第1章 金属断裂
金属材料的韧性

第一章 金属的力学性能
第三节 韧性与疲劳强度
二、疲劳强度 循环应力:应力的大小和方向随时间作周期性的变化。
零件在循环应力作用下,常在远小于该材料的σb,甚 至小于σS强度的情况下发生断裂的现象称为金属的疲劳,
金属疲劳的判据是疲劳强度。
7
韧性是指金属在断裂前吸收变形能量的能力,可用来衡量金属材料抵抗冲击载荷能力。
1.摆锤式一次冲击试验 脆转变温度越低,材料的低温冲击性能越好。
1.摆锤式一次冲击试验
冲击吸收功:试样在冲击试验力一次作用下折断时所吸收的功(Ak)。
冲击吸功(Ak)。
第三节 韧性与疲劳强度
机械零件一般是在受多次小能量重复冲击后才破坏的。
第三节 韧性与疲劳强度 40Cr钢冲击吸收功测定试验
冲击吸收功:试样在冲击试验力一次作用下折断时所吸收的功(Ak)。 第三节 韧性与疲劳强度
韧性是指金属在断裂前吸收变形能量的能力,可用来衡量金属材料抵抗冲击载荷能力。
一、韧性 韧性的判据通过冲击试验来测定。
一、韧性 1.摆锤式一次冲击试验
冲击吸收功 Ak 与温度有 关。由左图可知,Ak 随温度降
低而减少,在某一温度区域,
Ak急剧变化,此温度区域称为
韧脆转变温度。脆转变温度越 低,材料的低温冲击性能越好。
5
第一章 金属的力学性能
第三节 韧性与疲劳强度
一、韧性 2.小能量多次冲击试验简介 金属材料抵抗小能量多次冲击的能力叫做多冲抗力。 机械零件一般是在受多次小能量重复冲击后才破坏的。 多冲抗力可用一定冲击能量下冲断周次N表示。 试验证明,材料的多冲抗力取决于材料强度与韧性的综 合力学性能,冲击能量高时,主要取决于材料的韧性;冲击 能量低时,主要取决于强度。
1第一章 零件的失效

摩擦分类 形成良好润滑的措施
磨损分类 减少磨损的途径 减轻腐蚀的措施
一、零件失效的含义及基本形式 1.含义: 零部件失去原设计所规定的功能称为失效。失效不仅 是指完全丧失原定功能,而且还包含功能降低和有严 重损伤或隐患、继续使用会失去可靠性和安全性的零 部件。 2.失效的基本形式 零部件按失效模式分类可分为磨损、疲劳断裂、 变形、腐蚀等; 一个零件可能同时存在几种失效模式或失效机理。
4.混合摩擦
• 当动压润滑条件不具备,且边界膜遭破坏时, 就会出现液体摩擦、边界摩擦和干摩擦同时存 在的现象,这种摩擦状态称为混合摩擦。
三、减少摩擦的有效措施—润滑 1.润滑剂及主要性能
(1)润滑油:有机油、矿物油、合成油 性能指标:1)粘度 2)油性 3)凝点 4)闪点 和燃点 5)极压性能 6)氧化稳定性 (2)润滑脂: 钙基润滑脂、钠基润滑脂、锂基润滑 脂 性能指标: 1)针入度 2)滴点 3)安定性 (3)固体润滑剂 :石墨、二硫化钼、氮化硼 蜡、 聚氟乙烯、 酚醛树脂
• 2、按断口的微观特征分 • 晶间断裂 • 穿晶断裂 • 3、按零件断裂前所承受的载荷性质分 一次加载断裂 疲劳断裂
二、疲劳断裂
特点:零件破坏时的应力远低于零件材料 的抗拉强度,甚至低于材料的屈服强度 表现:脆性断裂
疲劳断裂失效机理: 金属零件疲劳断裂实质上是 一个累计损伤过程。大体可划分 为滑移、裂纹成核、微观裂纹扩 展、宏观裂纹扩展、最终断裂几 个过程。
(4)腐蚀磨损
形成:摩擦表面与酸、碱、盐、接触发生腐蚀, 在有相对运动时表面金属剥落形成腐蚀磨损。 影响因素:环境、润滑油的腐蚀性。
分类:氧化磨损、微动磨损、化学腐蚀磨损
①氧化磨损
氧化磨损是金属与空气中的氧作用形成氧化膜, 氧化膜被磨损形成氧化磨损。是最常见的一种 磨损形式,曲轴轴颈、气缸、活塞销、齿轮啮 合表面、滚珠或滚柱轴承等零件都会产生氧化 磨损。与其它磨损类型相比,氧化磨损具有最 小的磨损速度,有时氧化膜还能起到保护作用; 影响因素:影响氧化磨损的因素有滑动速度、 接触载荷、氧化膜的硬度、介质中的含氧量、 润滑条件以及材料性能等。
第1章 金属断裂

解理断的过程(三各阶段):
a) 塑性变形形成微裂纹; b) 裂纹在同一个晶粒内初期长大; c) 裂纹越过晶界向相邻晶粒扩展。
a)
b)
c)
2. 柯垂耳位错反应理论 (解理裂纹)
在α-Fe (bcc)中:
滑移面(110),滑移方向[111]。 右图中两个正交滑移面(101)与 (101)相交于解理面(001)中的 [010]轴线。 若沿(101)和(101)各有柏 氏矢量为a/2[111]和a/2[111]的平行 位错列在交叉线上相遇,即可形成 新位错a[001],其反应式如下:
1)弹性体裂纹失稳扩展判据 无限大板拉紧再固定拉应力σ,单位厚度 主要研究有2c长裂纹后强度情况
① 开长2c裂纹能量情况 a. 弹性能减少量(能量释放率)
c 2 2 We E 2 2 (1 2 ) c E 平面应力 平面应变
b. 表面能增加 Ws=(2c· 1· γ)×2=4cγ ② 裂纹扩展 2c→2c+2dc a. 扩展单位面积释放能量(弹性能变化)
舌状花样形成方式: 解理裂纹沿孪晶界扩展留下舌头状凹台或凸台。
另外:还有准解理(是解 理而非解理)。特点:断 裂路径不再与晶粒位相有 关,不再沿一定的晶体学 平面,主要与细小碳化物 质量有关。(撕裂棱较多,往
