变速箱体加工过程资料
汽车变速箱箱体加工工艺及夹具设计

汽车变速箱箱体加工工艺及夹具设计
汽车变速箱箱体加工工艺:
1. 预处理:将箱体零件进行清洗、除油等处理。
2. 外观检查:进行外观检查,确认箱体零件是否存在缺陷或划痕等问题。
3. 装夹:将箱体零件放入夹具中进行装夹,确保零件不会因加工过程中移动和变形。
4. 粗加工:采用车削和铣削等工艺对箱体零件进行粗加工,以移除多余的金属材料,制作出初步形状。
5. 精加工:在粗加工完成后,进行精加工,采用平面磨或者线切割等工艺,对箱体零件进行加工,确保精度和表面质量。
6. 清洗:将加工完成的箱体零件进行清洗,清除可能存在的金属屑和油脂等。
7. 组装:将加工完成的箱体零件进行组装。
夹具设计:
1. 针对汽车变速箱箱体的形状和工艺特点,设计夹具,确保夹具能够牢固地固定零件,不会因为零件形状而导致变形和移动。
2. 考虑到加工和清洗的需要,夹具应该设计成易于拆卸和清洗的形式。
3. 使用夹具夹持箱体时,夹具表面应该保证平整和光滑,以避免对箱体表面造成损伤。
4. 对于一些需要双面加工的箱体零件,可以采用双面夹具进行
加工,以提高工作效率。
5. 在夹具的设计中应该考虑到工作人员的安全和作业的舒适性。
变速箱箱体的机械加工工艺规程
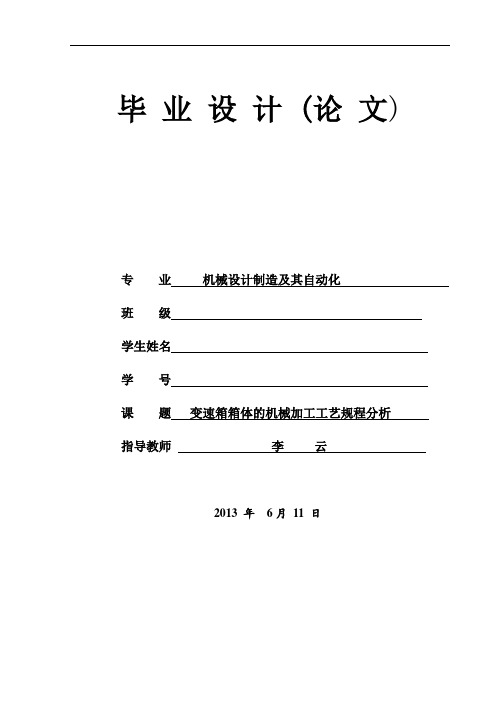
毕业设计 (论文)专业机械设计制造及其自动化班级学生姓名学号课题变速箱箱体的机械加工工艺规程分析指导教师李云2013 年6月11 日摘要本设计是某叉车变速箱箱体零件的加工工艺规程及变速箱检修及常见故障诊断。
某叉车变速箱箱体零件的主要加工表面是平面及孔系。
一般来说,保证平面的加工精度要比保证孔系的加工精度容易。
因此,本设计遵循先面后孔的原则。
并将孔与平面的加工明确划分成粗加工和精加工阶段以保证孔系加工精度。
粗基准选择顶面和两个输出轴孔为粗基准,以底面与两个定位销作为精基准。
主要加工工序安排是先以支承孔系定位加工出顶平面,再以顶平面与支承孔系定位加工出工艺孔。
在后续工序中除个别工序外均用顶平面和工艺孔定位加工其他孔系与平面。
整个加工过程均选用组合机床。
因此生产效率较高。
适用于大批量、流水线上加工,能够满足设计要求。
叉车在使用的过程中,随着行驶里程的增多和作业时间的增加,变速器工作时不停地换挡,使变速器内的齿轮和操纵机构在使用中容易振动磨损,导致机构产生发响、跳档、乱档、渗漏等故障现象,严重时影响叉车的正常使用。
常见故障有:变速器跳档、变速器乱档、变速器异响、变速器漏油等。
因此变速箱需要定期检修维护以及掌握对变速箱的常见故障诊断是很有必要的。
关键词:变速箱;箱体;加工工艺;故障AbstractThe design is about the special purpose clamping apparatus of the machining technology process and some working procedures of the car gearbox parts. The main machining surface of the car gearbox parts is the plane and a series of hole. Generally speaking, to guarantee the working accuracy of the plane is easier than to guarantee the hole’s. So the design follows the principle of plane first and hole second. And in order to guarantee the working accuracy of the series of hole, the machining of the hole and the plane is clearly divided into rough machining stage and finish machining stage. The supporting hole of the input bearing and output bearing is as the rough datum. And the top area and two technological holes are as the finish datum. The main process of machining technology is that first, the series of supporting hole fix and machine the top plane, and then the top plane and the series of supporting hole fix and machine technological hole. In the follow up working procedure, all working procedures except several special ones fix and machine other series of hole and plane by using the top plane and technological hole. The machining way of the series of supporting hole is to bore hole by coordinate. The combination machine tool and special purpose clamping apparatus are used in the whole machining process. The clamping way is to clamp by pneumatic and is very helpful. The instruction does not have to lock by itself. So the product efficiency is high. It is applicable for mass working and machining in assembly line. It can meet the design