蜗轮蜗杆软件说明书
机械设计课程设计单级蜗轮蜗杆减速器说明书
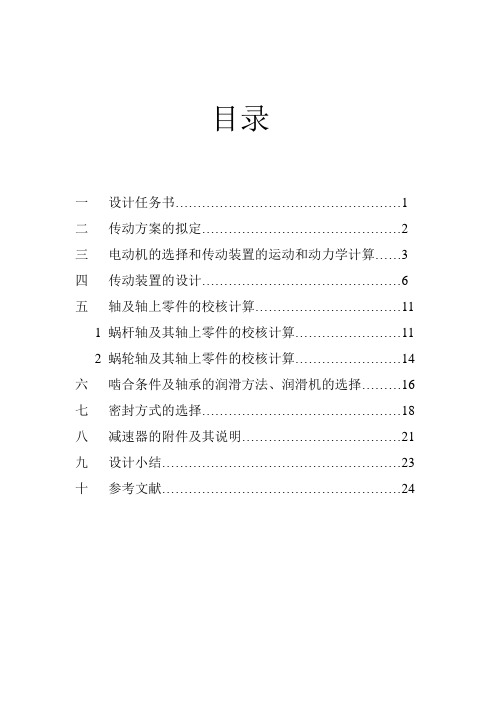
目录一设计任务书 (1)二传动方案的拟定 (2)三电动机的选择和传动装置的运动和动力学计算 (3)四传动装置的设计 (6)五轴及轴上零件的校核计算 (11)1 蜗杆轴及其轴上零件的校核计算 (11)2 蜗轮轴及其轴上零件的校核计算 (14)六啮合条件及轴承的润滑方法、润滑机的选择 (16)七密封方式的选择 (18)八减速器的附件及其说明 (21)九设计小结 (23)十参考文献 (24)第一章.设计任务书1.1设计题目设计用于带速传输机的传动装置。
1.2工作原理及已知条件工作原理:工作传动装置如下图所示:设计数据:运输带工作拉力F=2500N运输带工作速度v=1.10m/s卷筒直径D=400mm工作条件:连续单向运转,工作时轻微冲击,灰尘较少;运输带速度允许误差±5%;一班制工作,3年大修,使用期10年(卷筒支承及卷筒与运输带间的摩擦影响在运输带工作拉力F中已考虑)。
加工条件:批量生产,中等规模机械厂,可加工7~8级齿轮。
设计工作量:1.减速器装配图1张;2.零件图1~3张;3.设计说明书1.3原始数据已知条件传送带工作拉力F(N) 传送带工作速度v(m/s)滚筒直径D(mm)参数2500 1.10 4001-电动机2、4-联轴器3-一级蜗轮蜗杆减速器5-传动滚筒6-输送带第二章. 传动方案选择2.1传动方案的选择该工作机采用的是原动机为Y系列三相笼型异步电动机,三相笼型异步电动机是一般用途的全封闭自扇冷式电动机,电压380 V,其结构简单、工作可靠、价格低廉、维护方便;另外其传动功率大,传动转矩也比较大,噪声小,在室内使用比较环保。
因为三相电动机及输送带工作时都有轻微振动,所以采用弹性联轴器能缓冲各吸振作用,以减少振动带来的不必要的机械损耗。
总而言之,此工作机属于小功率、载荷变化不大的工作机,其各部分零件的标准化程度高,设计与维护及维修成本低;结构较为简单,传动的效率比较高,适应工作条件能力强,可靠性高,能满足设计任务中要求的设计条件及环境。
一级蜗轮蜗杆课程设计说明书

机械设计说明书题目:一级蜗杆减速器设计学校:系别:机械学院专业: 学生姓名:学号:指导教师:目录摘要 (4)1.蜗轮蜗杆减速器的介绍 (4)1.1蜗轮蜗杆减速器简介 (4)1.2蜗杆传动特点 (5)2总体传动方案的选择与分析 (5)2.1传动方案的选择 (5)2.2传动方案的分析 (6)2.3电动机的选择 (7)2.3.1. 电动机功率的确定 (7)2.3.2. 确定电动机的转速 (7)3.传动装置运动及动力参数计算 (8)3.1 各轴的转速计算 (8)3.2. 各轴的输入功率 (9)3.3 各轴的输入转矩 (9)4.蜗轮蜗杆的设计,三维结构及其参数计算 (10)4.1蜗轮三维图 (10)4.2蜗杆三维结构 (12)4.3传动参数 (12)4.4蜗轮蜗杆材料及强度计算 (13)4.5计算相对滑动速度与传动效率 (13)4.6确定主要集合尺寸 (14)4.7热平衡计算 (14)4.8蜗杆传动的几何尺寸计算 (15)5联轴器选择与轴承的设计计算与校核 (16)5.1联轴器的选择 (16)5.1.1载荷计算 (16)5.1.2选择联轴器的型号 (16)5.2轴承的选择及校核与三维图 (17)5.2.1蜗轮的轴承 (17)5.2.2蜗杆的轴承 (18)5.2.3初选输入轴的轴承型号 (18)5.2.5计算轴承内部轴向力 (19)5.2.6计算轴承的轴向载荷 (19)5.2.7计算当量动载荷 (19)5.2.8计算轴承实际寿命 (20)6轴的结构设计 (21)6.1蜗杆工程图如下: (21)6.2蜗杆轴的径向尺寸的确定 (21)6.3蜗杆轴的轴向尺寸的确定 (22)6.4蜗轮轴的结构造型如下: (22)6.5蜗轮轴的轴上零件的定位、固定和装配 (23)6.6蜗轮轴的径向尺寸的确定 (23)6.7蜗轮轴的轴向尺寸的确定 (23)6.8蜗轮的强度校核 (24)7键连接设计计算 (26)7.1蜗杆连接键 (26)7.2蜗轮键的选择与校核 (27)8 减速器箱体结构设计 (27)9减速器润滑的概要说明 (30)9.1减速器的结构 (30)9.2减速箱体的结构 (30)9.3速器的润滑与密封 (31)10减速器零件的三维建模 (32)10.1减速器蜗杆的三维模型 (32)10.2减速器蜗轮的三维模型 (32)10.3 减速器箱体的三维模型 (33)10.4其他零件三维模型成型 (34)10.4.1 轴承的三维模型成型 (34)10.4.2 轴承盖、油标、通气塞的三维模型 (34)11.蜗轮蜗杆装配体三维图和爆炸图 (35)11.1装配图 (35)11.2爆炸图 (36)12.各个零件图结构 (36)13.参考文献 (38)致谢 (39)摘要蜗轮蜗杆减速器的计算机辅助机械设计,计算机辅助设计及辅助制造(CAD/CAM)技术是当今设计以及制造领域广泛采用的先进技术,通过本课题的研究,将进一步深入地对这一技术进行深入地了解和学习。
蜗轮蜗杆减速器说明书

机械设计课程设计设计题目:单级蜗杆减速器专业班级:机械0702学生姓名:熊明春学生学号:指导教师:岳大鑫设计时刻:目录设计任务书---------------------------------------------------------------3整体方案设计------------------------------------------------------------41.传动方案拟定---------------------------------------------------------------42.电动机的选择---------------------------------------------------------------43.传动系统的运动和动力参数---------------------------------------------5传动零件的设计计算1.蜗轮蜗杆初选-----------------------------------------------------------72.联轴器的选择计算-----------------------------------------------------103.转动轴承的选择和寿命计算-----------------------------------------11 4.轴的设计计算和校核--------------------------------------------------15●减速器箱体及附件的设计1.箱体设计--------------------------------------------------------------------202.键的选择及校核-------------------------------------------------------------213.螺栓的选择-------------------------------------------------------------------224.润滑和密封形式的选择,润滑油和润滑脂的选择-------------------235.设计小结--------------------------------------------------------------------25●参考资料1参考资料-----------------------------------------------------------------------25设计任务书1.设计题目:带式运输机传动装置的设计2.带式运输机工作原理及传动方案如图:3.已知条件:1)工作条件:两班制,持续单向运转,载荷较平稳,室内工作,有粉尘,环境最高温度35度。
两级蜗轮蜗杆减速器说明书(课程设计)

原始数据:钢绳拉力kN F /钢绳速度)min/(1-⋅m v 卷筒直径mm D /178330工作条件:连续单向运转,工作时有轻微振动,小批量生产,单班制工作,使用期限8年,运输带速度允许误差为±5%1.电机选择工作机所需输入功率817100060 2.34100010000.97w w Fv P kw η⨯⨯===⨯所需电动机的输出功率d p3.54wd aP P kw η==传递装置总效率2412345a ηηηηηη= 式中:1η:蜗杆的传动效率0.752η:每对轴承的传动效率0.983η:直齿圆柱齿轮的传动效率0.974η:联轴器的效率0.995η:卷筒的传动效率0.96所以 420.750.980.970.990.6577a n =⨯⨯⨯=2.343.5578kw 0.6577d P ==故选电动机的额定功率为4kw8100060601000607.72min 3.14330v n r D π⨯⨯==⨯⨯=⨯卷357407.72(162.121544)minn i i n r ==⨯⨯= 卷蜗齿卷()()符合这一要求的同步转速有750r/min , 1000r/min , 1500r/min 电机容量的选择比较:表1.1 电动机的比较方案 型号 额定功率 /kw 同步转速 /r/min 满载转速 /r/min重量 价格 1Y160M 1-84750720重高2.34w p kw =3.54d p kw =0.6577a η=7.72/minn r =卷2Y132M 1-641000960中中3 Y112M-4 4 1500 1440 轻 低考虑电动机和传动装置的尺寸 重量及成本,可见第二种方案较合理,因此选择型号为:Y132M 1-6D 的电动机。