往有一定的塑性)
解理:一定 晶体内平面 准解理:不一定 与解理的区别 裂纹源 解理:晶界 准解理:第二相
x E 。 E E a0 → th 2 a0
→
th 2 πa0 E
2)能量平衡法求σth与E关系
① σth与拉断外力做功W外关系
W外 =
第1章金属材料的性能与结构
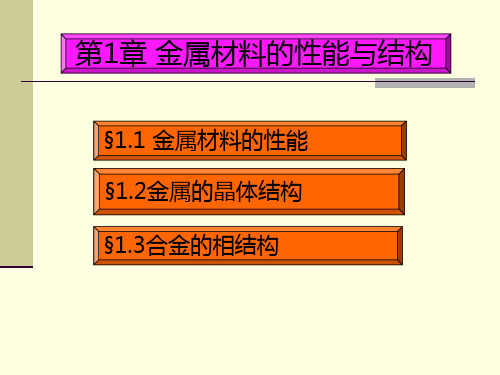
1.晶体结构的基本知识
由于晶体原子排列呈周期性,因此, 可以从晶格中选取一个能够完全反应晶 格中原子排列特征的最小的几何单元, 来分析晶体中原子排列的规律性,这个 最小的几何单元称为晶胞 。
1.晶体结构的基本知识
晶格
晶胞
1.晶体结构的基本知识
Z c
α
β a
X a γ
b
Y
图1-9 晶胞的晶格常数和轴间夹角的表示法
()
MPa
b
s
e
b
s
e
应变(%)
图1-2 单轴拉伸曲线示意图
2、金属的力学性能的指标一般有哪些? 怎样获得这些指标? 塑性是指金属材料在外力作用下,发生 永久变形而不破坏的能力。在工程中常用 塑性指标来判断金属材料的可成形性,常 用伸长率和断面收缩率来表征。 伸长率指试样在拉伸过程中,拉断标距长 度的延长值(见图1-1)与原始标距长度的 比值,即:
1.2.1 金属
在固态金属中,吸引力与排斥力的大 小以及它们的结合能量都随原子间距离 的变化而发生改变。这样就存在一个原 子间距,此时原子间相互排斥力与吸引 力相等,原子处于稳定平衡状态,该原 子间距即为平衡距离,这时原子之间的 结合能为最低,系统此时最稳定。
1.2.2 金属的晶体结构
1.晶体结构的基本知识 2. 常见金属的晶体结构 3. 晶面指数和晶向指数
第1章 金属材料的性能与结构
§1.1 金属材料的性能 §1.2金属的晶体结构
§1.3合金的相结构
1.1 金属材料的性能
金属材料是金属元素或以金属元素为 主构成的具有金属特性的材料的统称。 金属材料一般分为:黑色金属和有色 金属,黑色金属有钢、铸铁、铬、锰; 其他的金属,如铝、镁、铜、锌等及其 合金都为有色金属。 金属材料的性能包括:力学性能、物 理化学性能、工艺性能、经济性能等。
工程材料与机械制造基础第二版课后练习题含答案

工程材料与机械制造基础第二版课后练习题含答案第一章金属材料选择题1.金属的基本结构单位是()。
A. 原子 B. 分子 C. 离子 D. 高分子2.金属的导电性好,是因为()。
A. 金属原子共用周围电子形成了一个电子云 B. 金属原子之间的原子序数很大 C. 金属原子之间的距离很远D. 金属原子的原子半径很大3.现代材料科学的研究表明,金属的显微结构主要包括()两种结构。
A. 晶体和非晶体B. 多晶和单晶C. 非晶体和薄层结构D. 单晶和二晶轴4.在常温下铁、钨属于()。
A. 非晶态材料 B. 晶态材料 C. 二相材料 D. 单晶体材料5.劈铅试验所测试的是材料()。
A. 塑性 B. 韧性 C. 硬度 D. 强度简答题1.什么是金属材料?金属材料具有哪些特点?2.金属的结晶状态有哪些?请简述它们的特点。
3.介绍一下金属断裂的过程。
4.解释一下热处理和强化的含义。
答案选择题:1. A 2. A 3. B 4. B 5. D简答题:1.金属材料是一类以金属元素为主要组成成分的工程材料,具有一系列特点,如:密度大,强度高,塑性良好,导电导热性好等。
同时,也具有一些不足之处,如:易受腐蚀,疲劳寿命相对较短等。
2.金属的结晶状态主要有三种,分别为单晶、多晶以及非晶态。
单晶指的是具有完整晶格结构的材料,其具有优异的物理性能,但制造成本较高。
而多晶则指晶粒较小、有多个晶粒构成的材料。
这类材料具有低成本、高韧性等特点。
非晶态指材料的内部没有固定的原子排列方式,呈无序状态。
这类材料具有高强度、低应力腐蚀等特点。
3.金属断裂的过程主要包括两个阶段,分别为起始裂纹形成阶段和扩展裂纹阶段。
在起始裂纹形成阶段,由于外力作用,材料内部会出现微小的损伤,如缺陷、气孔等,这些损伤会在外力作用下产生应力集中。
当应力集中超过材料强度极限时,就会出现一条裂纹。
在扩展裂纹阶段,裂纹会不断扩大,细微损伤逐渐聚集,最终导致材料破裂。
第一章 材料在静载下的力学行为3(4.1金属的断裂)
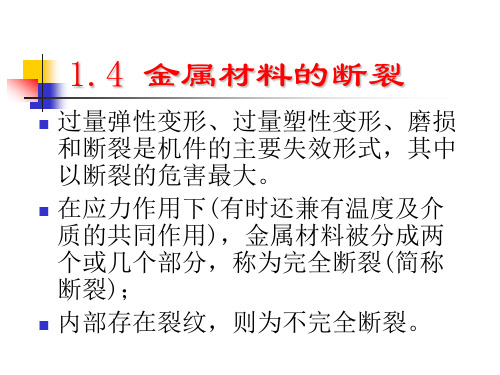
沿晶断裂的断口形貌呈冰糖状,有时也称“萘状断 口”,上左图为18CrNiWA钢的冰糖状断口。 如晶粒很细小,则肉眼无法辨认出冰糖状形貌,此 时断口一般呈晶粒状,颜色较纤维状断口明亮,但 比纯脆性断口要灰暗些。 穿晶断裂和沿晶断裂有时可以混合发生。
剪切断裂与解理断裂
(1)剪切断裂是金属材料在切应力作用下沿滑 移面分离而造成的滑移面分离断裂,其中又 分滑断(纯剪切断裂)和微孔聚集型断裂。
(2)解理断裂
解理断裂是金属材料在一定条件下(如低温),当外 加正应力达到一定数值后,以极快速率沿一定晶体 学平面产生的穿晶断裂,因与大理石断裂类似,故 称此种晶体学平面为解理面。 一般在体心立方、密排六方金属中发生,而面心立 方金属只在特殊情况下才发生。 解理面一般是低指数晶面或裸露后表面能最低的晶 面。 解理断裂总是脆性断裂,但有时在解理断裂前也显 示一定的塑性变形,所以解理断裂与脆性断裂不是 同义词,解理断裂指断裂机理而言,脆性断裂则指 断裂的宏观性态。
