工序拆分与工时测算表
工时计算方法大全(各机床工时、各工序工时)
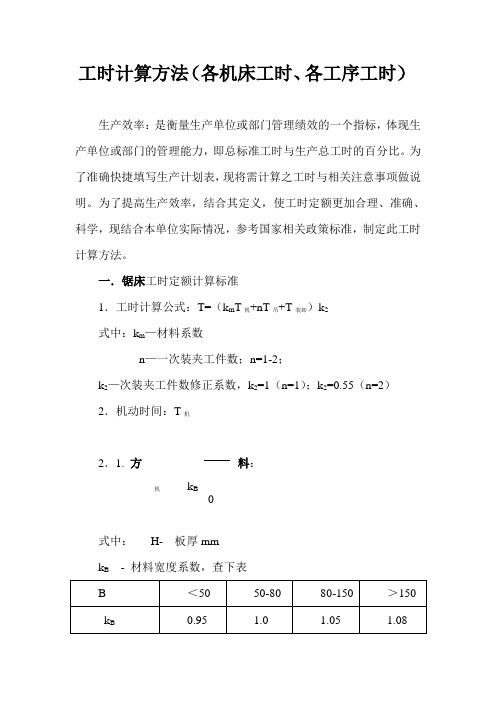
工时计算方法(各机床工时、各工序工时)生产效率:是衡量生产单位或部门管理绩效的一个指标,体现生产单位或部门的管理能力,即总标准工时与生产总工时的百分比。
为了准确快捷填写生产计划表,现将需计算之工时与相关注意事项做说明。
为了提高生产效率,结合其定义,使工时定额更加合理、准确、科学,现结合本单位实际情况,参考国家相关政策标准,制定此工时计算方法。
一.锯床工时定额计算标准1.工时计算公式:T=(k m T 机+nT 吊+T 装卸)k 2 式中:k m —材料系数n —一次装夹工件数;n=1-2;k 2—次装夹工件数修正系数,k 2=1(n=1);k 2=0.55(n=2) 2.机动时间:T 机 2.1. 方料:式中: H- 板厚mm k B - 材料宽度系数,查下表T 机=k BH22.2.棒料:式中D —棒料外径 mm2.3. 管料:式中d 0—管料内径;mm2.4..方管:式中:H—方管外形高mm ;H 0—方管内腔高mm ; B 0—方管内腔宽mm ;3.吊料时间:4.装卸料时间及其它时间:T机=D24T 机=D —d 02 2410000T 机=H—H 0*B 0208000T吊=L 1000 T装卸LD综上所述:方料:T=(0.12+n0.0519H+0.001L )k 2-0.00013 H 0*B 0 (min ) 圆料:T=(0.12+n0.0429D+0.001L )k 2-0.0001 d 02 (min ) n —一次装夹工件数;n=1-2;k 2—次装夹工件数修正系数,k 2=1(n=1);k 2=0.55(n=2)二.剪板冲压折弯工时定额计算标准1..剪板工时定额计算方法剪板单件工时定额:a —每块工时系数、见表b —剪角次数剪板工时系数表=0.12+1800840T =k *a+b a3注:准备工时按100件基数计算,每件0.2,共计200分剪板毛刺工时:T=0.3 + 处理长度/400剪板校正T校=k*T材料系数K=1~1.52.冲压每冲一次工时3..折弯工时定额计算方法折弯工时定额:t2=Σa i折弯工时定额系数表注:规格栏中,为折弯长度,a为每折一刀的工时(理论计算:每刀0.15分×折1.5=0.225+0.2=0.425→0.5)↓准备工时三.风割焊接工时定额计算标准1.风割工时公式:修磨工时含补焊工时: T 修磨 = T 风割 /22.焊接单件工时: T 焊接=T 工件装卸+T 点焊+ T 全焊 2.1 装卸工件工时:T 工件装卸=(T 01+0.2n )B式中:T 01—装卸基本工时;(取T 01=0.2); n-- 工件数 B-- 重量系数(见表)2.2. 点焊单件工时:T 点焊= T 02+0.1J+0.1N式中:T 02—点焊基本工时;J —点焊数;N —点焊时工件翻转次数;2.3. 