合成氨工艺单元安全技术要求
氨合成过程安全技术要求

氨合成过程安全技术要求1氮氢气压缩安全技术1.1压缩机应设置一段入口压力低限报警装置和罗茨机、压缩机停车联锁装置;各段温度、入口分离器液位、压力应设置报警联锁;氮氢压缩机振动高限跳车联锁;压缩机温度、压力、入口分离器液位与供电系统应形成联锁关系。
1.2压缩机去变换、脱硫、“双甲”、合成各工序的工艺管道上,宜设置紧急切断阀。
1.3压缩机各段出口管道上应安装安全阀,安全阀出口导气管应接出室外;放空管应设置阻火器,高度应高于周边20m范围内操作平台3.5m以上;安全阀应定期校验,确保灵敏可靠。
1.4压缩机总集油槽上回气阀应保持常开,严禁超压。
1.5压力、温度、电流、电压、报警等仪表控制装置应定期校验,保证灵敏、准确、可靠。
1.6压缩机启动应先盘车,禁止使用吊车进行盘车,禁止带负荷启动。
1.7压缩机气缸水夹套用冷却水应设置冷却水压力低报警及联锁停车,或气缸水管出入口设置流量指示。
若气缸水夹套断水时,禁止立即补加冷却水,应停车自然冷却后,再进行处理。
1.8严格控制润滑油的油位及加油量,确保压缩机各部件供油正常。
齿轮油泵油压不能低于指标规定值,应设置油泵油压与压缩机运行联锁装置,严防注油器油管倒气。
1.9更换压缩机气缸活门,应确认压力卸尽、置换合格、隔离彻底,并挂牌标识后方可作业。
更换过程中要采取强制通风,不得撞击,严防煤气中毒及发生着火和爆燃事故。
1.10压缩机排油水阀宜设置双阀,排油水时,严禁过猛过快,防止大量窜气。
禁止数台压缩机同时排油水,以防进口总管压力波动及总集油槽超压发生事故。
1.11压缩机开停机、倒机过程中,升压或卸压必须缓慢,各段压力要平稳,防止气体倒流、高压气窜入低压系统、外工序的溶液水倒入压缩机发生事故。
1.12压缩机开机或倒车时,要认真检查相关的各个段间近路阀是否关严,不能内漏,以确保“双甲”和合成工序的正常操作。
1.13压缩机空气试压或试车,应遵守下列要求:——与正在生产系统用盲板隔绝,压缩机系统内可燃气置换彻底,各段出口压力、温度均不得超过规定指标;——已经投入运行的煤气压缩机不宜采用空气加压试车;若使用空气试车,需要将各段分离器、冷却器内油污置换彻底,并严密监视控制压缩比和各段出口温度;——如采用静电除焦设备,必须设置半水煤气氧气自动分析仪,且与静电除焦控制柜联锁,氧含量≥0.8%时电路应自动断开;——试车前应先盘车,并按同步电机、无负荷、负荷试车顺序进行。
(工艺技术)合成氨工艺简介

合成氨工艺控制方案总结一合成氨工艺简介中小型氮肥厂是以煤为主要原料,采用固定层间歇气化法制造合成氨原料气。
从原料气的制备、净化到氨的合成,经过造气、脱硫、变换、碳化、压缩、精炼、合成等工段。
工艺流程简图如下所示:该装置主要的控制回路有:(1)洗涤塔液位;(2)洗涤气流量;(3)合成塔触媒温度;(4)中置锅炉液位;(5)中置锅炉压力;(6)冷凝塔液位;(7)分离器液位;(8)蒸发器液位。
其中触媒温度控制可采用全系数法自适应控制,其他回路采用PID控制。
二主要控制方案(一)造气工段控制工艺简介:固定床间歇气化法生产水煤气过程是以无烟煤为原料,周期循环操作,在每一循环时间里具体分为五个阶段;(1)吹风阶段约37s;(2)上吹阶段约39s;(3)下吹阶段约56s;(4)二上吹阶段约12s;(5)吹净阶段约6s.l、吹风阶段此阶段是为了提高炉温为制气作准备的。
这一阶段时间的长短决定炉温的高低,时间过长,炉温过高;时间过短,炉温偏低并且都影响发气量,炉温主要由这一阶段控制。
般工艺要求此阶段的操作时间约为整个循环周期的18%左右。
2、上吹加氮制气阶段在此阶段是将水蒸汽和空气同时加入。
空气的加入增加了气体中的氮气含量,是调节H2/N2的主要手段。
但是为了保证造气炉的安全该段时间最多不超过整个循环周期的26%。
3、上吹制气阶段该阶段与上吹加氯制气总时间为整个循环的32%,随着上吹制气的进行下部炉温逐渐下降,为了保证炉况和提高发气量,在此阶段蒸汽的流量最好能得以控制。
4、下吹制气阶段为了充分地利用炉顶部高温、提高发气量,下吹制气也是很重要的一个阶段。
这段时间约占整个循环的40%左右。
5、二次上吹阶段为了确保生产安全,造气炉再度进行吹风升温之前,须把下吹制气时留在炉底及下部管道中的半水煤气吹净以防不测,故进行第二次上映。
这段时间约占7%左右。
6、吹净阶段这段时间主要是回收上行煤气管线及设备内的半水煤气。
约占整个循环的3%。
胺基化培训——胺基化工艺和设备安全技术
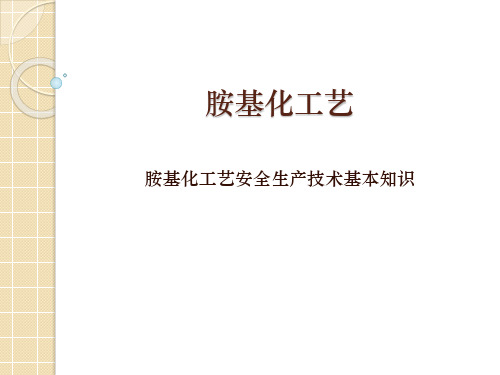
(4)按安全技术管理分类
上面所述的几种分类方法仅仅考虑了压力容器的某个设计参数或使用状 况,未能综合反映压力容器的危险程度。“原容规”综合考虑多种因素,将 压力容器分为第一类压力容器、第二类压力容器和第三类压力容器。
(5)按制造许可分类 根据制造能力、工艺水平、人员条件等,国家质量监督检验检疫总局令(第
工艺指标 甲醇预热后温度 蒸发过热器气化室温度 过热器出口原料气温度 原料气进合成塔前温度 合成塔反应热点温度 合成塔出口温度 蒸发器 a 合成气入口温度 粗胺槽温度 合成氨冷放空气温度
温度/℃
115 170 360
400 400(参考)
≤230 50 ≤10
工艺指标:压力
工艺指标
压力/MPa
蒸发器 b 加热蒸汽压力(阀前压力)
吸收液中的总胺≤11%
三、相关胺基化工艺联锁保护系统工作条件
警报和联 锁
传感 器位 号
传感器位 置
警报和联 锁设定值
目的/功能
警报
合成塔 3.0MPa
防止合成塔超压
警报和联锁启动后 应采取的措施
及时控制合成流量、 开大合成减压阀,联 系现场班长开大减 压阀阀门
警报
回流槽 >20%
防止回流槽的液 及时减少或增大回
脱水塔不同工艺阶段的组成成分及含量
组成成分
氨
