纯铝压铸工艺及压铸模技术要点总结
压铸工艺总结知识点

压铸工艺总结知识点压铸工艺是一种常用的金属加工工艺,通过对金属材料的加热融化后进行注入模具中,经过冷却固化后得到所需的零部件或产品。
它具有生产效率高、生产周期短、产品质量好等优点,被广泛应用于汽车制造、电子制造、机械制造等行业。
以下是对压铸工艺的总结知识点。
一、压铸工艺的基本原理1.压铸工艺的基本原理是利用金属在一定温度下的液态性质,在高压力下将熔融金属填充到模具腔中,并使其冷却凝固形成所需形状的零部件或产品。
2.压铸工艺主要涉及到金属材料的熔化、注入、冷却凝固等过程。
熔化过程通过加热金属到其熔点以上,使其变成液态;注入过程通过压力将熔融金属注入到模具中;冷却凝固过程通过降温,使金属从液态逐渐转变为固态。
二、压铸模具的结构和类型1.压铸模具是压铸工艺中最核心的设备之一,它包括上模和下模两部分。
上模为固定模,下模为动模。
2.压铸模具还包括模具腔、分型面、导向机构等部分。
模具腔是用来形成产品外形的腔体结构;分型面用于分离上模和下模;导向机构用于保证上下模的定位和运动方向。
三、压铸工艺的工艺参数1.压铸工艺中的主要参数包括注射压力、注射速度、保压时间、冷却时间等。
注射压力是指将熔融金属注入到模具腔中所施加的压力;注射速度是指熔融金属注入到模具腔中的速度;保压时间是指保持一定压力对熔融金属进行冷却固化的时间;冷却时间是指产品在模具中冷却至一定温度的时间。
2.合理的工艺参数能够保证产品的质量和生产效率,需要根据具体材料和产品要求进行调整和控制。
四、压铸材料的选择1.压铸工艺主要适用于铝合金、镁合金、锌合金等低熔点金属的加工,也可以用于一些高熔点金属材料的加工。
2.压铸材料的选择需要考虑产品的机械性能、导热性能、耐腐蚀性、成本等因素。
五、压铸工艺的优缺点1.压铸工艺具有生产效率高、生产周期短、产品质量好等优点,能够实现高精度、高复杂度的零部件生产。
2.压铸工艺的缺点是模具制造和维护成本较高,适用于大批量生产的零部件。
铝合金压铸技术要求
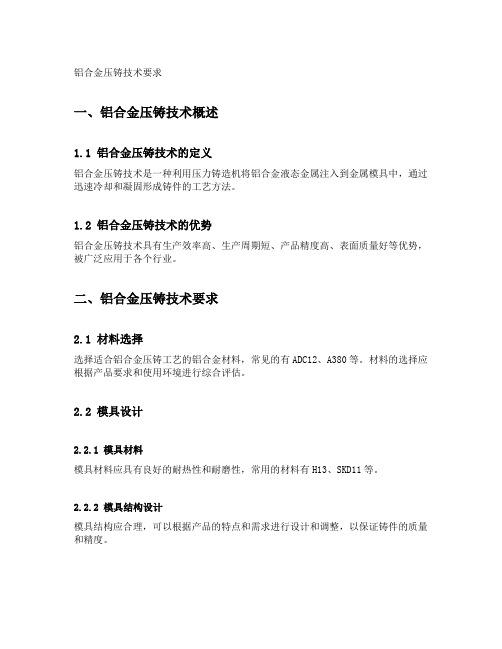
铝合金压铸技术要求一、铝合金压铸技术概述1.1 铝合金压铸技术的定义铝合金压铸技术是一种利用压力铸造机将铝合金液态金属注入到金属模具中,通过迅速冷却和凝固形成铸件的工艺方法。
1.2 铝合金压铸技术的优势铝合金压铸技术具有生产效率高、生产周期短、产品精度高、表面质量好等优势,被广泛应用于各个行业。
二、铝合金压铸技术要求2.1 材料选择选择适合铝合金压铸工艺的铝合金材料,常见的有ADC12、A380等。
材料的选择应根据产品要求和使用环境进行综合评估。
2.2 模具设计2.2.1 模具材料模具材料应具有良好的耐热性和耐磨性,常用的材料有H13、SKD11等。
2.2.2 模具结构设计模具结构应合理,可以根据产品的特点和需求进行设计和调整,以保证铸件的质量和精度。
2.3 注射设备2.3.1 压铸机选择根据产品的要求确定压铸机的型号和规格,包括锁力、注射压力等参数的选择。
2.3.2 注射系统注射系统包括注射缸、注射头、喷嘴等组成,其设计应合理,确保铝合金液态金属的注入和充填。
2.3.3 润滑系统润滑系统的设置对于铝合金压铸技术的稳定运行起着重要作用,应注意润滑剂的选择和使用。
2.4 工艺参数控制压铸工艺参数对于产品的质量和尺寸稳定性有很大的影响,应进行合理的控制和调整。
2.4.1 注射速度注射速度过快会导致铸件内部气孔、缺陷等问题,注射速度过慢会导致铝合金液态金属凝固不完全。
2.4.2 注射温度注射温度过高会导致铝合金液态金属粘度降低,流动性增强,但也会加快模具磨损。
注射温度过低则会导致液态金属凝固时间过长。
2.4.3 注射压力注射压力的控制对于铸件的密实性和表面质量有着重要影响,应根据产品要求进行精确控制。
2.4.4 注射时间注射时间应根据实际需要进行合理设置,以保证铝合金液态金属充填充实模腔。
2.5 热处理工艺铝合金压铸件在铸造成型后,经过热处理工艺可以改善其机械性能和物理性能,如固溶处理、时效处理等。
2.6 铸件表面处理铝合金压铸件的表面处理包括喷砂、喷涂、电镀等方法,以提高产品的外观质量和耐腐蚀性能。
压铸模设计要点及压铸工艺

压铸模设计要点及压铸工艺压铸模设计要点及压铸工艺金属液在通过浇口时,其填充方式可分为层流式填充、喷射流填充、雾化流填充三种方式。
当浇口速度较低时,填充方式显层流的状态;当速度增加,金属液不再是连续流出,而是呈粗颗粒状喷出;当速度更高时,水则会呈雾状的细微颗粒喷出。
采用层流填充或雾状流填充均可产生令人满意的铸件,粗颗粒流填充因在填充过程中热量损失多而填充不好。
一般而言,浇口愈薄,浇口速度愈高才能达到雾化流的状态金属液进入型腔的流动状态是由流道和内浇口的形式决定的。
目前使用较多的流道形式有扇形流道和锥形流道两种。