全焊单件工时:T 全焊= T 03+0.1M+0.1N+L Σ/200+0.2NC 式中:T 03—全焊基本工时;M —焊缝段数;N —全焊时工件翻转次数;L Σ--焊缝长 NC---焊接参数调节次数注:小件装卸与点焊工时合并,统称点焊工时; 重量系数(B )T风割=风割长度×3+1.5V1、飞溅按焊接工时的二分之一计算+0.12、校正按焊接工时的二分之一计算+0.13、有辅助工帮助表卸模,从焊接工时中分取三分之一4、焊接有准备工时按每项20分钟5、点焊螺母按0.5分钟一个四.钻床工时定额1、T=kT机+ T装卸其中k—难度系数有工差要求k=1.5 有深度要求k=1.1 扩孔及攻丝k=0.82、机动时间:T机注:L/D≥8时,须另增排屑时间60%。
工序动作拆解及增值分析表

动作23 动作24 动作25 动作26 动作27 动作28 动作29 动作30 动作31 动作32 工序4
动作3 动作1 动作2 动作3 动作4 动作5 动作6 动作7 动作8 动作9 动作10 动作11 动作12 动作13 动作14 动作15 动作16 动作17
动作18
动作19 动作20 动作21 动作22 动作23 动作24 动作26 动作27 动作28
电极和电极弹簧装入电极盖
右手拿电极盖,左手拿电池连接座夹具对准 右手拿螺丝2PCS 螺丝装入固定孔位 右手取电批 打螺丝1PCS 放电批 螺丝装入固定孔位 打螺丝3PCS 左手取出电池连接座放入托盘,右手放电批
动作类别
2.16 1.4
1.58 1.12 0.76 1.34 8.22 2.03 1.18 1.61 2.42
用时 改善后 宽放 总时间 存在问题&改善建议
1.15 1.9
2.69 1.15 3.91
3.1 0.68 1.17 1.22 3.05 2.24 1.79 1.05 1.34 2.23
2.2 1.72 1.12 2.61 0.99 1.03 1.25
1.7
1.33 1.04 0.78 1.02 0.91 1.09 1.36 2.49 1.71 1.02
存在问题&改善建议
减少1个电极和电极弹簧 建议装电极和电极弹簧改线外作业,现场为小批 量作业 操作困难,建议设计改善
工序5
动作1 动作2 动作3 动作4 动作5 动作6 动作7 动作8 动作9 动作10 动作11 动作12 动作13 动作14 动作16 动作17 动作18 动作19 动作20 动作21 动作22
工序3
工序4
工序工时拆分算法

工序工时拆分算法1.引言1.1 概述概述部分旨在介绍工序工时拆分算法的背景和基本概念,为读者提供对本文主题的初步了解。
在生产制造业中,工序工时拆分算法是一种重要的计算工具,用于将整体生产过程按照工序进行划分,并根据各个工序的特点和需求,合理地分配工时,以提高生产效率和优化生产资源利用率。
工序工时拆分算法的核心目标是实现对生产流程的细致拆分和有效规划,确保每个工序的时间和资源都能得到合理的安排,以实现更高效的生产结果。
