叶轮精密铸造工艺
叶轮精密铸造工艺
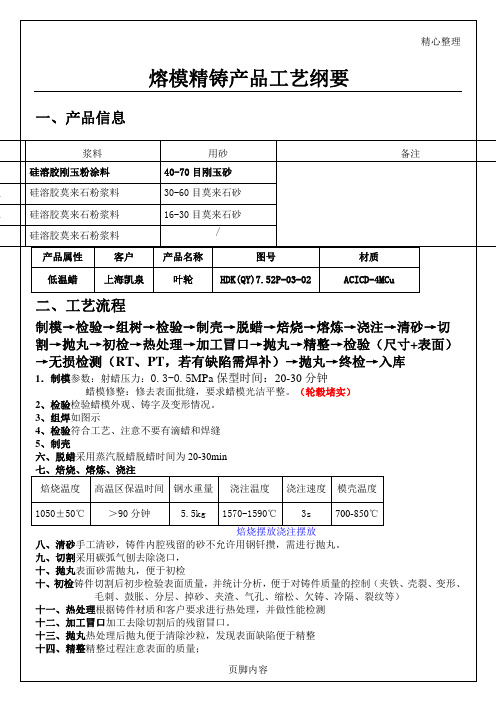
精心整理熔模精铸产品工艺纲要一、产品信息浆料用砂备注硅溶胶刚玉粉涂料40-70目刚玉砂层硅溶胶莫来石粉浆料30-60目莫来石砂层硅溶胶莫来石粉浆料16-30目莫来石砂硅溶胶莫来石粉浆料/产品属性客户产品名称图号材质低温蜡上海凯泉叶轮HDK(QY)7.52P-03-02 ACICD-4MCu二、工艺流程制模→检验→组树→检验→制壳→脱蜡→焙烧→熔炼→浇注→清砂→切割→抛丸→初检→热处理→加工冒口→抛丸→精整→检验(尺寸+表面)→无损检测(RT、PT,若有缺陷需焊补)→抛丸→终检→入库1.制模参数:射蜡压力:0.3-0.5MPa保型时间:20-30分钟蜡模修整:修去表面批缝,要求蜡模光洁平整。
(轮毂堵实)2、检验检验蜡模外观、铸字及变形情况。
3、组焊如图示4、检验符合工艺、注意不要有滴蜡和焊缝5、制壳六、脱蜡采用蒸汽脱蜡脱蜡时间为20-30min七、焙烧、熔炼、浇注焙烧温度高温区保温时间钢水重量浇注温度浇注速度模壳温度1050±50℃>90分钟 5.5kg 1570-1590℃3s 700-850℃焙烧摆放浇注摆放八、清砂手工清砂,铸件内腔残留的砂不允许用钢钎攒,需进行抛丸。
九、切割采用碳弧气刨去除浇口,十、抛丸表面砂需抛丸,便于初检十、初检铸件切割后初步检验表面质量,并统计分析,便于对铸件质量的控制(夹铁、壳裂、变形、毛刺、鼓胀、分层、掉砂、夹渣、气孔、缩松、欠铸、冷隔、裂纹等)十一、热处理根据铸件材质和客户要求进行热处理,并做性能检测十二、加工冒口加工去除切割后的残留冒口。
十三、抛丸热处理后抛丸便于清除沙粒,发现表面缺陷便于精整十四、精整精整过程注意表面的质量;页脚内容精心整理十五、检验根据图纸及公差标准检验铸件,根据客户及图纸要求检验表面质量十六、无损检测根据客户要求进行RT和PT检验(若有缺陷需焊补返修,焊补需根据相应的材质和客户标准进行)十七、终检十八、入库页脚内容。
双吸叶轮铸造工艺

双吸叶轮铸造工艺
双吸叶轮铸造工艺是一种用于制造双吸离心泵叶轮的工艺。
该工艺的基本步骤如下:
1. 模具准备:根据设计要求,制作双吸泵叶轮的模具。
2. 原材料准备:选择适合的铸造材料,通常使用不锈钢、铜合金或铸铁。
3. 融化材料:将选定的铸造材料放入高温熔炉中融化,直至达到合适的铸造温度。
4. 塑造叶轮:将熔化的铸造材料倒入准备好的模具中,并通过振动、压力或离心力等方式,使材料充分填充模具中,形成叶轮的形状。
5. 冷却固化:待铸造完成后,将叶轮从模具中取出,放置在冷却台上进行自然冷却和固化,以提高叶轮的强度和硬度。
6. 去除模具:待叶轮完全冷却固化后,将模具从叶轮上取下,得到最终的双吸泵叶轮产品。
7. 加工和修整:根据需要,对双吸泵叶轮进行精加工和修整,以提高叶轮的精度和表面质量。
8. 检验和测试:对双吸泵叶轮进行非破坏性和破坏性检验,检查其尺寸、质量和物理性能等,并进行必要的测试和测量。
9. 成品包装:将检验合格的双吸泵叶轮进行清洁和包装,以便运输和存储。
以上就是双吸叶轮铸造工艺的基本步骤,不同工厂和产品可能会有一些细微的差别和调整。
