防爆壳体检验规范
防爆检查内容细则及完好标准
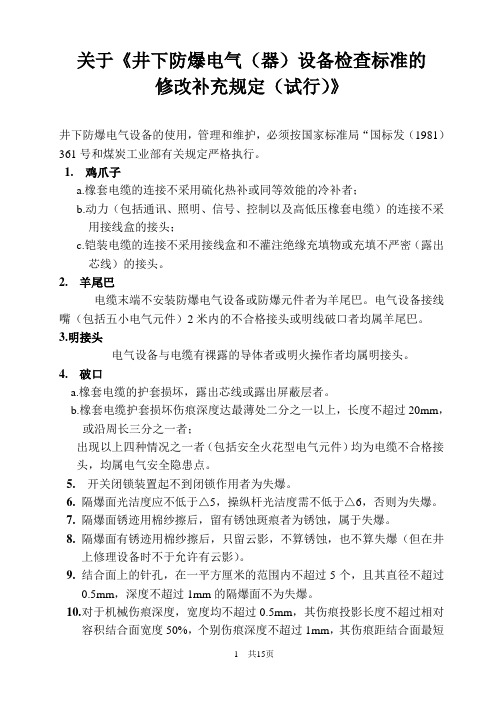
关于《井下防爆电气(器)设备检查标准的修改补充规定(试行)》井下防爆电气设备的使用,管理和维护,必须按国家标准局“国标发(1981)361号和煤炭工业部有关规定严格执行。
1.鸡爪子a.橡套电缆的连接不采用硫化热补或同等效能的冷补者;b.动力(包括通讯、照明、信号、控制以及高低压橡套电缆)的连接不采用接线盒的接头;c.铠装电缆的连接不采用接线盒和不灌注绝缘充填物或充填不严密(露出芯线)的接头。
2. 羊尾巴电缆末端不安装防爆电气设备或防爆元件者为羊尾巴。
电气设备接线嘴(包括五小电气元件)2米内的不合格接头或明线破口者均属羊尾巴。
3.明接头电气设备与电缆有祼露的导体者或明火操作者均属明接头。
4. 破口a.橡套电缆的护套损坏,露出芯线或露出屏蔽层者。
b.橡套电缆护套损坏伤痕深度达最薄处二分之一以上,长度不超过20mm,或沿周长三分之一者;出现以上四种情况之一者(包括安全火花型电气元件)均为电缆不合格接头,均属电气安全隐患点。
5.开关闭锁装置起不到闭锁作用者为失爆。
6.隔爆面光洁度应不低于△5,操纵杆光洁度需不低于△6,否则为失爆。
7.隔爆面锈迹用棉纱擦后,留有锈蚀斑痕者为锈蚀,属于失爆。
8.隔爆面有锈迹用棉纱擦后,只留云影,不算锈蚀,也不算失爆(但在井上修理设备时不于允许有云影)。
9.结合面上的针孔,在一平方厘米的范围内不超过5个,且其直径不超过0.5mm,深度不超过1mm的隔爆面不为失爆。
10.对于机械伤痕深度,宽度均不超过0.5mm,其伤痕投影长度不超过相对容积结合面宽度50%,个别伤痕深度不超过1mm,其伤痕距结合面最短无伤距离相加不大于相应容积规定的结合面宽度不算失爆,但其中有一项超过均为失爆。
11.隔爆面上不允许有油漆和机械性杂物,否则为失爆(如无意造成的油漆痕迹不超过隔爆面宽度的1/8不在此限)。
12.隔爆面应涂以适量的中性凡士林等合格的防锈油(如医用凡士林油)或磷化(磷化后也可涂凡士林油),如无防锈油或磷化面脱落均为失爆。
2024年防爆检查制度(二篇)

2024年防爆检查制度1、防爆检查要由经过专门培训取得《防爆检查合格证》的(防爆电工)专业人员具体操作。
2、防爆电气设备和五小电器必须取得防爆检查合格证才准入井,井下安装完毕必须发过防爆检查验收合格才准投入运行。
3、维护电工对管辖的防爆电气要坚持班班检查,并将检查的情况汇报工区作好记录,发现失爆要立即整改,严禁防爆电气失爆运行。
4、机电业务管理部门对矿井防爆电气要坚持正常检查,每周对每台件防爆电气的检查不得少于两次。
5、机电业务管理部门对矿井防爆电气的检查,发现失爆除了有权现场督促整改外,还可按规定对责任者处以一定数额的罚款。
2024年防爆检查制度(二)摘要:随着社会的不断发展,防爆安全成为了一个重要的话题。
为了保障公众的生命财产安全,各地纷纷推行防爆检查制度,力图在预防和控制防爆安全事故方面做出更为全面和严格的规范。
本文主要介绍了2024年防爆检查制度的基本内容,包括检查目标、检查内容、检查标准和处罚措施等方面。
同时,本文还讨论了防爆检查制度对社会的意义和影响,并提出了未来可能的发展方向。
一、检查目标2024年防爆检查制度的主要目标是保障公众的生命财产安全,预防和控制防爆安全事故的发生。
具体目标包括:确保防爆设备和设施的正常运行;加强对涉及爆炸危险的场所和企业的监管;提高社会公众的防爆意识和自觉性;完善防爆应急预案等。
二、检查内容2024年防爆检查涵盖的内容包括但不限于以下几个方面:检查防爆设备和设施的完整性和可靠性;检查存放和使用易燃易爆物品的场所和企业;检查公共场所和建筑物的防爆措施和安全管理情况;检查企业和个人的防爆意识和培训情况;检查防爆应急预案和演练情况等。
三、检查标准2024年防爆检查的标准主要基于现有的相关法律法规和技术标准,同时结合了实际情况做出了一些创新和完善。
具体标准包括:企业和场所必须具备必要的防爆设备和设施,例如爆炸防护设备、防爆电器等;仓库和工厂必须按照规定将易燃易爆物品分类存放,并且要定期检查防火设施的完好性;建筑物和公共场所必须安装并定期维护防爆灯具、防爆门窗等;企业和单位必须定期组织防爆演练,并且要进行防爆意识教育等。
防爆电机机壳检验规范

1.主题内容及适用范围
本规范规定了本厂电动机防爆机壳表面质量要求和检验方法。
本规范适用于防爆机壳(含机座、端盖、轴承盖、接线盒等的进货检验和加工完成后的表面质量验收。
2.表面质量技术要求
2.1机座铸件的表面质量要求按表1规定表1
2.2端盖铸件的表面质量要求按表2规定
表2
2.3轴承盖、接线盒等铸件的表面质量要求按表3规定表3
3.其他技术要求
3.1YBK2焊接机座,检查焊接表面是否有气孔、咬边、夹杂、焊流、表面裂纹等缺陷;
3.2机座、端盖、轴承盖、接线盒等主要技术参数应符合检验图纸要求;
3.3防爆外壳YB2、YBF2,供方能提供有资格试验室出具的有效的检验报告和有效的防爆电气配件生产资格证或防爆电气生产许可证;
3.4采购防爆外壳用于本厂安标认证或生产许可证产品使用的,应确认符合认证产品一致性要求。
4检验方法
4.1外观目测外壳表面质量应符合表1、表2、表3质量要求;
4.2外观目测符合3.2、3.3、3.4条要求;
4.3按检验图纸要求,使用卡尺、百分表等量具测量外壳主要技术参数均应符合;
5.验收规则
5.1每批进货检验按GB/T2828.1-2003抽样标准进行;
5.2批次判定合格的办理入库,批次不合格的按《不合格评审程序》执行。
防爆检查标准

防爆检查标准在工业生产和化工领域,防爆安全一直是一个重要的问题。
为了确保生产过程中的安全,防爆检查标准成为了必不可少的一部分。
