T202型铁钼有机硫加氢转化催化剂的硫化工艺
T202C(二甲基二硫)硫化方案

T202C有机硫加氢催化剂硫化方案T202C有机硫加氢催化剂硫化就是利用焦炉气中高浓度H2S或低浓度焦炉气加二甲基二硫,将催化剂的金属组分由氧化态转化成相应的硫化态的过程。
硫化的关键是要避免金属氧化态在与H2S反应转化成硫化态之前被热氢还原。
所以,催化剂硫化时,必须控制好温度与循环气中H2S含量,在H2S未穿透催化剂床层前,床层最高点温度不应超过230℃。
一、利用低硫煤气加二甲基二硫硫化方案1、硫化条件:气源:焦炉气硫化空速:一般控制在300~400h-1,2、升温硫化流程及曲线(1)流程:焦炉气——压缩机——升温炉——2台预加氢反应器并联——一级加氢反应器——放空(2)升温硫化及放硫曲线:见表1二、硫化说明及注意事项1、系统用氮气(氮气纯度>99.9%)置换合格后(主要指氧含量小于0.5%),点燃升温炉,根据升温曲线调节燃气量,一般控制升温炉出口温度不大于床层温度50℃,床层到200℃并拉平后,引入低硫煤气(经湿脱),并配入二甲基二硫,控制床层最高温度≤400℃。
用煤气升温也可以,只是对催化剂有一定影响。
2、铁钼反应器床层到200℃,开始有硫化反应,为了加速硫化,系统压力可逐渐提到1.0Mpa,另外开始滴加二甲基二硫。
(每吨催化剂约需二甲基二硫65Kg),3、硫化时注意提温不提氢,提氢不提温原则。
4、硫化初期,二甲基二硫配入后分析入口H2S≤10g/Nm3,硫化主期,逐步增加二甲基二硫加入量,使入口H2S达到10-20g/Nm3。
5、370℃时开始有放硫反应,为了加速放硫,在370℃恒温后,压力逐步降到0.1-0.2Mpa并停止加二甲基二硫。
6、硫化及放硫期间,每小时分析一次铁钼反应器进出口H2S和H2含量,当进出口H2S和H2含量基本相等时硫化结束,当出口H2S≤300mg/Nm3时,放硫结束。
7、硫化结束后将压力提到0.8Mpa、关闭进出口阀,使铁钼反应器保温、保压。
8、床层在120度以前主要是脱催化剂吸附水的过程,故应每半小时开导淋一次放水。
T202A型加氢催化剂在焦化干气脱硫装置上的应用
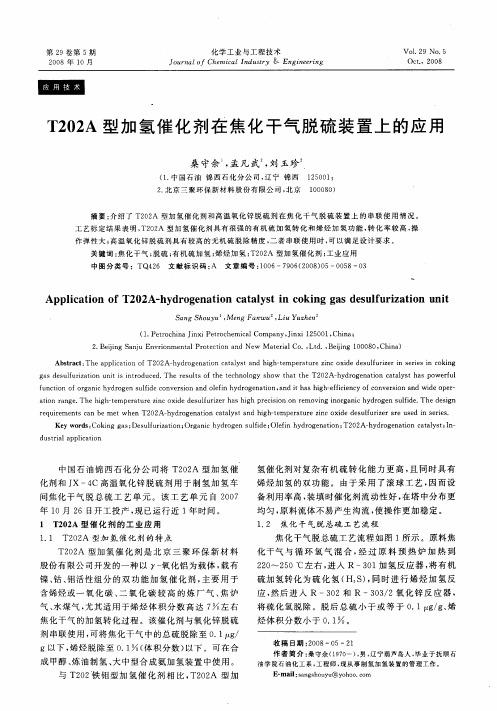
20 年 1 08 0月
化 学工 业 与工 程 技 术 J u n l f C e c lI d s y & E g n e ig o r a h mi n u t o a r n i er n
V o129 N O 5 . .
0 c. 00 t。2 8
T 0 A 型加 氢 催化 剂在 焦化 干气 脱 硫 装 置上 的应 用 22
桑 守余 孟 凡 武 刘 玉珍 , ,
(. 国石 油 锦 西石 化 分 公 司 , 宁 锦 西 15 0 ; 1中 辽 201
2 北 京 三 聚环 保 新 材 料 股 份 有 限 公 司 , 京 1 0 8 ) . 北 0 0 0
Ab t a t Th p l a i n o 0 A— y r g n t n c t l s n ih t mp r t r i co ie d s l r e n s re n c k n sr c : e a p i t fT2 2 h d o e a i a ay ta d h g —e e a u ezn x d e u f i r i e is i o ig c o o u z g sd s l rz t n u i i i to u e . e r s l ft e t c n l g h w h tt e T2 2 h d o e a i n c t l s a o ru a e u f ia i n t s n r d c d Th e u t o h e h o o y s o t a h 0 A— y r g n t a a y th s p we f l u o s o f n t n o r a i h d o e u f e c n e so n lf y r g n t n a d i h sh g — fiin yo o v r in a d wie o e — u c i fo g n c y r g n s li o v r i n a d o e i h d o e a i , n t a i h efce c fc n e so n d p r o d n o a in r n e Th i h tm p r t r ic o i ed s l r e a i h p e ii n o e vn n r a i h d o e ufd . ed sg t a g . eh g - e e a u e zn x d e u f i rh sh g r cso n r mo i g i o g nc y r g n s lie Th e i n o u z r q ie n sc n b twh n T2 2 h d o e a in c t l s n i h t mp r t r i co i e d s l rz ra e u e n s re . e u r me t a eme e 0 A— y r g n to a ay ta d h g — e e a u e zn xd e u f ie r s d i e is u Ke r s Co i g g s De u f rz to Or a i y r g n s l d ; ei y r g n t n T2 2 h d o e a i n c t l s ;n y wo d : k n a ; s lu i in; g n c h d o e u f e Olfn h d o e a i ; 0 A— y r g n t a a y t I — a i o o
