现场流水线改善报告
生产线改造年度工作总结汇报

生产线改造年度工作总结汇报尊敬的领导和各位同事:
我很荣幸能够在此向大家汇报我们生产线改造的年度工作总结。
在过去的一年里,我们团队经过不懈努力,取得了一系列显著的成就,为公司的发展和生产效率提升做出了重要贡献。
首先,我们在生产线改造方面取得了巨大的进步。
通过引进先进的生产设备和
技术,我们成功地提高了生产线的自动化程度,大大提升了生产效率和产品质量。
同时,我们还对生产流程进行了优化和改进,使得整个生产过程更加顺畅和高效。
其次,我们注重了员工的培训和技能提升。
通过组织各类培训和学习活动,我
们不断提升员工的技术水平和工作能力,使他们能够更好地适应新的生产线设备和流程,为生产线改造提供了有力的保障。
此外,我们还加强了生产线的安全管理工作。
我们制定了一系列严格的安全操
作规程和标准,加强了对生产线设备的维护和保养,有效地提高了生产线的安全性和稳定性,为员工的生命财产安全提供了有力的保障。
最后,我们还注重了与供应商和客户的沟通和合作。
通过与供应商的紧密合作,我们成功地引进了一批高性能的生产设备和原材料,为生产线改造提供了有力的支持。
同时,我们还积极与客户沟通,及时了解他们的需求和反馈,不断改进和优化我们的生产线,以满足客户的需求。
总的来说,我们在生产线改造方面取得了一系列显著的成就,为公司的发展和
生产效率提升做出了重要贡献。
但是,我们也清楚地意识到,生产线改造工作仍然存在一些问题和挑战,需要我们继续努力和改进。
我们将继续秉承“精益求精、追求卓越”的工作态度,不断提升自身的专业水平和团队协作能力,为公司的发展和生产线改造工作再创辉煌!
谢谢大家!。
生产现场改善方案

市摩卡科技制造中心生产现场改善报告尊敬的胡董事长、涂总:你们好!本人很快乐参加市摩卡科技,也同时感胡董与涂总的信认,本人将尽心尽职把公司的品质、效率搞上去,降低本钱、节约资源,以最少的投入创造最高的利润,同时也希望领导的支持和帮助,以下是我对公司现状分析与改善方案。
现状分析1、生产方面:1》没有生产流程图,标准工时,作业指导书,产能评估报告,按此人员的排布是否最适宜?2》生产线没有辅助治具的投入〔工具、夹具〕。
3》现场无7S 管控。
4》现场产能进度跟进无法提现,无生产看板,反响不出该线在做什么、并且现场管理拿什么现场数据去把握现状。
5》人员纪律松散,工衣着装颜色统一,不利于目视管理,在流水线分不清那个是管理那个是员工、那个是QC、那个是助拉,找也难6》现场规划不合理,无法提现一个顺畅的生产制程。
7》产品制程划分不合理,在组装部份还有在焊接PCB板,焊线或焊零部件。
8》生产线没有物料员,物料管控失控。
9》没有异常问题的检导,如生产品质例会、新产品导入会议10》现场管理的专业技能须进一步提升,执行力差。
2、品质方面1》来料检验控制没有标准与依据。
〔电子料、五金、线材、塑胶、包材〕2》没有品质过程控制相关规定。
3》出货检验没有标准性。
4》工程没有成品检验基准书、外观检验标准、部件检验基准书与制程生产的流程图、SOP、BOM(完整性)工夹具。
5》来料检验项目没有记录档案,无法追逆与控件控制。
3、生管〔PMC〕方面1》新产品导入〔PP\MP\试产〕没有产前会议的召开。
2》产品没有标准工时对计划的安排有一定的难度,不确定性3》欠料特别严重。
4》公司没有体系运作的模式。
针对以上相关问题本人提出以下相关改善方案一:培训教育方面1、组织各部们管理人员对其管理的专业知识、理论知识与技能进展培训与考核,以提升自我管理能力并作成培训计划大纲与试卷来对管理能力的评估。
2、组织作业员根本知识与专业技能与企业文化的培训。
以提高其技能到达我司之要求并作成培训计划大纲、与试卷来对其技能的评估。
改善的范文怎样写改善前改善后报告

改善的范文怎样写改善前改善后报告此类报告一般包含四个方面:(1)改善前的存在的问题、困境或缺陷(2)采取的改善的方案或措施(3)改善前后情况的对比:(4)改善后的成果参考的事例:生产流水线的改进一、改善前的问题点:1、流水线布局不合理,物流不畅通;2、平衡率偏低,效率低下;3、各工位所使用的工具无固定装置放置;4、部分工位会因物料配送不及时导致延误生产;5、5S推行不到位。
二、改善采取的措施:1、根据现生产机型安吉尔Y1160LKD-C制定工艺流程图,对工序重组,平衡各工位,并设定标准人力及产能;2、依据工艺流程图设计线体布局图,对各工位明确规定作业位置及摆放方式;3、工艺员对所用工具制作定位装置以便按位摆放;4、依据线体布局图推行5S;5、在实际生产中对工位内容再作调整,对作业方法进行修正以求完善。
三、改善前后对比:1、数据对比表2、成本对比表3、利润对比表四、改善后的成果:1、生产率:A.改善前23人作业,间接人员4人,时产45PCS,27人*7元/H ÷45PCS=4.2元;B.改善后24人作业,间接人员4人,时产55PCS, 28人*7元/H ÷55PCS=3.56元;C.节约成本:4.2-3.56=0.64元/台,平均日产量以600台计算,每月工作26天; 即:每天可节约成本:600台*0.64元/台=384元. 每月可节约成本:600台*26天*0.64元/台=9984元.每年可节约成本:600台*26天*12月*0.64元/台=119808元.D.生产率提高了:4.2元÷3.56元-1=17.98%。
2、5S推行:按制定的线体规划图进行按位摆放后,各工位均无乱放现象,5S 推行较为顺畅,生产现场有序进行。
3、IE思想推行:通过此次改善,让线长及全体员工都有深入参与,让他们有了成本意识,对工位及线体的改善方法有了初步了解,对于带动全体员工参与改善有着积极的影响。
流水线改善报告

结论:无瓶颈工位,能满足现有产能(不建议改善)
数据收集&分析
数据名称:《工艺流程图》 数据来源:根据实际状况绘制 目 的:确定工艺顺序,分析关键流程要数百分比,寻找并确定浪费状态。
•结论: •每个人每生产一台机器搬运&走 动时间占总生产时间的2.03%? •搬运&走动次占总动作数的55%?
•如何避免?