2.选择传动比2.1总传动比960124.357.72a n i n ===满卷2.2减速装置的传动比分配124.35a i i i ==蜗齿所以31.0875i =蜗 4i =齿3.各轴的参数将传动装置各轴从高速到低速依次定为I 轴 II 轴 III 轴 IV 轴 :I -0η、II I -η、 、III II -η 、V III -η 依次为电动机与I 轴 I 轴与II 轴 II 轴与III 轴 III 轴与V 轴的传动效率 则: 3.1各轴的转速960/min I n r =96030.8806/min 31.0875II n n r i ===满蜗30.8806/min III II n n r ==327.72/min 4.01III IV n n r i ===齿3.2各轴的输入功率Ⅰ轴 kw P P I d I 5222.399.05578.30=⨯==-ηⅡ轴 kw P P II I I II 5888.28.9075.05222.3=⨯⨯==-η Ⅲ轴kwP P III II II III 5117.28.9099.05888.2=⨯⨯==-ηⅣ轴kwP P V III III IV 3876.28.9097.05117.2=⨯⨯==-η3.3各轴的输出功率Ⅰ轴 kw P P I I I 4518.398.05222.30=⨯==-η Ⅱ轴 kw P P II I II II 5370.298.05888.2=⨯==-η Ⅲ轴 kw P P III II II III 4615.298.05117.2=⨯==-η Ⅳ轴 kw P P V III III IV 3398.298.03876.2=⨯==-η3.4各轴的输入转矩电动机 m N n P T d d ⋅=⨯==927.335960578.5395509550满 Ⅰ轴 m N N P T III ⋅==388.0359550Ⅱ轴 m N N P T IIIIII ⋅==119.68009550Ⅲ轴 m N N P T IIIIIIIII ⋅==536.77769550Ⅳ轴 m N N P T III⋅==280.529539550卷卷 3.5各轴的输出转矩电动机 m N T d ⋅=927.335 Ⅰ轴 m N N P T III ⋅==380.3349550124.35a i =31.0875i =蜗4i =齿Ⅱ轴 m N N PT IIII II⋅==997.57849550Ⅲ轴 m N N P T IIIIIIIII ⋅==185.27619550Ⅳ轴 m N N P T III⋅==574.428949550卷卷 3.6各轴的运动参数表表3.1 各轴的运动参数表轴号 功率)(kw P 转矩(N·m) 转速(r/min) 传动i效率η输入 输出 输入 输出 电机轴 4 3.5578 35.3927 960 10.991轴 3.5233 3.4579 35.038834.338096031.08752轴2.58892.2571800.620 784.5997 30.88060.73513轴 2.5117 2.4615 776.754 761.2185 30.8806 0.9702 4卷轴 2.38762.33982953.53 2894.4577.720.95064.蜗轮蜗杆的选择,5233.3kw P = ,875.031=i m in /960r n =4.1选择蜗轮蜗杆的传动类型根据GB/T10085—1998 选择ZI4.2选择材料蜗杆选45钢,齿面要求淬火,硬度为45-55HRC. 蜗轮用ZCuSn10P1,金属模制造。
蜗轮蜗杆减速机使用说明书手册使用说明书减速机

蜗轮蜗杆减速机使用说明书一、减速器的安装、使用与维护1、减速器主动轴直接与电机联接时推荐采用弹性联轴器,减速器被动轴直接与工作机联接时推荐采用齿式联轴器或其他非刚性联轴器。
2、减速器的主动轴线和被动轴线必须与相联接部分的轴线保证同心,其误差不得大于所有联轴器的允许值。
3、减速器安装使用手转动必须灵活,无卡住现象,蜗杆轴承和蜗轮轴承的轴向间隙应符合技术要求的规定。
4、减速器安装及在25﹪额定负荷下,蜗轮齿面接触斑点,按齿高不小于55﹪,按齿长不小于60﹪.5、安装好的减速器在正式使用前,应进行空载部分额定载荷间歇运转1-3小时后方可正是运转,运转应平稳无冲击,无异常振动和噪声及漏油等现象,最高油温不得超过85℃.如发现故障应及时排除。
6、减速器的润滑a.蜗杆涡轮齿合一般采用浸油润滑,浸油深度,对蜗杆在蜗轮之下和之侧的蜗杆全齿高,对蜗杆在蜗轮之上的为蜗轮外径1/3。
b.减速器推荐采用兰炼33﹟润滑油。
c.减速器的润滑油油量按油标加注,并参照下表所列油量备油。
新减速器(或新更换蜗杆副)第一次使用时,当运转7-14天后需更换新油,在以后的使用中应定期检查油的质量,对于混入杂质或老化变质的油必须随时更换。
但一般情况下,对于长期连续工作的减速器,须每2-3个月更换油一次,对于每天工作时间不超过8小时的减速器,须每4-6个月换油一次。
在工作中当发现油温显著升高,温升超过60℃或油温超过85℃,油的质量下降以及产生不正常的噪音等现象时,应停止使用,检查原因,如因齿面胶合等原因所致,必须修复排除故障,更换润滑油后再用。
7、减速器应半年一次或定期检修,发现擦伤胶合及显著磨损,必须采用有限措施制止。
备件必须按图样制造,保证质量,更换新的备件后必须经过跑合和负荷试车后再正式使用。
二、润滑油的选择本减速机在投入运行前必须力II入合适的润滑油至油标中心,油位过高或过低都可能导致运转温度升高。
首次使用24小时左右,必须将润滑油放掉,用轻油(柴油或煤油)冲洗干净,然后重新加入新的润滑油,以后每隔2000至2500小时必须重新冲洗和加入新的润滑油。
MATLAB课程设计说明书涡轮蜗杆设计校核软件

MATLAB课程设计涡轮蜗杆设计校核软件学生姓名指导教师专业系部所在单位:::::武杰民孙建亮工程设计与分析机械工程系燕山大学里仁学院目录第1章简介 (2)1.1 ··············································································错误!未定义书签。
1.2 ··············································································错误!未定义书签。
机械设计课程设计单级蜗轮蜗杆减速器说明书(DOC)
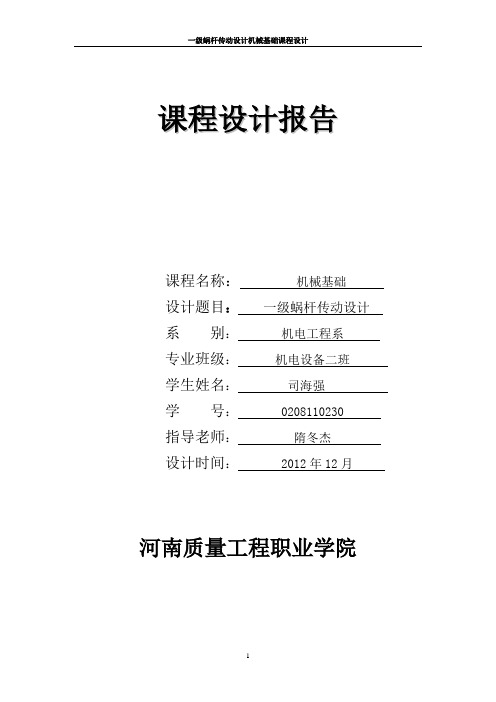
课程设计报告课程名称:机械基础设计题目:一级蜗杆传动设计系别:机电工程系专业班级:机电设备二班学生姓名:司海强学号: 020******* 指导老师:隋冬杰设计时间: 2012年12月河南质量工程职业学院河南质量工程职业学院《机械基础》课程设计任务书目录一传动方案的拟定 (3)二电动机的选择和传动装置的运动和动力学计算 (5)三传动装置的设计 (8)四轴及轴上零件的校核计算 (12)1 蜗杆轴及其轴上零件的校核计算 (12)2 涡轮轴及其轴上零件的校核计算 (15)五轴承等相关标准件的选择 (17)六密封方式的选择 (20)七参考资料 (23)第二章. 传动方案选择及机构运动简图2.1传动方案的选择该工作机采用的是原动机为Y系列三相笼型异步电动机,三相笼型异步电动机是一般用途的全封闭自扇冷式电动机,电压380 V,其结构简单、工作可靠、价格低廉、维护方便;另外其传动功率大,传动转矩也比较大,噪声小,在室内使用比较环保。
因为三相电动机及输送带工作时都有轻微振动,所以采用弹性联轴器能缓冲各吸振作用,以减少振动带来的不必要的机械损耗。
总而言之,此工作机属于小功率、载荷变化不大的工作机,其各部分零件的标准化程度高,设计与维护及维修成本低;结构较为简单,传动的效率比较高,适应工作条件能力强,可靠性高,能满足设计任务中要求的设计条件及环境。
2.2机构运动简图电动机联轴器蜗杆减速器联轴器滚筒输送带第三章. 电动机的选择和运动参数的计算3.1电动机的选择1. 选择电动机的类型按工作要求和条件选取Y 系列一般用途全封闭自扇冷鼠笼式三相异步电动机。
2.选择电动机容量(1)工作机各传动部件的传动效率及总效率查《机械设计课程设计》表2.3各类传动、轴承及联轴器效率的概略值,减速机构使用了一对滚动球轴承,一对联轴器和单线蜗轮蜗杆机构,各机构传动效率如下:)(99.0一对滚动球轴承=η; 995.0~99.0=η联轴器; 80.0=η四线涡轮蜗杆减速机构的总效率776.0~768.022=⨯⨯=ηηηη轴承单线蜗轮蜗杆联轴器总(2)选择电动机的功率所选电动机的额定功率应该等于或稍大于工作要求的功率。
蜗轮蜗杆减速器设计说明书

7计算模数m,m= ×d1/Z1=×29=,∴取m=6
3、按齿根弯曲强度设计
由m≥{(2KT1/φd·Z12)·(YFaYSa/[бF])}1/3
⑴确定公式内的各计算数值
1由图10-20c查得小齿轮弯曲疲劳强度极限бFE1=500 mpa,大齿轮弯曲疲劳强度极限бFE2=380 mpa。
∵бf≤ [бf],∴符合要求
6、验算效率η
η=~ tanγ/tan(γ+ψ)
γ=。;ψv=arctan fv;fv与相对滑速度Vs有关
Vs=πd1n1/60×1000 cosγ=π×80×960/60×1000。= m/s
从表11-8中用插值法查得fv=,ψv=,代入式中得η=>,大于原估计值,因式不用重算。
⑴确定公式内的各计算数值
1试选载荷系数Kt=
2计算小齿轮转矩,由先前算得T3=842790N·mm
3由表10-7选齿宽系数φd=1
4由表10-6查得材料的弹性影响系数 mpa1/2
5由图10-21d 查得小齿轮的接触疲劳强度极限бHlim1=600 mpa;大齿轮接触疲劳强度极限бHlim2=550 mpa
6计算应力循环次数N1=60×32×(10×250×16×=;N2=/=×106
7由图10-19取接触疲劳强度寿命系数KHN1=; KHN1=
8
9计算接触疲劳许用应力,取失效概率为1%,安全系数S=1,
[бH]1= KHN1·бlim1/S=×600 mpa=774 mpa
[бH]2= KHN2·бlim2/S=×550 mpa=583 mpa