T202有机硫加氢催化剂硫化方案
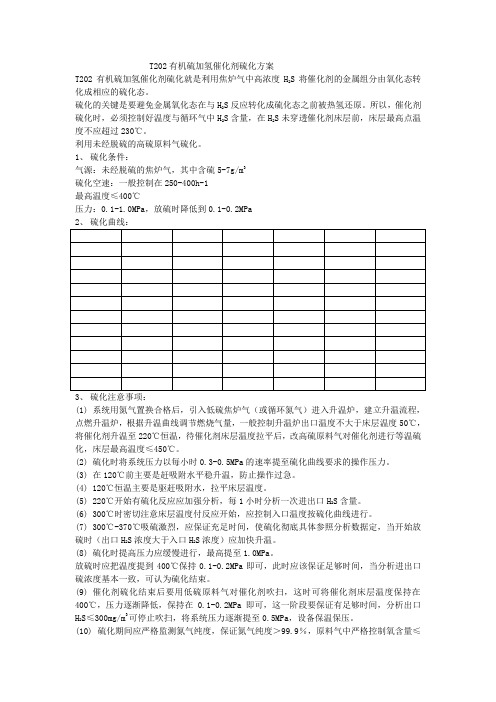
T202有机硫加氢催化剂硫化方案T202有机硫加氢催化剂硫化就是利用焦炉气中高浓度H2S将催化剂的金属组分由氧化态转化成相应的硫化态。
硫化的关键是要避免金属氧化态在与H2S反应转化成硫化态之前被热氢还原。
所以,催化剂硫化时,必须控制好温度与循环气中H2S含量,在H2S未穿透催化剂床层前,床层最高点温度不应超过230℃。
利用未经脱硫的高硫原料气硫化。
1、硫化条件:气源:未经脱硫的焦炉气,其中含硫5-7g/m3硫化空速:一般控制在250-400h-1最高温度≤400℃压力:0.1-1.0MPa,放硫时降低到0.1-0.2MPa(1)系统用氮气置换合格后,引入低硫焦炉气(或循环氮气)进入升温炉,建立升温流程,点燃升温炉,根据升温曲线调节燃烧气量,一般控制升温炉出口温度不大于床层温度50℃,将催化剂升温至220℃恒温,待催化剂床层温度拉平后,改高硫原料气对催化剂进行等温硫化,床层最高温度≤450℃。
(2)硫化时将系统压力以每小时0.3-0.5MPa的速率提至硫化曲线要求的操作压力。
(3)在120℃前主要是赶吸附水平稳升温,防止操作过急。
(4)120℃恒温主要是驱赶吸附水,拉平床层温度。
(5)220℃开始有硫化反应应加强分析,每1小时分析一次进出口H2S含量。
(6)300℃时密切注意床层温度付反应开始,应控制入口温度按硫化曲线进行。
(7)300℃-370℃吸硫激烈,应保证充足时间,使硫化彻底具体参照分析数据定,当开始放硫时(出口H2S浓度大于入口H2S浓度)应加快升温。
(8)硫化时提高压力应缓慢进行,最高提至1.0MPa。
放硫时应把温度提到400℃保持0.1-0.2MPa即可,此时应该保证足够时间,当分析进出口硫浓度基本一致,可认为硫化结束。
(9)催化剂硫化结束后要用低硫原料气对催化剂吹扫,这时可将催化剂床层温度保持在400℃,压力逐渐降低,保持在0.1-0.2MPa即可,这一阶段要保证有足够时间,分析出口H2S≤300mg/m3可停止吹扫,将系统压力逐渐提至0.5MPa,设备保温保压。
T202A脱硫剂硫化方案

T202A脱硫剂硫化方案本次公司因生产需要,将原脱氧槽脱氧剂更换为****公司T202A 镍钼脱硫剂,共6.5方。
T202A型加氢催化剂在未硫化前其活性金属组分:钴、钼、镍为氧化态。
为了最大的发挥其活性,使用前必须进行预硫化。
1、硫化原理及工艺条件1.1加氢催化剂的主要活性组分有 Co-Mo、Ni-Mo 和 Fe-Mo 等类型,在氢气存在条件下,可与H2S发生如下硫化反应:MoO3+H2+2H2S=MoS2+3H2O9Fe2O3+16H2S+11H2=2Fe9S8+27H2O9CoO+8H2S+H2=Co9S8+9H2O3NiO+H2+2H2S=Ni3S2+3H2O1.2 硫化剂及氢解反应常见的硫化剂有二硫化碳(CS2)、二甲基硫醚(DMS)、二甲基二硫(DMDS),均可以在 H2 气氛中发生氢解反应生成 H2S:CS2+4H2=2H2S+CH4CH3SCH3+2H2=H2S+2CH4CH3SSCH3+3H2=2H2S+2CH41.3 硫化剂用量简算法CS2用量:催化剂体积数(m3)×堆比重(T/m3)×65(Kg/T)=CS2用量(Kg)CS2一般为铁桶包装,规格:250Kg/桶,请自行核算所需购买数量。
DMDS 用量:催化剂体积数(m3)×堆比重(T/m3)×80(Kg/T)=DMDS 用量(Kg)DMDS 一般为铁桶包装,规格:250Kg/桶,请自行核算所需购1.4 硫化条件气源:原料气(其中 H2含量≥20%),硫化氢 3-10g/Nm3。
硫化的关键是要避免金属氧化物在与 H2S 反应转化成硫化态之前被热氢还原。
所以,催化剂硫化时,必须控制好温度与循环气中 H2S 含量,在 H2S 未穿透催化剂床层前,床层最高点温度不应超过 230℃ 2、升温硫化流程2.1 硫化工艺说明:2.1.1本次硫化升温阶段用1#氮压机氮气进行升温,升温热源用再生气预热器的中变气提供,速率控制用再生气预热器进口新配的DN125冷氮气阀控制。
神华二级铁钼T202硫化方案1(北京三聚)
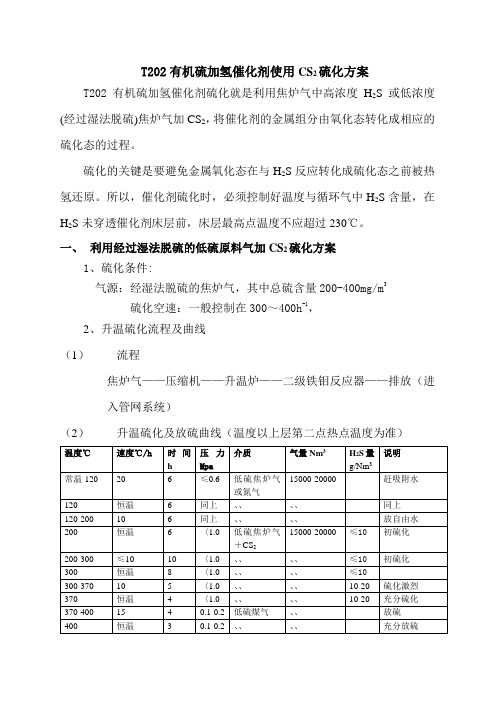
T202有机硫加氢催化剂使用CS2硫化方案T202有机硫加氢催化剂硫化就是利用焦炉气中高浓度H2S或低浓度(经过湿法脱硫)焦炉气加CS2,将催化剂的金属组分由氧化态转化成相应的硫化态的过程。
