机车减震弹簧的制造工艺研究
弹簧的制造工艺流程

弹簧的制造工艺流程弹簧的制造工艺流程在现代工业生产中,弹簧作为一种重要的机械零件,广泛应用于各个领域。
从汽车制造到家电、玩具等,弹簧在其中发挥着至关重要的作用。
然而,对于普通消费者来说,弹簧的制造过程常常被忽略。
本文将以从简到繁的方式,深入探讨弹簧的制造工艺流程,帮助读者更全面、深刻地了解弹簧的生产过程。
1. 弹簧的基本概念和用途在开始探讨弹簧的制造工艺之前,我们先来了解一下弹簧的基本概念和用途。
弹簧是一种有弹性的机械元件,它可以储存和释放力量,常用于控制、支撑、挤压等方面。
在汽车悬挂系统中,弹簧可以减震和支撑车身;在钟表中,弹簧则是控制时间精确度的关键部件。
可以说,弹簧在现代生活中随处可见,发挥着重要的功能。
2. 原材料的选择和加工弹簧的制造过程始于原材料的选择和加工。
一般情况下,常用的原材料包括不锈钢、碳钢等。
根据不同的应用领域和要求,制造者会选择不同材料的弹簧。
原材料的加工通常包括铸造、锻造、拉丝等工艺,以获得满足要求的弹簧材料。
3. 弹簧的成型在原材料加工完毕后,接下来是弹簧的成型工艺。
成型工艺通常有冷却成型和热卷制两种主要方式。
冷却成型是指通过外力和模具将原材料弯曲成所需形状的方式,适用于小型或精密弹簧的制造。
热卷制是将原材料加热至特定温度后,通过滚轮等设备将其成型。
热卷制适用于大型和复杂弹簧的制造,具有较高的生产效率和稳定性。
4. 钢丝的处理和加工弹簧中所使用的钢丝是一种重要的材料,它需要经过一系列的处理和加工过程。
钢丝会经过表面处理工艺,如酸洗、镀锌等,以提高其耐腐蚀性。
接下来,钢丝会通过预拉伸、轧制、切割等加工工艺,以获得符合规格要求的成品钢丝。
5. 弹簧的热处理为了提高弹簧的力学性能和使用寿命,弹簧通常需要进行热处理。
热处理是通过加热和冷却的方式,改变弹簧的组织结构和性能。
常见的热处理工艺包括淬火、回火、退火等。
通过合理的热处理工艺,可以使弹簧具有更好的弹性和耐久性。
6. 表面处理和涂层为了提高弹簧的表面质量和耐腐蚀性,通常还需要进行表面处理和涂层。
车辆用减震弹簧钢65Mn盘条的生产实践

1 前 言 酒钢集团宏兴炼轧厂二高线于2003年正式投产,运行至今已成功开发了焊条、焊丝、高碳钢、PC钢棒用钢等系列用钢盘条,约30多个牌号,规格有φ5.5mm~20mm,其中大部分已批量生产并投放市场,已形成一定的规模与影响力。
车辆用弹簧钢65Mn兼具高碳及低合金钢的特点,盘条经拉拔后用于制造车辆用减震弹簧。
65Mn 弹簧钢具有良好的淬透性,强度较高和较低的脱碳敏感性等优点,因而被广泛使用。
为满足用户对65Mn盘条冷加工性能不断提高的要求,简化工艺并减少氧化铁皮量,采用连铸小方坯为原料,通过优化高线控轧控冷工艺来提高产品质量,摸索不同控轧控冷工艺对于产品力学的影响,结合用户使用情况,不断改善提高拉拔性能,最终获得稳定的65Mn车辆减震弹簧钢生产工艺。
2 工艺流程设计 项目组依据宏兴炼轧厂现有的设备装备及车辆用弹簧钢的质量控制要求,制定了炼钢冶炼浇车辆用减震弹簧钢65Mn盘条的生产实践金武俊(酒钢集团宏兴股份公司炼轧厂,甘肃,嘉峪关,735100) 摘 要:主要介绍车辆用减震弹簧钢65Mn盘条的开发,通过合理的炼钢冶炼工艺控制,轧制过程中控轧控冷工艺,生产出性能稳定的φ6.5mm规格的盘条。
关键词:65Mn弹簧钢;索氏体;斯太尔摩线;力学性能;生产实践Production Practice of Damping Spring Steel 65Mn Wire Rod forVehiclesJin Wujun(Steel Making and Rolling Plant of Hongxing Iron & Steel Co. Ltd., Jiuquan Iron and Steel (Group) Corporation,Jiayuguan, Gansu,735100) Abstract: This paper mainly introduces the development of damping spring steel 65Mn wire rod for vehicles,through reasonable smelting process control and rolling control and cooling process,theφ6.5mm steel with stable performance can be produced. Key words: 65Mn spring steel; sorbite; stelmore line; mechanical properties; production practice- 45 -- 46 -注成150mm×150mm 端面的12米方坯,在炼轧厂高速线材生产线上进行轧制的工艺路线。
