幕墙玻璃加工工艺
玻璃幕墙的施工工艺方法
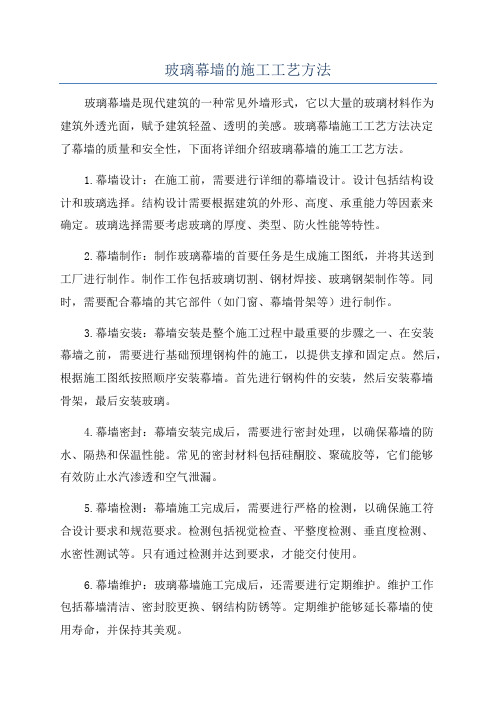
玻璃幕墙的施工工艺方法玻璃幕墙是现代建筑的一种常见外墙形式,它以大量的玻璃材料作为建筑外透光面,赋予建筑轻盈、透明的美感。
玻璃幕墙施工工艺方法决定了幕墙的质量和安全性,下面将详细介绍玻璃幕墙的施工工艺方法。
1.幕墙设计:在施工前,需要进行详细的幕墙设计。
设计包括结构设计和玻璃选择。
结构设计需要根据建筑的外形、高度、承重能力等因素来确定。
玻璃选择需要考虑玻璃的厚度、类型、防火性能等特性。
2.幕墙制作:制作玻璃幕墙的首要任务是生成施工图纸,并将其送到工厂进行制作。
制作工作包括玻璃切割、钢材焊接、玻璃钢架制作等。
同时,需要配合幕墙的其它部件(如门窗、幕墙骨架等)进行制作。
3.幕墙安装:幕墙安装是整个施工过程中最重要的步骤之一、在安装幕墙之前,需要进行基础预埋钢构件的施工,以提供支撑和固定点。
然后,根据施工图纸按照顺序安装幕墙。
首先进行钢构件的安装,然后安装幕墙骨架,最后安装玻璃。
4.幕墙密封:幕墙安装完成后,需要进行密封处理,以确保幕墙的防水、隔热和保温性能。
常见的密封材料包括硅酮胶、聚硫胶等,它们能够有效防止水汽渗透和空气泄漏。
5.幕墙检测:幕墙施工完成后,需要进行严格的检测,以确保施工符合设计要求和规范要求。
检测包括视觉检查、平整度检测、垂直度检测、水密性测试等。
只有通过检测并达到要求,才能交付使用。
6.幕墙维护:玻璃幕墙施工完成后,还需要进行定期维护。
维护工作包括幕墙清洁、密封胶更换、钢结构防锈等。
定期维护能够延长幕墙的使用寿命,并保持其美观。
以上是玻璃幕墙施工的主要工艺方法。
随着科技的发展,玻璃幕墙的施工技术也在不断更新,比如采用现成的模块化玻璃幕墙系统,以提高施工效率和质量。
在施工过程中,需要严格按照设计和规范要求进行操作,以确保幕墙的质量和安全性。
倾斜面幕墙玻璃施工工法
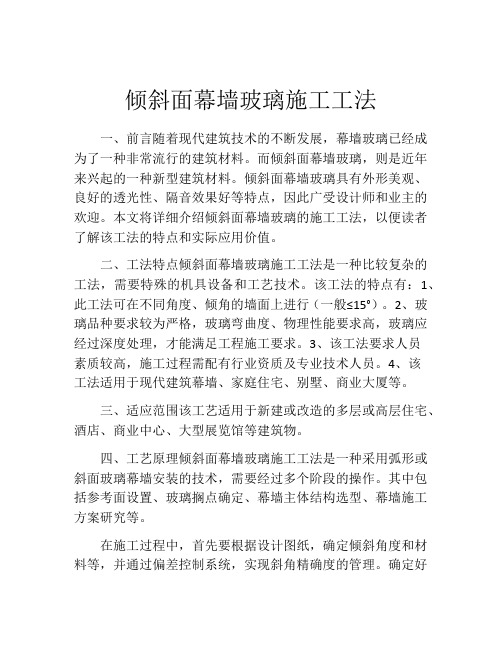
倾斜面幕墙玻璃施工工法一、前言随着现代建筑技术的不断发展,幕墙玻璃已经成为了一种非常流行的建筑材料。
而倾斜面幕墙玻璃,则是近年来兴起的一种新型建筑材料。
倾斜面幕墙玻璃具有外形美观、良好的透光性、隔音效果好等特点,因此广受设计师和业主的欢迎。
本文将详细介绍倾斜面幕墙玻璃的施工工法,以便读者了解该工法的特点和实际应用价值。
二、工法特点倾斜面幕墙玻璃施工工法是一种比较复杂的工法,需要特殊的机具设备和工艺技术。
该工法的特点有:1、此工法可在不同角度、倾角的墙面上进行(一般≤15°)。
2、玻璃品种要求较为严格,玻璃弯曲度、物理性能要求高,玻璃应经过深度处理,才能满足工程施工要求。
3、该工法要求人员素质较高,施工过程需配有行业资质及专业技术人员。
4、该工法适用于现代建筑幕墙、家庭住宅、别墅、商业大厦等。
三、适应范围该工艺适用于新建或改造的多层或高层住宅、酒店、商业中心、大型展览馆等建筑物。
四、工艺原理倾斜面幕墙玻璃施工工法是一种采用弧形或斜面玻璃幕墙安装的技术,需要经过多个阶段的操作。
其中包括参考面设置、玻璃搁点确定、幕墙主体结构选型、幕墙施工方案研究等。
在施工过程中,首先要根据设计图纸,确定倾斜角度和材料等,并通过偏差控制系统,实现斜角精确度的管理。
确定好参考面之后,就要进行模板的制作,利用模板来控制双曲面的曲率。
在玻璃的质量上,则要求玻璃造型要符合双曲面或倾斜面的要求,同时钢化或夹层玻璃的标准也要符合建筑幕墙要求。
最后要注意添加密封胶条,以防止雨水、灰尘等因素的侵入。
五、施工工艺1、参考线、布点:依据初步设计中的倾角和大小,通过斜线、闸墙上的坐标参考点来拆分出每一个玻璃搁点而确定每一个玻璃的数量和尺寸。
2、模板制作:依据排好的幕墙玻璃数量和尺寸,制定制作玻璃模板的施工方案,进行模板的制作。
3、幕墙框架安装:在搭建好的架子上,先进行钢梁挂点的校直和固定,确定好梁台位和幕墙嵌板钢梁的位置和孔径。
4、玻璃搁置:按照布点坐标确定好每一个玻璃的搁置位置和预制玻璃隐形连接方式安装固定号牌,制作好的玻璃模板和搁置口的对接方式,玻璃搁置时先单独搭装玻璃,玻璃搁置完毕后,再按模板香好批量搭装玻璃,每个玻璃安装名为1块、2块、3块......5、支护:将大块玻璃放置在支撑架上,靠近架子,确定好玻璃位置后,将支撑架向外移动,从而使玻璃搁置至位,并进行玻璃的预紧角度。
玻璃幕墙生产工艺
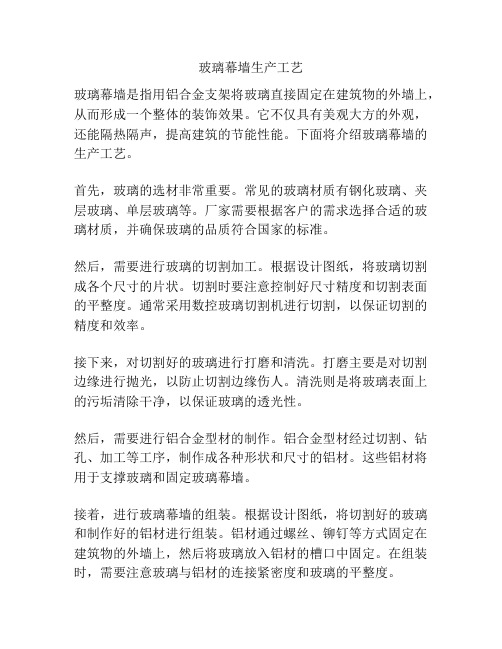
玻璃幕墙生产工艺玻璃幕墙是指用铝合金支架将玻璃直接固定在建筑物的外墙上,从而形成一个整体的装饰效果。
它不仅具有美观大方的外观,还能隔热隔声,提高建筑的节能性能。
下面将介绍玻璃幕墙的生产工艺。
首先,玻璃的选材非常重要。
常见的玻璃材质有钢化玻璃、夹层玻璃、单层玻璃等。
厂家需要根据客户的需求选择合适的玻璃材质,并确保玻璃的品质符合国家的标准。
然后,需要进行玻璃的切割加工。
根据设计图纸,将玻璃切割成各个尺寸的片状。
切割时要注意控制好尺寸精度和切割表面的平整度。
通常采用数控玻璃切割机进行切割,以保证切割的精度和效率。
接下来,对切割好的玻璃进行打磨和清洗。
打磨主要是对切割边缘进行抛光,以防止切割边缘伤人。
清洗则是将玻璃表面上的污垢清除干净,以保证玻璃的透光性。
然后,需要进行铝合金型材的制作。
铝合金型材经过切割、钻孔、加工等工序,制作成各种形状和尺寸的铝材。
这些铝材将用于支撑玻璃和固定玻璃幕墙。
接着,进行玻璃幕墙的组装。
根据设计图纸,将切割好的玻璃和制作好的铝材进行组装。
铝材通过螺丝、铆钉等方式固定在建筑物的外墙上,然后将玻璃放入铝材的槽口中固定。
在组装时,需要注意玻璃与铝材的连接紧密度和玻璃的平整度。
最后,进行玻璃幕墙的安装。
将已组装好的玻璃幕墙整体安装到建筑物的外墙上,一般采用吊装的方式。
安装时要注意固定的稳定性和与建筑物的密封性。
以上就是玻璃幕墙的生产工艺。
每个工序都需要严格控制和操作,以确保玻璃幕墙的质量和安全性。
玻璃幕墙作为一种现代化的建筑装饰材料,它的生产工艺也在不断改进和发展,以满足不同客户的需求。
幕墙生产加工流程、工艺、质量保证措施

幕墙生产加工流程、工艺、质量保证措施一、生产加工流程二、生产加工工艺1.工厂内生产加工的操作程序2.工厂内生产加工的工艺流程3.铝型材装配工艺流程4.玻璃板块加工工艺流程5.单元板块组装工艺流程三、材料加工质量保证措施1、生产制造程序2、下料工序质量控制3、组装工序质量控制4、组角工序质量控制点5、玻璃原板质量控制措施:6、铝合金型材质量控制措施:7、结构胶和耐侯胶:一、生产加工流程开工会议生产策划生产准备会议首样评审现场评审试验验证业主认可批量生产预备会议批量生产材料检验、工序自检、工序抽检、入库检验、成品检验、现场检验、监理监督是否满足要求采取纠正预防措施是否满足要求出厂生产总结会二、生产加工工艺本工程材料除特殊需要现场加工外其余的均在公司生产车间内加工制作完成后采用汽车运抵现场。
现场项目部提交的工程安装计划表及安装材料进场计划表确定批次材料的加工顺序,加工任务由项目管理中心下达,由生产部按期、按质、按量完成,生产加工全过程由公司质检员跟踪检验。
1.工厂内生产加工的操作程序加工由生产部组织进行。
操作程序是指生产部从接受任务到成品至现场全过程的生产活动和控制手段。
可分为以下几个阶段:(1)接受任务和下达任务根据项目管理中心下达的生产任务,制定生产加工计划,并将相关任务计划下达到各加工车间。
工艺编制和工时定额(2)工艺员根据加工图纸,编制各种加工零件的工艺卡片,同时,定额员根据工艺卡制定工时定额。
(3)车间加工车间技术工人按工艺卡、图纸技术要求、质量等级进行机械加工。
(4)质量检验在生产的全过程中始终贯穿着质量检验,包括自检、抽检的执行。