硫化的关键是要避免金属氧化态在与H2S反应转化成硫化态之前被热氢还原。
所以,催化剂硫化时,必须控制好温度与循环气中H2S含量,在H2S未穿透催化剂床层前,床层最高点温度不应超过230℃。
一、利用经过湿法脱硫的低硫原料气加CS2硫化方案1、硫化条件:气源:经湿法脱硫的焦炉气,其中总硫含量200-400mg/m3硫化空速:一般控制在300~400h-1,2、升温硫化流程及曲线(1)流程焦炉气——压缩机——升温炉——二级铁钼反应器——排放(进入管网系统)(2)升温硫化及放硫曲线(温度以上层第二点热点温度为准)硫化时间约60小时说明:二级铁钼装填T202的重量约40吨。
硫化氢理论加入量:40×65 kg(每吨催化剂需要65kg CS2)×0.842(CS2含S)×1.06(折合H2S)=2320kg实际硫化氢加入量:硫化气体一次通过吸收率按50%,需硫化氢2320kg×2=4640kg需要购买CS2约5.2吨实际吸硫量也可以通过每小时分析的进出口硫化氢含量差、气量,计算每小时的吸硫化氢量,再累加得出实际吸硫量,做硫化度参考。
二、硫化说明及注意事项1、系统用氮气(氮气纯度>99.9%)置换合格后(主要指氧含量小于0.5%),引入低硫煤气(经湿脱)进入升温炉,建立升温流程,点燃升温炉,根据升温曲线调节燃气量,一般控制升温炉出口温度不大于床层温度50℃,床层到200℃并拉平后改入高硫煤气(低硫原料气加CS2),控制床层最高温度≤420℃。
2、铁钼反应器床层到200℃,开始有硫化反应,为了加速硫化,系统压力可逐渐提到1.0Mpa,另外开始滴加CS2。
(每吨催化剂硫化约需CS2 65Kg),3、硫化时注意提温不提氢,提氢不提温原则。
精脱硫操作规程

精脱硫工段技术、操作规程一、岗位任务及职责范围 (2)二、产品说明 (2)三、原材料及化学品规格 (3)四、原材料及动力消耗定额 (3)五、生产原理 (4)六、岗位生产工艺流程 (7)七、本工段与其它工段的配合 (8)八、岗位操作程序 (9)(一)原始开车(检修后的开车) (9)(二)触媒的升温、还原、硫化: (10)(三)正常开车 (15)(四)正常停车 (16)(五)短期停车 (19)(六)紧急停车 (19)(七)正常调节 (19)(八)氧化铁、氧化锌倒槽操作 (20)(九)升温炉点火操作 (20)九、正常工艺指标 (21)十、异常现象及其处理 (22)十一、巡回检查 (23)十二、主要设备性能 (24)十三、附表 (25)十四、精脱硫安全技术规程 (27)一、岗位任务及职责范围1.岗位任务:从焦炉气压缩机来的经湿法脱硫后的焦炉煤气,流量30000M3,H2S含量小于20mg/Nm3,有机硫含量小于400mg/Nm3,通过两次有机硫加氢转化和两次脱除无机硫的干法流程,使焦炉气中的总硫含量(主要包括无机硫和有机硫)脱至0.1ppm以下,达到转化和甲醇合成的要求。
原料气H2S的存在,如果不脱除,会造成:○1设备、管道、阀门的腐蚀;○2转化催化剂、甲醇合成催化剂中毒,降低或失去活性。
2.岗位职责范围负责过滤器、预脱硫槽A/B、1#铁钼转化器、氧化铁脱硫槽A/B/C,2#铁钼转化器,氧化锌脱硫槽A/B,升温炉等设备及附属管道阀门,仪表的开停车、生产操作、维护保养;负责系统的缺陷检查、登记、消除及联系处理,防止系统泄漏污染环境。
做好设备检修前的工艺处理工作,检修后的运行和验收工作,负责本岗位消防器材,防毒面具等的使用与维护,负责本系统安全运行。
二、产品说明精脱硫后合格焦炉气:组成:V%H2:60.29 CO:6.35 CO2:2.75 CH4:26.04 N2:3.11 C mHn:0.71 总硫:0.1ppm三、原材料及化学品规格1、湿脱硫来原料焦炉气组成:V%H2:61.09 CO:6.28 CO2:2.72 CH4:25.76 N2:3.08 C mHn:0.70 O2:0.37 总硫:0.1ppm H2S:20mg/Nm3有机硫:400mg/Nm32、催化剂技术规格四、原材料及动力消耗定额3、原材料消耗4、催化剂、化学品消耗五、生产原理1、HT-03特种活性碳吸油剂HT-03特种活性碳吸油剂利用活性碳孔隙发达、比表面积大的特点,对大分子物质具有显著的吸附性,而且吸附饱和后可反复再生。
加氢催化剂硫化方案

制氢装置催化剂硫化方案硫化前准备:1、催化剂已按填装方案填装完毕2、压缩机已试机完成,达到开机条件,所有仪表已联校完成3、制氢系统已用氮气置换合格(O2<0.5%)、气密完成4、准备好硫化剂(DMDS)并注入至硫化剂罐,硫化剂线已试压、吹扫干净(用蒸汽、风彻底吹扫干净)5、准备好硫化用工具:硫化氢检测管、计量水器具、画好升温曲线、记录纸、对讲机消防器具等6、干气、氮气、循环水等已准备就绪LYT-701/LYT-702加氢催化剂硫化1、硫化机理LYT—701/702加氢催化剂活性组份氧化钴、氧化镍、三氧化钼在使用前需将其转化为硫化物才具有活性,这一过程为硫化,其机理为:DMDS(或CS2)+4H2=2H2S+CH4MoO3+2H2S+H2=MoS2+3H2OCoO+H2S=CoS+H2ONi0+ H2S=NiS+H2O硫化时,用干N2-H2(H2≥10%,O2<0.5%)作为硫化原料气,配以适量的CS2或者DMDS,经加热达到一定温度后进入催化剂床层,通常采用循环硫化或一次放空硫化方法。
