动力匹配设计规范
动力机器基础设计规范 GB 50040-96
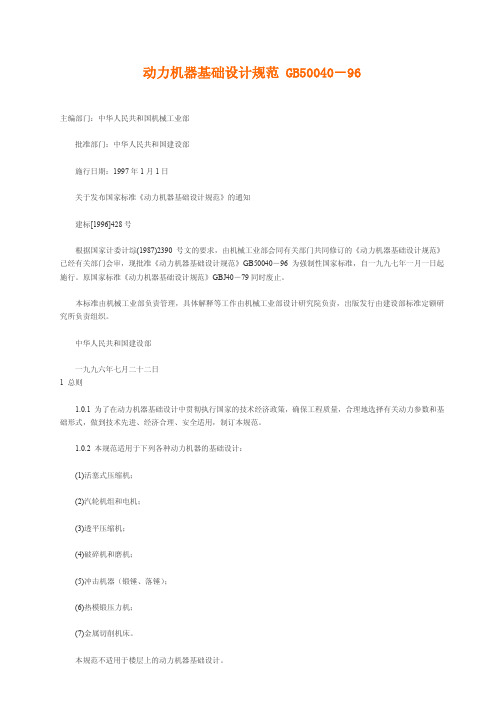
动力机器基础设计规范 GB50040-96主编部门:中华人民共和国机械工业部批准部门:中华人民共和国建设部施行日期:1997年1月1日关于发布国家标准《动力机器基础设计规范》的通知建标[1996]428号根据国家计委计综(1987)2390号文的要求,由机械工业部会同有关部门共同修订的《动力机器基础设计规范》已经有关部门会审,现批准《动力机器基础设计规范》GB50040-96为强制性国家标准,自一九九七年一月一日起施行。
原国家标准《动力机器基础设计规范》GBJ40-79同时废止。
本标准由机械工业部负责管理,具体解释等工作由机械工业部设计研究院负责,出版发行由建设部标准定额研究所负责组织。
中华人民共和国建设部一九九六年七月二十二日1 总则1.0.1 为了在动力机器基础设计中贯彻执行国家的技术经济政策,确保工程质量,合理地选择有关动力参数和基础形式,做到技术先进、经济合理、安全适用,制订本规范。
1.0.2 本规范适用于下列各种动力机器的基础设计:(1)活塞式压缩机;(2)汽轮机组和电机;(3)透平压缩机;(4)破碎机和磨机;(5)冲击机器(锻锤、落锤);(6)热模锻压力机;(7)金属切削机床。
1.0.3 动力机器基础设计时,除采用本规范外,尚应符合国家现行有关标准、规范的规定。
2 术语、符号2.1 术语2.1.1 基组foundation set动力机器基础和基础上的机器、附属设备、填土的总称。
2.1.2 当量荷载equivalent load为便于分析而采用的与作用于原振动系统的动荷载相当的静荷载。
2.1.3 框架式基础frame type foundation由顶层梁板、柱和底板连接而构成的基础。
2.1.4 墙式基础wall type foundation由顶板、纵横墙和底板连接而构成的基础。
2.1.5 地基刚度stiffness of subsoil地基抵抗变形的能力,其值为施加于地基上的力(力矩)与它引起的线变位(角变位)之比。
整车动力选型匹配
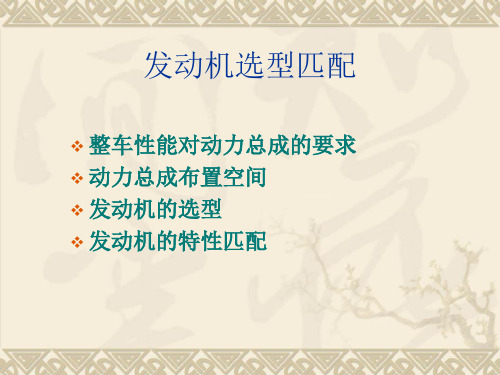
从图8—18中可知,最高挡时与发动机最 大功率相对应的车速一般等于或稍小于最 高车速。从功率平衡图上也可以分析出后 备功率的大小。当汽车在良好的水平路面 以车速等速行驶时,汽车的阻力功率为 (图8—18)。此时,驾驶员并不需要将节 气门全开而仅需维持部分开度、使发动机 的功率曲线如图中的虚线所示,以维持汽 车的等速行驶。发动机在此车速下所能发 出的最大功率为 ac ,两者之差为 ab ,称 为后备功率。在一般情况下,维持汽车等 速行驶所需的发动机功率并不大,发动机 油量调节机构位置在油量较低的位置;当 需要爬坡或加速时。驾驶员向加油方向调 整油量调节机构,使汽车的后备功率充分 发挥作用。显然,汽车的后备功率越大, 汽车的动力性能越好。
发动机先进技术:
MPI 多点燃油喷射 VVT 可变气门正时(Variable Valve Timing) TCI 增压中冷(Turbo Charged Intercooled) ETC 电子节气门(Electronic Throttle Control) CAI 可控均质燃烧 HCCI 均质压燃(Homegen Charge Compression Ignition) AIS 空气喷射系统(Air-assisted Injection System)
4.汽车测功机 例 转鼓试验台 优点: ①条件控制,数据准确、方便; ②不受气候条件限制; ③可测多个参数如排放; ④质量法、体积法均可。 缺点: ①空气阻力、滚动阻力是模拟的; ②惯性力也不精确; ③冷却条件不一样。
三、汽车燃料经济性的计算方法
1.等速行驶工况燃油消耗量的计算 1 g e , 阻力功率 P 已知:万有特性 n m ( Pf Pw ) Pg
发动机的选型匹配:
汽车研发:动力总成匹配设计与开发!