浇注系统由直浇道,横浇道和内浇道等三部份组成。
扇形流道较适合于内浇口长度较短的产品,锥形流道适合于内浇口长度较长的产品。
不管是扇形流道还是锥形流道,从流道开始到内浇口其截面积应该逐渐缩小,才能保证控制合金液的流态,并防止气体卷入浇注系统;横浇道应具有一定的长度,可对金属液起到稳流和导向作用压铸模设计要点:一、模架1.外表面要求光亮平整,前后模框加2个打出孔,注意要加在没有镶件的位置,防止零件掉出来。
2.为了防止模板变形,起码做2个支撑柱,一个放在分流锥,一个放在分流锥的上面,注意不要与其他零件干涉。
3.模具底板要做通,便于散热。
4.定位圈内孔表面要求内圆磨后氮化,并沿出模方向抛光。
5.定位圈表面的冷却环底部到分流锥表面的长度一般等于料饼厚度。
固定此冷却环的方式有2种:烧焊和加热压入。
6.分流锥一定要做运水来冷却,且离分流锥表面25-30mm.7.模架四个导柱孔要做撬模槽,深度8-10mm。
8.模架一定要调质处理的,最好是锻打的模架。
二、内模,镶件1. 加工后热处理前做去应力处理。
一般铝合金淬火HRC45+/-1°C,锌合金淬火HRC46+/-1-1°C2.内模的配合公差:一般做到小于模框0.05-0.08mm左右,可以用吊环轻松取出放入模框。
顶针配合公差:大于等于8mm的顶针间隙0.05mm,小于等于6mm的顶针间隙0.025mm。
铝压铸技术要求
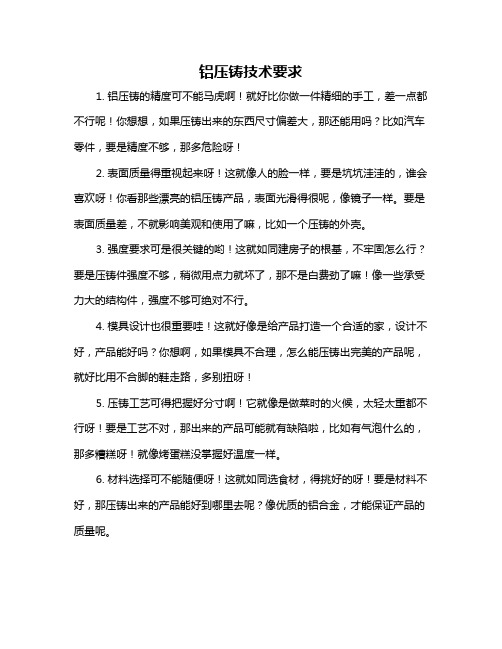
铝压铸技术要求
1. 铝压铸的精度可不能马虎啊!就好比你做一件精细的手工,差一点都不行呢!你想想,如果压铸出来的东西尺寸偏差大,那还能用吗?比如汽车零件,要是精度不够,那多危险呀!
2. 表面质量得重视起来呀!这就像人的脸一样,要是坑坑洼洼的,谁会喜欢呀!你看那些漂亮的铝压铸产品,表面光滑得很呢,像镜子一样。
要是表面质量差,不就影响美观和使用了嘛,比如一个压铸的外壳。
3. 强度要求可是很关键的哟!这就如同建房子的根基,不牢固怎么行?要是压铸件强度不够,稍微用点力就坏了,那不是白费劲了嘛!像一些承受力大的结构件,强度不够可绝对不行。
4. 模具设计也很重要哇!这就好像是给产品打造一个合适的家,设计不好,产品能好吗?你想啊,如果模具不合理,怎么能压铸出完美的产品呢,就好比用不合脚的鞋走路,多别扭呀!
5. 压铸工艺可得把握好分寸啊!它就像是做菜时的火候,太轻太重都不行呀!要是工艺不对,那出来的产品可能就有缺陷啦,比如有气泡什么的,那多糟糕呀!就像烤蛋糕没掌握好温度一样。
6. 材料选择可不能随便呀!这就如同选食材,得挑好的呀!要是材料不好,那压铸出来的产品能好到哪里去呢?像优质的铝合金,才能保证产品的质量呢。
7. 生产效率也很重要呢,你说是不是?这就好像比赛跑步,谁快谁就有优势呀!如果生产效率低,怎么跟别人竞争呀,尤其在量大的时候,不快怎么行呢!就好像打仗,速度可不能慢。
8. 质量检测绝对不能少哇!这就像是给产品做体检,有毛病就得赶紧治呀!不检测怎么知道产品合不合格呢,不管是小瑕疵还是大问题,都得检测出来呀!就像给病人看病一样仔细。
我的观点结论就是:铝压铸技术要求真的很多,每一项都非常重要,都需要我们认真对待,这样才能生产出高质量的铝压铸产品啊!。
铝合金压铸工艺

铝合金压铸工艺简介铝合金压铸是一种常见的金属成形工艺,通常用于制造各种铝合金零件。
其原理是将熔融的铝合金注入到模具中,并在一定的压力下冷却和凝固,最终得到所需的铝合金零件。
本文将介绍铝合金压铸的工艺流程以及相关的工艺参数。
工艺流程铝合金压铸的工艺流程主要包括模具准备、铝合金液态处理、注液和凝固、零件脱模和表面处理等几个主要步骤。
下面将详细介绍每个步骤的内容。
1. 模具准备在铝合金压铸工艺中,模具是非常重要的一部分。
首先需要根据所需零件的形状和尺寸设计制作模具。
模具通常由两部分构成,一部分是固定模,另一部分是活动模。
固定模固定在压铸机上,而活动模则与固定模相连,在注液和凝固过程中参与零件的成形。
模具内部还需要加工一些通道和排气口,以便铝合金的顺利注入和冷却。
在使用模具之前,还需要对其进行表面处理,以确保零件的顺利脱模。
2. 铝合金液态处理铝合金压铸需要使用熔融的铝合金作为原料。
在铝合金的制备过程中,需要控制好温度和成分的配比。
通常采用电炉或燃气炉加热铝合金,直到其达到液态状态。
同时,在熔炼过程中还需要添加一些合适的轻质合金元素,以提高铝合金的流动性和强度。
3. 注液和凝固当铝合金达到液态后,可以开始注入模具中进行成型。
首先将模具合拢,并在一定的压力下将铝合金注入到模具的腔室中。
在注液的过程中,铝合金要通过模具内部的通道和排气口,以确保零件填充完全且没有气泡。
注液的时间和压力应根据零件的大小和形状进行调整。
当铝合金填充完毕后,需要保持一定的压力,直到零件完全凝固。