本文将就防爆检查标准进行详细介绍,以便于大家更好地了解和应用。
首先,防爆检查标准的制定是基于相关法律法规和标准要求的。
在我国,防爆安全的相关法律法规主要包括《危险化学品安全管理条例》、《煤矿安全规程》等,这些法规对于防爆设备的选择、使用、维护等方面都有详细的规定,企业在进行防爆检查时必须要严格遵守相关法律法规的要求。
其次,防爆检查标准的内容主要包括防爆设备的选择和使用、防爆设备的维护和检修、防爆作业的管理等方面。
在选择和使用防爆设备时,必须要根据生产场所的具体情况和作业要求进行合理的选择,并且要确保设备的正常运行和有效使用。
在维护和检修防爆设备时,要按照相关规定进行定期的检查和维护,并且要及时处理设备的故障和隐患,以确保设备的安全可靠。
在防爆作业的管理方面,要建立健全的防爆管理制度,明确责任人和管理程序,加强对作业人员的安全教育和培训,确保作业的安全进行。
此外,防爆检查标准还要求企业要建立健全的防爆安全管理体系,包括安全生产责任制、安全生产标准化管理、安全生产培训等方面。
企业要加强对防爆安全管理的重视,做好安全生产工作,确保生产过程中的安全稳定。
总之,防爆检查标准是保障工业生产和化工领域安全生产的重要保障。
企业要严格遵守相关法律法规和标准要求,加强对防爆设备的选择、使用、维护和管理,建立健全的防爆安全管理体系,确保生产过程中的安全稳定。
只有这样,才能有效地预防和控制事故的发生,保障人员的生命财产安全。
希望本文对大家有所帮助,谢谢阅读。
防爆壳体检验要求示范

防爆壳体检验要求示范
一、前言
防爆壳是一种用于防止爆炸发生的装置,因此其质量和性能的检验非常重要。
本文将介绍防爆壳体检验的要求示范,以确保其质量和安全性。
二、外观检验
1.检查防爆壳的表面是否平整,无明显划痕或破损。
2.检查防爆壳的连接部位是否牢固,在正常使用情况下不会松动或脱落。
三、功能性检验
1.测试防爆壳的阻燃性能,使用明火或者高温热源靠近防爆壳,观察其是否能够有效阻止火焰蔓延。
2.测试防爆壳的防爆功能,使用适当的爆炸物模拟装置,在安全条件下进行爆炸,观察防爆壳是否能够有效地抵抗爆炸冲击。
四、安全性检验
1.检查防爆壳是否符合相关安全标准和规定,例如防爆等级、防护能力等。
2.通过非破坏性检测手段,例如X射线检测、超声波检测等,对防爆壳进行内部缺陷检测,确保其内部结构的完整性。
五、可靠性检验
1.对防爆壳进行耐久性测试,例如多次开启和关闭防爆壳门、多次冲
击等,以验证其在长时间使用过程中的可靠性。
2.进行防水性能测试,将防爆壳浸泡在一定深度的水中,观察其内部
是否受到水的侵入。
六、其他检验
1.检查防爆壳的包装是否完好无损,确保在运输和搬运过程中不会损
坏或变形。
2.检查防爆壳的相关标志和标识是否清晰可辨认,例如生产厂家、产
品型号等。
七、结论
根据以上要求示范进行防爆壳体检验,可以有效确保其质量和安全性。
在实际检验中,可以根据实际情况制定具体的检验方案和标准,以满足不
同防爆壳的检验需求。
检验结果应该及时记录和报告,对于不符合要求的
防爆壳应该及时处理、修复或替换,以保证其正常使用和安全性。
防爆壳体检验要求规范

隔爆壳体制造及出厂检验标准编制:审核:批准:隔爆壳体制造及出厂检验标准一、一般规定1.本标准适用于本公司隔爆壳体制造。
如图样或技术文件有特殊要求时应按图样或技术文件的规定执行。
2.本标准中各项规定,凡低于国家标准的,均按国家标准执行。
二、准备3.原材料牌号应符合图纸规定。
4.各种钢材在下料前应核实尺寸,其公差不符合本标准第5条规定者,均需矫正以达到要求公差。
5.钢板、扁钢的直线度及局部波状平面度的偏差不应超过表1的规定,否则必须矫正后方可使用。
表1 单位mm6.钢材的初步矫正,一般在冷态下在辊式矫正机或压力机进行。
用于次要焊接结构的钢板可放在平台上用平锤矫正。
7.钢材的矫正一般变形程度不大时,可用冷矫方法,弯曲较大的钢材应加热至900℃~1100℃时矫正。
矫正后的钢材表面不得有裂纹及明显痕迹,锤击痕深度对钢板为0.5mm,扁钢1mm(立面上)。
三、号料前的准备8.严格按照图样、技术文件、工艺要求及计算展开进行;下料偏差应符合《GB/T1804-1992 一般公差线性尺寸的未注公差》《GB/T1804-m》的要求。
9.样板的制造要考虑到结构在焊接时所产生的收缩量及零件的加工余量。
10.样板的外形尺寸偏差,当外形尺寸小于1米时为±0.4mm;大于1米时为±0.8mm。
11.样板上号料孔眼应用钻床钻孔,或用冲眼冲子冲成,但眼孔直径不能大于2毫米。
12.在样板上划线的偏差应符合下列规定:(1)相邻两孔的中心线的距离偏差为±0.15mm;(2)板边与边孔的中心线的距离偏差为±0.20mm;(3)相间(间隔一孔)钉孔中心线间的距离偏差为±0.30mm;(4)最大两端钉孔中心线的距离偏差为±0.40mm。
13.每个样板必须有标记(工号、图号、材料断面尺寸),样板经质量检查员验收签署后才可使用。
14.划线前,划线工应仔细检查样板是否合乎要求。
15.对单件小批生产的产品,允许直接在钢材上按图样进行划线。
防爆壳体检验要求规范
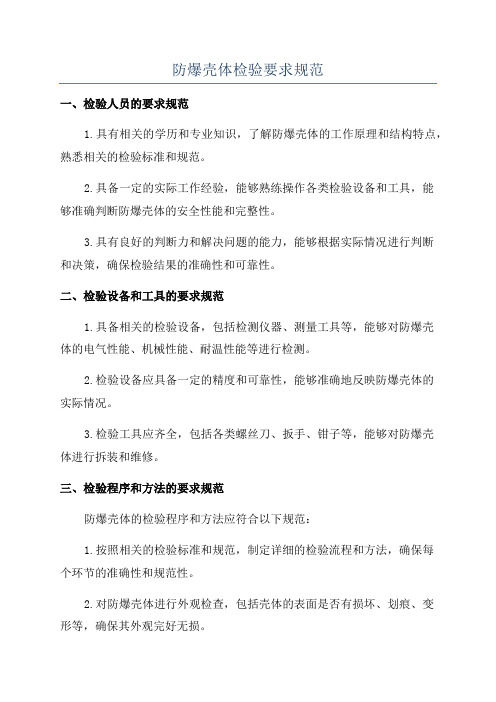
防爆壳体检验要求规范一、检验人员的要求规范1.具有相关的学历和专业知识,了解防爆壳体的工作原理和结构特点,熟悉相关的检验标准和规范。
2.具备一定的实际工作经验,能够熟练操作各类检验设备和工具,能够准确判断防爆壳体的安全性能和完整性。
3.具有良好的判断力和解决问题的能力,能够根据实际情况进行判断和决策,确保检验结果的准确性和可靠性。
二、检验设备和工具的要求规范1.具备相关的检验设备,包括检测仪器、测量工具等,能够对防爆壳体的电气性能、机械性能、耐温性能等进行检测。