涡轮叶片精铸全过程

涡轮叶片精铸全过程及其影响因素无余量熔模精密铸造目前为涡轮叶片制造的最佳手段。
其工艺流程主要包括型芯模具的设计与制造、压制型芯、蜡模模具的设计与制造、装配注蜡、涂浆制壳、干燥型壳、脱蜡、烧结、浇注金属、脱壳脱芯、激光打孔等环节。
模具的设计定型:1、精铸模具型腔体设计,首先建立叶片零件模型,包括叶身、缘板、榫头伸根的内型特征,以此构建叶身实体。
此后进行叶片的多态模型转化,由叶片零件模型转化到型腔体模型。
2、型腔优化及精铸仿真,根据铸件的收缩原理采用反变形优化工艺方法对型腔进行放型最终得到模具型腔。
3、精铸模具结构设计与制造,确定核心包络块并设计叶片精铸模具模架,再由模具标准件经机械加工、表面处理、装配、检测、修模到定型。
模具结构的合理性和尺寸精度对于熔模精铸件十分重要。
设计制造高质量的内外型模具即精铸模具就成为精密熔模铸造技术的关键。
陶瓷型芯的制造:在叶片蜡型压制之前是需制作设计陶瓷型芯模具,并压制合格陶瓷型芯。
陶瓷型芯的制备包括浆料的配制、型芯压制、型芯素肧的修理、烧结、强化及其过程质量控制与检验等。
决定浆料性能的因素有陶瓷粉料的成分与颗粒形状、增塑剂的成分和性质、粉料和增塑剂的比例等。
陶瓷型芯的质量很大程度上取决于素胚的压制质量,压制压力、锁模压力、浆料温度、保压时间等是影响陶瓷型芯压制质量的主要原因。
蜡模的制造工艺:合格的蜡型是制备精密铸件的前提,压制蜡型时,将陶芯放入蜡型模具中,并依靠定位元件对其定位。
生产中大多采用压力把糊状模料压入压型的方法制造熔模。
压制蜡基模料时,分型剂可为机油、松节油等;分型剂层越薄越好,使熔模能更好地复制压型的表面,提高熔模的表面光洁度。
模料压制温度、压注压力、保压时间、压型温度、和模力、分型剂种类及其用量,以及制模和存放熔模的环境都会影响蜡模的质量。
熔模铸型的制造工艺:首先是熔模的组装,把形成铸件的熔模和形成浇冒口系统的熔模组合在一起,主要采用焊接法,用薄片状的烙铁,将熔模的连接部位熔化,使熔模焊在一起。
航空发动机叶轮叶片制造工艺研究

航空发动机叶轮叶片制造工艺研究随着航空业的不断发展,航空发动机的性能和质量要求越来越高,而发动机叶轮叶片作为发动机的核心部件之一,其制造工艺对发动机的性能和寿命有着至关重要的影响。
本文旨在探究航空发动机叶轮叶片的制造工艺。
一、叶轮叶片的材料选择叶轮叶片是承受高温高压气流冲刷和疲劳循环作用的重要部件,因此材料的选择至关重要。
目前常用的叶片材料包括镍基合金、钛合金、镁合金等。
镍基合金是叶片材料的主要选择,主要因为其具有出色的高温性能和良好的耐腐蚀性能。
二、叶轮叶片的制造工艺1.锻造工艺锻造是叶片制造的主要工艺之一,常用的锻造工艺包括自由锻造、闭式锻造和等轴锻造。
自由锻造工艺适用于大型叶片的生产,闭式锻造适用于小型叶片的生产,而等轴锻造则可以获得均匀的组织结构和较高的材料性能。
2.热等静压成型工艺热等静压成型技术是近年来发展的新工艺,它可以通过热压技术实现叶片的无缝成型,获得均匀细致的组织结构,具有较高的材料性能和较好的抗疲劳性能。