(5)包装、运输至现场完成现场所需要的合格半成品和成品后,即可按照不同的包装要求对不同产品进行包装,并按一定的方法装车运至现场。
以上过程将在生产加工操作程序严格控制下进行。
2.工厂内生产加工的工艺流程在生产加工操作程序中,最重要的阶段是车间加工,其主要内容是对各种材料进行机械加工,以及组件的装配等。
玻璃幕墙工程施工

玻璃幕墙工程施工玻璃幕墙的施工工艺包括材料准备、构件制作、安装、密封等多个环节,下面将详细介绍玻璃幕墙工程的施工步骤。
一、材料准备1. 玻璃选择玻璃幕墙使用的玻璃通常是钢化玻璃、夹胶玻璃或层压玻璃,根据设计要求选择相应规格和型号的玻璃。
2. 铝型材玻璃幕墙的支架结构一般采用铝型材,也需要按照设计要求选择相应的规格和型号。
3. 密封胶玻璃安装时需使用密封胶进行密封,根据实际情况选择合适的密封胶。
二、构件制作1. 玻璃加工将设计好的玻璃尺寸交由玻璃加工厂进行切割、打孔、弯曲等加工,以满足设计要求。
2. 铝型材加工铝型材需要根据设计图纸进行加工,包括切割、打孔、弯曲等,以保证构件的精准度和稳固性。
三、安装1. 立柱安装首先需要安装立柱,固定在建筑结构上,然后安装连接件和固定件。
2. 安装玻璃将经过加工的玻璃安装在支架结构上,注意保证玻璃的平整度和垂直度。
3. 安装铝型材安装支撑结构,使用铝型材连接玻璃,保证整个幕墙结构的牢固性和稳定性。
4. 密封处理使用密封胶对玻璃和铝型材之间的接口进行密封处理,以防止水汽渗透和风沙侵蚀。
四、验收1. 视觉检查检查玻璃幕墙的外观质量,包括表面平整度、色泽均匀度等。
2. 结构检查检查支架结构的稳固性和牢固度,确保玻璃幕墙可以承受风压和地震等外部力的作用。
3. 密封性检查检查密封胶的密封性能,确保玻璃幕墙具有防水、防尘等功能。
以上就是玻璃幕墙工程的施工步骤,通过严格按照要求进行施工,可以确保玻璃幕墙的质量和安全性。
在施工过程中,需要注意保护好现场环境和施工人员的安全,遵守相关法规和规范,确保施工工程的顺利进行。
希望以上内容对你有所帮助。
外墙玻璃幕墙施工工艺
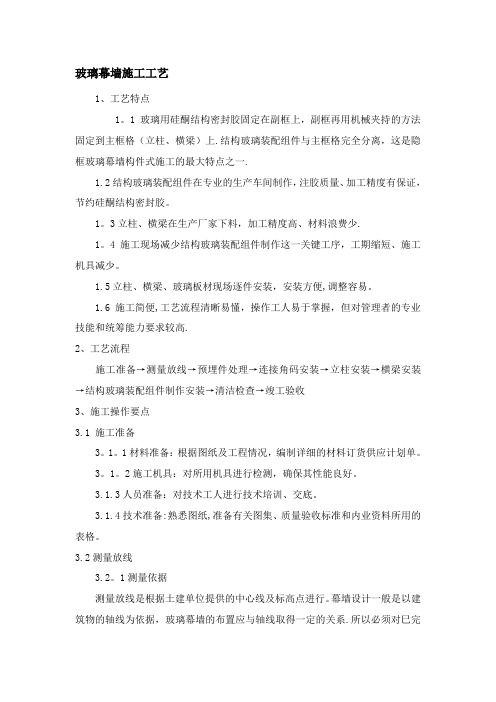
玻璃幕墙施工工艺1、工艺特点1。
1玻璃用硅酮结构密封胶固定在副框上,副框再用机械夹持的方法固定到主框格(立柱、横梁)上.结构玻璃装配组件与主框格完全分离,这是隐框玻璃幕墙构件式施工的最大特点之一.1.2结构玻璃装配组件在专业的生产车间制作,注胶质量、加工精度有保证,节约硅酮结构密封胶。
1。
3立柱、横梁在生产厂家下料,加工精度高、材料浪费少.1。
4施工现场减少结构玻璃装配组件制作这一关键工序,工期缩短、施工机具减少。
1.5立柱、横梁、玻璃板材现场逐件安装,安装方便,调整容易。
1.6施工简便,工艺流程清晰易懂,操作工人易于掌握,但对管理者的专业技能和统筹能力要求较高.2、工艺流程施工准备→测量放线→预埋件处理→连接角码安装→立柱安装→横梁安装→结构玻璃装配组件制作安装→清洁检查→竣工验收3、施工操作要点3.1 施工准备3。
1。
1材料准备:根据图纸及工程情况,编制详细的材料订货供应计划单。
3。
1。
2施工机具:对所用机具进行检测,确保其性能良好。
3.1.3人员准备:对技术工人进行技术培训、交底。
3.1.4技术准备:熟悉图纸,准备有关图集、质量验收标准和内业资料所用的表格。
3.2测量放线3.2。
1测量依据测量放线是根据土建单位提供的中心线及标高点进行。
幕墙设计一般是以建筑物的轴线为依据,玻璃幕墙的布置应与轴线取得一定的关系.所以必须对巳完工的土建结构进行测量.3。
2.2测量方法建筑物外轮廓测量:根据土建标高基准线复测每一层预埋件标高中心线,据此线检查预埋件标高偏差,并作好记录;找出幕墙立柱与建筑轴线的关系,根据土建轴线测量立柱轴线,据此检查预埋件左右偏差,并作好记录。
整理以上测量结果,确定幕墙立柱分隔的调整处理方案。
幕墙立柱外平面定位:根据设计图纸和土建结构误差确定幕墙立柱外平面轴线距建筑物外平面轴线的距离,在墙面顶部合适位置用钢琴线定出.幕墙立柱外平面轴线。
幕墙立柱轴线定位:幕墙前后位置确定后,结合建筑物外轮廓测量结果,用钢琴线定出每条立柱的左右位置。
玻璃幕墙工艺流程
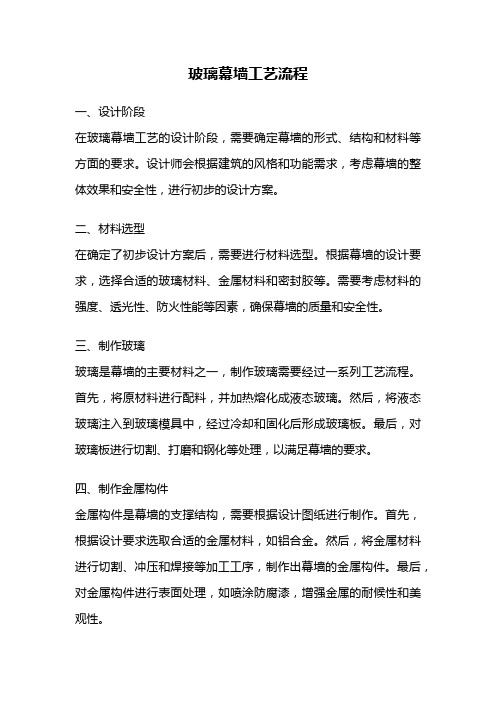
玻璃幕墙工艺流程一、设计阶段在玻璃幕墙工艺的设计阶段,需要确定幕墙的形式、结构和材料等方面的要求。
设计师会根据建筑的风格和功能需求,考虑幕墙的整体效果和安全性,进行初步的设计方案。
二、材料选型在确定了初步设计方案后,需要进行材料选型。
根据幕墙的设计要求,选择合适的玻璃材料、金属材料和密封胶等。
需要考虑材料的强度、透光性、防火性能等因素,确保幕墙的质量和安全性。
三、制作玻璃玻璃是幕墙的主要材料之一,制作玻璃需要经过一系列工艺流程。
首先,将原材料进行配料,并加热熔化成液态玻璃。
然后,将液态玻璃注入到玻璃模具中,经过冷却和固化后形成玻璃板。
最后,对玻璃板进行切割、打磨和钢化等处理,以满足幕墙的要求。
四、制作金属构件金属构件是幕墙的支撑结构,需要根据设计图纸进行制作。
首先,根据设计要求选取合适的金属材料,如铝合金。
然后,将金属材料进行切割、冲压和焊接等加工工序,制作出幕墙的金属构件。
最后,对金属构件进行表面处理,如喷涂防腐漆,增强金属的耐候性和美观性。
五、安装幕墙在安装幕墙之前,需要进行施工准备工作。
首先,对建筑外墙进行清理和处理,确保外墙的平整和牢固。
然后,根据设计图纸确定幕墙的安装位置和方式。
最后,进行幕墙的安装,包括固定金属构件、安装玻璃板和密封胶等。
安装过程中需要注意安全,确保幕墙的稳定性和密封性。
六、验收和维护完成幕墙的安装后,需要进行验收和维护工作。
验收包括对幕墙的外观质量、结构安全和功能性能等方面进行检查。
维护包括定期清洁幕墙、检查密封胶的状况和修补破损部分等,以延长幕墙的使用寿命和保持良好的外观效果。
总结:玻璃幕墙工艺流程包括设计阶段、材料选型、制作玻璃、制作金属构件、安装幕墙以及验收和维护等步骤。
在每个阶段都需要仔细考虑设计要求和施工细节,确保幕墙的质量和安全性。
玻璃幕墙作为现代建筑的重要组成部分,不仅具有美观的外观效果,还能提升建筑的节能性和舒适度。
随着建筑技术的不断进步,玻璃幕墙工艺也在不断创新和发展,为建筑行业带来更多可能性。
玻璃幕墙施工工艺(连接件、定位放线、竖梁安装、横梁安装)

玻璃幕墙施工工艺(连接件、竖梁定位放线、竖梁安装、横梁安装、横梁安装)1、连接件安装工艺及技术方案1.1工艺流程说明:工艺流程:熟悉图纸及技术交底→熟悉施工现场→寻准预埋铁件对准竖梁线→拉水平线控制水平高度及进深位置→点焊→检查→加焊→防腐→记录。
1.2 基本操作说明:1.2.1 熟悉图纸:了解前段工序的变化更改及设计变更。
1.2.2熟悉施工现场:施工现场的熟悉包括两方面的内容,一是对已施工工序质量的验收;二是对照图纸要求对下步工作的安排。
1.2.3寻准预埋铁件:预埋铁件的作用就是将连接件固定,使幕墙结构与主体砼结构连接起来。
故安装连接件时首先要寻找原预埋件,只有寻准了预埋件才能很准确地安装连接件。
1.2.4对照竖梁垂线:竖梁的中心线也是连接件的中心线,故在安装时要注意控制连接件的位置,其偏差小于2mm。
1.2.5拉水平线控制水平高低及进深尺寸。
虽然予埋铁件时已控制水平高度,但由于施工误差的影响,安装连接件时仍要拉水平线控制其水平及进深的位置以保证连接件的安装准确无误,方法参照前几道工序操作要求。
1.2.6点焊:在连接件三维空间定位确定准确后要进行连接件的临时固定即点焊。
点焊时每个焊接面点2~3点,要保证连接件不会脱落。
点焊时要两人同时进行,一人固定位置;另一人点焊,这样协调施工同时两人都要做好各种防护;点焊人员必须是有焊工技术操作证者,以保证点焊的质量。
1.2.7验收检查。
对初步固定的连接件按层次逐个检查施工质量,主要检查三维空间误差,一定要将误差控制在误差范围内。