甲醇 MMA DMA TMA H2O
Ⅲ塔
顶出/% 0.03 0.12
54.19 0.18 0.03
釜排/%
0.37 0.01
/
0.04 88.59
4.一甲胺与二甲胺分离 原理:Ⅳ塔利用一甲胺比二甲胺容易挥发的特点,Ⅲ塔顶馏出
合成氨生产贮存安全技术措施探讨
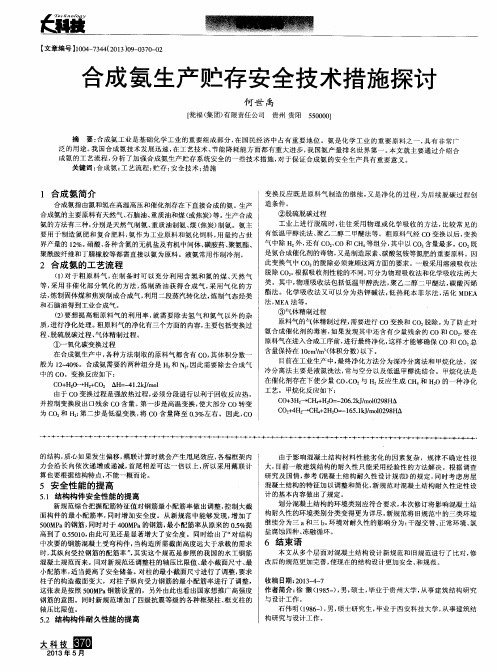
泛 的用 途 。 我国合成氨技术发展迅速 , 在工艺技术、 节 能 降耗 能 方 面 都 有 重 大 进 步 , 我 国氨 产 量 排 名 世 界 第 一 。 本 文 就 主 要 通 过 介 绍 合 成 氨 的工 艺 流程 , 分 析 了加 强 合 成 氨 生产 贮 存 系 统 安 全 的一 些 技 术 措 施 , 对 于 保 证 合 成 氨 的 安全 生 产 具 有 重 要 意 义 。 关键 词 : 合成氨 ; 工艺流程 ; 贮存 ; 安全技术; 措 施
法, ME A法等。
③气体精制过程 原料气的气体精制过程, 需要进行 C O变换和 C O 脱除。 为了防止对 氨合成催 化剂 的毒害, 如 果发现其 中还含有少量残余 的 C O和 C O , , 要在
原料气在进入合成工序 前, 进行最终净化, 这样才能够确保 C O和 C O , 总 ①一氧化碳变换过程 含量保持在 1 0 c mZ / m , ( 体积分数) 以下。 在合成氨生产 中, 各种方法制取的原料气都含有 C O , 其体积分数一 目前在工业生产 中, 最终净化方法分为深冷分离法和甲烷 化法。深 般为 1 2 - 4 0 %。合成氨需要的两种组分是 H 和N , 因此需要除去合成气 冷分离法 主要 是液氮洗法 , 常与 空分 以及低温 甲醇洗结合。 甲烷化法是
2 合成 氨 的工艺流 程
( 1 ) 对于粗 原料气 , 在制备 时可 以充 分利用含 氢和氮 的煤 、 天 然气 等, 采用 非催化部 分氧化的方法 , 炼制渣 油获得合 成气 , 采用气化 的方 法, 炼制固体煤和焦炭制成合成气 , 利用二段蒸汽转化法 , 炼制气态烃类 和 石 脑 油 得到 工 业 合 成 气 。 ( 2 ) 要想提高粗原料气 的利 用率, 就需要除去氢 气和氮气 以外 的杂 质, 进行净化 处理 。 粗原料气的净化有三个方面的 内容, 主要包括变换过 程、 脱硫脱碳过程 、 气体精制过程 。
合成氨生产操作安全技术
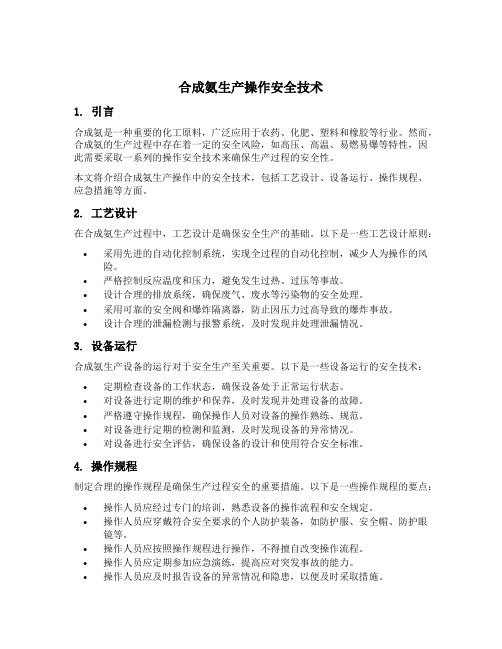
合成氨生产操作安全技术1. 引言合成氨是一种重要的化工原料,广泛应用于农药、化肥、塑料和橡胶等行业。
然而,合成氨的生产过程中存在着一定的安全风险,如高压、高温、易燃易爆等特性,因此需要采取一系列的操作安全技术来确保生产过程的安全性。
本文将介绍合成氨生产操作中的安全技术,包括工艺设计、设备运行、操作规程、应急措施等方面。
2. 工艺设计在合成氨生产过程中,工艺设计是确保安全生产的基础。
以下是一些工艺设计原则:•采用先进的自动化控制系统,实现全过程的自动化控制,减少人为操作的风险。
•严格控制反应温度和压力,避免发生过热、过压等事故。
•设计合理的排放系统,确保废气、废水等污染物的安全处理。
•采用可靠的安全阀和爆炸隔离器,防止因压力过高导致的爆炸事故。
•设计合理的泄漏检测与报警系统,及时发现并处理泄漏情况。
3. 设备运行合成氨生产设备的运行对于安全生产至关重要。
以下是一些设备运行的安全技术:•定期检查设备的工作状态,确保设备处于正常运行状态。
•对设备进行定期的维护和保养,及时发现并处理设备的故障。
•严格遵守操作规程,确保操作人员对设备的操作熟练、规范。
•对设备进行定期的检测和监测,及时发现设备的异常情况。
•对设备进行安全评估,确保设备的设计和使用符合安全标准。
4. 操作规程制定合理的操作规程是确保生产过程安全的重要措施。
以下是一些操作规程的要点:•操作人员应经过专门的培训,熟悉设备的操作流程和安全规定。
•操作人员应穿戴符合安全要求的个人防护装备,如防护服、安全帽、防护眼镜等。
•操作人员应按照操作规程进行操作,不得擅自改变操作流程。
•操作人员应定期参加应急演练,提高应对突发事故的能力。
•操作人员应及时报告设备的异常情况和隐患,以便及时采取措施。
5. 应急措施合成氨生产过程中,突发事故的发生是无法完全避免的,因此需要制定合理的应急措施。
以下是一些应急措施的要点:•设立应急预案,明确各种突发事故的处理流程和责任分工。
合成氨生产安全技术
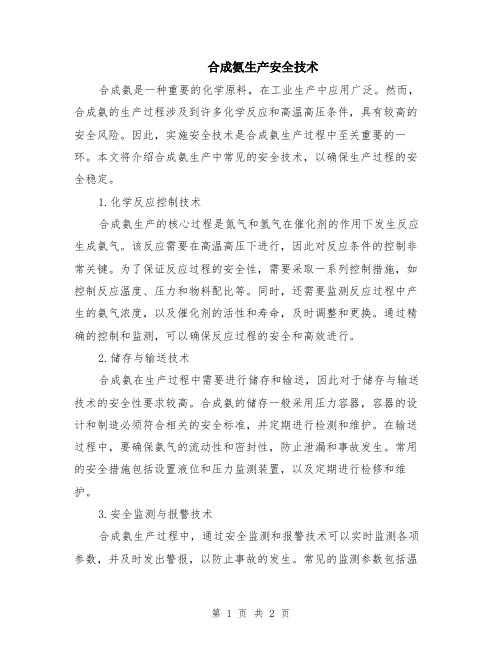
合成氨生产安全技术合成氨是一种重要的化学原料,在工业生产中应用广泛。
然而,合成氨的生产过程涉及到许多化学反应和高温高压条件,具有较高的安全风险。
因此,实施安全技术是合成氨生产过程中至关重要的一环。
本文将介绍合成氨生产中常见的安全技术,以确保生产过程的安全稳定。
1.化学反应控制技术合成氨生产的核心过程是氮气和氢气在催化剂的作用下发生反应生成氨气。
该反应需要在高温高压下进行,因此对反应条件的控制非常关键。
为了保证反应过程的安全性,需要采取一系列控制措施,如控制反应温度、压力和物料配比等。
同时,还需要监测反应过程中产生的氨气浓度,以及催化剂的活性和寿命,及时调整和更换。
通过精确的控制和监测,可以确保反应过程的安全和高效进行。
2.储存与输送技术合成氨在生产过程中需要进行储存和输送,因此对于储存与输送技术的安全性要求较高。
合成氨的储存一般采用压力容器,容器的设计和制造必须符合相关的安全标准,并定期进行检测和维护。
在输送过程中,要确保氨气的流动性和密封性,防止泄漏和事故发生。
常用的安全措施包括设置液位和压力监测装置,以及定期进行检修和维护。
3.安全监测与报警技术合成氨生产过程中,通过安全监测和报警技术可以实时监测各项参数,并及时发出警报,以防止事故的发生。