3.精密铸造工艺精密铸造技术可以获得高精度、高韧性的铸造件,其制造工艺相对简单,适用于复杂形状的叶片。
但需要注意的是,精密铸造的准确性和一致性对材料性能有很大的影响,需要进行严格控制。
三、叶片表面处理为了提高叶片的耐腐蚀性能和抗疲劳性能,需要对叶片进行表面处理。
常用的处理方法包括电火花加工、仿形磨削、化学抛光等。
其中,电火花加工可以获得复杂的形状和高精度,而仿形磨削则可以获得更好的表面粗糙度和平滑度。
四、结语航空发动机叶轮叶片的制造工艺是一个复杂而又重要的环节,需要各种工艺和技术的协同配合,才能获得高品质的叶片产品。
随着制造技术的不断发展,相信未来将会出现更加优秀的叶片制造工艺和材料,为航空发动机的性能提升提供更好的支持。
不锈钢叶轮的铸造工艺
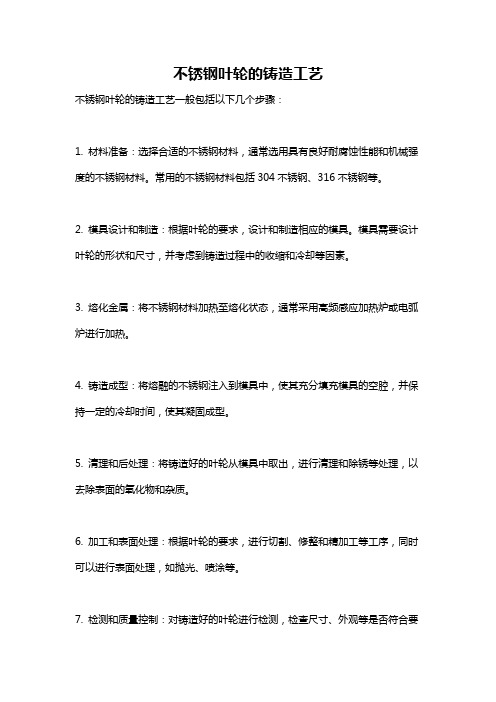
不锈钢叶轮的铸造工艺
不锈钢叶轮的铸造工艺一般包括以下几个步骤:
1. 材料准备:选择合适的不锈钢材料,通常选用具有良好耐腐蚀性能和机械强度的不锈钢材料。
常用的不锈钢材料包括304不锈钢、316不锈钢等。
2. 模具设计和制造:根据叶轮的要求,设计和制造相应的模具。
模具需要设计叶轮的形状和尺寸,并考虑到铸造过程中的收缩和冷却等因素。
3. 熔化金属:将不锈钢材料加热至熔化状态,通常采用高频感应加热炉或电弧炉进行加热。
4. 铸造成型:将熔融的不锈钢注入到模具中,使其充分填充模具的空腔,并保持一定的冷却时间,使其凝固成型。
5. 清理和后处理:将铸造好的叶轮从模具中取出,进行清理和除锈等处理,以去除表面的氧化物和杂质。
6. 加工和表面处理:根据叶轮的要求,进行切割、修整和精加工等工序,同时可以进行表面处理,如抛光、喷涂等。
7. 检测和质量控制:对铸造好的叶轮进行检测,检查尺寸、外观等是否符合要
求,并进行非破坏性和破坏性测试,以确保其质量符合标准要求。
以上是不锈钢叶轮的一般铸造工艺流程,具体的工艺参数和步骤可能会根据具体的叶轮设计和铸造工艺的要求而有所不同。
精密铸造不锈钢双吸叶轮工艺研究

精密铸造不锈钢双吸叶轮工艺研究摘要:文章简要介绍了不锈钢精密铸造的技术特点,并简要总结了目前涡轮铸造工艺的主要缺陷。
然后提出改进措施,描述改进现象,总结改进效果。
关键词:精铸工艺;不锈钢双吸叶轮;工艺研究;改进措施前言叶轮是造船、泵阀、运输等行业大型设备的重要组成部分,对整个设备的整体性能起着决定性的作用。
目前复杂的单片涡轮铸造工艺存在一定的生产困难,因此对涡轮铸造工艺的研究是铸造行业的一个热点问题。
这就是为什么铸造工艺,在生产中应用,远远不能满足需求,离心铸造生产质量、企业如何使用设备和技术,采用了铸造工艺合理组合,满足车轮生产工艺要求的制造工艺已成为生产领域的研究和铸造解决方案。
一、精密铸造不锈钢双吸叶轮概述1.双吸轮是双吸离心泵的中心部件,由两个相同直径的单吸轮同时工作组成,可实现相同直径的双吸。
其特点是结构对称、运行稳定、几乎完全无轴向力、优异的液压性能和高工作效率。
双抽离心泵具有高海拔、高流量的特点,广泛应用于农田灌溉、冶金化工等领域。
2.图1所示是为双吸叶轮结构示意图,由左、右盖板、叶片、轮毂四部分组成。
