克塑料注射机液压系统设计计算 完整版
注塑机液压系统回路i设计
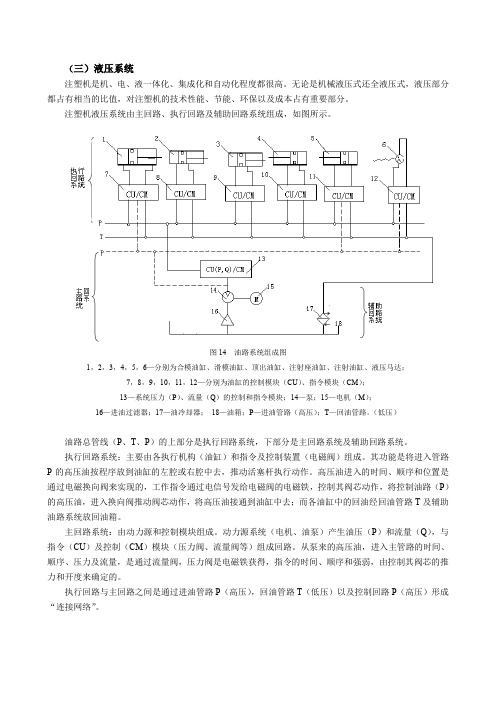
注塑机是机、电、液一体化、集成化和自动化程度都很高。
无论是机械液压式还全液压式,液压部分都占有相当的比值,对注塑机的技术性能、节能、环保以及成本占有重要部分。
注塑机液压系统由主回路、执行回路及辅助回路系统组成,如图所示。
图14 油路系统组成图1,2,3,4,5,6—分别为合模油缸、滑模油缸、顶出油缸、注射座油缸、注射油缸、液压马达;7,8,9,10,11,12—分别为油缸的控制模块(CU)、指令模块(CM);13—系统压力(P)、流量(Q)的控制和指令模块;14—泵;15—电机(M);16—进油过滤器;17—油冷却器;18—油箱;P—进油管路(高压);T—回油管路。
(低压)油路总管线(P、T、P)的上部分是执行回路系统,下部分是主回路系统及辅助回路系统。
执行回路系统:主要由各执行机构(油缸)和指令及控制装置(电磁阀)组成。
其功能是将进入管路P的高压油按程序放到油缸的左腔或右腔中去,推动活塞杆执行动作。
高压油进入的时间、顺序和位置是通过电磁换向阀来实现的,工作指令通过电信号发给电磁阀的电磁铁,控制其阀芯动作,将控制油路(P)的高压油,进入换向阀推动阀芯动作,将高压油接通到油缸中去;而各油缸中的回油经回油管路T及辅助油路系统放回油箱。
主回路系统:由动力源和控制模块组成。
动力源系统(电机、油泵)产生油压(P)和流量(Q),与指令(CU)及控制(CM)模块(压力阀、流量阀等)组成回路。
从泵来的高压油,进入主管路的时间、顺序、压力及流量,是通过流量阀,压力阀是电磁铁获得,指令的时间、顺序和强弱,由控制其阀芯的推力和开度来确定的。
执行回路与主回路之间是通过进油管路P(高压),回油管路T(低压)以及控制回路P(高压)形成“连接网络”。
注塑机应用液压组件非常广泛。
⑴.动力组件由电机带动泵实现电能—机械能—液压能的转换。
有各种油泵和液压马达。
油泵是靠封闭容腔使其容积发生变化来工作的。
理想的泵是没有的,因为结构上总会有制品缝隙就会有泄漏,而且机械磨损也会产生间隙,所以就要考虑泵的效率。
塑料注射机液压系统设计
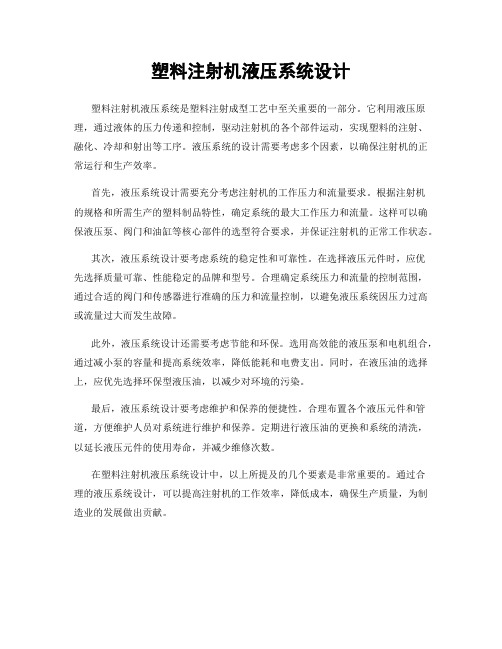
塑料注射机液压系统设计
塑料注射机液压系统是塑料注射成型工艺中至关重要的一部分。
它利用液压原理,通过液体的压力传递和控制,驱动注射机的各个部件运动,实现塑料的注射、融化、冷却和射出等工序。
液压系统的设计需要考虑多个因素,以确保注射机的正常运行和生产效率。
首先,液压系统设计需要充分考虑注射机的工作压力和流量要求。
根据注射机
的规格和所需生产的塑料制品特性,确定系统的最大工作压力和流量。
这样可以确保液压泵、阀门和油缸等核心部件的选型符合要求,并保证注射机的正常工作状态。
其次,液压系统设计要考虑系统的稳定性和可靠性。
在选择液压元件时,应优
先选择质量可靠、性能稳定的品牌和型号。
合理确定系统压力和流量的控制范围,通过合适的阀门和传感器进行准确的压力和流量控制,以避免液压系统因压力过高或流量过大而发生故障。
此外,液压系统设计还需要考虑节能和环保。
选用高效能的液压泵和电机组合,通过减小泵的容量和提高系统效率,降低能耗和电费支出。
同时,在液压油的选择上,应优先选择环保型液压油,以减少对环境的污染。
最后,液压系统设计要考虑维护和保养的便捷性。
合理布置各个液压元件和管道,方便维护人员对系统进行维护和保养。
定期进行液压油的更换和系统的清洗,以延长液压元件的使用寿命,并减少维修次数。
在塑料注射机液压系统设计中,以上所提及的几个要素是非常重要的。
通过合
理的液压系统设计,可以提高注射机的工作效率,降低成本,确保生产质量,为制造业的发展做出贡献。
240克塑料注射机液压系统设计计算

―240g注塑机液压系统的设计与计算大型塑料注射机目前完全由液压控制。
其基本工作原理是:粒状塑料通过料斗进入螺杆推进器,螺杆旋转将物料向前推动,同时,由于螺杆配有电加热器,物料熔化成粘液状态。
在此之前,夹紧机构已关闭。
模具关闭,当物料在螺旋桨的前端形成一定压力时,注射机构开始将液态物料以高压注入模具腔中,然后在一定的压力保持和冷却期间,打开模具以弹出模制的塑料产品。
完成一个动作周期。
现在以240g注塑机为例进行液压系统设计计算。
塑料注射器的工作周期为:夹紧→注射→保压→冷却→模子→喷射∣→螺杆预塑进料其中,合模的作用分为:快速合模,缓慢合模和合模。
夹紧时间相对较长,直到打开模具的时间就是夹紧阶段。
1. 240g注塑机液压系统设计要求及相关设计参数1.1液压系统要求(1)合模动作应平稳,两个模具合上时不应有冲击;(2)合模时,合模机构应保持合模压力,以防止在注射过程中合模冲开。
注射后,注射机构应保持注射压力,以用塑料填充空腔;(3)在预塑料进给过程中,螺杆旋转,并且将物料推入螺杆的前端。
此时,螺杆和注射机构一起向后移动。
为了使螺杆前端的塑料具有一定的密度,注射机构必须具有一定的抗退缩性。
(4)为确保安全生产,系统应配备安全联锁装置。
1.2液压系统设计参数240g注塑机的液压系统的设计参数如下:螺丝直径38mm螺丝行程:200mm最大注射压力143MPa螺杆驱动功率5KW螺杆转速61r / min注射座行程240mm注射座最大推力26kN 最大夹紧力(夹紧力)910kN 开启力44kN 移动模板最大行程350mm 快关速度0.1m / s 慢关速度0.02m / s 开模速度快0.13m / s 开模速度慢0.03m / s 注射速度0.07m / s 注射座前进速度0.06m / s 注射座向后移动速度0.08m / s2.液压执行原始负载力负载和扭矩计算2.1液压缸负载力的计算(1)夹紧缸的加载力锁模缸在合模过程中承受的载荷较小,其外载荷主要是可动模及其连杆部件的起动惯性力和导轨的摩擦力。
XS-ZY-250型塑料机注塑成型机液压系统设计

6.1验算回路中的压力损失……………………………………………………………22
6.2液压系统发热温升计算……………………………………………………………23
结论………………………………………………………………………………………26
关键词:注射机;液压系统;技术参数;节能
XS-ZY-250-type plastic injection molding machine hydraulic system design
Abstract
