四合一磷化液操作工艺
四合一磷化液指标

四合一磷化液指标磷化液是一种常用的表面处理剂,广泛应用于金属材料的防锈和增加粘附力等方面。
而四合一磷化液是一种新型的磷化液,具有更高的效果和更广泛的适用性。
本文将介绍四合一磷化液的主要指标,以帮助读者更好地了解和使用该产品。
首先,四合一磷化液的主要指标之一是膜层的厚度。
膜层的厚度直接影响其防锈和粘附力的效果。
一般来说,膜层越厚,其防锈效果就越好。
因此,在选择四合一磷化液时,需要关注其膜层厚度的指标,并根据具体应用需求进行选择。
其次,四合一磷化液的耐蚀性也是一个重要的指标。
耐蚀性是指膜层在受到腐蚀介质作用时的稳定性。
优秀的四合一磷化液应具有良好的耐蚀性,能够在恶劣的环境中保持膜层的完整性,从而保护金属材料不受腐蚀。
第三个指标是四合一磷化液的加工性能。
加工性能主要包括磷化速度和磷化液的稳定性。
磷化速度越快,生产效率就越高。
而稳定的磷化液能够长时间保持其性能,减少更换磷化液的频率。
因此,在选择四合一磷化液时,需要关注其加工性能指标,并结合实际需求进行选择。
最后,四合一磷化液的环保性也是一个重要的指标。
环保性是指磷化液在使用过程中对环境的影响程度。
优秀的四合一磷化液应该尽量减少对水质和大气的污染,并且能够符合相关的环保法规要求。
因此,在选择四合一磷化液时,需要关注其环保性指标,并选择符合环保要求的产品。
综上所述,四合一磷化液的指标对于选择和使用该产品非常重要。
在选择时,需要关注膜层厚度、耐蚀性、加工性能和环保性等指标,并结合实际需求进行选择。
通过合理选择四合一磷化液,可以更好地提高金属材料的防锈性能和粘附力,从而延长其使用寿命。
磷化工艺流程及技术要求
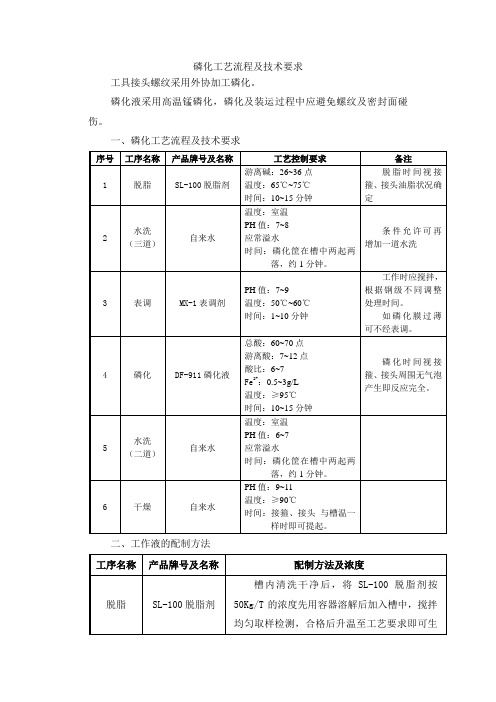
磷化工艺流程及技术要求工具接头螺纹采用外协加工磷化。
磷化液采用高温锰磷化,磷化及装运过程中应避免螺纹及密封面碰伤。
一、磷化工艺流程及技术要求序号工序名称产品牌号及名称工艺控制要求备注1 脱脂SL-100脱脂剂游离碱:26~36点温度:65℃~75℃时间:10~15分钟脱脂时间视接箍、接头油脂状况确定2水洗(三道)自来水温度:室温PH值:7~8应常溢水时间:磷化筐在槽中两起两落,约1分钟。
条件允许可再增加一道水洗3 表调MX-1表调剂PH值:7~9温度:50℃~60℃时间:1~10分钟工作时应搅拌,根据钢级不同调整处理时间。
如磷化膜过薄可不经表调。
4 磷化DF-911磷化液总酸:60~70点游离酸:7~12点酸比:6~7Fe2+:0.5~3g/L温度:≥95℃时间:10~15分钟磷化时间视接箍、接头周围无气泡产生即反应完全。
5水洗(二道)自来水温度:室温PH值:6~7应常溢水时间:磷化筐在槽中两起两落,约1分钟。
6 干燥自来水PH值:9~11温度:≥90℃时间:接箍、接头与槽温一样时即可提起。
二、工作液的配制方法工序名称产品牌号及名称配制方法及浓度脱脂SL-100脱脂剂槽内清洗干净后,将SL-100脱脂剂按50Kg/T的浓度先用容器溶解后加入槽中,搅拌均匀取样检测,合格后升温至工艺要求即可生产。
表调MX-1表调剂槽内清洗干净后,将MX-1表调剂按3Kg/T 的浓度加入槽中开启搅拌,升温至工艺要求即可生产。
磷化DF-911磷化液槽内清洗干净后,将DF-911磷化液剂按200Kg/T的浓度配制,搅拌均匀,取样检测合格后,升温至工艺要求后将还原铁粉按500Kg/T 均匀加入槽中,待没有气泡产生静止10分钟即可生产。
注:必要时在脱脂处理后,增加酸洗工序,酸洗时严格控制酸洗时间,通常不应超过1分钟。
磷化的过程与工艺