三维空间误差工地施工控制范围为垂直误差小于2mm,水平误差小于2mm,进深误差小于3mm。
1.2.8加焊正式固定:对验收合格的连接件进行固定,即正式烧焊。
烧焊操作时要按照焊接的规格及操作规定进行,一般情况下连接件的两边都必须满焊。
1.2.9验收:对烧焊好的连接件,现场管理人员要对其进行逐个检查验收,对不合格处进行返工改进,直至达到要求为止。
玻璃幕墙工程施工工艺

玻璃幕墙工程施工工艺玻璃幕墙施工要由专业队伍单独设计和施工,具体详专项方案,这里做系统论述。
1、工艺流程:→→→→→2安装各楼层紧固铁件:主体结构施工时埋件预埋形式及紧固铁件与埋件连接方法,均要按设计图纸要求进行操作,一般有以下两种方式:a在主体结构的每层现浇混凝土楼板或梁内预埋铁件,角钢连接件与预埋件焊接,然后用螺栓(镀锌)再与竖向龙骨连接。
b在主体结构的每层现浇混凝土楼板或梁内预埋“T”形槽埋件,角钢连接件与“T”形槽通过镀锌栓连接,即把螺栓预先穿入“T”形槽内,再与角钢连接件连接。
3横、竖龙骨装配:在龙骨安装就位之前,预先装配好以下连接件:竖向主龙骨之间接头用的镀锌钢板内套筒连接件;竖向主龙骨与紧固件之间的连接件。
横向次龙骨的连接件。
各节点的连接件的连接方法要符合设计图纸要求,连接必须牢固,横平竖直。
4竖向主龙骨安装:主龙骨一般由下往上安装,每两层为一整根,每楼层通过连接紧固铁件与楼板连接。
a先将主龙骨竖起,上、下两端的连接件对准紧固铁件的螺栓孔,初拧螺栓。
b主龙骨可通过紧固铁件和连接件的长螺栓孔上、下、左、右进行调整,左、右水平方向应与弹在楼板上的位置线相吻合,上、下对准楼层标高,前、后(即Z轴方向)不得超出控制线,确保上下垂直,同距符合设计要求。
c主龙骨通过内套管竖向接长,为防止铝材受温度影响而变形,接头处应留适当宽度的伸缩孔隙,具体尺寸根据设计要求,接头处上下龙骨中心线要对上。
d安装到顶层之后,再用精纬仪进行垂直度校正、检查无误后,把所有竖向龙骨与结构连接的螺栓、螺母、垫圈拧紧、焊牢。
所有焊缝重新加焊至设计要求,并将焊药皮砸掉,清理检查符合要求后,刷两道防锈漆。
5横向水平龙骨安装安好竖龙骨后,进行垂直度、水平度、间距等项检查,符合要求后,便可进行水平龙骨的安装。
安装前,将水平龙骨两端头套上防水橡胶垫。
用木支撑暂时将主龙骨撑开,接着装入横向水平龙骨,然后取掉木支撑后,两端橡胶垫被压缩,起到较好的防水效果。
幕墙工程现场施工工艺及标准
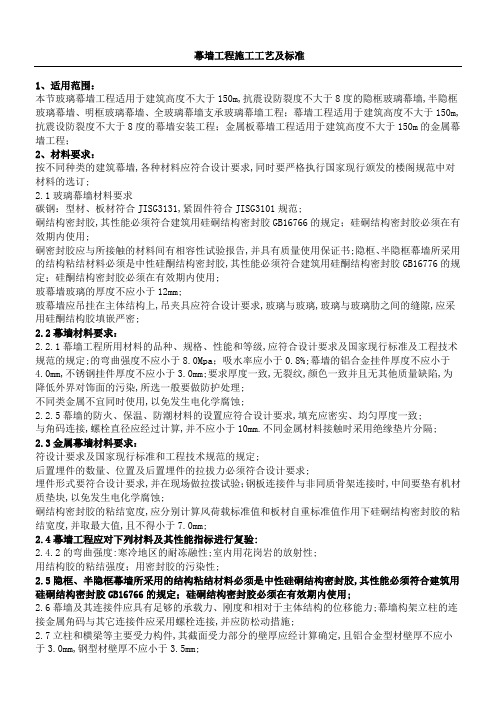
1、适用范围:本节玻璃幕墙工程适用于建筑高度不大于150m,抗震设防裂度不大于8度的隐框玻璃幕墙,半隐框玻璃幕墙、明框玻璃幕墙、全玻璃幕墙支承玻璃幕墙工程;幕墙工程适用于建筑高度不大于150m,抗震设防裂度不大于8度的幕墙安装工程;金属板幕墙工程适用于建筑高度不大于150m的金属幕墙工程;2、材料要求:按不同种类的建筑幕墙,各种材料应符合设计要求,同时要严格执行国家现行颁发的楼阁规范中对材料的选订;2.1玻璃幕墙材料要求碳钢:型材、板材符合JISG3131,紧固件符合JISG3101规范;硐结构密封胶,其性能必须符合建筑用硅硐结构密封胶GB16766的规定;硅硐结构密封胶必须在有效期内使用;硐密封胶应与所接触的材料间有相容性试验报告,并具有质量使用保证书;隐框、半隐框幕墙所采用的结构粘结材料必须是中性硅酮结构密封胶,其性能必须符合建筑用硅酮结构密封胶GB16776的规定;硅酮结构密封胶必须在有效期内使用;玻幕墙玻璃的厚度不应小于12mm;玻幕墙应吊挂在主体结构上,吊夹具应符合设计要求,玻璃与玻璃,玻璃与玻璃肋之间的缝隙,应采用硅酮结构胶填嵌严密;2.2幕墙材料要求:2.2.1幕墙工程所用材料的品种、规格、性能和等级,应符合设计要求及国家现行标准及工程技术规范的规定;的弯曲强度不应小于8.0Mpa;吸水率应小于0.8%;幕墙的铝合金挂件厚度不应小于4.0mm,不锈钢挂件厚度不应小于3.0mm;要求厚度一致,无裂纹,颜色一致并且无其他质量缺陷,为降低外界对饰面的污染,所选一般要做防护处理;不同类金属不宜同时使用,以免发生电化学腐蚀;2.2.5幕墙的防火、保温、防潮材料的设置应符合设计要求,填充应密实、均匀厚度一致;与角码连接,螺栓直径应经过计算,并不应小于10mm.不同金属材料接触时采用绝缘垫片分隔;2.3金属幕墙材料要求:符设计要求及国家现行标准和工程技术规范的规定;后置埋件的数量、位置及后置埋件的拉拔力必须符合设计要求;埋件形式要符合设计要求,并在现场做拉拨试验;钢板连接件与非同质骨架连接时,中间要垫有机材质垫块,以免发生电化学腐蚀;硐结构密封胶的粘结宽度,应分别计算风荷载标准值和板材自重标准值作用下硅硐结构密封胶的粘结宽度,并取最大值,且不得小于7.0mm;2.4幕墙工程应对下列材料及其性能指标进行复验:2.4.2的弯曲强度:寒冷地区的耐冻融性;室内用花岗岩的放射性;用结构胶的粘结强度;用密封胶的污染性;2.5隐框、半隐框幕墙所采用的结构粘结材料必须是中性硅硐结构密封胶,其性能必须符合建筑用硅硐结构密封胶GB16766的规定;硅硐结构密封胶必须在有效期内使用;2.6幕墙及其连接件应具有足够的承载力、刚度和相对于主体结构的位移能力;幕墙构架立柱的连接金属角码与其它连接件应采用螺栓连接,并应防松动措施;2.7立柱和横梁等主要受力构件,其截面受力部分的壁厚应经计算确定,且铝合金型材壁厚不应小于3.0mm,钢型材壁厚不应小于3.5mm;2.8隐框、半隐框幕墙构件板材与金属框之间硅硐结构密封胶的粘结宽度,应分别计算风荷载标准值和板材自重标准值作用下硅硐结构密封胶的粘结宽度,并取最大值,且不得小于7.0mm;2.9硅硐结构密封胶应打注饱满,并应温度15℃~30℃、相对湿度50%以上、洁净的室内进行;不得在现场墙上打注;2.10幕墙的防火除应符合现行国家标准建筑设计防火规范GBJ16和高层民用建筑设计防火规范GB50045的有关规定外,还应符合下列规定:1应根据防火材料的耐火极限决定防火层的厚度和宽度,并应在楼板处形成防火带;2防火层应采取隔离措施;防火层的衬板应采用经防腐处理且厚度不小于1.5mm的钢板,不得采用铝板;3防火层的密封材料应用防火密封胶;4防火层与玻璃不应直接接触,一块玻璃不应跨两个防火分区;2.11主体结构与幕墙连接的各种预埋件,其数量、规格、位置和防腐处理必须符合设计要求;2.12幕墙的金属框架与主体结构预埋件的连接、立柱与横梁的连接及幕墙面板的安装必须符合设计要求,安装必须牢固;2.13单元幕墙连接处和吊挂处的铝合金型材的壁厚应通过计算得出,并不得小于5mm;3、主要机具工具:3.1玻璃幕墙工程主要机具工具:打胶枪等;3.2幕墙工程主要机具工具:3.2.1主要机具:电锤,电焊机,型材切割机,云石锯,角磨机;打胶器,壁纸刀等;3.3金属幕墙工程主要机具工具:自攻钻及开槽机等;打胶枪、改锥、扳手、钳子、壁纸刀等;4、作业条件:4.1施工技术负责人在施工前应向施工人员做好技术交底工作,交待清楚预埋固定支座、铝合金骨架体系的划分尺寸及形式,玻璃与骨架间的连接的方法及连接要求等;4.2施工人员在明确图纸要求后方可施工;4.3施工时应搭好脚手架,保证脚手架的安全性,并预留施工人员的操作空间,脚手架上应设置安全网,以免在幕墙施工时发生物体坠落伤人;4.4幕墙施工前建筑主体需经验收,且砼强度达到幕墙设计要求;幕墙施工图已绘制完善,且已经各方认可;根据施工组织设计要求、人员、机具及前期施工材料已到位,足够的作业面;5、施工工艺:一、玻璃幕墙施工工艺1、工艺流程:放样定位→安装立柱→安装横梁→安装玻璃→打胶→清理2、操作工艺⑴、根据玻璃幕墙的造型,尺寸和图纸要求,在铝合金骨架体系与建筑结构之间设置连接固定支座;放样时,应使上下支座均在一条垂直线上,避免此位置上的立柱会发生歪斜;⑵、安装立住;在固定支座的两角钢间,用不锈钢对拉螺栓将立柱按安装标高要求固定好,立柱轴线的前后偏差和左右