4. 零件脱模在铝合金凝固后,需要将零件从模具中取出,这个过程称为脱模。
脱模的方法有很多种,可以通过机械力或气动力来推动零件从模具中顺利脱离。
在脱模之前,需要注意保护零件的表面,以免在脱模过程中造成刮擦或其他损坏。
5. 表面处理铝合金压铸零件脱模后,通常还需要进行一些表面处理工艺,以提高零件的外观和性能。
常见的表面处理方法包括机械抛光、电镀、喷涂、阳极氧化等。
完整版)铝合金压铸工艺

完整版)铝合金压铸工艺的分类压铸合金根据其成分和特性的不同,可分为铝合金、镁合金、锌合金、铜合金等几类。
其中,铝合金压铸件应用最广,其次为锌合金压铸件。
铝合金压铸件具有轻质、强度高、耐腐蚀、导热性好等优点,广泛应用于汽车、航空航天、电子、机械等领域。
锌合金压铸件具有良好的流动性、耐磨损、耐腐蚀等特点,主要应用于家电、电子、汽车等领域。
2.2压铸合金的性能要求压铸合金的性能要求主要包括力学性能、物理性能、化学性能和表面质量。
力学性能包括抗拉强度、屈服强度、伸长率等;物理性能包括密度、导热系数等;化学性能包括耐腐蚀性、氧化性等;表面质量包括表面光洁度、气孔、夹杂物等。
2.3压铸合金的选择在选择压铸合金时,需要考虑其应用领域、要求的性能、成本等因素。
铝合金压铸件适用于要求轻质、高强度、耐腐蚀的领域,如汽车、航空航天、电子等。
锌合金压铸件适用于要求良好流动性、耐磨损、耐腐蚀的领域,如家电、电子、汽车等。
镁合金压铸件则适用于要求轻质、高强度、高刚性的领域,如航空航天、汽车等。
2.4压铸合金的加工工艺压铸合金的加工工艺包括模具设计、热处理、涂料配制、浇注压射、保压、开模、抽芯取件、表面质量检查、时效处理、清理整修、铸件浸渗喷丸处理等。
其中,模具设计和制造、热处理工艺、涂料配制对铝合金压铸件的寿命影响较大。
保压、时效处理、铸件浸渗喷丸处理等工艺则可提高压铸件的力学性能和表面质量。
压铸合金是压铸生产的重要元素之一。
要生产优质的压铸件,需要合理的零件构造、设计完善的压铸模和工艺性能优越的压铸机,还需要性能良好的合金。
压铸合金具有较高的强度,因此在选择压铸合金时,应考虑使用性能、工艺性能、使用场合、生产条件和经济性等多种因素。
2.12各类压铸铝合金Al-Si合金是目前应用最为广泛的压铸铝合金。
它具有结晶温度间隔小、合金中硅相有很大的凝固潜热和较大的比热容等特点,因此铸造性能较好,充型能力也较好,热裂、缩松倾向也都比较小。
铝合金压铸原理及工艺

铝合金压铸原理及工艺【铝合金压铸原理及工艺】一、铝合金压铸的历史其实啊,铝合金压铸这门工艺可不是近几年才出现的新玩意儿。
早在 19 世纪初期,压铸技术就已经开始崭露头角了。
那时候,主要用于压铸一些简单的锌合金零件。
随着时间的推移,科技不断进步,到了 20 世纪中叶,铝合金压铸工艺逐渐成熟起来。
比如说,汽车工业的快速发展,就对零部件的生产提出了更高的要求,铝合金压铸凭借其出色的性能,在汽车制造中找到了用武之地。
从发动机部件到车身结构件,铝合金压铸制品的身影无处不在。
二、铝合金压铸的制作过程1. 模具设计与制造1.1 设计的重要性说白了就是,模具就像是一个容器,决定了最终压铸产品的形状和尺寸。
在设计模具时,工程师们得考虑好多因素,像是产品的结构复杂性、尺寸精度要求、脱模的便利性等等。
打个比方,要生产一个铝合金的手机外壳,模具就得设计得非常精细,每个孔位、每个弧度都得恰到好处,这样才能保证生产出来的外壳完美贴合手机内部的零部件,并且外观漂亮。
1.2 制造过程模具制造可是个技术活,一般会用到数控机床、电火花加工等先进设备。
先把一块钢材加工成大致的形状,然后再通过精细的打磨和抛光,让模具的表面变得光滑如镜。
这就好比是雕刻一件艺术品,需要工匠们有耐心、有技术,一点点地把模具雕琢出来。
2. 熔炼铝合金把铝合金原料放入熔炉中进行熔炼,这个过程就像是在煮一锅美味的汤。
要控制好温度、时间和熔炼剂的添加量,才能保证铝合金的成分均匀、纯净。
温度太高或者太低,都会影响铝合金的质量。
就像炒菜时火候掌握不好,菜就不好吃一样。
3. 压铸成型熔炼好的铝合金液被注入到模具中,通过压铸机施加高压,使其迅速填充模具型腔。
这个过程那叫一个快,眨眼之间,一个初步成型的铝合金零件就出来了。
想象一下,就像是用一个巨大的注射器,把液体快速推到一个模具里,填满每一个角落。
4. 脱模与后续处理压铸完成后,模具打开,零件被顶出脱模。
接下来,还需要进行一些后续处理,比如去毛刺、钻孔、攻丝等等,让零件更加完美。
压铸铝技术专题资料
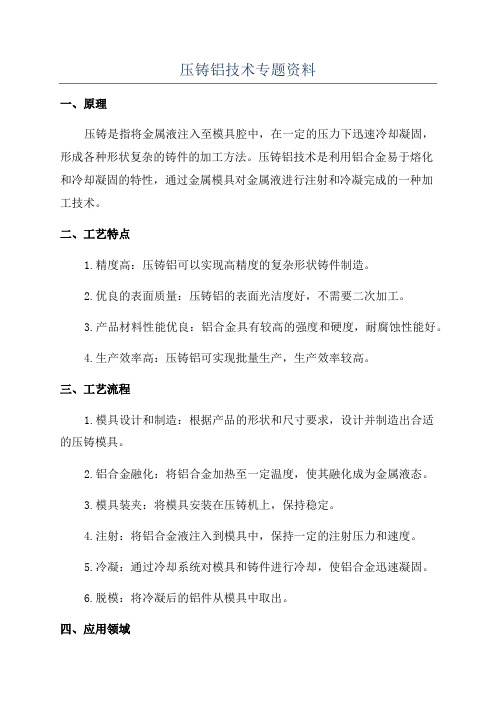
压铸铝技术专题资料一、原理压铸是指将金属液注入至模具腔中,在一定的压力下迅速冷却凝固,形成各种形状复杂的铸件的加工方法。
压铸铝技术是利用铝合金易于熔化和冷却凝固的特性,通过金属模具对金属液进行注射和冷凝完成的一种加工技术。