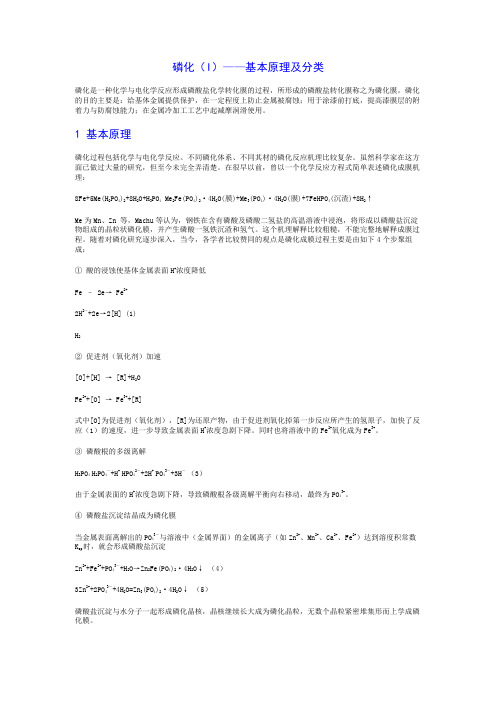
磷化(I)——基本原理及分类磷化是一种化学与电化学反应形成磷酸盐化学转化膜的过程,所形成的磷酸盐转化膜称之为磷化膜。
磷化的目的主要是:给基体金属提供保护,在一定程度上防止金属被腐蚀;用于涂漆前打底,提高漆膜层的附着力与防腐蚀能力;在金属冷加工工艺中起减摩润滑使用。
1 基本原理磷化过程包括化学与电化学反应。
不同磷化体系、不同其材的磷化反应机理比较复杂。
虽然科学家在这方面已做过大量的研究,但至今未完全弄清楚。
在很早以前,曾以一个化学反应方程式简单表述磷化成膜机理:8Fe+5Me(H2PO4)2+8H2O+H3PO4 Me2Fe(PO4)2·4H2O(膜)+Me3(PO4)·4H2O(膜)+7FeHPO4(沉渣)+8H2↑Me为Mn、Zn 等,Machu等认为,钢铁在含有磷酸及磷酸二氢盐的高温溶液中浸泡,将形成以磷酸盐沉淀物组成的晶粒状磷化膜,并产生磷酸一氢铁沉渣和氢气。
这个机理解释比较粗糙,不能完整地解释成膜过程。
随着对磷化研究逐步深入,当今,各学者比较赞同的观点是磷化成膜过程主要是由如下4个步聚组成:①酸的浸蚀使基体金属表面H+浓度降低Fe – 2e→ Fe2+2H2-+2e→2[H] (1)H2②促进剂(氧化剂)加速[O]+[H] → [R]+H2OFe2++[O] → Fe3++[R]式中[O]为促进剂(氧化剂),[R]为还原产物,由于促进剂氧化掉第一步反应所产生的氢原子,加快了反应(1)的速度,进一步导致金属表面H+浓度急剧下降。
同时也将溶液中的Fe2+氧化成为Fe3+。
③磷酸根的多级离解H3PO4 H2PO4-+H+ HPO42-+2H+ PO43-+3H-(3)由于金属表面的H+浓度急剧下降,导致磷酸根各级离解平衡向右移动,最终为PO43-。
④磷酸盐沉淀结晶成为磷化膜当金属表面离解出的PO43-与溶液中(金属界面)的金属离子(如Zn2+、Mn2+、Ca2+、Fe2+)达到溶度积常数K sp时,就会形成磷酸盐沉淀Zn2++Fe2++PO43-+H2O→Zn2Fe(PO4)2·4H2O↓(4)3Zn2++2PO43-+4H2O=Zn3(PO4)2·4H2O↓(5)磷酸盐沉淀与水分子一起形成磷化晶核,晶核继续长大成为磷化晶粒,无数个晶粒紧密堆集形而上学成磷化膜。
磷化前的预处理和两种常用磷化工艺
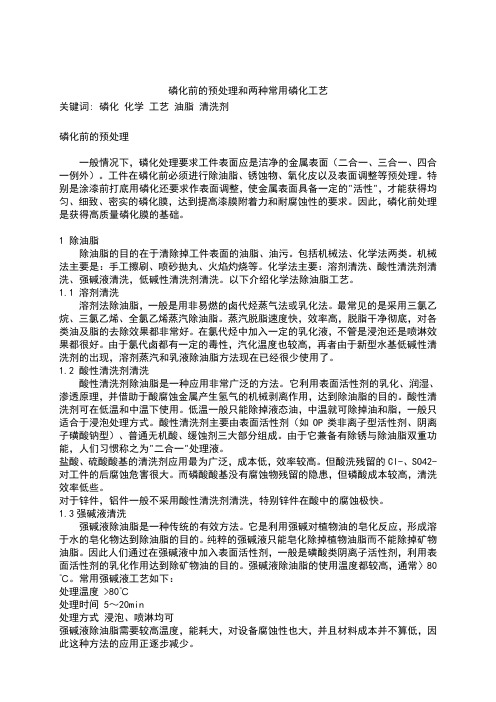
磷化前的预处理和两种常用磷化工艺关键词: 磷化化学工艺油脂清洗剂磷化前的预处理一般情况下,磷化处理要求工件表面应是洁净的金属表面(二合一、三合一、四合一例外)。
工件在磷化前必须进行除油脂、锈蚀物、氧化皮以及表面调整等预处理。
特别是涂漆前打底用磷化还要求作表面调整,使金属表面具备一定的"活性",才能获得均匀、细致、密实的磷化膜,达到提高漆膜附着力和耐腐蚀性的要求。
因此,磷化前处理是获得高质量磷化膜的基础。
1 除油脂除油脂的目的在于清除掉工件表面的油脂、油污。
包括机械法、化学法两类。
机械法主要是:手工擦刷、喷砂抛丸、火焰灼烧等。
化学法主要:溶剂清洗、酸性清洗剂清洗、强碱液清洗,低碱性清洗剂清洗。
以下介绍化学法除油脂工艺。
1.1 溶剂清洗溶剂法除油脂,一般是用非易燃的卤代烃蒸气法或乳化法。
最常见的是采用三氯乙烷、三氯乙烯、全氯乙烯蒸汽除油脂。
蒸汽脱脂速度快,效率高,脱脂干净彻底,对各类油及脂的去除效果都非常好。
在氯代烃中加入一定的乳化液,不管是浸泡还是喷淋效果都很好。
由于氯代卤都有一定的毒性,汽化温度也较高,再者由于新型水基低碱性清洗剂的出现,溶剂蒸汽和乳液除油脂方法现在已经很少使用了。