十二、设计小结………………………………………………………22
蜗轮蜗杆减速器说明书.

一级蜗轮蜗杆减速器设计说明书第一章绪论1.1本课题的背景及意义计算机辅助设计及辅助制造(CAD/CAM)技术是当今设计以及制造领域广泛采用的先进技术。
本次设计是蜗轮蜗杆减速器,通过本课题的设计,将进一步深入地对这一技术进行深入地了解和学习。
1.1.1 本设计的设计要求机械零件的设计是整个机器设计工作中的一项重要的具体内容,因此,必须从机器整体出发来考虑零件的设计。
设计零件的步骤通常包括:选择零件的类型;确定零件上的载荷;零件失效分析;选择零件的材料;通过承载能力计算初步确定零件的主要尺寸;分析零部件的结构合理性;作出零件工作图和不见装配图。
对一些由专门工厂大批生产的标准件主要是根据机器工作要求和承载能力计算,由标准中合理选择。
根据工艺性及标准化等原则对零件进行结构设计,是分析零部件结构合理性的基础。
有了准确的分析和计算,而如果零件的结构不合理,则不仅不能省工省料,甚至使相互组合的零件不能装配成合乎机器工作和维修要求的良好部件,或者根本装不起来。
1.2.(1)国内减速机产品发展状况国内的减速器多以齿轮传动,蜗杆传动为主,但普遍存在着功率与重量比小,或者传动比大而机械效率过低的问题。
另外材料品质和工艺水平上还有许多弱点。
由于在传动的理论上,工艺水平和材料品质方面没有突破,因此没能从根本上解决传递功率大,传动比大,体积小,重量轻,机械效率高等这些基本要求。
(2)国外减速机产品发展状况国外的减速器,以德国、丹麦和日本处于领先地位,特别在材料和制造工艺方面占据优势,减速器工作可靠性好,使用寿命长。
但其传动形式仍以定轴齿轮转动为主,体积和重量问题也未能解决好。
当今的减速器是向着大功率、大传动比、小体积、高机械效率以及使用寿命长的方向发展。
1.3.本设计的要求本设计的设计要求机械零件的设计是整个机器设计工作中的一项重要的具体内容,因此,必须从机器整体出发来考虑零件的设计计算,而如果零件的结构不合理,则不仅不能省工省料,甚至使相互组合的零件不能装配成合乎机器工作和维修要求的良好部件,或者根本装不起来。
蜗轮蜗杆减速机说明、安装、润滑、注意事项--管理资料

蜗轮蜗杆减速机说明、安装、润滑、注意事项--管理资料一、形式说明减速机的输入形式分为:孔输入、轴输入、延伸蜗杆轴型;减速机输出型形式分为:孔输出、单向轴输出、双向轴输出,。
二、基本性能1、蜗杆转速小于或等于1400rpm;2、中心距有25、30、40、50、63、75、90、110、130共9种;3、单机速比有7.5、10、15、20、25、30、40、50、60、80、100共11种速比;4、减速机可正、反方向运转。
三、安装1、可按实际要求采用多种安装形式,六个面均能安装;2、安装必须牢固、可靠;3、原动机、减速机的工作机构之间须仔细对中,误差不得大于所用联轴器的许用补偿;4、安装后用手转动,必须灵活、无卡滞现象,管理资料《蜗轮蜗杆减速机说明、安装、润滑、注意事项-》(https://www.)。
四、润滑油的使用更换1、第一次使用或更换蜗轮蜗杆减速机时运转150-400小时后更换润滑油,以后的换油周期小于或等于4000小时;2、定期检查油的份量和质量,保留足够润滑油,及时更换混入杂质或变质的油;3、注油量须按表要求,不同牌号的油禁止混用、牌号相同而粘度不同的油允许混用;4、注油量附表一、油品按附表二;5、减速机工作环境温度为—40°C~ 40°C,当环境温度低于0°C 时,起动前润滑必须加热到0°C以上或采用低凝固点的润滑油。
五、注意事项1、不得重力锤击减速机外壳,以免损坏;2、定期检修安装基础、密封件、传动轴等是否正常;3、如正常使用时,润滑油的最高温度应小于85°C。
油温温升变化异常,产生不正常噪声等现象时,应立即停机检查,排他故障后,主可继续使用;4、更换新的备件必须经跑合和负载试验后再正式使用。
蜗轮蜗杆减速器说明书

一级蜗轮蜗杆减速器设计解释书第一章绪论盘算机帮助设计及帮助制作(CAD/CAM)技巧是当今设计以及制作范畴广泛采取的先辈技巧.本次设计是蜗轮蜗杆减速器,经由过程本课题的设计,将进一步深刻地对这一技巧进行深刻地懂得和进修.1.1.1 本设计的设计请求机械零件的设计是全部机械设计工作中的一项重要的具体内容,是以,必须从机械整体动身来斟酌零件的设计.设计零件的步调平日包含:选择零件的类型;肯定零件上的载荷;零件掉效剖析;选择零件的材料;经由过程承载才能盘算初步肯定零件的重要尺寸;剖析零部件的构造合理性;作出零件工作图和不见装配图.对一些由专门工场大批临盆的尺度件主如果依据机械工作要乞降承载才能盘算,由尺度中合理选择.依据工艺性及尺度化等原则对零件进行构造设计,是剖析零部件构造合理性的基本.有了精确的剖析和盘算,而假如零件的构造不合理,则不但不克不及省工省料,甚至使互相组合的零件不克不及装配成合乎机械工作和维修请求的优越部件,或者根本装不起来.1.2.(1)国内减速机产品成长状态国内的减速器多以齿轮传动,蜗杆传动为主,但广泛消失着功率与重量比小,或者传动比大而机械效力过低的问题.别的材料品德和工艺程度上还有很多弱点.因为在传动的理论上,工艺水温和材料品德方面没有冲破,是以没能从根本上解决传递功率大,传动比大,体积小,重量轻,机械效力高级这些根本请求.(2)国外减速机产品成长状态国外的减速器,以德国.丹麦和日本处于领先地位,特殊在材料和制作工艺方面占领优势,减速器工作靠得住性好,应用寿命长.但其传动情势仍以定轴齿轮迁移转变为主,体积和重量问题也未能解决好.当今的减速器是向着大功率.大传动比.小体积.高机械效力以及应用寿命长的偏向成长.本设计的设计请求机械零件的设计是全部机械设计工作中的一项重要的具体内容,是以,必须从机械整体动身来斟酌零件的设计盘算,而假如零件的构造不合理,则不但不克不及省工省料,甚至使互相组合的零件不克不及装配成合乎机械工作和维修请求的优越部件,或者根本装不起来.机械的经济性是一个分解性指标,设计机械时应最大限度的斟酌经济性.进步设计制作经济性的重要门路有:①尽量采取先辈的现代设计理论个办法,力争参数最优化,以及应用CAD技巧,加速设计进度,下降设计成本;②合理的组织设计和制作进程;③最大限度地采取尺度化.系列化及通用化零部件;④合理地选择材料,改良零件的构造工艺性,尽可能采取新材料.新构造.新工艺和新技巧,使其用料少.质量轻.加工费用低.易于装配⑤努力改良机械的造型设计,扩展发卖量.进步机械应用经济性的重要门路有:①进步机械的机械化.主动化程度,以进步机械的临盆率和临盆产品的质量;②选用高效力的传动体系和支承装配,从而下降能源消费和临盆成本;③留意采取恰当的防护.润滑和密封装配,以延伸机械的应用寿命,并防止情形污染.机械在预定工作刻日内必须具有必定的靠得住性.进步机械靠得住度的症结是进步其构成零部件的靠得住度.此外,从机械设计的角度斟酌,肯定恰当的靠得住性程度,力争构造简略,削减零件数量,尽可能选用尺度件及靠得住零件,合理设计机械的组件和部件以及须要时拔取较大的安然系数等,对进步机械靠得住度也是十分有用的.1.4.研讨内容(设计内容)(1)蜗轮蜗杆减速器的特色蜗轮蜗杆减速器的特色是具有反向自锁功效,可以有较大的减速化,输入轴和输出轴不在统一轴线上,也不在统一平面上.但是一般体积较大,传动效力不高,精度不高.蜗轮蜗杆减速器是以蜗杆为主动装配,实现传动和制动的一种机械装配.当蜗杆作为传动装配时,在蜗轮蜗杆合营感化下,使机械运行起来,在此进程中蜗杆传动根本上战胜了以往带传动的摩擦损耗;在蜗杆作为制动装配时,蜗轮,蜗杆的啮合,可使机械在运行时停下来,这个进程中蜗杆蜗轮的啮合静摩擦达到最大,可使活动中的机械在刹时停滞.在工业临盆中既节俭了时光又增长了临盆效力,而在工艺设备的机械减速装配,深受用户的佳誉,是面前当代工业设备实现大小扭矩,大速比,低噪音,高稳固机械减速传动独揽装配的最佳选择.(2)计划订定A.箱体(1):蜗轮蜗杆箱体内壁线的肯定; (2):轴承孔尺寸的肯定;(3):箱体的构造设计;a.箱体壁厚及其构造尺寸的肯定b. 轴承旁衔接螺栓凸台构造尺寸的肯定c.肯定箱盖顶部外概况轮廓d. 外概况轮廓肯定箱座高度和油面e. 输油沟的构造肯定f. 箱盖.箱座凸缘及衔接螺栓的安插B.轴系部件(1) 蜗轮蜗杆减速器轴的构造设计a. 轴的径向尺寸的肯定b. 轴的轴向尺寸的肯定(2)轴系零件强度校核a. 轴的强度校核b. 滚动轴承寿命的校核盘算C.减速器附件a.窥视孔和视孔盖b. 通气器c. 轴承盖d. 定位销e. 油面指导装配f. 油塞g. 起盖螺钉h. 起吊装配第二章减速器的总体设计2.1.1 订定传动计划本传动装配用于带式运输机,工作参数:运输带工作拉力F=3KN,工作速度=1.2m/s,滚筒直径D=310mm,传动效力η=0.96,(包含滚筒与轴承的效力损掉)两班制,持续单向运转,载荷较安稳;应用寿命8年.情形最高温度80℃.本设计拟采取蜗轮蜗杆减速器,传动简图如图6.1所示.图6.1 传动装配简图1—电念头 2.4—联轴器 3—级蜗轮蜗杆减速器5—传动滚筒 6—输送带2.1.2 电念头的选择(1)选择电念头的类型按工作前提和请求,选用一般用处的Y系列三相异步电念头,关闭式构造,电压380V.(2)选择电念头的功率电念头所需的功率式中,单位为KW;η—电念头至工作机之间传动装配的总效力;,单位为KW;输送机所需的功率输送机所需的功率/1000=3000×1.2/1000×0.8=4.5 kW查表,(3)选择电念头的转速由表推举的传动比的合理规模,故电念头转速的可选规模为:(10~40)×73.96=740-2959r/min相符这规模的电念头同步转速有750.1000.1500.3000 r/min四种,现以同步转速1000 r/min和1500 r/min两种经常应用转速的电念头进行剖析比较.分解斟酌电念头和传动装配的尺寸.重量.价钱.