二、工艺特点1.精度高:压铸铝可以实现高精度的复杂形状铸件制造。
2.优良的表面质量:压铸铝的表面光洁度好,不需要二次加工。
3.产品材料性能优良:铝合金具有较高的强度和硬度,耐腐蚀性能好。
4.生产效率高:压铸铝可实现批量生产,生产效率较高。
三、工艺流程1.模具设计和制造:根据产品的形状和尺寸要求,设计并制造出合适的压铸模具。
2.铝合金融化:将铝合金加热至一定温度,使其融化成为金属液态。
3.模具装夹:将模具安装在压铸机上,保持稳定。
4.注射:将铝合金液注入到模具中,保持一定的注射压力和速度。
5.冷凝:通过冷却系统对模具和铸件进行冷却,使铝合金迅速凝固。
6.脱模:将冷凝后的铝件从模具中取出。
四、应用领域1.汽车工业:压铸铝应用于汽车发动机零部件、转向机构等高负荷零部件。
2.电子通讯:压铸铝常用于制造电子设备外壳、散热器等部件。
3.家电行业:压铸铝常见于制造电视支架、空调外壳等家用电器。
4.航空航天:压铸铝在飞机结构零部件中的应用逐渐增多。
五、压铸铝技术的发展趋势1.材料研发:研发更具性能优越的铝合金材料,提升铝合金的强度和耐腐蚀性能。
2.模具制造技术:发展出更精密、高效的模具制造技术,提高铝件的加工精度。
3.自动化生产:推动压铸铝技术向自动化方向发展,提高生产效率和产品质量。
在工业发展的过程中,压铸铝技术已经成为一种重要的金属加工技术。
通过不断的创新和技术进步,压铸铝将会在更广泛的领域得到应用,为各行业的产品提供更好的质量和性能。
铝合金真空压铸技术

铝合金真空压铸技术铝合金真空压铸技术是一种高效、精密的铝合金铸造工艺,通过在真空环境中进行压铸,可以有效避免铸件表面氧化、气孔等缺陷,提高铸件的质量和性能。
以下是关于铝合金真空压铸技术的详细介绍,包括其工艺流程、优势、应用领域等方面。
一、铝合金真空压铸技术概述铝合金真空压铸技术是一种在真空环境下进行的高压铸造工艺。
其主要步骤包括:模具封闭,抽真空,充填铝液,施加高压,保压定型,冷却固化,开模取件。
整个过程在真空条件下进行,以确保铸件表面无气孔、氧化等缺陷,同时通过高压实现铝液的充分充填,提高铸件的密度和机械性能。
二、铝合金真空压铸技术的工艺流程模具设计和制造:根据产品的形状和尺寸,设计并制造合适的压铸模具,确保模具具有足够的强度和耐磨性。
模具封闭:将设计好的模具封闭,形成一个密封的腔室,以准备进行真空铸造。
真空抽气:在模腔封闭后,通过真空泵将模腔内的空气抽出,创造真空环境。
真空状态有助于减少铝液中气体的溶解,防止气孔的生成。
铝液充填:在真空状态下,将预热至一定温度的铝液注入模腔,确保铝液在模腔中均匀充填。
施加高压:在铝液充填后,施加高压,使铝液充分充填模腔,提高铸件的密度和机械性能。
保压定型:在高压作用下,保持一段时间,使铝液定型成型。
冷却固化:在定型后,通过冷却系统将模腔内的铝液迅速冷却,固化成为铝合金铸件。
开模取件:冷却固化后,打开模具,取出成型的铝合金铸件,进行后续的处理和加工。
三、铝合金真空压铸技术的优势减少氧化和气孔:在真空环境下进行铸造可以有效减少铸件表面的氧化,同时通过真空抽气减少气体的溶解,避免气孔的生成,提高铸件的表面质量。
提高密度和机械性能:高压充填和保压定型能够使铝液充分充填模腔,提高铝合金铸件的密度和机械性能。
精密铸造:铝合金真空压铸技术可以实现更精密的铸造,适用于复杂形状、高精度要求的铝合金零件生产。
高生产效率:由于真空压铸工艺的高压和高速度,可以实现较短的充填时间和较快的冷却速度,提高生产效率。
压铸经验汇总
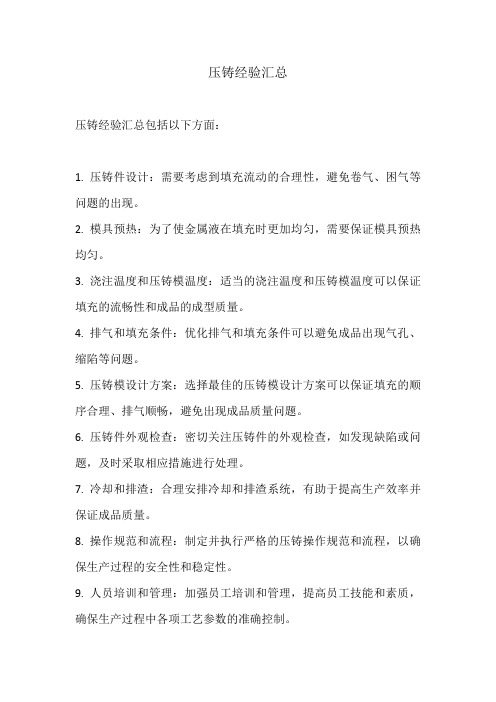
压铸经验汇总
压铸经验汇总包括以下方面:
1. 压铸件设计:需要考虑到填充流动的合理性,避免卷气、困气等问题的出现。
2. 模具预热:为了使金属液在填充时更加均匀,需要保证模具预热均匀。
3. 浇注温度和压铸模温度:适当的浇注温度和压铸模温度可以保证填充的流畅性和成品的成型质量。
4. 排气和填充条件:优化排气和填充条件可以避免成品出现气孔、缩陷等问题。
5. 压铸模设计方案:选择最佳的压铸模设计方案可以保证填充的顺序合理、排气顺畅,避免出现成品质量问题。
6. 压铸件外观检查:密切关注压铸件的外观检查,如发现缺陷或问题,及时采取相应措施进行处理。
7. 冷却和排渣:合理安排冷却和排渣系统,有助于提高生产效率并保证成品质量。
8. 操作规范和流程:制定并执行严格的压铸操作规范和流程,以确保生产过程的安全性和稳定性。
9. 人员培训和管理:加强员工培训和管理,提高员工技能和素质,确保生产过程中各项工艺参数的准确控制。
10. 设备维护和保养:定期对压铸设备进行维护和保养,确保设备运行正常,提高生产效率和成品质量。
11. 工艺改进和创新:鼓励员工进行工艺改进和创新,不断优化生产流程,提高生产效率和降低成本。