1.2 酸性清洗剂清洗酸性清洗剂除油脂是一种应用非常广泛的方法。
它利用表面活性剂的乳化、润湿、渗透原理,并借助于酸腐蚀金属产生氢气的机械剥离作用,达到除油脂的目的。
酸性清洗剂可在低温和中温下使用。
低温一般只能除掉液态油,中温就可除掉油和脂,一般只适合于浸泡处理方式。
酸性清洗剂主要由表面活性剂(如OP类非离子型活性剂、阴离子磺酸钠型)、普通无机酸、缓蚀剂三大部分组成。
由于它兼备有除锈与除油脂双重功能,人们习惯称之为"二合一"处理液。
盐酸、硫酸酸基的清洗剂应用最为广泛,成本低,效率较高。
但酸洗残留的Cl-、SO42-对工件的后腐蚀危害很大。
而磷酸酸基没有腐蚀物残留的隐患,但磷酸成本较高,清洗效率低些。
磷化液配制方法
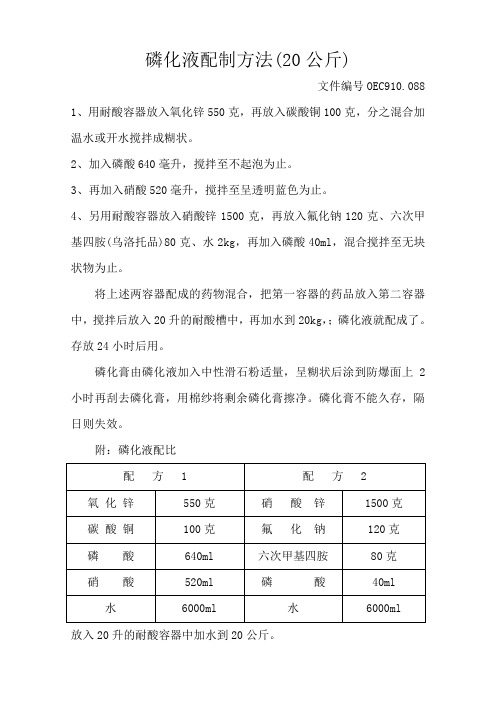
磷化液配制方法(20公斤)文件编号OEC910.088 1、用耐酸容器放入氧化锌550克,再放入碳酸铜100克,分之混合加温水或开水搅拌成糊状。
2、加入磷酸640毫升,搅拌至不起泡为止。
3、再加入硝酸520毫升,搅拌至呈透明蓝色为止。
4、另用耐酸容器放入硝酸锌1500克,再放入氟化钠120克、六次甲基四胺(乌洛托品)80克、水2kg,再加入磷酸40ml,混合搅拌至无块状物为止。
将上述两容器配成的药物混合,把第一容器的药品放入第二容器中,搅拌后放入20升的耐酸槽中,再加水到20kg,;磷化液就配成了。
存放24小时后用。
磷化膏由磷化液加入中性滑石粉适量,呈糊状后涂到防爆面上2小时再刮去磷化膏,用棉纱将剩余磷化膏擦净。
磷化膏不能久存,隔日则失效。
附:磷化液配比放入20升的耐酸容器中加水到20公斤。
磷化操作工艺说明1、用醇酸稀料或酒精清洗隔爆面上的油脂、污物。
2、用细纱布把隔爆面去锈,再用干净的棉纱擦干净,不得用化学的方法使隔爆面漏出金属光泽。
3、按冷磷化处理工艺守则文件编号OEC910.088配置的磷化液与滑石粉搅拌均匀,成为磷化涂膏。
4、涂膏前,隔爆面必须干燥,光泽干净。
5、将磷化膏均匀的涂在隔爆面上,厚度为2-4毫米,不得漏出金属表面,室温在30℃左右时,磷化时间为半小时,室温在20℃左右时,时间为5-10小时,室温在0度左右时,时间为20小时,涂膏时速度要快。
6、磷化膏不能长时间存放,超过24小时后,则失效。
7、金属表面涂膏后,用非金属刮刀除去涂膏,再用水冲洗干净,使金属表面出现一层棕色而均匀的磷化膜。
8、为了提高抗腐能力,可再涂上一层微薄的防锈油,如:石油碳酸钡,凡士林等油脂,若采用机油与石油碳酸钡各50%的混合液防锈效果更好。
常温磷化液
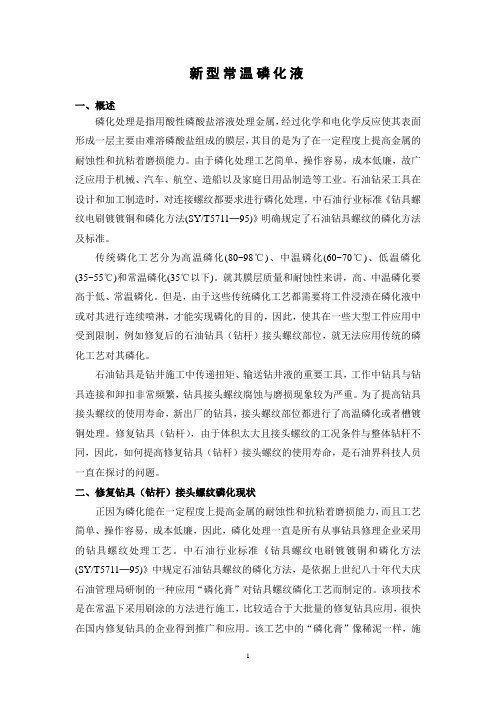
新型常温磷化液一、概述磷化处理是指用酸性磷酸盐溶液处理金属,经过化学和电化学反应使其表面形成一层主要由难溶磷酸盐组成的膜层,其目的是为了在一定程度上提高金属的耐蚀性和抗粘着磨损能力。
由于磷化处理工艺简单,操作容易,成本低廉,故广泛应用于机械、汽车、航空、造船以及家庭日用品制造等工业。
石油钻采工具在设计和加工制造时,对连接螺纹都要求进行磷化处理,中石油行业标准《钻具螺纹电刷镀镀铜和磷化方法(SY/T5711─95)》明确规定了石油钻具螺纹的磷化方法及标准。
传统磷化工艺分为高温磷化(80~98℃)、中温磷化(60~70℃)、低温磷化(35~55℃)和常温磷化(35℃以下)。
就其膜层质量和耐蚀性来讲,高、中温磷化要高于低、常温磷化。
但是,由于这些传统磷化工艺都需要将工件浸渍在磷化液中或对其进行连续喷淋,才能实现磷化的目的,因此,使其在一些大型工件应用中受到限制,例如修复后的石油钻具(钻杆)接头螺纹部位,就无法应用传统的磷化工艺对其磷化。
