【管理表格】普源科技有限公司程序文件
质量体系编写表格COP13-1

1、目的1.1为使各程序发现的不合格品,得到正确之明示、检讨、分隔、处理及记录。
2、概述2.1不合格品的内容:A.客户的投诉或退货。
B.不符合验收标准的材料。
(包含超过有效期的物料)C.不符合验收标准的半成品或完成品,(包含由于设备、仪器检定不合格,怀疑品质规格有影响的半成品或成品)。
3、职责3.1当不合格品是属于客户投诉时,QA部负责人、生产部负责人和PE负责人一道对客户内容进行分析及跟进,并把分析结论及改善行动呈交给客户。
3.2如属于材料验收问题3.2.1以IQC负责人为代表组成物料监审委员会(MRB),成员有:PC部负责人、生产部负责人、工程部负责人及采购部负责人。
若有部门负责人不能出席可另派其部门内代表参加。
3.2.2 IQC负责人负责对车间不合格品的退料进行品质确认后由MRB作出不合格品之处理决定。
3.2.3各部门负责人负责根据会议决定不合格品之处理行动。
3.2.4 MRB会议每天举行,检讨及处理不合格品。
3.3如属于半成品验收的问题,经PQC主管作出确认,如属于成品验收问题,需由QC部负责人作出确认。
确认后,即时签发不合格品处理报告,生产部负责人和PE负责人一道进行分析及跟进,及在不合格品处理报告限期前作改善行动,并把结论呈交QC部。
3.3.1 QC部负责明示和分隔检查中的不合格品。
4、程序4.1不合格品的明示和分隔根据COP12.1进行。
4.2 不合格品的处理决定记录于:A.来料检查报告。
B.成品检查记录表。
C.退料单。
D.每周不合格品处理报告。
4.3 不合格品的处理方法:A.退货B.拣用C.特采/放行(只限该批次,有需要时,先得客户同意)D.返工E.报废F.继续保存至下次MRB会议4.4不合格材料4.4.1 当IQC人员判定一种物料的检验结果为[不合格]时,则需及时向供应商发出[品质异常联络书],或将IQC Report直接传真给供应商,要求供应商改善,并由QC部追踪其改善结果。
质量体系编写表格COP7-1

1、目的
1.1本程序文件叙述客户提供物料之验证,贮存及维护的控制方法。
2、概述
2.1客户提供之物料是指客户免费提供及指定该物料,用于其产品上。
2.2本公司之香港物料属客户提供之物料。
3、职责
3.1采购人员负责提供[客户提供物料]的资料,包括规格、贮存方法等。
若这些物料有
问题时,负责联络客户解决。
3.2工程部负责人编定特别之客户提供物料的Part No.;
3.3仓库负责人负责正确贮存及维护客户提供物料。
4、程序
4.1当采购人员接到客户要求提供资料时,须将有关之清单通知工程部。
4.2 工程部负责人给该物料一个物料编号(P/N),并将资料项输入[物料清单](BOM)。
4.3所有客户提供物料的P/N均须登录后才能使用。
4.4当客户供应物料送抵工厂后,IQC按COP10.1要求进行验收工作。
4.5 IQC检查合格后,交货仓按COP1
5.1要求进行贮存。
4.6 若发现客户供应物料存在丢失、损坏或不符合现象,按[不合格品的管制程序]
(COP13.1)处理,唯须第一时间通知PC负责人, 同时由QC部发{品质异常联络书}通知客户有关情况.
4.7.对于客户供应物料(H.K来料),仓库需在指定的区域放置,并用明示牌予以明示,同时
在销存卡和仓库接受签上注明“HK”字样,以示区分.
4.8.采购部应确保客户提供之产品只用于生产客户指明的产品上.