从设计、工艺上解决摩托车后减振弹簧的弯曲变形

弯 曲变形 的主要 问题 ,现把 问题 及解 决过 程介 绍给 同行 ,望对 大家 的 工作能 有 所帮 助 。
后减 振 下护罩 弹 簧 阻尼器
上护罩
至上 下护 罩 间相互 磨损 ;更 严重 的是 ,由于弹 簧 的 弯 曲力矩 ,使活塞杆侧 向力加大 ,活塞杆 与油封 、导 向套之间产生严重偏磨 ,加速 了油封 唇 口的磨 损 ,致 使后减震 器出现渗 漏油 。根 据振龙减 震器公 司统 计 , 减震 器 因漏油退 货 的几乎 都是 弹簧 变形 造成 的 。 另 外 ,摩 托 车作 为载 人交通 工具 ,正常 设计每 车 应坐 2 ,但在农村却远不止 2 ,有的 3 、甚至 4人 , 人 人 人
工作 负荷 下疲 劳 强
i a值越小 ,应力集 中 戋 器公 司出现 的弹 震
变形 ,甚至 断 裂。
关键词 : 后 减 震 器弹簧 弯曲变形 设 计 工 艺
Ov r o n n i gDe e to fM o o c ce e c mi gBe d n f ci n o t r y l l Re r h c a o kAbs r e p i gTe h i al S o b rS rn c n c ly
Abs r c : Thef tg e sr n t fr a ho k a s r e p i g i r al f e td byc a k , f c s ta t ai u te g h o e rs c b o b rs rn sg e ty a c e r c s de e t, S a Sofm a e a ura e c  ̄o nt pe a i g tm p r t r . we a i e sr ng fs c bs r e C tr ls f c , o de ,o r tn e e a u e Lo rf tgu te t o ho k a o b r r i h s rn al tm e tt e d ma d o a i u te gt e s rn tma r i o d a a a e p g c l no e e n n f tg e s n h oft p g a x wo k ng l a nd m y c us i h r h i
摩托车液压式减震器的批量生产工艺和成本优化

摩托车液压式减震器的批量生产工艺和成本优化摩托车液压式减震器是摩托车重要的悬挂装置之一,它能够有效地减少由于路面不平造成的振动和冲击,提供舒适的骑行体验和安全性。
本文将探讨摩托车液压式减震器的批量生产工艺和成本优化。
首先,我们需要了解液压式减震器的工作原理。
液压减震器通过液压阻尼器来减缓车辆在路面行驶中的震动,并通过弹簧来支撑车身重量。
液压减震器的核心部件包括阻尼器和活塞,其批量生产工艺关键在于以下几个方面:首先,材料选择。
减震器的材料需要具备较高的强度和耐磨性,以确保其在长时间的使用过程中能够承受较大的压力和摩擦。
常用的材料有铝合金、钢材和高强度塑料等,根据不同的使用要求选用合适的材料能够有效地降低成本。
其次,制造工艺。
液压减震器的制造过程需要精确的加工和装配,保证各个零部件之间的密封性和工作效果。
首先是翻压杯的制作,通过冲压和成型工艺将材料制成凹凸不平的翻压杯,然后采用焊接或者机械连接的方式固定杯体。
活塞和阻尼器的制作则需要采用精密加工工艺,以保证其与杯体的配合度和密封性。
最后,通过装配和调试来检验减震器的性能和质量。
另外,生产工艺的优化可以通过自动化和智能化的手段来实现。
自动化生产线能够提高生产效率和工作精度,减少人力成本和人为误差。
智能化的生产设备和工艺控制系统能够更好地监测和控制生产过程,提高产品的质量和一致性。
通过优化生产工艺和引入新的制造技术,可以有效地降低生产成本和提高生产效率。
成本优化是批量生产过程中的重要环节。
首先,要从供应链的角度进行成本控制,选择可靠的供应商和优化物流配送,以降低原材料和零部件的采购成本。
其次,生产过程中要采用先进的成本控制方法,如精益生产和可持续制造,以最大限度地降低废品率和能源消耗,进一步降低成本。
此外,还要进行全面的质量控制和检测,确保生产出的减震器符合国际标准和客户要求,避免售后问题和退货。
成本优化需要持续的研究和改进,以确保企业在竞争激烈的市场中具有竞争力。
摩托车液压式减震器的弹簧设计与刚度优化
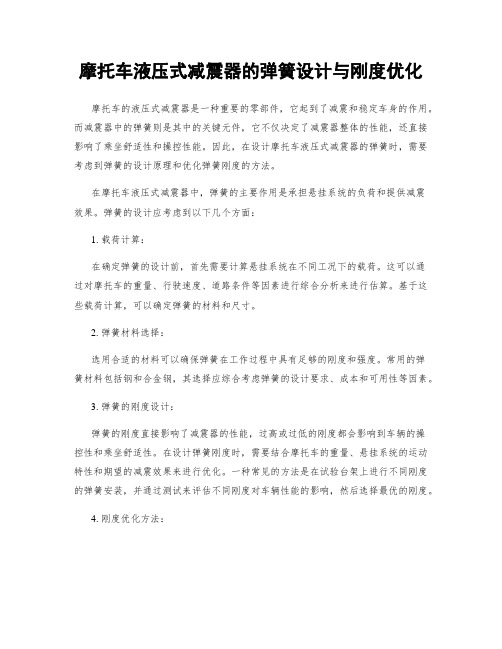