石油钻具是钻井施工中传递扭矩、输送钻井液的重要工具,工作中钻具与钻具连接和卸扣非常频繁,钻具接头螺纹腐蚀与磨损现象较为严重。
为了提高钻具接头螺纹的使用寿命,新出厂的钻具,接头螺纹部位都进行了高温磷化或者槽镀铜处理。
修复钻具(钻杆),由于体积太大且接头螺纹的工况条件与整体钻杆不同,因此,如何提高修复钻具(钻杆)接头螺纹的使用寿命,是石油界科技人员一直在探讨的问题。
二、修复钻具(钻杆)接头螺纹磷化现状正因为磷化能在一定程度上提高金属的耐蚀性和抗粘着磨损能力,而且工艺简单、操作容易,成本低廉,因此,磷化处理一直是所有从事钻具修理企业采用的钻具螺纹处理工艺。
中石油行业标准《钻具螺纹电刷镀镀铜和磷化方法(SY/T5711─95)》中规定石油钻具螺纹的磷化方法,是依据上世纪八十年代大庆石油管理局研制的一种应用“磷化膏”对钻具螺纹磷化工艺而制定的。
该项技术是在常温下采用刷涂的方法进行施工,比较适合于大批量的修复钻具应用,很快在国内修复钻具的企业得到推广和应用。
“四合一”金属磷化处理液
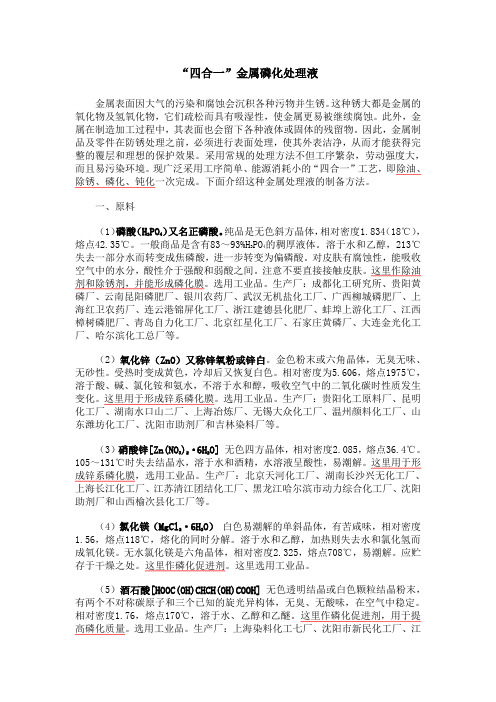
水 1000
2.操作步骤
把氧化锌用适量水调成糊状,在不断搅拌条件下,缓慢加入磷酸。
待磷酸将氧化锌充分溶解后,顺序加硝酸锌、酒石酸和氯化镁,再用水稀释至总体积的2/3,搅拌,溶解。
把重铬酸钾和钼酸铵分别溶解,加入上述药液中,搅拌、混合均匀,继之加入十二烷基苯磺酸钠并加水至足量,充分搅拌,混合均匀即可。
三、产品质量指标
外观透明溶液
PH值 1~2
相对密度 1.05~1.10
凝固点(℃)﹤-15
游离酸(以H
3PO
4
计,g/L)﹥ 100
四、产品使用方法与效果
将金属浸入70℃的处理液中5~15分钟,可使除油、除锈、钝化、磷化一次完成。
对于带有轻锈、轻油污的工件,可以简化工序,效果极好;对于重锈、重油脂及氧化皮也有较好的去除效果。
处理15分钟后,工件在磷化液中形成的磷化膜约为0.5g/m2左右。
磷化设备操作规程
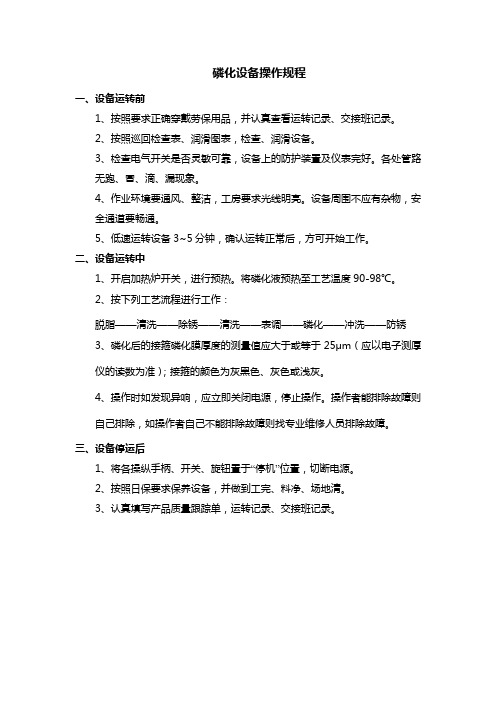
磷化设备操作规程
一、设备运转前
1、按照要求正确穿戴劳保用品,并认真查看运转记录、交接班记录。
2、按照巡回检查表、润滑图表,检查、润滑设备。
3、检查电气开关是否灵敏可靠,设备上的防护装置及仪表完好。
各处管路
无跑、冒、滴、漏现象。
4、作业环境要通风、整洁,工房要求光线明亮。
设备周围不应有杂物,安
全通道要畅通。
5、低速运转设备3~5分钟,确认运转正常后,方可开始工作。
二、设备运转中
1、开启加热炉开关,进行预热。
将磷化液预热至工艺温度90-98℃。
2、按下列工艺流程进行工作:
脱脂——清洗——除锈——清洗——表调——磷化——冲洗——防锈
3、磷化后的接箍磷化膜厚度的测量值应大于或等于25μm(应以电子测厚
仪的读数为准);接箍的颜色为灰黑色、灰色或浅灰。
4、操作时如发现异响,应立即关闭电源,停止操作。
操作者能排除故障则
自己排除,如操作者自己不能排除故障则找专业维修人员排除故障。
三、设备停运后
1、将各操纵手柄、开关、旋钮置于“停机”位置,切断电源。
2、按照日保要求保养设备,并做到工完、料净、场地清。
3、认真填写产品质量跟踪单,运转记录、交接班记录。
磷化处理工艺程序及操作方法
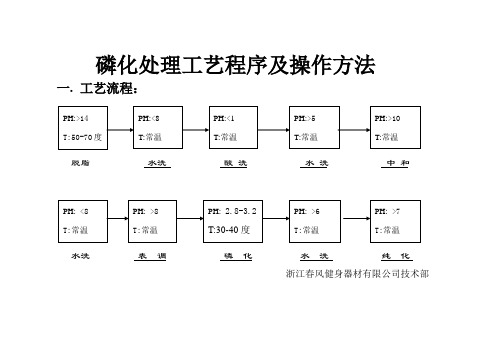
<工件不上膜>
A.槽液酸度偏低,应添加磷化剂;B.促进剂浓度偏低,应添加促进剂;C.槽液酸度偏高,应加碱中和.