偏差分别不应大于2mm和3mm;支座的角钢和铝合金立柱接触处用柔性垫片进行隔离;立柱安装调整后,应及时紧固;立柱在加长时应用配套的专用芯管连接,上下柱之间应留有空隙,空隙宽度不宜小于10m,其接头应为活动接头,从而满足立柱在热胀冷缩时发生的变形需求; ⑶、安装横梁;先确定各横梁在方柱上的标高位置,在此位置处用厚度不小于3mm的铝角将横梁与立柱连接起来,在横梁与立柱的接触处应设置弹性橡校垫;相邻两根横梁水平标高偏差不应大于1mm;同层横梁的标高偏差,当幕墙宽度小于或等于35m时,不应大于5mm;当幕墙宽度大于35m时,不应大于7mm,同一层横梁在安装时应由下而上进行;当一层高度的横梁装好后,应进行检查、调整、校正后再进行固定;⑷安装玻璃玻璃的安装应根据幕墙的具体种类来定;如幕墙玻璃采用镀膜玻璃时,镀膜的一面应向室内;①隐框幕墙玻璃:隐框幕墙的玻璃是用结构硅硐胶粘结在铝合金框格上,从而形成玻璃单元体;玻璃元体的加工一般在工厂内用专用打胶机来完成;这样能保证玻璃的粘结质量;在施工现场受环境条件的影响,较难保证玻璃与铝合金框格的粘结质量;玻璃单元体制成后,将单元件中铝合金框格的上边挂在横梁上,再用专用固定片将铝合金框格的其余三条边钩夹在立柱和横梁上,框格每边的固定片数量不少于二片;②明框玻璃幕墙;明框幕墙的玻璃是用压板和橡皮为固定在横梁和立柱上,压板再用螺栓固定在横梁或立柱上;在固定玻璃时,压板上的连接螺栓应松紧合适,从而使压板对玻璃不致压得过紧或过松;并使压板与玻璃间的橡皮条紧闭;在横梁上设置定位垫块,垫块的搁置点离玻璃垂直边缘的距离宜为玻璃宽度的1/4,且不宜小于150mm,垫块的宽度应不大于所支撑玻璃的厚度,长度不宜小于25mm,并符合有关要求;③半隐框幕墙;半隐墙幕墙在一个方向上隐框的,在另一方面上则为明框;它在隐框方向上的玻璃边缘用结构硅硐胶固定,在明框方向上的玻璃边缘用压板和连接螺栓固定,隐框边和明框边的具体施工方法可分别参照隐框幕墙和明框幕墙的玻璃安装方法;⑸打胶:打胶的温度和湿度应符合相关规范的要求;⑹清理:玻璃幕墙的玻璃安装完后,应用中性清洁剂和水对有污染的玻璃和铝型材进行清洗;二、幕墙施工工艺1、工艺流程:预埋件位置尺寸检查→安装预埋件→复测预埋件位置尺寸→测量放线→绘制工程翻样图→金属骨架加工→钢结构刷防锈漆→金属骨架安装→防火保温棉→隐蔽工程验收→饰面板加工→表面防护→饰面板安装→安装质量检查→灌注嵌缝硅胶→幕墙表面清洗2、操作工艺:⑴预埋件安装:预埋件应在土建施工时埋设,幕墙施工前要根据该工程基准轴线和中线以及基准水平点对预埋件进行检查和校核,一般允许位置尺寸偏差为±20mm;如有预埋件位置超差而无法使用或漏放时,应根据实际情况提出选用膨胀螺栓的方案,并必须报设计单位审核批准,且应在现场做拉拔试验,做好记录;⑵测量放线:①由于土建施工允许误差较大,幕墙工程施工要求精度很高,所以不能依靠土建水平基准线,必须由基准轴线和水准点重新测量,并校正复核;②按照设计在底层确定幕墙定位线和分格线;③经纬仪或激光垂直仪将幕墙的阳角和阴角引上,并用固定在钢支架上的钢丝线作标志控制线;④使用水平仪和标准钢卷尺等引出各层标高线;⑤确定好每个立面的中线;⑥测量时应控制分配测量误差,不能使误差积累;⑦测量放线应在风力不大于4级的情况下进行,并要采取避风措施;⑧所有外立面装饰工程应统一放基准线,并注意施工配合;⑶金属骨架安装①根据施工放样图检查放线位置;②安装固定竖框的铁件;③先安装同立面两端的竖框,然后拉通线顺序安装中间竖框;④将各施工水平控制线引至竖框上,并用水平尺校核;⑤按照设计尺寸安装金属横梁;横梁一定要与竖框垂直;⑥如有焊接时,应对下方和邻近的已完工装饰面进行成品保护;焊接时要采用对称焊,以减少因焊接产生的变形;检查焊缝质量合格后,所有焊点、焊缝均需去焊渣及防锈处理,如刷防锈漆等;⑦待金属骨架完工后,应通过监理公司对隐蔽工程检查后,方可进行下道工序;⑷防火、保温材料安装①必须采用合格的材料,即要求有出厂合格证;②在每层楼板与石板幕墙之间不能有空隙,应用镀锌钢板和防火棉形成防火带;③在北方寒冷地区,保温层最好应有防水、防潮保护层,在金属骨架内填塞固定,要求严密牢固;④幕墙保温层施工时,保温层最好应有防水、防潮保护层,以便在金属骨架内填塞固定后严密可靠;⑸饰面板安装①将运至工地的饰面板按编号分类,检查尺寸是否准确和有无破损、缺楞、掉角,按施工要求分层次将饰面板运至施工面附近,并注意摆放可靠;②先按幕墙面基准线仔细安装好底层第一皮板;③注意安放每皮金属挂件的标高,金属挂件应紧托上皮饰面板,而与下皮饰面板之间留有间隙;④安装时,要在饰面板的销钉孔或切槽口内注入胶,以保证饰面板与挂件的可靠连接;⑤安装时,宜先完成窗洞口四周的板镶边,以免安装发生困难;⑥安装到每一楼层标高时,要注意调整垂直误差,不要积累;⑦在搬运板时,要有安全防护措施,摆放时下面要垫木方;⑹嵌胶封缝板间的胶缝是石板幕墙的第一道防水措施,同时也使石板幕形成一个整体;①要按设计要求选用合格且未过期的耐候嵌缝胶;最好选用含硅油少的专用嵌缝胶,以免硅油渗透污染表面;②用带有凸头的刮板填装泡沫塑料圆条,保证胶缝的最小深度和均匀性;选用的泡沫塑料圆条直径应大于缝宽;③在胶缝两侧粘贴纸面胶带纸保护,以避免嵌缝胶污染板表面质量;④用专用清洁剂或草酸擦洗缝隙处板表面;⑤派受过训练的工人注胶,注胶应均匀无流淌,边打胶边用专用工具勾缝,使嵌缝胶呈微弧形凹面;⑥施工中要注意不能有漏胶污染墙面,如墙面上沾有胶液应立即擦去,并用清洁剂及时擦净余胶;⑦在大风和下雨时不能注胶;⑺清洗和保护施工完毕后,除去板表面的胶带纸,用清水和清洁剂将表面擦干净,按要求进行打蜡或刷保护剂;三、金属幕墙施工工艺1、工艺流程:测量放线→锚固件制作、安装→骨架制做安装→面板安装→嵌缝打胶→清洗保洁2、操作工艺:⑴、测量放线:根据设计和施工现场实际情况准确测放出幕墙的外边线和水平垂直控制线,然后将骨架竖框的中心线按设计分格尺寸弹到结构上;测量放线要在风力不大于4级的天气情况下进行,个别情况应采取防风措施;⑵、锚固件安装:幕墙骨架锚固件应尽量采用预埋件,在无预埋件的情况下采用后置埋件,埋件的结构形式要符合设计要求,锚栓要现场进行拉拔试验,满足强度要求后才能使用;锚固件一般由埋板和连接角码组成,施工时按照设计要求在已测放竖框中心线上准确标出埋板位置,后打孔将埋件固定,并将竖框中心线引至埋件上,然后计算出连接角码的位置,在埋板上划线标记,同一竖框同侧连接角码位置要拉通线检测,不能有偏差;角码位置确定后,将角码按此位置焊到埋板上,焊缝宽度和长度要符合设计要求,焊完后焊口要重新做防锈处理,一般涂刷防锈漆两遍;⑶、骨架制作安装:根据施工图及现场实际情况确定的分格尺寸,在加工场地内,下好骨架横竖料,并运至现场进行安装,安装前要先根据设计尺寸挂出骨架外皮控制线,挂线一定要准确无误,其控制质量将直接关系幕墙饰面质量,骨架如果选用铝合金型材,在锚固件一般采用螺栓连接,骨架在连接件间要垫有绝缘垫片,螺栓材质规格和质量要符合设计要求及规范规定,骨架如采用型钢,连接件即可采用螺栓也可采用焊接的方法连接,焊接质量要符合设计要求及规范规定,并要重新做防锈处理;主体结构与幕墙连接的各种预埋件,其数量、规格、位置和防腐处理必须符合设计要求;幕墙的金属框架与主体结构预埋件的连接、立柱与横梁的连接及幕墙面板的安装必须符合设计要求,安装必须牢固;⑷、面板安装面板要根据其材质选择合适的固定方式,一般采用自攻钉直接固定到骨架上或板折边加角铝后再用自攻钉固定角铝的方法,饰面板安装前要在骨架上标出板块位置,并拉通线,控制整个墙面板的竖向和水平位置;安装时要使各固定点均匀受力,不能挤压板面,不能敲击板面,以免发生板面凹凸或翘曲变形,同时饰面板要轻拿轻放,避免磕碰,以防损伤表面漆膜;面板安装要牢固,固定点数量要符合设计及规范要求,施工过程中要严格控制施工质量,保证表面平整,缝格顺直;⑸、嵌缝打胶:打胶要选用与设计颜色相同的耐侯胶,