常见的监测参数包括温度、压力、液位、气体浓度等。
通过设置安全监测仪表和自动报警系统,可以实现对关键参数的监测和报警,及时采取措施避免危险。
4.应急处理技术即使在严格控制和监测的情况下,合成氨生产过程中仍然可能发生事故。
因此,应急处理技术对于确保生产过程的安全至关重要。
在应急处理中,首先要迅速切断事故发生环节,关闭阀门、切断电源等,以停止事故的扩大。
同时,要组织人员撤离危险现场,并进行相应的紧急救援和处理。
合成氨生产企业应制定详细的应急预案,并进行定期演练,以确保人员的安全。
总而言之,合成氨生产过程中需要采取一系列的安全技术措施,以确保生产过程的安全稳定。
化学反应控制技术、储存与输送技术、安全监测与报警技术以及应急处理技术都是非常重要的一环。
化工安全 合成氨
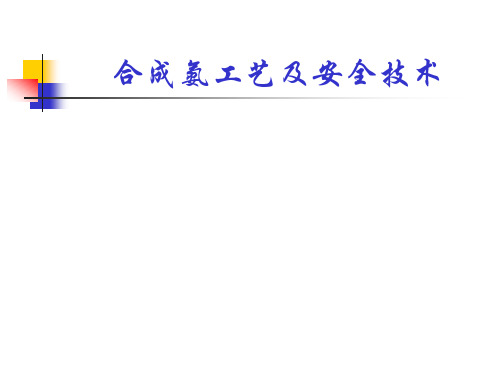
(13-9)
2
氨合成动力学
氢氮混合气在铁催化剂表面上发生的反应大体包括下列几步: 气体向催化剂表面(外表面和内表面)扩散。 气体向催化剂表面(外表面和内表面)扩散。 气体在催化剂表面发生活性吸附。 气体在催化剂表面发生活性吸附。 N2(气) 2N(吸附) H2(气) 2H(吸附) 吸附的氮和吸附的氢发生反应生成氨 N(吸附) + H(吸附) NH(吸附) NH(吸附) + H(吸附) NH2(吸附) NH2(吸附)+ H(吸附) NH3(吸附) 生成的氨从催化剂表面解吸 NH3(吸附) NH3 (气) 从催化剂表面向气体主流扩散。 解吸的氨 从催化剂表面向气体主流扩散。
表2—7 7 压强/MPa 400 温度/ ℃ 500 0.1 52.7 54.0 氨合成反应的热效应( 氨合成反应的热效应(-∆H⊝/KJ.mol-1) 10.1 53.8 54.7 20.2 55.3 55.6 30.4 56.8 56.5 40.5 58.2 57.6
(2) 化学平衡及平衡常数
四、氮的固定: 氮的固定: 把大气中的氮转化为氮的化合物叫做氮的固定。 把大气中的氮转化为氮的化合物叫做氮的固定。 包括: 包括: 自然固定:豆科植物固氮、雷雨天产生NO气体; NO气体 ① 自然固定:豆科植物固氮、雷雨天产生NO气体; 人工固定:合成氨等。 ② 人工固定:合成氨等。
一 概 述
1、合成氨的重要性 、 氨的合成使人类从自然界制取含氮化合物的最重要方法。 氮则是进一步合成含氮化合物的最重要原料,而含氮化合物在 人民生活中都是必不可少的。1977~1978年,世界含氮化合物 产量为4935万吨氮,1980~1981则达6284万吨。
x=0.70
-rA
x=0.80 x=0.90
2024年特殊动火作业的安全技术要求(2篇)

2024年特殊动火作业的安全技术要求化工企业生产的显著特点是易燃、易爆、易中毒、易腐蚀、生产连续性强。
在生产和检修过程中,一旦发生泄漏,必须立即进行设备的补焊堵漏,否则可能导致有毒物质扩散、爆炸、环境污染、人员伤亡或中毒等影响面很大的公众伤害事故。
连续生产设备的补焊堵漏需要进行特殊动火作业,危险性很高,稍有疏忽就可能发生事故。
本文以合成氨生产为例,介绍特殊动火作业的分类及安全技术要求。
在生产运行状态下,涉及易燃易爆介质的生产装置、储罐、容器、管道等部位,以及无法置换或很难置换的部位、无法拆除或很难拆除隔绝设备的动火作业,属于特殊危险动火作业。
特殊危险动火作业的动火证,除按一类动火办理审批手续外,还需由动火点所在单位中提出施工方案的主管领导负责初审签字,再经安全主管部门、保卫消防部门复查签字后,报公司负责人、总工程师或生产主管终审批准签字。
分类及应用范围在连续生产中,塔、槽、管道、反应釜等突然发生泄漏,又无法进行排空、清洗、置换时,只能进行特殊危险动火作业。
泄漏时动火危险性很高,必须有严密可靠的安全技术措施。
首先要查清设备、管道泄漏的根本原因。
如果管道、设备等容器壁大面积减薄、设备运行温度很低、泄漏处缺陷过大,就不能采用特殊危险动火作业。
因为即使暂时修复,不久后泄漏仍会扩大甚至发生爆炸。
经检验分析,能够断定泄漏是由于单位的点腐蚀或微波裂纹所致,修复后可恢复原安全性能的,才能动用特殊危险动火作业。
(一)正常生产时设备管道的补焊堵漏方法是:对漏点处进行堵漏处理→打卡子、塞塞子或模具堵漏→打包箍焊接。
各类盛有可燃气体、加热不分解液体的管道和设备,只要介质成分含量不在爆炸范围内,均可采用此法动火,具体见表1所示。
这种方法适用于中、低压部分设备管道的修补应急处理,如洗氨塔、变脱塔、洗气塔(脱硫、变脱的再生槽,脱碳的常解再生塔除外)等设备的损伤,或连接管道出现的点腐蚀。
动火情况要详细记录在案,以便停车检修时作进一步的更换处理。
合成氨生产企业安全标准化实施指南AQT

合成氨生产企业安全标准化实施指南Guidelines for safety standardization of ammonia enterprise自2009-1-1起执行 AQ/T2017-2008前言1 适用范围本标准规定了合成氨生产企业(以下简称企业)开展安全标准化的技术要求。
本标准适用于中华人民共和国境内采用合成工艺生产氨、甲醇及其衍生产品的企业。
2 规范性引用文件下列文件中的条款,通过本标准的引用而成为本标准的条款。
凡是注日期的引用文件,其随后所有的修改单(不包括勘误的内容)或修订版均不适用于本标准,然而,鼓励根据本标准达成协议的各方研究是否可使用这些文件的最新版本。
凡是不注日期的引用文件,其最新版本适用于本标准。