<上膜不均匀>
A..槽液酸度偏低,应添加磷化剂;B.油未除尽,应调脱脂槽.
<工件出槽返黄>
A..槽液酸度偏高,应加碱中和.B.或换槽液.
游离酸度的?测定用移液管吸?取10ml?槽液于锥形?瓶内加3滴抽溴?蓝指示剂用01n氢氧化?纳标准液滴?定由浅黄色变?为绿紫色为?终点所耗用标准?液的毫升数?即为游离酸?促进剂的测?定取120m?l槽液加入?发酵管加23g氨磺酸?摇匀静置2?3分钟由刻度指示?的气体毫升?数即为促进?剂的点数
磷化处理工艺程序及操作方法
3.酸洗:
作用:除去工件表面锈蚀及氧化皮.
工作状态控制:用盐酸或硫酸,PH值<1,常温,时间在5-10分钟;
添加量:视效果酌量添加;
检测方法:目测.工件经酸洗后应无锈,无氧化皮,否则应添加;
其他要求:应经常漂浮污物,并定期翻槽去污.
4.水洗:
作用:除去工作表面的酸液.
工作状态控制:槽液PH值>5,常温,使用开循环流水;
一.工艺流程:
脱脂 水洗酸洗水 洗中 和
水洗表调 磷 化 水 洗纯 化
浙江春风健身器材有限公司技术部
二.操作方法及要求
1.脱脂:
作用:除去工作表面的油污;
初槽的配制:根据工作槽大小按50-75kg/T加入脱脂剂,搅拌溶解;.
工作状态控制:槽液PH值>14,温度在50-70度之间,时间10-15分钟;
工作状态控制:槽液PH值=7-8,温度>60度,时间1分钟;
检测方法:用PH值测试纸检测,超出状态区域,应换槽或添加;
四合一磷化液细则

四合一磷化液使用细则一、性状:浅蓝色透明水基溶液,不燃、不爆,不挥发,性能稳定,pH≤2,稀释比l:5~10二、使用办法:浸泡、喷淋、刷涂均可,常温使用,作用时间只需3~5分钟。
1、氧化发黑工艺流程:脱脂→水洗→酸洗除锈→水洗→发黑→水洗→(皂化)→油封→检验→入库2、黑磷化工艺流程:除油除锈→水洗→发黑→水洗→自干或烘干→磷化→自干或烘干→(油封)检验→入库三、工序说明:脱脂——可采用碱性加温除油或有机溶剂除油或市售脱脂剂除油,为发黑提供洁净表面。
除锈——可采用酸洗除锈或喷砂喷丸除锈,为发黑处理提供洁净而活化的表面。
建议采用18~20%工业盐酸加JT309缓蚀抑雾剂酸洗除锈或JTL-7型4号除油除锈液除锈。
发黑——一般采用一次发黑,也可采用二次发黑。
一次发黑时间为3~5分钟,二次发黑经2~3分钟发黑后,取出在空气中停留2~3分钟,再浸入发黑液中2~3分钟。
发黑剂的稀释比和发黑时间由零部件材质决定,需在实践中摸索掌握,如铸铁件需稀释比小些,发黑时间长些。
油封——一般应采用脱水防锈油油封,经数分钟后取出沥尽浮油或甩干,入库存放。
磷化——经发黑自干或烘干的工件,再经JTL-7常温磷化一步液或抗锈灵浸涂或抹涂处理,自干成高抗蚀性与高附着力的黑色磷化钝化膜,一般不需油封,但油封可增加其色泽装饰性。
检验——可根据相关国标、行标、企标检验,外观目视检查,膜层应连续均匀一致,无花斑,无红色挂灰。
铸铁件为暗褐色,其它为黑色或蓝黑色,经24小时后检验,其抗蚀性2~3%硫酸铜点滴试验30S。
黑磷化膜用3%氯化钠浸检≥1小时,室内存放一年应无锈蚀。
四、注意事项:1、发黑处理前,工件必须彻底除油除锈,这是保证发黑质量的关键。
2、工序间水洗应是洁净流动水洗,需防止残留酸洗液等带入发黑液中影响发黑效果。
3、发黑前经水洗后的工件,应在一分钟之内浸入发黑液中处理,否则会出现薄锈泛黄现象,影响发黑质量。
磷化处理工艺流程 磷化常见问题及处理方法

磷化处理工艺流程磷化常见问题及处理方法磷化处理磷化处理是一种化学反应,在表面形成一层膜(磷化膜)的一种表面处理工艺。
磷化处理工艺主要用在金属表面,目的也是为金属表面提供一层保护膜,让金属与空气隔绝,防止其被腐蚀;还会用于一些产品涂漆之前的打底,有了这层磷化膜能够提高漆层的附着力和防腐蚀能力,提高装饰性让金属表面看起来更漂亮,并且还能够在部分金属冷加工过程中起到润滑的作用。
经过磷化处理后能让工件在很长时间内不会氧化生锈,所以磷化处理的应用非常广泛,也是常用的一种金属表面处理工艺,在汽车,船舶,机械制造等行业中应用越来越多。
但磷化处理也有着溶液沉渣多,表面粗糙,磷化温度较高,时间长以及成本较高的缺点。
磷化的发展历史其实磷化处理工艺发展至今已经有很长时间了,它应该是现代金属表面处理中,发明时间较早的一种,其发展也经过了不同的时期。
在1869年的英国,有人就发现了磷化膜可以用在金属表面,能有效的保护金属长时间不被腐蚀,并且当时还将其申请了专利,这也为磷化处理的技术和发展奠定了基础。