This design constitutes through work principle and its organization that understanding injects machine, analyze constitute of its typical model spare parts and act principle, and pass the work condition that the liquid presses system analysis, the initial calculation make sure it main technique parameter, design its liquid to press system, choose a reasonable liquid to press an original piece, make the oil pump turn of electrical engineering soon with note Su machine discharge and pressure product that the liquid press that work need into a direct proportion, reform a traditional metered pump change the Pin change to measure a pump, make to overflow to flow the return of valve oil discharge to decline to least thus, have no high pressure to reduce expenses energy loss and then have tradition to"consume ability type" that the high pressure reduce expenses to note Su machine to get stripe for have no the high pressure reduce expenses of"economy energy type" note Su machine.
注射机液压系统设计

目录1.引言 (1)2.正文 (2)2.1 250克注射机液压系统设计 (4)2.2 250注射机液压系统设计参数 (4)2.2.1 对液压系统的要求 (4)2.2.2 液压系统设计参数 (5)2.3 注射机液压执行元件的设计 (5)2.3.1 液压系统执行元件载荷和转矩的计算 (6)2.4 液压系统中主要参数的计算 (7)2.4.1 初选系统工作压力 (7)2.4.2 计算液压缸主要结构尺寸 (7)2.4.3 计算液压马达的排量 (10)2.4.4 计算液压执行元件实际工作压力 (11)2.4.5 计算液压执行元件实际需要的流量 (11)2.5.制定液压系统方案和拟定系统图 (12)2.5.1 制定系统的方案 (12)2.5.2 拟定液压系统图 (21)2.6.液压元件的选择 (21)2.6.1 液压泵的选择 (22)2.6.2 电动机功率的确定 (30)2.6.3 液压阀的选择 (31)2.6.4 液压马达的选择 (36)2.6.5 油管内径的计算 (36)2.6.6 油箱油箱容积的计算 (36)2.7 液压系统性能验算 (37)2.7.1 计算回路中的压力损失 (37)2.7.2 液压系统发热温升的计算 (39)2.8 常见系统故障与排除方法 (43)2.8.1 管路常见问题及排除 (43)2.8.2 蓄能器的故障及排除 (44)2.8.3 冷却器的故障和排除 (45)2.8.4 油箱的故障及排除 (46)2.9 结束语 (46)3.致谢词 (46)4.参考文献 (46)1.引言随着科技的发展脚步越来越快时,模具的成型设备也趁着这个势头突飞猛进。
国外塑料机械工业未来的总体发展趋势,是朝着精密、高质、高效、节能、低噪音及可持续发展的方向发展。
塑料机械工业所提供的装备主要是为信息、生物、建筑、包装、交通及家电等行业服务。
国外塑料机械工业的发展趋势大致包括以下几个方面。
微型大型并重微型化是今后各类塑机产品的发展方向之一。
注 塑 机 液 压 系 统 设 计

机电工程学院《液压与气压传动课程设计》说明书课题名称:注塑机液压系统设计学生姓名:学号:专业:班级:成绩:指导教师签字:2013年6月22日课程设计任务设计题目:注塑机液压系统设计一、设计要求及任务1.设计要求(1)最大注射量:250 cm3/次;螺杆直径: d=40mm;螺杆行程:s1=200mm;最大注射压力p=160MPa;注射速度:vw=0.075m/s;螺杆转速:n=65r/min;螺杆驱动功率:Pm=5.5kW;注射座最大推力:Fz=35(kN);注射座行程:s2=250(mm);注射座前进速度:vz1=0.075m/s;注射座后退速度:vz2=0.085m/s;最大合模力(锁模力)Fh=950 (kN);开模力:Fk=49 (kN);动模板(合模缸)最大行程s3=360 (mm);快速合模速度:vhG = 0.25m/s;慢速合模速度:vhm =0.03m/s;快速开模速度:vkG =0.15m/s;慢速开模速度:vkm =0.035m/s;(2)实现的工作循环:1)准备工作:料斗加料,螺旋机构将一定量的物料送入料筒,由桶外电加热器加热预塑,合上安全门。
2)工作循环:合模—注射—包压—冷却—预塑—注射模后退—开模—顶出制品—顶出缸后退—合模(3)液压系统原理方案设计;液压系统设计计算及元件选择;(4)注塑机液压系统总图设计。
2.设计任务(1)绘制液压系统原理图;(2)系统零部件的计算与选型;(3)按照要求编写设计说明书目录摘要 (Ⅰ)第1章绪论 (4)1.1 注塑机概述 (4)1.2 注塑机的工作循环过程 (4)1.3 注塑机对液压系统的要求 (4)1.4 液压系统设计参数 (4)1.5 注塑机液压系统原理图 (5)第2章计算执行元件的主要结构参数 (7)2.1 各液压缸的载荷力计算 (7)2.2 液压系统主要参数计算 (8)2.3 制定系统方案和拟定液压系统图 (10)第3章液压元件的选择 (13)3.1 液压泵的选择 (13)3.2 液压阀的选择 (14)3.3 液压马达的选择 (14)3.4 确定油箱的有效容积 (15)第4章液压系统性能验算 (16)4.1 验算回路中的压力损失 (17)4.2 系统总输出功率 (18)4.3 冷却器所需冷却面积的计算 (18)心得体会 (19)参考文献 (20)第1章绪论1.1注塑机概述注塑机是一种通用设备,通过它与不同专用注塑模具配套使用,能够生产出多种类型的注塑制品。
塑料注射机液压系统设计