GB 2894 安全标志GB 6222 工业企业煤气安全规程GB 11651 劳动防护用品选用规则GB 13690 常用危险化学品的分类及标志GB 15258 化学品安全标签编写规定GB 16179 安全标志使用导则GB 16483 化学品安全技术说明书编写规定GB 18218 重大危险源辨识GB 50016 建筑设计防火规范GB 50057 建筑物防雷设计规范GB 50058 爆炸和火灾危险环境电力装置设计规范GB 50140 建筑灭火器配置设计规范GB 50160 石油化工企业设计防火规范GB 50351 储罐区防火堤设计规范GBZ 1 工业企业设计卫生标准GBZ 2 工作场所有害因素职业接触限值GBZ 158 工作场所职业病危害警示标识AQ/T 9002 生产经营单位安全生产事故应急预案编制导则SH 3063—1999 石油化工企业可燃气体和有毒气体检测报警设计规范SH 3097—2000 石油化工静电接地设计规范AQ 3013—2008 危险化学品从业单位安全标准化通用规范3 术语和定义AQ 3013—2008确立的术语和定义适用于本标准。
4 要求企业应按照AQ 3013—2008第4章的规定,开展安全标准化工作。
合成氨生产安全技术

合成氨生产安全技术一、引言合成氨是一种重要的工业化学品,广泛应用于化肥、硝化胺、塑料、胶粘剂、药物等领域。
然而,合成氨的生产过程涉及高温、高压和易燃易爆气体的处理,存在一定的安全风险。
为了保障合成氨生产过程的安全性,需要严格遵循相关的安全技术措施。
本文将从反应器设计、工艺控制、设备选择和应急预案等方面介绍合成氨生产的安全技术。
二、反应器设计合成氨生产中最重要的环节是氨合成反应,该反应需要在高温(400-500℃)和高压(150-200bar)条件下进行。
因此,合成氨生产反应器的设计至关重要。
以下是一些关键技术要点:1. 材料选择:反应器内部的材料必须能够承受高温和高压的条件,并且具有良好的耐腐蚀性。
一般来说,合适的材料包括高铬钢、镍基合金等。
2. 压力容器设计:反应器必须设计成合适的压力容器,以承受高压条件。
在设计过程中,需要充分考虑材料和结构的强度,同时保证压力释放装置的可靠性。
3. 温度控制:反应器内部温度的控制对于合成氨生产的安全至关重要。
需要使用合适的隔热材料和冷却系统,以保持反应器内部温度在安全范围内。
三、工艺控制合成氨生产过程中的工艺控制是保证生产安全的另一个重要方面。
以下是一些关键技术要点:1. 严格控制反应气体的比例:合成氨反应需要适当的气体比例,通常为1:3的氮气和氢气比例。
过高或过低的气体比例都会导致反应异常,增加事故发生的风险。
2. 增加副反应的控制:合成氨反应会产生副反应,如甲烷和乙烷的生成。
这些副产物不仅会降低合成氨的产率,还会增加设备的积碳和安全风险。
因此,需要采取措施减少副反应的发生。
3. 确保气体的纯度和质量:反应气体的纯度和质量对合成氨生产的安全和产率有重要影响。
需要定期检测和维护气体供应系统,确保气体的纯度和质量符合要求。
四、设备选择合成氨生产过程中所使用的各种设备也对安全性有重要影响。
以下是一些关键技术要点:1. 压缩机选择:合成氨生产需要大量的氢气和氮气,因此选择合适的压缩机非常重要。
2023年安全工程师《安全生产专业实务(化工安全)》模拟试卷三
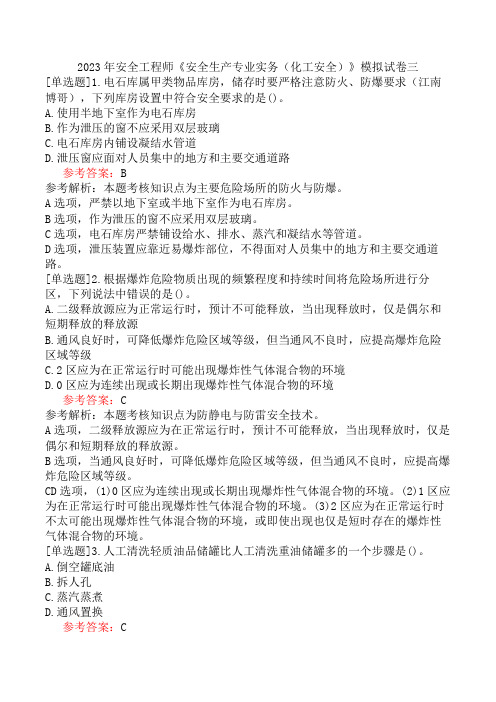
2023年安全工程师《安全生产专业实务(化工安全)》模拟试卷三[单选题]1.电石库属甲类物品库房,储存时要严格注意防火、防爆要求(江南博哥),下列库房设置中符合安全要求的是()。
A.使用半地下室作为电石库房B.作为泄压的窗不应采用双层玻璃C.电石库房内铺设凝结水管道D.泄压窗应面对人员集中的地方和主要交通道路参考答案:B参考解析:本题考核知识点为主要危险场所的防火与防爆。
A选项,严禁以地下室或半地下室作为电石库房。
B选项,作为泄压的窗不应采用双层玻璃。
C选项,电石库房严禁铺设给水、排水、蒸汽和凝结水等管道。
D选项,泄压装置应靠近易爆炸部位,不得面对人员集中的地方和主要交通道路。
[单选题]2.根据爆炸危险物质出现的频繁程度和持续时间将危险场所进行分区,下列说法中错误的是()。
A.二级释放源应为正常运行时,预计不可能释放,当出现释放时,仅是偶尔和短期释放的释放源B.通风良好时,可降低爆炸危险区域等级,但当通风不良时,应提高爆炸危险区域等级C.2区应为在正常运行时可能出现爆炸性气体混合物的环境D.0区应为连续出现或长期出现爆炸性气体混合物的环境参考答案:C参考解析:本题考核知识点为防静电与防雷安全技术。
A选项,二级释放源应为在正常运行时,预计不可能释放,当出现释放时,仅是偶尔和短期释放的释放源。
B选项,当通风良好时,可降低爆炸危险区域等级,但当通风不良时,应提高爆炸危险区域等级。
CD选项,(1)0区应为连续出现或长期出现爆炸性气体混合物的环境。
(2)1区应为在正常运行时可能出现爆炸性气体混合物的环境。
(3)2区应为在正常运行时不太可能出现爆炸性气体混合物的环境,或即使出现也仅是短时存在的爆炸性气体混合物的环境。
[单选题]3.人工清洗轻质油品储罐比人工清洗重油储罐多的一个步骤是()。
A.倒空罐底油B.拆人孔C.蒸汽蒸煮D.通风置换参考答案:C参考解析:本题考核知识点为储罐清洗。
人工清洗轻质油品(泛指汽油、煤油、柴油、石脑油、溶剂油、苯等)储罐的步骤一般为:倒空罐底油,与油罐相连的系统管线加堵盲板,拆人孔,蒸汽蒸煮,通风置换,进入内部高压水冲洗,清理污物。
合成氨生产企业安全标准化实施指南(AQT3017-2008)
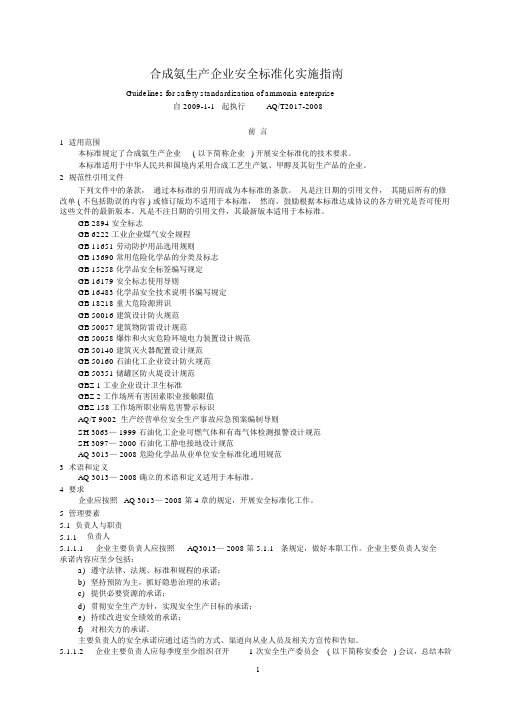
合成氨生产企业安全标准化实施指南Guidelines for safety standardization of ammonia enterprise自 2009-1-1起执行AQ/T2017-2008前言1适用范围本标准规定了合成氨生产企业( 以下简称企业) 开展安全标准化的技术要求。
本标准适用于中华人民共和国境内采用合成工艺生产氨、甲醇及其衍生产品的企业。
