过程异常处理流程图
制程处理异常流程图 Process Abnormal Flow

- 品保 - 生產 - 工程
- 工程 - 品保 - 生產
- 品保
1,發現異常單位開出《品質異常處理單》 2,環境(GP)異常,需提交環境管理者代表。 3,異常品可能流至客戶端,須通知客戶。必要時召回處理。
原因分析及改善
效果確認
NG
OK
結案
- 《品質異常處理單》需7個 工作日完成 - 《外部聯絡單》
- 《品質異常處理單》
- 追蹤1個月
責任單位
制程处理異常流程圖
使,當IPQC抽檢發現線上原材料、半成品、成品、維修品、重工 品有不良時。 2,當制程工藝中發現已經通過進料檢驗之原材料、半成品品質 出現異常(超過IQC AQL允收水準)。 3,生產線班組長或製造主管、IPQC等發現製程中品質異常包含 (不限于)以下情況時: - 制程不良率超出各段制程不良管制目標的2倍或以上 - 各段制程因單一不良項目(如電氣測試耐壓不良、短路、開路等) 超出正常制程不良率2倍或以上 - 同一故障現象連續發生(3次或以上) - 依據SPC管制圖、CPK製程能力分析等相關品質管制工具及統計 數據,經判定連續超出目標上限及目標下限異常值 - 制程檢測GP 異常 - 不同產品混料、不同批號混料、不良品混入良品 - 數量異常、材料錯誤(包括包材) - 工站跳過、操作與SOP不符 - 生產環境異常(溫濕度超出控制范圍) - 超出使用期限或超出各種管理項目 - 治具使用錯誤、防護失效 - 設備設定錯誤、測試條件錯誤 - 設備校驗、保養、點檢失效 - 設備發生多次的錯誤、故障 - 可能涉及到人體安全
《异常处理流程》PPT课件

注:整个流程涵盖了PDCA管理循环及纠正预防的管理理念
23
部门责任的判定
开发部:
1.未及时确认零件样品; 2.设计错误或疏忽; 3.设计的延误; 4.设计临时变更; 5.设计资料未及时完成; 6.设计需要修改,设计人员未得到相关负责人的确认就安
1.由主要负责人召集. 2.最终处理报告完成. 3.小组成员认同效果确认结果,以及预防措施执
行.
12
问题处理流程(8-D模式)
13
8-D的成果:
8-D首重利用团队力量,因此无论是问题分析,或是对 策执行,都希望集众人之智,完成众人之事.
8-D特别注重以问题为经验,以对策为行动,所以在最 终处理过程中,对预防工作做要求.
8-D的内容都是运用QC七大手法、问题分析模式、 统计技朮等常用工具,作业质量要求能一致,且容易被 执行.
8-D依其步骤可设定处理成员与检核时限,对权责与 效果确认,是可以被严谨安排的,而且有利于追踪.
龙头分厂生产运作流程
产品部订单
订单评审
N 工艺评估
设备 人员
产能评估
N
主生产计划拟制 (装配调度)
追溯方式亦须告知.
6
问题处理流程(8-D模式)
5W2H提问技术: Why? 为何这样做,有无必要? What? 目的是什么? Where? 哪里做?有无更合适的地方? When? 时间安排好不好? Who? 谁来做?几个人做? How to do? 这样做法有沒有更好的? How much? 这样做的成本多少?
1.召集有关人员成立小组. 2.决定小组成员负责事项. 3.确定主要负责人.