汽车研发:动力总成匹配设计与开发!速度与激情都是大家追求的目标,要实现这个目标,就需要下图中这样的美女小姐姐,还需要一辆这样的“野兽”,作为野兽,就需要有够劲爆的动力!今天就和漫谈君一起来看看动力总成匹配设计与开发漫谈君说好消息:汽车大漫谈4群已开通,话说都是汽车研发工程师,每天都在分享技术,有需要进群的童鞋,加漫谈君微信:autotechstudy,备注名称+专业哟,方便邀请进群!一、动力总成匹配的任务根据汽车的基本参数,通过计算选择一款发动机,以及与之匹配的轮胎、离合器、变速箱、传动轴和驱动桥。
并且对各个部件进行验算,是否各个部件匹配的良好,最后画出一张整车总体布置草图。
电动汽车采用电动轮驱动时,传动装置的多数部件常常可以忽略。
因为电动机可以带负载启动,所以电动汽车上无需传统内燃机汽车的离合器。
因为驱动电机的旋向可以通过电路控制实现变换,所以电动汽车无需内燃机汽车变速器中的倒档。
二、整车动力匹配的结构1发动机2离合器3变速箱4传动轴三、整车动力系统的性能要求1加速特性加速特性可以通过改进发动机的功率和燃油经济性来实现,方法如下:2换挡特性1)换挡反应:换挡延迟和延续;2)换挡质量:发动机速度改变扭矩改变能够平稳的传递;3)换挡进程:提供平稳的,连续的和可预见的发动机运行状态。
匹配动力系统的动力输出和加速要求。
3声音质量(NVH)使来自动力系统的声音与顾客所希望听到的声音一致。
4汽车性能开发以目标区域标准法规为基本要求,通过对市场顾客语言研究与benchmark研究,以竞争策略为指导,结合公司技术生产能力设定整车性能目标。
要保证性能指标的真正实现,必须将性能分解指标体现在相关系统部件结构设计上,并在系统及部件中最终体现,作为系统及部件性能指标验收的依据。
同时,对整车各系统及零部件选型报告进行确认,各系统模块按目标分解要求对零部件进行质量特性控制,保证满足整车及系统要求。
四、动力系统各部件的选型1发动机的选择1)发动机最大功率确定汽车的动力性能很大程度上取决于发动机的最大功率。
6-动力总成参数匹配与优化设计
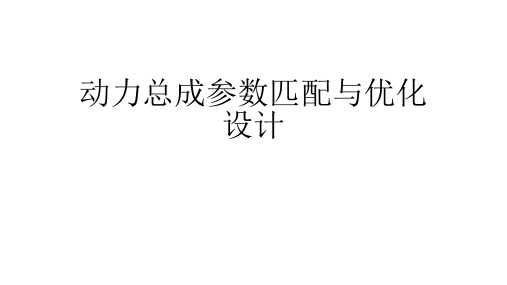
设计计算
对确定的车型的静态参数,动力性及通过性的定量验证。先 在理论上得到整车的性能参数
整车重量、轴荷分配及重心计算
按下列公式分别计算出汽车的最大总质量,前轴轴载质量, 后桥轴载质量及质心位置
M mi
i 1 n
M 1 m1i
i 1
n
M 2 m2i
i 1
n
M1i mi (1 Xi / L)
整车稳定性计算
1)汽车纵向行驶稳定性计算 汽车的纵向行驶稳定性即保证汽车上坡时不致纵向翻车,其 条件为: b
hg
b-质心距后桥的距离; hg-汽车质心高 ψ-道路附着系数
整车稳定性计算
2) 汽车横向稳定性计算 静态侧翻角计算:
B arctg 2 hg
B——前轮距 静态侧翻角β,《客车通用技术条件》中规定应大于35° 计算进行比较,然后优化
动力性能计算---仿真
4)加速性能分析 车辆从静止起步,全油门加速,计算车速从0-50km/h的加速 时间。 设置最高车速、满载爬坡度分析、制动距离分析。
动力性能计算
根据理论计算和仿真,基本可以确定待选用电机的基本参数, 比如最大功率、最大扭矩、最大转速、额定工作电压范围、工作电 流范围等等; 电池的基本使用参数:母线电压、母线电流、使用电芯及 PACK方式等等。
整车重量、轴荷分配及重心计算
计算的结构,前轴、后桥的载荷分配满足《客车通用技术条 件》中前轴轴载质量不小于车辆总质量的25%,驱动桥的轴载质量 不小于车辆总质量的50%的要求。 如果计算不符合要求,则进行优化。
动力性能计算---根据最高车速确定最大转速
P max
11990 3260 2540 6000 2310 2640/3350 7/7 N+1
动力匹配设计
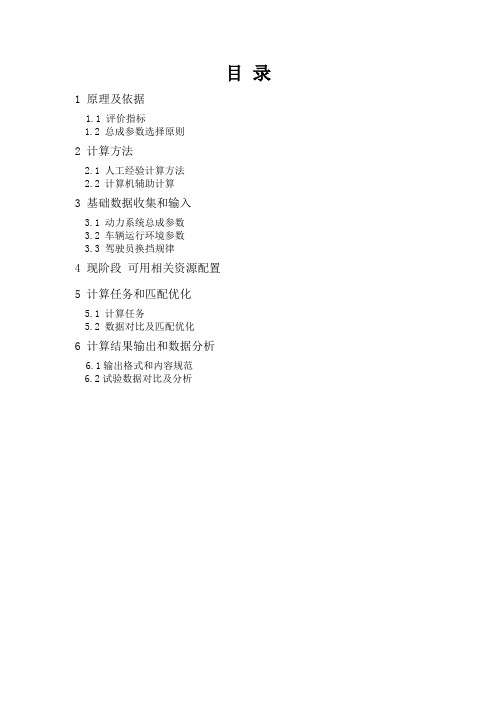
也就是确定变速器Ⅰ档传动比。 汽车爬大坡时车速很低,可以忽略空气阻力,汽车的最大驱动力 应为
Ft max F f Fi max
(1-4) (1-5) (1-6)
或 即
Ttq max i g1i0T r
i g1
6 计算结果输出和数据分析
6.1 输出格式和内容规范 6.2 试验数据对比及分析
符号及其意义
代号 物理意义 发动机额定功率下的转速 满载时车轮滚动半径 车速 汽车质量 重力加速度 汽车重力 迎风面积 发动机最大扭矩 发动机功率 汽车驱动力 空气阻力 坡度阻力 加速阻力 滚动阻力 阻力功率 燃油消耗率 燃油密度 坡度 动力因数 变速器传动比 主减速器传动比 传动系机械效率 滚动阻力系数 空气阻力系数 道路附着系数 柴油取为 0.81~0.83 r/min m km/h kg m/s N m
汽车比功率 1000 Pe CD A fg 3 u a max u a max m 3.6T 76.14mT
(1-2)
我国GB7258-2004《机动车运行安全技术条件》规定:三轮汽车、 低速货车及拖拉机运输机组的比功率不应小于4.0 kW/t,除无轨电车 外的其它机动车的比功率不允许小于 5.0 kW/t。 1.2.2 传动系最小与最大传动比的选择 汽车大多时间以最高档行驶,即用最小传动比的档位行驶。因此 最小传动比的选定很重要。 传动系的总传动比是传动系中各部件传动比的乘积,即
目 录
1 原理及依据
1.1 评价指标 1.2 总成参数选择原则
2 计算方法
2.1 人工经验计算方法 2.2 计算机辅助计算
3 基础数据收集和输入
(完整版)整车动力选型匹配
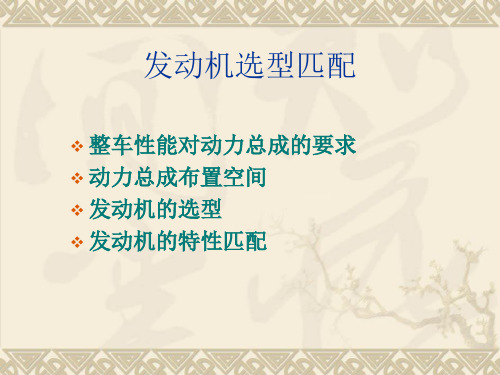
电子 风扇
前围板
一、布置空间的要求
一、布置空间的要求
一、布置空间的要求
图示为D19柴油机在V22机舱中的布置空间