requirements.Forklift trucks in use process, along with the increase in mileage and homework time increased, the transmission constantly shift at work, make the gears inside the transmission and control mechanism in the use of easy to wear and tear, vibration lead to produce hair ring, jumping gears, gears, such as seepage failure phenomenon, serious influence the normal use of forklift truck. Common faults are: the transmission gears, transmission gears, transmission of sound, transmission oil, etc.Therefore gearbox need regular maintenance, and to grasp the common fault diagnosis of gearbox is very be necessary.Key words: Gearbox; machining technology; special purpose clamping;faults目录摘要 (1)Abstract (2)第一章绪论 (5)1.1 概论 (5)1.2 国内外发展现状 (5)1.3 课题的研究意义 (5)第二章箱体的三维建模 (7)2.1 零件的分析 (7)2.1.1 零件的作用 (7)2.1.2 零件的工艺分析 (8)2.2 孔和平面的加工顺序 (8)2.3 变速箱箱体加工定位基准的选择 (9)2.3.1 粗基准的选择 (9)2.3.2 精基准的选择 (9)2.4 变速箱箱体加工主要工序安排 (9)2.5 变速箱箱体零件的三维模拟 (12)2.5.1 模拟软件UG NX6.0简介 (12)2.5.2 箱体的模拟意义分析 (12)2.5.3箱体的三维模拟步骤 (12)第三章加工余量确定及工序尺寸计算 (15)3.1 毛坯余量 (15)3.1.1公差等级的确定 (15)3.1.2 确定机械加工余量 (15)3.1.3 确定毛坯尺寸 (15)3.2 箱体各平面加工工序余量 (17)3.3 内孔2-φ120H8加工工序余量 (17)3.4 内孔φ100H7加工工序余量 (17)3.5内孔2-φ60H7加工工序余量 (17)3.6 最终毛坯工序加工余量及公差 (18)3.8 切削用量及机械加工时间的计算 (20)3.8.1 工序10 粗铣底面及精铣底面 (20)3.8.2 工序20 钻螺栓孔4-Φ20并攻丝 (21)3.8.3 工序30 粗铣顶面与螺纹端面及工序100 精铣顶面与螺纹端面 (22)3.8.4 工序40 粗铣前后面及工序110 精铣前后面 (23)3.8.5 工序50 粗铣左右两侧面及工序120 精铣左右两侧面 (24)3.8.6 工序60粗镗、工序80半精镗、工序140精镗孔2-φ120H7 (26)3.8.7 工序70粗镗工序90半粗镗工序140精镗孔φ100H7孔2-φ60H7 .. 29 第四章叉车变速箱检修及常见故障诊断与排除 (32)4.1叉车变速箱简介、功用及分类 (32)4.2机械变速箱的检修 (32)4.3变速箱常见故障诊断与排除 (35)4.3.1 机械变速箱常见故障诊断与排除 (35)4.3.2 液力变速箱常见故障诊断与排除 (36)总结 (41)致谢 (42)参考文献 (43)附录一科技文献及翻译 (44)附录二机械工艺规程卡片及工序卡片 (59)第一章绪论1.1 概论变速箱是叉车上最重要的机械设备。
变速箱箱体的机械加工工艺规程

变速箱箱体的机械加工工艺规程变速箱是汽车传动系统的重要组成部分,它通过不同的齿轮组合来实现不同的速度和扭矩输出。
而这些齿轮的运转离不开变速箱箱体的支撑和稳定,因此变速箱箱体的加工质量直接影响着汽车的性能和安全。
本文将介绍变速箱箱体的机械加工工艺规程,包括相关的工艺流程、设备和技术要点。
一、加工流程1、检查箱体毛坯:对毛坯进行外观、尺寸和材质等检查,并根据加工图纸确定加工工艺和加工参数。
2、分号廓、开整体孔:用数控车床对毛坯进行分号廓和开整体孔的加工,确保精度和尺寸配合。
3、铣凹槽、钻螺纹孔:用数控铣床对箱体进行凹槽、倒角和螺纹孔的加工,确保精度和表面质量。
4、车平面、切倒角:用数控车床对箱体进行平面和倒角加工,确保箱体的平整和美观度。
5、排刀台、磨平面:用磨床对箱体的主体结构进行平面的磨削,确保平面精密度和表面光洁度。
6、清洗箱体、质检:对加工好的箱体进行清洗和表面处理,同时进行质量检查和尺寸配合测试。
7、装配齿轮、检验调试:按照设计图纸进行齿轮的装配,进行齿轮间的配合度和转动力的调试。
二、设备要求1、数控机床:包括数控车床、数控铣床、数控磨床等设备,用于箱体的分号廓、开孔、加工凹槽、钻孔、车平面和磨削等加工工序。
2、高压清洗机:用于对加工好的箱体进行清洗和表面处理,确保箱体干净无油污,表面质量良好。
3、品质检测设备:包括示波器、卡尺、针对性量规等检测仪器,用于对箱体质量进行检测和质量保证。
三、技术要点1、机械加工工艺:对箱体进行加工时,需要结合箱体的加工图纸和加工参数进行加工,严格按照工艺流程和技术规范进行加工,确保箱体的尺寸和精度。
2、表面处理:对箱体进行表面处理时,需要选择合适的清洗剂和表面处理剂,同时注意处理时的温度和时间,确保箱体表面光洁度和质量。
3、质量检查:对加工好的箱体进行质量检查时,需要结合检测仪器和装配情况进行测试,其中重点检查加工尺寸和配合度,以确保产品质量。
综上所述,变速箱箱体的机械加工工艺规程是汽车传动系统中非常重要的一环,它直接影响着汽车的性能和安全。
变速箱体的制备方法
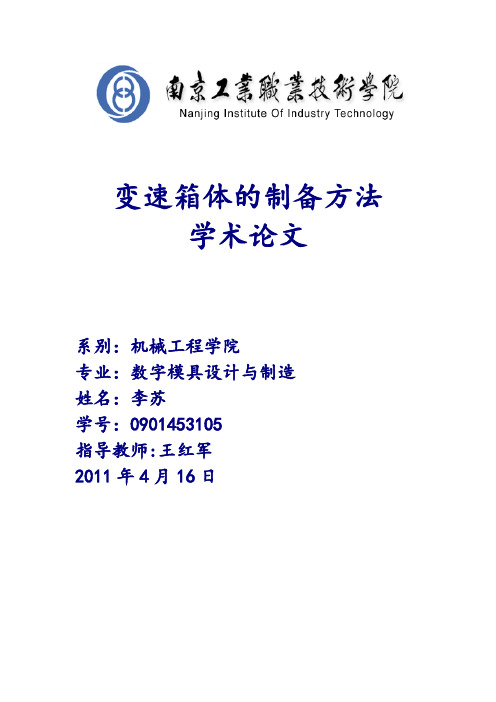
变速箱体的制备方法学术论文系别:机械工程学院专业:数字模具设计与制造姓名:李苏学号:0901453105指导教师:王红军2011年4月16日目录1.……………变速箱的制造流程2.…………各种类型变速箱的三维图3.……………工程图及结构原理图4.…………手动变速箱的工作原理一、变速箱的制造流程1.铸造铸造是将熔化的金属浇灌入铸型空腔中,冷却凝固后而获得产品的生产方法。