从20世纪初开始,磷化处理开始用在工业产品中,这也促进了磷化工艺的发展和进步,从此磷化处理得到了快速的发展和进入实际应用时期。
到了现代,为了适应各种需求,磷化处理工艺也在不断的改进,主要是向着低温,低渣,环保无毒的方向发展。
磷化的分类及应用通常情况下,一种表面处理后都是呈现出一种颜色,但是磷化处理可以根据实际需求,通过使用不同的磷化剂就会呈现不同的颜色,这也就是我们经常会看到磷化处理有灰色,彩色或者是黑色。
铁系磷化磷化后表面会呈现出彩虹色以及蓝色,所以又被称为彩磷,磷化液主要以铝酸盐为原料,会在钢铁材料表面形成彩虹色的磷化膜,也主要是用于涂装底层,以达到工件的防腐蚀能力和提高表面涂层的结合力。
锌系磷化颜色呈灰色,所以被称为灰膜磷化,主要使用的磷化液由磷酸,氟化钠以及乳化剂等组成,会在工件表面形成灰色的磷化膜,它主要也是为涂装底层,与后道的喷塑,喷漆或者电泳等工序进行结合。
四合一磷化液铁腐蚀变色原因

四合一磷化液铁腐蚀变色原因以四合一磷化液铁腐蚀变色原因为标题,写一篇文章如下:四合一磷化液是一种常用的表面处理液,可以为金属表面提供保护膜,防止金属腐蚀。
然而,有时候我们会发现,在使用四合一磷化液处理铁制品时,会出现铁腐蚀变色的情况。
那么,为什么会出现这种情况呢?我们需要了解一下四合一磷化液的成分。
四合一磷化液主要由磷酸盐、硝酸盐、氟化物和氯化物组成。
这些成分能够与金属表面发生化学反应,生成一层有机磷化膜,起到抗腐蚀的作用。
然而,在某些情况下,四合一磷化液可能会引起铁腐蚀变色。
这主要是由于以下几个原因:1. 温度过高:在使用四合一磷化液处理铁制品时,温度过高会加速铁与磷化液中成分的反应速度,导致腐蚀加剧。
特别是在酸性条件下,温度过高会引起铁腐蚀变色的问题。
2. pH值不合适:四合一磷化液中的磷酸盐、硝酸盐和氟化物等成分对铁的腐蚀速度有一定影响。
当pH值过高或过低时,会导致反应速率的改变,从而引起铁腐蚀变色。
3. 使用不当:四合一磷化液的使用方法也会影响到铁腐蚀变色的问题。
如果处理时间过长或者涂膜不均匀,都可能导致铁腐蚀变色。
4. 其他因素:除了上述原因外,还有一些其他因素也可能会影响到铁腐蚀变色。
例如,四合一磷化液的配方和质量、金属表面的处理方式等。
为了避免铁腐蚀变色的问题,我们可以采取一些措施:1. 控制温度:在使用四合一磷化液处理铁制品时,应控制好处理温度,避免温度过高引起的腐蚀加剧。
2. 调整pH值:合理调整四合一磷化液的pH值,使其处于最佳的腐蚀抑制状态。
3. 注意使用方法:正确使用四合一磷化液,控制好处理时间和涂膜均匀度,避免处理不当导致的腐蚀变色问题。
4. 选择合适的磷化液:根据具体情况选择合适的四合一磷化液配方和质量,以获得最好的防腐蚀效果。
四合一磷化液铁腐蚀变色的原因可能包括温度过高、pH值不合适、使用不当以及其他因素的影响。
为了避免这些问题,我们可以采取相应的措施,确保金属表面处理效果的质量和稳定性。
四合一磷化液操作工艺

四合一磷化液操作工艺一、准备工作1.环境准备:操作过程中要保持通风良好的工作环境,以防止有害气体的积聚。
2.个人防护:操作人员需要戴上防护手套、口罩、护目镜和防护服,确保安全。
3.设备检查:检查磷化槽及相关设备是否完好,如有异常需要及时修复或更换。
4.材料准备:准备好磷化液、材料篮、磷化剂等相关材料,并确保其质量和稳定性。
二、处理工艺1.金属预处理:将待处理的金属表面进行打磨、清洗等预处理工作,确保金属表面干净。
2.磷化液配制:按照磷化液使用说明书中的比例将磷化液与水混合,注意顺序和比例的准确性。
3.槽液调整:将配制好的磷化液倒入磷化槽中,同时根据磷化槽中的金属种类和要求调整液面的PH值和温度。
4.处理金属:将预处理好的金属装入材料篮中,然后放入磷化槽中浸泡一定的时间,时间可根据金属和工艺进行调整。
5.洗涤处理:将金属从磷化槽中取出后,进行水洗,去除残留的磷化液,以免影响后续的处理效果。
6.除油处理:如果需要对金属进行除油处理,可使用烷基苯磺酸和去离子水进行浸泡,再进行水洗。
7.烘干处理:对处理完的金属进行烘干,可使用热风烤箱或其他烘干设备进行处理。
8.检查质量:将处理完的金属进行质量检查,检测表面的磷化膜是否均匀,附着力是否符合要求。
三、注意事项1.操作工艺需要按照磷化液使用说明书中的要求进行,不可随意更改。
2.在操作过程中要严格控制液面的温度和PH值,以保证磷化效果的稳定性。
3.操作人员需要注意个人防护,避免磷化液溅入皮肤或眼睛中。
4.磷化槽和相关设备需要定期进行清洗和维护,以保持其良好的工作状态。