通过对生产过程进行适当的拆分和分析,可以更好地控制整个生产环境,提高生产线的灵活性和生产能力,从而增强企业的竞争力和市场占有率。
本文将详细介绍工序工时拆分算法的定义、原理和步骤。
首先,将对工序工时拆分算法进行规范化的解释和界定,明确其主要目标和作用。
接着,将揭示算法背后的数学模型和计算原理,并详细介绍算法的具体步骤和实施方法。
通过深入分析和解释,读者将能够全面理解和掌握工序工时拆分算法的核心要点和基本操作。
通过本文的阅读,读者将能够深入了解工序工时拆分算法的定义和原理,掌握其实施步骤和应用场景。
同时,本文还将对该算法的优势和适用范围进行评估和探讨,并展望未来的研究方向。
通过应用这一算法,企业可以更加高效地进行生产流程规划和资源分配,从而提高生产效率、降低生产成本,提升企业的竞争力和可持续发展能力。
请继续阅读本文的后续章节,让我们一起探索工序工时拆分算法的奥秘和潜力。
1.2 文章结构文章结构部分可以描述整篇文章的组织结构和各个章节的内容概要。
以下是一个可能的描述:在本文中,我们将讨论关于工序工时拆分算法的内容。
文章分为引言、正文和结论三个部分。
引言部分主要包括概述、文章结构和目的三个小节。
首先,我们将简要介绍工序工时拆分算法,并指出它在实际应用中的重要性。
然后,我们将阐述文章的整体结构,以帮助读者更好地理解和导航文章内容。
最后,我们将明确文章的目的,即为读者提供一个全面的了解工序工时拆分算法的指南。
工时计算表格-自动计算

价格(含税、人工、设备等) 序号 项 目 产 元/小时 1 2 3 4 24 25 5 6 22 23 7 8 9 10 11 12 13 14 15 16 17 18 19 20 21 26 27 C6140以下车床 C6150以上车床 1.6m立车 2.5m立车 数控车床 数控立车 铣床 大立铣(包括铣削动力头) 立式加工中心 卧式加工中心 插床 外圆磨(1m以下) 外圆磨(1m以上) 内圆磨 平面磨 工具磨 牛头刨 小龙门刨 大龙门刨 卧镗 摇臂钻(φ 40以下) 摇臂钻(φ 40以上) 摇臂钻(φ 80) 立钻(φ 25以下) 立钻(φ 25以上) 线切割 激光切割 20 25 50 80 40 50 22 26 50 80 20 20 25 20 20 20 20 30 80 30 20 25 26 20 25 4 品 元/分钟 0.33 0.42 0.83 1.33 0.67 0.83 0.37 0.43 0.83 1.33 0.33 0.33 0.42 0.33 0.33 0.33 0.33 0.50 1.33 0.50 0.33 0.42 0.43 0.33 0.42 0.07 零星加工 元/小时 30 40 65 100 70 80 30 35 80 120 25 30 35 30 25 20 25 45 90 45 25 30 32 25 30 5 元/分钟 0.50 0.67 1.08 1.67 1.17 1.33 0.50 0.58 1.33 2.00 0.42 0.50 0.58 0.50 0.42 0.33 0.42 0.75 1.50 0.75 0.42 0.50 0.53 0.42 0.50 0.08