4
问题处理流程(8-D模式)
异常处理作业流程图
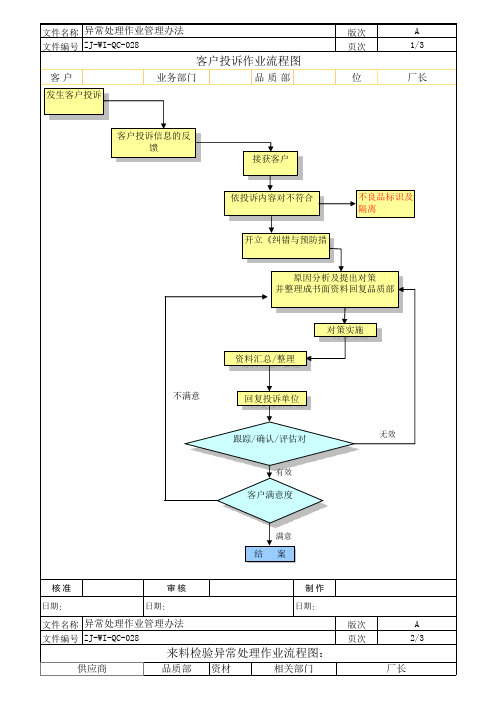
提出对策并实 施;书面回复
QA整理异常报告
对策实施效 果追踪确认
结案
相关部门会签
最终判定 与批示
核准 日期:
审核 日期:
制作 日期:
制程异常处理作业流程图:
生产部
品质部
工程/开发
责任部门
制程或检验发现异常 开具品质异常单
A 3/3
厂长
NO
QC确认不符 合事项
YES
QC确认制程 产品
NG
附《纠错与预防措施表》 并转入生产单位
不合格批处理 标示/隔离/退货/特 采/报废
初步确认分析
非制程不良
分析不良产生原因
制程不良
提出对策并实施; 书面回复品质部
文件名称 异常处理作业管理办法 文件编号 ZJ-WI-QC-028
客户投诉作业流程图
客户
业务部门
品质部
发生客户投诉
版次 页次
责任单 位
A 1/3
厂长
客户投诉信息的反 馈
接获客户
依投诉内容对不符合 开立《纠错与预防措
不良品标识及 隔离
原因分析及提出对策 并整理成书面资料回复品质部
不满意
资料汇总/整理
对策实施
YES
NO 各部门会签
异常单COPY各
MRB最终判定
开具不符合改善对策表
COPY供应商
供应商分析原因, 提出对策
不合格批处理 标示/隔离/退货
QA确认/评估对 策的符合性
NG OK
QA确认改
OK
结案
核准
审核
制作
日期:
日期:
日期:
文件名称 异常处理作业管理办法
版次
文件编号 ZJ-WI-QC-028
异常停线处理流程图

异常停线处理流程图
流程图 单位 时间 各单位权责 1.异常发生时,各制程反应问题点到质量/工艺或设备, 同 时开出停线通知单给质量追踪.
异常 发生
发生单位
5min
否 质量接到停 线信息后判 质量 10min 1.质量根据发生单位反馈问题点及停线判断标准初步判断 异常是否成立 2.异常成立则请工艺或技术单位进一步分析
质量召开异 常处理会议
发生单位 自行追踪 质量 5min
1.质量根据问题的严重性决定是否通知相关 单位开会议 2.不必开会则直接追踪责任单位改善处理
责任单位 改善对策
责任单位
5min
1.责任单位5min内给出改善对策及处理方法 2.若责任单位不能在15min内恢复产线生产必须 通知部门主管级以上领导处理
是 1.分析单位接到异常信息后15min给出初步 原因分析及责任单位,并通知责任单位确认 2.分析单位给出改善意见 3.质量跟踪责任单位改善对策及处理进度 4.若安全问题则由发生单位自行追踪责任单位 处理结案
分析单位
误判
安全异
工艺/技术 质量 责任单位召 责任单位
15min
必 要 开
制 程 异
不必开
不必sorting/重工
执行Sorting
必要 通知
质量
5min
若需要Sorting/重工质量负责召开处理会议
重 新 对 重策 新 对
通知PMC
PMC
5min
重大异常在30min内不能恢复生产则通知PMC, PMC根据实际情况决定是否调整排程
执行单位/技 术/工艺/质 量
执行单位 工艺 技术 质量
相关单位根据责任单位提供改善对策及处理方式 考量是否可以正常回复生产, 若不可恢复生产 则请责任单位重新给出对策
