试模表格
试模记录单(压铸)

试模费用明细
起始时间 结束时间
试模数 试模节拍:
合格数 S 试模费用
试模状况说明 原因分析 改善措施 结论
试模者
时间
设计者
时间
设计者
时间
模具经理
第一联车间存根
时间
移动模
□机水 □冷水 □热油
斜导柱滑块
□机水 □冷水 □热油
油压抽芯
□机水 □冷水 □热油
分流锥
汤勺角度 待机位置
□机水 □冷水 □热油
浇口套
给汤机调机参数
炉上待机时间
炉中取汤时间
□机水 □冷水 □热油
炉上计量时间 后退待机时间
一段吹气时间 旋转选择
喷雾机调机参数
喷雾时间 上升时间
二段吹气时间 离型剂配比浓度
±10ºC
开模时间 增压时间
压射 压力 射出原点位置
增压压力 铸造压力
低速开度 高速开度
射退开度
高速切点位置
减速位置
增压开度
射退延时时间
射止位置
增压位置
单循环周期
射出延时
订出行程位置
顶出延时
顶回延时
顶出速度
顶出压力
机台编号
机型
料饼厚度
产品毛重
单件净重Biblioteka 模具冷却系统操作者姓名
固定模
□机水 □冷水 □热油
客户名称
xxxx有限公司
压铸试模记录单(冷室机)
产品名称
规格型号
□试模 □生产
产品图号
第 次试模
编号: 版本:A/0
ERP编号
冲头尺寸
定位圈尺寸
模具编号
模穴
冷却水咀尺寸
模具重量
试模报告表格.doc
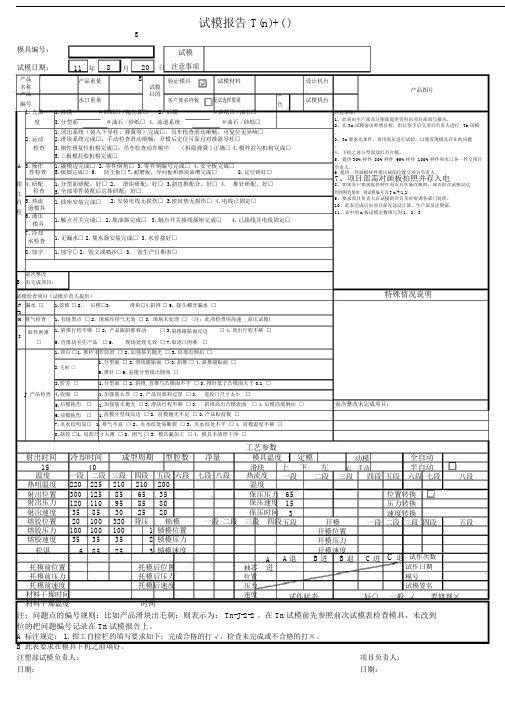
试模报告 T(n)+( )g模具编号:试模试模日期:11 年8月20 日 注意事项产品产品重量g 验证模具试模材料设计机台名称试模产品图片产品目的水口重量复试选样数量颜试模机台编号客户要求样板色1. 光洁1. 前模 #砂纸□ / 抛光膏□2. 后模 #砂纸□ / 油石□注意事项:度 3. 分型面#油石 / 砂纸□ 4. 流道系统#油石 / 砂纸□1、此表由生产部及注塑部提供资料由项目部填写报告。
2、在 Tn 试模前由师傅自检,组长签字后交项目负责人进行 Tn 试模1. 顶出系统(装入下导柱、弹簧等)完成□,吊车检查滑动顺畅,可复位无异响□2. 运动。
2. 滑块系统完成□,手动检查滑动顺畅,开模后定位可靠且对准斜导柱□3、Tn 要求先拿件,再用高压进行试验,以便发现模具存在的问题检查3. 刚性预复位机构完成□;吊车检查动作顺序( 拆除弹簧 ) 正确□ 4. 模外拉勾机构完成□ 。
4、下机之前分型面涂红丹合模。
5. 三板模拉胶机构完成□5、提供 30%样件 ,80%样件 ,95%样件 ,100%样件和水口各一件交项目3. 操作 1. 撬模边完成□ 2. 零件倒角□ 3. 零件刻编号完成□4. 安全板完成□A 负责人。
性检查 5. 模脚完成□ 6. 防尘板□ 7. 耐磨板,导向板和推块油槽完成□ 8. 定位销钉□ 6 提供一件画板样件指出缺陷位置交项目负责人。
钳 4. 研配 1. 分型面研配,好□ 2. 滑块研配,好□ 3. 斜直推配合,好□ 4. 推针研配,好□7、项目部需对画板拍照并存入电8、如果客户要求提供样件而没有实施改模的,或者前次试模没达 工 检查 5. 全部零件装配后总体研配,好□到预期效果的 , 则试模编号为 T(n)+(1,2) 。
5. 热流9、要求项目负责人在试模的次日及时协调各部门处理。
自 1. 插座安装完成□2. 安装电线无损伤□3. 密封垫无损伤□4. 电线已固定□10、此表完成后由项目部发送设计部、生产部及注塑部。