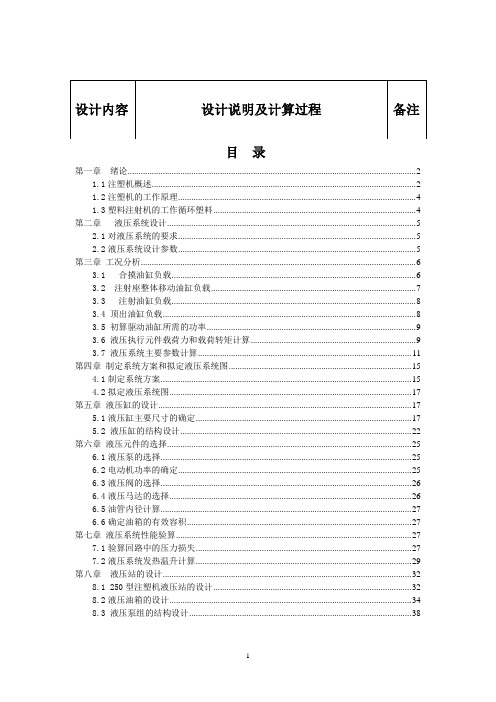
目录第一章绪论 (2)1.1注塑机概述 (2)1.2注塑机的工作原理 (4)1.3塑料注射机的工作循环塑料 (4)第二章液压系统设计 (5)2.1对液压系统的要求 (5)2.2液压系统设计参数 (5)第三章工况分析 (6)3.1 合摸油缸负载 (6)3.2 注射座整体移动油缸负载 (7)3.3 注射油缸负载 (8)3.4 顶出油缸负载 (8)3.5 初算驱动油缸所需的功率 (9)3.6 液压执行元件载荷力和载荷转矩计算 (9)3.7 液压系统主要参数计算 (11)第四章制定系统方案和拟定液压系统图 (15)4.1制定系统方案 (15)4.2拟定液压系统图 (17)第五章液压缸的设计 (17)5.1液压缸主要尺寸的确定 (17)5.2 液压缸的结构设计 (22)第六章液压元件的选择 (25)6.1液压泵的选择 (25)6.2电动机功率的确定 (25)6.3液压阀的选择 (26)6.4液压马达的选择 (26)6.5油管内径计算 (27)6.6确定油箱的有效容积 (27)第七章液压系统性能验算 (27)7.1验算回路中的压力损失 (27)7.2液压系统发热温升计算 (29)第八章液压站的设计 (32)8.1 250型注塑机液压站的设计 (32)8.2液压油箱的设计 (34)8.3 液压泵组的结构设计 (38)图3.2根据最大注射压力和螺杆直径,可确定注射缸的最大推力为:P4z=1/4兀d2螺P注=206.6(KN)保压过程中油缸负载一般要比注射过程油缸负载小,其值随制品形状,塑料品种以及成型工⑵注射座移动缸的活塞和活塞杆直径座移动缸最大载荷为其顶紧之时,此时缸的回油流量虽经节流阀,但流量极小,故背压视为零,则其活塞直径为 m m p F D y 076.0105.610344641=⨯⨯⨯⨯==ππ 0.1m设计说明及计算过程图2 注塑机液压系统原理图液压执行元件以及各基本回路确定之后,把它们有机地组合在一起。
注射机液压系统设计

本科毕业论文题目:SZ200/1000注射机液压系统设计院系:机械工程学院专业:班级:学生姓名:指导教师:论文提交日期:2011年月日论文答辩日期:2011年月日毕业设计任务书机械工程学院机械设计制造及自动化摘要本设计主要研究了SZ-200/1000注射机液压系统。
注射机包括注射装置和合膜装置。
在注射机注射成型过程中,将塑料注入注射机的料筒,在螺杆的作用下变成硬化的液体态,而后被注入模腔中形成成品,最后将制品顶出。
因此注射机的成型过程为闭模,注射座前移,注射保压,防流延,开模,顶出制件及注射座后移过程。
这一系列的动作过程是本次设计液压系统完成的。
本设计液压系统除包括注射缸,顶出缸,注射座移动缸,合模缸外,还有各种阀和液压泵,液压马达及各种辅助元件等。
为满足注射机的动作而设计各个液压回路,还因为考虑到为使各个动作快速改变及动作平稳,使用了叶片式双联泵并设计了三级压力设计回路和节流调速回路,以及在液压系统中增加了许多辅助元件。
此外本设计还设计了辅助件——油箱。
液压缸参数的设计包括各缸的缸筒内径,活塞杆直径,缸筒壁厚,活塞宽度,导向长度和隔套长度的设计。
各缸的校核强度和活塞杆连接螺栓的校核。
采用了开式,矩形结构。
关键词:液压系统,液压缸,油箱AbastractThis design studied the hydraulic system of the SZ-200/1000 injection machine primarily. The injection machine includesinjecting device and molding device. In the process of injection machine injecting model,the plastic will be infused into the charging barrel in injection molding machine,in the function of screw the plastic are turn to the plastifying liquid posture,then they are injected into mold antrum and become the produce,which will be crest out finall. Therefore the injecting model process of injection machine is a course as to shuttling the mold,injection seat forward leading,injecting,protecting to press,defending to flow to postpone,openning the mold,driving out manufacture piece and injection seat backspace. This a series of action process will be complete by the hydraulic pressure system in this design. The hydraulic pressure system in this design includs other then injection urn,still have every kind of value,hydraulic pump,hydraulic motor and different kinds of assistant component etc. For satisfaction with the action of injecting machine design every hydraulic pressure loop,in consideration of making each action fast to change and act steady,used a type of the doubt unite pump with vane,design the 3_rated pressure loop and throttle timing loop,and increase many assistance in hydraulic pressure system.In addition this design still designed the assistant a-oil tank,The design parameters