摩托车液压式减震器的弹簧设计与刚度优化摩托车的液压式减震器是一种重要的零部件,它起到了减震和稳定车身的作用。
而减震器中的弹簧则是其中的关键元件,它不仅决定了减震器整体的性能,还直接影响了乘坐舒适性和操控性能。
因此,在设计摩托车液压式减震器的弹簧时,需要考虑到弹簧的设计原理和优化弹簧刚度的方法。
在摩托车液压式减震器中,弹簧的主要作用是承担悬挂系统的负荷和提供减震效果。
弹簧的设计应考虑到以下几个方面:1. 载荷计算:在确定弹簧的设计前,首先需要计算悬挂系统在不同工况下的载荷。
这可以通过对摩托车的重量、行驶速度、道路条件等因素进行综合分析来进行估算。
基于这些载荷计算,可以确定弹簧的材料和尺寸。
2. 弹簧材料选择:选用合适的材料可以确保弹簧在工作过程中具有足够的刚度和强度。
常用的弹簧材料包括钢和合金钢,其选择应综合考虑弹簧的设计要求、成本和可用性等因素。
3. 弹簧的刚度设计:弹簧的刚度直接影响了减震器的性能,过高或过低的刚度都会影响到车辆的操控性和乘坐舒适性。
在设计弹簧刚度时,需要结合摩托车的重量、悬挂系统的运动特性和期望的减震效果来进行优化。
一种常见的方法是在试验台架上进行不同刚度的弹簧安装,并通过测试来评估不同刚度对车辆性能的影响,然后选择最优的刚度。
4. 刚度优化方法:在确定初始刚度后,可以通过几种方法进行进一步的刚度优化。
一种常用的方法是调整弹簧的线径和材料,以达到期望的刚度。
另一种方法是通过增加或减少弹簧的圈数来改变刚度。
在设计过程中,还需要考虑到弹簧的安装方式和调整方法。
良好的弹簧安装和调整可以确保减震器的性能最大化。
常见的安装方式有单边固定和双边固定两种,根据摩托车的悬挂系统和结构特点来选择合适的安装方式。
最后,弹簧的设计与刚度优化需要综合考虑车辆的使用环境、悬挂系统的运动特性以及乘坐舒适性和操控性能等因素。
通过合理选择材料、精确计算和优化设计,可以使摩托车液压式减震器的弹簧达到最佳的性能和效果。
60Si2Mn机车减震板簧热处理工艺设计

攀枝花学院学生课程设计(论文)题目:60Si2Mn机车减震板簧热处理工艺设计学生姓名: X X X 学号: XXXXXXXXXXX 所在院(系):材料工程学院专业: 20XX级材料成型及控制工程班级:材料成型及控制工程指导教师: X X X 职称:讲师2012年12月28日攀枝花学院教务处制攀枝花学院本科学生课程设计任务书注:任务书由指导教师填写。
课程设计(论文)指导教师成绩评定表摘要本课设计了60Si2Mn机车减震板簧热处理工艺设计。
提出了60Si2Mn钢机车板簧的最佳淬火温度。
试验表明,适当提高淬火温度至910℃左右,淬火后得到板条马氏体,有利于获得强度、塑性、韧性以及断裂韧性兼优的综合力学性能。
经420℃回火,保持较高的强度和韧性,满足汽车板簧小能量多冲和疲劳载荷的服役状态,具有较高的疲劳寿命等使用性能。
关键词:60Si2Mn;板簧;热处理艺;力学性能目录摘要 (Ⅰ)1、设计任务 (1)1.1设计任务 (1)1.2设计的技术要求 (1)2、设计方案 (2)2.1 变速箱设计的分析 (2)2.1.1工作条件 (2)2.1.2失效形式 (2)2.1.3性能要求 (2)2.2钢种材料 (3)3、设计说明 (4)3.1加工工艺流程 (4)3.2具体热处理工艺 (4)3.2.1预备热处理工艺 (5)3.2.2机械加工 (5)3.2.3奥氏体化 (5)3.2.4正火 (6)4、分析与讨论 (8)5、结束语 (9)6、热处理工艺卡片 (10)参考文献 (11)1 设计任务1.1设计任务60Si2Mn机车减震板簧热处理工艺设计1.2设计的技术要求60Si2Mn弹簧钢是应用广泛的硅锰弹簧钢,强度、弹性和淬透性较55Si2Mn 稍高。
60Si2Mn弹簧钢适于铁道车辆、汽车拖拉机工业上制作承受较大负荷的扁形弹簧或线径在30mm以下的螺旋弹簧、也适于制作工作温度在250 ℃以下非腐蚀介质中的耐热弹簧以及承受交变负荷及在高应力下工作的大型重要卷制弹簧以及汽车减震系统等。
弹簧减振系统的设计与优化
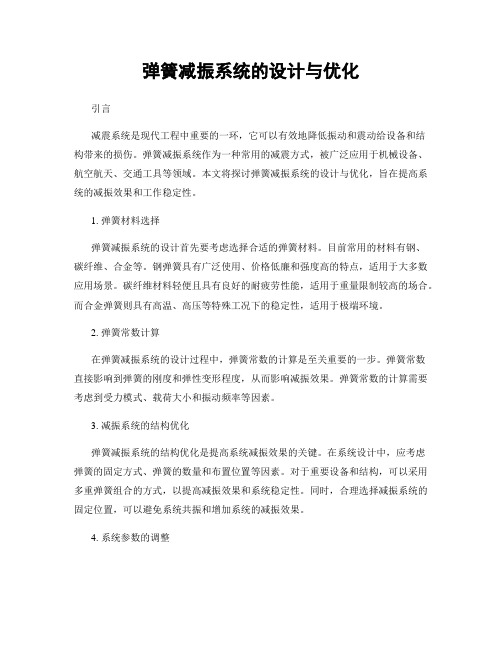
弹簧减振系统的设计与优化引言减震系统是现代工程中重要的一环,它可以有效地降低振动和震动给设备和结构带来的损伤。
弹簧减振系统作为一种常用的减震方式,被广泛应用于机械设备、航空航天、交通工具等领域。
本文将探讨弹簧减振系统的设计与优化,旨在提高系统的减振效果和工作稳定性。
1. 弹簧材料选择弹簧减振系统的设计首先要考虑选择合适的弹簧材料。
目前常用的材料有钢、碳纤维、合金等。
钢弹簧具有广泛使用、价格低廉和强度高的特点,适用于大多数应用场景。
