滚齿原理
滚齿加工方法和加工方案
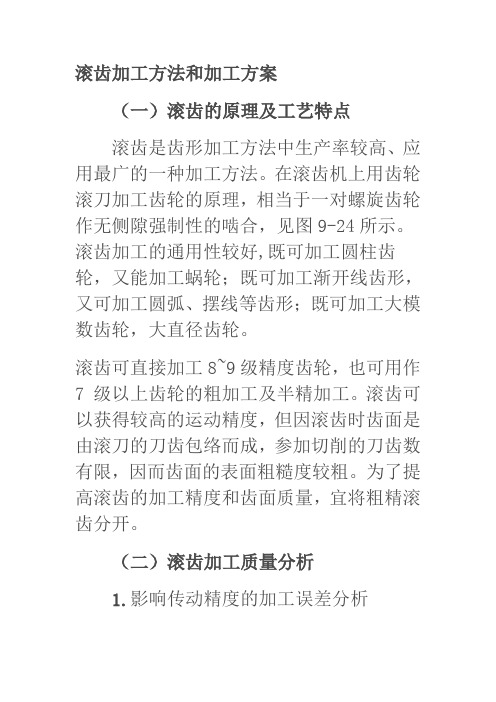
滚齿加工方法和加工方案(一)滚齿的原理及工艺特点滚齿是齿形加工方法中生产率较高、应用最广的一种加工方法。
在滚齿机上用齿轮滚刀加工齿轮的原理,相当于一对螺旋齿轮作无侧隙强制性的啮合,见图9-24所示。
滚齿加工的通用性较好,既可加工圆柱齿轮,又能加工蜗轮;既可加工渐开线齿形,又可加工圆弧、摆线等齿形;既可加工大模数齿轮,大直径齿轮。
滚齿可直接加工8~9级精度齿轮,也可用作7 级以上齿轮的粗加工及半精加工。
滚齿可以获得较高的运动精度,但因滚齿时齿面是由滚刀的刀齿包络而成,参加切削的刀齿数有限,因而齿面的表面粗糙度较粗。
为了提高滚齿的加工精度和齿面质量,宜将粗精滚齿分开。
(二)滚齿加工质量分析1.影响传动精度的加工误差分析影响齿轮传动精度的主要原因是在加工中滚刀和被切齿轮的相对位置和相对运动发生了变化。
相对位置的变化(几何偏心)产生齿轮的径向误差;相对运动的变化(运动偏心)产生齿轮的切向误差。
(1)齿轮的径向误差齿轮径向误差是指滚齿时,由于齿坯的实际回转中心与其基准孔中心不重合,使所切齿轮的轮齿发生径向位移而引起的周节累积公差,如图9—4所示。
齿轮的径向误差一般可通过测量齿圈径向跳动△Fr反映出来。
切齿时产生齿轮径向误差的主要原因如下:①调整夹具时,心轴和机床工作台回转中心不重合。
②齿坯基准孔与心轴间有间隙,装夹时偏向一边。
③基准端面定位不好,夹紧后内孔相对工作台回转中心产生偏心。
(2)齿轮的切向误差齿轮的切向误差是指滚齿时,实际齿廓相对理论位置沿圆周方向(切向)发生位移,如图9-5所示。
当齿轮出现切向位移时,可通过测量公法线长度变动公差△Fw来反映。
切齿时产生齿轮切向误差的主要原因是传动链的传动误差造成的。
在分齿传动链的各传动元件中,对传动误差影响最大的是工作台下的分度蜗轮。
分度蜗轮在制造和安装中与工作台回转中心不重合(运动偏心),使工作台回转中发生转角误差,并复映给齿轮。
其次,影响传动误差的另一重要因素是分齿挂轮的制造和安装误差,这些误差也以较大的比例传递到工作台上。
滚齿的加工原理及常见缺陷处理办法

滚齿的加工原理及常见缺陷处理办法齿轮是机械产品设计中的常用零件,而在齿轮齿形加工中,滚齿应用最广泛,它除可加工直齿、斜齿圆柱齿轮外,还可以加工蜗轮、花键轴等。
滚齿适用于单件小批量生产和大批大量生产。
本文将为大家介绍一下滚齿的加工原理及常见缺陷处理办法。
滚切齿轮可看作无啮合间隙的齿轮与齿条传动。
当滚齿旋转一周时,相当于齿条在法向移动一个刀齿。
滚齿是目前应用最广的切齿方法,可加工渐开线齿轮、圆弧齿轮、摆线齿轮、链轮、棘轮、蜗轮和包络蜗杆,精度一般可达到DIN4~7级。
目前滚齿的先进技术有多头滚刀滚齿、硬齿面滚齿技术、大型齿轮滚齿技术、高速滚齿技术等。
1齿数不正确主要原因1)分齿交换齿轮调整不正确2)滚刀选用错误3)工件毛坯尺寸正确4)滚切斜齿轮时,附加运动方向不对解决方法1)重新调整分齿交换齿轮,并检查中间轮加置是否正确2)合理选用滚刀3)更换工件毛坯4)增加或减少差动交换齿轮中的中间轮2齿形不正常——齿面出棱主要原因滚刀齿形误差太大或分齿无能无力瞬时速比较变化大,工件缺陷状况有四种1)滚刀刃磨后,刀齿等分性差2)滚刀轴向窜动林3)滚刀径向跳动大4)滚刀用钝解决方法主要方法:着眼于滚刀刃磨质量,滚刀安装精度以及机床主轴的几何精度:1)控制滚刀刃磨质量2)保证滚刀的安装精度,同时安装滚刀时不能敲击;垫圈端面平整;螺母端面要垂直;锥孔内部应清洁;托架装上后,不能留间隙3)复查机床主轴的旋转精度,并修复调整滚刀主轴轴承,尤其是止推垫片4)更换新刀3齿形不正常——齿形不对称主要原因1)滚刀安装不对中2)滚刀刃磨后,前刃面的径向误差大3)滚刀刃磨后,螺旋角或导程误差大4)滚刀安装角的误差太大解决方法1)用“啃刀花”法或刀规对刀2)控制滚刀刃磨质量3)重新调整滚刀的安装解4齿形不正常——齿形角不对主要原因1)滚刀本身的齿形角误差太大2)滚刀刃磨后,前刃面的径向性误差大3)滚刀安装角的误差大解决方法1)合理选用滚刀的精度2)控制滚刀的刃磨质量3)重新调整滚刀的安装角5齿形不正常——齿形周期性误差主要原因1)滚刀安装后,径向跳动或轴向窜动大2