35 50 50 45 55 50 50 15 20
0.58 0.83 0.83 0.75 0.92 0.83 0.83 0.25 0.33
各工序工时计算

工序 分条
工位
动作分解
推小车 将料放于小车上
拉料
推小车(运送原料) 撕取气泡垫 割取 2 米首件用料 将小车放置于指定位置
清洁入料棒
清洁机台
清洁收料棒 清洁黑色胶轮 清洁不锈钢轮 清洁刀架 清洁地面 打开入料棒
上料 分条作业
聚光卷放置于入料棒 关闭入料棒 入料棒充气 穿聚光卷(将聚光卷穿入机台) 下刀 将吸尘管装入刀架 调整刀架角度 拉开收料轮 1 装滚筒 分条后聚光卷对边 关闭收料轮 收料轮充气 拉开收料轮 2 装滚筒 分条后聚光卷对边 关闭收料轮 收料轮充气 打开各控制开关 分条工作(聚光卷长 250 米) 关闭各控制开关
各工序工时计算工序工位动作分解工时统计s第一次第二次第三次第四次第五次推小车将料放于小车上推小车运送原料撕取气泡垫割取2米首件用料将小车放置于指定位置清洁机台清洁入料棒清洁收料棒清洁黑色胶轮清洁不锈钢轮清洁刀架清洁地面打开入料棒聚光卷放置于入料棒关闭入料棒入料棒充气穿聚光卷将聚光卷穿入机台下刀将吸尘管装入刀架调整刀架角度拉开收料轮1装滚筒分条后聚光卷对边关闭收料轮收料轮充气拉开收料轮2装滚筒分条后聚光卷对边关闭收料轮收料轮充气分条作业打开各控制开关分条工作聚光卷长250分条收尾关闭各控制开关放去上料棒之气体将料筒放置于指定地点调整刀架角度用胶带封分条后聚光卷接口填写报表填写分条记录卡放去收料棒中之气体打开收料棒拿下收料棒上之聚光卷将分条后之聚光卷放置于指定位置各工序工时计算工序工位动作分解工时统计s第一次第二次第三次第四次第五次裁切清洁机台清洁料棒清洁收料棒清洁绿色胶轮清洁不锈钢轮清洁刀模清洁机仓清洁面板清洁机表面清洁面板清洁机皮带清洁面板清洁机滚轮清洁静电消除器清洁地面推小车将料放于小车上推小车运送原料穿材料放于料棒上打开冲压机器机器设定放置刀模至刀模架材料送入机台材料效正调整参数调效刀模平整度裁切效果及角度确认废料缠绕首件检查及尺寸确认栽切作业打开清洁机控制开关栽切工作聚光卷长250换pet关闭暂停开关放去收pet棒之气体拿去料棒上料筒及pet将料筒及pet放置于指定地点拉新的petpet置于料棒上新pet与旧pet接合用胶带将pet接合穿pet过机器换旧petpet对接正常作业各工序工时计算工序工位动作分解工时统计s第一次第二次第三次第四次第五次贴合清洁机台清洁料轴清洁收料轴清洁上压滚轴清洁下压滚轴清洁机台装材料效正材料推小车运送原料穿材料放于料棒上打开冲压机器切片机器设定调试放置刀模至刀模架将吸尘管装入刀架下刀角度确认拉开收料轮首件检查首件尺寸确认栽切作业打开清洁机控制开关换pet关闭暂停开关放去后pet棒之气体将料筒放置于指定地点拉新的pet置于料棒上新pet与旧pet接合用胶带pet接口穿pet过机器换前pet拿下收料棒上之pet正常作业