碳纤维材料轻便且具有良好的耐疲劳性能,适用于重量限制较高的场合。
而合金弹簧则具有高温、高压等特殊工况下的稳定性,适用于极端环境。
2. 弹簧常数计算在弹簧减振系统的设计过程中,弹簧常数的计算是至关重要的一步。
弹簧常数直接影响到弹簧的刚度和弹性变形程度,从而影响减振效果。
弹簧常数的计算需要考虑到受力模式、载荷大小和振动频率等因素。
3. 减振系统的结构优化弹簧减振系统的结构优化是提高系统减振效果的关键。
在系统设计中,应考虑弹簧的固定方式、弹簧的数量和布置位置等因素。
对于重要设备和结构,可以采用多重弹簧组合的方式,以提高减振效果和系统稳定性。
同时,合理选择减振系统的固定位置,可以避免系统共振和增加系统的减振效果。
4. 系统参数的调整弹簧减振系统的参数调整对于提高系统的工作效果至关重要。
首先,需要根据实际工况和振动特性,调整弹簧的刚度和预压力等参数,以达到最佳的减振效果。
其次,可以通过改变阻尼器的参数来优化系统的动态响应,以提高系统的稳定性和减振效果。
最后,可以通过调整质量块的位置和质量,来减小系统的共振频率,从而提高系统的减振效果。
5. 弹簧减振系统与其他减振方式的比较弹簧减振系统是一种常用的减振方式,然而也存在一些局限性。
与其他减振方式相比,弹簧减振系统具有较大的体积和重量,且在某些频率范围内的减振效果不佳。
因此,在实际应用中,需要根据具体情况选择合适的减振方式,如液压减振器、电磁减振器等,以满足工程需求。
空气弹簧减振器工艺
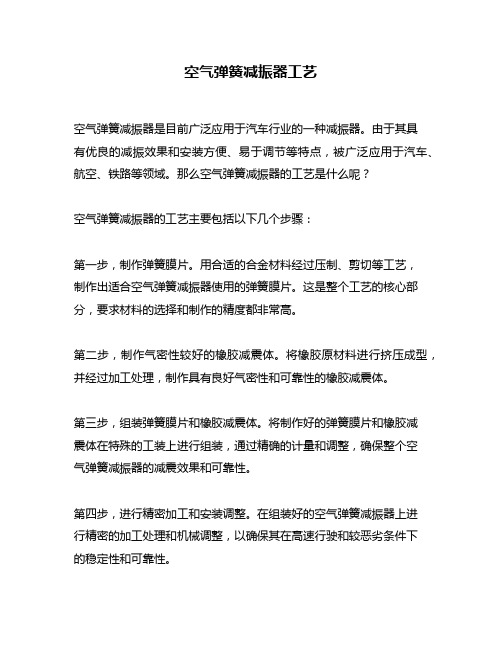
空气弹簧减振器工艺
空气弹簧减振器是目前广泛应用于汽车行业的一种减振器。
由于其具
有优良的减振效果和安装方便、易于调节等特点,被广泛应用于汽车、航空、铁路等领域。
那么空气弹簧减振器的工艺是什么呢?
空气弹簧减振器的工艺主要包括以下几个步骤:
第一步,制作弹簧膜片。
用合适的合金材料经过压制、剪切等工艺,
制作出适合空气弹簧减振器使用的弹簧膜片。
这是整个工艺的核心部分,要求材料的选择和制作的精度都非常高。
第二步,制作气密性较好的橡胶减震体。
将橡胶原材料进行挤压成型,并经过加工处理,制作具有良好气密性和可靠性的橡胶减震体。
第三步,组装弹簧膜片和橡胶减震体。
将制作好的弹簧膜片和橡胶减
震体在特殊的工装上进行组装,通过精确的计量和调整,确保整个空
气弹簧减振器的减震效果和可靠性。
第四步,进行精密加工和安装调整。
在组装好的空气弹簧减振器上进
行精密的加工处理和机械调整,以确保其在高速行驶和较恶劣条件下
的稳定性和可靠性。
以上就是空气弹簧减振器的工艺流程。
在实际制作过程中,还需要严格控制制作材料的选择和加工精度等因素,以确保最终制作出的空气弹簧减振器具有优良的减振效果和可靠性。
总之,空气弹簧减振器的工艺虽然看似简单,但其中包含的技术含量非常高。
唯有精湛的技艺和专业的制作工艺,才能制作出真正符合市场需求的高品质空气弹簧减振器。
橡胶弹簧橡胶减振垫设备工艺原理
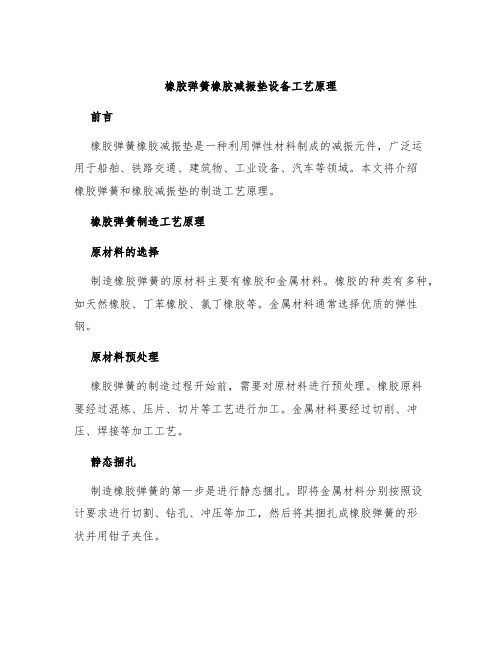
橡胶弹簧橡胶减振垫设备工艺原理前言橡胶弹簧橡胶减振垫是一种利用弹性材料制成的减振元件,广泛运用于船舶、铁路交通、建筑物、工业设备、汽车等领域。
本文将介绍橡胶弹簧和橡胶减振垫的制造工艺原理。
橡胶弹簧制造工艺原理原材料的选择制造橡胶弹簧的原材料主要有橡胶和金属材料。
橡胶的种类有多种,如天然橡胶、丁苯橡胶、氯丁橡胶等。
金属材料通常选择优质的弹性钢。
原材料预处理橡胶弹簧的制造过程开始前,需要对原材料进行预处理。
橡胶原料要经过混炼、压片、切片等工艺进行加工。
金属材料要经过切削、冲压、焊接等加工工艺。
静态捆扎制造橡胶弹簧的第一步是进行静态捆扎。
即将金属材料分别按照设计要求进行切割、钻孔、冲压等加工,然后将其捆扎成橡胶弹簧的形状并用钳子夹住。
静态捆扎后的橡胶弹簧需要进行橡胶注入。
先将橡胶制成一个圆柱形,再将其放到注射机中进行压缩,注入到捆扎的金属材料上。
橡胶注入时需要保证注入的量和压力的均匀性。
固化橡胶注入后需要进行固化。
一般的橡胶固化需要在高温高压下进行。
橡胶弹簧的固化时间与固化温度、压力及橡胶弹簧的尺寸等因素有关。
修整橡胶弹簧制造完毕后需要进行修整。
修整工艺主要是对橡胶弹簧的外形进行修整,并确保橡胶弹簧的型号与设计要求相符合。
橡胶减振垫制造工艺原理原材料的选择橡胶减振垫的制造工艺原理与橡胶弹簧相似,主要原材料为橡胶和金属材料。
但是橡胶减振垫对橡胶的性能要求较高,需选择性能稳定、厚度均匀等特性好的橡胶原材料。
原材料预处理与橡胶弹簧一样,橡胶减振垫的原材料需要进行预处理。
橡胶原料附加预处理压缩和切割等加工工艺,金属材料需要进行切割和冲压等处理。