12. 质量管理体系建设:建立完善的质量管理体系,确保生产出的压铸件符合相关标准和客户要求。
13. 环境控制:关注环境控制,减少污染和能源浪费,实现绿色生产。
14. 成本管控:合理安排生产计划,优化物料采购和库存管理,降低生产成本。
以上是压铸经验汇总的主要内容,希望能对您有所帮助。
铸造及压铸铝工艺

铸造及压铸铝工艺一、铸造铝工艺铸造铝工艺是通过将铝合金熔化后浇注到铸型中,使其冷却凝固形成所需形状的产品。
铸造铝工艺一般包括以下几个步骤:1.材料准备:选择合适的铝合金作为原材料,通常使用的铝合金有铝硅合金、铝铜合金、铝锌合金等。
2.设计铸型:根据产品的形状和尺寸要求,设计适合的铸型,可以是砂型、金属型、陶瓷型等。
3.熔炼铝合金:将选定的铝合金原料放入炉中,加热熔化。
需要注意的是控制熔化温度和时间,以确保铝合金的质量。
4.浇注铸型:将熔融的铝合金倒入准备好的铸型中,让其充分填充整个型腔。
5.等待凝固:待铝合金在铸型中冷却凝固后,将铸件取出,通常需要清理和修整,以得到最终的成品。
压铸铝工艺是在高压下将铝合金熔融液注入到模具中,通过快速冷却凝固来制造铝合金零件。
压铸铝工艺一般包括以下几个步骤:1.材料准备:与铸造铝工艺相似,选择合适的铝合金作为原材料。
2.设计模具:根据产品的形状和尺寸要求,设计适合的压铸模具。
模具一般由两部分组成,上模和下模。
3.加热熔融:将选定的铝合金原料放入熔炉中进行加热,直至完全熔融成液态。
4.注射液体铝合金:将熔融的铝合金通过注射系统注入到上模中,快速注入并确保充满整个型腔。
5.快速冷却凝固:在注射完成后,将模具放入冷却介质中,使液态铝合金快速凝固,并保持所需形状。
6.模具开启:待铝合金冷却凝固后,打开模具并取出铝合金零件。
7.零件处理:通常还需要进行修整、清洁、修边等工艺,以得到最终的成品。
铸造和压铸铝工艺在应用上有一些不同之处。
压铸铝工艺适用于生产复杂形状的铝合金零件,精度高,表面光洁度好;而铸造铝工艺则适用于生产大型铝合金构件,成本较低,但精度和表面光洁度相对较差。
同时,对于铸造和压铸铝工艺的控制要点包括:熔炼温度控制、注射温度和压力控制、冷却时间控制等等。
合理控制这些参数可以确保产品质量,并提高生产效率。
总而言之,铸造及压铸铝工艺是常见的铝合金加工工艺,适用于不同形状和尺寸的铝合金制品制造。
压铸铝工艺 (3)
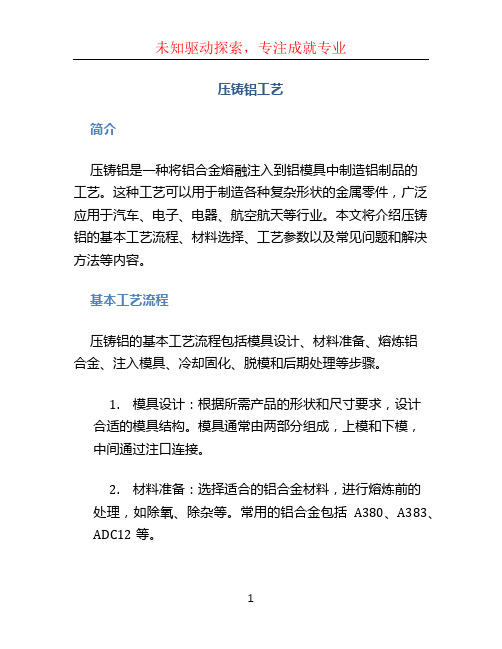
压铸铝工艺简介压铸铝是一种将铝合金熔融注入到铝模具中制造铝制品的工艺。
这种工艺可以用于制造各种复杂形状的金属零件,广泛应用于汽车、电子、电器、航空航天等行业。
本文将介绍压铸铝的基本工艺流程、材料选择、工艺参数以及常见问题和解决方法等内容。
基本工艺流程压铸铝的基本工艺流程包括模具设计、材料准备、熔炼铝合金、注入模具、冷却固化、脱模和后期处理等步骤。
1.模具设计:根据所需产品的形状和尺寸要求,设计合适的模具结构。
模具通常由两部分组成,上模和下模,中间通过注口连接。
2.材料准备:选择适合的铝合金材料,进行熔炼前的处理,如除氧、除杂等。
常用的铝合金包括A380、A383、ADC12等。
3.熔炼铝合金:将铝合金料加热至一定温度,使其熔化,通常使用电炉或气炉进行熔炼。
控制合金的成分和温度是保证产品质量的关键。
4.注入模具:在铝合金熔融状态下,将其注入模具中。
铝液通过注口进入模腔,充满整个腔体,并逐渐冷却固化。
5.冷却固化:注入模具后,铝合金开始冷却,逐渐凝固形成产品的形状。
冷却时间需要根据产品的尺寸和结构进行合理控制。
6.脱模:冷却固化后,打开模具,将产品从模具中取出。
脱模时需要注意避免产生裂纹或变形。
7.后期处理:脱模后的产品可能需要进行修整、打磨、表面处理等工序,以提高其外观和性能。
材料选择压铸铝常用的材料包括A380、A383、ADC12等铝合金。
这些铝合金具有优良的流动性、强度和耐腐蚀性能,适合用于制造各种金属零件。
•A380:铝合金中较常用的一种,具有良好的流动性和机械性能。
适用于制造复杂形状的零件,广泛应用于汽车和电子设备等行业。
•A383:与A380相比,A383的含铜量更高,具有更高的强度和耐热性能。
适用于承受较大压力和温度的零件制造。
•ADC12:具有较高的铝含量和强度,适用于制造要求较高的零件,如汽车发动机壳体、电器外壳等。
选择合适的铝合金材料需要考虑产品的用途、强度要求、耐腐蚀性能等因素。
压铸工艺总结知识点2000字(10篇)
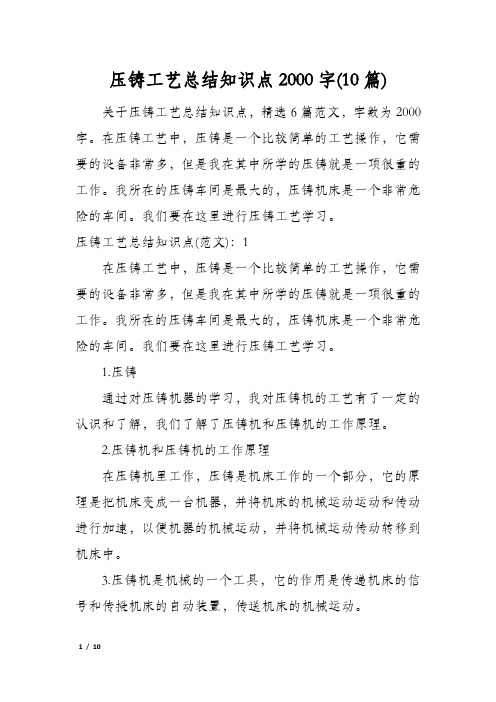
压铸工艺总结知识点2000字(10篇)关于压铸工艺总结知识点,精选6篇范文,字数为2000字。
在压铸工艺中,压铸是一个比较简单的工艺操作,它需要的设备非常多,但是我在其中所学的压铸就是一项很重的工作。