过程异常处理流程图
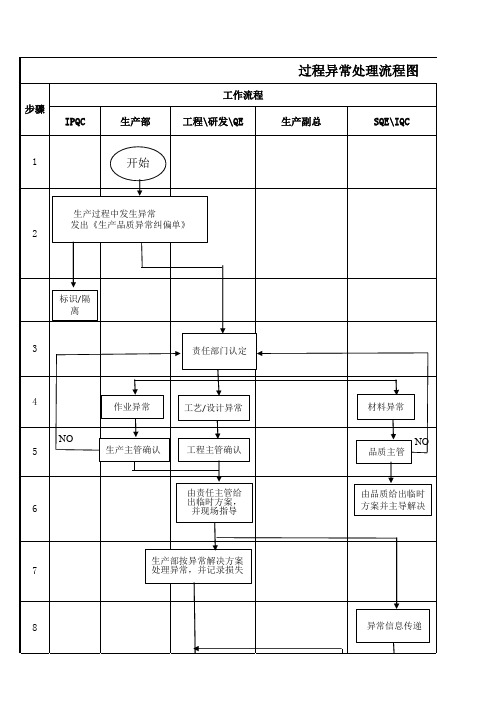
品质工程师根据品质数据判定是否可以结案
8
材料异常 NO
品质主管 由品质给出临时 方案并主导解决
异常信息传递
9 10 11 12 编制:
效果验证
NO
O K
由责任部门给出长 期纠正措施
上报副总,组队 分析原因
依来料异常处 理流程处理
确定处理对策
NO 品质工程师以及巡检进行监督实施,并对效果确认
结案 审核:
工作内容
1、异常包括:1、巡检人员在首件检验不良、巡线过程发现工艺 纪律不符、产品抽检不良;2、生产人员在生产过程中发现的不 符合作业SOP或产品异常等; 2、生产过程中,生产班组长、员工以及品质巡检发现异常后应 立即向所属部门报告,经主管确认后发出《生产品质异常纠偏单 》; 2、IPQC将生产异常纠偏单交给品质工程师进行分析
1、对于作业不良、工程不良要求责任人给出异常处理方式,如 挑选、返工等,如需改变操作手法等需更改SOP; 2、对于材料不良,要求IQC立即对物料进行确认并给出临时方 案:挑选、更换,对于无法挑选更换的需立即通知采购调货处理 。
针对判定批量返工的并存在品质隐患的: 由品质经理与副总一起裁决最总如何处理;
在确认异常后,由巡检立即对生产产品进行标识/隔离,必要的 需暂时停线
品质工程师对异常现象进行确认,并认定异常责任部门,涉及到 比较专业技能的内容需寻求品质主管或相关开发工程师进行分析
根据原因分析确定异常是属于作业不良\工艺、设计不良还是来 料不良
确认异常归属后由IPQC通知相应部门主管立即前往现场进行确认 处理,品质工程师进行现场跟踪
异常处理流程图

问题处理
品管部 各责任部 门
品管部 责任部门 人员
人员从接 到通知到 达现场时 间:10分
首件/巡 检记录/ 生产日报
钟
填写临时对策 填写纠正预防对策 对改善措施的跟进验证结果 处理结果知会相关单位
各责任部门现场对异常进行确认、分析, 制定临时对策方案,并将异常情况通知到 PMC/采购部。
各责任部 门
/
流程结束
/
/
/
序 号
流程图
检验准备
异常处理流程图
工作重点
流程开始
责任部门 责任岗位 时效性 相关表单
/
/
/
/
进料异常 物料异常
制程异常
异常 判定 填写异常联络单 作业异常
转序异常 继续作业
对物料的进料、生产制程及本单位生产完 成后的转序阶段,依相关的标准文件进行 品保部 检验和记录
1.品管人员依据相应的标准及严重程度进 行判定,可放行的继续下一工位,自己无 品质部 法判定或需要协助的呈报品质主管判定。
IQC PQC FQC 作业员 班组长
IQC PQC FQC
/
/
立即处理 /
技术异常
品管课长对问题再次确认和判定,可接受 进行下一工位,不可接受的要求QC对问题 进行统计描述,填写相关异常单。 2.品管课长对问题性质进行判定,并通知 相关责任部门到现场对问题进行分析和处 理。 3.各相关部门人员在接到通知后在规定时 间内到达现场对问题进行分析。(如出差 应指定代理人处理)
各责任部 分人员
30分钟
品质部备案,并由责任部门对异常问题填 写纠正与预防措施具体内容
责任部门
责任部门 人员