动作 操作 检查 走动 搬运 储存 发生数 5 1 10 8 2 时间 40.32 6.1 0.16 0.8 47.3 百分比 85.10% 12.87% 0.34% 1.67% 2
数据收集&分析
数据名称:《搬运流程图》 数据来源: 实测 目 的:确定各工作站物料起始点及重点搬运路径并分析原因,降低搬运次数,消除搬运浪费
平衡率=72.7% T.T=5(分/台) 试缝纫好机器
9
检查
9
10 11
10 检查 11 检查
平衡率=86.5% T.T=4(分/台)
质量合格机器
12 清洁
13 包装
12
13
清洁
包装
结论:1.通过拆分和重组工序,细化作业内容,在人数不变前提下提升产线平衡率,提高目标产能
效果展示
电脑线作业模拟图-未来
方案效果预计
跑合好机器
工艺程序图-之前 跑合好机器
1 调试 2 调试
调试好机器
名称 调试 试缝 绣花 检查 清洁 包装 合计 人数 时间(min) 3 14.1 3 10 2 7.9 3 6.1 1 4.8 1 3.6 13 46.5
工艺程序图-之后
1 2
外观检查 参数设置 张力调试 花样测试 花样测试 检查 检查 检查 返工 绣花 绣花
生产工艺改善报告。
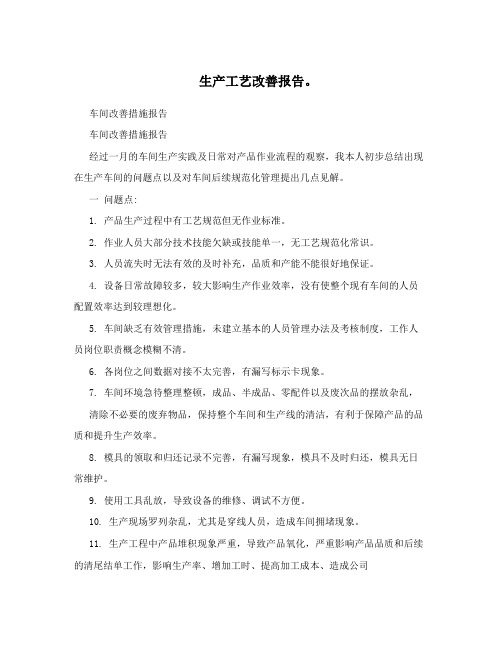
生产工艺改善报告。
车间改善措施报告车间改善措施报告经过一月的车间生产实践及日常对产品作业流程的观察,我本人初步总结出现在生产车间的问题点以及对车间后续规范化管理提出几点见解。
一问题点:1. 产品生产过程中有工艺规范但无作业标准。
2. 作业人员大部分技术技能欠缺或技能单一,无工艺规范化常识。
3. 人员流失时无法有效的及时补充,品质和产能不能很好地保证。
4. 设备日常故障较多,较大影响生产作业效率,没有使整个现有车间的人员配置效率达到较理想化。
5. 车间缺乏有效管理措施,未建立基本的人员管理办法及考核制度,工作人员岗位职责概念模糊不清。
6. 各岗位之间数据对接不太完善,有漏写标示卡现象。
7. 车间环境急待整理整顿,成品、半成品、零配件以及废次品的摆放杂乱,清除不必要的废弃物品,保持整个车间和生产线的清洁,有利于保障产品的品质和提升生产效率。
8. 模具的领取和归还记录不完善,有漏写现象,模具不及时归还,模具无日常维护。
9. 使用工具乱放,导致设备的维修、调试不方便。
10. 生产现场罗列杂乱,尤其是穿线人员,造成车间拥堵现象。
11. 生产工程中产品堆积现象严重,导致产品氧化,严重影响产品品质和后续的清尾结单工作,影响生产率、增加工时、提高加工成本、造成公司经济损失。
二改善计划及措施:1. 制定公司产品生产规范工艺流程,设置关键岗位工艺管控办法。
有利于对产品品质进行管控,以减少产品品质不良现象,并可初步设定生产合格率目标,减少无谓的返工和人力浪费,从而提升产品品质及生产效率。
2. 人员岗位职责的明确化,建立责任机制和追踪机制,有利于岗位人员的责任心的提升,并实施奖罚制度,不能做多做少一个样,做好做坏一个样,做与不做一个样,提升员工的积极性和责任感。
3. 要求员工做到每一道工序的自检和互检,以保证没有漏装、错装及破损和不合格品进入下一道工序。
4. 在早会上,管理人员可总结前日生产时发现的品质、车间及生产过程等发生问题,避免后续生产中再次发生,有利于对员工进行品质和责任教育。
流水线改善报告

开发:
制造:
品管:
工程:
不易看出产能配平,平衡难度很大很难找到平衡点。
很难及时看到速度的快慢。
产线类型
思想观念
物料流通
管理水平
流水拉
追求的是产线的整体配合,所有员工的思想观念的统一,执行力的统一,集体利益
流通材料少,流通速度快,产线很少有材料的堆积;不产生无效的搬运时间
对于现场人员的综合能力要求很高,有较高的观察,调配能力,否则直接影响到产能。相关部门的配合速度要快,解决问题必须快,有效。尽可能缩短解决时间,否则会造成全线停线。
深圳市鹏毅实业有限公司
SHEN ZHEN PANG NGAI INDUSTRIAL CO., LTD.
