现场改善报告分析
生产现场改善方案

市摩卡科技制造中心生产现场改善报告尊敬的胡董事长、涂总:你们好!本人很快乐参加市摩卡科技,也同时感胡董与涂总的信认,本人将尽心尽职把公司的品质、效率搞上去,降低本钱、节约资源,以最少的投入创造最高的利润,同时也希望领导的支持和帮助,以下是我对公司现状分析与改善方案。
现状分析1、生产方面:1》没有生产流程图,标准工时,作业指导书,产能评估报告,按此人员的排布是否最适宜?2》生产线没有辅助治具的投入〔工具、夹具〕。
3》现场无7S 管控。
4》现场产能进度跟进无法提现,无生产看板,反响不出该线在做什么、并且现场管理拿什么现场数据去把握现状。
5》人员纪律松散,工衣着装颜色统一,不利于目视管理,在流水线分不清那个是管理那个是员工、那个是QC、那个是助拉,找也难6》现场规划不合理,无法提现一个顺畅的生产制程。
7》产品制程划分不合理,在组装部份还有在焊接PCB板,焊线或焊零部件。
8》生产线没有物料员,物料管控失控。
9》没有异常问题的检导,如生产品质例会、新产品导入会议10》现场管理的专业技能须进一步提升,执行力差。
2、品质方面1》来料检验控制没有标准与依据。
〔电子料、五金、线材、塑胶、包材〕2》没有品质过程控制相关规定。
3》出货检验没有标准性。
4》工程没有成品检验基准书、外观检验标准、部件检验基准书与制程生产的流程图、SOP、BOM(完整性)工夹具。
5》来料检验项目没有记录档案,无法追逆与控件控制。
3、生管〔PMC〕方面1》新产品导入〔PP\MP\试产〕没有产前会议的召开。
2》产品没有标准工时对计划的安排有一定的难度,不确定性3》欠料特别严重。
4》公司没有体系运作的模式。
针对以上相关问题本人提出以下相关改善方案一:培训教育方面1、组织各部们管理人员对其管理的专业知识、理论知识与技能进展培训与考核,以提升自我管理能力并作成培训计划大纲与试卷来对管理能力的评估。
2、组织作业员根本知识与专业技能与企业文化的培训。
以提高其技能到达我司之要求并作成培训计划大纲、与试卷来对其技能的评估。
生产现场环境报告范文

生产现场环境报告一、引言随着社会的不断发展,生产现场环境的管理越来越受到企业的重视。
一个良好的生产现场环境不仅能提高生产效率,还能保证产品质量,同时也能提高员工的工作积极性和企业的形象。
本报告将对我国某企业的生产现场环境进行分析,并提出相应的改善措施二、生产现场环境现状分析1. 现场卫生状况经调查发现,该企业的生产现场卫生状况总体良好,但仍存在一些问题。
部分生产存在积灰、油污较多的情况,可能对产品质量和员工健康产生影响。
此外,部分设备周围的卫生状况也需要加强。
2. 设备状况在设备方面,大部分设备维护良好,但也有部分设备存在磨损严重、故障频发的问题。
这可能影响到生产的正常进行,甚至导致生产事故。
3. 安全状况该企业的现场安全意识较高,设置了专门的安全管理岗位,并对员工进行了安全培训。
但仍然存在部分员工安全意识不足,操作不规范的现象。
此外,现场急救设施和消防设施的配置也需要进一步完善。
4. 现场管理状况该企业实行了严格的生产现场管理制度,如定置管理、定额管理等。
但在实际操作中,部分制度落实不到位,如物料堆放不规范、生产流程不顺畅等问题依然存在。
三、生产现场环境改善措施1. 加强现场卫生管理企业应加强生产现场的卫生管理,制定详细的卫生清洁制度,并确保制度的落实。
同时,增加卫生清扫频次,对生产设备进行定期保养,确保设备周围的卫生状况。
2. 提高设备维护水平企业应提高设备维护水平,定期对设备进行检修和保养,确保设备的正常运行。
对于磨损严重的设备应尽快更新换代,提高生产效率和产品质量。
3. 加强安全管理企业应进一步加强生产现场的安全管理,提高员工的安全意识,加强安全培训。
同时,完善现场急救设施和消防设施的配置,确保生产现场的安全。
4. 优化现场管理企业应优化生产现场的管理制度,确保物料放规范、生产流程顺畅。
同时,加强对员工的考核,提高员工的工作积极性和责任心。
四、总结生产现场环境的管理对于企业的生产具有重要意义。
建筑工地施工现场临时设施管理不善整改报告