24小时
由品管部对验证暂时对策、纠正与预防措 施具体内容,并填写验证结果。验证OK后 存档。
异常处理汇报流程图

3分钟以内
设备组/行政部人员 确认原因及处理方
案
5分钟以内
备 注: 1.G.H项异
常 2.处E项理异完常毕 处理完毕后
预计6小时后会延 误
60分钟内仍未恢复 正常
10分钟以内
3.A.B.C.D 项处理完毕 后于次日 内,责任部 门将异常原 因改善对策 及处理结果 提报至副总 经理室. 4.F.项异常 处理完结后 于次日内, 生产部将异 常原因改善 对策及处理 结果提报至 计划部. 5.所有异常 当日未处理 完毕,相关 主管不得离 开. 编 制:
20分钟以内未恢复
生产部主管
60分钟以内未恢复 正常动作
工程部
主管
120分钟以内未恢复
品质部主管
正常动作
计划部主管
180分钟以内未恢 复正常动作
D
待治工具/ 原物料
FPC到当前站前12 小时仍待治工具/
原物料
生产部\采购部
FPC到站前6小时仍 待治工具/原物料
生产部主管 工程部主管 采购部负责人 计划部主管
异常处理汇报流程图
A
不合格品异 常
发现问题即上报
工艺
确认
FPC 30分钟未有处理结 生产部主管 同样总是点连续两
果
计划、品质主管
批板(含)
体系异 常
12小时内未恢复
品保部体系工程师
24小时内未恢复
质保部负责人
36小时内未恢复
48小时内恢复
管理者代表停 产整顿
C
工艺工程异 常
审核:
批准:
预计一天后会延误
市场部主管 计划部主管
预计6小时后会延误
设备部与生产部主
G
停水/电/气
制程异常处理流程图

注:执行日期以会签日期为准。
制常的通知部门及上报部门,有各分厂长知会技术部人员处理和对异常的预判, ②各部门协同配合,并遵循上下级式管理,技术部人员或现场检验员只需与责任分厂厂长进行沟通,一 直认可后,具体的指令下达则由分厂长直接对下级下达, ③现场操作人员若切实有其它造成重大异常的原因,各部门应充分分析其原因,给予判断,责任划分时 需如实考虑。 会签:
NG OK
由技术部、质保部、生产部共同分析原 因,确定责任部门或责任人并由质保部 开出《纠正措施预防表》 OK N G 责任部门或个人依据《纠正措施预防表 》的要求进行临时措施的实施 OK 检验员或技术人员对效果的确认
OK 质保部进行验证,并确认改善 效果 OK
责任厂长签字确 认
正常生产
OK 技术部制作“受控文件”即永久预防措 施 N G OK 质保部跟踪验证最终效果并判断异常是 否能关闭 OK 结案、归档
制程异常处理流程图
现场检验员/操机人员发现异常
轻微可立即纠正的异常 OK 通知班长或厂长判断是否可以 继续生产 NG
重大异常/或明确异常根本原因 OK OK 检验员开具《半成品首检巡检记录单》 或《装配厂反馈问题处理跟踪表》,由 班长或操机人员对不良品进行隔离并标 示
OK
技术部、质保部、生产部共同 给出处理措施与预防方案
制程异常处理流程图

备注:停线超过30分钟还无法确定及找到方案时,QE或PE职员下令拉长换线处理,并通知生产管理.
为了保障生产顺利,PE安排生产进行选别或加工时,生产无条件必须接受,生产可提出工时申请单进行工时索赔.