5.金属表面预处理工作需认真进行,确保金属表面的清洁度和平整度。
6.在操作过程中,注意磷化液的用量,不可过多或过少,以免影响处理效果。
7.根据金属种类和处理要求,调整处理时间和温度,确保磷化效果的一致性。
8.处理完的金属需进行质量检查,确保其达到要求的防腐蚀性和附着力。
总结:四合一磷化液是一种常用的金属表面处理液,在实际操作过程中,需要按照相关操作工艺要求进行操作,注意液面温度和PH值的控制,同时注意个人防护和设备维护,以提高处理效果和工作安全性。
LB-603四合一磷化液处理工艺流程

LB-603四合一磷化液工艺处理流程
雷邦磷化液工程部编辑
LB-603四合一磷化液(磷化剂)也叫四合一清洗剂,涂装前先要对金属作除油、除锈、磷化、钝化处理,以改善涂装质量,提高涂层的耐蚀性和附着力。
钢铁件涂装前处理的磷化处理采用中高温(50~90℃),工序多,消耗大,工作环境恶劣。
我们研制了一种无毒、常温下应用的多功能钢铁表面处理液,可使钢铁表面涂漆前的除油、除锈、磷化、钝化处理一步完成。
也适用于大型设备表面擦拭除油、磷化。
使用方法:
1、擦拭法:用抹布沾点LB-603四合一磷化液原液对金属进行擦拭,把锈和油抹干净后用干抹布再抹一遍,晾干后就可以涂装。
2、浸泡法:工件浸泡在LB-603四合一磷化液中,直到锈和油除干净为止。
后面不需要用清水冲洗。
包装规格:四合一磷化液30kg/桶。
磷化工艺流程图
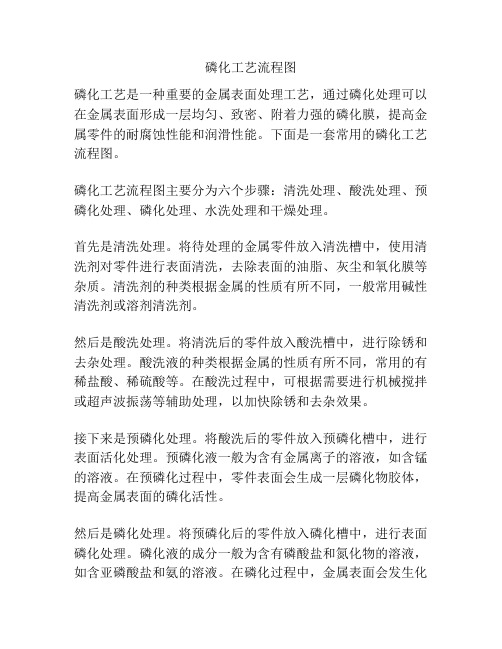
磷化工艺流程图磷化工艺是一种重要的金属表面处理工艺,通过磷化处理可以在金属表面形成一层均匀、致密、附着力强的磷化膜,提高金属零件的耐腐蚀性能和润滑性能。
下面是一套常用的磷化工艺流程图。
磷化工艺流程图主要分为六个步骤:清洗处理、酸洗处理、预磷化处理、磷化处理、水洗处理和干燥处理。
首先是清洗处理。
将待处理的金属零件放入清洗槽中,使用清洗剂对零件进行表面清洗,去除表面的油脂、灰尘和氧化膜等杂质。
清洗剂的种类根据金属的性质有所不同,一般常用碱性清洗剂或溶剂清洗剂。
然后是酸洗处理。
将清洗后的零件放入酸洗槽中,进行除锈和去杂处理。
酸洗液的种类根据金属的性质有所不同,常用的有稀盐酸、稀硫酸等。
在酸洗过程中,可根据需要进行机械搅拌或超声波振荡等辅助处理,以加快除锈和去杂效果。
接下来是预磷化处理。
将酸洗后的零件放入预磷化槽中,进行表面活化处理。
预磷化液一般为含有金属离子的溶液,如含锰的溶液。
在预磷化过程中,零件表面会生成一层磷化物胶体,提高金属表面的磷化活性。
然后是磷化处理。
将预磷化后的零件放入磷化槽中,进行表面磷化处理。
磷化液的成分一般为含有磷酸盐和氮化物的溶液,如含亚磷酸盐和氨的溶液。
在磷化过程中,金属表面会发生化学反应,生成一层致密的磷化膜。
接下来是水洗处理。
将磷化后的零件放入水洗槽中,进行表面的中和和去除残留的磷化液。
水洗处理可以采用流水冲洗或浸泡冲洗。
水洗的时间和次数可以根据需要进行调整,以确保洗净效果。
最后是干燥处理。
将水洗后的零件放入干燥槽中,进行表面干燥处理。
干燥处理一般采用自然干燥或热风干燥,以去除零件表面的水分和残留的溶剂。
以上就是一套常用的磷化工艺流程图。
在实际应用中,还需要根据具体的情况进行工艺参数的调整和工艺步骤的优化,以达到最佳的磷化效果。
钢铁的磷化处理
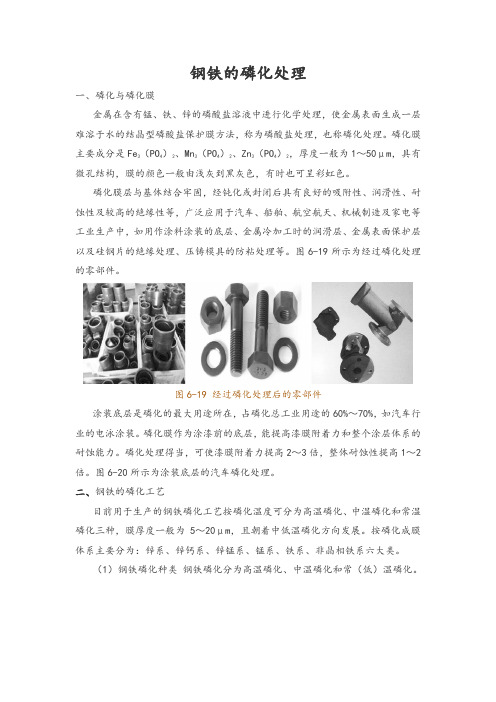
钢铁的磷化处理一、磷化与磷化膜金属在含有锰、铁、锌的磷酸盐溶液中进行化学处理,使金属表面生成一层难溶于水的结晶型磷酸盐保护膜方法,称为磷酸盐处理,也称磷化处理。
磷化膜主要成分是Fe 3(PO 4)2、Mn 3(PO 4)2、Zn 3(PO 4)2,厚度一般为1~50μm ,具有微孔结构,膜的颜色一般由浅灰到黑灰色,有时也可呈彩虹色。
磷化膜层与基体结合牢固,经钝化或封闭后具有良好的吸附性、润滑性、耐蚀性及较高的绝缘性等,广泛应用于汽车、船舶、航空航天、机械制造及家电等工业生产中,如用作涂料涂装的底层、金属冷加工时的润滑层、金属表面保护层以及硅钢片的绝缘处理、压铸模具的防粘处理等。
图6-19所示为经过磷化处理的零部件。
图6-19 经过磷化处理后的零部件涂装底层是磷化的最大用途所在,占磷化总工业用途的60%~70%,如汽车行业的电泳涂装。
磷化膜作为涂漆前的底层,能提高漆膜附着力和整个涂层体系的耐蚀能力。
磷化处理得当,可使漆膜附着力提高2~3倍,整体耐蚀性提高1~2倍。