1.甄纳-斯特罗位错塞积理论
在滑移面上的切应力作用下, 刃型位错在晶界前受阻并互 相靠近形成位错塞积,如果 塞积头处的应力集中不能为 塑性变形所松弛,当切应力 达到某一临界值时,塞积头 处的最大拉应力能够等于材 料理论断裂强度而形成高nb、 长为r的楔形裂纹。
解理裂纹的形成,并不意味着裂纹将迅速扩 展而导致金属材料完全断裂。 柯垂耳用能量分析法推导出解理裂纹扩展的 临界条件为
放射区的形成过程
纤维区中裂纹扩展是很慢的,当其达到临界尺寸后 就快速扩展而形成放射区。 放射区有放射线花样特征。放射线平行于裂纹扩展 方向而垂直于裂纹前端(每一瞬间)的轮廓线,并逆 指向裂纹源。 撕裂时塑性变形量越大,则放射线越粗。对于几乎 不产生塑性变形的极脆材料,放射线消失。 温度降低或材料强度增加,由于塑性降低,放射线 由粗变细乃至消失。
材料断口分析(前言、第一章)
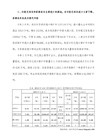
29
脆断的特点:
1、断裂时承受的工作应力很低,一般低于σ0.2 2、裂纹源总是从内部的宏观缺陷处开始 3、T↓,脆断倾向↑
4、断口平齐、光亮,且与正应力垂直,断口上常
呈人字纹或放射性花样
30
2、断裂路径
沿晶断裂:裂纹萌生和发展是在晶界处发生的过程 穿晶断裂:裂纹萌生和发展是在晶粒内部处发生的过程
m sin
其中:
2 x
σm理论断裂强度
x为原子偏离平衡位置的位移x=a-a0 当 x很小时, sinx=x, 则:
2 x m
(1)
51
当 x很小时,ε和σ之间仍符合虎克定律,则:
x E E a0
由(1)、(2)式可得:
( 2)
E m 2 a0
3、位错墙侧移理论
4、位错交滑移成核理论 5、同号刃位错聚集成核理论
44
位错塞积理论—stroh理论
问题:①裂纹形成只与外加切应力有关,而与应力 状态无关,与实际不符; ②未考虑第二相粒子的影响。
45
位错反应理论—cottrel理论
问题:未考虑材料中的第二相粒子,因它们
的形状和分布影响断裂性质
46
根据断口三要素可以判断裂纹源的位置及宏观裂纹扩展方向 裂纹源的确定: ①利用纤维区,通常情况裂源位于纤维区的中心部位,因此找到纤维 区的位置就找到了裂源的位置; ②利用放射区形貌特征,一般情况下,放射条纹的收敛处为裂源位 置; ③根据剪切唇形貌特征来判断,通常情况下裂纹处无剪切唇形貌特 征, 而裂源在材料表面上萌生。
56
令
d (u1 u2 ) 0 da
d (4a
即 可得
2 a 2
金属工艺学第一章金属材料性能ppt课件.ppt
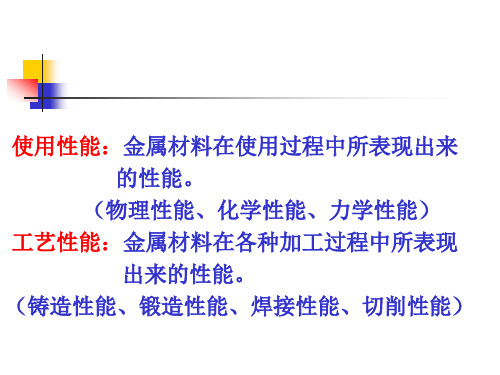
拉伸试验
强度:材料在外力作用下抵抗永久变形和 断裂的能力。
塑性:材料在外力作用下产生永久变形而 不破坏的能力。
硬度
硬度:金属材料抵抗其他更硬物体压入表面的 能力,衡量材料的软硬程度。
硬度试验方法很多,机械工业普遍采用 压入法来测定硬度,压入法又分为布氏硬度、 洛氏硬度、维氏硬度等。
布氏硬度是用单位压痕面积的力作 为布氏硬度值的计量,符号HBS、HBW
洛氏硬度是用压痕深度作为洛氏 硬度值的计量即,符号HR
维氏硬度也是以单位压痕面积的力作为 硬度值计量。试验力较小,压头是锥面夹角 为136°的金刚石正四棱锥体,维氏硬度用符 号HV表示。
冲击韧性和疲劳强度
冲击韧性:冲击载荷下材料抵抗变形和断 裂的能力。
疲劳强度:金属材料在无数次重复或交变 载荷作用下而不致引起断裂的 最大应力。
使用性能:金属材料在使用过程中所表现出来 的性能。
(物理性能、化学性能、力学性能) 工艺性能:金属材料在各种加工过程中所表现
出来的性能。 (铸造性能、锻造性能、焊接性能、切削性能)
1. 金属材料的力学性能
力学性能:指金属材料在外力(载荷)作用下 所表现出的抵抗变形和破坏的能力。
强度、塑性、硬度、冲击韧度和疲劳强度等。 外力形式:拉伸、压缩、弯曲、剪切、扭转等。 载荷形式:静载荷、冲击载荷、交变载荷等。
2.金属材料物理性能和化学性能
物理性能:密度、熔点、导热性、导电 性金属材料的工艺性能(略)
工艺性能:铸造性能、锻造性能、 焊接性能、切削加工性能
大连理工大学精品课程-材料力学性能-第一章-金属断裂(2)

解理面(001) 扩展方向[110]
挛晶面(112) 挛晶方向[111]
27
图1-67 解理舌形成示意图
2020年7月26日 第一章 单向静载下材料的力学性能 星期日 准解理
材料中弥散细小的第二
相影响裂纹的形成与扩展,
使裂纹难于严格按一定晶体
学平面扩展,断裂路径不再 与晶粒位向有关,主要与细 小碳化物质点有关。其微观 特征似解理河流但又非真正 28 解理,故称准解理。
24
图1-64 河流通过大角度 晶界时的扇形花样
2020年7月26日 第一章 单向静载下材料的力学性能 星期日
当解理裂纹通过扭转晶界时,因晶界两侧晶
体以边界为公共面转动一个角度,使两侧解理裂