我所在的压铸车间是最大的,压铸机床是一个非常危险的车间。
我们要在这里进行压铸工艺学习。
压铸工艺总结知识点(范文):1在压铸工艺中,压铸是一个比较简单的工艺操作,它需要的设备非常多,但是我在其中所学的压铸就是一项很重的工作。
我所在的压铸车间是最大的,压铸机床是一个非常危险的车间。
我们要在这里进行压铸工艺学习。
1.压铸通过对压铸机器的学习,我对压铸机的工艺有了一定的认识和了解,我们了解了压铸机和压铸机的工作原理。
2.压铸机和压铸机的工作原理在压铸机里工作,压铸是机床工作的一个部分,它的原理是把机床变成一台机器,并将机床的机械运动运动和传动进行加速,以便机器的机械运动,并将机械运动传动转移到机床中。
3.压铸机是机械的一个工具,它的作用是传递机床的信号和传授机床的自动装置,传送机床的机械运动。
我们学习的是压型的机床的特点和作用,我们学习的是压铸机器。
4.电气设备电气设备是一种高压电气设备,它的主要用于机床通过电压、电压、电流、电压等自动装置。
它的电气设备通过电能与机床通电,能够发电。
主要用于电源的自动装置。
电气设备的电气设备可靠地位较高,能够在电气设备的自动装置内。
电气设备是电力设备的一种特种设备,它的功率是电气的电能和电能的电能相结合,电能的电能主要通过电能转换为机床的设备。
5.机床的工作原理机床主要的功率是电能的转速、速度、传动、工件的工作电源,机床是机床和电气设备之间相互作用、相互连接,相互辅助的机床,机床通过机床的自身原理来实现机床的工作功率。
电工主要用于维持机床的工作原理和机器的正常运作。
6.压铸机器在压铸机器中,压铸机的工作原理是机床的电气设备的电气控制系统和电气设备的自动化系统,电气设备的自动控制系统是机床与电气设备之间、电气设备与电气设备之间电气设备和电气设备之间电气设备的电气自动控制系统。
压铸必备知识点总结

压铸必备知识点总结一、压铸的原理及工艺流程1. 压铸的原理压铸是一种通过高压将金属液态材料注入模具中,使其凝固成型的金属制造工艺。
它可以制造复杂形状的零部件,并且具有较高的生产效率和成型精度。
2. 工艺流程(1)原料准备:首先需要将金属材料加热至液态状态。
(2)模具设计:根据零部件的形状和尺寸,设计相应的压铸模具。
(3)注射成型:将液态金属材料通过高压注入模具中,使其凝固成型。
(4)冷却处理:待零部件凝固后,进行冷却处理,确保其尺寸稳定。
(5)去除模具:将成型的零部件从模具中取出,进行去毛刺和表面处理。
二、压铸的材料及设备1. 压铸材料常见的压铸材料包括铝合金、锌合金、镁合金、铜合金等。
不同的材料有着不同的物理性能和适用范围,需要根据具体的使用要求进行选择。
2. 压铸设备(1)压铸机:是进行压铸的主要设备,通常由注射系统、射压系统、液压系统等组成。
(2)模具:根据产品的形状和尺寸,设计相应的压铸模具。
(3)辅助设备:包括加热炉、冷却设备、去毛刺机等,用于辅助完成压铸工艺的各个环节。
三、压铸工艺的注意事项1. 温度控制在压铸过程中,材料的温度控制非常重要。
过低的温度会影响材料的流动性,导致产品表面不光滑;而过高的温度则会引起材料氧化、蒸发,损害产品质量。
2. 压力控制压铸过程中施加的压力能够决定产品的密实度和形状精度。
因此,需要根据产品的具体要求,合理控制压铸的压力大小。
3. 模具设计合理的模具设计能够有效提高产品的成型质量。
需要考虑产品的结构特点、浇口设计、冷却系统等因素,以提高产品的整体性能。
4. 表面处理压铸后的产品通常需要进行去毛刺、抛光等表面处理工艺,以提高产品的表面质量和外观。
四、压铸的应用领域压铸工艺被广泛应用于汽车、机械、电子、航空航天等领域。
常见的应用包括汽车零部件、电子设备外壳、家用电器等。
五、压铸的发展趋势随着科技的不断进步,压铸工艺也在不断发展。
未来,压铸工艺将更加注重产品的高精度、高复杂度,推动压铸工艺向着智能化、自动化方向发展。
压铸工艺及操作规程(3篇)

第1篇一、压铸工艺概述压铸是一种将金属熔体在高压下注入到铸模中,冷却凝固后得到所需的铸件的金属成型方法。
压铸工艺具有生产效率高、尺寸精度好、表面光洁度高等优点,广泛应用于汽车、家电、电子等行业。
二、压铸工艺流程1. 铝合金熔炼:将铝锭或铝合金锭放入熔炼炉中,通过加热熔化成铝液。
2. 模具准备:根据产品图纸制作或选用合适的模具,并对模具进行预热。
3. 铝液准备:将熔化的铝液过滤、除气、去除杂质,使其达到压铸要求。
4. 压射成型:将铝液注入到预热的模具中,在高压下使铝液充满模具型腔。
5. 冷却凝固:铝液在模具中冷却凝固,形成铸件。
6. 取件:将铸件从模具中取出。
7. 清理:对铸件进行去毛刺、抛光等表面处理。
8. 检验:对铸件进行尺寸、表面质量、机械性能等检验。
三、压铸操作规程1. 安全操作:操作者必须穿戴好劳保用品,如工作服、手套、眼镜等,确保人身安全。