打胶前要在板缝中嵌塞大于缝宽2—4mm的泡沫棒,嵌塞深度要均匀,打胶厚度一般为缝宽的1/2;打胶时板缝两侧饰面板要粘贴美纹纸进行保护,以防污染,打完后要在表层固化前用专用刮板将胶缝刮成凹面,胶面要光滑圆润,不能有流坠、褶皱等现象,刮完后应立即将缝两侧美纹纸撕掉;打胶操作阴雨天不宜进行;硅硐结构密封胶应打注饱满,并应温度15℃~30℃、相对湿度50%以上、洁净的室内进行;不得在现场墙上打注;⑹、清洗保洁:待耐胶固化后,将整片幕墙用清水清洗干净,个别污染严重的地方可采用有机溶剂清洗,但严禁用尖锐物体刮,以免损坏饰面板表现涂膜;清洗后要设专人保护,在明显位置设警示牌以防污染或破坏;6、应注意的质量问题6.1玻璃幕墙中的明龙骨幕墙的框料和隐框幕墙的拼缝应横平竖直,隐框幕墙的缝宽应均匀,并符合设计要求;玻璃的安装方向应正确;6.2玻璃的品种,规格与颜色应与设计相符,整个幕墙玻璃的色泽应均匀,不得有颜色变色,镀膜脱落现象;6.3幕墙中的铝合金型材表面不应有脱膜现象;明龙骨幕墙的装饰扣板表面应平整,不应有变形,波纹或局部压碰等肉眼可观察到的质量缺陷;6.4幕墙的上下边及侧边封口,沉降缝、伸缩缝、防震缝的处理及防雷体系应符合设计要求;6.5铝合金骨料及玻璃的表面应洁净,不得有污物;玻璃应安装或粘结牢固,橡胶条和密封条应镶嵌密实,填充平整;6.6严格控制板质量,材质和加工尺寸都必须合格;6.7要仔细检查每块板有没有裂纹,防止板在运输和施工时发生断裂;6.8测量放线要十分清确,各专业施工要组织统一放线、统一测量,避免各专业施工因测量和放线误差发生施工矛盾;6.9预埋件的设计和放置要合理,位置要准确;6.10根据现场放线数据绘制施工放样图,落实加工尺寸;6.11安装和调整板位置时,可用垫片适当调整缝宽,所用垫片必须与挂件是同质材料;6.12固定金属挂片的螺栓要加弹簧垫圈,或调平调直拧紧螺栓后,在螺帽上抹少许胶固定;锚固件及骨架连接件等采用焊接的部位,焊接质量一定要符合设计要求,焊口涂刷防锈漆前要将焊渣焊药清理干净,防锈漆涂刷要到位,不能有漏刷漏涂等现象;6.13面板固定方法、固定点间距要符合设计要求,固定要牢固无松动;6.14饰面板运输安装过程中要注意保护,不能损坏划伤,影响饰面效果;6.15胶缝要宽窄、深浅一致,表现要光洁,不能有凹凸不平或剥裂等现象;9.11加强班组建设,做好班前安全教育;。
明框玻璃幕墙施工工艺流程

明框玻璃幕墙施工工艺流程一、明框玻璃幕墙施工准备1.施工现场准备(1)施工前,首先要对现场管理和安装人员进行全面的技术交底和质量交底及安全规范教育,备齐防火和安全器材与设施。
(2)在构件进场搬运、吊装时,需要加强保护,不得碰撞和损坏。
构件应放在通风、干直立摆放,在室外堆放时,应采取防护措施。
(3)构件应按品种、规格、种类和编号堆放在专用架子或垫木上。
玻璃构件应稍稍倾斜直立摆放,在室外堆放时,应采取防护措施。
(4)构件安装前,均应进行检验与校正。
构件应符合设计图纸及相关质量标准的要求,不得有变形、损伤和污染,不合格构件不得上墙安装。
玻璃幕墙构件在运输、堆放、吊装过程中有可能会人为地使构件产生变形、损坏等,在安装之前一定要提前对构件进行检验,发现不合格的应及时更换。
同时,幕墙施工承包商应根据具体情况和以往施工经验,对易损坏和丢失的构件、配件、玻璃、密封材料、胶垫等,应有一定的更换储备数量,一般构件、配件等在1%~5%,玻璃在安装过程中的损坏率为总块数的3%~5%。
(5)构件在现场的辅助加工如钻孔、攻丝、构件偏差的现场修改等,其加工位置、精度、尺寸应符合设计要求。
(6) 玻璃幕墙与主体结构连接的预埋件,应在主体结构施工时按设计要求埋设。
在放置预埋件之前,应按幕墙安装基线校核预埋件的准确位置,预埋件应牢固固定在预定位置上,并将锚固钢筋与主体构件主钢筋用铁丝绑扎牢固或点焊固定,防止预埋件在浇注混凝土时,位置变动。
施工时预埋件锚固钢筋周围的混凝土必须密实振捣,混凝土拆模时后,应及时将预埋件钢板表面上的砂浆清除干净。
2. 施工技术准备。
(1)熟悉本工程玻璃幕墙的特点,其中包括骨架设计的特点,玻璃安装的特点及构造方面的特点。
然后根据其特点,研究具体的施工方案。
(2)对照玻璃幕墙的骨架设计,复查主体结构的施工质量。
因为主体结构的施工质量如何,对骨架的位置影响较大。
特别是墙面的垂直度、平整度偏差,将影响整个幕墙的水平位置。
钢结构点式玻璃幕墙加工安装说明

钢结构点式玻璃幕墙加工安装钢结构点式玻璃幕墙是指接受钢结构(鱼腹式、三角形金属绗架)作为支撑受力体系,在钢结构上伸出钢爪固定玻璃的全玻璃幕墙。
金属绗架上安装钢爪,面板玻璃四角开孔,钢爪上的紧固件穿过玻璃上的孔,紧固后将玻璃固定在钢爪上,钢爪有H 形、X形、I形等,紧固件有浮头式、沉头式,当单层玻璃接受沉头式时,其厚度不能小于10mm,当接受中空玻璃时,有穿透式和不穿透式,穿透式贯穿两层玻璃及空气层,不穿透式固定在内片玻璃上。
金属绗架是由杆件组成的格构体系,当荷载只作用在节点上时,各杆只有轴力,截面上的应力分布匀整,可以充分发挥材料的作用。
该幕墙类型类似于四点支撑板,玻璃四角的爪件承受着风荷载和地震作用并传递到后面的钢结构上,最终传递到主体结构上。
一、点支式全玻幕墙构件制作及施工技术要求接受的玻璃必需经过钢化处理,并应经过均热处理,应符合有关国家标准的规定。
当幕墙有非隔热性的防火要求时,宜接受单片防火玻璃。
夹层和中空玻璃的内外片玻璃厚度差值不宜大于2mm。
1、玻璃的制作及施工技术要求①玻璃的切角、钻孔、磨边等必需在钢化前进行,钻孔直径不小于5mm, 并不小于玻璃板厚t,孔径不大于玻璃面板短边长度的1/3。
钻孔孔位允许偏差±0.8mm,孔距允许偏差±1.0mm,孔轴和玻璃平面垂直度允许偏差±0.2°。
孔洞边缘距板边间距大于或等于板厚度的2倍且不小于孔径。
位于玻璃面板角部的钻孔,孔边缘至玻璃面板角部顶点的距离不小于4t。
玻璃面板短边长度不小于8t。
②PVB夹胶玻璃内层玻璃6-12mm,外层玻璃厚8-15mm,且外层夹胶玻璃厚度最小为8mm(当风力很小而且幕墙高度较低时酌情运用),夹胶玻璃最大分格尺寸不宜超过节2m×3m,如经特别处理或有特别要求,在实行相应平安措施后可以适当放宽。
接受夹层玻璃应接受聚乙烯醇缩丁醛(PVB)胶片干法加工合成技术,且胶片厚度不得小于0.76mm。
玻璃幕墙工艺构造(单元式幕墙)、高清节点图

玻璃幕墙工艺构造(单元式幕墙)、高清节点图(1)骨架。
由纵向立柱和横档组成,它是用来支撑玻璃、固定玻璃,并通过连接件与墙体结构相连。
它将玻璃的自重和风荷载及其他荷载传给主体结构,使玻璃与墙体结构连成一整体。
① 型钢骨架:型钢做玻璃幕墙的骨架,玻璃镶嵌在铝合金的框内,然后再将铝合金框与骨架固定。
型钢组合的框架,其网格尺寸的适当可适当加大,但对主要受弯构件,截面不能太小,挠度最大处宜控制在5mm以内。
否则将影响铝窗的玻璃安装,也影响幕墙的外观。
② 铝合金型材骨架:用特殊断面的铝合金型材作为玻璃幕墙的骨架,玻璃镶嵌在骨架的凹槽内,玻璃幕墙的立柱与主体结构之间,用连接板固定。
安装玻璃时,先在立柱的内侧上安铝合金压条,然后将玻璃放入凹槽内,再用密封材料密封。
支承玻璃的横梁略有倾斜,目的是排除因密封不严而流入凹槽的雨水,并将外侧盖封住。
(2)玻璃是建造玻璃幕墙的关键材料。
它直接制约幕墙的各项性能,同时也是幕墙艺术风格的主要体现者,因此选用玻璃是幕墙设计的主要内容,如果玻璃选用不当会产生相当严重的后果。
要根据使用要求分别选用孵化玻璃、吸热玻璃、钢化玻璃、热反射镀膜玻璃、低辐射镀膜玻璃以及由这些单层玻璃组合成的夹层玻璃和中空玻璃。
① 浮法玻璃:浮法玻璃生产的成型过程是在通入保护气体(N2及H2)的锡槽中完成的。
熔融玻璃从池窑中连续流入并漂浮在相对密度大的锡液表面上,在重力和表面张力的作用下,玻璃液在锡液面上铺开、摊平、形成上下表面平整、硬化、冷却后被引上过渡辊台。