of the hydraulic cylinder include every cylinder’s innerdiameter,piston pole diameter,cylinder’s wall thickness,pision’width,guide length and parttion cover length. In this design also have the strength checking of every cylinder and piston pole linking bolts checking.adopting the open type,rectangle construction.Key words:hydraulic system , hydraulic cylinder , oil tank目录引言 (1)第一章结构说明 (3)1.1 选择注射机模型 (3)1.2 选择注射装置形 (3)1.2.1 注射装置的结构 (3)1.2.2 螺杆传动系统的选择与连接 (3)1.2.3 注射座的设计 (4)1.2.4 油缸的结构与设置 (4)1.3 选择合模装置 (4)1.3.1 总体方案的设计 (4)1.3.2 顶出结构 (5)1.4 液压系统设计 (6)第二章SZ-200/1000 注射机液压系统的设计 (7)2.1 螺杆直径 (7)2.2 油缸负载计算 (8)2.2.1 合模油缸负载 (8)2.3 油缸工作压力和流量的确定 (10)2.3.1 油缸工作压力的确定 (10)2.4 油缸各参数计算 (12)2.4.1 注射油缸 (12)2.4.2 合模缸 (12)2.4.3 注射座移动缸 (13)2.4.4 顶出缸 (13)2.5 明确各执行元件的载荷 (14)2.5.1 合模缸 (14)2.5.2 注射座移动缸 (14)2.5.3 注射座 (14)2.5.4 顶出缸 (14)2.6 液压泵的流量及选择............. . (15)2.7 液压马达的选择 (16)2.8 工作系统的流量、工作压力及速度的计算 (16)2.9 注射机各动作循环中油缸所需功率的计算 (17)2.10 油箱的设计计算………………………………………….. . 192.10.1 油箱的设计方案…………………………………… . 192.10.2 容积及其主体尺寸的确定 (20)第三章示意图 (21)3.1 SZ-200/1000 注射机液压系统 (21)3.2 注射座移动缸示意图及说明 (24)3.3 油箱示意图及说明................................................. . 25 3.4 顶出缸端盖.. (26)结论 (27)致谢……………………………………………………………………………. .29引言塑料注射成型设备出现在二十世纪七十年代,在仅有的七十年左右的时间己发展成为一种非常重要、最具代表性的塑料加工方法和机种,注塑制品也为越来越多的行业采用。
液压系统设计计算举例

液压系统设计计算举例液压系统设计计算举例XS-ZY-500注塑机液压系统设计计算⼆、XS-ZY-500注塑机成型设计技术参数公称注射量(L) 0.5螺杆直径(mm) 63螺杆⾏程(mm) 200最⼤注射压⼒(MPa) 110注射容量(理论值)(cm) 665预塑电机(KW) 7.5塑化容量(N/h) 450螺杆转速(r/min) 20—80 料筒加热功率(KW) 14注射座⾏程(mm) 280合模⼒(KN) 3500启模⼒(KN) 135顶出⼒(KN) 30最⼤注射⾯积(cm) 1000模板最⼤开距(mm) 950拉杆间距(mm) 540x440 模具最⼤厚度(mm) 450模具最⼩厚度(mm) 300注射总⼒(KN) 345注射座最⼤推⼒(KN) 73螺杆驱动功率PM(KW) 5KW各油缸运动数值如下:快速合模速度(m/s) 0.12慢速合模速度(m/s) 0.024 快速启模速度(m/s) 0.13慢速启模速度(m/s) 0.028 快速注射速度(m/s) 0.07注射座前移速度(m/s) 0.06注射座后退速度(m/s) 0.08顶出速度(m/s) 0.04三、⼯况分析xxxx塑料注射成型机械液压系统的特点是在整个动作循环过程中,系统负载和速度变化均较⼤,在进⾏⼯况分析时必须加以考虑:(⼀)合模油缸负载xxxx闭模动作的⼯况特点是:模具闭合过程中的负载是轻载,速度有慢—快—慢的变化;模具闭合后的负载为重载,速度为零。
1. 根据合模⼒确定合模缸推⼒:根据连杆受⼒分析可得出合模油缸推⼒为:式中:N1z——合模油缸为保证模具锁紧所需的推⼒,N.ssssss N合————模具锁紧所需的合模⼒,N.ssssss l1/l——有关长度⽐,⼀般取其值为0.7.为保证模具锁紧⼒(3500KN)所需的油缸推⼒为: N1z=223KN2. 空⾏程时油缸推⼒:aaaa空⾏程时油缸推⼒P1q只须克服摩擦⼒的要求,根据设计经验得:N1q=0.14N1z z, 故s N1q=31.22KN3. 启模时油缸的推⼒:ssss启模时油缸的推⼒需满⾜启模⼒和克服油缸摩擦⼒的要求。
简易注塑机液压系统设计

目录一、设计要求和概述 (3)1.1设计任务: (3)1.1.1动作参数 (3)1.2 设计要求说明 (3)1.2.1 液压系统设计 (3)1.2.2 液压装置结构设计 (3)1.2.3 绘制工程图、编写设计说明书 (4)二、拟定液压系统原理图 (4)2.1 确定供油方式 (4)2.2 调速方式的选择 (4)2.3 速度换接方式的选择 (4)2.4 液压系统原理图 (5)2.5 系统工作原理 (5)2.6 电磁铁动作顺序表 (6)三、液压系统的计算和选择液压元件 (6)3.1 液压执行元件主要尺寸的确定 (6)3.1.1 工作压力P的确定 (6)3.1.3 计算注塑液压缸内径圆D和活塞直径d (7)3.1.4 计算在各工作阶段液压缸所需的流量 (8)3.2.2 泵的流量确定 (9)3.2.3 选择液压泵的规格 (9)3.2.4 与液压泵匹配的电动机的选定 (10)3.3 液压阀的选择 (10)3.4 确定管道尺寸 (11)3.5 液压油箱容积的确定 (11)四、液压系统的验算 (12)4.1 压力损失的验算 (12)4.1.1 进油路压力损失 (12)4.1.2 回油路的压力损失 (13)4.1.3 泵出口的压力Pp (14)4.2系统温升的验算 (14)五、集成块设计 (16)集成块油路图设计,如图 (16)设计过程如下: (16)5.3.1 制做液压元件样板 (16)5.3.2 决定通道的孔径 (17)5.3.3 集成块上液压元件的布置 (17)5.3.4 集成块上液压元件布置程序 (17)5.4 集成块(闭合模模块)零件图的绘制 (17)开闭模模块集成单元设计 (19)5.5课程设计心得 (20)5.6参考文献 (181)一、设计要求和概述1.1设计任务:1.1.1动作参数设计一台简易注塑机液压系统,动作顺序如下:1 模运动缸前进,闭模,行程L1,负载力F1,速度V1。