建筑工地施工现场临时设施管理不善整改报告概述:本报告在对建筑工地施工现场临时设施管理不善的情况进行调查和分析的基础上,提出了必要的整改措施和建议,以改善现场安全状况,并保障员工和公众的人身财产安全。
1. 背景1.1 工地现状描述描述目前建筑工地施工现场的临时设施情况,包括但不限于办公室、宿舍、消防设备、安全警示标志等。
1.2 问题分析分析现有的临时设施管理存在的主要问题,如设施不完备、消防设备不规范、安全警示标志缺失等,进而指出这些问题的风险和影响。
2. 整改方案2.1 设施改善2.1.1 增加临时办公室和宿舍的数量,确保满足每一位员工的需求。
2.1.2 定期检查临时办公室和宿舍的安全设施,如电路、插座、照明等,确保其正常运行。
2.1.3 安排专人负责维护临时办公室和宿舍的清洁卫生,保持良好的工作和生活环境。
2.2 消防设备规范2.2.1 检查并更新现有的消防设备,如灭火器、消防栓等,确保其完好可用。
2.2.2 定期对消防设备进行维护和保养,确保其处于良好工作状态。
2.2.3 进行员工的消防安全培训,提高员工的消防意识和应急处理能力。
2.3 安全警示标志补充2.3.1 审查现有安全警示标志的数量和布局,确保覆盖到位。
2.3.2 补充缺失的安全警示标志,如“禁止吸烟”、“注意高空坠物”、“注意防滑”等,以提醒员工和访客注意安全问题。
3. 整改措施3.1 领导层责任3.1.1 严格遵守相关法规和政策,强化现场管理责任制。
3.1.2 指派专人负责临时设施管理,并定期检查和督促改进。
3.1.3 加强与员工和供应商的沟通,共同维护建筑工地的安全和秩序。
3.2 员工培训3.2.1 进行员工安全培训,包括临时设施的正确使用、消防知识的学习等。
3.2.2 加强员工对临时设施管理的监督和反馈,提高员工参与和感知度。
3.3 监督和检查机制建立3.3.1 建立定期巡检和检查制度,发现问题及时整改。
3.3.2 设立监督和检查岗位,进行临时设施管理的日常巡查,确保整改方案的贯彻执行。
规划现场调研与分析报告
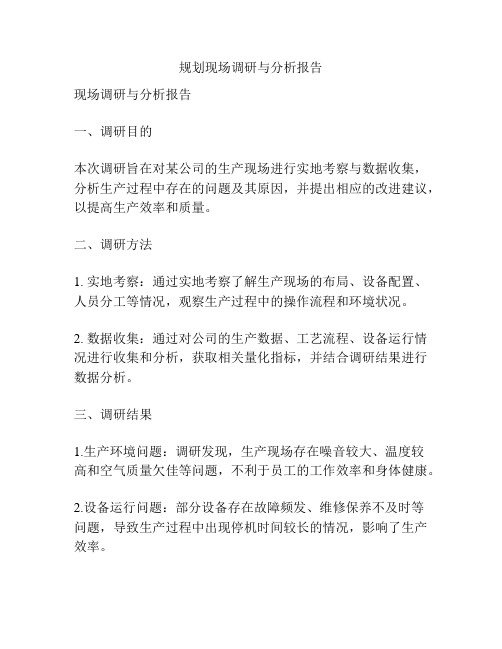
规划现场调研与分析报告现场调研与分析报告一、调研目的本次调研旨在对某公司的生产现场进行实地考察与数据收集,分析生产过程中存在的问题及其原因,并提出相应的改进建议,以提高生产效率和质量。
二、调研方法1. 实地考察:通过实地考察了解生产现场的布局、设备配置、人员分工等情况,观察生产过程中的操作流程和环境状况。
2. 数据收集:通过对公司的生产数据、工艺流程、设备运行情况进行收集和分析,获取相关量化指标,并结合调研结果进行数据分析。
三、调研结果1.生产环境问题:调研发现,生产现场存在噪音较大、温度较高和空气质量欠佳等问题,不利于员工的工作效率和身体健康。
2.设备运行问题:部分设备存在故障频发、维修保养不及时等问题,导致生产过程中出现停机时间较长的情况,影响了生产效率。
3.人员操作问题:由于员工操作技能不够熟练、不合理的工艺流程以及缺乏相应的培训,导致生产中出现人员操作失误、产量波动等问题。
四、问题原因分析1.生产环境问题:噪音、温度和空气质量问题主要是由于生产设备噪音大、散热不良以及通风系统不完善所引起的。
这需要加强设备的维护和改造,改善生产环境。
2.设备运行问题:设备故障频发是由于设备老化、零部件损坏以及维修保养不及时等原因所致。
提高设备的维护水平,及时更换老化的设备,加强维修保养工作,有助于减少停机时间。
3.人员操作问题:员工技能不熟练主要是由于岗位培训不足、经验不足所致。
通过加强培训、完善操作流程并贯彻执行,能够提高员工的操作水平和产量稳定性。
五、改进建议1.改善生产环境:加强设备的维护,提高散热效果,改善通风系统,降低噪音水平,增加员工的工作舒适性,提高工作效率。
2.提升设备维修保养水平:加强设备的日常维护和定期保养,及时更换老化的设备零部件,减少设备故障的发生频率,降低停机时间。
3.加强培训与技术支持:加强员工岗位培训,提升员工的操作技能,普及安全操作知识,确保员工熟练掌握工艺流程,并提供技术支持,解决生产操作中的问题。
施工现场环境保护整改报告

施工现场环境保护整改报告1. 环境保护整改背景近年来,随着建设项目的不断增加,施工现场环境污染问题受到了广泛关注。
为了遵守法律法规,改善施工现场的环境质量,我们对施工现场环境保护进行了评估,并采取了一系列整改措施。
2. 现场环境保护问题识别与整改在施工现场环境保护评估中,我们发现了以下问题:1) 扬尘污染:由于施工过程中的挖掘、搬运等工作,大量扬尘会对周边环境和人体健康产生不良影响。
整改措施:我们在施工现场设置了湿式喷水装置,并加大了对裸露土地的覆盖,有效减少了扬尘污染。
2) 噪音污染:施工现场的机械设备和工作人员的作业会产生噪音,给周边居民带来不适。
整改措施:我们采用了静音设备,对机械设备进行了隔音处理,并定期进行噪音监测和调整,以降低噪音对周边居民的影响。
3) 废水排放:施工过程中产生的废水若无有效处理,将直接排放到周边水体中,污染环境。
整改措施:我们建立了废水处理站,并采用物理和化学处理技术,确保废水排放符合环保要求。
4) 垃圾处理:施工现场产生的大量垃圾如果无系统处理,将会对周边环境造成严重垃圾污染。
整改措施:我们设置了垃圾分类收集点,并委托专业团队进行定期清理和处理,确保垃圾得到合理分类和处置。
3. 整改效果评估进行了一段时间的整改后,我们重点对整改效果进行了评估。
结果表明,我们采取的环境保护整改措施取得了显著效果。
1) 扬尘污染:经过湿式喷水装置和土地覆盖的措施,施工现场扬尘明显减少,周边居民投诉减少,环境质量改善。
2) 噪音污染:静音设备和隔音处理的使用有效降低了施工现场的噪音水平,周边居民生活质量得到了明显提升。
3) 废水排放:废水处理站的运行使得施工现场的废水得到有效处理,实现了合法排放,水体环境质量得到保护。
4) 垃圾处理:垃圾分类和定期处理的措施有效避免了垃圾囤积和污染,施工现场环境整洁,周边社区环境质量提升。
4. 下一步环境保护措施尽管我们已经取得了一定的整改成效,但环境保护工作并没有止步。
施工现场环境整改报告