发文单位
发文日期
拟制
审核
批准
工程部
2011.08.31
余晓秋
关于流水拉改善报告
一、流水线的产线情况:
日期
产线
产品编号
作业人数
日产能
节拍时间
瓶颈工序
原因分析
9月19日
4233线
H09-000159
36人
平板拉
体现的是个人的速度,极易造成工序产能的不平衡,造成产线配置不平衡
流通物料的投入较多,流通速度较慢,产线出现大量的材料的堆积,同时产生大量的无效搬运时间。
异常只影响单个工站或相邻工站,
五、总结:
流水线在品质控制、人员管理、物料流通、产能速度控制、5S管理及现场管理水平上比平板拉要有优式,在产能上目前仍未发现明显改善(与新开时间短,适应有关)。产能仍需观测评估。
流水拉
流水拉必须及时替岗,时间控制严格,否则会造成整条产线停滞,直接影响产能。
流通时间短,能迅速发现问题,批量很少,问题能得到尽快解决。
产线流水线平衡改善范例以及报告

高
高 高
改善方案:
1、拆机壳工站拆分为2个,1个负责拆机壳、 透明片检查;另一个负责切隔板 2、装屏与装喇叭、咪头工站位置交叉互换 3、在装屏与装主板之间,增加一个工站,负责 安装按键、剪显示器支架 4、减去合盖工位插线部分,分割到装切换板工位
改善前工位图:
改善后工位图:
80D21数据分析表:
80D21流水线效率提升报告
第三部分:再次改善
主因分析:
人 机
线速设定缺乏依据 新人操作不熟练
工作内容不固定
工艺分配不合理 来料不良比例高
现场物料没有及时处理
平 衡 率 、 产 量 低
料
法
环
具体分析:
工站 拆机壳 切隔板 装喇叭、咪头 装屏 装按键、切隔板 装主板 装切换、插线 合盖 新人,操作速度慢 主板来料不良 中 高 主因分析 影响程度
时间
45 40 35 30 25 20 15 10 5 0
柱状图:
拆 机 壳 切 隔 装 板 喇 叭 、 咪 头 装 装 按 屏 键 、 剪 支 架 装 装 主 切 板 换 板 、 插 线 合 盖
各工站工时图
工站
时间
结果分析:
单小时人均产能提升:48.39% 产线平衡率:81.27%
(√) (×)
预期效果:
红色装主板工位,为预测值
许长伟 2012.08.27
第四部分:持续改进方向
80D21流水线效率提升报告
第一部分:现状描述
问题描述
1、问题描述 工站间存在积压、等待现象
产线平衡率较低 小时产量、日产量较低
改善目标
产线平衡率至少85% 单小时人均产能至少提升50%
IE现场改善专案报告

2015年10月 2015年11月 2015年12月
李自岳/ 刘庆鹤
付国华/ 张文雅
计划 执行
2016年1月
付国华
IE
计划 执行
李自岳/ 刘庆鹤
赵永强
计划 执行
李自岳/ 刘庆鹤
赵永强
计划 执行
李自岳/ 刘庆鹤
赵永强
计划 执行
李自岳/ 刘庆鹤
赵永强
计划 执行
李自岳/ 刘庆鹤
赵永强
计划 执行
李自岳/ 刘庆鹤
一.成立背景及课题选定
1.2 课题选定之订单分析
根据10月份产能分析得,该型号订单量占公司总订订量的34.8%。
二.改善计划及目标设定
2.1 改善计划
内容
冲压A903车间LAYOUT布置
效果确认
A903改善48米流水线作业 改为30米作业(41人)
流程改善(山积表/平衡率 /IE七大手法)
A903改善(41人改为36 人,产能不变)
TT:22.4s
12
12
8
2 2
TT:19s
五.效果确认
5.1 各项指标数
41人
生
产
人
36人 数
:
减
少
改善前
改善后
5
人
400
350
面
300 200
220
积 :
减
100
少
13
0
0
改善前 改善后 M²
生 产 人 数 : 减 少 5 人
流 水 60
线 50
长 40
度 30
: 20
减 少
18
10 0
米
48米 改善前
改善报告怎么写
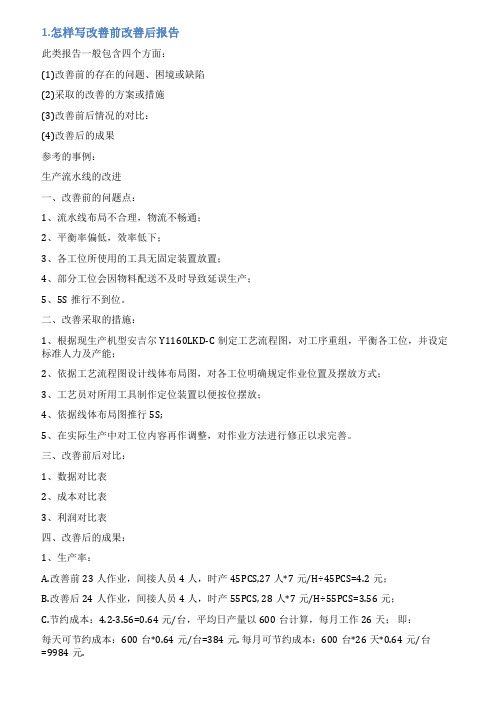
1.怎样写改善前改善后报告此类报告一般包含四个方面:(1)改善前的存在的问题、困境或缺陷(2)采取的改善的方案或措施(3)改善前后情况的对比:(4)改善后的成果参考的事例:生产流水线的改进一、改善前的问题点:1、流水线布局不合理,物流不畅通;2、平衡率偏低,效率低下;3、各工位所使用的工具无固定装置放置;4、部分工位会因物料配送不及时导致延误生产;5、5S推行不到位。
二、改善采取的措施:1、根据现生产机型安吉尔Y1160LKD-C制定工艺流程图,对工序重组,平衡各工位,并设定标准人力及产能;2、依据工艺流程图设计线体布局图,对各工位明确规定作业位置及摆放方式;3、工艺员对所用工具制作定位装置以便按位摆放;4、依据线体布局图推行5S;5、在实际生产中对工位内容再作调整,对作业方法进行修正以求完善。
三、改善前后对比:1、数据对比表2、成本对比表3、利润对比表四、改善后的成果:1、生产率:A.改善前23人作业,间接人员4人,时产45PCS,27人*7元/H÷45PCS=4.2元;B.改善后24人作业,间接人员4人,时产55PCS, 28人*7元/H÷55PCS=3.56元;C.节约成本:4.2-3.56=0.64元/台,平均日产量以600台计算,每月工作26天;即:每天可节约成本:600台*0.64元/台=384元. 每月可节约成本:600台*26天*0.64元/台=9984元.每年可节约成本:600台*26天*12月*0.64元/台=119808元. D.生产率提高了:4.2元÷3.56元-1=17.98%。
2、5S推行:按制定的线体规划图进行按位摆放后,各工位均无乱放现象,5S推行较为顺畅,生产现场有序进行。
