硫化时间
橡胶制品的硫化时间及正硫化时间
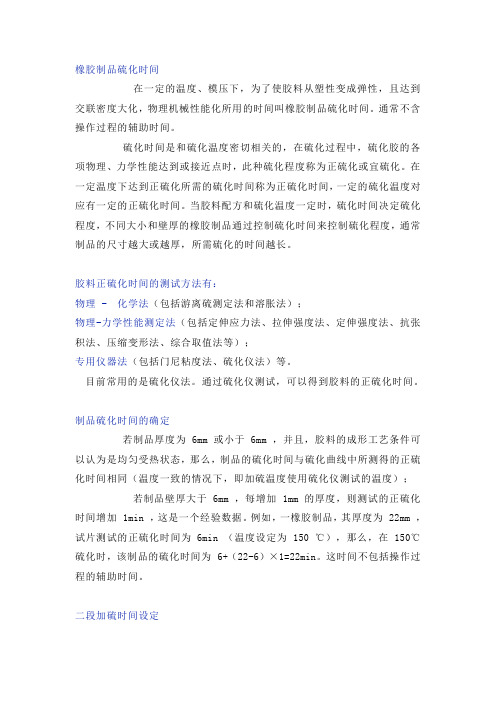
橡胶制品硫化时间在一定的温度、模压下,为了使胶料从塑性变成弹性,且达到交联密度大化,物理机械性能化所用的时间叫橡胶制品硫化时间。
通常不含操作过程的辅助时间。
硫化时间是和硫化温度密切相关的,在硫化过程中,硫化胶的各项物理、力学性能达到或接近点时,此种硫化程度称为正硫化或宜硫化。
在一定温度下达到正硫化所需的硫化时间称为正硫化时间,一定的硫化温度对应有一定的正硫化时间。
当胶料配方和硫化温度一定时,硫化时间决定硫化程度,不同大小和壁厚的橡胶制品通过控制硫化时间来控制硫化程度,通常制品的尺寸越大或越厚,所需硫化的时间越长。
胶料正硫化时间的测试方法有:物理 - 化学法(包括游离硫测定法和溶胀法);物理-力学性能测定法(包括定伸应力法、拉伸强度法、定伸强度法、抗张积法、压缩变形法、综合取值法等);专用仪器法(包括门尼粘度法、硫化仪法)等。
目前常用的是硫化仪法。
通过硫化仪测试,可以得到胶料的正硫化时间。
制品硫化时间的确定若制品厚度为 6mm 或小于 6mm ,并且,胶料的成形工艺条件可以认为是均匀受热状态,那么,制品的硫化时间与硫化曲线中所测得的正硫化时间相同(温度一致的情况下,即加硫温度使用硫化仪测试的温度);若制品壁厚大于 6mm ,每增加 1mm 的厚度,则测试的正硫化时间增加 1min ,这是一个经验数据。
例如,一橡胶制品,其厚度为 22mm ,试片测试的正硫化时间为6min (温度设定为 150 ℃),那么,在 150℃硫化时,该制品的硫化时间为 6+(22-6)×1=22min。
这时间不包括操作过程的辅助时间。
二段加硫时间设定为了达到合理的制造工艺和合理成本,把橡胶硫化分为一段、二段两个过程来完成的工艺方法,其第二段的工艺就是所谓的二段加硫。
一段硫化主要是使制品得到定形,然后将未100% 正硫化状态而得到定形的制品集中起来进行二段硫化。
这样,提升了一段硫化的效率,二段硫化的集中处理,也提升了效率,节省了能源。
硫化曲线t10和t90

硫化曲线t10和t90硫化曲线是用来研究橡胶硫化过程的一种实验方法,通过观察硫化曲线的变化,可以了解橡胶硫化的速度、硫化程度以及最佳硫化条件等信息。
在硫化曲线中,t10和t90是两个重要的参数,它们分别表示橡胶硫化开始和结束的时间点。
本文将深入探讨硫化曲线中的t10和t90参数的意义,以及它们在橡胶硫化过程中的应用。
第一部分:硫化曲线的定义和意义硫化曲线是用来描述橡胶硫化过程中硫化程度随时间的变化。
通常,硫化曲线的横轴表示时间,纵轴表示硫化程度,硫化程度通常用硫化度或者硬度来表示。
硫化曲线的形状和特征可以反映出橡胶硫化的速度和程度,对橡胶的性能和质量有重要的影响。
t10和t90是硫化曲线中的两个重要时间点。
t10表示橡胶开始硫化的时间点,通常也称为10%硫化时间;t90表示橡胶硫化完成的时间点,通常也称为90%硫化时间。
这两个时间点对于研究橡胶硫化过程的速度和程度具有重要的意义。
第二部分:t10和t90在橡胶硫化过程中的应用1.硫化速度的评估t10和t90可以用来评估橡胶的硫化速度。
硫化速度快的橡胶,t10和t90的数值会比较小,反之则较大。
通过比较不同橡胶的t10和t90数值,可以了解不同橡胶的硫化速度的差异,进而选择最适合的橡胶材料。
2.硫化程度的控制t10和t90还可以用来控制橡胶的硫化程度。
通过控制硫化曲线中的t10和t90参数,可以调整橡胶的硫化程度,从而满足不同产品对橡胶硫化程度的要求。
例如,对于一些需要较高硫化程度的橡胶制品,可以通过延长t90时间来提高硫化程度。
3.工艺条件的优化t10和t90还可以用来优化橡胶硫化的工艺条件。
通过调整硫化曲线中的t10和t90参数,可以确定最佳的硫化温度、硫化时间和硫化剂用量等工艺条件,以获得最佳的硫化效果。
第三部分:如何测试t10和t90要测试橡胶的t10和t90参数,通常可以采用动态硫化曲线分析仪进行实验。
在实验中,先将橡胶样品置于硫化机中,然后加入硫化剂和促进剂,在一定的温度和时间条件下进行硫化。
橡胶硫化时间和硫化剂用量
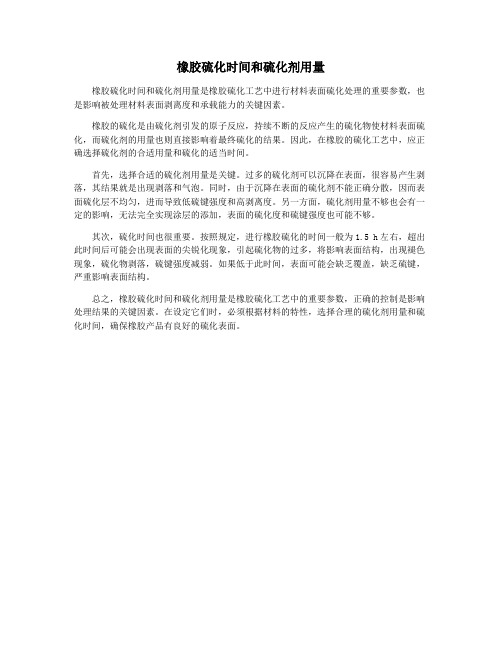
橡胶硫化时间和硫化剂用量
橡胶硫化时间和硫化剂用量是橡胶硫化工艺中进行材料表面硫化处理的重要参数,也是影响被处理材料表面剥离度和承载能力的关键因素。
橡胶的硫化是由硫化剂引发的原子反应,持续不断的反应产生的硫化物使材料表面硫化,而硫化剂的用量也则直接影响着最终硫化的结果。
因此,在橡胶的硫化工艺中,应正确选择硫化剂的合适用量和硫化的适当时间。
首先,选择合适的硫化剂用量是关键。
过多的硫化剂可以沉降在表面,很容易产生剥落,其结果就是出现剥落和气泡。
同时,由于沉降在表面的硫化剂不能正确分散,因而表面硫化层不均匀,进而导致低硫键强度和高剥离度。
另一方面,硫化剂用量不够也会有一定的影响,无法完全实现涂层的添加,表面的硫化度和硫键强度也可能不够。
其次,硫化时间也很重要。