纹存在位向差,故裂纹不能直接越过晶界而必须
重新成核,裂纹将沿若干组
新的相互平行的解理面扩展
而使台阶激增,形成为数众
1
m
E s
a0
2
s——表面能;
a0——原子面间距; E——弹性模量
1
1
形成裂纹的力学条件为: (f
i )
d
2
Es 2
2r a0
可得: f i 2Er s
da0
f——形成裂纹所需
的切应力;
7
2020年7月26日 第一章 单向静载下材料的力学性能 星期日 (二)、解理裂纹的扩展 以上所述主要涉及解理裂纹的形成,并不意味 着由此形成的裂纹将迅速扩展而导致材料断裂。解 理断裂过程包括以下三个阶段:塑性变形形成裂 纹;裂纹在同一晶粒内初期长大;裂纹越过晶界向 相邻晶粒扩展。
多的 “河流”,这与通过大角
度晶界的情况类似。
25
图1-65 河流花样通过扭转晶界
金属材料的力学性能

第1章 金属材料的力学性能
二、洛氏硬度 HR ( Rockwll hardness ) 1、测量原理
10HRC≈HBS
洛氏硬度测试示意图
第1章 金属材料的力学性能
三、维氏硬度 HV
1、测量原理:
第1章 金属材料的力学性能
2、表示方法: 符号HV。标注时,硬度值写在符号之前,如666HV
3、特点: 维氏硬度试验的测试精度较高,测试的硬度范围大,被测试样的厚度 或表面深度几乎不受限制(如能测很薄的工件、渗氮层、金属镀层等)。 但是, 维氏硬度试验操作不够简便,试样表面质量要求较高,故在生 产现场很少使用。
抗拉强度为设计机械零件和选材的主要依据。
σe σs σb
第1章 金属材料的力学性能
(二)疲劳强度
工程上规定,材料经无数次重复循环(交变)载荷作用而不发生 断裂的最大应力称为疲劳强度。表示材料经无数次交变载荷作用而 不致引起断裂的最大应力值。
钢材的循环次数一般取 N = 107 有色金属的循环次数一般取 N = 108
主要指标: 强度、塑性、冲击韧性和硬度。
第1章 金属材料的力学性能
1.1 强度
按照载荷的性质,金属材料的强度有静强度、疲劳强度和 冲击强度。一般意义上的强度是指静强度。
(一)强度 一、拉伸试验
1.拉伸试样 标准试样(按GB/T6397-1986规定) 常用圆截面拉伸试样 : 长试样:L0=10d0 短试样:L0=5d0
钢铁材料的疲劳曲线
第1章 金属材料的力学性能
疲劳的危害:
金属断口分析

《金属断口分析》第一章金属的断裂第一节断裂分类失效形式:过大的弹性变形;塑性形变;断裂;材料变化。
其中危害最大的是破裂特别是断裂。
通过对断口形貌特征进行分析从而获得金属断裂机理。
一,宏观脆性断裂与延伸断裂从宏观上看,断裂分为脆性断裂和延性断裂脆性断裂指以材料表面、内部的缺陷或是微裂纹为源,在较低的应力水平下(一般不超过材料的屈服强度),在无塑性变形或只有微小塑性变形下裂纹急速扩展。
在多晶体中,断裂时沿着各个晶体的内部解理面产生,由于材料的各个晶体及解理面方向是变化的,因此断裂表面在外观上呈现粒状。
脆性断裂主要沿着晶界产生,称为晶间断裂。
其断口平齐。
延性断裂是在较大的塑性变形产生的断裂。
它是由于断裂缓慢扩展而造成的。
其断口表面为无光泽的纤维状。
延性断裂经过局部的颈缩,颈缩部位产生分散的空穴,小空穴不断增加和扩大聚合成微裂纹。
二,穿晶断裂和沿晶断裂依据裂纹扩展途径不同,断裂分为穿晶断裂和沿晶断裂,或二者兼有。
穿晶断裂是指裂纹穿过晶体内部的途径发生的;穿晶断裂可能是延性的,也可能是脆性的。
若断裂是穿过晶体沿解理面断开,但无明显塑性变形为脆性断裂。
若穿晶断裂时出现塑性变形则为延性断裂。
沿晶断裂指以裂纹沿着晶界扩展的方式进行。
沿晶断裂多为脆性断裂,,但也有延性的。
应力腐蚀断口,氢脆断口都是沿晶断裂的脆性断裂。
三,韧窝、解理、准解理、沿晶和疲劳断裂这主要是根据微观断裂机制上而言四,正断和切断根据断面的宏观取向与最大正应力交角,断裂方式分为正断和切断正断性断裂是指宏观断面的取向与最大正应力相垂直,如解理断裂切断性断裂指宏观断面的取向与最大切应力方向相一致,而与最大正应力成45度第二节材料的韧性与断裂力学第二章断口分析技术第一节裂纹源位置的判别进行断裂分析首要任务是从碎片中找出最初的断裂部分,然后在其上找出裂纹源,逐步分析产生断裂的原因和性质。
寻找裂纹源的方法:1.T型法如果有两条相交的裂纹构成“T”型,通常横穿整个试样的裂纹为主裂纹,另一条为二次裂纹,2.分叉法样品断裂中,产生许多分叉,裂纹分叉的方向为裂纹扩展方向,扩展的反方向为裂源位置。
第一章 金属材料的力学性能

Fb σb= S0
四、塑性的衡量(塑性指标):伸长率 δ和断面收缩率 Ψ 塑性的衡量(塑性指标):伸长率 和断面收缩率 ):
1)伸长率( δ ) )伸长率( 伸长率是指试样拉断 后标距增长量与原始 标距的百分比,即: 标距的百分比,
lk-l0 δ=
×100%
l0
lk——试样拉断后的标距 试样拉断后的标距,mm; 试样拉断后的标距 l0——试样的原始标距 。 试样的原始标距,mm。 试样的原始标距
第一章 金属材料及热处理基础知识