3、IE思想推行:通过此次改善,让线长及全体员工都有深入参与,让他们有了成本意识,对工位及线体的改善方法有了初步了解,对于带动全体员工参与改善有着积极的影响。
供参考2.改善报告格式情况汇报,就是情况报告,属于报告文种。
生产线改善总结汇报
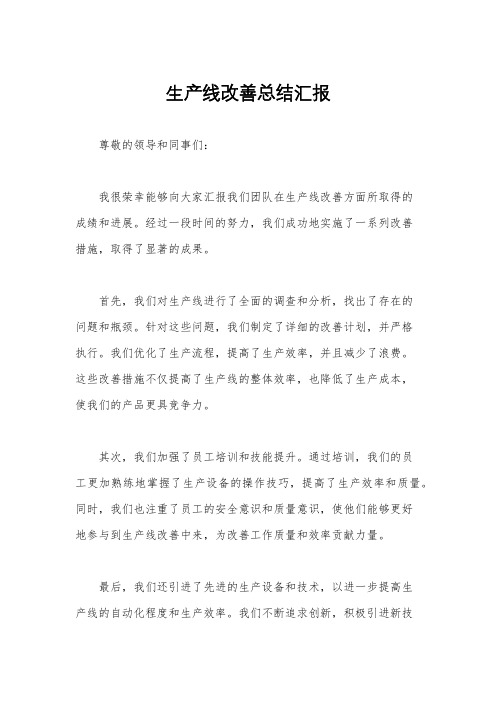
生产线改善总结汇报
尊敬的领导和同事们:
我很荣幸能够向大家汇报我们团队在生产线改善方面所取得的
成绩和进展。
经过一段时间的努力,我们成功地实施了一系列改善
措施,取得了显著的成果。
首先,我们对生产线进行了全面的调查和分析,找出了存在的
问题和瓶颈。
针对这些问题,我们制定了详细的改善计划,并严格
执行。
我们优化了生产流程,提高了生产效率,并且减少了浪费。
这些改善措施不仅提高了生产线的整体效率,也降低了生产成本,
使我们的产品更具竞争力。
其次,我们加强了员工培训和技能提升。
通过培训,我们的员
工更加熟练地掌握了生产设备的操作技巧,提高了生产效率和质量。
同时,我们也注重了员工的安全意识和质量意识,使他们能够更好
地参与到生产线改善中来,为改善工作质量和效率贡献力量。
最后,我们还引进了先进的生产设备和技术,以进一步提高生
产线的自动化程度和生产效率。
我们不断追求创新,积极引进新技
术,新设备,不断提高生产线的智能化水平,使我们能够更好地适
应市场的需求变化。
通过这些改善措施的实施,我们的生产线取得了显著的进步。
生产效率得到了提高,产品质量得到了保障,生产成本得到了控制,我们的竞争力也得到了增强。
我们相信,这些改善措施将为公司的
发展和未来的市场竞争提供有力支持。
在未来的工作中,我们将继续努力,不断改进生产线,提高生
产效率和质量,为公司的可持续发展做出更大的贡献。
谢谢大家的支持和合作!
此致。
敬礼。
流水线工作总结报告3篇

2019流水线工作总结报告3篇流水线工作总结报告一通过这次的实习,我们学到了很多课堂上学不到的知识。
我们也了解和掌握了车间管理、生产技术和工艺过程,对我们的专业有了更深层次的了解。
在实习中我们拥有了社会了实践能力,社会沟通能力,还有工作经验,这些都是重要的,在课堂上学不来的。
在这次生产实习过程中,不但对所学习的知识加深了了解,更加重要的是更正了我们的劳动观点和提高了我们的独立工作能力等。
我们还知道自己存在的不足,但是我们都会改正,在以后学习工作中我们会更加的努力。
一、安全生产工作内容:1,加强特种设备使用、管理培训,操作手基本上掌握了运行原理,也简单调试维修,也应急预防措施。
油炸锅,锅炉,杀菌锅基本落实到人。
加大特种设备的巡检力度,车间主任必须一日三检。
2,整改不合理生产流程,减少半成品在流水线停留时间,避免了物理,微生物污染,同时提高了生产效率。
现在生产周期从原来的36小时缩短到24小时。
3,精细科学管理,从年初制定科学精细管理,到逐步实施,车间设备,产品出现异常情况能够及时,快速解决,短时间不能解决的也能很快上报到中高层,大大减少了半成品不合格率,并半成品能够及时分离分类处理,减少了工厂的损失,也提高的成品合格率。
4,加强员工的培训。
本年度由生产部,品管部等多部联合组织管理者、员工培训,增强员工的质量意识,节约意识。
同时不同岗位做不同的岗位培训,让员工熟练,科学操作设备。
5,组织学习消防知识,遇到突发事件的处理方法和逃生技能。
二、有公司团队支持1.领导对我信任自从老师任命我为调漆室主管,他就一直信任着我,放手让我自由地进行相应的管理工作。
当我出错的时候,他并不是严厉地批评我,而是耐心地对我进行指导。
俗话说,滴水之恩,当以涌泉相报。
为了感谢老师对我的知遇之恩,从我主持管理工作那天起,我就不敢有一丝的松懈和半点的懒惰,生怕把工作做差了,辜负老师对我的期望。
因为作为一个高素质高水平的管理人员,不但需要具备丰富的实践经验和强劲的工作能力,同时,还必须丰沛的管理知识和强烈的责任意识,所以,在工作之余,我挤出时间读了很多管理方面的书籍,从中学到了大量优秀的理论知识,大大提高了我的管理水平。
2024年2月流水线生产个人总结范文

2024年2月流水线生产个人总结范文我的2024年2月份是在一家汽车制造公司的流水线上度过的。
作为一名生产组长,我负责指导和管理工人,确保生产线顺利运作。
在这个月里,我遇到了一些挑战,但也取得了一些成果。
在这篇个人总结中,我将回顾这个月的工作,并提出一些改进的建议。
首先,让我来回顾一下2月份的工作内容。
这个月我们的生产任务非常艰巨,因为我们公司推出了一款新车型,需要大量生产并按时交付给客户。
我们的生产线在这期间一直处于高负荷运转状态。
我和我的团队加班加点,确保生产线不断运转,并及时解决一些突发问题。
虽然有时候我们会因为一些技术故障导致生产线停工一段时间,但我们都尽力将影响降到最低。
其次,我要感谢我的团队成员们在这个月的辛勤工作和付出。
每天,他们都全身心地投入到工作中,保证生产线的顺利运作。
他们不断学习和成长,提高了自己的技能水平,这对我们的生产效率有很大的提升。
作为团队的领导者,我非常欣赏他们的工作态度和团队精神。
然而,在这个月也遇到了一些问题和挑战。
首先,由于生产任务的紧迫性,我们的工人们面临着巨大的压力。
有时候他们需要加班工作,长时间的工作可能会导致他们的疲劳和精神压力。
为了解决这个问题,我和公司的人力资源部门一起制定了一套合理的工作时间表,尽量避免过度疲劳的情况发生。
另外一个问题是技术故障的出现。
由于新车型的生产线上使用了一些新的机器和设备,我们在初期遇到了一些技术故障。