2 注射缸前进,注射,行程L2,负载力F2,速度V2。
塑料注射成型机液压系统的设计

目录1 绪论 (1)2 主要技术参数 (2)3 工况分析 (4)3.1 和模油缸缸负载…………………………………………………………3.1.2 空行程油缸推力…………………………………………………3.2 注射座整体移动油缸负载………………………………………………3.3 注射液压缸负载…………………………………………………………3.4 顶出油缸负载……………………………………………………………3.5 初算驱动油缸所需的功率………………………………………………4 油缸工作压力和流量的确定………………………………………………………4.1 油缸工作压力的确定…………………………………………………………4.2 油缸几何尺寸的确定…………………………………………………………4.2.1 根据和模油缸最大推力确定和模油缸内径…………………………4.2.2 根据注射座最大推力确定注射座移动油缸内径……………………4.2.3 根据注射油缸最大推力确定注射油缸内径…………………………4.2.4 根据顶出油缸最大推力确定顶出油缸内径…………………………4.3 根据确定的油缸直径标准值,计算实际使用的油缸工作压力,绘制整个动作循环图………………………………………………………………………4.4 油缸所需流量的确定…………………………………………………………4.5 油缸功率图的绘制……………………………………………………………5 液压系统方案和工作原理图的拟定…………………………………………………6 液压元件的选择………………………………………………………………………6.1 油泵的选择……………………………………………………………………6.1.1 油泵工作压力的确定……………………………………………………6.1.2 油泵流量的确定…………………………………………………………6.1.3 油泵电机功率的确定……………………………………………………6.2 控制阀的选择…………………………………………………………………6.3 油管内径的确定………………………………………………………………6.3.1大泵吸油管内径计算……………………………………………………6.3.2 小泵吸油管内径计算……………………………………………………6.3.3 大泵压油管内径计算……………………………………………………6.3.4 小泵压油管内径计算……………………………………………………6.3.5 双泵并联,压力油汇合后油管内径的确定…………………………7 压力系统性能的验算………………………………………………………………… 7.1 系统的压力损失验算……………………………………………………………7.1.1 局部压力损失计算…………………………………………………………7.1.2 沿程损失计算………………………………………………………………7.2液压系统发热量的计算和油冷却器传热面积的确定…………………………7.2.1液压系统发热量的计算……………………………………………………7.2.2 油箱容量计算和油箱散热面积的确定……………………………………7.2.3 油冷却器的计算……………………………………………………………参考文献……………………………………………………………………………………致谢…………………………………………………………………………………………附录…………………………………………………………………………………………1绪论注塑机是中国产量和应用量最大的塑机品种,也是中国塑机出口的主力80年代以后,中国注塑机行业得到快速发展,年增长率在20%以上,并逐步形成了以浙江宁波、广东东莞、顺德等地为主的加工基地。
塑料注射成型机液压系统设计任务书

西安科技大学高新学院毕业设计(论文)任务书系别:机电信息学院专业:机械设计制造及其自动化学生姓名:学号:设计(论文)题目:SX-ZY-250型塑料注射成型机液压系统设计起迄日期:2012年9月24日—2012年12月16日设计(论文)地点:西安科技大学高新学院指导教师:专业教研室负责人:发任务书日期:2012年8月25日毕业设计(论文)任务书1.本毕业设计(论文)课题应达到的目的:通过本课题的设计,能综合运用所学基本理论以及学到的实践知识进行的基本训练,掌握液压系统设计的思维和方法,专用元件和通用元件的参数确定。
通过给定设计题目,初步掌握确定压力,进行缸的主要参数的初步确定,按系列要求确定缸体和活塞杆的直径。
然后确定其他元件的参数,最后进行效核。
通过液压课程设计,提高学生分析和解决实际液压问题的能力。
2.本毕业设计(论文)课题任务的内容和要求(包括原始数据、技术要求、工作要求等):设计SX-ZY-250型塑料注射成型机液压系统。
该注塑机能完成的主要动作有:闭模(包括:慢速闭模-快速闭模-低压慢速闭模-高压闭模动作等);注射(注射充模行程可实现三级注射速度控制,即:注射速度Ⅰ,注射速度Ⅱ,注射速度Ⅲ);保压;启模(含慢速启模-快速启模-慢速启模);顶出;注射座整体前移和后退。
此外,预塑和螺杆后退等辅助动作也能够实现。
设计过程中液压元件所选用型号正确、有理有据;整个液压系统设计科学、规范、合理。
3.对本毕业设计(论文)课题成果的要求〔包括毕业设计、论文、图表、实物样品等〕:(1)液压系统总图1张(A0);(2)液压站总图1张;(3)液压缸装配图1张;(4)合模、顶出液压系统原理图1张(5)设计计算说明书。
①液压系统总体方案的分析论证;②液压元件设计计算和液压元器件的选择;③液压站的设计计算;④液压缸的设计计算;⑤SX-ZY-250型塑料注射成型机液压系统工作原理及工作流程。