2. 设备检查:开机前,检查设备是否正常运行,如油压、冷却系统、控制系统等。
3. 模具准备:根据产品图纸制作或选用合适的模具,并对模具进行预热。
4. 铝液准备:将熔化的铝液过滤、除气、去除杂质,使其达到压铸要求。
5. 压射成型:将铝液注入到预热的模具中,在高压下使铝液充满模具型腔。
6. 冷却凝固:铝液在模具中冷却凝固,形成铸件。
7. 取件:将铸件从模具中取出。
8. 清理:对铸件进行去毛刺、抛光等表面处理。
9. 检验:对铸件进行尺寸、表面质量、机械性能等检验。
10. 设备维护:定期对设备进行保养、检修,确保设备正常运行。
四、注意事项1. 铝液温度:铝液温度应控制在合适的范围内,过高或过低都会影响铸件质量。
2. 压射压力:压射压力应根据产品材质、厚度等因素进行调整,确保铸件成型质量。
3. 模具预热:模具预热温度应控制在合适的范围内,过高或过低都会影响铸件质量。
4. 铝液过滤:铝液过滤可有效去除杂质,提高铸件质量。
5. 模具维护:定期对模具进行检查、清洗、维护,确保模具使用寿命。
铝合金压铸

铝合金压铸1. 引言铝合金压铸是一种广泛应用于制造业的铝合金加工方法。
铝合金以其低密度、高强度和良好的耐腐蚀性能,在汽车、电子、航空航天等领域中得到了广泛的应用。
压铸技术可以高效地生产出复杂形状的铝合金零件,因此在铝合金加工中占据重要地位。
本文将介绍铝合金压铸的工艺流程、优势和应用领域,并讨论一些常见问题。
2. 工艺流程铝合金压铸的工艺流程主要包括模具设计、合金熔炼、注射成形、冷却和处理。
2.1 模具设计模具设计是铝合金压铸的第一步。
模具需要根据所需零件的形状和尺寸进行设计,包括模具的结构、内腔和冷却系统。
模具设计要考虑到零件的收缩率和变形,以确保最终产品的质量。
2.2 合金熔炼铝合金压铸所使用的合金通常是从铝锭中熔化得到的。
合金的成分可以根据具体应用需求进行调整。
在熔化过程中,需要控制合金的温度、气氛和熔化时间,以确保合金的纯度和一致性。
2.3 注射成形熔化的铝合金被注入到预先设计好的模具中。
注射时需要控制注射速度和压力,以防止产生气体孔洞或缺陷。
注射成形后,需要等待一段时间,让注入的铝合金在模具中冷却和凝固。
2.4 冷却和处理冷却过程包括模具内外的冷却系,以确保铝合金零件能够迅速冷却并保持其形状稳定。
在冷却后,铝合金零件需要进行一些处理,如去除模具的挂钩和余震,修整边缘和表面处理等。
3. 优势铝合金压铸相比其他加工方法具有以下优势:3.1 快速生产铝合金压铸能够实现高效快速的生产。
模具的设计和制造时间相对较短,而且铝合金的注射成形过程也比较迅速。
这意味着铝合金压铸可以满足紧急需求或大批量生产的要求。
3.2 复杂零件制造铝合金压铸可以生产出形状复杂的零件,包括薄壁结构、凹凸面和细节部分等。
这使得铝合金压铸在汽车、电子和航空航天等领域中得到广泛应用。
3.3 成本效益相比其他铝合金加工方法,铝合金压铸具有较低的成本。
模具的制造成本相对较低,并且可以在多次使用中平摊成本。
此外,铝合金的重量轻,材料成本较低。
压铸实践知识点总结大全
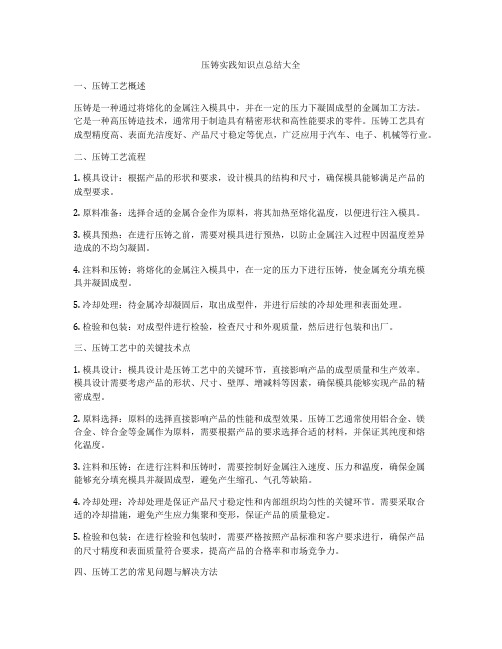
压铸实践知识点总结大全一、压铸工艺概述压铸是一种通过将熔化的金属注入模具中,并在一定的压力下凝固成型的金属加工方法。
它是一种高压铸造技术,通常用于制造具有精密形状和高性能要求的零件。
压铸工艺具有成型精度高、表面光洁度好、产品尺寸稳定等优点,广泛应用于汽车、电子、机械等行业。
二、压铸工艺流程1. 模具设计:根据产品的形状和要求,设计模具的结构和尺寸,确保模具能够满足产品的成型要求。
2. 原料准备:选择合适的金属合金作为原料,将其加热至熔化温度,以便进行注入模具。
3. 模具预热:在进行压铸之前,需要对模具进行预热,以防止金属注入过程中因温度差异造成的不均匀凝固。
4. 注料和压铸:将熔化的金属注入模具中,在一定的压力下进行压铸,使金属充分填充模具并凝固成型。
5. 冷却处理:待金属冷却凝固后,取出成型件,并进行后续的冷却处理和表面处理。
6. 检验和包装:对成型件进行检验,检查尺寸和外观质量,然后进行包装和出厂。
三、压铸工艺中的关键技术点1. 模具设计:模具设计是压铸工艺中的关键环节,直接影响产品的成型质量和生产效率。
模具设计需要考虑产品的形状、尺寸、壁厚、增减料等因素,确保模具能够实现产品的精密成型。
2. 原料选择:原料的选择直接影响产品的性能和成型效果。
压铸工艺通常使用铝合金、镁合金、锌合金等金属作为原料,需要根据产品的要求选择合适的材料,并保证其纯度和熔化温度。
3. 注料和压铸:在进行注料和压铸时,需要控制好金属注入速度、压力和温度,确保金属能够充分填充模具并凝固成型,避免产生缩孔、气孔等缺陷。
4. 冷却处理:冷却处理是保证产品尺寸稳定性和内部组织均匀性的关键环节。