二、发动机的选型
❖ 1、发动机结构 ❖ 2、发动机的外特性
负荷特性、速度特性 ❖ 3、发动机的万有特性
1、发动机结构
❖ 发动机的基本结构型式 ❖ 发动机的基本参数 ❖ 发动机的先进技术
❖ 发动机的选型匹配: 主要表现为
❖
动力性匹配
❖
经济性匹配
(—)汽车的驱动力
❖ 汽车发动机输出的转矩,经传动
系作用在汽车的驱动轮上,受力
简图如图8—10所示。 从中可以
看出,作用在驱动轮上的转矩Ttq
使车轮对路面产生一个圆周切向
力F0,即车轮对道路的作用力; 而道路对车轮的反作用力Ft是驱 动汽车行驶的外力,通常被称为
发动机先进技术:
▪ MPI 多点燃油喷射 ▪ VVT 可变气门正时(Variable Valve Timing) ▪ TCI 增压中冷(Turbo Charged Intercooled) ▪ ETC 电子节气门(Electronic Throttle Control) ▪ CAI 可控均质燃烧 ▪ HCCI 均质压燃(Homegen Charge Compression Ignition) ▪ AIS 空气喷射系统(Air-assisted Injection System)
万有特性曲线一般是以转速n为横坐标,以负荷(平均有效压力pme) 为纵坐标。在图上绘出若干条等油耗曲线和等功率曲线。两种类型 内燃机典型的万有特性如图所示。根据需要,还可在万有特性曲线 上绘出等节气门开度线、等排放线、等过量空气系数线等。
❖ 在万有特性图上,最内层的等燃油消耗率曲线相当于内燃 机运转的最经济区域,等值曲线越向外,经济性越差。
动力系统匹配和选型设计规范
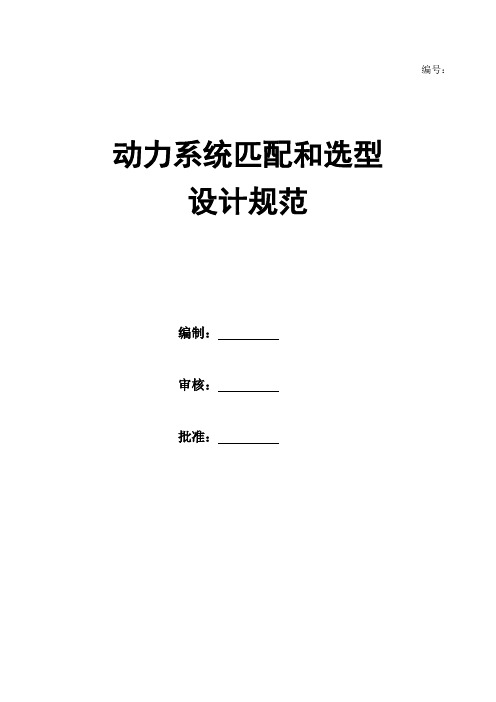
编号:动力系统匹配和选型设计规范编制:审核:批准:目录前言 21.适用范围 32.引用标准 33.选型匹配设计主要工作内容及流程 44.产品策划 55.资源调查 56.分析与筛选 67.设计参数输入 68.预布置与匹配分析计算 69.法规对策分析18前言本标准是为了规范我公司汽车动力总成(MT)匹配设计而编制。
标准中对设计程序、参数的输入、参照标准、匹配计算等方面进行了描述和规定,此标准可作为今后汽车动力总成(MT)匹配设计参考的规范性指导文件。
1.适用范围本方法适用于基于现有动力总成资源,选择满足整车设计要求的动力总成(MT)的一般方法与原则。
2.引用标准GB 16170-1996 汽车定置噪声限制GB 1495-2002 汽车加速行驶车外噪声限值及测量方法GB/T12536-1990 汽车滑行试验方法GB/T12543-2009 汽车加速性能试验方法GB/T12544-1990 汽车最高车速试验方法GB/T12539-1990 汽车爬陡坡试验方法GB/T12545.1- 2008 汽车燃料消耗量试验方法GB/T18352.3- 2005 轻型汽车污染物排放限值测量方法3.选型匹配设计主要工作内容及流程4.产品策划产品策划的目的是依据整车设计要求,确定动力总成选型的范围、条件及基本技术指标。
根据整车设计任务书要求,确定以下输入条件:整车输入条件—车辆类型;4市场定位—经济型、中级或高级;动力总成布置型式—前置后驱、后置后驱;整车尺寸参数—外形尺寸、轮距、轴距、整备质量、总质量、离地间隙;前悬和后悬;轮胎规格;风阻系数;整车重量参数—整备质量、载客量、总质量、轴荷分配;整车目标性能—动力性(最高车速、加速时间、汽车的比功率和比转矩指标、最大爬坡度)、经济性指标、排放水平;产品策划的内容是根据整车设计要求,确定资源调查的具体指标范围:型式(类型)、发动机功率范围、对配套变速器的要求。
5.资源调查根据设计任务书及产品策划要求进行资源调查,调查市场上发动机及变速器资源及相关信息,包括:(1)发动机、变速器技术参数外形尺寸—长宽高及相对变速器输出轴尺寸技术指标—功率、扭矩、速比、排放水平技术状态—开发阶段、定型产品、匹配车型、批量生产(2)品牌及产品来源—国产化、自主研发、合作开发(3)服务—配套车型、附件提供状态、配套体系完整性(4)风险性分析—配套意向、批量供货能力资源调查方法为信息收集与厂家专访。
动力系统匹配基础

2 ) 最小传动比的选择 3 ) 最大传动比的选择 4 )传动系档数与各档传动比的选择 5 ) 利用燃油经济性-加速时间曲线确定动力装置 参数
应用工程部内训课程
1)发动机功率的选择
先从保证汽车预期的最高车速来初步选择发动机应有 的功率。〔从动力性角度出发〕 根据最高车速计算发动机最大功率 1 Pe Pf Pw
提高换档舒适性
减小速比级差
应用工程部内训课程
变速器档位数对加速时间的影响
9档箱连续换档 加速时间 16档箱连续换 档加速时间
此积分面积代表 由速度u1到速度 u2的加速时间
由于档位密布, 积分面积减小
实际操作中,由于驾驶员的因素无法保证理论分析的效果,但是对于AMT 变速箱,可以按照理论的换档点进行换档,从而减少加速时间。
应用工程部内训课程
应用工程部内训课程
应用工程部内训课程
应用工程部内训课程
实际上,对于挡位较少(如 5 挡以下)的变速 器,各挡传动比之间的比值常常并不正好相等,即 并不是正好按等比级数来分配的。这主要是因为各 挡利用率差别很大的缘故。
汽车主要是用较高档行驶。例如中型货车 5 挡 变速器中的 l、2、3 三个挡位的总利用率仅为 10% -15%,所以较高档位相邻两挡间的传动比的间隔 应小些,特别是最高挡与次高挡之间更应小些。
配送
市内及城市之间
矿山工地
80 40 凹凸不平 40~70
90~110 70~80 高速公路 60~100
80~90 55~65 良好路面 50~70
90~100 60~70 良好路面 30~40
应用工程部内训课程
1)不同工况下动力系统的匹配要求
长距离运输:
电动汽车动力匹配计算规范(纯电动).