传动等到市场供给情形,拔取比较适合的计划,现选用型号为Y132M—4.2.1.3 肯定传动装配的传动等到其分派减速器总传动等到其分派:减速器总传动比/73.96=19.47式中i—传动装配总传动比,单位r/min,单位r/min2.1.4 盘算传动装配的活动和动力参数(1)各轴的输入功率轴Ⅰ轴Ⅱ(2)各轴的转速轴Ⅰ:轴Ⅱ:/19.47=73.96 r/min(3)各轴的输入转矩d/nm=9550轴Ⅰ:1/n1=9550轴Ⅱ:2/n2=9550上述盘算成果汇见表3-1表3-1传动装配活动和动力参数2.2 传动零件的设计盘算2.2.1 蜗轮蜗杆传动设计一.选择蜗轮蜗杆类型.材料.精度依据GB/T10085-1988的推举,采取渐开线蜗杆(ZI)蜗杆材料选用45钢,整体调质,概况淬火,齿面硬度45~50HRC.蜗轮齿圈材料选用ZCuSn10Pb1,金属模锻造,滚铣后加载跑合,8级精度,尺度包管侧隙c.(1)选z1,z2:1=2,z2= z1×n1/n2=2×≈39.z2在30~64之间,故合乎请求.(2)蜗轮转矩T2:T2=T1×i106×××0.82/(3)载荷系数K:因载荷安稳,查表7.8取K=1.1(4)材料系数ZE查表(5)许用接触应力H]查表H]=220 Mpa N=60×jn2×L h=60××1××107H×220=178.5 Mpa(6):(7)初选的值:查表7.1取m=6.3,d1=63(8)导程角(9)滑动速度Vs(10)啮合效力由Vs=4.84 m/s查表得ν=1°16′(11取轴承效力T2=T1×i106(12)磨练的值原选参数知足齿面接触疲惫强度请求1=2,z2=39(1)中间距a(2)蜗杆尺寸分度圆直径d1 d1=63mm齿顶圆直径da1 da1=d1+2ha1=(63+2×齿根圆直径df1 df1=d1﹣2hf=63﹣2×导程角右旋轴向齿距 Px1=π×齿轮部分长度b1 b1≥×××取b1=90mm(2)蜗轮尺寸分度圆直径d2 d2=m×z2×齿顶高 ha2=ha*××齿根高 hf2= (ha*+c*)×m=(1+0.2)×齿顶圆直径da2 da2=d2+2ha2=245.7+2××齿根圆直径df2 df2=d2﹣﹣导程角右旋轴向齿距 Px2=Px1=π××齿宽角 sin(α蜗轮咽喉母圆半径 rg2=a—﹣(3)热均衡盘算①估算散热面积A②验算油的工作温度tiKs=20 W/(㎡·℃).80℃油温未超出限度(4)润滑方法依据Vs=4.84m/s,查表7.14,采取浸油润滑,油的活动粘度V40℃=350×10-6㎡/s(5)蜗杆.蜗轮轴的构造设计(单位:mm)①蜗轮轴的设计最小直径估算dmin≥cc查《机械设计》表11.3得 c=120 dmin≥=120×依据《机械设计》表11.5,选dmin=48d1= dmin+2a =56 a≥≈4d2=d1+ (1~5)mm=56+4=60d3=d2+ (1~5)mm=60+5=65d4=d3+2a=65+2×6=77 a≥≈6×≈8d5=d4﹣2h=77﹣2×5.5=66d6=d2=60l1=70+2=72②蜗杆轴的设计最小直径估算dmin≥cdmin=30d1=dmin+2a=20+2×2.5=35 a=(0.07~0.1)dmind2=d1+(1~5)=35+5=40d3=d2+2a=40+2×2=44 a=(0.07~0.1)d2d4=d2=40蜗杆和轴做成一体,即蜗杆轴.蜗轮采取轮箍式,青铜轮缘与锻造铁心采取H7/s6合营,并加台肩和螺钉固定,螺钉选6个几何尺寸盘算成果列于下表:2.3 轴的设计2.3.1 蜗轮轴的设计(1)选择轴的材料拔取45钢,调质,硬度HBS=230,由表查1.10-3)(2)初步估算轴的最小直径取C=120,得dmin≥=120依据《机械设计》表11.5,选dmin=63(3)轴的构造设计①轴上零件的定位.固定和装配单级减速器中,可将齿轮按排在箱体中心,相对两轴承对称散布,齿轮左面由轴肩定位,右面用套筒轴向固定,周向固定靠平键和过渡合营.两轴承分离以轴肩和套筒定位,周向则采取过渡合营或过盈合营固定.联轴器以轴肩轴向定位,右面用轴端挡,圈轴向固定.键联接作周向固定.轴做成阶梯形,左轴承从做从左面装入,齿轮.套筒.右轴承和联轴器依次右面装到轴上.②肯定轴各段直径和长度Ⅰ段d1=50mm L1=70mmⅡ段选30212型圆锥滚子轴承,其内径为60mm,宽度为22mm.故Ⅱ段直径d2=60mm.Ⅲ段斟酌齿轮端面和箱体内壁.轴承端盖与箱体内壁应有必定距离,则取套筒长为38mm.故L3=40mm,d3=65mm.Ⅳ段d4=77mm,L4=70mmⅤ段d5=d4+2h=77+2×5.5=88mm,L5=8mmⅥ段d6=65mm,L6=22mmⅦ段 d7=d2=760mm,L7=25(4)按弯扭合成应力校核轴的强度①绘出轴的构造与装配图 (a)图②绘出轴的受力简图 (b)图③绘出垂直面受力争和弯矩图(c)图轴承支反力:F RBV=Fr+F RAV盘算弯矩:截面C右侧弯矩截面C左侧弯矩④绘制程度面弯矩图 (d)图轴承支反力:截面C 处的弯矩⑤绘制合成弯矩图 (e)图图3.2 低速轴的弯矩和转矩(a)轴的构造与装配 (b)受力简图 (c)程度面的受力和弯矩图 (d)垂直面的受力和弯矩图 (e)合成弯矩图 (f)转矩图 (g)盘算弯矩图⑥绘制转矩图 (f)图105⑦绘制当量弯矩图 (g)图转矩产生的扭剪应力按脉动轮回变更,取0.6,截面C 处的当量弯矩为⑧校核安全截面C 的强度安然. 图3.3 蜗轮轴的构造图d M ECe 7.7771.01062.3511.03335=⨯⨯=⨯=σ2.3.3 蜗杆轴的设计(1)选择轴的材料拔取45钢,调质处理,硬度HBS=230,剪切疲惫极限(2) 初步估算轴的最小直径最小直径估算dmin≥取dmin=20(3)轴的构造设计按轴的构造和强度请求拔取轴承处的轴径d=35mm,初选轴承型号为30207圆锥滚子轴承(GB/T297—94),采取蜗杆轴构造,个中,齿顶圆长度尺寸依据中心轴的构造进行具体的设计,校核的办法与蜗轮轴相相似,经由具体的设计和校核,得该蜗杆轴构造是相符请求的,是安然的,轴的构造见图3.4所示:图3.4 蜗杆轴的构造草图第三章轴承的选择和盘算3.1 蜗轮轴的轴承的选择和盘算按轴的构造设计,初步选用30212(GB/T297—94)圆锥滚子轴承,内径d=60mm,外径D=110mm,B=22mm.(1)盘算轴承载荷①轴承的径向载荷轴承A轴承B②轴承的轴向载荷轴承的派生轴向力查表得:30212°38′32″所以无外部轴向力.轴承A被“压紧”,所以,两轴承的轴向力为③盘算当量动载荷由表查得圆锥滚子轴承30211轴承A e取X=1,Y=0,轴承B e取X=1,Y=0,3.2 蜗杆轴的轴承的选择和盘算按轴的构造设计,选用30207圆锥滚子轴承(GB/T297—94),经校核所选轴承能知足应用寿命,适合.具体的校核进程略.3.3 减速器锻造箱体的重要构造尺寸(单位:mm)(1) 8,(2) 8,(3) 箱座.箱盖.箱座底的凸缘厚度:(4) 地脚螺栓直径及数量:依据=154.35,得取d f=18,地脚螺钉数量为4个;(5)(6) 箱盖.箱座联络螺栓直径~14.4,取(7) 表2.5.1轴承端盖螺钉直径:(8) 检讨孔盖螺钉直径:本减速器为一级传动减速器,所以取(9) ,把数据代入上述公式,得数据如下:(10) 表2.5.2螺栓相干尺寸:(11)准尽量接近,(12) ;(13),由构造肯定;(14) 箱外壁至轴承座端面的距离:(15) 箱盖.(16)(17) 锻造斜度.过渡斜度.锻造外圆角.内圆角:锻造斜度:10,:20,第四章其他零件设计4.1.1高速轴键联接的选择和强度校核高速轴采取蜗杆轴构造,是以无需采取键联接.4.1.2 低速轴与蜗轮联接用键的选择和强度校核(1) 选用通俗平键(A型)按低速轴装蜗轮处的轴径d=77mm,查表,选用键22×14×63 GB1096—2003.(2) 强度校核键材料选用45钢,键的工作长度按公式的挤压应力故键的联接的强度是足够的.4.2 联轴器的选择和盘算4.2.1 高速轴输入端的联轴器盘算转矩,查表取,有查表选用TL5型弹性套柱销联轴器,材料为35钢,许用转矩,许用转速标识表记标帜:LT5联轴器30×50 GB4323—84.选键,装联轴器处的轴径为30mm,选用键8×7×45 GB1096—79,对键的强度进行校核,键同样采取45钢,有关机能指标见(2.6.2),按公式的挤压应力及格.所以高速级选用的联轴器为LT5联轴器30×50 GB4323—84,所用的联络键为8×7×45 GB1096—79.4.2.2 低速轴输出端的联轴器依据低速轴的构造尺寸以及转矩,选用联轴器LT8联轴器50×70 GB4323—84,所用的联络键为14×9×60 GB1096—79,经由校核盘算,选用的键是相符联络的强度请求的,具体的盘算进程与上面雷同,所以省略.4.3 减速器的润滑减速器中蜗轮和轴承都须要优越的润滑,起重要目标是削减摩擦磨损和进步传动效力,并起冷却和散热的感化.别的,润滑油还可以防止零件锈蚀和下降减速器的噪声和振动等. 本设计拔取润滑油温度C t ︒=40时的蜗轮蜗杆油,蜗轮采取浸油润滑,浸油深度约为h1≥1个螺牙高,但油面不该高于蜗杆轴承最低一个滚动体中间.4.4 部分零件加工工艺进程4.4.1 轴的加工工艺进程轴的工艺进程相对于箱盖,底座要简略很多,本设计输出轴的一般工艺进程为:(1) 落料.锻打(2) 夹短端.粗车长端端面.打中间孔(3) 夹短端.粗车长端各档外圆.倒角(4) 反向夹长端,粗车短端外圆.倒角.粗车短端端面.打中间孔(5) 热处理(6) 夹短端,半精车短端外圆(7) 反向夹长端,半精车短端外圆(8) 磨长端外圆(9) 反向磨短端外圆(10) 铣两键槽(11) 加工好的蜗轮轴4.4.2 箱体加工工艺进程蜗轮蜗杆减速器的箱盖和箱体,它们的工艺进程比较庞杂,先是箱盖和箱体分离单独进行某些工序,然后合在一路加工,最后又离开加工.箱盖单独先辈行的工序有:(1)箱盖锻造(2)回火.清沙.去毛刺.打底漆.毛坯磨练(3)铇视孔顶面(4)铇剖分面(5)磨剖分面(6)钻.