在橡胶减振垫的制造过程中需要进行音频监测。
由于橡胶减振垫常用于减少振动和噪声的传递,需要对其制造过程中的噪音进行监测,以保证橡胶减振垫质量的稳定性。
注塑橡胶减振垫的制造过程中需要进行注塑。
注塑工艺是将橡胶材料放入注射机中进行注塑,以确保其质量稳定。
加工和修整橡胶减振垫制造完毕后要进行加工和修整。
一种摩托车减震弹簧[实用新型专利]
![一种摩托车减震弹簧[实用新型专利]](https://img.taocdn.com/s3/m/a10a6f4ff524ccbff12184f9.png)
专利名称:一种摩托车减震弹簧
专利类型:实用新型专利
发明人:马泽民,马友芳,赵春伟,梁泉申请号:CN201020269528.6
申请日:20100722
公开号:CN201731008U
公开日:
20110202
专利内容由知识产权出版社提供
摘要:本实用新型涉及车辆减震弹簧,尤其是一种摩托车减震弹簧,由油淬火回火弹簧钢丝绕制而成的圆柱右旋压缩弹簧,弹簧的线径A为7.0±0.035mm,弹簧外径B为Φ54±0.3mm,弹簧高度C 为225±2mm,弹簧一端小节距的圈数为4.5~5.5,小节距t1为11mm~12mm,另一端节距的圈数为10.5~9.5,节距t2为16mm~17mm,弹簧端圈磨面角度为270°~330°该弹簧由两种节距尺寸,因而具有两种刚度特性,能够随着载重的大小或路面的颠簸调节缓冲力度,从而控制用户乘坐的舒适性;该弹簧选用油淬火回火弹簧钢丝,经自动生产线加工而成,生产效率高,产品缺陷率低,其安全性能达到了国外同类弹簧的水平。
申请人:常州市铭锦弹簧有限公司
地址:213179 江苏省常州市武进区雪堰镇潘家工业集中区常州市铭锦弹簧有限公司
国籍:CN
代理机构:常州市维益专利事务所
代理人:王凌霄
更多信息请下载全文后查看。
机车减震弹簧的制造工艺研究

机车减震弹簧的制造⼯艺研究机车减震弹簧的制造⼯艺研究0引⾔弹簧⾏业在整个制造业当中虽然是⼀个⼩⾏业,但其所起到的作⽤是不可低估的。
国家的⼯业制造业、汽车⼯业要加快发展,作为基础件、零部件之⼀的弹簧⾏业就更加需要有⼀个发展的超前期,才能适应国家整个⼯业的快速发展。
另外,弹簧产品规模品种的扩⼤、质量⽔平的提⾼也是机械设备更新换代的需要和配套主机性能提⾼的需要,因此,整个国家⼯业的发展,弹簧产品是起到重要作⽤。
交通运输市场,包括为汽车/摩托车/柴油机和铁道等⾏业提供配套和维修件弹簧,这是弹簧⾏业⽬前最重要,最有发展前途的市场,销售额接近全⾏业的40%。
其中摩托车、电动车销售市场依旧很⼤,尚未限牌的⼤中城市和沿海发达地区对⾼档产品的需求和内陆⼩城市及农村市场对中低档产品的需求仍然具有很⼤的空间。
减震弹簧是机车减震器最重要的零件之⼀,是⽤于吸收运动冲击能量,使机车获得⾼平顺性、⾼舒适性的专⽤件。
减震弹簧设计与制造的优劣直接影响减震器的减震性能、寿命、经济性及整机的安全性。
1减震弹簧的选材与造型1.1减震弹簧的选材作为摩托车、电动车⽤弹簧, 长期处于反复受⼒和回复过程, 疲劳寿命需达到10万次以上,外⼒卸载后应回复到初始位置, 要求弹簧的塑性变形越⼩越好, 钢丝应具有较⾼的弹性极限, 较⾼的回复⼒, 要求屈服强度和抗拉强度较⾼。
[1]⽬前,市⾯上常⽤的有碳素弹簧钢、合⾦弹簧钢、不锈钢弹簧钢以及铜合⾦、镍合⾦和橡胶等。
本⼯艺采⽤65Mn钢,65Mn 钢属于碳素弹簧钢,主要⽣产成钢丝、钢带、⽤于制造各种截⾯较少的扁,圆弹簧,板簧和弹簧⽚等。
有着强度较⾼,淬透性较⼤,脱碳倾向⼩,价格低廉,切削性好等优点。
1.2减震弹簧的造型机车⽤减震弹簧是承受压⼒的螺旋弹簧,也称为圆柱螺旋弹簧。
压缩弹簧⼀般⽤料的截⾯基本都是圆形,但形状和尺⼨种类繁多,既有等直径、等节距, 也有变直径、变节距弹簧,不同的设计主要为满⾜安装空间、⼒值、刚度的要求。
一种增强机车弹簧刚度的减振设计

的能力, 达到了减振效果, 有利于提速后机车行驶的平 稳性和安全性。
参考文献
% * 2 ! 张英会7 弹簧7 机械工业出版社, %("& 王福天7 车辆动力学7 中国铁道出版社, %("% 赵叔东7 韶山" 型电力机车7 中国铁道出版社, %((" 汪曾祥, 魏先英, 刘祥至7 弹簧设计手册7 上海科学技术出版 社, %("1 # ) 编辑 第一、 二、 三作者单位: 郑州轻工业学院 邮政编码: 河南・!1&&&* 第四作者单位: 太原工业大学 收稿日期: *&&%年%月 玉 林+