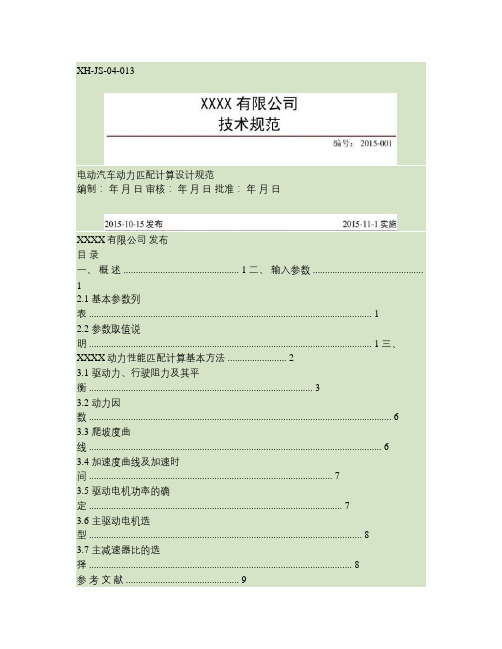
XH-JS-04-013电动汽车动力匹配计算设计规范编制:年月日审核:年月日批准:年月日XXXX有限公司发布目录一、概述 ............................................... 1 二、输入参数 (1)2.1 基本参数列表 (1)2.2 参数取值说明 ................................................................................................................... 1 三、XXXX动力性能匹配计算基本方法 (2)3.1 驱动力、行驶阻力及其平衡 (3)3.2 动力因数 (6)3.3 爬坡度曲线 (6)3.4 加速度曲线及加速时间 (7)3.5 驱动电机功率的确定 (7)3.6 主驱动电机选型 (8)3.7 主减速器比的选择 (8)参考文献 (9)一、概述汽车作为一种运输工具,运输效率的高低在很大程度上取决于汽车的动力性。
动力性是各种性能中最基本、最重要的性能之一。
动力性的好坏,直接影到汽车在城市和城际公路上的使用情况。
因此在新车开发阶段,必须进行动力性匹配计算,以判断设计方案是否满足设计目标和使用要求。
二、输入参数2.1 基本参数列表进行动力匹配计算需首先按确定整车和发动机基本参数,详细精确的基本参数是保证计算结果精度的基础。
下表是XXXX动力匹配计算必须的基本参数,其中发动机参数将在后文专题描述。
表1动力匹配计算输入参数表。
2.2 参数取值说明1)迎风面积迎风面积定义为车辆行驶方向的投影面积,可以通过三维数模的测量得到,三维数据不健全则通过设计总布置图测得。
XXXX车型迎风面积为A1一般取值5-8 m2 。
2)动力传动系统机械效率根据XXXX车型动力传动系统的具体结构,传动系统的机械效率ηT主要由主驱动电机传动效率、传动轴万向节传动效率、主减速器传动效率等部分串联组成。
电动汽车动力匹配设计规范方案
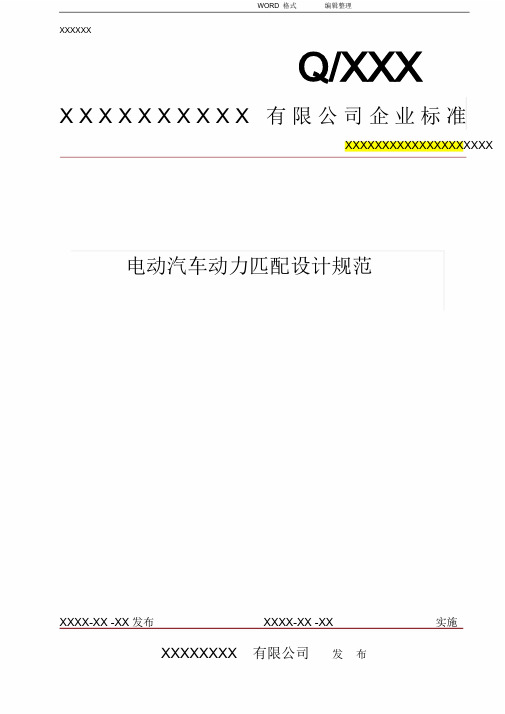
WORD 格式编辑整理XXXXXXQ/XXXX X X X X X X X X X 有限公司企业标准XXXXXXXXXXXXXXXXXXXX 电动汽车动力匹配设计规范XXXX-XX -XX发布XXXX-XX -XX 实施XXXXXXXX 有限公司发布专业知识分享目次前言 (Ⅱ)1 范围 (1)2 规范性引用文件 (1)3 术语和定义 (1)4 技术要求 (3)4.1 评价指标 (3)4.2 计算方法 (4)4.3 基础数据收集和输入 (10)4.4 计算任务和匹配优化 (10)4.5 计算结果输入及数据分析 (13)前言我公司缺少关于动力匹配方面的设计规范,给整车动力性、经济性方面的计算造成障碍。
自本规范下发之日起,本文件将指导后续工作中动力性、经济性的计算。
本标准按照GB/T 1.1 —2009 给出的规则起草。
本标准由XXXX提出。
本标准由XXXX负责起草。
本标准主要起草人:XXX本标准于XXXX年XX月首次发布。
电动汽车动力匹配设计规范1 范围本规范规定了电动汽车动力匹配设计规范的术语和定义、技术要求、试验方法、检验规则、标志、包装、运输和贮存。
本规范适用于XXXX整车动力性能匹配与计算。
2 规范性引用文件下列文件中的条款通过本标准的引用而成为本标准的条款。
凡是注日期的引用文件,其随后所有的修改单(不包括勘误的内容)或修订版均不适用于本标准,凡是不注日期的引用文件,其最新版本适用于本标准。
GB/T 12534-1990 汽车道路试验方法通则GB/T 12544-2012 汽车最高车速试验方法GB/T 12543-2009 汽车加速性能试验方法GB/T 18386-2005 电动汽车能量消耗率和续驶里程试验方法GB/T 19596-2004 电动汽车术语3 术语和定义GB/T 19596 中界定的术语和定义适用于本标准。
下列术语和定义适用于本文件。
4.6续驶里程电动汽车在动力蓄电池完全充电状态下,以已定的行驶工况,能连续行程的最大距离,单位为km。
电动汽车动力匹配设计规范模板

物理意义
电动机额定功率下的转速 满载时车轮滚动半径 车速 整车质量 重力加速度 整车重力 迎风面积 电动机最大扭矩
电动机功率 电动汽车驱动力
空气阻力
坡度阻力
加速阻力
2
表 1 本规范所引用的符号及意义
单位
r/min m
km/h kg m/s" N m2 N•m
kW N
N
N
N
Ff
滚动阻力
Q/XXXXXXXXXX-201X N
3
代号
•
D1
4
□T
f
5
0
P
续表(1)
物理意义
坡度 动力因数 主减速器传动比
传动系机械效率 滚动阻力系数
空气阻力系数 道路附着系数
阻力功率
单位
kW
4 原理及依据
4.1 评价指标 4.1.1 整车动力性评价指标
汽车的动力性是指汽车在良好路面上直线行驶时由汽车受到的纵向外力决定的,所能达到的平均行驶速 度。从获得尽可能高的平均行驶速度的观点出发,汽车的动力性主要可由以下三个指标来评定。4.1.1.1 最高车 速
D=G
Dg=fcos 缢+SU1 缢
max
(1-8)
用 cos 仏=Jl-sin—代入整理可得: 爬坡
时%• a—arcsinxJ1_口二+/
1+广
(1-9)
可忽略
max
不计。
然后D根ln据nx求出最大爬坡度。
由公为 的式动I(档1力-5)和公式(1-9)计算结果可分析,若公式(1-5)计算最大爬坡度大于公式(1-9)计算最人爬坡度,则说明整车最大
4. 2.1 人工经验计算方法
动力匹配设计规范
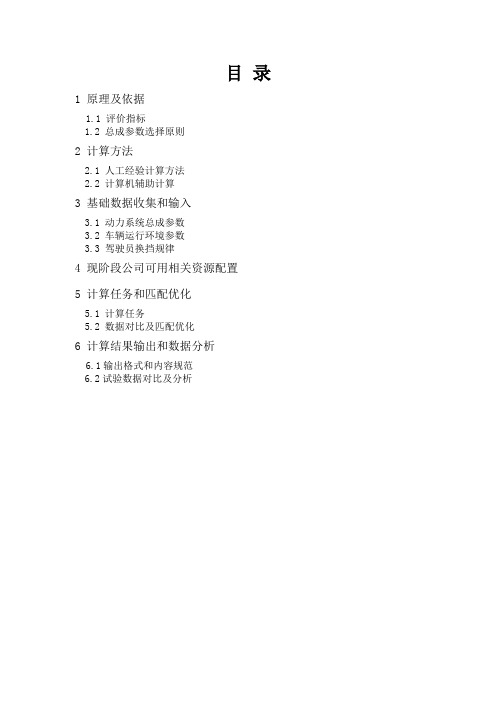
目录1 原理及依据1.1 评价指标1.2 总成参数选择原则2 计算方法2.1 人工经验计算方法2.2 计算机辅助计算3 基础数据收集和输入3.1 动力系统总成参数3.2 车辆运行环境参数3.3 驾驶员换挡规律4 现阶段公司可用相关资源配置5 计算任务和匹配优化5.1 计算任务5.2 数据对比及匹配优化6 计算结果输出和数据分析6.1输出格式和内容规范6.2试验数据对比及分析一规范适用范围本规范规定了动力总成系统传统匹配设计方法及利用AVL Cruise软件对整车动力性和燃油经济性进行计算,并对动力总成系统配置优化。