试模记录表

压力 (Kgs)
机 型
速度 (%)
锁模压 力
位置 (mm)
S S
试模时间
储 料 冷 却 参 数
参数
压力
项目
(Kgs)
加料一
加料二
加料松
顶针
先冷却:
s
后冷却:
s
冷却水 前模
开模速 试模人
员 项目人
员
速度 (%)
位置 (mm)
s
射出时限:
s
周 期:
后模
熔胶位置
深圳市仁智塑胶五金制品有限公司
试模记
模具编号
制作人
模架规格
试模数量
啤
试 模 □短射
产 品 □困气
缺 陷 □缺胶 试模结果
所 属 公 司
试模次数
材料
颜色
试模录像 生产全自
动 □高压
□拖花
□高速 □气纹
出模数量 交板时间 □断差
□变形
□粘前 模
□接合 线
产品结构
最短成型周期
试 模 □运水
模 具 □吊模
模具重 水量口单 □码模槽
□批锋 □缩水 □顶高 □尺寸 缺 陷 □行位 □斜顶 □抽蕊
□试模时 料管温度
℃℃
℃
℃
℃
热咀温度
℃℃
℃
℃
℃
模具温度 前模仁_____℃ 后模仁_____℃ 镶件_____℃ 行位_____℃ 斜顶_____℃
射 出 保 压 参 数
参数
项目
射出一段 射出二段 射出三段 射出四段 射出五段 保压一段 保压二段
试模报告表格

J 产品检查 4.收缩 □
1.加强筋太厚 □ 2.产品局部料过厚 □ 3.进胶口尺寸太小 □
5.后模拖伤 □ 1.加强筋未抛光 □ 2.滑块行程不够 □ 3.斜推高出凸模表面 □ 4.后模局部倒扣 □ 前
6.前模拖伤 □ 1.前模分型线反边 □ 2.前模抛光不足 □ 3.产品贴前模 □
次
7.夹水纹明显 □
3.斜推碰贴面反边 □ 4.顶出行程不够 □ 7.取浇口困难 □
1.顶白 □
1.推杆未作防滑 □ 2.加强筋未抛光 □ 3.局部有倒扣 □
2.毛刺 □
1.分型面 □ 2.滑块碰贴面 □ 3.斜推 □ 4.斜推碰贴面 □ 5.推针 □ 6.前模分型线出圆角 □
3.阶差 □
1.分型面 □ 2.斜推,直推与凸模面不平 □ 3.推针低于凸模面大于0.1 □
1.排气不良 □
2.夹水纹处易断裂 □
3.夹水纹处不平 □
4.前模温度不够 □
8.缺胶 □
1.局部尺寸太薄 □ 2.困气 □ 3.模具漏加工 □ 4.模具未清理干净 □
工艺参数
射出时间 15 温度
热咀温度 射出位置 射出压力 射出速度 熔胶位置 熔胶压力 熔胶速度
松退 托模前位置 托模前压力 托模前速度 材料干燥时 材料干燥温
冷却时间 成型周期 型腔数 净量
模具温度 定模
动模
40
滑块 上 下 左 右 手动
一 二段 三段 四段 五段 六段 七段 八段 热流度 一段 二段 三段 四段
220 225 210 210 200
温度
300 125 85 65 35
保压压力 65
120 110 95 85 80
保压速度 15
35 85 30 25 20
试模单

试模材料
试模日期
压铸机机型
□250T□280T□400T□630T
料管形式
□整体□分体
锤头直径
□50□60□70□80□90
抽芯形式
□无抽芯□斜导柱□油缸
冷却水
□动模□定模□分流锥□浇口套
倒拉杆
□有□无
快压行程cm
参考值
冷却时间s
参考值
增压压力Mpa
参考值
实际值
实际值
实际值
快压开度(或速度)
产品图号
模具图号
模具制作方
申请人