标准工时及产能测算表

标准工时及产能测算表
表格编号:XX/QR-SC-014A 说明:本文档主要用于测算某一生产线各工序的标准工时以及标准产能,同时可以用来进行生产线工序平衡分析。
本表格对标准工时、瓶颈工时、产线平衡率、人均产能等关键数据的计算方式进行了详细说明,且在表格中以自动函数形式呈现。
(表格中内含自动计算公式,只需录入部分基本数据即可。
)
3.标准工时=实测时间(即表格中平均工时)×评比系数×(1+宽放率) 4.总标准工时=各工序标准工时之和;
5.瓶颈工时=所有工序中标准工时最大值(工位平衡时间最大值); 6.产线平衡率=总标准工时/(瓶颈工时×直接人力总数);
7.不平衡损失=瓶颈工时×直接人力总数-总标准工时; 8.损失率=(1-产线平衡率)*100%
9. 生产线每小时产能(最大产能)=3600/瓶颈工时; 10.每小时人均产能=3600/(瓶颈工时×直接人力总数)。
标准工时计算表
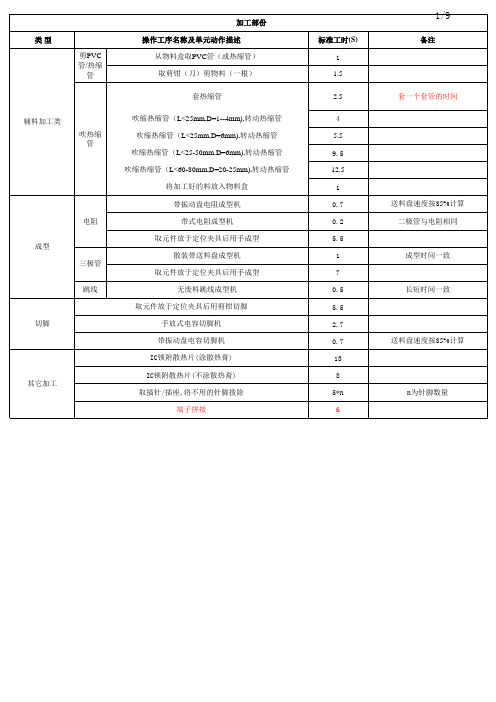
1.n为纸卡数量。2.使用周转箱时 不含此工时
装配部份 类型 操作工序名称及单元动作描述 从拉带(台面)取机,使热缩管处对于风筒口 吹缩热缩管(L<25mm,D=1--4mm),转动热缩管 吹缩热缩管(L<25mm,D=6mm),转动热缩管 吹套管 吹缩热缩管(L<25-50mm,D=6mm),转动热缩管 吹缩热缩管(L<60-80mm,D=20-25mm),转动热缩管 放机板到拉带(台面) 取机板放于台面 从物料盒取扎带到导线处 从物料盒取扎带穿过所扎的导线机板孔处 扎线类 从物料盒取扎带穿过所扎的导线再套胶柱 穿扎带孔,拉紧扎带 取剪钳将扎带剪断,且放回台面 放机板于拉带(台面) 取机板放于台面 取胶壶点红胶到一个螺丝头,并放回胶壶于台面 取胶壶点黄胶到电容处,并放回胶壶于台面 取胶壶点黄胶到线头(插座)处,并放回胶壶于台面 点胶类 取胶枪打熔胶固定一根导线,并放回胶枪于台面 取竹签沾混合胶点到按扭,放竹签于台面 取竹签沾快干胶点到胶件处,放竹签于台面 放机板于拉带(台面) 取机 放入夹具对位好 从物料盒取一粒螺丝放到电批嘴上 机牙 打螺丝,松开电批(L=4~8mm) 自攻牙 锁螺丝类 机牙 打螺丝,松开电批(L=9~19mm) 自攻牙 机牙 打螺丝,松开电批(L=20~30mm) 自攻牙 放机板于拉带(台面) 从拉带取机放于台面 取面片将保护蜡纸撕去并放入废料盒 贴面片 粘贴类 贴贴纸 贴贴纸,并将贴纸贴平 4.5 贴面片 取白布抺平面片,放回抺布 从物料盒(拉带)取贴纸 3 1 2 3.5 5.5 4 1.5 2.5 2.5 2 2 8.5 6 5 1 1 3 2 1.5 9.5 12.5 1 2 1.5 4 5.5 4 4.5 1 2 5 5.5 5 标准工时(S) 3 4 5.5