在汽车制造过程中,采用铸铁制成毛坯的零件很多,约占全车重量10%左右,变速器箱体。
制造铸铁件通常采用砂型。
砂型的原料以砂子为主,并与粘结剂、水等混合而成。
砂型材料必须具有一定的粘合强度,以便被塑成所需的形状并能抵御高温铁水的冲刷而不会崩塌。
为了在砂型内塑成与铸件形状相符的空腔,必须先用木材制成模型,称为木模。
炽热的铁水冷却后体积会缩小,因此,木模的尺寸需要在铸件原尺寸的基础上按收缩率加大,需要切削加工的表面相应加厚。
空心的铸件需要制成砂芯子和相应的芯子木模(芯盒)。
有了木模,就可以翻制空腔砂型(铸造也称为“翻砂”)。
在制造砂型时,要考虑上下砂箱怎样分开才能把木模取出,还要考虑铁水从什么地方流入,怎样灌满空腔以便得到优质的铸件。
砂型制成后,就可以浇注,也就是将铁水灌入砂型的空腔中。
浇注时,铁水温度在1250—1350度,熔炼时温度更高。
2.锻造在汽车制造过程中,广泛地采用锻造的加工方法。
锻造分为自由锻造和模型锻造。
自由锻造是将金属坯料放在铁砧上承受冲击或压力而成形的加工方法(坊间称“打铁”)。
汽车的齿轮和轴等的毛坯就是用自由锻造的方法加工。
模型锻造是将金属坯料放在锻模的模膛内,承受冲击或压力而成形的加工方法。
模型锻造有点像面团在模子内被压成饼干形状的过程。
与自由锻相比,模锻所制造的工件形状更复杂,尺寸更精确。
汽车的模锻件的典型例子是:发动机连杆和曲轴、汽车前轴、转向节等。
3.冷冲压冷冲压或板料冲压是使金属板料在冲模中承受压力而被切离或成形的加工方法。
变速箱箱体工艺流程工序
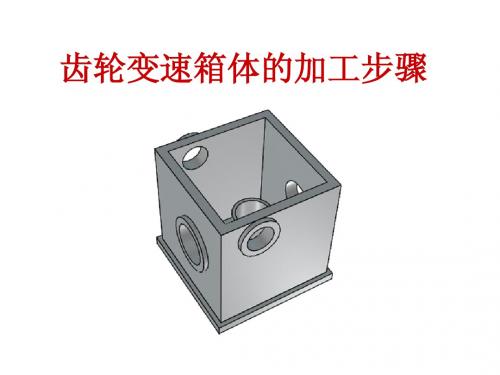
加 工 简 图 三
加 工 步 骤
பைடு நூலகம்
3.在花盘上装上角铁和导向板,通过插入主轴孔的测量棒用游标高度 尺或量块调整好角铁平面至主轴中心的距离为(123±0.05)mm,然后将 φ30mm测量棒紧密配合进底孔中,将箱体放在角铁上,并以底面及箱 体侧面定位块为基准,测量两个测量棒的中心距为(55±0.05)mm, 测好后紧固角铁,取下主轴测量棒及φ30mm的测量棒
+ (1)加工φ300 0.03 mm同轴孔及一侧凸台端面 (2)将工件掉头装夹,车另一侧凸台端面
加 工 简 图 四
加 工 步 骤
4.按照上一步的方法,将角铁底面与主轴中心调整到81mm(12342),再将底孔中心线与主轴中心线调整到(40±0.05)mm,固 定角铁,取下主轴测量棒及φ30mm测量棒
+ (1)车φ45 0 0.039 mm同轴孔及一侧端面
(2)将工件掉头装夹,车另一侧端面
齿轮变速箱体的加工步骤
加 工 简 图 一
135
加 工 步 骤
1.以箱体底面为基准面,用四爪单动卡盘夹住工件
车顶面,控制箱体的内腔深度135mm
加 工 简 图 二
145
2.以箱体顶面为基准面,用四爪单动卡盘夹住工件,找正 加 工 步 骤
(1)钻底孔φ27mm (2)车底孔φ30mm (3)车底面,控制箱体全高145mm (4)车止口φ45mm
变速箱体的机械加工工艺规程及专用夹具设计与制作

湖南工贸技师学院技师论文案例报告题目:设计“变速箱体”零件的机械加工工艺规程及相关工序的专用夹具内容:1.零件图一张2.毛坯图一张3.机械加工工艺过程综合卡片一张(或机械加工工艺规程卡片一套)4.夹具装配图一张5.夹具体零件图一张6.课程设计说明书一份原始资料:该零件图样,Q=20000台/年,n=1件/台,每日1班班级学号:9 号学生:吕沛思指导教师:张璐青系(教研室)主任:王定勇变速箱体的工艺与夹具的设计与制作湖南工贸技师学院吕沛思摘要:本文对变速箱体的加工难点、生产类型进行了分析,针对零件的结构特点进行毛坯设计、对其工艺过程进行了设计。
为提高生产效率,设计了铣削窄槽夹具,对其它箱体零件的加工有一定的借鉴意文。
关键词:变速箱工艺夹具设计一、分析零件图纸并确定其生产类型1.零件的作用变速箱体的材料HT200,是减速箱的重要零件(见图立体1-1及零件图1-2),其主要作用是:①、起支承作用,并在此基础上安装轴类零件及轴上零件。
②、利用它们的工艺结构起到其他重要零件的定位作用。
③、用以连接机器设备与地面的基础零件。
图1-1 变速箱体立体图2.零件的结构分析该零件是属于箱体零件,通过对该零件图的重新绘制,对零件有些深入的了解。
此零件为典型的箱体类零件,并不是所有的表面和轮廓都要加工,除几个轴承孔外,其他部分加工精度要求不高,都比较容易获得。
主要保证好输入轴与输出轴孔的精度以及两个面的位置度。
此零件的工艺路线完全按照:先面后孔,先粗后精,先主后次,基准先行的一般工艺原则所进行的。
其设计基准与装配基准为底平面,所以应先将其加工完成。
两侧面与轴承孔的中心线有垂直度的要求,但是精度要求并不是特别高,容易保证形位公差要求。
此零件孔较多,但大部是小螺丝孔,只要能满足装配即可。
考虑到加工该零件所需要刀具繁多,而且为大批量生产,所以选在数控立式和卧式加工中心上完成加工。
因此要设计专用夹具,其后有根据工艺路线专门设计的夹具具体分析。
变速箱体加工工艺过程
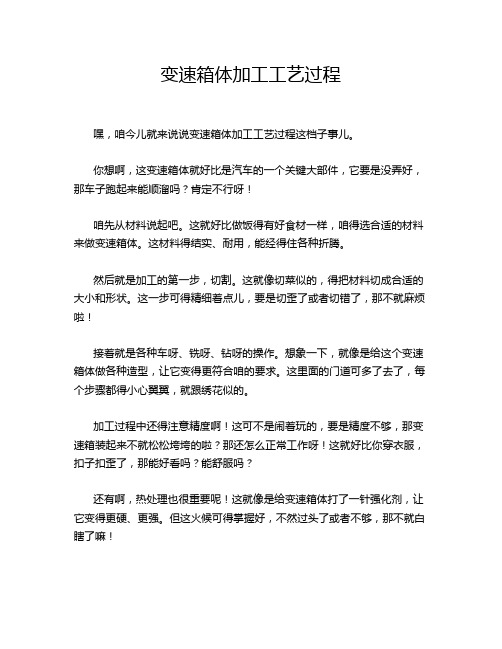
变速箱体加工工艺过程
嘿,咱今儿就来说说变速箱体加工工艺过程这档子事儿。
你想啊,这变速箱体就好比是汽车的一个关键大部件,它要是没弄好,那车子跑起来能顺溜吗?肯定不行呀!
咱先从材料说起吧。
这就好比做饭得有好食材一样,咱得选合适的材料来做变速箱体。
这材料得结实、耐用,能经得住各种折腾。
然后就是加工的第一步,切割。
这就像切菜似的,得把材料切成合适的大小和形状。
这一步可得精细着点儿,要是切歪了或者切错了,那不就麻烦啦!
接着就是各种车呀、铣呀、钻呀的操作。
想象一下,就像是给这个变速箱体做各种造型,让它变得更符合咱的要求。
这里面的门道可多了去了,每个步骤都得小心翼翼,就跟绣花似的。
加工过程中还得注意精度啊!这可不是闹着玩的,要是精度不够,那变速箱装起来不就松松垮垮的啦?那还怎么正常工作呀!这就好比你穿衣服,扣子扣歪了,那能好看吗?能舒服吗?
还有啊,热处理也很重要呢!这就像是给变速箱体打了一针强化剂,让它变得更硬、更强。
但这火候可得掌握好,不然过头了或者不够,那不就白瞎了嘛!