按照规定,进行橡胶硫化的时间一般为1.5 h左右,超出此时间后可能会出现表面的尖锐化现象,引起硫化物的过多,将影响表面结构,出现褪色现象,硫化物剥落,硫键强度减弱。
如果低于此时间,表面可能会缺乏覆盖,缺乏硫键,严重影响表面结构。
总之,橡胶硫化时间和硫化剂用量是橡胶硫化工艺中的重要参数,正确的控制是影响处理结果的关键因素。
在设定它们时,必须根据材料的特性,选择合理的硫化剂用量和硫化时间,确保橡胶产品有良好的硫化表面。
T90硫化报告

T90硫化报告Tc90:亦称正硫化时间,是到达90%硫化时所需要的时间。
1、硫化的定义:硫化是使塑性橡胶线性分子结构转变为三维网状体形结构的过程。
通俗地讲也就是在一定的工艺条件下,胶料配方组分中的生胶与硫化配合剂发生化学反应,使橡胶由线型结构大分子交联成为立体网状结构大分子的交联过程。
“硫化”一词有其历史性,因最初的天然橡胶制品用硫磺作交联剂进行交联而得名,随着橡胶工业的发展,现在可以用多种非硫磺交联剂进行交联。
因此硫化的更科学的意义应是“交联”或“架桥”,即线性高分子通过交联作用而形成的网状高分子的工艺过程。
从物性上即是塑性橡胶转化为弹性橡胶或硬质橡胶的过程“硫化”的含义不仅包含实际交联的过程,还包括产生交联的方法。
2、硫化原理:生橡胶受热变软,遇冷变硬、发脆,不易成型,容易磨损,易溶于汽油等有机溶剂,分子内具有双键易起加成反应,容易老化。
为改善橡胶制品的性能,生产上要对生橡胶进行一系列加工过程,在一定条件下,使胶料中的生胶与硫化剂发生化学反应,使其由线型结构的大分子交联成为立体网状结构的大分子,使从而使胶料具备高强度、高弹性、高耐磨、抗腐蚀等等优良性能。
这个过程称为橡胶硫化。
一般将硫化过程分为四个阶段,诱导一预硫一正硫化一过硫。
为实现这一反应,必须外加能量使之达到一定的硫化温度,然后让橡胶保温在该硫化温度范围内完成全部硫化反应。
硫化指橡胶分子同硫化剂之间发生交联反应,也就是在一定的工艺条件下,胶料配方组分中的生胶与硫化配合剂发生化学反应,使橡胶由线型结构大分子交联成为立体网状结构大分子(network)的交联过程。
胶料由塑性变成了弹性,从而获得了所需的产品形状和满足使用要求的各种性能。
硫化后,橡胶大分子交联成空间网状结构,使大分子运动受到,定限制,在外力作用下,不容易发生较大的位移,因而硫化后橡胶的抗拉强度、定伸强度和弹性提高当而延伸率减沙无并失去可溶性,只能有限地溶胀。
硫化过程实质上是一个交联过程,由于最初使用的交联剂都是硫黄,所以取名为硫化,并习惯把经过交联的橡胶称为硫化胶。
橡胶硫化过程的四阶段:起硫、欠硫、正硫和过硫

橡胶硫化过程的四阶段:起硫、欠硫、正硫和过硫胶料在硫化时,其性能随硫化时间变化而变化的曲线,称为硫化曲线。
从硫化时间影响胶料定伸强度的过程来看,可以将整个硫化时间分为四个阶段:硫化起步阶段、欠硫阶段、正硫阶段和过硫阶段。
1)硫化起步阶段(又称焦烧期或硫化诱导期)硫化起步的意思是指硫化时间胶料开始变硬而后不能进行热塑性流动那一点的时间。
硫起步阶段即此点以前的硫化时间。
在这一阶段内,交联尚未开始,胶料在模型内有良好的流动性。
胶料硫化起步的快慢,直接影响胶料的焦烧和操作安全性。
这一阶段的长短取决于所用配合剂,特别是促进剂的种类。
用有超速促进剂的胶料,其焦烧比较短,此时胶料较易发生焦烧,操作安全性差。
在使用迟效性促进剂(如亚磺酰胺)或与少许秋兰姆促进剂并用时,均可取得较长的焦烧期和良好的操作安全性。
但是,不同的硫化方法和制品,对焦烧时间的长短亦有不同要求。
在硫化模压制品时,总是希望有较长的焦烧期,使胶料有充分时间在模型内进行流动,而不致使制品出现花纹不清晰或缺胶等到缺陷。
在非模型硫化中,则应要求硫化起步应尽可能早一些,因为胶料起步快而迅速变硬,有利于防止制品因受热变软而发生变形。
不过在大多数情况下仍希望有较长的焦烧时间以保证操作的。
2)欠硫阶段(又称预硫阶段)硫化起步与正硫化之间的阶段称为欠硫阶段。
在此阶段,由于交联度低,橡胶制品应具备的性能大多还不明显。
尤其是此阶段初期,胶料的交联度很低,其性能变化甚微,制品没有实用意义。
但是到了此阶段的后期,制品轻微欠硫时,尽管制品的抗张强度、弹性、伸长率等尚未达到预想的水平,但其抗撕裂性耐磨性和抗动态裂口性等则优于正硫化胶料。
因此,如果着重要求后几种性能时,制品可以轻微欠硫。
3)正硫阶段大多数情况下,制品在硫化时都必须使之达到适当的交联度,达到适当的我联度的阶段叫做正硫化阶段,即正硫阶段。
在此阶段,硫化胶的各项物理机械性能并非在同一时都达到最高值,而是分别达到或接近最佳值,其综合性能最好。
硫化曲线t10和t90
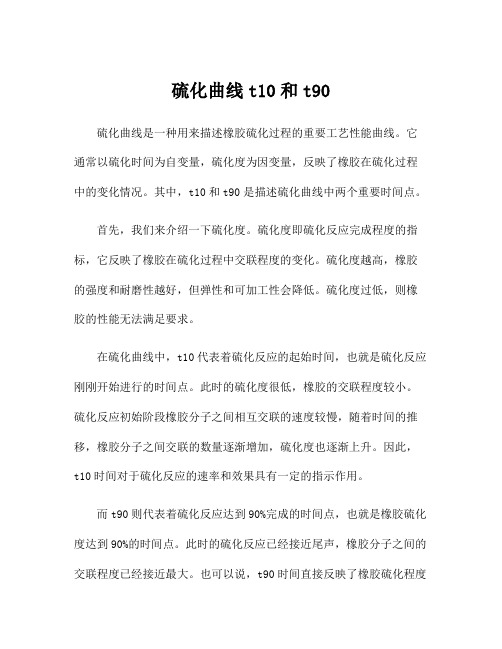
硫化曲线t10和t90硫化曲线是一种用来描述橡胶硫化过程的重要工艺性能曲线。
它通常以硫化时间为自变量,硫化度为因变量,反映了橡胶在硫化过程中的变化情况。
其中,t10和t90是描述硫化曲线中两个重要时间点。
首先,我们来介绍一下硫化度。
硫化度即硫化反应完成程度的指标,它反映了橡胶在硫化过程中交联程度的变化。
硫化度越高,橡胶的强度和耐磨性越好,但弹性和可加工性会降低。