)机床工作台回转不均匀3)跨轮或分齿交换齿轮安装偏心或齿面磕碰4)刀架滑板有松动5)工件装夹不合理产生振摆解决方法1)控制滚刀的安装精度2)检查机床工作台分度蜗杆的轴向窜动,并调整修复之3)检查跨轮及分齿交换齿轮的安装及运转状况4)调整刀架滑板的塞铁5)合理选用工件装夹的正确方案6齿圈径向跳动超差主要原因工件内孔中心与机床工作台回转中心不重合(1)有关机床、夹具方面:•工作台径向跳动大•心轴磨损或径向跳动大•上下顶针有偏差或松动•夹具定位端面与工作台回转中心线不垂直•工作装夹元件,例如垫圈和并帽精度不够(2)有关工作方面:•工件定位孔直径超差•用找正工件外圆安装时,外圆与内孔的同轴度超差•工件夹紧刚性差解决方法着眼于控制机订工作台的回转精度与工件的正确安装(1)有关机床和夹具方面:•检查并修复工作台回转导轨•合理使用和保养工件心轴•修复后立柱及上顶针的精度•夹具定位端与工作台回转中心线不垂直•提高工件装夹元件精度,例如垫圈和并帽(2)有关工件方面:•控制工件定位孔的尺寸精度•控制工件外圆与内孔的同轴度误差•夹紧力应施于加工刚性足够的部件主要原因7齿圈径向跳动超差主要原因滚刀垂直进给方向与齿坯内孔轴线方向偏斜太大。
滚齿加工原理

滚齿加工原理
滚齿加工,又称滚轮齿轮,是机床和金属切削机械中最常见的加工方式之一。
其原理是利用滚轮齿轮滚动在给定平面和形状上,将金属材料进行切削加工。
滚轮齿轮的刃口宽度和深度决定了滚轮齿轮的切削精度和能力。
滚轮齿轮的加工原理是,将滚轮齿轮的齿嵌入刃口中,并将滚轮齿轮旋转至合适速度,利用滚轮齿轮齿面的接触,从而使得齿轮滚轧刀具的加工工件的表面产生切口的滚辊。
滚齿加工时,金属材料因受滚轮齿轮的切削力而发生形变,滚轮齿轮上的刃口与金属材料发生摩擦,从而在金属材料表面形成滚动移动的切口,使其表面形成滚齿状。
由于滚齿加工的工作过程中,采用的刃口较为细腻,因此可以对金属材料表面的几何形状、坐标尺寸、曲面等尺寸进行精确加工。
滚齿加工原理

滚齿加工原理滚齿加工是一种常见的齿轮加工方法,通过滚刀和工件的相对运动来实现齿轮的加工。
在滚齿加工中,滚刀的齿廓与工件的齿廓相吻合,通过滚刀的旋转和进给运动,使工件上的齿廓逐渐被滚刀切削成型。
滚齿加工具有高效、精度高、表面质量好等优点,因此在齿轮制造中得到了广泛应用。
滚齿加工的原理主要包括滚刀和工件的相对运动、切削力的产生和切削过程的控制。
首先,滚刀和工件的相对运动是滚齿加工的基础。
滚刀通常采用滚刀架上的滚刀头,通过主轴的旋转驱动滚刀头进行旋转运动,同时通过进给机构使滚刀头沿工件轴向移动,从而实现滚刀和工件的相对运动。
在这一过程中,工件也会随着滚刀的进给而旋转,以便使滚刀能够顺利地切削工件的齿廓。
其次,切削力的产生是滚齿加工的关键。
在滚刀和工件的相对运动过程中,滚刀的刀齿会与工件的齿廓接触并切削工件材料,从而产生切削力。
这些切削力包括切向力和径向力,它们会影响滚刀和工件的相对位置和相对运动状态,因此需要通过合理的滚刀设计和切削参数选择来控制切削力的大小和方向,以保证滚齿加工的稳定性和加工质量。
最后,切削过程的控制是滚齿加工的关键技术之一。
在滚刀和工件的相对运动过程中,需要通过控制滚刀的旋转速度、进给速度和切削深度等参数,来实现对齿廓的精确切削。
同时,还需要考虑切削润滑和冷却、切屑排出等工艺因素,以保证滚齿加工的稳定性和加工质量。
综上所述,滚齿加工是一种高效、精度高、表面质量好的齿轮加工方法,其原理包括滚刀和工件的相对运动、切削力的产生和切削过程的控制。
通过合理的滚刀设计和切削参数选择,可以实现对齿轮的精确加工,满足不同工件的加工要求。
因此,滚齿加工在齿轮制造中具有重要的应用价值,对于提高齿轮加工效率和质量具有重要意义。
滚齿刀工作原理

滚齿刀工作原理
滚齿刀是一种用于加工直齿与斜齿锥齿轮的切削工具。
它的工作原理是通过滚削方式将滚齿刀与工件表面之间的接触点沿齿轮齿廓线逐渐滚动,实现对工件齿轮的切削加工。
具体而言,滚齿刀的齿面与齿廓线是相吻合的,采用与齿轮直径相等的滚削刃,带动工件的旋转。
在滚齿刀与工件接触并开始滚动后,滚削刃沿着工件齿廓线持续滚动切削,从而形成齿轮的齿形。
滚削的切削力主要作用在滚削刃的法线方向,而非切向方向,因此滚齿刀的切削力相对较小,有利于提高加工精度和切削效率。