4.主要参考文献:[1]杨培元、朱福元主编《液压系统设计简明手册》机械工业出版社2011.06.01[2]何存兴、杨曙东主编《液压传动与气压传动》华中科技大学出版社2008.04.01[3]沈兴全、吴秀玲主编《液压传动与控制》国防工业出版社2005.05.01[4]贾铭新主编.《液压传动与控制》国防工业出版社2011.07.17[5]章宏甲、黄谊主编《液压传动》机械工业出版社1993[6]北京化工学院-华南工学院合编《塑料机械液压传动》中国轻工业出版社1983[7]《液压传动设计手册》上海科学技术出版社1981[8]黎启柏主编 《液压元件手册》工业技术出版社2000[9]冯少如主编.《塑料成型机械》西北工业大学出版社1992[10]雷天觉主编液压工程手册机械工业出版社1990[11]Arthur Akers Hydraulic Power System Analysis2006-04-175.本毕业设计(论文)课题工作进度计划:9月7日之前完成“开题报告的撰写”;9月14日之前完成参考资料的搜集;9月21日之前完成设计方案的拟定;10月21日之前完成设计图纸;10月30日之前完成“技术总结报告的撰写”。
注塑机液压系统设计计算
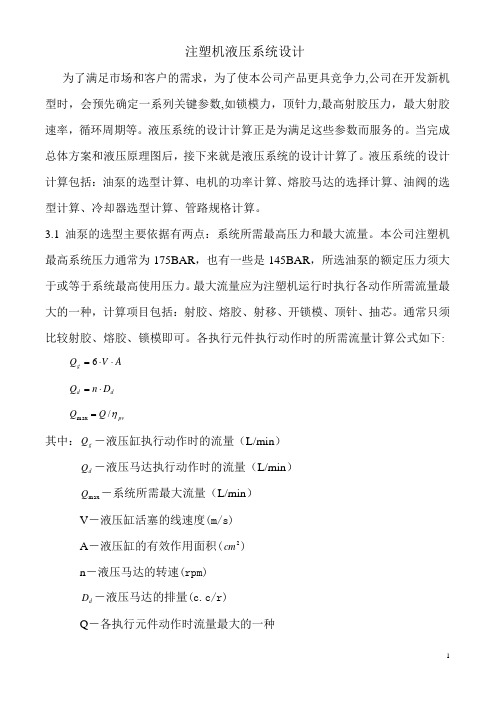
注塑机液压系统设计为了满足市场和客户的需求,为了使本公司产品更具竞争力,公司在开发新机型时,会预先确定一系列关键参数,如锁模力,顶针力,最高射胶压力,最大射胶速率,循环周期等。
液压系统的设计计算正是为满足这些参数而服务的。
当完成总体方案和液压原理图后,接下来就是液压系统的设计计算了。
液压系统的设计计算包括:油泵的选型计算、电机的功率计算、熔胶马达的选择计算、油阀的选型计算、冷却器选型计算、管路规格计算。
3.1油泵的选型主要依据有两点:系统所需最高压力和最大流量。
本公司注塑机最高系统压力通常为175BAR ,也有一些是145BAR ,所选油泵的额定压力须大于或等于系统最高使用压力。
最大流量应为注塑机运行时执行各动作所需流量最大的一种,计算项目包括:射胶、熔胶、射移、开锁模、顶针、抽芯。
通常只须比较射胶、熔胶、锁模即可。
各执行元件执行动作时的所需流量计算公式如下:A V Q g ⋅⋅=6d d D n Q ⋅=pvQ Q η/max = 其中:gQ -液压缸执行动作时的流量(L/min )d Q -液压马达执行动作时的流量(L/min ) m a x Q -系统所需最大流量(L/min )V -液压缸活塞的线速度(m/s)A -液压缸的有效作用面积(2cm )n -液压马达的转速(rpm)d D -液压马达的排量(c.c/r)Q -各执行元件动作时流量最大的一种pv η-液压泵的容积效率(一般取0.85-0.95)根据系统所需最大流量即可计算出液压泵的排量,公式如下:n Q D b /1000max ⋅=其中: b D -液压泵的排量(c.c/r)n -电机转速(rpm)选取液压泵时,其排量应大于或等于b D .3.2电机功率计算可按如下公式:L=P D n b ⋅⋅/612000其中:L -电机功率(KW)P -系统所需最高压力(BAR)其余同上.3.3熔胶马达的选取除应满足转速要求(排量已在前面确定),还需保证熔胶所需扭矩.计算公式如下:b M =55.0772D ⋅/Py其中: b M -比扭矩(kg.m/bar)D -螺杆直径(mm)Py -熔胶使用压力(BAR)3.4油阀的选型计算请参考«液压阀的选型计算规范»3.5冷却器的选型计算主要考虑热交换量,其计算公式如下:r ps L n Q ⋅=式中:Q -热交换量ps n -热交换系数(一般取0.25至0.5,本公司的机铰式注塑机上取0.35,直压式的取0.4)r L -液压系统输入功率然后根据冷却器的性能曲线来选取冷却器.3.6管路选型计算公式如下:[]410613.1⨯⨯⨯=V Q PZ d[]&pd⨯≥2δ其中:d -管的内径δ-管的壁厚Qpz -管的通过流量[]V -管的许用流速(压力管路:[]V <6.5m/s 回油管路:[]V <2.5m/s ) []&-管材的许用应力。
注塑机设计参数计算及设计参考
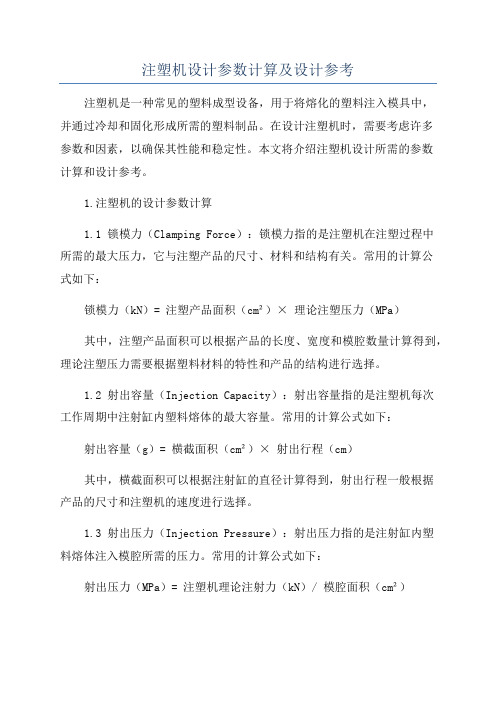
注塑机设计参数计算及设计参考注塑机是一种常见的塑料成型设备,用于将熔化的塑料注入模具中,并通过冷却和固化形成所需的塑料制品。
在设计注塑机时,需要考虑许多参数和因素,以确保其性能和稳定性。
本文将介绍注塑机设计所需的参数计算和设计参考。
1.注塑机的设计参数计算1.1 锁模力(Clamping Force):锁模力指的是注塑机在注塑过程中所需的最大压力,它与注塑产品的尺寸、材料和结构有关。
常用的计算公式如下:锁模力(kN)= 注塑产品面积(cm²)× 理论注塑压力(MPa)其中,注塑产品面积可以根据产品的长度、宽度和模腔数量计算得到,理论注塑压力需要根据塑料材料的特性和产品的结构进行选择。
1.2 射出容量(Injection Capacity):射出容量指的是注塑机每次工作周期中注射缸内塑料熔体的最大容量。
常用的计算公式如下:射出容量(g)= 横截面积(cm²)× 射出行程(cm)其中,横截面积可以根据注射缸的直径计算得到,射出行程一般根据产品的尺寸和注塑机的速度进行选择。
1.3 射出压力(Injection Pressure):射出压力指的是注射缸内塑料熔体注入模腔所需的压力。
常用的计算公式如下:射出压力(MPa)= 注塑机理论注射力(kN)/ 模腔面积(cm²)其中,注塑机理论注射力可以根据锁模力和模腔数量进行计算,模腔面积可以根据模腔的尺寸计算得到。
1.4 射胶时间(Injection Time):射胶时间指的是注塑机从开始注塑到注塑结束所需的时间。
常用的计算公式如下:射胶时间(s)= 射胶容积(cm³)/ 射胶速度(cm³/s)其中,射胶容积可以根据注射缸的容积计算得到,射胶速度一般根据产品的要求和注塑机的性能进行选择。
2.注塑机的设计参考2.1结构设计:注塑机的结构设计需要考虑机身的稳定性、模具的固定和模板的传动。
常见的设计参考包括使用优质的材料、合理的结构布局和精确的加工制造。
注塑机液压液压系统设计计算规范

注塑机液压系统设计计算标准1.目的:指导注塑机液压系统的设计开发2.适用范围:本标准适用于本公司的生产的液压式塑料成型机的开发 3.内容:为缩短用液压驱动的注塑机的开发周期,简化液压系统的开发过程, 为此制定了本标准,用于确定注塑机液压系统各参数,正确选购液压元件的型 号。
同时本标准也作为新手上路的教材。
为了满足市场和客户的需求,为了使本公司产品更具竞争力,公司在开发新机型时,会预先确定一系列关键参数,如锁模力,顶针力,最高射胶压力,最大射胶速率,循环周期等。
液压系统的设计计算正是为满足这些参数而服务的。
当完成总体方案和液压原理图后,接下来就是液压系统的设计计算了。
液压系统的设计计算包括:油泵的选型计算、电机的功率计算、熔胶马达的选择计算、油阀的选型计算、冷却器选型计算、管路规格计算。
3.1油泵的选型主要依据有两点:系统所需最高压力和最大流量。
本公司注塑机最高系统压力通常为175BAR ,也有一些是145BAR ,所选油泵的额定压力须大于或等于系统最高使用压力。