硫化度过低,则橡胶的性能无法满足要求。
在硫化曲线中,t10代表着硫化反应的起始时间,也就是硫化反应刚刚开始进行的时间点。
此时的硫化度很低,橡胶的交联程度较小。
硫化反应初始阶段橡胶分子之间相互交联的速度较慢,随着时间的推移,橡胶分子之间交联的数量逐渐增加,硫化度也逐渐上升。
因此,t10时间对于硫化反应的速率和效果具有一定的指示作用。
而t90则代表着硫化反应达到90%完成的时间点,也就是橡胶硫化度达到90%的时间点。
此时的硫化反应已经接近尾声,橡胶分子之间的交联程度已经接近最大。
也可以说,t90时间直接反映了橡胶硫化程度的快慢与充分性。
通常情况下,t90时间越短,说明橡胶的硫化反应速率快且充分,橡胶材料的性能也会相应提升。
硫化曲线的形状通常可分为四个阶段:橡胶化、股化、稳态硫化和过硫化。
在橡胶化阶段,曲线可以近似看作是一条直线,此时的硫化度较低。
股化阶段是曲线的斜率逐渐减小的阶段,此时的硫化度随时间的增长而逐渐上升。
稳态硫化阶段是指曲线呈现出平缓的状态,此时橡胶的硫化度已经接近最大值。
过硫化阶段是曲线开始出现下降趋势,此时橡胶的硫化度开始下降,原因往往是交联程度过高导致橡胶断裂。
通过观察硫化曲线的t10和t90时间,可以评估硫化反应的速率和完成程度。
通常来说,t10时间越短,说明橡胶的硫化反应速率快;而t90时间越短,说明橡胶的硫化程度充分。
因此,对于某些特定的应用领域,我们可以根据t10和t90时间的要求来优化橡胶材料的硫化工艺。
总结起来,硫化曲线中的t10和t90时间点是描述橡胶硫化过程的重要参数。
橡胶硫化压力、温度、(厚制品)时间计算(公式全,收藏)
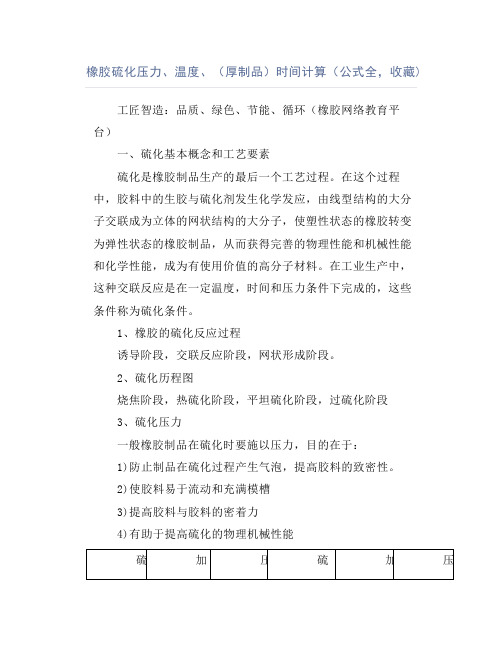
橡胶硫化压力、温度、(厚制品)时间计算(公式全,收藏)工匠智造:品质、绿色、节能、循环(橡胶网络教育平台)一、硫化基本概念和工艺要素硫化是橡胶制品生产的最后一个工艺过程。
在这个过程中,胶料中的生胶与硫化剂发生化学发应,由线型结构的大分子交联成为立体的网状结构的大分子,使塑性状态的橡胶转变为弹性状态的橡胶制品,从而获得完善的物理性能和机械性能和化学性能,成为有使用价值的高分子材料。
在工业生产中,这种交联反应是在一定温度,时间和压力条件下完成的,这些条件称为硫化条件。
1、橡胶的硫化反应过程诱导阶段,交联反应阶段,网状形成阶段。
2、硫化历程图烧焦阶段,热硫化阶段,平坦硫化阶段,过硫化阶段3、硫化压力一般橡胶制品在硫化时要施以压力,目的在于:1)防止制品在硫化过程产生气泡,提高胶料的致密性。
2)使胶料易于流动和充满模槽3)提高胶料与胶料的密着力4)有助于提高硫化的物理机械性能硫化机把压力传递给模型,再由模型传递给胶料;二是硫化介质直接加压(如蒸汽加压);三是以压缩空气加压;四是由注压机注压等。
4、硫化温度和硫化时间硫化温度是橡胶发生硫化反应的基本条件,它直接影响硫化速度和产品质量。
硫化温度高,硫化速度快,生产效率高。
反之,硫化速度慢,生产效率低。
硫化温度高低应取决于胶料配方,其中最重要的是取决于橡胶种类和硫化体系。
但应注意的是,高温橡胶分子链裂解,至发生硫化返原现象,结果导致强伸性能下降,困此硫化温度不宜太高。
温度是硫化三大要素之一,与所有化学反应一样,硫化反应随温度升高而加快,并且大体适用范特霍夫定律,即温度每上升8~10。
C(约相当于一个表压的蒸汽压力),其反应速度约增加一倍;或者说,反应时间约减少一半。
随着室温硫化胶料的增加和高温硫化出现,硫化温度趋向两个极端。
从提高硫化效率来说,应当认为硫化温度越高越好,但实际上不能无限提高硫化温度。
首先受到橡胶导热性极小阻碍,对于厚制品来说,采用高温硫化很难使内外层胶料同时达到平坦范围;其次,各种橡胶的耐高温性能不一,有的橡胶经受不了高温的作用,如高温硫化天然橡胶时,溶于橡胶中的氧随温度提高而活性加大,引起强烈的氧化作用,破坏了橡胶的组织,降低了硫化胶的物理机械性能,第三,高温对橡胶制品中的纺织物有害为棉纤维布料超过期作废140℃时,强力下降,在240℃下加热四小时则完全破坏。
硅胶硫化时间和温度

硅胶硫化时间和温度
硅胶是一种常用于制造各种密封件和电子元器件的材料,它具有优良的耐热性、耐化学性和电绝缘性。
硅胶在制造过程中需要进行硫化处理,以使其具有更好的物理性能和化学稳定性。
硫化时间和温度是影响硅胶硫化效果的重要因素。
硫化时间是指硫化反应所需的时间,它与硫化温度、硅胶种类和硫化剂种类等因素有关。
通常情况下,硫化时间越长,硅胶的物理性能和化学稳定性就越好。
但是过长的硫化时间会导致硅胶的成本增加和生产周期延长,因此需要在硫化时间和产品质量之间做出平衡。
硫化温度是指硫化反应所需的温度,它是影响硫化时间和硫化效果的关键因素。
硅胶的硫化温度通常在150-200℃之间,不同种类的硅胶硫化温度会有所差异。
在硫化过程中,温度过高会导致硅胶老化和变质,温度过低则会延长硫化时间,影响生产效率。
因此,选择合适的硫化温度对于保证硅胶的物理性能和化学稳定性具有重要意义。
总之,硅胶的硫化时间和温度是影响硅胶硫化效果的重要因素,要根据具体生产要求和产品质量要求合理选择。