在整个加工过程中,每一个环节都不能马虎。
就好像盖房子,一块砖没砌好,可能整座房子都不稳。
咱得认真对待每一个细节,把这个变速箱体加工得漂漂亮亮、结结实实的。
最后组装起来,嘿,一个完美的变速箱体就诞生啦!它能让车子跑得稳稳当当,顺顺利利的。
你说这变速箱体加工工艺过程是不是特别神奇?特别重要?咱可不能小瞧了它呀!它可是汽车能好好跑起来的关键之一呢!所以啊,那些搞变速箱体加工的师傅们,真的是太厉害啦,他们就像魔法师一样,能把那些原材料变成这么重要的部件。
咱得给他们点个大大的赞!。
汽车变速箱体加工工艺及夹具设计
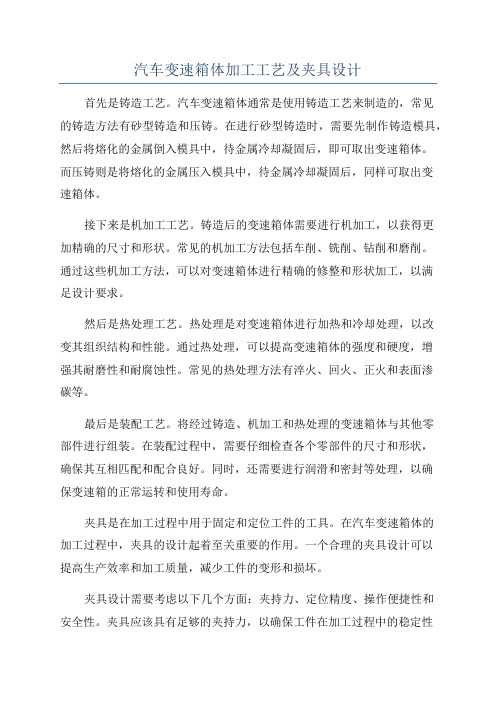
汽车变速箱体加工工艺及夹具设计首先是铸造工艺。
汽车变速箱体通常是使用铸造工艺来制造的,常见的铸造方法有砂型铸造和压铸。
在进行砂型铸造时,需要先制作铸造模具,然后将熔化的金属倒入模具中,待金属冷却凝固后,即可取出变速箱体。
而压铸则是将熔化的金属压入模具中,待金属冷却凝固后,同样可取出变速箱体。
接下来是机加工工艺。
铸造后的变速箱体需要进行机加工,以获得更加精确的尺寸和形状。
常见的机加工方法包括车削、铣削、钻削和磨削。
通过这些机加工方法,可以对变速箱体进行精确的修整和形状加工,以满足设计要求。
然后是热处理工艺。
热处理是对变速箱体进行加热和冷却处理,以改变其组织结构和性能。
通过热处理,可以提高变速箱体的强度和硬度,增强其耐磨性和耐腐蚀性。
常见的热处理方法有淬火、回火、正火和表面渗碳等。
最后是装配工艺。
将经过铸造、机加工和热处理的变速箱体与其他零部件进行组装。
在装配过程中,需要仔细检查各个零部件的尺寸和形状,确保其互相匹配和配合良好。
同时,还需要进行润滑和密封等处理,以确保变速箱的正常运转和使用寿命。
夹具是在加工过程中用于固定和定位工件的工具。
在汽车变速箱体的加工过程中,夹具的设计起着至关重要的作用。
一个合理的夹具设计可以提高生产效率和加工质量,减少工件的变形和损坏。
夹具设计需要考虑以下几个方面:夹持力、定位精度、操作便捷性和安全性。
夹具应该具有足够的夹持力,以确保工件在加工过程中的稳定性和精确性。
同时,夹具还应具有良好的定位精度,以确保工件的正确位置和形状。
操作便捷性是指夹具的设计应该简单易用,方便操作人员进行装夹和取卸工件。
同时,夹具还应具有良好的安全性,以避免意外事故的发生。
在夹具设计中,需要根据变速箱体的形状和尺寸,选择适当的夹具类型和夹持方式。
常见的夹具类型有平行夹具、三爪夹具和冲击夹具等。
同时,还需要考虑夹具的刚度和稳定性,以确保夹具在加工过程中不产生松动和变形。
总之,汽车变速箱体加工工艺和夹具设计是汽车制造中不可或缺的环节。
变速器箱体加工工艺规程及其工艺卡设计

题目变速器下箱体加工工艺规程学生姓名李勇专业班级机械设计制造及其自动化1班学号2220122173指导教师连峰完成时间2015年7 月23日目录一制定箱体加工工艺规程的原始材料 (1)1零件工作图和必要的装配图 (1)2零件的生产纲领和生产类型 (1)3毛坯的生产条件和供应条件 (1)4本厂的生产条件 (1)5各有关手册、标准和指导性文件 (1)二减速器箱体加工工艺规程的步骤和内容......... 错误!未定义书签。
1阅读装配图和零件图......................... 错误!未定义书签。
2工艺审查 (9)3熟悉和确定毛坯.............................. 错误!未定义书签。
4拟定机械加工工艺路线 (10)4.1加工方法的选择 (10)4.2定位基准 (9)4.3工序顺序的安排 (10)4.4热处理工序的安排 (10)4.5辅助工序的安排 (10)5确定工艺设备() (12)5.1选择机床 (12)5.2选择量具5.3选择夹具5.4选择刀具 (12)5.5专用机床设计任务书5.6确定加工工艺路线6确定技术要求和检验方法7确定加工余量、计算工序尺寸和公差8确定切削用量................................ 错误!未定义书签。
8.1粗、精铣切削用量......................... 错误!未定义书签。
8.2钻削加工切削用量的选择................... 错误!未定义书签。
8.3基本时间的确定 (16)9确定时间定额10填写工艺文件减速器成品图一制定箱体加工工艺规程的原始材料1零件工作图和必要的装配图2零件的生产纲领和生产类型大批量3毛坯的生产条件和供应条件4本厂的生产条件5各有关手册、标准和指导性文件1 减速器实用技术手册编辑委员会编. 《减速器实用技术手册》北京:机械工业出版社, 19922 冯辛安主编.《机械制造装备设计》第2版大连理工大学北京:机械工业出版社, 2007.123 黄如林主编.《切削加工简明实用手册》北京:化学工业出版社,2004.74 戴曙主编. 《金属切削机床》北京:机械工业出版社, 2005.15冯之敬主编《机械制造工程原理》清华大学出版社,2008.66邢闽芳主编《互换性与技术测量》清华大学出版社,2007.4二减速器箱体加工工艺规程的步骤和内容1阅读装配图和零件图零件主视图零件左视图及局部视图2工艺审查减速器的主要加工表面为孔系和平面,为了保证箱体部件的装配精度,对箱体零件的加工,主要有如下技术要求:支承孔的尺寸精度、形状精度和表面粗糙度箱体上的主要支承孔(主轴孔)尺寸公差等级为IT6级,圆度为0.006~0.008mm,表面粗糙度值为Ra0.4~0.8um.其他支承孔的尺寸公差等级为IT6~IT7级,圆度为0.01mm左右,表面粗糙度值为Ra1.6~3.2um。
变速箱箱体零件的加工工艺规程及专用夹具设计说明书

摘要在整个毕业设计过程中,综合应用工程图学,机械设计、机械制造工艺学、机械几何精度设计等相关理论知识。
本设计为变速箱箱体零件的加工工艺规程及专用夹具设计。
在工艺规程设计过程中,详细分析箱体零件的技术要求,变速箱箱体的主要加工表面是平面及孔系,一般来说保证平面的加工精度要比保证孔系的加工精度容易,因此,本设计遵循先面后孔的原则,并明确划分粗、精加工阶段。