最大流量应为注塑机运行时执行各动作所需流量最大的一种,计算项目包括:射胶、熔胶、射移、开锁模、顶针、抽芯。
通常只须比较射胶、熔胶、锁模即可。
各执行元件执行动作时的所需流量计算公式如下:AV Q g ⋅⋅=6dd D n Q ⋅= pvQ Q η/max =其中:gQ -液压缸执行动作时的流量(L/min )d Q -液压马达执行动作时的流量(L/min ) max Q -系统所需最大流量(L/min ) V -液压缸活塞的线速度(m/s) A -液压缸的有效作用面积(2cm ) n -液压马达的转速(rpm) d D -液压马达的排量(c.c/r)Q -各执行元件动作时流量最大的一种pvη-液压泵的容积效率(一般取0.85-0.95)根据系统所需最大流量即可计算出液压泵的排量,公式如下:nQ D b /1000max ⋅=其中: b D -液压泵的排量(c.c/r) n -电机转速(rpm)选取液压泵时,其排量应大于或等于b D . 3.2电机功率计算可按如下公式:L=P D n b ⋅⋅/612000 其中:L -电机功率(KW)P -系统所需最高压力(BAR) 其余同上.3.3熔胶马达的选取除应满足转速要求(排量已在前面确定),还需保证熔胶所需扭矩.计算公式如下:b M =55.0772D ⋅/Py其中: b M -比扭矩(kg.m/bar)D -螺杆直径(mm) Py -熔胶使用压力(BAR)3.4油阀的选型计算请参考«液压阀的选型计算规范» 3.5冷却器的选型计算主要考虑热交换量,其计算公式如下:rps L n Q ⋅=式中:Q -热交换量psn -热交换系数(一般取0.25至0.5,本公司的机铰式注塑机上取0.35,直压式的取0.4)r L -液压系统输入功率然后根据冷却器的性能曲线来选取冷却器. 3.6管路选型计算公式如下:[]410613.1⨯⨯⨯=V Q PZd[]&pd⨯≥2δ其中:d -管的内径 δ-管的壁厚 Qpz -管的通过流量[]V -管的许用流速(压力管路:[]V <6.5m/s 回油管路:[]V <2.5m/s ) []&-管材的许用应力 例案如下PT850油压系统计算实例一.设计要求1.用途用于热熔性塑料的成型,最大锁模力8500KN.2.工艺过程循环图快速合模低压锁模高压锁紧 射台前移安全门关 射胶顶针 保压快速开模 冷却熔胶3.系统设计技术参数4.系统设计的其他要求a. 射胶速度和螺丝转速无级可调,而且可预置。
- 1、下载文档前请自行甄别文档内容的完整性,平台不提供额外的编辑、内容补充、找答案等附加服务。
- 2、"仅部分预览"的文档,不可在线预览部分如存在完整性等问题,可反馈申请退款(可完整预览的文档不适用该条件!)。
- 3、如文档侵犯您的权益,请联系客服反馈,我们会尽快为您处理(人工客服工作时间:9:00-18:30)。
―240克塑料注射机液压系统设计计算大型塑料注射机目前都是全液压控制。
其基本工作原理是:粒状塑料通过料斗进入螺旋推进器中,螺杆转动,将料向前推进,同时因螺杆外装有电加热器,而将料融化成黏液状态,在此之前,合模机构已将模具闭合,当物料在螺旋推进器前端形成一定压力时,注射机构开始将液状料高压快速注射到模具型腔中,经一定时间的保压冷却后,开模将成型的塑料制品顶出,使完成了一个动作循环。
现以240克塑料注射机为例,进行液压系统设计计算。
塑料注射器的工作循环为:合模→注射→保压→冷却→开模→顶出∣→螺杆预塑进料其中合模的动作又分为:快速合模、慢速合模、锁模。
锁模的时间比较长,直到开模前这段时间都是锁模阶段。
1.240克塑料注射机液压系统设计要求及有关设计参数1.1对液压系统的要求(1)合模运动要平稳,两篇模具闭合时不应有冲击;(2)当模具闭合后,合模机构应保持闭合压力,防止注射时将模具冲开。
注射后,注射机构应保持注射压力,使塑料充满型腔;(3)预塑进料时,螺杆转动,料被推倒螺杆前端,这时,螺杆同注射机构一起向后退,为使螺杆前端的塑料有一定的密度,注射机构必须有一定的后退阻力;(4)为保证安全生产,系统应设有安全联锁装置。
1.2液压系统设计参数240克塑料注射机液压系统设计参数如下:螺杆直径 38mm 螺杆行程: 200mm最大注射压力 143MPa 螺杆驱动功率 5KW螺杆转速 61r/min 注射座行程 240mm注射座最大推力 26kN 最大合模力(锁模力)910kN开模力 44kN 动模板最大行程 350mm快速闭模速度0.1m/s 慢速闭模速度0.02m/s快速开模速度 0.13m/s 慢速开模速度 0.03m/s注射速度 0.07m/s 注射座前进速度 0.06m/s注射座后移速度 0.08m/s2.液压执行原件载荷力荷载和转矩计算2.1个液压缸的载荷力计算(1)合模缸的载荷力合模缸在模具闭合过程中是轻载,其外载荷主要是动模及其联动部件的启动惯性力和导轨的摩擦力。
锁模时,动模停止运动,其外载荷就是给定的锁模力。
开模时,液压缸除要克服给定的开模力外,还克服运动部件的摩擦力。
(2)注射座移动缸载荷力座移缸在推进和退回注射座的过程中,同样要克服摩擦阻力和惯性力,只有当喷嘴接触模具时,才须满足注射座最大推力。
(3)注射缸载荷力 注射缸的载荷力在整个注射过程中是变化的,计算时,只须求出最大载荷力。
Fw=4πd ²p式中,d--------螺杆直径,由给定参数知:d=0.038m ;p------喷嘴处最大注射压力,已知p=162MPa 。
由此求得Fw=180kN 。
各液压缸的外载荷力计算结果列于表1。
取液压缸的机械效率为0.9,求得相应的作用于活塞上的载荷力,并列于表1中 表1各液压缸的载荷力液压缸名称 工况 液压缸外载荷 kN F w活塞上载荷力kN F 合模缸合模 90 100锁模9101011。
2.2进料液压马达载荷转矩计算Tw=πn 2c p =606114.321053⨯⨯⨯=783N •m取液压马达的机械效率为0.95,则其载荷转矩T=m ηw T =95.0783=824N •m 3.液压系统主要参数计算.3.1初选系统工作压力240克塑料注射机属于小型液压机,载荷最大时为锁模工况,此时,高压油用增压缸提供;其他工况时,载荷都不太高,参考设计手册,初步确定液压系统工作压力为6.5MPa 。
3.2计算液压缸的主要结构尺寸(1)确定合模缸的活塞及活塞杆直径合模缸最大载荷时,为锁模工况,其载荷为889kN ,工作在活塞杆受压状态。