滚齿刀工作原理的优点主要包括:加工精度高、加工速度快、表面质量好、切削力小以及工具寿命长等。
这使得滚齿刀广泛应用于齿轮制造、机械加工等行业中。
滚齿加工原理

滚齿加工原理
滚齿加工是一种常用的齿轮加工方法,通过滚压切削齿轮齿廓,以提高齿轮的精度和质量。
其原理是利用齿轮加工工具的齿形来修磨齿轮齿廓,通过加工工具与齿轮的滚动动作,将加工切削力分散在齿轮齿廓的多个点上,从而减小了切削力对齿轮的影响。
滚齿加工主要包括滚切和滚削两种方法。
滚切是指将齿轮加工工具的齿形与齿轮的齿槽进行配合,进行接触滚动,通过切削和塑性变形来修磨齿轮齿廓。
滚切加工时,加工工具与齿轮的齿槽之间形成一定的压力,使加工工具的齿形形成切槽运动,同时还会产生金属流、压痕等现象,从而使齿轮的齿廓得到一定的修磨和精确度的改善。
滚削是指齿轮加工工具通过滚轮与齿轮的齿廓进行接触滚动,实现齿轮齿廓的修整。
滚削加工时,加工滚轮的周向速度与齿轮的直线运动速度相匹配,使其能够稳定地与齿轮的齿廓接触,并通过滚动方式修整齿轮齿廓的精度和晶界。
总的来说,滚齿加工是一种通过齿轮加工工具与齿轮齿廓之间的接触滚动,利用切削和塑性变形来修整齿轮齿廓的加工方法。
通过滚动动作,滚齿加工能够更好地控制切削力和修整齿轮齿廓的精度,提高齿轮的质量和使用寿命。
滚齿加工方法和加工方案
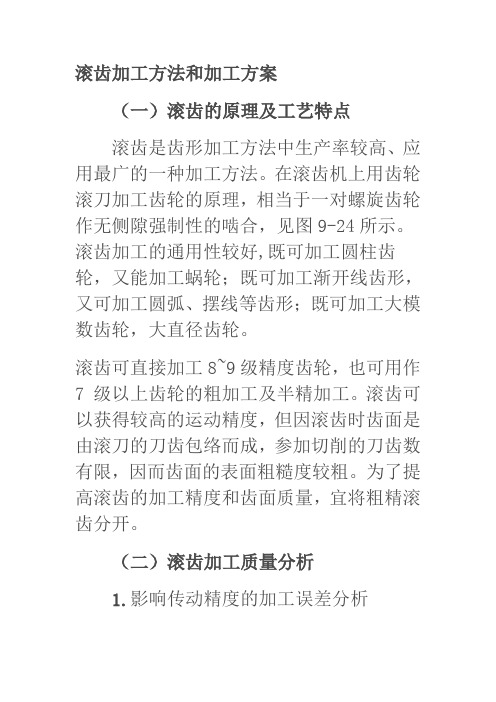
滚齿加工方法和加工方案(一)滚齿的原理及工艺特点滚齿是齿形加工方法中生产率较高、应用最广的一种加工方法。
在滚齿机上用齿轮滚刀加工齿轮的原理,相当于一对螺旋齿轮作无侧隙强制性的啮合,见图9-24所示。
滚齿加工的通用性较好,既可加工圆柱齿轮,又能加工蜗轮;既可加工渐开线齿形,又可加工圆弧、摆线等齿形;既可加工大模数齿轮,大直径齿轮。
滚齿可直接加工8~9级精度齿轮,也可用作7 级以上齿轮的粗加工及半精加工。
滚齿可以获得较高的运动精度,但因滚齿时齿面是由滚刀的刀齿包络而成,参加切削的刀齿数有限,因而齿面的表面粗糙度较粗。
为了提高滚齿的加工精度和齿面质量,宜将粗精滚齿分开。
(二)滚齿加工质量分析1.影响传动精度的加工误差分析影响齿轮传动精度的主要原因是在加工中滚刀和被切齿轮的相对位置和相对运动发生了变化。
相对位置的变化(几何偏心)产生齿轮的径向误差;相对运动的变化(运动偏心)产生齿轮的切向误差。
(1)齿轮的径向误差齿轮径向误差是指滚齿时,由于齿坯的实际回转中心与其基准孔中心不重合,使所切齿轮的轮齿发生径向位移而引起的周节累积公差,如图9—4所示。
齿轮的径向误差一般可通过测量齿圈径向跳动△Fr反映出来。
切齿时产生齿轮径向误差的主要原因如下:①调整夹具时,心轴和机床工作台回转中心不重合。
②齿坯基准孔与心轴间有间隙,装夹时偏向一边。
③基准端面定位不好,夹紧后内孔相对工作台回转中心产生偏心。
(2)齿轮的切向误差齿轮的切向误差是指滚齿时,实际齿廓相对理论位置沿圆周方向(切向)发生位移,如图9-5所示。
当齿轮出现切向位移时,可通过测量公法线长度变动公差△Fw来反映。
切齿时产生齿轮切向误差的主要原因是传动链的传动误差造成的。
在分齿传动链的各传动元件中,对传动误差影响最大的是工作台下的分度蜗轮。
分度蜗轮在制造和安装中与工作台回转中心不重合(运动偏心),使工作台回转中发生转角误差,并复映给齿轮。
其次,影响传动误差的另一重要因素是分齿挂轮的制造和安装误差,这些误差也以较大的比例传递到工作台上。
《机械制造工艺基础》—滚齿的原理及运动

3、垂直进给运动: 滚刀沿工件的轴向作进 给移动。 (齿宽)
机械制造工艺基础
课堂练习
再次观看多媒体演示
做一做
1、试述滚齿的原理? 2、滚齿加工时,齿形的形成应由 运动 获得,完成齿宽方向的加工由 运动获得。
机械制造工艺基础
机械制造工艺基础
讲授新课
二、滚齿的运动分析
1、主运动: 滚刀的旋转运动。
机械制造工艺基础
讲授新课
二、滚齿的运动分析
2、展成运动:滚刀与工件的啮合运动。
传动比: N工/N刀=K/Z
(齿形)
刀具每转一转时,工件相应地转过K/Z转。
(K:滚刀头数;Z:工件齿数)
机械制造工艺基础
讲授新课
二、滚齿的运动分析
滚齿的原理及运动
机械制造工艺基础
复习回顾
铣齿: 1、铣齿定义? 2、铣齿加工的原理?