这些故障导致生产线停工了一段时间,同时也给我们的工作带来了不必要的麻烦。
为了解决这个问题,我们邀请了技术专家对设备进行维护,并对工人进行了相关培训,以便他们能够更好地应对技术故障。
基于以上经验和教训,我提出了一些建议来改进我们的生产线。
首先,我们可以进一步优化工作时间表,确保员工的工作负荷合理分配,减少因为过度疲劳而带来的工作质量下降的问题。
此外,我们还可以加强设备的维护和保养,以减少技术故障的发生。
同时,我们也应该提供相关的培训和学习机会,让员工能够掌握和应对新的技术和设备。
生产效率提升改善案例

生产效率提升改善案例
一、提高流水线生产效率的改善案例
1、改善设备设计:一种常见的改善方式是,改变设备设计,使整个
流程更加顺畅。
例如,一个公司正在使用一条慢速的旧型自动化装配线,
由于原先装配线太慢,以至于每一次的装配循环时间都要超过一小时,很
难实现高效率的生产。
因此,该公司进行了一次改良,在拆卸旧线的过程中,改变了设备的位置,增加了一定数量的传送带,增加了一些工作台,
使得整个过程更加顺畅,最终将整个流水线的生产时间缩短到30分钟,
从而大大提高了生产效率。
2、加强信息传输:另一种提高流水线生产效率的方式是,通过安装
和升级计算机系统,加强信息传输,以有效控制整个生产过程。
例如,一
家公司在安装计算机系统之前,流水线的每一个步骤的控制都需要人工完成,操作不方便,需要大量的管理精力,费用也很高。
但是,安装完成后,整个流水线就可以以计算机系统为基础,实时控制所有的生产过程,使得
生产过程更加高效,提高了生产效率。
3、优化物料搬运:另一种常见的生产改进方式是,通过优化物料搬运,使得整个流水线上的工作人员更加高效。
技术改造报告范文
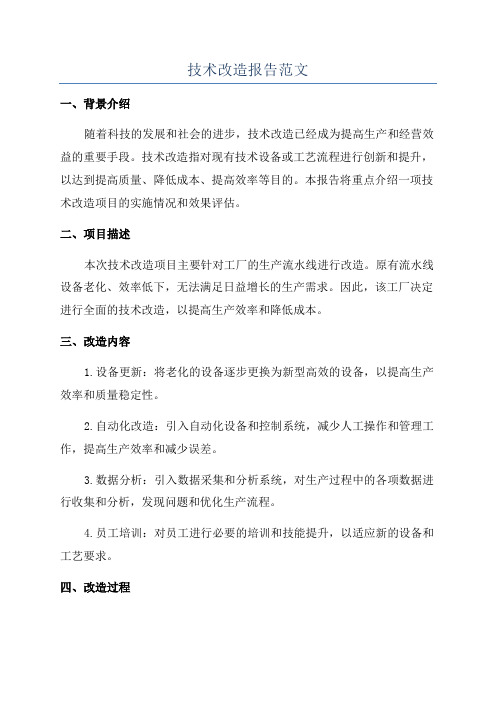
技术改造报告范文一、背景介绍随着科技的发展和社会的进步,技术改造已经成为提高生产和经营效益的重要手段。
技术改造指对现有技术设备或工艺流程进行创新和提升,以达到提高质量、降低成本、提高效率等目的。
本报告将重点介绍一项技术改造项目的实施情况和效果评估。
二、项目描述本次技术改造项目主要针对工厂的生产流水线进行改造。
原有流水线设备老化、效率低下,无法满足日益增长的生产需求。
因此,该工厂决定进行全面的技术改造,以提高生产效率和降低成本。
三、改造内容1.设备更新:将老化的设备逐步更换为新型高效的设备,以提高生产效率和质量稳定性。
2.自动化改造:引入自动化设备和控制系统,减少人工操作和管理工作,提高生产效率和减少误差。
3.数据分析:引入数据采集和分析系统,对生产过程中的各项数据进行收集和分析,发现问题和优化生产流程。
4.员工培训:对员工进行必要的培训和技能提升,以适应新的设备和工艺要求。
四、改造过程1.设备采购和安装:根据项目需求,与供应商合作,选购适合的设备,并由专业的安装团队进行设备的安装和调试工作。
2.自动化改造:根据生产流程,对需要进行自动化的环节进行改造和调试,确保设备的自动化和可靠性。
3.数据分析系统的引入:与专业的数据分析团队合作,开展数据分析系统的设计和部署工作,确保数据采集和分析的准确性和有效性。
4.员工培训:组织专业培训师对员工进行培训,提高员工的技能水平,以适应改造后的工作要求。
五、改造效果评估1.生产效率提升:通过对比改造前后的生产数据,发现生产效率提高了30%以上,生产线的产能大幅度提升。
2.成本降低:由于新设备的投入和自动化改造的实施,人工成本大幅度降低,生产成本减少了20%以上。
3.质量稳定:新设备的使用和数据分析的引入,提高了产品质量的稳定性,减少了缺陷率,改善了产品的信誉和市场竞争力。
六、结论通过本次技术改造项目的实施,工厂的生产效率得到了显著提升,成本得到了有效控制,产品质量稳定性得以提升。
OE工厂改善报告
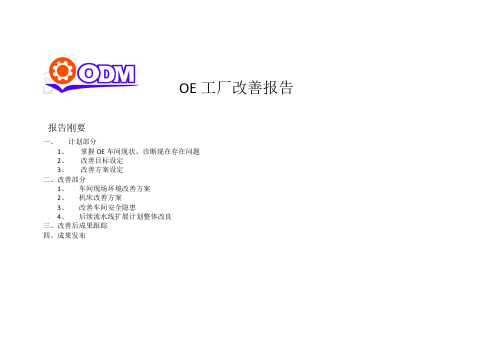
OE工厂改善报告
报告刚要
一、计划部分
1、掌握OE车间现状、诊断现在存在问题
2、改善目标设定
3、改善方案设定
二、改善部分
1、车间现场环境改善方案
2、机床改善方案
3、改善车间安全隐患
4、后续流水线扩展计划整体改良
三、改善后成果跟踪
四、成果发布
OE工厂现状掌握
现场情况
1、工装摆放比较混乱、状态不明确
2、电路、气路、水管布置不规范,存在安全隐患
3、区域划分不明确、油品没有颜色标示
4、生产设备有部分地方连接不合理、导致劳动力浪费
改善目标确定
1、工装器具摆放整齐、状态明确
2、电线、气管、水管布置合理清晰,用不同的颜色予以区分
3、区域划分明确、不同的油品用不同颜色予以区分
4、改进设备的硬件
改善方案
改善前后对比
改善前后对比。
生产线改善工作总结汇报
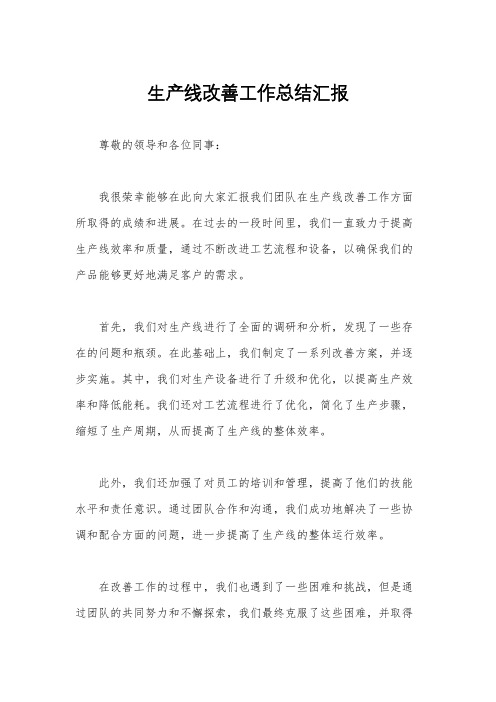
生产线改善工作总结汇报
尊敬的领导和各位同事:
我很荣幸能够在此向大家汇报我们团队在生产线改善工作方面所取得的成绩和进展。
在过去的一段时间里,我们一直致力于提高生产线效率和质量,通过不断改进工艺流程和设备,以确保我们的产品能够更好地满足客户的需求。
首先,我们对生产线进行了全面的调研和分析,发现了一些存在的问题和瓶颈。
在此基础上,我们制定了一系列改善方案,并逐步实施。
其中,我们对生产设备进行了升级和优化,以提高生产效率和降低能耗。
我们还对工艺流程进行了优化,简化了生产步骤,缩短了生产周期,从而提高了生产线的整体效率。
此外,我们还加强了对员工的培训和管理,提高了他们的技能水平和责任意识。