5记录及表格
无。
表格模板-管理表格普源科技有限公司程序文件1 精品
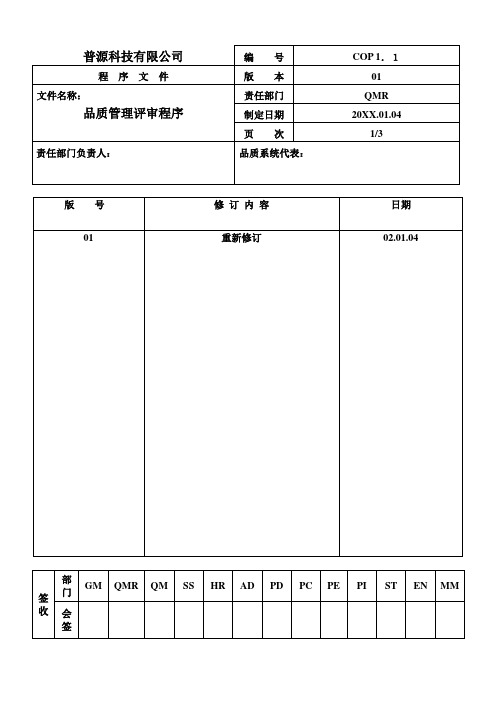
1、目的1.1本程序文件旨在界定职责和方法,通过定期管理评审,去保证和维持公司品质系统的有效性、连续性和适用性,并达到国际标准ISO9000的要求。
2、概述2.1管理评审委员会由营运总监和各部门负责人及以上人员组成。
2.2管理评审会议至少每六个月召开一次。
3、职责3.1营运总监(COO)负责主持管理评审会议,并确认会议记录和任何会议上提出的有关品质系统的变动或改善内容。
3.2品质系统代表(QMR)负责安排会议议程,撰写会议记录和负责跟进会议上确定的任何改善行动。
3.3各部门负责人负责提出问题讨论并有效执行会议决定的改善行动。
4、程序4.1QMR至少每6个月安排召开一次「管理评审会议」(或当任何一个部门负责人申请并得到营运总监同意时),QMR须于会前预备讨论议程。
4.2管理评审会议议程,至少包括以下各点:1)检讨上一次「管理评审会议」改善行动的跟进结果。
2)检讨自从上一次「管理评审会议」至今之间所有的“内部品质审核报告”。
3)检讨纠正及预防措施的跟进情况。
4)检讨顾客反馈。
5)检讨供应商表现和产品品质表现。
6)品质方针、品质目标。
7)可能影响品质管理体系的变化因素4.3于会议上讨论时,提出的问题及其对策,须列明执行责任者、预计完成日、并由QMR记录于会议记录上,呈交营运总监确认。
4.4管理评审会议记录须包括以下各点:1)会议时间、日期2)会议地点3)参加会议人员名单4)讨论项目5)问题及对策6)对策执行负责人,及预计完成日期(或跟进日期)7)QMR和总经理或营运总监的确认、签署8)会议记录副本之签收4.5QMR须确保管理评审会议记录副本派发到营运总监及各部门负责人。
4.6各部门负责人须按时执行所管理范围的改善或预防措施。
4.7QMR负责按照「预计完成日期」,跟进所有会议记录上决定的改善或预防措施的完成日期,并督促所有责任者按时完成,QMR在必要时提供协助,务求达到品质系统的有效和适用性。
4.8所有行动的进度及有效性将于下一次「管理评审会议」上检讨。
质量体系编写表格COP3-1

1、目的1.1本程序文件叙述客户订单(即生产通知单或内部订购单)合同评审条件及方法,旨在接受订单前确保我们有能力达到客户的要求。
2、概述2.1本程序适用于本公司生产的各类产品来自客户(HK业务部)的订单。
3、职责3.1SS部负责与客户进行信息的交流反馈,及将客户的生产单及补充资料发给PC部。
3.2 PC部门收到客户订单后,根据生产能力评估进行合同评审。
3.3 PC负责人负责制定及确认一些跟进措施,以表明本公司有能力满足订单要求。
4、程序4.1 销售支援部(SS部)以书面(或口头)订单形式,发给PC部。
4.2 当PC人员接到客户订单后,查看以下资料是否足够A:产品型号B;订单数量C:交货期4.3生产计划员根据销售支援部发出的“生产单情况表”,PE部发出的“生产能力评估表”以及现有的人员、设备编写每周“生产计划”,经PC负责人审核签名后,于每周六将“生产计划”发至各相关部门。
4.4确保订单资料完整后,PC人员签署于订单上,然后于每星期六,根据[生产能力评估表]把该订单编入“生产计划”,经PC负责人确认后,发给有关部门。