- 1 -。
橡胶件硫化作业指导书

1.预先领取骨架、胶料,并检查胶料、骨架、涂胶是否正常,上次余留涂过胶粘剂的骨架需重新抛沙、涂胶才能使用,所有骨架涂完面胶4个小时后才能使用,禁止用手直接拿骨架,装模时保持手套洁净
2.当温度达到工艺要求15分钟后,打开设备检查其运行是否正常、模具是否正常
3.清理模腔,喷少许脱模剂,待干燥后,把骨架正确放入模腔中,合模,按自动按钮,同时观察锁模压力达到要求后,方可开始注胶
产品型号
HS0248
作业指导书
文件编号
HS/P-C-06
产品名称
液压减震
编制时间
橡胶牌号
50A-1
保存单位
硫化车间
硫化工艺
产品简图
温度
164℃
注胶压力
10 MPa
时间
420秒
注胶时间
45秒
压力
15 MPa
胶重
440克/模
排气
2--3次
模比
1:2
过程控制
1工艺参数:
1硫化温度:160 +5,硫化时间t+30秒
4.当硫化达到规定时间后,自动开模(开模时应注意模具或产品是否粘在上模,如有应及时采取措施,避免产品或模具拉伤),改为手动,打开托板,取出制品,
5.检测制品有无缺陷,并分区放置
6.所有用品都必须按规定放置,绝对禁止螺丝刀、脱模剂和骨架放在一起
7.清理模具和注胶筒中的胶皮,按上述步骤进行下一轮循环
8.下班要对设备、模具进行清理和维护,整理自己的用品、打扫环境卫生,把产品放到指定位置,做好交接记录
2注胶时间控制在35—60秒之内;
注胶压力可根据不同的设备、模具进行调整,但注胶压力不能大于锁模压力,可通过注胶速度调整注胶时间
xilinx u200 硫化标准

xilinx u200 硫化标准
一、目的
本标准规定了Xilinx U200系列FPGA芯片的硫化要求、工艺流程、操作规程及注意事项,旨在确保生产过程中的硫化效果和质量。
二、适用范围
本标准适用于使用Xilinx U200系列FPGA芯片的所有生产过程,包括但不限于电路板焊接、系统集成等。
三、硫化要求
1. 温度控制:在硫化过程中,温度应保持在250℃±5℃的范围内,保持温度稳定,避免温度过高或过低。
2. 时间控制:硫化时间应不少于30分钟,以保证芯片充分硫化,提高硫化质量。
3. 湿度控制:硫化环境湿度应保持在30%~60%的范围内,以防止静电和氧化。
4. 清洁度控制:焊接前应对电路板进行清洁,去除油污、氧化层等杂质,保证焊接质量。
四、工艺流程
1. 预热:将电路板放入硫化炉中,预热至规定温度。
2. 装载:将Xilinx U200系列FPGA芯片按照规定的位置放置在电路板上。
3. 焊接:在规定温度和时间下进行焊接,保证芯片与电路板良
好连接。
4. 后处理:焊接完成后,取出电路板,进行必要的后处理工作,如冷却、清洁等。
五、操作规程
1. 在操作前应详细了解Xilinx U200系列FPGA芯片的规格书和本标准,确保正确理解和掌握硫化要求。
2. 在操作过程中应穿戴好防静电工作服和手套,防止静电对芯片造成损坏。
3. 在装载芯片时应注意轻拿轻放,避免碰撞和划伤芯片表面。
硫化橡胶正硫化时间的确定方法
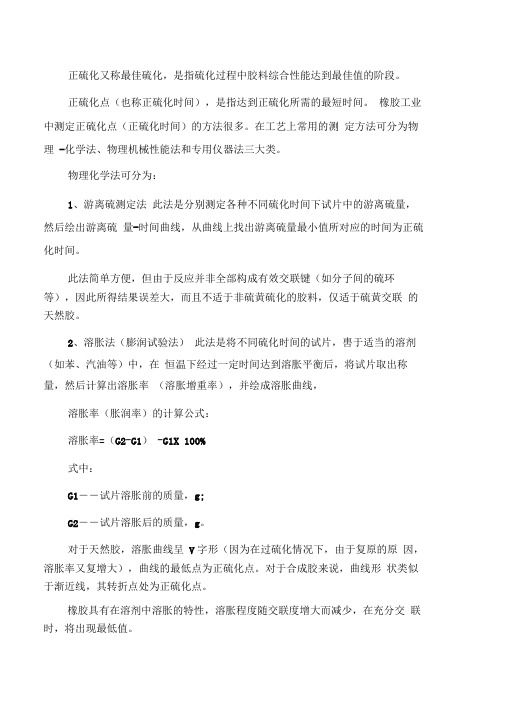
正硫化又称最佳硫化,是指硫化过程中胶料综合性能达到最佳值的阶段。
正硫化点(也称正硫化时间),是指达到正硫化所需的最短时间。
橡胶工业中测定正硫化点(正硫化时间)的方法很多。
在工艺上常用的测定方法可分为物理-化学法、物理机械性能法和专用仪器法三大类。
物理化学法可分为:
1、游离硫测定法此法是分别测定各种不同硫化时间下试片中的游离硫量,然后绘出游离硫量-时间曲线,从曲线上找出游离硫量最小值所对应的时间为正硫化时间。
此法简单方便,但由于反应并非全部构成有效交联键(如分子间的硫环等),因此所得结果误差大,而且不适于非硫黄硫化的胶料,仅适于硫黄交联的天然胶。
2、溶胀法(膨润试验法)此法是将不同硫化时间的试片,軎于适当的溶剂(如苯、汽油等)中,在恒温下经过一定时间达到溶胀平衡后,将试片取出称量,然后计算出溶胀率(溶胀增重率),并绘成溶胀曲线,
溶胀率(胀润率)的计算公式:
溶胀率=(G2-G1) -G1X 100%
式中:
G1――试片溶胀前的质量,g;
G2――试片溶胀后的质量,g。
对于天然胶,溶胀曲线呈V字形(因为在过硫化情况下,由于复原的原因,溶胀率又复增大),曲线的最低点为正硫化点。
对于合成胶来说,曲线形状类似于渐近线,其转折点处为正硫化点。
橡胶具有在溶剂中溶胀的特性,溶胀程度随交联度增大而减少,在充分交联时,将出现最低值。
溶胀法是公认为测定正硫化的标准方法,由此法测定的正硫化点,为理论正硫化点。
硫化时间1

1/2
• h —布层相当于胶层的当量厚度,cm • h —布层实际厚度,cm
2
• α -布层的热扩散系数,cm²/s • α -胶层的热扩散系数,cm²/s • 制品的总计算厚度: • H =制品的胶层厚度+布层当量厚度 求出滞后时间与制品的硫化时间。p99
2 1 总
二 硫化时间的调整
三 硫化效应与厚制品等效硫化 时间的确定