攻起盖螺钉完成前述单独工序后,即可进行下列工序:(1)箱盖.箱体瞄准张开,夹紧;钻.铰定位销孔,敲入圆锥销(2)钻箱盖和箱体的联接螺栓孔,刮鱼眼坑(3)离开箱壳,消除剖分面毛刺.清算切屑(4)张开箱壳,敲入定位销,拧紧联接螺栓(5)铣两头面(6)粗镗各轴轴承座孔(7)精镗各轴轴承座孔(8)钻.攻两头面螺孔(9)拆开箱壳(10)装上油塞,箱体地脚螺栓孔划线(11)钻地脚螺栓孔.刮鱼眼坑(12)箱盖上固定视孔盖的螺钉孔划线(13)钻.攻固定视孔盖的螺钉孔(14)去除箱盖.箱体接合面毛刺,消除铁屑(15)内概况涂红漆结论此次经由过程对已知前提对蜗轮蜗杆减速器的构造外形进行剖析,得出总体计划.按总体计划对各零部件的活动关系进行剖析得出蜗轮蜗杆减速器的整体构造尺寸,然后以各个体系为模块分离进行具体零部件的设计校核盘算,得出各零部件的具体尺寸,再从新调剂整体构造,整顿得出最后的设计图纸和解释书.此次设计经由过程对蜗轮蜗杆减速器的设计,使我对成型机械的设计办法.步调有了较深的熟习.熟习了蜗轮.轴等多种经常应用零件的设计.校核办法;控制了若何选用尺度件,若何查阅和应用手册,若何绘制零件图.装配图;以及设计非尺度零部件的要点.办法. 此次设计贯串了所学的专业常识,分解应用了各科专业常识,查各类常识手册从中使我进修了很多日常平凡在教材中未学到的或未深刻的内容.我信任此次设计对今后的工作进修都邑有很大的帮忙. 因为本身所学常识有限,而机械设计又是一门异常深邃的学科,设计中肯定消失很多的缺少和须要改良的地方,愿望先生指出,在今后的进修工作中去完美它们.参考文献1 吴彦农,康志军.Solidworks2003实践教程. 淮阴:淮阴工学院,20032 叶伟昌. 机械工程及主动化简明手册(上册). 北京:机械工业出版社,20013 徐锦康. 机械设计. 北京:机械工业出版社,20014 成大先. 机械设计手册(第四版第4卷). 北京:化学工业出版社,20025 葛常清. 机械制图(第二版). 北京:中国建材工业出版社,20006 朱敬. 孙明,邵谦谦.AutoCAD2005.电子工业出版社,20047 董玉平. 机械设计基本.机械工业出版社,20018 曾正明. 机械工程材料手册. 北京:机械工业出版社,20039 周昌治. 杨忠鉴,赵之渊,陈广凌. 机械制作工艺学. 重庆:重庆大学出版社,199910 曲宝章. 黄光烨. 机械加工工艺基本. 哈尔滨:哈尔滨工业大学出版社,200211 张福润. 徐鸿本,刘延林. 机械制作基本(第二版). 武汉:华中科技大学出版社,200212 徐锦康. 机械设计. 北京:高级教导出版社,200413 宁汝新. 赵汝嘉. CAD/CAM技巧. 北京:机械工业出版社,200314 司徒忠. 李璨. 机械工程专业英语. 武汉:武汉理工大学出版社,200115 牛又奇. 孙开国. 新编Visual Basic程序设计教程. 姑苏:姑苏大学出版社,200216 甘登岱. AutoCAD2000.航空工业出版社,200017 夸克工作室.SolidWorks2001.科学出版社,200318 吴威望. SolidWorks2003.科学出版社,200419 甘永立. 几何量公役与检测.上海科学技巧出版社,2004。
(完整版)两级蜗轮蜗杆减速器说明书(毕业课程设计附CAD图)

机械设计课程设计计算说明书题目设计电动机卷扬机传动装置专业班级机械设计制造及其自动化08级1班学号学生姓名熊丁指导教师周毓明何斌锋西安文理学院2010年12月西安文理学院机械设计课程设计任务书学生姓名熊丁专业班级 08机械设计制造及其自动化(1)班学号指导教师职称教研室题目设计电动卷扬机传动装置编号W-10传动系统图:原始数据:工作条件:连续单向运转,工作时有轻微振动,小批量生产,单班制工作,使用期限8年,运输带速度允许误差为±5%要求完成:1.减速器装配图1张(A2)。
2.零件工作图2张(箱体和轴)。
3.设计说明书1份,字。
开始日期 2010 年 12 月 6 日完成日期 2010 年 12 月 31 日2010年 12 月 1 日目录1.电机选择 ................................................................................................................................................. 2.选择传动比 .............................................................................................................................................2.1总传动比 ........................................................................................................................................2.2减速装置的传动比分配 ................................................................................................................ 3.各轴的参数 .............................................................................................................................................3.1各轴的转速 ....................................................................................................................................3.2各轴的输入功率 ............................................................................................................................3.3各轴的输出功率 ............................................................................................................................3.4各轴的输入转矩 ............................................................................................................................3.5各轴的输出转矩 ............................................................................................................................3.6各轴的运动参数表 ........................................................................................................................4.蜗轮蜗杆的选择 .......................................................................................................................................4.1选择蜗轮蜗杆的传动类型 ............................................................................................................4.2选择材料 ........................................................................................................................................4.3按计齿面接触疲劳强度计算进行设 ............................................................................................4.4蜗杆与蜗轮的主要参数与几何尺寸 ............................................................................................4.5校核齿根弯曲疲劳强度 ................................................................................................................4.6验算效率 ........................................................................................................................................4.7精度等级公差和表面粗糙度的确定 ............................................................................................ 