2.检验设备应具备一定的精度和可靠性,能够准确地反映防爆壳体的实际情况。
3.检验工具应齐全,包括各类螺丝刀、扳手、钳子等,能够对防爆壳体进行拆装和维修。
三、检验程序和方法的要求规范防爆壳体的检验程序和方法应符合以下规范:1.按照相关的检验标准和规范,制定详细的检验流程和方法,确保每个环节的准确性和规范性。
2.对防爆壳体进行外观检查,包括壳体的表面是否有损坏、划痕、变形等,确保其外观完好无损。
3.对防爆壳体进行电气性能检验,包括耐压测试、绝缘电阻测试、接地测试等,确保其电气性能符合要求。
4.对防爆壳体进行机械性能检验,包括强度测试、密封性测试等,确保其机械性能符合要求。
5.对防爆壳体进行耐温性能检验,包括加热测试、热冲击测试等,确保其能够在高温环境下正常工作。
6.根据检验结果,对防爆壳体进行评估和判定,给出合格或不合格的结论。
四、检验结果的记录和报告的要求规范防爆壳体的检验结果应进行详细的记录和报告,包括以下几个方面:1.记录每个检验环节的检验方法、检验结果和检验日期等,确保记录的准确性和可追溯性。
2.对于不合格项,应记录具体的不合格现象和原因,并提出相应的处理建议。
3.生成详细的检验报告,包括检验结论、不合格项处理情况、检验人员签字等,确保报告的完整性和可信度。
综上所述,防爆壳体检验要求规范涉及到检验人员的要求、检验设备和工具的要求、检验程序和方法的要求,以及检验结果的记录和报告的要求等。
防爆壳体检验要求规范
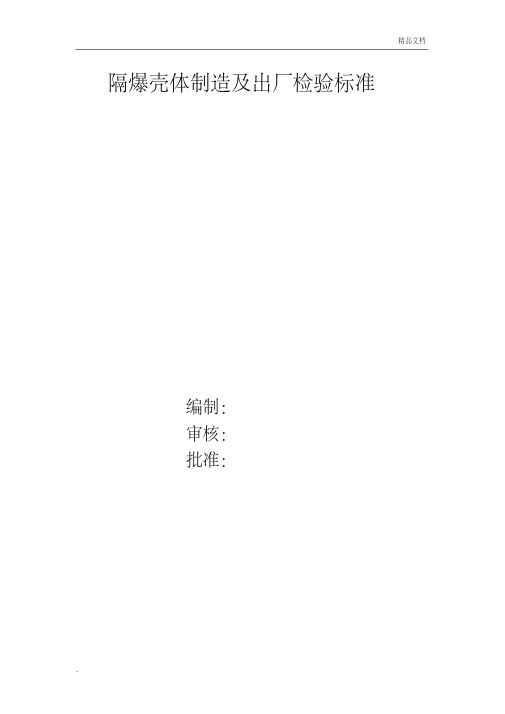
隔爆壳体制造及出厂检验标准编制:审核:批准:隔爆壳体制造及出厂检验标准一、一般规定1.本标准适用于本公司隔爆壳体制造。
如图样或技术文件有特殊要求时应按图样或技术文件的规定执行。
2.本标准中各项规定,凡低于国家标准的,均按国家标准执行。
二、准备3.原材料牌号应符合图纸规定。
4.各种钢材在下料前应核实尺寸,其公差不符合本标准第5条规定者,均需矫正以达到要求公差。
5.钢板、扁钢的直线度及局部波状平面度的偏差不应超过表1的规定,否则必须矫正后方可使用。
表1单位mm厚度(t )在1米长度内的直线度和局部波状凹凸平面度允许偏差(f )测量工具简要≤4 3 钢直尺,1米的平尺>4~8 2 >8~14 1.5 >1416.钢材的初步矫正,一般在冷态下在辊式矫正机或压力机进行。
用于次要焊接结构的钢板可放在平台上用平锤矫正。
7.钢材的矫正一般变形程度不大时,可用冷矫方法,弯曲较大的钢材应加热至900℃~1100℃时矫正。
矫正后的钢材表面不得有裂纹及明显痕迹,锤击痕深度对钢板为0.5mm,扁钢1mm(立面上)。
三、号料前的准备8.严格按照图样、技术文件、工艺要求及计算展开进行;下料偏差应符合《GB/T1804-1992 一般公差线性尺寸的未注公差》《GB/T1804-m》的要求。
9.样板的制造要考虑到结构在焊接时所产生的收缩量及零件的加工余量。
10.样板的外形尺寸偏差,当外形尺寸小于1米时为±0.4mm;大于1米时为±0.8mm。
11.样板上号料孔眼应用钻床钻孔,或用冲眼冲子冲成,但眼孔直径不能大于2毫米。
12.在样板上划线的偏差应符合下列规定:(1)相邻两孔的中心线的距离偏差为±0.15mm;(2)板边与边孔的中心线的距离偏差为±0.20mm;(3)相间(间隔一孔)钉孔中心线间的距离偏差为±0.30mm;(4)最大两端钉孔中心线的距离偏差为±0.40mm。
防爆检查标准

防爆检查标准防爆检查是指对可能发生爆炸危险的场所、设备和工艺进行定期检查,以确保其安全运行。
防爆检查标准是对防爆设备和防爆场所进行检查的依据,它的制定和执行对于保障人员生命财产安全具有重要意义。
本文将就防爆检查标准进行详细介绍,以便各单位和个人能够更好地了解和执行相关标准。
首先,防爆检查标准应包括对防爆设备和防爆场所的具体要求。
对于防爆设备,应包括其安全使用、维护、保养和检修等方面的要求,例如防爆电气设备的防护等级、防爆灯具的防爆等级等。
对于防爆场所,应包括其防爆区域的划分、防爆设备的设置和使用、防爆标志的设置等方面的要求,确保防爆场所内的设备和工艺能够安全运行。
其次,防爆检查标准应包括对防爆设备和防爆场所的检查内容和方法。
检查内容应包括对设备和场所的全面检查,包括设备的外观、电气连接、接地情况、防爆设备的完好性等方面的检查。
检查方法应包括目视检查、测量检查、试验检查等,以确保对设备和场所进行全面、细致的检查。
另外,防爆检查标准应包括对检查结果的评定和处理要求。
对于检查结果,应根据实际情况进行评定,对于存在安全隐患的设备和场所应及时进行处理,包括停止使用、维修更换等。
对于检查结果的处理,应包括对于安全隐患的整改要求和时限,确保安全隐患能够得到及时有效的处理。
最后,防爆检查标准应包括对防爆检查的管理和执行要求。
管理要求包括对防爆检查的组织、计划、实施和监督等方面的要求,确保防爆检查能够得到有效的管理和执行。
执行要求包括对防爆检查人员的资质、培训和责任等方面的要求,确保防爆检查能够得到专业、严格的执行。
综上所述,防爆检查标准是对防爆设备和防爆场所进行检查的依据,其制定和执行对于保障人员生命财产安全具有重要意义。
各单位和个人应严格执行相关标准,确保防爆设备和防爆场所的安全运行,防范和减少事故的发生。
希望本文能够对各单位和个人有所帮助,促进防爆检查工作的规范和落实。
防爆检查标准
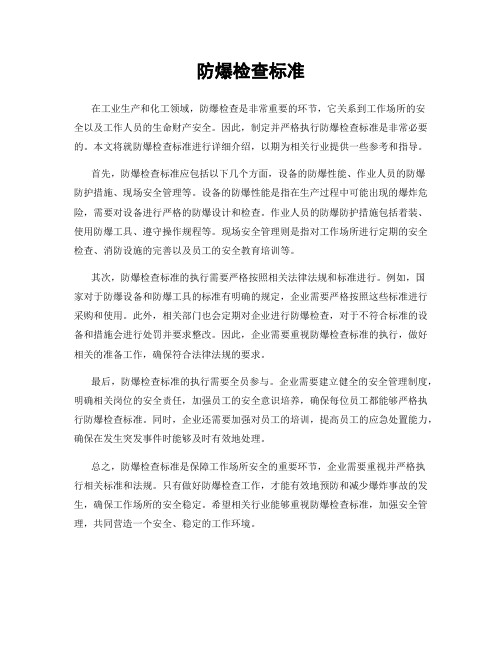
防爆检查标准在工业生产和化工领域,防爆检查是非常重要的环节,它关系到工作场所的安全以及工作人员的生命财产安全。
因此,制定并严格执行防爆检查标准是非常必要的。
本文将就防爆检查标准进行详细介绍,以期为相关行业提供一些参考和指导。