7/9
生产工序工时表
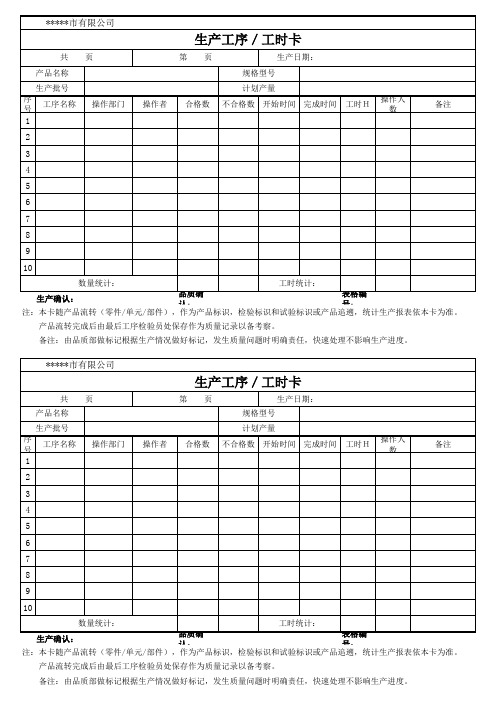
生产确认:认:号:
生产确认:认:号: 备注:由品质部做标记根据生产情况做好标记,发生质量问题时明确责任,快速处理不影响生产进度。
注:本卡随产品流转(零件/单元/部件),作为产品标识,检验标识和试验标识或产品追遡,统计生产报表依本卡为准。
产品流转完成后由最后工序检验员处保存作为质量记录以备考察。
备注:由品质部做标记根据生产情况做好标记,发生质量问题时明确责任,快速处理不影响生产进度。
注:本卡随产品流转(零件/单元/部件),作为产品标识,检验标识和试验标识或产品追遡,统计生产报表依本卡为准。
产品流转完成后由最后工序检验员处保存作为质量记录以备考察。
1工序工时计算表

a,定额为粗磨工 时; b,精磨工时=粗磨 工时(1-1/5);
磨外圆
φ 4-φ 30
>φ 35 <φ 30 磨内圆 φ 35-100 >φ 100 工具磨加工 平面 内圆靠端面 外圆靠端面 L<100 L>100
c,5件以上且5件 零件平铺不超磁 台加工面积时乘 以系数0.8,20件 以上且20件零件 平铺不超过磁台 加工面积时乘以 系数0.6。 出现零件很长但 磨削长度短的情 况时,在装夹不 困难的情况下用 磨削长度计算。 10件以上乘以系 数0.8。
台阶圆半径差<10
最低工时3分钟
注:1,平磨高度限高350mm;2,外圆带锥度加5分钟;内圆带锥加10分钟;3,Cr12和SKD材料磨内 孔乘以系数1.8;硬质合金乘以系数2;(D>φ 150,L>300)或(D<φ 15,L>300)乘以系数1.3;4, 公差值ห้องสมุดไป่ตู้0.005乘以系数1.3,公差值为0.002乘以系数2;5,磨削加工单个零件最小工时为10分钟 。
磨削工时定额计算表
加工内容 工件最大尺寸:20-100 工件最大尺寸:100-200 工件最大尺寸:200-300 磨单一平面 工件最大尺寸:300-400 工件最大尺寸:400-500 工件最大尺寸:500-600 工件最大尺寸:700-800 工件最大尺寸:6-15 工件最大尺寸:15-40 工件最大尺寸:45-55 磨六面 工件最大尺寸:60-100 工件最大尺寸:120-250 工件最大尺寸:270-350 应用范围 单件加工定额工时(分 钟) 6 8 12 15 20 30 50 15 18 22 25 30 30 40 45 55 10 备注
标准工时及产能计算表

班次:
产线:
产品型号:
日期:
目标效率:
90%
人均产能(pcs/hr):
7
平均工时(s):
15
不平衡损失(sec):
336
目标良率:
85%
工序最小工时(s):
10
瓶颈工时(s):
37
产线平衡率:
30%
工序(N o.)