机械制造工艺基础
导入新课
铣齿加工的原理:
每铣过一
个齿,停 下来,用 分度头转
效 率
过一定的
低
角度,然
后再铣另
一个齿。
提
连
高
续
效
切
率
削
机械制造工艺基础
讲授新课
一个做成刀具,另一个看出齿坯。 在啮合的过程中,把齿坯的齿形加工出来。
归纳总结 ——滚 齿 的原理及运动
滚齿原理
一对轴线相互交叉的螺旋圆柱齿轮相啮合 的原理
1.主运动——滚刀的旋转运动。
运动分析
2.展成运动——滚刀与工件啮合运动。(齿形) N工/N刀=K/Z
3.垂直进给运动——滚刀沿工件的轴向作 进给移动。(齿宽)
机械制造工艺基础
滚齿加工原理
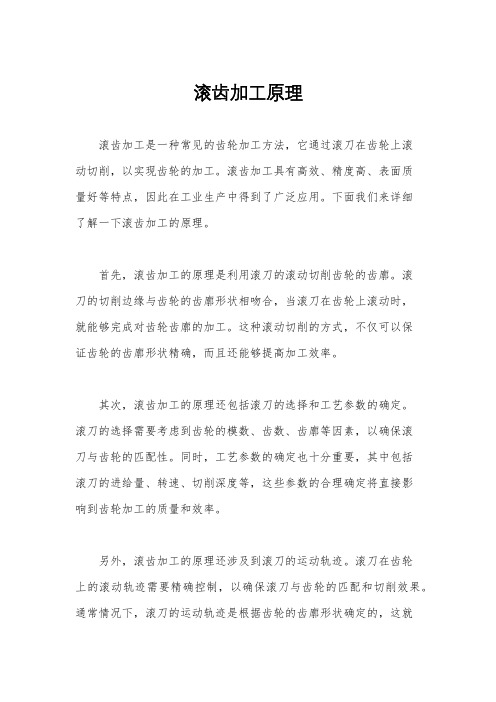
滚齿加工原理滚齿加工是一种常见的齿轮加工方法,它通过滚刀在齿轮上滚动切削,以实现齿轮的加工。
滚齿加工具有高效、精度高、表面质量好等特点,因此在工业生产中得到了广泛应用。
下面我们来详细了解一下滚齿加工的原理。
首先,滚齿加工的原理是利用滚刀的滚动切削齿轮的齿廓。
滚刀的切削边缘与齿轮的齿廓形状相吻合,当滚刀在齿轮上滚动时,就能够完成对齿轮齿廓的加工。
这种滚动切削的方式,不仅可以保证齿轮的齿廓形状精确,而且还能够提高加工效率。
其次,滚齿加工的原理还包括滚刀的选择和工艺参数的确定。
滚刀的选择需要考虑到齿轮的模数、齿数、齿廓等因素,以确保滚刀与齿轮的匹配性。
同时,工艺参数的确定也十分重要,其中包括滚刀的进给量、转速、切削深度等,这些参数的合理确定将直接影响到齿轮加工的质量和效率。
另外,滚齿加工的原理还涉及到滚刀的运动轨迹。
滚刀在齿轮上的滚动轨迹需要精确控制,以确保滚刀与齿轮的匹配和切削效果。
通常情况下,滚刀的运动轨迹是根据齿轮的齿廓形状确定的,这就要求滚刀的设计和制造具有高精度。
最后,滚齿加工的原理还包括切削液的使用。
在滚齿加工过程中,切削液的使用对于降低切削温度、减少摩擦和延长刀具寿命都起着重要作用。
因此,合理选择切削液的种类和使用方法,对于滚齿加工的效果有着直接的影响。
总的来说,滚齿加工的原理是基于滚刀的滚动切削齿轮的齿廓,需要合理选择滚刀和确定工艺参数,控制滚刀的运动轨迹,并合理使用切削液。
这样才能够实现齿轮加工的高效、高精度和高质量。
滚齿加工作为一种重要的齿轮加工方法,在工业生产中具有着重要的地位和作用,值得我们深入学习和研究。
滚齿机原理
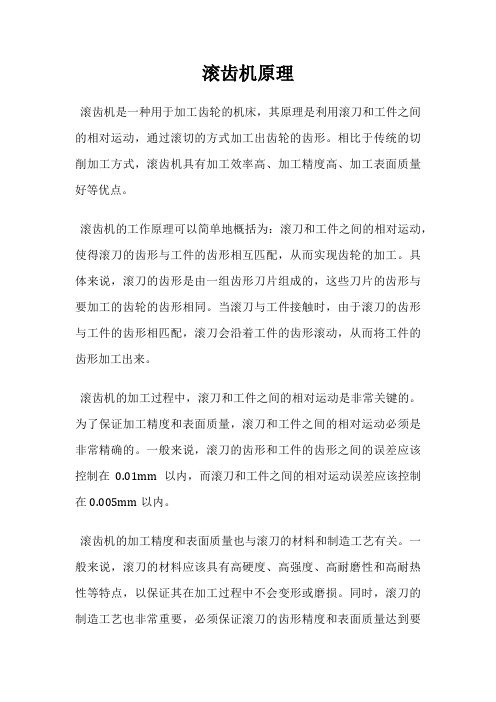
滚齿机原理
滚齿机是一种用于加工齿轮的机床,其原理是利用滚刀和工件之间的相对运动,通过滚切的方式加工出齿轮的齿形。
相比于传统的切削加工方式,滚齿机具有加工效率高、加工精度高、加工表面质量好等优点。
滚齿机的工作原理可以简单地概括为:滚刀和工件之间的相对运动,使得滚刀的齿形与工件的齿形相互匹配,从而实现齿轮的加工。
具体来说,滚刀的齿形是由一组齿形刀片组成的,这些刀片的齿形与要加工的齿轮的齿形相同。
当滚刀与工件接触时,由于滚刀的齿形与工件的齿形相匹配,滚刀会沿着工件的齿形滚动,从而将工件的齿形加工出来。
滚齿机的加工过程中,滚刀和工件之间的相对运动是非常关键的。
为了保证加工精度和表面质量,滚刀和工件之间的相对运动必须是非常精确的。
一般来说,滚刀的齿形和工件的齿形之间的误差应该控制在0.01mm以内,而滚刀和工件之间的相对运动误差应该控制在0.005mm以内。
滚齿机的加工精度和表面质量也与滚刀的材料和制造工艺有关。
一般来说,滚刀的材料应该具有高硬度、高强度、高耐磨性和高耐热性等特点,以保证其在加工过程中不会变形或磨损。
同时,滚刀的制造工艺也非常重要,必须保证滚刀的齿形精度和表面质量达到要