2、硫化过程1、反应系统气密合格,建立氢气-氮气循环后,进行催化剂硫化。
硫化条件:氢压,MPa ≦0.5MPa循环介质,% N2-H2混合气氢气含量,%(v/v) 30-50空速,h-1 200-500第一个恒温硫化阶段床层温度和时间 230℃恒温6小时第二个恒温硫化阶段床层温度和时间 300℃恒温4-6小时第三个恒温硫化阶段床层温度和时间 350℃恒温4小时硫化剂二甲基二硫或二硫化碳理论需硫量,m %(对催化剂) 约8.0吸硫量计算公式为:⎥⎦⎤⎢⎣⎡⨯+⨯⨯+⨯⨯=C B A c s M C M B M A w w 06.329/806.32306.32s w :理论吸硫量c w :催化剂装量A:MoO 3的百分含量;A M :MoO 3的分子量,143.94B :CoO 的百分含量B M :CoO 的分子量,74.93C:NiO 的百分含量C M :NiO 的分子量,74.70理论生成水重量为:DMDS (或CS 2)注入量计算式:(催化剂量)×8%×94(DMDS 分子量或CS 2)/64(硫分子量)=硫注入量 硫注入量×1.1(10%的余量)=实际硫注入量0.452 吨 气体含硫量计算式:X (气体循环量Nm3)/22.4×0.5%(硫含量)×94(DMDS 分子量或CS2)/64(硫分子量)=X’ Kg 二甲基二硫性质:分子式:CH3SSCH3 分子量:94.20 CAS :624-92-0 淡黄色透明液体。
甲醇生产技术第三章脱硫

第三章 脱硫
这几种主要硫化物的性质如下。 1.硫化氢(H2S) 无色气体,有毒,溶于水呈酸性,与碱作用生成盐,可
被碱性溶液脱除,能与某些金属氧化物作用,氧化锌脱
硫就是利用这一性质。 2.硫氧化碳(COS) 无色无味气体,微溶于水,与碱作用缓慢生成不稳定盐, 高温下与水蒸气作用转化为硫化氢与二氧化碳。
四、开停车操作
(二)停车 1.短期停车 2.紧急停车 3.长期停车
四、开停车操作
(三)倒车 ①按正常开车步骤启动备用机,待运转正常后,逐渐关 小其回路阀,提高出口压力,当备用机出口压力与系统
压力相等时,逐渐开启其出口阀;同时开启在用机回路
阀,关闭其出口阀。 ②停在用机,关闭其出口阀。 ③倒车过程中开、关阀门应缓慢、以保证系统气体压力、 流量的稳定。防止抽负或系统压力突然升高及气量波动 。
面上,以便捕集,溢流回收硫磺。
③空气作用同时将溶解在吸收液中二氧化碳吹除出来, 从而提高溶液PH,实际生产1kg硫化氢约需60~ 110m3/(m2·h)空气,再生时间维持在8~12min。
二、湿法脱硫
3.栲胶法工艺流程
图2 —2
湿法脱硫工艺硫程
二、湿法脱硫
(三)其他脱硫法简介 1.ADA法 (1)脱硫塔中的反应
②经常注意罗茨机进出口压力变化,防止罗茨机和高压
机抽负。 ③保持贫液槽和脱硫塔液位正常,防止泵抽空。
三、操作要点
(四)防止带液和跑气 控制冷却塔液位不要过高,以防气体带液,液位不要过 低,以防跑气。
(五)巡回检查
①根据记录报表,按时做好记录。 ②每15min检查一次气柜高度。 ③每15min检查一次系统各点压力和温度。 ④每半小时检查一次各塔液位。
(1)原因
加氢裂化催化剂预硫化操作规程

加氢裂化催化剂预硫化操作规程一、催化剂预硫化的目的加氢裂化催化剂的活性金属组分主要是Mo、Ni、Co和W,同其它新催化剂或再生后的催化剂一样,其所含的活性金属组分(Mo、Ni、Co、W)都是以氧化态的形式存在。
大量的研究和工业实践证明,催化剂经过硫化,活性金属组分由氧化态转化为硫化态,具有良好的加氢活性和热稳定性。
因此,在加氢催化剂接触原料油汽之前,先进行预硫化,将催化剂活性金属组分由氧化态转化为硫化态。
本装置使用的FZC系列保护剂为Mo-Ni系活性金属氧化物,FF-20精制催化剂活性金属为W-Mo-Ni系金属氧化物,FC-14裂化催化剂的活性金属为W-Ni系金属氧化物,予硫化能使MoO3、WO3和NiO转变为具有较高活性的MoS2、WS2和Ni3S2金属硫化物。
催化剂硫化一般分为湿法硫化和干法硫化两种,湿化硫化为在氢气存在下,采用硫化物或馏分油在液相或半液相状态下的预硫化;干法硫化为在氢气存在下,直接用含有一定浓度的H2S或直接向循环氢中注入有机硫化物进行的预硫化。
湿法硫化分为两种:一种为催化剂硫化过程所需要的硫油外部加入的硫化物而来,一种为依靠硫化油自身的硫进行预硫化。
本装置预硫化工艺为干法气相硫化。
使用二甲基二硫化物C2H6S2(DMDS)作为硫化剂。
二、催化剂预硫化的原理催化剂预硫化是基于硫化剂(DMDS)临氢分解生成硫化氢(H2S),H2S与催化剂活性金属氧化态反应转化成相应金属硫化态的反应。
其相关的硫化反应如下:(CH3)2S2+3H2→ 2H2S+2CH4MoO3 + 2H2S + H2→ MoS2 + 3H2O3NiO + 2H2S + H2→ Ni3S2 + 3H2OWO3 + 2H2S + H2→ WS2 + 3H2O三、具备条件(1)经过气密检验和紧急泄压试验,确认系统严密性和联锁系统性能安全可靠。