申请日期
模具类别
□新模□备模
第次试模
试模原因
□新模□上次失败□修改□送样
A部分——模具检查表
项目
内容
检查结果
1
模芯、分流锥、浇口套比模框面高0.05-0.15mm
2
顶针面与型腔面配平或高0.1-0.15mm,顶针端面是曲面的必须做防转定位
3
型芯台阶面高出型腔面0.05-0.1mm
参考值
增压开度
参考值
铝液温度
参考值
实际值
实际值
实际值
试模反馈:
□飞铝□拉伤□冲浇口□滑块窜铝□型芯断□粘动定模□冷却水不通
□型腔损坏□抽芯损坏□型芯断□错模严重□顶针问题□产品变形或拉断
试模总结:
试制工程师/日期
模具设计工程师/日期
4
滑块间隙合理,滑动顺畅,无歪斜卡滞现象
5
抽芯油缸附件检查,包括撞块、行程开关,接合模后滑块与锁紧块配合面贴合紧密
7
顶板顶出和回退顺畅,无歪斜卡滞异响现象
8
上次模具修改项(模具设计工程师或试制工程师手工填写)
试模校准记录表

压碎值指标测定仪校准记录表(150)校准:校核:日期:校准:校核:日期:水泥胶砂流动度试模校准记录表(152)校准:校核:日期:混凝土/砂浆的立方体/棱柱体试模校准记录表(153/154)校准:校核:日期:水泥胶砂试模校准记录表(157-160)校准:校核:日期:混凝土/砂浆的立方体/棱柱体试模校准记录表(161)校准:校核:日期:校准:校核:日期:校准:校核:日期:混凝土/砂浆的立方体/棱柱体试模校准记录表(166-167)校准:校核:日期:混凝土/砂浆抗渗试模校准记录表(168)校准:校核:日期:混凝土/砂浆的立方体/棱柱体试模校准记录表(169/170)校准:校核:日期:混凝土/砂浆的立方体/棱柱体试模校准记录表(171-172)校准:校核:日期:混凝土/砂浆的立方体/棱柱体试模校准记录表(173/175)校准:校核:日期:混凝土/砂浆的立方体/棱柱体试模校准记录表(176-177)校准:校核:日期:混凝土/砂浆的立方体/棱柱体试模校准记录表(178)校准:校核:日期:混凝土/砂浆的立方体/棱柱体试模校准记录表(179/186)校准:校核:日期:混凝土/砂浆的立方体/棱柱体试模校准记录表(187)校准:校核:日期:混凝土/砂浆的立方体/棱柱体试模校准记录表(188-189)校准:校核:日期:混凝土/砂浆的立方体/棱柱体试模校准记录表(190-191)混凝土/砂浆的立方体/棱柱体试模校准记录表(192)混凝土/砂浆圆柱体试模校准记录表(193-194)校准:校核:日期:混凝土/砂浆抗渗试模校准记录表(195)。
五金模具试模记录表

执行
试模、试装安排:(先确认图纸或样品)
计划安排完成时间:月日时
执行部门领导签字:
年月日
五金模具试模具问题记录表
编号:
产品型号、名称
零部件名称、图号
工装名称
工装编号
类型
□塑料模□冲压模 □工装夹具 □其他
试模设备名称
试模设备型号
试模日期
试模状况
工装模具情况:
*工装模具结构合理性: □合理□一般 □不合理
工 装 试 模 通 知 单
编号:
产品ቤተ መጻሕፍቲ ባይዱ号、名称
零部件名称、图号
工装模具名称
工装模具编号
通知
类型
①存根②试模部门
□塑料模□冲压模 □工装夹具 □其他
设
备
名称
材料/零件/产品
名称
其它
规格
规格/图号
要求完成时间
月日时
第几次试模、试装
第□1,□2,□3,□4,□5 次试模
试模、试装数量
申请人签字
试模、试装车间