构简单、 制造和维修容易、 成本较低、 自重较轻等优点, 得到了广泛应用, 我国电力机车多采用圆柱螺旋弹簧。 由于圆柱螺旋弹簧曾出现过压损坏现象, 因此不采用 更大的弹簧代替原弹簧, 而是在原弹簧的基础上加上 一个同材料的等变形弹簧作为内卷弹簧。 这样, 在不增 大弹簧占用面积的基础上, 达到了增大刚度的目的, 即 将直径不同的两螺旋弹簧套装在一起, 组成双卷并列 式组合螺旋弹簧。 两个螺旋弹簧一个左旋, 一个右旋, 以免相互卡住。 假设在不采用组合弹簧的情况下, 要增大刚度, 必 须采用更大簧条直径的弹簧。 设这个弹簧簧条直径为 修正系数为 $, 应力为 !4567 载荷为 %456 7 !" 中径为 #, 挠度为 &。 如果用组合弹簧代替单卷弹簧, 必须满足以下条 应力 !" 和 件: 双卷弹簧的外卷和内卷的指数 ’" 和 ’# 、 挠度 &" 和 &# 要分别等于单卷弹簧的 ’、 以此 !# 、 ! 和 &, 来推出二者之间的尺寸关系。 ! " # 弹簧指数相等 即 式中 说明它们的挠曲程度一样, 由 1"2 1#2 挠曲引起的应力修正系数也一样。 ’" 8 ’# 8 ’ 8 # 9 ! 8 #" 9 !" 8 ## 9 !# $ 8 $" 8 $# 的中径和簧条直径。 ! $ # 使应力相等 即 ! 8 !"456 8 !#456 表明充分利用了材料的强度。 1’2
减震弹簧是这样制造的

减震弹簧是这样制造的
常规意义上的减震弹簧的线径从很微小到很大,都是可以说是有这个作用。
减震弹簧不分大小,有微型的,还有超大型的,比如铁路上,大型机械上的都是常规上的减震弹簧,还有的就是微型电路上的弹簧,按照用途也可以称为减震弹簧。
不过传统认识上我们称为微型的为压簧,而线径在3.0上面的为传统的减震大弹簧
通常来说,弹簧的绕制方法分冷卷法与热卷法两种。
1、冷卷法:簧丝直径d≤8mm的采用冷卷法绕制。
冷态下卷绕的弹簧常用冷拉并经预先热处理的优质碳素弹簧钢丝,卷绕后一般不再进行淬火处理,只须低温回火以消除卷绕时的内应力。
2、热卷法:簧丝直径较大(d>8mm)的弹簧则用热卷法绕制。
在热态下卷制的弹簧,卷成后必须进行淬火、中温回火等处理。
当使用成形后不需淬火、回火处理的材料制造弹簧时,其工艺过程为
螺旋压缩弹簧:卷制、去应力退火、两端面磨削、(抛丸)、(校整)、(去应力退火)、立定或强压处理、检验、表面防腐处理、包装。
减振器生产工艺
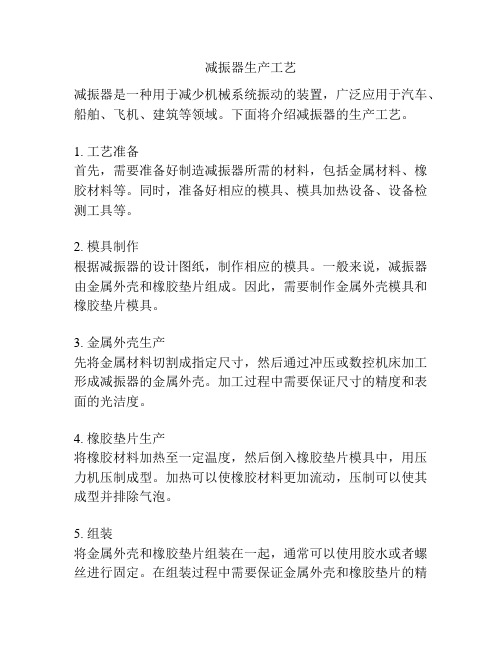
减振器生产工艺
减振器是一种用于减少机械系统振动的装置,广泛应用于汽车、船舶、飞机、建筑等领域。
下面将介绍减振器的生产工艺。
1. 工艺准备
首先,需要准备好制造减振器所需的材料,包括金属材料、橡胶材料等。
同时,准备好相应的模具、模具加热设备、设备检测工具等。
2. 模具制作
根据减振器的设计图纸,制作相应的模具。
一般来说,减振器由金属外壳和橡胶垫片组成。
因此,需要制作金属外壳模具和橡胶垫片模具。
3. 金属外壳生产
先将金属材料切割成指定尺寸,然后通过冲压或数控机床加工形成减振器的金属外壳。
加工过程中需要保证尺寸的精度和表面的光洁度。
4. 橡胶垫片生产
将橡胶材料加热至一定温度,然后倒入橡胶垫片模具中,用压力机压制成型。
加热可以使橡胶材料更加流动,压制可以使其成型并排除气泡。
5. 组装
将金属外壳和橡胶垫片组装在一起,通常可以使用胶水或者螺丝进行固定。
在组装过程中需要保证金属外壳和橡胶垫片的精
确对位。
6. 检测
对于生产好的减振器进行检测,主要包括外观检查、尺寸测量、质量检验等。
确保减振器的质量符合标准要求。
7. 包装
对检测合格的减振器进行包装,通常使用泡沫箱或纸箱进行包装,以保护减振器不受损坏。
以上就是减振器的生产工艺简要介绍。
在实际生产过程中,还需要注意操作人员的安全和环境保护,确保生产过程的高效和稳定。
此外,随着科技的发展和创新,减振器生产工艺也在不断改进和更新,以满足越来越高的质量要求。
机车用钛合金弹簧的设计与制备

机车用钛合金弹簧的设计与制备
杨海瑛;赵亮;应扬;曹祖涵;郭荻子;李磊
【期刊名称】《钛工业进展》
【年(卷),期】2024(41)2
【摘要】钛合金弹簧替代钢制弹簧应用于机车悬架弹簧可以减重40%~60%,而且钛合金弹簧具有良好的耐蚀性和阻尼特性,不仅能够抵御恶劣环境的腐蚀,增加机车的行驶里程,还能增强机车的操控性和乘架的舒适性。
通过赛车用悬架弹簧实例,详细介绍TB9钛合金弹簧的设计方法和制备过程。
计算得到钛合金悬架弹簧的螺旋角为9.45°,已经超出弹簧设计国家标准范围,因此对公式进行了修正。
此外,还研究了温度对TB9钛合金弹簧刚度的影响。
研究发现,随着温度的上升,TB9钛合金弹簧的刚度逐渐下降。
【总页数】4页(P31-34)
【作者】杨海瑛;赵亮;应扬;曹祖涵;郭荻子;李磊