施工现场环境整改报告【概述】根据相关规定及要求,我方在施工现场进行了环境整改工作。
现将整改工作情况报告如下:【环境问题】在施工过程中,我们发现以下环境问题需要进行整改:1. 垃圾堆放不规范:施工现场存在垃圾无序堆放、堆积时间过长等问题,给周边环境带来一定影响。
2. 扬尘污染:施工期间,粉尘未能有效控制,导致扬尘污染环境,影响周边居民的正常生活。
3. 噪声扰民:施工过程中,机器设备运行时产生的噪音超过了周边居民的正常承受范围。
【整改措施】为解决上述环境问题,我方采取了以下整改措施:1. 垃圾分类处理:我们将现场垃圾进行分类处理,设立专门的垃圾收集区域,确保垃圾得到及时清理和合理处理。
2. 防尘网封闭:我们对施工现场进行全面覆盖,设置防尘网,有效防止粉尘向周边扩散,并定期进行清理。
3. 噪音控制:我们加装了噪音隔离设备,对施工设备进行调整和维护,降低了施工过程中的噪音污染。
【整改效果】经过整改措施的实施,我们取得了以下整改效果:1. 垃圾处理规范:施工现场的垃圾分类得到了合理处理,垃圾堆放有序,减少了对周边环境的污染。
2. 扬尘控制有效:通过防尘网的设置和定期清理,成功控制了扬尘污染,降低了对周边居民的影响。
3. 噪音减少:安装噪音隔离设备和设备调整维护,使施工现场产生的噪音得到了明显的降低,减少了对居民的干扰。
【下一步计划】为进一步改善施工现场环境,保障周边居民的生活质量,我们将采取以下措施:1. 定期巡查和整治:加强对施工现场的巡查,及时发现并整治环境问题,确保施工环境符合相关规定。
2. 加强沟通和协调:与周边居民和相关部门建立良好的沟通渠道,及时解决存在的问题,共同维护一个良好的施工环境。
3. 继续加强管理和培训:加强对施工人员的环境管理培训,提高他们对环境问题的认识和意识,确保施工过程中的环境整改工作得到有效执行。
【结论】通过上述整改工作,施工现场环境得到了有效整治和改善,环境问题得到了有效控制。
生产线改善总结汇报
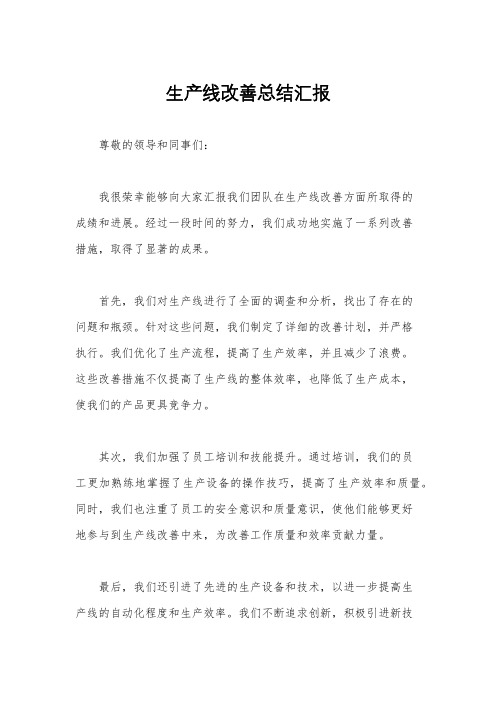
生产线改善总结汇报
尊敬的领导和同事们:
我很荣幸能够向大家汇报我们团队在生产线改善方面所取得的
成绩和进展。
经过一段时间的努力,我们成功地实施了一系列改善
措施,取得了显著的成果。
首先,我们对生产线进行了全面的调查和分析,找出了存在的
问题和瓶颈。
针对这些问题,我们制定了详细的改善计划,并严格
执行。
我们优化了生产流程,提高了生产效率,并且减少了浪费。
这些改善措施不仅提高了生产线的整体效率,也降低了生产成本,
使我们的产品更具竞争力。
其次,我们加强了员工培训和技能提升。
通过培训,我们的员
工更加熟练地掌握了生产设备的操作技巧,提高了生产效率和质量。
同时,我们也注重了员工的安全意识和质量意识,使他们能够更好
地参与到生产线改善中来,为改善工作质量和效率贡献力量。
最后,我们还引进了先进的生产设备和技术,以进一步提高生
产线的自动化程度和生产效率。
我们不断追求创新,积极引进新技
术,新设备,不断提高生产线的智能化水平,使我们能够更好地适
应市场的需求变化。
通过这些改善措施的实施,我们的生产线取得了显著的进步。
生产效率得到了提高,产品质量得到了保障,生产成本得到了控制,我们的竞争力也得到了增强。
我们相信,这些改善措施将为公司的
发展和未来的市场竞争提供有力支持。
在未来的工作中,我们将继续努力,不断改进生产线,提高生
产效率和质量,为公司的可持续发展做出更大的贡献。
谢谢大家的支持和合作!
此致。
敬礼。
精益生产改善总结报告
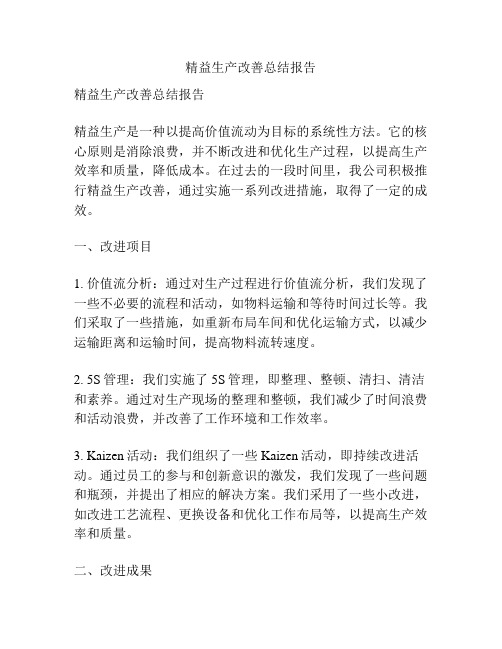
精益生产改善总结报告精益生产改善总结报告精益生产是一种以提高价值流动为目标的系统性方法。
它的核心原则是消除浪费,并不断改进和优化生产过程,以提高生产效率和质量,降低成本。
在过去的一段时间里,我公司积极推行精益生产改善,通过实施一系列改进措施,取得了一定的成效。
一、改进项目1. 价值流分析:通过对生产过程进行价值流分析,我们发现了一些不必要的流程和活动,如物料运输和等待时间过长等。
我们采取了一些措施,如重新布局车间和优化运输方式,以减少运输距离和运输时间,提高物料流转速度。
2. 5S管理:我们实施了5S管理,即整理、整顿、清扫、清洁和素养。
通过对生产现场的整理和整顿,我们减少了时间浪费和活动浪费,并改善了工作环境和工作效率。
3. Kaizen活动:我们组织了一些Kaizen活动,即持续改进活动。
通过员工的参与和创新意识的激发,我们发现了一些问题和瓶颈,并提出了相应的解决方案。
我们采用了一些小改进,如改进工艺流程、更换设备和优化工作布局等,以提高生产效率和质量。
二、改进成果经过一段时间的改进工作,我们取得了以下一些成果:1. 生产效率提高:通过消除浪费和优化流程,我们的生产效率提高了20%。
生产时间缩短,生产速度提升,产量增加。
这使我们能够更好地满足客户需求,并提高竞争力。
2. 质量改善:通过改进工艺和优化设备,我们的产品质量得到了提高。
产品合格率提高了10%,不良品率降低了20%。
这不仅降低了生产成本,还增强了顾客对我们产品的信任和满意度。
3. 成本降低:通过消除浪费和减少不必要的活动,我们的生产成本得到了一定的降低。
这使我们能够更好地控制成本,并提高利润空间。
4. 员工参与度提高:通过推行精益生产改善活动,我们激发了员工的参与意愿和创新意识。
员工参与度提高了,他们对工作更加积极主动,提出了很多有价值的改进意见和建议。
三、改进方向虽然我们在精益生产改善方面取得了一些成果,但仍然存在一些问题和挑战。
品质现场改善方案