5.圆柱齿轮的设计 .....................................................................................................................................5.1材料选择 ........................................................................................................................................5.2按齿面接触强度计算设计 ............................................................................................................5.3计算 ................................................................................................................................................5.4按齿根弯曲强度计算设计 ............................................................................................................5.5取几何尺寸计算 ............................................................................................................................ 6.轴的设计计算 .......................................................................................................................................6.1蜗杆轴 ............................................................................................................................................6.1.1按扭矩初算轴径 ........................................................................................................................6.1.2蜗杆的结构设计 ........................................................................................................................6.2蜗轮轴 ............................................................................................................................................6.2.1输出轴的设计计算 ....................................................................................................................6.2.2轴的结构设计 ............................................................................................................................6.3蜗杆轴的校核 ................................................................................................................................6.3.1求轴上的载荷 ............................................................................................................................6.3.2精度校核轴的疲劳强度 ............................................................................................................6.4蜗轮轴的强度校核 ........................................................................................................................6.4.1精度校核轴的疲劳强度 ............................................................................................................6.4.2精度校核轴的疲劳强度 ............................................................................................................7.滚动轴承的选择及校核计算 ...................................................................................................................7.1蜗杆轴上的轴承的选择和寿命计算 ............................................................................................7.2蜗杆轴上轴承的选择计算 ............................................................................................................8.键连接的选择及校核计算 .......................................................................................................................8.1输入轴与电动机轴采用平键连接 ................................................................................................8.2输出轴与联轴器连接采用平键连接 ............................................................................................8.3输出轴与蜗轮连接用平键连接 .................................................................................................... 9.联轴器的选择计算 .................................................................................................................................9.1与电机输出轴的配合的联轴器 ....................................................................................................9.2与二级齿轮降速齿轮轴配合的联轴器 ........................................................................................10.润滑和密封说明 .....................................................................................................................................10.1润滑说明 ......................................................................................................................................10.2密封说明 ...................................................................................................................................... 11.拆装和调整的说明 ............................................................................................................................... 12.减速箱体的附件说明 ...........................................................................................................................13.设计小结 ................................................................................................................................................. 14.参考文献 ...............................................................................................................................................。