应用于各种工程领域中的材料,如在机械工业中,建筑及桥 应用于各种工程领域中的材料,如在机械工业中,建筑及桥 于各种工程领域中的材料 等等, 统称为工程材料。 梁中,等等,——统称为工程材料。 统称为工程材料 其中用来制造各种机电产品的材料 用来制造各种机电产品的材料, 称为机械工程材料 其中用来制造各种机电产品的材料,——称为机械工程材料 称为机械工程材料. 主要包括: 主要包括: 1)金属材料:钢,铸铁,铜及铜合金,等等。 铸铁,铜及铜合金,等等。 )金属材料: 2)非金属材料:塑料,橡胶,工业陶瓷,等等。 )非金属材料:塑料,橡胶,工业陶瓷,等等。 3)复合材料:由两种或两种以上性质不同的材料复合而成的 )复合材料: 多相材料。 多相材料。 金属材料是制造机器的最主要材料。 金属材料是制造机器的最主要材料。 是制造机器的最主要材料 1、金属材料按含金属元素数量的多少分为: 、金属材料按含金属元素数量的多少分为: 1)纯金属 一种金属 一种金属). )纯金属(一种金属 2)合金(以一种金属为基 其他金属或非金属) 其他金属或非金属) )合金(以一种金属为基+其他金属或非金属
刚度、强度、 第一节 刚度、强度、塑性
刚度、强度、弹性和塑性是根据拉伸试验测定出 塑性是根据拉伸试验 刚度、强度、弹性和塑性是根据拉伸试验测定出 来的。 来的。 一、拉伸试验与拉伸曲线 1、拉伸试样 试验前在试棒上打出标距 试验前在试棒上打出标距 按国标规定标准拉伸试样可分为: 按国标规定标准拉伸试样可分为: 板形试样: 1) 板形试样:原材料为板材或带材 圆形试样:长试样L 短试样L 2) 圆形试样:长试样L0=10d0,短试样L0=5d0 其中: 为试样标距, 其中:L0为试样标距,d0为试样直径
束德林主编工程材料力学性能第三版 第1章

图1-21 冰糖状断口 (SEM)
(三) 纯剪切断裂与微孔聚集型断裂、解理断裂
(1)剪切断裂 剪切断裂是金属材料在切应力作用下,沿滑移面分离而造成的滑移面分离
断裂,其中又分纯剪切断裂和微孔聚集型断裂。
(2)解理断裂 解理断裂是金属材料在一定条件下(如低温),当外加正应力达到--定数值后,
五、缩颈现象和抗拉强度
(一)缩颈的意义 (二)缩颈判据 (三)确定缩颈点及颈部应力的修正 (四)抗拉强度
(三)确定缩颈点及颈部应力的修正
' zh
(1
zh
2R ) ln(1
a
)
a
2R
' zh
' zh
——修正后的真实应力
zh ——颈部轴向真实应力
R ——颈部轮廓线曲率半径
a ——颈部最小截面半径
一、断裂的类型 (一) 韧性断裂与脆性断裂 (二) 穿晶断裂与沿晶断裂 (三) 纯剪切断裂与微孔聚集型断裂与解理断裂
(一)韧性断裂与脆性断裂
韧性断裂是金属材料断裂前产 生明显宏观塑性变形的断裂,这种 断裂有一个缓慢的撕裂过程,在裂 纹扩展过程中不断地消耗能量。
中、低强度钢的光滑圆柱试样 在室温下的静拉伸断裂是典型的韧 性断裂,其宏观断口呈杯锥形,由 纤维区、放射区和剪切唇三个区域 组成,即所谓的断口特征三要素。
冶金质量的好坏,故可用以评定材料质量。 金属材料的塑性常与其强度性能有关。
七、屈强比
材料屈强比值的大小,反映了材料均匀塑形变形的能力和应 变硬化性能,对材料冷成型加工具有重要意义。
八、静力韧度
韧度是度量材料韧性的力学性能指标,其中又分静力韧度、冲击韧度和断裂 韧度。
第01章 单向静拉伸力学性能

37
经典弹性理论:变形完全回复;单值对应;线性关系。
滞弹性体的应力与应变关系仍然是 线性的。它与非弹性体有明显区别。
38
弹性体与滞弹性体区别:
弹性体:每一 σ 值准确对应于一个 ε 值,即 σ 、ε 是 唯一的;
滞弹性体:每个 σ 值对应两个 ε 值,其中之一属加载, 另一则属卸载条件下的 ε 值。
真实应力-应变曲线:
定义式 : σzh = F/S 定义式: εzh = ΔL/L
22
(1)在Ⅰ区,为直线,真应力与真应变成直线关系。 (2)在Ⅱ区,为均匀塑性变形阶段,是向下弯曲的曲线,
遵循Hollomon关系式: σzh =K(εzh)n
K,n均为材料常数;n为形变强化指数;K为硬化系数 一般金属材料,1>n>0 σ= Eε
⑴ 金属原子的种类(非过渡族、过渡族) ⑵ 晶体结构 (单晶体和多晶体) (3) 冷变形(织构) ⑷ 显微组织(热处理后) (5)温度 (6)加载速率 (7)相变
34
四、弹性比功
1、比例极限 2、弹性极限 3、弹性比功(弹性比能、应变比能)
物理意义:吸收弹性变形功的能力。 几何意义:应力-应变曲线上弹性阶段下的 面积。 计算式:ae =σeεe/2 =σe2/2E 用途:弹簧
σ 和 ε 的关系表现为一个椭圆。
3、滞弹性的内耗
39
(1)金属的内耗—金属材料在交变载荷下吸收 不可逆变形功的能力。
在机械振动过程中由于滞弹性造成震动能量 损耗,机械能散发为热能。
滞弹性回线中所包围的 面积代表振动一周所产生的 能量损耗,回线面积越大, 则能量损耗也越大。
40 (2)产生内耗的原因:
(1)最广泛使用的力学性能检测手段。 (2)试验的应力状态、加载速率、温度等都是
工程断裂力学第一章 (1)

怎样冶炼、加工和热处理可以得到最佳效果?