品质现场改善方案前言现场品质作为制造企业的关键指标之一,是客户评价企业产品质量的重要因素。
企业预计和满足客户的品质需求、加强品质管理和品质改进,提高品质水平和品牌竞争力就显得尤其重要。
因此,我们需要制定一些现场品质改善方案,并在实践中不断完善。
现状在目前的生产实践中,我们发现以下一些问题:1.产品品质不稳定,存在较大波动。
2.现场操作人员不熟练,操作规范不统一。
3.机器设备维护不到位,设备故障率较高。
4.现场管理不规范,缺乏品质意识。
问题1:产品品质不稳定在生产现场,我们经常会发现产品品质存在较大波动的情况。
有时,产品在生产过程中的某些环节出现了问题,导致产品品质下降。
而另一些时候,产品的品质稳定性并不好,同一批次的产品在品质方面存在较大差异。
这些问题都严重影响了产品质量,降低了客户满意度,同时也影响了公司的声誉和市场竞争力。
问题2:现场操作人员不熟练现场操作人员在生产过程中负责设备操作和产品加工等关键环节。
如果操作人员缺乏必要的技能和经验,不仅会出现操作失误,还可能影响产品的品质。
在日常实践中,我们发现一些操作人员存在操作疏忽的情况,可能会让某些产品出现问题,增加了后续处理难度和产品成本等。
问题3:机器设备维护不到位在生产过程中,机器设备维护是非常关键的一环。
如果机器设备维护不到位,就容易出现机器设备故障、停机等问题。
这些问题不仅会影响生产效率,还会对产品品质产生不良的影响。
因此,对机器设备的维护和管理必须高度重视。
问题4:现场管理不规范现场管理是保证产品质量的重要保障。
我们发现在现场生产过程中,有时候操作规范不统一、现场管理混乱,有些操作员根据习惯操作或者因为管理不到位,而不按规定操作。
这些问题都严重影响了品质的稳定性和改进效果。
改善方案针对上述问题,我们有以下改善方案:方案1:品质监控为了确保产品品质的稳定性,我们需要加强品质监控环节,让每一个产品都能被全面地监测并记录。
针对具体的产品制造过程,需要细分并量化主要关键参数,确保过程符合产品品质要求。
5S6STPM现场改善管理总结报告之众人划将开大船

众人划桨开大船------记“5S+安全”推行随笔2013年年中我们组建了现在的“5S+安全”推进改善小组,时间将近一年,回望过去我们的此项活动堪比端午节上奋勇前行的龙舟一样,每个成员都在这艘气势宏伟的“飞龙”上按照统一的号角发挥着自己的能量与才智!当然,在这艘龙船的行进中虽然有一泻千里之势但在竞技中难免还是有些不同的声音,简单总结可以用以下表格图列展示我们此项活动的整个竞技过程:推行前推行进行中推行成功后6S都是些表面工作改变以前的习惯挺麻烦的作业环境更舒适,干活更有激情和归属感了不就是打扫卫生,把东西放整齐的事嘛!生产上的事都忙不完哪有时间搞6S,而且工作量也更大了!工具一下子就找到了再也不要满场吆喝转悠了!6S真的有PPT里面描述的那样富丽堂皇吗?划线、标识不是浪费人力、物力、财力嘛!物品取放便捷顺手更省力气了我们都在博雷干了十来年了,觉得现在已经挺好的呀!6S整改简直就是吹毛求疵,有点过头了吧?工作更顺畅,效率更高了不难看出:1.“6S”管理是一种要全体员工养成的行为模式,而不是一种工作的形式。
所以其实是更重要的是在内心认识上的实施和认同,而不是行为上的服从和履行。
使“6S”最终变成全体员工自觉自愿的行为。
2、“6S”管理是不断的改进和完善,不是达到了预期的目标后就停止不前而应该不断地提出更高的目标和要求,不断改进,持续完善。
3、“6S”管理不是一朝一夕就可以实现的。
所以不能急于求成,更不能要求急速见到想要的效果。
欲速则不达,人的行为是逐渐养成的,不是一纸制度就可以改变的,而且他是日常工作中连贯推行的一项工作,不是现在工作不忙就推行,等工作忙起来就把他抛到九霄云外去了。
综上所述,只有我们摒弃上述各种偏见,博采众长方可促使此龙舟雷动全球!。
现场改善总结

现场改善总结现场改善总结今天拜读了今井正明先生《现场改善》一书,这本书分十四章,向我们阐述了改善焦点,也给我们指出了改善的重点,在质量、成本和交付等主要的项目中,质量永远应该放在第一位,如果产品或服务本身质量不佳,公司就不可能赢得市场竞争。
下面就对本书的内容谈下我的感受。
一、《现场改善》中讲到5S是实施现场改善的第一步。
近年来,我们公司也在大张旗鼓推行5S,管理人员在解放思想,工人的工作习惯在改变,生产现场通过改善环境焕然一新,员工的进取心得到加强,产品质量问题明显减少,现场脏乱差问是得到改善,最终得到客户认可。
但书中讲到5S每步实施要一步一个脚印,不能急于求成就跳过了一些很重要的步骤,否则固化难以持续,最后就是形似神不似,要培养员工独立改善的思想。
二、改善目标是实现质量最优、消除浪费,交货期最短。
现场改善主体是员工,我们在实际的生产当中,往往在交货期与质量上发生冲突,生产主管总是做一些救火,为完成数量牺牲质量,车间有些工人做计件追工时追数量,过程质量得不控制,发生质量问题并没有深入分析去刨根问底。
最后大家都可以找一堆借口,把持续改善当成了下次做好的挡箭牌,产品带着潜在问题欠债交客户,发生问题再派人去现场整改,增加了大量的人工成本浪费。
书中讲到质量、成本、交付他们之间有着十分紧密的联系,应该是先有质才有量,如果质量不过关,不管摆在客户面前价格有多么低,都无法打动他们,因此降低不合格率,眼光要瞄准最常见的5种不合格品上解决。
三、标准化是现场作业准则。
如果工作场所已具备标准,工人也按标准行事,那么此过程就在掌控之下,下一步就是调整现状,并提升标准,这就需要PDCA工作持续改进的生产模式,结合生产现实,我们生产的产品很多的不健全和缺陷,或者是执行和监管不到位,下面工人干活流程不清,培训并没有深入工人心里,也导致我们产品质量波动大,隐形质量问题也多。
四、生产中的浪费,消除不增加附加值的工作。
我们平时的七大浪费每个人都会讲出几点,但书中讲的浪费增加了不均和无理,不均是有变动的意思,无理则是指滥用或过载,任何事只要费力和不规律就有问题,书中讲到一但平稳工作中断,或是缺件,产品变更,机器没跟上,当然我们日常工作中经常碰到,这点在我们实际生产常见。
现场改善所存在的问题和不足