本规范适用于目前我公司所有车型。
二规范性引用文件GB7258-2004 《机动车运行安全技术条件》。
本规范中所引用的符号及意义动力匹配设计规范1 原理及依据1.1评价指标1.1.1汽车动力性评价指标汽车的动力性是指汽车在良好路面上直线行驶时由汽车受到的纵向外力决定的,所能达到的平均行驶速度。
从获得尽可能高的平均行驶速度的观点出发,汽车的动力性主要可由以下三个指标来评定。
1.1.1.1最高车速最高车速U max是指在水平良好的路面上汽车能达到的最高行驶速度。
它仅仅反映汽车本身具有的极限能力,并不反映汽车实际行驶中的平均速度。
1.1.1.2加速性能汽车的加速能力常用原地起步连续换档加速时间与最高档或次高档加速时间来表示。
原地起步连续换档的加速时间是指用一档或二档起步,以最大加速度按最佳换档时间逐步换至最高档,加速至某一预定的距离或车速所需要的时间。
该项指标反映了汽车在各种车速下的平均动力性。
最高档或次高档加速时间是指用最高档或次高档由某一较低车速全力加速至某一高速所需要的时间。
因为超车时汽车与被超汽车并行,容易发生安全事故,所以最高档或次高档加速能力强,行驶就更安全。
1.1.1.3爬坡性能汽车的爬坡能力是用满载时汽车在良好路面上的最大爬坡度i max 来表示的。
显然,最大爬坡度是指一档时的最大爬坡度。
动力总成悬置系统匹配设计指南

目次
1 范围......................................................................................................................................................................1 2 规范性引用文件 ..................................................................................................................................................1 3 符号定义 ..............................................................................................................................................................1 4 动力总成悬置系统的基本知识 ..........................................................................................................................2
2 规范性引用文件
下列文件对本文件的引用是必不可少的。凡是注日期的引用文件,仅注日期的版本适用于本文件。 凡是不注日期的引用文件,其最新版本(包括所有的修改单)适用于本文件。
GB/T 3512 硫化橡胶或热塑性橡胶热空气加速老化和耐热试验 GB/T 7759 硫化橡胶、热塑性橡胶 常温、高温和低温下压缩永久变形测定 GB/T 7762 硫化橡胶或热塑性橡胶 耐臭氧龟裂 静态拉伸试验 GB/T 528 硫化橡胶或热塑性橡胶拉伸应力应变性能的测定 GB/T 531.1 硫化橡胶或热塑性橡胶压入硬度试验方法第一部分:邵氏硬度计法(邵尔硬度) GB/T 1682 硫化橡胶 低温脆性的测定 单试样法 Q/J B019 整车金属零部件涂层技术条件
动力总成悬置系统匹配设计规范

动力总成悬置系统匹配设计规范一、悬置系统主要作用 (1)二、元件的主要种类 (1)三、悬置系统的设计指标 (2)四、悬置系统设计参数的输入 (3)1、动力总成的惯性参数 (3)2、动力总成悬置系统的位置数据 (4)3、动力总成悬置系统的刚度数据 (4)4、变速器的各挡速比和主减速比 (5)5、发动机的其他参数 (5)6、动力总成悬置系统及周边的相关数模 (5)五、总成悬置系统的解耦设计及固有频率的合理配置 (5)1、解耦设计的原因 (5)2、固有频率的合理配置 (6)3、悬置系统解耦特性和固有频率的计算方法 (6)4、解耦和固有频率的合理配置的评价方法 (9)5、悬置系统解耦计算和固有频率配置的目的 (9)六、悬置系统的工况计算 (10)七、悬置支架设计 (12)八、置系统设计时应遵循的主要规范 (12)九、结语 (16)一、悬置系统主要作用发动机悬置是指专门设计制造的可以作为一个独立系统进行装备使用的安装在发动机与汽车底盘之间,以隔离(减少)发动机振动能量向周围环境的传播和影响为目的的隔振系统。
合理设计和使用发动机悬置,可以明显降低动力总成及车体的振动水平,减少系统传递给车体的激振力,以及由此激发的车身钣合金和底盘相关零件的振动和噪声,从而明显提高车辆的耐久性和乘坐舒适性。
悬置系统的主要作用如下:1、固定并支承汽车动力总成;悬置首先是一个支撑元件、它必须能支承发动机总成的重量,使其不至于产生过大的静态位移而影响正常工作。
从支承的角度考虑,要求悬置刚度越高越好;从隔振的角度考虑,要求悬置的刚度越低越好。
因此悬置要有合适的刚度。
2、限位作用发动机在受到各种干扰力(如制动、加速或其他动载荷)作用的情况下,悬置能有效的限制其最大位移,以避免发生与相邻件的碰撞与干涉,确保发动机能正常工作。
衰减作用于动力总成上的一切动态力和对车身造成的冲击。
3、隔振降噪作用承受和衰减动力总成内部因发动机不平衡旋转和平移质量产生的往复惯性力、力矩和不平衡扭矩;隔离发动机激励而引起的车架或车身的振动。
电动汽车动力匹配方案设计成果特点

电动汽车动力匹配方案设计成果特点一、引言随着环境保护意识的提高和能源消耗问题的日益凸显,电动汽车作为一种绿色环保的交通工具逐渐受到人们的关注和青睐。
而电动汽车的核心之一就是动力匹配方案设计,它直接关系到车辆的性能、续航里程和用户体验。
本文将就电动汽车动力匹配方案设计的成果特点进行全面、详细、完整地探讨。