首先,防爆检查标准应包括以下几个方面,设备的防爆性能、作业人员的防爆防护措施、现场安全管理等。
设备的防爆性能是指在生产过程中可能出现的爆炸危险,需要对设备进行严格的防爆设计和检查。
作业人员的防爆防护措施包括着装、使用防爆工具、遵守操作规程等。
现场安全管理则是指对工作场所进行定期的安全检查、消防设施的完善以及员工的安全教育培训等。
其次,防爆检查标准的执行需要严格按照相关法律法规和标准进行。
例如,国家对于防爆设备和防爆工具的标准有明确的规定,企业需要严格按照这些标准进行采购和使用。
此外,相关部门也会定期对企业进行防爆检查,对于不符合标准的设备和措施会进行处罚并要求整改。
因此,企业需要重视防爆检查标准的执行,做好相关的准备工作,确保符合法律法规的要求。
最后,防爆检查标准的执行需要全员参与。
企业需要建立健全的安全管理制度,明确相关岗位的安全责任,加强员工的安全意识培养,确保每位员工都能够严格执行防爆检查标准。
同时,企业还需要加强对员工的培训,提高员工的应急处置能力,确保在发生突发事件时能够及时有效地处理。
总之,防爆检查标准是保障工作场所安全的重要环节,企业需要重视并严格执行相关标准和法规。
只有做好防爆检查工作,才能有效地预防和减少爆炸事故的发生,确保工作场所的安全稳定。
希望相关行业能够重视防爆检查标准,加强安全管理,共同营造一个安全、稳定的工作环境。
防爆壳体检验要求规范

隔爆壳体制造及出厂检验标准编制:审核:批准:隔爆壳体制造及出厂检验标准一、一般规定1.本标准适用于本公司隔爆壳体制造。
如图样或技术文件有特殊要求时应按图样或技术文件的规定执行。
2.本标准中各项规定,凡低于国家标准的,均按国家标准执行。
二、准备3.原材料牌号应符合图纸规定。
4.各种钢材在下料前应核实尺寸,其公差不符合本标准第5条规定者,均需矫正以达到要求公差。
5.钢板、扁钢的直线度及局部波状平面度的偏差不应超过表1的规定,否则必须矫正后方可使用。
表1 单位mm6.钢材的初步矫正,一般在冷态下在辊式矫正机或压力机进行。
用于次要焊接结构的钢板可放在平台上用平锤矫正。
7.钢材的矫正一般变形程度不大时,可用冷矫方法,弯曲较大的钢材应加热至900℃~1100℃时矫正。
矫正后的钢材表面不得有裂纹及明显痕迹,锤击痕深度对钢板为0.5mm,扁钢1mm(立面上)。
三、号料前的准备8.严格按照图样、技术文件、工艺要求及计算展开进行;下料偏差应符合《GB/T1804-1992 一般公差线性尺寸的未注公差》《GB/T1804-m》的要求。
9.样板的制造要考虑到结构在焊接时所产生的收缩量及零件的加工余量。
10.样板的外形尺寸偏差,当外形尺寸小于1米时为±0.4mm;大于1米时为±0.8mm。
11.样板上号料孔眼应用钻床钻孔,或用冲眼冲子冲成,但眼孔直径不能大于2毫米。
12.在样板上划线的偏差应符合下列规定:(1)相邻两孔的中心线的距离偏差为±0.15mm;(2)板边与边孔的中心线的距离偏差为±0.20mm;(3)相间(间隔一孔)钉孔中心线间的距离偏差为±0.30mm;(4)最大两端钉孔中心线的距离偏差为±0.40mm。
13.每个样板必须有标记(工号、图号、材料断面尺寸),样板经质量检查员验收签署后才可使用。
14.划线前,划线工应仔细检查样板是否合乎要求。
15.对单件小批生产的产品,允许直接在钢材上按图样进行划线。
防爆设备标准及检查方法范文(3篇)

防爆设备标准及检查方法范文防爆设备是用于防止爆炸事故的发生及减轻其危害的特种设备。
根据《特种设备安全法》及相关法律法规,防爆设备必须符合一定的标准要求,并定期进行检查评估。
本文将介绍防爆设备标准及检查方法,以确保防爆设备的安全性能和可靠性。
一、防爆设备标准1. GB 3836.1-2010防爆电器通用要求该标准规定了防爆电器的一般要求,包括分类、防护等级、防爆结构、使用要求等。
防爆设备必须符合该标准的要求,确保其安全可靠地运行。
2. GB 3836.2-2010 防爆电气设备“d”类该标准规定了使用于可燃性气体环境的“d”类防爆电气设备的要求。
电气设备必须具备防止火花、电弧和高温表面等产生的能力,防止可燃性气体的燃烧和爆炸。
3. GB 3836.3-2010 防爆电气设备“c”类该标准规定了使用于可燃性液体环境的“c”类防爆电气设备的要求。
电气设备必须具备能够抑制可燃性液体产生的火花、电弧和高温表面等的能力,防止可燃性液体的燃烧和爆炸。
4. GB 3836.4-2010 防爆电气设备“b”类该标准规定了使用于可燃性粉尘环境的“b”类防爆电气设备的要求。
电气设备必须具备绝缘保护、封闭性能和防爆外壳等措施,防止可燃性粉尘的燃烧和爆炸。
5. GB 3836.5-2010 防爆电气设备“e”类该标准规定了使用于煤矿环境的“e”类防爆电气设备的要求。
电气设备必须具备对煤尘和甲烷等可燃性气体的抗腐蚀、防爆和防静电等能力,防止煤矿事故的发生。
二、防爆设备检查方法对于防爆设备的检查方法可以分为日常检查和定期检查,下面将介绍具体的检查内容和方法。
1. 日常检查:(1)外观检查:检查防爆设备的外观是否有明显的破损、变形等现象。
(2)密封性能检查:检查防爆设备的密封性能是否正常,是否有泄露现象。
(3)开关检查:检查防爆电气设备的开关是否灵活,触点是否磨损,接触可靠。
(4)线缆连接检查:检查防爆电气设备的线缆连接是否牢固,是否有松动现象。
防爆电气设备防爆检查标准

防爆电气设备检查标准第一条本标准适用于公司矿井井下和地面具有瓦斯、煤尘爆炸环境中使用的防爆电气设备和连线电缆。
第二条防爆电气设备、小型电器必须有永久性的防爆标志(Exdi)、煤安标志(MA)、产品“铭牌”,无“防爆标志”、“煤安标志”为失爆,无“铭牌”为不完好。