辊台的辊子转动,把玻璃带拉出锡槽进入退火窑,经退火、切裁,就得到平板玻璃产品。
浮法与其他成型方法比较,其优点是:适合于高效率制造优质平板玻璃,如没有波筋、厚度均匀、上下表面平整、互相平行 ;生产线的规模不受成形方法的限制,单位产品的能耗低 ; 成品利用率高; 易于科学化管理和实现全线机械化、自动化,劳动生产率高;连续作业周期可长达几年,有利于稳定地生产 ;可为在线生产一些新品种提供适合条件,如电浮法反射玻璃、退火时喷涂膜玻璃、冷端表面处理等。
01幕墙生产加工流程、工艺、质量保证措施

01幕墙生产加工流程、工艺、质量保证措施前言幕墙是现代建筑中应用广泛的外墙装饰材料,其功能不仅包括外观装饰,还要具备防水、防风、隔热、隔音等多种特性。
幕墙的生产加工流程和质量保证措施是保证幕墙质量的重要因素,本文将介绍幕墙生产加工流程、工艺及其质量保证措施。
一、幕墙生产加工流程1.1 设计和制作图纸幕墙的制作需要制作设计和施工图纸。
设计师根据建筑的风格,确定幕墙的设计风格、颜色和材料。
施工图纸包括幕墙制作需要的各种尺寸和加工要求。
1.2 零部件的制作1.2.1 铝型材的制作铝合金材料是生产幕墙的首选材料之一。
首先,根据施工图纸制定的要求,对铝材进行切割和开孔加工,然后将材料按图纸要求进行弯曲和冲压。
1.2.2 钢化玻璃的制作钢化玻璃是幕墙的常用材料之一。
制作钢化玻璃的要求非常高,需要对玻璃进行加热处理和急冷处理,使其具有良好的强度和韧性。
1.2.3 其他零部件的制作除了铝型材和钢化玻璃以外,幕墙还需要制作其他的零部件,如密封胶条、连接件等。
这些零部件的制作需要按照图纸要求进行加工,确保其质量。
1.3 部件的组装和加工1.3.1 铝型材的组装和加工铝型材的组装需要注意连接点的加工和位置,保证组装后的铝型材结构稳定,不易变形。
同时,铝型材的加工也需要进行表面处理和喷涂等操作,以提高其防腐蚀性和表面美观度。
1.3.2 玻璃的加工和组装幕墙的玻璃需要进行边缘的打磨和钻孔,以便与铝型材连接。
组装过程中,需要按照图纸要求进行断桥和密封处理,确保玻璃的密闭性。
1.3.3 其他零部件的组装幕墙的其他零部件,如密封胶条、连接件等的组装需要按照图纸要求进行连接和密封处理,确保其牢固和密闭性。
1.4 测试和品质保证1.4.1 试装和测量在幕墙制作完成后,需要进行试装和测量,确保其是否符合图纸要求。
同时,在试装过程中需要对连接点及其附近进行全面的检查和测试,确保幕墙的结构稳定,不易变形。
1.4.2 品质保证对于幕墙的制作过程中,每一道工序都需要进行严格的品质保证。
铝包钢龙骨玻璃幕墙施工工法

铝包钢龙骨玻璃幕墙施工工法一、前言铝包钢龙骨玻璃幕墙施工工法是一种常用的建筑外墙装饰工法,它以铝合金材料作为龙骨的支撑结构,采用高强度的玻璃作为外墙材料,具有结构轻巧、防火性能好、隔音降噪效果佳等特点。
本文将对这一工法进行详细介绍。
二、工法特点铝包钢龙骨玻璃幕墙施工工法具有以下特点:1. 结构轻巧:采用铝合金材料作为龙骨的支撑结构,具有重量轻、强度高的特点,减轻了建筑物的自重,降低了负荷。
2. 防火性能好:铝合金材料具有良好的耐火性能,能有效防止火灾事故的发生,提高建筑物的安全性。
3. 隔音降噪效果佳:铝合金材料具有良好的隔音效果,能够降低建筑内部与外部的噪音传递,提供一个安静的工作及生活环境。
4. 施工速度快:采用铝包钢龙骨玻璃幕墙施工工法可以实现工厂化预制,减少施工现场作业,大大提高了施工速度。
5. 施工质量高:通过严格的工艺控制和质量检测,能够确保幕墙的尺寸精度、平整度和装配质量,提高了施工质量。
6. 美观大气:铝合金材料具有优良的表面处理性能,可以根据建筑的要求进行多种颜色和表面处理,使幕墙具有较好的装饰效果。
三、适应范围铝包钢龙骨玻璃幕墙施工工法适用于各类建筑物,特别是高层建筑、商业综合体、办公楼、酒店等具有较高安全要求和装饰要求的建筑。
四、工艺原理铝包钢龙骨玻璃幕墙的施工工法与实际工程之间的联系主要体现在以下几个方面:1. 结构设计:根据建筑物的要求,设计合理的龙骨结构,以及幕墙与建筑物之间的连接方式,确保施工的稳定性和安全性。
2. 材料选用:铝合金材料具有优良的耐腐蚀性和强度,玻璃材料具有良好的透光性和防尘性,选择合适的材料可以提高施工工艺的可行性和效果。
3. 工艺流程:根据施工工艺的要求,确定龙骨安装、玻璃安装、密封胶处理等具体的工艺步骤和方法,并进行详细的分析和解释。
4. 技术措施:对施工过程中可能遇到的问题,采取相应的技术措施进行解决,确保施工的顺利进行。
五、施工工艺铝包钢龙骨玻璃幕墙的施工工艺主要包括以下几个施工阶段:1. 龙骨安装:首先在建筑物的结构上安装龙骨,保证龙骨的垂直度和平整度,然后进行龙骨的连接和固定,确保稳定性。
全玻璃幕墙工程施工工艺
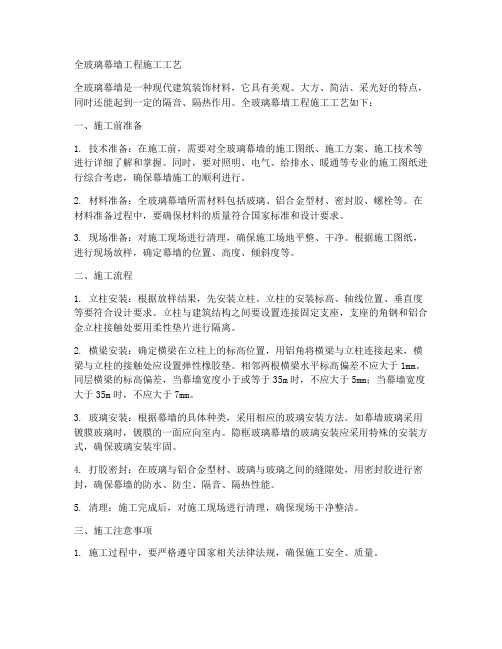
全玻璃幕墙工程施工工艺全玻璃幕墙是一种现代建筑装饰材料,它具有美观、大方、简洁、采光好的特点,同时还能起到一定的隔音、隔热作用。
全玻璃幕墙工程施工工艺如下:一、施工前准备1. 技术准备:在施工前,需要对全玻璃幕墙的施工图纸、施工方案、施工技术等进行详细了解和掌握。
同时,要对照明、电气、给排水、暖通等专业的施工图纸进行综合考虑,确保幕墙施工的顺利进行。
2. 材料准备:全玻璃幕墙所需材料包括玻璃、铝合金型材、密封胶、螺栓等。
在材料准备过程中,要确保材料的质量符合国家标准和设计要求。
3. 现场准备:对施工现场进行清理,确保施工场地平整、干净。
根据施工图纸,进行现场放样,确定幕墙的位置、高度、倾斜度等。
二、施工流程1. 立柱安装:根据放样结果,先安装立柱。
立柱的安装标高、轴线位置、垂直度等要符合设计要求。
立柱与建筑结构之间要设置连接固定支座,支座的角钢和铝合金立柱接触处要用柔性垫片进行隔离。
2. 横梁安装:确定横梁在立柱上的标高位置,用铝角将横梁与立柱连接起来,横梁与立柱的接触处应设置弹性橡胶垫。
相邻两根横梁水平标高偏差不应大于1mm。
同层横梁的标高偏差,当幕墙宽度小于或等于35m时,不应大于5mm;当幕墙宽度大于35m时,不应大于7mm。
3. 玻璃安装:根据幕墙的具体种类,采用相应的玻璃安装方法。
如幕墙玻璃采用镀膜玻璃时,镀膜的一面应向室内。
隐框玻璃幕墙的玻璃安装应采用特殊的安装方式,确保玻璃安装牢固。
4. 打胶密封:在玻璃与铝合金型材、玻璃与玻璃之间的缝隙处,用密封胶进行密封,确保幕墙的防水、防尘、隔音、隔热性能。
5. 清理:施工完成后,对施工现场进行清理,确保现场干净整洁。
三、施工注意事项1. 施工过程中,要严格遵守国家相关法律法规,确保施工安全、质量。
2. 幕墙施工过程中,要注重与建筑其他专业的协调,确保幕墙施工与建筑其他部分的顺利进行。
3. 施工过程中,要关注天气变化,避免在雨、雪天气进行施工。
玻璃幕墙施工工艺

玻璃幕墙施工工艺玻璃幕墙作为一种现代建筑外墙装饰材料,具有美观、透光性好等特点,越来越受到人们的喜爱。
在玻璃幕墙的施工过程中,需要经历多个工艺步骤,这些步骤的正确操作对于确保玻璃幕墙的安全和质量至关重要。
下面将介绍一下玻璃幕墙的施工工艺。
一、基础处理:在施工前,首先需要对施工基础进行处理。
这一步骤主要包括地面处理和墙体处理两部分。
地面处理需要确保地面平整、结实,以便于后续的施工操作;墙体处理需要清除墙体表面的杂物,并进行打磨、除尘等工作,以确保墙体的平整度和强度。
二、铝合金支架安装:在基础处理完成后,需要进行铝合金支架的安装。
铝合金支架是玻璃幕墙的骨架,承担着固定玻璃和承重的作用。
安装过程中,需要按照设计要求进行支架的定位和固定,确保支架的牢固和平直度。
三、玻璃安装:在支架安装完成后,需要进行玻璃的安装。
首先,需要按照设计要求进行玻璃的尺寸测量和加工,确保玻璃的精准度和质量。
然后,将预先加工好的玻璃安装在支架上,采用专用的夹具和胶水进行固定。