涡轮蜗杆减速器说明书

设计题目:矿用回柱绞车传动装学生姓名:王丽娟)(学生学号:0309135831 班09-4专业班级:电力学院热能指导教师:周晓谋设计题目J.矿用回柱绞车传动装置设计1.设计条件(1)机器功用:煤矿井下回收支柱用的慢速绞车;(2)工作情况:工作平稳,间歇工作(工作于间歇时间比为1:2),绳筒转向定期变换;(3)运动要求:绞车绳筒转速误差不超过8%;(4)工作能力:储备余量10%;(5)使用寿命:10年;每年350天;每天8小时;(6)检修周期:一年小修,五年大修;(7)生产批量:小批生产;(8)生产厂型:中型机械厂。
2.原始数据3.设计任务(1)设计内容①电动机选型;②开式齿轮设计;③减速器设计;④联轴器选择设计;⑤滚筒轴系设计;⑥其他。
(2)设计工作量①减速器装配图1张;②零件图两张(高速轴与低速齿轮);③设计计算说明书1份。
4.设计要求:J8蜗杆-齿轮减速器要求蜗杆减速器设计成:阿基米德蜗杆减速器。
)1(.(2)第一级开式齿轮与蜗杆传动合并设计成蜗杆—齿轮减速器。
2. 电动机选择(1)电动机输出功率计算若已知工作机上作用力和线速度时:)m F(N)/s v(?(kW)/1000vP'=F'(r/min)n时:和转速若已知工作机上的阻力m)T(N''? (kW)Tn9550P/?本设计中:F=56 KN F=56 KN已知滚筒上钢绳的牵引力:V=0.15m/s V=0.15m/s钢绳的最大线速度:?的计算:得9-1查表?0.96?卷筒:1??0.9610.90.90.90.90.90.80.5mi 147mimi mi mi mi K K K13.0K12.4K11.5KW5082.94833.414616.31K mi73.mi''?30?12滑动速度'??)?V(60)/nd(?1000cos1s1m/s0.079??10d1V m/s10?选择材料:sHR45-510.730m20/m146.1m320.585m18.715/m14209.012.5 m53?:蜗轮分度圆直径d?mz?12.5?4022d?500mm2 :蜗轮圆周速度v?1.92 m/s2???500?73.5/60000v?nd/60000?222(符合估计))齿根弯曲疲劳强度校核计算(3 ?蜗轮齿根弯曲应力F7-10由《机械设计》式KT2??2][?Y?FFF?cosmdd21Y?2.32F Y蜗轮齿形系数F2?mm13.72N/?F7.9 由《机械设计》表??][<FF2?1.1?1837240弯曲强度足够???2.32F?'''112?500?12.5?cos123459热平衡计算(4)./v7.10由查《机械设计》表s'?30?1V'?30?1V'5934tan12???0.89则?1?0.89'')30tan(123459?11??0.992??0.99 :轴承效率2?0.96?3??0.96 :搅油耗损的效率3??0.84 ????0.96??0.99?0.89?则312K散热系数?2?C/m?K17 W2α按通风良好,取17?m/WC K?t?85C C?t85 :油的工作温度故2m2.59 A?0.846)?1000?18.59?(1?A20)17?(85?(5)其它主要尺寸计算由《机械设计》表7.4、表7.5*齿顶高系数1?h a蜗杆齿顶圆直径d?137 mm a1*12.5?2?12hm?112??d?d aa11 h?15mm**m??齿根高h(h?c1.2)m f1af1mm h?15f2**m?1.2c?x)mh?(h?af22*?0.2通常取c蜗杆齿根圆直径d?82 mm1f15112?2???dd?2h1f1f1蜗杆螺纹部分长度b?(11?0.06z)m?(11?0.06?40)?12.5?167.5(圆整)mm b?168211蜗轮喉圆直径*d?d?2hm?500?2?1?12.5?525(圆整)2aa2d?525 mm2a蜗轮根圆直径d?470 mm470??dd15??500?2h2?2f22f2f54m m HB26HB21/70/5511.214.11.11.21./6152//52/37/29N1./27/2110./m1.1.1.m189.2.0.8m m2.52.21.61.7m86.2 m85.31754195726HBHB21/70/5514.111.21.21.286//698.698.//37/29N1./27/211.1.1.m189.2.0.820mm2.82.21.51.7m103.8m96.4m17m6222mm670.01m0.00mT?120770N?mm1转矩T,T21mm N?T?1837242d蜗杆分度圆直径1??202?Z1Z蜗杆头数??1234′59′′1mm112?d/112=2156.61d120770?2?/?F2T圆周力11t11mm500?d2500=7348.96?1837240/?T?F2/d2轴向力212a F?2156.61N1t??径向力tantan?FF?F1r1at2N?F7348.961a 2)初步估算轴的直径N2674.80F?1r 45号钢调质处理选取材料Pd?A8-2 由《机械设计》式3n计算轴的最小直径并加大3%以考虑键槽影响由《机械设计》表8.6 取A=11518.59d?27.6mm?1.03d??115则3minmin14703)I轴蜗杆的结构设计)确定轴的结构方案1(右轴承从轴的右端装入,靠轴肩定位;左轴承从轴的左端装入,并靠轴.。
蜗轮蜗杆软件说明书

目 录第一章蜗轮软件 (1)第一节引言 (1)第二节参数输入 (4)第四节测量项目选择 (9)第五节系统复位和测头标定 (10)第六节系统自检 (11)第七节结果显示 (13)第八节结果存盘 (15)第九节打印输出 (16)第十节文件管理结果复现 (17)第十一节评估参数 (18)第二章蜗杆软件 (21)第一节 引 言 (21)第二节蜗杆类型 (24)第三节蜗杆参数 (27)第四节系统复位和测头标定 (31)第五节系统自检 (32)第六节结果显示 (34)第七节结果存盘 (35)第八节打印输出 (36)第九节结果调盘结果复现 (37)第十节 评估参数 (38)第一章 蜗 轮 软 件第一节 引 言1.1软件运行环境圆柱齿轮测量软件系统运行的硬件环境以精达公司为测量仪器配置的计算机硬件为准。
1.2软件安装将JD 齿轮测量中心蜗轮软件解压到D 盘根目录下的《精达软件系统》文件夹内(如果这个文件夹内有这个软件,直接把原来的替换即可),同时将相应的仪器配置文件拷贝到D 盘根目录下,安装完成。
1.3软件功能1.采用基准样板校正仪器精度;2.蜗轮误差评值(包括总误差、形状误差、斜率误差、鼓形量、齿距误差等);3.参数输入、参数存盘、参数调盘、测量设置、文件管理、结果复现、系统复位、测头标定、系统自检、操作提示、过程显示、报告单打印等。
1.4测量项目齿廓profile : αf f 齿廓形状误差 Profile form error αf fαH f 齿廓斜率误差Profile angle error αH f αF 齿廓总误差 Profile total error αFαC齿廓鼓形评定 Profile crowning αC 周节pitch : p F累计误差 Cumulative pitch error p Fpt f 齿距误差 Adjacent pitch error pt fu f相邻齿距差 Difference between adjacent pitchs u f 径 跳Fr : r F 径跳 Runout error r F1.5注意:1 打开电源时,需先打开计算机的电源,然后打开仪器电源。
- 1、下载文档前请自行甄别文档内容的完整性,平台不提供额外的编辑、内容补充、找答案等附加服务。
- 2、"仅部分预览"的文档,不可在线预览部分如存在完整性等问题,可反馈申请退款(可完整预览的文档不适用该条件!)。
- 3、如文档侵犯您的权益,请联系客服反馈,我们会尽快为您处理(人工客服工作时间:9:00-18:30)。
目 录第一章蜗轮软件 (1)第一节引言 (1)第二节参数输入 (4)第四节测量项目选择 (9)第五节系统复位和测头标定 (10)第六节系统自检 (11)第七节结果显示 (13)第八节结果存盘 (15)第九节打印输出 (16)第十节文件管理结果复现 (17)第十一节评估参数 (18)第二章蜗杆软件 (21)第一节 引 言 (21)第二节蜗杆类型 (24)第三节蜗杆参数 (27)第四节系统复位和测头标定 (31)第五节系统自检 (32)第六节结果显示 (34)第七节结果存盘 (35)第八节打印输出 (36)第九节结果调盘结果复现 (37)第十节 评估参数 (38)第一章 蜗 轮 软 件第一节 引 言1.1软件运行环境圆柱齿轮测量软件系统运行的硬件环境以精达公司为测量仪器配置的计算机硬件为准。