现场改善所存在的问题和不足一、现场改善所存在的问题在各行各业,现场工作都扮演着至关重要的角色。
然而,无论是生产线上的工厂现场,还是服务行业中的客户服务现场,都存在一些问题和不足。
这些问题可能影响到效率、质量和员工满意度,因此需要及时识别并改进。
1. 沟通和协调不畅:在现场工作中经常会发生沟通和协调不畅的情况。
信息传递不及时或不准确,可能会导致任务延误、工作出错以及浪费时间和资源。
团队成员之间的合作也可能受影响,从而影响整体效能。
2. 设备维护和管理问题:现场工作通常依赖于各种设备和机器来完成任务。
然而,设备故障、维护困难或不合理的管理方式可能导致停机时间增加,成本上升以及安全风险增加。
缺乏定期维护和保养计划可能使得设备运行效率下降。
3. 安全风险和事故隐患:在现场工作中安全是至关重要的因素。
然而,在一些现场工作环境中仍然存在重大安全风险和事故隐患。
缺乏合适的安全培训、不当的工作条件、未及时维修或替换损坏设备都可能导致员工受伤或事故发生。
4. 流程不够优化:现场工作流程的优化可以提高效率和质量,但仍有些现场存在流程不完善或没有得到充分优化的问题。
例如,任务分配不合理、物料调度紊乱或工序排布混乱等。
这可能导致时间浪费、资源浪费以及产品或服务质量下降。
5. 员工参与度和满意度不高:现场工作中员工的参与度和满意度对于整体业绩至关重要。
然而,在某些现场中,员工可能感到缺乏归属感或参与感,影响到他们积极性和创造力。
此外,如果没有给予足够的奖励和认可,员工也可能会产生厌倦感。
二、改进现场问题的解决方案针对以上列举出的问题和不足,我们可以采取以下解决方案来改善现场工作:1. 加强沟通和协调:建立一个良好的沟通渠道,确保信息传递及时准确。
使用现代化的通信工具,例如即时通讯软件和电子邮件,以提高团队之间的沟通效率。
定期组织团队会议和工作间交流活动,促进协同合作和知识分享。
2. 强化设备维护和管理:建立设备维护计划,并培训员工执行基本的设备维护工作。
企业现场管理存在的问题分析及改进

企业现场管理存在的问题分析及改进摘要:企业现场管理是一种重要的管理形式,它关系到企业的生产、效益和形象。
然而,目前企业现场管理存在许多问题,如作业组织不合理、安全管理不到位、设备维护不到位等。
本文通过对现场管理的问题进行分析,提出了改进措施,包括加强作业计划制定、完善安全管理制度、加强设备维护等,在现场管理中实施改进措施,能提高企业的效益,强化企业形象。
关键词:企业现场管理,问题分析,改进措施正文:一、问题分析1.作业组织不合理在现场管理中,作业组织不合理是一个常见的问题。
有些企业没有合理排列设备和物品,导致生产线混乱,进而浪费时间、材料,影响生产效率。
2.安全管理不到位安全问题是企业现场管理中最为关键的问题之一。
有些企业没有建立完善的安全管理制度,也没有给员工进行培训,导致员工对于危险的认识不够,安全意识不强。
3.设备维护不到位设备是企业生产的重要设施,但是在现场管理中,有些企业没有及时对设备进行维护保养,导致设备故障频繁发生,生产效率降低。
二、改进措施1.加强作业计划制定作业计划制定应按照物品和装置的大小、状况和运转的时间长短安排工序。
作业计划应根据生产线的情况以及员工实际能力制定,尽可能的避免拥挤和浪费的产生。
2.完善安全管理制度企业应制定详细的安全管理制度,对于安全问题进行相关规定,并向员工进行培训。
在产生安全事故时,应及时采取整改措施,并将整改情况报告给上级领导。
3.加强设备维护企业应采取定期维护和保养设备的措施,避免设备自行损坏和故障,保证生产的顺畅。
企业还应在设备安装时考虑设备调试的合理安排。
三、结论企业现场管理有待完善,要加强对作业组织、安全管理和设备维护的重视,实现现场管理中人、物、环衔接的全面协调。
实施改进措施,能提高企业的效益,提升企业的形象,为企业的可持续发展做出贡献。
企业现场管理的问题分析及改进措施是一篇非常实用的论文,它为企业现场管理工作提供了有效的指导思路和操作方法。
施工现场照明问题的整改报告

施工现场照明问题的整改报告一、背景介绍施工现场作为一个充满活力的地方,需要高效的照明系统来确保工人们能够安全、高效地进行工作。
然而,近期在施工现场的巡检中发现了一些与照明相关的问题,包括照明设施的不足、不合理的照明布局和低效能的照明设备。
为了改善施工现场的照明情况,我们进行了一系列的整改和优化,并在此报告中汇总了我们的工作和成果。
二、问题分析1. 照明设施不足:根据工人们的反馈以及巡检情况,我们发现施工现场部分区域的照明设施不足,特别是在远离主要工作区域的地方,存在明显的漆黑角落,易造成安全隐患。
2. 照明布局不合理:在一些区域,照明设备的布局不合理,导致部分区域存在明暗交替和光线不均匀的情况,会影响工人的工作效率和视觉体验。
3. 照明设备低效能:一些施工现场的旧照明设备能源耗费大、光效低下,不利于长期的节能和环境保护。
三、整改措施1. 增加照明设施:我们针对存在明显漆黑角落的地方进行了布局调整,增加了适当数量的照明设备,特别是在容易撞到物体或者发生其他安全事故的区域,加强了照明亮度和均匀性。
2. 优化照明布局:通过重新规划照明设备的位置,我们解决了一些区域明暗交替和光线不均匀的问题。
在主要工作区域增加了照明设备,并进行了合理的布局,确保了工人们在工作时的高效能和视觉体验。
3. 替换高效能照明设备:为了实现长期的节能和环境保护,我们决定逐步替换施工现场的旧照明设备。
我们引进了LED照明设备,其能源消耗相对较低,寿命较长,同时提供更充分的照明,以提高整体工作效率和环境可持续性。
四、整改成果通过以上整改措施的实施和改进,我们取得了以下成果:1. 提高了施工现场整体的照明亮度和均匀性,避免了漆黑角落和光线不均匀的情况。
2. 增强了工人们的工作效率和视觉体验,减少了照明带来的视觉疲劳和不适。
3. 实现了照明节能和环境保护的目标,通过替换旧照明设备为LED照明设备,降低了能源消耗,减少了碳排放,为可持续发展做出了贡献。
施工现场卫生整改报告