前五个问题可以用断裂力学
的方法来解决;后面四个问题则 属于材料或金属学的领域。因此, 断裂是与力学、材料和工程应用 有关的问题。应综合力学、材料 学和工程应用等方面着手研究。
解决断裂问题的思路
为解决上面所提的工程问题和材料问题,对于含裂纹的受力 机械零件或构件,必须先找到一个能表征裂纹端点区应力应变场 强度(intensity)的参量,就象应力可以作为裂纹不存在时的表 征参量一样。
就在这种背景下诞生了。从上世纪五十年代中期以来,
在工程方面,已广泛应用于宇航、航空、海洋、兵器、
断裂力学的关键问题(一)
1.多小的裂纹或缺陷是允许存在的,即此小裂纹或缺陷不会在预定
的服役期间发展成断裂时的大裂纹? 2.多大的裂纹就可能发生断裂,即用什么判据判断断裂发生的时机?
3.从允许存在的小裂纹扩展到断裂时的大裂纹需要多长时间,即机
应力应变场强度的参量达到临界值时,就要发生断裂。
这个发生断裂的临界值很可能是材料常数,它既可表征 材料抵抗断裂的性能,亦可用来衡量材料质量的优劣。
影响断裂的两大因素
载荷大小和裂纹长度
考虑含有一条宏观裂纹的 构件,随着服役时间后使 用次数的增加,裂纹总是 愈来愈长。在工作载荷较 高时,比较短的裂纹就有 可能发生断裂;在工作载 荷较低时,比较长的裂纹 才会带来危险。这表明表 征裂端区应力变场强度的 参量与载荷大小和裂纹长 短有关,甚至可能与构件 的几何形状有关。
裂纹开始扩展的启裂点与裂纹扩展失去控制的失稳断裂点非常接
近。裂纹扩展后,载荷即迅速下降,断裂过程很快就结束了。 韧性断裂的载荷与变形量关系如图所示,有较长的非线性阶
段,启裂后,裂纹可以缓慢地扩展一段时间,除非变形量增到失
断裂与断口分析(前言、第一章)

2、韧性断裂(滑移分离)
3、解理断裂(准解理断裂) 4、沿晶断裂
5、环境断裂(SCC、氢脆、蠕变等)
6、疲劳断裂 7、工程实际断裂分析(材料加工、P/M)
8、断口分析技术
8
第一章
§1 断裂分类
金属的断裂
§2 断口三要素 §3 断裂过程 §4 断裂强度
9
§1
Hale Waihona Puke 断裂分类1、断裂性质 塑性断裂:断裂前发生较大的塑性变形,断口呈暗灰色纤维状
3、T↓,脆断倾向↑
4、断口平齐、光亮,且与正应力垂直,断口上常呈人 字纹或放射性花样
11
2、断裂路径
沿晶断裂:裂纹萌生和发展是在晶界处发生的过程 穿晶断裂:裂纹萌生和发展是在晶粒内部处发生的过程
穿晶断裂可以是韧性的(微孔聚集型断裂),也可以是脆性的(解理 断裂、穿晶应力腐蚀断裂) 沿晶断裂多为脆断(氢脆断裂),少数为韧性断裂(高温蠕变断裂)
解理断裂:这是一种在正应力作用下所产生的穿晶断裂,通常断裂面是严格 沿一定的晶面(解理面)而分离。
bcc、hcp在低温、冲击载荷作用下常发生解理断裂
注意:通常解理断裂总是脆性断裂,但脆性断裂不一定是解理断裂
14
剪切断裂:在切应力作用下,沿滑移面滑移而造成的滑
移面分离的断裂。它包括:
滑断(纯剪切型断裂)——纯金属、单晶体金属。断口呈锋利楔形或刀尖形 微孔聚集型断裂——大多数钢铁材料、有色金属材料
15
5、其它
•应力状态:静载断裂(拉伸、剪切、扭转)
动载断裂(冲击、疲劳)
•裂纹扩展速度:快速断裂(拉伸、冲击) 缓慢断裂(疲劳) 延迟断裂(SCC、氢脆) •断裂能量:低能断裂(结晶学断裂) 中能断裂 高能断裂(非结晶学断裂)
哈工大断裂力学讲义第一章
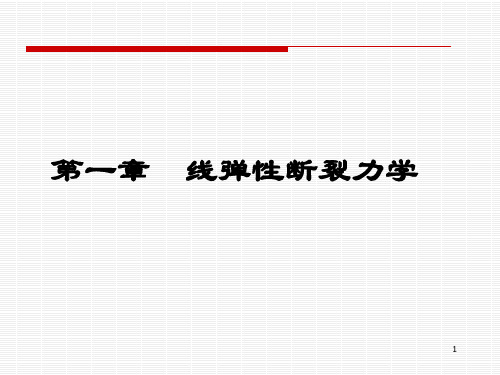
GⅠ
KⅠ2 E
E E
E
1
E
2
平面应力 平面应变
同理
GⅡ
KⅡ2 E
GⅢ
1
E
KⅢ2
32
4G 2
22
v KⅠ a x (2k 2)
4G 2
31
a
在闭合时,应力在 a那段所做旳功为
B 0
yvdx
GⅠ
B Ba
a
0 yvdx
1 a
a 0
KⅠ KⅠ
2 x 4G
a
2
x
(2k
2)dx
4k 1 4G
KⅠ2
平面应力
k
3 1
,
GⅠ
KⅠ2 E
平面应变
k 3 4
GⅠ
1 2
E
KⅠ2
13
撕开型裂纹(Ⅲ型):在平行于裂纹面 而与裂纹前沿线方向平行旳剪应力 作用下,裂纹沿裂纹面撕开扩展.
二.裂纹尖端附近旳应力场.位移场
1.Ⅰ型裂纹 问题旳描述:无限大板,有一长为 2a 旳穿透裂纹,在无限
远处受双向拉应力 旳作用.拟定裂纹尖端附近旳应力
场和位移场.
14
1939年Westergaurd应力函数
3
Griffith研究了如图所示厚度为B旳薄平板。上、下端受 到均匀拉应力作用,将板拉长后,固定两端。由Inglis解得到 因为裂纹存在而释放旳弹性应变能为
U 1 2 a2 2B
E
U 1 a2 2B
E
平面应变 平面应力
4
另一方面,Griffith以为,裂纹扩展形成新旳表面, 需要吸收旳能量为
解析函数性质:任意解析函数旳实部和虚部都是解析旳.