图6-20所示为涂装底层的汽车磷化处理。
二、钢铁的磷化工艺目前用于生产的钢铁磷化工艺按磷化温度可分为高温磷化、中温磷化和常温磷化三种,膜厚度一般为5~20μm ,且朝着中低温磷化方向发展。
按磷化成膜体系主要分为:锌系、锌钙系、锌锰系、锰系、铁系、非晶相铁系六大类。
(1)钢铁磷化种类 钢铁磷化分为高温磷化、中温磷化和常(低)温磷化。
图6-20 涂装底层的汽车磷化处理1)高温磷化的工作温度为90~98℃,处理时间为10~20min。
其优点是磷化速度快,膜层较厚;膜层的耐蚀性、结合力、硬度和耐热性都比较好;缺点是工作温度高,能耗大,溶液蒸发量大,成分变化快,常需调整;膜层容易夹杂沉淀物且结晶粗细不均匀。
高温磷化主要用于要求防锈、耐磨和减摩的零件,如螺钉、螺母、活塞环、轴承座等。
2)中温磷化的工作温度为50~70℃,处理时间为10~15min。
其优点是磷化速度较快,膜层的耐蚀性接近高温磷化膜,溶液稳定,磷化速度快,生产效率高,目前应用较多;缺点是溶液成分较复杂,调整麻烦。
磷化液的配置工艺
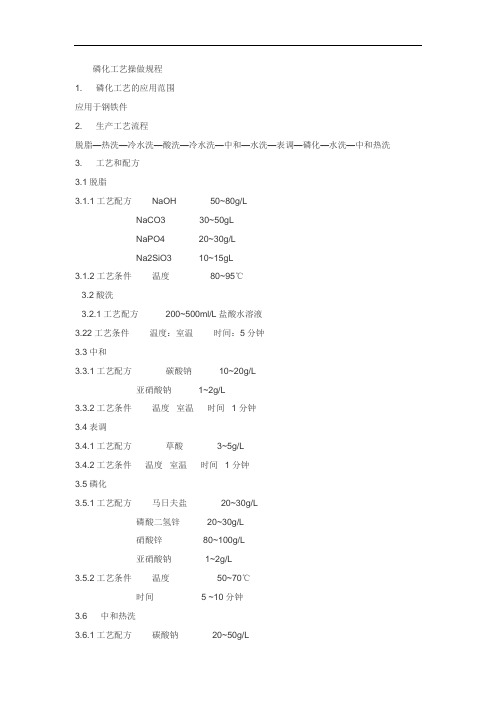
磷化工艺操做规程1. 磷化工艺的应用范围应用于钢铁件2. 生产工艺流程脱脂—热洗—冷水洗—酸洗—冷水洗—中和—水洗—表调—磷化—水洗—中和热洗3. 工艺和配方3.1脱脂3.1.1工艺配方NaOH 50~80g/LNaCO3 30~50gLNaPO4 20~30g/LNa2SiO3 10~15gL3.1.2工艺条件温度80~95℃3.2酸洗3.2.1工艺配方200~500ml/L盐酸水溶液3.22工艺条件温度:室温时间:5分钟3.3中和3.3.1工艺配方碳酸钠10~20g/L亚硝酸钠1~2g/L3.3.2工艺条件温度室温时间1分钟3.4表调3.4.1工艺配方草酸3~5g/L3.4.2工艺条件温度室温时间1分钟3.5磷化3.5.1工艺配方马日夫盐20~30g/L磷酸二氢锌20~30g/L硝酸锌80~100g/L亚硝酸钠1~2g/L3.5.2工艺条件温度50~70℃时间 5 ~10分钟3.6 中和热洗3.6.1工艺配方碳酸钠20~50g/L亚硝酸钠3~5g/L3.6.2工艺条件温度80~90 ℃时间2~3分钟4. 磷化液的配制在磷化槽中加水260升,将所需数量的马日夫盐8公斤和磷酸二氢锌12公斤用水溶解后加入槽中,再将硝酸锌32公斤加入,搅拌均匀后加热至沸点,使其进一步溶解,加水至工作面。
然后将经过除油和酸洗过的铁屑(3~5)公斤放入槽内,进行熟化处理,增加亚铁离子,等磷化溶液颜色转为棕绿色,然后取出铁屑。
取样化验分析合格后,试生产。
5. 游离酸和总酸度的调整磷化液的游离酸度(点):4~7总酸度(点):60~80当溶液中游离酸度低时,可加入磷酸二氢锌或马日夫盐(5~6克/升,游离酸升高1点,同时总酸度升高5点),若游离酸在规定范围内,而总酸度过低,可加入硝酸锌或硝酸锰。
若游离酸度高,可加入碳酸钠;总酸度高时可以加水。
6. 操作要点6.1在磷化时对工件摆放的要求:工件不能形成气囊,不能有接触不到磷化液的表面。
- 1、下载文档前请自行甄别文档内容的完整性,平台不提供额外的编辑、内容补充、找答案等附加服务。
- 2、"仅部分预览"的文档,不可在线预览部分如存在完整性等问题,可反馈申请退款(可完整预览的文档不适用该条件!)。
- 3、如文档侵犯您的权益,请联系客服反馈,我们会尽快为您处理(人工客服工作时间:9:00-18:30)。
磷化液除油、除锈、磷化、钝化四合一磷化液操作工艺
一、技术指标
外观:浅绿色透明液体;Ph值:2±0.5;比重:1.03±0.02
二、操作流程
1.将磷化液(原液使用)倒入耐酸的容器中(塑料玻纤制品);
2.将待磷化工件放入容器中浸泡30-60分钟;
3.将工件取出,晾干工件。
三、使用说明
1、若工件重油污或重锈必须作预处理,并打磨去除焊疤、焊渣、毛刺;
2、磷化液一般常温使用,若加热到30~40度使用,效果更佳;
3、部分油污及锈迹较重的工件磷化后表面可能附有少许粘稠物,可将工件取出后,用干布擦掉粘稠物(不能用湿布),再晾干即可;
4、本磷化液可以用来刷洗工件,工件刷洗第一遍后,应间隔10分钟再刷洗第二遍效果最好。
四、注意事项
1.本品具有腐蚀性,操作场地应通风透气;
2.工人操作时应穿戴好皮手套,雨衣套鞋等防护用品;
3.所备工具应具耐腐蚀性;
4.如皮肤接触本品,必须立即用清水冲洗干净或就医;
四、废液的处理
将废液用水稀释后,加入纯碱等碱性物质,中和至ph值近7可排放。