通过团队合作和沟通,我们成功地解决了一些协调和配合方面的问题,进一步提高了生产线的整体运行效率。
在改善工作的过程中,我们也遇到了一些困难和挑战,但是通过团队的共同努力和不懈探索,我们最终克服了这些困难,并取得
了显著的成效。
现在,我们的生产线运行更加稳定,产品质量得到了进一步提升,客户的满意度也得到了显著提高。
总的来说,我们在生产线改善工作方面取得了一定的成绩,但也意识到还有很多地方需要进一步改进和完善。
我们将继续努力,不断优化生产线,提高生产效率和产品质量,为公司的发展做出更大的贡献。
谢谢大家的支持和配合!
此致。
敬礼。
工厂改善项目可行报告

工厂改善项目可行报告在当今竞争激烈的市场环境下,工厂改善项目成为了许多企业提升效率、降低成本、提高竞争力的重要举措之一。
本报告旨在分析现有工厂存在的问题,提出改善方案,并评估其可行性。
1. 问题分析1.1 生产效率低下当前工厂生产线存在生产效率低下的问题,主要表现在生产过程中频繁的停机维护、生产线布局不合理等方面,导致生产效率无法达到最优水平。
1.2 能源消耗过高工厂能源消耗过高,主要原因是设备老化、能源管理不善、生产过程中存在能源浪费等问题,严重影响了企业的经济效益。
1.3 产品质量不稳定由于生产设备调整不当、操作技术不到位等原因,工厂产品存在质量不稳定的情况,这不仅增加了生产成本,还影响了客户满意度。
2. 改善方案2.1 更新设备针对工厂存在的设备老化问题,建议逐步更新设备,引入先进的生产技术和设备,以提升生产效率和产品质量。
2.2 优化生产线布局重新规划和优化生产线布局,使生产过程更加流畅,减少停机时间,提高生产效率。
2.3 强化能源管理加强对能源的监测和管理,采取节能措施,优化生产过程,降低能源消耗,提高能源利用率。
2.4 培训提升员工技能加强对员工的技术培训,提升其操作技能和质量意识,从根本上保障产品质量稳定。
3. 可行性评估3.1 技术可行性现代化设备更新、生产线布局优化等技术手段已在许多企业得到成功应用,具备较高的技术可行性。
3.2 经济可行性虽然改善项目需要一定的投资,但通过提升生产效率、降低能源消耗和减少质量问题带来的损失,预计将在较短时间内实现投资回报,具备较高的经济可行性。
3.3 管理可行性改善项目需要全体员工的积极配合和管理层的有效领导,通过培训提升员工技能、加强能源管理等措施,管理可行性较高。
结论综合考虑技术、经济和管理等方面的可行性评估,工厂改善项目具备较高的可行性。
通过逐步实施改善方案,相信能够有效提升工厂生产效率、降低成本、提高产品质量,从而增强企业的竞争力和可持续发展能力。
现场流水线改善报告

现场流水线改善报告F隽魉改善蟾蟾嫒:郎2009/12/16现场改善热一、二、三、四、五、六、七、八、九、十、十一十二目的生a管理看板改善生a使用料P 箱、泡ぜ巴瓿善钒b架a料盒分及定x 涂油a品的放置C台放置工作桌改造孔位z具定位流水上附著油污改善流水速c十a能φ毡^物料架磨合后a品冷sb置1一、目的通^建立一l影辶魉,M行作I方法、生a性、h境、效率、目管理、5S、化等方面的改善。
在保C安全生a的同r,亩提高生a效率、品|及增加附加r值,并水平展_于其它e……2二、生a管理看板改善多N冢Ho算,前面目已wF最K Y果部份目c 目前H生aCNe 不符合外技g人T不R全,常ro法及rj o法wF 首件a品的息改善前3g接人T各时段异常原因记录,便于及时处理首件a品相P生a息改善后每月表F 秀的作IT4三、生a使用料P 料P改善前1.使用材料榕2.泡どo料耸3.同一穴追N物料4.材|,移r容易倒翻物料5.容易破p,使用周期短6.外^不y一,o驶5料P改善后1.使用材料槿榘咨板材,使用周期L2. 料P上可以插入使用物料料,可目管理,Y合SOP可避免物料使用e`。
3.外^以左D示剩格一致,驶推行。
4.不同物料可分放置。
6四、箱、泡ぜ巴瓿善钒b架a.箱放置改善改善前:箱放置在地上, 凌y、易脏、拿取不方便,箱容易磨损。
U型F架改善后:使用U型F架放置箱,箱抽取方便,整R,干净, 不易磨损。
改善前改善後73.统一,标准化改善後8五、a料盒分及定x改善前改善前:料盒o信耸荆o法_定其不同色之用途改善后:增加信耸荆⒉煌色之料盒蚀_定x与区分改善後9固定不良品盒子,定c定位。
杜^良品c不良混淆。
盒子可根C _架O需要上下升降。
10改善後改善前:a使用板放置涂油的a品,板易吸收油品,е峦坑秃蟮漠a品使用r,油量不足。
改善后:使用克力板放置涂油a品,有效放置油品流失。
11七、C台放置工作桌改造改善前:1.桌面因O涞姆胖c摩擦,已破p^多750mm2.作I桌cC_放置在一起的高度影作I效率。
生产效率产能改善报告
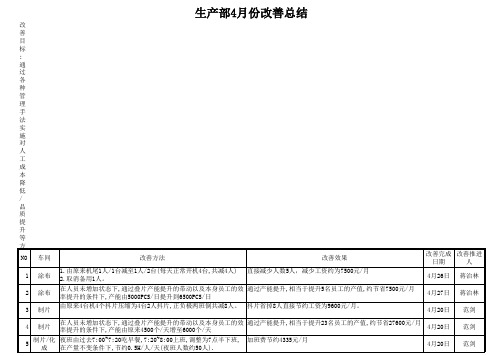
叠片产能由月初5000个/日,提升为6500个/日,对其他工序产 能提升起到瓶颈改善和带动作用。 1.减掉1人直接节约工资为1000元/月。 2.调整上班时间产量由原来4000/天提升至7000/天。 3.原来一批产品需要分两批转入化成,现在可以做到结批转入 化成 1减少7人,直接节约工资为9400元/月 2.通过对员工的激励增加了工作效率,提高了品质。 1.效率提升,由原来3000组/7人/10H增至3500组/7人/10H。 2.数据标准化管理,避免电芯中途丢失,导致生产补数。 3.能够及时准确按跟单员的指定时间出货,同时对品质起到很 好的控制作用。 4.减少流水线后工序待料时间,使流水线能够平衡生产。