• 由于胶料达到正硫化后都有一个硫化平 坦范围,因此在改变硫化条件时,只要 把改变后的硫化效应控制在原来硫化条 件的最小硫化效应和最大硫化效应之内, 制品的物理机械性能就可与原硫化条件 相近。即E <E<E
min max
• 原制品等效硫化时间的确定 由于橡胶是一种热的不 良导体,因而厚制品在硫化时各部位或各部件的温度 是不相同的(即使是同一部位或同一部件在不同的硫 化时间内温度也是不同的),在相同的硫化时间内所 取得的硫化效应也是不同的。并且,随着制品厚度的 增加这种现象越为明显。为了正确确定厚制品的硫化 工艺时间和各层胶件的胶料配方,往往需要首先拟定 一个硫化工艺条件,然后将厚制品与该硫化工艺条件 下进行硫化。同时,测出各胶层温度随硫化时间的变 化情况,计算出各胶层的硫化效应,再将其分别与各 胶层胶料试片在硫化仪上测出的达到正硫化的允许硫 化效应相比较,如果各胶层的实际硫化效应都在允许 的范围之内,即可认为拟定的硫化工艺条件是适宜的。 否则,要对硫化工艺条件或各胶层胶料配方作调整。
1 1 2 2
三 硫化效应与厚制品等效硫化 时间的确定
• ⑴ 硫化效应 硫化效应是衡量胶料硫化程度深 浅的尺度。硫化效应大,说明胶料硫化程度深, 硫化效应小,说明胶料硫化程度浅。它等于硫 化强度与硫化时间的乘积。 • E=Ιτ • 式中 E——硫化效应; • Ι——硫化强度; • τ——硫化时间,min
皮带接头硫化工艺及时间

胶带接头硫化工艺及硫化时间
龙华煤矿机运队
2014年9月15日
胶带接头硫化工艺及硫化时间
硫化1.6米皮带,6人专业人员施工,硫化一个接头,大概的需要以下时间:
1.断旧带(拆架子、上夹板、准备工具),1.5小时。
2. 抽旧带、装新带(断新带),2.5小时。
3.剥胶、剥绳(搭接接头2.4米),4小时。
4.断绳、刮钢丝绳,2小时。
5.安装硫化机下机架、水板及加热板,0.5小时。
6.清洗钢丝绳(将裁好的钢丝绳和坡口处用120#汽油清洗一遍,涂刷胶浆二次并进行干燥),0.5小时
7.铺设下胶、钢丝绳、上胶,1时。
8. 安装硫化机上机架、水板、加热板紧固螺栓,0.5小时。
9.加压、升温、保温,1小时。
10.降温(当温度降至70℃时,即可卸压拆模硫化机),4小时。
11.拆卸硫化机、电源、张紧皮带、安装机架,1小时。
12.收拾工器具、材料及杂物,打扫现场卫生。
橡胶制品硫化的三大参数:时间、温度、压力
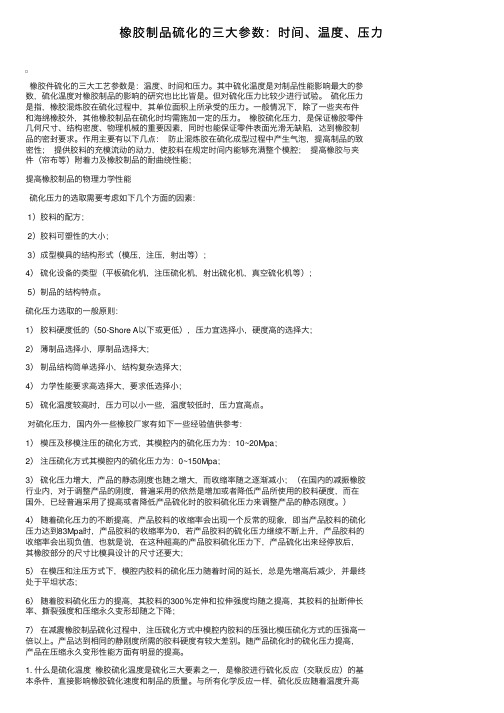
橡胶制品硫化的三⼤参数:时间、温度、压⼒橡胶件硫化的三⼤⼯艺参数是:温度、时间和压⼒。
其中硫化温度是对制品性能影响最⼤的参数,硫化温度对橡胶制品的影响的研究也⽐⽐皆是。
但对硫化压⼒⽐较少进⾏试验。
硫化压⼒是指,橡胶混炼胶在硫化过程中,其单位⾯积上所承受的压⼒。
⼀般情况下,除了⼀些夹布件和海绵橡胶外,其他橡胶制品在硫化时均需施加⼀定的压⼒。
橡胶硫化压⼒,是保证橡胶零件⼏何尺⼨、结构密度、物理机械的重要因素,同时也能保证零件表⾯光滑⽆缺陷,达到橡胶制品的密封要求。
作⽤主要有以下⼏点:防⽌混炼胶在硫化成型过程中产⽣⽓泡,提⾼制品的致密性;提供胶料的充模流动的动⼒,使胶料在规定时间内能够充满整个模腔;提⾼橡胶与夹件(帘布等)附着⼒及橡胶制品的耐曲绕性能;提⾼橡胶制品的物理⼒学性能硫化压⼒的选取需要考虑如下⼏个⽅⾯的因素:1)胶料的配⽅;2)胶料可塑性的⼤⼩;3)成型模具的结构形式(模压,注压,射出等);4)硫化设备的类型(平板硫化机,注压硫化机,射出硫化机,真空硫化机等);5)制品的结构特点。
硫化压⼒选取的⼀般原则:1)胶料硬度低的(50-Shore A以下或更低),压⼒宜选择⼩,硬度⾼的选择⼤;2)薄制品选择⼩,厚制品选择⼤;3)制品结构简单选择⼩,结构复杂选择⼤;4)⼒学性能要求⾼选择⼤,要求低选择⼩;5)硫化温度较⾼时,压⼒可以⼩⼀些,温度较低时,压⼒宜⾼点。
对硫化压⼒,国内外⼀些橡胶⼚家有如下⼀些经验值供参考:1)模压及移模注压的硫化⽅式,其模腔内的硫化压⼒为:10~20Mpa;2)注压硫化⽅式其模腔内的硫化压⼒为:0~150Mpa;3)硫化压⼒增⼤,产品的静态刚度也随之增⼤,⽽收缩率随之逐渐减⼩;(在国内的减振橡胶⾏业内,对于调整产品的刚度,普遍采⽤的依然是增加或者降低产品所使⽤的胶料硬度,⽽在国外,已经普遍采⽤了提⾼或者降低产品硫化时的胶料硫化压⼒来调整产品的静态刚度。
)4)随着硫化压⼒的不断提⾼,产品胶料的收缩率会出现⼀个反常的现象,即当产品胶料的硫化压⼒达到83Mpa时,产品胶料的收缩率为0,若产品胶料的硫化压⼒继续不断上升,产品胶料的收缩率会出现负值,也就是说,在这种超⾼的产品胶料硫化压⼒下,产品硫化出来经停放后,其橡胶部分的尺⼨⽐模具设计的尺⼨还要⼤;5)在模压和注压⽅式下,模腔内胶料的硫化压⼒随着时间的延长,总是先增⾼后减少,并最终处于平坦状态;6)随着胶料硫化压⼒的提⾼,其胶料的300%定伸和拉伸强度均随之提⾼,其胶料的扯断伸长率、撕裂强度和压缩永久变形却随之下降;7)在减震橡胶制品硫化过程中,注压硫化⽅式中模腔内胶料的压强⽐模压硫化⽅式的压强⾼⼀倍以上。
不同颜色橡胶硫化时间