第三条防爆电气设备、小型电器下井前必须经专职防爆检查员检查,粘贴“防爆检查合格证”,并签发“入井许可证”才能下井,现场检查无“防爆检查合格证”为失爆。
二、壳体第四条凡是转轴穿过隔爆外壳壁的地方应有隔爆轴承盖,否则为失爆。
第五条隔爆壳变形长度超过50mm,凸凹深度超过5mm为失爆。
第六条隔爆外壳开焊为失爆,锈蚀严重、有锈皮脱落为失爆;油漆皮脱落较多为不完好。
第七条穿越隔爆腔的接线座有裂缝或晃动为失爆。
第八条隔爆外壳上的观察窗内密封衬垫必须采用具有一定强度的金属包覆的不燃性材料制成,衬垫的厚度不能小于2mm。
当外壳,当外壳净容积不大于100cm3时,衬垫宽度不得小于9.5mm。
否则为失爆。
观察窗玻璃表面伤痕深度小于1mm 为不完好,否则为失爆。
三、防爆面第九条隔爆接合面间隙和宽度不得小于表1、表2的规定,快开式门或盖的隔爆接合面的最小有效宽度不小于25毫米,否则为失爆。
1、静止隔爆面的间隙与接合面宽度:表12、活动部分(操纵杆和电机轴)隔爆接合面间隙与接合面宽度:表2第十条隔爆面划伤为不完好,其深度与宽度大于0.5mm,或无伤隔爆面有效宽度小于表1、表2规定值的2/3,为失爆。
无伤隔爆面的有效宽度计算见图1。
L1—无伤隔爆面有效宽度L —隔爆面规定宽度 L1—螺孔边缘至隔爆面边缘最短有效宽度。
第十一条转盖式或插盖式隔爆面的宽度不得小于25mm,间隙不得大于0.5mm,否则为失爆。
快开式门或盖因变形打不开,且隔爆面间隙大于或结合机有效宽度小于表1规定值为失爆,否则为不完好。
第十二条隔爆面的表面粗糙度应不大于6.3μm,操纵杆粗糙度应不大于3.2μm,否则为失爆。
防爆检查标准

防爆检查标准
防爆检查是指对潜在的爆炸危险进行检查和评估,以确保工作场所的安全。
在
进行防爆检查时,需要遵循一定的标准和程序,以确保检查的全面性和准确性。
本文将介绍防爆检查的标准和相关内容,以供参考。
首先,进行防爆检查时,需要对工作场所的潜在危险进行全面的评估。
这包括
对可能存在的爆炸危险源进行识别和分析,对可能存在的防爆措施进行评估,以及对可能存在的爆炸危险进行定量分析。
通过全面的评估,可以确保对潜在危险的全面了解,为后续的防爆措施提供依据。
其次,防爆检查需要遵循相关的标准和规范。
在进行防爆检查时,需要遵循国
家相关的标准和规范,以确保检查的准确性和可靠性。
例如,对于化工企业的防爆检查,需要遵循《化工企业爆炸危险性评价标准》等相关标准,对可能存在的爆炸危险进行评估和控制。
另外,防爆检查还需要依靠专业的人员和设备。
在进行防爆检查时,需要依靠
具有相关专业知识和经验的人员,进行全面的评估和分析。
同时,还需要依靠先进的检测设备和工具,对可能存在的爆炸危险进行定量分析和检测,以确保检查的准确性和可靠性。
最后,防爆检查需要及时进行整改和改进。
在进行防爆检查后,需要及时对可
能存在的安全隐患进行整改和改进,以确保工作场所的安全。
同时,还需要对防爆措施进行定期的检查和评估,及时发现和解决可能存在的安全隐患,以确保工作场所的持续安全。
总之,防爆检查是确保工作场所安全的重要环节,需要遵循一定的标准和程序,依靠专业的人员和设备,及时进行整改和改进。
只有这样,才能有效地防范潜在的爆炸危险,确保工作场所的安全。
防爆检查标准

INSERT YOUR LOGO防爆检查标准通用模板Make all the staff know what they should and should not do, clarify their responsibilities, and fully mobilize the enthusiasm of all the staff to become the driving force for the production and operation of the enterprise.撰写人/风行设计审核:_________________时间:_________________单位:_________________防爆检查标准通用模板使用说明:本管理制度文档可用在管理中,为使全体人员都知道应该做什么,不应该做什么,以及明确自己的主要职责,所担负的职责对整个企业工作具有的意义和作用,从而把全体人员的工作积极性充分地调动起来,成为推动企业生产经营工作的动力。
为便于学习和使用,请在下载后查阅和修改详细内容。
一、防爆检查总则:1.为了进一步贯彻执行《煤矿安全规程》和《阳煤集团机电设备防爆检查标准》,切实提高井下机电从业者对防爆电气性能的认识,在实际工作中便于掌握运用标准,从而加强对煤矿井下防爆电气的科学管理,提高维修质量,消灭电气失爆,实现电气设备安全运行,特制订本《细则》。
2.所有井下电气设备(包括小型电气设备)的选用,都必须符合《煤矿安全规程》第444条和第7条的要求。
3.专职防爆检查员必须经过上级主管部门培训考试,并取得合格证。
4.防爆电气设备,在入井前必须经专职防爆检查员检查其“产品合格证”、“防爆合格证”、“煤矿矿用产品安全标志”及安全性能;检查合格并签发合格证后,方准入井。
5.下井防爆电气设备变更额定值使用和进行技术改造时,必须经国家授权的矿用产品质量监督检验部门检验。
6.井下防爆电气设备的运行、维护和修理工作,都必须符合防爆性能的各项技术要求。
隔爆兼本安壳体检验规范13-9-30

检验员日期
检验科室:日期:201年月日
2
法兰紧固螺纹M6,孔距符合图纸
3
防爆本安过线螺纹精度符合6H
本安壳体
4
壳体厚度符合要求
装配
5
两个壳体在同一面,主体美观
三:隔爆面参数:游标卡尺、卷尺、粗糙度样块、刀口尺等
技术要求
实测值
检验结果
检验员
技术要求
实测值
检测结果
检验员
日期
1
隔爆面长度≥12
5平面度
2
孔到腔体边距离l≥9
防爆结合面l≥8
3
粗糙度
一:外观检查:目测,卷尺,游标卡尺等
1