(2)供氢系统确保稳定可靠,1401-K-101及1401-K-102运转正常。
精脱硫系统催化剂与转化催化剂的升温与还原复件

精脱硫转化系统开车方案及操作规程第一节精脱硫转化系统生产原理及流程一、原理1、精脱硫原理通过铁钼触媒及镍钼触媒将焦炉气中的硫醇(RSR,噻吩(GH4S)、二硫化碳(CS)、硫氧化碳(COS等有机硫加氢转化成无机硫HS、不饱和烃加氢转化为饱和烃;再利用铁锰脱硫剂及氧化锌脱硫剂,除去HS,使焦炉气硫含量w O.lppm。
(1)加氢反应RSH+2+RH+2S+Q;RSR ' +H二RH+R H+HS+QCHS+4H=GH0+HS+Q; CS 2+4H二CH+2HS+QCOS+24CO+H5+Q C 2H+H二GH+Q生产中铁钼触媒在进行上述反应的同时还存在以下副反应:CO+32+CH+HO+Q(甲烷化反应)2 H+O=2HO+Q(燃烧反应)C2H二C+CH+Q(析碳反应)2CO二C+C+Q(析碳反应)生产中加氢反应及副反应均为放热反应,在操作中应控制好触媒层温度。
铁钼触媒主要的副反应是甲烷化反应,因此操作中要注意原料气中CO 含量的变化。
(2)脱硫反应①铁锰脱硫剂对H2S的吸收反应:FeS+HS二FeS+HMnO+HB二MnS+HOMn S+2S= MnS+H2②氧化锌脱硫剂对硫的吸收反应:Zn O+bS=Z nS+bO2、转化原理在焦炉气中加入水蒸汽,在一定压力及温度下,通过催化剂作用,生成合成甲醇有用的H2、CO及CQ。
转化反应:CH+H2C= CO+3出QCO+ H 20= CQ+H2+QCH 4 = C+2H— Q二、流程1、精脱硫转化系统流程叙述来自焦炉气压缩机(C201)的焦炉气含H b S< 20mg/Nm有机硫250mg/Nm其压力为2.5MPa温度100〜110C。
焦炉气通过两台并联的脱油剂槽(D106a、b)脱除掉焦炉气中的油水之后进入冷热交换器(E104),被来自铁锰脱硫槽D103a D103b的一级脱硫气第一次加热;然后进入原料气第一预热器(E101)被来自转化气废热锅炉(E105)的转化气第二次加热;再经原料气第二预热器(E102)被来自气气换热器(E103)的转化气第三次加热;最后进入加热炉B101被第四次加热。
T202型铁钼催化剂的硫化及应用

干法冷激气 焦
南
பைடு நூலகம்
1 用 C 化 铁 钼 催 化 剂 前 期 准备 工作 S硫
( ) 用 现 有 干 法 脱 硫 氧 化 锰 脱 硫 槽 倒 槽 1利 时, 在不 影 响 生 产 的 前 提 下 , 相 应 的 管 线 , 配 使
申 液
图 1 T0 2 2型 铁 钼 催 化 剂升 温 硫 化 工 艺流 程
温 。当床 层 最 低 点 温 度 达 到 6 ℃ 时 , 0 5 0 分 ., 10 15MP . ,. a进行 3次 吹除 。在用 焦炉气 对 T0 22 转 化器 升温 过 程 中 , 稳定 控 制 放 空 气 量 。入 口阀
与放空 阀相 配合 , 防止 系 统大 幅波 动 。T 0 2 2型铁 钼催化 剂升 温硫化 工艺 参数 见表 1 。
T0 22型铁 钼催 化 剂 升 温 硫 化 工 艺 流 程 参 见
图1 。按 工 艺 流 程将 焦 炉 气 引 入 T 0 2 2转化 器并 放空 , 控制 T 0 2 2转化 器 内压力 ≤0 6MP 均 匀 升 . a
变换一脱碳一 甲烷化 , 净化成合 格 的氮氢 气后方 可 生产合成 氨 。在净化 车 间干法脱 硫 工段采 用 T0 22 铁钼预转 化器 ( 小铁 钼 ) 一 0 钼转化 器一2台 2铁
3个氧 化锰脱 硫槽 可与铁 钼转 化器 互相 替代 。 () S 2 C 提前装 入贮 罐 , 相应 管线 与铁 钼 转 将
化 器相连 。 () 3 氧化 锰 脱 硫 槽 提 前 装 铁 钼 催 化 剂 , 为保 证 催化剂 装填 质量 , 装填前 将 炉 内清 理干 净 , 查 检 内衬及箅 子板 以及 中心 管 完好 , 确定 测 温 电偶 并 准 确好用 。装 填 严格 按 照 制 定 的装 填 程 序 进行 。
钼基加氢脱硫催化剂的制备及应用研究进展
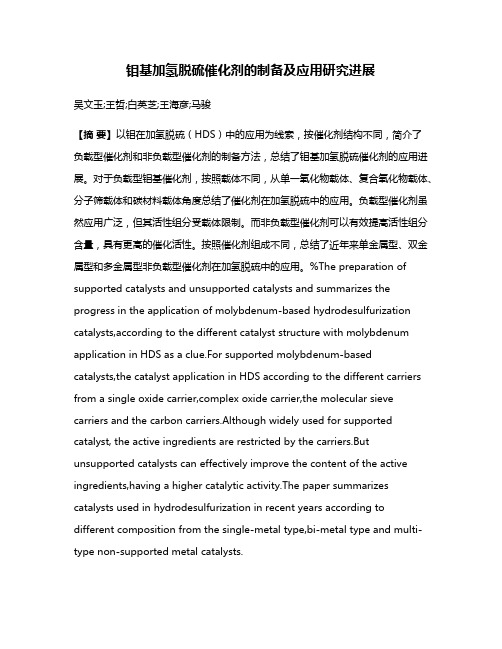
钼基加氢脱硫催化剂的制备及应用研究进展吴文玉;王哲;白英芝;王海彦;马骏【摘要】以钼在加氢脱硫(HDS)中的应用为线索,按催化剂结构不同,简介了负载型催化剂和非负载型催化剂的制备方法,总结了钼基加氢脱硫催化剂的应用进展。
对于负载型钼基催化剂,按照载体不同,从单一氧化物载体、复合氧化物载体、分子筛载体和碳材料载体角度总结了催化剂在加氢脱硫中的应用。
负载型催化剂虽然应用广泛,但其活性组分受载体限制。
而非负载型催化剂可以有效提高活性组分含量,具有更高的催化活性。
按照催化剂组成不同,总结了近年来单金属型、双金属型和多金属型非负载型催化剂在加氢脱硫中的应用。