玻璃安装过程中,需要注意对玻璃的保护,防止划伤和损坏。
四、密封胶安装:玻璃安装完成后,需要对玻璃与支架之间的间隙进行密封处理。
密封胶具有防水、防风、隔热等功能,能够提高玻璃幕墙的安全性和保温性能。
在安装密封胶时,需要先进行材料的配比和搅拌,然后用专用工具将密封胶填充到玻璃与支架之间的缝隙中,确保密封胶的均匀性和密封性。
五、玻璃清洁和保护:玻璃安装和密封胶安装完成后,还需要对玻璃进行清洁和保护。
清洁过程中,需要使用专业的清洁剂和工具进行清洗,确保玻璃表面的干净和亮丽。
保护过程中,需要使用专业的保护膜覆盖在玻璃表面,以防止划痕和污染。
六、验收和保养:玻璃幕墙施工完成后,需要进行验收和保养。
验收过程中,需要对玻璃幕墙进行外观、性能等方面的检查,以确保施工质量符合设计要求。
保养过程中,需要定期对玻璃进行清洁和维护,及时修复和更换受损的部分,延长玻璃幕墙的使用寿命。
在玻璃幕墙的施工过程中,还需要注意安全施工,遵守相关的法规和规范。
幕墙施工方案和技术措施

幕墙施工方案和技术措施第二章、施工方案和技术措施根据本项目的施工情况和我司的过往施工经验,采取如下施工方案和技术措施。
第一节加工工艺、设备、检测、运输方案1、玻璃幕墙构件加工工艺玻璃构件在净化的玻璃加工厂加工。
玻璃经切割,倒棱、磨边、净化后用双组分结构胶合成。
每项工程在大面积打胶前,必须用选定的结构胶做相容性试验。
相容性试验合格后,才能进行大面积打胶。
玻璃加工精度表:用结构胶将玻璃构件与铝合金付框粘接在一起,组装的工序是:净化:用化学清洁溶液(试剂级丁酮、异丙醇或二甲苯)对需注胶部位进行清洗。
化学清洁溶液不得混用。
清洗方法为“二块抹布法”,抹布必须用白色清洁、柔软、烧毛处理的白布,其他抹布严禁使用。
设置垫条:设置垫条是为了给注胶创造一个空腔,空腔的宽度尺寸和胶缝宽缝尺寸一致,设置时要采用靠尺或定位器定位,以保证垫条定位正确;玻璃构件定位:玻璃构件要固定在铝合金框规定位置,定位采用平台夹具进行,以保证两者基准线重合,要求一次定位成功。
此时要求质检员进行首检。
并把检验结果记录在案。
注胶:将注胶处周围非注胶面用保护胶带保护,防止这些部位被污染。
检查密封胶品种牌号,失效期及相容性试验报告,全部符合才能使用。
所使用的结构胶为双组份,注胶时要保持一定速度,以保证胶注满空腔,并溢出2至3毫米,注胶速度要均匀,防止空穴和减少气泡残留。
注胶结束后,立即用刮勺将胶缝压实刮干。
对双组分胶要做蝴蝶试验和扯断试验及切开实验,试验合格后再注胶,并将试验记录编号保存,同时按规定作剥离试验。
剥离样品不合格时,查明原因并采取补救措施。
即使剥离样品显示好粘合性,我公司仍对合格的玻璃板块任意抽检进行常规的切开检查粘合剥离试验。
并将试验记录编号保存。
清洁污渍:注胶完毕,应将胶缝四周保护胶带撕掉,保护胶带以外的胶污渍用溶剂清洗干净。
注胶完毕后,质检员要对所有注胶成品进行抽检,抽检率为1%。
并在每块板块的右上角铝框上贴上标签(标明规格、打胶日期及试件编号)并建立起挡案保存,以便出现问题时查找。
玻璃幕墙施工工艺及流程
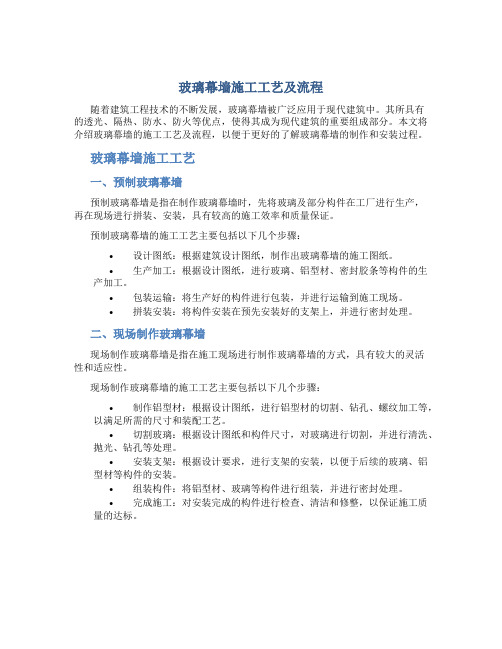
玻璃幕墙施工工艺及流程随着建筑工程技术的不断发展,玻璃幕墙被广泛应用于现代建筑中。
其所具有的透光、隔热、防水、防火等优点,使得其成为现代建筑的重要组成部分。
本文将介绍玻璃幕墙的施工工艺及流程,以便于更好的了解玻璃幕墙的制作和安装过程。
玻璃幕墙施工工艺一、预制玻璃幕墙预制玻璃幕墙是指在制作玻璃幕墙时,先将玻璃及部分构件在工厂进行生产,再在现场进行拼装、安装,具有较高的施工效率和质量保证。
预制玻璃幕墙的施工工艺主要包括以下几个步骤:•设计图纸:根据建筑设计图纸,制作出玻璃幕墙的施工图纸。
•生产加工:根据设计图纸,进行玻璃、铝型材、密封胶条等构件的生产加工。
•包装运输:将生产好的构件进行包装,并进行运输到施工现场。
•拼装安装:将构件安装在预先安装好的支架上,并进行密封处理。
二、现场制作玻璃幕墙现场制作玻璃幕墙是指在施工现场进行制作玻璃幕墙的方式,具有较大的灵活性和适应性。
现场制作玻璃幕墙的施工工艺主要包括以下几个步骤:•制作铝型材:根据设计图纸,进行铝型材的切割、钻孔、螺纹加工等,以满足所需的尺寸和装配工艺。
•切割玻璃:根据设计图纸和构件尺寸,对玻璃进行切割,并进行清洗、抛光、钻孔等处理。
•安装支架:根据设计要求,进行支架的安装,以便于后续的玻璃、铝型材等构件的安装。
•组装构件:将铝型材、玻璃等构件进行组装,并进行密封处理。
•完成施工:对安装完成的构件进行检查、清洁和修整,以保证施工质量的达标。
玻璃幕墙施工流程一、验收在进行玻璃幕墙的施工前,需要进行现场的验收工作,包括设备设施、场地环境、材料等方面的验收。
二、基础进行玻璃幕墙施工前,需要对地基进行处理,包括地面平整、地基加固等。
三、支架根据设计图纸、施工方案,安装支架,为后续的构件安装提供基础条件。
四、铝型材制作和安装根据设计要求,进行铝型材的制作和安装,包括切割、加工、螺纹等处理。
五、玻璃制作和安装根据设计要求和现场尺寸情况,进行玻璃的切割、加工、钻孔等处理,并进行安装、调试和密封处理。
- 1、下载文档前请自行甄别文档内容的完整性,平台不提供额外的编辑、内容补充、找答案等附加服务。
- 2、"仅部分预览"的文档,不可在线预览部分如存在完整性等问题,可反馈申请退款(可完整预览的文档不适用该条件!)。
- 3、如文档侵犯您的权益,请联系客服反馈,我们会尽快为您处理(人工客服工作时间:9:00-18:30)。
幕墙玻璃加工工艺幕墙玻璃加工工艺1 材料选择玻璃根据设计图纸的要求选用,送样品和产品合格证等资料报业主同意封样。
然后按封样样品采购玻璃,不许中途变更。
2 钢化玻璃加工钢化玻璃加工工艺流程(1)接单接单审查后统计及搭配,必须使利用率达到最高程度,在加工单确认无误的情况下,方能到材料部门办理领用手续。
(2)材料领用与搬运a.材料领用手续审批后领用材料,搬运需用吊车(或行车)时,必须专职人员操作。
b.领用的整箱玻璃摆放,应保证玻璃箱的倾斜度,玻璃开箱时应注意避免铁钎与玻璃碰撞,造成玻璃碎裂。
c.大片玻璃搬运或开盖时应注意以下事项:a)检查玻璃吸盘是否正常。
b)检查大片玻璃四周是否有裂痕现象,如发现裂痕应及时处理,方能搬运。
c).检查无异常现象,方能将玻璃吸盘适当用力压在玻璃面上,吸扣压紧,并检查玻璃吸压是否扣牢。
d).人工搬运玻璃,需四人保持一致,避免玻璃大幅度摇摆,造成玻璃碎裂。
玻璃平放时,四人必须配合一致,同时平放于台面上。
e). 行车吊运时,应注意行吊行走平稳,定时检查电动玻璃吸盘的充电情况。
(3)玻璃切割1、手工切割a. 测量尺寸的测量仪必须是同一类型,度量时要准确。
b. 玻璃切割时误差不能超过1 毫米。
c.切割后的半成品应按指定地方堆放整齐,堆放时必须在块与块之间用纸隔开(计划清洗的玻璃除外)。
2、机器切割玻璃a.启动玻璃切割机(包括电脑及打印机)b.将原片规格和割片数量、规格尺寸输入电脑,电脑自动拼图,计算所用原片数量及利用率。
c.打印拼图结果,并转送至玻璃切割机。
d.装载原片玻璃于机器切割台并按要求定好位。
e.选择并运行切割程序,切割玻璃。
f.分离割片,并将其搬运存放于指定架上。
(4)磨边a.启动玻璃磨边机b.调整机器参数,即磨削量、压带宽度、传送速度以及需抛光时调整各抛光轮气压值。
c. 试磨:用一块与所要磨的玻璃类型、厚度相同的玻璃进行试磨,检查其磨削量、前后倒角、磨边质量是否符合要求,不符合要求,重新调整,直到满意,确认参数。
d. 装载玻璃磨边。
e. 检查磨边质量,适当调整机器参数。
f. 磨好边的玻璃,搬至指定玻璃架,并贴上标签。
(5)清洗a. 玻璃清洗机使用前检查,看水量是否充足。
b. 启动清洗机(包括水处理系统),把机器置于自动运行状态。