2规范性引用文件下列文件中的条款,通过本标准的引用而成为本标准的条款。
凡是注日期的引用文件,其随后所有的修改单 ( 不包括勘误的内容 ) 或修订版均不适用于本标准,然而,鼓励根据本标准达成协议的各方研究是否可使用这些文件的最新版本。
凡是不注日期的引用文件,其最新版本适用于本标准。
GB 2894 安全标志GB 6222 工业企业煤气安全规程GB 11651 劳动防护用品选用规则GB 13690 常用危险化学品的分类及标志GB 15258 化学品安全标签编写规定GB 16179 安全标志使用导则GB 16483 化学品安全技术说明书编写规定GB 18218 重大危险源辨识GB 50016 建筑设计防火规范GB 50057 建筑物防雷设计规范GB 50058 爆炸和火灾危险环境电力装置设计规范GB 50140 建筑灭火器配置设计规范GB 50160 石油化工企业设计防火规范GB 50351 储罐区防火堤设计规范GBZ 1 工业企业设计卫生标准GBZ 2 工作场所有害因素职业接触限值GBZ 158 工作场所职业病危害警示标识AQ/T 9002 生产经营单位安全生产事故应急预案编制导则SH 3063— 1999 石油化工企业可燃气体和有毒气体检测报警设计规范SH 3097— 2000 石油化工静电接地设计规范AQ 3013— 2008 危险化学品从业单位安全标准化通用规范3术语和定义AQ 3013— 2008 确立的术语和定义适用于本标准。
4要求企业应按照AQ 3013— 2008 第 4 章的规定,开展安全标准化工作。
2024年合成氨生产安全技术(3篇)
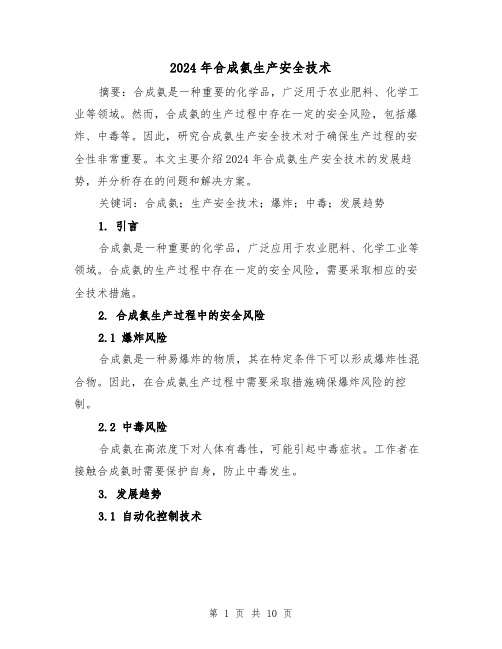
2024年合成氨生产安全技术摘要:合成氨是一种重要的化学品,广泛用于农业肥料、化学工业等领域。
然而,合成氨的生产过程中存在一定的安全风险,包括爆炸、中毒等。
因此,研究合成氨生产安全技术对于确保生产过程的安全性非常重要。
本文主要介绍2024年合成氨生产安全技术的发展趋势,并分析存在的问题和解决方案。
关键词:合成氨;生产安全技术;爆炸;中毒;发展趋势1. 引言合成氨是一种重要的化学品,广泛应用于农业肥料、化学工业等领域。
合成氨的生产过程中存在一定的安全风险,需要采取相应的安全技术措施。
2. 合成氨生产过程中的安全风险2.1 爆炸风险合成氨是一种易爆炸的物质,其在特定条件下可以形成爆炸性混合物。
因此,在合成氨生产过程中需要采取措施确保爆炸风险的控制。
2.2 中毒风险合成氨在高浓度下对人体有毒性,可能引起中毒症状。
工作者在接触合成氨时需要保护自身,防止中毒发生。
3. 发展趋势3.1 自动化控制技术2024年,合成氨生产过程中的自动化控制技术将得到更广泛的应用。
通过引入自动化控制系统,可以确保生产过程中的参数控制和安全操作的准确性。
3.2 环境监测技术合成氨生产过程中的环境监测技术也将得到进一步的发展。
通过实时监测环境参数,可以及时发现异常情况并采取相应的措施保护工作人员的安全。
3.3 事故应急处置技术在2024年,合成氨生产过程中的事故应急处置技术也将得到提升。
针对爆炸、中毒等事故情况,将建立更完善的应急预案和处置方案,以确保事故能得到及时有效的处理。
4. 解决方案4.1 安全生产培训和教育加强对从业人员的安全培训和教育,提高他们的安全意识和应急处置能力。
4.2 引入新技术和装备引入新的安全技术和装备,如智能传感器、无人机等,提高生产过程的安全性。
4.3 加强监测和预警系统建设加强监测和预警系统的建设,通过实时监测合成氨生产过程中的环境参数,及时预警并采取相应的措施。
5. 结论合成氨是一种重要的化学品,生产过程中存在一定的安全风险。
合成氨安全生产技术
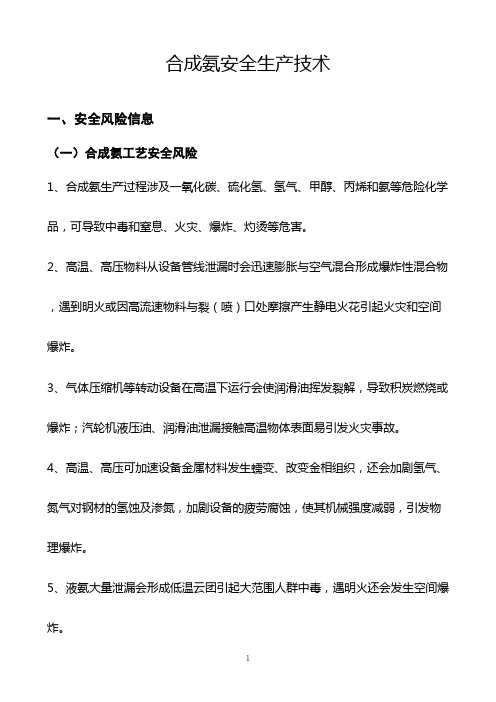
合成氨安全生产技术一、安全风险信息(一)合成氨工艺安全风险1、合成氨生产过程涉及一氧化碳、硫化氢、氢气、甲醇、丙烯和氨等危险化学品,可导致中毒和窒息、火灾、爆炸、灼烫等危害。
2、高温、高压物料从设备管线泄漏时会迅速膨胀与空气混合形成爆炸性混合物,遇到明火或因高流速物料与裂(喷)口处摩擦产生静电火花引起火灾和空间爆炸。
3、气体压缩机等转动设备在高温下运行会使润滑油挥发裂解,导致积炭燃烧或爆炸;汽轮机液压油、润滑油泄漏接触高温物体表面易引发火灾事故。
4、高温、高压可加速设备金属材料发生蠕变、改变金相组织,还会加剧氢气、氮气对钢材的氢蚀及渗氮,加剧设备的疲劳腐蚀,使其机械强度减弱,引发物理爆炸。
5、液氨大量泄漏会形成低温云团引起大范围人群中毒,遇明火还会发生空间爆炸。
6、高温、高压使可燃气体爆炸极限扩宽,气体物料一旦过氧(亦称透氧),极易在设备和管道内发生爆炸等。
7、高压、高温煤粉从设备管线泄漏时,会迅速形成爆炸性混合物,造成粉尘爆炸或空间爆鸣。
8、液氧、液氮和液氩等低温液体泄漏,可造成人员严重冻伤;低温介质进入非低温材质的设备或管道,可造成设备管道损坏。
9、工艺路线中高压、中压、低压管路并存,且有个别管路相互连接,操作不当可能出现高压串低压,进而引发管道、容器爆炸等。
10、煤炭储运和煤粉制备过程中,静电不及时导除或富氧环境极易引发粉尘爆炸。
(二)主要设备设施安全风险1、加压煤气化炉、变换炉、甲烷化炉、脱硫脱碳等吸收塔、氨合成塔及其废热锅炉、液氨中间储槽、液氨罐等承压设备,生产运行过程中超温、超压,检测、控制、管理手段不完善等可造成泄漏,引发火灾和爆炸。
2、煤浆泵、溶液泵、氮氢气压缩机、氨压缩机等机泵在运转及检维修过程中可因冲击和撞击,造成物体打击、机械伤害等。
3、高温设备及管道的保温措施不完善,可造成灼烫、火灾等。
4、放射性检测仪表安全防护失效可造成辐射危害。
5、电气设备安装、使用和维护不当,可造成触电事故。
合成氨生产企业安全标准化实施指南[AQT3017_2008]