需内部加工的物料,PC部须于[生产计划]发行前向各加工部门发出[加工通知单],通知各加工部门加工生产。
4.5“生产计划”内含生产能力评估功能,若生产部之标准工时,大于“订单所需工时”,则表示正常OK,若少于“订单所需工时”PC负责人须于“生产计划”内,注明“跟进措施”(例如:加班若干小时),或通知客户延期。
4.6若订单属于“急单”(即于下周“生产计划”发出前须完成者),PC人员须发出“客户急单通知书”,PC负责人根据生产能力状态,确认可以插单生产或提出跟进措施,以完成该急单要求,然后直接通知生产部生产而不须排入“生产计划”。
4.7若客户订单上任何资料有更改,须由客户更新订单文件,若客户以电话(口头)通知,PC人员须将更改内容,填入“客户订单补充表”上,然后重复4.4-4.6之评审工作。
质量体系编写表格COP2 1

修订内容日期版号重新修订4.1.5 质量策划内容制定于[质量策划控制表]上,内容包括:每次召开品质管理评审会议(COP1.1)时,高级副总裁兼营运总监与 QMR 及各部门负责人商讨,制定公司相关职能及各层次之质量目标。
质量目标确定后,部门负责人必须于一个月内制定相关质量策划,用以实现质量目 标要求。
1、目的 1.1 本程序文件概述本公司的品质系统之基本运作,并制定质量目标及策划,以满足公 司发展的要求。
2、概述 2. 1 本程序文件适用于任何公司职能,及任何类别的产品或客户。
3、职责 3.1 高级副总裁兼营运总监确保公司在相关职能上建立可测量之质量目标,并使其内容 与品质政策保持一致。
3.2 品质管理代表(QMR )负责建立ISO9001: 2000品质系统,制定程序文件以反应 系统的运作情况,同时制定相关质量策划,以实现质量目标要求。
3.3 各部门负责人负责切实执行品质系统和质量策划的各项要求。
3.4 工程部、ME 部及品管部负责制定实现产品过程策划的各类文件。
4、程序 4.1 品质目标及策划4.1.1 4.1.2 质量目标必须是可测量的,精神上来源于品质政策。
4.1.3 质量目标确定后,由QMR 收集及立案,并形成文件。
4.1.4质量目标现状资料策划措施F .所需资源G.持续改善跟进情况,etc.4.1.6各部门负责人负责切实执行品质系统和质量策划的各项要求及适时填写质量策划控制表所需之进度内容。
4.1.7 QMR 须跟据质量策划控制表的计划,督促工作进度,并在每一次品质管理评审会议之前,收集、统计及将各质量策划的进度情况向高级副总裁兼营运总监汇报。
以上文件内容已包括实现产品各工序的资源,规格参数及验收准则,及必要之相关 记录方法。
建立文件化的品质系统,展示市场、设计、采购、生产及服务等活动的能力,并达 到ISO9000品质标准的要求。
4.3.2品质手册、程序文件和工序指导书等文件表达了品质系统的运作。
仓存管理程序表格格式
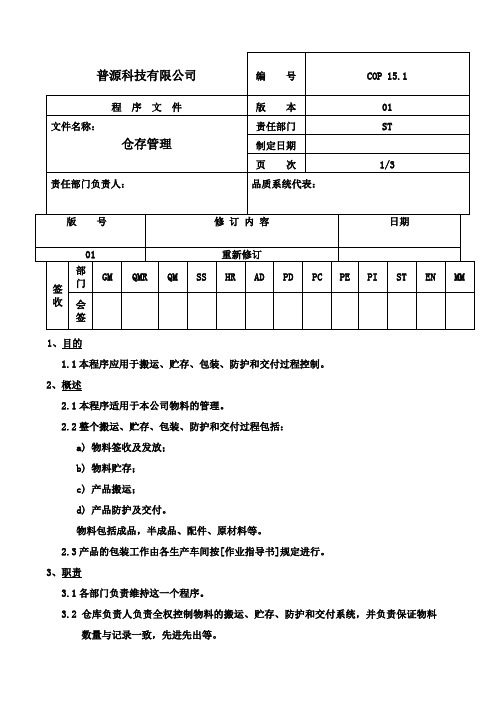
1、目的
1.1本程序应用于搬运、贮存、包装、防护和交付过程控制。
2、概述
2.1本程序适用于本公司物料的管理。
2.2整个搬运、贮存、包装、防护和交付过程包括:
a)物料签收及发放;
b)物料贮存;
c)产品搬运;
d)产品防护及交付。
物料包括成品,半成品、配件、原材料等。
2.3产品的包装工作由各生产车间按[作业指导书]规定进行。
3、职责
3.1各部门负责维持这一个程序。