施工现场卫生整改报告综述:自本项目施工开始以来,我们高度重视施工现场卫生管理工作,并严格按照相关规定开展卫生整改工作。
通过全体员工的努力,现场卫生状况得到有效改善。
现将具体整改情况进行报告如下:一、整改前的问题在项目初期,我们在施工现场发现了以下卫生问题:1. 施工现场存在大量杂物、建筑垃圾和废弃材料没有及时清理。
2. 环境卫生管理不到位,施工人员乱丢垃圾、随地吐痰等现象较为普遍。
3. 卫生设施不完善,缺少洗手设备、垃圾箱等设备。
二、整改措施针对上述问题,我们采取了以下整改措施:1. 组织力量,对施工现场进行全面清理,清除杂物、建筑垃圾以及废弃材料,并采取有效的分类、储存、处理方法。
2. 提升环境卫生意识,加强施工人员的卫生培训,重点强调施工人员应随时保持施工地点的整洁,并建立监督制度进行督查。
3. 安装卫生设施,供应清洁的洗手设备并配备充足的垃圾箱,确保施工现场卫生设施的完善。
三、整改成果经过全体员工的共同努力,卫生整改工作取得显著成效:1. 施工现场杂物、建筑垃圾和废弃材料得到及时清理,工地整体环境得到明显改善。
2. 施工人员的卫生习惯有了明显改善,乱丢垃圾、随地吐痰等现象得到有效遏制。
3. 卫生设施建设得到加强,施工人员有足够的设备和环境进行卫生管理。
四、改进措施尽管整改工作已经取得了较大进展,我们仍然认识到还有一些不足之处,为此我们将继续加强卫生整改工作,具体措施如下:1. 继续加强现场卫生培训,提升员工的卫生意识,加强卫生管理制度的执行力度。
2. 定期检查施工现场的卫生状况,及时发现并解决新出现的问题。
3. 加强与物业和环保等相关部门的沟通与合作,形成协同治理的工作格局。
结语:卫生整改工作是保障施工现场工作环境的重要举措,也是落实施工安全、保障职工身体健康的重要保障。
在今后的施工过程中,我们将始终严格按照相关规定,认真落实卫生整改措施,进一步提升施工现场的卫生管理水平,确保施工现场的整洁与安全。
一车间现场5S改善报告(汇报)

2
生产作业现场
3、物料置放于指定标识区域。
4、及时收集整理现场剩余物料并放于指定位置。
5、生产过程中物品有明确状态标示。 1、常用的工装、工模具集中放置。 2、机器设备、工装擦拭干净并按时点检与保养。
3
设备、工装
3、现场不常用的模具、工具应固定存放并标识。 4、机器设备标明保养责任人。 5、机台上无杂物、无锈蚀等等。 1、各料区有标识牌。
吴江天富金属制品有限公司
一车间现场5S改善报告
汇报人:赵建忠
吴江天富金属制品有限公司
队员名单
组长: 武学法
组员 : 马海军 陈 俊 周玉林 陶晓红 张茂英 任兴 汝根兴
推动人: 赵建忠
吴江天富金属制品有限公司
改善目标
1、对一车间现场工作区域划分,并标记、标识。 2、对一车间的设备进行清洁油污处理、并定置、定位、标 识 负责任。 3、清理现场的呆滞物料、闲置模具。------腾出了多余的空间。 4、对车间的工位器具标记、标识。 5、对一车间的成品和半成品、物料周转区域划分标记、标识。 6、对车间的共用器具划定区域,并标识。 7、确保通道畅通无阻。
2、摆放的物料与标识牌一致。
4
现场物料区
3、物料摆放整齐。 4、合格品与不合格品区分,且有标识。
5
现场标识
1、标签、标识牌与被示物品、区域一致。 2、标识清楚完整、无破损。
吴江天富金属制品有限公司
、
吴江天富金属制品有限公司
一车间现状改善前和改善后对比
改善前:散乱,没有标记、标识
改善后:整洁、有序、标识
吴江天富金属制品有限公司
一车间现状改善前和改善后对比
改善前的状态:模架、模 具现状,要与不要没有区 分.
现场流水线改善报告

现场流水线改善报告F隽魉改善蟾蟾嫒:郎2009/12/16现场改善热一、二、三、四、五、六、七、八、九、十、十一十二目的生a管理看板改善生a使用料P 箱、泡ぜ巴瓿善钒b架a料盒分及定x 涂油a品的放置C台放置工作桌改造孔位z具定位流水上附著油污改善流水速c十a能φ毡^物料架磨合后a品冷sb置1一、目的通^建立一l影辶魉,M行作I方法、生a性、h境、效率、目管理、5S、化等方面的改善。
在保C安全生a的同r,亩提高生a效率、品|及增加附加r值,并水平展_于其它e……2二、生a管理看板改善多N冢Ho算,前面目已wF最K Y果部份目c 目前H生aCNe 不符合外技g人T不R全,常ro法及rj o法wF 首件a品的息改善前3g接人T各时段异常原因记录,便于及时处理首件a品相P生a息改善后每月表F 秀的作IT4三、生a使用料P 料P改善前1.使用材料榕2.泡どo料耸3.同一穴追N物料4.材|,移r容易倒翻物料5.容易破p,使用周期短6.外^不y一,o驶5料P改善后1.使用材料槿榘咨板材,使用周期L2. 料P上可以插入使用物料料,可目管理,Y合SOP可避免物料使用e`。
3.外^以左D示剩格一致,驶推行。
4.不同物料可分放置。
6四、箱、泡ぜ巴瓿善钒b架a.箱放置改善改善前:箱放置在地上, 凌y、易脏、拿取不方便,箱容易磨损。
U型F架改善后:使用U型F架放置箱,箱抽取方便,整R,干净, 不易磨损。
改善前改善後73.统一,标准化改善後8五、a料盒分及定x改善前改善前:料盒o信耸荆o法_定其不同色之用途改善后:增加信耸荆⒉煌色之料盒蚀_定x与区分改善後9固定不良品盒子,定c定位。
杜^良品c不良混淆。
盒子可根C _架O需要上下升降。
10改善後改善前:a使用板放置涂油的a品,板易吸收油品,е峦坑秃蟮漠a品使用r,油量不足。
改善后:使用克力板放置涂油a品,有效放置油品流失。
11七、C台放置工作桌改造改善前:1.桌面因O涞姆胖c摩擦,已破p^多750mm2.作I桌cC_放置在一起的高度影作I效率。
关于生产现场标识牌改善报告