![合成氨生产企业安全标准化实施指南[AQT3017_2008]](https://img.taocdn.com/s3/m/6a7f56cbdaef5ef7ba0d3ce1.png)
合成氨生产企业安全标准化实施指南Guidelines for safety standardization of ammonia enterprise自2009-1-1起执行 AQ/T2017-2008前言1 适用范围本标准规定了合成氨生产企业(以下简称企业)开展安全标准化的技术要求。
本标准适用于中华人民共和国境内采用合成工艺生产氨、甲醇及其衍生产品的企业。
2 规范性引用文件下列文件中的条款,通过本标准的引用而成为本标准的条款。
凡是注日期的引用文件,其随后所有的修改单(不包括勘误的内容)或修订版均不适用于本标准,然而,鼓励根据本标准达成协议的各方研究是否可使用这些文件的最新版本。
凡是不注日期的引用文件,其最新版本适用于本标准。
GB 2894 安全标志GB 6222 工业企业煤气安全规程GB 11651 劳动防护用品选用规则GB 13690 常用危险化学品的分类及标志GB 15258 化学品安全标签编写规定GB 16179 安全标志使用导则GB 16483 化学品安全技术说明书编写规定GB 18218 重大危险源辨识GB 50016 建筑设计防火规范GB 50057 建筑物防雷设计规范GB 50058 爆炸和火灾危险环境电力装置设计规范GB 50140 建筑灭火器配置设计规范GB 50160 石油化工企业设计防火规范GB 50351 储罐区防火堤设计规范GBZ 1 工业企业设计卫生标准GBZ 2 工作场所有害因素职业接触限值GBZ 158 工作场所职业病危害警示标识AQ/T 9002 生产经营单位安全生产事故应急预案编制导则SH 3063—1999 石油化工企业可燃气体和有毒气体检测报警设计规范SH 3097—2000 石油化工静电接地设计规范AQ 3013—2008 危险化学品从业单位安全标准化通用规范3 术语和定义AQ 3013—2008确立的术语和定义适用于本标准。
4 要求企业应按照AQ 3013—2008第4章的规定,开展安全标准化工作。
合成氨行业造气单元安全检查表

合成氨行业造气单元安全检查表该单元主要检查造气工段生产系统的生产工艺、生产设备及管道、安全设施及平台、栏杆等防护设施。
依据《工业企业煤气安全规程》GB6222-2005、《小氮肥安全技术规程》化督发(1995)904号、《发生炉煤气站设计规范》GB50195-94等标准、规范。
表5-1造气单元安全检查表序号检查项目和内容检查结果检查依据检查记录平面布置1.煤气站区应位于工业企业厂区主要建筑物和构筑物全年最小频率风向的上风侧。
《发生炉煤气站设计规范》GB50195—94 5.0.1.12.应靠近煤气负荷比较集中的地点。
《发生炉煤气站设计规范》GB50195—943.应便于煤、灰渣、末煤、焦《发生炉煤气站设序号检查项目和内容查结果检查依据查记录油、焦油渣的运输和贮存以及循环水的处理。
计规范》GB50195—94 5.0.1.24.5.0.1.4 应便于与锅炉房共用煤和灰渣的贮运设施以及末煤的利用。
《发生炉煤气站设计规范》GB50195—94 5.0.1.35.应留有扩建的余地。
《发生炉煤气站设计规范》GB50195—94 5.0.1.56.煤气站的厂房应与其他生产厂房分开布置,其间距应符合现行国家标准《建筑设计防火规范》的有关规定。
小型热煤气站的厂房,可与煤气用户的车间毗连,但应设防火墙。
《发生炉煤气站设计规范》GB50195—94 5.0.2序号检查项目和内容查结果检查依据查记录7.煤气站主厂房的正面,宜垂直于夏季最大频率风向;室外煤气净化设备,宜布置在主厂房夏季最大频率风向的下风侧。
《发生炉煤气站设计规范》GB50195—94 5.0.38.循环水系统、焦油系统和煤场等的建筑物和构筑物,宜布置在煤气站主厂房、煤气排送机间、空气鼓风机间等的夏季最大频率风向的下风侧,并应防止冷却塔散发的水雾对周围环境的影响。
《发生炉煤气站设计规范》GB50195—94 5.0.59.室外煤气净化设备、循环水系统、焦油系统和煤场等建筑物和构筑物,宜布置在煤气发生站的主厂房、煤气加压机问、空气鼓风机间等的常年最小频率风向的上风《工业企业煤气安全规程》GB6222-2005 5.1.1.2序号检查项目和内容查结果检查依据查记录侧,并应防止冷却塔散发的水雾对周围的影响。
合成氨行业尿素单元安全检查表

合成氨行业尿素单元安全检查表该单元主要检查尿素合成工段生产系统的生产工艺、生产设备及管道、安全设施及平台、栏杆等防护设施。
依据《工业企业总平面设计规范》GB50187-93、《石油化工工艺装置布置设计通则》SH 3011-2000、《化工企业安全卫生设计规定》HG20571-95、《工业企业设计卫生标准》GBZ1-2000、《小氮肥安全技术规程》化督发[1995]904号等标准、规范。
表5-3尿素单元安全检查表序号检查项目和内容检查结果检查依据检查记录设备工艺1.合成塔塔顶工作平台应有足够大的作业空间、安全护栏、安全扶梯,并备有适用的灭火器材。
《小氮肥安全技术规程》化督发(1995)904号第3.9.1条2.严格控制触媒层温度及系统压力在规定的指标范围内,严禁超温、超压。
《小氮肥安全技术规程》化督发(1995)904号第3.9.6条3.合成塔卸压放空,应开塔后放空阀。
如塔前、塔后同时放空,必须保持塔前压力大于塔后压力,以防气体倒流使触媒粉末吹入电加热器。
卸压操作要缓慢平稳,卸压速率控制在≤0.4MPa/分,切忌过猛过快。
《小氮肥安全技术规程》化督发(1995)904号第3.9.8条4.应定期检查,并经常注意低压系统压力变化,谨防合成废热锅炉列管、氨冷器盘管泄漏,以避免高压气体窜入低压系统引起爆炸。