c.装载玻璃清洗,检查清洗效果,如不合要求,则调整水温,洗刷速度及传送速度,直至合格。
d. 按规定的顺序,规格装载玻璃,自动清洗。
e. 清洗后的玻璃堆放时,块与块之间用纸隔开,各种规格分开并标记好,避免损坏和造成混乱。
(6)钢化a. 检查清洗后的玻璃是否符合要求,凡有夹砂、划痕等缺陷的玻璃不能钢化。
b. 根据深加工玻璃的图纸要求,调整好钢化炉参数。
c. 先取2 块相同厚度的同类玻璃作钢化,检查钢化效果是否符合要求。
d. 装载玻璃钢化。
e. 钢化后的玻璃应认真检查,合格产品搬运至指定玻璃架。
(7)均质处理按图纸要求需作均质处理的钢化玻璃必须到引爆炉作均质处理,然后运至半成品区转入下道工序。
3 钢化中空玻璃加工钢化中空玻璃加工工艺流程钢化中空玻璃加工各工序要领材料领用、搬运、切割、磨边、清洗、钢化、均质处与2 相关工序相同。
(1)组装铝框a. 根据加工单从铝材切割工序领取已切割好的铝条。
b. 批量选取装框所用铝条,在其中一端装好角接头,并用布沾上二甲苯或酒精擦拭干净。
c. 把装好角接头擦拭干净的铝条放在干燥剂填充机上填充干燥剂。
d. 取下已装好干燥剂的铝条放在工作面上,组装成铝间框.把铝间框有序挂在或摆在干净的地方。
(2)涂丁基胶a.接通丁基胶挤出机电源,预热丁基胶至设定温度(或在上次开机时已设定温度自动预热)。
b.启动传送带,检查传送速度及挤出压力是否需要重新调整,直至符合要求。
c.把其中一个铝间框放入测量装置测量铝条宽度,喷咀间距自动调整。
d. 铝间框靠紧定位板,放在传送带上,自动注胶。
e. 每个框四边涂好胶,按顺序挂在检查粘框站铁钩上。
(3)检查粘框及合片a. 根据工艺要求,调节粘框定位机构,保证注胶浓度符合要求。
b. 启动检查粘框站及合片挤压铝,并转到自动运行状态。
c. 玻璃自动进入检查站,人工检查外观是否符合质量要求,不符合要求的进行处理或下线;第一片玻璃检查合格后踏下开关,进入合片挤压站;第二片玻璃检查合格后,按要求粘好框及踏下开关,进入合片挤压站。
d. 合片挤压站自动合片挤压。
(4)自动注胶a. 启动自动注胶机。
b. 待合片挤压工序准备好,开始混胶直至均匀,然把自动控制注胶机置于自动运行状态。
c. 合好片的中空玻璃进入注胶机,注胶机开始注胶,检查注胶质量是否符合要求.不符合要求时调整机器有关参数,直到满意。
d. 注胶机自动注胶,注好胶的中空玻璃用自动吸盘卸下,放在专用玻璃架上存放。
e. 注胶完毕,进行A 组份冲洗注胶枪,直至排胶无黑色为止。
4 热弯玻璃的加工及精度控制(1) 产前准备:根据弯曲玻璃的数量、尺寸准备原材料、模具材料。
(2) 模具设计:根据玻璃的弯曲要求(单曲面、双曲面、球体等),技术部设计小组采用CAD 画图电脑模拟设计和实物模具制作。
1.根据客户提供的图样或设计方案放样,将不规则曲面图形(3D 图形)分多段作XY、XZ、YZ 平面投影,转化为若干个平面图形.同时将3D曲面分成若干条等距曲线,通过电脑自动玻璃切割机,CAD 画图将曲线切割为1:1 玻璃模板以作模具制作样板,切割精度为正负0.5mm。
2.制作木制模型:技术部制作小组模拟3D 图形,按照设计的模具加工工艺制作一定比例样品模型,检测模具生产的可行性和准确性,并为1:1 的热弯模具制作提供三维形象图形,尺寸误差保证在正负1mm。
(3) 弯管:模具制作小组根据样品模型和玻璃模板将管材分段折弯,保证每段弧度与高精度玻璃模板弧度保持一致,弧度误差控制在0.3%之内。
(4) 模具制作:用弯好的镀锌管制作热弯模具,按照玻璃立体图、实物模具、各平面投影图将各弧度的镀锌管在立体空间里焊接在角钢底架上,在每条弯管下焊接支撑钢管。
(5) 模具校核:用玻璃模板对每条镀锌弯管进行弧度校核并加以纠正。
在镀锌弯管的适当部位用支撑管加以固定以防模具变形。
(6) 模具整理:将成型的模具表面打磨,去掉表面杂物和碎屑,在镀锌弯管表面刷涂氧化物保护层以保护模具表面光滑。
(7) 玻璃加工:根据放样分段投影平面图形、实物模型测量、热弯玻璃受热拉伸等特性结合,技术部设计小组通过CAD 绘图将3D 曲面转化为平面展开图,并转到电脑自动玻璃切割机进行玻璃切割;玻璃边部用异型磨边机进行抛光处理。
(若3D 曲面无法在不破坏玻璃的情况下进行平面展开,则提出图形修改意见)(8) 玻璃热弯:根据玻璃加工要求,将四件8mm 玻璃整齐放置在模具上叠烧,玻璃间放置隔离材料,将玻璃推入热弯炉加热成型。
在热弯烧制时,根据玻璃的不同部位和形状控制相应区域温度、加热时间、保温时间,保证玻璃与模具的吻合性和玻璃的质量。
随时观察玻璃整体与模具间的吻合程度,升温和降温速度均要严格控制。
(9) 检验:玻璃出炉后,检查核对玻璃的尺寸、弧度、外观质量、玻璃间吻合度。
(10) 检验合格后贴半成品标识转运到下道工序进行加工。
(11) 作生产、质量记录,清理现场,保养设备。
加工好的磨具成品2 不锈钢驳接系统及其连接件加工工艺2.1 拉杆及玻璃肋板的定位2.1 不锈钢玻接系统加工本工程采用不锈钢玻接系统为特种不锈钢夹具,全部委托贵航加工,批量生产前,样品已进行工业性试验,符合设计要求.由于该不锈钢夹具全部委托贵航生产,我方只派机械工程师常驻该厂生产车间,进行产品质量全过程的监督与控制,工艺流程暂略.2.2 其他连接件加工其他连接件由公司加工生产中心加工,品质部检验合格签发合格证.运至工地安装,采用汽车运输以减少途中运输时间,现场设临时仓库以储备待安装半成品,并由专人管理仓库.2.3 不锈钢杆的加工1)本工程不锈钢杆采用Ф12 不锈钢钢棒,其非弹性变形量较小。
2)不锈钢钢棒进场后,应进行力学性能检测。
同一批拉杆中取样不少于 3 件,进行破坏性试验。
不锈钢杆力学性能应保证。
3)不锈钢杆下料前应进行材料、复核材质。
4)不锈钢杆制作完成后,应进行尺寸复查后,再进行表面处理。
表面处理根据设计要求采用抛光或亚光。
5)不锈钢杆加工过程中,应严格执行半成品保护程序,防止由于施工过程或其它工序施工破坏拉杆表面效果。
不锈钢杆采用软塑包裹或彩条布、麻袋片进行包裹保护。
2.2 安装顺序在拉杆与玻璃肋板的安装过程中要掌握好施工顺序,安装必须按先上后下,先横后竖的原则进行安装。
根据图纸给定的拉杆长度尺寸,加1mm-3mm 从顶部结构开始挂杆呈自由状态,待全部竖向杆安装结束后进行调整,调整顺序也是先上后下,按尺寸控制单元逐层调整到位.2.3 玻璃安装及控制(1)玻璃到达施工现场后,由现场质检员与安装组长对玻璃的表面质量,公称尺寸进行100%的检测。
同时使用玻璃边缘应力仪对玻璃的钢化情况进行全检。
玻璃安装顺序采用先上后下,逐层安装调整,(2)玻璃垂直运输:采用在脚手架上临时搭设的简易龙门吊,使用真空吸盘及尼龙包装带垂直提升到安装平台上进行定位,安装。
在整个过程中减少尺寸积累误差在每个控制单元内尺寸公差带为3mm。
(3)玻璃安装质量应符合下述要求:a. 两邻两玻璃面接缝高低差:±0mmb. 上、下两块玻璃接缝水平偏差:±0mmc. 左、右两块玻璃接缝水平偏差:±0mmd. 玻璃外表面垂直接缝偏差:±0mme. 玻璃外表面水平接缝偏差:±0mmf. 玻璃外表面平整度:H≤20m,3.0mmg. 胶缝宽度(与设计比):±5mm2.4 打胶工艺控制与检测1)在玻璃安装调整结束后进行打胶使玻璃的缝隙密封。
2)打胶顺序是先上后下,先竖向后横向。
3)打胶过程应注意事项:先清洗玻璃,特别是玻璃边部与胶连接处的污迹要清洗擦干,在贴美纹纸后要24 小时之内打胶并及时处理,打好的胶不得有外溢,毛刺等现象;打胶时采用双人里外同步对打的方法,保证胶缝填实;在刮胶过程中必须保正横向和纵向交缝的接口处平滑,如有凸起必须在胶表面硫化前修整好,保证在胶缝处排水通畅;在隔日打胶时,胶缝连接处先清洗已打好的胶头,切除园弧头部以保正两次打胶的连接紧密;如在自检中发发现有局部打胶缺陷(如气泡、空心、断缝、表面严重裂纹),必须将该部分切除清理后再进行补胶。
感谢您的阅读!。