毛刺、飞边情况: □无毛刺飞边 □少量的□严重
有无影响产品装配的毛刺、飞边: □无□少量,可接受□严重,不可用
问题记录:
改善建议;
试模单位
试模人员
*工装模具可操作性: □好□一般 □需改进
*工装模具安全性: □好□需警示标志 □危险
*工装模具实用性: □好□一般 □需改进
*工装模具完整性: □完整□不完整
*工装模具外观质量:□好□一般 □需改进
*加工精度是否达到要求: □是□小部分不符 □大部分不符
*按要求做热处理及其他表面处理:□是□小部分不符 □大部分不符
压铸试模记录表

产品名称:模具编号:适用设备:模具负责人: K3号:模穴:试模设备:项目负责人:产品材料:安装预复位安装油泵压室直径∮80项目理论值实际值项目理论值实际值项目理论值实际值项目实际值压射比压/Mpa 40MPa 低速开度/转0.2铸造温度/℃670顶回时间/s 压射力/T315KN 高速起点位置设定温度/℃670勺在炉时/s 压射缸表压/Mpa高速行程机械油温/℃/臂退等时/s ACC压力/Mpa 80bar 高速开度/转模具温度/℃200-300动喷脱时/s ACC降量/Mpa <1增压开度/转循环时间/s 定喷脱时/s高压压力/Mpa 80-100bar 增压储能器充油压力/Mpa原料比率/%7:3吹气时间/s料柄厚度/mm15冷却时间/s脱模剂型号冲头油/颗粒油类别结论1.模具外形长2.油缸拆装是3.模具吊装是4.法兰配合是5.压板槽位置6.水管油管安7.油缸抽拉运8.滑块拔出距9.导柱导套运10.顶板导柱导11.顶杆运行是12.压机拉杆和13.机械手取件14.料缸活塞运15.是否粘模?16.是否飞铝?18.滑块拔出后19.模芯是否有20.产品合格率21.每模成型周17.有没有固定位置的固定缺陷?(如:裂纹、穿透性冷隔、欠铸、表面气孔等) XX机械有限公司意见、建议(问题描述)项目ADC122基本信息产品重量:快压射件数:成品件数:成型慢压射件数:试模件数:运行试 模 记 录 试模时间: 第 次试模试模过程检查项目安装产品检测及模具安装要求:外表无明显冷隔缺陷项目负责人签字:主管签字:增压件数:提交顾客:保留 模,其余回炉剩余 件移交工程压机工艺参数编制:流道+料饼重量:试模组长签字:样件数量、重量信息渣包+排气重量:总重量:是否是否。
试模报告表格

1.触点开关完成□ 2.集油器完成□ 3.触点开关接线插座完成□ 4.已接线并电线固定□
1.无漏水□ 2.集水器安装完成□ 3.水管接好□
8.蚀字 1.蚀字□ 2.蚀文或喷沙□ 3.蚀生产日期表□
B
前次整改 未完成项目:
试模检查项目(试模负责人提供)
F -3
漏水
□
1.前模 □ 2.后模 □ 3.滑块 □
注意事项: 1、此表由生产部及注塑部提供资料由项目部填写报告。 2、在Tn试模前由师傅自检,组长签字后交项目负责人进行Tn试模 。 3、Tn要求先拿件,再用高压进行试验,以便发现模具存在的问题 。 4、下机之前分型面涂红丹合模。 5、提供30%样件,80%样件,95%样件,100%样件和水口各一件交项目 负责人。 6、提供一件画板样件指出缺陷位置交项目负责人。 7、项目部需对画板拍照并存入电子档案。 8、如果客户要求提供样件而没有实施改模的,或者前次试模没达 到预期效果的,则试模编号为T(n)+(1,2……)。 9、要求项目负责人在试模的次日及时协调各部门处理。 10、此表完成后由项目部发送设计部、生产部及注塑部。 11、表中的n按试模次数填写为1,2,3……