关于生产现场标识牌改善报告一、引言生产现场标识牌是现代工业生产过程中不可或缺的一种工具,它们能够帮助员工准确地了解工作区域和设备的信息,提高生产效率,降低事故风险。
然而,在我们公司的生产现场中,我们发现一些问题存在于标识牌的设计和实施中,这些问题可能会对员工的工作效率和安全造成影响。
基于此,我们决定进行一次生产现场标识牌改善项目,旨在提高我们生产现场标识牌的质量和效果。
二、问题分析在对目前生产现场标识牌进行评估后,我们发现以下几个问题存在:1.标识牌设计不规范:目前的标识牌设计缺乏一致性,颜色、字体和图案的选择没有遵循统一的原则,有些标识牌信息不清晰,甚至无法辨认。
2.标识牌位置不合理:一些重要设备和工作区域的标识牌位置不明显,员工在操作时需要花费额外的时间和精力来寻找相关标识牌信息。
3.标识牌维护不及时:标识牌经常因为日常运营中的各种原因而损坏或丢失,但缺乏及时的检修和更换,给员工工作带来不便。
三、改善措施为了解决上述问题,我们拟定以下改善措施:1.标识牌设计规范化:制定一套统一的标识牌设计规范,包括标准的颜色、字体和图案选择,以及标识牌的尺寸和形状规定。
规范化的设计能够提高标识牌的辨识度和信息传达效果。
2.标识牌位置合理化:根据不同设备和工作区域的特点,重新规划标识牌的位置,确保它们能够被员工在第一时间发现。
设备和工作区域的标识牌应该放置在员工操作的视线范围内,避免员工在操作时需要额外的寻找过程。
3.标识牌维护及时化:建立标识牌维护和更换的工作程序,设立专人负责标识牌的定期检查和维护,及时修复和更换破损或丢失的标识牌。
同时,建立一个标识牌库存,以备替换需要维护或更换的标识牌。
四、执行计划实施本次生产现场标识牌改善项目的计划如下:1.制定标识牌设计规范:成立一个项目小组,由专业设计人员和相关部门的代表组成,负责制定标识牌设计规范。
规范制定完成后,进行内部沟通和培训,确保相关人员能够正确理解和应用。
现场改善--挤压压痕改善报告
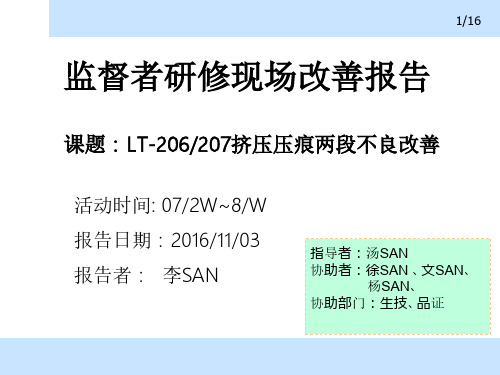
3.現状把握
5/16
挤压工序不良发生状况
4 不良合計数
3.5
不良率
3
不
良
2.5
数
(
2
个
)
1.5
1
LT-212異 品混入
1
LT-206絞 り後圧痕二
段
1
0.0294
LT-207絞 り後圧痕二
段
2
0.5
0
月份
00
"16/1
0
"16/2
0
"16/3
0.0004 0
"16/4 "16/5
0 0.0004
0
0
"16/6 "16/7 "16/8/1W "16/8/3W "16/8/4W
0.034
0.029
0.024 不
0.019
良 率
( 0.014
) 0.009
0.004
-0.001
%
生産数 絞り不良 異品混入 未絞り 不良合計数 不良率
207503 0 0 0
0 0
133267 0 0 0
1/16
监督者研修现场改善报告
课题:LT-206/207挤压压痕两段不良改善
活动时间: 07/2W~8/W 报告日期:2016/11/03 报告者: 李SAN
指导者:汤SAN 协助者:徐SAN 、文SAN、
杨SAN、 协助部门:生技、品证
1、活动计划和实际
2/16
计划:
实际:
活动项目
题目选定 现状把握 目标设定 要因分析 改善对策 效果确认 总结与感想
- 1、下载文档前请自行甄别文档内容的完整性,平台不提供额外的编辑、内容补充、找答案等附加服务。
- 2、"仅部分预览"的文档,不可在线预览部分如存在完整性等问题,可反馈申请退款(可完整预览的文档不适用该条件!)。
- 3、如文档侵犯您的权益,请联系客服反馈,我们会尽快为您处理(人工客服工作时间:9:00-18:30)。
•摆放区域内干净无杂物污渍 15 凳子区域 •区域标识清楚无破损 •摆放整齐 清洁1次/日 维护/随时 班长安排
Great Company Great People
9
2区(10拉位置)问 题改善改善区域 标准化制定
10
10拉报告制作活 动内容报告整理
11 17 23
12 18 24
执行情况确认 向后计划制定
报告完成班长物料 1.2区问题点整理 会议召开10拉成果 3定标准制定 共享经验推广 规范化实施
13
3区(SMT)问题点 发现
14
3区(SMT)问题点 发现并改善
15
3区(SMT)问题点 改善改善区域标 准化制定
16 22
SMT报告制作活 3区SMT问题点整理 4区办公室,MD拉 动内容报告整理 3定标准制定 问题点发现 规范化实施
19
4区办公室,MD拉 问题点发现并进行 改善
20
所有T5S问题点回 顾标准进行制定
21
所有班长会议召开 ALL拉巡回问题点 评价,确认LIST制定 制定标准共享ALL 指导改善 改善情况确认 进行推广
QCD Global Top Player
DT 制造现场5S规范
NO. 项目 5S标准图片 5S标准说明 备注 对象
19
Label放置
待用 LABEL放置区
•LABEL摆放整齐有序 •放在手插拉前区域并做明确标示
清洁1次/1天 标签维护/随时
物料员
•回收资材区域用红色胶带制作并标示 21 回收资材区 域 •放置回收物不可超过拉的高度 •2Hr1次值日人员清理 清洁1次/1HR 标签维护/随时 值日人员
5S运营标准确立,习惯化推进 现场自律
Before -Internal Monitoring Point
Great Company Great People
QCD Global Top Player
’06 LGEHZ PJT 登錄書
Theme
DM事業本部 活動 期間
LGEHZ
决 裁
TEAM長
QCD Global Top Player
DT 制造现场5S规范
NO. 项目 5S标准图片 5S标准说明 备注 对象
•各种标识定位定量放置
3*600=1800 16 手插工程 使用中1人1盒 备用1盒 •IDE 排插两盒使用备用一盒 •各标识清晰无脏污破損 •作业台面整洁亮丽 •详细清扫位置参照 LIST 清洁1次/日 维护/随时 手插
区域更换1次/月 损坏/老化时随时更 换
ALL
Great Company Great People
QCD Global Top Player
DT 制造现场5S规范