材料物理性能第一章第五节断裂分析

材料物理性能第一章第五节断裂分 析
1.2 脆性断裂
材料物理性能---断裂
• 脆性断裂是材料断裂前基本上不产生明显 的宏观塑性变形,没有明显的预兆,突然 快速的断裂,具有很大的危险性。
• 脆性断裂的断口,一般与正应力垂直,宏 观上比较齐平光滑,呈放射状或结晶状。
析
材料物理性能---断裂
预防脆性断裂失效的措施
• (1)设计上的措施 ①应保证工程构件的工作温度高于所用材料的脆
性转变温度,避免出现低温脆断;②结构设计应尽量避免三向应力的工 作条件,减少应力集中。
• (2)制造工艺的措施 ①应正确制订和严格执行工艺规程,避免过热、
过烧、回火脆、焊接裂纹及淬火裂纹;②热加工后应及时回火,消除内 应力,对电镀件应及时而严格地进行除氢处理。
• (3)使用上的措施 ①应严格遵守设计规定的使用条件,如使用环境
温度不得低于规定温度;②使用操作应平稳,尽量避免冲击载荷。
材料物理性能第一章第五节断裂分 析
材料物理性能---断裂
2 穿晶断裂与沿晶断裂
材料物理性能第一章第五节断裂分 析
材料物理性能---断裂
穿晶断裂和沿晶断裂的SEM图
穿晶断裂
沿晶断裂
断裂垂直于最大正 应力者叫正断
中心部分大致为正断, 两侧部分为切断,故 为混合型断口
沿着最大切应 力方向断开的 叫切断
材料物理性能第一章第五节断裂分 析
材料物理性能---断裂
1 韧性断裂与脆性断裂
1.1 韧性断裂
• 韧性断裂是材料断裂前及断裂过程中产生 明显宏观塑性变形的断裂过程。
• 韧性断裂时一般裂纹扩展过程较慢,而且 要消耗大量塑性变形能。
- 1、下载文档前请自行甄别文档内容的完整性,平台不提供额外的编辑、内容补充、找答案等附加服务。
- 2、"仅部分预览"的文档,不可在线预览部分如存在完整性等问题,可反馈申请退款(可完整预览的文档不适用该条件!)。
- 3、如文档侵犯您的权益,请联系客服反馈,我们会尽快为您处理(人工客服工作时间:9:00-18:30)。
3. 微孔聚集断裂的微观断口特征 韧窝形状:视应力状态不同而异,等轴、拉长和撕裂韧 窝。 韧窝大小(直径与深度):决定于第二相质点的大小和 密度、基体材料的塑变能力和应变硬化指数、外加应力大小 和状态。
4. 微观上出现韧窝,其宏观上不一定就是韧性断裂。
第五节 金属的沿晶断裂(属脆性断裂之一) 断口形貌特征: 宏观形貌:呈“冰糖状”。 微观形貌:带有晶界刻面 (即小平面)的所谓 “冰糖块”状形貌。
4Ep (c i ) 2 ( 1 ) d
1
2
铁素体γp
碳化物中形成裂纹后,要使裂纹扩展到相 邻铁素体中,还需克服铁素体的表面能,令γp 为铁素体的比表面能与γc之和,则上式为:
晶 界 碳 化 物 γc
裂纹
4Ep ( c i ) 2 ( 1 ) d
We→We+dWe
2c·1→(2c+2dc) · 1
dWe d c 2 2 2c ( ) 2dc 2dc E E
b. 形成单位新表面所需表面能 Ws→Ws+dWs → 2c· 1→(2c+2dc) · 1 c. 失稳条件(临界条件)
dWs d (4c ) 2 2dc 2dc
th
→
th th 2πa0 th 2a0 E E
W外 E th 2a0
② W外与表面能及E的关系能量平衡,
W外 2 1 0
③ σth与E关系
th
通常,
0 a0 E /100
→ห้องสมุดไป่ตู้
W外 2a0 E /100
W外 E 2 a0 E E 2 a0 100 2a0 10
正断抗力 Smax→Sot——材料抵抗正断破坏的能力。
②切断——断口取向与最大切应力方向一致,与最大 正应力呈45°角。切断是由于切应力或且应变所引起的 剪切型断裂。常发生于塑变不受约束或约束较小的情 况,如拉伸断口的剪切唇。
切断抗力 tmax→tk——材料抵抗切断破坏的能力。
的裂纹将迅速扩展而导致金属材料完全断裂。
解理断的过程(三各阶段):
a) 塑性变形形成微裂纹; b) 裂纹在同一个晶粒内初期长大; c) 裂纹越过晶界向相邻晶粒扩展。
a)
b)
c)
2. 柯垂耳位错反应理论 (解理裂纹)
在α-Fe (bcc)中:
滑移面(110),滑移方向[111]。 右图中两个正交滑移面(101)与 (101)相交于解理面(001)中的 [010]轴线。 若沿(101)和(101)各有柏 氏矢量为a/2[111]和a/2[111]的平行 位错列在交叉线上相遇,即可形成 新位错a[001],其反应式如下:
产生原因:晶界弱化。 晶界弱化原因:沿晶界分布脆性相薄膜,很软的 相,低熔点合金或杂质向晶界富集,可产生 沿晶脆断。
有以下几种: 微孔型——焊接热影响区,高温蠕变; 非微坑型——氢脆、应力腐蚀、回火脆 第二相网状物质——铸造金属、焊接接头
第六节.