若发现低压系统压力突然升高,而原因不明时,应作紧急停车处理。
《小氮肥安全技术规程》化督发(1995)904号第3.9.10条5.要控制合成塔进口压差,一般不超过0.8MPa,最大不超过1.0MPa,超过上述规定,必须及时处理,以防内件受损。
《小氮肥安全技术规程》化督发(1995)904号第3.9.14条6.要经常检查循环机工作内件的运转、密封、润滑情况,如发现撞击、震动、大量泄漏等异常现象,应及时处理,避免高压气体冲击发生着火和爆炸。
《小氮肥安全技术规程》化督发(1995)904号第3.9.15条7.要严格控制液氨贮槽压力在规定指标范围内。
- 1、下载文档前请自行甄别文档内容的完整性,平台不提供额外的编辑、内容补充、找答案等附加服务。
- 2、"仅部分预览"的文档,不可在线预览部分如存在完整性等问题,可反馈申请退款(可完整预览的文档不适用该条件!)。
- 3、如文档侵犯您的权益,请联系客服反馈,我们会尽快为您处理(人工客服工作时间:9:00-18:30)。
合成氨工艺单元安全技术要求5.1一般要求5.1.1合成氨装置生产过程应采用DCS控制系统对各个阶段的反应器(如:氨合成塔、尿素合成塔、变换炉、气化炉)温度、压力、液位、进出反应容器物料流量、工艺介质的PH 值等参数进行动态监控,为工艺操作提供安全、准确的信息。
5.1.2涉及“两重点一重大”的煤气化、氨合成等生产装置应设置紧急停车系统(ESD),构成一、二级重大危险源的应设置独立的安全仪表系统(SIS)。
5.1.3ESD或SIS系统按照安全独立的原则要求设置,独立于DCS集散控制系统,其安全级别高于DCS,至少应满足下列要求:——DCS应通过对关键单元和部件冗余配置,实现提高系统运行可靠性的要求;——DCS应具有先进的硬件及软件环境,能满足运行用户的先进控制与实时过程优化软件的要求;——DCS和SIS应采用UPS电源装置供电,并满足《仪表供电设计规范》HG/T 20509的要求;——DCS系统应采用等电位接地技术;——生产装置试车、开车前,应进行联调与试运,使系统各部分处于正常工作状态,完整地投入运行。
5.1.4一般信号报警应在操作员站显示,重要信号报警除在操作员站显示外,宜在辅助操作台上设灯光显示单元和音响单元。
5.1.5联锁系统的设计应满足化工装置的试车、运行和联锁回路的调试、测试和维护等要求。
气化单元应设置系统停车信号声光报警。
5.1.6合成氨生产装置应满足合成氨重点监管危险化工工艺重点监控工艺参数和安全控制要求。
5.1.7工艺系统以及承压设备应设立安全阀、爆破板等防爆泄压系统。
5.1.8可燃性物料的放空管路系统设立阻火器、水封等阻火设施。
5.1.9系统存在不同压力等级并存的高压段设备应设置液位报警、联锁,应设置工艺气吸收、分离等设备,液位应控制稳定。
5.1.10合成氨装置应设置集中控制室,新、改、扩建控制室须符合《石油化工企业设计防火标准》GB 50160、《建筑设计防火规范》GB 50016和《石油化工控制室抗爆设计规范》GB 50779要求。
5.1.11装置现场设置的工业用工程站应标示清楚,同步配置快速接口及连接软管。
5.1.12氢气管线设备运行安全应按照《氢气使用安全技术规程》GB 4962规定要求执行。
5.1.13工艺和作业过程的设计、组织和实施应满足《生产过程安全卫生要求总则》GB/T 12801的要求。
5.1.14空分氧气、氮中氧、合成气、精制气等工艺气应设置在线分析。
5.1.15涉及一氧化碳、硫化氢、甲醇、丙烯、氨和氢气等有毒或可燃气体的释放源场所,应按照《石油化工可燃气体和有毒气体检测报警设计标准》GB/T 50493设置气体泄漏探测报警设施。
5.1.16生产装置、罐区等应按照《石油化工企业设计防火标准》GB 50160等设置完善的消防系统,配置相应的消防器材、设备和设施,并定期检查、检验,确保充足、完好。
5.1.17涉及关键装置、重点部位应设置视频监控系统。
5.2煤粉制备单元5.2.1原料煤储存、输送系统应设立完善的冲洗设施、除尘抑尘设施、安全检测装置、泄压装置、防火装置、DCS自动控制系统。
5.2.2皮带输送装置应设置紧急停车系统,包括DCS急停设施、现场紧急停车拉绳、现场急停按钮等。
5.2.3原料煤储存设施、输送设施、除尘抑尘设施检修前,须确认粉尘清理彻底。
5.2.4煤粉应密闭输送,输送装置应设置防止静电积聚设施。
5.2.5粉煤气化原料制备、输送和储存应采用氮气或二氧化碳等惰性气体保护,并设置O2浓度分析仪及CO在线监测设施。
5.2.6煤粉制备应设置防止断料设施,防止热风门内漏检测设施,粉煤制备磨机出口温度应高于其露点。
5.2.7煤炭储存、输送场所电气设备应采用防尘型电气设备。
5.2.8储煤系统的运转设备、皮带输送系统及电器设备应设置齐全完善的防护装置,皮带运输机四周应设防护栏、警示标识牌,穿越皮带运输机位置应设置过桥。
5.2.9皮带应停机清理,检维修必须断电挂牌。
5.2.10煤炭粉碎前,应设置除铁、除杂装置。
5.2.11煤粉制备装置系统置换,氧含量应控制在5 %以下。
5.2.12煤粉制备、储存和输送应符合《粉尘防爆安全规程》GB 15577要求,系统检修处理时,须置换合格并盲板隔离。
5.3煤气化单元5.3.1水煤浆、干煤粉气化安全技术5.3.1.1气化装置应设置紧急停车系统,至少涵盖以下工艺联锁条件:——气化炉支撑板温度;——合成气出口温度;——激冷水流量;——氧气总管压力;——高压氮气压力;——入炉氧流量;——入烧嘴冷却水流量、出烧嘴冷却水流量;——入烧嘴冷却水压力、出烧嘴冷却水温度;——烧嘴冷却水进出口压差;——出洗涤塔合成气温度;——洗涤塔液位;——锁斗压力、锁斗冲洗水液位;——煤浆或煤粉流量;——渣口压差。
——其他必要条件。
5.3.1.2气化装置安全联锁应完好有效,装置投料前必须调试合格并保存记录。