NO. 项目 5S标准图片 5S标准说明 备注 对象
cm 4 蓝色胶带用 途
•用于作资材区域 •限位区域 •良品/待检品区域 •器材放置区域 •文件放置区域等
FI-6 整理整顿 问题点图片 问题点图片说明 FI-6 整理整顿
改 善 前 改善名:拉行板海绵垫子改善 拉别:A1 分类:整理整顿 问题点: 拉行板海绵垫子破损严重
改善Idea: 改 善 后 邀请PM 对拉行板定期确认不良更换 (每周一次)
Great Company Great People
QCD Global Top Player
为什么要做(背景)? 内/外部环境 外部 •客户要求逐渐提高,品质保证成 为市场重点。
How to do 活动方法 ? • 组成专门改善TEAM,协作分析改善 • 跟踪到LINE,彻底改善T5S相关问题 • 利用6 sigma 工具分析检讨 推进日程
內部
定义 (D) 测定 (M)
07.1~ 07.15~ 07.19~07.24 0725~07.28 07.05~07.20 定性性:
•作业不良为品质保证埋下隐患,导致 分析 (A) 工程不良日益上升。 改善 (I) 控制 (C) 能够得到的经营 上的成果是? 定量性(金额):
Neck Point
Top 指导支持必要
改善金額: 100K$
T5S提高,竞争力加强,确保Global
No 1
Great Company Great People
Great Company Great People
QCD Global Top Player
DT 制造现场5S规范
NO. 项目 5S标准图片 5S标准说明 备注 对象
13
限高线
•仓库及拉上资材堆放处用线条注明 限高:XXX米以下 •所有有关人员遵守该规定进行管理
更换次/月
包装班班长 /系长
•干净无尘
物流革新
RTY_ p RTY_ q
Great Company Great People
QCD Global Top Player
FI-6活动现况及目标制定
D
M
A
I
C
为优化经营,设定FI-6的T5S项目的目标
T5S 70
Point
推 进方向
B等級確保(80分)
44
60%↑ T5S 自律运营. Target
DT 制造现场5S规范
NO. 项目 5S标准图片 7cm 7cm 5S区域制作 方法(一)
DT以该种方法 为基准
5S标准说明
备注
对象
1
• 区域四角用折线围起 • 每个角尺寸如图所示:7cm • 边角为圆角 • 区域追加后物品必须严格放置在区域 内部
区域更换1次/月 损坏/老化时随时更 换
ALL
7cm
FI-6 整理整顿 问题点图片 问题点图片说明 FI-6 整理整顿
改 善 前 改善名:拉行板海绵垫子改善 拉别:A1 分类:整理整顿 问题点: 拉行板海绵垫子破损严重
改善Idea: 改 善 后 邀请PM 对拉行板定期确认不良更换 (每周一次)
Great Company Great People
QCD Global Top Player
各拉别活动推进日程说明
会议讨论FI-6计 划制定 1区(1拉位置)问 题发现 1区(1拉位置)问题 发现并进行改善
D
M
A
I
C
1区(1拉位置)问题 改善区域标准化 制定
1拉报告制作活动 报告完成班长物 内容报告整理 料会议召开1拉成 果共享经验推广
7
2区(10拉位置)问 题发现
8
2区(10拉位置)问 题发现并进行改 善
•干净无污痕 9 墙壁
•无碰撞划痕
•无脚印灰尘 •每周大清扫要进行
清洁1次/班 维护/随时
ALL
Great Company Great People
QCD Global Top Player
DT 制造现场5S规范
NO. 项目 5S标准图片 5S标准说明 备注 对象
10
灭火器箱
•放置于指定区域 •灭火器前1米处不可随便摆放物品 •表面干净无尘 •安全担当每日确认灭火器状态等相关信息
维护/随时
班长/安全 担当
•放置于规定区域 11 消防器材 •消防器材前1米处不可随便摆放物品 •表面干净无尘 •安全担当每日确认消防栓状态等相关信息 维护/随时 班长/安全 担当
•放置于LINE规定区域内 12 手推式 灭火器 •保持通道顺畅 •表面干净无尘 •消防器材前1米处不可随便摆放物品 •安全担当每日确认灭火器状态等相关信息 维护/随时 班长/安全 担当
每月物料员从自焊 机担当出定量领取
ALL
cm 5
•不良品区域
红色胶带用 途
•危险品区域
•垃圾及回收 箱/桶放置区域
每月物料员从自焊 机担当出定量领取
ALL
cm
6
黄色胶带用 途
•用于制作通道限位
每月物料员从自焊 机担当出定量领取
ALL
Great Company Great People
QCD Global Top Player
FI-6 整理整顿 问题点图片 问题点图片说明 FI-6 整理整顿
改 善 前 改善名:包装位扫描PC线改善 拉别:A1 分类:整理整顿 问题点: 拉包装位扫描PC 电源线乱,未进行整理
改 善 后
改善Idea:
拉包装位扫描PC线进行重新布线整理
Great Company Great People
QCD Global Top Player
DT 制造现场5S规范
NO. 项目 5S标准图片 5S标准说明 备注 对象
7
整体通道
•通道由两条黄色胶带组成 •通道间距离根据自体拉距离制定 •通道内不可放置任何物品不可堵塞 •地面干净整洁,无灰尘纸屑 •胶带破损随时安排修补
清洁1次/班 维护/随时 胶带更换1次/月
ALL
•安全出口要标识 8 安全出口 •安全通道保持通畅 •每月月底安全担当检查是否有电源 清洁1次/班 维护/随时 ALL
2
5S区域制作 方法(二)
•区域对角用折线围起 • 每个角尺寸如图所示:7cm • 边角为圆角 • 区域追加后物品必须严格放置在区域 内部
7cm
区域更换1次/月 损坏/老化时随时更 换
ALL
3
5S区域制作 方法(三)
•区域四边连接在一起围成四方形 •尺寸稍大于存放物品大小 • 边角为圆角 • 区域追加后物品必须严格放置在区域 内部
决 裁
制作
王加华
革新TEAM
管理者
DS生产担当
FI-6 T5S现场改善活动报告
目 录
1 2 3 4 5 Theme选定背景 Y的现水准测定