二、动力匹配方案的基本原则电动汽车动力匹配方案的设计需要考虑多个因素,包括电池容量、电机功率、驱动系统效率等。
在设计过程中,我们需要遵循以下基本原则:2.1 性能匹配原则电池容量、电机功率和驱动系统效率需要相互匹配,以充分发挥电动汽车的性能潜力。
如果电池容量太小,将限制续航里程;如果电机功率过大,将导致能源浪费和车辆安全问题;如果驱动系统效率低下,将增加能源消耗。
2.2 续航里程原则动力匹配方案设计的关键目标之一是实现较长的续航里程。
通过合理设计电池容量、车重、空气动力学性能等因素,最大限度地延长电动汽车的行驶里程,提高用户的使用便利性和体验。
2.3 能源利用率原则电动汽车作为一种绿色环保的交通工具,应尽可能提高能源利用率,减少能源的浪费和污染。
因此,在动力匹配方案设计中,需要合理选择电池类型和电机控制策略,以提高能源的转化效率和利用率。
2.4 安全可靠原则电动汽车动力匹配方案的设计还需要考虑安全可靠性。
通过合理选择电池和电机的工作参数,建立完善的电池管理系统和安全保护装置,保证车辆在正常使用和紧急情况下的安全性和可靠性。
三、电动汽车动力匹配方案设计成果特点电动汽车动力匹配方案设计的成果特点主要体现在以下几个方面:3.1 多种方案对比在电动汽车动力匹配方案设计过程中,我们需要对多种方案进行对比分析。
通过对不同电池容量、不同电机功率和不同驱动系统效率的方案进行模拟和优化,找出最优的方案,以满足电动汽车的性能和续航里程需求。
3.2 多维度参数优化动力匹配方案设计需要考虑多个参数的综合优化。
除了电池容量和电机功率,还需要考虑电机转速、驱动系统传动比等因素对性能的影响。
发动机动力匹配方法
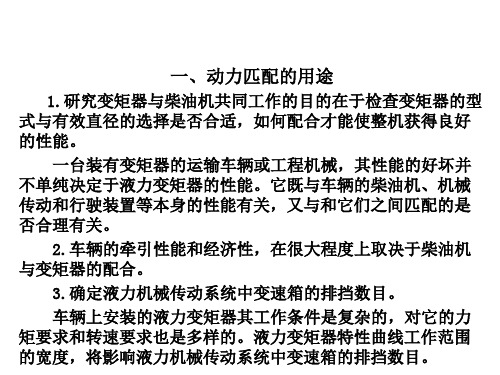
(3)燃油消耗率 发动机每发出1kW有效功率,在1h内所消耗的燃油质量(以g 为单位),称为燃油消耗率,用be表示,燃油消耗率越低,经济 性越好。发动机的性能是随着许多因素而变化的,其变化规律称 为发动机特性。 (4)怠速 柴油机的不带负载最低稳定转速,一般称为怠速。 (5)最高转速 柴油机在最大油门下不带负载转速,一般称为最高转速,一 般为额定转速的1.07~1.1倍。 (6)调速率 柴油机调速区段的转速范围,调速率计算公式为: 调速率=(最高转速-额定转速)/额定转速*100%
2.发动机性能参数及性能曲线 发动机的性能参数即发动机的速度特性,指发动机的功 率、转矩和燃油消耗率三者随曲轴转速变化的规律。这个特 性是通过发动机在试验台架上进行试验求得,试验时,先保 持一定的发动机节气门开度,同时用测功器对发动机曲轴施 加一定的阻力矩,当发动机运转稳定后,即阻力矩与发动机 发出的有效转矩相等时,用转速表测出此时的稳定转速n,同 时在测功器上测出该转速下发动机有效转矩Te,根据下式计 算出有效功率Pe: Pe=Te.n/9550
匹配中用到的几个参数: 1.循环圆直径D: 由泵轮、涡轮和导轮组成封闭的环形空间,通常叫做循环圆, 它的直径就是循环圆直径。 2.变矩系数K: 涡轮轴输出力矩与泵轮轴输入力矩之比。即 K=M2/M1 式中,M1—泵轮轴上的输入力矩; M2—涡轮轴上的输出力矩。 (1)当制动工况时,涡轮停止转动,此时,变矩系数最大, 用K0表示 ,表示液力变矩器启动能力,克服超载能力。 3.变矩器的传动效率η
变矩器的传动效率η :即涡轮轴上输出功率与泵轮轴上输入 功率之比。 η =N2/N1=M2*n2/M1/n1=K*i 式中, N1—泵轮轴上的输入功率; N2—涡轮轴上的输出功率; 4.变矩器的传动比i 涡轮轴输出转速与泵轮轴转速之比,即 i=n2/n1 式中, n1—泵轮轴输入转速; n2—涡轮轴输出转速。
动力总成悬置系统匹配设计

动力总成悬置系统匹配设计方法一、动力总成设计参数的输入1、动力总成的惯性参数动力总成的惯性参数包括动力总成的质量、质心位置以及动力总成的转动惯量10个数据。
质心位置的描述采用发动机坐标系,发动机坐标系的定义:坐标原点O 为发动机缸体后端面和发动机曲轴中心线的交点,x轴正向为过O点平行与曲轴中心线指向发动机端,z轴正向为过质心点平行于气缸中心线垂直向上,y轴正向根据右手定则确定,如下图示:转动惯量的描述采用动力总成质心坐标系下。
质心坐标系定义如下:坐标原点O为动力总成的质心,坐标方向和发动机坐标系相同,如下图所示:动力总成的惯性参数如表1所示:表1动力总成的惯性参数动力总成惯性参数的测定可采用三线摆法测定,误差要求在5%以内。
2、动力总成悬置系统的位置数据动力总成的位置数据包括所有悬置弹性中心的位置、发动机坐标原点位置、变速箱输出轴位置。
所有坐标均采用整车坐标系。
其中位置参数表如表2所示:表2动力总成悬置系统的位置数据3、动力总成悬置系统的刚度数据动力总成悬置系统的刚度参数为各个悬置的三向刚度,刚度参数采用悬置自身的坐标系。
坐标原点为悬置的弹性中心,三个方向为悬置的弹性主轴方向(p、q、r)。
参数表如下所示:表2动力总成悬置系统的位置数据4、变速器的各挡速比和主减速比表3变速箱各档速比和主减速比5、发动机的其他参数这些参数包括发动机的额定功率、最大扭矩、气缸数、发动机的怠速转速、最高转速、扭矩随转速的关系曲线。
参数表如下:表4 发动机的其他参数6、动力总成悬置系统及周边的相关数模二、动力总成悬置系统的解耦设计及固有频率的合理配置1、悬置系统的主要作用动力总成悬置系统的基本功用为:固定并支承汽车动力总成;承受和衰减动力总成内部因发动机不平衡旋转和平移质量产生的往复惯性力、力矩和不平衡扭矩;承受和衰减汽车行驶过程中,例如在换档、加速、启动等工况下作用于动力总成上的一切动态力和对车身造成的冲击;隔离由于发动机激励而引起的车架或车身的振动;隔离由于路面不平度以及车轮所受路面冲击而引起的车身振动向动力总成的传递。
重卡动力系统匹配

变速器档位数对整车动力性、经济性的影响
仿真试验参数
• 变速器 ++++++++
+++++++
16档,速比:15.39 – 0.85 9档,速比:10.26 – 0.74
• 整车 典型重卡
总重49 tons;轮胎滚动半径:0.522m
• 后桥
16档箱匹配3.8速比,总传动比58.48
9档箱匹配5.1速比,总传动比:52.33