3.2仓库负责人负责全权控制物料的搬运、贮存、防护和交付系统,并负责保证物料
数量与记录一致,先进先出等。
4、程序
4.1仓管员根据公司的[物料需求单]或采购单资料核收供应商的进料,有差异时呈报
MM部,并根据[来料物料清单]填写[来料通知单]通知检查员检查,合格、特采或返工的物料才可入仓。
4.2物料的收、发、存、搬运遵循有关仓库工作流程之规定。
4.3仓库每月末进行一次实物盘点,检查内容有:
帐本数与实际数是否相符;
a)保管状况是否良好;
b)有使用期限的材料是否过期。
将检查结果记录[盘点表]上。
4.4成品和材料交付规定:
a)成品须先经QA检查合格并出[成品检查报告]后方可出货;
b)依据“出货通知”出货;
c)成品及材料出货须按P/O要求包装;
d)出货后仓管员填写[出柜资料]。
5.记录及表格
5.1《盘点表》。
(FM-ST-1511—02)
5.2《出柜资料》(FM-ST-15102-03)
5.3。
- 1、下载文档前请自行甄别文档内容的完整性,平台不提供额外的编辑、内容补充、找答案等附加服务。
- 2、"仅部分预览"的文档,不可在线预览部分如存在完整性等问题,可反馈申请退款(可完整预览的文档不适用该条件!)。
- 3、如文档侵犯您的权益,请联系客服反馈,我们会尽快为您处理(人工客服工作时间:9:00-18:30)。
1、目的
1.1对过程中阻碍产品品质的各个因素进行操纵,确保产品品质满足规定的要求。
2、概述
2.1 本程序文件适用于生产过程操纵及适当环境下生产。
2.2 生产过程包括装配、注塑、车缝及五金加工。
3、职责
3.1PC部负责有效安排生产打算,确保资源的充分利用,以最低的成本按时完成生产,
确保货期的准时达成。
3.2生产部通过有效治理,负责确保全部生产操作符合规定之作业要求,以保证品质的
制造过程,同时达到生产打算的有效执行和要求。
3.3PE部负责制定[工程流程图]、[检查指导书]、[作业指导书]及必要时提供技术支援
和有效之工夹具,以确保生产效率的提高和品质问题的减少。
4、程序
4.1当PC部收到[生产通知单]后,即作合同评审(COP3.1)。
4.2若能通过评审的[生产通知单],有关人员需每周制定或更新一份[生产打算]/ [加工打
算](加工车间用)交PC负责人确认后,发出给有关使用部门(COP3.1)。
4.3生产部收到[生产打算]/[加工打算]后,应考虑是否有能力按生产打算生产,如以下
几种因素:
A.物料的实际状况。
B.人员的满足状况。
C.PD交货期的缓急状况。
D.机器、工夹具的预备状况。
4.4如生产部无法满足以上要求时,则由PC提出并作以下处理:
A.在满足客户要求的前提下,由PC变更生产打算。
B.如不能满足客户要求,通知销售支援部与客户进行沟通修改订单的要求(方法
参照[合同评审程序])。
4.5当生产之前预备资源满足后,可安排有效之生产。
4.6生产部依据[生产打算]和[物料需求单]中“实际用量”栏之数量发出[领料单],将[领
料单]副本交到仓库领料,并按各型号之[工程流程图]进行排拉生产。
非流水线生产车间的作业及检测人员的安排见[非流水车间人员配制要领]。
4.7生产部依照[作业指导书]及[生产通知单]要求作业,直至包装后的成品存放于待检
区,待FQC作最终检查(COP10.1)。
4.8每个生产工序的半成品,均由生产线检测工按[检查指导书]及[生产通知单]要求进行