双吸叶轮CF8M材质,轮廓最大直径的车轮是450mm维度和退出25mm,热结的圆的直径的轮毂,轮毂为150mm,长度是180mm,直径60毫米的孔。
尺寸公差要求ISO8062CT6叶片粗糙度工作3.2,铸件RT区域检验,100% PT ASMEB16.34 ii验收标准。
中心轮毂的两端在中心又小又大,不利于顺序凝固,收缩缺陷可能发生在较厚的部分。
虽然外形覆盖板直径的车轮,车轮输出规模很小,腔体内部的车轮是后轮的外墙之间的狭窄空间,后轮的内心是狭窄的后车轮过热,后轮的双重愿望车轮外壁之间的联络,这可能造成提现故障回路源头。
此外,双抽汽涡轮的法兰极薄,进口法兰厚度仅为2 - 3mm,容易导致冷绝缘、铸件不足等进口法兰缺陷。
因此,在生产合格产品时,必须消除中心轮毂根部和环弧R处的收缩缺陷,防止冷绝缘和进口叶片浇注不足。
- 1、下载文档前请自行甄别文档内容的完整性,平台不提供额外的编辑、内容补充、找答案等附加服务。
- 2、"仅部分预览"的文档,不可在线预览部分如存在完整性等问题,可反馈申请退款(可完整预览的文档不适用该条件!)。
- 3、如文档侵犯您的权益,请联系客服反馈,我们会尽快为您处理(人工客服工作时间:9:00-18:30)。
硅溶胶莫来石粉浆料
16-30目莫来石砂
沾浆
硅溶胶莫来石粉浆料
/
六、脱蜡采用蒸汽脱蜡脱蜡时间为20-30min
七、焙烧、熔炼、浇注
焙烧温度
高温区保温时间
钢水重量
浇注温度
浇注速度
模壳温度
1050±50℃
>90分钟
1570-1590℃
3s
700-850℃
焙烧摆放浇注摆放
八、清砂手工清砂,铸件内腔残留的砂不允许用钢钎攒,需进行抛丸。
九、切割采用碳弧气刨去除浇口,
十、抛丸表面砂需抛丸,便于初检
十、初检铸件切割后初步检验表面质量,并统计分析,便于对铸件质量的控制(夹铁、壳裂、变形、毛刺、鼓胀、分层、掉砂、夹渣、气孔、缩松、欠铸、冷隔、裂纹等)
十一、热处理根据铸件材质和客户要求进行热处理,并做性能检测
十二、加工冒口加工去除切割后的残留冒口。
十三、抛丸热处理后抛丸便于清除沙粒,发现表面缺陷便于整
十四、精整精整过程注意表面的质量;
十五、检验根据图纸及公差标准检验铸件,根据客户及图纸要求检验表面质量
十六、无损检测根据客户要求进行RT和PT检验(若有缺陷需焊补返修,焊补需根据相应的材质和客户标准进行)
十七、终检
十八、入库
1.制模参数:射蜡压力:保型时间:20-30分钟
蜡模修整:修去表面批缝,要求蜡模光洁平整。(轮毂堵实)
2、检验检验蜡模外观、铸字及变形情况。
3、组焊如图示
4、检验符合工艺、注意不要有滴蜡和焊缝
5、制壳
层数
浆料
用砂
备注
面层
硅溶胶刚玉粉涂料
40-70目刚玉砂
二层-三层
硅溶胶莫来石粉浆料
30-60目莫来石砂
叶轮精密铸造工艺
熔模精铸产品工艺纲要
一、产品信息
产品属性
客户
产品名称
图号
材质
低温蜡
上海凯泉
叶轮
HDK(QY)
ACICD-4MCu
二、工艺流程
制模→检验→组树→检验→制壳→脱蜡→焙烧→熔炼→浇注→清砂→切割→抛丸→初检→热处理→加工冒口→抛丸→精整→检验(尺寸+表面)→无损检测(RT、PT,若有缺陷需焊补)→抛丸→终检→入库