外壳材质
Q235AHT250
2
表面无明细划伤,凸凹痕、裂缝变形
结果
检测员
日期
、裂缝等,焊后做时效处理。
5
焊缝高度大于3
进线嘴焊接要横平竖直
二:尺寸大小:游标卡尺、卷尺等
防爆壳体
结果
检测员
日期
1
法兰厚度≥10mm
防爆检查标准
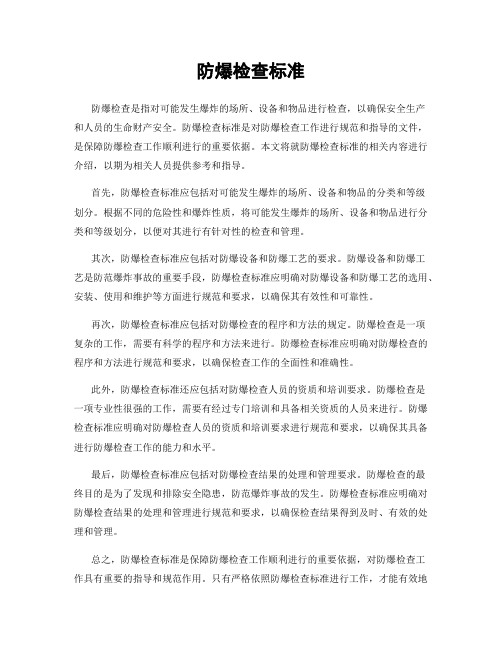
防爆检查标准防爆检查是指对可能发生爆炸的场所、设备和物品进行检查,以确保安全生产和人员的生命财产安全。
防爆检查标准是对防爆检查工作进行规范和指导的文件,是保障防爆检查工作顺利进行的重要依据。
本文将就防爆检查标准的相关内容进行介绍,以期为相关人员提供参考和指导。
首先,防爆检查标准应包括对可能发生爆炸的场所、设备和物品的分类和等级划分。
根据不同的危险性和爆炸性质,将可能发生爆炸的场所、设备和物品进行分类和等级划分,以便对其进行有针对性的检查和管理。
其次,防爆检查标准应包括对防爆设备和防爆工艺的要求。
防爆设备和防爆工艺是防范爆炸事故的重要手段,防爆检查标准应明确对防爆设备和防爆工艺的选用、安装、使用和维护等方面进行规范和要求,以确保其有效性和可靠性。
再次,防爆检查标准应包括对防爆检查的程序和方法的规定。
防爆检查是一项复杂的工作,需要有科学的程序和方法来进行。
防爆检查标准应明确对防爆检查的程序和方法进行规范和要求,以确保检查工作的全面性和准确性。
此外,防爆检查标准还应包括对防爆检查人员的资质和培训要求。
防爆检查是一项专业性很强的工作,需要有经过专门培训和具备相关资质的人员来进行。
防爆检查标准应明确对防爆检查人员的资质和培训要求进行规范和要求,以确保其具备进行防爆检查工作的能力和水平。
最后,防爆检查标准应包括对防爆检查结果的处理和管理要求。
防爆检查的最终目的是为了发现和排除安全隐患,防范爆炸事故的发生。
防爆检查标准应明确对防爆检查结果的处理和管理进行规范和要求,以确保检查结果得到及时、有效的处理和管理。
总之,防爆检查标准是保障防爆检查工作顺利进行的重要依据,对防爆检查工作具有重要的指导和规范作用。
只有严格依照防爆检查标准进行工作,才能有效地预防和减少爆炸事故的发生,确保安全生产和人员的生命财产安全。
希望相关人员能够认真学习和遵守防爆检查标准,做好防爆检查工作,为安全生产和社会稳定做出应有的贡献。
防爆装置检验标准规范

防爆装置检验标准规范1.引言本文档旨在制定防爆装置的检验标准规范,以确保产品的安全性和质量。
防爆装置是一种重要的安全设备,用于防止爆炸事故的发生。
该标准规范是为生产商、测试实验室和监管机构提供的指南。
2.定义2.1 防爆装置:指用于控制和防止爆炸事故的设备或系统。
2.2 检验:指对防爆装置进行测试和评估,以验证其符合相关安全标准和法规要求。
3.检验范围本标准规范适用于所有类型的防爆装置,包括但不限于爆炸防护设备、防爆电气设备和防爆机械设备。
4.检验要求4.1 安全性检验4.1.1 防爆装置应符合国家和国际相关的安全标准和法规要求。
4.1.2 检验应包括对防爆装置的结构、材料、工艺和性能的评估。
4.1.3 检验应检测防爆装置在正常使用条件下的可靠性和稳定性。
4.2 功能性检验4.2.1 防爆装置应满足其设计和使用的功能要求。
4.2.2 检验应包括对防爆装置的正常工作和应急情况下的性能测试。
4.2.3 检验应验证防爆装置的响应时间、灵敏度和精度等功能指标。
5.检验方法5.1 样品选取5.1.1 样品数量应符合统计学原则,足以代表生产批次的质量。
5.1.2 样品的选取应随机进行,以避免样本的偏倚。
5.2 检验设备5.2.1 检验设备应符合相关标准,并在检验前进行校准和验证。
5.2.2 检验设备应能满足对防爆装置各项性能和功能的测试要求。
5.3 检验步骤5.3.1 检验应按照相关标准和检验方案进行,确保检验的全面性和准确性。
5.3.2 检验过程中应记录检验参数、结果和判定依据,以备查证和分析。
6.检验报告6.1 检验报告应明确记录检验的目的、方法、结果和结论。
6.2 检验报告应包括样品信息、检验日期和检验员信息等必要内容。
6.3 检验报告应保存一定的时间,以备监管机构的审查和验证。
7.监督和执法7.1 监督机构应对防爆装置的生产、销售和使用进行监督和检查。
7.2 对于不符合检验标准规范的防爆装置,监督机构应采取相应的执法措施,并追究相关责任。
防爆壳体检验规范
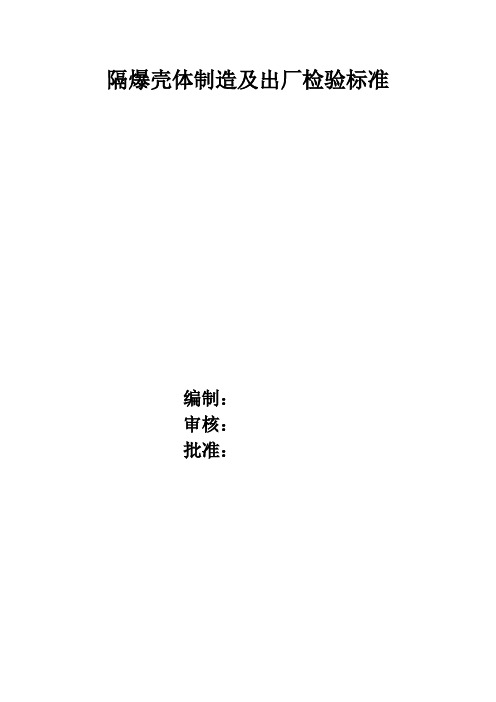
隔爆壳体制造及出厂检验标准编制:审核:批准:隔爆壳体制造及出厂检验标准一、一般规定1.本标准适用于本公司隔爆壳体制造。
如图样或技术文件有特殊要求时应按图样或技术文件的规定执行。
2.本标准中各项规定,凡低于国家标准的,均按国家标准执行。
二、准备3.原材料牌号应符合图纸规定。
4.各种钢材在下料前应核实尺寸,其公差不符合本标准第5条规定者,均需矫正以达到要求公差。
5.钢板、扁钢的直线度及局部波状平面度的偏差不应超过表1的规定,否则必须矫正后方可使用。
表1 单位mm6.钢材的初步矫正,一般在冷态下在辊式矫正机或压力机进行。
用于次要焊接结构的钢板可放在平台上用平锤矫正。
7.钢材的矫正一般变形程度不大时,可用冷矫方法,弯曲较大的钢材应加热至900℃~1100℃时矫正。
矫正后的钢材表面不得有裂纹及明显痕迹,锤击痕深度对钢板为0.5mm,扁钢1mm(立面上)。
三、号料前的准备8.严格按照图样、技术文件、工艺要求及计算展开进行;下料偏差应符合《GB/T1804-1992 一般公差线性尺寸的未注公差》《GB/T1804-m》的要求。
9.样板的制造要考虑到结构在焊接时所产生的收缩量及零件的加工余量。
10.样板的外形尺寸偏差,当外形尺寸小于1米时为±0.4mm;大于1米时为±0.8mm。