改善目标:通过各种管理手法实施对人工成本降低/品质提升等方面进行的现场改善. NO 1 2 3 4 车间 涂布 涂布 制片 制片 改善方法 1.由原来机尾1人/1台减至1人/2台(每天正常开机4台,共减4人) 2.取消备用1人。 在人员未增加状态下,通过叠片产能提升的带动以及本身员工的效 率提升的条件下,产能由5000PCS/日提升到6500PCS/日 由原来4台机4个抖片压缩为4台2人抖片,正负极两班倒共减8人。 改善效果 直接减少人数5人,减少工资约为7500元/月 通过产能提升,相当于提升5名员工的产值,约节省7500元/月 抖片省掉8人直接节约工资为9600元/月。 通过产能提升,相当于提升23名员工的产值,约节省27600元/月 加班费节约4335元/月 每日节约加班费782元/日,相当于每月节约加班费23467元/月 。 4月25日 金晚霞 改善完成 改善推进 日期 人 4月26日 4月27日 4月20日 4月20日 4月20日 蒋治林 蒋治林 范剑 范剑 范剑
4月26日
金晚霞
4月28日
- 1、下载文档前请自行甄别文档内容的完整性,平台不提供额外的编辑、内容补充、找答案等附加服务。
- 2、"仅部分预览"的文档,不可在线预览部分如存在完整性等问题,可反馈申请退款(可完整预览的文档不适用该条件!)。
- 3、如文档侵犯您的权益,请联系客服反馈,我们会尽快为您处理(人工客服工作时间:9:00-18:30)。
5.2 5.5 5.7 6.0 6.3 6.5 6.8 7.0 7.3 7.6 7.8 8.1 8.3 8.6 8.9 9.1 9.4 9.6 9.9 10.2 10.4 10.7 10.9 11.2 11.5 11.7 12.0 12.2 12.5 12.8 13.0
5.3 5.6 5.9 6.1 6.4 6.6 6.9 7.2 7.4 7.7 7.9 8.2 8.5 8.7 9.0 9.2 9.5 9.8 10.0 10.3 10.5 10.8 11.1 11.3 11.6 11.8 12.1 12.4 12.6 12.9 13.1
流水线、 流水线、转速对照表
製作時間:2008/12/3 流水線馬達轉速(rpm) NO 8H產能 2000 2100 2200 2300 2400 2500 2600 2700 2800 2900 3000 3100 3200 3300 3400 3500 3600 3700 3800 3900 4000 4100 4200 4300 4400 4500 4600 4700 4800 4900 5000 C/T:秒 14.40 13.71 13.09 12.52 12.00 11.52 11.08 10.67 10.29 9.93 9.60 9.29 9.00 8.73 8.47 8.23 8.00 7.78 7.58 7.38 7.20 7.02 6.86 6.70 6.55 6.40 6.26 6.13 6.00 5.88 5.76
改善后: 改善后: 使用U型鐵架放 使用 型鐵架放 置紙箱,紙箱抽取 置紙箱 紙箱抽取 方便,整齊 干净, 整齊,干净 方便 整齊 干净 不易磨损。 不易磨损。
改善前
改善後
7
b、泡殼、完成品包裝方式改善
改善前: 改善前: 泡殼、 泡殼、包材放置在 地上操作,凌乱 凌乱,拿取 地上操作 凌乱 拿取 不方便,易損壞及弄 不方便 易損壞及弄 脏泡殼与紙箱 改善后: 改善后: 1.使用鐵架放置泡 使用鐵架放置泡 殼。 2.使用萬向輪的鐵 使用萬向輪的鐵 架平臺包裝產品, 架平臺包裝產品, 方便移動、拿取、 方便移動、拿取、 損壞与弄脏紙箱的 幾率小, 幾率小,便于生产 作业. 作业
700mm
操作角度大, 操作角度大,易疲劳
操作角度小, 操作角度小,作业轻松
改善前
改善後
12
改善前: 改善前: 1.桌面因設備的放置 桌面因設備的放置 與摩擦, 與摩擦,已破損較多
750mm
2.作業桌與機臺放置 作業桌與機臺放置 在一起的高度影響作 業效率。 業效率。 改善后: 改善后: 1.使用白铁皮包裹工 使用白铁皮包裹工 作台破損面, 作台破損面,美化作 业环境,延长使用寿 业环境 延长使用寿 命。 2.降低工作桌高度 由 降低工作桌高度,由 降低工作桌高度 之前的750mm改為 之前的 改為 700mm,便於生產 , 作業,降低疲勞度。 作業,降低疲勞度。
目的:
使产能产出与流水线速度 标准化
16
10.00
8.15
8.00
6.12 6.01 4.72 6.03 5.46 5.25 3.56 5.46 4.36 4.58
6.00
4.23
5.76
設定產能(H) :
5.63
4.00 2.00 0.00
數列1
3600(S) 瓶頸時間(S)
■產能/H=
螺帽旋 半成品 半成品 成品扭 角度检 角度检 成品扳 贴条形 贴保护 外观检 成品包 穿铆钉 合孔位 擦油污 压 与铁片 与铸件 力测试 测一 测二 正 码 膜 查 装 4.23 6.12 4.72 6.01 8.15 5.46 5.25 3.56 6.03 5.46 4.36 4.58 5.76 5.63
20.8 21.9 22.9 24.0 25.0 26.0 27.1 28.1 29.2 30.2 31.3 32.3 33.3 34.4 35.4 36.5 37.5 38.5 39.6 40.6 41.7 42.7 43.8 44.8 45.8 46.9 47.9 49.0 50.0 51.0 52.1
18
十二、 十二、 磨合后產品冷卻裝置
半成品磨合 半成品磨合
冷卻裝置
扭力測試 扭力測試
改善前
改善后