不同颜色橡胶硫化时间
橡胶硫化时间是指在一定的温度和压力下,橡胶从塑性状态转变为弹性状态,并且达到最佳物理机械性能的时间。
不同颜色的橡胶由于其成分和配方可能会有不同的硫化时间。
以下是一些常见颜色橡胶的硫化时间参考。
1.天然橡胶(NR):通常在140-150°C下硫化,硫化时间约为15-30分钟。
2.丁苯橡胶(SBR):在150-160°C下硫化,硫化时间约为20-40分钟。
3.顺丁橡胶(BR):在150-160°C下硫化,硫化时间约为20-40分钟。
4.氯丁橡胶(CR):在160-170°C下硫化,硫化时间约为30-60分钟。
5.丁腈橡胶(NBR):在150-190°C下硫化,硫化时间约为20-80分钟。
6.硅橡胶(VMQ):在140-160°C下硫化,硫化时间约为2-4小时。
7.氟橡胶(FVMQ):在150-200°C下硫化,硫化时间约为2-4小时。
请注意,这些硫化时间仅供参考,实际硫化时间可能会因橡胶配方、硫化体系、模具设计、温度控制等因素而有所不同。
在生产过程中,通常会通过实验和测试来确定最佳的
硫化时间。
最佳硫化时间

最佳硫化时间
最佳硫化时间取决于具体的硫化材料和硫化条件。
一般情况下,硫化时间应根据硫化反应速率、硫化温度和硫化物的类型来确定。
硫化时间通常需要根据硫化物的类型和硫化温度来进行试验和优化。
一般而言,硫化时间应足够长,以确保硫化物充分形成,但也要避免过长的硫化时间,以免造成过硫化或过硫化。
在一些常见的硫化反应中,如橡胶硫化,一般硫化时间可在
15分钟至4小时之间。
具体的硫化时间会受到硫化温度、硫
化剂和橡胶种类的影响。
总而言之,最佳硫化时间需要根据具体的硫化材料和硫化条件进行试验和优化确定。
聚氨酯硫化时间-概述说明以及解释

聚氨酯硫化时间-概述说明以及解释1.引言1.1 概述概述聚氨酯是一种重要的工业材料,具有优异的性能和广泛的应用领域。
在聚氨酯的生产和应用过程中,硫化时间是一个非常重要的参数。
硫化时间影响着聚氨酯材料的硬度、强度、耐磨性等性能。
因此,了解和控制聚氨酯的硫化时间对于保证产品质量和性能至关重要。
本文将介绍聚氨酯硫化时间的相关知识,探讨影响聚氨酯硫化时间的因素以及在实际应用中如何控制硫化时间。
通过深入了解聚氨酯硫化时间的重要性和控制方法,有助于提高聚氨酯制品的生产效率和质量。
文章结构部分主要是对整篇文章的组织和布局进行介绍,包括各章节的内容安排和逻辑顺序。
在本篇文章中,共分为引言、正文和结论三个部分。
具体的文章结构如下:1. 引言部分:1.1 概述:对聚氨酯硫化时间的问题进行简要介绍,引起读者的兴趣。
1.2 文章结构:介绍本文的各个部分及其内容,让读者对整篇文章有个整体的了解。
1.3 目的:明确本文的写作目的和意义,指引读者在阅读过程中关注的重点。
2. 正文部分:2.1 聚氨酯的特性:详细介绍聚氨酯的性质、结构和应用领域,为后续讨论聚氨酯硫化时间奠定基础。
2.2 影响聚氨酯硫化时间的因素:探讨影响聚氨酯硫化时间的各种因素,包括原材料、工艺等,为后续实际应用中的控制提供参考依据。
2.3 实际应用中的聚氨酯硫化时间控制:介绍在实际应用中如何控制聚氨酯硫化时间,以满足不同需求和要求。
3. 结论部分:3.1 总结聚氨酯硫化时间的重要性:总结聚氨酯硫化时间对产品质量和性能的重要性,强调其在生产中的必要性。
3.2 对聚氨酯硫化时间的展望:展望聚氨酯硫化时间在未来的发展趋势和应用前景,指出未来的研究方向和重点。
3.3 结论:对全文进行总结和概括,强调重点内容,呼应文章开头的写作目的。
1.3 目的本文旨在探讨聚氨酯硫化时间这一重要参数在工业生产中的意义和影响。
通过分析聚氨酯的特性、影响硫化时间的因素以及实际应用中的控制方法,我们希望能够加深对这一技术指标的理解,为相关行业的生产工作提供参考和指导。
硫化时间
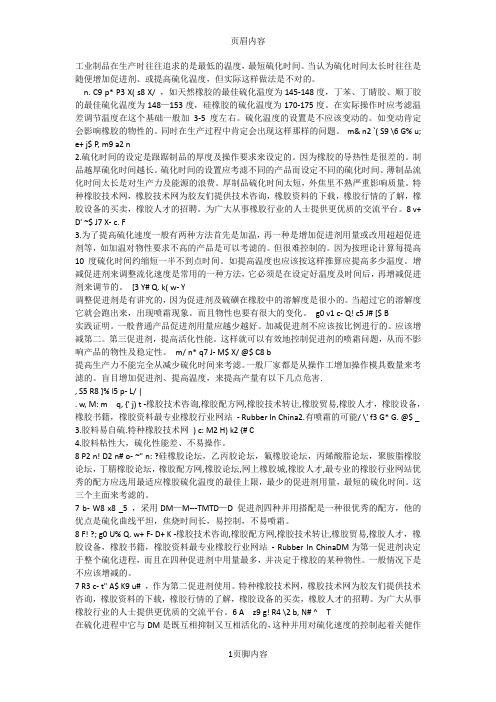
工业制品在生产时往往追求的是最低的温度,最短硫化时间。
当认为硫化时间太长时往往是随便增加促进剂、或提高硫化温度,但实际这样做法是不对的。
n. C9 p* P3 X( s8 X/ ,如天然橡胶的最佳硫化温度为145-148度,丁苯、丁睛胶、顺丁胶的最佳硫化温度为148—153度,硅橡胶的硫化温度为170-175度。
在实际操作时应考滤温差调节温度在这个基础一般加3-5 度左右。
硫化温度的设置是不应该变动的。
如变动肯定会影响橡胶的物性的。
同时在生产过程中肯定会出现这样那样的问题。
m& n2 `( S9 \6 G% u; e+ j$ P, m9 a2 n2.硫化时间的设定是跟踞制品的厚度及操作要求来设定的。
因为橡胶的导热性是很差的。
制品越厚硫化时间越长。
硫化时间的设置应考滤不同的产品而设定不同的硫化时间。
薄制品流化时间太长是对生产力及能源的浪费。
厚制品硫化时间太短,外焦里不熟严重影响质量。
特种橡胶技术网,橡胶技术网为胶友们提供技术咨询,橡胶资料的下载,橡胶行情的了解,橡胶设备的买卖,橡胶人才的招聘。
为广大从事橡胶行业的人士提供更优质的交流平台。