求,才能保证加工出的齿轮的精度和表面质量。
滚齿机是一种非常重要的齿轮加工设备,其原理是利用滚刀和工件之间的相对运动,通过滚切的方式加工出齿轮的齿形。
滚齿机具有加工效率高、加工精度高、加工表面质量好等优点,是现代制造业中不可或缺的一部分。
滚齿相关知识

滚齿相关知识滚齿相关知识1.滚齿加工原理和工艺特点滚齿是应用一对螺旋圆柱齿轮的啮合原理进行加工的。
所用刀具称为齿轮滚刀。
滚齿是齿形加工中生产率较高、应用最广的一种加工方法。
滚齿加工通用性好,既可加工圆柱齿轮,又可加工蜗轮;既可加工渐开线齿形又可加工圆弧、摆线等齿形;既可加工小模数、小直径齿轮,又可加工大模数、大直径齿轮。
滚齿原理滚齿的加工精度等级一般为6~9级,对于8、9级精度齿轮,可直接滚齿得到,对于7级精度以上的齿轮,通常滚齿可作为齿形的粗加工或半精加工。
当采用AA级齿轮滚刀和高精度滚齿机时,可直接加工出7级精度以上的齿轮。
2.滚齿加工精度分析在滚齿加工中,由于机床、刀具、夹具和齿坯在制造、安装和调整中不可避免的存在一些误差,因此被加工齿轮在尺寸、形状和位置等方面也会产生一些误差。
这些误差将影响齿轮传动的准确性、平稳性、载荷分布的均匀性和齿侧间隙。
滚齿误差产生的主要原因和采取的相应措施见下表3.齿轮滚刀齿轮滚刀一般是指加工渐开线齿轮所用的滚刀。
它是按螺旋齿轮啮合原理加工齿轮的。
由于被加工齿轮是渐开线齿轮,所以它本身也应具有渐开线齿轮的几何特性。
齿轮滚刀从其外貌看并不象齿轮,实际上它仅有一个齿(或二个、三个齿),但齿很长而螺旋角又很大的斜齿圆柱齿轮,因为它的齿很长而螺旋角又很大,可以绕滚刀轴线转好几圈,因此,从外貌上看,它很象一个蜗杆。
如图所示。
为了使这个蜗杆能起切削作用,须沿其长度方向开出好多容屑槽,因此把蜗杆上的螺纹割成许多较短的刀齿,并产生了前刀面和切削刃。
每个刀齿有一个顶刃和两个侧刃。
为了使刀齿有后角,还要用铲齿方法铲出侧后面和顶后刀面。
但是各个刀齿的切削刃必须位于这个相当于斜齿圆柱齿轮的蜗杆的螺纹表面上,因此这个蜗杆就称为滚刀的基本蜗杆。
标准齿轮滚刀精度分为四级:AA、A、B、C。
加工时按照齿轮精度的要求,选用相应的齿轮滚刀。
AA级滚刀可以加工6~7级齿轮;A级可以加工7~8级齿轮;B级可加工8~9级齿轮;C级可加工9~10级齿轮。
滚齿原理及滚刀基本知识
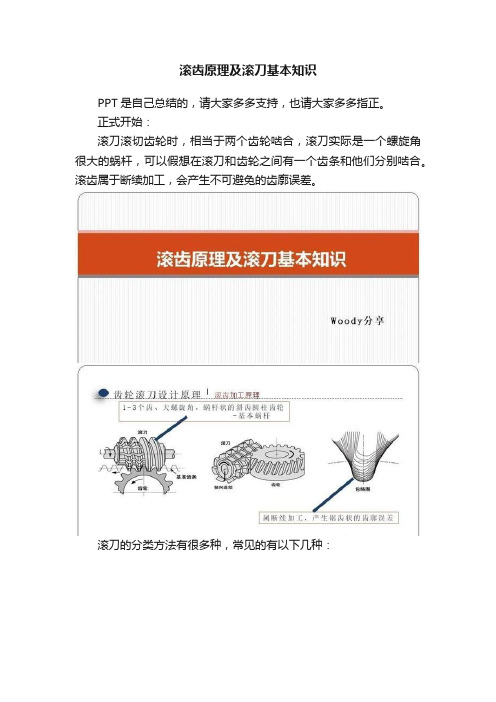
滚齿原理及滚刀基本知识
PPT是自己总结的,请大家多多支持,也请大家多多指正。
正式开始:
滚刀滚切齿轮时,相当于两个齿轮啮合,滚刀实际是一个螺旋角很大的蜗杆,可以假想在滚刀和齿轮之间有一个齿条和他们分别啮合。
滚齿属于断续加工,会产生不可避免的齿廓误差。
滚刀的分类方法有很多种,常见的有以下几种:
滚刀的基本齿形有以下四种:
滚刀的各个参数中,外径和长度是两个需要考虑多个因素的参数。
滚刀的头数个孔径的选择原则:
滚刀的容屑槽分为:螺旋槽和直槽两种。
滚刀的前角分为:零前角、正前角和负前角三种。
零前角是目前使用最广泛的形式,因为这样易加工和修磨。
正前角多用在齿轮模数较大,切削量大的粗加工情况下使用。
负前角多用在热后硬刮削的情况下,要求切削厚度不能太大。
下面是滚刀的顶刃后角和侧刃后角示意图
下面是常见剃磨前齿轮端面各个部分的含义示意图。
滚刀设计中经常使用变压力角(转位设计),即重新选择齿轮的节圆位置,以应对一些特殊情况。
今天分享到这,关注我,后续更新更多内容。
滚齿和插齿的工作原理

滚齿和插齿的工作原理
滚齿和插齿是齿轮加工中常用的两种方法,它们的工作原理如下:
1. 滚齿工作原理:
滚齿是一种通过切削方法将齿形逐渐切割形成的加工过程。