作业内容
实测作业时间(sec/pc)
平均工时 宽放率
标准工时 人力配置 工位平衡时间 最大产能(p
15
9
尺寸检验+边缘检验
10
11
9
9
9
10
10
1.0
11
2
5
10
鐳刻
10
10
10
10 10
10
10
1.1
12
1
12
11
涂黑
10
9
10
9
10
10
10
1.1
12
1
12
12
背贴
25
22
24
23 24
24
10
1.1
29
3
10
13
成检
30
33
29
26 35
31
10
1.1
37
3
12
直接人力 (人)
班长
间接人力(人) 包装
和;8.各工序最高允许工时=标准产能/直接人力。最大产能=单位标准时间/瓶颈工序标准时间
整修
工作时间 (Hrs)
节拍
标准时间
预定效率 直通率 标准产能
标准工时及产能计算表

部门主管:
现场工序调整填写IE现场改善
标准工时 (s)
73.28 82.52 40.94 93.74 49.30 121.90 80.10 58.10 123.00 58.98 160.84 194.72 79.44 67.12 58.76 125.86 89.78 155.78 56.12 1338.28 .94
121 127 119 115
28
33
25
30
1195
1183 194.72
1189 1201 工序最小工时 (s):
不平衡损失
44.80 10% 53.20 10% 15.40 10% 63.40 10% 23.00 10% 89.00 10% 51.00 10% 31.00 10% 90.00 10% 31.80 10% 124.40 10% 155.20 10% 50.40 10% 39.20 10% 31.60 10% 92.60 10% 59.80 10% 119.80 10% 29.20 10% 1194.80 10%
7、人均产能=每小时产能/总人数
8、不平衡损失=瓶颈工时×总人数-各工序(每人)时间之和;
9、最大产能=单位标准时间/瓶颈工序标准时间。
线长/物料员
备注:维修员Fra bibliotek当生产均衡率<90%时,需对生产平衡率进行现场改善, 改善步骤:工位摄影 填写IE工序工时分析表 改善瓶颈工位的工序作业 效果表
制表人:
班组长:
产品名 称
工序 (No.)
工序名称
标准工时及产能计算表
型号/模块
线别
文件编号:
测试日期
实测作业时间(s) 实测1 实测2 实测3 实测4 实测5
8工作时间测算表MS-002-R040 成本分析
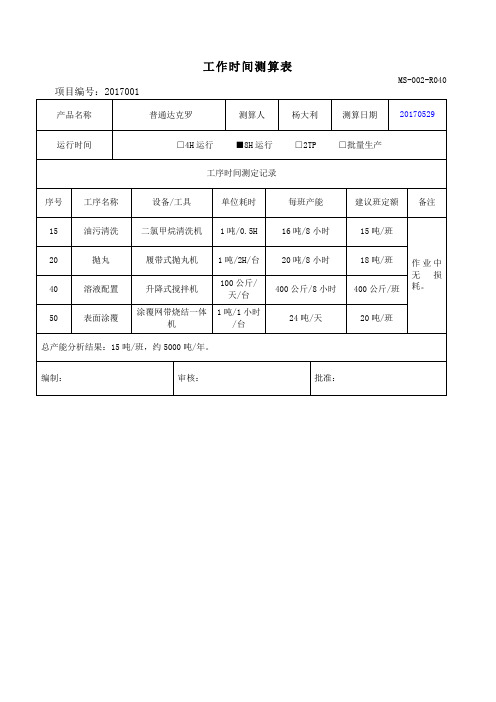
工作时间测算表MS-002-R040项目编号:2017001产品名称 普通达克罗测算人杨大利测算日期20170529运行时间□4H 运行 ■8H 运行 □2TP □批量生产工序时间测定记录序号 工序名称 设备/工具 单位耗时 每班产能 建议班定额 备注15 油污清洗 二氯甲烷清洗机 1吨/0.5H 16吨/8小时 15吨/班 作业中无损耗。
20 抛丸 履带式抛丸机 1吨/2H/台 20吨/8小时 18吨/班40 溶液配置 升降式搅拌机 100公斤/天/台 400公斤/8小时400公斤/班 50表面涂覆涂覆网带烧结一体机1吨/1小时/台24吨/天20吨/班总产能分析结果:15吨/班,约5000吨/年。