11.样板上号料孔眼应用钻床钻孔,或用冲眼冲子冲成,但眼孔直径不能大于2毫米。
12.在样板上划线的偏差应符合下列规定:(1)相邻两孔的中心线的距离偏差为±0.15mm;(2)板边与边孔的中心线的距离偏差为±0.20mm;(3)相间(间隔一孔)钉孔中心线间的距离偏差为±0.30mm;(4)最大两端钉孔中心线的距离偏差为±0.40mm。
13.每个样板必须有标记(工号、图号、材料断面尺寸),样板经质量检查员验收签署后才可使用。
14.划线前,划线工应仔细检查样板是否合乎要求。
15.对单件小批生产的产品,允许直接在钢材上按图样进行划线。
- 1、下载文档前请自行甄别文档内容的完整性,平台不提供额外的编辑、内容补充、找答案等附加服务。
- 2、"仅部分预览"的文档,不可在线预览部分如存在完整性等问题,可反馈申请退款(可完整预览的文档不适用该条件!)。
- 3、如文档侵犯您的权益,请联系客服反馈,我们会尽快为您处理(人工客服工作时间:9:00-18:30)。
隔爆壳体制造及出厂检验标准编制:审核:批准:隔爆壳体制造及出厂检验标准一、一般规定1.本标准适用于本公司隔爆壳体制造。
如图样或技术文件有特殊要求时应按图样或技术文件的规定执行。
2.本标准中各项规定,凡低于国家标准的,均按国家标准执行。
二、准备3.原材料牌号应符合图纸规定。
4.各种钢材在下料前应核实尺寸,其公差不符合本标准第5条规定者,均需矫正以达到要求公差。
5.钢板、扁钢的直线度及局部波状平面度的偏差不应超过表1的规定,否则必须矫正后方可使用。
表1 单位mm6.钢材的初步矫正,一般在冷态下在辊式矫正机或压力机进行。
用于次要焊接结构的钢板可放在平台上用平锤矫正。
7.钢材的矫正一般变形程度不大时,可用冷矫方法,弯曲较大的钢材应加热至900℃~1100℃时矫正。
矫正后的钢材表面不得有裂纹及明显痕迹,锤击痕深度对钢板为0.5mm,扁钢1mm(立面上)。
三、号料前的准备8.严格按照图样、技术文件、工艺要求及计算展开进行;下料偏差应符合《GB/T1804-1992 一般公差线性尺寸的未注公差》《GB/T1804-m》的要求。
9.样板的制造要考虑到结构在焊接时所产生的收缩量及零件的加工余量。
10.样板的外形尺寸偏差,当外形尺寸小于1米时为±0.4mm;大于1米时为±0.8mm。
11.样板上号料孔眼应用钻床钻孔,或用冲眼冲子冲成,但眼孔直径不能大于2毫米。
12.在样板上划线的偏差应符合下列规定:(1)相邻两孔的中心线的距离偏差为±0.15mm;(2)板边与边孔的中心线的距离偏差为±0.20mm;(3)相间(间隔一孔)钉孔中心线间的距离偏差为±0.30mm;(4)最大两端钉孔中心线的距离偏差为±0.40mm。
13.每个样板必须有标记(工号、图号、材料断面尺寸),样板经质量检查员验收签署后才可使用。
14.划线前,划线工应仔细检查样板是否合乎要求。
15.对单件小批生产的产品,允许直接在钢材上按图样进行划线。
16.号料时应考虑留出工艺损耗量。
四、切料17.钢材可以用机械剪切、锯床、气割等方法。
18.切料后,边棱上的堆积物、毛刺和凸起部分均应清除。
切料尺寸偏差应符合下列规定(1)钢板的机械剪切线与号线的偏差不大于表2的规定。
表2 单位mm(2)钢板下料时,沿长度或宽度方向的偏斜(如图1)不得超过板料剪切偏差所允许的范围(表2)正负图1(3)气割后要保留号料线,气割线与号料线的偏差,对于手工切割时不超过±1.5毫米,对自动或半自动的切割不超过1毫米。
19.框架法兰下料偏差(如图2)m=L1-(n×2)图2L端加工的偏差为+2~+4。
L端不加工的偏差为-0.5~+1,端面斜偏差不超过0.5mm,但不能超过两端不加工面的偏差值(如图3)。
图320.出线板下料不分长短边偏差为-0.5-1.0。
21.底板下料不分长短边偏差为-0.5-1.0,对角线性偏差不超过1.5mm。
22.出线室的钢板展开长度下料偏差为+1.0-0.5,宽度偏差为+2.0+1.0。
23.方箱体展开长度下料偏差为+2.0+1.0,对角线性偏差不超过1.5mm。
圆箱体展开长度下料偏差为+3.0+1.0,对角线性偏差不超过1.5mm。
24.接线室上盖下料不分长短边偏差为+1.0+0.5.25.各种内腔安装底板下料不分长短边偏差为±1。
五、焊接件的对装要求26.对拼装前,全部零部件须经检查合格。
27.对装结构零件及整个结构时,必须严格保持图样上的标准尺寸。
尺寸不合格的零件,禁止用强力矫正,以防引起过大的应力;但允许用轻轻打击,用弓形卡牵引的方法进行零件的局部调整。
但隔爆面加工后的部件严禁矫正。
28.结构件边缘上的裂纹和其他缺陷,经技术检查部门同意后,允许焊补。
29.对装焊接零件时,焊接间隙及焊接件相互位置的偏差应符合下列规定:(1)对装对接接头(图4)时,当对接两板厚度相同,两个焊边允许的偏差按表3规定。
图4表330.坡口的焊接形式及偏差 表4。
表431.框架法兰焊接偏差,m 偏差应减去a 1、a 2长度的误差(图5)。
c =±0.3L=±1.0H=±1.0图5 m=±1.5六、焊接技术条件 (一)一般规则32.焊工应经专门培训考核合格,才能担任焊接工作,持证上岗。
33.焊接专职检查人员应由具有一定理论及实践经验的人员担任,并需经总工程师(或公司技术总负责人)审批。
34.检查人员对违反规定的焊接作业,有权制止,直至得到纠正。
(二)技术要求35.Ⅰ、Ⅱ级焊缝破口的加工采用机械的方法(门法兰、箱体法兰、接线上腔法兰)。
Ⅰ、Ⅱ级焊缝破口的加工可采用气割等方法。
36.焊接材料的选用,应根据木材的化学成分、机械性能、焊前预热及焊后回火等综合考虑。
37.多层焊接时,在焊接每层焊缝以前,应对前一层焊缝进行检查,如发现夹渣、气孔和裂纹时,应将缺陷部分除净再焊。