滚齿工作原理主要包括以下几个步骤:
- 首先,确定齿轮的模数、齿数等参数,并选择合适的滚刀。
- 将工件安装在滚齿机床上,并将滚刀与工件配合。
- 开始滚齿加工时,滚刀通过旋转和推进的方式,沿着工件的齿廓线进行滚切,逐渐切削出目标齿形。
- 在滚切过程中,滚齿机床会控制滚刀的运动轨迹,使其与工件表面有良好的接触,确保切削质量和精度。
- 最后,通过多次滚切,逐渐将整个齿轮的齿形切削完成。
滚齿工作原理的优点是可以高效地加工出精密的齿形,具有较高的加工效率和较好的表面质量,适用于批量生产。
2. 插齿工作原理:
插齿是一种通过切削方法将齿形逐个切割形成的加工过程。
插齿工作原理主要包括以下几个步骤:
- 首先,确定齿轮的模数、齿数等参数,并选择合适的插齿刀具。
- 将工件安装在插齿机床上,并将插齿刀具与工件配合。
- 开始插齿加工时,插齿刀具通过旋转和推进的方式,沿着工件的齿廓线逐个切削出目标齿形。
- 在插齿过程中,插齿机床会控制插齿刀具的运动轨迹,使其与
工件表面有良好的接触,确保切削质量和精度。
- 最后,通过多次插齿,逐渐将整个齿轮的齿形切削完成。
插齿工作原理的优点是可以灵活地加工各种齿形,适用于小批量和单件生产,但加工效率相对较低。
总之,滚齿和插齿都是常用的齿轮加工方法,它们的工作原理不同,适用于不同的加工需求和生产情况。
滚齿加工原理

滚齿加工原理
滚齿加工是一种常用的齿轮加工方法,其原理是利用滚刀和被加工齿轮的齿廓之间的相互作用,通过滚动切削的方式进行加工。
滚刀是一种特殊的切削工具,其齿形与被加工齿轮的齿形相吻合。
在加工过程中,滚刀与齿轮的啮合在不断变化,随着滚刀的旋转,同时也推动齿轮进行旋转。
滚刀与齿轮的啮合关系可以通过滚刀的移动轨迹来描述。
在滚刀移动的过程中,其切削刀具的工作面与被加工齿轮齿廓的接触点不断变化,同时也顺时针或逆时针旋转。
这种旋转运动使得刀具能够不断地与被加工齿轮的齿廓进行切削,形成齿轮的齿形。
滚刀与被加工齿轮的啮合过程中,由于切削速度的分配不均匀,齿廓上会产生一定的残余切削量。
为了保证齿轮的准确性和质量,需要进行补偿刀具的设计。
通过在滚刀的刀径上增加一定的加工余量,可以消除齿廓上的残余切削量,从而得到精确的齿轮齿形。
滚齿加工具有以下特点:
1. 可以高效、精确地加工大量齿轮,生产效率高;
2. 加工后的齿轮具有较高的精度和质量,能够满足各种工程要求;
3. 加工过程中切削力小,能够减少切削力对工件的变形和刀具的磨损;
4. 适用于加工各种齿轮,如圆柱齿轮、锥齿轮、斜齿轮等;
总之,滚齿加工是一种高效、精确的齿轮加工方法,通过滚刀与齿轮的相互作用,实现对齿轮齿形的精确切削,得到高质量的齿轮产品。
齿轮滚齿加工原理

齿轮滚齿加工原理
齿轮滚齿加工原理是指通过滚刀或滚模与齿轮齿面接触,在一定的轨迹和条件下,使齿轮齿面的金属材料逐渐被剥离、变形和重新组织,最终形成准确的齿形。
滚齿加工相比于传统的切削加工具有许多优点。
首先,滚齿加工可以在较高的速度下进行,从而提高生产效率。
其次,滚齿加工可以保证齿面的光洁度和精度,降低齿轮齿面的表面粗糙度和硬度,提高齿轮的使用寿命。
此外,滚齿加工还可以更好地控制齿轮的齿形和齿距,确保齿轮的传动效率和运动平稳性。
滚齿加工的原理是利用滚刀或滚模的载齿面与齿轮齿面接触,沿着齿轮齿面的轨迹进行滚动。
在滚动的过程中,滚刀或滚模的载齿面会与齿轮齿面发生相对滑动,使齿轮齿面的金属材料逐渐被剥离、变形和重新组织,形成准确的齿形。
滚齿加工主要通过滚刀或滚模上的多个齿槽或齿形来传递力量和热量,实现齿轮材料的塑性变形和金属粒子的流动,从而改变齿轮齿面的形状。