需要采取合适的冷却措施,避免产生应力集聚和变形,保证产品的质量稳定。
5. 检验和包装:在进行检验和包装时,需要严格按照产品标准和客户要求进行,确保产品的尺寸精度和表面质量符合要求,提高产品的合格率和市场竞争力。
四、压铸工艺的常见问题与解决方法1. 表面质量不良:该问题可能是由于模具表面损坏或磨损引起的,解决方法是修复或更换损坏的模具部件,保证模具表面的光洁度和平整度。
纯铝压铸工艺及压铸模技术要点总结

纯铝压铸技术的要点总结目录:一、流道设计二、浇口厚度设计三、渣包设计四、顶针孔间隙设计五、钢材及热处理六、铝液温度七、根据压铸件氧化的颜色需求选择合适的铝含量成份八、铸件坯料氧化条件【关于纯铝压铸模设计的一些知识】流道设计:1.可以用圆形流道,(比较难加工,成本高些),或者用梯形流道,梯形流道避免宽而薄,以防热量损失,最好配备模温机生产,模温300度;2.产品较大时,流道大小设计和普通铝无差异,产品比较小时,流道就增大20~50 % ;浇口厚度设计:纯铝压铸的浇口设计一般比普通压铸开的厚些,最起码1.2MM厚起步,有条件尽量开厚些;开太薄容易堵塞;渣包设计:1.建议渣包比平时的做大一些,多排些冷料,避免氧化异色;2.普通铝合金铸件排渣比为铸件25~30% ;纯铝可以做到100% ,小产品会更大;3.渣包开排气槽,1.5~0.25MM递减式设计;顶针孔间隙设计:间隙比普通铝压铸模放大1.5~2.0倍,放心不会跑料;钢材及热处理:可选用国产8418 ,热处理:48~50HRC 比较合理;模芯大的更低些,镶针镶件硬度可以高些,易断的部件降低点热处理硬度;铝液温度:保持铝液的稳定性,一般生产在700~730度,也可以高于730度,最高不高于750度,最低不低于700就好;根据压铸件氧化的颜色需求选择合适的铝含量成份:1.氧化黑色,建议用铝含量低的铝锭,可以用ADC10;2.氧化灰色,比如铁灰色,建议铝含量在95~97%的铝锭;3.氧化粉红色等绚丽色,建议用铝含量97.5%以上的铝锭,这种是压铸最难的,对模具设计,压铸工艺,设备有一定的要求;4.Si含量大于0.5%,氧化绚丽色做不好;5.Mg含量大于3%,对氧化绚丽色不受影响;6.Mn 含量大于2.2% ,氧化银色不纯;铸件坯料氧化条件:1.铸件氧化前不做喷砂,抛丸,研磨处理;毛坯质量很高,表面无水纹,可以直接氧化处理效果最好,因为铸件表面最致密;2. 但铸件表面有水纹的情况下,氧化是遮盖不住的;。
- 1、下载文档前请自行甄别文档内容的完整性,平台不提供额外的编辑、内容补充、找答案等附加服务。
- 2、"仅部分预览"的文档,不可在线预览部分如存在完整性等问题,可反馈申请退款(可完整预览的文档不适用该条件!)。
- 3、如文档侵犯您的权益,请联系客服反馈,我们会尽快为您处理(人工客服工作时间:9:00-18:30)。
纯铝压铸技术的要点总结目录:
一、流道设计
二、浇口厚度设计
三、渣包设计
四、顶针孔间隙设计
五、钢材及热处理
六、铝液温度
七、根据压铸件氧化的颜色需求选择合适的铝含量成份
八、铸件坯料氧化条件
【关于纯铝压铸模设计的一些知识】
流道设计:
1.可以用圆形流道,(比较难加工,成本高些),或者用梯形流道,梯形流道避免宽而薄,以防热量损失,最好配备模温机生产,模温300度;
2.产品较大时,流道大小设计和普通铝无差异,产品比较小时,流道就增大20~50 % ;
浇口厚度设计:
纯铝压铸的浇口设计一般比普通压铸开的厚些,最起码1.2MM厚起步,有条件尽量开厚些;开太薄容易堵塞;
渣包设计:
1.建议渣包比平时的做大一些,多排些冷料,避免氧化异色;
2.普通铝合金铸件排渣比为铸件25~30% ;纯铝可以做到100% ,小产品会更大;
3.渣包开排气槽,1.5~0.25MM递减式设计;
顶针孔间隙设计:
间隙比普通铝压铸模放大1.5~2.0倍,放心不会跑料;
钢材及热处理:
可选用国产8418 ,热处理:48~50HRC 比较合理;模芯大的更低些,镶针镶件硬度可以高些,易断的部件降低点热处理硬度;
铝液温度:
保持铝液的稳定性,一般生产在700~730度,也可以高于730度,最高不高于750度,最低不低于700就好;
根据压铸件氧化的颜色需求选择合适的铝含量成份:
1.氧化黑色,建议用铝含量低的铝锭,可以用ADC10;
2.氧化灰色,比如铁灰色,建议铝含量在95~97%的铝锭;
3.氧化粉红色等绚丽色,建议用铝含量97.5%以上的铝锭,这种是压铸最难的,对模具设计,压铸工艺,设备有一定的要求;
4.Si含量大于0.5%,氧化绚丽色做不好;
5.Mg含量大于3%,对氧化绚丽色不受影响;
6.Mn 含量大于2.2% ,氧化银色不纯;
铸件坯料氧化条件:
1.铸件氧化前不做喷砂,抛丸,研磨处理;毛坯质量很高,表面无水纹,可以直接氧化处理效果最好,因为铸件表面最致密;
2. 但铸件表面有水纹的情况下,氧化是遮盖不住的;。