在进行镗孔专用夹具设计中,阐述了定位方案的选择、夹紧机构的设计、镗模主要零件设计,运用AutoCAD完成此专用夹具的装配图和夹具零件图。
关键词:变速箱;加工工艺;夹具设计;第一章零件的工艺分析及生产类型的确定ABSTRACTIn the whole process of graduation design, the comprehensive application engineering graphics, mechanical design,mechanical manufacturing technology, mechanical geometry precision design and related theory knowledge. This design for gear-box parts processing procedure and special fixture design. In process planning process, a detailed analysis of the technical requirements of the case accessories, gear-box main processing surface is flat and hole department, generally guarantee machining precision of the plane than guarantee hole machining precision of the department, therefore, this design to follow the principle of after make face first, and clearly hole diameter, finishing stage division. Special fixture design in boring, expounds the positioning of the choice, clamping mechanism design, boring major parts design, mould using AutoCAD complete this special jig's drawings and fixture detail drawings.Keywords: transmission; Processing craft; Fixture design;第一章零件的工艺分析及生产类型的确定1.1零件的分析箱体类零件时机器及其部件的基础件,变速箱箱体的主要作用是支撑各传动轴、轴承、套、和齿轮,并且保证各轴几间的中心距及平行度,按规定的传动关系变速并协调地运动。
设计“变速箱体”零件的机械加工工艺规程及指定夹具设计

设计“变速箱体”零件的机械加工工艺规程及指定夹具设计引言变速箱体是汽车传动系统中的关键部件,其加工精度直接影响到整车的性能和可靠性。
本文旨在介绍变速箱体零件的机械加工工艺规程以及相应的夹具设计。
第一章:变速箱体零件概述1.1 变速箱体的功能变速箱体是安装和支撑变速箱内部零件的壳体。
它需要具备足够的强度和刚性,以承受传动过程中的力。
1.2 变速箱体的材料通常采用高强度铸铁或铝合金材料。
1.3 变速箱体的结构特点结构复杂,包含多个孔、槽和凸台等特征。
第二章:机械加工工艺规程2.1 加工工艺流程铸造或锻造:根据材料特性选择合适的成型工艺。
粗加工:去除多余的材料,形成接近最终尺寸的毛坯。
半精加工:进一步加工,确保尺寸精度。
精加工:达到设计图纸要求的精度和表面粗糙度。
检验:对加工后的零件进行尺寸和外观检验。
2.2 关键加工步骤铣削:用于加工平面和凹槽。
钻孔:用于加工通孔和盲孔。
镗孔:用于加工内孔,确保孔的尺寸和位置精度。
磨削:用于提高表面质量和尺寸精度。
2.3 加工参数选择合适的切削速度、进给速度和切削深度。
2.4 加工质量控制定期对加工设备进行校准和维护。
采用在线或离线检测方法,确保加工质量。
第三章:夹具设计3.1 夹具设计原则确保夹具的稳定性和可靠性。
便于操作,提高加工效率。
能够适应不同的加工工序。
3.2 夹具类型固定夹具:用于固定零件,防止加工过程中的移动。
可调夹具:可以根据零件尺寸进行调整。
专用夹具:针对特定零件设计的夹具。
3.3 夹具设计要点定位:确保零件在夹具中的位置准确。
夹紧:提供足够的夹紧力,防止加工过程中的振动。
操作性:夹具应易于操作,方便工人使用。
3.4 夹具材料选择根据夹具的负载和使用环境选择合适的材料。
第四章:工艺规程的实施与优化4.1 工艺规程的制定根据变速箱体的设计要求和加工特点,制定详细的工艺规程。
4.2 工艺规程的实施组织培训,确保操作人员熟悉工艺规程。
制定操作手册,指导日常加工工作。
变速箱体加工工艺研究方法及过程
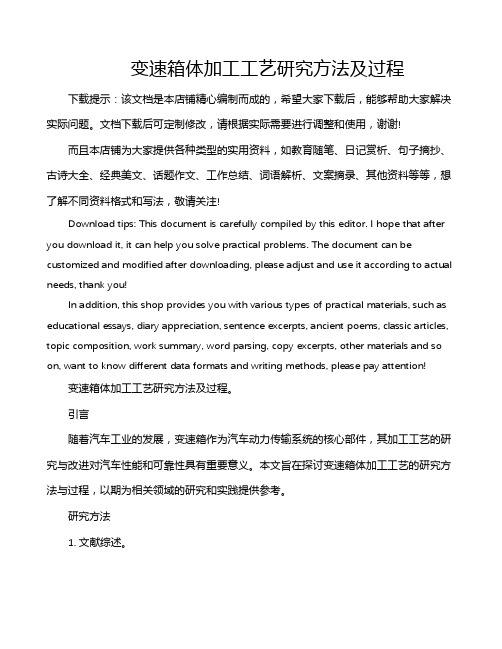
变速箱体加工工艺研究方法及过程下载提示:该文档是本店铺精心编制而成的,希望大家下载后,能够帮助大家解决实际问题。
文档下载后可定制修改,请根据实际需要进行调整和使用,谢谢!而且本店铺为大家提供各种类型的实用资料,如教育随笔、日记赏析、句子摘抄、古诗大全、经典美文、话题作文、工作总结、词语解析、文案摘录、其他资料等等,想了解不同资料格式和写法,敬请关注!Download tips: This document is carefully compiled by this editor. I hope that after you download it, it can help you solve practical problems. The document can be customized and modified after downloading, please adjust and use it according to actual needs, thank you!In addition, this shop provides you with various types of practical materials, such as educational essays, diary appreciation, sentence excerpts, ancient poems, classic articles, topic composition, work summary, word parsing, copy excerpts, other materials and so on, want to know different data formats and writing methods, please pay attention!变速箱体加工工艺研究方法及过程。
