺寸计算 (14)六、确定模架尺寸 (15)1、导柱的结构 (15)2、导套的结构 (15)七、参考资料 (16)@一、塑料碗的零件图|1.塑料碗的3D模型(SolidWorks造型)2.塑料碗的尺寸图二、塑料碗制品的结构特点1.餐具外观酷似瓷器或象牙,不易脆裂又适宜机械洗涤。
2.刚性和强度比传统的塑料制品好,制品不易变形。
(3.耐高温性能较好,可以能用作微波炉餐具但低温脆性高。
4.在室温下不固化,一般在130~150℃热固化,加少量酸催化可提高固化速度。
5.塑料碗采用凹模结构设计,凹模是成型产品外形的主要部件。
其结构特点:随产品的结构和模具的加工方法而变化。
镶拼的组合方式的优点:对于形状复杂的型腔,若采用整体式结构,比较难加工。
所以采用组合式的凹模结构。
同时可以使凹模边缘的材料的性能低于凹模的材料,避免了整体式凹模采用一样的材料不经济,由于凹模的镶拼结构可以通过间隙利于排气,减少母模热变形。
对于母模中易磨损的部位采用镶拼式,可以方便模具的维修,避免整体的凹模报废。
组合式凹模简化了复杂凹模的机加工工艺,有利于模具成型零件的热处理和模具的修复,有利于采用镶拼间隙来排气,可节省贵重模具材料。
三、选择的塑料及其性能、成型条件|1.选择的塑料:PP(聚丙烯)塑料的性能:PP是一种半结晶性材料。
它比PE要更坚硬并且有更高的熔点。
由于均聚物型的PP温度高于0℃以上时非常脆,因此许多商业的PP材料是加入1~4%乙烯的无规则共聚物或更高比率乙烯含量的钳段式共聚物。
共聚物型的PP材料有较低的热扭曲温度(100℃)、低透明度、低光泽度、低刚性,但是有更强的抗冲击强度。
PP的强度随着乙烯含量的增加而增大。
PP的维卡软化温度为150℃。
由于结晶度较高,这种材料的表面刚度和抗划痕特性很好。
PP不存在环境应力开裂问题。
通常,采用加入玻璃纤维、金属添加剂或热塑橡胶的方法对PP进行改性。
PP的流动率MFR范围在1~40。
低MFR的PP材料抗冲击特性较好但延展强度较低。
对于相同MFR的材料,共聚物型的强度比均聚物型的要高。
由于结晶,PP的收缩率相当高,一般为~%。
并且收缩率的方向均匀性比PE-HD等材料要好得多。
加入30%的玻璃添加剂可以使收缩率降到%。
均聚物型和共聚物型的PP材料都具有优良的抗吸湿性、抗酸碱腐蚀性、抗溶解性。
然而,它对芳香烃(如苯)溶剂、氯化烃(四氯化碳)溶剂等没有抵抗力。
PP也不象PE那样在高温下仍具有抗氧化性。
的成型条件:塑料碗在注射成型时,要经过三个阶段的转换:一是塑料未进入料筒时的颗粒状态;二是塑料在料筒中的塑化流动而达到的熔融状态;三是塑料通过注射模浇注系统的冲模流动及冷却定型。
在每个阶段中,都要有特定的工艺成型条件。
颗粒状态(1)预热干燥原料应先进行预热干燥处理,预热时间为,料温升至80C°-100C°。
原因是原料中往往水分含量太高,如果直接放入料筒,会导致制品表面暗淡,色泽不均匀以及表面气泡等故障。
但是预热时间要适当,温度也不能过高。
温度太高会导致制品表面产生焦斑;预热温度太高或预热时间太长会导致制品表面色泽不均匀。
、(2)加料计量进料量要准确。
如果原料过多会造成制品飞边多,清理困难;如果原料太少,会造成成型压力不够,制品不能完全固化等弊端。
熔融状态(1)控制成型温度和压力根据PP塑料的最佳成型条件要求,应将模具的成型温度控制在150-220C°之间;初压控制在 70Mpa-90Mpa之间,加压时间为1-5s。
原料温度太高,容易导致制品表面有焦斑及制品色泽不均匀;初压时间太长,会导致制品表面疏松;成型温度和压力不适当,会导致塑料流动性能太差。
(2)排气在成型时会产生缩合水及挥发性气体,所以应当在成型时进行排气以防止制品表面疏松。
通常放气的次数和时间长短凭经验确定,放气动作力求迅速。
只要卸除一下压力,再立即恢复到原来的压力,放气动作就算完成了。
我们的塑料碗结构不复杂,所以不必从模具方面考虑排气结构。
冲模流动及冷却定型^(1)固化阶段排气后即刻合模升压至70-90Mpa,时间70s左右。
在此阶段,固化时间应当充足,否则会导致制品表面暗淡。
(2)出模完成固化之后,风冷制品,顶出机构将制品顶出。
(3)出模后的加工我们制作的是食品器具,所以制品出模后,应入120C°以上的烘箱中加热30—60min,使之进一步固化。
最后进行打磨飞边,完成塑料碗的制作。
四、确定型腔数、排列方式和分型面1、型腔数目的确定)型腔数目的确定,应根据塑件的几何形状及尺寸、质量、批量大小、交货长短、注射能力、模具成本等要求来综合考虑。
根据注射机的最大锁模力确定型腔数目n ,即件废锁A AFf fn-=式中锁F——注射机的额定锁模力(N)废A——模具上浇注系统及飞边在分型面上的投影面积(m2)件A——塑件在分型面的投影面积(m2)f ——单位面积所需的锁模力(N/m2)大多数小型件常用多型腔注射模,面高精度塑件的型腔数原则上不超过4个,生产中如果交货允许,我们根据上述公式估算,采用一模二腔。