批准:生产作成来料异常处理流程产线来料异常发生
QE/PE 确定IQC 来
QE 影响程度确认QE 通知IQC 确认通知生产及计划
IQC 确认无库存
继续生产联络IQC 小大产线产品能选别生产暂时安排人继续生产OK OK OK 无法选别能让步接收吗NG
NG 停线处理
供应商联系及对策
QE/PE 指令暂时:选别
生产统计工时交要求供应商对:
产线不良返工
仓库不良返工纠正预防措施单对策回复检讨、结案
IQC 内部检讨与对IQC 确认有库存
仓库有没有不同质量是OK 的吗?继续生产OK OK 代仓库有没有不同批次
或不同日期的物料质量是OK 的吗?继续生产
OK OK NG
同一批物料也是质量是OK 的吗?领取仓库物料继
OK OK NG
NG QE/PE 指令暂时:加工IQC 统计不良数
据通知供应商QE 工作范围IQC 工作范围。
生产异常处理流程图(只作参考)

产生记录 1 2 3 、、、 《《《 制首制 程件程 检检巡 验查检 不记记 合录录 格表表 登》》 记 表 》
参考文件 1 2 、、 《《 不生 合产 格过 品程 控控 制制 程程 序序 》》
处置单位原因分术,采 暂定对策及永久对策 购,商务 给予改善。
效果确认
NG
OK
改善结案
5、品质部对异常改 善效果进行确认如OK 品质,生产,技 则结案,如NG需再行 术,采购,商务 分析解决。
审核:
编制:
生产异常处理流程图
编号:
作业流程图 制程异常发生
工作内容
负责单位
1、各作业工序发生 生产,品质 异常
确认能否自行解决
NG
发出制程异常处理单
2、该异常发生工序 人员是否能自行改善 解决,如是则纠正即 生产,品质 可,否则,发出制程 异常处理单。 3、处置单位针对异 生产,技术,采 常不良进行原因分析 购 。
质量异常处理流程图

零(合)检检验记录(专检)质量记录台帐
产品标识卡
质量问题通知单
退修品通知单
质量问题通知单
紧急/例外放行申请单
退修品通知单
质量问题通知单
紧急/例外放行申请单
退修品通知单
质量问题通知单
紧急/例外放行申请单退修品通知单
质量问题通知单
紧急/例外放行申请单
十你想过普通的生活,就会遇到普通的挫折。你想过最好的生活,就一定会遇上最强的伤害。
质量异常处理基准
异常
发生时流程
1、停止生产2、隔离标识3、报告班长4、等待指示
1首次发现的不合格
2初物不合格
3关键工序的不合格
4性能项目的不合格
5不良品的连续发生
6其它不合格
责任者
操作工
上序操作工、班长
检查员
工艺员
车间主任
质量部长
技术部长
主管经理
处置对策
内容
异常定义:连续三件不合格以及控制图出现异常。
车间主任:组织追溯不合格品;向质量部报告。
不合格品处置;停产或再生产指示
对不合格进行评审,对工程进行确认,向质量部报告。
对不合格进行评审,对工程进行确认,明确处理方法。
对不合格进行评审。
再生产品质
确认
品质确认后作业开始。
追溯无误后恢复生产。
确认生产的产品无误。
对不合格进行功能性能试验。
记录
零(合)检检验记录(自检)
处置方式:停机、隔离、标识、向上序操作工、班长、检验员报告,等待作业。异常排除后再作业。
上序操作工:自检追溯确认,返工返修后再检验。
班长:互检、追溯、确认,向车间主任报告。处置不合格。
制程品质异常处理流程图-050