引言随着汽车工业的发展,变速箱作为汽车动力传输系统的核心部件,其加工工艺的研究与改进对汽车性能和可靠性具有重要意义。
变速器下箱体加工工艺规程

变速器下箱体加工工艺规程1. 引言本文档旨在描述变速器下箱体的加工工艺规程,为加工人员提供详细的操作指南和工艺要求。
变速器下箱体是变速器的重要组成部分,其制作质量直接影响到变速器的性能和可靠性。
因此,正确的加工工艺是保证变速器下箱体质量的关键。
2. 加工工艺流程2.1 设计和准备工作在进行下箱体加工之前,需要进行以下准备工作:1.查阅变速器下箱体的详细设计图纸,了解箱体的结构和尺寸要求。
2.准备好所需的原材料,包括合适的金属板材和零部件。
3.准备好所需的加工设备和工具,如剪板机、冲床、焊接机等。
2.2 材料切割根据设计图纸上的尺寸要求,使用剪板机或激光切割机对金属板材进行切割。
注意要准确控制切割尺寸,并保证切割边缘的平整度。
2.3 零部件加工根据设计要求,对下箱体的各个零部件进行加工。
具体步骤如下:1.按照图纸上的尺寸要求,使用冲床对盖板和底板进行冲孔处理。
2.按照图纸上的示意图,使用加工设备和工具对各个零部件进行弯曲、铆接或冲压等加工操作。
3.对连接件进行加工,确保连接的可靠性和紧密度。
2.4 焊接和固定根据设计要求,对下箱体的各个零部件进行焊接和固定。
具体步骤如下:1.对需要焊接的零部件进行表面处理,确保焊接质量。
2.使用适当的焊接方法和设备,进行焊接操作。
注意要控制好焊接温度和时间,避免过热或过焊。
3.检查焊接接头的质量,确保连接的牢固和密封性。
2.5 表面处理完成下箱体的加工后,进行表面处理,以保证箱体的美观和耐腐蚀性。
具体步骤如下:1.对下箱体进行除锈、打磨和清洗等表面处理操作。
2.在表面处理完成后,使用喷涂或电镀等方法,对下箱体进行涂装或镀铬等处理。
2.6 组装和检验完成下箱体的加工和表面处理后,进行组装和检验。
具体步骤如下:1.根据设计要求,对各个零部件进行组装。
注意要确保各个零部件的匹配度和连接的可靠性。
2.进行箱体的整体检验,并进行功能性测试,以验证箱体的性能和可靠性。
3.对检验结果进行记录和汇总,以备后续工艺改进和质量控制。
汽车变速箱体加工工艺及夹具设计

汽车变速箱体加工工艺及夹具设计一、零件的分析1.零件的作用题目给出的零件是汽车变速箱体。
变速箱箱体的要紧作用是支承各传动轴,保证各轴之间的中心距及平行度,并保证变速箱部件与发动机正确安装。
〔因此:变速箱体在整个变速器的组成中的功用是保证其他各个部件合理正正确的位置,使之有一个协调运动的根底构件。
〕因此汽车变速箱箱体零件的加工质量,不但直截了当碍事汽车变速箱的装配精度和运动精度,而且还会碍事汽车的工作精度、使用性能和寿命。
汽车变速箱要紧是实现汽车的变速,改变汽车的运动速度。
以适应各种不同的路面。
变速箱是由齿轮,齿轮轴和变速器箱体等零件构成。
变速箱是一个典型的箱体零件,其外形复杂,壁薄,需要加工多个平面,孔系和螺纹孔,刚度低,受力和热变形等因素碍事产生变形和震动。
2.零件的工艺分析由汽车变速箱箱体零件图可知。
汽车变速箱箱体是一个簿壁壳体零件,它的外外表上有六个平面需要进行加工。
支承孔系在左右端面上。
此外各外表上还需加工一系列螺纹孔。
因此可将其分为三组加工外表。
它们相互间有一定的位置要求。
现分析如下:〔1〕以顶面为要紧加工外表的加工面。
这一组加工外表包括:顶面T3的铣削加工;6×M8的螺孔加工;2×φ10的工艺孔〔定位销孔〕加工。
其中顶面T3有外表粗糙度要求为Ra3.2μm,6个M8×1.25-2螺孔均有位置度要求为0.15mm,端部倒角45°至螺纹深度。
〔2〕以φ85、φ94、φ72mm的支承孔为要紧加工外表的加工外表。
这一组加工外表包括:1个φ85mm孔、1个φ94mm孔、和两个φ72的孔;尺寸为218±0.2mm与φ85、φ94、2个φ72mm孔轴线相垂直的左右端面〔T1、T2〕。
在T1外表上4各M12x1.75-2的螺孔,φ25孔及R8孔的加工,其中φ25孔的位置精度:±mm的螺纹孔。
其中:4个孔有粗糙度要求Ra1.6mm及端面45°倒角要求。
变速器加工工艺知识-壳体、轴、齿轮
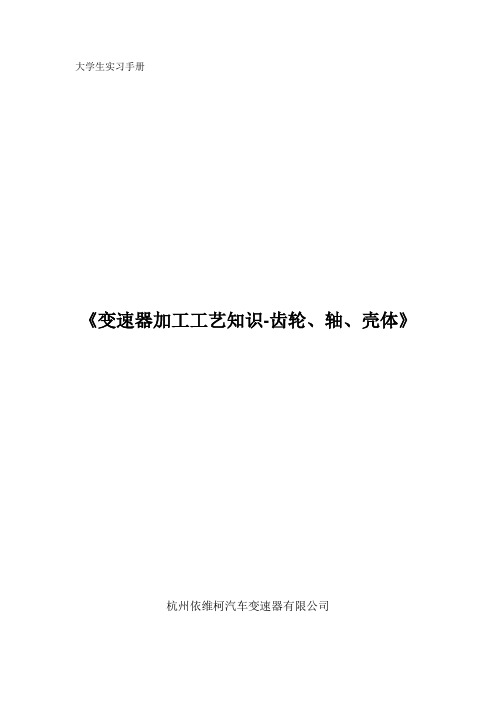
大学生实习手册《变速器加工工艺知识-齿轮、轴、壳体》杭州依维柯汽车变速器有限公司现状描述:目前,我公司生产的汽车变速器主要是采用手动换挡型式,匹配发动机排量为0.8-1.8L,搭载于经济型轿车上。
随着近今年的发展,逐步往自动换档型发展。
变速器主要涉及核心零件轴及齿轮、壳体的生产、总成装配、试验检测等过程在公司内进行。
第一部分:齿轮、轴类零件1.齿轮工艺流程简介:齿轮一般有两种结构:根据不同结构要求.齿轮零件加工主要工艺流程采用的是锻造制坯→正火→精车加工→插齿→倒尖角→滚齿→剃齿→(焊接)→热处理→磨加工→对啮修整。
热后齿部一般不再加工,除了主减从齿或顾客要求磨齿的零件。
2.轴类工艺流程简介:输入轴:锻造制坯→正火→精车加工→搓齿→钻孔→插齿→倒尖角→滚齿→剃齿→热处理→磨加工→对啮修整。
输出轴:锻造制坯→正火→精车加工→搓齿滚齿→剃齿→热处理→磨加工→对啮修整。
3.具体工艺流程简介:详细介绍如下:(1)锻造制坯:热模锻是汽车齿轮件广泛使用的毛坯锻造工艺。
以前较广泛采用的是热锻和冷挤压的毛坯,近年来,楔横轧技术在轴类加工上得到了大量推广。
这项技术特别适合为比较复杂的阶梯轴类制坯,它不仅精度较高、后序加工余量小而且生产效率高。