【作者单位】西北有色金属研究院;西部金属材料股份有限公司
【正文语种】中文
【中图分类】TG146.23
【相关文献】
1.机车车辆截锥螺旋压缩弹簧减振设计与研究
2.基于AVR单片机的机车弹簧测试仪的设计
3.机车受电弓弓头弹簧系统的优化设计
4.准高速电力机车弹簧悬挂参数设计与机车横向稳定性初探
5.机车车辆弹簧支撑圈端部与有效圈间的间隙设计
因版权原因,仅展示原文概要,查看原文内容请购买。
- 1、下载文档前请自行甄别文档内容的完整性,平台不提供额外的编辑、内容补充、找答案等附加服务。
- 2、"仅部分预览"的文档,不可在线预览部分如存在完整性等问题,可反馈申请退款(可完整预览的文档不适用该条件!)。
- 3、如文档侵犯您的权益,请联系客服反馈,我们会尽快为您处理(人工客服工作时间:9:00-18:30)。
机车减震弹簧的制造工艺研究
0引言
弹簧行业在整个制造业当中虽然是一个小行业,但其所起到的作用是不可低估的。
国家的工业制造业、汽车工业要加快发展,作为基础件、零部件之一的弹簧行业就更加需要有一个发展的超前期,才能适应国家整个工业的快速发展。
另外,弹簧产品规模品种的扩大、质量水平的提高也是机械设备更新换代的需要和配套主机性能提高的需要,因此,整个国家工业的发展,弹簧产品是起到重要作用。
交通运输市场,包括为汽车/摩托车/柴油机和铁道等行业提供配套和维修件弹簧,这是弹簧行业目前最重要,最有发展前途的市场,销售额接近全行业的40%。
其中摩托车、电动车销售市场依旧很大,尚未限牌的大中城市和沿海发达地区对高档产品的需求和内陆小城市及农村市场对中低档产品的需求仍然具有很大的空间。
减震弹簧是机车减震器最重要的零件之一,是用于吸收运动冲击能量,使机车获得高平顺性、高舒适性的专用件。
减震弹簧设计与制造的优劣直接影响减震器的减震性能、寿命、经济性及整机的安全性。
1减震弹簧的选材与造型
1.1减震弹簧的选材
作为摩托车、电动车用弹簧, 长期处于反复受力和回复过程, 疲劳寿命需达到10万次以上,外力卸载后应回复到初始位置, 要求弹簧的塑性变形越小越好, 钢丝应具有较高的弹性极限, 较高的回复力, 要求屈服强度和抗拉强度较高。
[1]目前,市面上常用的有碳素弹簧钢、合金弹簧钢、不锈钢弹簧钢以及铜合金、镍合金和橡胶等。
本工艺采用65Mn钢,65Mn 钢属于碳素弹簧钢,主要生产成钢丝、钢带、用于制造各种截面较少的扁,圆弹簧,板簧和弹簧片等。
有着强度较高,淬透性较大,脱碳倾向小,价格低廉,切削性好等优点。
1.2减震弹簧的造型
机车用减震弹簧是承受压力的螺旋弹簧,也称为圆柱螺旋弹簧。
压缩弹簧一般用料的截面基本都是圆形,但形状和尺寸种类繁多,既有等直径、等节距, 也有变直径、变节距弹簧,不同的设计主要为满足安装空间、力值、刚度的要求。
表1为几种常见的等直径、不同节距弹簧的优缺点。
表1 等直径、不同节距减震弹簧的优缺点
2生产弹簧的主要仪器及设备
YH-680CNC电脑数控卷簧机,自动卷簧机是生产弹簧的专用设备, 它的高度自动化在提升生产效率、工艺水平等方面发挥了巨大的作用。
它把钢丝线材卷绕成一定形状的弹簧,供回火、端磨等后续工序处理。
自动卷簧机不仅可以卷制圆柱形螺旋弹簧,而且能卷制各种形状的变径、变距弹簧。
具有成形速度快、性能稳定强和精准度高等特点,真正实现了人机对话,具备一分钟弹簧成型的能力,并在保证速度、精度和性能的条件下,噪音低,操作更简便。
M7745K-9S数控弹簧双端面磨床,该机床具有上下两个磨头,其主轴位于同一轴线上,上下磨头由两个磨轮电机分别独立驱动。
磨头进给可以调速,上磨头砂轮磨损时,可以通过上磨轮补偿电机进行补偿,下砂轮磨损时,通过下磨轮补偿电机进行补偿。
另外,本机床采用双料盘交替进行工作,即一个磨削另一个进行检测货上、下料,可大大提高生产效率。
换盘方式可采用自动换盘或手动换盘。
RJC530连续式热风回火炉,也称输送带式电控回火炉(网带炉),采用进口PID智能化温度控制仪及完整的自动控制系统,在500℃炉温内,可按工艺要求设定任何温度,控温精度±3℃,配有热风搅拌装置,炉温精确均衡,回火工件质量稳定可靠。
另外还需要全自动送线架,抛丸机,强压机,整形工具等,这边就不再一一做具体说明。
3生产工艺
3.1生产工艺流程
下面以电动车前减震弹簧(等直径、变节距弹簧)的常用尺寸Ø3.3mm*外径21.5mm*高度215mm*36圈(如图)1为例,来说明弹簧的加工工艺流程。
加工时,可按以下工艺执行:卷簧-热处理-磨两端面-抛丸-强压-整形-二次回火-表面处理。
图 1电动车前减震弹簧尺寸图
技术要求如下:
①旋向:右旋②总圈数36,有效圈数34,密圈17,密圈解距6.54,拐点55,疏圈17圈③去应力回火处理④两端面磨平,去除内毛刺⑤在ps载荷下做永久变形不能大于自由高度的0.3% ⑥表面上油处理⑦其余技术要求按GB1239.2.2级精度执行
3.2主要工序
3.2.1卷簧处理
在加工前, 根据弹簧的线径、外径、长度、节距等要求先进行弹簧特征数据转换,编制程序。
65Mn钢丝经KJS-1000自动送线架送YH-680CNC自动卷簧机,KJS-1000全自动送线架可以承载1吨以内的钢丝,在运转过程中通过自动调节送线速度,使配套主机设备与它的送线速度保持同步,当发生绞线、断线或送线完毕后,会发出报警信号并自动停机。
3.2.2热处理
经卷簧机卷制后的弹簧,内部产生了较高的内应力,必须进行去应力退货(俗称低温回火)。
回火处理的目的之一是能提升钢材的抗力强度,保证其能正常的进行回弹,保证弹簧的效果。
回火之后的弹簧可以将抗压强度提升到百分之九十以上,减少了弹簧的抗蠕变性。
第二就是消除金属丝冷加工和弹簧卷绕成时所产生的残余应力,它可以显著地改善冷成形弹簧的力学性能和使用特性。
[2]第三是稳定弹簧形状,回火15-30分钟后弹簧外圈会缩到一个稳定水平。
因此,卷制好的弹簧将会由人工送入连续式热风回火炉中进行低温回火定型,回火炉温度设定为350˚C,时间为半小时。
弹簧回火处理需要注意的事项如下:
①避免以提高温度缩短时间的方式进行弹簧回火处理。
②硬度:随回火温度的升高,硬度稍微上升后就下降。
疲劳性能最好的温度略低于硬度最大的温度。
③缩径:碳钢弹簧回火时外径会缩小,所以卷簧时应预留一些尺寸。
④弹簧回火色:回火色与温度和钢丝表面的残留物有关,颜色不均匀与温度分布或炉膛内的气流有关。
如果期望颜色均匀,要管理好炉子及装料方式;如果局部有油或指印,回火后会变色。
⑤回火温度:一般采用的回火温度在250-350℃,如采用200-250℃处理钢丝,虽然可以提高强度,但塑韧性也会损失,可导致拉簧做弯钩或扭簧弯腿时发生断裂。
3.3磨簧
弹簧经卷簧机卷制并回火后,形成的是弹簧半成品,两个端面不平行,需经磨簧机将两端面磨平,目的之一是使压缩面由点接触改为线接触或者面接触,增加受力面积,避免接触面刮伤,第二是使两端面与弹簧的轴线保持一定的垂直度。
3.4抛丸处理
弹簧要求有较高的表面质量,划痕、折叠、氧化脱碳等表面缺陷往往会成为弹簧工作时应力集中的地方和疲劳断裂源。
抛丸处理是目前应用最广泛的改善弹簧表面质量的方法之一。
抛丸处理就是通过直径0.3-0.4mm的不锈钢丸粒高速撞击弹簧表面,使弹簧表层发生塑性变形,从而形成一定厚度的表面强化层,不仅改善弹簧表面质量,提高表面强度,使表面处于压应力状态,从而提高弹簧疲劳强度(一般可提高20%-35%),将弹簧的使用寿命提高3-10倍。
3.5强压处理
弹簧受到长期反复静压作用,其自由高度将有一定缩减,力学性能也无法一直保持设计要求。
因此, 弹簧制成后都要进行强压处理,使弹簧在超过弹簧极限变形状态保持一定时间, 产生小塑性变形,获得强化效应,从而提高弹簧承受静载荷及有限次动载荷的能力,一般可提高其承载能力约25%。
强压处理是把弹簧压缩到产生与工作应力相反的有益的残余应力,如果强压处理适当,处理后的弹簧自由高度稳定,并清除弹簧使用早期弹力衰减,以保证弹簧工作可靠性,在同样的工作条件下,弹簧的疲劳寿命可以提高5%—35%。
[3]强压方法是利用强压机用较慢速度(约1min)把弹簧压至规定高度,然后缓慢放开(约1min),使弹簧产生塑性变形。
3.6手工整形
根据图纸的要求,每个弹簧必须在专用的整形台上逐个整形,主要任务是保证其垂直度
和总长度。
3.7二次回火
为进一步消除弹簧内部的内应力,定型弹簧的形状和尺寸,同时改善弹簧的物理性能,提升弹簧的疲劳寿命,减少弹簧在工作中的形变量,调整钢丝的抗拉强度和硬度等等。
弹簧制成后需二次回火,温度设定为300 ˚C ,10分钟。
3.8表面处理
弹簧在制造、存放、使用等过程中,经常会遭受周围介质的腐蚀。
由于弹簧在工作时是靠弹力发挥作用,弹簧被腐蚀后弹力会发生改变而丧失功能。
所以防止弹簧的腐蚀可以保证弹簧的工作稳定,并延长其使用寿命。
弹簧一般是用喷塑或电镀的方法以获得金属保护层。
电镀保护层不但可以保护弹簧不受腐蚀,还能改善弹簧的外观。
有些电镀金属还能改善弹簧的工作性能,比如提高弹簧的表面硬度,增加弹簧的抗磨损能力,提高热稳定性,防止射线腐蚀等。
镉比较安定,耐腐蚀性能较强。
镉镀层光亮美观、质软、可塑性好,最适宜于弹簧作保护层。
4结束语
长期大量的生产实践表明,按本工艺流程来生产减震弹簧,生产效率高,弹簧在疲劳寿命,压缩性能,抗永久变形等方面具有良好的性能,完全能满足客户的技术和性能要求。