制程品质异常处理流程图-050深圳市南邦电子有限公司Shenzhen BANBANG Electric Co., Ltd.版本/版次 A/0 文件编号 DW-QC-050拟定日期 2010-4-28 生效日期 2010-4-28文件名称制程质量异常处理流程图发放形式新版本发行版本更改/修订取代文件文件修改记录序号修订日期变更编号修改内容修改原因版本/次总页数 1 2 3 4 5 会签部门姓名会签意见会签部门姓名会签意见 ?总经办 ?市场部 ?产品开发部 ?财务部 ?品质部 ?生产部 ?行政部 ?采购部 ?仓库 ?PMC 核准审核制定制作单位发行章袁志勇品质部未经许可不得翻印深圳市南邦电子有限公司文件编号 DW-QC-050Shenzhen NANBANG Electric Co., Ltd.文件类别指导书版次 A/0 文件名称制程质量异常处理流程图页次 1/1 流程图重点说明生产制程不良控制标准老化前不良1%以上开出品质异常单产品老化不良1‰以上开出品质异常单老化后不良2‰以上开出品质异常单品保确认后填写不良现象,不良品标示清楚,交接PE分析. 品保确认PE接到品质异常联络单后,分析不良原因,并记录其不良原因.PE拿到样品与PE分析品质异常联络单,找责任单位同品保人员开会检讨、改善.在确认并签名责任单位主管填写临时对策与永久对责任单位策责任单位将品质异常联络单交给品保,品保在责任单位完成时间跟踪改善结品保跟踪果,OK后由品保归档,NG则重新知会相关部门开会检讨.品质异常联络单由品保归档,保存. 归档下面是赠送的中秋节演讲辞,不需要的朋友可以下载后编辑删除~~~谢谢中秋佳节演讲词推荐中秋,怀一颗感恩之心》老师们,同学们:秋浓了,月圆了,又一个中秋要到了!本周日,农历的八月十五,我国的传统节日——中秋节。
中秋节,处在一年秋季的中期,所以称为“中秋”,它仅仅次于春节,是我国的第二大传统节日。
中秋的月最圆,中秋的月最明,中秋的月最美,所以又被称为“团圆节”。
车间异常处理流程图
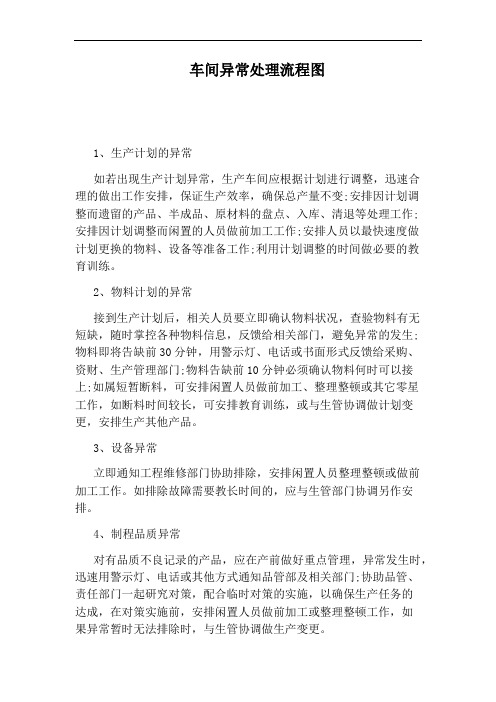
车间异常处理流程图
1、生产计划的异常
如若出现生产计划异常,生产车间应根据计划进行调整,迅速合理的做出工作安排,保证生产效率,确保总产量不变;安排因计划调
整而遗留的产品、半成品、原材料的盘点、入库、清退等处理工作;
安排因计划调整而闲置的人员做前加工工作;安排人员以最快速度做
计划更换的物料、设备等准备工作;利用计划调整的时间做必要的教
育训练。
2、物料计划的异常
接到生产计划后,相关人员要立即确认物料状况,查验物料有无短缺,随时掌控各种物料信息,反馈给相关部门,避免异常的发生;
物料即将告缺前30分钟,用警示灯、电话或书面形式反馈给采购、
资财、生产管理部门;物料告缺前10分钟必须确认物料何时可以接上;如属短暂断料,可安排闲置人员做前加工、整理整顿或其它零星
工作,如断料时间较长,可安排教育训练,或与生管协调做计划变更,安排生产其他产品。
3、设备异常
立即通知工程维修部门协助排除,安排闲置人员整理整顿或做前加工工作。
如排除故障需要教长时间的,应与生管部门协调另作安排。
4、制程品质异常
对有品质不良记录的产品,应在产前做好重点管理,异常发生时,迅速用警示灯、电话或其他方式通知品管部及相关部门;协助品管、
责任部门一起研究对策,配合临时对策的实施,以确保生产任务的
达成,在对策实施前,安排闲置人员做前加工或整理整顿工作,如
果异常暂时无法排除时,与生管协调做生产变更。
5此外,如遇到设计工艺异常应迅速通知品管、生技或开发部。
水电异常则要迅速采取措施降低损失,通知工程动力维修部门抢修,对于闲置人员可做其他安排。