比如我公司生产的H331.6A及H319.5A的轴类毛坯就是采用楔横轧,现在已逐步实现了批量生产。
(2)正火:这一工艺的目的是获得适合后序齿轮切削加工的硬度和为最终热处理做组织准备,以有效地减少热处理变形。
公司所用齿轮钢的材料通常为20CrMnTi(H)及20MnCr5,一般的正火由于受人员、设备和环境的影响比较大,使得工件冷却速度和冷却的均匀性难以控制,造成硬度散差大,金相组织不均匀,直接影响机加工和最终热处理;使得热变形大而无规律,零件质量无法控制,对刀具的磨损也较大,尤其对搓齿这种受力大的工序更是明显。
为此,采用等温正火工艺。
实践证明,采用这种等温正火有效地改变了一般正火的弊端,产品质量稳定可靠。
汽车变速箱箱体加工工艺及夹具设计

1汽车变速箱加工工艺规程设计1.1零件的分析1.1.1零件的作用题LI给出的零件是汽车变速箱箱体。
变速箱箱体的主要作用是支承各传动轴,保证各轴之间的中心距及平行度,并保证变速箱部件与发动机正确安装。
因此汽车变速箱箱体零件的加丄质量,不但直接影响汽车变速箱的装配精度和运动精度,而且还会影响汽车的工作精度、使用性能和寿命。
汽车变速箱主要是实现汽车的变速,改变汽车的运动速度。
汽车变速箱箱体零件的顶面用以安装变速箱盖,前后端面支承孔020〃〃”、080〃""用以安装传动轴,实现其变速功能。
1.1.2零件的工艺分析山汽车变速箱箱体零件图可知。
汽车变速箱箱体是一个簿壁壳体零件,它的外表面上有五个平面需要进行加工。
支承孔系在前后端面上。
此外各表面上还需加工一系列螺纹孔。
因此可将其分为三组加工表面。
它们相互间有一定的位置要求。
现分析如下:(1)、以顶面为主要加工表面的加工面。
这一组加工表面包括:顶面的铳削加工;8xM10-6H的螺孔加工;2“12也°27讪的工艺孔加工。
其中顶面有表面粗糙度要求为凡63“〃,8个螺孔均有位置度要求为旅).3〃初,2个工艺孔也有位置度要求为^0. bum。
⑵、以0120也巴巾”、08()4叫加、^10044,035wwi的支承孔为主要加工表面的加工面。
这一组加工表面包括:2个>2个和1个0100乜叫沏的孔;尺寸为365± 0.025mm的与2x0120“°加”、2x^80+O0,3nw;7 的4个孔轴线相垂直的前后端面;前后端面上的3个M14-6H、16个MW-6H的螺孔,以及4个(f)\ 5mm、2个的孑L;还有刃外两个在同一中心线上与两端面相垂直的030= 囂〃皿的倒车齿轮轴孔及其内端面和两个MIO-6H的螺孔。
其中询后端面有表面粗糙度要求为屁63“”,3个M14-6H、16个M10-6H的螺孔,4个015加加、2个她讪的孔均有位置度要求为如.3〃〃“,两倒车齿轮轴孔内端面有尺寸要求为及表面粗糙度要求为Ra3.2pn。
- 1、下载文档前请自行甄别文档内容的完整性,平台不提供额外的编辑、内容补充、找答案等附加服务。
- 2、"仅部分预览"的文档,不可在线预览部分如存在完整性等问题,可反馈申请退款(可完整预览的文档不适用该条件!)。
- 3、如文档侵犯您的权益,请联系客服反馈,我们会尽快为您处理(人工客服工作时间:9:00-18:30)。
吏速箱箱体的机械加工工艺过程变速箱箱体机械加工生产线的安排是先面后孔的原则,最后加螺纹孔。
这样安排,可以首先把铸件毛坯的气孔、砂眼、裂纹等缺陷在加工平面时暴露出来,以减少不必要的工时消耗。
此外,以平面为定位基准加工内孔可以保证孔与平面、孔与孔之间的相对位置袂度。
蛛纹预孔攻丝安排在生产线后段工序加工,能缩短工件油送距离,防止主要输送表面拉伤。
变速箱箱体的机械加工工艺过程基本上分三个阶段,即粗加工、半精加工和精加工阶段。
从毛坯的粗铣至成品的最终检验共33道工序。
其主要加工工序如表3.2.1a五、变速箱箱体加工工艺过程分析及典型夹具1.定位基准的选择。
变速箱箱体粗基准的选择有两种方式。
其一,为了 保证主要轴承孔的加工余量均匀,箱体内零件间有足够的装配间隙,以轴承孔作为粗基 准。
此方式夹具结构复杂,零件定位后需加辅助支承,工件稳定性较差。
CAIfIC 变速箱箱 体就是以轴承孔作为粗基准的。
其二,是在变速箱箱体的毛坯上铸出作为粗基准的工艺凸 台,为此要求工艺凸台至主要工作表面的毛坯面保持严格的尺寸和公差 丄F06S 带同步器变速箱箱体ZU2-Q 蛋式J .3.1的粗基准就选用此方式,如图323所示。
这种粗基准选择可保证主要加工平面及轴承孔有足够的加工余量•并使加工余量均匀,工件定位稳定。
精基准选择是上盖联接平面和两个工艺孔。
此方案可使夹具结构简单、装夹工件方便可靠.适于自动线大t流水生产。
可以满足螺纹联接孔的技术要求。
但设计基准和工艺基准不重合,箱体前、后端面对轴承孔垂直度的精度不易保证。
CALOC 变速箱箱体的两个工艺孔安排在箱体的对角线上,对角线的长短影响定位精度。
LFi)55带同步器变速箱箱体的两个工艺孔安排在箱体的同一侧上,这既可满足定位精度,又可使夹具结构简单、调整容易。
如图324所示。
工艺基准为两个"12*g918,中心距为〔3fi7 t}.US)二的孑L,而装配用的基准定位环孔为两个$13级罗mm fL,二者不能互代,因生产线较长,经多次装夹,定位精度下降或丧失。
定位环孔长度仅有5二,从产品的结构上也不允许将装配其准孔作为工尹孔用。
以一面两销作为精基准,不适合于中小批量多品种的生产。
目前先进国家已采用柔性生产线来加工变速箱箱体,用铣削过的平面作为精基准,这祥改换品种容易,便生严线更具有灵活性。
2.关键工序及典型夹具。
关键工序及典型夹具分述如下①变速箱箱体上盖接合面:铣削变速箱箱体上盖接合面安排在第一道工图j.u粗革it去揮】4想一特件毛毎凸音序,作为后面工序加工的精基准CA 15 变速箱箱体此工序加工,选用50 年代苏联产的532/73转盘式铣床。
一个主轴箱上安装粗铣、半精铣两个铁头,工作台为回转式。
主切削参数:粗铣端铣刀转速。
二9D r / min ,半精铣端铁刀转速。
=iao:/rain,走刀量f = b30 mm / min ,粗铣加工余量为5 mm半精铣的加工余量为0.5二。
以轴承孔为定位基准(见图3.2.5)。
用单轨吊将工件吊装在夹具上,锥顶尖将i4l, B 轴承孔。