%The preparation of supported catalysts and unsupported catalysts and summarizes the progress in the application of molybdenum-based hydrodesulfurization catalysts,according to the different catalyst structure with molybdenum application in HDS as a clue.For supported molybdenum-based catalysts,the catalyst application in HDS according to the different carriers from a single oxide carrier,complex oxide carrier,the molecular sieve carriers and the carbon carriers.Although widely used for supported catalyst, the active ingredients are restricted by the carriers.But unsupported catalysts can effectively improve the content of the active ingredients,having a higher catalytic activity.The paper summarizes catalysts used in hydrodesulfurization in recent years according to different composition from the single-metal type,bi-metal type and multi-type non-supported metal catalysts.【期刊名称】《应用化工》【年(卷),期】2016(045)005【总页数】5页(P967-971)【关键词】钼基催化剂;负载型;非负载型;加氢脱硫【作者】吴文玉;王哲;白英芝;王海彦;马骏【作者单位】辽宁石油化工大学石油化工学院,辽宁抚顺 113001;辽宁石油化工大学石油化工学院,辽宁抚顺 113001;辽宁石油化工大学石油化工学院,辽宁抚顺 113001;辽宁石油化工大学石油化工学院,辽宁抚顺 113001;辽宁石油化工大学石油化工学院,辽宁抚顺 113001【正文语种】中文【中图分类】TQ51目前,世界原油重质化程度逐年加重,人类环保意识增强,清洁燃料生产成为社会关注的问题。
钼基加氢脱硫催化剂硫化和碳化过程研究的开题报告

钼基加氢脱硫催化剂硫化和碳化过程研究的开题报告一、选题背景随着现代工业生产的发展,大量的化石燃料的使用造成了严重的环境污染问题。
其中,化石燃料中含有的硫化物是一种严重的污染物,会对大气、土壤和水体等环境产生严重的危害。
为了减轻环境污染的影响,需要对化石燃料进行特殊的处理,去除其中的硫化物。
钼基加氢脱硫催化剂是一种常用的硫化物去除催化剂,具有处理效率高、稳定性好、操作简单等优点,在石油加工、化工等领域得到广泛应用。
然而,在使用过程中,钼基加氢脱硫催化剂也会出现硫化和碳化现象,导致催化剂的失效。
因此,对钼基加氢脱硫催化剂的硫化和碳化过程进行深入的研究,对于进一步提高催化剂的使用寿命和效率具有重要的意义。
二、研究目的本研究旨在通过对钼基加氢脱硫催化剂的硫化和碳化过程进行深入的研究,揭示硫化和碳化现象的产生原因和机理,为进一步提高催化剂的使用寿命和效率提供理论基础和实验支持。
三、研究内容和方法(一)研究内容1. 钼基加氢脱硫催化剂的制备与表征;2. 催化剂的硫化和碳化过程的实验研究;3. 实验结果分析与讨论;4. 催化剂的再生研究。
(二)研究方法1. 利用X射线衍射、扫描电子显微镜等技术对催化剂进行表征;2. 设计催化剂的硫化和碳化实验方案,分析实验结果;3. 运用催化剂的物理化学原理,分析硫化和碳化现象的产生原因和机理;4. 对催化剂的再生过程进行实验研究。
四、预期成果1. 揭示钼基加氢脱硫催化剂硫化和碳化现象的产生机理;2. 提出针对性强的解决方案,以延长催化剂的使用寿命;3. 探索催化剂在工业应用中的具体应用方案。
加氢催化剂硫化方案
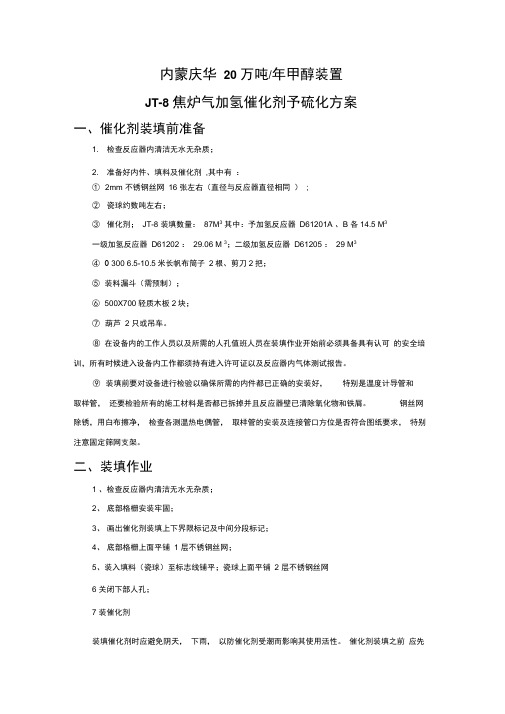
内蒙庆华20 万吨/年甲醇装置JT-8 焦炉气加氢催化剂予硫化方案一、催化剂装填前准备1. 检查反应器内清洁无水无杂质;2. 准备好内件、填料及催化剂,其中有:①2mm 不锈钢丝网16 张左右(直径与反应器直径相同);②瓷球约数吨左右;③催化剂;JT-8 装填数量:87M3其中:予加氢反应器D61201A 、B 各14.5 M3一级加氢反应器D61202 :29.06 M 3;二级加氢反应器D61205 :29 M3④0 300 6.5-10.5米长帆布筒子2根、剪刀2把;⑤装料漏斗(需预制);⑥500X700轻质木板2块;⑦葫芦 2 只或吊车。
⑧在设备内的工作人员以及所需的人孔值班人员在装填作业开始前必须具备具有认可的安全培训,所有时候进入设备内工作都须持有进入许可证以及反应器内气体测试报告。