》2、型腔的排列方式考虑到模具成型零件和抽芯结构以及出模方式的设计,模具的型腔排列方式如下图所示:图(1)3、分型面的设计分型面位置选择的总体原则,是能保证塑件的质量、便于塑件脱模及简化模具的结构,分型面受到塑件在模具中的成型位置、浇注系统设计、塑件的结构工艺性及精度、嵌件位置形状以及推出方法、模具的制造、排气、操作工艺等多种因素的影响,因此在选择分型面时应综合分析比较具体可以从以下方面进行选择。
a)确保塑件尺寸精度,有同轴度要求的部分全部在动模部分成型,选分型面时,还应考虑减小由脱模斜度造成塑件的大小端尺寸差异。
b)"c)确保塑件表面要求,分型面尽可能选择在不影响塑件外观的部位以及塑件外观的要求,而且分型面处产生的飞边应容易修整加工。
d)考虑锁模力,尽可能减少塑件在分型面上的投影面积。
e)考虑模板间距。
f)便于塑件顺利脱模,尽量使塑件开模时留在动模部分。
g)考虑侧抽芯机构,应尽量避免侧抽芯机构。
h)尽量方便浇注系统的布置。
i)便于排溢。
j)便于嵌件的安放。
k)|l)模具整体结构简化,尽量减少分型面的数目,尽量采用平直分型面。
m)考虑模具制造难易性。
五、选择注射机和注射机参数1 、注射机的组成注射机的全称应为塑料注射成型机。
注射机主要由注射装置、合模装置、液压传动系统、电器控制系统及机架等组成。
工作时模具的动、定模分别安装于注射机的移动模板和定模固定模扳上,由合模机构合模并锁紧,由注射装置加热、塑化、注射待融料在模具内冷却定型后由合模机构开模,最后由推出机构将塑件推出。
1、锁模油缸2、锁模机构3、移动模板4、顶出杆5、定模固定板6、控制台7、料筒及加热器8、料斗9、定量供料装置 10、注射油缸注塑机的选择与参数校核根据课程设计实际要求我们选用型号为XS-Z-60的注射机,如图其主要技术参数如下:最大注射容量为60cm3;注射压力为122Mpa;锁模力为500kN;最大注射面积为130cm2;最大模具厚度为200cm;最小模具厚度为70mm;喷嘴圆弧半径R12mm;喷嘴孔半径R2mm;中心顶出孔半径R25mm;模板开模行程180mm。
根据上述所选注射机进行参数校核。
2.锁模力的校核按F≥KpA分公式校核锁模力。
其中,F为注射机的最大锁模力;p为模内平均压力(型腔内熔体的平均压力);A分为所有制品、流道和浇口在分型面上的投影面积之和。
K为压力损耗系数,一般取。
由于制品材料为pp,属于中等粘度塑料和有精度要求的制品,查相关资料得:p为,取p=30MPa进行校核。
A分是分型面上的投影面积,经计算(可利用软件的分析功能进行计算),得到单个塑件的投影面积为4755mm2,浇注系统的投影面积约为80mm2,则两个制品、流道和浇口在分型面上的投影面积之和A分为9710mm2因此:KpA分= N=321X103N=321kNF=500kN≥321kN所以锁模力足够,满足锁模要求。
3. 注射量的校核经计算得到单个塑件的体积为15.86cm3,浇注系统的体积约为2cm3,因此,模具中塑件和浇注系统的总重量Gmax=2x15.86cm3+2cm3=33.72cm3.注射机的注射量G=60cm3,按校核公式=60x0.8cm3=48cm3≥33.72cm3,满足注射成型的要求。
4. 核膜机构的尺寸的校核(1)模具厚度的校核注射机允许安装的模具最高厚度为200mm;注射机允许安装的模具最小厚度为70mm。
模具实际厚度 H=定模座厚度+型腔板厚+型芯固定板厚+垫铁厚+垫块厚+动模座板厚 =20mm+30mm+30mm+32mm+35mm+20mm=167mm显然,注射机允许安装的模具最小厚度≤模具实际厚度H≤注射机允许安装的模具最大厚度,模具厚度满足要求。
(2)开模行程的校核按开模取件的最小开距进行校核。
该模具的浇注系统为侧浇口形式,单分型面注射模,可按下式校核:S≥H1+H2(5-10)mm其中,注射机最大开模行程S为180mm;制品的推出距离H1为10mm:制品的总高度H2为50mm。
H1+H2+(5-10)mm=10mm+50mm+10mm=70mm显然,注射机最大开模行程S≥70mm,模具的开模行程足够六、模具型腔和型芯尺寸计算下图为我们所设计的塑料碗的结构尺寸图,我们根据图示的尺寸大小计算出型腔和型芯的尺寸。
1、型腔的内形尺寸计算碗口部分的型腔内形尺寸: 1腔D =[]zx Q m 0s1cp S1S1d d∆+∆-+=314.1014.143%)2115151+⎥⎦⎤⎢⎣⎡⨯-⨯+=38.00+上述计算中,塑件公差s1∆取1.14mm ,塑料平均收缩率cp Q 取2%,综合修正系数x 取3/4。