该平面的技术要求:平面度公差为0.1。
,表面粗糙度为R,3.2hem,加工余量为5.。
EH3.2.i5 GUS雯速掐肅样悦構上平面工艺总图顶紧,锥顶尖顶紧A轴承孔。
这种方法零件夹持稳定性不好,只能保证平面度公差0.15,,表面粗糙度R.6.3 gym,达不到设计要求。
LFE15S带同步器变速箱箱体的此2序采用卧式双铣头双工位移动工作台式组合机床。
作为第一道工序,上料方式采用单轨吊,起重点为轴承孔。
该方法零件定位稳定,起吊灵活方便。
在半精铣前降低夹紧力,以消除粗铣时因夹紧力过大造成的工件变形,并且工件的内应力也可得到瞬时释放与平衡。
粗铣端铣刀选用机夹密齿铣刀,用以切除铸件毛坯余童。
半精铣也选用机夹密齿铣刀,上有修光刀齿。
表面粗糙度可达}, 3.2 }m o由于半精铣切削余量较小,可减少热变形。
主要切削参数:粗铣端铣刀转速n=50 r/rnin,半精铣端铣刀转速n二100 r/min.粗铣切削速度v = fit . 83 m/min , 半精铣切削速度。
=125.65 m/min,粗铁切削深度。
,}3 一5 mm半精帆切削深度OPT。
. 5 mm o 图3.2.6为其夹具结构原理图。
将工件吊至2,3.4支承板上,手动将工件推向前并向左,使工件工艺凸台紧靠支承板前面及左面,油缸7辅助顶紧工件,压板1,5在油缸9,10作用下夹紧工件,完成工件的安装。
田3」衍夹具站构烈理陌—冥鬻览陽袁舉硯;$卫一竟策因模善*USI舁一笹肆戎鶯績口3,10—'②工艺孔的加工:基准面的平面度、定位销孔的尺寸精度及定位销孔对基准平面的垂直度影响着变速箱箱体的定位精度。
CAjS.变速箱箱体定位销孔的加工设备为立式单面多轴钻孔组合机, 活动式钻模板,高速钢复合钻饺刀具。
由于受复合钻头的引导结构限制,钻头和铰刀连接部分刚性非常差,切削时易产生弯曲变形。
钻孔时钻头的引导在铰刀上,导向部位距工件较远,易引偏,铰孔不能修正这些位置误差。
定位销孔尺寸的加工精度为1'I'8 ,位置公差为土0.U8二。
主要切削参数:切削速度。
= 9 .5 m/nun ,走刀量f 二0.3 mm/r ,转速n = 252 rlmin 。
此切削参数钻孔时切削速度偏低,而铰孔时切削速度又偏高,切削参数未尽合理。
LF()bS 带同步器变速箱箱体工艺孔的加工设备是卧式单面移动工作台式三工位组合机床,固定式钻模板。
第一工位钻中心孔,第二工位钻孔} ii. s }, 第三工位铰孔声12十吕.}18} 。
钻中心孔可以保证定位销孔的位篮尺寸(36} } D.os) ,二、三工位最后保证定位销孔的尺寸精度。
这种工艺方法消除了复合钻铰刀加工定位销孔的弊病。
③轴承孔的精挺加工:CA15 变速箱箱体轴承孔的加工设备为双面卧式组合机床,采用惶模架结构。
轴承孔的尺寸精度、水平和垂直两个平面的平行度、两端孔的同轴度,都取决于幢模架和铿杆的配合精度。
此种结构方式不能采用高速锉削,切削速度一般不大于SDmrnlmin,性模和惶杆之间的间隙为D.D1 mm一O.DS ,如过小,镬模导套和惶杆易研死,过大又很难控制精度,因此,此种工艺方式只能保证轴承孔尺寸精度r 价,水平和垂直两个平面的平行度公差为n.m 全长。
1.Fnss 带同步器变速箱箱体轴承孔稍度实现起来难度很大,因此采用日本国生产的卧式五轴金刚健床。
刀具为硬质合金机央刀具,刀尖圆角半径为a.8 二。
采用一面两销定位,且两销结构形式为死销,定位精度高。
主要切削参数: 四个铀承孔的切削速度,=los }}}. 倒车惰轮轴孔的切削速度v =80 m/min ,走刀量f} 2g }}n, 直径切削余量为D.55 mm切削余量较小,又是薄壁零件,夹紧力为 5 880 IV,不宜过大,作用点在箱壁处,防止受力、受热变形。
位头的材料为高弹性合金钢。
此工序可以保证孔径公差峨,表面粗糙度R,1 .6 um.轴承孔相互之间在水平和垂直两个平面内的平行度公差为0 .D4 mm/科6n}una2.4J0U2-带弋孔*3支承—■导向扳i,沖一预宅程乘灣工舛托IS许、I—交改極柚Mill-刖数定慳的图3.2.7为精健轴承孔夹具结构原理图。
用手将工件推人工件托板6,8上。
侧导向板3,11起侧导向作用,防止零件扭斜。
可上下移动的预定位板5,9,.起预定位作用。
侧导向板3,11、工件托板6,$和抽缸7,14连接在一起,在油缸作用下,使工件下落至2,4,12带气孔支承钉上,工件定位销孔穿上定位销1,13,工件完成定位。
工件与夹具四个支承钉间有间隙报警装置,当工件和支承钉的间隙大于0 .1 mm时,报警红灯即亮,说明装夹或工件定位面平面度不合格。
该机床具有手动补偿装置。
其补偿原理如图328所示。
压缩空气经过净化以后,进人调压阀E,变成恒定的39.2 x 1(14 Pa压缩空气。
压缩空气进人气缸以后。
推动油增压装置。
压缩气缸A的右端,使左腔的油压扩大54倍至1 950 x图3 2^补怜机人一弋飯僅一祜蔦低一增压后樋曽甘借樓止—记压闺』一a力杆1 了Pa的压力油,通过管路C进人D室,使径向补偿头产生逆时针微量转动,从而实现补偿。
如需继续补偿,通过补偿调节器再供一次压缩空气即可。
压力和补偿值成线性函数关系,如图3.2.9所示。
④变速箱箱体前后端面的加工:为保证两个端面对轴承孔的垂直度,CA15和LF'(1155两种变速箱箱体采用的定位基准均为第一轴和第二轴轴承孔。
前后端面的精加工,不采用一面两销定位,因为两个工艺孔经过二十几个工序的使用,精度已经丧失。
经计算,该方法保证不了端面的位置公差。
采用轴承孔定位.可以使测t基准、定位基准和设计基准重合,避免了基准不重合产生的误差。
图3甲2.}U 为该工序夹具结构原理图。
以箱体上盖连接平面和两个 工艺孔做预定位。
支承板与上盖连接平面预留1 rxun 间隙。
齿条活塞杆3,6通过齿轮5 使心轴1,}穿人轴承孔,限制四个自由度。
用四个相同的油缸,,通过弹黄8使倾斜角为 70的斜楔顶起四个相同支承销10,将上盖连接平面托平并自锁,限制一个转动自由度。
削 边销9限制一个移动自由度。
夹紧点在箱体顶部。
心越闻粧 山、―悔轮悟寡fHT-載 內涯Iff丼・;—酗边ifl I。