所需之制程中检查.(COP10.1) 生产线检测工检查位置依照[工程流程图]要求。
4.9 [作业指导书]内容包括各工序半成品作业步骤、注意事项、部件及设备状况、技术
要求等。
[检查指导书]内容包括各工序半成品检查步骤、注意事项、仪器设备及技术参数等。
4.10生产部负责人负责监督每个工序,确保所有制作按工艺文件要求执行,及保证所有
生产工序均有受控版号之工艺文件。
4.11在制程检测中,检测工将检查结果记入[生产线每日检查日报]内,生产部有关人员必
须定时确认检查结果,及时操纵及解决不良问题,生产部定时确认之要求按[生产线每日检测日报]之所述要求进行。
4.12生产部当遇上较大品质问题(如物料、工艺等)或重复发生问题时,可考虑发出[改
善措施要求表](CAR)给责任部门改善。
4.13若产品之生产过程或由于某种因素(下工序材料不足、机械故障etc.)而临时搁置时,
要求所被搁置之半成品须有状态明示,明示方法是在半成品上注明:
A.产品型号
B.数量
C.下工序名称
(注:确保工序名称之一致性)。
完成生产之成品,由于生产部发出[成品检验通知单]给QC部进行最终检查。
4.14生产使用的工作设备,包括机器、模具、夹具,均由PE部及动力设备科进行确认、
登记,定期检查及修理(COP11.2)。
4.15如生产中仪器、设备显现故障,使用部门应赶忙通知有关部门进行修理,同时在设
备上挂上“暂停使用”的标签。
4.16对严峻损坏的而且不能修复的仪器、设备,由主管部门提出报废申请(见COP11.1、
COP11.2),对报废的要标示“禁止使用”的标贴。
4.17生产线上使用的仪器,由生产部负责治理(COP11.1)。
4.18每日的生产状况,由各车间统计员记入[生产日报表]中。
4.19每份订单量产之前20PCS成品交由QA做信任性测试,以确保能顺利进行量产。
4.19.1一样性的信任性测试按照[成品检查基准规定]中的要求进行,结果记录在[信任性测
试报告]中。
A.测试结果判定合格时,生产线可按打算进行量产。
B.测试结果判定不合格时,责任部门需作出改善,同时再送20PCS成品给QA重新测试。
4.19.2专门性的信任性测试按照[成品寿命试验要领]进行,结果记录于[试验报告书]内。
若
在试验的过程中发觉品质问题时,需及时发行[改善行动报告书]要求责任部门作出
改善行动。
QA主管应统筹讨论有关产品的品质状况及需要时采取行动,幸免不良
品流到客户手中。
4.19.3当生产部收到有关改善联络书须及时检讨缘故,必要时组织召开会议,要求PE部、
EN部作出技术支援,会议出席部门至少须有QA部、EN部、PE部,会议内容记
录在[会议记录]中。
4.20 [检查指导书]和[作业指导书]中要求作业者对比进行检查或作业的样板,由PE部技
术人员负责制作及确认,并交由生产部有关人员负责保管。
4.21 样板必须包括以下内容:
A.部品编号或产品型号。
B.有效期
签名确认
4.22工作环境
4.22.1各部门负责执行[5S推行治理方案]及[职业健康安全卫生体系]有关要求,确保职员和
产品质量有一个良好的工作环境。
5记录及表格
5.1产品明示卡(FM-PD-0911-01)
5.2 成品检验通知单(0FM-PD-0912-01)5.3 QA信任性测试报告(FM-QA-0913-01) 5.4 生产日报表(FM-PD-0914-02)。