8.缺胶 □
1.局部尺寸太薄 □ 2.困气 □ 3.模具漏加工 □ 4.模具未清理干净 □
工艺参数
射出时间 冷却时间 成型周期 型腔数 净量
模具温度 定模
动模
全自动
15
40
滑块
温度 一段 二段 三段 四段 五段 六段 七段 八段 热流度
热咀温度 220 225 210 210 200
温度
上 下 左 右 手动
半自动
一段 二段 三段 四段 五段 六段 七段
八段
砼试模自校表格

0.00、0.00、0.00、0.00、0.02
90.02、89.94、90.00、90.02、90.00、90.02、89.94、90.00
符合要求
3平整、光滑ຫໍສະໝຸດ 150×150×150150.00、150.02、149.96、150.04、149.74
90.02、90.14、90.00、90.00、90.00、90.00、89.92、90.10
符合要求
5
平整、光滑
150×150×150
150.00、150.02、150.00、149.98、150.06
0.00、0.02、0.01、0.00、0.00
90.06、90.00、90.10、90.04、9004、90.10、90.00、90.02
90.10、90.12、90.06、89.96、90.04、90.00、90.00、90.02
符合要求
校验结论:依据《工程试验仪器校验检验方法》校验方法,该混凝土试模合格。
校验员:复核人:
校验日期:下次校验日期:
校验用标准器具名称:钢直尺、塞尺、游标卡尺、万能角度尺
环境条件:温度19℃相对湿度60%
符合要求
6
平整、光滑
150×150×150
149.92、150.00、150.02、150.06、150.00
0.01、0.00、0.02、0.00、0.00
90.02、90.06、90.00、90.08、90.16、90.04、90.00、89.92
符合要求
7
平整、光滑
150×150×150
150.04、149.96、150.00、150.02、150.00
- 1、下载文档前请自行甄别文档内容的完整性,平台不提供额外的编辑、内容补充、找答案等附加服务。
- 2、"仅部分预览"的文档,不可在线预览部分如存在完整性等问题,可反馈申请退款(可完整预览的文档不适用该条件!)。
- 3、如文档侵犯您的权益,请联系客服反馈,我们会尽快为您处理(人工客服工作时间:9:00-18:30)。
前次整改未完成项目: 5.后模拖伤 □ 1.加强筋未抛光 □ 2.滑块行程不够 □ 3.斜推高出凸模表面 □ 4.后模局部倒扣 □ 前次整改未完成项目:
6.前模拖伤 □ 1.前模分型线反边 □
7.夹水纹明显□ 1.排气不良 □ 夹水纹明显□
2.夹水纹处易断裂 □
8.缺胶 □
1.局部尺寸太薄 □
工艺参数 射出时间 冷却时间 成型周期
颜 色
设计机台
产品图片
试模机台