5.3.1.3气化炉投料前,氮气置换氧含量必须≤0.5 %。
5.3.1.4气化炉停炉后氮气置换CO+H2≤0.5 %。
5.3.1.5氧管线应设置止回阀和氮气保护设施,严禁油脂污染,检修部位脱脂合格方可投用。
5.3.1.6气化装置应严格控制操作压力、氧煤比、工艺气温度、气化炉炉温及外壁温度等工艺参数在指标范围内运行。
5.3.1.7气化装置开停车过程应严格执行升降温速率,初始开车烘炉或更换耐火砖后第一次开车,应严格执行升温曲线。
5.3.1.8气化炉升压速率不宜大于0.1 MPa/min。
5.3.1.9渣水处理系统应保持合理液位,严禁合成气带水带灰。
5.3.1.10及时调节系统水平衡,维持气化炉激冷室液位和洗涤塔液位正常。
5.3.2固定床无烟块煤(型煤)气化安全技术5.3.2.1造气炉下行煤气阀和吹风阀应设安全联锁装置。
5.3.2.2煤气下行管、灰斗和炉底空气管道应安装爆破板,爆破板应安装防护罩。
5.3.2.3吹风阀应设置双阀或增装蝶阀。
5.3.2.4煤气炉应设置一次风管线防爆板和自动放空设施,主要液压阀应安装阀位指示。
5.3.2.5夹套锅炉和废热锅炉汽包应设置安全阀。
5.3.2.6汽包蒸汽出口阀在开车前应检查确认处于全开状态;关汽包放空阀,必须先开出口阀;关汽包出口阀,必须先开放空阀。
5.3.2.7夹套锅炉和废热锅炉汽包应设有低限报警装置,日常运行液位控制在1/2~2/3的高度,一旦断水,未经自然冷却严禁加水。
5.3.2.8造气炉应保持炭层高度及炉温稳定,如遇空气鼓风机跳车应紧急停炉。
5.3.2.9煤气发生炉停车打开炉盖前,必须先开抽引蒸汽(空气)防爆;观察炉面时,必须佩带防护面罩;当打疤或停炉时,炉口应放安全网罩。
5.3.2.10气柜应满足《工业企业湿式气柜技术规范》GB/T 51094要求,还应满足以下条件:——半水煤气中氧含量应≤0.5 %,氧含量≥0.8 %时应高高报警,氧含量≥1 %时应联锁停炉;——气柜前洗气塔有氧表的,洗气塔氧含量≥0.8 %时应高高报警,氧含量≥1 %时应联锁系统停车;——气柜应装有手动、自动放空装置,放空管或顶部排放管应有消除静电设施;——造气、脱硫、压缩单元应设置气柜远传监控设施;——气柜应设容积指示仪、高低限位报警器。
5.3.2.11吹风气锅炉除执行锅炉相关安全规程外,还应设置防超压、防回火水封,吹风气管线应设置防爆膜,前烟道侧面应设置自泄式防爆门,并严格控制温度、压力、气体成分及流量等工艺指标。
5.4气体净化单元5.4.1变换工艺安全技术5.4.1.1开工加热炉操作应遵循“先通工艺气、后投加热炉,先停加热炉、后停工艺气”原则。
投用前必须置换合格;一次点火失败或中间熄火时必须重新进行置换,取样分析合格后方可重新点火。
采用电加热方式升温时,电气和工艺应联合检查合格后方可投用。
5.4.1.2升温还原时如发生断电、断水、断气,应立即停用电加热器。
紧急停车时应保持系统正压。
5.4.1.3变换炉降温、触媒钝化操作后检修,应严格进行物理隔离。
5.4.1.4升温硫化临时使用的二硫化碳罐应远离明火,罐内要加水保护,夏季应落实遮阳措施。
用氮气瓶压力压入系统时,罐内压力不得超过0.05 MPa。
作业现场要备消防器材和防毒面具。
5.4.1.5系统应设置热水泵跳车、饱和热水塔液位高、低限报警信号。
5.4.1.6工艺气宜设置氧含量在线分析及报警、联锁设施;氧含量控制应≤0.5 %,饱和热水塔液位、变换炉温度、煤气中硫化氢含量等应制定工艺指标并严格执行。
5.4.1.7参与原料气配比的蒸汽压力应高于变换系统压力,并设置压差低限报警。
5.4.1.8装置正常运行温度较高、开车前后温度变化较大的连接法兰,在开车过程中应进行热紧,宜设置防雨雪设施。
5.4.1.9变换升温硫化时,应密切注意温升情况,发生偏离升温曲线时,应及时调整CS2添加量和加热炉温度。
5.4.1.10变换升温硫化期间放空气体严禁现场放空。
5.4.2脱硫工艺安全技术5.4.2.1静电除焦塔进口原料气管线必须设置氧含量在线分析仪表和报警联锁设施,一般控制氧含量≤0.5 %,当≥0.8 %时必须断电停车;静电除焦塔投用前绝缘≥50 MΩ,夹套温度宜控制在90 ℃~110 ℃。
5.4.2.2罗茨风机厂房必须设置强制通排风设施;罗茨风机出口管路必须设置止回阀或停(跳)车自动切断装置,加装消声设施;风机进口管路应设置防止风机抽负压的检测、报警、联锁设施,出口管路设置防止风机过载的压力检测、报警及循环大回路联锁设施。
5.4.2.3静电除焦塔、脱硫塔检修打开前,应采取防止设备内壁硫化亚铁、积焦自燃措施。
5.4.2.4应设置脱硫塔、清洗塔或分离器、液封等液位和脱硫塔压力(压差)声光报警设施,保证液位、压力稳定正常。
5.4.2.5硫磺储存场所禁止同时存放氧化剂和易燃物品。
5.4.2.6采用克劳斯硫回收工艺,应设置炉膛压力联锁、酸性气流量联锁、火焰监测器等仪表系统。
5.4.2.7采用克劳斯硫回收工艺配氧操作时,应设置在线氧/酸性气比值仪。
5.4.3碳酸丙烯脂脱碳工艺安全技术5.4.3.1必须严格控制贫液中含水量≤2 %。
5.4.3.2必须严格控制吸收塔(或水洗塔)、闪蒸器(或氢氮回收器)等液位指标,吸收塔液位应设置联锁报警设施。
5.4.3.3脱碳水洗塔塔后分离器,应安装自动排水和液位声光报警装置。
5.4.4变压吸附脱碳工艺安全技术5.4.4.1装置应设置自动切塔与恢复程序,进吸附塔前应设油水分离设施。
5.4.4.2装置应设置程控阀开关控制及阀位检测、模拟量检测与调节、故障报警联锁。
5.4.4.3油泵站应设双电源供电,油压系统应设置压力高低限报警联锁和低限自启功能。
5.4.4.4操作工应定时巡检液压系统,检查油温、油位是否正常,系统有无漏油点。
5.4.4.5装置临时停车及开车前,应确认各吸附塔的压力与停车联锁状态的一致性。