46.2
40
30
Route 8.2
各种路况下的总油耗量
-1.5
47.2
45.7
Route 5
FIGE Cycle
-1.2
35.5
34.3
高速公路
变速器档位数对百公里油耗的影响
在同样车速下,发动机发出的功 率相同。
档位 ,后备功率 发动机的负荷率 燃油消耗率 百公里油耗
档位 ,后备功率 发动机的负荷率 燃油消耗率 百公里油耗
• 发动机 340马力,欧3发动机 输出扭矩1700 Nm
模拟计算 使用的工
况
• Route 8.2 • Route 5 • Fige Test • Highway
距离(km)
250.4 213.6 29.5 118.1
停车次数
12 13 4 0
变速器档位数对整车动力性的影响
Zugkraftkraft und Fahrwiderstandslinien
重卡动力系统匹 配
目录
1. 动力系统匹配的目的 2. 动力系统匹配指标体系 3. 影响整车动力性、经济性的因素 4. 发动机的外特性对整车动力性的影响 5. 发动机的万有特性对整车经济性的影响 6. 变速箱档位数及速比对整车动力性、经济性的影响 7. 后桥速比对整车动力性、经济性的影响 8. 不同工况下动力系统的匹配要求 9. 动力系统匹配举例 10. 总结
- 1、下载文档前请自行甄别文档内容的完整性,平台不提供额外的编辑、内容补充、找答案等附加服务。
- 2、"仅部分预览"的文档,不可在线预览部分如存在完整性等问题,可反馈申请退款(可完整预览的文档不适用该条件!)。
- 3、如文档侵犯您的权益,请联系客服反馈,我们会尽快为您处理(人工客服工作时间:9:00-18:30)。
目录1 原理及依据1.1 评价指标1.2 总成参数选择原则2 计算方法2.1 人工经验计算方法2.2 计算机辅助计算3 基础数据收集和输入3.1 动力系统总成参数3.2 车辆运行环境参数3.3 驾驶员换挡规律4 现阶段公司可用相关资源配置5 计算任务和匹配优化5.1 计算任务5.2 数据对比及匹配优化6 计算结果输出和数据分析6.1输出格式和内容规范6.2试验数据对比及分析一规范适用范围本规范规定了动力总成系统传统匹配设计方法及利用AVL Cruise软件对整车动力性和燃油经济性进行计算,并对动力总成系统配置优化。
本规范适用于目前我公司所有车型。
二规范性引用文件GB7258-2004 《机动车运行安全技术条件》。
本规范中所引用的符号及意义动力匹配设计规范1 原理及依据1.1评价指标1.1.1汽车动力性评价指标汽车的动力性是指汽车在良好路面上直线行驶时由汽车受到的纵向外力决定的,所能达到的平均行驶速度。
从获得尽可能高的平均行驶速度的观点出发,汽车的动力性主要可由以下三个指标来评定。
1.1.1.1最高车速最高车速U max是指在水平良好的路面上汽车能达到的最高行驶速度。
它仅仅反映汽车本身具有的极限能力,并不反映汽车实际行驶中的平均速度。
1.1.1.2加速性能汽车的加速能力常用原地起步连续换档加速时间与最高档或次高档加速时间来表示。
原地起步连续换档的加速时间是指用一档或二档起步,以最大加速度按最佳换档时间逐步换至最高档,加速至某一预定的距离或车速所需要的时间。
该项指标反映了汽车在各种车速下的平均动力性。
最高档或次高档加速时间是指用最高档或次高档由某一较低车速全力加速至某一高速所需要的时间。
因为超车时汽车与被超汽车并行,容易发生安全事故,所以最高档或次高档加速能力强,行驶就更安全。
1.1.1.3爬坡性能汽车的爬坡能力是用满载时汽车在良好路面上的最大爬坡度i max 来表示的。
显然,最大爬坡度是指一档时的最大爬坡度。
有些国家用汽车在一定坡道上能达到的车速来表明其爬坡能力。
该项指标所反映的是汽车低速时的动力性。
现有的汽车动力性的评价指标只是反映了汽车本身具有的极限能力,在一定程度上反映了汽车动力性的好坏,但由于未与复杂的实际使用工况统一考虑,因而往往与汽车实际使用效果相差很大。
1.1.2 汽车燃油经济性评价指标在保证动力性的条件下,汽车以尽量小的燃油消耗量经济行驶的能力称为汽车的燃油经济性。
汽车的燃油经济性通常用一定工况下汽车行驶百公里的燃油消耗量或一定燃油量能行驶的里程来衡量。
在我国及欧洲,燃油经济性指标的单位为 L/100km,即行驶 100km 所消耗的燃油量。
1.1.2.1等速燃油消耗等速行驶百公里燃油消耗量是常用的一种评价指标,指汽车在一定载荷下,以最高档在水平良好路面上等速行驶 100km 的燃油消耗量。
测出每隔 10km/h 或20km/h 速度间隔的等速百公里燃油消耗量,绘制成曲线,称为等速百公里燃油消耗量曲线,用它来综合评价汽车的燃油经济性。
1.1.2.2加速燃油消耗加速燃油消耗是指用最高档从某一车速开始全油门加速行驶500m的燃油消耗量,换算成百公里油耗量。
对重型汽车而言,在最高档满载时加速度非常小,行驶500m的速度增加量很小,目前重型汽车很少采用这一指标来评价汽车的经济性。
1.1.2.3多工况燃油消耗等速行驶工况没有全面的反映汽车的实际运行状况,是车辆行驶的一个理想状态,而车辆在实际使用过程中总会或多或少加速、减速等工况,如在市区行驶时,会频繁的出现加速、减速、怠速停车等行驶工况。
因此各国都制定了一些典型的循环行驶试验工况,模拟汽车实际运行工况,并以其百公里燃油消耗量来评定相应性工况的燃油经济性。
许多国家对循环工况都进行了大量的研究,如欧洲的ECE循环,英国的NEDC循环,美国的UDDS循环,日本的JPN10DDS循环等。
我国也制定了货车的路上行驶循环工况:六工况行驶循环,用这些循环工况测出的燃油消耗量即为多工况燃油消耗量。
这是评价汽车燃料经济性的一个实用方法。
六工况循环是模拟干线公路行驶工况,适用于载货汽车(总质量在3500kg以上)和除了城市客车以外的其他类型客车的燃料消耗测定。
考虑加速性的差异,对总质量在14000kg以下和总质量大于14000kg的汽车,六工况的定义也不相同,表1-1是总质量大于14000kg 的汽车的六工况的定义(比较适用于我公司)。
这里我们以SX4185NM351牵引车列车为例,对满载的重型汽车能否实现六工况循环进行简单分析。