滚齿加工的过程中,需要考虑许多因素,包括滚刀或滚模的结构参数、齿轮材料的性质、滚齿的轨迹和速度等。
合理选择滚刀或滚模的形状和尺寸,以及控制滚齿的轨迹和速度,可以确保齿轮的滚齿加工过程稳定、高效,同时保证齿轮齿面的质量和精度。
总之,齿轮滚齿加工利用滚刀或滚模与齿轮齿面的接触,通过滚动的过程实现齿轮齿面的塑性变形和形状改变,从而获得准
确的齿形。
这种加工方法具有高效、高精度和高质量的特点,在工程领域中得到广泛的应用。
第二节 滚齿..

机械制造工艺基础
•知识小结: •一、滚齿的工艺特点
二、滚齿的原理 实质: 三、滚齿的运动 1.主运动
2.分齿运动
3.垂直进给运动
Logo
机械制造工艺基础
•作业布置: •简述滚齿的运动?
Logo
Thank you!
机 械 制 造 工 艺 基 础
第十章 齿形的加工
机械制造工艺基础
第二节 滚齿
知 识 目 标
技 能 目 标
Logo
•掌握滚齿的原理及运动。
•学会正确应用滚齿机进行齿形切削。
机械制造工艺基础
第 二节 滚齿
滚齿不仅能加工直齿轮和斜齿轮,还可以加工花键轴和蜗轮等; 其他许多零件如链轮、棘轮、圆弧点啮合齿轮及摆线齿轮等也都 可以设计专用滚刀来加工。 它既可用于大批量生产,也可以用于单件小批量生产中加工圆柱 齿轮。
一、滚齿的工艺特点
(1)滚刀通用性好。
(2)齿形精度及分度精度高。
(3)生产效率高。
Logo
(4)刀具和设备费用高。
机械制造工艺基础
二、滚齿的原理
• 滚齿是用齿轮滚刀在滚齿机上加工齿轮和蜗轮齿形的方法
,实质上是按一对螺旋齿轮相啮合的原理进行加工。
Logo
机械制造工艺基础
机械制造工艺基础
Logo
机械制造工艺基础
•三、滚齿的运动
•滚齿机在加工直齿轮时,有以下几个运动: •1.主运动 •在滚齿时,滚刀的旋转运动就是主运动。
•2.分齿运动
•滚刀与齿坯之间强制保持一对螺旋齿轮啮合运动关系的运动。 •3.垂直进给运动
•为切出整个齿宽,滚刀需要沿工件的轴向作进给移动,即为垂
直进给运动。
Logo
滚齿相关知识

滚齿相关知识1.滚齿加工原理和工艺特点滚齿是应用一对螺旋圆柱齿轮的啮合原理进行加工的。
所用刀具称为齿轮滚刀。
滚齿是齿形加工中生产率较高、应用最广的一种加工方法。
滚齿加工通用性好,既可加工圆柱齿轮,又可加工蜗轮;既可加工渐开线齿形又可加工圆弧、摆线等齿形;既可加工小模数、小直径齿轮,又可加工大模数、大直径齿轮。
滚齿原理滚齿的加工精度等级一般为6~9级,对于8、9级精度齿轮,可直接滚齿得到,对于7级精度以上的齿轮,通常滚齿可作为齿形的粗加工或半精加工。
当采用AA级齿轮滚刀和高精度滚齿机时,可直接加工出7级精度以上的齿轮。
2.滚齿加工精度分析在滚齿加工中,由于机床、刀具、夹具和齿坯在制造、安装和调整中不可避免的存在一些误差,因此被加工齿轮在尺寸、形状和位置等方面也会产生一些误差。
这些误差将影响齿轮传动的准确性、平稳性、载荷分布的均匀性和齿侧间隙。
滚齿误差产生的主要原因和采取的相应措施见下表3.齿轮滚刀齿轮滚刀一般是指加工渐开线齿轮所用的滚刀。
它是按螺旋齿轮啮合原理加工齿轮的。
由于被加工齿轮是渐开线齿轮,所以它本身也应具有渐开线齿轮的几何特性。
齿轮滚刀从其外貌看并不象齿轮,实际上它仅有一个齿(或二个、三个齿),但齿很长而螺旋角又很大的斜齿圆柱齿轮,因为它的齿很长而螺旋角又很大,可以绕滚刀轴线转好几圈,因此,从外貌上看,它很象一个蜗杆。
如图所示。
为了使这个蜗杆能起切削作用,须沿其长度方向开出好多容屑槽,因此把蜗杆上的螺纹割成许多较短的刀齿,并产生了前刀面和切削刃。
每个刀齿有一个顶刃和两个侧刃。
为了使刀齿有后角,还要用铲齿方法铲出侧后面和顶后刀面。