生产异常排除后,一定要坚持“三不”原则进行处理,以避免类似问题的重复发生。
异常处理及操作流程ppt课件

3、遇到异常不要慌张,检查现场现物,判断重要迅速处理,处乱不惊。
4、制定应急措施和再发防止措施。 应急措施具体作法:①明确发生异常时的群体。②将异常现象迅速通知有 关单位,并要求其参与处理。③对过程采取处置措施,使异常现象暂时控 制而不再恶化。④将异常群体选别,对不良品修理,调整或对人员作教育 训练。⑤将处置内容记入异常报告单。 再发防止具体作法:①检讨相关标准(ⅰ、是否有标准?标准明确了没 有?答案若是否定,则增订标准。ⅱ、是否遵守标准?若遵守标准而结果 又不好,则修改标准。ⅲ、标准了解了没有?若不了解则须培训标准。) ②对策愚巧化:若牵涉到要小心,注意、加强等因数,则尽量考虑使用防、 呆的方法。
操作方法有隐患 无标准化 指导书
法
环
管理
6、异常发生后操作步骤
6.1、检查现场现物,判断重要性,迅速处理。 6.2、联络关系部署 6.3、迅速确定,进行后工程品质确认; 6.4、进行对象范围把握和不良品排除(不良品分类识别,良品选出等) 6.5、问题严重时,向上司报告——等待指示; 6.6 、追查不合格品源头; 6.7 、联络前后工程,品管部; 6.8 、对发生工程进行对策处置; 6.9 、在此加合格标志,控制流出; 6.10、在合格品到来前点检,选出不合格品; 6.11 、工程内剩余工件及库存品也全数检选出; 6.12 、不合格品必需进行识别; 6.13 、修复是遵守规定。 ; 6.14、排除原因,启动设备; 6.15、研究对策和在发生防止,再次明确指导各工程异常是什么。
应急措施
如遇重大问题或需相关部门共同协商解 决的,由生管主导召开现场会。
应急措施由生管主导,生产、品管共同确认后 方可实施,重大品质问题延误交期的需计划部 确认。根据实际情况决定是否停产或转
异常管理程序及异常处理流程图

程序文件
異常管理程序
文件編號﹕____________
版 本﹕___________
修 訂﹕____________
日 期﹕___________
審 核﹕____________
日 期﹕___________
批 准﹕____________
日 期﹕___________
文件編號
有流到客戶端 公司內部討論 聯繫顧客處理
使用表單/文件/ 说明
進料檢驗結果報告表 廠商品質改善報告 品質異常處理單 不合格品處理單 品質異常改善追蹤單 客訴處理單
廠商品質改善報告 3 個工作日回復 品質異常處理單 7 個 工作日完成 品質異常改善追蹤單 3 個工作日完成 一般客訴三個工作日 完成 重大客訴一個工作日 完成
文件編號
程
序
文
件
版本/次
A0
異常管理程序
頁
碼
第 2 頁 共 10 頁
4.1.3 供應商提出之其制程品質異常或環境管理、測定異常時,SQE開出《廠商品質改善
報告》要求供應商於3個工作日內回復分析報告及改善對策(環境管理、測定異常需
要1個工作日內回復風險評估,3個工作日內回復分析報告及改善對策)。
4.1.4 供應商審查時,發現潛在的品質、環境異常時,SQE開出需將缺失項目列入《供應
異常處理流程圖
異常來源 ooug
發放異常報告
實施緊急處理
緊急對策討論
原因分析
NG
復線對策 追蹤確認 OK 影響範圍評估 異常品處理
短期對策制訂
長期對策制訂
NG
對策效果 確認
OK
結案
生產是否停止作業-出貨是否停止作業 不良原因調查 產線復線之臨時對策討論 風險波及範圍的判斷