1.2软件安装将JD 齿轮测量中心蜗轮软件解压到D 盘根目录下的《精达软件系统》文件夹内(如果这个文件夹内有这个软件,直接把原来的替换即可),同时将相应的仪器配置文件拷贝到D 盘根目录下,安装完成。
1.3软件功能1.采用基准样板校正仪器精度;2.蜗轮误差评值(包括总误差、形状误差、斜率误差、鼓形量、齿距误差等);3.参数输入、参数存盘、参数调盘、测量设置、文件管理、结果复现、系统复位、测头标定、系统自检、操作提示、过程显示、报告单打印等。
1.4测量项目齿廓profile : αf f 齿廓形状误差 Profile form error αf fαH f 齿廓斜率误差Profile angle error αH f αF 齿廓总误差 Profile total error αFαC齿廓鼓形评定 Profile crowning αC 周节pitch : p F累计误差 Cumulative pitch error p Fpt f 齿距误差 Adjacent pitch error pt fu f相邻齿距差 Difference between adjacent pitchs u f 径 跳Fr : r F 径跳 Runout error r F1.5注意:1 打开电源时,需先打开计算机的电源,然后打开仪器电源。
等仪器初始化完成后,再加伺服ON。
2在进行测头校正之前,请检查“参数输入”界面内“测头直径”的值,是否与仪器现在安装的测头的直径相同。
第二节参数输入2.1参数输入打开蜗轮软件,在主界面中选中被测蜗轮的类型后,单击确定按钮,进入参数输入界面,如图2.1所示:图2.1 参数输入图2.2 蜗轮参数输入文件名:由数字、字母、中文、下划线及标点符号组成,最多有21个字符;齿轮号No :由数字、字母、中文、下划线及标点符号组成;蜗杆头数Z1:与蜗轮配对的蜗杆的头数。
蜗轮齿数(Number of teeth)2Z :模数(Module )n M :蜗轮的轴向模数蜗杆齿形角(profile angle )α:蜗杆导程角(reference lead angle ))/(Z +−γ:蜗轮齿宽(Face width )B :蜗轮的实际齿宽;变位系数(Modification coefficients )n X :顶圆直径(Tip diameter of worm wheel )e d :根圆直径(root diameter of worm wheel )f d :全齿高(total depth )h :测头直径c d :测头型式:球型或者锥形。
角度输入方式:1.度分秒采用度分秒格式时,输入的螺旋角和压力角按照度分秒的方式显示,输入时,度、分、秒之间用标点符号或者英文字母隔开。
2.度格式采用度格式时,输入的螺旋角和压力角按照角度的方式显示,正常输入。
2.2测量位置计算蜗杆参数输入完毕后,需要进行测量计算,得到蜗轮的测量参数。
蜗杆参数输入完毕后,单击标准计算。
图2.3 2.3齿形测量参数通过2.3的操作得到齿形测量参数如下图:图2.4 齿形测量参数计算之后,根据需要调节起测、起评、终评和终测的位置,还可以调节合适的误差放大比和长度放大比。
2.4齿距测量参数图2.5 齿距测量参数可以在该界面中调节合适的齿距误差放大比。
2.5测量位置设定测量之前,要设定好如下位置:上端面高度、齿形测量截面、齿距测量截面和齿距测量位置。
如图2.6所示:图2.6 测量位置设定上端面高度人工输入,齿形测量截面、齿距测量截面和齿距测量位置通过测量位置计算得到。
第三节测量设置3.1测量设置的进入图3.1 测量设置3.2测量设置的功能测量设置中可以设置齿轮测量的评值方法、测量进入动作、测量结果显示、打印背景和显示方式。
3.3测量设置说明3.3.1测量误差评定方式四点固定:根据齿轮的起测,起评,终评,终测四点进行评定;自动评值:根据工件实际形式自动推算出评定点。
3.3.2测头进入方式启动测量后测头的进入方式有两种选择:自动进入和手动进入。
自动进入:选择自动进入时,启动测量后测头自动移动到齿顶圆的位置,并自动进入齿槽,自动寻找齿面。
手动进入:选择手动进入时,启动测量后测头自动停到外圆位置,需要人为的对准齿槽,按开始测量键继续进行测量,另外,当选择手动进入时,标定测头时会停在校准块的中部,按开始测量键后才可继续测头标定。
3.3.3测量结果的打印自动打印:选择自动打印,测量完成后,直接打印报告单。
选择打印:测量完成后,可人为选择打印。
3.3.4测量结果打印时间测量时间:打印报告单上显示的是测量时的时间;当前时间:打印报告单上显示的是当前的时间。
3.3.5测量结果保存方式选择保存:当测量完后,只有选择结果存盘时才会把测量结果保存。
自动保存:每次测量结束时,都会把结果自动保存在默认文件夹里,文件名以图号+时间命名。
3.3.6结果显示背景选择黑色背景:结果显示和打印的背景为黑色。
标尺网格:结果显示和打印的背景为网格。
3.3.7齿形齿向结果显示同屏显示:齿形齿向的测量误差曲线在同一屏幕上显示,为同屏显示。
分屏显示:齿形齿向的测量误差曲线不在同一屏幕上显示,分别在不同屏幕上显示。
3.3.8评值输出线型选择中线:测量误差曲线的输出,以最小二乘法计算出误差中线,并显示。
包络线:显示以起评、终评、测量曲线的最大误差和最小误差为界限,画出的一条边框。
第四节测量项目选择图4.1测量项目选择可以测量的项目有齿形和齿距齿形测量分为:标准四齿、标准三齿、标准二齿和单齿,同时又可以选择测量左齿面或者右齿面。
若齿形不测,选择不测量。
如果左右面和不测量均不选,则左右面均测量。
齿距测量有四种选择:标准双面、左齿面、右齿面和不测量。
第五节系统复位和测头标定5.1系统复位打开伺服-on后,进入程序主界面,首先进行系统复位。
系统复位可以使用控制面板系统复位按键,也可以单击主界面上的系统复位按键,也可以使用F4功能键,系统复位可以在主界面,参数输入界面,或者测量设置界面中进行。
系统复位提示框如下:图5.1系统复位5.2测头标定系统复位,测头标定都是测量之前的准备过程。
测头标定前要输入测头的直径和测头的类型,确保测头的直径和类型与当前仪器安装的测头一致,如果当前测头被碰弯,请重新标定测头。
测头的直径也可以在系统复位后再输入。
测头标定提示框如下图所示:图5.2测头标定第六节系统自检6.1系统自检的进入在齿轮主界面中单击“系统自检”,即可弹出自检对话框;通过按F11功能键(可在主界面、参数输入界面、测量项目选择界面中使用),弹出自检对话框。
6.2系统自检说明测量之前进行系统自检是为了检查测量系统当前的状态,如下图所示:图6.1 系统自检6.2.1自检状态说明一图6.2 状态(一)图五所示的提示框检测的内容有:C轴当前位置(C 0.0000)、X轴当前位置(X 0.0000)、Y轴当前位置(Y 0.0000)、Z轴当前位置(Z 0.0000);电感测头示值或数字测头示值(AD -409.4);测头保护状态(BAK);X轴正限位状态(LX+)、X轴负限位状态(LX-)、X轴Home状态(HOMX);Y轴正限位状态(LY+)、Y轴负限位状态(LY-)、Y轴Home状态(HOMY);Z轴正限位状态(LZ+)、Z轴负限位状态(LZ-)、Z轴Home状态(HOMZ);X轴正向摇杆的状态(X+)、X轴负向摇杆的状态(X-);Y轴正向摇杆的状态(Y+)、X轴负向摇杆的状态(Y-);Z轴正向摇杆的状态(Z+)、X轴负向摇杆的状态(Z-);高低速状态(H/L)。
6.2.2自检状态说明二图6.3 状态(二)查看伺服状态(Servo state:),正常为8888,(仪器型号不同,显示的也可能不同,以培训说明为准);各轴驱动器状态,如图所示:正常显示为normal:C轴报警( C AXIS ALM )X轴报警( X AXIS ALM )Y轴报警( Y AXIS ALM )Z轴报警( Z AXIS ALM )6.2.3自检状态说明三图6.4 状态(三)Probe Calibration:F5(level)表示测头左右标定;Probe type:ball 表示测头为球形;Probe Dia.:1.500 表示测头直径为1.5mm;Not Control !!!表示没有控制卡;Not Gather !!!表示没有采集卡;正常情况下上述显示字体为蓝色,显示为红色表示错误。
第七节结果显示启动测量,进入结果显示界面,测量过程中可以动态实时显示测量结果。
测量结束后,可以翻页查看各个测量项目的结果,并可以通过当前界面的评值设置修改显示的形式;对于起评、终评位置,可以通过鼠标左键拖动起评、终评线直接修改,也可以在结果显示界面中通过评值设置进行修改。
图7.1 评值设置蜗轮只能测量齿形和齿距,所以不分同屏显示和分屏显示,齿形显示如图7.2。
图7.2 齿形显示 齿距显示结果如图7.3所示:图7.3 齿距显示第八节结果存盘测量结束后,在测量界面内点击结果存盘按钮,进入结果存盘界面内。
在文件名内输入文件名,保存格式为mea,结果存盘时,名字后会自动添加mea后缀,也可以手动输入加.mea,应正确保存测量结果,避免保存结果丢失。
文件的保存路径,用户可以自行修改。
图8.1 结果存盘第九节打印输出以通用激光打印机输出测量结果报告单。
图9.1第十节文件管理结果复现10.1文件管理的进入在主界面中单击文件管理功能键进入。
图10.1 文件管理10.2文件管理的使用进入文件管理界面后,找到所要查看的文件。
单击文件名,在界面的左半部会出现工件的基本参数,以及测量该工件的操作员和测量工件的时间。
打开文件,便直接进入了“测量结果”的界面,在“测量结果”界面里会显示出工件的误差曲线及各项误差值。
用户可以进入其它界面,查看当时测量工件时的所有参数的设置。