⑨装填前要对设备进行检验以确保所需的内件都已正确的安装好,特别是温度计导管和取样管,还要检验所有的施工材料是否都已拆掉并且反应器壁已清除氧化物和铁屑。
钢丝网除锈,用白布擦净,检查各测温热电偶管,取样管的安装及连接管口方位是否符合图纸要求,特别注意固定筛网支架。
二、装填作业1 、检查反应器内清洁无水无杂质;2、底部格栅安装牢固;3、画出催化剂装填上下界限标记及中间分段标记;4、底部格栅上面平铺1 层不锈钢丝网;5、装入填料(瓷球)至标志线铺平;瓷球上面平铺2 层不锈钢丝网6 关闭下部人孔;7 装催化剂装填催化剂时应避免阴天,下雨,以防催化剂受潮而影响其使用活性。
催化剂装填之前应先筛去粉尘。
催化剂装填时,从上人孔放入加料帆布筒10.0 米左右和漏斗连接;催化剂装填时视装填设备及人员情况,可进行一台或多台反应器的装填作业。
①漏斗内倒入催化剂0.5-1.0 吨;可根据具体情况确定。
并用吊车吊至反应器人孔上方,漏斗与帆布筒相连,放入催化剂。
②视吊装催化剂的量,取出漏斗和帆布筒由软梯进入反应器,用木板刮平催化剂;③刮平后,根据具体装填高度,帆布筒剪掉约 1 米,继续装催化剂,装量根据第一次实际装填情况可调节。
铁钼加氢催化剂
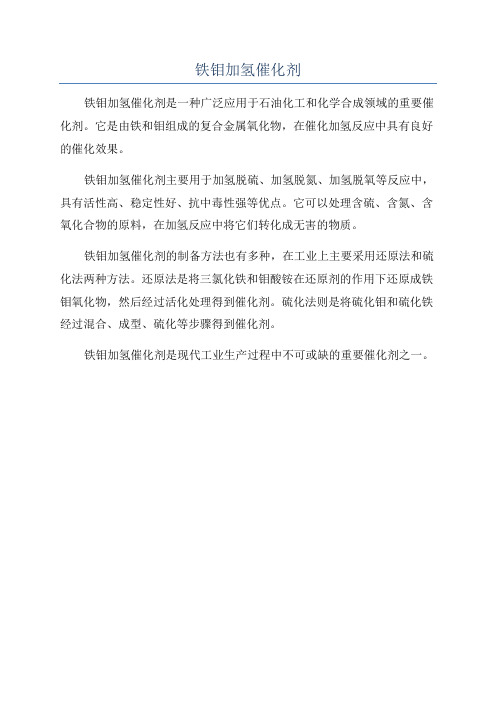
铁钼加氢催化剂
铁钼加氢催化剂是一种广泛应用于石油化工和化学合成领域的重要催化剂。
它是由铁和钼组成的复合金属氧化物,在催化加氢反应中具有良好的催化效果。
铁钼加氢催化剂主要用于加氢脱硫、加氢脱氮、加氢脱氧等反应中,具有活性高、稳定性好、抗中毒性强等优点。
它可以处理含硫、含氮、含氧化合物的原料,在加氢反应中将它们转化成无害的物质。
铁钼加氢催化剂的制备方法也有多种,在工业上主要采用还原法和硫化法两种方法。
还原法是将三氯化铁和钼酸铵在还原剂的作用下还原成铁钼氧化物,然后经过活化处理得到催化剂。
硫化法则是将硫化钼和硫化铁经过混合、成型、硫化等步骤得到催化剂。
铁钼加氢催化剂是现代工业生产过程中不可或缺的重要催化剂之一。
- 1、下载文档前请自行甄别文档内容的完整性,平台不提供额外的编辑、内容补充、找答案等附加服务。
- 2、"仅部分预览"的文档,不可在线预览部分如存在完整性等问题,可反馈申请退款(可完整预览的文档不适用该条件!)。
- 3、如文档侵犯您的权益,请联系客服反馈,我们会尽快为您处理(人工客服工作时间:9:00-18:30)。
T202型铁钼有机硫加氢转化催化剂的硫化工艺
T202型铁钼有机硫加氢转化催化剂的硫化工艺
童庆慧,潘利新
(黑龙江黑化集团有限公司,黑龙江齐齐哈尔161041)摘要:介绍了T202 型铁钼有机硫加氢转化催化剂硫化工艺的应用情况,阐述了以CS2为硫化剂时的操作要点,指出在系统外硫化工艺可以提高经济效益,工艺管线改造后使干法脱硫槽可以根据生产实际情况倒换,无需停车。
关键词:焦炉气;硫化反应;硫化剂
中图分类号:TQ 113 文献标识码:A 文章编号:1004-0935(2013)07-0877-03
黑龙江黑化集团有限公司硝铵厂合成氨系统是以焦化厂副产焦炉气为原料生产合成氨,设计生产能力为55 kt/a, 经过技术改造,生产能力达到65kt/a。
焦炉气中硫的存在除了会毒害催化剂外,还会腐蚀设备和管道,因此原料气的净化脱硫是很重要的一步。
有机硫的脱除多采用加氢转化脱除方法。
加氢转化催化剂的作用在于使烃类原料中所含的有机硫化合物产生氢解反应,转化成易于脱除的无机硫(主要是硫化氢),以便进一步除去。
焦炉气中有机硫组份较复杂,多用铁钼催化剂。
国内常用的铁钼加氢转化多为T202 型,系用γ-Al2O3 担载2.9%~4.3% Fe2O3 和7.5%~10.5% MoO3。
1·催化剂的装填及升温硫化
1.1 催化剂的装填
在加氢转化反应器中,T202 型有机硫加氢催化剂一般分三段填装。
按照触媒装填要求,每一层下面覆二层白钢网,网上压大小瓷球各一层,然后装触媒,触媒上再压大小瓷球各一层。
最下面一层装触媒106 桶计4.24 t。
中层装触媒130 桶计5.2 t。
上层连中心管装触媒161 桶计6.44 t。
共计397 桶,总计15.88 t。
下层装完瓷球后距人孔100 mm,中层距人孔150 mm,上层距中心管上端100 mm。
1.2 催化剂的升温硫化
T202 型催化剂在未硫化前其金属组分铁和钼为氧化态,对一氧化碳含量高的原料气甲烷化副反应较大,同时,对有机硫化物虽有一定活性,但活性不稳定,而且活性较硫化态的低,因此,T202 型催化剂在使用前必须进行硫化处理。
我公司的硫化方法在2007 年以前用焦炉气中的硫进行硫化,之后用二硫化碳作为硫化剂,加到焦炉气中,由于客观条件限制,无法采用循环方式进行硫化,因此二硫化碳用量比循环方式有所浪费。
大多数加氢催化剂完成硫化需用硫(0.06~0.09)kg/kg 催化剂,但实际加入硫量需按过量20%左右考虑,即以(0.07~0.11)kg/kg 催化剂为宜,以确保硫化安全,因此我公司购进2 t 二硫化碳作硫化剂。
1.2.1 硫化流程
焦炉气流程:小铁钼→2#铁钼→放空。
CS2 流程:干法冷激气→CS2 贮罐→2#小铁钼。
1.2.2 升温硫化时间表(见表1)
1.3 硫化过程