注意事项: 注意事项: 此表由生产部及注塑部提供资料由项目部填写报告。 1、此表由生产部及注塑部提供资料由项目部填写报告。 Tn试模前由师傅自检 组长签字后交项目负责人进行Tn 试模前由师傅自检, Tn试模 2、在Tn试模前由师傅自检,组长签字后交项目负责人进行Tn试模 。 Tn要求先拿件 再用高压进行试验, 要求先拿件, 3、Tn要求先拿件,再用高压进行试验,以便发现模具存在的问题 。 下机之前分型面涂红丹合模。 4、下机之前分型面涂红丹合模。 提供30 样件,80%样件,95%样件,100% 30% 5、提供30%样件,80%样件,95%样件,100%样件和水口各一件交项目 负责人。 负责人。 提供一件画板样件指出缺陷位置交项目负责人。 6、提供一件画板样件指出缺陷位置交项目负责人。 项目部需对画板拍照并存入电子档案。 7、项目部需对画板拍照并存入电子档案。 如果客户要求提供样件而没有实施改模的, 8、如果客户要求提供样件而没有实施改模的,或者前次试模没达 到预期效果的,则试模编号为T )+(1 ……) 到预期效果的,则试模编号为T(n)+(1,2……)。 9、要求项目负责人在试模的次日及时协调各部门处理。 要求项目负责人在试模的次日及时协调各部门处理。 10、此表完成后由项目部发送设计部、生产部及注塑部。 10、此表完成后由项目部发送设计部、生产部及注塑部。 11、表中的n按试模次数填写为1 11、表中的n按试模次数填写为1,2,3……
创维精密科技有限公司
试模报告T 试模报告T(n)+( ) 模具编号: 模具编号: 试模日期: 试模日期:
产品 名称 产品 编号 1.光洁 度
试模 11 年
产品重量 水口重量
8
月
20 日 注意事项 g
试模 目的 验证模具
客户要求样板
NO:SKY-PM-003-FM002/AO
试模材料 复选框 试样数量
砂纸□ 抛光膏□ 砂纸□ 油石□ 1.前模 #砂纸□/抛光膏□ 2.后模 #砂纸□/油石□ 油石/砂纸□ 油石/砂纸□ 3.分型面 #油石/砂纸□ 4.流道系统 #油石/砂纸□ 顶出系统(装入下导柱、弹簧等)完成□ 吊车检查滑动顺畅,可复位无异响□ 1.顶出系统(装入下导柱、弹簧等)完成□,吊车检查滑动顺畅,可复位无异响□ 2.运动 2.滑块系统完成□,手动检查滑动顺畅,开模后定位可靠且对准斜导柱□ 滑块系统完成□ 手动检查滑动顺畅,开模后定位可靠且对准斜导柱□ 检查 3.刚性预复位机构完成□;吊车检查动作顺序(拆除弹簧)正确□ 4.模外拉勾机构完成□ 刚性预复位机构完成□ 吊车检查动作顺序(拆除弹簧)正确□ 模外拉勾机构完成□ 三板模拉胶机构完成□ 5.三板模拉胶机构完成□ 撬模边完成□ 零件倒角□ 零件刻编号完成□ 安全板完成□ 3.操作 1.撬模边完成□ 2.零件倒角□ 3.零件刻编号完成□ 4.安全板完成□ A 模脚完成□ 防尘板□ 耐磨板,导向板和推块油槽完成□ 定位销钉□ 性检查 5.模脚完成□ 6.防尘板□ 7.耐磨板,导向板和推块油槽完成□ 8.定位销钉□ 分型面研配, 滑块研配, 斜直推配合, 推针研配, 4.研配 1.分型面研配,好□ 2.滑块研配,好□ 3.斜直推配合,好□ 4.推针研配,好□ 钳 检查 5.全部零件装配后总体研配,好□ 全部零件装配后总体研配, 工 5.热流 自 插座安装完成□ 安装电线无损伤□ 密封垫无损伤□ 电线已固定□ 1.插座安装完成□ 2.安装电线无损伤□ 3.密封垫无损伤□ 4.电线已固定□ 检 道模具 6.液压 触点开关完成□ 集油器完成□ 触点开关接线插座完成□ 已接线并电线固定□ 1.触点开关完成□ 2.集油器完成□ 3.触点开关接线插座完成□ 4.已接线并电线固定□ 模具 7.冷却 无漏水□ 集水器安装完成□ 水管接好□ 1.无漏水□ 2.集水器安装完成□ 3.水管接好□ 水检查 8.蚀字 蚀文或喷沙□ 蚀生产日期表□ 1.蚀字□ 2.蚀文或喷沙□ 3.蚀生产日期表□ 蚀字□