该车型发动机为WP10.290,发动机的最大扭矩为1160N.m;变速器为9JS119,最高档为直接档;驱动桥主减速比为4.8(我公司常用);列车满载总质量为50t,其直接档的最大加速为0.08,次高档的最大加速度也仅为0.13,都小于工况中所要求达到的加速度,由此可见,重型汽车满载时无法实现六工况。
另外,对高速公路行驶的重型汽车而言,六工况也不能够反映出车辆的实际使用工况,高速公路的繁忙程度不至于使汽车频繁的处于加速状态,而且车辆通常能以较高的速度行驶,70km/h应是其最常用的速度,因此,在分析公路运输车辆(如牵引车列车)的多工况燃油消耗时,定义了一个简单的复合工况,即由起步连续换档加速到70km/h,再以70km/h匀速行驶一段时间,将这两部分的燃油消耗相加,即可认为近似得出了牵引车实际行驶工况的燃油消耗,而对于工程车辆,由于其运行工况复杂,无法自定义一个接近其实际运行工况的路谱,现阶段只能采用调整滚动阻力系数来简单对比动力系统性能趋势,若要模拟出车辆实际运行状况,需要采集实地路谱。
1.2总成参数选择原则 1.2.1.发动机功率选择设计中通常先从保证汽车预期的最高车速来初步选择发动机应有的功率。
最高车速虽然仅是动力性能的一个指标,但它实质上也反映了汽车的加速能力和爬坡能力。
这是因为最高车速越高,要求的发动机功率越大,汽车后备功率大,加速与爬坡能力必然较好。
给出了期望的最高车速,选择的发动机功率应大体等于,但不小于以最高车速行驶时阻力功率之和,即⎪⎭⎫⎝⎛+=3max max 7614036001a D a T e u A C u Gf P η (1-1) 在给定m 、D C 、A 、f 、T η之值后,便能求出应有功率的数值。
在实际工作中,还利用现有汽车统计数据初步估计汽车比功率来确定发动机应有功率。
汽车比功率是单位汽车总质量具有的发动机功率,比功率的常用单位为kW/t ,可由下式表示:3max max 14.766.31000a TD a T e u m A C u fg m P ηη+==汽车比功率 (1-2) 我国GB7258-2004《机动车运行安全技术条件》规定:三轮汽车、低速货车及拖拉机运输机组的比功率不应小于4.0 kW/t ,除无轨电车外的其它机动车的比功率不允许小于 5.0 kW/t 。
1.2.2传动系最小与最大传动比的选择汽车大多时间以最高档行驶,即用最小传动比的档位行驶。
因此最小传动比的选定很重要。
传动系的总传动比是传动系中各部件传动比的乘积,即0i i i g t = (1-3)式中,g i 为变速器的传动比;0i 为主减速器的传动比;这里不考虑分动器和副变速器。
设最高车速为max a u ,当主减速器的选择使得阻力功率曲线正好与发动机功率曲线交在其最大功率点上。
若当发动机最大功率时的车速称为p u ,则有p a u u =m ax 。
过去,多数汽车将最小传动比选择得使p a u u =m ax ,或p u 稍小于max a u 。
近年来,为了提高燃油经济性,出现了减小最小传动比的趋势,即令p u 稍大于max a u (即变速箱有超速挡)。
确定最大传动比时,要考虑三方面的问题:最大爬坡度、附着率及汽车最低稳定车速。
对于普通汽车来说,传动系最大传动比m ax t i 是变速器Ⅰ档传动比1g i 与主减速器传动比0i 的乘积。
当0i 已知时,确定传动系最大传动比也就是确定变速器Ⅰ档传动比。
汽车爬大坡时车速很低,可以忽略空气阻力,汽车的最大驱动力应为max max i f t F F F += (1-4)或max max 01max sin cos ααηG Gf ri i T Tg tq += (1-5)即 Ttq g i T rf G i ηαα0max max max 1)sin cos (+≥(1-6)最大传动比确定后,还应计算驱动轮的附着率,检查附着条件是否满足上坡或加速的要求。
必要时,只能从汽车总体布置和结构入手,改善汽车的附着能力。
1.2.3主减速器传动比的确定在动力装置其他参数不变的情况下,若要选定最佳主减速器传动比,可根据燃油经济性与动力性的计算,绘制燃油经济性—加速时间曲线。
纵坐标为加速时间,横坐标为循环工况的燃油经济性。
计算出不同主减速器比0i 取不同值时的曲线,当0i 值较大时,加速时间较短但燃油经济性下降;当0i 值较小时,加速时间延长但燃油经济性改善。
0i 选择中间的某一个值,则可以兼顾动力性与燃油经济性。
若以动力性为目标,则可选用较大的0i 值;若以燃油经济性为主要目标,可选较小的0i 值。
燃油经济性—加速时间曲线通常大体上呈C 形,所以又称之为C 曲线。
1.2.4变速器与主减速器传动比的确定在不改变发动机的条件下,可利用C 曲线从数种变速器中选出合适的变速器及主减速器传动比。
确定变速器和主减速器比时,可以绘制不同变速器的燃油经济性—加速时间曲线,根据设计的主要目标选用其中的一个,并根据其C 曲线确定主传动比。
2 计算方法2.1人工经验计算方法 2.1.1最高车速计算:⑴ 发动机最高转速和传动系决定的最高车速:0.377g nru i i =(2-1)⑵ 按功率平衡决定的最高车速: 汽车在平直路面匀速行驶时的阻力功率为:f wTP P η+故功率平衡方程可简化为: 3max max ()3600761401f wD e TTG f u C A u P P P ηη⨯⨯⨯⨯==++ (2-2) 由公式(2-1)和公式(2-2)计算结果可分析,若公式(2-1)计算车速大于公式(2-2)计算车速,则说明整车在最高车速工况下无后备功率;若公式(2-1)计算车速小于公式(2-2)计算车速,则说明整车在最高车速工况下有后备功率,故其实际最高车速取二者之中较小者。
2.1.2最大爬坡度计算⑴ 地面附着性能允许的最大爬坡度:汽车行驶方程式:t f i w j F F F F F +++= 汽车以最低档稳定速度爬坡时0dudt=,即0j F =; 同时爬坡时行驶速度不大,可近似认为空气阻力0w F =, 所以汽车行驶方程式简化为:t f i F F F += 按车辆在坡道上的附着条件可知:cos sin cos f G G G αϕαα•+•=即 max tg f αϕ-=然后再根据max max tg i α=换算成最大爬坡度max i f ϕ-= (2-3) 轮胎与路面的附.附着系数。