但是各个刀齿的切削刃必须位于这个相当于斜齿圆柱齿轮的蜗杆的螺纹表面上,因此这个蜗杆就称为滚刀的基本蜗杆。
标准齿轮滚刀精度分为四级:AA、A、B、C。
加工时按照齿轮精度的要求,选用相应的齿轮滚刀。
AA级滚刀可以加工6~7级齿轮;A级可以加工7~8级齿轮;B级可加工8~9级齿轮;C级可加工9~10级齿轮。
- 1、下载文档前请自行甄别文档内容的完整性,平台不提供额外的编辑、内容补充、找答案等附加服务。
- 2、"仅部分预览"的文档,不可在线预览部分如存在完整性等问题,可反馈申请退款(可完整预览的文档不适用该条件!)。
- 3、如文档侵犯您的权益,请联系客服反馈,我们会尽快为您处理(人工客服工作时间:9:00-18:30)。
滚齿原理:滚齿加工是展成法原理来加工齿轮。
用滚刀来加工对轮相当于一对交错螺旋轮啮合。
这对啮合齿轮传动副中,一个齿轮齿数很少,一个或几个,螺旋角很大就演变成了一个蜗杆,再将蜗杆开槽并铲背,就成为齿轮滚刀。
齿轮滚刀螺旋线法向剖面各刀齿面也一根齿条,当滚刀连续转动时就相于一根无限长齿条沿刀具轴向连续移动。
,齿轮滚刀按给定切削速度作旋转运动时,工件则按齿轮齿条啮合关系传动(即当滚刀转一圈,相当于齿条移动一个或几个齿距,齿轮坏也相应转过一个或几个齿距),齿坏上切出齿槽,形成渐开线齿面,,如图
所示。
,滚齿轮过程中,分布螺旋线滚刀各刀齿相继切出齿槽中一薄层金属,每个齿槽滚刀旋转中由几个刀齿依次切出,渐开线是展成法,成形运动是由滚刀旋转运动和工件旋轻快运动组成复合运动(B11+B12),,这个复合运动称为展成运动。
当滚刀与工件连续转动时,便工件整个圆周上依次切出所有齿槽。
这一过程中,齿面形成与齿轮分度是同时进行。
展成运动也就是分度运动。
由上所述,到渐开线齿廓和齿数,滚齿时,滚刀和工件之间必须保持严格相对运动关系,即当滚刀转过1时,工件相应转过K/Z(K为滚刀头数,Z为工件齿数。
)
1、加工直齿圆柱齿轮传动原理
用滚刀加工直齿圆柱齿轮必须具备以下两个运动:形成渐开线齿廓展成运动和形成直线齿面(导线)运动。
图
是滚切直齿圆柱齿轮传动原理图。
(1)展成运动传运链渐开线文化部廓是由展成法形成,靠滚刀旋转运动B11和工件旋转运动B12组复合运动,,滚刀主轴和工作台传动链(刀具-4-5-U X-6-7-工作台)为展成运动传动链,由它保证工件和刀具之间严格运动关系。
其中置换机构U X,适于工作齿数和滚刀头数变化。
显然这是一条内联系传动链,要求传动比准确,要求滚刀和工件两者旋转方向必须符合一对交错轴螺旋齿轮啮合时相对运动方向。
当滚刀旋转方向一定时,工件旋转方向由滚刀螺旋方向确定。
(2)主运动传动链每一个表面成表运动都必须有一个外联系传动与动车源相联系,图中,展成运动外联系传动链为电动机-1-2-U V-3-4-滚刀。
条传动甸产生切削运动,金属切削原理定义,这个运动是运动。
其传动链中换置机构U V用于调整渐开线齿廓成形速度,应当工艺条件确定滚刀转速来调整其传动比。
(3)垂直进给运动传动链,切出整个齿宽,滚刀自身旋转同时,必须沿工件轴线作上线进给运动A2.这种形成导线方法是相切法。
这里,滚刀垂直进给运动是滚刀刀架沿立柱导轨移动实现。
使刀架到运动,用垂直进给传动链“7-8-U f-9-10” 将工作台和刀架联系起来。
传动链中置换机构U f用于调整垂直进给量大小
和进给方向,以适应不同加工表面粗糙度要求。
刀架垂直进给运动是简单运动,,这条传动链是外联系传动链。
这里所采用工作台作为间接动力源,滚齿时进给量通常是以工件每转一转,刀架位移量来计量,且刀架运动速度较低,以保证齿面加工表面粗糙度要求。
采用这种传动方案,不令可满足工艺上需要能简化机床结构。