8 v+ D' ~$ J7 X- c. F3.为了提高硫化速度一般有两种方法首先是加温,再一种是增加促进剂用量或改用超超促进剂等,如加温对物性要求不高的产品是可以考滤的。
但很难控制的。
因为按理论计算每提高10度硫化时间约缩短一半不到点时间。
如提高温度也应该按这样推算应提高多少温度。
增减促进剂来调整流化速度是常用的一种方法,它必须是在设定好温度及时间后,再增减促进剂来调节的。
[3 Y# Q. k( w- Y调整促进剂是有讲究的,因为促进剂及硫磺在橡胶中的溶解度是很小的。
当超过它的溶解度它就会跑出来,出现喷霜现象。
而且物性也要有很大的变化。
g0 v1 c- Q! c5 J# [$ B实践证明。
一般普通产品促进剂用量应越少越好。
加减促进剂不应该按比例进行的。
正硫化时间
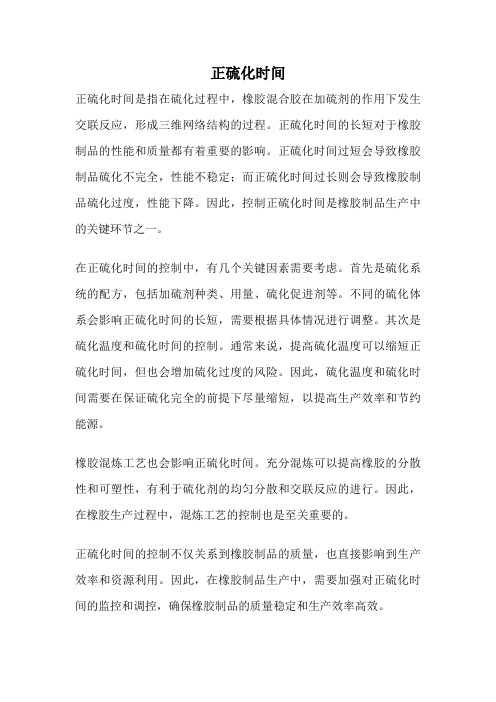
正硫化时间
正硫化时间是指在硫化过程中,橡胶混合胶在加硫剂的作用下发生交联反应,形成三维网络结构的过程。
正硫化时间的长短对于橡胶制品的性能和质量都有着重要的影响。
正硫化时间过短会导致橡胶制品硫化不完全,性能不稳定;而正硫化时间过长则会导致橡胶制品硫化过度,性能下降。
因此,控制正硫化时间是橡胶制品生产中的关键环节之一。
在正硫化时间的控制中,有几个关键因素需要考虑。
首先是硫化系统的配方,包括加硫剂种类、用量、硫化促进剂等。
不同的硫化体系会影响正硫化时间的长短,需要根据具体情况进行调整。
其次是硫化温度和硫化时间的控制。
通常来说,提高硫化温度可以缩短正硫化时间,但也会增加硫化过度的风险。
因此,硫化温度和硫化时间需要在保证硫化完全的前提下尽量缩短,以提高生产效率和节约能源。
橡胶混炼工艺也会影响正硫化时间。
充分混炼可以提高橡胶的分散性和可塑性,有利于硫化剂的均匀分散和交联反应的进行。
因此,在橡胶生产过程中,混炼工艺的控制也是至关重要的。
正硫化时间的控制不仅关系到橡胶制品的质量,也直接影响到生产效率和资源利用。
因此,在橡胶制品生产中,需要加强对正硫化时间的监控和调控,确保橡胶制品的质量稳定和生产效率高效。
总的来说,正硫化时间是橡胶制品生产中一个至关重要的参数,其控制涉及到硫化体系、硫化温度、硫化时间和混炼工艺等多个方面。
只有合理控制正硫化时间,才能生产出质量稳定的橡胶制品,提高生产效率,降低生产成本,实现经济效益和社会效益的双赢。
- 1、下载文档前请自行甄别文档内容的完整性,平台不提供额外的编辑、内容补充、找答案等附加服务。
- 2、"仅部分预览"的文档,不可在线预览部分如存在完整性等问题,可反馈申请退款(可完整预览的文档不适用该条件!)。
- 3、如文档侵犯您的权益,请联系客服反馈,我们会尽快为您处理(人工客服工作时间:9:00-18:30)。
工业制品在生产时往往追求的是最低的温度,最短硫化时间。
当认为硫化时间太长时往往是随便增加促进剂、或提高硫化温度,但实际这样做法是不对的。
n. C9 p* P3 X( s8 X/ 1.因为硫化温度决定于橡胶的品种,如天然橡胶的最佳硫化温度为145-148度,丁苯、丁睛胶、顺丁胶的最佳硫化温度为148—153度,硅橡胶的硫化温度为170-175度。
在实际操作时应考滤温差调节温度在这个基础一般加3-5 度左右。
硫化温度的设置是不应该变动的。
如变动肯定会影响橡胶的物性的。
同时在生产过程中肯定会出现这样那样的问题。
$ m& n2 `( S9 \6 G% u; e+ j$ P, m9 a2 n 2.硫化时间的设定是跟踞制品的厚度及操作要求来设定的。
因为橡胶的导热性是很差的。
制品越厚硫化时间越长。
硫化时间的设置应考滤不同的产品而设定不同的硫化时间。
薄制品流化时间太长是对生产力及能源的浪费。
厚制品硫化时间太短,外焦里不熟严重影响质量。
特种橡胶技术网,橡胶技术网为胶友们提供技术咨询,橡胶资料的下载,橡胶行情的了解,橡胶设备的买卖,橡胶人才的招聘。
为广大从事橡胶行业的人士提供更优质的交流平台。
8 v+ D' ~$ J7 X- c. F
3.为了提高硫化速度一般有两种方法首先是加温,再一种是增加促进剂用量或改用超超促进剂等,如加温对物性要求不高的产品是可以考滤的。
但很难控制的。
因为按理论计算每提高10度硫化时间约缩短一半不到点时间。
如提高温度也应该按这样推算应提高多少温度。
增减促进剂来调整流化速度是常用的一种方法,它必须是在设定好温度及时间后,再增减促进剂来调节的。
* [3 Y# Q. k( w- Y
调整促进剂是有讲究的,因为促进剂及硫磺在橡胶中的溶解度是很小的。
当超过它的溶解度它就会跑出来,出现喷霜现象。
而且物性也要有很大的变化。
( g0 v1 c- Q! c5 J# [$ B
实践证明。
一般普通产品促进剂用量应越少越好。
加减促进剂不应该按比例进行的。
应该增减第二。
第三促进剂,提高活化性能。
这样就可以有效地控制促进剂的喷霜问题,从而不影响产品的物性及稳定性。
3 m/ n* q7 J- M$ X/ @$ C8 b
提高生产力不能完全从减少硫化时间来考滤。
一般厂家都是从操作工增加操作模具数量来考滤的。
盲目增加促进剂、提高温度,来提高产量有以下几点危害.