前次整改
特殊情况说明
1.推杆未作防滑 □ 2.加强筋未抛光 □ 3.局部有倒扣 □ 1.分型面 □ 2.滑块碰贴面 □ 3.斜推 □ 4.斜推碰贴面 □ 5.推针 □ 6.前模分型线出圆角 □ 斜推, 推针低于凸模面大于0 1.分型面 □ 2.斜推,直推与凸模面不平 □ 3.推针低于凸模面大于0.1 □ 1.加强筋太厚 □ 2.产品局部料过厚 □ 3.进胶口尺寸太小 □ 2.前模抛光不足 □ 3.产品贴前模 □ 3.夹水纹处不平 □ 4.前模温度不够 □ 2.困气 □ 3.模具漏加工 □ 4.模具未清理干净 □
B 未完成项目: 未完成项目:
试模检查项目(试模负责人提供) 试模检查项目( 试模负责人提供) F 漏水 □ 1.前模 □ 2.后模 □ 3.滑块 □ 4.斜推 □ 5.接头螺牙漏水 □ -3 此项检查用高速,高压试模) H 排气检查 1.有烧黑点 □ 2.现场作排气无效 □ 3.现场未处理 □ (注:此项检查用高速,高压试模) I 取件困难 1.斜推行程不够 □ 2.产品跟斜推移动 □ □ 5.直推块夹住产品 □ 6.现场处理无效 □ 1.顶白 □ 2.毛刺 □ 3.阶差 □ J 产品检查 4.收缩 □ 3.斜推碰贴面反边 □ 4.顶出行程不够 □ 7.取浇口困难 □
标注规定: 钳工自检栏的填写要求如下:完成合格的打√ 检查未完成或不合格的打× A 标注规定:1.钳工自检栏的填写要求如下:完成合格的打√,检查未完成或不合格的打×。 此表要求在模具下机之前填好。 B 此表要求在模具下机之前填好。 注塑部试模负责人: 项目负责人: 注塑部试模负责人: 项目负责人: 日期: 日期: 日期: 日期:
型腔数
净量
全自动 半自动
五段 六段 七段 位置转换 压力转换 速度转换 二段 三段 四段 八段
五段
C退 试作次数 试作日期 模号 试模签名 要修理× 一般 √ 要修理×
问题点的编号规则:比如产品滑块出毛刺:则表示为:TnTn试模前先参照前次试模表检查模具 试模前先参照前次试模表检查模具, 注:问题点的编号规则:比如产品滑块出毛刺:则表示为:Tn-J-2-2。在Tn试模前先参照前次试模表检查模具,未改到 位的把问题编号记录在Tn试模报告上。 位的把问题编号记录在Tn试模报告上。 Tn试模报告上
三段 210 85 95 30 320 100 35 25 15 40 温度 一段 二段 220 225 热咀温度 300 125 射出位置 120 110 射出压力 35 85 射出速度 20 100 熔胶位置 100 100 熔胶压力 35 35 熔胶速度 6 85 松退 托模前位置 托模前压力 托模前速度 材料干燥时间 材料干燥温度 模具温度 动模 定模 滑块 上 下 左 右 手动 四段 五段 六段 七段 八段 热流度 一段 二段 三段 四段 210 200 温度 65 35 65 保压压力 85 80 15 保压速度 20 3 25 保压时间 背压 锁模 一段 二段 三段 四段 五段 开模 一段 开模位置 1 锁模位置 开模压力 2 锁模压力 开模速度 3 锁模速度 托模后位置 抽芯 A进 A退 进 B进 B退 C进 托模后压力 位置 托模后速度 压力 速度 时间 试作状态 好○