38.不同厚度钢板焊接时,如图中未注明焊脚高度,则其焊脚高度等于薄板的厚度。
(三)焊接工艺的要求39.焊接接头形式和尺寸按表4选用。
40.焊前应将坡口表面及内外侧10毫米范围内的油、锈污物及水气清除干净。
41.焊接工艺对外界环境的要求(1)恶劣天气(下雨、下雪、大风及高湿度等室外作业)如无有效措施,禁止施焊。
(2)当焊接温度低于0℃时,应考虑在始焊外100毫米范围内预热到约15℃(手触感温暖),不准用重锤打击所焊的构件,在焊接过程中保证焊缝能够自由收缩。
(3)壳体焊接一般应在室内进行,室温不得低于5℃,当室温低于0℃时按要求(2)。
(四)焊接变形的矫正42.焊接构件如有变形,允许用局部加热的方法矫正。
加热温度为800~850℃,但不允许在300~500℃时矫正。
低碳钢焊接构件的矫正可在冷态下进行。
(五)焊接的检查及验收43.验收应在焊接构件4小时后进行(完全冷却后)。
44.焊件检查前应将焊缝上的渣皮及飞溅物等清除干净。
45.用肉眼或借助放大镜环件检查焊缝的外观质量。
46.用尺或样板抽查焊缝及构件的几何尺寸。
47.焊缝的形状偏差及外部应无明显缺陷。
咬边的深度不应超过0.5mm,最长不超过焊缝长度的10%。
不允许烧穿,不允许有裂纹,不允许鳞状波纹高低不一致或太高,不允许有皱纹形成不均匀。
焊缝不均匀偏差Δ=1.5mm。
最大不超过Δ=2mm。
(图6)图6焊缝高度不正确:①平焊凸出偏差0.5~1mm。
②角焊高度不够,偏差4~12±0.5mm。
③不允许有焊缝间断,不允许有漏出弧坑状的缺陷,未焊头未按有关规定执行,不允许有气孔。
④焊缝尺寸不正确K=+1.0mm的偏差。
-0.548.检查人员及操作者的代号标记自定。
(六)静压试验应根据《GB3836.2-2000》15.1.2执行,机械加工及验收一、技术条件及验收49.原材料应符合图纸规定,如不符合时,在保证零件机械性能和使用寿命的条件下可按照的材料代用制度代用。
50.零件的加工表面上,不允许又降低零件精度及寿命的缺陷(如沟痕、碰伤等)。
加工后各部毛刺应除净,切断时留下的余头要削平。
51.在图纸上未注明零件的倒钝或圆角尺寸,加工时一般须有0.2~0.5×45°的倒棱或半径为0.2~0.5毫米的圆角。
52.过度圆角或圆根表面粗糙度,应按与之相连接地两表面中等级较高的粗糙度加工。
53.零件加工后在转移工序、车间或仓库存放的,必须防止其表面碰伤、锈蚀及变形。
54.零件的尺寸未注公差时,其偏差值按GB/T1804-m级。
55.各种螺纹加工其精度等级为6H或6g。
56.隔爆面加工粗糙度不低于,按钮孔的粗糙度不低于。
二、划钻孔、铰孔57.严格按图样要求进行,其钻孔粗糙度不低于,铰孔不低于。
58.出线板上面的孔位置度偏差不大于1mm,必须进行铰孔,达到其技术要求及公差。
59.划钻孔的部位相对偏差为1.5mm。
60.各种法兰框架、盖板划钻孔,相邻两孔偏差不大于0.3mm,多孔最大公差带不大于0.4mm。
61.钻铰孔应垂直,每100mm长度其偏差不大于0.30mm(如图7)。
图762.开门铰链必须采用铰孔配销轴方法,钻铰链轴销孔,焊接前应保证有足够的配钻铰孔余量。
63.加工各种按钮杆应严格按图样要求,其直径超差量均不大于-0.005mm。
64.其他加工件偏差均不低于GB/T1804-C级。
三、隔爆面加工前处理65.壳体焊接完成后,经过48小时的自然冷却后,对其进行内应力振动时效处理,较小壳体处理时间不小于20分钟,较大壳体处理时间不小于30分钟。
如采用回火处理,回火温度应控制在600~650℃,保温时间1小时,保温后以小于2.5~3℃/分的速度缓慢冷却至30℃以下出路或随炉冷却。
消除内应力后,应仔细检查焊缝质量,如发现焊缝有裂纹应进行补焊,在进行相关水压试验检查。
66.抛丸处理应将加工过部位进行保护处理,不得损坏其加工后的隔爆面、螺孔、窗口、出线孔、绝缘座孔等部位。
四、其他部分67.带螺纹联通节无螺纹部分应保证长度在12.5+1mm螺纹精度等级不低于7g级,粗糙度不低于。
68.组合开关扭杆,开关扭杆,开槽对称度偏差不大于0.07mm。
69.按钮套座的孔加工必须铰制达到公差要求,粗糙度不低于,最低不得低于。
70.按钮杆粗糙度不得低于,其几何尺寸满足图样要求。
71.各种卡快加工面粗糙度不得低于。
72.大联通节内孔加工粗糙度不得低于,其公称尺寸+0.40mm。
73.快开门的加工部件必须严格按图样加工,粗糙度及精度不得降低。
拼装、装配及验收一、一般规定74.所有机件(包括外购件),必须经技术检查部门检查合格后,方准装配。
75.应在装配前,操作者必须熟悉装配技术文件及要求,了解其结构、性能和装配数据,周密考虑装配方法和程序。
76.熟悉GB3836.1-2000、GB3836.2-2000中的技术要求。
77.熟悉本标准的各项规定。
二、技术条件78.所有零部件装配前必须将切削、毛刺、油污等杂物清除干净。
79.隔爆面不得有划痕、锈蚀和任何损伤。
必须对隔爆面采取有效保护措施。
80.装配前必须将隔爆面进行防蚀处理,处理时严格按有关规程进行。
81.装配转动部位应涂少量润滑脂。
82.装配弹簧时,不准拉长或切短。
83.装配过程中的机械加工(如钻孔。
铰孔、攻丝等)工序和焊接工序应符合本标准中的有关规定。
84.整机装配应清理干净所有部位的毛刺、焊渣和油污等。
三、紧固件装配(一)螺纹连接85.螺栓螺钉头部或螺母的端面必须与被紧固的零件表面均匀接触,不许用手锤矫正螺栓的歪斜。
86.螺孔攻丝后,中心线对接合面的垂直度极限偏差不大于0.03%。
87.紧固螺钉时,要根据被联接件的形状、螺钉分布情况,对称逐次拧紧。
89.螺栓紧固后漏出螺母的长度应有1~3丝;沉头螺钉拧紧后钉头不得凸出被联接件表面。