, S5 R8 ]% l5 p- L/ | 1.物性影响。
. w, M: m q, {' j) t -橡胶技术咨询,橡胶配方网,橡胶技术转让,橡胶贸易,橡胶人才,橡胶设备,橡胶书籍,橡胶资料最专业橡胶行业网站- Rubber In China2.有喷霜的可能/ \' f3 G* G. @$ _
3.胶料易自硫.特种橡胶技术网) c: M2 H) k2 {# C
4.胶料粘性大,硫化性能差、不易操作。
8 P2 n! D2 n# o- ~" n: ?硅橡胶论坛,乙丙胶论坛,氟橡胶论坛,丙烯酸脂论坛,聚胺脂橡胶论坛,丁腈橡胶论坛,橡胶配方网,橡胶论坛,网上橡胶城,橡胶人才,最专业的橡胶行业网站优秀的配方应选用最适应橡胶硫化温度的最佳上限,最少的促进剂用量,最短的硫化时间。
这三个主面来考滤的。
7 b- W8 x8 _5 目前国内有很多橡胶厂的工艺生产8MM厚度以下的模压制品,采用DM—M---TMTD—D 促进剂四种并用搭配是一种很优秀的配方,他的优点是硫化曲线平坦,焦烧时间长,易控制,不易喷霜。
8 F! ?; g0 U% Q. w+ F- D+ K -橡胶技术咨询,橡胶配方网,橡胶技术转让,橡胶贸易,橡胶人才,橡胶设备,橡胶书籍,橡胶资料最专业橡胶行业网站- Rubber In ChinaDM为第一促进剂决定于整个硫化进程,而且在四种促进剂中用量最多,并决定于橡胶的某种物性。
一般情况下是不应该增减的。
7 R3 c- t" A$ K9 u# M的用量少一点它可以提高硫化速度,作为第二促进剂使用。
特种橡胶技术网,橡胶技术网为胶友们提供技术咨询,橡胶资料的下载,橡胶行
情的了解,橡胶设备的买卖,橡胶人才的招聘。
为广大从事橡胶行业的人士提供更优质的交流平台。
6 A z9 g! R4 \2 b, N# ^ T
在硫化进程中它与DM是既互相抑制又互相活化的,这种并用对硫化速度的控制起着关健作用。
并且是一种塑解剂,有利于橡胶分子的塑解。
5 x: A8 c* V/ C7 O2 e" r特种橡胶技术网,橡胶技术网为胶友们提供技术咨询,橡胶资料的下载,橡胶行情的了解,橡胶设备的买卖,橡胶人才的招聘。
为广大从事橡胶行业的人士提供更优质的交流平台。
TMTD是第三促进剂它是一种超超促进剂用于加快硫化速度,一般用量不超过DM的10%,否则用多了胶料易自硫,胶料物性下降。
1 y% e' Q7 o& t
促进剂D本身是种中速促进剂。
单一用时硫化速度不快,一般用于厚制品。
但是它是一种碱性促进剂,与DM及M并用时可以迅速活化,硫化速度立即加快。
它作为助促进剂用,主要当作活化剂使用,用于撑控硫化速度。
一般不超过DM的20%。
它在调控硫速时与TMTD 一起调整为好。
特种橡胶技术网,橡胶技术网为胶友们提供技术咨询,橡胶资料的下载,橡胶行情的了解,橡胶设备的买卖,橡胶人才的招聘。
为广大从事橡胶行业的人士提供更优质的交流平台。
! V, u F8 w4 r1 A8 v
TMTD在高温下会分解出M迅速活化D/DM。
特种橡胶技术网,橡胶技术网为胶友们提供技术咨询,橡胶资料的下载,橡胶行情的了解,橡胶设备的买卖,橡胶人才的招聘。
为广大从事橡胶行业的人士提供更优质的交流平台。
9 ]2 H* `& J+ y, O' |
不同的促进剂在橡胶中的溶解度是不同的,这种多种促进剂并用后可以减少单一促进的用量。
对控制橡胶制品中的促进剂喷霜起着关健的作用。
也大大地方便了硫化速度的调节。
不同的物性,不同的焦烧、不同的硫化时间,应用不同的促进剂搭配。
盲目地提高硫化温度来加快硫化速度是一种最愚蠢的做法。
-橡胶技术咨询,橡胶配方网,橡胶技术转让,橡胶贸易,橡胶人才,橡胶设备,橡胶书籍,橡胶资料最专业橡胶行业网站- Rubber In China& _8 J3 G0 t- q. Q) [8 |/ u
用最佳的硫化温度,合理地使用促进剂搭配,照样能设计出硫化速度快,物性良好的配方,在是日常生产中,要追求快速硫化在1.5分以下可以采用M/H 或M/TS并用,要求一般的焦烧、较快的硫速的在3分促以下的可以采用DM/D/TMTD,在4.5分钟以下可以采用DM/M/TMTD并用。
类似的并用举不胜举。
硅橡胶论坛,乙丙胶论坛,氟橡胶论坛,丙烯酸脂论坛,聚胺脂橡胶论坛,丁腈橡胶论坛,橡胶配方网,橡胶论坛,网上橡胶城,橡胶人才,最专业的橡胶行业网站/ w" D9 m1 {% B7 W6 r' {
最佳硫化时间也不是随便而定的,是根据产品的厚度、硫化温度计算出的,计算公式书上都有的我也不多讲了,也可用实践经验公室估算,6MM以下按T90时间,超过6MM可以按T90+(m-6)分钟计算。
能生产出一种优秀的产品除了要有一张合理优秀的配方。
硅橡胶论坛,乙丙胶论坛,氟橡胶论坛,丙烯酸脂论坛,聚胺脂橡胶论坛,丁腈橡胶论坛,橡胶配方网,橡胶论坛,网上橡胶城,橡胶人才,最专业的橡胶行业网站" J" h l) t7 U. o
在硫化时间、温度、压力及生产工艺因素方面也是同等重要。
4 ~/ o* j' K; z! L) 。