纯剪切断裂
没有裂纹的形成与扩张
第七节.断裂分类及其特征
f max(70.5 )
o
d / 2 1/2 ( i )( ) r
滑移面上有效切应力
i
甄纳认为nb、长为r的楔形裂纹(空洞形位错),斯特罗应力形成裂纹
当σfmax达到材料的理论断裂强度σth时,则在σth作用下将
使塞积群前端形成微裂纹。
以上所述主要涉及解理裂纹的形成,并不意味着由此形成
3)按断口机制分 ① 解理断——正应力作用下所产生的穿晶断。 特点:断裂面是严格沿一定的晶面(即解理面,一般是低 指数晶面或表面能最低的晶面)而分离。如体心、密排六方 金属与合金在低温、冲击下能使解理断发生。
通常解理断是脆断,但脆断不一定是解理断。前者指断裂 机理而言,后者则指断裂的宏观性态。
② 剪切断——切应力作用下沿滑移面滑移而造成滑移面分离
1)弹性体裂纹失稳扩展判据 无限大板拉紧再固定拉应力σ,单位厚度 主要研究有2c长裂纹后强度情况
① 开长2c裂纹能量情况 a. 弹性能减少量(能量释放率)
c 2 2 We E 2 2 (1 2 ) c E 平面应力 平面应变
b. 表面能增加 Ws=(2c· 1· γ)×2=4cγ ② 裂纹扩展 2c→2c+2dc a. 扩展单位面积释放能量(弹性能变化)
2)塑性体塑性扩展条件
临界条件: c 实际金属中断裂前一定存在裂纹(或相当于裂纹),使断 裂强度显著下降。
c
E ( p 声热 )
第二节 初生微裂纹来源(机制) 大量实验观察表明,显微裂纹总是在强烈塑变区产生, 即裂纹形成与金属局部塑变有关,也就是与位错运动有关。 1. 甄纳-斯特罗位错塞积理论 (解理裂纹)
x E 。 E E a0 → th 2 a0
→
th 2 πa0 E
2)能量平衡法求σth与E关系
① σth与拉断外力做功W外关系
W外 =
/2
0
1 dx
/2
0 2
th sin
2πx
dx th
/2
0
sin
2πx
dx
这些模型的基本出发点都是在切应力作用下,先使位错 运动,然后由于不同原因而造成位错运动受阻,由塞积位错 的弹性应力场的拉应力而造成开裂。 4. 微孔聚集型微裂纹理论
第三节 金属的解理断裂(脆性断裂)(包括裂纹形成及扩展) 1. 解理断裂的定义及发生晶体类型 微观特征是平坦的镜面。 1)定义(解理断裂及解理面) 金属材料在一定条件下,当外加正应力达到一定数值后, 以极快速度沿一定的晶体学平面产生的穿晶断裂,是金属原 子正向分离,这个一定的晶体学平面称为解理面。 2)解理面的特性 一般都是低指数晶面或表面能最低的晶面。 例如:α-Fe滑移面为 {110};解理面为{001}。 3)晶体类型 通常体心立方、密排六方、低温fcc也可。 4)解理断裂与脆性断裂区别 解理断裂总是脆性断裂,有时解理前也有一定塑性,解 理断裂是指断裂机理,脆性断裂是断裂宏观状态。
滑断(纯剪切断)
纯金属、单晶体常发生,断 口呈锋利的楔型。 高纯金属、多晶体完全韧断 呈刀尖型。如Pb及其合金。
③ 微孔聚集型——经微孔形核、长大互相连接导致断裂
晶内微孔聚集穿晶断——低碳钢杯锥状断口 沿晶微孔聚集沿晶断——高温蠕变
4)按断口取向与最大正应力夹角分 ①正断——断口取向与最大正应力垂直,正断是由拉 应力或正应变所引起的脱离型断裂。常见于解理断和 塑变约束较大的场合。
c
E 100 E 1000
σth大小:晶须大小差不多, 大块材料
实际金属的断裂应力仅为理论σth值的1/10~1/1000。原因何在?
σc与σth差别原因:引出Griffith理论。
2. 实际断裂强度(格雷菲斯裂纹理论) 有裂纹,拉断(裂纹失稳扩展)看强度到底有什么变化。 条件:无限大板,单位厚度(面积为只乘长度)
1
2
晶粒直径 d
碳化物边界形成裂纹的Smith模型
c 之 若外加切应力分量处于上两式所确定的应力 c 和 间,则碳化物中形成裂纹后,尚需经过裂纹扩展阶段裂纹才 能通过相邻铁素体,这是一种裂纹扩展所控制的断裂。类似 柯垂耳模型的推导,可得到裂纹扩展所控制的断裂判据:
4Ep f 2 ( 1 ) c 0
1. 断裂的分类
1)按断裂前变形(我国断面收缩率5%) ① 韧断——断前产生明显宏观塑变。 特点:断口呈暗灰色,纤维状。 ② 脆断——断前基本上不产生塑变。 特点: ①低应力脆断(工作应力<材料的σs); ②脆断源从内部的宏观缺陷处开始; ③温度↓脆断倾向↑; ④断口平齐光亮,与正应力⊥,呈人字纹 或放射花样,结晶状。
a/2[111] + a/2[111]
a[001]
因为反应后能量有所降低,故合成的新位错是稳定的,是 不动位错。当塞积位错较多时,其多余的半原子排象楔子 一样插入(001)中,使之解理开裂,形成裂纹。
3. 夹杂物边界形成微裂纹的Smith理论 (解理裂纹)
上述微裂纹形成模型都忽略了材料中的硬而脆的第二相粒子。这些 粒子的形状、尺寸、分布将影响材料断裂的性质。粗碳化物粒子将促进 钢发生解理断裂,而含细碳化物粒子的钢却表现出较好的韧性。基于此 Smith提出了新的解理断模型。 根据Smith理论,塞积头前端造成拉应力集中,此应力将使碳化物 开裂,其条件(此时τ=τc): σ
舌状花样形成方式: 解理裂纹沿孪晶界扩展留下舌头状凹台或凸台。
另外:还有准解理(是解 理而非解理)。特点:断 裂路径不再与晶粒位相有 关,不再沿一定的晶体学 平面,主要与细小碳化物 质量有关。(撕裂棱较多,往
往有一定的塑性)
解理:一定 晶体内平面 准解理:不一定 与解理的区别 裂纹源 解理:晶界 准解理:第二相
2. 解理断裂过程 屈服(少量变形)→生成终止于晶界的初生裂纹→初 生裂纹越过晶界(如何越过?)→扩展→断裂。 初生裂纹按斯特罗(Zener-Stroh )、斯米特 (Smith)、柯垂耳(Cottrell)理论机制生成。终止于晶 界,其断裂面没有花样(即刚开始无花样,若在在自己境 内扩展就有了花样)。 初生裂纹面与其相邻 的一个晶粒相交于晶界, 外力与此处产生巨大应力 集中,使相邻晶粒不同高 度的解理面开裂,形成平 台,平台之间二次解理形 成台阶等(也可撕裂)。
通常脆断也产生微量塑变,一般规定光滑拉伸ψ<5%为脆断。材料 韧、脆性根据断前塑变量恒量,实验条件改变,材料韧脆行为也改变。
2)按裂扩展路径分
① 穿晶断裂——裂纹穿过境内
裂纹 晶界
韧断:大多数室温拉断 脆断:低温下拉断