编制: 审核: 批准:产品生产成本分析表项目编号:MS-002-R041 产品名称普通达克罗规格500小时标准使用材料抗锈999 编制日期20170529 500小时生产成本消耗工序名称人工工资资源消耗单项合计备注材料406 406进货检验(金属件) 3.9 3.9进货检验(溶液) 6.8 6.8油污清洗18 23 41抛丸44 52 96溶液配置21 76 97表面涂覆36 228 264包装19 3 22管理费52 24.976.9财务费29 27.556.5销售费10 2.812.8税金132.6132.6其他27 60 87单位汇总成本266.7 1035.8 1032.5 无不良质量损失供货价1800利润空间497.5 利润率27.64%编制:审核:。
工时测定表
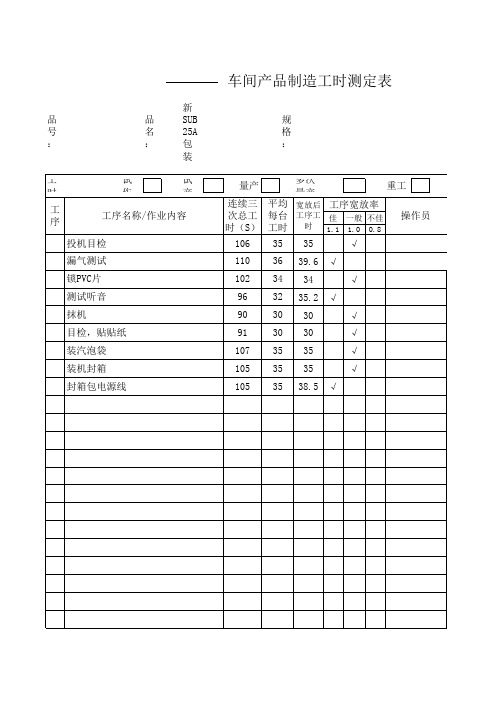
合计总工时:
工时平衡率(不得低于85%):
生技部经理:
车间经理:
测试者:
备注
瓶颈工时*工序数
35
√
操作员
110 36 39.6 √
102 34 34
√
96 32 35.2 √
90 30 30
√
91 30 30
√
107 35 35
√
105 35 35
√
105 35 38.5 √
宽放率
0.84736
PS:标准工时=瓶颈工时*工序数*生产线宽放(1.1); 工时平衡率=宽放后工序工时∑/瓶颈工时*工序数
品号:
车间产品制造工时测定表
品名: 新SUB25A包装
规格:
工时测定阶段: 试作
试产பைடு நூலகம்
工序
工序名称/作业内容
投机目检 漏气测试 锁PVC片 测试听音 抹机 目检,贴贴纸 装汽泡袋 装机封箱 封箱包电源线
量产
多次量产
重工
连续三 次总工 时(S)
106
平均 每台 工时
35
宽放后 工序宽放率
工序工 佳 一般 不佳 时 1.1 1.0 0.8
工分表格公式模板

工分表格公式模板
工分表格是用于记录工作分配和工时分配的表格,其具体内容和公式模板可能因不同的工作环境、行业、公司而异。
以下是一个简单的工分表格公式模板示例,您可以根据具体需要进行调整和扩充:
假设工分表格包括以下列:
1.任务名称(Task):描述工作的具体任务或项目。
2.工作人员(Worker):执行该任务的工作人员。
3.计划工时(Planned Hours):计划分配给任务的工时。
4.实际工时(Actual Hours):实际花费在任务上的工时。
5.工分(Work Points):用于衡量任务难度和工作量的工分。
在这个模板中,您可以使用以下公式:
•计划工时:简单地填写计划分配的工时。
•实际工时:由执行任务的工作人员记录实际花费的工时。
•工分:您可以根据任务的复杂性、重要性等因素来分配工分。
工分可能是一个相对主观的度量,可以根据具体情况进行调整。
在Excel或其他电子表格软件中,您可以使用公式来计算总体计划工时、总体实际工时以及总体工分。
例如:
•总体计划工时:SUM(计划工时范围)
•总体实际工时:SUM(实际工时范围)
•总体工分:SUM(工分范围)
这只是一个简单的模板示例,具体的工分表格可能需要根据具体的工作情境、公司政策和行业标准进行定制。