⑴置换合格后系统引入焦炉气,按升温要求将床层温度升至200 ℃后恒温,恒温期间将各温度点拉齐。
⑵当床层温度拉齐后开始向系统加CS2,用针型阀控制加入量。
并逐渐将压力提至1.0 MPa 以上。
⑶硫化初期:CS2 加入少量,以工焦气3 000m3/h,入口CS2 浓度2 000×10-6。
通过
计算,CS2 贮罐液位每小时下降1 cm(储罐直径1 000 mm)。
⑷硫化主期:适当提高CS2 加入量,以升温速度为准,可以使CS2 贮罐液位每小时下降3~5 cm。
⑸370 ℃左右有放硫反应,为了加速放硫,370℃恒温后压力可逐渐降至0.1~0.2 MPa。
并停止加CS2。
⑹在整个升温过程中,每半小时记录1 次。
室外人员每半小时报告一次系统压力、CS2 贮罐液位高度及针型阀开度、铁钼入口阀及放空阀开度。
当温度达到200 ℃、开始加CS2 后,每半小时分析1 次出入口H2S。
⑺触媒层温度达到300 ℃时为硫化主期,此时切忌超温。
一旦发现温升过快应马上采取措施,减少CS2 加入量、开冷激或将铁钼切除。
⑻原料气中氧含量<0.5%。
1.4 操作要点
⑴室外设两人专岗,负责工艺调节。
调节铁钼槽压力及CS2 加入量。
⑵CS2 加入的动力由干法脱硫冷激气体提供。
需要保证气体畅通,密切注意CS2 贮罐压力不能低于铁钼槽压力。
⑶铁钼压力表安装在入口处,以利于对系统压力的调节。
每一次开关入口阀或放空阀时,都要注意一下压力的变化。
⑷当铁钼床层温度200~300 ℃及300 ℃恒温区间,以CS2 贮罐液位下降1 cm/h 为准。
当床层温度在300~370 ℃以及370 ℃恒温区间内,以CS2贮罐液位下降3~5 cm/h 为准。
⑸脱硫室外人员要经常观察CS2 贮罐液位,以保证CS2 的加入速度,但不能加入过快。
⑹2#铁钼由常温→120 ℃时,每小时排放铁钼出口导淋1 次。
2·经验总结
⑴CS2 遇空气可自燃,加入过程中要严防泄漏。
我厂在准备工作就绪后,开始向储罐内加CS2 时,当时使用了较为安全的方法,利用抽油器将CS2 打入盛有水的贮罐。
首先将桶装CS2 吊至脱硫循环槽上部,让其有一个液位差应该是可以完成的。
但是由于抽油器不打量,检查时泄漏的CS2 溅到去溶碱房蒸汽管线上,形成自燃,工作被迫停止。
⑵通过资料显示,CS2 桶装上部水封量应达到总容积的1/4。
但此批CS2 没达到这一要求所以在用虹吸的方法导CS2 时还要向桶内加一些水。
在抽取虹吸管时用水浇,抽空后向桶内加一些水后封桶。
⑶装有CS2 的桶经常用水浇,以达到降温的目的。
(4)开始升温时,触媒升至200 ℃恒温后马上向系统加CS2。
防止触媒在高温区时间长,出现H2与氧化铁、氧化钼的还原反应为主的现象。
我公司在2010年铁钼升温硫化时就出现了因气量少,床层温度拉平慢,各点温差大的情况,CS2 加入时间较晚,硫化反应慢,硫化度不如2007 年那炉催化剂的情况。
(5)硫化时气量要均衡,测量设施要齐备,分析手段要齐全,计算更要相对准确。
CS2 需要多准备一些,这样的升温硫化,CS2 需要准备2 t。
(6)硫化结束放硫时加大空速,把反应热带走,严防超温现象发生。
(7)新触媒放硫结束后要尽快使之串入系统,使空速达到最大,以利于带走反应热,减少冷激的使用量。
3·经济效益分析
以我公司2007 年铁钼触媒硫化共用111 h 计算,从焦炉气使用量上看,合成氨减产282 t。
假如大修开车时在系统内硫化,平均用时80 h,应减少合成氨640 t。
此次CS2 加上运输费用是12 000 元左右。
此次干法管线改造的材料费用可能比较高,但其是一项长期使用的费用,可以不计或少计。
综上可见经济效益115 万元。
而且2007 年因第一次使用二硫化碳,
其间有不足之处,导致升温硫化时间延长。
从2012 年这炉来看,升温硫化时间为98 h,因此可见在系统外升温硫化可产生较大经济效益。
4 ·结束语
我公司自2003 年对系统进行改造后,合成氨产量达到65 kt/a,随着产量的大幅增长,净化系统首先出现了甲烷一段转化及二段转化出口指标超标现象,经分析确定是干法脱硫系统因负荷增大出现问题,因此我公司将氧化锰脱硫剂改为铁锰脱硫剂,同时也根据生产实际情况及时更换铁钼催化剂。
而铁钼的升温硫化时间一般在80 h 以上,我公司未使用二硫化碳进行硫化时,只能是系统停车待硫化结束后,生产系统才能正常生产,而引入二硫化碳后,铁钼催化剂可在生产系统外进行升温硫化,不影响生产系统的运行。
同时,为了确保生产稳定,如果在正常运行过程中,如出现铁钼催化剂活性到了末期,也可先维持生产,在系统外将催化剂升温硫化后并入系统。
我公司干法脱硫系统流程为:铁钼预转化器→铁钼转化器→1#铁锰脱硫槽→2#铁锰脱硫槽→3#铁锰脱硫槽→氧化锌脱硫槽(其中三槽铁锰两开一备),为了更有效的利用催化剂,还将工艺管线进行改造,使铁钼脱硫槽后所连接的两个铁锰脱硫槽可相互倒换,这样干法脱硫系统几个脱硫槽可灵活运用,确保了生产的稳定。
参考文献:
[1]向德辉, 刘惠云. 化肥催化剂实用手册[M]. 北京:化学工业出版社,1992:45-52.[2]贺永德.现代煤化工技术手册[M]. 北京:化学工业出版社,2011.。