活塞直径 D=()]1p π[p 4221ϕ--F此时1p 是由增压缸提供的增压后的进油压力,初定增压比为5,则1p =5×6.5MPa=32.5MPa ,锁模工况时,回油量极小,故P 2≈0,求得合模缸的活塞直径为D h =m64105.3214.31010114⨯⨯⨯⨯=0.199m,取D h =0.2m按表2—5取d /D=0.7,则活塞杆直径d h =0.7×0.2m=0.14m ,取d h =0.15m 。
为设计简单加工方便,将增压缸的缸体与合模缸体做成一体(见图1),增压缸的活塞直径也为0.2m 。
其活塞杆直径按增压比为5,求得 D z=52h D =52.02=0.089m,取d z =0.09m (2)注射座移动缸的活塞和活塞杆直径座移动缸最大载荷为其顶紧之时,此时缸的回油量虽经节流阀,但流量极小,故背压视为零,其活塞杆直径为D h=14P Fπ=m 63105.610294⨯⨯⨯⨯π=0.075m,取D y =0.01m 由给定的设计参数知,注射座往复速比为0.08/0.06=1.33查表2—6得d/D=0.5,则活塞杆直径为:=0.5×0.01m=0.05m(3)确定注射缸的活塞及活塞杆直径当液态塑料充满模具型腔时,注射缸的载荷达到最大值213KN ,此时注射活塞移动速度也近似等于零,回油量极小;故备压力可以忽略不计,这样D s =14P F π=m 64105.610184⨯⨯⨯⨯π=0.188m,,取D s =0.20m 活塞杆直径一般与螺杆外径相同,取d s =0.038m 。
3.3计算液压马达的排量液压马达是单向旋转的,其回油直接回油箱,其视为出口压力为零,机械效率为0.95,这样 V M =m W P T ηπ12=r m /95.010*******.3235⨯⨯⨯⨯=0.8×10-3m 3/r 3.4计算液压执行元件实际工作压力按最后确定的液压缸的结构尺寸合液压马达排量,计算出各工况时液压执行元件实际工作压力,见表2,3.5计算液压执行元件实际所需流量根据最后确定的液压缸的结构尺寸或液压马达的排量及其运动速度或转速,计算出个液压执行原件实际所需流量,见表3。
4制定系统方案和拟定液压系统图(1)执行机构的确定本机动作机构处螺杆是单向旋转外,其他机构均为直线往复运动,各直线运动机构均采用单活塞杆双作用液压缸直接驱动,螺杆则用液压马达驱动,从给定的设计参数可知,锁模时所需的力气最大,为910KN。
为此设置增压液压缸,得到锁模时的局部高压来保证锁模力。
(2)合模缸动作回路合模缸要求其实现快速.慢速.锁模.开模动作。
其运动方向由电液换向阀直接控制。
快速运动时,需要有较大流量供给。
慢速合模只要有小流量供给即可。
锁模时,由增压缸供油。
(3)液压马达动作回路螺杆不要求反转,所以液压马达单向旋转即可,由于其转速要求较高,而对速度平稳性无过高要求,故采用旁路节流调速方式。
(4)注射缸运作回路注射缸运动速度也较快,平稳性要求不高,故也采用旁路节流调速方式。
由于预塑时有背压要求,有无杆腔出口处串联背压阀。
(5)注射座移动缸运作回路注射座移动缸,采用回油节流调速回路。
工艺要求其不工作时,处于浮动状态,故采用Y型中位机能的电磁换向阀。
(6)安全联锁措施本系统为保证安全生产,设置的安全门,太安全门下端装一个行程阀,用来控制合模缸的运作。
将行程阀串在控制合模缸换向的液动阀控制油路上,安全门没有关闭时,行程阀没被压下,液动换向阀不能进控制油,电液换向阀不能换向,合模缸也不能合模。
只有操作者离开,将安全门关闭,压下行程阀,合模缸才能合模从而保障了人身安全。
(7)液压源的选择该液压系统在整个工作循环中需油量变化较大,另外,闭模和注射后又要求有较长时间的保压,所以选用双泵供油系统。
液压缸快速运作时,双泵同时供油,慢速运作或保压时由小泵单独供油,这样可减少功率损失,提高系统效率。
液压执行元件及各基本回路确定之后,把它们有机地组合在一起。
去掉重复多余的元件,把控制液压马达的换向阀与泵的卸荷阀合并,使之一阀两用。
考虑注射缸同合模缸之间有顺序动作的要求,两回路接合部串联单向顺序阀,再加上其他一些辅助元件便构成了240克塑料注射机完整的液压系统图,见系统原理图,其动作循环表,见原理图下方表。
5.液压元件的选择5.1 液压泵的选择(1)液压泵工作压力的确定Pp≥P1+∑△P多余的元件,把控制液压马达的换向阀与泵的卸荷阀合并,使之一阀两用。
考虑注射缸同合模缸之间有顺序动作的要求,两回路接合部串联单向顺序阀,再加上其他一些辅助元件便构成了240克塑料注射机完整的液压系统图,见图2,其动作循环表,见表4。
5.1 液压泵的选择(1)液压泵工作压力的确定Pp≥P1+∑△PP1是液压执行元件的最高工作压力,对于本系统,最高工作压力是增压缸锁模时的入口压力,P1=6.5MPa;∑△P是泵到执行元件间总的管路损失。
由系统图可见。
从泵到增压缸之间串接有一个单向阀和一个换向阀,取∑△P=0.5MPa。
液压泵工作压力为 Pp=(6.5+0.5)MPa=7MPaq≥K(∑qmax)(2)液压泵流量的确定p由工况图看出,系统最大流量发生在快速合模工况,∑qmax=3L/s。
取泄露系q=3.6L/s (216L/min)数K为1.2,取得液压泵流量p选用YYB-BC171/48B型双联叶片泵,当压力为7MPa时,大泵流量为157.3L/min,小泵流量为44.1L/min。
5.2电动机功率的确定注射机在整个动作循环中,系统的压力和流量都是变化的,所需功率变化较大,为满足整个工作循环的要求,按较大功率段来确定电动机功率。
从工况图看出,快速注射工况系统的压力和流量均较大。
此时,大小泵同时参加工作,小泵排油除保证锁模压力外,还通过顺序阀将压力油供给注射缸,大小泵出油汇合推动注射缸前进。
前面的计算已知,小泵供油压力为Pp1=7MPa,考虑大泵供油压力应为Pp2=(5.9+0.5)=6.4MPa,取泵的总效率,泵的总驱动功率为P=p ppqpqpη2 211+=21.924KW考虑到注射时间较短,不过3s,而电动机一般允许短时间超载25℅,这样电动机功率还可降低一些。
P=21.924×100/125=17.54KW验算其他共况时,液压泵的驱动功率均小于或近于此值。
差产品样本,选用18KW的电动机。
5.3液压阀的选择选择液压阀主要根据阀的工作压力和通过阀的流量。
本系统工作压力在7MPa左右,所以液压阀都选用中、高压阀。
所选阀的规格型号见表5。
5.4液压马达的选择在3.3节已求得液压马达的排量为0.8L/r,正常工作时,输出转矩783N.m,系统工作压力为7MPa。
选SZM0.9双斜盘轴向柱塞式液压马达。
其理论排量为0.873L/r,额定压力为20MPa,额定转速为8~100r/min,最高转矩为3057N.m,机械效率大于0.90。
三本系统管路径较为复杂,取其主要几条(其余略),有关参数及计算结果列于表6。