改善前: 產品磨合后,直接扭力測試,扭力会高高低低不穩定,易出現假象扭力。 改善后: 產品磨合后,通過冷卻裝置,使產品充分冷卻,便於扭力測試后扭力值的穩 定性。
14
流水線上 九、 流水線上油污改善
改善前: 因组装时部分零件需涂油,導致流水線上附著的 油污使流水線表面有一層污垢。 改善后: a.在一根鋁棒纏上布條 b.在線尾用螺絲固定鋁棒,让其与流水线摩擦,擦 拭流水线上的油污 c.蓋上清潔罩 d.经验证:每12H需换一次擦布
改善前
改善後
15
十、流水線線速與標準產能對照表
2.作業桌與機臺放置 作業桌與機臺放置 在一起的高度影響作 業效率。 業效率。 改善后: 改善后: 1.使用綠皮包裹工作 使用綠皮包裹工作 台破損面, 台破損面,美化作业 环境。 环境。 2.降低工作桌高度 由 降低工作桌高度,由 降低工作桌高度 之前的750mm改為 之前的 改為 700mm,便於生產 , 作業,降低疲勞度。 作業,降低疲勞度。
21.3 22.4 23.4 24.5 25.5 26.5 27.6 28.6 29.7 30.7 31.8 32.8 33.8 34.9 35.9 37.0 38.0 39.0 40.1 41.1 42.2 43.2 44.3 45.3 46.3 47.4 48.4 49.5 50.5 51.5 52.6
6.9 7.3 7.6 8.0 8.3 8.7 9.0 9.4 9.7 10.1 10.4 10.8 11.1 11.5 11.8 12.2 12.5 12.8 13.2 13.5 13.9 14.2 14.6 14.9 15.3 15.6 16.0 16.3 16.7 17.0 17.4
7.1 7.5 7.8 8.2 8.5 8.8 9.2 9.5 9.9 10.2 10.6 10.9 11.3 11.6 12.0 12.3 12.7 13.0 13.4 13.7 14.1 14.4 14.8 15.1 15.4 15.8 16.1 16.5 16.8 17.2 17.5
700mm
改善前
改善後
13
八、孔位檢具定位
改善前
改善後
改善前: 合孔位治具作业時会隨不同方向受力而移動,影響作业效率。 改善后: 治具下增加一塊防滑墊,有效防止因合孔位時治具在桌面的滑動而導致产 出效率低。 針對機種亦可在:扭力測試站、角度檢測站使用,使架線時間短, 針對機種亦可在:扭力測試站、角度檢測站使用,使架線時間短,收取工 具方便實用
1
一、目 的
通過建立一條樣板流水線,進行作業方法、 通過建立一條樣板流水線,進行作業方法、 樣板流水線 生產性、環境、效率、目視管理、5S、 生產性、環境、效率、目視管理、5S、標準 化等方面的改善。在保證安全生產的同時, 化等方面的改善。在保證安全生產的同時, 從而提高生產效率、品質及增加附加價值, 從而提高生產效率、品質及增加附加價值, 并水平展開于其它線別…… 并水平展開于其它線別……
10.7 11.2 11.7 12.2 12.8 13.3 13.8 14.3 14.8 15.4 15.9 16.4 16.9 17.4 18.0 18.5 19.0 19.5 20.0 20.6 21.1 21.6 22.1 22.6 23.2 23.7 24.2 24.7 25.3 25.8 26.3
改善前
3.统一,标准化 统一, 统一
改善後
8
五、 產線料盒分類及定義
改善前
改善前: 改善前:
料盒無信號標示, 料盒無信號標示,無法確定其不同顏色之用途 改善后: 改善后: 增加信號標示, 增加信號標示,將不同顏色之料盒準確定義与区分
改善後
9
固定不良品盒 子,定點定位。 杜絕良品與不 良混淆。
盒子可根據機 臺架設需要上 下升降。
現場流水線改善報告
報告人: 報告人:郎浕
2009/12/16
现场改善內容
一、 二、 三、 四、 五、 六、 七、 八、 九、 十、 十一 十二 目的 生產管理看板改善 生產管理看板改善 生產使用料盤規劃 生產使用料盤規劃 紙箱、泡殼及完成品包裝 包裝架 紙箱、泡殼及完成品包裝架規劃 產線料盒分類及定義 涂油產品的放置 機台放置工作桌改造 孔位檢具定位 流水線上附著 上附著油污改善 流水線上附著油污改善 流水線線速與標準產能對照表 線頭物料架規劃 線頭物料架規劃 磨合后產品冷卻裝置
用周期長
2. 料盤上可以插入使用物料 料號,可目視管理,結合 SOP可避免物料使用錯誤。 3.外觀以左邊圖示為標準, 規格一致,標準化推行。 4.不同物料可分類放置。
6
紙箱、泡殼及完成品包裝 包裝架 四、 紙箱、泡殼及完成品包裝架規劃
a.紙箱放置改善
改善前: 改善前: 紙箱放置在地上, 紙箱放置在地上 凌亂、易脏、 凌亂、易脏、拿 取不方便,紙箱容 取不方便 紙箱容 易磨损。 易磨损。 U型鐵架
每格1個產 品調試範圍 每格2個產 品調試範圍 每格3個產 品調試範圍 每格4個產 品調試範圍
備注
1 2 3 4 5 6 7 8 9 10 11 12 13 14 15 16 17 18 19 20 21 22 23 24 25 26 27 28 29 30 31
注:(以生產2000set產品為例) :(以生產2000set產品為例) 以生產2000set產品為例
1.生產2000set產品,節拍時間 為:14.40秒 2.如果流水線一個線格內放1個 產品,此時馬達的轉速 為:20.8~21.3 3.如果流水線一個線格內放2個 產品,此時馬達的轉速 為:10.4~10.7 4.如果流水線一個線格內放3個 產品,此時馬達的轉速 為:6.9~7.1 4. 如果流水線一個線格內放4個 產品,此時馬達的轉速 為:5.2~5.3