异常处理流程图

职责
IPQC及生产主管确
认
IPQC及生产主管确认OK
OK
品质主管
同时判断是否停止生产
半小时内
责任部门不认可
责任部门认可
责任部门
3-5个工作日
IPQC
IPQC
技术部、生产部、品质部
总经理品质主管及总经理
问题连续三批未发生
技术部、生产部、品质部
流 程 图
IPQC或其他任
何员工品质主管
技术部、生产部、品质部
异常提出时机
开出品质异常处理单
审核
异常分析
找出异常责任部门并
制定临时处理措施
审核及批准
依不合格品控制程序4.2-4.3
IPQC 与生产主管意见分歧
异常关闭
责任部门填写相
关改善措施
措施审批
跟踪验证及效
果确认。
- 1、下载文档前请自行甄别文档内容的完整性,平台不提供额外的编辑、内容补充、找答案等附加服务。
- 2、"仅部分预览"的文档,不可在线预览部分如存在完整性等问题,可反馈申请退款(可完整预览的文档不适用该条件!)。
- 3、如文档侵犯您的权益,请联系客服反馈,我们会尽快为您处理(人工客服工作时间:9:00-18:30)。
品质工程师根据品质数据判定是否可以结案
8
材料异常 NO
品质主管 由品质给出临时 方案并主导解决
异常信息传递
9 10 11 12 编制:吴烧威
效果验证
NO
O K
由责任部门给出长 期纠正措施
上报副总,组队 分析原因
依来料异常处 理流程处理
确定处理对策
NO 品质工程师以及巡检进行监督实施,并对效果确认
结案 审核:马文虎
工作内容
1、异常包括:1、巡检人员在首件检验不良、巡线过程发现工艺 纪律不符、产品抽检不良;2、生产人员在生产过程中发现的不 符合作业SOP或产品异常等; 2、生产过程中,生产班组长、员工以及品质巡检发现异常后应 立即向所属部门报告,经主管确认后发出《生产品质异常纠偏单 》; 2、IPQC将生产异常纠偏单交给品质工程师进行分析
步骤
IPQC
1
生产部
工作流程
过程异常处理流程图
工程\研发\QE
生产副总
SQE\IQC
开始
生产过程中发生异常 发出《生产品质异常纠偏单》 2
标识/隔 离
3
责任部门认定
4 NO
5
6
作业异常Βιβλιοθήκη 工艺/设计异常生产主管确认
工程主管确认
由责任主管给 出临时方案, 并现场指导
生产部按异常解决方案
7
处理异常,并记录损失
在确认异常后,由巡检立即对生产产品进行标识/隔离,必要的 需暂时停线
品质工程师对异常现象进行确认,并认定异常责任部门,涉及到 比较专业技能的内容需寻求品质主管或相关开发工程师进行分析
根据原因分析确定异常是属于作业不良\工艺、设计不良还是来 料不良
确认异常归属后由IPQC通知相应部门主管立即前往现场进行确认 处理,品质工程师进行现场跟踪
1、对于作业不良、工程不良要求责任人给出异常处理方式,如 挑选、返工等,如需改变操作手法等需更改SOP; 2、对于材料不良,要求IQC立即对物料进行确认并给出临时方 案:挑选、更换,对于无法挑选更换的需立即通知采购调货处理 。
针对判定批量返工的并存在品质隐患的: 由品质经理与副总一起裁决最总如何处理;
1、SQE/IQC对不良状况情况进行确认,并将异常信息传递给资源 管理以及采购员; 2、SQE/IQC需要针对异常流出原因进行分析,检讨为何无法检出 导致流入产线。
IPQC和生产班组长对解决方案进行操作验证
对于生产异常问题由IPQC追踪各责任部门的异常回复,由品质工 程师对异常回复的可执行性和符合性进行判定